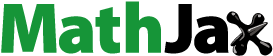
1. Introduction
The treatment of breast cancer is one of the most significant worldwide medical challenges. The patient undergoes ablation after a breast cancer diagnosing. There is a need to reconstruct the breast after ablation as soon as possible. The field of health science is still open for new approaches from different branches. There are several challenging ways, promising better recovery of patients. On the one side, there is predicted of surgery by modern numerical approaches, e.g. finite element method. On the other hand, there are improvements on daily stuffs during the recovery period, e.g. bra. Find more suitable surgical bra helping patients in the postoperative period. The interaction between the breast and the bra can be analysed using a numerical approach. A key component of the finite element model (FEM) is a material model that characterises the mechanical behaviour of the breast implant.
FEM is a common approach to overcome engineering challenges in many fields. This method is also increasingly used in the health sector. In the case of post reconstruction bras, FEM can show high contact pressure between the bra and the breast of a patient. This pressure can have an adverse effect on the recovery time after reconstruction surgery after breast ablation.
The aim of this contribution is to evaluate the accuracy of breast implant material model from article proposed by Kovar et al. (Citation2016).
2. Methods
The experimental sample was the round breast implant McGhan TSLP235g (textured shell surface, soft touch, low profile plus, size range 235 g). The implant was placed on the plane desk and compressed by a hemispherical punch with a diameter 25 mm. The velocity of the punch was 30 mm/min with a total displacement 25 mm. All processes of measurement were captured by an optical system ARAMIS (GOM) for taking a true strain of the sample. The frame rate was three images per second. The experiment was repeated five times after material relaxation.
The MSC. Marc software (MSC.Software Ltd., the Czech Republic) was used for numerical analyses of the breast implant. The material identification was done by the automatic fitting function implement in MSC. Marc. It was used force-displacement data from the experiment. The Yeoh constitutive equation resulted in the best fit between the experimental data and model data. This model is a phenomenological model for the deformation of nearly incompressible material like a gel inside the breast implant. The strain energy function is written in terms of the principal stretches I as:
where Ci are material constants. The original model proposed by Yeoh had a cubic form with only I1 dependence and is applicable to purely incompressible materials. The constants from the material data fitting function are seen in Table .
Table 1. Constants for Yeoh material model of breast implant [MPa].
The real geometry of breast implant was acquired by a 3D scanner NextEngine (Santa Monica, California). Thanks to the symmetry, it was decided for reduction on the axial symmetry model. The axial symmetry model is shown on Figure .
Results from axial symmetry model were equal to results from the full model. The convergence study was made. The highest density of elements was chosen most at the top of the implant. Largest deformations are assumed in this area. Final model contained 212 triangular elements. Punch was modelled as the quadrant and base desk was modelled by line. Contact between an implant and a desk was set as frictional one with friction coefficient 0.8 (rubber-metal). Friction coefficient was set on 0.6 (rubber-plastic) between punch and implant. Computing time of the axial symmetry model was less than 5 seconds on a regular computer.
3. Results and discussion
The comparison of the force displacement curve from the FEM analysis and the experimental data can be seen in Kovar et al (Citation2016). This curve has good match with satisfactory error.
However aim of this article is comparing the deformed shape of implant. Surface curve from axial symmetry model has significantly more different shape than the curve from real measurement done by Aramis. These shapes are shown on Figure .
There is not full meridian of breast implant, but only the area around the bulging edge of implant. A section near to the punch is pulled into the center. Bottom side of the implant is not visible because measuring head of Aramis from the start of shooting. These are reasons why is captured smaller area than during the start of the experiment. Despite this, we can make a conclusion following from comparison the FEM model with Aramis data. Over the measured region, the displacement of the implant surface in the experiment was greater than the corresponding model displacements. This error has been attributed to the use only one material model and modelling implant as one part. It is necessary to get a good shape consensus for the further usable in the FEM model of breast with a bra.
4. Conclusions
Modelling the interaction between the breast and the postoperative bra is interesting not only from faster recovery, but also in term of patient comfort. One of the challenges is to find a usable material model of breast implant, which can be used on many sizes of implants. The final behaviour of model breast with a bra depends on the properties of the implant. This article shows the validation of model that assumes the implant is homogeneous. Only one material model cannot achieve a satisfactory match between the surface curve in the experiment and the FEM simulation. The original assumption was wrong. Modelling the implant as a heterogeneous material may result in a better agreement between the model data and experimental data. The implant will be divided on cover material and filling gel in the future work. They have same chemical behaviour, but they have differing state of aggregation.
Acknowledgements
This publication was written at the Technical University of Liberec as part of the project “SGS 2017- 21196 of the Technical University of Liberec - Textile Faculty, Czech Republic” with the support of the Specific University Research Grant, as provided by the Ministry of Education, Youth and Sports of the Czech Republic in the year 2017.
Reference
- Kovar M, Sobotka J, Capek L. 2016. Punch test of breast implant. EAN 2016 - 54th International Conference on Experimental Stress Analysis; May 30–June 2; Srní, Czech Republic. p. 75–76.