ABSTRACT
The applications of polypropylene/carbon fiber (PP/CF) composite are hindered by the high flammability of PP substrate. This work reports a facile solvothermal method to modify CF though grafting maleic anhydride (MAH) on its surface, with the goal of enhancing the compatibility of intumescent flame retardant (IFR) with PP substrate, thus enhancing the flame-retardant and mechanical performance of the resulting PP/CF/IFR composite. The effect of maleic anhydride-g-carbon fiber (MAH-g-CF) to IFR ratio on the overall performance of the composite was assessed. The possible interactions between MAH-g-CF and IFR were characterized by dynamic thermomechanical analysis and Fourier-transform infrared spectroscopy. Results show that when 3 wt% MAH-g-CF and 22 wt% IFR were added to the PP substrate, the composite exhibited a much lower heat release rate value and smoke suppression ability. Meanwhile, the composites achieved 26.7 MPa in tensile strength and 50.6 MPa in flexural strength. We propose that MAH on MAH-g-CF acts as a compatibilizer that improves the adhesion and cross-linking between CF and IFR, thereby enhancing mechanical strength and flame-retardancy of the PP/IFR/MAH-g-CF composite.
GRAPHICAL ABSTRACT
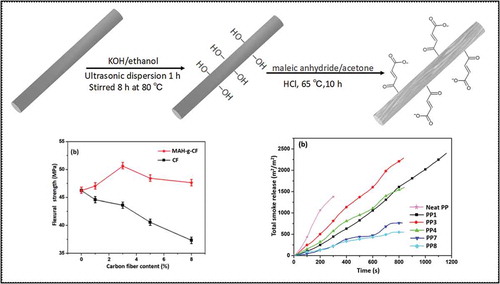
1. Introduction
Carbon fibers (CFs) have been widely used as structural materials to reinforce polypropylene (PP) due to its outstanding skeleton support effect [Citation1–Citation3]. CF is capable of endowing high strength and stability to PP substrate through improving stress transfer ability at the phase interface when certain amount of CFs was added [Citation4]. However, the high flammability of PP substrate challenges its applications [Citation5].
Recent works have put much efforts to reduce the flammability of PP through adding flame retardant [Citation6,Citation7]. Among the R&D flame retardants, intumescent flame retardant (IFR) has been regarded as the most promising one. It is generally composed of three ingredients: an acid source, a charring agent and a blowing agent [Citation8–Citation10]. Ammonium polyphosphate (APP) is widely used as both acid agent and blowing agent in IFR system. Acid agent can catalyze charring agent cross-linking and the blowing agent promotes the char expanded to develop intumescent char at the surface of polymer, which serves as a barrier to restrain heat transfer between the heat source and the condensed phase [Citation11]. Furthermore, charring agent is also an important part of IFR system. IFR was initially developed by Camino et al. [Citation12] and Bourbigot et al. [Citation13] and its composition was further optimized in recent years. For example, Li and his co-workers developed a hyperbranched triazine charring agent (ETPC). This PP/ETPC-based IFR composites exhibit favorable water resistance and higher Limiting Oxygen Index (LOI) value (34%) at 24 wt% of ETPC-based IFR [Citation14]. Basically, it has been well established that the excellent synergistic effect of P-N elements promotes the formation of cross-linked char layers in the condensed phase, resulting in the enhancement of the flame retardancy performance [Citation15,Citation16].
Recent works have also shown IFR was effective to improve flame retardancy of various CF-reinforced composites [Citation17,Citation18]. Zhao et al. reported that CF could be used as a synergistic agent to limit smoke release. When 5 wt% CF and 15 wt% APP were incorporated, the prepared Thermoplastic polyurethane (TPU) composites exhibited favorable flame retardancy and outstanding smoke suppression performance [Citation19]. However, most of the studies mainly focus on improving the mechanical and flame-retardant properties of the polymer while ignoring the interactions among CF, IFR and PP. Due to the smooth and chemically inert surface of neat CF, it cannot maximize its potential to boost the performance. Therefore, improving compatibility between the CF, IFR and PP is important for improving the mechanical and flame-retardant properties. In order to increase the interfacial adhesion, some promising ways to decorate CF such as surface oxidation [Citation20], electrochemical modification [Citation21], introducing some active groups onto CF surface to improve surface activity and roughness have been developed, which could reduce stress concentration and enhance mechanical interlocking [Citation22,Citation23].
Herein, a functional carbon-based filler, maleic anhydride grafted carbon fiber (MAH-g-CF), was synthesized via a facile solvothermal method. The chemical structure of MAH-g-CF was characterized by Raman and Fourier-transform infrared (FTIR) spectra. In addition, MAH-g-CF was added into the PP/IFR composite to improve its mechanical and flame retardancy performance. The possible mechanism of flame-retardant enhancement was initially proposed. This work shows a facile technique route to enhance the flame retardancy of PP/IFR composite without compromising its mechanical performance, which could be extended to other engineered polymer composites.
2. Experimental
2.1 Materials
PP (T30S) was supplied by Sinopec Beihai Co. Ltd. (Beihai, P. R. China). APP was obtained from Zhejiang Tianyuan Chemical Industry Co. Ltd. (Jinhua, P. R. China). CFs of HTS340 type were purchased from Toho Lamac Co. Ltd. (Tokyo, Japan). Maleic anhydride (MAH) was obtained from Tianjin Damao Chemical Reagent Co. Ltd. (Tianjin, P. R. China). Hydrochloric acid (HCl), acetone and anhydrous ethanol were purchased from Tianjin Zhiyuan Chemical Reagent Co. Ltd. (Tianjin, P. R. China). IFR was comprised of APP and triazine-based char-forming agent. The structure of triazine-based char-forming agent is shown in .
2.2 Preparation
2.2.1. Maleic anhydride grafted carbon fiber
CF-OH was prepared according to the typical procedure. First, 2.5 g CF was added into a flask containing 1 g KOH and 40 ml ethanol [Citation24]. After ultrasonic dispersion for 0.5 h, the mixture was poured into a Teflon reaction kettle and reacted at 85 °C under vacuum for 10 h. The resulting particles were collected via filtration, washed with ethanol three times and dried under vacuum at 65 °C overnight.
Six grams of MAH and 1.5 ml HCl were dispersed in acetone via ultrasonication for 0.5 h. Then the solution and 3 g CF-OH were placed into a Teflon reaction kettle and kept at 65 °C for 8 h. The resulting MAH-g-CFs were collected by filtration and washed with ethanol and deionized water to remove the residual acid. The obtained particles were dried under vacuum at 65 °C overnight. The relevant synthesis steps are shown in .
2.2.2. Preparation of PP/IFR/MAH-g-CF composites
All samples were prepared according to the formulation in by a two-roll mill at a temperature range of 180–185 °C for 15 min. After mixing, the samples were hot-pressed under 10 MPa for 5 min at about 185 °C into a sheet of suitable size for analysis.
Table 1. The content of neat PP, PP/IFR, PP/IFR/CF and PP/IFR/MAH-CF composites.
2.3 Characterization
Thermogravimetric analysis (TGA) was performed on a TGA400 thermo-analyzer instrument (PerkinElmer Inc., Fremont, CA, USA) from room temperature to 700 °C at a linear heating rate of 10 °C·min−1 under air and nitrogen (N2) atmospheres, respectively. Each sample was tested in an Al2O3 crucible with a weight about 5–8 mg. FTIR spectra were recorded with a VERTEX70 spectrometer (Bruker Instrument Co. Ltd., Dresden, Germany) with thin films of KBr at room temperature. The measurement was carried out in the optical range of 4000–500 cm−1. Raman measurements were performed with a LabRam HR Evolution Raman microscope (Horiba France Sas, Palaiseau, France), using an Ar+ ion laser with excitation wavelength of 514 nm. The morphology of CF, the char residues and its dispersion in PP were observed using a JSM-7001F scanning electron microscope (SEM; Japan Electron Optics Laboratory Co. Ltd., Tokyo, Japan). Dynamic mechanical analysis (DMA) was carried out with a DMA 2980 setup (TA Instruments, Newcastle, DE, USA) on samples with of 50 × 10 × 3 mm. The heating rate was 3 °C min−1 from −50 to 150 °C.
The combustion performance of the composites was tested on a vertical burning instrument (CFZ-2, Jiangning Analysis Instrument Co., Nanjing, P. R. China). Each sample was tested with dimensions of 127 × 12.7 × 3.2 mm, according to UL-94 test standard (ASTM D3801). The flame retardancy properties of PP and its composites were characterized via cone calorimeter test (CCT) based on ASTM E1354/ISO 5660. Each sample with the size of 100 × 100 × 4 mm burned at a heat flux of 50 kW/m2.
The mechanical performance of the composites was examined using Instron universal test machine UT4304 (SANS Instrument Co. Ltd., Shanghai, P. R. China) at a crosshead speed of 50 mm/min. The sample size was 150 × 10 × 4 mm for tensile test and 80 × 10 × 4 mm for flexural test.
3. Results and discussion
3.1 Characterization of MAH-g-CF
presents a comparison of the FTIR spectra of CF, CF-OH and MAH-g-CF in the spectral range of 4000–500 cm−1. For the spectrum of CF, there was no obvious absorption peak at high wavenumbers due to the poor activity of CF. However, a strong and broad adsorption band appeared at 3447 cm−1 after KOH/ethanol treatment, which was attributed to the stretching vibration of −OH bands, indicating that CF was successfully hydroxylated. After surface modification, the FTIR spectrum of MAH-g-CF exhibited several featured absorption modification bands [Citation25]. As shown in , the absorption bands at 1666 and 759 cm−1 became broad, which could be attributed to C double bond (C=C). In addition, the peak at about 900 cm−1 assigned to C−O−C in MAH was disappeared, indicating that the five-membered rings in MAH are completely opened [Citation26,Citation27]. The peaks at 1795 and 1274 cm−1 are characteristic of C=O stretching vibration [Citation28]. The FTIR results indicated that MAH was successfully grafted onto CF surface.
The SEM images of the CF, CF-OH and MAH-g-CF are shown in (–). It can be seen that the surface of untreated CF is smooth and inerratic. Some changes occurred on the CF surface after surface hydroxylation. Some shallow textures and grooves were induced onto the surface of CF-OH sample after the KOH/ethanol treatment. However, the surface of CFs became rather rough after MAH grafting. The SEM images demonstrated that the surface roughness of CF was remarkably enhanced after MAH grafting.
To further confirm the MAH was grafted onto the surface of CF, the Raman spectra analysis was performed. According to the previous reports [Citation29], D band (at about 1350 cm−1) reflected the lattice defect of carbon atoms. G band (at about 1590 cm−1) was usually assigned to the E2g phonon of sp2 atoms. In order to evaluate the intensity ratio between D band and G band, Each spectrum is subjected of peak fitting by using origin 8.6 to resolve the curve into two Gaussian bands. As shown in and , it presented that the intensity ratio of D/G bands (AD/AG) of CF-OH (2.87) was higher than that of untreated CF (2.65) due to the more oxygen functional groups located on the CF-OH surface. Noticeably, AD/AG value of MAH-g-CF increased to 2.97, indicating that oxygen functional groups in MAH introduced into CF surface and further increased carbon disorder and decreased the graphitization degree of CF [Citation30,Citation31].
Table 2. Raman analysis of CF, CF-OH and MAH-g-CF.
3.2 Mechanical properties of IFR PP composites
The mechanical properties of PP composite with different amount of CF were examined by tensile test and bending test, and the results are presented in . When CF content was 1 wt%, the tensile strength of the composite was lower than that of the PP/IFR composites ()). However, increasing the CF content to 3 wt% greatly increased the mechanical performance of the composite. Meanwhile, the tensile strength of the PP/IFR/MAH-g-CF composites was higher than that of the PP/IFR/CF composites. It appeared that the flexural strength decreased significantly along with the increase of CF content ()). However, the PP/IFR/MAH-g-CF composites exhibited higher flexural strength than PP/IFR/CF composites. When MAH-g-CF content was 3 wt%, the flexural strength of the resulting composite achieved 50.6 MPa, corresponding to 9.5% improvement, in comparison to that for PP/IFR composite (46.2 MPa). The reason was probably that the MAH-g-CF acted as a compatibilizer that could enhance the interfacial adhesion between CF and IFR. In addition, further increasing MAH-g-CF loading from 3–5 and 8 wt%, respectively, resulted in the decreased of tensile strength and flexural strength due to the agglomeration of particles causing stress concentration at the phase interface, which affected the increased degree of mechanical performance [Citation28].
Figure 5. (a) Tensile strength and (b) flexural strength of the composites reinforced by CF and MAH-g-CF in different contents. Note: the content of PP was 75 wt% and IFR/CF (IFR/MAH-g-CF) maintained 25 wt%, the content of IFR decreases with the increasing content of CF (MAH-g-CF) content according to the content in . The concentrations of CF (MAH-g-CF) were 0, 1, 3, 5 and 8 wt%.
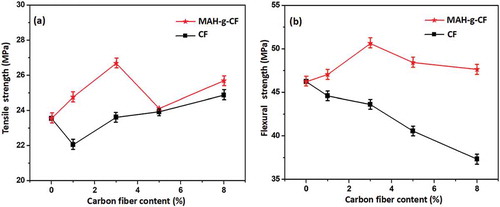
In order to evaluate the interfacial interaction between CF and IFR in the composites, DMA was further conducted. From , it was apparent that the storage modulus increased obviously with higher CF loading. Notably, when storage modulus of PP3 (PP/22 wt% IFR/3 wt% CF) sample was compared to that of PP7 (PP/22 wt% IFR/3 wt% MAH-CF) and PP4 (PP/20 wt% IFR/5 wt% CF) to PP8 (PP/20 wt% IFR/5 wt% MAH-CF), respectively, the reinforcement effect was more significant after grafting modification at the same CF loading. The peak at lower temperature from 0–50 °C corresponded to the glass transition temperature (Tg) of PP composites (). The Tg values of the composites were almost the same from each other. Tan δ value of PP3 and PP4 was higher than that of PP1, which was attributed to CF addition to the PP/IFR composites, thus more defects formed in CF and IFR phase interfaces. This also resulted in higher loss modulus in the composites. Meanwhile, tan δ value of PP7 is lower than that of PP1 and PP3 after grafting modification of CF. The mechanical reinforcement of DMA test may be due to two factors: first, an augmented surface roughness reduced stress concentration, thus enhanced mechanical bonding. Moreover, compatibilization reaction of MAH-g-CF and IFR increased the cross-link density of the interphase region [Citation30]. The possible compatibilization reaction is shown in . IFR particles possess active end-functional groups (NH2 or NH), which can react with the −COOH groups in MAH-g-CF to generate hydrogen bond to strengthen the interfacial adhesion between CF and IFR, thus restrain the molecular mobility of IFR in the interfacial zone [Citation32,Citation33].
Figure 6. The DMA curves of the composites (a) storage modulus and (b) loss factor (tan δ) versus temperature.
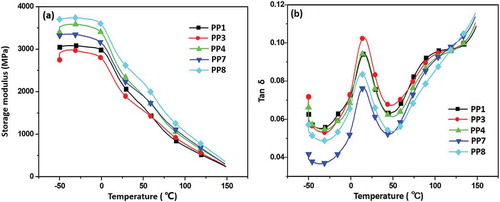
The SEM images of fracture surface of the PP/IFR, PP/IFR/CF and PP/IFR/MAH-g-CF composites are presented in and S1. As shown in and S1(a), a small amount of exposed IFR particles aggregated in PP/IFR composites. It could be observed that some CFs were pullout on the fracture surface in the , and S1(b,c), which resulted in some structural defects in the composites due to the weak interfacial adhesion. Especially, for PP4 (Figure S1(c)), many pullout defects existed on the fracture surface, showing that high amount of untreated CF was poorly bonded to the matrix. However, the fracture surface of PP7 and PP8 was compact and existed less holes which indicated that the phenomenon of pullout was improved after surface modification of CF. Notably, incorporating 3 wt% of MAH-g-CF (PP7), the fillers were embedded on the fracture surfaces of PP matrix uniformly and the IFR particles and CF were tightly bonded. This suggests that MAH on MAH-g-CF strengthens the interfacial interaction between IFR and CF ( and S1(d)).
3.3 Test for combustion behavior of PP composites
3.3.1. Flame retardancy of PP/IFR/MAH-g-CF composites
The flammability of PP composites was evaluated by UL-94 test and the obtained results are given in . Due to inflammability of neat PP, its UL-94 test gave no rating. With the increasing the IFR/CF or IFR/MAH-g-CF content, the flame retardancy of the composite was gradually improved. When IFR was 25 wt%, the flame-retardant property of the PP/IFR composite reached UL-94 V0 rating. Meanwhile, the composites maintained a favorable flame retardancy when CFs were added into IFR, but PP4 sample with 5 wt% CF content only reached UL-94 V1 rating (3.2 mm), which showed much lower flame retardancy than PP8 at the same MAH-g-CF content due to the poor interaction between flame retardants. These results indicated that IFR and CF had an efficient synergistic effect of flame retardant after grafting modification, which could improve the flame retardancy property of the resulting composite. Furthermore, the flame retardancy of the composites was compromised with the increasing amount of CF and MAH-CF (8 wt%), respectively, which was attributed to the lower addition of IFR produced inferior quality carbon layer so that it could not protect inner matrix protection when burning.
Photographs of the specimens after the UL-94 tests are presented in . It could be seen that neat PP burned violently with almost no char left. Obviously, intumescent char was formed in the end of specimens when the flame retardant was added into the composites. Generally, the barrier could slow the heat transfer between gas and condensed phases, thus extinguished flame in a short time. In addition, for PP4, some holes existed in the char indicating that some flammable volatiles causing the further decomposition, which resulted in the worse UL-94 test result (V1 rating).
In order to further evaluate the char-forming behavior between PP4 and PP8, the sample was ignited under the flame of UL-94 test and the residue was retained (sample size 40 × 40 × 3.2 mm). The photographs of residues were presented in . For , the residues of PP4 showed many grooves and exhibited obvious holes. Compared with PP4, PP8 exhibited compact and continuous char. Therefore, PP8 with intense intumescent char offered a good barrier for flame-retardant performance in UL-94 test. The result showed a viable way that MAH-g-CF could enhance char quality and improved flame retardancy.
3.3.2. Cone calorimeter test
The CCT is a useful tool to study the flammability. Several representative parameters such as heat release rate (HRR), total heat release (THR) and total smoke release (TSR) record the process of combustion. The HRR curves of PP composites are displayed in and the typical cone data are shown in . Neat PP burned faster after ignition which displayed only one peak of HRR. Its peak heat release rate (PHRR) reached 1050 kW/m2. It was clear that the PP/IFR/CF and PP/IFR/MAH-g-CF samples presented two obvious HRR peaks. The first peak was ascribed to the heat transfer at the initial stage of combustion. The second peak was attributed to the volatile gases that could break through the char, which ignites the inner PP matrix. As shown in , comparing with PP1, with the addition of CF, the PHRR value of PP composites reduced. Notably, the PHRR of PP7 (142 kW/m2) reduced by 8.5% than that in PP3 (155 kW/m2), while the PHRR of PP8 (130 kW/m2) reduced by 11.7% than that in PP4 (146 kW/m2) at the same IFR content. It indicated that the compact char layer caused by MAH grafting could postpone heat release. Moreover, the THR value increased significantly by adding CF due to the high thermal conductivity, which accelerated heat dissipation.
Table 3. UL-94 results of neat PP, PP/IFR, PP/IFR/CF and PP/IFR/MAH-CF composites.
Table 4. CCT data of neat PP, PP/IFR, PP/IFR/CF and PP/IFR/MAH-g-CF composites.
Time to ignition (TTI) and fire growth rate (FGR) [Citation34] are important parameters to assess the fire hazards of PP composites. With regard to TTI, all the flame-retardant PP composites are ignited in a very short time due to low thermal stability of the IFR and MAH. Based on the HRR curves, FGR can be calculated according to the following equation in to evaluate the fire hazard of the composites. Generally, the higher FGR value means easy flashover. There was no doubt that neat PP flashes easily (7.39 kW/m2s) meaning higher fire hazard. However, compared with PP1, the value of FGR decreased after adding CF. It was noteworthy that PP7 sample exhibited low FGR value (0.41 kW/m2s), indicating that MAH grafting was an effective method to enhance flame retardancy.
The TSR curve of PP composites is presented in . The slope of the curve shows the smoke release rate. As shown in , neat PP released a lot of smoke in a short period of time. Besides, thermal degradation of PP1 was longer than that of other samples, which indicated that PP1 could not form a dense char layer in a short time to suppress the combustion of PP, thus released more smoke. Obviously, the TSR of PP7 (765 m2/m2) and PP8 (549 m2/m2) reduced by 213.4% and 336.6%, respectively, in comparison to that of PP1 (2398 m2/m2). The incorporation of MAH-g-CF could effectively form dense char layer during combustion, which decreased the TSR.
3.3.3. Thermogravimetric analysis
shows the TGA and DTG curve of flame-retardant PP composites from room temperature to 700 °C under air atmosphere and the corresponding TGA and DTG data are shown in . Obviously, neat PP exhibited quickly weight loss at range of 248–380 °C with Tmax of 305 °C. Neat PP maintained little residue at 500 °C. Furthermore, all the PP/IFR/CF or PP/IFR/MAH-g-CF composites exhibited the similar thermal degradation behavior. As shown in , the first degradation stage was around 270–430 °C, which recorded the process of degradation of the composites until the cross-linked barrier formed. Since then, the decomposition rate became slow. The second stage was around 630 °C, which was attributed to the heat flow break through the char and therefore causes the degradation of inner PP matrix. It could be seen that PP1 presented lower char yield (5.6%) at 700 °C, indicating that its protective barrier was not strong enough to withstand high temperature under air atmosphere. Notably, T5% and Tmax of PP7 were as high as 283.6 and 358.1 °C, respectively. Tmax of PP/IFR/MAH-CF composites were lower than that of PP/IFR/CF composites, likely due to the decomposition of grated MAH caused by its low thermal stability. However, PP7 still presented lowest Rmax value (8.24%·min−1) and highest char residue at 700 °C (12.7%). These results indicated that the MAH on MAH-g-CF could improve the adhesive strength between CF and IFR and promote the cross-linking between CF and IFR, therefore produce higher residue char for PP/IFR/MAH-g-CF composites.
Table 5. TGA data of neat PP, PP/IFR, PP/IFR/CF and PP/IFR/MAH-g-CF composites in air.
Figure 11. (a) TGA and (b) DTG curves of neat PP, PP/IFR, PP/IFR/CF and PP/IFR/MAH-g-CF composites in air.
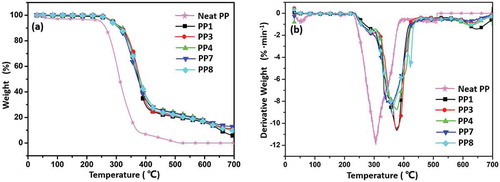
To further evaluate the charring potential of the composites, TGA was carried out from room temperature to 700 °C under N2 atmosphere and the corresponding TGA and DTG data are shown in and . Compared with the TGA data in air atmosphere, the thermal degradation of all composite was delayed in N2 atmosphere. However, neat PP still burned violently when it was ignited. Obviously, PP1 showed higher thermal decomposition temperature (T5% was 355.1 °C) and favorable thermal stability (Tmax was 457.3 °C), which may be due to the high content of acid source in IFR allows for stronger cross-linking ability to form carbon, thus delaying the degradation under the protection of N2 atmosphere. When incorporating CF into IFR system, char yield of PP3 (13.6%) and PP4 (10.6%) was lower than that of PP1 (13.9%). The result indicated that carbonization ability mainly depended on the cross-linking of APP in N2 atmosphere. However, PP7 still exhibited highest char residue at 700 °C (14.8%). We suggest that MAH on MAH-g-CF increased the cross-linking density in condensed phase, thereby improving the quality of char and enhancing the flame-retardant performance.
Table 6. TGA data of neat PP, PP/IFR, PP/IFR/CF and PP/IFR/MAH-g-CF composites in N2.
3.3.4. SEM images of char residues
SEM images of char residues remained after CCT are shown in . PP/IFR (PP1) composite obviously exhibited holes and defects on the char layer surface ()); therefore, the heat and flammable volatiles could penetrate char layer into the flame zone during burning, which resulted in lower flame-retardant efficiency. The addition of CF effectively enhanced the amount of char layer (–). Obviously, CF could act as a skeleton to construct char layer. It could be observed that the exposed short CFs were wrapped in the residue (), which was resulted from the poor compatibility with IFR. The char layers presented in PP7 and PP8 () were more compact than that in PP3 ()) and PP4 ().The possible reason was that the surface modification of CF improved the compatibility between IFR and CF to form a better barrier to protect the inner PP. Besides, compared with PP7 (, PP8 () exhibited more obvious porous structure, which was attributed to the less cross-linking reaction at low IFR content. Based on these results above, it appeared that MAH-g-CF facilitated the formation of compact and stable char layer, thus excellent flame-retardant efficiency could be achieved (sample PP7 with 22 wt% IFR and 3 wt% MAH-g-CF).
3.3.5. Possible mechanism of the enhanced flame retardancy
In order to investigate the synergistic mechanism of flame retardancy between IFR and MAH-g-CF, FTIR analysis of IFR and MAH-g-CF powder was carried out at different temperatures (). At room temperature, a board band around 3400–3200 cm−1 was observed, which was attributed to the absorption of the NH4+ in the APP. The adsorption bands at 1250, 1070 and 1000 cm−1 were assigned to stretching vibration of P = O, P-O-NH4+ and P-O-P groups, respectively. The absorption signals of charring agent and MAH-g-CF overlapped with the strong APP signal at high concentrations. Notably, as the degradation temperature increased, the absorption band around 1700–1630 cm−1 intensified, which was well consistent with the fact that dehydration and carbonization occurred at about 300 °C [Citation15]. This process was accompanied by the formation of phosphorus polyaromatic structure, carbonyl groups in the MAH-g-CF and the release of NH3 and H2O gases. Meanwhile, the band of P-O-P at 1000 cm−1 became broader, indicating the formation of polyphosphoric acid. At this stage, polyphosphoric acid, acting as acid source, can further promote the dehydration and cross-linking reaction of particles, resulting in the formation of thermally stable char that contained P-N-C chemical structure in the engineered flame-retardant system [Citation35]. Besides showing synergistic effect of APP and charring agent, the MAH-g-CF also contributed to forming more char residue during the thermal degradation process, which was in accordance with the TGA analysis. At 500 °C, the adsorption band at 1630 cm−1 became wider but weaker, indicating that the P-N-C structure was destroyed and stable C=C bonds were simultaneously produced in the residue [Citation36]. In addition, the characteristic adsorption band for P-O-P and P-O-NH4+ disappeared, but an intensive absorption band (950 cm−1)for PO3 appeared [Citation9,Citation37], which indicated that the char residue of IFR contained phosphocarbonaceous (P-C) macromolecules. Based on these results above, the possible synergistic effects during the thermal degradation were proposed. As shown in during the burning process, the P-O-P and phosphorus polyaromatic structure (P-N-C) were formed between APP and triazine char forming agent due to the dehydration reaction. The dehydration reaction was accompanied with the release of NH3 and H2O. Then NH2 groups in IFR were reacted with −COOH groups in MAH-g-CF to release H2O. When IFR was interacting with MAH-g-CF to form cross-linked char, CF served as a material support to enhance the strength of char.
4. Conclusions
In summary, we had synthesized a functional carbon-based filler, MAH-g-CF, by a solvothermal method. The MAH-g-CF serving as a promising filler exhibited an outstanding ability of smoke suppression and char formation in CCT and TGA. The lower value of pHRR and FGR indicated less fire hazard. Meanwhile, incorporation of MAH-g-CF (3 wt%) improved tensile strength and flexural strength of the composite to 26.7 and 50.6 MPa, respectively. It was proposed that the synergetic effect of P, C and N significantly contributed to the flame retardancy performance. The MAH-grafting modification enhanced interfacial interaction between IFR and CF to improve the flame retardancy performance. This engineered flame-retardant system could be extended to other polyolefin polymers for they potentially shared similar flame retardancy mechanism with PP.
Supplemental Material
Download MS Word (1.9 MB)Disclosure statement
No potential conflict of interest was reported by the authors.
Supplementary material
Supplementary data can be accessed here
Additional information
Funding
References
- Yao SS, Jin FL, Rhee KY, et al. Recent advances in carbon-fiber-reinforced thermoplastic composites: A review. Compos Part B-Eng. 2018;142:241–250.
- Karsli NG, Aytac A. Effects of maleated polypropylene on the morphology, thermal and mechanical properties of short carbon fiber reinforced polypropylene composites. Mater Des. 2011;32:4069–4073.
- Arao Y, Yumitori S, Suzuki H, et al. Mechanical properties of injection-molded carbon fiber/polypropylene composites hybridized with nanofillers. Compos Part A-Appl S. 2013;55:19–26.
- Gao SL, Mader E, Zhandarov SF. Carbon fibers and composites with epoxy resins: topography, fractography and interphases. Carbon N Y. 2004;42:515–529.
- Zhang S, Horrocks AR. A review of flame retardant polypropylene fibres. Prog Poly Sci. 2003;28:1517–1538.
- Bourbigot S, Duquesne S. Fire retardant polymers: recent developments and opportunities. J Mater Chem. 2007;17:2283–2300.
- Liu Y, Zhao J, Deng CL, et al. Flame-retardant effect of sepiolite on an intumescent flame-retardant polypropylene system. Ind Eng Chem Res. 2011;50:2047–2054.
- Liu Y, Deng CL, Zhao J, et al. An efficiently halogen-free flame-retardant long-glass-fiber-reinforced polypropylene system. Poly Degrad Stab. 2011;96:363–370.
- Zhu C, He M, Liu Y, et al. Synthesis and application of a mono-component intumescent flame retardant for polypropylene. Poly Degrad Stab. 2018;151:144–151.
- Alongi J, Han Z, Bourbigot S. Intumescence: tradition versus novelty. Comprehensive Review Prog Poly Sci. 2015;51:28–73.
- Kurt R, Mengeloglu F, Meric H. The effects of boron compounds synergists with ammonium polyphosphate on mechanical properties and burning rates of wood-HDPE polymer composites. Eur J Wood Wood Pro. 2012;70:177–182.
- Camino G, Costa L, Martinasso G. Intumescent fire-retardant systems. Poly Degrad Stab. 1989;23:359–376.
- Bourbigot S, Bras ML, Duquesne S, et al. Recent advances for intumescent polymers. Macromol Mater Eng. 2004;289:499–511.
- Yang K, Xu MJ, Li B. Synthesis of N-ethyl triazine–piperazine copolymer and flame retardancy and water resistance of intumescent flame retardant polypropylene. Poly Degrad Stab. 2013;98:1397–1406.
- Nguyen C, Kim J. Thermal stabilities and flame retardancies of nitrogen–phosphorus flame retardants based on bisphosphoramidates. Poly Degrad Stab. 2008;93:1037–1043.
- Xu ZZ, Huang JQ, Chen MJ, et al. Flame retardant mechanism of an efficient flame-retardant polymeric synergist with ammonium polyphosphate for polypropylene. Poly Degrad Stab. 2013;98:2011–2020.
- Wang X, Kalali EN, Wan JT, et al. Carbon-family materials for flame retardant polymeric materials. Prog Poly Sci. 2017;69:22–46.
- Savas LA, Mutlu A, Dike AS, et al. Effect of carbon fiber amount and length on flame retardant and mechanical properties of intumescent polypropylene composites. J Compos Mater. 2018;52:519–530.
- Zhao XL, Chen CK, Chen XL. Effects of carbon fibers on the flammability and smoke emission characteristics of halogen-free thermoplastic polyurethane/ammonium polyphosphate. J Mater Sci. 2016;51:3762–3771.
- Zhang GX, Sun SH, Yang DQ, et al. The surface analytical characterization of carbon fibers functionalized by H2SO4/HNO3 treatment. Carbon N Y. 2008;46:196–205.
- Cao H, Huang Y, Zhang Z, et al. Uniform modification of carbon fibers surface in 3-D fabrics using intermittent electrochemical treatment. Compos Sci Tech. 2005;65:1655–1662.
- Zhao F, Huang Y, Liu L, et al. Formation of a carbon fiber/polyhedral oligomeric silsesquioxane/carbon nanotube hybrid reinforcement and its effect on the interfacial properties of carbon fiber/epoxy composites. Carbon N Y. 2011;49:2624–2632.
- Moaseri E, Maghrebi M, Baniadam M. Improvements in mechanical properties of carbon fiber-reinforced epoxy composites: A microwave-assisted approach in functionalization of carbon fiber via diamines. Mater Des. 2014;55:644–652.
- Song P, Shen Y, Du B, et al. Fabrication of fullerene-decorated carbon nanotubes and their application in flame-retarding polypropylene. Nanoscale. 2009;1:118–121.
- Song P, Xu L, Guo Z, et al. Flame-retardant-wrapped carbon nanotubes for simultaneously improving the flame retardancy and mechanical properties of polypropylene. J Mater Chem. 2008;18:5083–5091.
- Huang YL, Ma CCM, Yuen SM, et al. Effect of maleic anhydride modified MWCNTs on the morphology and dynamic mechanical properties of its PMMA composites. Mater Chem Phys. 2011;129:1214–1220.
- Boztuğ A, Coşkun A, Bolayır G, et al. Preparation of compatible blends of poly(methyl methacrylate) used in dentistry with a reactive terpolymer containing maleic anhydride and their thermomechanical characterization. J Appl Poly Sci. 2006;100:363–367.
- Wu G, Ma L, Liu L, et al. Interface enhancement of carbon fiber reinforced methylphenylsilicone resin composites modified with silanized carbon nanotubes. Mater Des. 2016;89:1343–1349.
- Tuinstra F, Koenig JL. Raman spectrum of graphite. J Chem Phys. 1970;53:1126–1130.
- Feng C, Liang M, Jiang J, et al. Synergism effect of CeO2 on the flame retardant performance of intumescent flame retardant polypropylene composites and its mechanism. J Anal Appl Pyrol. 2016;122:405–414.
- Wei YX, Deng C, Zhao ZY, et al. A novel organic-inorganic hybrid SiO2 @DPP for the fire retardance of polycarbonate. Poly Degrad Stab. 2018;154:177–185.
- Song P, Shen Y, Du B, et al. Effects of reactive compatibilization on the morphological, thermal, mechanical, and rheological properties of intumescent flame-retardant polypropylene. Acs Appl Mater Interf. 2009;1:452–459.
- Huang G, Wang S, Song P, et al. Combination effect of carbon nanotubes with graphene on intumescent flame-retardant polypropylene nanocomposites. Compos Part A-Appl S. 2014;59:18–25.
- Schartel B, Hull TR. Development of fire‐retarded materials—interpretation of cone calorimeter data. Fire Mater. 2007;31:327–354.
- Shao ZB, Deng C, Tan Y, et al. Flame retardation of polypropylene via a novel intumescent flame retardant: ethylenediamine-modified ammonium polyphosphate [J]. Poly Degrad Stab. 2014;106:88–96.
- Shao ZB, Deng C, Tan Y, et al. An efficient mono-component polymeric intumescent flame retardant for polypropylene: preparation and application. Acs Appl Mater Interfaces. 2014;6:7363–7370.
- Gao S, Zhao X, Liu GS. Synthesis of an integrated intumescent flame retardant and its flame retardancy properties for polypropylene. Poly Degrad Stab. 2016;138:106–114.