ABSTRACT
Calcium sulfonate complex grease is often selected for rolling bearing lubrication if there is a risk for water ingress, because it is reported throughout literature that it can absorb large quantities of water. In this article, atomic force microscopy (AFM) measurements have been performed on a commercially available grease with and without water to investigate the microstructural change under the influence of water. From the results it is clear that the formation of large (inverted) micelles, which can be up to a few micrometers in diameter, is the main mechanism responsible for the absorption water. These results can be used to explain the earlier reported effect of water on the rheological and lubricating properties of these grease types. It is shown here that the size distribution of the micelle structure is a function of the amount of water mixed into the bulk grease.
Introduction
The impact of the ingress of water into lubricating grease on its tribological properties is a topic that is not widely covered in the open literature. In contrast, oil in water has received much more attention in the (recent) past; see, for example Cantley (Citation1), Lugt (Citation2), and Mistry (Citation3). In 1977 it was shown that water contamination can significantly reduce the life of oil-lubricated bearings (Cantley (Citation1)). For a grease-lubricated bearing, water may cause a variety of issues ranging from corrosion (if free water is present; Lugt (Citation2)) to a reduction in consistency, leading to leakage or extensive aging due to the lack of channeling (Mistry (Citation3)). Additionally, water in grease may have an impact on the film thickness and affect bleeding behavior (Cyriac, et al. (Citation4)). In addition to the impact on life, a reduction in low-temperature performance was observed (Cyriac, et al. (Citation5)). In general, the resistance of a grease to water is related to the ability to absorb large quantities of water, without significantly affecting its properties. In previous studies, the authors have shown that the maximum amount of water that can be absorbed and its influence on performance is related to the grease type; see Cyriac, et al. (Citation5)–(Citation7). There are various standardized tests for the performance of grease under the influence of water ingress, such as water washout, water resistance, and water spray off (for a more complete overview, see Lugt (Citation2)). However, these do not answer the fundamental question of how the grease structure itself is influenced by the ingress of water. It is generally perceived that calcium sulfonate complex–thickened greases (denoted CaS) can absorb large quantities of water, even up to 44 wt%, which makes them a prime candidate for applications where water ingress is expected (Leckner (Citation8)). These properties can be ascribed to the microstructure of CaS, which is clearly different from that of other greases. First a short description of the unique microstructure of CaS based greases is given, after which the effect of water on the thickener is shown.
Historically, calcium overbased sulfonates are used as detergents in engine oils (Kobylyansky, et al. (Citation9)). These are dispersions in oil of amorphous calcium carbonate (with a size of 1.5 to 10 nm; Hone, et al. (Citation10)) that is stabilized by a surfactant (molecule with a polar head group, usually alkyl benzene sulfonic acid). In the grease-making process, the amorphous carbonate is converted into a crystalline carbonate (mostly calcite). A description of the manufacturing process can be found in Denis and Sivak (Citation11) and Fish (Citation12). Before 1985, calcium sulfonate greases were niche and only produced in small quantities. The grease had the desirable characteristics of high dropping point and good extreme pressure and antiwear characteristics but also had negative properties such as high thickener concentration, complex manufacturing, and high costs (Fish (Citation12)). The complex calcium sulfonate was then invented, where anhydrous calcium 12-hydroxystearate was used as a complexing agent (Muir and `Blokhuis (Citation13)). This increased the water spray-off performance and made it possible to reduce the thickener concentration.
Microstructure of CaS
Calcium sulfonate greases are made by converting a fluid detergent that contains overbased calcium sulfonate based on amorphous calcium carbonate to a grease containing overbased calcium sulfonate where the calcium carbonate consists of calcite particles (Kumar, et al. (Citation14)). This is done by treating the liquid with an active compound such as water, alcohol, or lower carboxylic acid (Muir (Citation15)). Its particular rheology is caused by the high degree of association between the wafer-like calcite particles (Muir (Citation15)). Fluid overbased calcium sulfonate is a colloidal dispersion of inverse micelles formed by amorphous CaCO3 in oil stabilized by a surfactant (calcium sulfonate; see . The term overbased is used to describe the excess of metal (Ca) over that required to neutralize the sulfonic acid. The number of carbon atoms in the hydrocarbon chain (alkyl chain length) is between 12 and 30 (Macwood and Muir (Citation16)), and the number of calcium carbonate groups in the fluid may be as large as 40 (Muir (Citation15)). shows an example of the micelles of a complex overbased calcium sulfonate grease. Here Ca 12-hydroxystearate is used as a complexing agent. In many patented versions, boric acid is used as a complexing agent. Small angle X-ray scattering measurements on fluid overbased calcium sulfonate have shown that the calcium core has a radius of 2.0 nm and, including the calcium sulfonate shell, has a radius of 2.9 nm (Giasson, et al. (Citation17)). In Tobias and Klein (Citation18), the formation of reverse micelles with a calcium carbonate core and calcium sulfonate surfactant molecules was investigated using molecular dynamics computer simulations. In their simulations, they found similar results; that is, a core radius of 1.15 nm and a surfactant layer thickness of 0.9 nm. The inverse micelles form agglomerates with a roughly spherical structure (Makedonsky, et al. (Citation19)). The crystallographic structure of the grease is calcite; see . This is different from a fluid sulfonate, which contains amorphous CaCO3, having particle size less than 2–15 nm (Muir (Citation15)). Grease-like sulfonate contains predominantly crystalline calcite (wafer-like platelets) with a much larger particle size (15–500 nm; Muir (Citation15)).
Figure 1. Micelles of overbased complex calcium sulfonate, after Kobylyanski, et al. (Citation9). The core consists of calcium carbonate and calcium metaborate. The core is covered with overbased calcium sulfonate and calcium 12-hydroxystaerate.
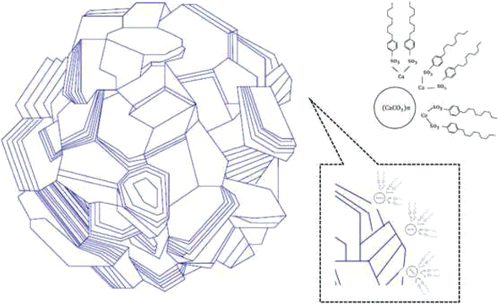
Figure 2. Structure of calcium sulfonate grease (Giasson, et al. (Citation17); Authier and Herman (Citation23)). The size of the calcite core is 15–500 nm (Muir (Citation15)).
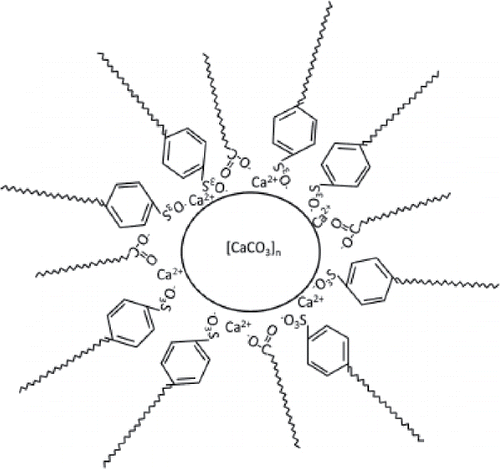
General properties of CaS
Due to the lubricating properties of the calcite particles, performance additives containing sulfur, phosphorous, or zinc may not be needed (Ward (Citation20)). The crystalline calcite consists of ultrathin calcite layers/slices of calcium carbonate with a large surface-to-volume ratio, have a great surface activity, and cover the surface, forming a tribolayer/ferrite(oxide) structures on the surface (Kobylyansky, et al. (Citation9)). The thickener makes a viscous deposit of calcium carbonate (Giasson, et al. (Citation17)). It is first adsorbed on the film to form a physisorbed layer (Liu, et al. (Citation21)). This has been confirmed in Hunt (Citation22), where it was shown (using scanning electron microscopy) that the bonding was horizontal and that the platelet structure forms a fish scale–like coating. Then the adsorbed calcium sulfonate creates sulfonate chains perpendicular to the surface. At low loads, the film is physically bonded, reducing friction and wear. At high loads, the shear will be higher and the sulfonates are ejected from the contact and a tribochemical film is formed (CaCO3, CaO, iron oxide, and FeSO4).
Calcium sulfonate thickener greases therefore have good extreme pressure and antiwear properties without the use of additives (Komatsuzaki (Citation24); Gow (Citation25)). The calcite wafer-like platelets oriented parallel to the surface in the fish scale–like pattern also provide an excellent barrier to water, preventing surface corrosion in the case of water ingress (Muir, et al. (Citation26)). EMCOR test results are clearly excellent with calcium sulfonate grease: calcium sulfonate grease has excellent anticorrosion protection, even in the absence of additives (Kimura, et al. (Citation27)). According to Authier and Herman (Citation23), the good performance of calcium sulfonate in the presence of water is also ascribed to the polar action of sulfonates giving good adhesion to steel and good water washout properties. Calcium sulfonates are used as anticorrosion additives; calcium carbonate neutralizes the acids formed in the corrosion process and delay or prevent corrosion. Next to the inherent lubricating properties, a calcium sulfonate–based grease has excellent mechanical stability properties (Macwood and Muir (Citation16); Authier and Herman (Citation23); Kimura, et al. (Citation27)). Authier and Herman (Citation23) ascribe this to the fact that the micelles may not be destroyed by mechanical (shear) stress. It is only that the network is altered but stabilizes again after working the grease. These greases have a high dropping point (>310°C; Macwood and Muir (Citation16)) and can therefore be applied at high temperatures (>150°C; Kimura, et al. (Citation27)). The grease has very good performance in the water washout test (ISO 11009). Additivation may reduce this somewhat. Work penetration (100,000 strokes) in the presence of 10% water is also excellent.
A weak point of calcium sulfonate grease is its low-temperature performance, which is better for lithium complex greases. According to Macwood and Muir (Citation16), this is caused by the high thickener content compared to other greases. In Fish and Ward (Citation28), this is ascribed to the fact that calcium sulfonate greases are gels (and therefore do not separate much oil). The high thickener content also reduces pumpability (Madius and Smets (Citation29)). Regardless of these shortcomings, calcium sulfonate complex grease are used in a wide range of applications, because of the variety of excellent properties, but primarily in industrial applications (Macwood and Muir (Citation16)). Calcium sulfonate greases are preferred in many applications where water resistance is required, such as in steel mills (Denis and Sivik (Citation11)). In these applications, they are preferred over aluminum or lithium complexes (Fish and Ward (Citation28)). CaS grease not only performs well in the presence of water but also has excellent high-temperature performance (>150°C; Gow (Citation25)). The density of calcium sulfonate greases is higher than that of water, which makes them suitable even for underwater applications (Makedonsky, et al. (Citation19)).
Water in CaS
Previous measurements done by the current authors on the effect of water on the film-forming capabilities of water-contaminated grease showed that CaS can absorb 44 wt% water, defined here as the ratio of the mass of water and that of the total mixture multiplied by 100%Footnote1 ; see Cyriac, et al. (Citation30). In another study it was suggested that CaS can absorb large quantities of water; the maximum quantity tested was 30 wt%, and the author suggested 60 wt% to be the maximum (Leckner (Citation8)). The remarkable absorption of water in CaS grease should be ascribed to the thickener structure because a (mineral) oil is typically hydrophobic and the concentration of additives is too low to be able to absorb large quantities of water. The saturation point is only 0.02–0.03% for mineral oils and 0.1% for synthetic oils (Eachus (Citation31)). The yield stress, zero-shear viscosity, and plateau modulus actually increase as a function of water; see measurements for a mineral oil–based grease in . There are two hypotheses on how water is absorbed by the thickener. It may be the formation of large inverted micelles as speculated in Leckner (Citation8), see or it may be swelling of the individual suspended thickener particles by absorption between the calcite core and the surfactant, as speculated in, for example, Cyriac, et al. (Citation32). The suggestion of the formation of large inverted micelles originated from the pulsed field gradient nuclear magnetic resonance measurements described in Leckner (Citation8). Here how much water was absorbed in different grease types was and whether this water would still be present in a free form were investigated.
Figure 3. The effect of water on the rheology of a calcium sulfonate complex grease with a mineral base oil. Data from Cyriac, et al. (Citation30). (a) Zero-shear viscosity; (b) yield stress as defined by the method described in Cyriac, et al. (Citation34); (c) plateau modulus.
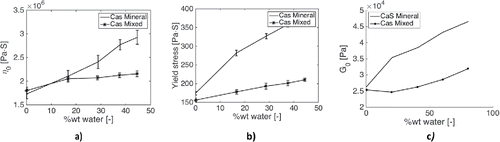
Figure 4. Inverted micelles formed in a CaS grease, illustrating the terms confined and less confined. The ratio between these two may give an indication of the micelle size. Reproduced with permission from Leckner (Citation8).
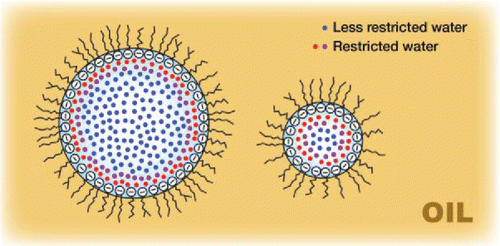
For the CaS-type greases used in that study, two different diffusion rates were measured, suggesting that water was present in both a bonded/restricted form and in a less restricted form, Leckner (Citation8). In this publication, the author avoided using the term free water because the water was still restricted and not in a free droplet shape. The results indicate that a major fraction of the water (approximately 90%) is still present in a less restricted form; for example, inside a larger structure. It was speculated that most probably the high diffusion rate originates from inside large inverted micelles. The second lower rate was close to that of water in a mineral oil (Lees and Sarram (Citation33)), from which it was concluded that this originates from the shell of the micelles or dissolved water in the base oil.
In another paper (Cyriac, et al. (Citation32)), small angle X-ray scattering measurements were performed on two commercial CaS greases where the results suggested that the thickener particles increased slightly under the influence of water. The quantity of this swelling is approximately the size of two monolayers of water, suggesting that water is nesting between the surfactant and the calcite core. The same type of mechanism was suggested regarding CaS particles added to an oil (Tavacoli, et al. (Citation35)), indicating that CaS particles may be hydrophilic. Though these studies suggest that a (small) portion of the water is bonded either to the thickener structure itself or dissolved in the base oil, the pulsed field gradient nuclear magnetic resonance from Leckner (Citation8) also suggests that the larger portion of the water is still mobile and thus not bonded/dissolved.
To form (inverted) micelles, a hydrophilic and a hydrophobic part are needed. The outer part of the shell could consist of particles bonded to water, whereas the hydrophobic head is oriented on the inner side. This hypothesis is further strengthened by the observed shear banding for the water-contaminated grease, clearly visible in a flow curve measurement as shown . This suggests that there is a local activation of a high concentration of a second alien substance such as water, which could be explained by the presence of (inverted) micelles; see, for example, Divoux, et al. (Citation36).
Methods and materials
Grease
The first step is to select grease to mix the water into. The selected grease is presented in . The mixing of water into the grease samples was done using a scaled in-house grease worker; for details, see Cyriac, et al. (Citation30). This grease was selected because it was used in previous studies on the effect of water on the performance of lubricating grease by the current authors (Cyriac, et al. (Citation5)–(Citation7)). This gives the possibility to link the observations done in these studies to the current one.
Table 1. Properties of the CaS used in this article.
Microstructural analyses
Atomic force microscopy (AFM) images were obtained in tapping mode using cantilevers with a width and length of 20 and 125 μm, respectively, resulting in a stiffness of approximately 40 N/m and characteristic frequency of 330 kHz. This operation mode gives two main signals back: A topography image and a phase image. The first gives an impression of the surface topography, whereas the second gives an indication of how the tip is interacting with the surface and can give an indication of material variations. A full explanation of the technique is outside the scope of the current article and the interested reader is referred to Haugstad (Citation37). The main advantage of utilizing AFM to assess the microstructure over scanning electron microscopy/transmission electron microscopy is that no to little sample preparation is needed. Though in some cases the grease is still quenched before AFM measurements (Roman, et al. (Citation38)), even this step is omitted in the current study. Sample preparation is limited to only gently smearing a very small amount of grease onto a microscopy glass. One could therefore consider the samples as received when analyzed.
Results
Imaging using AFM
First, samples are prepared from the fresh grease without water; see . In the topography image, the thickener particles are clearly visible above the base oil. In the phase image, the contour of the particles becomes even more clear. The size of the particles is in the range as suggested in Authier and Herman (Citation23). Some minor artefacts, referred to as striping, can be observed in the topography image in . This type of artefact typically results from pollution of the AFM tip. These artefacts are more pronounced in the topography signal than in the phase contrast images. This, together with the sharper contrast of the particle contour, motivated a focus on the phase image for analysis in this publication, unless otherwise stated. When water is mixed into the grease, a clear change in the microstructure is observed, as in shown in . Here, large features can be seen. At first glance, one might think that these larger features are just water droplets; however, a closer look (, mainly visible in the phase contrast measurement) shows that it is clear that the thickener particles are agglomerated on the edges of the larger structures. This confirms the suggestion made in Leckner (Citation8) that inverted micelles are formed with the CaS particles at the boundaries (possibly causing the low diffusion rate signal).
In the phase image of , it can also be clearly seen that around the edges thickener particles are merging into the larger micelle and that a rough shell is formed consisting of particles. Also in the topography image, it can be seen that the complete surface is covered by thickener particles; clearly, the top surface shows characteristic features of the thickener particles. This suggests that the hydrophilic core is oriented toward the water, whereas the hydrophobic surfactant is keeping the whole droplet in suspension, forming a stable system.
Quantifying the effect of water on the microstructure
Now that it has been proven/confirmed that inverted micelles are formed in the presence of water, the next step is to investigate the effect of dissolved water in the grease on the grease microstructure and to quantify this. First, the microstructure of the grease without water was determined as a baseline. This is done by excluding the unaffected part of the grease structure. By analyzing over 10 images of three different samples of the dry grease structure, as, for example, shown in , it is observed that there are no features present larger than 100 nm in equivalent radius in the dry grease, giving a baseline. Moreover, it is assumed that the micelles/structures formed under the influence of water are elliptical (which is quite a reasonable assumption, as can be seen from ). The tools that were used for identifying the micelles and measuring their size and location are available in the standard image toolbox of the mathematical higher order language used; a detailed description is outside the scope of the current publication. A result of the methodology used is shown in . The data used for this quantification typically consist of five images with a size 10 × 10 µm, obtained with a 512 × 512 resolution. This results in a smallest particle size that can be determined of 20 nm, which is one order lower than the minimum radius set. The probability density is plotted versus the equivalent radius of the micelles/features for different water concentrations in . Here it should be noted that the total number of micelles observed shows a large spread for the different samples (not shown).
Figure 9. Example of identification using image recognition toolbox, showing the raw phase image, the binary image, the identified micelles, and the resulting particle distribution function. Results for one measurement done on a sample with 40% water content.
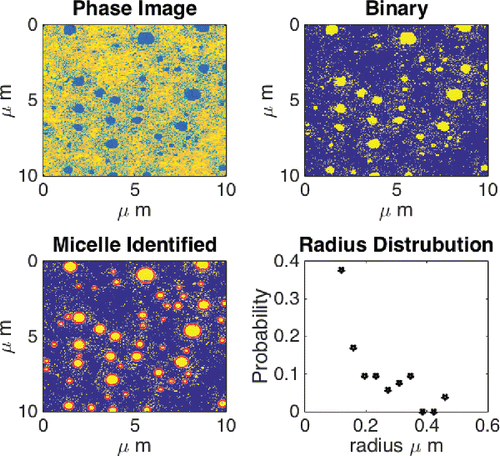
Figure 10. Probability density function as a function of water concentration: (a)20%, (b) 30%, (c) 40%, (d) 50%, (e) 55%, and (f) 60% and (g) comparison of the different water concentrations.
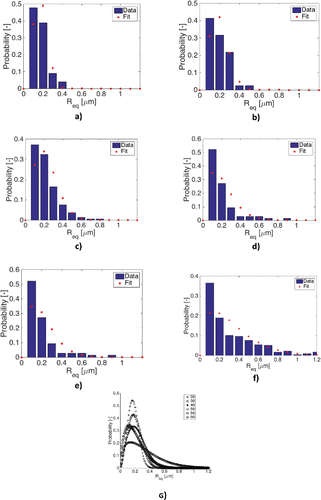
Therefore, no conclusion can be drawn regarding the total number of micelles present in the grease. However, a clear effect of water concentration on the size distribution can be seen. These distributions are built up from more than 100 micelles to ensure that they are statistically significant. The maximum size is reached at around 55–60 wt% water, after which the water is no longer mixed into the grease but forms free water; that is, grease is mixed in water. The micelles are growing significantly as a function of water concentration, which is clearly seen in the shift in the probability density functions shown in . Here a Weibull curve is fitted through the different data sets. It can be seen that there is a clear shift toward larger micelles with an increase of water content for the mineral oil–based grease. This corresponds well with the observations in Leckner (Citation8), suggesting that a large portion of the water is inside a large feature. It can also be seen that a clear saturation level is reached around 50% and at 60% the distribution goes toward mainly larger micelles. However, it should be mentioned that with 60% water, free water was still clearly observed after mixing; these results should therefore be interpreted with great care. Nevertheless, they are included to show that a possible effect of saturation might be the sudden growth in micelle size, causing an instability of the grease structure.
Discussion
The work in this article has revealed the mechanism explaining the high absorption of water. This can be used to explain some phenomena observed in previous studies by the current authors. First, the growth in micelle size can provide a possible explanation for the shear banding behavior observed in . The consistency increases with increasing concentration of water due to the presence of a polydisperse micellar structure. The shear rate in a plate–plate rheometer is defined as the ratio of the speed difference of the plates and the gap height. However, in the case of a lubricating grease (as a non-Newtonian material), the shear rate will not be uniform across the gap between the two plates in the plate–plate rheometer (Li, et al. (Citation39)). The shear rate should therefore be called the apparent shear rate. It is likely that at a critical apparent shear rate, larger micelles filled with water will break up into smaller cells at a zone of high shear, leading to a reduction of the measured viscosity (the ratio of the measured shear stress and apparent shear rate), which may also be called shear instability. With increasing apparent shear rate, a more uniform micelle distribution is achieved with a size corresponding to the size that can be expected with lower water concentrations. The viscosity becomes less sensitive to the concentration of mixed water, as shown in . Ultimately, at very high shear rates, the viscosity converges to one single line, suggesting that the micelles are all destroyed. In addition, previously observed effects of water on the bleeding of CaS and, in turn, its lubricating performance (see Cyriac, et al. (Citation7)) can be explained by the clustering of the particles around water droplets. The larger particles form a stronger network, not only increasing the consistency of the grease (Cyriac, et al. (Citation30)) but also reducing the bleeding behavior of the grease. As water enters into the matrix and forms droplets with calcite as an outer shell acting as a thickener, the oil–thickener ratio is significantly reduced and effectively one ends up with a stiff grease that hardly bleeds, as would be the case for a grease with excess amounts of thickener.
Conclusion
The results obtained with the current measurement method (AFM) are in good agreement with other methods used previously and confirm the hypothesis made in Leckner (Citation8) that inverted micelles are formed. In addition, this corresponds well with the increase in rheological parameters and reduced film forming under starved conditions as mentioned in Cyriac, et al. (Citation7), (Citation30) and the shear banding observed. The mechanism behind the formation of micelles may be due to the fact that the thickener structure consists of a hydrophilic calcite core and a hydrophobic shell. The calcite core adheres to the water and forms a large structure around the water droplet. The shear stability of the formed structure is a point of further interest.
Acknowledgments
The authors express their gratitude to Y. Zhou for preparing the samples used in this study and R. Zoetemelk of ST Instruments for providing assistance and cantilevers for the AFM analysis.
Notes
1 Note that Cyriac, et al. (Citation8) took the ratio of the mass of water and grease multiplied by 100%. To be able to relate the current results to other studies, in this article the amount of water is expressed in weight percentage.
References
- Cantley, R. E. (1977), “The Effect of Water in Lubricating Oil on Bearing Fatigue Life,” A S L E Transactions, 20(3), pp 244–248.
- Lugt, P. M. (2013), Grease Lubrication in Rolling Bearings. Tribology Series, John Wiley & Sons, Hoboken, NJ.
- Mistry, A. (2005), “Performance of Lubricating Greases in the Presence of Water,” NLGI Spokesman, 68(12), pp 8–15.
- Cyriac, F., Lugt, P. M., and Bosman, R. (2016), “Effect of Thickener Particle Geometry and Concentration on the Grease EHL Film Thickness at Medium Speeds,” Tribology Letters, 61(2), pp 18–31.
- Cyriac, F., Lugt, P. M., and Bosman, R. (2016), “The Impact of Water on the Yield Stress and Startup Torque of Lubricating Greases,” Tribology Transactions, 60(5), pp 824–831.
- Cyriac, F., Lugt, P. M., and Bosman, R. (2017), “Impact of Water on the Rheology of Lubricating Greases,” Tribology and Lubrication Technology, 73(2), pp 679–689.
- Cyriac, F., Lugt, P. M., and Bosman, R. (2016), “Impact of Water on EHL Film Thickness of Lubricating Greases in Rolling Point Contacts,” Tribology Letters, 61(3), pp 1–8.
- Leckner, J. (2013), “Water + Grease = Fatal Attraction?,” 25th ELGI Annual General Meeting, April 20–23, 2013, pp 1–18, Amsterdam, The Netherlands.
- Kobylyansky, E. V., Mishchuk, O. A., and Ishchuk, Y. L. (2004), “Lubricating Properties of Thixotropic Systems Based on Overbased Calcium Sulphonate,” Lubrication Science, 16(3), pp 293–302.
- Hone, D. C., Robinson, B. H., Steytler, D. C., Glyde, R. W., and Galsworty, J. R. (2000), “Mechanism of Acid Neutralization by Overbased Colloidal Additives in Hydrocarbon Media,” Langmuir, 16(2), pp 340–346.
- Denis, R., and Sivik, M. (2009), “Calcium Sulphonate Grease-Making Process,” NLGI Spokesman, 73(5), pp 30–37.
- Fish, G. (2014), Calcium Sulphonate Greases, Performance and Applications Overview, Axel Christiernsson: Wickliffe, Ohio, US.
- Muir, R., and Blokhuis, W. (1985), “High Performance Calcium Borate Modified Overbased Calcium Sulfonate Complex Greases,” U.S. Patent 4560489.
- Kumar, A., Humphreys, S., and Mallory, B. (2012), “Overbased Calcium Sulfonate Greases for Extreme Environment,” Greasetech India, 14(3), pp 5–12.
- Muir, R. J. (1988), “High Performance Calcium Sulfonate Complex Lubricating Grease,” NLGI Spokesman, 52(4), pp 140–146.
- Macwood, W., and Muir, R. (1999), “Calcium Sulfonate Grease … One Decade Later,” NLGI Spokesman, 63(5), pp 24–37.
- Giasson, S., Espinat, D., and Palermo, T. (1993), “Study of Microstructural Transformation of Overbased Calcium Sulphonates during Friction,” Lubrication Science, 5(2), pp 91–111.
- Tobias, D. J., and Klein, M. L. (1996), “Molecular Dynamics Simulations of a Calcium Carbonate/Calcium Sulfonate Reverse Micelle,” The Journal of Physical Chemistry, 100(16), pp 6637–6648.
- Makedonsky, O., Kobylyansky, E., and Ishchuk, Y. (2003), “Structure and Physico-Chemical Properties of Overbased Calcium Sulfonate Complex Greases,” Eurogrease, 1, pp 1–5.
- Ward, B. (2006), “Understanding Calcium Sulfonate Thickeners,” Machinery Lubrication, 2006(7), pp 58–59.
- Liu, D., Zhao, G., and Wang, X. (2012), “Tribological Performance of Lubricating Greases Based on Calcium Carbonate Polymorphs under the Boundary Lubrication Condition,” Tribology Letters, 47(2), pp 183–194.
- Hunt, M. (1975), “Structurally Modified Overbased Metal Salt Dispersions for Rust-Preventive Coatings,” Lubrication Engineering, 31(4), pp 183–186.
- Authier, D., and Herman, A. (2013), “Calcium Sulfonate Carbonate Greases: A Solution to Water Resistance,” Eurogrease, 3, pp 19–35.
- Komatsuzaki, S. (2002), “Prospects of Grease Lubrication: Technological Trends of Grease Lubrication,” Japanese Journal of Tribology, 47(1), pp 1–13.
- Gow, G. (2005), Thickeners in the Grease Matrix Market and Product Trends, Axel Christiernsson: Kansas, US.
- Muir, R., Mackwood, W., and Dunn, W. (2002), “Calcium Sulfonate Grease, The Next Generation Food Machinery Grease,” 69th Annual Meeting, National Lubricating Grease Institute, Coronado, CA.
- Kimura, Y., Takemura, K., Araki, J., and Kojima, H. (2006), “Study of Synthetic Oil Based Calcium Sulfonate Complex Greases,” NLGI Spokesman, 70(9), pp 20–26.
- Fish, G., and Ward, W. C., Jr. (2012), “Calcium Sulfonate Greases Revisited,” NLGI Spokesman, 76(5), pp 1–20.
- Madius, C., and Smets, W. (2013), Grease Fundamentals: Covering the Basis of Lubricating Grease, Axel Christiernsson: Kansas, US.
- Cyriac, F., Lugt, P. M., and Bosman, R. (2016), “Impact of Water on the Rheology of Lubricating Greases,” Tribology Transactions, 59(4), pp 679–689.
- Eachus, A. C. (2005), “The Trouble with Water,” Tribology & Lubrication Technology, 61(10), pp 1–32.
- Cyriac, F., Lugt, P. M., and Bosman, R. (2014), “Impact of Water on Calcium Sulfonate Greases,” ASME/STLE International Joint Tribology Conference, May 19–22, 2014, Orlando, FL.
- Lees, F. P., and Sarram, P. (1971), “Diffusion Coefficient of Water in Some Organic Liquids,” Journal of Chemical & Engineering Data, 16(1), pp 41–44.
- Cyriac, F., Lugt, P. M., and Bosman, R. (2015), “On a New Method to Determine the Yield Stress in Lubricating Grease,” Tribology Transactions, 58(6), pp 1021–1030.
- Tavacoli, J. W., Dowding, P. J., Steytler, D. C., Barnes, D. J., and Routh, A. F. (2008), “Effect of Water on Overbased Sulfonate Engine Oil Additives,” Langmuir, 24(8), pp 3807–3813.
- Divoux, T., Fardin, M. A., Manneville, S., and Lerouge, S. (2016), “Shear Banding of Complex Fluids,” Annual Review of Fluid Mechanics, 48(1), pp 81–103.
- Haugstad, G. (2012), “Overview of AFM,” Atomic Force Microscopy, pp 1–32, John Wiley & Sons: New Jersey.
- Roman, C., Valencia, C., and Franco, J. M. (2016), “AFM and SEM Assessment of Lubricating Grease Microstructures: Influence of Sample Preparation Protocol, Frictional Working Conditions and Composition,” Tribology Letters, 63(2), pp 20.
- Li, J. X., Westerberg, L. G., Höglund, E., Lugt, P. M., and Baart, P. (2014), “Lubricating Grease Shear Flow and Boundary Layers in a Concentric Cylinder Configuration,” Tribology Transactions, 57(6), pp 1106–1115.