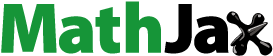
ABSTRACT
Ethanol is a significant source of energy as a biofuel; however, its production using corn involves the generation of harmful emissions from both fermentation tanks and dryers. Scrubbers control the emissions from fermentation tanks, while the emissions from the dryers are controlled by regenerative thermal oxidizers. Potential alternatives to these energy- and water-intensive technologies are biotrickling filters (BTFs). In this study, two BTFs were operated in parallel to treat formaldehyde and methanol emissions in a volumetric ratio of 4:1, one at 25°C (mesophilic), and the other at 60°C (thermophilic). The mesophilic BTF simulated emissions from fermentation tanks, while the thermophilic BTF simulated emissions from dryers. Both beds were operated at an empty bed residence time of ~30 s and influent formaldehyde concentrations of 20, 50, and 100 parts per million per volume (ppmv). Formaldehyde polymerization was reduced in this study by adding NaOH to pH levels of 7.0–7.4 and heating the solution to a temperature of 60°C. BTFs have successfully removed formaldehyde at typical ethanol plants emissions ~21 ppmv. The BTF technology have the potential in replacing the conventional air treatment methods used at ethanol plants.
Implications: Currently, ethanol plants remove and treat hazardous air pollutants (HAPs) using wet scrubbers from the fermenter off-gasses and using thermal oxidizers to combust off-gasses. The utilization of biotrickling filters (BTFs) for HAP removal generally and formaldehyde particularly has wide implication in the field of renewable energy. Utilizing BTFs in the 200+ ethanol plants in USA will save cost and reduce water and energy needs significantly. BTFs can reduce an ethanol plant’s carbon intensity (CI) by 1 to 3 g CO2/MJ. This can result in roughly $50 million per year in additional revenue in Nebraska for instance.
Introduction
The ethanol industry is an important industry in the United States (US). The US Congress passed a law in 2007 that mandates the production of renewable biofuels to reach 36 billion gallons by 2022 (U.S. Congress, Citation2007). According to the US Congress, ~15 billion of the 36 billion gallons should be derived from cellulosic feedstock. As of January 2020, ethanol production has reached a capacity of 17.3 billion gallons per year (U.S. Energy Information Administration Citation2020). The Midwest states of Iowa and Nebraska are the top two producers for ethanol each year (U.S. Energy Information Administration Citation2020). Ethanol manufacturing results in the production of several volatile organic compounds (VOCs), including acetaldehyde, acrolein, formaldehyde, methanol, ethanol, and acetic acid (Brady and Pratt Citation2012; Cohen et al. Citation2021). VOCs are typical air pollutants that could affect humans’ welfare (Garcia et al. Citation2015; Wu et al. Citation2018). It was reported that around 3.3 million people die prematurely due to air pollution complications (Hoek et al. Citation2013; Wu et al. Citation2018). The US Environmental Protection Agency (EPA) identified 187 pollutants as hazardous air pollutants (HAPs) in terms of carcinogenic impact (USEPA Citation2017a). Formaldehyde is a major HAP of concern because it is categorized as a carcinogenic compound under the International Agency for Research on Cancer (IARC) (IARC Citation2011). The US EPA limits the emissions for an entire ethanol plant to 10 tons per year (tpy) for an individual HAP and 25 tpy for all HAPs (USEPA Citation2017b).
To control HAP emissions, the US EPA has identified the best available control technologies (BACTs) (USEPA Citation2016). The traditional technologies used to control emissions from ethanol plants are regenerative thermal oxidizers (RTOs) and water scrubbers (USEPA Citation2019). Both technologies require a considerable amount of energy and are costly to operate. In a personal communication with an ethanol plant director (Lyndon Citation2019), it was highlighted that the RTO maintenance costs ~$1 million per year. However, the average size of an RTO is ~18 MMBtu/h which will combust ~155 million standard cubic feet (SCF) of natural gas per year (Nester Citation2007). Concentrations of the VOCs in the waste gas stream are essential to identify the design and size of RTOs (Sorrels et al. Citation2017). The lower explosive limit (LEL) is a limit that defines the minimum concentration of that compound that can produce more energy than is needed to raise its temperature to be ignited (Sorrels et al. Citation2017). If a compound in the waste gas has a value higher than 50% of its LEL, it must be first diluted with air to meet the regulations (Sorrels et al. Citation2017). At a conservative price of $4.00 per 1000 SCF, a total cost of over 600,000 USD per year is required to operate an RTO (U.S. Energy Information Administration Citation2019). However, prices in the USA, and elsewhere in the world, can be higher than 4.00 USD per 1000 SCF. Catalytic thermal oxidizers (CTOs) are a similar technology to RTOs. However, CTOs treat VOCs and HAPs at lower temperatures than RTOs and use a catalyst to speed up the oxidation of VOCs to water and CO2 (USEPA Citationn.d.). The cost of removing a pollutant based on styrene as the pollutant removed for the CTOs is ~ 2,974 $/ton removed (USEPA Citationn.d.). Other than ethanol production, the combustion of biogas fuels can also produce harmful air emissions such as formaldehyde, styrene, and VOCs (e.g., Mustafi, Raine, and Bansal Citation2006; Pérez, Álvarez-Hornos, and Portune et al. Citation2015; Dobslaw et al. Citation2017; San-Valero et al. Citation2017; Dobslaw et al., Citation2019a). A study by Dobslaw et al. (Citation2019a) has evaluated removing a crude gas mixture containing NO, NOx, NO2, CO, VOCs, and formaldehyde (Dobslaw et al., Citation2019a). The reactor used to perform the treatment consisted of a two-stage chemical scrubber with an optional biofilter operated at thermophilic conditions (55–60°C) (Dobslaw et al., Citation2019a). The chemical scrubber showed an efficiency of 95.7–97.2% in removing formaldehyde from the crude gas, and oxygen injection is important to allow for more efficient formaldehyde biodegradation (aerobic conditions) (Dobslaw et al., Citation2019a). The biofilter showed no treatment of the gases at thermophilic conditions (Dobslaw et al., Citation2019a).
Biotechnologies have been recognized recently as BACTs for low to moderate VOC concentrations in the waste gas streams (e.g., Liu et al. Citation2021; Malhautier et al. Citation2021; Wu et al. Citation2018). These biotechnologies include biofilters (BF), bioscrubbers (BS) and biotrickling filters (BTFs) (Ryu, Cho, and Lee Citation2011; Wu et al. Citation2018). The main difference between BFs, BSs, and BTFs is the type of environment the microbes exist in and the mechanism the liquid is delivered or exist in (Wu et al. Citation2018). For BFs and BTFs, the microorganisms are fixed, meaning they grow on the packing material. However, for the BSs the microorganisms are suspended in a bioreactor (Wu et al. Citation2018). For BFs the water is stationary, meaning water is occasionally put on the bed to maintain the moisture content in the BF (Wu et al. Citation2018). The water for BSs continuously flows as it contains the microbes growing in suspension. The water for BTFs flows continuously or dis- continuously as it contains the nutrient solution needed for microbial stability and growth (Wu et al. Citation2018). BTFs, when compared to BFs and BSs, have a better capability in treating VOCs (Wu et al. Citation2018). The flow of the nutrient solution in the BTFs allows for a defined pH and nutrient supply compared to BFs. It allows for higher removal efficiencies in the BTFs (Seignez et al. Citation2004; Wu et al. Citation2018). BTFs also show faster biodegradation of VOCs when compared to BSs, since pollutants get enriched with extracellular polymeric substances (EPSs) that allow more microorganisms to be able to access and biodegrade the pollutants more effectively rather than in a BS (Wu et al. Citation2018).
BTFs are an attractive solution that could replace the BACTs used at ethanol plants (Duerschner, Aly Hassan, and Dvorak Citation2020). BTFs are packed beds with biologically active material or an inert material on which biofilms can attach (Bruneel et al. Citation2018; Crocker and Schnelle Citation1998; Delhoménie and Heitz Citation2005; Duerschner, Aly Hassan, and Dvorak Citation2020; Gabriel and Deshusses Citation2003). As contaminants spread along BTFs, they are transferred to the aqueous layer, then adsorbed in the aqueous layer, absorbed into the biofilm layer, and biodegraded within the biofilm layer (Barbusiński et al. Citation2020). Biofilm in the BTFs is usually aerobic microorganisms since biodegradation in the BTFs occurs under aerobic conditions (Barbusiński et al. Citation2020). The development of the microorganisms in the BTFs may take days to months, depending on the concentration of the microorganisms in the BTF (Barbusiński et al. Citation2020). A trickling liquid with nutrients and minerals is added along the beds periodically (Gabriel and Deshusses Citation2003). The nutrients are essential to maintain the biofilm. It usually consists of macronutrients such as N, P, S, and K; and micronutrients like vitamins and metals (Bak et al., Citation2017; Barbusiński et al. Citation2020). BTFs can also be used in hybrid with a biofilter to treat pollutants, as other studies have pointed this out (Dobslaw et al., Citation2019b; Karre et al. Citation2012; Wang and Chen Citation2006). BTFs operating costs could range between $1.9 to $3.8 per 1000 m3 of air treated (depending on several factors such as nitrate loading, contaminants treated, etc.) (Deshusses and Cox Citation1999). The prices of operating the BTFs are competitive to the RTOs and water scrubbers (Deshusses and Cox Citation1999; USEPA Citation2003). Some limitations that could affect the removal efficiencies are the high accumulation of biomass in the bed and the mass gas transfer (Wu et al. Citation2018).
Formaldehyde is a HAP emitted from both fermenters and dryers in ethanol plants. The waste gases from the fermentation process are emitted at temperatures lower than 35°C. Exhaust gases from the drying process are usually emitted at temperatures ranging from 100°C to 140°C. The exhaust gases from the drying process are then passed through a cyclone that cools the gases to a temperature in the range of 40°C to 55°C (Chen et al. Citation2010).
Formaldehyde biofiltration has been evaluated in several studies (Chen et al. Citation2010; Fulazzaky, Talaiekhozani, and Abd Majid Citation2016; Fulazzaky et al. Citation2013; Jamshidi et al. Citation2018; Maldonado-Diaz and Arriaga Citation2015; Rezaei, Fazlzadehdavil, and Hajizadeh Citation2015; Talaiekhozani et al. Citation2016; Teh and Mahmood Citation2013; Xu et al. Citation2010). However, all these studies have only evaluated formaldehyde biofiltration at ambient temperatures. No study has evaluated formaldehyde biodegradation at high temperatures. Moreover, several of these studies have used formalin as a source of influent formaldehyde (Maldonado-Diaz and Arriaga Citation2015; Rezaei, Fazlzadehdavil, and Hajizadeh Citation2015; Teh and Mahmood Citation2013), but none of them have reported the polymerization of formaldehyde into paraformaldehyde in the gaseous state.
In this study, the biodegradation of formaldehyde and methanol was evaluated in two parallel BTFs: one at ambient temperature (25°C), known as the mesophilic BTF, and the other at a high temperature (60°C), known as the thermophilic BTF. The purpose of evaluating the biodegradation of formaldehyde and methanol at these two temperatures was to simulate the emissions from both fermenters, which are close to ambient temperatures, and grain dryers which are at a high temperature. The removal efficiency of the BTFs was evaluated at increasing loading rates. Temperatures of 16 and 40°C were also evaluated to see how other temperature variations could affect the biodegradation.
Materials and methods
Biotrickling filter
Two BTFs were operated in parallel. In each BTF media comprising (0.3″–0.5″) (0.76 cm- 1.3 cm) pellets of diatomaceous earth (Celite 6 mm R-635 Bio-Catalyst Carrier; Celite Corp., Lompoc, CA) was housed in a glass column of 3-in (7.6 cm) internal diameter. The media had a mean pore diameter of 20 µm, Brunauer–Emmett–Teller surface area of 0.27 m2/g, and a bed density of 513 kg/m3. It mainly comprised SiO2, with a significant fraction of Al2O3. The thermophilic BTF was heated using a heating tape and controlled using BriskHeat X2-120JTP Single Zone PID temperature controller (Cole-Palmer, Vernon Hills, IL).
The beds were seeded with microorganisms. The mesophilic BTF bed was submerged overnight in backflow activated sludge from aeration obtained from a local wastewater treatment plant. In contrast, the thermophilic bed was submerged overnight in a cooking compost slurry. The compost was taken from yard waste from the center of a windrow and then mixed with water to create the slurry. Two grams per liter of glucose were added to both BTFs overnight. Afterward, both BTFs were used for the degradation of acetaldehyde (Duerschner et al. Citation2020).
The columns extend for 3 in (7.6 cm) above the top of the packing material, where the HAP-laden air was introduced at the top to enable uniform mixing. Each BTF was equipped with sampling ports located at packed depths of 4.5 (11.4 cm), 13.5 (34.3 cm), 22.5 (57.2 cm), 31.5 (80.0 cm), and 36 in (91.4 cm). For the thermophilic BTF, a thermocouple was inserted at a bed depth of 22.5 inches (57.2 cm) to control the temperature better; therefore, no samples were taken at that depth. All connections were airtight. Air from any sampling port could be directed for analysis to either a Nicolet IS20 FTIR spectrometer equipped with a gas cell or a 490 μ-GC equipped with a thermal conductivity detector and a two-channel module.
Gas delivery system
The apparatus used to test the HAP-laden air concentration is the same setup used by Duerschner, Aly Hassan, and Dvorak (Citation2020). House air was filtered through a Parker Filtration 2000 series compressed air and Balston sterile air filter, followed by a Parker compressed air gas water separator. The air was filtered to avoid any impurities that could affect the volatilization of formalin. Following filtration, the airstream was split, and the flow rate was regulated to 8 L/min (corresponding to an EBRT of 30s, bed volume of ~4 L) using two Aalborg mass flow controllers (Orangeburg, New York). Liquid formalin (containing 37% formaldehyde by weight and 15% of methanol as a stabilizer) was infused into the air stream through a septum housed in a stainless-steel tee union. A Harvard Apparatus Pump 11 Elite syringe pump (Holliston, MA) and Luer lock tip syringes were used to regulate the infusion. Sodium hydroxide (NaOH) and phosphate buffer were added to the formalin solution contained in the syringes to obtain a pH between 7.2 and 7.4. The resulting solution/mixture was heated at 60°C to minimize the polymerization of formalin.
Nutrient delivery system
Nutrient/buffer solution was delivered to the BTF beds intermittently using a pump and timer-controlled solenoid valves. The nutrient solution comprised essential inorganic salts and vitamins necessary for the growth of microorganisms, and was a once-through flow, and was not recycled. A fresh five-gallon nutrient solution batch was prepared every five days. A pressure valve and a misting nozzle controlled the pipe delivering solution to the BTFs. The valve was opened for 5 s in a 5-min cycle controlled by a timer. The composition of the nutrient solution was similar to the one reported by Sorial et al. (Citation1997).
Sampling setup
A Nicolet IS20 Fourier transform infrared (FTIR) spectrometer (Thermo Fischer, MA) detected formaldehyde gas concentrations. The FTIR spectrometer was equipped with a 2-m gas cell. The volume of the gas cell was 200 mL, and it was kept at a temperature of 161°C to avoid condensation on the walls. Nitrogen gas was used to keep the instrument at a constant purge to eliminate any condensation in the instrument or the gas cell. A resolution of 0.5 cm−1 was chosen to provide a high measurement resolution. A 64-scan procedure was chosen to ensure high sensitivity and eliminate noise associated with the sample spectrum. The sample was allowed to fill the 200 mL gas cell for ~10 min at a flow rate of 1 L/min. Then the inlet and outlet valves of the gas cell were closed for 5 min to stabilize the sample temperature inside the gas cell for better detection of formaldehyde and to avoid condensation on the walls of the gas cell. The wavelength range used for detecting the formaldehyde spectrum was between 2657.0 and 2784.0 cm−1. All formaldehyde detections were taken in triplicate. Samples from the influent and effluent were taken daily.
The 490 μ-GC equipped with a thermal conductivity detector and a two-channel module was used to detect CO2, N2, and O2. The first channel detected N2 and O2, and the second channel detected CO2 gas. The first channel contained a 10-m MS5A heated injector maintained at 60°C with a channel temperature of 75°C. The second channel contained a 4-m PPQ module with an injector temperature of 50°C and a column temperature of 55°C. For both channels, the sample inline temperature was 35°C, and the injection pump runtime was 5 s.
The liquid effluent was used to analyze volatile suspended solids (VSS) and chemical oxygen demand (COD). VSS was determined using methods 2540 D and 2540 E as standard methods (APHA Citation2005). COD was determined using HACH (Loveland, Colorado) 820 vials. Nitrate was determined using standard methods (Goldman and Jacobs Citation1961; Hoather and Rackham Citation1959; Navone Citation1964). All samples were tested in triplicate.
Results and discussion
Polymerization of formaldehyde
Generating formaldehyde vapors at a high concentration was challenging because of polymerization. The generation of long-chain paraformaldehyde of up to 100 monomer units was observed. Paraformaldehyde is insoluble in water and is a white waxy powder (Kiernan Citation2000). The polymerization of formaldehyde inhibits the infusion of stable influent formaldehyde concentrations into the BTFs. Accordingly, the polymerization of formaldehyde needs to be successfully reduced.
Previous studies have used formalin solutions to generate formaldehyde vapors (Chen et al. Citation2010; Prado, Veiga, and Kennes Citation2004; Rezaei, Fazlzadehdavil, and Hajizadeh Citation2015; Talaiekhozani et al. Citation2016; Teh and Mahmood Citation2013). However, none of these studies reported the occurrence of any formaldehyde polymerization. Furthermore, no methods of formaldehyde depolymerization were proposed.
In a study on the elimination of the polymerization of formaldehyde, Kiernan (Citation2000) found that adding a hydroxide source (such as NaOH) for buffering paraformaldehyde to a pH between 7.00 and 7.40 and heating the solution to 60°C can help reduce formaldehyde polymerization (Kiernan Citation2000). This procedure was implemented in the present study. A 1-M NaOH solution was used as the hydroxide source. Phosphate buffer was used to help maintain the pH levels in the formalin solution between 7.00 and 7.40. The solution was heated in a water bath at 60°C before use.
BTF performance
Each BTF was operated at a constant formaldehyde influent concentration that was increased stepwise. Three phases were investigated corresponding to 20, 50, and 100 ppmv influent concentrations. lists the operation duration, influent concentration, loading rate, elimination capacity, and removal efficiency of both BTFs. Variability of the influent concentration was observed because of the partial polymerization of formaldehyde to form paraformaldehyde, especially at high concentrations. The actual measured concentrations of the mesophilic BTF were 14.0 6.1, 34.5
20.2, and 92.5
5.6 ppmv in phases I, II, and III, respectively. Similarly, for the thermophilic BTF, the actual measured concentrations in ppmv were 16.0
9.1, 36.6
21.1, and 100.2
8.9 at phases I, II, and III, respectively. The measured concentrations are the averages of three samples taken on each operating day.
Table 1. Different phases of operation for both mesophilic and thermophilic BTFs, with various operating conditions such as duration, influent concentration, loading rate, elimination capacity, and removal efficiency. Error ranges represent one standard deviation
shows the loading rate versus the elimination capacity of both BTFs throughout the three phases. For both BTFs, the elimination capacity increased proportionally with the loading rate. shows that the data points would lie on the 1:1 line if complete degradation occurs. This study did not establish a maximum elimination capacity for formaldehyde. The highest elimination capacity recorded was 60.0 g m−3 h−1 in Phase III. The elimination capacity established in this study was higher than those established in other studies (13.3 g m−3 h−1 (Fulazzaky, Talaiekhozani, and Abd Majid Citation2016); 8.7 g m−3 h−1 (Xu et al. Citation2010); and 4.0 g m−3 h−1 (Rezaei, Fazlzadehdavil, and Hajizadeh Citation2015)). A high elimination capacity is expected at high loading rates. However, in this study, operating the BTFs at high loading rates was not possible due to formaldehyde’s polymerization and maintaining a constant influent concentration at high loading rates. However, at typical ethanol plants, where emissions from fermentation tanks and dryers are 21 and 30 ppmv, respectively (Brady and Pratt Citation2012), the BTFs completely degrade formaldehyde. Moreover, formaldehyde has never been studied under thermophilic conditions. The performance of both BTFs decreases at high formaldehyde loading rates.
Performance of mesophilic BTF
Figure S1 (see supplemental material) demonstrates the effect of influent formaldehyde concentration on the efficiency of the mesophilic BTF in all three phases. Complete removal of formaldehyde was achieved. During the acclimation period for phase I, where the target concentration was 20 ppmv, average removal efficiency of 74% was recorded. The acclimation period is needed for microorganisms capable of biodegrading formaldehyde to grow and dominate the existing microbial community. The removal efficiency increased to 94% on the 5th day, after which it never decreased below 80%. The average removal efficiency for the entire phase was 90.1 12.4%. The highest recorded elimination capacity for phase I was 4.9 g m−3 h−1.
For phase II, the target concentration was 50 ppmv; the removal efficiency never decreased below 93% for the entire duration. The average removal efficiency for the entire phase was 99.0 2.0%. The highest recorded elimination capacity for phase II was 15.2 g m−3 h−1. For phase III, the target concentration was 100 ppmv; the removal efficiency never decreased below 98% for the entire duration. The average removal efficiency for the entire phase was 99.5
0.7%. The highest recorded elimination capacity for phase III was 20.4 g m−3 h−1. Variability of influent formaldehyde concentrations was observed in phases I and II. However, for phase III, the influent formaldehyde concentration was maintained at the target influent concentration. The variability of the influent formaldehyde concentration affected the removal efficiency and the bed height.
Several studies in the literature have looked at the ability of BTFs in biodegrading formaldehyde at mesophilic conditions. Table S1 (see supplemental material) summarizes the studies discussed (Chen et al. Citation2010; Jamshidi et al. Citation2018; Maldonado-Diaz and Arriaga Citation2015; Rezaei, Fazlzadehdavil, and Hajizadeh Citation2015; Talaiekhozani et al. Citation2016; Teh and Mahmood Citation2013). A study by Talaiekhozani et al. (Citation2016) proved that BTFs could biodegrade formaldehyde with high removal efficiencies of 95, 97, and 99% at different gas flow rates of 90, 291, and 1512 L/h (Talaiekhozani et al. Citation2016). Chen et al. (Citation2010) have reported a max EC of 15 g m−3 h−1 at an LR of 15 g m−3 h−1 and an EBRT 10s (Chen et al. Citation2010). Controlling the pH was a critical factor in achieving an efficient performance of BTFs, as was reported by Maldonado-Diaz and Arriaga (Citation2015). The pH was adjusted using ozone, and the highest EC reported was 126.5 g m−3 h−1 at an LR of 126.5 g m−3 h−1. Jamshidi et al. (Citation2018) have also reported an average removal of the mean formaldehyde removal efficiency of 89.7 ± 5% for the highest operating concentration range of 7.58–9.5 ppmv (Jamshidi et al. Citation2018). A study by Rezaei, Fazlzadehdavil, and Hajizadeh (Citation2015) reported an EC of 4.0 g m−3 h−1 at LR of 5.4 g m−3 h−1 at an EBRT of 180 s. These studies strengthen our findings on the capability of BTFs of treating formaldehyde at mesophilic conditions.
For all three phases, the average VSS values for the effluent liquid were 20.3 6.4, 40.3
22.2, and 77.6
20.2 mg/L for phases I, II, and III, respectively. The VSS increased with increasing loading rates, suggesting an increase in biomass with an increase in the concentration of the effluent liquid. Effluent COD in mg/L averaged 9.4
11, 33.5
16.3, and 58.4
2.9 for phases I, II, and III, respectively. The COD of the nutrient solution in the holding tank was assumed to be zero. The source of the COD in the liquid effluent is the soluble fraction of the HAPs and their biodegradation byproducts. The effluent COD will be discussed further in Section 3.5.
The pH of the holding tank was, on average 8.23 0.32 for the three phases. The average pH for the liquid effluent was 8.72
0.05, 8.85
0.11, and 8.94
0.57 for phases I, II, and III, respectively. An increase in the pH level was observed for the three phases. This was expected because of the aerobic biodegradation of formaldehyde. No acidification was observed in the bed, as was noted in previous studies (Chen et al. Citation2010; Maldonado-Diaz and Arriaga Citation2015).
Nitrate was also measured in this study to investigate the uptake of nitrate by the microorganisms from the nutrient solution. The nutrient solution in the holding tank nitrate concentration was fixed at 495 mg/L, and the actual measured nitrate concentration in the holding tank was 467.8 Nitrate was used as a nitrogen source instead of ammonia because the utilization of Nitrogen from ammonia could develop a large number of nitrifying bacteria within the bed (Sorial et al. Citation1997). Nitrifying bacteria could hinder the availability of NH3-N to the VOC-biodegrading microbes and decrease the performance of those microbes in the bed (Sorial et al. Citation1997). The actual measured nitrate concentrations in mg/L in the liquid effluent throughout the three phases were 365.7
72.6,
54.3, and 183.6
68.3 mg/L for phases I, II, and III, respectively. As expected, the nitrate uptake by the microorganisms increased with increasing formaldehyde concentration throughout the three phases.
Performance of thermophilic BTF
Figure S2 (see supplemental material) demonstrates the effect of the influent concentration on the removal efficiency of the thermophilic BTF in the three phases. As shown in Figure S2, complete removal of formaldehyde was achieved throughout the three phases. For phase I, the target concentration was 20 ppmv, and the average removal efficiency for the entire phase was 97.0 6.0%. The highest recorded elimination capacity for phase I was 5.4 g m−3 h−1. Inconsistent loading affected the BTF removal efficiency. However, the removal efficiency never decreased below 76%.
For phase II, the target concentration was 50 ppmv. The average removal efficiency for the entire phase was 92.0 10.0%. The removal efficiency never decreased below 76%. The highest recorded elimination capacity for phase II was 14.1 g m−3 h−1. For phase III, the target concentration was 100 ppmv. The average removal efficiency for the entire phase was 96.7
3.0%. The removal efficiency never decreased below 92%. The highest recorded elimination capacity for phase III was 20.6 g m−3 h−1. The variability of influent formaldehyde concentrations was also observed for phases I and II, as was the case for the mesophilic BTF. For phase III, minimum variability was observed.
For the three phases, the average VSS values for the liquid effluent were 10.2 7.3, 17.2
11.6, and 43.1
9.3 mg/L for phases I, II, and III, respectively. The VSS increased with increasing loading rates, suggesting an increase in biomass. Effluent COD in mg/L averaged 14.2
4.0, 45.9
7.0, and 116.25
44.2 for phases I, II, and III, respectively.
No studies in the literature that we know of have evaluated formaldehyde at thermophilic conditions. However, two carbon compounds such as ethanol and acetaldehyde, were evaluated at thermophilic conditions. Duerschner, Aly Hassan, and Dvorak (Citation2020) evaluated the biodegradation of acetaldehyde at thermophilic conditions. The study reported a max EC of 28.9 g m−3 h−1 at an LR of 140 g m−3 h−1 with an EBRT of 32s (Duerschner, Aly Hassan, and Dvorak Citation2020). The poor performance was attributed to the low availability of acetaldehyde to the microorganisms due to the low solubility of acetaldehyde at higher temperatures (Duerschner, Aly Hassan, and Dvorak Citation2020). Cox et al. (Citation2001) reported a max EC for ethanol at 140 g m−3 h−1 when the LR was 160 g m−3 h−1. The EBRT used was 57s (Cox et al. Citation2001). It was noted that the solubility and bioavailability of formaldehyde to the microorganisms could be attributed to the lower performance at thermophilic conditions compared to the mesophilic BTF seen in this study observed by Duerschner, Aly Hassan, and Dvorak (Citation2020).
The average pH for the liquid effluent was 8.33 0.12, 8.54
0.0.34, and 8.73
0.55 for phases I, II, and III, respectively. An increase in pH levels was observed for the three phases, which was expected because of the aerobic biodegradation of formaldehyde. Similar to the mesophilic BTF, no acidification in the bed was observed.
The influent nitrate in the holding tank and its measured values are similar to those reported for the mesophilic BTF. The actual measured nitrate concentration in mg/L in the liquid effluent throughout the three phases was 377.0 45.3,
53.8, and 205.5
49.5 mg/L for phases I, II, and III, respectively. More nitrate uptake by the microorganisms was observed at higher influent formaldehyde concentrations. This is expected because of higher added carbon coming from the influent formaldehyde.
Biodegradation of methanol
Methanol and formaldehyde coexist in formalin solution. Methanol is used as a stabilizer in the formalin solution to prevent formaldehyde from polymerizing and volatilizing. Methanol constitutes ~15% of the volume of formalin. In this study, methanol biodegradability was investigated along with formaldehyde biodegradability (primarily because methanol is also found in ethanol plant waste gas streams).
Phases II and III corresponded to influent methanol concentrations of 12 and 24.5 ppmv, respectively. Unfortunately, data for phase I could not be extracted owing to technical difficulties with the analytical instrument. lists the operation duration, influent concentration, loading rate, elimination capacity, and removal efficiency for methanol for both BTFs. The actual measured concentrations for the mesophilic BTF were 16.4 8.8 and 26.1
5.9 ppmv in phases II and III, respectively. Similarly, for the thermophilic BTF, the actual measured concentrations in ppmv were 19.6
9.7 and 26.9
7.0 at phases II and III, respectively. The measured concentrations reflect an average of three samples collected on each operating day.
Table 2. Different operation phases for both mesophilic and thermophilic BTFs, with operating conditions such as duration, influent concentration, loading rate, elimination capacity, and removal efficiency for methanol biodegradation. Error ranges represent one standard deviation
shows the elimination capacity versus the loading rates of both BTFs for the biodegradation of methanol throughout phases II and III. The loading rate and elimination capacity along the bed depths have also been considered in . For both BTFs, the elimination capacity increased proportionally with the loading rate. From , if complete degradation occurs, the data points lie on the 1:1 line. This study did not establish a maximum elimination capacity for methanol. The highest elimination capacity recorded for methanol was 13.0 g m−3 h−1.
summarizes previous studies on the biofiltration of methanol, either individually or in a binary mixture with another substrate. The addition of methanol to VOC could have a positive, negative, or no impact on the biodegradation of other VOCs in a mixture. This depends on the BTF media, temperature, pH, nutrients, and VOC loading rates. Methanol biofiltration was studied individually and was effectively biodegraded to elimination capacities up to 330 g m−3 h−1 (Guerrero et al. Citation2019). Methanol in a mixture with H2S did not affect the biodegradation of H2S, indicating that the biodegradations of both compounds are mutually independent (Sologar, Lu, and Allen Citation2003).
Table 3. Summary of methanol biofiltration studies
Methanol can improve the biodegradation of compounds (e.g., formaldehyde, acetaldehyde). The presence of methanol had a positive impact on the biodegradability of n-hexane, with n-hexane being more readily bioavailable for microorganisms in a mixture with methanol (Zehraoui, Hassan, and Sorial Citation2013). In addition, adding methanol to a mixture with dimethyl sulfide improved the degradation of dimethyl sulfide by alleviating the pH in the BTF and enhancing biomass growth (Zhang, Liss, and Allen Citation2007).
In this study, the corresponding EBRT at which the highest elimination capacity was established was 3.9 s (port 2 mesophilic BTF). Prado, Veiga, and Kennes (Citation2004) investigated the biodegradation of methanol in a mixture with formaldehyde in a BTF. The study reported an elimination capacity of 2.3 g m−3 h−1 at a loading rate of 4.0 g m−3 h−1 (Prado, Veiga, and Kennes Citation2004). The corresponding EBRT was 71.9 s (Prado, Veiga, and Kennes Citation2004). In this study, a higher elimination capacity was observed for methanol at a lower EBRT than in the study by Prado, Veiga, and Kennes (Citation2004). Prado, Veiga, and Kennes (Citation2004) suggested that high methanol loading rates would affect formaldehyde removal because methanol is a more accessible carbon source for microorganisms.
The operating conditions of the studies listed in are different from those in this study. The loading rates of methanol in most of those studies are higher than those in our study (Guerrero et al. Citation2019; Sologar, Lu, and Allen Citation2003; Zehraoui, Hassan, and Sorial Citation2013; Zhang, Liss, and Allen Citation2007), resulting in higher elimination capacities. Moreover, different mixtures were used in some of the studies (Sologar, Lu, and Allen Citation2003; Zehraoui, Hassan, and Sorial Citation2013; Zhang, Liss, and Allen Citation2007), whereas the study by Prado, Veiga, and Kennes (Citation2004) had a mixture similar to that in our study. The packing materials used in most of the studies are different from those in our study (Guerrero et al. Citation2019; Prado, Veiga, and Kennes Citation2004; Sologar, Lu, and Allen Citation2003; Zhang, Liss, and Allen Citation2007), and the EBRTs of all the studies listed in are dissimilar to this studys’ packing.
Figure S3 (see supplemental material) demonstrates the effect of the influent methanol concentration on the efficiency of the mesophilic BTF in phases II and III. Complete removal of methanol was achieved in both phases. For phase II, the target methanol concentration was 12 ppmv. The average removal efficiency for the entire phase was 97.6 3.3%. The removal efficiency never decreased below 86%. The average elimination capacity for phase II was 3.4
1.9 g m−3 h−1. For phase III, the target concentration was 24.5 ppmv. The average removal efficiency for the entire phase was 97.1
6.1%. The removal efficiency never decreased below 82%. The average elimination capacity for phase III was 5.4
1.2 g m−3 h−1.
Figure S4 (see supplemental material) demonstrates the effect of the influent methanol concentration on the efficiency of the thermophilic BTF in phases II and III. Complete removal of methanol was achieved in both phases. For phase II, the target methanol concentration was 12 ppmv. The average removal efficiency for the entire phase was 92.8 5.0%. The removal efficiency never decreased below 86%. The average elimination capacity for phase II was 3.4
1.8 g m−3 h−1. For phase III, the target concentration was 24.5 ppmv. The average removal efficiency for the entire phase was 97.9
3.7%. The removal efficiency never decreased below 82%. The average elimination capacity for phase III was 4.9
1.2 g m−3 h−1.
Carbon mass balance
To confirm the approximate fractionation of CO2 in the effluent water stream and gaseous CO2 as a byproduct of microbial degradation, a mass balance on carbon in the BTFs was performed. shows the carbon mass balance for each BTF. The only source of input carbon in this figure is the feed of gaseous formaldehyde. Inorganic carbon sources are not considered. The house air used to volatilize formaldehyde, which contains CO2, is considered but subtracted from the effluent CO2. CO2 is measured using the u-GC. The effluent carbon in the gas phase includes CO2 and nondegraded formaldehyde. COD is the only source of effluent carbon in the liquid phase. COD composition includes microorganisms, soluble byproducts, and dissolved formaldehyde. Identification of byproducts was not feasible because of the unavailability of instruments needed to quantify these byproducts. For the mesophilic BTF, the influent carbon was transformed into approximately 69%, 49%, and 46% of CO2 for phases I, II, and III, respectively. For the thermophilic BTF, the influent carbon was transformed into approximately 48.6%, 26.5%, and 26.4% of CO2 for phases I, II, and III, respectively. The mass balance shows an increase in CO2 and COD occurs with increasing loading rate, indicating that the elimination capacity increases as the loading rate increases. CO2 production did not stabilize with an increase in loading rates, suggesting that a maximum elimination capacity was not reached for both BTFs.
BTF performance at 16°C and 40°C
This section collates the results from the biodegradation of formaldehyde at 16°C and 40°C. The mesophilic BTF was used for the operation of the BTF at 16°C, and the thermophilic BTF was used for the operation of the 40°C BTF. Except for the temperature change, the operating conditions remained the same as those in phase III. The target influent formaldehyde concentration was 100 ppmv. The actual measured influent concentrations for BTF at 16°C and 40°C were 109.0 20.8 and 108.0
12.5 ppmv, respectively.
shows the loading rate versus the elimination capacity for both BTFs. The loading rate and elimination capacity along the bed depths have also been considered in . shows that as the loading rate increases, the elimination capacity increases. A maximum elimination capacity of 30 g m−3 h−1 was established for the BTF at 40°C. For the BTF at 16°C, no maximum elimination capacity was established; however, the highest reported elimination capacity was 45.0 g m−3 h−1. The temperature change affected the removal efficiencies of both BTFs compared with the mesophilic and thermophilic BTFs discussed previously.
Figure S5 (see supplemental material) shows the effect of the influent formaldehyde concentration on the removal efficiencies of the BTFs at 16°C and 40°C. The average removal efficiency for the entire phase for the BTF at 16°C was 76.7 18.2%. The lowest removal was 30% on day 3 of operating the BTF. However, the removal efficiency did not decrease below 40.0% afterward. The average elimination capacity for the BTF at 16°C was 12.1
3.3 g m−3 h−1 at an average loading rate of 15.8
2.9 g m−3 h−1. For the BTF operated at 40°C, the average removal efficiency for the entire operating period was 76.2
21.2%. The average elimination capacity for the BTF at 40°C was 11.1
3.3 g m−3 h−1 at an average loading rate of 14.5
1.7 g m−3 h−1.
The average VSS values for both BTFs at 16°C and 40°C were 139.3 50.8 and 89.9
2.9 mg/L, respectively. Effluent COD in mg/L averaged 191.75
71.5 and 223.9
40.2 for BTFs at 16°C and 40°C, respectively. The average pH for the liquid effluent is 8.75
0.38 and 8.67
0.41 for BTFs at 16°C and 40°C, respectively. The average nitrate in the liquid effluent averaged for the BTFs at 16°C, and 40°C was 192.4
83.2 and 220.2
67.3 mg/L, respectively.
Methanol biodegradation was also investigated in this study. shows that as the loading rate increases, the elimination capacity of methanol increases. No maximum elimination capacity was established; however, the highest elimination capacity recorded for both BTFs at 16°C and 40°C was 30.0 and 23.6 g m−3 h−1, respectively.
Higher elimination capacities were obtained for the BTFs at 16°C and 40°C as compared with the mesophilic and thermophilic BTFs as discussed previously. A reason for this observation was the higher variations of methanol influent concentration, as shown in Figure S6 (see supplemental material). Figure S6 shows that the influent methanol concentration was higher than the target for days 5–10 and 15–25 in the 16°C BTF. This explains why the BTF at 16°C had higher elimination capacities than the mesophilic BTF, where the variations in influent methanol concentrations were not as high. The variations were also observed for the BTF at 40°C, which explains the higher elimination capacity observed because of, the higher varied methanol loading rates. The average removal efficiency for both BTFs at 16°C and 40°C was 84.6 17.9% and 77.7
20.3%, respectively.
Formaldehyde biodegradation pathways
There are diverse microorganisms that have the capability of metabolizing formaldehyde in nature. The microbes that have been identified to degrade formaldehyde are bacteria, fungi, yeast, and marine algae (Shao et al. Citation2020). Methylobacterium sp. MF1 and Methylobacterium sp. XJLW (Mitsui et al. Citation2006; Qiu et al. Citation2014; Shao et al. Citation2020) are bacterial strains that are identified to metabolite formaldehyde. Also, Aspergillus nomius, Debaryomyces vanriji, and Nannochloropsis, which are fungi, yeasts, and marine algae strains, respectively (Shao et al. Citation2020). These microorganisms can be obtained through wastewater or the soil, depending on the strain needed (Shao et al. Citation2020).
Generally, C1 compounds are metabolized by first the oxidation of the C1 compound to formaldehyde, then the oxidation of formaldehyde to carbon dioxide, and finally the absorbtion into the biomass (Shao et al. Citation2020). There are many means by which formaldehyde is oxidized based on the literature. The most widespread pathway uses tetrahydromethanoprotein (H4MPT) as the cofactor (Chistoserdova Citation2011; Shao et al. Citation2020). In the H4MPT pathway, the formaldehyde and the H4MPT are reacted to form methylene- H4MPT, which is catalyzed by the formaldehyde-activating enzyme (fae) (Chistoserdova Citation2011; Shao et al. Citation2020). The formaldehyde is then carried away through the H4MPT pathway to produce formic acid, which then is transferred using the formate dehydrogenase to become water and carbon dioxide, while the C1 unit is assimilated into serine cycle by employing the tetrahydrofolate (H4F) pathway (Shao et al. Citation2020). It is to be noted that if fae does not exist, this will lead to inefficient metabolization and detoxification of formaldehyde, where the C1 unit goes directly into the H4F pathway. The H4F pathway is carried out by the MtdA and Fch enzymes (Chistoserdova Citation2011; Shao et al. Citation2020). The pathway acts in a reductive manner to reach the serine cycle (Chistoserdova Citation2011; Shao et al. Citation2020). The ribulose monophosphate pathway (RuMP) is another pathway used to detoxify formaldehyde by microorganisms (Shao et al. Citation2020).
It is important to consider these pathways and how microorganisms degrade formaldehyde to apply them on a pilot/industrial level. The regulatory functions and enzymes used to carry the reactions could improve our understanding of what microorganisms to choose for our application. This finding can help us avoid problems in our BTF, such as spores or the possibility of leakage of the bacteria out of the BTF.
Conclusions
Replacing scrubbers and RTOs with BTFs is feasible for controlling formaldehyde and methanol emissions from fermentation tanks and DDGS dryers’ emission streams in ethanol plants. Both the mesophilic (25°C) and thermophilic (60°C) BTFs successfully biodegraded formaldehyde fumes with high removal efficiency at typical concentrations at ethanol plants. It was concluded that BTFs could successfully remove formaldehyde from waste gas streams from ethanol plants at typical emissions of 21 ppmv from fermentation tanks at ambient and 30 ppmv from the dryers at elevated temperatures. The polymerization of formaldehyde can be reduced by adding NaOH to pH levels between 7.00 and 7.40 and heating the solution to 60°C. Further research is needed to investigate the ability of a pilot-scale BTF reactor at ethanol plants to remove the mixture of contaminants introduced by the waste gases of ethanol production.
Suppl_Materials_Final_Clean.docx
Download MS Word (2.4 MB)Acknowledgment
This work was supported by the Nebraska Center for Energy Sciences Research (NCESR), Cycle 13.
Disclosure statement
No potential conflict of interest was reported by the author(s).
Data availability statement
The data is available upon request from AAH at [email protected].
Supplementary material
Supplemental data for this paper can be accessed on the publisher’s website
Additional information
Funding
Notes on contributors
Mitham Al-Faliti
Mitham Al-Faliti is currently a PhD student at Howard University based in Washington D.C. Mitham obtained his master’s from the University of Nebraska-Lincoln with focus on the biological treatment of hazardous air pollutants from ethanol plants. Currently Mitham’s research focus in his PhD is wastewater-based epidemiology and quorum sensing.
Bruce Dvorak
Bruce Dvorak is a Professor at the University of Nebraska-Lincoln. Dr. Dvorak is a licensed professional engineer with over 30 years of experience. Dr. Dvorak’s efforts in research have developed outreach programs that improves environmental sustainability for both water and industrial systems. Dr. Dvorak’s research focus includes life cycle assessment, physical-chemical treatment process, environmental engineering, and sustainability of water and wastewater systems.
Ashraf Aly Hassan
Ashraf Aly Hassan is an Assistant Professor at the United Arab Emirates University based in Abu Dhabi. Previously, he used to work at the University of Nebraska Lincoln, Nebraska Department of Environmental quality and also, he worked at the Environmental Protection Agency. Dr. Ashraf has over 20 years of experience of practicing environmental engineering and he is also a licensed professional engineer. Dr. Ashraf’s research focus includes, biotrickling filters, biological treatment of hazardous air pollutants, and biological desalination.
References
- APHA. 2005. Standard methods for the examination of water and wastewater. Washington, DC: American Public Health Association.
- Bak, A., V. Kozik, P. Dybal, S. Sulowicz, D. Kasperczyk, S. Kus, and Barbusinski, K. 2017. Abatement robustness of volatile organic compounds using compact trickle-bed bioreactor: Biotreatment of styrene, ethanol and dimethyl sulfide mixture in contaminated airstream. Int. Biodeterior. Biodegradation 119:316–28. doi:https://doi.org/10.1016/j.ibiod.2016.10.039.
- Barbusiński, K., K. Urbaniec, D. Kasperczyk, and M. Thomas. 2020. Biofilters versus bioscrubbers and biotrickling filters: State-of-the-art biological air treatment. In From biofiltration to promising options in gaseous fluxes biotreatment, eds. G. Soreanu, and É. Dumont, 29–51. Elsevier. doi:https://doi.org/10.1016/B978-0-12-819064-7.00002-9.
- Brady, D., and G. C. Pratt. 2012. Volatile organic compound emissions from dry mill fuel ethanol production. J. Air Waste Manag. Assoc. 57 (9):1091–102. doi:https://doi.org/10.3155/1047-3289.57.9.1091.
- Bruneel, J., C. Walgraeve, J. Mukurarinda, N. Boon, and H. Van Langenhove. 2018. Biofiltration of hexane, acetone and dimethyl sulphide using wood, compost and silicone foam. J. Chem. Technol. Biotechnol. 93 (8):2234–43. doi:https://doi.org/10.1002/jctb.5566.
- Chen, L. J., K. M. Bangs, K. A. Kinney, L. E. Katz, and S. A. Frank. 2010. Biofiltration of simulated air pollutants from Distillers Dried Grains with Solubles (DDGS) dryer vents at corn-derived ethanol plant production facilities. Environ. Prog. Sustain. Energy 29 (1):116–26.
- Chistoserdova, L. 2011. Modularity of methylotrophy, revisited. Environ. Microbiol. 13 (10):2603–22. doi:https://doi.org/10.1111/j.1462-2920.2011.02464.x.
- Cohen, G., N. Kreutzer, K. Mowat, A. A. Hassan, and B. Dvorak. 2021. Compliance with hand sanitizer quality during the SARS-CoV-2 pandemic: Assessing the impurities in an ethanol plant. J. Environ. Manage. 297:113329. doi:https://doi.org/10.1016/j.jenvman.2021.113329.
- Cox, H. H. J., T. Sexton, Z. M. Shareefdeen, and M. A. Deshusses. 2001. Thermophilic biotrickling filtration of ethanol vapors. Environ. Sci. Technol. 35 (12):2612–19. doi:https://doi.org/10.1021/es001764h.
- Crocker, B., and K. Schnelle. 1998. Air pollution control for stationary sources. In Encyclopedia of environmental analysis and remediation, ed. R. A. Meyers, 1–2. New York: John Wiley and Sons, Inc.
- Delhoménie, M., and M. Heitz. 2005. Biofiltration of air : A review. Crit. Rev. Biotechnol. 8551 (25):53–72. doi:https://doi.org/10.1080/07388550590935814.
- Deshusses, M. A., and H. H. J. Cox. 1999. A cost benefit approach to reactor sizing and nutrient supply for biotrickling filters for air pollution control. Environ. Prog. 18 (3):188–96. doi:https://doi.org/10.1002/ep.670180315.
- Dobslaw, D., K. Engesser, H. Störk, and T. Gerl. 2019a. Low-cost process for emission abatement of biogas internal combustion engines. J. Clean. Prod. 227:1079–92. doi:https://doi.org/10.1016/j.jclepro.2019.04.258.
- Dobslaw, D., J. Schöller, D. Krivak, S. Helbich, and K.-H. Engesser. 2019b. Performance of different biological waste air purification processes in treatment of a waste gas mix containing tert-butyl alcohol and acetone: A comparative study. Chem. Eng. J. 355:572–85. doi:https://doi.org/10.1016/j.cej.2018.08.140.
- Dobslaw, D., A. Schulz, S. Helbich, C. Dobslaw, and K. Engesser. 2017. VOC removal and odor abatement by a low-cost plasma enhanced biotrickling filter process. J. Environ. Chem. Eng. 5 (6):5501–11. doi:https://doi.org/10.1016/j.jece.2017.10.015.
- Duerschner, C., A. Aly Hassan, and B. Dvorak. 2020. Biofiltration of acetaldehyde resulting from ethanol manufacturing facilities. Chemosphere 241 (2):124982. doi:https://doi.org/10.1016/j.chemosphere.2019.124982.
- Fulazzaky, M. A., A. Talaiekhozani, and M. Z. Abd Majid. 2016. Formaldehyde removal mechanisms in a biotrickling filter reactor. Ecol. Eng. 90:77–81. doi:https://doi.org/10.1016/j.ecoleng.2016.01.064.
- Fulazzaky, M. A., A. Talaiekhozani, M. Z. A. Majid, M. Ponraj, and A. Goli. 2013. Evaluation of gas retention time effects on the bio-trickling filter reactor performance for treating air contaminated with formaldehyde. RSC Adv. 3 (38):17462. doi:https://doi.org/10.1039/c3ra41391h.
- Gabriel, D., and M. A. Deshusses. 2003. Retrofitting existing chemical scrubbers to biotrickling filters for H2S emission control. Proc. Natl. Acad. Sci. 100 (11):6308–12. doi:https://doi.org/10.1073/pnas.0731894100.
- Garcia, C. A., P. S. Yap, H. Y. Park, and B. L. Weller. 2015. Association of long-term PM2.5 exposure with mortality using different air pollution exposure models: Impacts in rural and urban California. Int. J. Environ. Health Res. 26:1–13. doi:https://doi.org/10.1080/09603123.2014.1003040.
- Goldman, E., and R. Jacobs. 1961. Determination of nitrates by ultraviolet absorption. J. Am. Water Works Assoc. 53 (2):187–91. JSTOR. doi:https://doi.org/10.1002/j.1551-8833.1961.tb00651.x.
- Guerrero, K., A. Arancibia, M. Caceres, and G. Aroca. 2019. Release of formaldehyde during the biofiltration of methanol vapors in a peat biofilter inoculated with Pichia pastoris GS115. Electron. J. Biotechnol. 40:10–16. doi:https://doi.org/10.1016/j.ejbt.2019.04.003.
- Hoather, R. C., and R. F. Rackham. 1959. Oxidised nitrogen in waters and sewage effluents observed by ultra-violet spectrophotometry. Analyst 84 (1002):548–51. doi:https://doi.org/10.1039/an9598400548.
- Hoek, G., R. M. Krishnan, R. Beelen, A. Peters, B. Ostro, B. Brunekreef, and J. D. Kaufman. 2013. Long-term air pollution exposure and cardio- respiratory mortality: A review. Environ. Health 12 (1):43–57. doi:https://doi.org/10.1186/1476-069X-12-43.
- IARC. 2011. Formaldehyde. AIRC Monographs. https://monographs.iarc.fr/wpcontent/uploads/2018/06/mono100F-29.pdf.
- Jamshidi, A., Y. Hajizadeh, -M.-M. Amin, G. Kiani, R. Haidari, K. Falahi‐Nejad, and I. Parseh. 2018. Biofiltration of formaldehyde, acetaldehyde, and acrolein from polluted airstreams using a biofilter. J. Chem. Technol. Biotechnol. 93 (5):1328–37. doi:https://doi.org/10.1002/jctb.5496.
- Karre, A., K. Jones, J. Boswell, and J. Paca. 2012. Evaluation of VOC emissions control and opacity removal using a biological sequential treatment system for forest products applications. J. Chem. Technol. Biotechnol. 87 (6):797–805. doi:https://doi.org/10.1002/jctb.3779.
- Kiernan, J. A. 2000. Formaldehyde, formalin, paraformaldehyde and glutaraldehyde: What they are and what they do. Micros. Today 8 (1):8–12. doi:https://doi.org/10.1017/S1551929500057060.
- Liu, J., J. Sun, C. Lu, X. Kang, X. Liu, and P. Yue. 2021. Performance and substance transformation of low-pH and neutral-pH biofilters treating complex gases containing hydrogen sulfide, ammonia, acetic acid, and toluene. Environ. Sci. Pollut. Res. 28 (23):30058–69. doi:https://doi.org/10.1007/s11356-021-12602-9.
- Lyndon, J. 2019. Nebraska, Personal Communications with M. Al-Faliti, June 2019.
- Maldonado-Diaz, G., and S. Arriaga. 2015. Biofiltration of high formaldehyde loads with ozone additions in long-term operation. Appl. Microbiol. Biotechnol. 99 (1):43–53. doi:https://doi.org/10.1007/s00253-014-5848-7.
- Malhautier, L., J. Rocher, O. Gouello, J. Jobert, C. Moura, Y. Gauthier, A. Bertin, J. Després, and J. Fanlo. 2021. Treatment of gaseous emissions from tire manufacturing industry using lab-scale biofiltration pilot units. J. Hazard. Mater. 420:126614. doi:https://doi.org/10.1016/j.jhazmat.2021.126614.
- Mitsui, R., Kitazawa, H., Sato, T., & Tanaka, M. (2006). Formaldehyde uptake by Methylobacterium sp. MF1 and Acidomonas methanolica MB 58 with the different formaldehyde assimilation pathways. Environmental Sciences, 13, 185–192
- Mustafi, N. N., R. R. Raine, and P. K. Bansal. 2006. The use of biogas in internal combustion engines: A review. Proceedings of the ASME 2006 Internal Combustion Engine Division Spring Technical Conference. ASME 2006 Internal Combustion Engine Division Spring Technical Conference (ICES2006), Aachen, Germany, May 7–10. ASME. pp.225–34. doi:https://doi.org/10.1115/ices2006-1306.
- Navone, R. 1964. Proposed method for nitrate in potable waters. J. AWWA 56 (6):781–83. doi:https://doi.org/10.1002/j.1551-8833.1964.tb01270.x.
- Nester, J. L. 2007. The importance of a flexible emissions control system deisgn. Ethanol Producer Magazine. http://ethanolproducer.com/articles/3106/the-importance-of-a-flexible-emissions-control-system-design.
- Pérez, M. C., F. J. Álvarez-Hornos, K. Portune, and C. Gabaldón 2015. Abatement of styrene waste gas emission by biofilter and biotrickling filter: comparison of packing materials and inoculation procedures. Appl. Microbiol. Biotechnol. 99 (1):19–32. doi:https://doi.org/10.1007/s00253-014-5773-9.
- Prado, Ó. J., M. C. Veiga, and C. Kennes. 2004. Biofiltration of waste gases containing a mixture of formaldehyde and methanol. Appl. Microbiol. Biotechnol. 65 (2):235–42. doi:https://doi.org/10.1007/s00253-004-1616-4.
- Qiu, L., W. Chen, L. Zhong, W. Wu, S. Wu, J. Chen, F. Zhang, & W. Zhong. (2014). Formaldehyde biodegradation by immobilized Methylobacterium sp. XJLW cells in a three-phase fluidized bed reactor. Bioprocess and biosystems engineering 37 (7):1377–84. doi:https://doi.org/10.1007/s00449-013-1110-4
- Rezaei, M., M. Fazlzadehdavil, and Y. Hajizadeh. 2015. Formaldehyde removal from airstreams using a biofilter with a mixture of compost and woodchips medium. Water Air Soil Pollut. 226 (2242). doi:https://doi.org/10.1007/s11270-014-2242-0.
- Ryu, H. W., K.-S. Cho, and T.-H. Lee. 2011. Reduction of ammonia and volatile organic compounds from food waste-composting facilities using a novel anti-clogging biofilter system. Bioresour. Technol. 102 (7):4654–60. doi:https://doi.org/10.1016/j.biortech.2011.01.021.
- San-Valero, P., A. Dorado, V. Martínez-Soria, and C. Gabaldón. 2017. Biotrickling filter modeling for styrene abatement. Part 1: Model development, calibration and validation on an industrial scale. Chemosphere 191:1066–74. doi:https://doi.org/10.1016/j.chemosphere.2017.10.069.
- Seignez, C., N. Adler, C. Thoeni, M. Stettler, P. Pringer, and C. Holliger. 2004. Steady-state and transient-state performance of a biotrickling filter treating chlorobenzene-containing waste gas. Appl. Microbiol. Biotechnol. 65 (1). doi: https://doi.org/10.1007/s00253-003-1531-0.
- Shao, Y., Y. Wang, R. Zhao, J. Chen, F. Zhang, R. J. Linhardt, and W. Zhong. 2020. Biotechnology progress for removal of indoor gaseous formaldehyde. Appl. Microbiol. Biotechnol. 104 (9):3715–27. doi:https://doi.org/10.1007/s00253-020-10514-1.
- Sologar, V. S., Z. Lu, and D. G. Allen. 2003. Biofiltration of concentrated mixtures of hydrogen sulfide and methanol. Environ. Prog. 22 (2):129–36. doi:https://doi.org/10.1002/ep.670220215.
- Sorial, B. G. A., F. L. Smith, M. T. Suidan, A. Pandit, P. Biswas, and R. C. Brenner. 1997. Evaluation of trickle bed air biofilter performance for BTEX removal. Environ. Eng. 123 (6):530–37. doi:https://doi.org/10.1061/(ASCE)0733-9372(1997)123:6(530).
- Sorrels, J. L., A. Baynham, D. Randall, and C. Hancy. 2017. Chapter 2—Incinerators and oxidizers. 70. Environmental Protection Agency (EPA).
- Talaiekhozani, A., M. R. Talaei, M. A. Fulazzaky, and H. N. Bakhsh. 2016. Evaluation of contaminated air velocity on the formaldehyde removal efficiency by using a biotrickling filter reactor. J. Air Pollut. Health 1 (3):171–80.
- Teh, S. J., and N. Z. Mahmood. 2013. Potential of vermicompost as biofilter for the removal of formaldehyde (Doctoral dissertation, Jabatan Kejuruteraan Kimia, Fakulti Kejuruteraan, Universiti Malaya). 2nd International Conference on Environment, Energy and Biotechnology, 11–15.
- United States Congress. 2007. Energy information and security act of 2007. 110th Congress, Washington, DC.
- U.S. Energy Information Administration. 2019. Natural gas price. https://www.eia.gov/dnav/ng/ng_pri_sum_dcu_nus_m.htm.
- U.S. Energy Information Administration. 2020. U.S. fuel ethanol production capacity increased by 3% in 2019. https://www.eia.gov/todayinenergy/detail.php?id=45316.
- USEPA. 2003. Using bioreactors to control air pollution. https://www3.epa.gov/ttncatc1/dir1/fbiorect.pdf.
- USEPA. 2016. RACT/BACT/LAER clearinghouse. Technology Transfer Network Clearn Ir Technology Center. https://www3.epa.gov/ttncatc1/rblc/htm/welcome.html
- USEPA. 2017a. Initial list of hazardous air pollutants with modifications. https://www.epa.gov/haps/initial-list-hazardous-air-pollutants-modifications.
- USEPA. 2017b. Area source standards. https://www3.epa.gov/airtoxics/area/arearules.html#final.
- USEPA. 2019. RACT/BACT/LAER clearinghouse. Clean Air Technology Center. https://www.epa.gov/catc/ractbactlaer_clearinghouse_rblc_basic_information.
- USEPA. n.d. Monitoring by control technique – Catalytic oxidizer. https://www.epa.gov/air-emissions-monitoring-knowledge-base/monitoring-control-technique-catalytic-oxidize.
- Wang, J., and J. Chen. 2006. Removal of dichloromethane from waste gases with a bio-contact oxidation reactor. Chem. Eng. J. 123 (3):103–07. doi:https://doi.org/10.1016/j.cej.2006.06.023.
- Wu, H., H. Yan, Y. Quan, H. Zhao, N. Jiang, and C. Yin. 2018. Recent progress and perspectives in biotrickling filters for VOCs and odorous gases treatment. J. Environ. Manage. 222:409–19. doi:https://doi.org/10.1016/j.jenvman.2018.06.001.
- Xu, Z., N. Qin, J. Wang, and H. Tong. 2010. Formaldehyde biofiltration as affected by spider plant. Bioresour. Technol. 101 (18):6930–34. doi:https://doi.org/10.1016/j.biortech.2010.03.128.
- Zehraoui, A., A. A. Hassan, and G. A. Sorial. 2013. Biological treatment of n-hexane and methanol in trickle bed air biofilters under acidic conditions. Biochem. Eng. J. 77:129–35. doi:https://doi.org/10.1016/j.bej.2013.06.001.
- Zhang, Y., S. N. Liss, and D. G. Allen. 2007. Enhancing and modeling the biofiltration of dimethyl sulfide under dynamic methanol addition. Chem. Eng. Sci. 62 (9):2474–81. doi:https://doi.org/10.1016/j.ces.2007.01.035.