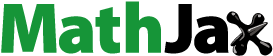
ABSTRACT
Several studies have been conducted to decrease the cost of sorbents used for the control of mercury emissions. Thus far, several sorbents with low surface areas have been reported to exhibit promising mercury removal capacities. However, based on the results reported, it is difficult to understand the mechanisms of adsorption and oxidization of elemental mercury on sorbents with low surface areas compared to those with higher surface areas. Three types of materials with different surface areas were evaluated herein for use as carbon sorbents for the adsorption of elemental mercury: (1) coal, (2) sewage sludge, and (3) unburned carbon. The respective raw sorbents and FeCl3-impreganted congeners were evaluated. Each sorbent was tested in a fixed-bed reactor system under two simulated flue gas conditions (1) without and (2) with 20 ppm hydrogen chloride (HCl). The injection of HCl increased the mercury adsorption efficiency of all tested sorbents by decreasing the emission of elemental mercury. Doping the sorbent with FeCl3 increased the mercury adsorption efficiency during the earlier test period under both simulated flue gas conditions (without and with HCl). FeCl3-impregnated activated carbon and FeCl3-impregnated unburned carbon emitted large amounts of oxidized mercury during the later test periods.
Implications: We tested three types of sorbents to investigate the mercury adsorption characteristics of sorbents with low surface area. The mercury adsorption test was conducted by varying the raw material of the sorbent, chemical impregnation of the sorbent and the simulated flue gas composition. We found that HCl in simulated flue gas increased the mercury adsorption efficiency of both the raw and FeCl3-impregnated sorbents by decreasing the emission of elemental mercury.
Introduction
Mercury has been reported to exist in three forms in combustion flue gases: elemental mercury (Hg0), oxidized mercury (Hg2+), and particulate mercury (HgP) (Galbreath and Zygarlicke Citation2000; Granite, Pennline, and Senior Citation2015; Lee and Wilcox Citation2017; UNEP Citation2013; Wilcox et al. Citation2012). Among the three forms of mercury, elemental mercury is difficult to remove using existing air pollution control devices. Injection of activated carbon has been suggested as an effective and simple method of controlling the adsorption of elemental mercury from combustion flue gases (Fuente-Cuesta et al. Citation2015; Pavlish et al. Citation2003; Wilcox et al. Citation2011; Yang et al. Citation2019). Many studies have been conducted to decrease the cost of sorbents (González-García Citation2018; Xu et al. Citation2018; Yu et al. Citation2016). Thus, many inexpensive materials have been tested and suggested as raw sorbent materials to control mercury emissions, such as coconut husk (Johari et al. Citation2016), waste wood (Yu et al. Citation2016), fruit peel (Bhakta et al. Citation2017), fly ash (Yang et al. Citation2019), sewage sludge (Park and Lee Citation2018), and gasification char (Fuente-Cuesta et al. Citation2012). Materials with a high content of bromine or chlorine have been reported to have high Hg0 adsorption capacities (Fuente-Cuesta et al. Citation2012). In addition, chemically promoted sorbents demonstrate good performance in Hg0 adsorption (Hu et al. Citation2006; Liu, Xu, and Liu Citation2020; Qi et al. Citation2015; Wang et al. Citation2018, Citation2015).
Bamboo charcoal with a surface area of 91 m2/g exhibited very low efficiency for adsorbing elemental mercury, whereas FeCl3-impregnated bamboo charcoal afforded almost 100% elemental mercury adsorption efficiency under 6% oxygen (O2), 2800 mg/m3 sulfur dioxide (SO2), 130 mg/m3 nitrogen monoxide (NO), 12% carbon dioxide (CO2), and nitrogen (N2) (Tan, Niu, and Chen Citation2015). Fly ash afforded approximately 40% elemental mercury adsorption efficiency, whereas cupric chloride (CuCl2)- and FeCl3-impregnated fly ash afforded elemental mercury adsorption efficiencies of 95% and 75%, respectively, under N2 gas environment (Xu et al. Citation2013). In addition, fly ash promoted with manganese acetate (Mn(CH3COOH)3 · 4H2O) and iron(III) nitrate (Fe(NO3)3) afforded 98% elemental mercury removal efficiency, whereas raw fly ash showed 20% elemental mercury removal efficiency under air environment (Xing, Xu, and Zhong Citation2012). It has been reported that the elemental mercury removal efficiency of a sorbent can be enhanced by the oxidation of elemental mercury via iron and Cl present in the sorbent (Han et al. Citation2016; Hou et al. Citation2013; Liu, Xu, and Liu Citation2020; Shu, Lu, and He Citation2013; Tan et al. Citation2012).
The elemental mercury adsorption efficiencies of the sorbents are also significantly affected by the flue gas composition. Tire pyrolysis char showed 90% elemental mercury adsorption efficiency when exposed to simulated flue gas consisting of 490 ppm NO, 17 ppm nitrogen dioxide (NO2), 3.5 μg/m3 Hg0, and N2 balance, whereas it afforded 47% efficiency under N2 environment. When 6% O2, 12% CO2, and 1800 ppm SO2 were added to the simulated flue gas, the efficiency decreased to 80%. When 200 ppm of hydrogen chloride (HCl) was added to the simulated flue gas, the efficiency increased to approximately 99% (Seneviratne et al. Citation2007). It has been reported that SO2 inhibits elemental mercury adsorption because SO2 competes with elemental mercury for the active site of the sorbent (Xu et al. Citation2013; Zhou et al. Citation2018) on the other hand, NO increased the elemental mercury adsorption efficiency of the sorbent (Yang et al. Citation2014; Zhou et al. Citation2018). In particular, HCl gas plays an important role in increasing the elemental mercury adsorption efficiency of sorbents (Diamantopoulou, Skodras, and Sakellaropoulos Citation2010; Min et al. Citation2017; Olson et al. Citation2004; Tong et al. Citation2015; Yang et al. Citation2007). In a previous study, we also showed that sewage sludge activated carbon sorbents with a low surface area of 4–64 m2/g afforded high elemental mercury adsorption capability with the injection of HCl gas (Park and Lee Citation2018). Many researchers have reported that sorbents with low surface areas have promising capability for the control of elemental mercury. Specifically, these sorbents demonstrated high elemental mercury adsorption efficiency in the presence of HCl gas. However, most previous studies investigated only elemental mercury emissions after adsorption onto sorbents. Based on the results reported, it is difficult to understand the effect of low surface area sorbents on elemental mercury oxidation and adsorption compared to other sorbents with higher surface areas.
The mercury adsorption characteristics of sorbents with low surface areas are investigated in this study by varying the raw material, chemical promotion of the sorbent, and simulated flue gas composition. The emission of both elemental and oxidized mercury after the adsorption of elemental mercury on the carbon sorbents is investigated. Three types of materials are used to make the carbon sorbents for the adsorption of elemental mercury: (1) coal, (2) sewage sludge, and (3) unburned carbon. The sorbent made from each material is tested as a raw sorbent or as the FeCl3-impregnated congener. Each sorbent was also tested under two simulated flue gas conditions, i.e., with and without HCl gas.
Experimental
Sorbent preparation
Sewage sludge and coal were used as raw materials to prepare the activated carbon sorbents. Using a rotary kiln reactor, activated carbon was manufactured through the carbonization and activation processes. Carbonization of the raw material was performed under N2 gas environment. The carbonized material was activated by injecting water vapor. A detailed description of the manufacturing method can be found in our previous publication (Min, Ahmad, and Lee Citation2017; Park and Lee Citation2018). Sewage sludge was selected as the raw material for generating activated carbon with a low surface area. The sewage sludge was carbonized at 400°C for 1 h and then activated at 850°C for 1 h by injecting water vapor. The Brunauer–Emmett–Teller (BET) surface area of the activated carbon made from sewage sludge (sludge AC) was as low as 40.5 m2/g, as shown in .
Table 1. Physical properties of prepared samples
Coal was selected to produce activated carbon with a high surface area. Coal is a general raw material for activated carbon used for the control of mercury emissions. In this study, coal was carbonized at 700°C for 30 min and then activated at 900°C for 30 min. As shown in , the BET surface area of the activated carbon made from coal (coal AC), 219.4 m2/g, was significantly higher than that of the sludge AC.
Unburned carbon (unburned C) from fly ash was selected as the non-activated sorbent with a low surface area. Unburned carbon has been reported to show mercury adsorption ability (Xu et al. Citation2013; Yu et al. Citation2016). shows the ultimate analysis data for sludge AC, coal AC, and unburned C, respectively, acquired using an elemental analyzer (Vario MICRO cube, Elementar, Germany).
Table 2. Results of ultimate analysis
Each sorbent was impregnated with FeCl3 (≥97.0%, Junsei, Japan). FeCl3 (0.5 g) was first dissolved in 100 mL of isopropyl alcohol (≥99.9%, Kanto Chemical, Japan). Each sorbent (4.5 g) was then added to the FeCl3 solution and stirred for 2 h. The solution was filtered, and the filtered solid was dried at 100°C. The Fe content of the filtrate was analyzed using ion chromatography (Dionex Integrion + Dionex Aquion, Thermo Scientific, USA). The concentration of FeCl3 on the sorbent was 7.3, 4.5, and 1.0% for coal AC, sludge AC, and unburned C, respectively. This shows that the concentration of FeCl3 impregnated on the sorbent is largely dependent on the surface area of the sorbent. The BET surface area, micropore volume, and mesopore volume of each sorbent were determined using an analyzer (BELSORP-mini, BEL Japan, Inc., Japan). The results are shown in .
Mercury adsorption test
Six sorbents were tested for the adsorption of elemental mercury using a fixed-bed reactor system. The adsorption tests were performed by injecting 1 L/min simulated flue gas with two compositions: 12% CO2, 5% O2, 7% H2O, 65–75 μg/m3 Hg0, 500 ppm SO2, and 200 ppm NO (1) without and (2) with 20 ppm HCl. The sorbent (30 mg) was pre-mixed with 6 g silica granules (Model S150-3, Fisher Scientific, USA), placed in a fixed-bed reactor at 140°C, and tested for 280 min. A detailed description of the experimental system is provided in our previous publication (Park and Lee Citation2018). The Ontario Hydro Method was used to determine the concentrations of oxidized mercury and elemental mercury, respectively. The outlet gas after flowing through the fixed-bed reactor first entered a 1 N potassium chloride (KCl) impinger train to absorb oxidized mercury and then entered a 4% (w/w) potassium permanganate (KMnO4) and 10% sulfuric acid (H2SO4) impinger train to absorb elemental mercury. The concentrations of the outlet elemental mercury () and outlet oxidized mercury (
) were then determined. The impinger trains were changed to new impinger trains at test times of 10, 20, 30, 40, 160, and 280 min. During the first 40 min of the test, the impinger trains were changed every 10 min because the outlet mercury concentrations varied faster during the earlier time of the test. Subsequently, the impinger trains were changed every 120 min to investigate the mercury emission over a longer period of time. The concentration of inlet elemental mercury (
) was determined by analyzing the simulated flue gas flowing through the bypass line before and after each test. At each time interval, the oxidized mercury emission percentage (
) and elemental mercury emission percentage (
) were determined from the following equations, respectively:
The mercury adsorption efficiency was also determined from the following equation:
All tests were performed in duplicate, and the average and standard error of the results were calculated.
Results and discussion
Analysis of coal AC
Coal AC, which has the highest surface area among the sorbents evaluated in this study, was first tested for the adsorption of elemental mercury. and show the emission of oxidized mercury and elemental mercury from coal AC and FeCl3-coal AC, respectively. Because these sorbents demonstrated high mercury adsorption efficiencies, the y axes of and span 0 to 20%.
Figure 1. Emission of oxidized and elemental mercury from (a) coal AC and (b) FeCl3-coal AC under simulated flue gas without HCl
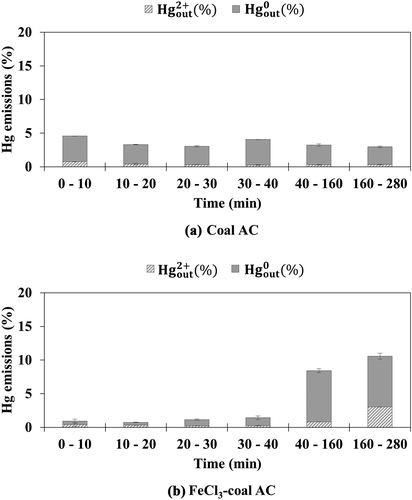
Figure 2. Emission of oxidized and elemental mercury from (a) coal AC and (b) FeCl3-coal AC under simulated flue gas with HCl
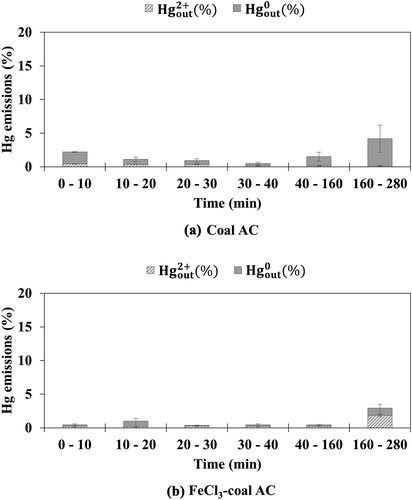
When exposed to simulated flue gas without HCl, the emission of elemental mercury from coal AC was in the range of 2.7‒3.8%, accompanied by minimal oxidized mercury emission, for the overall test period, as shown in . The emission of elemental mercury from FeCl3-coal AC decreased significantly to less than 1% for the test time of 0–40 min, as shown in . However, the emission of oxidized mercury from FeCl3-coal AC was higher than that from coal AC during the test time of 40–280 min. This shows that elemental mercury is oxidized by FeCl3, but some of the resultant oxidized mercury is not adsorbed onto the sorbent. This suggests that the raw carbon surface on FeCl3-coal AC may be responsible for the re-adsorption of the resultant oxidized mercury generated from the reaction between FeCl3 and elemental mercury (Lee, Lee, and Keener Citation2009).
show the emission of oxidized mercury and elemental mercury from the coal AC and FeCl3-coal AC, respectively, using simulated flue gas with HCl. Comparison of the results in and demonstrates that coal AC exhibited higher mercury adsorption efficiency when HCl was contained in the simulated flue gas. Comparison of the data in and illustrates that FeCl3-coal AC also showed higher mercury adsorption efficiency with the injection of HCl. In particular, FeCl3-coal AC showed significantly lower elemental mercury emissions in the later test period when HCl was contained in the simulated flue gas. This indicates that the presence of HCl gas is effective for the adsorption of elemental mercury onto the raw carbon surface of the FeCl3-coal AC.
Analysis of sludge AC
Sludge AC and FeCl3-sludge AC were also tested under simulated flue gas without and with HCl, respectively. Sludge AC has been reported to have Hg0 oxidation capacity because of its large ash content, including metal oxides (Park and Lee Citation2018). However, sludge AC emitted a large amount of oxidized mercury under simulated flue gas without HCl, as shown in . This may be ascribed to the low BET surface area of the sludge AC. On the other hand, FeCl3-sludge AC showed high mercury adsorption efficiencies of more than 95% within the first 30 min, as shown in . The tests for FeCl3-coal AC showed that doping sludge AC with FeCl3 was also effective in increasing its mercury adsorption efficiency during the first tens of minutes. In addition, similar to the results for coal-AC and FeCl3-coal AC, FeCl3-sludge AC showed higher oxidized mercury emissions than sludge AC after 30 min. Although the oxidation capacity of sludge AC was enhanced by doping with FeCl3, a large amount of oxidized mercury was not adsorbed onto the FeCl3-sludge AC. Because of the low raw carbon surface area of FeCl3-sludge AC, re-adsorption of the resultant oxidized mercury was limited after 30 min.
Figure 3. Emission of oxidized and elemental mercury from (a) sludge AC and (b) FeCl3-sludge AC under simulated flue gas without HCl
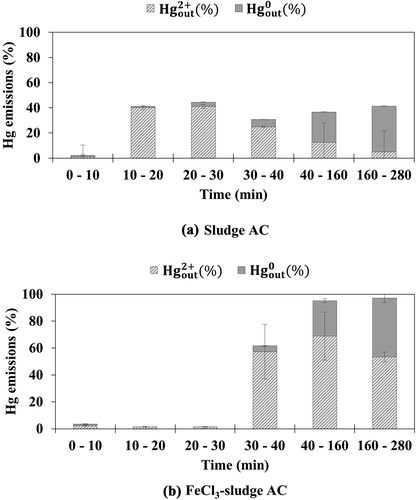
With the injection of HCl, the mercury adsorption efficiency of sludge AC increased significantly within the first 20 min, as shown in . Comparison of the results after 30 min in and shows that the elemental mercury emissions decreased and the oxidized mercury emissions increased with the injection of HCl. The decreased elemental mercury emissions may be ascribed to an increase in the adsorption of elemental mercury onto the raw carbon surface of sludge AC in the presence of HCl. The increased oxidized mercury emissions may be ascribed to the limited raw carbon surface area of sludge AC at the later time of the test. shows the oxidized mercury and elemental mercury emission data for the FeCl3-sludge AC. Similar to the results for sludge AC, FeCl3-sludge AC also showed high mercury adsorption efficiency during the earlier time of the test. Comparing the results after 40 min in and shows that FeCl3-sludge AC exhibited significantly lower elemental mercury emission when HCl was contained in the simulated flue gas, as also observed for FeCl3-coal AC. This again indicates that HCl gas is effective in increasing the adsorption of elemental mercury onto the raw carbon surface of FeCl3-sludge AC.
Analysis of unburned carbon
Unburned C and FeCl3-unburned C were tested under simulated flue gas conditions with and without HCl. show the mercury emission as a function of the test time for unburned C and FeCl3-unburned C, respectively, under simulated flue gas without HCl. Unlike coal AC and sludge AC, unburned C did not demonstrate mercury adsorption capacity. This may be ascribed to the very low surface area and non-detectable micropore volume of unburned C. FeCl3-unburned C showed higher mercury adsorption efficiency than unburned C during the earlier time of the test. However, the minimal increase in the mercury adsorption efficiency of FeCl3-unburned C may be ascribed to the low concentration of FeCl3 impregnated on the unburned C.
Figure 5. Emission of oxidized and elemental mercury from (a) unburned C and (b) FeCl3-unburned C under simulated flue gas without HCl
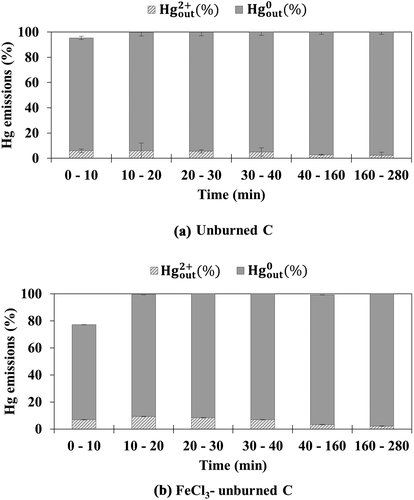
show the emission of mercury as a function of time for the unburned C and FeCl3-unburned C, respectively, under simulated flue gas with HCl. The injection of HCl increased the mercury adsorption efficiency of both unburned C and FeCl3-unburned C by decreasing the emission of elemental mercury, as also observed for coal AC and sludge AC. In addition, the mercury adsorption efficiency of FeCl3-unburned C was higher than that of unburned C, especially during the earlier time of the test, as observed for FeCl3-coal AC and FeCl3-sludge AC. However, the emission of oxidized mercury was higher for FeCl3-unburned C than for unburned C. This indicates that the re-adsorption of the resultant oxidized mercury onto the raw carbon surface of FeCl3-unburned C is limited owing to its very low surface area. Although the unburned C sorbents demonstrated significantly lower mercury adsorption efficiency than coal AC and sludge AC, their Hg0 oxidation and adsorption properties were similar to that of the coal AC and sludge AC sorbents depending on the chemical promotion and simulated flue gas composition.
Conclusion
Coal AC, sludge AC, unburned C, and their FeCl3-impregnated counterparts were tested as sorbents for elemental mercury under two simulated flue gas conditions (with and without HCl gas, respectively). For all tested sorbents, HCl gas was effective in increasing the mercury adsorption efficiency of both the raw and FeCl3-impregnated sorbents by decreasing the emission of elemental mercury. The FeCl3-impregnated sorbents demonstrated higher mercury adsorption efficiency than the raw sorbents, especially during the earlier test period. The mercury adsorption efficiency of coal AC with a surface area of 219.4 m2/g exceeded 95% for the duration of the test when exposed to simulated flue gas with HCl. However, sludge AC with a surface area of 40.5 m2/g showed high mercury adsorption efficiency under simulated flue gas conditions with HCl during the first 20 min of the test. The mercury adsorption efficiency of FeCl3-sludge AC with a surface area of 34 m2/g exceeded 95% under both simulated flue gas conditions (without and with HCl) during the first 30 min of the test. Considering the particle residence times in full-scale particulate control devices, the sludge AC sorbent is promising for the control of mercury emissions. In addition, this can be a promising alternative method to ocean dumping for the disposal of sewage sludge. However, pilot- or full-scale tests are still recommended to confirm if the sludge AC sorbents are technically and economically feasible to be used for the control of mercury emissions. FeCl3-sludge AC and FeCl3-unburned C emitted large amounts of oxidized mercury during the later test periods. This indicates that FeCl3 impregnated on the sorbent effectively oxidizes elemental mercury, but the raw carbon surface of the sorbent may be responsible for the re-adsorption of the resultant oxidized mercury. The unburned C sorbents demonstrated significantly lower mercury adsorption efficiencies than coal AC and sludge AC because of the low surface areas of the former: 6.5 m2/g for unburned C and 6.1 m2/g for FeCl3-unburned C. However, the Hg0 oxidation and adsorption behavior of these sorbents was similar to that of the coal AC and sludge AC sorbents depending on the chemical promotion and simulated flue gas composition.
Disclosure statement
No potential conflict of interest was reported by the author(s).
Additional information
Funding
Notes on contributors
Jeongmin Park
Jeongmin Park is a graduate student in the Department of Environmental Engineering at Chungbuk National University, Korea.
Sang-Sup Lee
Sang-Sup Lee is a professor in the Department of Environmental Engineering at Chungbuk National University, Korea.
References
- Bhakta, J. N., S. Rana, S. Lahiri, and Y. Munekage. 2017. Sorption of mercury onto waste material derived low-cost activated carbon. Appl. Water Sci. 7 (1):199–206. doi:https://doi.org/10.1007/s13201-014-0236-0.
- Diamantopoulou, I. R., G. Skodras, and G. P. Sakellaropoulos. 2010. Sorption of mercury by activated carbon in the presence of flue gas components. Fuel Process. Technol. 91:158–63. doi:https://doi.org/10.1016/j.fuproc.2009.09.005.
- Fuente-Cuesta, A., I. Diamantopoulou, M. A. Lopez-Anton, M. Diaz-Somoano, M. R. Martínez-Tarazona, and G. P. Sakellaropoulos. 2015. Study of mercury adsorption by low-cost sorbents using kinetic modeling. Ind. Eng. Chem. Res. 54:5572–79. doi:https://doi.org/10.1021/acs.iecr.5b00262.
- Fuente-Cuesta, A., M. Diaz-Somoano, M. A. Lopez-Anton, M. Cieplik, J. L. G. Fierro, and M. R. Martínez-Tarazona. 2012. Biomass gasification chars for mercury capture from a simulated flue gas of coal combustion. J. Environ. Manage. 98:23–28. doi:https://doi.org/10.1016/j.jenvman.2011.12.013.
- Galbreath, K. C., and C. J. Zygarlicke. 2000. Mercury transformations in coal combustion flue gas. Fuel. Process. Technol. 65–66:289–310. doi:https://doi.org/10.1016/S0378-3820(99)00102-2.
- González-García, P. 2018. Activated carbon from lignocellulosics precursors: A review of the synthesis methods, characterization techniques and applications. Renewable Sustainable Energy Rev. 82:1393–414.
- Granite, E. J., H. W. Pennline, and C. Senior, eds. 2015. Mercury control: For coal-derived gas streams. Weinheim: Wiley VCH.
- Han, L., X. He, C. Yue, Y. Hu, L. Li, L. Chang, H. Wang, and J. Wang. 2016. Fe doping Pd/AC sorbent efficiently improving the Hg0 removal from the coal-derived fuel gas. Fuel 182:64–72. doi:https://doi.org/10.1016/j.fuel.2016.05.046.
- Hou, W. H., J. S. Zhou, Y. Zhang, X. Gao, Z. Y. Luo, and K. Cen. 2013. Effect of H2S on elemental mercury removal in coal gas by Fe2O3. Proc. CSEE 33 (23):92–98.
- Hu, C. X., J. S. Zhou, Z. Y. Luo, H. E. Sheng, G. K. Wang, and K. F. Cen. 2006. Effect of oxidation treatment on the adsorption and the stability of mercury on activated carbon. J. Environ. Sci. 18 (6):1161–66. doi:https://doi.org/10.1016/S1001-0742(06)60056-9.
- Johari, K., N. Saman, S. T. Song, C. S. Chin, H. Kong, and H. Mat. 2016. Adsorption enhancement of elemental mercury by various surface modified coconut husk as eco-friendly low-cost adsorbents. Int. Biodeterior. Biodegrad. 109:45–52. doi:https://doi.org/10.1016/j.ibiod.2016.01.004.
- Lee, S. S., J. Y. Lee, and T. C. Keener. 2009. Bench-scale studies of in-duct mercury capture using cupric chloride-impregnated carbons. Environ. Sci. Technol. 43 (8):2957–62. doi:https://doi.org/10.1021/es801943t.
- Lee, S. S., and J. Wilcox. 2017. Behavior of mercury emitted from the combustion of coal and dried sewage sludge: The effect of unburned carbon, Cl, Cu and Fe. Fuel 203:749–56. doi:https://doi.org/10.1016/j.fuel.2017.04.104.
- Liu, D., W. Xu, and Y. Liu. 2020. Seaweed bio-chars modified with metal chloride for elemental mercury capture from simulated flue gas. Atmos. Pollut. Res. 11(6):122–130. doi:https://doi.org/10.1016/j.apr.2020.03.006
- Min, H., T. Ahmad, and S. Lee. 2017. Mercury adsorption characteristics as dependent upon the physical properties of activated carbon. Energy & Fuels 31 (1):724–29. doi:https://doi.org/10.1021/acs.energyfuels.6b02246.
- Olson, E. S., B. A. Mibeck, S. A. Benson, J. D. Laumb, C. R. Crocker, G. E. Dunham, R. K. Sharma, S. J. Miller, and J. H. Pavlish. 2004. The mechanistic model for flue gas-mercury interactions on activated carbons: The oxidation site. Prepr. Pap. Am. Chem. Soc. Div. Fuel Chem. 49 (1):279.
- Park, J., and S. S. Lee. 2018. Adsorption of mercury by activated carbon prepared from dried sewage sludge in simulated flue gas. J. Air Waste Manage. Assoc. 68 (10):1077–84. doi:https://doi.org/10.1080/10962247.2018.1468364.
- Pavlish, J. H., E. A. Sondreal, M. D. Mann, E. S. Olson, and K. C. Galbreth. 2003. Status review of mercury control options for coal-fired power plants. Fuel Process. Technol. 82:89–165. doi:https://doi.org/10.1016/S0378-3820(03)00059-6.
- Qi, H., W. Xu, J. Wang, L. Tong, and T. Zhu. 2015. Hg0 removal from flue gas over different zeolites modified by FeCl3. J. Environ. Sci. 28:110–17. doi:https://doi.org/10.1016/j.jes.2014.05.050.
- Seneviratne, H. R., C. Charpenteau, A. George, M. Millan, D. R. Dugwell, and R. Kandiyoti. 2007. Ranking low cost sorbents for mercury capture from simulated flue gases. Energy Fuels 21 (6):3249–58. doi:https://doi.org/10.1021/ef070028x.
- Shu, T., P. Lu, and N. He. 2013. Mercury adsorption of modified mulberry twig chars in a simulated flue gas. Bioresour. Technol. 136:182–87. doi:https://doi.org/10.1016/j.biortech.2013.02.087.
- Tan, Z., G. Niu, and X. Chen. 2015. Removal of elemental mercury by modified bamboo carbon. Chin. J. Chem. Eng. 23 (11):1875–80. doi:https://doi.org/10.1016/j.cjche.2015.09.001.
- Tan, Z., S. Su, J. Qiu, F. Kong, Z. Wang, F. Hao, and J. Xiang. 2012. Preparation and characterization of Fe2O3–SiO2 composite and its effect on elemental mercury removal. Chem. Eng. J. 195:218–25. doi:https://doi.org/10.1016/j.cej.2012.04.083.
- Tong, L., W. Xu, X. Zhou, R. Liu, and T. Zhu. 2015. Effects of multi-component flue gases on Hg0 removal over HNO3-modified activated carbon. Energy Fuel. 29:5231–36. doi:https://doi.org/10.1021/acs.energyfuels.5b00683.
- UNEP. 2013. Global mercury assessment 2013: Sources, emissions, releases and environmental transport. Geneva, Switzerland: Chemicals Branch, UNEP.
- Wang, X., L. Wang, Z. Bian, P. Ning, P. Wang, F. Wang, and Y. Ma. 2018. Adsorption of gaseous elemental mercury by ferric‐chloride-modified activated carbon under low-temperature conditions. CLEAN–Soil Air Water 46 (12):1800351. doi:https://doi.org/10.1002/clen.201800351.
- Wang, X. Q., P. Wang, P. Ning, Y. X. Ma, F. Wang, X. L. Guo, and Y. Lan. 2015. Adsorption of gaseous elemental mercury with activated carbon impregnated with ferric chloride. RSC Adv. 5 (32):24899–907. doi:https://doi.org/10.1039/C5RA01011J.
- Wilcox, J., E. Rupp, S. C. Ying, D. H. Lim, A. S. Negreira, A. Kirchofer, F. Feng, and K. Lee. 2012. Mercury adsorption and oxidation in coal combustion and gasification processes. Int. J. Coal Geol. 90−91:4–20. doi:https://doi.org/10.1016/j.coal.2011.12.003.
- Wilcox, J., E. Sasmaz, A. Kirchofer, and S. S. Lee. 2011. Heterogeneous mercury reaction chemistry on activated carbon. J. Air Waste Manage. Assoc. 61:418–26. doi:https://doi.org/10.3155/1047-3289.61.4.418.
- Xing, L., Y. Xu, and Q. Zhong. 2012. Mn and Fe modified fly ash as a superior catalyst for elemental mercury capture under air conditions. Energy Fuel. 26 (8):4903–09. doi:https://doi.org/10.1021/ef3005256.
- Xu, W., H. Wang, T. Zhu, J. Kuang, and P. Jing. 2013. Mercury removal from coal combustion flue gas by modified fly ash. J. Environ. Sci. 25 (2):393–98. doi:https://doi.org/10.1016/S1001-0742(12)60065-5.
- Xu, Y., F. Deng, Q. Pang, S. He, Y. Xu, G. Luo, and H. Yao. 2018. Development of waste-derived sorbents from biomass and brominated flame retarded plastic for elemental mercury removal from coal-fired flue gas. Chem. Engi. J. 350:911–19. doi:https://doi.org/10.1016/j.cej.2018.06.055.
- Yang, H., Z. Xu, M. Fan, A. E. Bland, and R. R. Judkins. 2007. Adsorbents for capturing mercury in coal-fired boiler flue gas. J. Hazard. Mater. 146:1–11. doi:https://doi.org/10.1016/j.jhazmat.2007.04.113.
- Yang, J., Y. Zhao, J. Zhang, and C. Zheng. 2014. Regenerable cobalt oxide loaded magnetosphere catalyst from fly ash for mercury removal in coal combustion flue gas. Environ. Sci. Technol. 48 (24):14837–43. doi:https://doi.org/10.1021/es504419v.
- Yang, Y., S. Miao, J. Liu, Z. Wang, and Y. Yu. 2019. Cost-effective manganese ore sorbent for elemental mercury removal from flue gas. Environ. Sci. Technol. 53 (16):9957–65. doi:https://doi.org/10.1021/acs.est.9b03397.
- Yu, J. G., B. Y. Yue, X. W. Wu, Q. Liu, F. P. Jiao, X. Y. Jiang, and X. Q. Chen. 2016. Removal of mercury by adsorption: A review. Environ Sci Pollut Res 23 (6):5056–76. doi:https://doi.org/10.1007/s11356-015-5880-x.
- Zhou, Q., Y. Duan, M. Chen, M. Liu, P. Lu, and S. Zhao. 2018. Effect of flue gas component and ash composition on elemental mercury oxidation/adsorption by NH4Br modified fly ash. Chem. Engi. J. 345:578–85. doi:https://doi.org/10.1016/j.cej.2018.02.033.