ABSTRACT
An activated carbon commercially available named HGR, produced by Calgon-Carbon Group, was used to adsorbe metallic mercury. The work is part of a wider research activity by the same group focused on the removal of metallic and divalent mercury from combustion flue gas. With respect to previously published papers, this one is aimed at studying in depth thermodynamic equilibria of metallic mercury adsorption onto a commercial activated carbon. The innovativeness lies in the wider operative conditions explored (temperature and mercury concentrations) and in the evaluation of kinetic and thermodynamic data for a commercially available adsorbing material. In detail, experimental runs were carried out on a laboratory-scale plant, in which Hg° vapors were supplied in a nitrogen gas stream at different temperature and mercury concentration. The gas phase was flowed through a fixed bed of adsorbent material. Adsorbate loading curves for different Hg° concentrations together with adsorption isotherms were achieved as a function of temperature (120, 150, 200°C) and Hg° concentrations (1.0−7.0 mg/m3). Experimental runs demonstrated satisfying results of the adsorption process, while Langmuir parameters were evaluated with gas–solid equilibrium data. Especially, they confirmed that adsorption capacity is a favored process in case of lower temperature and they showed that the adsorption heat was –20 kJ/mol. Furthermore, a numerical integration of differential equations that model the adsorption process was proposed. Scanning electron microscopy (SEM) investigation was an useful tool to investigate about fresh and saturated carbon areas. The comparison between them allowed identification of surface sites where mercury is adsorbed; these spots correspond to carbon areas where sulfur concentration is greater.
Implications: Mercury compounds can cause severe harm to human health and to the ecosystem. There are a lot of sources that emit mercury species to the atmosphere; the main ones are exhaust gases from coal combustion and municipal solid waste incineration. Furthermore, certain CO2 capture processes, particularly oxyfuel combustion in a pulverized fuel coal-fired power station, produce a raw CO2 product containing several contaminants, mainly water vapor, oxygen, and nitrogen but also mercury, that have to be almost completely removed; otherwise these would represent a strong drawback to the success of the process.
Introduction
The adverse effects of mercury on human health are a well-known problem (Nordberg et al., Citation2007), as mercury is a persistent toxic pollutant that accumulates very efficiently in aquatic food (Pavlish, Citation2009). For this reason, in 2006 the European Commission established strict mercury concentration limits in some aquatic species (European Commission, Citation2006) reserved to human consumption. Mercury emissions increase over the time due to natural and anthropogenic activities. The average mercury emissions from coal combustion plants in China were estimated to be about 3.0% on an annual basis (Jiang et al., Citation2006; Wu et al., Citation2006). Moreover, with about 500–800 t of anthropogenic mercury emissions, China contributes with 25% to 40% of global mercury emissions (Wang et al., Citation2014). U.S. emissions make no exception, with approximately 50 tons of mercury being released into the atmosphere annually from coal-fired power plants, contributing nearly to one-third of the U.S. man-made mercury emissions (Pacyna et al., Citation2010).
Among the anthropogenic sources, the coal-fired utility boilers (Uddin et al., Citation2008; Granite et al., Citation2000), the combustion of municipal solid wastes (MSW) (Serre and Silcox, Citation2000; Jurng et al., Citation2002), and the cement production processes (Zheng et al., Citation2012a; Zheng et al., Citation2012b; Prisciandaro et al., Citation2003) are the main sources of mercury emissions. According to Pacyna et al. (Citation2006) and Takaoka et al. (Citation2011), mercury emissions in MSW incinerations range from 200 to 1000 μg Hg/N-m3, while they vary between 5 and 20 μg Hg/N-m3 in coal combustion plants (Zheng et al., Citation2012a). Mercury emissions from cement and mineral production are the second largest anthropogenic sources, with numeric values close to those found in coal-fired boilers.
For MSW Hg in flue gas interacts and reacts with other species, with complex mechanisms. Essentially in these plants mercury can be released in three different forms: elemental (Hg°), oxidized (Hg2+), and particulate–bound (Hgp) mercury. Temperatures are higher inside the combustion chamber of MSW incinerators, so thermodynamic equilibrium, which establishes in these conditions, promotes the formation of elemental mercury (Hg°), also due to the reducing properties of SO2. When flue gas escapes from the combustion chamber, it passes through cold zones of the incineration plant, where gas temperature decreases. There Hg° converts into bivalent mercury (Hg2+) due to the oxidation processes, which cause the formation of HgCl2, in the presence of HCl (Heidel et al., Citation2014; Karatza et al., Citation1996b).
Hgp can be efficiently removed by the existing particulate control technologies (i.e., electrostatic precipitator or baghouse; Shigeo et al., Citation2006; Chang John and Ghorishi, Citation2003), but an ad hoc system has to be developed to reduce mercury emissions in the vapor phase: Hg° or Hg2+.
Many authors have studied Hg° or Hg2+ capture by means of sorbent injection (Pavlish et al., Citation2003; Yang et al., Citation2007; Karatza et al., Citation1998; Karatza et al. Citation1996c; Lancia et al., Citation1996). This is a promising technology to remove both elemental and oxidized mercury (Bustard et al., Citation2004). The sorbent is injected downstream of the combustion chamber and the heat exchanger, but upstream of the particulate control devices—an electrostatic precipitator (ESP) and a fabric filter (FF). The injected sorbents adsorb mercury from the flue gas and then they are captured along with fly ash by the ESP or FF (Zhong et al., Citation2014; Scala et al., Citation2008). When a fabric filter is used, the mercury adsorption is more effective; the capture will continue over the cake covering the filter, and a lower amount of sorbent is required. The main drawbacks of this solution are the sorbent costs, the high amount of sorbent required, the disposal of the exhaust sorbent mixed with fly ash, the excessive loading of particulate to the baghouse filter, and eventually the lower capture efficiency of Hg° with respect to Hg2+.
The capture of elemental mercury is still an open problem and a lot of applied research is being carried out to develop a reliable and cost-effective process. The research activities on this topic may be classified into two groups. The first focuses on testing new adsorbing materials (Zhong et al., Citation2014; Karatza et al., Citation2011; Ie et al., Citation2012; Skodras et al., Citation2007; Hu et al., Citation2009; Lee et al., Citation2009; Almquist et al., Citation2013), with a higher efficiency in capturing the elemental mercury, and on the comprehension of the chemical phenomena (Karatza et al., Citation2013; Li et al., Citation2002; Li et al., Citation2003) occurring in the gas phase where other species (e.g. O2, NO, SO2, H2O, HCl) are simultaneously present. The second group focuses on the direct (Scala et al., Citation2011; Li et al., Citation2009) or catalytic (Eswaran and Stenger, Citation2005; Lee et al., Citation2008) oxidation of elemental mercury and the successive capture of the oxidized mercury.
This paper, which belongs to the first group, reports a study of the thermodynamic equilibria involved in elemental mercury adsorption onto activated carbon. The aim is to experimentally investigate the mechanisms involved in Hg° adsorption onto a commercial HGR activated carbon, by using a lab-scale apparatus, in which a fixed bed is used to adsorb Hg° vapors in a nitrogen stream. The temperatures and Hg° concentrations investigated are those typical of baghouse conditions, in which flue gas penetrates a filter cake (i.e., a fixed bed) of fly ash and sorbent. To study the thermodynamic equilibria in depth, a wide range of values of Hg° concentration in the inlet stream to the bed is examined, with temperature values that span from 120 to 200°C. In these conditions the adsorbate loading curves and the adsorption isotherms were obtained. The fresh carbon and the carbon after adsorption process were observed with scanning electron microscopy (SEM), to locate the sites where Hg° is particularly adsorbed. Furthermore, a model based on the Langmuir isotherm is proposed: the Langmuir parameters were used to evaluate the heat of adsorption and to hypothesize a dependence of the equilibrium constant on the temperature of the Arrhenius type. Finally, a comparison between the adsorption isotherms achieved in this work with those obtained using Darco G60 as solid sorbents (Karatza et al., Citation2011) is performed.
Experimental
reports a sketch of experimental device used for adsorption runs. In this apparatus (Karatza et al., Citation2011; Karatza et al., Citation1996a; Karatza et al., Citation2000), the gas stream at the required temperature and Hg° concentration is produced, and the capture of mercury vapors, on a fixed bed of adsorbent material, is performed. The gas stream is obtained by evaporating liquid mercury contained in a thermostatted glass saturator into a stream of pure nitrogen. The saturator is made of a horizontally placed string of 10 empty glass spheres with 30 mm ID, connected by short and narrow glass tubes (about 1 mm ID, 5 mm in length), into which about 350 g of liquid mercury (reagent-grade Hg° from BDH Inc., Canada) was deposited. This device allows both a relatively large gas–liquid contact area (over the spheres) and a good mixing of the gas (in the tubes). The mass flow rate of nitrogen into the saturator is kept constant by a hot wire flow rate controller, and the Hg° concentration in the gas stream fed to the reactor is controlled by varying the temperature of the saturator and by diluting the saturated stream in the junction with a stream of pure nitrogen, the flow rate of which is controlled by another hot wire flow rate controller. The diluted stream is fed to a glass reactor containing sorbent. The reactor is 35 mm ID and 60 mm high, and was kept in a thermostatted oven equipped with a PID temperature controller. The adsorbing bed is made of 0.015 g of adsorbing particles mixed with 3.0 g of 100-µm glass beads as inert additive, and its length is 4 mm. This arrangement is chosen with the aim of avoiding channeling while keeping a small reactive surface. Furthermore, to avoid losses of powder in the gas stream, a downward flow is used in the reactor.
The reactor is filled up with activated carbon, of commercial kind (HGR by Calgon-Carbon Corp.), which has the function to adsorb mercury onto its surface. Technical features of the carbon matter used are 592 kg/m3 bulk density, 4.5 μm solid particles average diameter, 628 m2/g BET surface area, and sulfur content in the range of 8−15% by weight.
Experimental runs were carried out with Hg° concentration (c0) ranging from 1 to 7 mg/m3 and bed temperature (T) varying from 120 to 200°C. The gas superficial velocity was 7.52 × 10−2 m/s, according to the flow rate of the gas phase, which was fixed at 7.22 × 10−5 m3/s.
The Hg° concentration in the outlet gas stream from the reactor was determined as a function of time, by using the mercury continuous analyzer MONITOR 2000 by Seefelder Messtechnik (Germany). After each run the mercury on the bed material was measured by leaching the solids with aqua regia (HNO3 + 3HCl) and then analyzing the solution by means of cold vapor atomic absorption (CVAA; Quantitech Ltd., England), using NaBH4 as reducing agent. A difference not larger than 8% was found in the mercury material balance (Karatza et al., Citation2011). In another work (Karatza et al., Citation2000) details about micrograph investigations were reported.
Results
shows adsorbate loading curves as a function of time for three different temperatures, 120, 150, and 200°C. For each temperature investigated, three different concentrations of Hg° in the gas entering the reactor are examined. Here the saturation conditions were reached in about 1 hour, but, broadly, this time depends on the experimental conditions.
Figure 2. Adsorbate loading curves as a function of time at 120, 150, and 200°C and for different Hg° concentrations in the gas fed to the reactor. □ c0 = 1.7 mg/m3, ◊ c0 = 3.5 mg/m3, ◊ c0 = 6.1 mg/m3.
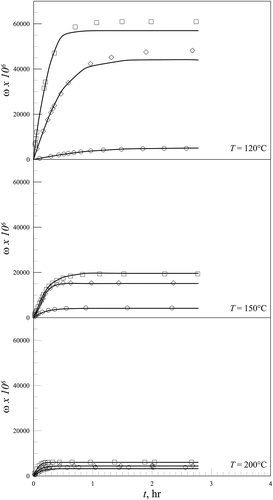
When thermodynamic equilibrium is reached, the adsorbate loading represents the amount of mercury adsorbed on the solid in saturation conditions (ω*). This value, achieved for different Hg° concentrations in the gas fed to the reactor, permitted to draw adsorption isotherms. They are shown in , where the dependence on temperature values investigated was also detected. Isotherm curve behavior strengthens the nature of the process under investigation; adsorption is an exothermic one, because when temperature values are lower, adsorption capacity increases.
SEM investigations on fresh samples of HGR carbon allowed investigation of their surface microstructure and chemical composition, too. compares fresh carbon in its typical micrograph configuration (Figure 4a) with an analogue one of the same carbon nature after the saturation, at T = 120°C and c0 = 3.93 mg/m3 (Figure 4b).
Figure 4a displays different single carbon particles with irregular surface, different shape and brightness, and no macroporosity. The energy-dispersive x-ray spectroscopy (EDS) microanalysis carried out on the circled and squared zones in the figure, characterized by a different light intensity, facilitated the identification of diverse zones with different surface composition. reports their elemental composition. The picture captured showed that the circled zone (Figure 4a) with very low brightness can be considered as representative of sulfur-rich areas, while the squared zone with high brightness can be representative of low sulfur content, but with high silicon and aluminum concentration.
Table 1. Local composition (%) obtained by EDS microanalysis of different zones in Figure 4.
The data in regarding the zones of Figure 4b (mercury-saturated carbon) showed that a high mercury concentration is found in conjunction with high sulfur concentration (white spots–circled zones). The totally gray squared area was typical of very low sulfur concentration with no Hg content.
Discussion
Experimental runs performed in this work showed that the process investigated is an adsorption one, rather than a gas–solid reaction. Furthermore, they disclosed that gas-phase concentration is a critical parameter to determine adsorbate loading values in equilibrium conditions. In particular, its highest value is 7.5 × 10−2 g/g; if we hypothesize a hexagonal close packing of a monolayer of Hg°, the surface coverage is about 20 m2/g. However, a great part of the solid surface doesn’t participate in the adsorption process, because its available surface area (628 m2/g) results in a much larger value. Using the well-known Langmuir isotherm to interpret the physical interaction between sorbent and adsorbate, the overall rate of the process can be expressed as the difference between adsorption and desorption rate, as stated by the following equation:
where c is the Hg° concentration in the gas phase, ω is its concentration as adsorbate on the solid, ωmax is the asymptotic adsorbate concentration, and k1 and k2 are the kinetic constants of the adsorption and of the desorption reaction, respectively. At equilibrium (r = 0) such a rate equation leads to the Langmuir isotherm:
where is the equilibrium constant.
reports the equilibrium data, which are useful to calculate Langmuir parameters for different temperature values investigated. reports Langmuir parameters, which were computed by means of a nonlinear regression technique.
Table 2. Langmuir and kinetic parameters for HGR activated carbon.
shows continuous lines, which are representative of Langmuir isotherms computed with the values of ; these parameter values demonstrated that the highest temperature values, the lowest both K and ωmax. This behavior permitted assuming a dependence of the equilibrium constant K on the temperature of the Arrhenius type, according to its physical meaning, leading to the following equation:
where Ko is the preexponential factor and ∆Hads is the heat of adsorption. A nonlinear regression analysis of the data in gave for Ko the value of 1.03 m3/g and for ∆Hads the value of −20.8 kJ/mol, which is in the same order of the heat of condensation for Hg°. The values of K, together with the continuous line obtained using eq 3 with Ko = 1.03 m3/g and ∆Hads = −20.8 kJ/mol, are reported in in the form of an “Arrhenius” plot.
Figure 4. (a) Fresh carbon. (b) Saturated carbon (T = 120°C; c0 = 3.93 mg/m3). SEM micrograph of HGR carbon.
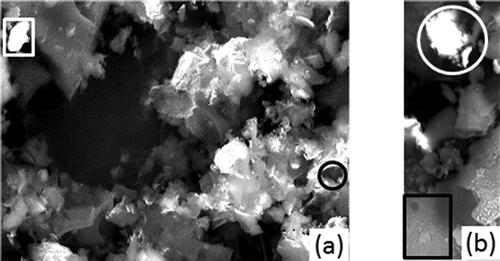
In the results relative to Hg° adsorption on HGR carbon presented here are compared to those obtained in the same experimental apparatus by using Darco G60 carbon (Karatza et al., Citation2011). In that work very similar values were found for Ko and ∆Hads (0.72 m3/g and –22 kJ/mol, respectively). However, HGR carbon is much more effective for metallic mercury capture than Darco G60 carbon, and this circumstance is reflected in the fact that the asymptotic adsorbate concentrations for HGR carbon are about 200 times those for Darco G60 carbon. This result could be justified by the presence of sulfur on HGR carbon, which increases the number of active sites and in this way enhances the carbon adsorption capacity.
Figure 6. Comparison between adsorption isotherms on HGR ○ (present work) and Darco G60 □ (Karatza et al., Citation2011), with T = 120°C and T = 150°C. Langmuir equation.
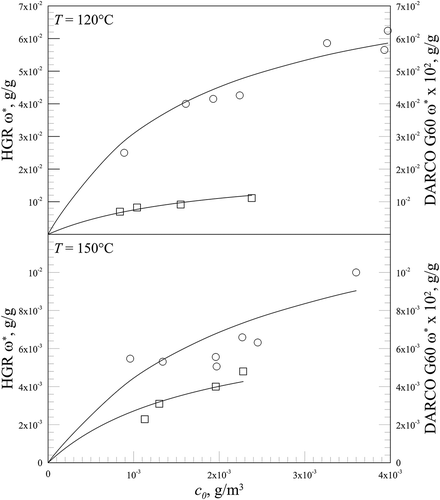
The values of the kinetic constants k1 and k2 can be evaluated considering a balance on Hg° adsorbed in the bed. Indicating the axial coordinate in the bed with x and the time with t, it is
where V is the superficial velocity of the gas, ε is the external void fraction of the bed, and ρb is the bulk density of the adsorbent particles. Such a balance equation has to be associated to a constitutive equation for the rate of accumulation on the solid; by neglecting the diffusional resistances and considering eq 1, the constitutive equation can be expressed as follows:
Equations 4 and 5 have to be integrated subject to the following boundary conditions:
The system of eqs 4 and 5 with the boundary conditions 6 was solved using the analytical method proposed by Rhee (Rhee et al., Citation1986). Using the values of K and ωmax experimentally determined for the different temperatures, the Hg° concentration profiles both in the gas and on the solid phase could be obtained as a function of time. A comparison between model and experimental results was possible in terms of cout as a function of the run time, which can easily be obtained from the solution of eqs 4 and 5. The only parameter in such equations is k1. Its values, together with the ones of k2, are reported in . These values, as expected, significantly depend on bed temperature, but are independent of the Hg° inlet concentration to the adsorbing bed. Both kinetic constant values (k1 and k2) increase as the temperature increases; this behavior is in agreement with the physical meaning of these parameters, even if their ratio (K) decreases as the temperature increases, because of the exothermic nature of the adsorption phenomenon.
Conclusions
In this paper experimental runs were carried out on a lab-scale plant to study the adsorption process of elemental mercury vapors on HGR carbon, a commercial solid sorbent. During the tests some variable processes were varied, like Hg° concentration and bed temperature. Results obtained demonstrated the satisfactory behavior of HGR carbon, whose effectiveness in capturing elemental mercury is enhanced at low temperatures. Implementation of Langmuir model confirmed the nature of adsorption isotherms and permitted computing its characteristic constants, together with the heat of adsorption (∆Hads). The SEM technique was a useful tool to locate sites where mercury adsorption is more efficient; they correspond with carbon areas where sulfur concentration is higher.
Experimental data obtained in this paper will be valued in the following step of the experimental work, aimed at the study of thermodynamic equilibria of elemental mercury adsorption on activated carbon, when O2, SO2, and H2O in the gas phase are simultaneously present.
Nomenclature
c0 Hg° | = | inlet concentration |
cout Hg° | = | outlet concentration |
Hg° | = | elemental mercury |
Hg2+ | = | oxidized mercury |
Hgp | = | particulate-bound mercury |
k1 | = | adsorption kinetic constant |
k2 | = | desorption kinetic constant |
K | = | equilibrium constant |
Ko | = | preexponential factor |
V | = | gas superficial velocity |
∆Hads | = | heat of adsorption |
ε | = | external void fraction |
ρb | = | bulk density |
ω | = | Hg° concentration as adsorbate |
ω* | = | Hg° concentration as adsorbate at saturation |
ωmax | = | asymptotic adsorbate concentration |
Additional information
Notes on contributors
D. Musmarra
Prof. Eng. Dino Musmarra is an associate professor at the Second University of Naples, Department of Civil Engineering, Design, Building and Environment.
D. Karatza
Dott. Eng. Despina Karatza is an assistant professor at the Second University of Naples, Department of Civil Engineering, Design, Building and Environment.
A. Lancia
Prof. Eng. Amedeo Lancia is a full professor at the University of Naples “Federico II,” Department of Chemical Engineering, Materials and Industrial Production.
M. Prisciandaro
Prof. Eng. Marina Prisciandaro is an associate professor at the University of L’Aquila, Department of Industrial and Information Engineering and Economics.
G. Mazziotti di Celso
Dott. Eng. Giuseppe Mazziotti di Celso is an assistant professor at the University of Teramo, Faculty of Bioscience and Agro-Food and Environmental Technology.
References
- Almquist, C., and N. Quin. 2013. Pyrolysis of deinked paper sludge to synthesize adsorbents for elemental Hg vapors. Environ. Prog. Sustain. Energy 32:524–34. doi:10.1002/ep.11652
- Bustard, J., M. Durham, T. Starns, C. Lindsey, C. Martin, R. Schlager, and K. Baldrey. 2004. Full-scale evaluation of sorbent injection for mercury control on coal-fired power plants. Fuel Process. Technol. 85:549–62. doi:10.1016/j.fuproc.2003.11.021
- Chang John, C.S., and B.S. Ghorishi. 2003. Simulation and evaluation of elemental mercury concentration increase in flue gas across a wet scrubber. Environ. Sci. Technol. 37(24): 5763–66. doi:10.1021/es034352s
- Eswaran, S., and H.G. Stenger. 2005. Understanding mercury conversion in selective catalytic reduction (SCR) catalysts. Energy Fuels 19:2328–34. doi:10.1021/ef050087f
- European Commission. 2006. Commission Regulation No 1881/2016 19 December 2006. Setting maximum levels for certain contaminants in foodstuffs.
- Granite, E.J., H.W. Pennline, and R.A. Hargis. 2000. Novel sorbents for mercury removal from flue gas. Ind. Eng. Chem. Res. 39:1020–29. doi:10.1021/ie990758v
- Heidel, B., M. Hilber, and G. Scheffknecht. 2014. Impact of additives for enhanced sulfur dioxide removal on re-emissions of mercury in wet flue gas desulfurization. Appl. Energy 114:485–91. doi:10.1016/j.apenergy.2013.09.059
- Hu, C., J. Zhou, S. He, Z. Luo, and K. Cen. 2009. Effect of chemical activation of an activated carbon using zinc chloride on elemental mercury adsorption. Fuel Process. Technol. 90:812–17. doi:10.1016/j.fuproc.2009.03.020
- Ie, I.R., W.C. Chen, C.S. Yuan, C.H. Hung, C.Y. Lin, H.H. Tsai, and Y.S. Jen. 2012. Enhancing the adsorption of vapor-phase mercury chloride with an innovative composite sulfur-impregnated activated carbon. J. Hazard. Mater. 217–18:43–50. doi:10.1016/j.jhazmat.2012.02.035
- Jiang, G.B., J.B. Shi, and X.B. Feng. 2006. Mercury pollution in China. Environ. Sci. Technol. 40:3673–3678. doi:10.1021/es062707c
- Jurng, J., T.G. Lee, and G.W. Lee. 2002. Mercury removal from incineration flue gas by organic and inorganic adsorbents. Chemosphere 47:907–913. doi:10.1016/S0045-6535(01)00329-0
- Karatza, D., A. Lancia, and D. Musmarra. 1998. Fly ash capture of mercuric chloride vapors from exhaust combustion gas. Environ. Sci. Technol. 32:3999–4004. doi:10.1021/es971074m
- Karatza, D., A. Lancia, D. Musmarra, and F. Pepe. 1996a. Adsorption of metallic mercury on activated carbon. Twenty-Sixth Symposium International on Combustion, The Combustion Institute, 2439–45.
- Karatza, D., A. Lancia, D. Musmarra, and C. Zucchini. 2000. Study of mercury absorption and desorption on sulfur impregnated carbon. Exp. Thermal Fluid Sci. 21:150–55. doi:10.1016/S0894-1777(99)00065-5
- Karatza, D., A. Lancia, D. Musmarra, F. Pepe, and G. Volpicelli. 1996b. Kinetics of adsorption of mercuric chloride vapors on sulfur impregnated activated carbon. Combust. Sci. Technol. 112:163–74. doi:10.1080/00102209608951954
- Karatza, D., A. Lancia, D. Musmarra, F. Pepe, and G. Volpicelli. 1996c. Removal of mercuric chloride from flue gas by sulfur impregnated activated carbon. Hazard. Waste Hazard. Mater. 13:95–105. doi:10.1089/hwm.1996.13.95
- Karatza, D., A. Lancia, M. Prisciandaro, D. Musmarra, and G. Mazziotti di Celso. 2013. Influence of oxygen on adsorption of elemental mercury vapors onto activated carbon. Fuel 111: 485–91. doi:10.1016/j.fuel.2013.03.068
- Karatza, D., M. Prisciandaro, A. Lancia, and D. Musmarra. 2011. Silver impregnated carbon for adsorption and desorption of elemental mercury vapors. J. Environ Sci. 23:1578–84. doi:10.1016/S1001-0742(10)60528-1
- Lancia, A., D. Karatza, D. Musmarra, and F. Pepe. 1996. Adsorption of mercuric chloride from simulated incinerator exhaust gas by means of SorbalitTM particles. J. Chem. Eng. Jpn. 29:939–46. doi:10.1252/jcej.29.939
- Lee, S.S., J.Y. Lee, and C.T. Keener. 2009. Mercury oxidation and adsorption characteristics of chemically promoted activated carbon sorbents. Fuel Process. Technol. 90:1314–18. doi:10.1016/j.fuproc.2009.06.020
- Lee, W.C., D.S. Serre, Y. Zhao, J.S. Lee, and W.T. Hastings. 2008. Mercury oxidation promoted by a selective catalytic reduction catalyst under simulated Powder River Basin coal combustion conditions. J. Air Waste Manage. Assoc. 58:484–93. doi:10.3155/1047-3289.58.4.484
- Li, Y., M. Daukoru, A. Suriyawong, and P. Biswas. 2009. Mercury emissions control in coal combustion systems using potassium iodide: Bench-scale and pilot-scale studies. Energy Fuels 23:236–43. doi:10.1021/ef800656v
- Li, Y.H, C.W. Lee, and B.K. Gullett. 2002. The effect of activated carbon surface moisture on low temperature mercury adsorption. Carbon 40:65–72. doi:10.1016/S0008-6223(01)00085-9
- Li, Y.H, C.W. Lee, and B.K. Gullett. 2003. Importance of activated carbon’s oxygen surface functional groups on elemental mercury adsorption. Fuel 82:451–57. doi:10.1016/S0016-2361(02)00307-1
- Niksa, S., and N. Fujiwara. 2005. Predicting extents of mercury oxidation in coal-derived flue gases. J. Air Waste Manage Assoc. 55:930–39. doi:10.1080/10473289.2005.10464688
- Nordberg, G.F., Fowler B.A., Nordberg M., and L. Friberg. 2007. Handbook on Toxicology of Metals. San Diego, CA: Academic Press.
- Pacyna, E.G., J.M. Pacyna, F. Steenhuisen, and S. Wilson. 2006. Global anthropogenic mercury emission inventory for 2000. Atmos. Environ. 40:4048–63. doi:10.1016/j.atmosenv.2006.03.041
- Pacyna, E.G., J.M. Pacyna, K. Sundseth, J. Munthe, K. Kindbom, and S. Wilson. 2010. Global emission of mercury to the atmosphere from anthropogenic sources in 2005 and projections to 2020. Atmos. Environ. 44(20): 2487–89. doi:10.1016/j.atmosenv.2009.06.009
- Pavlish, J.H. 2009. Preface to the AQVI special issue of Fuel Processing Technologies entitled: Air quality VI: Mercury, trace elements, SO3, particulate matter, and greenhouse gases. Fuel Process. Technol. 90:1327–32. doi:10.1016/j.fuproc.2009.09.006
- Pavlish, J.H., E.A. Sondreal, M.D. Mann, E.S. Olson, K.C. Galbreath, and D.L. Laudal. 2003. Status review of mercury control options for coal-fired power plants. Fuel Process. Technol. 82(2–3):89–165. doi:10.1016/S0378-3820(03)00059-6
- Prisciandaro, M., G. Mazziotti di Celso, and F. Vegliò. 2003. Effect of burning supplementary waste fuels on the pollutant emissions by cement plants: A statistical analysis of process data. Resources Conserv. Recycling 39: 161–84. doi:10.1016/S0921-3449(02)00170-2
- Rhee, H.-K., R. Aris, and N.R. Amundson. 1986. First Order Partial Differential Equations, Vol. 1. Englewood Cliffs, NJ: Prentice Hall.
- Scala F., R. Chirone, and A. Lancia. 2011. Elemental mercury vapor capture by powdered activated carbon in a fluidized bed reactor. Fuel 90:2077–2082. doi:10.1016/j.fuel.2011.02.042
- Scala, F., and H.L. Clack. 2008. Mercury emissions from coal combustion: Modeling and comparison of Hg capture in a fabric filter versus an electrostatic precipitator. J. Hazard. Mater. 152:616–23. doi:10.1016/j.jhazmat.2007.07.024
- Serre, S.D., and G.D. Silcox. 2000. Adsorption of elemental mercury on the residual carbon in coal fly ash. Ind. Eng. Chem. Res. 39:1723–30. doi:10.1021/ie990680i
- Shigeo, I., Y. Takahisa, and A. Kazuo. 2006. Emissions of mercury and other trace elements from coal-fired power plants in Japan. Sci. Total Environ. 368(1): 397–402.
- Skodras, G., I. Diamantopoulou, A. Zabaniotou, G. Stavropoulos, and G.P. Sakellaropoulos. 2007. Enhanced mercury adsorption in activated carbons from biomass materials and waste tires. Fuel Process. Technol. 88:749–758. doi:10.1016/j.fuproc.2007.03.008
- Takaoka, M., N. Takeda, T. Fujiwara, M. Kurata, and T. Kimura. 2011. Control of mercury emission from municipal solid waste incinerator in Japan. J. Air Waste Manage. Assoc. 52:931–940. doi:10.1080/10473289.2002.10470831
- Uddin, M.A., T. Yamada, and R. Ochiai. 2008. Role of SO2 for elemental mercury removal from coal combustion flue gas by activated carbon. Energy Fuels 22:2284–89. doi:10.1021/ef800134t
- Wang, S., L. Zhang, L. Wang, Q. Wu, F. Wang, and J. Hao. 2014. A review of atmospheric mercury emissions, pollution and control in China. Front. Environ. Sci. Eng. 8:631–49. doi:10.1007/s11783-014-0673-x
- Wu, Y., S.X. Wang, D.G. Streets, J.M. Hao, M. Chao, and J.K. Jiang. 2006. Trends in anthropogenic mercury emissions in China from 1995 to 2003. Environ. Sci. Technol. 40:5312–5318. doi:10.1021/es060406x
- Yang, H., Z. Xu, M. Fan, A.E. Bland, and R.R. Judkins. 2007. Adsorbents for capturing mercury in coal-fired boiler flue gas. J. Hazard Mater. 146(1–2):1–11. doi:10.1016/j.jhazmat.2007.04.113
- Zheng, Y., A.D. Jensen, C. Windelin, and F. Jensen. 2012a. Review of technologies for mercury removal from flue gas from cement production processes. Prog. Energy Combust. Sci. 38:599–629. doi:10.1016/j.pecs.2012.05.001
- Zheng, Y., A.D. Jensen, C. Windelin, and F. Jensen. 2012b. Dynamic measurement of mercury adsorption and oxidation on activated carbon in simulated cement kiln flue gas. Fuel 93:649–57. doi:10.1016/j.fuel.2011.09.053
- Zhong, L., Y. Zhang, Z. Liu, Z. Sui, Y. Cao, and W.P. Pan. 2014. Study of mercury adsorption by selected Chinese coal fly ashes. J. Thermal Anal. Calorim. 116:1197–203. doi:10.1007/s10973-014-3657-y