Abstract
Valuable metal materials can be recovered from spent nickel–metal hydride (NiMH) batteries. However, little attention has been paid to the metal compositions of individual components of NiMH batteries, although this is important for the selection of the appropriate recycling process. In this study, NiMH batteries were manually disassembled to identify the components and to characterize the metals in each of these. A preliminary economic analysis was also conducted to evaluate the recovery of valuable metals from spent NiMH batteries using thermal melting versus simple mechanical separation. The results of this study show that metallic components account for more than 60% of battery weight. The contents of Ni, Fe, Co, and rare earth elements (REEs) (i.e., valuable metals of interest for recovery) in a single battery were 17.9%, 15.4%, 4.41%, and 17.3%, respectively. Most of the Fe was in the battery components of the steel cathode collector, cathode cap, and anode metal grid, while Ni (>90%) and Co (>90%) were mainly in the electrode active materials (anode and cathode metal powders). About 1.88 g of REEs (Ce, La, and Y) could be obtained from one spent NiMH battery. The estimated profits from recovering valuable metals from spent NiMH batteries by using thermal melting and mechanical processes are 2,329 and 2,531 USD/ton, respectively, when including a subsidy of 1,710 USD/ton. The findings of this study are very useful for further research related to technical and economic evaluations of the recovery of valuable metals from spent NiMH batteries. Implications: The spent nickel–metal hydride (NiMH) batteries were manually disassembled and their components were identified. The metals account for more than 60% of battery weight, when Ni, Fe, Co, and rare earth elements (REEs) were 17.9%, 15.4%, 4.41%, and 17.3%, respectively, in a single battery. The estimated profits of recovering valuable metals from NiMH batteries by using thermal melting and mechanical processing are 2,329 and 2,531 USD/ton, respectively, when including a subsidy of 1,710 USD/ton. These findings are very useful to develop or select the recovery methods of valuable metals from spent NiMH batteries.
Introduction
Batteries are used to power equipment such as telephones, flashlights, radios, watches, and so on. However, the disposal of spent batteries can lead to the release of mercury, lead, zinc, cadmium, manganese, nickel, and lithium, which can harm both the environment and the health of humans and other animals (Bernardes et al., Citation2004). Only about 13% of spent batteries are recovered in Taiwan, although the consumption of batteries keeps increasing.
The metallic scraps in batteries can be recovered by different recycling processes, such as mineral processing techniques (Tenório and Espinosa, Citation2002) and pyrometallurgical (Ammann, Citation1995; Jordi, Citation1995) or hydrometallugical treatments (Bartolozzi et al., Citation1995; Raghavan et al., Citation2000; Rudnik and Nikiel, Citation2007; Zhang et al., Citation1998). The products of these spent battery recycling processes are metallic alloys or compounds, or solutions containing abundant metal ions (Bernardes et al., Citation2004).
Nickel–metal hydride (NiMH) batteries were developed in 1989 and commercialized in Japan in 1990, and have the advantages of high electrochemical capacity, safety, good environmental compatibility, the ability to function efficiently within a wide temperature range, long lifetimes, and low self-discharge rates (Zhang et al., Citation1999). Before 1992, NiCd batteries accounted for most of the market for portable rechargeable batteries. In 1992, around half of the NiCd batteries in the world were replaced by NiMH batteries, due to the issue of Cd toxicity (Rydh and Svärd, Citation2003), as well as the better performance (e.g., larger energy density and absence of memory effect) of NiMH batteries (Bertuol et al., Citation2006). In the European Union (EU), sales of NiMH batteries increased from <6,000 to ~10,000 tons from 1999 to 2003 (Müller and Friedrich, Citation2006).
shows the cross-sectional profile of an NiMH battery. Nickel oxyhydroxide (NiOOH) is used in both electrodes. The reversible chemical reaction at the cathode is the same as that of the nickel–cadmium cell (NiCd) as shown in eq 1; however, the anode uses a hydrogen-absorbing alloy instead of cadmium, as in eq 2. The “Me” represents the intermetallic compound(s) in the anode of an NiMH cell. Several different compounds have been developed and classified into two main classes. The most general one is AB5, where A is a rare earth element (REE) mixture of neodymium (Nd), lanthanum (La), cerium (Ce), and praseodymium (Pr). B is aluminum (Al), cobalt (Co), manganese (Mn), or nickel (Ni). The other higher capacity group is AB2, where A is titanium (Ti) or vanadium (V), and B is composed of zirconium (Zr) or nickel (N), modified with chromium (Cr), cobalt (Co), iron (Fe), or manganese (Mn). All of the compounds just listed have the same chemical reversibility to form a mixture of metal hydride compounds (Ying et al., Citation2006).
Cathode reversible reaction:
Anode reversible reaction:
Nowadays, more attention is being paid to the recovery of battery wastes due to the containing valuable metals (particularly rare earth elements (REEs) (Tanong et al., Citation2014). Bertuol et al. (Citation2006) investigated the chemical composition of spent NiMH batteries and metal recovery through mechanical processing, and found that while magnetic separation is an efficient way to recover nickel alloy, there is still a problem with regard to cadmium contamination. Hydrometallurgical methods can also be used to recover metals from batteries, and acid leaching may be used to extract metals from spent NiMH and NiCd batteries (Pietrelli et al., Citation2005). Li et al. (Citation2009) developed a hydrometallurgical procedure that achieved >98% efficiency for the recovery of Ni, Co, and REEs from spent NiMH batteries, when Innocenzi (Citation2012) approached >99% of the same metal composition by a sequential sulfuric acid leaching and selective precipitations. The two cross-flow liquid–liquid extraction steps were further reported to be adequate to extract 100% of Zn and about 95% of Mn, while the residual Ni was about 80% of its initial content (Innocenzi and Vegliò, Citation2012a, 2012b). Electrochemical deposition after solvent extraction was also tested for the recovery of Ni and Co from NiMH batteries (Tzanetakis and Scott, Citation2004a, Citation2004b). Ni-based alloy accounts for a significant fraction of a single NiMH battery (Tenório and Espinosa, Citation2002). A lower and safer thermal treatment for recovering Ni, La, and Ce has been reported (Shin et al., Citation2015). However, the compositions of individual components of NiMH batteries, which are important for selecting the appropriate recovery process, have not yet been reported in detail. Nevertheless, there are still a few studies focusing on the beneficiation of detail NiMH recycling, with many research studies on lithium–ion batteries (Javorsky da Costa et al., Citation2015, Zeng et al., Citation2014). In this study, cylindrical NiMH batteries were manually disassembled to identify the individual components, and the metal compositions of each of these were also examined. The values of the metals in the batteries were estimated and then considered in relation to two metal separation processes (thermal melting and mechanical processing) in order to carry out a preliminary economic evaluation of recovery of such metal scraps.
Materials and methods
NiMH batteries (with the specifications of 1.2 V, AAA, and 900 mAh) were purchased from a company in Taiwan. The NiMH batteries were characterized in a laboratory using the serial steps of discharging the electricity (checked using a multimeter), disassembling the NiMH batteries, identifying/weighing each structural component, assigning numbers, then carrying out digestion, and instrumental analysis. shows the disassembled battery components.
Figure 2. (a) Appearance of an NiMH battery. (b) Top washer. (c) Cylindrical case. (d) Insulation tube. (e) Cathode cap. (f) Steel cathode collector. (g) Gasket. (h) Insulating bottom terminal. (i) Robber disk (sealing plate). (j) Anode. (k) Paper separator. (l) Metal powder (anode). (m) Metal powder (cathode).
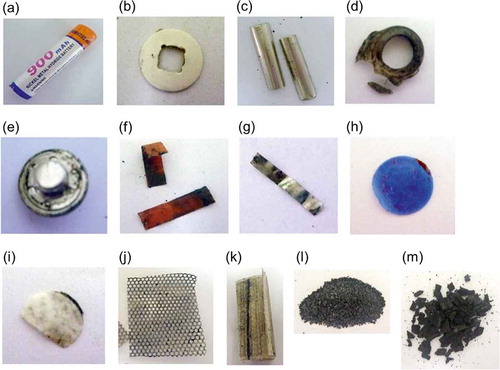
Digestion of battery samples
The digestion of battery component samples followed Method R353.00C, as regulated by the Taiwan Environmental Protection Administration (TEPA). For battery digestion, each battery component sample (0.3 g) was held in a flask with a watch glass cover and mixed with 200 mL nitric acid, isothermally heated <100°C for 20 min without boiling, and then statically cooled down. After the addition of 10 mL nitric acid, the cooled sample was again isothermally heated <100°C for another 10 min. The cooled sample along with the flask and clock glass were then washed with deionized water, and the liquid sample with residuals was filtered. The filtrate was then diluted with deionized water to 50 mL for instrumental analysis.
Instrumental analysis
The digested samples were analyzed using an atomic absorption spectrophotometer (GBC SENSAA) for 12 metal elements (Al, Cd, Co, Cr, Cu, Fe, K, Mg, Mn, Ni, Pb, and Zn). The As, Ag, Ca, Ba, Hg, Na, Sb, Se, Ti, and V were analyzed with inductively coupled plasma–mass spectrometry (ICP-MS; Agilent 7500a), while the REEs (Ce, La, and Y) were measured based on x-ray fluorescence (XRF; Spectro XEPOS).
Results and discussion
Characterization of the NiMH spent batteries
The battery components were identified and weighed, with the results listed in . The average weight of the same type of battery from the same company was 10.9 g (n = 6). The NiMH batteries were mainly composed of metallic parts, including a steel cathode collector, cathode cap, metal connector, anode metal grid, and anode and cathode metal powders, accounting for more than 90% of the total weight. The weight percentages (based on the total weight) of the anode and cathode metal powders were 29.3% and 33.2%, respectively, while that of the steel cathode collector was 20.7%. Plastic and paper parts were only less than 10% weight of the battery.
Table 1. Mass ratios (%) of the components in a spent NiMH battery (n = 6).
The NiMH battery components, classified into plastic, paper, and metal categories, are shown in . The cylindrical NiMH batteries tested in this study had noticeably more metal and less plastic (92.9% and 2.58%, respectively) than seen with the cell phone NiMH batteries examined by Tenório and Espinosa (Citation2002) (with metal and plastic at 37% and 22%, respectively), and thus the cylindrical NiMH batteries are better for metal recovery than cell phone batteries.
The 27 metal elements analyzed in this study contributed more than 60% of the battery weight. Among the tested metals, Ni, Fe, and La accounted for the highest content (17.9%, 15.4%, and 12.1%, respectively), followed by Ce, Co, K, Na, Zn, and Mn (5.16%, 4.41%, 1.74%, 1.02%, 0.795%, and 0.726%, respectively), as shown in .
Table 2. Metal contents in a spent NiMH battery.
In other words, the recovered weights of Ni, Fe, La, Ce, Co, Zn, and Mn (metals of interest) from one NiMH battery reached about 1.95, 1.68, 1.32, 0.562, 0.481, 0.0866, and 0.0791 g, respectively. The leached metal ions, such as Ni and Co species, can be further recovered using electrochemical methods for the co-deposition of Ni and Co (Lupi and Pilone, Citation2002). Ni–Co co-deposition may reduce the operational procedures needed for NiMH battery recycling, and produce an alloy with applications in several industrial sectors. The contents of the other tested metals, including toxic ones (i.e., As, Cr, Hg, and Pb), were much lower than those of metals of interest for recovery. The content of REEs in the batteries was 17.3%, corresponding to the recovered weight of 1.88 g. Among the REEs, the highest contents were for La and Ce (12.1% and 5.16%, respectively).
Metal contents of individual components
presents metal contents of each battery component, and it can be seen that there is an abundance of valuable metals in the NiMH batteries. In the steel cathode collector, the Fe and Ni contents were 42.2% and 1.91%, respectively, whereas those in the cathode cap were 93.2% and 8.62%, respectively. However, the metal connector was mainly made of Ni (84.1%) and the other elements were all at low levels. Fe and Ni were also abundant in the anode metal grid (44.8% and 10.1%, respectively), which had notable levels of Co and Mn (0.850% and 0.298%, respectively).
Table 3. Contents in μg/g (RSD%) of metals in individual components of NiMH batteries (n = 3).
In contrast, the contents of Fe were low but those of Ni were high in the anode and cathode metal powders. Furthermore, a high content of REEs (41.2% La and 17.6% Ce) was found in the anode metal powder. The metal contents in the nonmetal components (plastic sleeve, plastic grommet, seal, insulator, and separator) of the tested NiMH batteries were very low, while the amounts of toxic metals (As, Cr, Hg, and Pb) were very lower in all components. Nevertheless, the Cr contents were relatively high in the cathode cap, orange cathode seal, anode blue insulator, and cathode cotton insulator than in the other components.
shows the contributions of individual components to the Fe, Ni, Co, and REEs (Ce, La, and Y) that are of interest for recovery, based on the data in . Approximately 57% of Fe was contributed by the steel cathode collector. Moreover, the cathode cap and steel cathode collector together contributed around 87% of the total Fe in an NiMH battery, indicating that Fe was mostly used in the outside parts of the battery, although the anode metal grid still contributed 12.9% to the total Fe. The total Fe content in the other components amounted to less than 0.4% of the whole. Ni and Co were found to concentrate in the anode and cathode metal powders (more than 90%); the Ni was mainly in the cathode metal powder, while the Co was mainly in the anode metal powder. Like Co, most of REEs were contributed from the anode metal powder (99.6%), and ~1.88 g REEs could be obtained from one spent NiMH battery. Since about 90% of metals of interest were in the anode and cathode metal powders, these two components are more important than the others for recovery of valuable metals (mainly Co, Ni, and REEs).
Comparison of chemical compositions of different batteries
lists the chemical compositions of the cylindrical NiMH battery investigated in this study and those of different types of German batteries reported in the literature (Müller and Friedrich, Citation2006). As presented in , Ni and Fe were the main components in all the compared batteries. The mass percentages of Ni in the German batteries were in the range 29–42%, which is noticeably higher than that of the cylindrical Taiwanese NiMH battery examined in the current work (about 18.4%). Higher percentages of plastic and lower percentages of Fe were found for the German prismatic cell than for the other batteries, and thus more plastic material is used in the fabrication of such batteries. The content of Co ranged between 2% and 4% for all the German batteries, compared to 4.41% for the cylindrical Taiwanese NiMH battery. The percentages (6–10%) of REEs (Ce, La, Nd, and Pr) found in the German batteries were lower than that found for the Taiwanese cylindrical cell (17.3%) (Ce, La, and Y).
Table 4. Compositions (%) of different type batteries.
shows the electrode active metal compositions of the cylindrical NiMH battery investigated in this study and those of different batteries reported in previous works (AB5 and AB2 batteries [Pietrelli et al., Citation2005] and cell phone NiMH batteries [Bertuol et al., Citation2006, Citation2009]). It is interesting to note that Co, Ni, Mn, and REEs are the common electrode active materials for the cylindrical NiMH, AB5, AB2, and cell phone NiMH batteries. The Ni content was higher in the anode than in the cathode for the cylindrical NiMH battery examined in this work, but an opposite trend was observed for the AB5, AB2, and cell phone batteries. In addition, the anode Ni content of the cylindrical NiMH battery was greater than those seen in the AB5, AB2, and cell phone NiMH batteries, while the cathode Ni content of the cylindrical NiMH battery was lower than that seen in the cell phone NiMH batteries, AB5, and AB2. Co was the second most abundant electrode metal element in the cylindrical and cell phone NiMH batteries. The amount of rare earth elements was higher in the investigated cylindrical NiMH battery (58.8%) than in the cell phone NiMH batteries (43.1–53.4%) and AB5 battery (16.4%), and was comparable with that in monazite (Pietrelli et al., Citation2005). The Zr content found in this study was lower than that in the anode of AB2 (39%); the Cd content was smaller than that in the electrodes of the cell phone NiMH batteries (~10–12%) (Bertuol et al. (Citation2006)). The Ti (0.186%) and Cr (0.0115%) contents were both lower than those in the AB2.
Table 5. Anode/cathode active compositions (%) of NiMH batteries investigated in this and earlier studies.
Economic evaluation of recovering valuable metals from NiMH batteries
To evaluate the economic feasibility of recovering valuable metals from NiMH batteries, we compare the costs of two recovery processes (thermal melting and mechanical processes), as shown in and . In general, whole batteries are melted in the thermal melting treatment to obtain slag and ingots after cooling. In the thermal melting process, a high portion of the metals can be transformed into ingots due to their specific gravities (Kuo et al., Citation2009). The corresponding amounts of ingot and slag obtained from the thermal melting of spent NiMH batteries were based on a preliminary experiment of the thermal melting of spent NiMH batteries. Ni, Fe, and Co were the major target metals for recovery, because the NiMH batteries used in this study had high contents of these. shows the preliminary estimation of the costs of the input and output materials for the thermal melting of NiMH batteries according to the preliminary spent NiMH thermal melting experiment and our previous study (Kuo et al., Citation2009). According to the recovery and treatment rates of dry cells reported by the Taiwan Environmental Protection Administration (TEPA) (Taiwan Environmental Protection Administration, Citation2009), the company treating the batteries has to pay 690 U.S. dollars (USD) per ton of NiMH batteries to the company that collects the batteries, and may receive 1,710 USD of subsidy from the TEPA, assuming that its operating capacity is 5,000 tons of spent NiMH batteries/year. In the process of thermal melting, the amount of additives (mixed with spent NiMH batteries) was 66.7% by weight, and the amounts of ingot and slag produced were 42.7% and 21.4% of the input battery weight, respectively. The prices of metal and ash were calculated according to the scrap prices of metal exchange markets. The price of Zn ingot was 2,000 USD/ton, when it was estimated by 60% of the Zn scrap price (1,200 USD/ton). If the content of Zn was 10% in the fly ash, then the estimated price of fly ash was 120 USD/ton. The ingot had 44.8% Ni, 31.8% Fe, 10.6% La, 6.01% Co, and 4.54% Ce, and the prices of Ni, Fe, La, Co, and Ce scraps were 14,000, 263, 4,230, 14,300, and 4,730 USD/ton, respectively. Therefore, the estimated price of ingot was ~7,880 USD/ton. The price of slag (which can be used as a pavement subbase material), was estimated to be 30 USD/ton. The total income from selling slag, ingot, and ash together was 3,365 USD, and the input costs (including the spent NiMH battery and 40% w/w additive) was about 725 USD for 1 ton of NiMH batteries. Accordingly, the total outcomes were 3,259 and 2,746 USD/ton-battery for the years 1 and 2–9, respectively, and the incomes were both 5,075 USD/ton-battery for the thermal melting process (). These results indicate that the profit from the metal recovery of a spent NiMH treatment plant was roughly 2,329 USD/ton-battery after considering the cost of construction and the depreciation of machines and buildings.
Table 6. Preliminary economic evaluation of metal recovery from thermal melting of NiMH batteries.
Although Fe and Ni, the most abundant elements of interest in the NiMH batteries, are distributed in different battery components, >90% of Fe was in the steel cathode collector, cathode cap, and anode metal grid components, which together accounted for about 30.1% of battery weight. More than 90% of Ni was in anode and cathode powders that were responsible for 62.5% of battery weight. The contribution of the other battery components to battery weight was 7.4%. Since the steel cathode collector, cathode cap, and anode metal grid all have better prices than the anode and cathode powders, it is advisable to separate most of the Fe and Ni from the other metals using simple size classification following the operation of a hammer mill and magnetic separation. In this study, hammer and knife mills were used to break the thin steel collectors and the circuits of batteries, while magnetic separation was applied to separate the metallic and nonmetallic components. Note that the size classification collection adopted in this simple mechanical process was for the purpose of Fe- and Ni-rich component separation.
presents the details of the economic evaluation of metal recovery from NiMH batteries based on a mechanical operating process that consists of a series of treatment units, such as hammer milling, magnetic separation, knife milling, magnetic separation, and size separation (Tenorio and Espinosa, Citation2002). Approximately 0.301 ton Fe-rich and 0.625 ton Ni-rich scraps could be recovered from 1 ton of NiMH batteries. It is assumed that the operation capacity, startup costs, staff salaries, shipping expenses, land and construct lease costs, and taxes are the same as the corresponding costs in the thermal melting process. The total weight of Fe-rich components in one ton of NiMH batteries was 301 kg, suggesting a total amount of 153 kg of Fe (~51%). A profit of 270 USD was achieved by selling the Fe scrap obtained from size classification collection. The price of metallic powder scraps was at least 5,170 USD/ton-scrap. The values of Ni and Co in the 625 kg metallic powder scraps (that contains 166 and 43.2 kg of Ni and Co, respectively) were 14,330 and 19,841 USD, respectively. The costs of waste treatment were based on incineration of the materials that could not be recycled. When the 1,710 USD/ton subsidy and the price of NiMH battery collection (690 USD/ton) were included, the total income and outcome were 4,559 and 2,027 USD, respectively, suggesting a profit of ~2,531 USD. According to Tenorio and Espinosa (Citation2002), the estimated overall yield was 86% when considering the loss of recovery operation. Further knife milling and magnetic separation are necessary to improve the separation efficiency of the metals of interest. Although these scraps can be sold as products in metal markets, the valuable metals in them can be further separated and recovered by leaching and subsequent electro-deposition.
Table 7. Preliminary economic evaluation of metal recovery from NiMH batteries using a simple mechanical process.
Summary
Metals in the NiMH battery were components of the steel cathode collector, anode metal powder, and cathode metal powder that, on average, accounted for 20.7%, 29.3%, and 33.2% of total battery weight, respectively.
Among the metals of interest for recovery, the highest contents were found for Ni, Fe, and La (17.9%, 15.4%, and 12.1%, respectively), followed by Ce, Co, K, Na, Zn, and Mn (5.16%, 4.41%, 1.74%, 1.02%, 0.795%, and 0.726%, respectively).
The cathode cap and steel cathode collector contributed ~87% of total Fe in a single NiMH battery, whereas Ni and Co (the main electrode active materials of NiMH batteries) were concentrated in the electrode metal powders (>90%).
The Ni was located chiefly in the cathode metal powders, while the Co was mainly in the anode metal powders.
Most of the rare earth elements (REEs) were in the anode metal powder (99.6%), and ~1.88 g REEs could be obtained from one spent NiMH battery.
The profits that can be obtained by recovering valuable metals from each ton of spent NiMH batteries through thermal melting and mechanical processes are roughly 619 and 821 USD, respectively.
In the case of TEPA subsidy (1,710 USD) included, the profits are much higher (approximately 2,329 and 2,531 USD, respectively).
This study provides very useful information for further research associated with technical and economic evaluations of recovering valuable metals from spent NiMH batteries.
ORCID
Kuo-Lin Huang
http://orcid.org/0000-0002-4069-8234Yi-Ming Kuo
http://orcid.org/0000-0002-5711-9884Additional information
Notes on contributors
Sheng-Lun Lin
Sheng-Lun Lin is an assistant professor in the Department of Civil Engineering and Geomatics, Super Micro Mass Research and Technology Center, and Center for General Education, Cheng Shiu University, Kaohsiung City, Taiwan.
Kuo-Lin Huang
Kuo-Lin Huang is a professor in the Department of Environmental Engineering and Science, National Pingtung University of Science and Technology, Pingtung, Taiwan.
I-Ching Wang
I-Ching Wang is a postdoctoral researcher in the Department of Safety Health and Environmental Engineering, Chung Hwa University of Medical Technology, Tainan City, Taiwan.
I-Cheng Chou
I-Cheng Chou is a researcher in the Department of Environmental Resource, Refining & Manufacturing Research Institute CPC Corporation, Chiayi City, Taiwan.
Yi-Ming Kuo
Yi-Ming Kuo is a professor in the Department of Safety Health and Environmental Engineering, Chung Hwa University of Medical Technology, Tainan City, Taiwan.
Chung-Hsien Hung
Chung-Hsien Hung is a research associate professor in Super Micro Mass Research and Technology Center and Center for General Education, Cheng Shiu University, Kaohsiung City, Taiwan.
Chitsan Lin
Chitsan Lin is a professor in the Department of Marine Environmental Engineering, National Kaohsiung Marine University, Kaohsiung City, Taiwan.
References
- Ammann, P. 1995. Economic considerations of battery recycling based on the Recytec process. J. Power Sources 57:41–44. doi:10.1016/0378-7753(95)02237-6
- Bartolozzi, M., G. Braccini, S. Bonvini, P.F. Marconi. 1995. Hydrometallurgical recovery process for nickel-cadmium spent batteries. J. Power Sources 55:247–250. doi:10.1016/0378-7753(95)02180-O
- Bernardes, A.M., D.C.R. Espinosa, J.A.S. Tenorio. 2004. Recycling of batteries: a review of current processes and technologies. J. Power Sources 130:291–8. doi:10.1016/j.jpowsour.2003.12.026
- Bertuol, D.A., A.M. Bernardes, J.A.S. Tenório. 2006. Spent NiMH batteries: Characterization and metal recovery through mechanical processing. J. Power Sources 160:1465–70. doi:10.1016/j.jpowsour.2006.02.091
- Bertuol, D.A., A.M. Bernardes, J.A.S. Tenório. 2009. Spent NiMH batteries–The role of selective precipitation in the recovery of valuable metals. J. Power Sources 193:914–23. doi:10.1016/j.jpowsour.2009.05.014
- Innocenzi, V., and F. Vegliò, 2012. Recovery of rare earths and base metals from spent nickel-metal hydride batteries by sequential sulphuric acid leaching and selective precipitations. J. Power Sources 211:184–91. doi:10.1016/j.jpowsour.2012.03.064
- Innocenzi, V., and F. Vegliò, 2012. Separation of manganese, zinc and nickel from leaching solution of nickel-metal hydride spent batteries by solvent extraction. Hydrometallurgy 129-130:50–58. doi:10.1016/j.hydromet.2012.08.003
- Javorsky da Costa, A., J. F. Matos, A. M. Bernardes, 2015. Beneficiation of cobalt, copper and aluminum from wasted lithium-ion batteries by mechanical processing. Inter. J. Miner. Process 145:77–82. doi:10.1016/j.minpro.2015.06.015
- Jordi, H. 1995. A financing system for battery recycling in Switzerland. J. Power Sources 57:51–3. doi:10.1016/0378-7753(95)02240-6
- Kuo, Y.M., J.E. Chang, C.H. Jin, J.Y. Lin, G.P. Chang-Chien. 2009. Vitrification for reclaiming spent alkaline batteries. Waste Manage. 29:2132–9. doi:10.1016/j.wasman.2009.01.008
- Li, L., S. Xu, Z. Ju, F. Wu. 2009. Recovery of Ni, Co and rare earths from spent Ni-metal hydride batteries and preparation of spherical Ni(OH)2. Hydrometallurgy 100:41–6. doi:10.1016/j.hydromet.2009.09.012
- Lupi, C. and D. Pilone. 2002. Ni-MH spent batteries: a raw material to produce Ni-Co alloys. Waste Manage. 22:871–4. doi:10.1016/S0956-053X(02)00074-0
- Müller, T., and B. Friedrich. 2006. Development of a recycling process for nickel-metal hydride batteries. J. Power Sources 158:1498–509. doi:10.1016/j.jpowsour.2005.10.046
- Pietrelli, L., B. Bellomo, D. Fontana, M. Montereali. 2005. Characterization and leaching of NiCd and NiMH spent batteries for the recovery of metals. Waste Manage. 25:221–6. doi:10.1016/j.wasman.2004.12.013
- Raghavan, R., P.K. Mohanan, S.R. Swarnkar. 2000. Hydrometallurgical processing of lead-bearing materials for the recovery of lead and silver as lead concentrate and lead metal. Hydrometallurgy 58:103–16. doi:10.1016/S0304-386X(00)00108-0
- Rudnik, E. and M. Nikiel. 2007. Hydrometallurgical recovery of cadmium and nickel from spent Ni-Cd batteries. Hydrometallurgy 89:61–71. doi:10.1016/j.hydromet.2007.05.006
- Rydh, C.J. and B. Svärd. 2003. Impact on global metal flows arising from the use of portable rechargeable batteries. Sci. Total Environ. 302:167–84. doi:10.1016/S0048-9697(02)00293-0
- Shin, S. M., D. J. Shin, G. J. Jung, Y.H. Kim, J. P. Wang, 2015. Recovery of electrodic powder from spent nickel-metal hydride batteries (NiMH). Arch. Metall. Mater. 40(2): 1139–43. doi:10.1515/amm-2015-0085
- Taiwan Environmental Protection Administration. 2009. Waste battery recycling rate of clearance and disposal fees. Ed. Taiwan Environmental Protection Administration.
- Tanong, K., J.-F. Blais, G. M. Mercier. 2014. Recycling technologies for battery waste. Recent Pat. Engine. 8(1): 13-23(11). doi:10.2174/1872212108666140204004041
- Tenório, J.A.S. and D.C.R. Espinosa. 2002. Recovery of Ni-based alloys from spent NiMH batteries. J. Power Sources 108:70–3. doi:10.1016/S0378-7753(02)00007-1
- Tzanetakis, N. and K. Scott. 2004a. Recycling of nickel-metal hydride batteries. I: Dissolution and solvent extraction of metals. J. Chem. Technol. Biotechnol. 79:919–26. doi:10.1002/jctb.1081
- Tzanetakis, N. and K. Scott. 2004b. Recycling of nickel-metal hydride batteries. II: Electrochemical deposition of cobalt and nickel. J. Chem. Technol. Biotechnol. 79:927–34. doi:10.1002/jctb.1082
- Ying, T.-K., X.-P. Gao, W.-K. Hu, F. Wu, D. Noréus. 2006. Studies on rechargeable NiMH batteries. Int. J. Hydrogen Energy 31(4):525–30. doi:10.1016/j.ijhydene.2005.04.018
- Zeng, X., J. Li, N. Singh. 2014. Recycling of spent lithium-ion battery: A critical review. Crit. Rev. Environ. Sci. 44(10):1129–65. doi:10.1080/10643389.2013.763578
- Zhang, P., T. Yokoyama, O. Itabashi, T.M. Suzuki, K. Inoue. 1998. Hydrometallurgical process for recovery of metal values from spent lithium-ion secondary batteries. Hydrometallurgy 47:259–71. doi:10.1016/S0304-386X(97)00050-9
- Zhang, P., T. Yokoyama, O. Itabashi, Y. Wakui, T.M. Suzuki, K. Inoue. 1999. Recovery of metal values from spent nickel-metal hydride rechargeable batteries. J. Power Sources 77:116–22. doi:10.1016/S0378-7753(98)00182-7