Abstract
The aim of this study was to evaluate the behavior of Hg, As, and Se in cement production. Two types of cement plants were studied, including the vertical shaft kiln (VSK) and preheater–precalciner kiln (PPK) processes. Determination of Hg, As, and Se in the main material and gas streams were performed. It was found that recycling of particulate matter captured by an air pollution control device caused a significant enrichment of Hg and As inside both processes. The total quantity of Hg entering the process and the quantity emitted to the atmosphere were found to be 10–109 and 6.3–38 mg, respectively, per ton of clinker produced. The average Hg emission was calculated to be around 41% of the total mercury input. The emissions found complied with the European Union (EU) limit and exceeded partly the U.S. limit. Furthermore, it was found that oxidized mercury was the dominant species in the PPK process, whereas the reduced form was dominant in the VSK process, due to the oxidizing and reducing gas conditions, respectively. Regarding the distribution of As and Se, the major amounts were bound to the solid materials, that is, cement clinker and particulate matter. Based on cement production data in China in 2013, the annual emissions of Hg and As were estimated to be in the range of 8.6–52 and 4.1–9.5 tons, respectively.
Implications: There are fairly limited studies on Hg, As, and Se measurements from cement manufacturing facilities in China, and even more limited studies on the behavior in vertical shaft kilns. The needs for increased emission reduction efforts in energy-intensive industries are globally recognized, and an improved understanding of the processes ongoing in a cement kilns system is decisive. Since the processes are complex and almost impossible to recreate in the laboratory, field measurements are indeed important. The findings in the present study were solely based on field measurements and the data are considered to be valuable for the further development of emission reduction technology.
Introduction
The effects of Hg, As, and Se on the environment and health have received wide attention (Tian et al., Citation2010, Citation2011; Al-Abed et al., Citation2008; Lenz and Lens, Citation2009). The Minamata Convention on Mercury is a global treaty to protect human health and the environment from the adverse effects of Hg. The Government of China supported this global initiative and signed the convention on October 10, 2013. The main emission sources are coal-fired power plants, coal-fired industrial boilers, production of nonferrous metal, waste incineration, and cement clinker production (United Nations Environmental Programme [UNEP], Citation2013a,b).
In Europe, the following directives are relevant to the toxic element emission: Directive 2000/76/EC on the incineration of waste, Directive 2008/1/EC concerning integrated pollution prevention and control, and Directive 2010/75/EU on industrial emissions (integrated pollution prevention and control). Since the early 2000s, the European Union (EU) has placed a strict Hg regulation on cement producers, reducing the Hg emissions to 20–60 mg per ton of clinker produced (mg/t) (Neundorfer, Citation2010). The stack gas emission limit is 0.05 mg/N-m3 for Hg and 0.5 mg/N-m3 for the sum of Sb, As, Pb, Cr, Co, Cu, Mn, Ni, and V at 10% O2. In the United States, an average Hg emission factor of 65 mg/t exists (U.S. Environmental Protection Agency [EPA], Citation1997). Furthermore, the regulations are dependent whether the plants co-process hazardous waste or nonhazardous wastes. For existing cement plants in the former category, the limit for the total concentration of Hg in the waste input is 3.0 mg/kg. The stack gas emission limits for Hg and the sum of As, Be, and Cr are 0.120 and 0.056 mg/N-m3 at 7% O2¸ respectively (40 CFR 63 Subpart EEE, Citation2014). For new cement plants the corresponding limits are 1.9 mg/kg for the waste input and 0.120 mg/N-m3 and 0.054 mg/N-m3 for the flue gas at 7% O2. The mercury limit of U.S. standards will be equivalent to 0.088 mg/N-m3 when it is corrected to an oxygen value of 10% and 273 K. It is still greater than the European or Chinese standards. The Hg limits for processes without co-processing of hazardous waste are limited to a 30-day average of 27.5 and 10.5 mg/t of clinker for existing and new plants, respectively.
In December 2013, the Ministry of Environmental Protection (MEP) in China published a revised air pollutant emission standard for cement industry and two new standards focusing on co-processing of wastes. The regulation sets the emission limit for Hg to 0.05 mg/N-m3 (at 10% O2) and the sum of Tl, Cd, Pb, and As to 1 mg/N-m3 (at 10% O2) (MEP, Citation2013a, Citation2013b).
In China today, the dry process equipped with a preheater and precalciner kiln (PPK) accounts for 90% and the rest is by a semidry process that applies a vertical shaft kiln (VSK) (China Cement Association [CCA], Citation2013). In recent years, several studies have been conducted on the analysis and control of Hg and other elemental emissions from coal-fired power plants and waste incineration plants in China (Tian et al., Citation2010, Citation2011; Chen et al., Citation2013a, Citation2013b) and worldwide (Senior et al., Citation2000; Jeon et al., Citation2008; UNEP, Citation2008a, Citation2008b). However, comprehensive and detailed studies regarding Hg, As, and Se emissions from cement plants are limited. Guo and Eckert (Citation1996) evaluated the concentration of heavy metals (including As) from stack emissions, kiln dust, and the clinker from one cement plant. In another field study, the distribution of added HgO tracer has been reported in order to assess the distribution and mass balance (Eriksen et al., Citation2000). In addition, Won and Lee (Citation2012) estimated the total annual Hg emissions from cement plants located in South Korea using field measurements and statistical data. They estimated an annual Hg emission in the range of 1.17–1.53 tons and an emission factor in the range of 26–34 mg/t clinker. The complex preheater and precalciner cement manufacturing process results in a complicated element distribution. The main reasons for this include that captured particulate matter (PM) is usually reintroduced into the kiln. In addition, the hot flue gases are used to preheat the raw materials and fuel. This involves chemical reactions, with deposition to and reemission of volatile species from solid material surfaces. The mercury enrichment caused by the recycling of captured PM has been indicated by Wang et al. (Citation2014) and Mlakar et al. (Citation2010). The former authors reported the emission factor for Hg to be 44–72 mg/t clinker. Studies regarding the mercury behavior in the VSK process are few, and even more limited when As and Se are included.
In this study, Hg, As, and Se were determined in individual raw materials, fuels, clinkers, and stack gas for two PPK plants and two VSK plants. Their mass distribution, input factors, and emission factors were calculated. Finally, the total annual Hg emissions from cement production in China were estimated based on the emission factors calculated from the field tests and the annual production statistics.
Material and Methods
Cement kiln description
Cement production involves heating, calcining, and sintering of blended and ground raw materials (raw meal), typically limestone and clay or shale and other materials, to form clinker. Clinker formation takes place at a material temperature of 1450ºC in rotary kilns. After rapid cooling, the clinker is ground with typically 3–5% of gypsum to give Portland cement (Karstensen, Citation2008). In addition, blended cements are produced by intergrinding the cement clinker with various amounts of materials like fly ash, granulated blast furnace slag, limestone, and natural or artificial Pozzolanas (Hewlett, Citation1998).
A PPK consists of a tower with usually five- or six-staged heat exchange cyclones (preheater) and a second combustion device (precalciner), which is connected to the rotary kiln; see . In a modern PPK, the production capacity can reach up to 10,000 tons of clinker per day. In the semidry vertical shaft kiln (VSK) process, the production capacity is much lower and usually less than 300 tons of clinker per day. Such a kiln is a refractory-lined, vertical cylinder, 2–3 m in diameter and 8–10 m high and fed from the top with a mix of dry ground raw material and fuel called black meal, consisting of approximately 13% of coal or coke. Prior to feeding into the kiln, water is added at an average moisture content of 12%; see . The clinker is discharged by a rotary grate at the bottom part of the cylinder.
Figure 1. Outline of the processes and sampling spots of the flue gases in (a) a dry process cement kiln with preheater and precalciner (PPK) and (b) a semidry process vertical shaft kiln (VSK). Sampling of solid materials is indicated with (s).
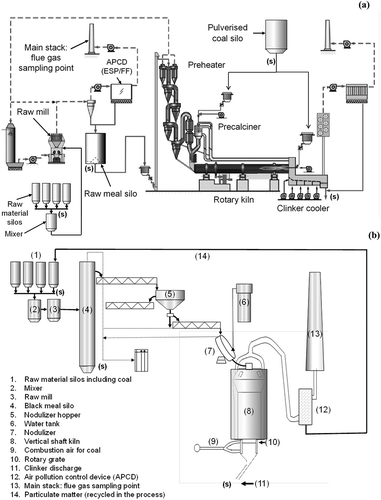
Field test measurements were conducted at four different cement plants and included six separate production lines in China; see . The sample names indicate the plant type and the test plant number (VSK1, VSK2, PPK1, and PPK2). All facilities were equipped with air pollution control devices (APCD), including either fabric bag filter (FF), electrostatic precipitator (ESP) or a wet scrubber (WS). Flue gas was sampled in the main stack when the plants were operating under normal and stable conditions; see and .
Table 1. Characteristics and location of cement plants and test details.
Sampling and chemical analysis of Hg, As, and Se in the flue gas
A KNJ M-5 Source Sampling (KNJ Engineering, South Korea) unit was used for isokinetic flue gas sampling, complying with EPA Method 5. The Ontario Hydro Method (OHM) was used for the sampling of Hg from the flue gas described in ASTM D6784-02. For the sampling of As and Se, EPA Method 29 was followed. Flue gas was simultaneously sampled in duplicate. The total sampling time for one sample (Hg or As and Se) was 2–3 hr. The sampling time for collection of 1 m3 dry flue gas was approximately 1 hr. The collected subsamples were recovered and digested according their respective methods. For the determination of the Hg in the final sample solutions, the cold-vapor fluorescence spectrometry (CVAFS) technique was applied using an XGY-1011A atomic fluorophotometer. The detection limit was 0.05 ng/mL. The chemical analyses were carried out at Zhejiang University. For the As and Se analyses, the two-way atomic fluorescence spectrometer AFS 2202-10127 was applied at Hangzhou Supervision, Inspection and Test Center of Mineral Resources, Ministry of Land and resources. The detection limits were 4 µg/L and 10 mg/L, respectively.
Pre and post leak checks were performed for each sampling procedure. The results from the sampling tests carried out in duplicate were averaged. For the blanks, including field blank (n = 6) and laboratory blank (n = 18), the Hg, As, and Se levels were below the method detection limit.
Sampling and chemical analysis of Hg, As, and Se in the solid samples
Samples of the raw materials, fuel, and clinker were collected; see . The raw material and the fuel (coal or lignite) samples were collected at the hopper of the respective material silo; see and . In the PPK and VSK process, each type of raw material is dosed and mixed in accordance with its composition before it is pulverized in the raw mill. The milled raw materials are mixed with PM (captured by the APCD) to constitute the final raw meals (for PPK and VSK) and stored in the homogenizing silo prior to the feeding. The final raw meals were sampled at the hopper of the raw meal and black meal homogenizing silos for PPK and VSK, respectively. The clinker was sampled after the clinker cooler (PPK) and at the clinker discharge (VSK). For all materials, 3–4 subsamples with weight of 1 kg were collected and thoroughly mixed and homogenized to form the final laboratory sample. The concentrations of Hg, As, and Se were determined according to EPA Method 7473 and ASTM D6722-01. The mercury analyzer MA-2000 was used for determination of Hg with a method detection limit of 0.5 µg/kg. The 4015 two-way atomic fluorescence spectrometer AFS 2202-10127 was used for the analyses of As and Se with method detection limits of 1 mg/kg and 0.01 mg/kg, respectively. Digestion of solid samples and the analyses of Hg were conducted at Zhejiang University. The As and Se were analyzed at Hangzhou Supervision, Inspection and Test Center of Mineral Resources, Ministry of Land and Resources. According to the operation record, only the As and Se sampled in the solution were analyzed.
Table 2. Material component compositions (%) in the raw material mix and the total concentrations of Hg, As, and Se in the solid fractions (mg/kg).a
Calculation of constituent concentrations in raw material mix and in PM
The constituent concentrations were measured in the separate raw materials, the final raw meals (regular and black meal), and in the clinker; see . Based on these analyses, concentrations of Hg, As, and Cd were estimated for the raw material mix by multiplying the concentrations in the separate raw materials with the corresponding component share (%) in the raw material mix. The adjusted raw material concentrations were then summarized to constitute a final value for the mix; see .
The constituent concentrations in recycled PM were calculated according to eq 1:
where CPM is the constituent concentration (mg/kg) in recycled PM, CFinal raw meal is the constituent concentration (mg/kg) in the final raw meal for PPK and VSK stored in raw meal silo including milled raw material mix and recycled PM, α is the weight fraction (%) of raw material mix in the final raw meal, of which 94% and 99.3% were assumed for the PPK and VSK processes, respectively, and β is the weight fraction of recycled PM in final raw meal, of which, 6% and 0.7% were assumed for PPK and VSK processes, respectively.
The calculations made by eq 1 provide only estimates of the target element concentrations. It can be mentioned that potential adsorption of the target elements from the flue gases to material surfaces in the raw mill can obviously not be accounted for in the preceding equation. The calculations were only made in the cases where the constituent concentrations in the final raw meal were higher than in the raw material mix.
Results and Discussion
Hg, As, and Se contents in solid samples
The total element contents are shown in . In general, the concentrations depended on the available raw materials and fuels in different regions, as expected. It can also be seen that the element contents of the feedstock and fuel significantly differ from kiln to kiln. Limestone is the main material component in cement clinker production and constituted around 72–86% of the raw material mix. The Hg content in the limestone samples was found to be in the range of 0.001–0.04 mg/kg. For the other raw materials the concentration was in most of the cases below 0.1 mg/kg, except for coal fly ash and pyrite cinder. It can also be seen that the Hg concentration calculated for the raw material mix samples was in the range of 0.002–0.07 mg/kg. The highest concentration (0.07 mg/kg) was obtained in VSK2a/b, most likely due to high Hg concentrations in the coal fly ash, iron-rich material, and the intermixed coal compared to the limestone used in the sampling period. This showed the impact from waste materials and coal on the raw material mix. The same raw material impact was observed for As and Se.
When the element concentrations in the final raw meal were compared with corresponding concentrations in the raw material mix, the following was observed. Concentrations of As and in particular Hg were in most cases higher in the final raw meal than in the raw material mix. This tendency was not observed for Se. This can be subscribed to the volatility of the elements, which is higher for Hg than for As and Se. It can be seen that the Hg level in the final raw meal increased more than one order of magnitude. The increase was lower for As and and Se. In general, species are volatilized in high temperature zones and condensed at particle surfaces in cooler areas; that is, an accumulation onto PM in the APCD was expected. Since the PM fraction was mixed with the milled raw material mix, the concentration of volatile species in the final raw meal increased. In addition, the increased Hg concentration in the final raw meal can also be subscribed to adsorption onto the raw materials in the raw mill. Thus, Hg is reintroduced in the kiln and volatilized. This internal cycle enriches the Hg inside the kiln. This was also indicated by the estimated values for PM in , as concentrations of 0.2–14 mg/kg were determined for Hg. The same tendency was observed by Mlakar et al. (Citation2010). They reported Hg concentrations of 0.02, 0.06, and 0.24 mg/kg in the raw material mix, raw mill meal, and final raw meal, respectively.
Regarding the total contents in the cement clinker, low concentrations of Hg, As, and Se were found in most of the samples. Typical average concentrations of these constituents in final cements are around 0.05, 11, and <2 mg/kg, respectively (van der Sloot et al., 2011; Verein Deutscher Zementwerke [VDZ], Citation2001). It can be seen that As concentrations of 65 and 90 mg/kg were found in PPK2a and VSK2a/b, respectively. In the latter case, high concentrations of As were also found in the raw materials and in the final raw meal, which may explain the high value, as the volatility of As compounds was significantly lower than for Hg. The high value obtained for PPK2a could not be explained by the raw material input and showed somehow the challenge in obtaining consistent field data from a high-temperature incineration process. However, the results indicated that significant quantities of As and Se are transferred into clinker. In the case of Hg, small amounts were retrieved in the clinker, as discussed later.
Hg, As, and Se concentrations in flue gas
The measured concentrations of total Hg (THg) in the flue gas (the sum of GOM, Hg0 and HgP) are shown in . It ranged from 3.1 to 8.2 µg/N-m3 and from 6.6 to 37 µg/N-m3 for VSK and PPK, respectively. These values were lower than the Chinese National Standard limit of 50 μg/N-m3. The dominant Hg species were found to be the oxidized form (GOM) in PPKs and the elemental form (Hg0) in VSKs. This is explained by the oxidizing conditions present in the former process with an O2 level of around 5.6% and negligible CO concentration at the outlet of the first preheater cyclone. More reducing conditions were present in the VSK process with O2 and CO levels at 2.8% and 1.2%, respectively. In addition, it seems like a tendency toward lower THg was found in the VSK flue gas.
Table 3. Particles, Hg, As, and Se concentrations in flue gas.
Furthermore, increased concentrations of THg were observed in the flue gas when the PPKs were running in direct modes, that is, the flue gas was directly routed to the main fabric filter or ESP without adsorbing onto the raw meal in the raw mill. Higher temperatures in flue gas are also common in direct mode operations due to less heat exchange. Earlier studies regarding THg emissions from PPKs reported concentration ranges of 0.89–18 μg/N-m3 (Won and Lee, Citation2012), 4.8–28 μg/N-m3 (Wang et al., Citation2014), 1–12 μg/N-m3 (Mlakar et al., Citation2010), and 4.0-25 μg/N-m3 (Conesa et al., Citation2008). Regarding the concentrations of As and Se in the flue gas, small concentrations were generally observed for Se, as can be seen in . In the case of As, most of the measurements were below 5 μg/N-m3. Varying results of As were found in earlier studies for PPKs. Guo and Eckert (Citation1996) reported 6.0 μg/N-m3, whereas Gupta et al., (Citation2012) reported 37 μg/N-m3 and Conesa et al. (Citation2008) reported emissions of 0.9–3.7 μg/N-m3 when waste tires or sewage sludge was used as co-fuel.
Mass stream distribution of Hg, As, and Se
Assessment of the mass stream distribution could lead to a better understanding of the transport of the target elements. The input streams include the raw materials, coal, and recycled PM, whereas the output streams include flue gas, clinker, and PM captured by APCD; see and . Since the PM was entirely used as feedstock, the recovery of the elements in flue gas and clinker was calculated based on the input from raw materials and coal excluding the PM and the output from flue gas and clinker. The feeding rates and flue gas flows specified in were used in the calculations.
Except for PPK1, the results showed that 5.8–77% and 36–73% of input Hg were transferred into flue gas from the VSK and PPK processes, respectively. The high value of PPK1 (434%) may be due to the higher Hg concentration in PM, which was transferred to the flue gas during recycling. It should also be emphasized that the calculation was based on Hg concentrations near the quantification limit, which will cause uncertainty. Mlakar et al. (Citation2010) showed that the Hg flue gas emission in the annual mass balance was in the range of 40–70% of the inputs, and the difference between inputs and outputs obtained in the mass balances could be assigned to mercury cycling causing a significant Hg enrichment (accumulation) inside the process. In Wang et al. (Citation2014), the Hg output/input ratio was measured as 1.0–1.3 in 3 cement plants, whereas 94–98% of the Hg input was emitted by the flue gases. Regarding As and Se, low levels in the flue gas were found, which showed that low levels of these elements were transferred to the flue gas.
Regarding the output through clinker (Output 2), the major results indicated that a low percentage of input of Hg was transferred to the clinker, whereas most of the Se and As were recovered in the clinker. The distribution proportions above 100% were due to the increased level of As in PM being transferred into clinker.
The practice of recirculation of PM from the APCD causes accumulation of volatile and semivolatile elements. The results in the study strongly indicate such accumulation. Furthermore, when the outputs (quantity in flue gas and clinker) were smaller than the input, this indicated increased concentrations in PM. That may imply that Hg will accumulate within the system and eventually be emitted into atmosphere. In the case of As, accumulation in the PM seems to readily occur, as enrichment in the clinker output stream was observed, most likely due to the recycling of PM.
Estimates of total annual emissions of Hg and As from cement plants in China
The calculated emission factors for THg and As used were 6.3–38 mg/t and 0.04–6.6 mg/t, respectively. The unusual high As value for VSK1 (110 mg/t) and the low value for VSK2c (not detected) shown in were disregarded. In China, the annual clinker production was 1.36 billion tons in 2013. This corresponded to an annual cement production of 2.4 billion tons (National Bureau of Statics of China, Citation2013). Applying this statistics and the emission factors obtained in the present study, it was found that the annual emission of Hg and As was 8.6–52 tons and 0.05–9.0 tons, respectively. Earlier estimations for Hg have been reported to be 3–90 mg/t (UNEP, Citation2013a,b). The results gained in the present study may contribute to obtain more precise and accurate emission estimates.
Table 4. Element mass stream distribution based on the quantity entering the process by the raw material mix (input) and the exit mass through flue gases (output 1) and the clinker (output 2).a
Conclusion
It can be concluded that most of the Hg that entered the process was not retrieved in the cement clinker. The opposite seemed to be the case for As and Se. The analysis strongly indicated that the target elements were accumulated in the PM collected by the APCDs. However, Hg also seemed to be enriched in the internal kiln cycle by adsorption to raw meal material surfaces. In addition, all the PM was reused as feedstock in both processes, which resulted in accumulation of Hg within the facility. This may eventually be emitted into the atmosphere. The oxidized forms of Hg in the flue gas were found to be predominant in the PPKs, whereas the reduced form (Hg0) was more present in the VSKs. For the PPK process, the concentration of all species in the flue gas increased during the direct mode operation, which showed the effect of adsorption to the raw material surfaces.
The concentrations of THg in the flue gas are specified as 3.1–8.2 μg/N-m3 for VSK and 6.6–37 μg/N-m3 for PPK. This is below the current new issued Hg limit in China. The input factor of Hg was in the range of 10–109 mg/t and the emission factor of Hg ranged between 8 and 38 mg/t, which is within the low end of the EU limit but partly exceeds the U.S. limit. The estimation showed that on average, around 41% of the mercury input was released to the atmosphere. For As, flue gas concentrations of 2.3–4.4 μg/N-m3 were determined, which gave emission factors in the range of 2–7 mg/t. The input factor of Se ranged between 592 and 5754 mg/t, and the output factor of Se (clinker) was in the range of 320–3056 mg/t. The calculations also showed that the annual Hg and As emissions in China were 8.6–52 tons and 4.1–9.5 tons, respectively.
The needs for increased emission reduction efforts in energy-intensive industries are globally recognized and an improved understanding of the processes ongoing in a cement kilns system is decisive. Since the processes are complex and almost impossible to recreate in laboratory, field measurements are indeed important. The findings in the present study were solely based on field measurements and the data are considered to be valuable for the further development of emission reduction technology.
Acknowledgments
Xintai Cement Company, Henan YuheTongli Cement Co., Ltd., Zibo Luzhong Cement Co., Ltd., and Shandong Donghua Cement Co., Ltd., are acknowledged for field testing in the study. Zhejiang University is acknowledged for the assistance in sampling and the analyses of Hg, As, and Se.
Funding
This project has been co-funded by Sino-US project (X-83192101-0) Managing Pollution From Persistent Organic Pollutants (POPs) and other toxic substances in China, and Sino-Norway Project (CHN-2150,-09/059) on Environmentally Sound Management of Co-Processing of Hazardous and Industrial Wastes in Cement Kilns in China (Phase II).
Additional information
Funding
Notes on contributors
Dahai Yan
Dahai Yan is an associate researcher and Li Li is researcher at China Research Academy of Environment Science. Zheng Peng is a senior engineer, Qiong Ding is a researcher, and Yong Ren and Chen Jiang are engineers at the Foreign Economic Cooperation Office of the Ministry of Environmental Protection, China. Kåre Helge Karstensen is a chief scientist and Christian J. Engelsen is a senior scientist at SINTEF, Norway.
Zheng Peng
Dahai Yan is an associate researcher and Li Li is researcher at China Research Academy of Environment Science. Zheng Peng is a senior engineer, Qiong Ding is a researcher, and Yong Ren and Chen Jiang are engineers at the Foreign Economic Cooperation Office of the Ministry of Environmental Protection, China. Kåre Helge Karstensen is a chief scientist and Christian J. Engelsen is a senior scientist at SINTEF, Norway.
Qiong Ding
Dahai Yan is an associate researcher and Li Li is researcher at China Research Academy of Environment Science. Zheng Peng is a senior engineer, Qiong Ding is a researcher, and Yong Ren and Chen Jiang are engineers at the Foreign Economic Cooperation Office of the Ministry of Environmental Protection, China. Kåre Helge Karstensen is a chief scientist and Christian J. Engelsen is a senior scientist at SINTEF, Norway.
Kåre Helge Karstensen
Dahai Yan is an associate researcher and Li Li is researcher at China Research Academy of Environment Science. Zheng Peng is a senior engineer, Qiong Ding is a researcher, and Yong Ren and Chen Jiang are engineers at the Foreign Economic Cooperation Office of the Ministry of Environmental Protection, China. Kåre Helge Karstensen is a chief scientist and Christian J. Engelsen is a senior scientist at SINTEF, Norway.
Christian J. Engelsen
Dahai Yan is an associate researcher and Li Li is researcher at China Research Academy of Environment Science. Zheng Peng is a senior engineer, Qiong Ding is a researcher, and Yong Ren and Chen Jiang are engineers at the Foreign Economic Cooperation Office of the Ministry of Environmental Protection, China. Kåre Helge Karstensen is a chief scientist and Christian J. Engelsen is a senior scientist at SINTEF, Norway.
Li Li
Dahai Yan is an associate researcher and Li Li is researcher at China Research Academy of Environment Science. Zheng Peng is a senior engineer, Qiong Ding is a researcher, and Yong Ren and Chen Jiang are engineers at the Foreign Economic Cooperation Office of the Ministry of Environmental Protection, China. Kåre Helge Karstensen is a chief scientist and Christian J. Engelsen is a senior scientist at SINTEF, Norway.
Yong Ren
Dahai Yan is an associate researcher and Li Li is researcher at China Research Academy of Environment Science. Zheng Peng is a senior engineer, Qiong Ding is a researcher, and Yong Ren and Chen Jiang are engineers at the Foreign Economic Cooperation Office of the Ministry of Environmental Protection, China. Kåre Helge Karstensen is a chief scientist and Christian J. Engelsen is a senior scientist at SINTEF, Norway.
Chen Jiang
Dahai Yan is an associate researcher and Li Li is researcher at China Research Academy of Environment Science. Zheng Peng is a senior engineer, Qiong Ding is a researcher, and Yong Ren and Chen Jiang are engineers at the Foreign Economic Cooperation Office of the Ministry of Environmental Protection, China. Kåre Helge Karstensen is a chief scientist and Christian J. Engelsen is a senior scientist at SINTEF, Norway.
References
- 40 CFR 63 Subpart EEE. 2014. http://www.gpo.gov/fdsys/pkg/CFR-2014-title40-vol12/pdf/CFR-2014-title40-vol12-part63-subpartEEE.pdf
- Al-Abed, S.R., G. Jegadeesan, K.G. Scheckel, and T. Tolaymat. 2008. Speciation, characterization, and mobility of As, Se, and Hg in flue gas desulphurization residues. Environ. Sci. Technol. 42:1693–98. doi:10.1021/es702479n
- Chen, J., G.J. Liu, Y. Kang, B. Wu, R.Y. Sun, C.C. Zhou, and D. Wu. 2013a. Atmospheric emissions of F, As, Se, Hg, and Sb from coal-fired power and heat generation in China. Chemosphere 90:1925–32. doi:10.1016/j.chemosphere.2012.10.032
- Chen, L.G., M. Liu, R.F. Fan, S.X. Ma, Z.C. Xu, M.Z. Ren, and Q.S. He. 2013b. Mercury speciation and emission from municipal solid waste incinerators in the Pearl River Delta, South China. Sci. Total Environ. 447:396–402. doi:10.1016/j.scitotenv.2013.01.018
- China Cement Association. 2013, Production data of cement clinker in 2012. China Cement Association. http://www.dcement.com/Article/201301/113202.html
- Conesa, J.A., A. Gálvez, F. Mateos, I. Martín-Gullón, and R. Font. 2008. Organic and inorganic pollutants from cement kiln stack feeding alternative fuels. J. Hazard. Mater. 30:585–92. doi:10.1016/j.jhazmat.2008.01.116
- Eriksen, D., L.A. Tokheim, T.A. Eriksen, J. Meyer, and C. Qvenild. 2000. Assessment of mercury emission at Norcem’s cement kiln by the use of 203Hg-tracer. J. Radioanal. Nuclear Chem. 273:3. doi:10.1007/s10967-007-0940-4
- Guo, Q., and J.O. Eckert, Jr. 1996. Heavy metal outputs from a cement kiln co-fired with hazardous waste fuels. J. Hazard. Mater. 51:47–65. doi:10.1016/S0304-3894(96)01800-6
- Gupta, R.K., D. Majumdar, J.V. Trivedi, and A.D. Bhanarkar. 2012. Particulate matter and elemental emissions from a cement kiln. Fuel Process. Technol. 104:343–51. doi:10.1016/j.fuproc.2012.06.007
- Hewlett, P.C. 1998. Lea’s chemistry of cement and concrete. Oxford, MA: Butterworth-Heinemann.
- Jeon, S.H., Y. Eom, and T.G. Lee. 2008. Photocatalytic oxidation of gas-phase elemental mercury by nanotitanosilicatefibers. Chemosphere 71:969–74. doi:10.1016/j.chemosphere.2007.11.050
- Karstensen, K.H., 2008. Formation, release and control of dioxins in cement kilns. Chemosphere 70:543–60. doi:10.1016/j.chemosphere.2007.06.081
- Lenz, M., and P.N.L. Lens. 2009. The essential toxin: The changing perception of selenium in environmental sciences. Sci. Total Environ. 407(12):3620–33. doi:10.1016/j.scitotenv.2008.07.056
- Ministry of Environmental Protection of China. 2013a. Ministry of Environmental Protection of China, Standard for pollution control on co-processing of solid wastes in cement kiln, GB 30485-2013. Beijing, December. http://www.mep.gov.cn/gkml/hbb/qt/201312/t20131227_265763.htm.
- Ministry of Environmental Protection of China. 2013b. Ministry of Environmental Protection of China, Environmental protection technical specification for co-processing of solid wastes in cement kiln, HJ 662-2013. Beijing, December. http://www.mep.gov.cn/gkml/hbb/qt/201312/t20131227_265763.htm.
- Mlakar, T.J., M. Horvat, T. Vuk, A. Stergarsek, J. Kotnik, J. Tratnik, and V. Fajon. 2010. Mercury species, mass flows and processes in a cement plant. Fuel 89:1936–45. doi:10.1016/j.fuel.2010.01.009
- National Bureau of Statics of China. 2013. http://data.stats.gov.cn/search/keywordlist2?keyword=2013%E5%B9%B4%20%E6%B0%B4%E6%B3%A5%E4%BA%A7%E9%87%8F
- Neundorfer. 2010. Comparison: U.S. and European Cement Kiln Emission Regulations. www.neundorfer.com
- Senior, C.L., A.F. Sarofim, T. Zeng, J.J. Helble, and R. Mamani-Paco. 2000. Gas-phase transformations of Hg in coal-fired power plants. Fuel Process. Technol. 63:197e213. doi:10.1016/S0378-3820(99)00097-1
- Tian H.Z., Y. Wang, Z.G. Xue, K. Cheng, Y.P. Qu, F.H. Chai, and J.M. Hao. 2010. Trend and characteristics of atmospheric emissions of Hg, As, and Se from coal combustion in China, 1980–2007. Atmos. Chem. Phys. 10:11905–19. doi:10.5194/acp-10-11905-2010
- Tian, H.Z., Y. Wang, Z.G. Xue, Y.P. Qu, F.H. Chai, and J.M. Hao. 2011. Atmospheric emissions estimation of Hg, As, and Se from coal-fired power plants in China, 2007. Sci. Total Environ. 409:3078–81. doi:10.1016/j.scitotenv.2011.04.039
- United Nations Environmental Programme. 2008a. The global atmospheric Hg assessment: Sources, emissions and transport. http://www.chem.unep.ch/Hg/Atmospheric_Emissions/Atmospheric_emissions_Hg.htm
- United Nations Environmental Programme. 2008b. Technical background report to the global atmospheric Hg assessment. http://www.unep.org/hazardoussubstances/Hg/HgPublications/Global AtmosphericHgAssessmentSourcesEm/tabid/3618/language/en-US/Default.aspx
- United Nations Environmental Programme. 2013a. Minamata convention on mercury. http://www.mercuryconvention.org
- United Nations Environmental Programme. 2013b. Toolkit for identification and quantification of mercury sources, Reference report and guideline for inventory level 2, Version 1.2. April. Geneva, Switzerland: UNEP Chemicals Branch.
- U.S. Environmental Protection Agency. 1997. Locating and estimating air emissions from sources of mercury and mercury compounds. Report EPA-454/R-97-012, (NTIS PB98-117054). Research Triangle Park, NC: Office of Air Quality Planning and Standards.
- Verein Deutscher Zementwerke e.V. 2001. Trace elements in German standards cements, 2001. Dusseldorf, Germany: VDZ Verein Deutscher Zementwerke e.V.
- Van der Sloot, H.A., A. van Zomeren, R. Stenger, M. Schneider, G. Spanka, E. Stoltenberg-Hansson, and P. Dath. 2008. Environmental Criteria for Cement Based Products, ECRICEM. Executive Summary. Energy Research Centre of the Netherlands (ECN). ECN Report N° ECN-E–08-011. http://www.ecn.nl/docs/library/report/2008/e08011.pdf
- Wang, F.Y., S.X. Wang, L. Zhang, H. Yang, Q.R. Wu, and J.M. Hao. 2014. Mercury enrichment and its effects on atmospheric emissions in cement plants of China. Atmos. Environ. 92:421–28. doi:10.1016/j.atmosenv.2014.04.029
- Won, J.H., and T.G. Lee. 2012. Estimation of total annual mercury emissions from cement manufacturing facilities in Korea. Atmos. Environ. 62:265–71. doi:10.1016/j.atmosenv.2012.08.035