ABSTRACT
Metal additive manufacturing technologies, such as electron beam powder bed fusion (PBF-EB), rely on layer heating to overcome the so-called “smoke” phenomenon. When scaled up for industrial manufacturing, PBF-EB becomes less productive due to the lengthy preheating process. Currently, only the electron beam (EB) is used for preheating in PBF-EB, resulting in increased manufacturing times, energy consumption, and in some cases limiting the applicability of the technology. In this study, a new preheating approach is suggested that incorporates a near-infrared radiation (NIR) emitter inside an PBF-EB system. The NIR unit eliminates the need for EB heating, reducing build time and powder charging. Successful builds using 316 L and Ti6Al4V precursor powders validate the feasibility of the proposed approach. The produced samples exhibit similar properties to those obtained by the standard PBF-EB process. The introduction of NIR technology also reduced build cost and increased the service intervals of the electron gun.
Introduction
Additive manufacturing (AM) in metal is gaining interest within the industry as an alternative and supplement to traditional manufacturing, driven by the promise of short lead times, freedom of design, and unique processing opportunities. Metal AM is currently dominated by powder bed fusion (PBF) technologies: laser-based equipment (PBF-LB) accounts for the largest market share, followed by electron beam PBF (PBF-EB), with both methods having their own advantages.[Citation1– 8] PBF-EB is a growing field and offers some benefits over PBF-LB such as better part stacking, which increases manufacturing efficiency, lower residual stresses, a cleaner process environment (vacuum), faster beam speed, higher energy density, and, in many cases, better beam energy absorption, and greater beam penetration depth.[Citation2,Citation5] The number of vendors in the field of PBF-EB has increased in recent years,[Citation3,Citation9] which has resulted in the introduction of many innovative approaches to the basic technology.[Citation10–16] One limitation of PBF-EB is the charging of powder particles, which can result in what is known as “smoke”—when coulomb forces act to form a powder cloud in the working chamber – immediately terminating the process.[Citation9,Citation17,Citation18] Arcam AB (currently ARCAM EBM, a part of GE, Mölnlycke, Sweden), the first company to release an PBF-EB system[Citation19] (commonly termed electron beam melting, EBM), applies a low-pressure He-controlled vacuum of 10−3 mBar to reduce electrostatic charging of the powder.[Citation9,Citation20] Jeol (Tokyo, Japan) utilizes a “e-shield” surrounding the build area to avoid both the scattering of powder particles and layer charging.[Citation21,Citation22] Wayland Additive (Huddersfield, United Kingdom) induces a field of positive ions above the powder bed to neutralize the negative charge of the powder surface.[Citation23] Freemelt (Mölndal, Sweden) offers an optional shield-heating plate that can swivel between the powder bed and the electron source.[Citation24] This plate is heated by the incident electron beam (EB), which heats the powder below through secondary radiation. To the best knowledge of the authors, the use of a separate heating source inside the PBF-EB chamber has not been suggested. In this study, the use of near-infrared radiation (NIR) is proposed as an alternative heating approach to partially or fully eliminate the need for EB heating and powder pre-sintering. The proposed NIR technology utilizes wavelengths of 800 nm to 1500 nm from sources that use electrically heated filaments enclosed in glass. The radiator temperature of the emitters ranges from 2900 K to 3200 K and enables contactless, fast, and charge-free heating16.
The impact of electrons is an effective method to heat and melt metal powder into AM parts. However, heating and pre-sintering of the powder bed with electrons presents certain challenges. For instance, only conductive powders can be used, and even so there is a significant risk of smoke in the case of an improper choice of process parameters.[Citation9,Citation22] For this reason, EBM heating is conducted by repeatedly scanning the powder with a defocused beam while slowly increasing the intensity,[Citation25–28] which increases the layer processing time. In many cases, this increase is significant, and in some cases, the overall pre-sintering and heating time can exceed the melting time. The preheating or pre-sintering of powder is needed to avoid smoke and ensure the target process temperature, which is commonly set between 400 and 1100°C depending on the precursor alloy. Post- and/or intermediate heating can be applied after or between the melting of different models to decrease the thermal variation over the layer. The heated area and heating rates are limited by the performance of the electron source and the nature of the precursor powder (some powders are more susceptible to smoking and thus demand a gentler, longer preheating process).[Citation26] This is particularly significant for large build volumes since they result in greater heat loss, consequently decreasing productivity and increasing total energy consumption. The heated areas also extend beyond the melt envelope, meaning that a large beam energy input is needed to maintain the upper layer temperatures. Some materials require relatively high process temperatures, which further increases the load upon the electron source and can result in high column temperatures (ultimately terminating the process). Electron sources have a limited service life from the time of assembly, which requires them to be replaced if the remaining “safe service time” is insufficient for the process of an upcoming build. Although the standard (A2 system) EBM preheating process utilizes relatively fast beam scanning rates of about 40 m/s, the preheating and post-heating processes commonly occupy the majority of the PBF-EB layer processing time. As an example, for the builds tested in this research using standard EB heating, preheating represented 30–80% of the overall layer manufacturing time. In general, the proportion of the layer processing time used for pre-sintering and to maintain the desired process temperature increases for larger builds and higher process temperatures.
It is hypothesized that the integration of an NIR unit in an PBF-EB system can help overcome the limitations mentioned above. Additionally, this will decrease the load on the electron source and is therefore expected to extend its lifetime. This work constitutes a feasibility study to confirm that NIR can be effectively used as an alternative heating source in the PBF-EB process by integrating a 6 kW NIR unit into an Arcam EBM system.
Materials and methods
Experimental setup
All the experiments were performed using a modified Arcam EBM, hereafter referred to by its serial number: “R1021.” This is an early S12 model that has been modified to the main specifications of an A2 model by replacing the electron column (thermionic emission filament), chamber interior, and control units. R1021 was further modified to incorporate a specially developed NIR unit. The modifications are schematically presented in . The 6 kW water-cooled 100 mm x 120 mm NIR unit () was developed and optimized for increased absorption at the metal surface by the company Adphos Digital Printing GmbH (Bruckmuhl-Heufeld, Germany).[Citation29] NIR equipment from Adphos is used in industrial settings for a wide range of applications of both large-area and focused heating up to and above 1 MW/m.[Citation2] The NIR unit was mounted side by side with the standard Arcam rake prism using a dedicated EBM-manufactured stainless steel 316 L bracket. This enables the NIR unit to move together with the rake, minimizing changes to the system and making it possible to use the EBM Control 3.2 software currently running the system. During the experiments, the NIR was manually activated by the operator. A built-in function of EBM Control 3.2 was used to block the EB gun when the NIR system was moving over the build area.
Figure 1. a) Schematic representation of the experimental setup, b) Photo of the NIR unit mounted in the EBM chamber.
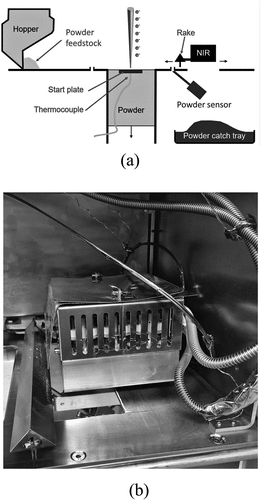
Since the amount of heat that would be generated by the NIR system in the vacuum and re-absorbed by the surrounding elements was unknown, the NIR was equipped with water cooling. The need for cooling was evaluated during different stages of the process by measuring the temperature difference between the incoming and returning cooling water for a given flow (0.41 l/min at 3.2 bar). The cooling water was fed through the EBM vacuum chamber using an external pump (Wilo WJ-203-X-EM/C) and vacuum feedthrough (Pfeiffer 120×FL040–2-SS) and routed through the chamber using convoluted flexible metal tubes (Swagelok, Ohio, USA), as seen on the right-hand side of . The power for the NIR unit was delivered to the chamber via a 2-pin feedthrough (Pfeiffer 120×ST040-1-20-2) using Kapton insulated wires (Vacom KAP-BAND-L-AWG14) to avoid outgassing. Additionally, feedthrough couplings for extra thermocouples (Pfeiffer 120×TK040–4) and sensor signals (Pfeiffer 120×SD040–9) were added to monitor and control the NIR in semi-automatic and automatic modes during the further development stages. Every device mounted inside R1021 was ultra-high vacuum compatible and hence did not affect the standard atmosphere of the EBM process (He controlled vacuum at~10−3 mBar).
Experiment settings
A number of experiments were conducted with the setup described above to assess the NIR potential for PBF AM using PBF-EB as an example. Three experimental settings were proposed, as described in sections 2.2.1 to 2.2.3. For all the experiments, log files were saved for additional analysis, and manufactured samples were collected for further characterization.
Heating the start plate by NIR
In the first stage, stainless steel start plates were heated by NIR inside the EBM chamber under the target working atmosphere to evaluate how the 6 kW NIR unit functioned in a vacuum and measure the heating rates and temperatures that could be achieved. Two common sizes of start plates for R1021 were used: square (150 mm x 150 mm) and circular (⌀82 mm). All start plates were cut from 10 mm-thick 304 stainless steel using an abrasive water jet. The start plates were placed over Ti6Al4V powder and leveled according to the standard EBM procedure. Different power settings on the NIR unit were evaluated, and the plate temperature and chamber pressure dynamics were compared to the standard EBM start plate heating process.
Powder sintering by NIR
The potential of NIR to sinter powder was explored by heating a loose powder bed using NIR inside the EBM chamber at the standard process atmosphere. The aim was to find the optimal settings for NIR heating that resulted in proper sintering for both 316 L and Ti6Al4V precursor powders. Both single layer sintering and consecutive layer sintering (“powder cakes”) were studied. The single layer preheating was performed on a cold (~20°C) powder bed deposited over the start plate. The consecutive layer preheating was performed on top of a square start plate heated to the process temperature (810 ºC for 316 L and 730 ºC for Ti6Al4V). The sintered powder was evaluated using scanning electron microscopy (SEM, Tescan Vega, Brno, Czech Republic) to compare the structure and inter-grain bridges against samples produced using standard EB and NIR sintering.
Sample manufacturing with the aid of NIR heating
Once the optimal heating and sintering parameters were identified, solid samples were manufactured using NIR for heating and sintering followed by EB melting. The NIR was used to heat the start plate to the process temperature and sinter every layer prior to EB melting; in some cases it was also used for post-heating. The process step sequence is illustrated in . Manufactured samples included rectangular blocks of different sizes, cylinders, and gyroid lattices according to the build file shown in . All EB heating functions were disabled in the standard build setup window, and a layer thickness of 70 µm was used. The NIR heating time was controlled to maintain a stable temperature, as measured by the thermocouple connected to the bottom of the start plate. Hence, the heating time varied across the different experiments, but could be read from the log files after the builds were completed. Samples were produced from 316 L and Ti6Al4V commercial precursor powders (see section 2.3 for details). Reference builds were performed using the standard EBM settings and procedures. Representative samples were selected for further evaluation using SEM imaging (Tescan Maia 3, Brno, Czech Republic), Rockwell C hardness measurements (Mitutoyo, HR-200, Kanagawa, Japan), and Archimedes density measurements. Samples were prepared using water-cooled cutting, grinding (SiC), polishing (diamond suspension), and etching (Krolls reagent on Ti6Al4V samples and electrochemical oxalic acid treatment at 3.5 V for 316 L).
Figure 2. a) Cold start plate inside the EBM chamber, b) NIR heating of the start plate, c) Start plate heated to is 810°C using NIR, d) EB melting stage, e) Build file used for all experiments in section 2.2.3.
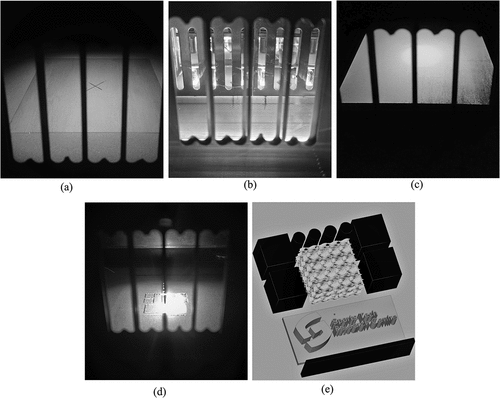
Powder specifications
The precursor powders used in this work were gas atomized 53–150 µm 316 L (Carpenter powder products AB, Torshälla, Sweden) and plasma atomized 45–150 µm Ti6Al4V (Arcam AB, Mölndal, Sweden). Both powder batches were recycled prior to the experiments, but the apparent density (ASTM B212) and flowability (ASTM B213) were found to be within the specified value range required for PBF-EB; SEM imaging confirmed a mostly spherical morphology of the powder grains. Since all measurements are relative, compositional characterization of the powder batches was not performed.
Results and discussion
Heating the start plate with NIR
It was possible to heat the start plates up to 950°C using NIR (it should be noted that R1021 was not specifically designed for the processing of high-temperature materials). This value does not seem to be limited by the technology; a further increase in temperature was manually prevented to avoid damaging the setup. This temperature is sufficient for most PBF-EB materials, for which the process temperature is set as 40–80% of the melting point.[Citation30,Citation31] For a small group of alloys, such as TiAl,[Citation9] an NIR setup with greater power output mounted inside a PBF-EB machine that supports higher temperatures may be necessary. presents the comparison of the start plate temperature dynamics (as measured by a thermocouple under the start plate) for standard EB and NIR heating using the heat source power shown in . The corresponding heating rates of both methods are comparable. It can be seen that the NIR heating rate starts to decrease at around 800–900°C, indicating the expected limit of the heating capacity for the present setup. The EB start plate heating process includes a “start plate outgassing” stage, during which the beam intensity is decreased and temperature maintained around 450°C for a selected time. This allows for the desorption of impurities from the start plate and underlying powder, leading to a certain amount of degradation of the chamber vacuum and allowing the pumps to restore the target vacuum values. This ensures stable electron emission and a sufficient mean free path, which is essential for the manufacturing process. Since the EB is not active during NIR heating, the outgassing stage could possibly be omitted. However, experiments were also conducted in which the start plate temperature was kept constant. It was determined that after the initial fast start plate heating at 6 kW NIR power, it was sufficient to apply 0.6–1.2 kW NIR power to maintain the square start plate temperature of 450°C. As indicated earlier, EB heating includes a 3-minute outgassing stage for the circular plates and a 15-minute stage for the square plates. The NIR heating reaches the process temperatures for both Ti6Al4V and 316 L before the outgassing stage is complete with standard EB heating. In the scenario shown in , the heating time to the process temperature of Ti6Al4V is reduced by 13% at a mean NIR heating rate of 97°C/min (between 100 and 730°C) for the circular plate. The same value for the square plate is 56% at 60°C/min. With the NIR power set to 4–5 kW, the start plate heating time was similar to that of EB heating, including the outgassing stage. shows the dynamics of the vacuum in the chamber and the cooling water temperature during the NIR heating experiments. shows that the vacuum is kept at a level normal to the EBM even with the NIR emitters active.
Figure 3. Heating of square and circular start plates placed over a loose Ti6Al4V powder bed. All time data is zeroed at 100°C to avoid lag that arises due to the thermocouple being placed below the start plate. a) Temperature measured under the start plate, b) Power applied by the heat sources, c) Corresponding chamber vacuum, d) NIR cooling water temperature dynamics.
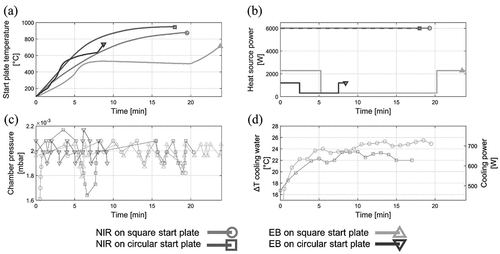
The need for NIR system cooling occurred mostly during the start plate heating phase (during maximum NIR power), and the demand for cooling increased as the start plate size increased. It can be noted from that after the first period of heating, the cooling water temperature in the return pipe stabilized. Accounting for the specific heat capacity for water and used flow rates, it can be determined that the maximum cooling used at 6 kW NIR power was 672W for circular start plates and 729W for square start plates.
Powder sintering by NIR
NIR preheating applied to a single layer of 316 L and Ti6Al4V powders deposited over the start plate resulted in a level of sintering comparable to that achieved by common EB settings for the tested power level (although such sintering is difficult to achieve in the EB case for cold powder layers). It is clear that NIR sintering is more uniform, as EB sintering often results in harder sintered tracks surrounded by softer sintered areas. The bands of condensed sintering typical of EB preheating were not observed in the NIR cases. illustrates the changes in the sintered powder under EB for different surface energy settings. As the energy and beam application time increase, the EB sintering progresses from a homogeneous “loose sintering” () to the formation of islands of harder sintering () and finally to solid material, essentially melted over a thin surface area (). In the case of NIR, a different pattern was observed, as illustrated in . NIR allows for much better sintering control and greater sintering depth. Even when NIR sintering was applied at full power (6 kW) for 15 minutes, it was not possible to replicate the EB “solid metal surface” (). Instead, a red-hot, hard-sintered upper layer with a thickness of about 20 mm was created. It should be noted that the EB energy mostly affects the thin uppermost layer of powder, while NIR provides much deeper penetration. This provides a wider window of parameters for sintering and heating without the powder melting. In addition, the corresponding “bridges” connecting adjacent powder grains after adequate sintering needed to support “smoke-free” EB melting are much less pronounced than in the case of NIR sintering. This means that the NIR-sintered powder is easier to break apart into individual particles, providing better powder recovery after the build is complete (EB sintered powder tends to break in clusters). This is a noteworthy difference given that the EB power used for sintering (1200–2280 W) is much less than that of NIR.
Figure 4. EB sintering of 316L stainless steel with a fixed beam focus offset of 200 mA at: a) a beam speed of 14,000 mm/s and beam current 10.5 mA for 15 repetitions, b) a beam speed of 14,000 mm/s and beam current 10.5ma for 20 repetitions, c) a beam speed of 11,000 mm/s and beam current 15 mA for 20 repetitions.
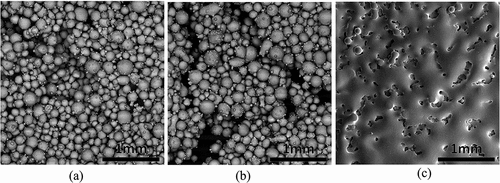
Figure 5. NIR sintering progress at different energy levels and durations for Ti6Al4V powder (a-d) and 316L powder (e-h). 3 kW power was used in a) and e) for 28 seconds as well as b) and f) for 56 seconds. 6 kW power was used in c) and g) for 28 seconds as well as d) and h) for 56 seconds.
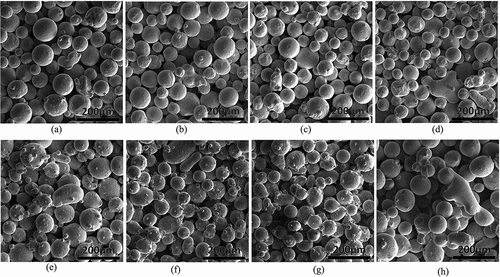
It should be highlighted that it was possible to achieve sufficient NIR sintering to support EB melting for NIR energy levels of 2–6 kW. Increasing the NIR energy speeds up the heating process, but no partial or full layer melting was observed up to the maximum of 6 kW. However, some particles formed clusters at random locations, but these were not regular as in the EB case. Early experiments with more powerful NIR sources showed the possibility of melting even 2–3-mm-thick powder layers, which means that the surface energy intake from NIR sources can be increased if necessary. Below 2 kW NIR power, the heating process was relatively slow compared to EB, hence it was not further investigated. shows how NIR sintering progresses when using different energy and heating times for Ti6Al4V () and 316 L () precursor powders. The sample in is loosely sintered compared to that showed in 5b, which was sintered for a longer time, but both cases were sufficient to avoid smoke and support uninterrupted EB melting. Some powder clusters are formed during NIR sintering and grow in size with increasing NIR duration and power (). Although there is no good quantitative way of describing a sintered powder, the consistency of the sample in is very similar to that in , indicating that the sintering is more dependent on total energy input than power. The same situation is true for 316 L, as indicated in .
NIR preheating was applied to each of the consecutively deposited layers of 316 L and Ti6Al4V powder, resulting in a “powder cake”; this was also analyzed and presented similar results as for single layer sintering. In all cases, the NIR-sintered powder cakes had comparable consistency to the EB-sintered ones, but, in line with previous results, also had more distributed “bridging” between the particles, as shown in . For 316 L, in particular, the results show that the sintered powder can be preserved for better recovery ( versus 6b) while still supporting “smoke-free” stable EB melting. The EB-sintered powders () show areas where the powder grains are almost completely melted together, while the NIR-sintered powders () are comparatively homogeneous and their morphology after sintering and recovery is much closer to the initial state. In all tested cases, the sintered powder could be recycled using a standard powder recycling system (PRS) by blasting it with precursor powder.
Sample manufacturing using NIR heating
The EB melting process after NIR start plate heating and powder layer preheating was similar to the standard EBM process. This was also true for the bottom temperature, as shown for Ti6Al4V in . Most samples produced using the NIR-assisted process showed swelling due to excessive energy input, as standard EBM melt settings were used to avoid complicating the comparison by introducing additional parameters. This indicates that NIR heat is distributed deeper in the powder bed, which is speculated to result in better heat retention. Therefore, the consecutive EB melting stages in NIR-supported processes need to be re-adjusted. These results suggest that EB melting following NIR heating should have a lower melt energy compared to the standard EBM process. Example of Ti6Al4V samples that exhibited swelling on their upper surfaces (typical of excessive melting energy)[Citation32] is shown in . Even with the swelling on the surface, the microstructure and sub-structure in the bulk of the sample are similar in the 316 L case when comparing the NIR-aided process () to a standard EBM process (). The same is true for Ti6Al4V ( vs 7f). It can however be noted that the grains are slightly larger in the NIR-assisted samples for both alloys, as can be expected at higher energy input.
Figure 7. a) Example of bottom temperature during the first 40 layers of Ti6Al4V for NIR-assisted and standard EB builds, b) 316L microstructure from NIR-assisted build, c) 316L microstructure from standard EBM build, d) Ti6Al4V build before powder cake removal, e) Ti6Al4V microstructure in NIR-assisted build, f) Ti6Al4V microstructure in standard EBM build.
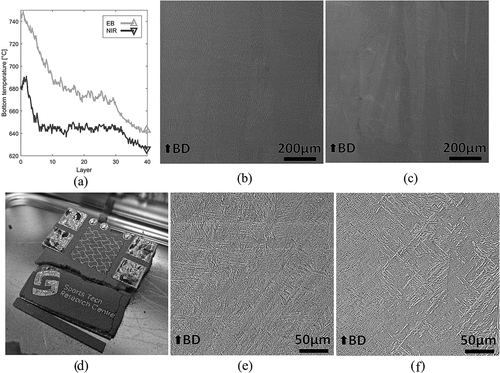
Hardness and Archimedes density were analyzed on the 15 mm x 15 mm square samples. As expected from the microstructures shown in , all analyzed material properties were similar between the NIR-assisted process and standard EBM process. The obtained microstructures are similar to what has earlier been reported for PBF-EB.[Citation33–36] As shown in , fully dense material was produced in the NIR-assisted process, and the resulting material hardness was the same for both processes when considering the standard deviation of the measurements. The only exception is that Ti6Al4V resulted in a higher density in the presented measurements for the NIR-assisted processes. The density was showed to be over 100%, which could be explained by excessive energy input causing Al evaporation[Citation37] when using standard EBM settings in the NIR-assisted process.
Table 1. Measured Rockwell hardness and Archimedes density values of NIR-assisted and original fully EB-supported process. Standard deviation values are included in parenthesis. The nominal density was set as 8.0000 g/cm3 for 316 L, 4.4500 g/cm3 for Ti6Al4V, and 0.9984 g/cm3 for water at 19°C.
Given the current experiments and manual activation of the NIR, it is not possible to report any representative values for the process time. The active heating time (beam on) for the standard EBM process in the used build file () was~49 seconds for 316 L and~13 seconds for Ti6Al4V for each layer. The active heating time (emitter on) for NIR-assisted builds varied for each layer but was normally between 5 and 15 seconds for both materials. However, due to the manual control of the process, including 12 operator inputs per layer as well as unnecessary rake movement (a drawback of working with EBM control version 3.2), the layer time was approximately 20% longer for NIR-assisted builds. Based on the active heating time, the results still indicate that once the NIR is fully integrated in the PBF-EB control and system design, the layer heating time can be expected to be reduced by 13–80% depending on the precursor alloy and required process temperature. Additionally, all NIR-assisted builds operated at a lower column temperature. For 316 L, the gun temperature peak was reduced by 13°C, and the mid process (sample height Z = 3–4 mm) temperature was reduced by 8°C. For Ti6Al4V, the temperature difference was smaller but still detectable (3°C).
NIR performance
The NIR unit operated well without any noticeable degradation of the emitters after 11 builds and approximately 50 different heating experiments. NIR allowed for better temperature control compared to EB heating, especially in the preheating parameter development stages. It was found that “failed builds” could be saved after smoke events by restarting the process and applying longer preheating times. Even cakes that had been “blown away” after smoke events could be repaired because of the deep heat distribution of NIR.
As previously mentioned, and as visible in , active cooling of the NIR unit is mostly necessary when heating for periods of a few minutes or more. This type of heating is commonly present only during the initial start plate heating. During the actual build process, the NIR unit will be inactive for the majority of the time. Therefore, it could be possible to cool the unit by placing it in contact with a thermal bridge instead of using water cooling. However, if the NIR was integrated in the PBF-EB system design early on, the cooling could be simplified.
Conclusions
This study showed that NIR integration is a promising method to overcome some of the limitations and challenges of PBF-EB. The NIR unit functioned without problem in a vacuum, and no emitter degradation was noticed. Builds using NIR heating only were successfully performed for two common but very different PBF-EB materials, Ti6Al4V and 316 L. The microstructure and properties of the resulting bulk material were very similar to the standard processes. The results show that the standard EBM process settings can be used, but the energy level should be reduced to avoid material swelling. Therefore, the application of NIR heating for other alloys or other PBF equipment should be relatively straightforward. The main findings can be summarized as follows:
Powder bed heating could be conducted at full 6 kW without any risk of melting, charging, or smoking. This provided a good pre-sintering for EB and allowed a broader sintering regime since high power EB heating tends to melt the powder. The possibility of applying full power in combination with the deep energy distribution that NIR provides also presented new opportunities to save failed builds.
The load on the electron gun was decreased by using NIR to heat and sinter, which is expected to increase filament lifetime. Column temperature reduction of up to 13°C was observed, which can help processing materials at high temperatures. An additional benefit of using the NIR-assisted process is to avoid filament damaging arc trips and contamination, which occurs in the standard process during the initial heating stage.
Charge-free heating for reduced time intervals is considered one of the crucial factors for future industrial applications of PBF-EB systems. Today, NIR sources with dimensions that significantly exceed those of existing working areas in metal-AM systems are available in industrial settings. Heating a larger area with EB requires faster deflection rates and higher energy input (in many cases together with longer heating times), demanding compromises on beam spot size, resolution, surface roughness, etc. By using NIR for heating, this problem is eliminated, as the emitters can be designed to heat any area. Additionally, the experiments indicate that if NIR can be applied in an automatic fashion, the process time can be significantly reduced. The time reduction will depend on the process, material, and build size, but for the cases tested in the present work, potential heating time reductions of up to 80% each layer were observed. Additionally, the results show that the initial heating time could be reduced by up to 56% using NIR.
The NIR-sintered powder cakes showed similar consistency to the EB ones, simultaneously being more homogeneous and having less pronounced inter-grain bridges. This should lead to more efficient recycling with the potential for less damage to the powder during industrial manufacturing. The fact that EB-sintered cakes broke into powder clusters while the NIR-sintered cakes easily separated into powder particles confirmed this. It can be also noted that chargeless heating may facilitate the use of precursor powders that has not yet been compatible with PBF-EB processes (e.g., powders with low conductivity).
Further work should aim to investigate how NIR technology can be used to redefine the PBF-EB process (e.g., if helium gas can be eliminated, if new process modes should be considered, and how far the conductivity of the precursor powders can be reduced). Some adjustments to the melting themes are needed to avoid swelling. However, this is not considered a crucial problem at this stage of development. In addition, more thorough analysis of the potential for energy savings and to reduce build times should also be performed. To reach the full potential of the suggested approach, the NIR heating should be integrated into the PBF system and driving software design early on. This would optimize the process time and interconnection between NIR and EB, enabling, for example, an automatic recovery following process instabilities or smoke events.
Acknowledgments
The authors would like to thank Dr. Kai K. O. Bär, Rolf Wirth (adphos Innovative Technologies GmbH) and Karl Neulinger (St. Pölten, AUT) for their contributions and for participation of the presented investigations. We would also like to gratefully acknowledge adphos Group for the Near infrared equipment and test set-up provision.
Disclosure statement
No potential conflict of interest was reported by the author(s).
Additional information
Funding
References
- Ladani, L.; Sadeghilaridjani, M. Review of Powder Bed Fusion Additive Manufacturing for Metals. Metals (Basel). 2021, 11, 9. DOI: 10.3390/met11091391.
- Sing, S. L.; An, J.; Yeong, W. Y.; Wiria, F. E. Laser and Electron-Beam Powder-Bed Additive Manufacturing of Metallic Implants: A Review on Processes, Materials and Designs. J. Orthop. Res. 2016, 34(3), 369–385. DOI: 10.1002/JOR.23075.
- Fu, Z.; Körner, C. Actual State-Of-The-Art of Electron Beam Powder Bed Fusion. Eur. J. Mater. 2022, 2(1), 54–116. DOI: 10.1080/26889277.2022.2040342.
- Botero, C.; Ramsperger, M.; Selte, A.; Åsvik, K.; Koptyug, A.; Skoglund, P.; Roos, S.; Rännar, L. E.; Bäckström, M. Additive Manufacturing of a Cold-Work Tool Steel Using Electron Beam Melting. Steel Res. Int. 2020, 91(5), 1900448. DOI: 10.1002/SRIN.201900448.
- Zhang, L. C.; Liu, Y.; Li, S.; Hao, Y. Additive Manufacturing of Titanium Alloys by Electron Beam Melting: A Review. Adv. Eng. Mater. 2018, 20(5), 1700842. DOI: 10.1002/ADEM.201700842.
- Wu, L.; Das, S.; Gridin, W.; Leuders, S.; Kahlert, M.; Vollmer, M.; Niendorf, T. Hot Work Tool Steel Processed by Laser Powder Bed Fusion: A Review on Most Relevant Influencing Factors. Adv. Eng. Mater. 2021, 23(7), 2100049. DOI: 10.1002/ADEM.202100049.
- Azam, F. I.; Abdul Rani, A. M.; Altaf, K.; Rao, T. V. V. L. N.; Zaharin, H. A. An In-Depth Review on Direct Additive Manufacturing of Metals. IOP Conf. Ser Mater. Sci. Eng. 2018, 328, 1. DOI: 10.1088/1757-899X/328/1/012005.
- Laleh, M.; Sadeghi, E.; Revilla, R. I.; Chao, Q.; Haghdadi, N.; Hughes, A. E.; Xu, W.; De Graeve, I.; Qian, M.; Gibson, I., et al. Heat Treatment for Metal Additive Manufacturing. Prog. Mater. Sci. 2022, 133, 101051. DOI: 10.1016/J.PMATSCI.2022.101051.
- Körner, C. Additive Manufacturing of Metallic Components by Selective Electron Beam Melting - A Review. Int. Mater. Rev. 2016, 61(5), 361–377. DOI: 10.1080/09506608.2016.1176289.
- WO2020157133A1 - Spot preheating - Google Patents. https://patents.google.com/patent/WO2020157133A1/en (accessed 2022 November 16).
- WO2022170296A1 - Heating techniques for additive manufacturing - Google Patents. https://patents.google.com/patent/WO2022170296A1/en (accessed 2022 November 16).
- CN111804916B - Preheating method for electron beam 3D printing powder bed - Google Patents. https://patents.google.com/patent/CN111804916B/en (accessed 2022 November 16).
- WO2022136843A1 - Additive manufacturing using powder bed fusion - Google Patents. https://patents.google.com/patent/WO2022136843A1/en?q=waylandadditive&oq=waylandadditive (accessed 2022 November 16).
- SE2050445A1 - Preheating of powder bed - Google Patents. https://patents.google.com/patent/SE2050445A1/en?oq=SE2050445A1 (accessed 2022 November 16).
- EP2911181B1 - Method of controlling an electron gun and electron beam additive manufacturing machine - Google Patents. https://patents.google.com/patent/EP2911181B1/en?q=jeol+electron+beam+additive+manufacturing&oq=jeol+electron+beam+additive+manufacturing (accessed 2022 November 16).
- Espacenet – search results. https://worldwide.espacenet.com/patent/search/family/064083085/publication/EP3703885A1?q=pn%3DEP3703885A1 (accessed 2022 November 16).
- Milberg, J.; Sigl, M. Electron Beam Sintering of Metal Powder. Prod. Eng. 2008, 2(2), 117–122. DOI: 10.1007/s11740-008-0088-2.
- Chiba, A.; Daino, Y.; Aoyagi, K.; Yamanaka, K. Smoke Suppression in Electron Beam Melting of Inconel 718 Alloy Powder Based on Insulator–Metal Transition of Surface Oxide Film by Mechanical Stimulation. Mater. 2021, 14(16), 4662. DOI: 10.3390/MA14164662.
- Wang, J.; Tang, H. Review on Metals Additively Manufactured by SEBM. 2016, 31(2), 86–89. DOI: 10.1179/1753555715Y.0000000081.
- Galati, M.; Iuliano, L. A Literature Review of Powder-Based Electron Beam Melting Focusing on Numerical Simulations. Addit. Manuf. 2018, 19, 1–20. DOI: 10.1016/J.ADDMA.2017.11.001.
- JAM-5200EBM Electron Beam Metal AM Machine | Products | JEOL Ltd. https://www.jeol.co.jp/en/products/am/JAM-5200EBM.html (accessed 2022 May 12).
- Cordero, Z. C.; Meyer, H. M.; Nandwana, P.; Dehoff, R. R. Powder Bed Charging during Electron-Beam Additive Manufacturing. Acta. Mater. 2017, 124, 437–445. DOI: 10.1016/J.ACTAMAT.2016.11.012.
- NeuBeam - Wayland Additive Limited. https://www.waylandadditive.com/neubeam/ (accessed 2022 May 12).
- ProHeat – new innovation for powder heating without electron interaction | Freemelt. https://freemelt.com/mfn_news_en/proheat-new-innovation-for-powder-heating-without-electron-interaction/ (accessed 2022 May 12).
- Landau, E.; Tiferet, E.; Ganor, Y. I.; Ganeriwala, R. K.; Matthews, M. J.; Braun, D.; Chonin, M.; Ziskind, G. Thermal Characterization of the Build Chamber in Electron Beam Melting. Addit. Manuf. 2020, 36(August), 101535. DOI: 10.1016/j.addma.2020.101535.
- Lin, Z.; Dabakhsh, S.; Rashid, A. Developing Processing Windows for Powder Pre-Heating in Electron Beam Melting. J. Manuf. Process. 2022, 83(September), 180–191. DOI: 10.1016/j.jmapro.2022.08.063.
- Arnold, C.; Böhm, J.; Körner, C. In Operando Monitoring by Analysis of Backscattered Electrons during Electron Beam Melting. Adv. Eng. Mater. 2020, 22(9), 1901102. DOI: 10.1002/ADEM.201901102.
- Ameen, W.; Al-Ahmari, A.; Ahmed, N.; Alshammary, W.; Salunkhe, S.; Hussein, H. M. A. Investigation the Effect of Electron Beam Melting Parameters on Overhang Structure Deformation. Mater. Technol. 2021, 37(10), 1586–1593. DOI: 10.1080/10667857.2021.1994174.
- Adphos Group | NIR Technology, Solutions, Applications and Dryers. https://www.adphos.com/ (accessed 2022 June 16).
- Lee, H. J.; Ahn, D. G. Investigation of Elimination of Powder Spreading in Manufacture of Thin and Wide Preheating Beads from Co–Cr Alloy Powders Using a P-Ebeam. J. Mater. Res. Technol. 2021, 14, 1873–1883. DOI: 10.1016/J.JMRT.2021.07.078.
- Murr, L. E.; Martinez, E.; Amato, K. N.; Gaytan, S. M.; Hernandez, J.; Ramirez, D. A.; Shindo, P. W.; Medina, F.; Wicker, R. B. Fabrication of Metal and Alloy Components by Additive Manufacturing: Examples of 3D Materials Science. J. Mater. Res. Technol. 2012, 1(1), 42–54. DOI: 10.1016/S2238-7854(12)70009-1.
- Roos, S.; Rännar, L. -E. Metals Process Window for Electron Beam Melting of 316LN Stainless Steel. Metals. 2021, 11(1), 137. DOI: 10.3390/met11010137.
- Mohammadhosseini, A.; Fraser, D.; Masood, S. H.; Jahedi, M. Microstructure and Mechanical Properties of Ti–6Al–4V Manufactured by Electron Beam Melting Process. Mater. Res. Innovations. 2013, 17(SUPPL 2), s106–112. DOI: 10.1179/1432891713Z.000000000302.
- Eskandari Sabzi, H. Powder Bed Fusion Additive Layer Manufacturing of Titanium Alloys. Mater. Sci. Technol. 2019, 35(8), 875–890. DOI: 10.1080/02670836.2019.1602974.
- Tong, J.; Bowen, C. R.; Persson, J.; Plummer, A. Mechanical Properties of Titanium-Based Ti–6Al–4V Alloys Manufactured by Powder Bed Additive Manufacture. Mater. Sci. Technol. Mater. Sci. Technol. 2016, 33(2), 138–148. DOI: 10.1080/02670836.2016.1172787.
- Li, H.; Liang, X.; Li, Y.; Lin, F. Performance of High-Layer-Thickness Ti6Al4V Fabricated by Electron Beam Powder Bed Fusion under Different Accelerating Voltage Values. Mater. 2022, 15(5), 1878. DOI: 10.3390/MA15051878.
- Kirchner, A.; Klöden, B.; Luft, J.; Weißgärber, T.; Kieback, B. Process Window for Electron Beam Melting of Ti-6Al-4V. Powder Metall. 2015, 58(4), 246–249. DOI: 10.1179/0032589915Z.000000000244.