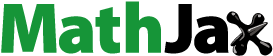
ABSTRACT
Compressed Natural Gas (CNG) has been applied worldwide for in-used engines, especially CNG engines that are converted from the conventional engines. However, it encounters the problem related to the low power and high fuel consumption of the conventional engine fueled by CNG. This paper presents an experimental study on performance enhancement of a CNG engine converted from the spark-ignition engine by the implementation of fuel additive Maz 100. In experimental work, a fuel additive supplying system was developed to impose a certain amount of fuel additive to the intake manifold of the test engine. The study results show that when using Maz 100, the brake power of the test engine improves approximately 6.75% on average at full load conditions. The brake specific fuel consumption (BSFC) reduces 6.49% on average at full load and 3.53% on average at partial load condition. In addition, besides the benefit of performance enhancement, exhaust emissions of the test engine in the case of operating with fuel additive have changed considerably. Particularly, the CO emission reduces 36.1% at full load and 18.4% on average at partial load conditions. The HC emission reduces 37.1% at full load and 35.0% on average at partial load conditions. The NOx emission increases slightly in low-speed regimes and reduces in high-speed regimes when the engine operates at the full opened throttle condition. At partial load condition and speed of 3000 rpm, the NOx emission reduces 22.6% on average.
Implications: This paper presents a solution for performance enhancement and emission reduction of natural gas engine by using fuel additive. Performance and emission characteristics of the natural gas engine fueled with fuel additive have been assessed in the laboratory. The performance of the test engine improves remarkably. The brake power of the test engine improves approximately 6.75% on average at full load conditions when the engine operates with fuel additive. The brake specific fuel consumption reduces 3.53% on average at partial load condition. The emission of pollution has different trends. The CO and HC emission reduces at testing conditions. The NOx emission increases slightly in low-speed regimes and reduces in high-speed regimes when the engine operates at the full opened throttle condition. The implementation of fuel additive is a potential solution for power improvement and emission reduction of natural gas engine.
Introduction
Controlling the emission of air pollution from in-used vehicles is the most important issue in growing countries, as mentioned in many studies. A potential solution that has recently been focused by scientists is the implementation of renewable and alternative energy sources to replace conventional energies as gasoline and diesel oil. In Vietnam, scientists have done experimental studies on the application of alternative fuel in both currently used and new-generation engines. Some considerable works on using alternative fuel in vehicles had been conducted and achieved recognition results on the development progress of renewable energies in the country (Duc and Duy Citation2018; Duc, Tien, and Duy Citation2016; Nguyen Duc et al. Citation2019). Among alternative fuels for internal combustion engine (ICE), natural gas (NG) has been pointed out as the potential energy source of the future to replace traditional energy sources such as gasoline and diesel fuel. NG is specified by advantage properties so it has been used widely for exhaust emission reduction and fuel economy enhancement.
Not only in Vietnam, but scientists in worldwide, also prefer to study the application of NG in vehicles and achieved worthy results. As mentioned in the report of the U.S. Department of Energy (Accessed January 19, 2020. https://afdc.energy.gov/vehicles/natural_gas_emissions.html), utilizing NG in transportations can reduce up to 11% amount of greenhouse gas emissions in comparison to the case of fueling with gasoline. In addition, the usage of NG in diesel vehicles has benefit of considerable nitrogen oxide (NOx) emissions and soot reduction (Karagöz et al. Citation2016). In the research of Park et al. (Park, Shim, and Bae Citation2019) that was conducted on a duel fuel CNG-diesel engine, a heavy-duty diesel engine was modified to fuel by duel fuel CNG-diesel with NG substitution of 40%. The carbon monoxide (CO) and unburned hydrocarbon (HC) could be reduced to low level by controlling the equivalence ratio and initial charge temperature. Many studies on emission characteristics of spark-ignition (SI) engine fueled with NG had been conducted. An experimental assessment study carried out by Barros et al. (Barros Zárante and Sodré Citation2009) to evaluate the emission level of the gasoline engine following the emission test cycle U.S. FTP-7. The results pointed out that the usage of NG as a substitute for gasoline could reduce emissions of CO by 75% and CO2 by 33%. The engine fueled with NG had CO emission level below regulated limit, even the test engine was not equipped with the catalytic converter. Other research on the same topic conducted by Zhang et al. (Citation2011) also shows that exhaust emissions from vehicles fueled by CNG, including CO, HC, and NOx reduced up to 30% compared to those of gasoline when the vehicle was tested following the European Driving Cycle. Yao et al. (Citation2014) had carried out an experimental research to evaluate exhaust emission level of 20 taxis fueled by CNG or gasoline. The study results show that the test vehicles produced a lower level of CO2 and CO when the engine fueled with CNG. However, in the opposite trend, NOx and HC emissions were significantly higher. The study results conducted by Yontar et al. (Yontar and Doğu Citation2018a, Citation2019, Citation2018b) on the effects of CNG on performance and emission of SI engine show that HC and CO emission reduced, and NOx emission increased when the engine operated with CNG in comparison to the case of fueling with gasoline.
NG compounds of mostly methane gas, which has a higher H/C ratio in comparison with conventional gasoline (Huang and Crookes Citation1998; Kato et al. Citation1999; Xu and Cho Citation2016), so that the CO and CO2 pollutant level reduces remarkably. CNG is normally supplied to intake manifold in the gaseous state for both aspirate or port fuel injection systems, thereby the better fuel-air mixture formation. As a result, more efficient combustion and low HC emission could be achieved. Moreover, the CNG engine emits less HC emission compared to gasoline engines because HC emission causes by fuel absorption/desorption from lubricant oil and cylinder wall are prevented, especially in cold start condition (Huang and Crookes Citation1998). NOx emission is popularly known as the production of the chemical reaction between oxygen and nitrogen atoms in high-temperature conditions. Some studies show that NOx level reduced when operating with CNG (Evans and Blaszczyk Citation2005; Pourkhesalian, Shamekhi, and Salimi Citation2010). However, other studies had opposite results on NOx production (Aslam et al. Citation2006).
However, in opposition to the benefit in emission characteristics, studies also pointed out that CNG engines converted from gasoline engines have worse performance characteristics. Because CNG is usually supplied in-directly to the engine, thereby the reduction in the charge mixture at the end of the suction stroke, and as a result, output power reduces dramatically. This issue was pointed out clearly in the experimental research on dual-fuel CNG-gasoline SI engine conducted by Yontar et al. (Yontar and Doğu Citation2018a). The study results show that the volumetric efficiency of the engine reduced up to 10% when the engine operated with CNG. Hence, the engine performance characteristics reduce remarkably in comparison with that of the gasoline engine. Aslam et al. (Aslam et al. Citation2006) had pointed that, as supplying CNG into the intake manifold of the engine in the gaseous state by a mixer venture, the brake mean effective pressure reduced by 16% on average compared to the original case although the ignition timing (IT) had been adjusted in order to reach the maximum brake torque. Another study conducted by Evan et al. (Evans and Blaszczyk Citation2005) also showed that the engine performance characteristic could be enhanced by the way of advancing the IT as the engine fueled with CNG. The IT of the engine should be advanced from 2 to 10 crank angle (CA) degrees (deg) in order to obtain maximum brake power (BP). Similar to the research of Evan et al. (Evans and Blaszczyk Citation2005), Kaleemuddin and Rao (Citation2009) had also pointed that the IT of the CNG engine converted from conventional SI engine should be advanced from 2 to 5 CA deg for the more efficient combustion process. Porkhesalian et al. (Pourkhesalian, Shamekhi, and Salimi Citation2010) conducted an experimental study on converting four cylinders, port fuel injection, SI engine to operate with bi-fuel CNG/gasoline without IT advancing. The results show that gaseous fuel supplied to the intake manifold significantly affected to the volumetric efficiency of the test engine. A reduction of approximately 12% on average of the volumetric efficiency and 20% of BP were recorded when the engine was fueled with CNG by using the venture system. Another study was conducted by Kalam and Masjuki (Citation2011) in finding the solution to regain the performance characteristic of the CNG engine converted from a conventional gasoline engine. By using a mixer venture, the BP of the test engine reduced up to 20% although CNG has higher heating value (per kg of fuel) than conventional fuel. However, if the engine was modified to use a direct-injection system, the engine performance enhanced up to 10% compared to the case of the original gasoline engine. The results meant that the implementation of CNG by direct-injection system would result in no replacement of intake air by gaseous fuel phenomena. Hence, an improvement in output power could be achieved. However, the author also implied that the direct-injection system was more complicated so it was not suitable for real-world applications in CNG engines converted from conventional engines. In comparison with gasoline, CNG is also specified by higher RON (Research Octane Number) and lower laminar flame speed that could result in longer combustion duration. Consequently, lower thermal efficiency and higher cycle to cycle variation could be encountered (Dhyani and Subramanian Citation2019; Ran et al. Citation2020).
In our previous research (Nguyen Duc et al. Citation2019), we developed a bi-fuel supply system for currently used SI engine in order to run on either CNG or gasoline flexibly. In experimental work, an independent gaseous port injection system had been designed to provide gaseous fuel into the intake manifold of the converted engine. After modification, the performance characteristics of the test engine such as BP, brake torque (BT), energy consumption (EC), and emissions with each kind of fuel were assessed. Because of the lower heating value (HV) in the volume of CNG and reduction in mass of the inducted mixture caused by gaseous fuel taking place in the intake manifold, the BP of the test engine decreased approximately 19% at full load condition on average and the mass flow rate of intake air reduced from 7.3% to 9.5% in the range of test speed. In the experiment, because of the complex structure of the ignition system, the IT of the test engine was not adjusted to an optimized value for CNG fuel so that the combustion process was ineffective, thereby inefficiency economic characteristics of the engine fueled with CNG. The average specific energy consumption (SEC) increased up to 14% at full load and 30% on average at partial load condition when the engine was fueled with CNG.
For performance improvement, solutions relating to engine structure modifications had been studied. For instance, compression ratio increasing, design special geometric intake manifold for more swirl during suction stroke, advancing IT were workable solutions, which had been carried out for performance enhancement of CNG engines. Hosmath et al. (Hosmath et al. Citation2016) pointed out that CNG is specified by higher RON in comparison with gasoline fuel, so that the CNG engine could operate at a higher compress ratio for engine performance enhancement. According to the study of Harinath Reddy and John Abraham (Reddy and Abraham Citation2013), introducing swirl mixing between fuel and air in the intake manifold could contribute to the reduction of ignition delay and increase of burning velocity. As discussed above (Aslam et al. Citation2006; Evans and Blaszczyk Citation2005), advancing the IT of the CNG engine is a feasible solution to regain engine performance. However, these solutions are only applied widely in new-generation CNG engines, which have been designated to operate with NG. So finding solutions, which can be applied in CNG engines converted from the in-used engine are necessary for developing countries like Vietnam.
The implementation of fuel additive, which has been applied widely in not only conventional fuel engines but also alternative fuel engines for fuel efficiency and performance improvement, has been conducted. The fuel additive supplied to intake mixture, or in the fuel. The blend could contribute to high burning speed and complete combustion, there-by improvement in fuel economy and reduction in emission. For example, hydrogen used as a fuel additive has been known as an effective solution for combustion advancement in ICE. Tuan et al. (Le Anh et al. Citation2013) used HHO enriched air to improve the performance characteristic and reduce pollution emissions of a single carburetor engine. The HHO gas was produced by the electrolysis process of distilled water. By the method of continuous supplying the HHO gas into the intake manifold of the test engine, the performance improved and HC emission decreased while NOx emission increased. The implementation of hydrogen in the CNG engine had been carried out by Orhan Akansu et al. (Citation2004) and Huang et al. (Citation2007). The results show that hydrogen implementation could result in significant CO and HC reduction, and engine efficiency improvement. The usage of hydrogen as an effective gas to enhance the higher flame rate of the CNG engine was discussed in the review study of Alrazen and Ahmad (Citation2018). Also, the physicochemical properties of hydrogen and the mixture of hydrogen-CNG were also clearly explained (Yan, Xu, and Wang Citation2018). Not only in SI engines, hydrogen was also used effectively in compress ignition (CI) engines. In 2016, a research was conducted by Javed et al. (Citation2016) to analyze the vibration of a biodiesel engine with hydrogen supplied as secondary fuel. Dimethyl ether (DME) is one of the sustainable energy sources used in diesel vehicles because it is specified by high vapor pressure and low boiling temperature properties. The usage of DME in the CI engine results in high thermal efficiency and ultra-low emission as clearly presented in the research of Zhen Huang et al. (Citation2009). Acetone has been applied in ICE to improve engine performance and reduce emissions because it plays an important role in raising of the vaporization ability of fuel, especially in cold starting condition (Elfasakhany Citation2016). Methyl tertiary butyl ether was used as oxygenated fuel in the research of Poulopoulos (Poulopoulos and Philippopoulos Citation2001) for HC and CO reduction. Nanoscale Cerium oxide is used as a diesel additive to reduce particulate matter and enhance fuel economy by the improvement of the self-ignited combustion process. Owing to the advantageous properties, this kind of additive is commonly used in bio-diesel engines (Appavu and Venkata Ramanan Citation2018; Karthikeyan, Elango, and Prathima Citation2016; Özgür, Özcanli, and Aydin Citation2015). Maznitro (Maz) has been known as an effective fuel additive in liquid fuel as well as boiler gas fuel for both fuel economy enhancement and reduction of emission (Lim Citation2010; Long Citation2010a; Yiming et al. Citation2004). Maz is compounded of mostly nitropropane and other components such as nitro-methane, nitro-ethane, toluene, ester. The proportion of Maz additive in gasoline fuel varies from 500 to 1000 ppm (Gunawan and Zaenuri Citation2010; Long Citation2010a, Citation2010b; Yiming et al. Citation2004). Maz is specified by special characteristics as high burning velocity, good vaporization and diffusion ability, and clean-burning. Therefore, Maz can be used effectively in gasoline vehicles for power enhancement, fuel consumption reduction, and low emission levels.
In this experimental study, as the next step of our previous study (Nguyen Duc et al. Citation2019), we continue to carry out a test on the implementation of Maz additive to enhance the performance characteristics of the CNG engine converted from currently used gasoline engines. In experimental work, a fuel additive supplying system was developed for additive providing to the intake manifold of the test engine. The performance and emission characteristics of the NG engine with Maz additive have been evaluated. The results of this study are helpful for applying NG fuel widely as the potential alternative energy source to replace conventional gasoline fuel in order to solve the energy crisis and environmental problems in Vietnam.
Experimental procedure
Testing engine, fuel and fuel additive
The testing engine used in this experimental study is a four-cylinder, inline, multi-port injection SI CNG engine converted from a conventional gasoline engine. The specifications of the testing engine are presented in . In this study, we used commercial CNG and Maz 100 in experimental work with properties as shown in and (Gunawan and Zaenuri Citation2010; Long Citation2010b; Yiming et al. Citation2004).
Table 1. Specifications of testing engine.
Table 2. Properties of testing fuel.
Table 3. Properties of fuel additive Maz 100.
Fuel additive supplying system design
In this study, a fuel additive supplying system has been designed in order to control the amount of fuel additive supplement into the intake manifold of the testing engine. The principle schematic of the fuel additive supplying system has been shown in .
As observed in the schematic, fuel additive is pressurized in a container (6) by compressed air to guarantee a constant injection pressure. Fuel additive has been supplied to the vaporizator by a liquid injector (5), which is controlled according to testing conditions for a suitable amount of fuel additive. Mass flow rate of fuel additive supplied to the intake manifold of the testing engine has been guaranteed around a constant proportion to the amount of supplying fuel at each testing condition by adjusting the injection command from the fuel additive controller (10). Because flow rate of fuel additive is relatively low, so that in the experiment, we use single port fuel injection system for additive supplying and the mass of fuel additive (ma) is determined by EquationEquation 1(1)
(1) :
where mf is the mass flow rate of CNG fuel consumed by the test engine, γf is the ratio of supplied fuel additive to consumed CNG.
The γf ratio value of ≈ 800ppm was selected in this study. The value means that 0.8 g of fuel additive had been used for 1 kg of CNG. This ratio was similar to that of fuel additive in blend with conventional gasoline.
In testing condition, at each operating mode, the mass flow rate of NG has been controlled to guarantee the stoichiometric of air to fuel ratio of 1.0. Consequently, the flow rate of fuel additive can be determined based on the mass flow rate of intake air and the stoichiometric air to fuel ratio of CNG as shown in EquationEquation 2(2)
(2) :
where mair is the mass flow rate of intake air; (A/F)CNG is stoichiometric air to fuel ratio of CNG, (A/F)CNG = 16.8. As a result, the proportion of flow rate of additive to flow rate of intake air γa is determined as EquationEquation (3)(3)
(3) and the mass of fuel additive is determined by EquationEquation (4)
(4)
(4) :
Besides, a heat transfer system had been designed to improve the mixing process between fuel additive and intake air by utilizing heat energy from the recirculated exhaust gas. As illustrated in , an amount of exhaust gas, after flowing out of the engine, has been recirculated to the vaporizator (4). In the heat transfer compartment of the vaporizator, there is a convection heat transfer process between exhaust gas to the wall of the transfer compartment, conduct heat transfer between the outside wall and the inside wall of the compartment, and convection heat transfer process between the inside walls to additive moisture.
As presented in , Maz 100 has a relatively high boiling point. It has a temperature of initial boiling point at 100°C and the absolute boiling point at 130°C. So in the experiment, it is necessary to heat up supplied additive to reach a temperature above 130°C to ensure it evaporates absolutely before mixing with intake air. At each operation condition of the engine, the necessary heat energy taking from recirculated gases is determined by EquationEquation (5)(5)
(5) :
where Ma is the mole flow rate of fuel additive (mol/s); CpL and CpG are constant pressure specific heat of fuel additive at liquid and gaseous state, respectively, kJ/mol.K; ΔT100 is difference temperature of fuel additive at the moment of injection and 100°C; ΔT is difference temperature of the additive at moisture state to the liquid state (100°C); and hhh is the heat of vaporization of fuel additive (kJ/mol).
Experimental equipment
The testing equipment used in the experiment includes a dynamometer, emission measurement analyzers, indiset device, and mass flow meter of fuel and intake air. The details of these devices have been clearly shown in . The schematic of the experimental test rig is shown in .
Table 4. Experimental equipment properties.
Testing procedures
The performance characteristics of the test engine such as the BP, in-cylinder profile, and emissions of air pollution have been recorded for evaluation at each testing condition. At fully opened throttle, engine speeds were varied from 1000 to 4000 rpm with an interval of 500 rpm. At partial load condition, the throttle was adjusted at the various positions while engine speed was constantly kept at 3000 rpm. In the experimental procedure, actual air to fuel ratio was guaranteed around stoichiometric value by controlling the mass flow rate of CNG supplied through the injection duration.
Results and discussion
Comparison of the engine performance and economy characteristics
shows the experimental comparison of BP curves as a function of engine speed in the case of fueling with gasoline and CNG with and without fuel additive. The change in BP at full load condition as the engine operated with CNG had been discussed clearly in our previous study (Nguyen Duc et al. Citation2019). The BP of the CNG engine reduced dramatically up to 19% on average. This result is in accordance with other studies (Aslam et al. Citation2006; Tahir et al. Citation2015). When the engine operated with CNG-fuel additive, the performance improved remarkably at high-speed regimes. However, at low-speed regimes, the effect of fuel additive on performance is trivial. As the engine operated with CNG-fuel additive, the BP improves about 6.75% on average in comparison to the case of without fuel additive. The average brake specific fuel consumption (BSFC) of the test engine reduces approximately 6.49% at full load and 3.53% at partial load conditions, on average (a and b). At high engine speed, the reduction of BSFC is up to 7.6% at the speed of 4000 rpm. However, at low-speed regimes, the enhancement of BSFC in the case of fueling with fuel additive is only 2.0% at the speed of 1500 rpm. This phenomenon could be explained that, because in low-speed conditions, the cycle duration is long enough for complete combustion so fuel additive will not play an important role in the improvement of the combustion process. These results confirm that fuel additive can improve combustion efficiency. The appearance of fuel additive in intake mixture increase burning velocity resulting in more complete combustion. Therefore, the performance characteristics and fuel economy are enhanced especially at high engine speed regimes. When the CNG engine operated at a constant speed of 3000 rpm, the effect of fuel additive can be observed clearly in high load condition at which the amount of supplied fuel additive is more than low load conditions. The reduction of BSFC varies from 0% to 6.52% as the load condition increasing from 10% to full load. Utilizing fuel additive is a simple method in comparison to the others for engine performance enhancement and can be applied widely in real-world operation of the vehicle fueled with CNG.
Figure 3. Comparison of brake power in the case of with and without fuel additive at full load condition.
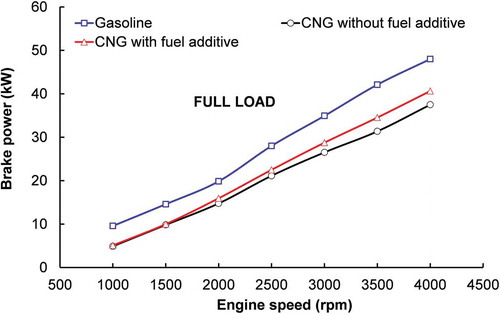
Figure 4. Comparison of BSFC in the case of with and without fuel additive at full load (a) and partial load (b) conditions.
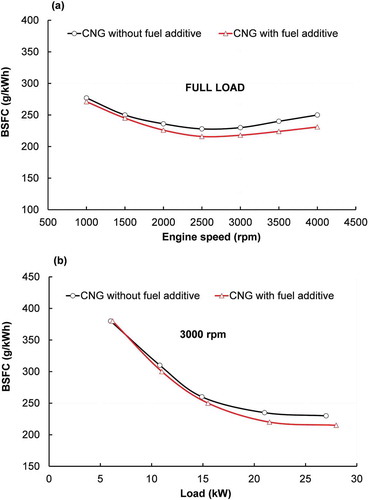
The effect of fuel additive on the combustion process can be observed clearly through the in-cylinder profile comparison in . presents the comparisons of in-cylinder pressure profiles of the test engine at an engine speed of 3000 rpm and full load condition, in the case of operating with gasoline and CNG with and without fuel additive. The higher RON and lower heating value and flame speed of CNG lead to a decrease in peak in-cylinder pressure compared to that of gasoline. The peak value closes to 62 bar at CA of 367 deg for gasoline and 50.64 bar at CA of 375 deg for CNG-without fuel additive. This result is in agreement with the study of Ting (Ting and Checkel Citation1995).
Figure 5. Comparison of measured in-cylinder pressure profile in the case of with and without fuel additive.
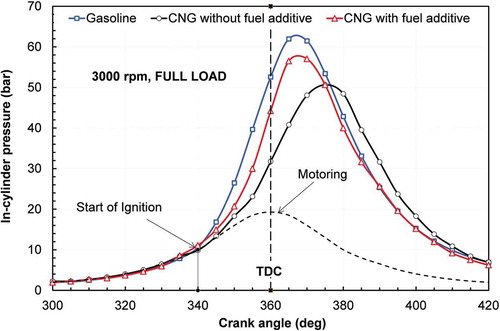
When the CNG engine operates with a fuel additive, the peak in-cylinder pressure is considerably higher in comparison with the case without the fuel additive system. In addition, the in-cylinder pressure profile is shifted to the left of the figure; this means that the combustion process is improved. The difference in the combustion pressure profile can be observed at around the top dead center, where the rate of burning reaches its peak. The peak pressure is closed to 57 bar at CA of 367 deg for the case of operating with fuel additive. The higher peak pressure in the case of operating with a fuel additive is the result of the higher burning velocity of CNG fuel and air. The mixture of fuel and air is burned quicker and more completed around the top dead center (TDC) when there was the appearance of fuel additive in the charge mixture. On the other hand, the higher burning speed in the case of operating with fuel additive could contribute to a shorter combustion process, thereby the reduction of wall heat loss.
shows the comparison of in-cylinder temperature profile that was calculated from the measured in-cylinder profile following the gas law as present in EquationEquation (6)(6)
(6) (Guardiola et al. Citation2016):
Figure 6. Comparison of calculated in-cylinder temperature profile in the case of with and without fuel additive.
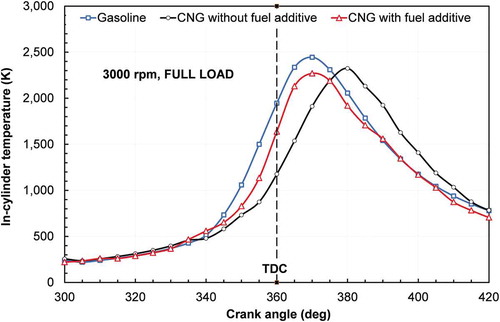
where Tcal(α) is the calculated in-cylinder temperature at CA α (K), Pmeas(α) is the measured in-cylinder pressure at CA α (N/m2), V(α) is the instantaneous volume at CA α (m3), m is the in-cylinder trapped mass (kg), and R is the gas constant (⁓286 J/kg.K for the mixture of burned gas and air (Lapuerta, Armas, and Hern´andez Citation1999)).
The terms of Pmeas(α) and m were obtained from experimental results and V(α) was calculated from engine structure parameters including bore, stroke, compression ratio, length of the connecting rod.
The results on peak temperature calculated from pressure profile as the CNG engine operates with a fuel additive are about 2269 K at CA of 370 deg, while as the obtained value for the case of operating without fuel additive is 2324 K at CA of 380 deg. This means that the expanded stroke of the CNG engine with a fuel additive is more effective and less of heat loss through the cylinder wall.
Comparisons of exhaust emissions
Besides performance advantage, the usage of fuel additive can result in a reduction of some gaseous emissions. In this study, emissions of CNG engine in the cases of operating with and without fuel additive have been evaluated according to the steady-state. Firstly, the engine speed varies from 1000 to 4000 rpm at the full opened throttle, and secondly, the test engine operates at different loads at a constant engine speed of 3000 rpm. The comparison of exhaust emission components of the test engine in two cases is shown from –.
Figure 7. Comparison of CO in the case of with and without fuel additive at full load (a) and partial load (b) conditions.
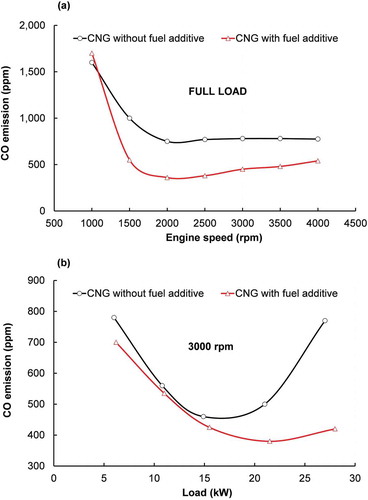
Figure 8. Comparison of HC in the case of with and without fuel additive at full load (a) and partial load (b) conditions.
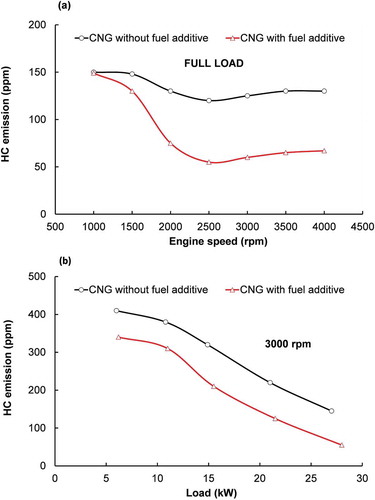
Figure 9. Comparison of NOx in the case of with and without fuel additive at full load (a) and partial load (b) conditions.
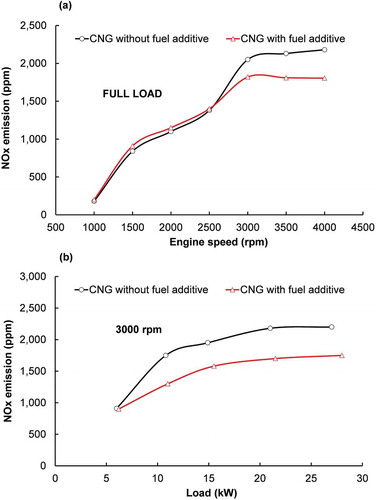
Figure 10. Comparison of CO2 in the case of with and without fuel additive at full load (a) and partial load (b) conditions.
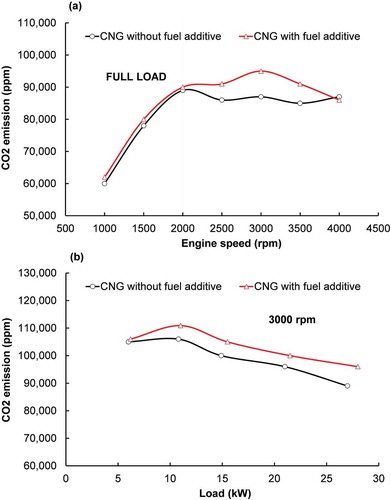
The CO emission resulted from incomplete combustion of air and fuel tends to be reduced 19% on average in the case of fueling with fuel additive at full load condition (a). At low speed or load conditions, the reduction of CO emission is slightly in the case of operating with fuel additive. The reason could explain this result at low-speed conditions, the effects of fuel additive on the combustion process are trivial as discussed above. However, at high speed or high load conditions, the CO emission reduces significantly. There is a lower level of CO up to 52.0% at a speed of 2000 rpm and 36.1% on average at full load condition and up to 46.8% and 18.4% on average at partial load conditions (b).
At fully opened throttle condition, the HC emission of the engine in the case of operating with fuel additive reduces up to 54.2% and 37.1% on average (a). At partial load condition and speed of 3000 rpm, HC emission reduces from 17.1% to 62.1% and 35.0% on average (b). Similar to the variation in CO emission, the reason that contributes to the reduction of HC emission is the more completed burning process when the CNG engine operating with a fuel additive, especially at high speed and load regimes.
The formation of NOx, which depends on the combustion temperature as reported in many studies (Flynn et al. Citation2000; Nebel and Jackson Citation1958), tends to decrease in the case of operating with fuel additive for both full load and partial load conditions. At full load condition (a), NOx increases slightly in low engine speed regimes (1000 rpm to 2500 rpm). However, in high engine speed regimes, NOx decreases up to 20.7% at the speed of 4000 rpm. At partial load condition, NOx decrease from 1.1% to 34.6% as an increasing load and about 22.7% on average in the case of operating with fuel additive (b). The variation of NOx emission at partial load condition is suitable with the change of in-cylinder temperature profile. When the CNG engine operates with fuel additive at full load condition and speed of 3000 rpm, the peak in-cylinder temperature reduces up to 55 K, as a result, NOx level decreases. At partial load condition and speed of 3000 rpm, the NOx emission reduces 22.6% on average.
The results in (a and b) show that the amount of CO2 as the engine operates with fuel additive tends to increase approximately 4.0% and 4.5% on average at full load and partial load conditions, respectively. These results are consistent with the reduction of CO and HC emission when the combustion process is more completed with the appearance of fuel additive.
Conclusion
The experimental study on the performance enhancement of a multi-port injection, SI engine fueled with CNG, has been conducted. The study results showed that using fuel additive Maz 100 supplied into the intake manifold is a good solution to improve the performance of the CNG engine. The brake power of the CNG engine operating with fuel additive improves 6.7% on average at full opened throttle condition. The fuel economy, which is specified by the brake specific fuel consumption, reduces approximately 6.49% and 3.53% on average at full load and partial load condition. The appearance of Maz 100 as a fuel additive in intake charge has an effect on the combustion process of the CNG engine. The peak in-cylinder pressure increases from 50.64 bar at a crank angle of 375 degrees to close to 57 bar at a crank angle of 367 degrees. In addition, the emission of air pollution was also evaluated when the CNG engine operated with fuel additive. The CO and HC emission reduces in both full load and partial load conditions. The CO emission reduces 36.1% and 18.4% on average at full load and partial load conditions, respectively. The HC emission reduces 37.1% and 35.0% on average at full load and partial load condition, respectively. The NOx emission tends to decrease when the engine operates at high-speed and full opened throttle. However, the NOx emission increases slightly when the engine operates at full opened throttle and low-speed regimes. At partial load condition and speed of 3000 rpm, the NOx emission reduces 22.6% on average. The CO2 emission decreases approximately 4.0% and 4.5% on average at full load and partial load condition as the CNG engine operating with fuel additive.
Nomenclature
ETB: High dynamic engine testbed
CEB: Combustion Emission Bench
NDIR: Non-Dispersive Infrared
THC: Total Hydrocarbon Content
FID: Flame Ionization Detector
CLD: Chemiluminescence Detector
Acknowledgments
The authors gratefully acknowledge Research Center for Engines, Fuels and Emissions, School of Transportation Engineering, Hanoi University of Science and Technology, Vietnam for experimental equipment support.
Disclosure statement
No potential conflict of interest was reported by the authors.
Additional information
Notes on contributors
Vinh Duy
Vinh Nguyen is lecturer in Faculty of Vehicle and Energy Engineering, Phenikaa University.
Khanh Duc
Khanh Duc is lecturer in Department of Internal Combustion Engine, School of Transportation Engineering, Hanoi University of Science and Technology.
Trung Nguyen Thanh
Trung Nguyen Thanh is lecturer in Automotive Engineering Faculty, College of Agricultural Mechanics.
Long Dinh
Long Hoang Dinh is lecturer in Department of Internal Combustion Engine, School of Transportation Engineering, Hanoi University of Science and Technology.
Tuan Le Anh
Tuan Le Anh is professor and dean of School of Transportation Engineering, Hanoi University of Science and Technology.
References
- Alrazen, H. A., and K. A. Ahmad. 2018. HCNG fueled spark-ignition (SI) engine with its effects on performance and emissions. Renewable Sustainable Energy Rev. 82:324–42. doi:10.1016/j.rser.2017.09.035.
- Appavu, P., and M. Venkata Ramanan. 2018. Study of emission characteristics of a diesel engine using cerium oxide nanoparticle blended pongamia methyl ester. Int. J. Ambient Energy. doi:10.1080/01430750.2018.1477063.
- Aslam, M. U., H. H. Masjuki, M. A. Kalam, H. Abdesselam, T. M. I. Mahlia, and M. A. Amalina. 2006. An experimental investigation of CNG as an alternative fuel for a retrofitted gasoline vehicle. Fuel 85:717–24. doi:10.1016/j.fuel.2005.09.004.
- Barros Zárante, P. H., and J. R. Sodré. 2009. Evaluating carbon emissions reduction by use of natural gas as engine fuel. J. Nat. Gas Sci. Eng. 1 (6):216–20. doi:10.1016/j.jngse.2009.11.002.
- Dhyani, V., and K. A. Subramanian. 2019. Experimental based comparative exergy analysis of a multi-cylinder spark ignition engine fuelled with different gaseous (CNG, HCNG, and hydrogen) fuels. Int. J. Hydrogen Energy 44:20440–51. doi:10.1016/j.ijhydene.2019.05.229.
- Duc, K. N., and V. N. Duy. 2018. Study on performance enhancement and emission reduction of used fuel-injected motorcycles using bi-fuel gasoline-LPG. Energy Sustainable Dev. 43:60–67. doi:10.1016/j.esd.2017.12.005.
- Duc, K. N., H. N. Tien, and V. N. Duy. 2016. Performance enhancement and emission reduction of used motorcycles using flexible fuel technology. J. Energy Inst. 2–9. doi:10.1016/j.joei.2016.09.004.
- Elfasakhany, A. 2016. Performance and emissions analysis on using acetone–gasoline fuel blends in spark-ignition engine. Eng. Sci. Technol. Int. J. 19 (3):1224–32. doi:10.1016/j.jestch.2016.02.002.
- Evans, R. L., and J. Blaszczyk. 2005. A comparative study of the performance and exhaust emissions of a spark ignition engine fueled by natural gas and gasoline. Proc. Inst. Mech. Eng. Part D J. Automob. Eng. 211:39–47. doi:10.1243/0954407971526209.
- Flynn, P. F., G. L. Hunter, L. Farrel, R. P. Durrett, O. Akinyemi, A. O. Zur Loye, … W. J. Pitz. 2000. The inevitability of engine-out NOx emissions from spark-ignited and diesel engines. Proc. Combust. Inst. 28 (1):1211–18. doi:10.1016/s0082-0784(00)80332-x.
- Guardiola, C., P. Olmeda, B. Pla, and P. Bares. 2016. In-cylinder pressure based model for exhaust temperature estimation in internal combustion engines. Appl. Therm. Eng. doi:10.1016/j.applthermaleng.2016.12.092.
- Gunawan, R., and T. Y. Zaenuri (2010). Maz technology – The detergency combustion control package for gasoline, diesel, ethanol and biodiesel to promote efficiency and cleaner emission. Proceedings of Conference on Lanlian Maz Oil-saving and Emission – reducing fuel oil additive, Beijing – China 13 June, 2010.
- Hosmath, R. S., N. R. Banapurmath, S. V. Khandal, V. N. Gaitonde, Y. H. Basavarajappa, and V. S. Yaliwal. 2016. Effect of compression ratio, CNG flow rate and injection timing on the performance of dual fuel engine operated on honge oil methyl ester (HOME) and compressed natural gas (CNG). Renewable Energy 93:579–90. doi:10.1016/j.renene.2016.03.010.
- Huang, J., and R. J. Crookes. 1998. Assessment of simulated biogas as a fuel for the spark ignition engine. Fuel 77:1793–801. doi:10.1016/S0016-2361(98)00114-8.
- Huang, Z., X. Qiao, W. Zhang, J. Wu, and J. Zhang. 2009. Dimethyl ether as alternative fuel for CI engine and vehicle. Front. Energy Power Eng. China 3:99–108. doi:10.1007/s11708-009-0013-1.
- Huang, Z., J. Wang, B. Liu, K. Zeng, J. Yu, and D. Jiang. 2007. Combustion characteristics of a direct-injection engine fueled with natural gas–hydrogen blends under different ignition timings. Fuel 86 (3):381–87. doi:10.1016/j.fuel.2006.07.007.
- Javed, S., Y. V. V. S. Murthy, R. U. Baig, and T. N. Rao. 2016. Vibration analysis of a diesel engine using biodiesel fuel blended with nano particles by dual fueling of hydrogen. J. Nat. Gas Sci. Eng. 33:217–30. doi:10.1016/j.jngse.2016.05.026.
- Kalam, M. A., and H. H. Masjuki. 2011. An experimental investigation of high performance natural gas engine with direct injection. Energy 36:3563–71. doi:10.1016/j.energy.2011.03.066.
- Kaleemuddin, S., and G. Amba Prasad Rao. 2009. Development of dual fuel single cylinder natural gas engine an analysis and experimental investigation for performance and emission. American J. Appl. Sci. 6 (5):929–36. doi:10.3844/ajassp.2009.929.936.
- Karagöz, Y., T. Sandalcı, U. O. Koylu, A. S. Dalkılıç, and S. Wongwises. 2016. Effect of the use of natural gas–diesel fuel mixture on performance, emissions, and combustion characteristics of a compression ignition engine. Adv. Mech. Eng. 8 (4):168781401664322. doi:10.1177/1687814016643228.
- Karthikeyan, S., A. Elango, and A. Prathima. 2016. The effect of cerium oxide additive on the performance and emission characteristics of a CI engine operated with rice bran biodiesel and its blends. Int. J. Green Energy 13 (3):267–73. doi:10.1080/15435075.2014.952419.
- Kato, K., K. Igarashi, M. Masuda, K. Otsubo, A. Yasuda, K. Takeda, and T. Sato. 1999. Development of engine for natural gas vehicle. SAE Trans. 108:939–47. doi:10.4271/1999-01-0574.
- Lapuerta, M., O. Armas, and J. J. Hern´andez. 1999. Diagnosis of DI diesel combustion from in-cylinder pressure signal by estimation of mean thermodynamic properties of the gas. Appl. Therm. Eng. 19 (5):513–29. doi:10.1016/S1359-4311(98)00075-1.
- Le Anh, T., K. Nguyen Duc, H. Tran Thi Thu, and T. Cao Van. 2013. Improving performance and reducing pollution emissions of a carburetor gasoline engine by adding HHO gas into the intake manifold. SAE Technical Paper 2013-01-0104. doi: 10.4271/2013-01-0104.
- Lim, F. 2010. Maz fuel additive for boiler gas fuel. Proceedings of the Conference on Lanlian Maz Oil-saving and Emission – reducing fuel oil additive, Beijing – China 13 June, 2010.
- Long, H. D. 2010a. More miles for less fuel – A study of fuel additive on motorcycles. J. Sci. Technol. Tech. Univ. 79:154–58. ISSN 0868-3980.
- Long, H. D., Maz 100 & Maz 200 fuel additive – Testing results and evaluation, Proceedings of Conference on Lanlian Maz Oil-saving and Emission – reducing fuel oil additive, Beijing – China 13 June, 2010b.
- Nebel, G. J., and M. W. Jackson. 1958. Some factors affecting the concentration of oxides of nitrogen in exhaust gases from spark ignition engines. J. Air Pollut. Control Assoc. 8 (3):213–19. doi:10.1080/00966665.1958.10467847.
- Nguyen Duc, K., V. Nguyen Duy, L. Hoang-Dinh, T. Nguyen Viet, and T. Le-Anh. 2019. Performance and emission characteristics of a port fuel injected, spark ignition engine fueled by compressed natural gas. Sustainable Energy Technol. Assess. 31:383–89. doi:10.1016/j.seta.2018.12.018.
- Orhan Akansu, S., Z. Dulger, N. Kahraman, and T. N. Veziroǧlu. 2004. Internal combustion engines fueled by natural gas-hydrogen mixtures. Int. J. Hydrogen Energy 29:1527–39. doi:10.1016/j.ijhydene.2004.01.018.
- Özgür, T., M. Özcanli, and K. Aydin. 2015. Investigation of nanoparticle additives to biodiesel for improvement of the performance and exhaust emissions in a compression ignition engine. Int. J. Green Energy 12 (1):51–56. doi:10.1080/15435075.2014.889011.
- Park, H., E. Shim, and C. Bae. 2019. Injection strategy in natural gas-diesel dual-fuel premixed charge compression ignition combustion under low load conditions. Engineering 5:548–57. doi:10.1016/j.eng.2019.03.005.
- Poulopoulos, S. G., and C. J. Philippopoulos. 2001. Speciated hydrocarbon and carbon monoxide emissions from an internal combustion engine operating on methyl tertiary butyl ether-containing fuels. J. Air Waste Manage. Assoc. 51 (7):992–1000. doi:10.1080/10473289.2001.10464323.
- Pourkhesalian, A. M., A. H. Shamekhi, and F. Salimi. 2010. Alternative fuel and gasoline in an SI engine: A comparative study of performance and emissions characteristics. Fuel 89:1056–63. doi:10.1016/j.fuel.2009.11.025.
- Ran, Z., D. Hariharan, B. Lawler, and S. Mamalis. 2020 January 15. Exploring the potential of ethanol, CNG, and syngas as fuels for lean spark-ignition combustion - An experimental study. Energy Vol. 191:116520. doi: 10.1016/j.energy.2019.116520.
- Reddy, H., and J. Abraham. 2013. Influence of turbulence–kernel interactions on flame development in lean methane/air mixtures under natural gas-fueled engine conditions. Fuel 103:1090–105. doi:10.1016/j.fuel.2012.07.074.
- Tahir, M. M., M. S. Ali, M. A. Salim, R. A. Bakar, A. M. Fudhail, M. Z. Hassan, and M. S. A. Muhaimin. 2015. Performance analysis of a spark ignition engine using compressed natural gas (CNG) as fuel. Energy Procedia 68:355–62. doi:10.1016/j.egypro.2015.03.266.
- Ting, D. S. K., and M. D. Checkel (1995), The effects of turbulence on spark-ignited, ultra lean, premixed methane–air flame growth in a combustion chamber, SAE Paper 952410.
- Xu, C. C., and H. M. Cho. 2016. The study of the effect of the natural gas in the CNG engine. Int. J. Appl. Eng. Res. 11:7688–90.
- Yan, F., L. Xu, and Y. Wang. 2018. Application of hydrogen enriched natural gas in spark ignition IC engines: From fundamental fuel properties to engine performances and emissions. Renewable Sustainable Energy Rev. 82:1457–88. doi:10.1016/j.rser.2017.05.227.
- Yao, Z., X. Cao, X. Shen, Y. Zhang, X. Wang, and K. He. 2014. On-road emission characteristics of CNG-fueled bi-fuel taxis. Atmos. Environ. 94:198–204. doi:10.1016/j.atmosenv.2014.05.027.
- Yiming, G., F. Lim, C. Ruibing, Q. Weizhou, and W. Mingding. 2004. China to explore and set its independent fuel standards – Application research on MAZ Fuel additive. SAE Technical Paper 2004-01-2938.
- Yontar, A. A., and Y. Doğu. 2018a. Investigation of the effects of gasoline and CNG fuels on a dual sequential ignition engine at low and high load conditions. Fuel 232:114–23. doi:10.1016/j.fuel.2018.05.156.
- Yontar, A. A., and Y. Doğu. 2018b. Experimental and numerical investigation of effects of CNG and gasoline fuels on engine performance and emissions in a dual sequential spark ignition engine. Energy Sources Part A 1–17. doi:10.1080/15567036.2018.1495783.
- Yontar, A. A., and Y. Doğu. 2019. Effects of equivalence ratio and CNG addition on engine performance and emissions in a dual sequential ignition engine. Int. J. Engine Res. 146808741983419. doi:10.1177/1468087419834190.
- Zhang, C. H., Y. L. Xie, F. S. Wang, Z. Y. Ma, D. H. Qi, and Z. W. Qiu. 2011. Emission comparison of light-duty in-use flexible-fuel vehicles fueled with gasoline and compressed natural gas based on the ECE 15 driving cycle. Proc. Inst. Mech. Eng. Part D J. Automob. Eng. 225:90–98. doi:10.1243/09544070JAUTO1510.