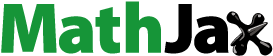
ABSTRACT
Over 150 refractory high-entropy alloys (RHEAs) have been proposed in the last decade. Early alloys such as MoNbTaW and MoNbTaVW still show an unparalleled yield strength of approximately 400 MPa at 1600°C. However, RHEAs with even elevated high-temperature strength are necessary in aerospace vehicles and nuclear reactors to cope with advanced technology in the future. Here, solid-solution strengthening calculation and melting point prediction are combined to design single-phase RHEA for attaining ultrahigh strength at 1600°C. The results show that Hf0.5MoNbTaW and HfMoNbTaW alloys after fully homogeneous treatment at 2100°C for 2 h reveal a homogenous body-centered cubic phase. HfMoNbTaW alloy exhibits a yield strength of 571 MPa at 1600°C, much higher than that of MoNbTaVW (477 MPa). It is found that a plateau of strength occurs from 800°C to 1200°C, which is important for raising the strength level of RHEAs at high temperatures. This strengthening mechanism is explained with the change of deformation mode from screw to edge dislocations, which contributes an edge-dislocation-induced strength. A similar alloy design strategy could be applied to develop more RHEAs with an ultrahigh strength level.
1. Introduction
Following the first publications in 2004, the concept of high-entropy alloys (HEAs) has been exploited in alloys design to develop new alloys for academic research and industrial applications [Citation1,Citation2]. Furthermore, various novel design methodologies have been proposed to widen the pool of potential compositions and applications [Citation3,Citation4]. Diffusion theory [Citation5], dislocation theory [Citation6–9], and mechanical properties [Citation10,Citation11] have been used to describe the deformation mechanisms of HEAs at elevated temperatures. However, the trade-off between strength and ductility or a win-win for both is always the goal to pursue, by which high accommodation of active slip planes is proposed to be the key strategy to attain the highest combination of strength and ductility [Citation12]. It has been reported that various alloys have very outstanding mechanical properties [Citation13–17]. Special categories of HEAs, such as refractory high-entropy alloys (RHEAs) [Citation18,Citation19], eutectic HEAs [Citation20], high-entropy superalloys [Citation21], and light-weight HEAs [Citation22,Citation23], also have their unique attractions in mechanical properties and hence the potential for various applications in energy, aerospace, and other industries.
After the first development of RHEAs in 2010, over 150 kinds of compositions have been reported, with their potential for use in high-temperature applications such as gas turbine engines and rocket nozzles. Various studies focused on ductility enhancement [Citation24,Citation25], better oxidation resistance [Citation26], and nuclear reactor material applications [Citation27,Citation28]. According to a review by Senkov et al. [Citation19], the only alloys to pass high-temperature compression tests at 1600°C were MoNbTaW and MoNbTaVW. The main reason for the difficulty to perform compression tests at extremely high temperatures is the lack of suitable material as a jig material that provides high strength at extremely high temperatures. Recently, Wang et al. strengthened the grain boundary of an MoNbTaW-refractory high-entropy alloy through doping with B or C in trace amount, which simultaneously increases room-temperature strength and toughness [Citation29]. This study provides a good strategy to increase the ductility of RHEAs by doping suitable elements.
Several theoretical models of solid-solution strengthening have been proposed to explain how different constituent elements affect room-temperature or elevated-temperature strength [Citation9,Citation30–33]. We previously designed a RHEA that exhibited higher elevated-temperature strength and discussed the effect of the constituent elements on equiatomic HfMoNbTaTiZr alloys by using the subtraction method [Citation33]. For higher room-temperature strength, one should add elements such as Mo, which significantly interact with the other elements. For higher elevated-temperature strength, one should add the elements that possess a high melting point such as Mo, Nb, or Ta. For higher ductility, one should add more Nb. With Ti or Zr addition, both the elevated-temperature strength and the density decrease.
In this study, Hf0.5MoNbTaW and HfMoNbTaW RHEAs were designed for extremely high elevated-temperature strength by using the above guidelines: Ti and Zr of HfMoNbTaTiZr were replaced by W to increase the melting point and Young’s modulus. The proposed alloys will be compared with standard MoNbTaVW that contains vanadium instead of hafnium. Moreover, homogenization treatments at a temperature of 2100°C for 2 h, followed by air cooling, were conducted in an ultrahigh-temperature furnace in order to get the fully homogeneous state. Their microstructures and mechanical properties were investigated using scanning electron microscopy (SEM), energy-dispersive spectroscopy (EDS), X-ray diffraction (XRD), and hardness and compression testing. The phase, temperature-dependent strength, and the ultrahigh elevated-temperature strength are discussed with the solution-strengthening mechanism, especially focusing on the contribution of edge-dislocation-induced strength.
2. Methods
2.1 Materials
All the alloys in this study were manufactured using a vacuum arc melting furnace with a water-cooled copper mold. The purity of pure elements was 99.9 wt%. The raw material was melted in sequence from a high melting point to a low melting point. For example, among Hf, Mo, Nb, Ta, and W, Ta and W were melted first followed by Mo, Nb, and Hf, in sequence. Homogenization treatment was conducted in an ultrahigh-temperature furnace ST-BI01. The furnace was heated using a graphite heater and controlled by using an infrared thermometer. After repeated creation of a vacuum of 3 × 10−2 Torr and purge with Ar three times, the sample was heated up to 2100°C at a heating rate of 10°C/min. But the furnace was vented by passing 150-sccm Ar flow and kept at a positive pressure higher than 1 atm when the temperature was raised above 1400°C. According to equation PV = nRT, it is difficult to maintain the vacuum condition above 1400°C. Furthermore, even little amount of oxygen would cause severe oxidation at 2100°C. By keeping Ar gas flowing out of the chamber, the oxygen in the atmosphere would not get into it. After homogenization treatment at 2100°C for 2 h, the sample was moved down to the cooling chamber and subjected to an Ar flow cooling.
2.2 Alloy analysis
The microstructures and compositions of the alloys were analysed using an SEM (JEOL-IT100) equipped with EDS capability. An XRD Bruker D2 PHASER was used to check the crystal structure with a scan rate of 8°/min. Hardness was measured by using a Vickers hardness tester (Matsuzawa Seiki MV-1) under 5 kgf. The room-temperature compression tests were conducted with an Instron 4468 universal testing machine, and the high-temperature compression tests were performed on a Gleeble-3500 thermal-mechanical simulator with a strain rate of 10−3 1/s for all compression tests. The cylindrical samples used for compression testing were 5 mm in diameter and 8 mm in height, while the samples used for compression testing at 1600°C were 3.6 mm in diameter and 6 mm in height. Shear modulus was measured via nanoindentation by using a Hysitron TI-980 Triboindenter.
3. Results
3.1 Microstructure and mechanical properties
shows the microstructure analyses with backscattering electron images and X-ray diffraction patterns of Hf0.5MoNbTaW and HfMoNbTaW in both as-cast and as-homogenized states. The compositions of the alloys in both states are shown in . The as-cast structure is dendritic in which the dendritic region (A) is rich in higher-melting point element, W and Ta, and the interdendric region (B) is rich in the lowest-melting point element, Hf. This is reasonable since higher melting point elements tend to crystallize first from the melt during solidification. It can be noted that the interdendrite of HfMoNbTaW also has a higher Hf content than Hf0.5MoNbTaW.
Figure 1. SEM backscatter electron images of (a) Hf0.5MoNbTaW and (b) HfMoNbTaW in the as-cast state and (c) Hf0.5MoNbTaW and (d) HfMoNbTaW in the as-homogenized state; XRD patterns of (e) Hf0.5MoNbTaW and (f) HfMoNbTaW in both states.
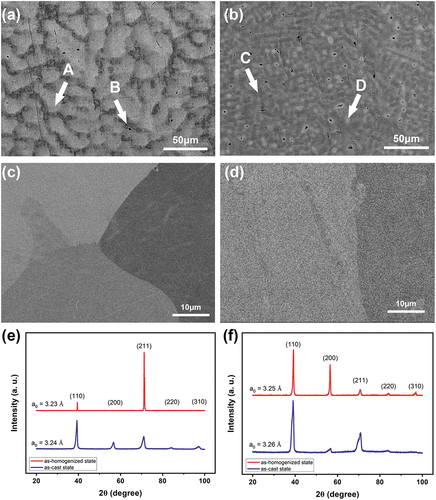
Table 1. Compositions of Hf0.5MoNbTaW and HfMoNbTaW in the as-cast state (at%).
According to the previous study [Citation34], MoNbTaW is single phase with a bcc structure. Hf is a Laves phase former. According to , when Hf is added to the MoNbTaW system, the bcc phase forms first during solidification, and the remaining becomes the Laves phase. As a result, both the melting point difference and Laves phase formation indicate that the interdendritic phase would be rich of Hf.
Figure 2. CALPHAD calculation result of different atomic fractions of Hf added to the MoNbTaW system using the TCHEA4 thermodynamic database supplied by ThermoCalc.
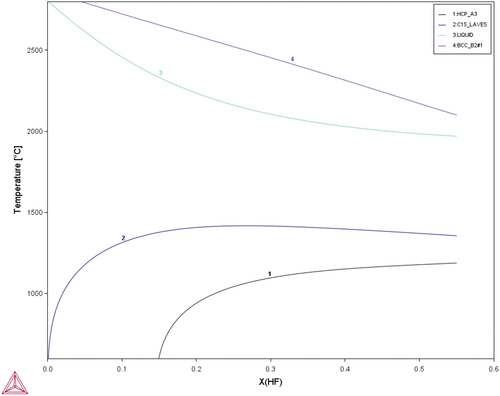
As the severe partition of Hf would cause problems on mechanical properties, especially at high temperature, homogenization treatment must be performed. Heat treatment at 2100°C for 2 h followed by air cooling indeed ensures complete homogenization and no precipitation during cooling as shown in . The EDS mapping results are also shown in . From , the lattice constants of Hf0.5MoNbTaW and HfMoNbTaW in the as-cast state are 3.24 and 3.26 Å, respectively, whereas the lattice constants of Hf0.5MoNbTaW and HfMoNbTaW in the as-homogenized state are 3.23 and 3.25 Å, respectively. It is apparent that the peak broadening in the as-cast state is due to the composition variation between dendrite and interdendrite regions. The peak of the as-cast state could be decoupled because of the dendritic structure. However, the two decoupled peaks are very close and merge into one peak, which is hard to distinguish.
The hardness values of Hf0.5MoNbTaW and HfMoNbTaW in the as-cast state were 543 ± 10 and 550 ± 9 HV, respectively. After homogenization, the hardness values of Hf0.5MoNbTaW and HfMoNbTaW were 540 ± 5 and 571 ± 8 HV, respectively. The hardness of the as-homogenized state was almost unchanged compared to that of the as-cast state for Hf0.5MoNbTaW, whereas that of HfMoNbTaW increases from 550 HV to 571 HV. This is reasonable as HfMoNbTaW has a larger segregation of Hf in the interdendritic region, and thus, the homogenization process let a larger amount of Hf dissolve into the matrix, which causes a larger solid-solution strengthening effect.
The flow stress curves of the elevated-temperature compression tests from ambient temperature to 1600°C for Hf0.5MoNbTaW and HfMoNbTaW in the as-cast and as-homogenized states are shown in . The yield strengths at elevated temperatures are summarized in . However, the hardness values of Hf0.5MoNbTaW and HfMoNbTaW in the as-cast state were 543 ± 10 (5321 MPa) and 550 ± 9 HV (5390 MPa), respectively. By estimating the ultimate strengths of the alloys using the empirical relation that hardness is equal to three times the ultimate strength, in units of MPa [Citation35], it could be noted that the samples were fractured below predicted strengths from their hardness values. In addition, the strength of HfMoNbTaW, 1561 MPa, is not only higher than that of Hf0.5MoNbTaW in the as-homogenized state but also much higher than that, 1058 MPa, of MoNbTaW [Citation34]. This indicates that adding Hf into the MoNbTaW can increase yield strength by 47.5% due to the strong solution-hardening effect.
Figure 4. The compression flow stress curves of Hf0.5MoNbTaW (a) in the as-cast state and (b) in the as-homogenized state; the flow stress curves of HfMoNbTaW (c) in the as-cast state and (d) in the as-homogenized state; and (e) the temperature dependence of yield strengths of Hf0.5MoNbTaW-C and HfMoNbTaW-C in the as-cast state, Hf0.5MoNbTaW-H and HfMoNbTaW-H in the as-homogenized state, and MoNbTaW [Citation34] and MoNbTaVW [Citation34].
![Figure 4. The compression flow stress curves of Hf0.5MoNbTaW (a) in the as-cast state and (b) in the as-homogenized state; the flow stress curves of HfMoNbTaW (c) in the as-cast state and (d) in the as-homogenized state; and (e) the temperature dependence of yield strengths of Hf0.5MoNbTaW-C and HfMoNbTaW-C in the as-cast state, Hf0.5MoNbTaW-H and HfMoNbTaW-H in the as-homogenized state, and MoNbTaW [Citation34] and MoNbTaVW [Citation34].](/cms/asset/ce188cfd-2af2-4abc-9d9e-f2208be4fe36/tsta_a_2129444_f0004_oc.jpg)
Table 2. The yield strengths (MPa) at different temperatures for Hf0.5MoNbTaW and HfMoNbTaW in the as-cast state and the as-homogenized state.
shows the yield strengths of the experimental alloys at elevated temperatures, which are compared with those of MoNbTaW and MoNbTaVW [Citation34] from room temperature to 1600°C. In the as-cast state, HfMoNbTaW possessed a higher elevated-temperature strength than MoNbTaVW below 1200°C, and Hf0.5MoNbTaW possessed a higher elevated-temperature strength than MoNbTaVW above 1200°C. The strength of HfMoNbTaW was even lower than those of Hf0.5MoNbTaW and MoNbTaVW at 1600°C. The CALPHAD calculation results are shown in , for which the TCHEA4 thermodynamic database supplied by ThermoCalc was employed. From , solidification starts from 2480°C to 2220°C, which results in the dendritic structure. From , the interdendrite of HfMoNbTaW (D) is rich in 46% Hf, which causes the decrease of the solid solution-strengthening effect. The Hf-rich interdendritic phase possesses a lower melting point and weakens the solid-solution strengthening effect, so the strength at 1600°C is lower than MoNbTaVW.
Figure 5. CALPHAD calculation result of HfMoNbTaW using the TCHEA4 thermodynamic database supplied by ThermoCalc.
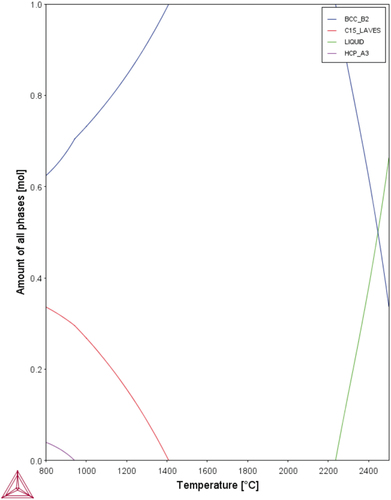
This is also why Hf0.5MoNbTaW and HfMoNbTaW were homogenized at ultrahigh temperature of 2100°C for 2 h, which successfully allowed the Hf0.5MoNbTaW and HfMoNbTaW to form a single homogenous phase, respectively. From , it can be seen that both the as-homogenized states of Hf0.5MoNbTaW and HfMoNbTaW revealed much higher strengths than MoNbTaW and MoNbTaVW, from room temperature to 1600°C. The as-homogenized state of HfMoNbTaW provided the highest strength at 1600°C, which was 571 MPa and became the highest of all the RHEAs without trace doping B or C.
The plateau strength shown in was present in the strength variation with temperature for each RHEA. For example, the plateau strength of HfMoNbTaW was approximately 950 MPa from 800 to 1200°C, while the plateau strength of MoNbTaVW was 550 MPa from 600 to 1000°C. We defined this temperature window as critical temperature Tc, or knee temperature [Citation36]. Tc is known to be an intrinsic property of body-centered cubic (bcc) materials, while the strengthening mechanism still remains unclear [Citation37]. Below Tc, the strength of the material decreases when temperature increases or strain rate decreases. This softening phenomenon results from thermal activation of the slip of screw dislocation and the double-kink mechanism [Citation38]. At Tc the strength of a material becomes independent of temperature or strain rate. Above Tc temperature, usually between 0.3 and 0.5 of the melting point, diffusion, grain boundary sliding, or dynamic recovery would occur, resulting in reduced strength as temperature increases again. One of the statements describing the plateau strength is that screw and edge dislocations have equal mobility at this Tc temperature [Citation39]. Thus, plateau strength reflects a transition of slip mode from screw to edge dislocation during deformation.
4. Discussion
4.1 Strategy to optimize refractory alloy strength
High strength at ambient temperatures and high melting points of constituent elements are key factors that can contribute to the high-temperature strength of a refractory alloy at elevated temperatures. shows the physical and mechanical properties of the refractory elements Cr, Hf, Mo, Nb, Ta, Ti, V, W, and Zr, in which Mo, Nb, Ta, and W have the highest melting points. These four elements were therefore selected for the preparations used in this study.
Table 3. Physical and mechanical properties of refractory elements [Citation56].
The fifth element to be added to the MoNbTaW alloy must exhibit a strong interaction with the other four elements, and the increases in strength may be examined by using solid-solution-strengthening calculations. The solid-solution-strengthening mechanism of RHEAs was first proposed by Senkov et al. and then modified by Yao et al. [Citation40,Citation41]. The solution-strengthening value ∆σi contributed by element i is
where A is a material-dependent dimensionless constant that equals 0.04, G represents the shear modulus of the alloy, ci is the atomic fraction of element i, and fi is the mismatch parameter of element i, which is related to its shear modulus and atomic size. fi is calculated using the following expression:
where the value of α depends on the type of dislocation present [Citation42]. For screw dislocation control, α is approximately 2–4. For edge dislocation control, α should not be lower than 16. For mixed dislocation, the α value is chosen to be 9. δG,i and δr,i are the modulus mismatch and atomic radius mismatch parameters, respectively, and represented by
There are nine atoms in the i-centered cluster in the bcc lattice and eight atoms neighboring the center atom, i. δG,ij and δa,ij are the differences in shear modulus and atomic radius between elements i and j, respectively, and represented by
where Gi and Gj are the shear moduli of elements i and j, respectively, and ri and rj are the atomic radiuses of elements i and j. The amount of solution strengthening ∆σ is the summation of all ∆σi,
The calculated yield strength is the summation of ∆σ and the average yield stress
, according to the rule of mixing,
where σi is the yield strength of pure element i. Because the shear modulus of the HfMoNbTaW alloy system remains unknown, the average shear modulus of the alloy is used to replace the shear modulus G to facilitate estimation.
is represented by
where Gi is the shear modulus of the pure element i. One can easily observe that higher G and δG,i or δr,i values would lead to an increase in the room-temperature strength of an RHEA. Furthermore, the melting point according to the rule of mixing is defined by
where Tm,i is the melting point of pure element i. Elevated-temperature strength was estimated by assessing and
. If the proposed RHEA possessed a higher
and
than MoNbTaVW, a higher elevated-temperature strength than that of MoNbTaVW might be achieved. For illustrating the worse design, when Cr is added, the
increases, but the
decreases, and the Laves phase might precipitate, which lessens solid-solution strengthening. When Ti is added,
does not significantly change, but
decreases. When Zr is added,
increases significantly, but
does not increase.
In this study, Hf proved to be the optimal choice because it involved an increase in both and
, since it possessed the lowest shear modulus and highest atomic radius among the Hf, Mo, Nb, Ta, and W elements and the highest melting point among the Cr, Hf, Ti, V, and Zr elements. shows the way in which the molar ratio of Hf affected the theoretical strength (
and melting temperature (
) of MoNbTaW alloy systems. Although
decreased with the addition of Hf,
of equiatomic HfMoNbTaW was still higher than that of MoNbTaVW. Furthermore, the theoretical strength (
) increased 30.8% from 2393 to 3131 MPa during equiatomic addition of Hf into MoNbTaW and was thus significantly higher than that of MoNbTaVW. From the literature, we predict that the
may be higher than the real strength of an alloy, because the
is referred to in our calculations, rather than the real shear modulus. The real shear modulus of MoNbTaVW is 75 GPa [Citation43], which is lower than the
of 87.94 GPa. However, even if a value of 75 GPa was used in our calculations of
, the resulting strength is still approximately 2000 MPa, which is significantly higher than the experimental value of 1246 MPa [Citation34]. The reasons for this result will be described in a later section.
4.2 The phase stability of HfMoNbTaW
Due to the extraordinary mechanical properties of the HfMoNbTaW alloy, we focus on this alloy for further discussion. From the binary phase diagram of Hf-Mo and Hf-W, HfMo2 and HfW2 form in the Laves phase with an AB2 structure [Citation44]. However, the experimental alloys were designed using only solid-solution theoretical strengthening. Even in cases in which there is no other precipitate or cluster shown in the microstructure, long-term phase stability is still crucial at elevated temperatures. Phase formation empirical rules for HEAs from the literature were applied in the case of the experimental alloys, and the detailed calculation procedures for each parameter are shown below.
Thermodynamics parameters, atomic size parameter, and electronic parameters are used to examine the tendency of solid-solution formation [Citation45,Citation46]. The thermodynamics parameters are mixing entropy ∆Smix, mixing enthalpy ∆Hmix, and Ω and represented as
where R is the gas constant and ∆Hij is the enthalpy of the binary liquid state of elements i and j at an equiatomic composition from Miedema’s model [Citation47,Citation48]. The atomic size parameter is atomic size difference δ represented as
is the average radius of the alloy defined by the rule of mixture:
Electronic parameters are the valence electron concentration VEC [Citation49] and the Allen electronegativity difference ΔχAllen [Citation50] represented as
where VECi is the valence electron concentration of element i [Citation51], is the electronegativity of element i from the study by Allen et al [Citation52], and
is the average electronegativity of the alloy defined by the rule of mixture shown as
In , the parameters for each element are shown for the theoretical predictions. There are three criteria for predicting the phases and crystal structure of HEAs. The first rule is that a disordered solid-solution phase forms when Ω is higher than 1.1 and δ is below 6.6% [Citation46]. This means that mixing enthalpy and atomic size difference are low enough not to form an ordered structure phase near the melting point. The second rule is that it is stable when rgw VEC is below 6.87 [Citation49]. The third rule is that the Laves phase forms when ∆χAllen is higher than 7% and δ is higher than 5% in HEAs [Citation53]. This is because the Laves phase forms when the electronegativity differences and atomic size differences between elements reach certain critical values. shows the ∆Hij, , and VECi for selected elements, while all the parameter calculation results for HfMoNbTaW are summarized in . The CALPHAD calculation results are also shown in .
Table 4. The values of ∆Hij (kJ/mol), , and VECi of selected elements.
Table 5. Summarized thermodynamics parameters, atomic size parameter, and electronic parameters of HfMoNbTaW.
As shown in , the phase formation rules predict that HfMoNbTaW formed a disordered solid-solution phase, from the VEC and Ω values. The higher Ω value indicates that a disordered solid-solution phase not only formed near the melting point but also extended to the lower temperature region. However, from the ∆χAllen and δ values, the Laves phase was expected to precipitate in the cooling process during casting. Theoretically, HfMoNbTaW might begin to melt at approximately 2200°C and possess a stable disorder solid-solution phase from 1400°C to the melting point. The Laves phase would then precipitate below 1400°C, as shown in . However, refractory elements usually exhibit slow diffusion processes. During solidification by casting, the water-cooled copper mold provided a higher cooling rate and thus inhibited Laves precipitation. After homogenization treatment, the air-cooling process led to a temperature drop from 2100 to 800°C in only 5 minutes and a drop to room temperature in 2 h. It was thus difficult for the Laves phase to form in such a short period of time, due to the low diffusion rate of RHEAs. SEM images, EDS mapping, and XRD patterns also prove the presence of a single phase after homogenization treatment. The solid-solution-strengthening effect may be discussed in detail only without elemental segregation and precipitates.
4.3 Correction of the theorical yield strength for plateau strength
A theoretically predicted value is generally larger than the experimental value. Here, we reviewed all the assumptions employed in our calculations and developed a new theory. First, the Young’s modulus of HfMoNbTaW was measured using nanoindentation techniques and was used to calculate the experimental shear modulus. This could be obtained using the following equation [Citation54]:
where E and ν are the Young’s modulus and the Poisson’s ratio of the test material, respectively, Er is the reduced Young’s modulus of the test material measured by nanoindentation, Ei and νi are the Young’s modulus and the Poisson’s ratio of the diamond indenter, respectively, ν is equal to 0.35, which is the common value for RHEAs [Citation43], and the Ei and νi values are 1141 GPa and 0.07, respectively. Thus, the E was calculated to be 188 ± 3 GPa. By using the expression: G = E/[2(1 + ν)], we further obtained a shear modulus of 73 ± 1 GPa for HfMoNbTaW.
However, the assumption of α = 9 that we used for mix dislocation control was an overestimate because deformation is usually controlled by screw dislocation at low temperatures under real conditions [Citation40], which is represented by a value of α = 2. If one assumes values of G = 73 and α = 2 for the solid-solution-strengthening calculation, is equal to 2002 MPa. This value is much closer to the yield strength of 1569 MPa of HfMoNbTaW and close to the predicted strength of 1903 MPa estimated from the hardness value of 571 HV in the as-homogenized state. Edge dislocation theory has recently been applied to explain the phenomena of high strength at high temperatures and plateau strength in RHEAs [Citation7,Citation8]. This is because edge dislocation has been previously observed at a low-strain rate and at high temperatures. The scenario becomes that an assumption of α = 2 is reasonable as deformation is controlled by screw dislocations at lower temperatures, and thermal activation causes a reduction in strength as temperature increases up to Tc and the plateau strength in a range of temperatures is a transition of slip mode from screw dislocation to edge dislocation, which means that strength at high temperatures is progressively controlled by new slip mode of edge dislocations. Thus, we will attempt to explain the plateau strength by inference to check whether the edge dislocation theory can explain the origin of high strength at high temperatures or not.
First, strength at room temperature is predicted by the fitting equation from high-temperature strength so that we could see its consistency with that predicted from solid-solution-strengthening calculations under edge dislocation control. The relationship between strength, strain rate, and temperature has been established by Leyson et al. from the thermal activation Arrhenius model [Citation55]. When the temperature increases, dislocation would move to other position easier, so the yield strength decreases. Therefore, no matter temperature is above or below Tc, the reason for the decreasing yield strength when temperature elevates is thermal activation. Grain boundary sliding and dynamic recovery are all important factors, but we choose not to discuss here. This results in three equations in different finite temperature ranges. Maresca et al. used an ad hoc adjustment to accurately approximate them across the full temperature range using the following equation [Citation8]:
where σ is the yield stress, σ0 is the zero-temperature yield stress, k is the Boltzmann constant, ∆Eb is the characteristic energy barrier, is the strain rate, and
is the reference strain rate. By applying a natural logarithm to both sides, this equation can be expressed as
with the form y = a + bx. shows a plot of ln σ vs. T0.91 for T = 1200, 1400, and 1600°C. After linear fitting, the extrapolation method was used to estimate strength at 298 K, which provided a value of 4536 MPa. Meanwhile, α = 16 was adopted for edge dislocation control in the equations from (1) to (9) for solid-solution strengthening, providing a value of = 4206 MPa. These two values calculated from different equations are highly consistent with each other and within a 7.2% difference, which indicates that the strength results from the dominant slip mode of edge dislocations above Tc. This also demonstrates that the strength of the HfMoNbTaW alloy can only come from the activation of screw dislocations at room temperature, because the strength of the edge dislocation is too high. Therefore, the whole scenario is that the strength decreases with increasing temperature due to thermal activation of screw dislocations until Tc. The alloy exhibits gradually increasing work-hardening capacity when temperature exceeds Tc; as a result, the activated edge dislocation begins to contend in general yielding after microyielding along grain boundaries and results in plateau strength over a wide temperature range. The edge dislocation becomes dominant in general yielding and results in high strength at high temperatures above Tc.
Figure 7. The plot of ln σ vs. T0.91 for T based on equation (22) and the data at 1200, 1400, and 1600°C. The linear fitting and extrapolation method were used to estimate the strength value at 25 °C.
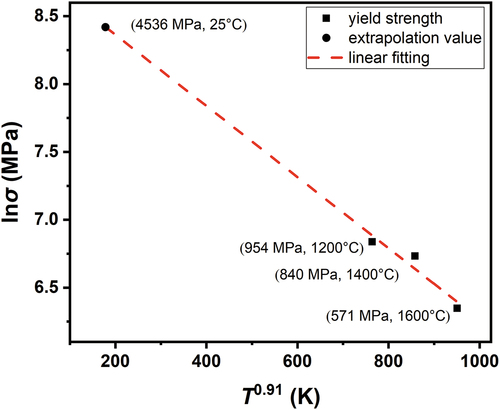
We also calculated for MoNbTaVW with α = 2 and α = 16, and the values were 1993 MPa and 2915 MPa. Then, we plot the lnσ of MoNbTaVW vs. T0.91 for T equals to 1200°C, 1400°C, and 1600°C. After linear fitting, the extrapolation method is used to estimate the strength at 298 K, which is 2950 MPa. Although 1993 MPa is not close to the 1246 MPa for room temperature strength of MoNbTaVW, 2915 MPa is almost consistent with 2950 MPa. Also, the temperature-strength curve of MoNbTaVW shows the plateau strength around 840 MPa and the Tc window around 600°C and 800°C, which means that there is a transition of slip mode. As a result, the room temperature strength of MoNbTaVW is controlled by screw dislocation, and the high temperature strength is controlled by edge dislocation.
We believe that this mechanism can comprehensively explain the Tc, plateau strength phenomena and high elevated-temperature strength that occurs in bcc-type RHEAs.
5. Conclusions
Refractory Hf0.5MoNbTaW and HfMoNbTaW RHEAs with ultra-high temperature strength have been designed using high-melting-point elements and verified by the solid-solution strengthening theory.
After homogenization treatment at 2100°C for 2 h with subsequent air cooling, the RHEAs reveal no composition segregation and precipitates.
The HfMoNbTaW in the as-homogenized state provides the highest elevated-temperature yield strength of 571 MPa at 1600 °C.
The plateau strengths of the Hf0.5MoNbTaW and HfMoNbTaW alloys displayed in the medium range of elevated temperatures have been demonstrated to be resulted from the transition of slip mode from screw dislocation to edge dislocation.
The whole scenario of the evolution of strength with temperature is that the strength decreases with increasing temperature due to thermal activation of screw dislocations up to Tc, the alloy exhibits gradually increased work-hardening capacity when temperature exceeds Tc, the activated edge dislocation begins to contend in general yielding after microyielding along grain boundaries and results in plateau strength over a wide temperature range, and thus, the edge dislocation becomes dominant in general yielding and results in high strength at high temperatures above Tc.
Acknowledgements
This work was financially supported by the “High Entropy Materials Center” from The Featured Areas Research Center Program within the framework of the Higher Education Sprout Project by the Ministry of Education (MOE) and from the Project NSTC 111-2634-F-007-008 and NSTC111-2224-E-007-003 by the National Science and Technology Council (NSTC) in Taiwan.
Disclosure statement
No potential conflict of interest was reported by the author(s).
References
- Yeh JW, Chen SK, Lin SJ, et al. Nanostructured high-entropy alloys with multiple principal elements: novel alloy design concepts and outcomes. Adv Eng Mater. 2004;6(5):299–303.
- Miracle DB, Senkov ON. A critical review of high entropy alloys and related concepts. Acta Mater. 2017;122:448–511.
- Jien-Wei Y. Recent progress in high entropy alloys. Ann Chim Sci Mat. 2006;31(6):633–648.
- George EP, Raabe D, Ritchie RO. High-Entropy alloys. Nature Rev Mater. 2019;4(8):515–534.
- Tsai KY, Tsai MH, Yeh JW. Sluggish diffusion in Co-Cr-Fe-Mn-Ni high-entropy alloys. Acta Mater. 2013;61(13):4887–4897.
- George EP, Curtin WA, Tasan CC. High entropy alloys: a focused review of mechanical properties and deformation mechanisms. Acta Mater. 2020;188:435–474.
- Maresca F, Curtin WA. Theory of screw dislocation strengthening in random BCC alloys from dilute to “High-Entropy” alloys. Acta Mater. 2020;182:144–162.
- Maresca F, Curtin WA. Mechanistic origin of high strength in refractory BCC high entropy alloys up to 1900K. Acta Mater. 2020;182:235–249.
- Lin KH, Tseng CM, Chueh CC, et al. Different lattice distortion effects on the tensile properties of Ni-W dilute solutions and CrFeni and CoCrfemnni concentrated solutions. Acta Mater. 2021;221:117399.
- Yeh JW. Physical metallurgy of high-entropy alloys. Jom-Us. 2015;67(10):2254–2261.
- Cheng CY, Yang YC, Zhong YZ, et al. Physical metallurgy of concentrated solid solutions from low-entropy to high-entropy alloys. Curr Opin Solid St M. 2017;21(6):299–311.
- Yeh JW. Strength through high slip-plane density. Science. 2021;374(6570):940–941.
- Gludovatz B, Hohenwarter A, Catoor D, et al. A fracture-resistant high-entropy alloy for cryogenic applications. Science. 2014;345(6201):1153–1158.
- Li Z, Pradeep KG, Deng Y, et al. Metastable high-entropy dual-phase alloys overcome the strength-ductility trade-off. Nature. 2016;534(7606):227–230.
- Huang H, Wu Y, He J, et al. Phase-Transformation ductilization of brittle high-entropy alloys via metastability engineering. Adv Mater. 2017;29(30):1701678.
- Lei Z, Liu X, Wu Y, et al. Enhanced strength and ductility in a high-entropy alloy via ordered oxygen complexes. Nature. 2018;563(7732):546–550.
- Yang T, Zhao YL, Tong Y, et al. Multicomponent intermetallic nanoparticles and superb mechanical behaviors of complex alloys. Science. 2018;362(6417):933–937.
- Senkov ON, Wilks GB, Miracle DB, et al. Refractory high-entropy alloys. Intermetallics. 2010;18(9):1758–1765.
- Senkov ON, Miracle DB, Chaput KJ, et al. Development and exploration of refractory high entropy alloys-A review. J Mater Res. 2018;33(19):3092–3128.
- Lu Y, Dong Y, Guo S, et al. A promising new class of high-temperature alloys: eutectic high-entropy alloys. Sci Rep. 2014;4(1):6200.
- Tsai CW, Tsai MH, Tsai KY, et al. Microstructure and tensile properties of Al0.5CoCrCuFeNi alloys produced by simple rolling and annealing. Mater Sci Tech Lond. 2015;31(10):1178–1183.
- Kumar A, Gupta M. An insight into evolution of light weight high entropy alloys: a review. Metals-Basel. 2016;6(9):199.
- Tseng K, Yang Y, Juan C, et al. A light-weight high-entropy alloy Al 20 Be 20 Fe 10 Si 15 Ti 35. Sci China Technol Sci. 2018;61(2):184–188.
- Sheikh S, Shafeie S, Hu Q, et al. Alloy design for intrinsically ductile refractory high-entropy alloys. J Appl Phys. 2016;120(16):164902.
- Lilensten L, Couzinie JP, Bourgon J, et al. Design and tensile properties of a bcc Ti-rich high-entropy alloy with transformation-induced plasticity. Mater Res Lett. 2017;5(2):110–116.
- K-C L, Chang Y-J, Murakami H, et al. An oxidation resistant refractory high entropy alloy protected by CrTao 4-based oxide. Sci Rep. 2019;9(1):1–12.
- Kareer A, Waite JC, Li B, et al. Short communication: ‘low activation, refractory, high entropy alloys for nuclear applications’. J Nucl Mater. 2019;526:151744.
- Lu YP, Huang HF, Gao XZ, et al. A promising new class of irradiation tolerant materials: Ti2ZrHfV0.5Mo0.2 high-entropy alloy. J Mater Sci Technol. 2019;35(3):369–373.
- Wang Z, Wu H, Wu Y, et al. Solving oxygen embrittlement of refractory high-entropy alloy via grain boundary engineering. Mater Today. 2022;54:83–89.
- Coury FG, Kaufman M, Clarke AJ. Solid-Solution strengthening in refractory high entropy alloys. Acta Mater. 2019;175:66–81.
- LaRosa CR, Shih M, Varvenne C, et al. Solid solution strengthening theories of high-entropy alloys. Mater Charact. 2019;151:310–317.
- Kim IH, Oh HS, Kim SJ, et al. Rapid assessment of solid solution hardening via atomic size misfit parameter in refractory concentrated alloys. J Alloy Compd. 2021;886:161320.
- Tseng KK, Juan CC, Tso S, et al. Effects of Mo, Nb, Ta, Ti, and Zr on mechanical properties of equiatomic Hf-Mo-Nb-Ta-Ti-Zr alloys. Entropy-Switz. 2019;21(1):15.
- Senkov ON, Wilks GB, Scott JM, et al. Mechanical properties of Nb25Mo25Ta25W25 and V20Nb20Mo20Ta20W20 refractory high entropy alloys. Intermetallics. 2011;19(5):698–706.
- Zhang P, Li SX, Zhang ZF. General relationship between strength and hardness. Mat Sci Eng A Struct. 2011;529:62–73.
- Trefilov M VI, YV G IV. Characteristic temperature of deformation of crystalline materials. Cryst Res Technol. 1984;19(3):413–421.
- Chen H, Kauffmann A, Laube S, et al. Contribution of lattice distortion to solid solution strengthening in a series of refractory high entropy alloys. Metall Mater Trans A. 2018;49a(3):772–781.
- Seeger A. Peierls barriers, kinks, and flow stress: recent progress. Z Metallkd. 2002;93(8):760–777.
- Schneider AS, Kaufmann D, Clark BG, et al. Correlation between critical temperature and strength of small-scale bcc pillars. Phys Rev Lett. 2009;103(10):105501.
- Senkov ON, Scott JM, Senkova SV, et al. Microstructure and room temperature properties of a high-entropy TaNbhfzrti alloy. J Alloy Compd. 2011;509(20):6043–6048.
- Yao HW, Qiao JW, Hawk JA, et al. Mechanical properties of refractory high-entropy alloys: experiments and modeling. J Alloy Compd. 2017;696:1139–1150.
- Fleischer RL. Substitutional solution hardening. Acta Metall Mater. 1963;11(3):203–&.
- Fazakas E, Zadorozhnyy V, Varga L, et al. Experimental and theoretical study of Ti20Zr20Hf20Nb20X20 (X= V or Cr) refractory high-entropy alloys. Int J Refract Metals Hard Mater. 2014;47:131–138.
- Baker H, Okamoto H. ASM H. Alloy phase diagrams. Vol. 3. USA: ASM International; 1992. p. 3.13.
- Zhang Y, Zhou YJ, Lin JP, et al. Solid‐solution phase formation rules for multi‐component alloys. Adv Eng Mater. 2008;10(6):534–538.
- Yang X, Zhang Y. Prediction of high-entropy stabilized solid-solution in multi-component alloys. Mater Chem Phys. 2012;132(2–3):233–238.
- De Boer FR, Mattens WC, Boom R, et al. Cohesion in Metals: Transition Met Alloys. Elsevier. 1988.
- Takeuchi A, Inoue A. Classification of bulk metallic glasses by atomic size difference, heat of mixing and period of constituent elements and its application to characterization of the main alloying element. Mater Trans. 2005;46(12):2817–2829.
- Guo S, Ng C, Lu J, et al. Effect of valence electron concentration on stability of fcc or bcc phase in high entropy alloys. J Appl Phys. 2011;109(10):103505.
- Poletti MG, Battezzati L. Electronic and thermodynamic criteria for the occurrence of high entropy alloys in metallic systems. Acta Mater. 2014;75:297–306.
- Guo S, Liu CT. Phase stability in high entropy alloys: formation of solid-solution phase or amorphous phase. Prog Nat Sci Mater Int. 2011;21(6):433–446.
- Mann JB, Meek TL, Knight ET, et al. Configuration energies of the d-block elements. J Am Chem Soc. 2000;122(21):5132–5137.
- Yurchenko N, Stepanov N, Salishchev G. Laves-Phase formation criterion for high-entropy alloys. Mater Sci Tech Lond. 2016;33(1):17–22.
- Oliver WC, Pharr GM. An improved technique for determining hardness and elastic-modulus using load and displacement sensing indentation experiments. J Mater Res. 1992;7(6):1564–1583.
- Leyson GPM, Curtin WA. Solute strengthening at high temperatures. Model Simul Mater Sc. 2016;24(6):065005.
- Goodfellow [internet]. England: goodfellow Cambridge Ltd; 2008-2020 [cited 2020 Jun 30]. Available from: https://www.goodfellow.com/uk/en-gb/metal