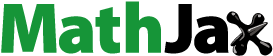
ABSTRACT
A novel process for recovering manganese (Mn) values from two types of ferromanganese (FeMn) fumes (wastes from smelters) was developed incorporating several stages of leaching, roasting, and precipitation. Fumes containing high K (as K2O) were first leached in water at ambient conditions to recover K, purified to remove metal impurities, and precipitated as 99.9% pure K2SO4. The residues containing Mn and remaining impurities were then leached in sulfuric acid at 80 °C using oxalic acid as reductant yielding Mn sulphate liquors. The leach liquors were then purified to remove Fe at 95°C as jarosite at pH 2.8 and Fe(III) hydroxides at pH 5.5. Base and transition metal impurities were removed as sulfides. K, Na, Ca, and Mg were separated from Mn in a novel step based on precipitation of Mn hydroxide from the Mn sulphate liquors. Subsequent redissolution of Mn hydroxide in sulfuric acid under reducing conditions using oxalic acid produced a high purity Mn sulphate liquors containing <5 ppm of these impurities. After evaporation by boiling manganese sulphate monohydrate (MSM) was crystallized, achieving purity >99.5%. Another fume containing oil contaminants having low K was subjected to sulfation roasting to produce Mn sulphate. The calcine was water leached to produce Mn sulfate liquors and treated in a similar process to make high purity MSM. Novelty aspects of the proposed process include the recovery of K as a by-product and separation of Mn2+ from other impurities by its selective precipitation to produce a high purity Mn sulphate solution for MSM recovery.
Implications: Ferro-manganese smelters discharge wastes (fumes) that are collected by bag filters or electrostatic precipitators and then store them on the ground with coverage to prevent their dispersion into the surrounding atmosphere. The work presented propose a process to reprocess these wastes into high purity manganese sulphate monohydrate (MSM). Processing of wastes containing high potassium as KOH also yields high purity potassium sulfate used as fertilizers. Some smelters spray oil onto the fume dumps to prevent material being blown onto the surrounding area. The oil-contaminated fumes have to be first roasted to burn off the oil, before they can be processed. The process developed therefore converts a hazardous waste into high purity MSM and potassium sulphate used in many applications.
Introduction
High purity manganese sulphate monohydrate, MSM (MnSO4.H2O) has found increasing use as a precursor for the making of electrolytic manganese dioxide (EMD) used in alkaline batteries. MSM is also a major component in the making of Ni-Co-Mn-Li oxide cathode materials of Li-ion battery. Resources of manganese are generally from ores, ocean nodules, or secondary materials containing pyrolusite/MnO2 or rhodochrosite/MnCO3 minerals (Liu et al. Citation2019) mixed with other minerals of iron, base metals, and clay containing Ca, Mg, Al, and Si, etc. Another source of manganese also comes from fumes generated from smelters and electric arc furnaces making ferro-manganese (FeMn) alloys used in specialty steel making (Gaal, Tangstad, and Ravary Citation2010).
Processing and recovering of Mn values from the above resources vary greatly depending on the nature and mineral form of the Mn resources (Zhang and Cheng Citation2007). Extraction of manganese from traditional MnO2 containing ores requires roasting using a reductant such as C, CO, H2, SO2, etc. (Liu et al. Citation2019, Citation2018; Sahoo and Rao Citation1989; You et al., Citation2015; Zhang and Cheng Citation2007; Zhang et al. Citation2017, Citation2015), producing MnO before acid dissolution. The ores can also be directly treated in a hydrometallurgical route based on acid leaching and inorganic reductants such as SO2, FeSO4, Fe scraps, pyrite, etc. (Bafghi et al. Citation2008; Cai et al. Citation2019; Lu et al., Citation2016; Naik, Sukla, and Das Citation2000; Vu et al. Citation2005), and organic matters (Liu et al. Citation2019; Tang et al. Citation2014).
Ocean nodules as rich sources of Mn, Co, Cu, and Ni, are currently drawing great attention as most high-grade Mn resources on dry land are dwindling (Abramovski et al. Citation2017; Vereshchagina et al. Citation2019). As these nodules contain mainly manganese dioxide the extraction techniques are either via reduction roasting or leaching as above. As these resources also contain high grades of Cu, Ni, Co the processing techniques are more complex involving the recovery and purification of these metal values (Randhawa, Hait, and Jana Citation2016).
Smelters or electric arc furnaces used for producing ferro-manganese or silicon-manganese alloys used in special steel production release fumes from their stacks which are harmful materials to the environment. Toxic chemicals in the atmospheric waste discharge/fumes are harmful to human health (Lucas et al. Citation2015), although tremendous efforts by plant operators have been spent to prevent the wastes stored on the open ground from spreading into the surrounding air. Although there have been many studies reported in the literature on the recycling of these materials mainly back to the ferro-manganese smelters or electric arc furnaces, several impurities such as Zn, Pb, carbonaceous substances in the wastes are causing difficulties in their re-use (Gaal, Tangstad, and Ravary Citation2010; Ordiales et al. Citation2016; Shen et al. Citation2007).
Most studies in the literature evaluated techniques for recovery of Mn values as Mn metal, electrolytic manganese dioxide (EMD), or chemical manganese dioxide (CMD) used in the manufacturing of steel and alkaline dry cell batteries. High purity (>99%) manganese sulphate monohydrate (MSM) currently used in the making of cathode materials for Li-ion batteries has not been made from the available resources using conventional techniques as impurities such as Fe, Ni, Co, Cr, etc., have to be removed to ppm levels. Although known techniques for removing iron as Fe(OH)3 or jarosite (Dutrizac Citation2008; Tam and Tran Citation1991) and other base metals using hydroxide and sulfide precipitation (Grootscholten, Keesman, and Lens Citation2008; Lewis Citation2010; Veeken et al., Citation2003) could be applied, the novel process developed in this study involved a three-stage purification in which the above metal impurities were first removed. This paper describes the conditions for making >99.5% pure MSM using the developed process.
Experimental procedures
Raw materials and chemicals
The FeMn fumes used in this study were collected from two different sources. The high potassium fume was from SIMPAC electric arc furnaces operating in Pohang, South Korea. The other sample contaminated with oil was collected from an outdoor waste dump discharged by TEMCO Ltd. in Tasmania, Australia. XRD analysis results showed that most of the Mn existed as MnO⋅Mn2O3(Mn3O4) in both samples (). The compositions of these FeMn fumes are tabulated in . Due to different natures of the fume samples, different processing steps have to be incorporated to recover K from the SIMPAC fumes (as the main impurity if left in the final MSM product) or to burn off the oil component of the TEMCO material. All of the chemicals (Na2S, H2O2, sulfuric acid, etc.) used in this study are of analytical grade supplied by Duksan Korea.
Table 1. Compositions of FeMn fumes used in this study.
Equipment
The study involves the use of equipment and software for analyzing the process, materials, and products. Stabcal and HSC chemistry softwares were used to model the speciation of the process conditions involved in Mn hydroxide precipitation. X-Ray Diffraction (XRD) patterns were measured using a Rigaku MiniFlex 600 diffractometer. All solution compositions are determined using an ICP-OES (GENESIS FES). Roasting of the FeMn fumes requires the use of a muffle furnace (Ajeon Heating Industrial ABN 102 c).
Experimental methodology
The two different sources of fumes above have been subjected to several treatment stages summarized in the flowsheet shown in . The high potassium (K) FeMn fumes contain >30% K as K2O was easily leached using water, virtually producing concentrated KOH liquors. For SIMPAC FeMn fumes, K was first leached using de-ionized water. The remaining Mn containing residues were then leached in diluted sulfuric acid to produce Mn sulphate liquors using 2 M oxalic acid solution as a reductant. Added reagents were calculated from Mn level in the solution at H2SO4/Mn and H2C2O4/Mn2O3 molar ratios of 1.15:1 and 1.1:1, respectively.
The TEMCO oil containing FeMn dust, on the other hand, was mixed with concentrated sulfuric acid (98%) at 1.5:1 H2SO4/Mn molar ratio and roasted at 500°C for 3 hrs in the muffle furnace. This was to burn off the oil used for de-dusting of the waste dump to prevent the fine dust blown off into the surrounding atmosphere. The oil component also acted as a reductant during the acid roasting, converting most Mn values and other metals to sulphate forms.
The produced SIMPAC fumes were then water leached to extract Mn values together with other impurities such as Fe, Co, Ni, Cu, Zn, Pb, etc., and other potential elements of the final MSM products such as remaining K, Na, Ca, and Mg. In the leaching step, hydrogen peroxide (28%) was added at 1.2:1 H2O2/Fe molar ratio to oxidize Fe(II) to Fe(III) and maintaining Fe(III) level in the solution. The leached liquor was then subjected to a three-stage purification, involving 1) precipitation of jarosite and Fe hydroxides; 2) sulfides of base and transition metals; and, 3) finally Mn hydroxide to separate other elements such as K, Na, Ca, and Mg using a round bottom glass reactor incorporating a motored stirrer and fitted with a reflux condenser. When heating was required a heating mantle was used with temperature controlled to ± 1°C. The same reactor was also used for precipitation of Fe as jarosite (at 95°C) and other metal impurities using Na2S. The Mn hydroxide was then re-dissolved in sulfuric acid to produce a high purity Mn sulphate solution from which high purity MSM product was then re-crystallized after evaporation via boiling. Details of all steps involved will be presented in detail in the following sections.
The extra step required for processing the SIMPAC fumes includes the leaching of K using water, in a 6-stage counter-current water leaching () to concentrate the potassium levels to 210 g/L K in liquors having pH >14. Subsequent purification yielded K liquors free of metal ions, which were then subjected to reaction with H2SO4 to precipitate high purity K2SO4.
Results and discussion
Potassium leaching and recovery
The leaching of the K2O from the SIMPAC fumes yielded very strong KOH solutions. In a single pass leaching, the K recovered reached 43.9 g/L K. A multi-stage water leaching was implemented and this would yield a final KOH liquor having concentration up to 210.7 g/L K, facilitating the precipitation of the final K2SO4 product to achieve >80% recovery as the solubility of this compound is at ~30 g/L K as predicted from Stabcal modeling shown in . The K leaching efficiency decreasing from ~75% (Stage 1) to 55% (Stage 6) while the Mn fume slurry was maintained at a density of 20% w/v. The water leaching forming KOH and the precipitation of K sulphate releasing H+ are illustrated as the reactions below:
Figure 4. Stabcal modeling of a 210 g/L K as K2SO4 sulphate showing the equilibrium level of ~30 g/L K in the pH 7-9 range.
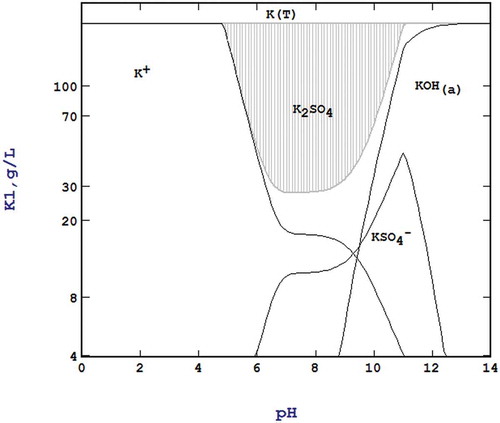
The hydroxide ions formed from the water leaching of K2O are neutralized by the H+ released according to the following reaction:
The overall reaction for the K recovery circuit therefore is:
A novelty aspect of this study is this recovery of K from the unique SIMPAC fume material without which K would severely contaminate the final liquor. Other sources of Mn used for making Mn sulphate would not be subjected to this K recovery stage.
The K2SO4 solutions contained high levels of base and transition metal impurities which have to be removed by the conventional sulfide precipitation (using Na2S/metal molar ratio of >5:1) before crystallization by pH adjustment to neutral conditions using sulfuric acid ().
A high purity K2SO4 could be produced using this process with the product composition confirmed by ICP-OES and XRD analysis shown in and , respectively.
Table 2. Composition of K2SO4 products confirming impurities of most metals below detection limits (<1 ppm).
Roasting and extraction of Mn
HSC software was used to model the roasting of Mn oxide in sulfuric acid over the temperature range 25– 1000°C. Results shown in shows the formation of MnSO4 and Fe2(SO4)3 in the temperature range 100– 500°C, according to the reactions:
Note that these sulphate processes thermodynamically take place at low temperatures as well as yielding different types of Mn and Fe sulfate.
Above 650°C, Mn2O3 and MnO2 are formed, rendering them insoluble in water. Above 500°C Fe2O3 also starts forming and is insoluble in water.
The sulfation roasting of fumes containing oil to produce Mn sulphate at temperatures in the range 400– 700°C confirmed by HSC modeling above, which shows the formation of Mn and Fe sulfate in the calcine at the optimum temperature in the range 400– 500°C to maximize Mn and minimize Fe in the leach liquors (). A low dissolved Fe in the leached solution would facilitate the filtration of the Mn sulphate solution after its precipitation (to be discussed in detail in a later section). Above 500°C Mn and Fe oxides are formed which are insoluble in water.
Figure 7. Leaching efficiency of Mn and Fe into water from calcines produced over a temperature range 400-700°C.
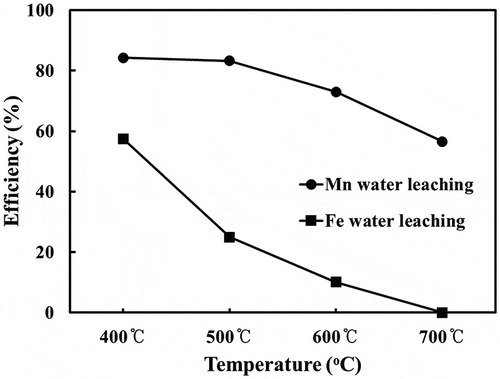
Increasing sulfuric acid during the roasting stage also affects the dissolution of the calcines in water, differently for the main constituents of the FeMn fumes, namely, Mn, Fe, and Zn. A higher sulfuric acid addition does not increase the Mn extraction as much compared to that of Fe as shown in .
Figure 8. Effect of Mn/H2SO molar ratio showing more Fe is dissolved during water leaching at higher acid used during roasting of FeMn fumes (Conditions: 500°C, 3 hrs).
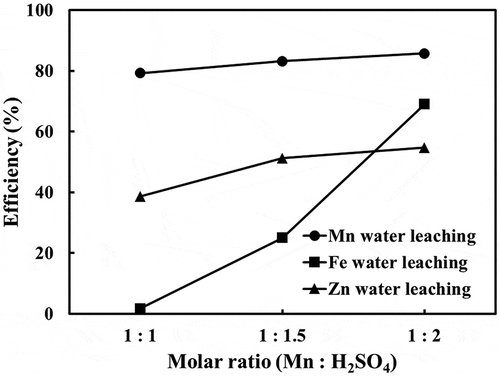
The SIMPAC Mn containing residues that have been subjected to K extraction during the water leaching stage were then leached in sulfuric acid at 80°C and at a slurry density of 20% w/v in the presence of oxalic acid to dissolve the MnO·Mn2O3 material into solution. The intermittent addition of oxalic acid causes the Eh and pH of the solution to oscillate as shown in . To maintain Fe in the solution as Fe3+ for precipitating jarosite (KFe3(SO4)2(OH)6) the solution Eh was maintained at >800 mV vs standard calomel electrode until it reached a steady state after 150 min of leaching.
Figure 9. Variation of Eh and pH during reduction sulphuric acid leaching using oxalic acid reductant.
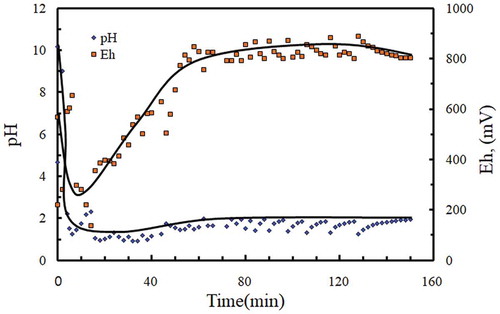
The typical composition shown in shows high levels of Mn and other impurities in the leach liquors. High extraction efficiency (>60%) was achieved for most impurities with 97% Mn extracted. Ca level was controlled by gypsum CaSO4 formation and stayed low at 0.29 g/L.
Table 3. Typical composition of Mn sulphate leach liquors.
To produce MSM, all metal impurities have to be removed to ppm levels. Elements such as Ca, K, Na, or Mg if not removed would potentially also co-crystallize with Mn sulphate, contaminating the final product.
While Fe and other metal impurities can be removed by conventional technique as reviewed in the literature survey presented in the Introduction section (Dutrizac Citation1983), such as precipitation of jarosite or Fe hydroxide and metal sulfides, K, Na, Ca, Mg cannot be removed by precipitation techniques. The purification of the above liquors requires a 3-stage process described in the following sections.
Removal of Fe and other metal impurities
A complex scheme of 3-stage purification was developed to remove major impurities (Fe, Al, Zn, Pb, Cu, Co, Ni) and elements (K, Na, Ca, and Mg) from the liquors. Fe, mainly as Fe3+ if the Eh was controlled at >800 mV () was mostly removed by jarosite precipitation at pH 2– 3 and 95°C. As reviewed by Dutrizac (Citation2008) and illustrated in a study by Tam and Tran (Citation1991) the efficacy of Fe removal and the rate of precipitation are controlled by the K/Fe molar ratio. The presence of high level of K in the leach liquors in this study facilitates the precipitation of jarosite to reduce both K and Fe simultaneously. After jarosite precipitation lime was added to adjust the pH to pH 5.5 to remove residual Fe as Fe (III) hydroxides.
The removal of Fe can be illustrated by the following reactions:
Na2S was then used to precipitate heavy and transition metals at molar ratio of Na2S/(total metal) >5:1 at ambient conditions. As reviewed by Lewis (Citation2010), residual Fe, Cu, Zn, Co, Ni, and other transition metals will be precipitated as sulfides to ppm ranges using sulfide/metal ion molar ratio in the range 5– 20:1.
The sulfide precipitation reactions can be represented by:
shows the conditions of the Mn sulphate solutions through various stages of Fe and other metal purification. Fe, Zn as main impurities as well as other metals were removed to less than detection limits after the 2-stage purification.
Table 4. Conditions of the Mn sulphate liquors through various stages of Fe and other metal purification.
It is noted that levels of K, Mg, Ca, and Na are still high in the liquors after the first two purification stages. The reduction of Mn concentration was mainly due to dilution when reagents were added during the precipitation stages whereas Ca level increased in steps where lime was used for neutralization.
Separation of Ca, Mg, K and Na
The third stage of purification to remove K, Na, Ca, and Mg was conducted via a novel step in which Mn was precipitated as hydroxide by adding NaOH leaving these elements behind. Stabcal modeling () showed that Mn could be precipitated as hydroxide in the range pH 6.5– 8.5 (shaded zone of ) leaving K, Ca, and Mg in the liquor (). As shown , after Mn precipitation, K, Mg, and Ca remained in solution, based on the mass balance of each element in the liquors before and after precipitation. Therefore, most impurities were not precipitated with Mn.
Table 5. Composition of the diluted Mn solution and after Mn precipitation using sodium hydroxide.
Figure 10. Stabcal modelling showing the pH range (pH 6.5-8.5) for selective precipitation of Mn hydroxide.
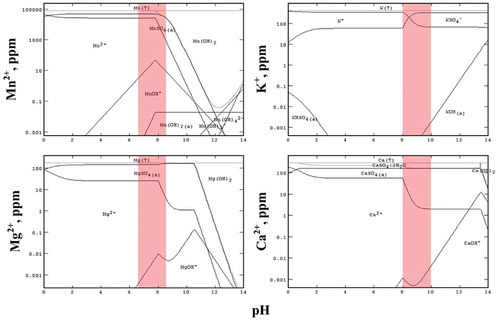
Experimental results confirmed the modeling prediction during a typical precipitation run () showing 99% of Mn was recovered from this stage. The brownish precipitate obtained indicated the presence of MnOOH (Mn3+) in the mixture of Mn hydroxide, which requires the addition of H2O2 and sulfuric acid to redissolve all Mn values as Mn2+ in Mn sulphate. H2O2 has a lower potential than Mn3+ (as in MnOOH) and Mn4+ (as in MnO2) thus converts all Mn to Mn2+ as Mn sulphate, typically recognized as a pink solution compared to a reddish color liquor if Mn3+ co-exists. The acidic Mn sulphate then requires neutralization using minimal amounts of high purity MnO (>99%) to produce a neutral Mn sulphate liquor having very low impurities (<5 ppm) of K, Na, Ca, and Mg (). Subsequent evaporation to concentrate the liquor by boiling then produces MSM crystals to be recovered by centrifuging.
Table 6. Typical composition of the high purity Mn sulphate solution before MSM crystallization.
The novel steps involved in separating Ca, Mg, K, and Na from the Mn by precipitating the Mn values developed herewith allows the production of >99.5% pure MSM compared to commercial products ().
Table 7. Composition of the MSM products produced from this study compared to commercial specifications.
XRD and DTA analysis ( and ) confirm the manganese sulphate monohydrate as the final product produced from this novel process.
Conclusion
High purity manganese sulphate monohydrate, MSM (MnSO4.H2O) was produced from two types of FeMn smelter wastes (fumes) using a novel process developed incorporating several stages of leaching, roasting, and precipitation. Fumes containing high K (as K2O) from SIMPAC (Korea) were first leached in water at ambient conditions to render K as KOH solutions. This represents a novel process step as most Mn sources do not contain high levels of K, which would severely contaminate the final MSM product. The leached solution of pH >14 was purified to remove metal impurities (Fe, base, and transition metals such as Pb, Zn, Cu, Co, Ni) and precipitated as 99.9% pure K2SO4 by pH adjustment to neutral conditions using sulfuric acid. The residues containing Mn and remaining impurities were then leached in sulfuric acid at 80°C using oxalic acid as reductant yielding impure Mn sulphate liquors containing the same impurities above. The leach liquors were then purified to remove Fe at 95°C as jarosite at pH 2.8 and Fe (III) hydroxides at pH 5.5. Base and transition metal impurities were removed as sulfides.
A novel step based on precipitation of Mn hydroxide from the Mn sulphate liquors by adding NaOH to pH 8.5 separating Mn from K, Na, Ca, and Mg remaining in the liquors. Subsequent re-dissolution of Mn hydroxide in sulfuric acid under reducing conditions using oxalic acid produced a high purity Mn sulphate liquors containing <5 ppm of these impurities. After evaporation by boiling,>99.5% pure manganese sulphate monohydrate (MSM) was crystallized. Another fume containing oil contaminants having low K was subjected to sulfation roasting to produce Mn sulphate. The calcine was water leached to produce Mn sulphate liquors and treated in a similar process to make high purity MSM.
Disclosure statement
No potential conflict of interest was reported by the authors.
Additional information
Notes on contributors
Yeon Ho Lee
Yeon Ho Lee got his Ph.D. from Chonnam National University in 2018.
Jong Hyeok Kang
Jong Hyeok Kang is a Master's student at Chonnam National University.
Sangyun Seo
Sangyun Seo is a senior researcher at Korea Resources Corporation and currently studying Mineral Economics for his secondary PhD at Curtin University.
Tam Tran
Tam Tran and Myong Jun Kim are professors at the Department of Energy and Resources Engineering at Chonnam National University.
Myong Jun Kim
Tam Tran and Myong Jun Kim are professors at the Department of Energy and Resources Engineering at Chonnam National University.
References
- Abramovski, T., V. P. Stefanova, R. Causse, and A. Romanchuk. 2017. Technologies for the processing of polymetallic nodules from Clarion Clipperton zone in the Pacific Ocean. J. Chem. Technol. Metall. 52 (2):258–69.
- Bafghi, M. S., A. Zaker, Z. Ghasemin, and M. Adel. 2008. Reductive dissolution of manganese ore in sulphuric acid in the presence of iron metal. Hydrometallurgy 90 (2):207–12. doi:10.1016/j.hydromet.2007.07.003.
- Cai, X., F. Shen, Y. Zhang, H. Hu, Z. Huang, Y. Yin, X. Liang, Y. Qin, and J. Liang. 2019. Mineralisation of organics in hazardous waste sulphuric acid by natural manganese oxide ore and a combined MnO2/activated carbon treatment to produce qualified manganese sulphate. J. Hazard. Mater. 366:466–74. doi:10.1016/j.jhazmat.2018.12.021.
- Dutrizac, J. E. 1983. Factors affecting alkali jarosite. Metall. Trans B 14:531–39. doi:10.1007/BF02653939.
- Dutrizac, J. E. 2008. Factors affecting the precipitation of potassium jarosite in sulphate and chloride media. Metall. Mater. Trans B 39:771–83. doi:10.1007/s11663-008-9198-7.
- Gaal, S., M. Tangstad, and B. Ravary. 2010. Recycling of waste materials from the production of FeMn and SiMn. The Twelfth International Ferroalloys Congress Sustainable Future. Helsinki, Finland. June 6–9. Accessed July 1, 2019. https://www.pyrometallurgy.co.za/InfaconXII/081-Gaal.pdf.
- Grootscholten, T., K. Keesman, and P. Lens. 2008. Modelling and on-line estimation of zinc sulphide precipitation in a continuously stirred tank reactor. Sep. Purif. Technol. 63:654–60. doi:10.1016/j.seppur.2008.07.004.
- Lewis, A. E. 2010. Review of metal sulphide precipitation. Hydrometallurgy 104:222–34. doi:10.1016/j.hydromet.2010.06.010.
- Liu, B., Y. Zhang, M. Lu, Z. Su, G. Li, and T. Jiang. 2019. Extraction and separation of manganese and iron from ferruginous manganese ores: A review. Miner. Eng. 131:286–303. doi:10.1016/j.mineng.2018.11.016.
- Liu, B. B., Y. B. Zhang, J. Wang, Z. J. Su, G. H. Li, and T. Jiang. 2018. New understanding on separation of Mn and Fe from ferruginous manganese ores by the magnetic reduction roasting process. Appl. Surf. Sci. 444:133–44. doi:10.1016/j.apsusc.2018.02.234.
- Lu, J. M., D. Dreisinger, and T. Glück. 2016. Electrolytic manganese metal production from manganese carbonate precipitate. Hydrometallurgy 161:45–53. doi:10.1016/j.hydromet.2016.01.010.
- Lucas, E. L., L. Bertrand, S. Guazzetti, F. Donna, F. M. Feli, T. R. Jursa, R. Lucchini, and D. R. Smith. 2015. Impact of ferromanganese alloy plants on household dust manganese levels: Implications for childhood exposure. Environ. Res. April 138:279–90. doi:10.1016/j.envres.2015.01.019.
- Naik, P. K., L. B. Sukla, and S. C. Das. 2000. Aqueous SO2 leaching studies on Nishikhal manganese ore through factorial experiment. Hydrometallurgy 54:217–28. doi:10.1016/S0304-386X(99)00075-4.
- Ordiales, M., J. Iglesias, D. Fernández-González, J. Sancho-Gorostiaga, A. Fuentes, and L. F. Verdeja. 2016. Cold agglomeration of ultrafine oxidized dust (UOD) from ferromanganese and silicomanganese industrial process. Metals 6:203–08. doi:10.3390/met6090203.
- Randhawa, N. S., J. Hait, and R. K. Jana. 2016. A brief overview on manganese nodules processing signifying the detail in the Indian context highlighting the international scenario. Hydrometallurgy 165:166–81. doi:10.1016/j.hydromet.2015.09.013.
- Sahoo, P. K., and K. S. Rao. 1989. Sulphation roasting of low grade manganese ore optimisation by factorial design. Int. J. Min. Proc. 25 (1–2):147–52. doi:10.1016/0301-7516(89)90061-6.
- Shen, R., G. Zhang, M. Dell’Amico, P. Brown, and O. Ostrovski. 2007. A feasibility study of recycling of manganese furnace dust. Innovation in Ferro Alloys Industry - INFACON XI, 507–19.
- Tam, T. H., and T. Tran. 1991. Kinetic study on the precipitation of alunite from manganese sulphate solutions. Hydrometallurgy 27:85–97. doi:10.1016/0304-386X(91)90080-6.
- Tang, Q., H. Zhong, S. Wang, J. Li, and G. Liu. 2014. Reductive leaching of manganese oxide ores using waste tea as reductant in sulphuric acid solution. Trans. Nonferrous Met. Soc. China 24:861–67. doi:10.1016/S1003-6326(14)63136-8.
- Veeken, A. H. M., L. Akoto, L. W. H. Pol, and J. Weijma. 2003. Control of the sulphide (S2-) concentration for optimal zinc removal by sulfide precipitation in a continuously stirred tank reactor. Water Res. 37:3709–17. doi:10.1016/S0043-1354(03)00262-8.
- Vereshchagina, O. S., E. N. Perovaa, A. I. Brusnitsyna, V. B. Ershovaa, A. K. Khudoleya, V. V. Shilovskikhb, and E. V. Molchanovac. 2019. Ferromanganese nodules from the Kara Sea: Mineralogy, geochemistry and genesis. Ore. Geol. Rev. 106:192–204.
- Vu, H., J. Jandova, K. Lisa, and F. Vranka. 2005. Leaching of Mn deep ocean modules in FeSO4 H2SO4-H2O solutions. Hydrometallurgy 77:47–153. doi:10.1016/j.hydromet.2004.09.012.
- You, Z. X., G. H. Li, W. Zhang, Z. W. Peng, and T. Jiang. 2015. Extraction of manganese from iron rich MnO2 ores via selective sulphation roasting with SO2 followed by water leaching. Hydrometallurgy 156:225–31. doi:10.1016/j.hydromet.2015.05.017.
- Zhang, W., and C. Y. Cheng. 2007. Manganese metallurgy review. Part 1: Leaching of ores/secondary materials and recovery of electrolytic/chemical manganese dioxide. Hydrometallurgy 89:137–59. doi:10.1016/j.hydromet.2007.08.010.
- Zhang, Y., M. Du, B. Liu, Z. Su, G. Li, and T. Jiang. 2017. Separation and recovery of iron and manganese from high iron manganese oxide ores by reduction roasting and magnetic separation technique. Sep. Sci. Technol. 52:1321–32. doi:10.1080/01496395.2017.1284864.
- Zhang, Y. B., Y. Zhao, Z. X. You, D. X. Duan, G. H. Li, and G. H. T. Jiang. 2015. Manganese extraction from high-iron-content manganese oxide ores by selective reduction roasting-acid leaching process using black charcoal as reductant. J. Cent. South Univ. 22:2515–20. doi:10.1007/s11771-015-2780-7.