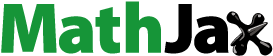
ABSTRACT
Oxide-dispersion-strengthened (ODS) steels are promising material candidates for nuclear fission and fusion applications. Nanosized oxide particles in as-rolled ODS steel PM2000 were investigated by using transmission electron microscopy. Uniformly distributed nanosized particles and heterogeneously distributed large dispersoids were observed in the steel. Three nanosized oxide phase types, Al2Y4O9, Y3Al5O12 and YAlO3, were present in the steel. Nanosized aluminum yttrium oxide Al2Y4O9, which has an orthorhombic P Bravais lattice rather than a monoclinic P Bravais lattice, was identified. Nanosized yttrium aluminum oxides that consisted of Y3Al5O12 and YAlO3 were also identified. The formation mechanism of Al2Y4O9/Y3Al5O12/YAlO3 phases in the steel resulted from the processing (hot-extrusion/hot-rolling) procedures. Al diffusion from the steel matrix into the Y2O3 particle fragments induced the nucleation and growth of the Al2Y4O9/Y3Al5O12/YAlO3 phases.
1. Introduction
Oxide-dispersion-strengthened (ODS) alloys are of considerable potential interest for structural applications in nuclear fission and fusion power plants because of their good high-temperature strength, creep rupture strength, corrosion resistance and resistance to radiation damage. ODS steels are manufactured by using a mixture of metallic powders with yttrium-oxide powder by mechanical alloying after consolidation and thermomechanical processing. The ferrite matrix yttria (Y2O3) is thermodynamically stable and was found to improve the high-temperature strength and maintain the resistance to superior ODS steel radiation [Citation1–3]. Titanium addition improves the creep rupture strength and produces finer oxide particles [Citation4]. An increasing proportion of chromium and aluminum improves the resistance to corrosion and oxidation [Citation5,Citation6].
The nature of the oxide dispersoids determines the ODS steel properties. Because nanoscale oxide particles in ODS steels can serve as a strong block for mobile dislocations and as a sink for radiation defects at the particle-matrix interfaces [Citation7], which enhances the high-temperature creep properties and radiation resistance, a study on the nature of dispersoids would be valuable in terms of establishing how the ODS steel compatibility would change in nuclear applications.
When added to the starting powder to prepare ODS Fe–Cr–Al alloys, Y2O3 dispersoids were not retained in the final product [Citation8]. Rather, mixed oxides formed because Y2O3 and metallic elements react during the high-temperature processing of PM2000. The change in oxide type during ODS fabrication requires further investigation.
Limited investigations and discussions exist on oxide types, size distributions and the small oxide-phase formation mechanism in PM2000 [Citation9–13]. Although several nanosized oxide phases have been identified in ODS steel PM2000, the oxide dispersoids in PM2000 remain unclear. The purpose of this work is to report oxide phases with different types, as Al2Y4O9 an orthorhombic P Bravais lattice and reveal smaller size distribution of these dispersoids. In this work, we focused on three oxides: Al2Y4O9, Y3Al5O12 and YAlO3. The crystal structure of Y3Al5O12 was determined to be tetragonal P Bravais, which was not clarified in previous research. The formation mechanism and smaller size distributions of these three oxides were also revealed in this work.
2. Experimental procedures
The material that was used was a commercial ODS steel PM2000, which is an iron–chromium-based ferritic steel that was produced by Plansee GmbH. The steel was supplied as an as-rolled 60-mm-diameter rod. The nominal composition of the steel was 20Cr, 5.5Al, 0.5Ti and 0.5Y2O3 (weight percent). Metallographic specimens were cut from the steel rod by spark erosion and prepared by using standard procedures of grinding, polishing and etching [Citation14]. The etchant that was used to reveal the steel microstructure was a solution of 15 mL HNO3–30 mL HCl–45 mL glycerol. The use of extraction carbon replica is an effective method to identify the nature of nanosized precipitates in steels [Citation15]. Extraction carbon replicas were prepared from the etched metallographic specimens by the method described elsewhere [Citation16]. Replicas were examined by a FEI Tecnai F20 and FEI Tecnai F30 transmission electron microscopy (TEM) at 200 and 300 kV. Energy dispersive X-ray (EDX) spectrometers on the TEM were used to analyze the chemical composition of the extracted oxide particles on the replicas. The oxide phases were identified by a combination of EDX analysis and electron diffraction along with the Powder Diffraction File database of the Joint Committee on Powder Diffraction Standards (JCPDS). The oxide particle size was measured from TEM micrographs of the replicas.
3. Overview of yttrium aluminum oxides
Current well-studied Y–Al–O oxides include Y3Al5O12, YAlO3 and Y4Al2O9. These oxides form from two stable crystals as Al2O3 and Y2O3 with different combination ratios. In this work, we focused only on the crystal structures of these Y–Al–O oxides.
As a single crystal, Y3Al5O12 has a cubic P Bravais lattice (a = 12.009 Å, b = 12.009 Å, c = 12.009 Å, JCPDS file 033-0040) or tetragonal P Bravais lattice (a = 7.510 Å, b = 7.510 Å, c = 4.240 Å, JCPDS file 009-0310). The melting point is 1970°C [Citation17].
YAlO3 has a perovskite-like orthorhombic P Bravais lattice (a = 5.330 Å, b = 7.375 Å, c = 5.180 Å) with space group Pnma [Citation18]. According to the orthorhombic structure’s mechanical stability criteria, YAlO3 has a mechanical stability from 0–20 GPa and 0–1300 K [Citation19–21]. YAlO3 also has another crystal structure as hexagonal P Bravais lattice (a = 3.678 Å, b = 3.678 Å, c = 10.483 Å) [Citation22].
In most cases, Y4Al2O9 is determined to be a monoclinic crystal by X-ray and neutron diffraction on powder and single-crystal samples [Citation23]. Al2Y4O9 has another crystal structure as an orthorhombic P Bravais lattice (a = 10.460 Å, b = 10.546 Å, c = 3.684 Å, JCPDS file 014-0475).
These three oxide crystal structures were determined by researchers in the past. However, for ODS steel, especially for as-rolled PM2000, the crystal structures and formation mechanism of nanosized dispersoids remain in discussion. In this work, we analyzed every Al–O–Y crystal structure and tried to explain the formation mechanism.
4. Results and discussion
and show examples of TEM images that were taken from replica samples of the PM2000 steel. shows the dispersoids distribution in the steel. The large dispersoids clustered heterogeneously in different areas with 25–100 nm diameters. shows that the nanosized oxide particles were distributed uniformly in the steel with an average diameter of ∼20 nm.
Figure 1. TEM micrograph of carbon replica prepared from as-rolled PM2000 steel, showing dispersoids distributed heterogeneously in steel.
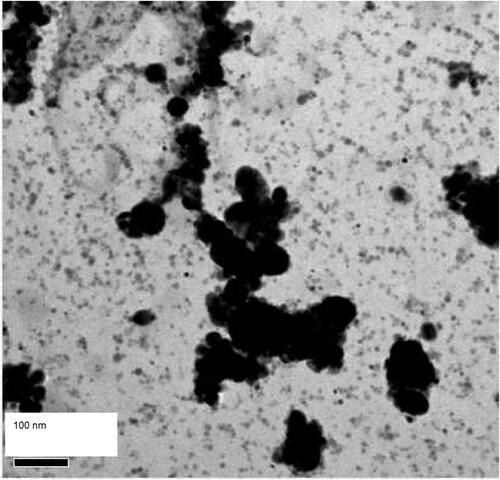
Figure 2. TEM micrograph of carbon replica prepared from as-rolled PM2000 steel, showing nanosized oxide particles distributed uniformly in steel.
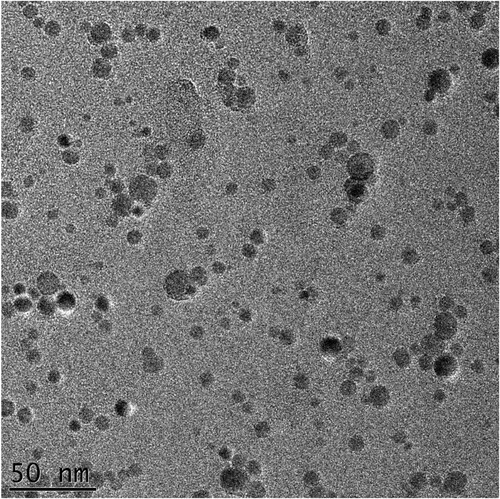
To study the uniformly distributed nanosized particles, more than 50 TEM images and 500 particles were investigated. In , dispersoids of interest of 10–50 nm comprised 70% of the studied particles. EDX analysis indicated that 70% of the particles appeared to be Al-Y-O oxide. Previous research has also found compositions of a similar size [Citation5,Citation9]. The large particles occupied 21% and were composed mostly of Al–Fe–Y–O chemical elements. Shen et al. [Citation9] described these dispersoids in their research. The large clustered particles were Al2Fe2O6, Al3FeO6, Al2O3, and Al3Ti5O2.
The TEM micrographs of carbon replica samples that were prepared from PM2000 steel ((a)) show large particle P1 with a 65 nm diameter along with many nanosized particles, including particle P2. The chemical composition of particle P1 was 20.92Al, 0.02Ti, 0.10Fe, 18.16Y, 60.76O (atomic percent). This composition indicates that particle P1 belongs to a Y–Al oxide phase with chemical formula YAlO3. (b) shows the selected-area electron diffraction (SAED) pattern of particle P1. This pattern matched the diffraction pattern from yttrium aluminum oxide (YAlO3, orthorhombic P Bravais lattice, space group: Pbn* with the lattice parameters a/b/c = 5.179/5.329/7.37 Å, JCPDS file 08–0147/33-0041) in the zone axis of [201] [Citation24]. Based on the pattern indexing and EDX analysis, particle P1 was identified to be the YAlO3 phase. Previous research has shown the presence of the YAlO3 phase in the as-rolled PM2000 steel with the observed YAlO3 particle size ranging from 35 to 84 nm in diameter [Citation9].
Figure 4. (a, b) TEM micrographs of carbon replica prepared from as-rolled PM2000 steel, showing large YAlO3 oxide particle P1 and nanosized Al2Y4O9 oxide particle P2 marked with arrows; (c) SAED pattern of particle P1 in the zone axis of [201]; (d) FFT pattern generated from particle P2 in the zone axis of .
![Figure 4. (a, b) TEM micrographs of carbon replica prepared from as-rolled PM2000 steel, showing large YAlO3 oxide particle P1 and nanosized Al2Y4O9 oxide particle P2 marked with arrows; (c) SAED pattern of particle P1 in the zone axis of [201]; (d) FFT pattern generated from particle P2 in the zone axis of [231¯].](/cms/asset/b6b8e351-0482-4323-8b60-6ee324891460/tphm_a_1979677_f0004_ob.jpg)
EDX analysis does not provide reliable stoichiometric atomic ratios of the nanosized particles in (a, b) and hence the nature of these particles is speculative. During exposure in air, carbon replicas may absorb oxygen and build up a layer of oxygen contamination on the replica surface, which results in an increase in oxygen concentration in the EDX data of nanosized oxide particles. In this investigation, the qualitative analysis of the nanosized oxide phase was based mainly on an analysis of the diffraction patterns.
(c) shows the fast Fourier transformation (FFT) pattern that was generated from the arrow-marked particle P2 in (a, b). This pattern could not be matched to the JCPDS database patterns for YAlO3 (JCPDS file 08–0147/33-0041), Y3Al5O12 (JCPDS file 09–0310), Al2Y4O9 (monoclinic P Bravais lattice, space group: P21/c with parameters a/b/c = 0.747/1.053/1.119 nm and β = 108.88°, JCPDS file 83–0935) [Citation25] or Y4Al2O9 (JCPDS file 22–0987) [Citation26] oxide phases, but instead it matched well with the diffraction pattern from Al2Y4O9 (orthorhombic P Bravais lattice with parameters a/b/c = 1.046/1.054/0.3684 nm, JCPDS file 14–0475) [Citation27] in the zone axis of . This pattern indicated estimated interplanar spacings of ∼d1/d2/d3 = 0.2630/0.3230/0.3130 nm, which show an agreement with the interplanar spacings, d1/d2/d3 = 0.2896/0.2908/0.3300 nm, for
/
/
lattice planes in the zone axes of
for the Al2Y4O9 phase, respectively. Therefore, the observed nanosized particle P2 was identified to be Al2Y4O9 with an orthorhombic P crystal structure.
Hsiung et al. [Citation28,Citation29] suggested that nanoparticles in the MA956 steel belong to the Y4Al2O9 (monoclinic P Bravais lattice, space group: P21/c with lattice parameters a/b/c = 0.7375/1.0507/1.1113 nm and β = 108.58°, JCPDS file 22–0987) phase, which is similar to Al2Y4O9 (JCPDS file 83–0935). We suggest that the identified nanosized phase in the as-rolled PM2000 steel belongs to the Al2Y4O9 with an orthorhombic P Bravais lattice, rather than to the Al2Y4O9 (JCPDS file 83–0935) or the Y4Al2O9 with a monoclinic-simple crystal structure.
shows additional TEM micrographs of the carbon replica from the as-rolled PM2000 steel with FFT patterns. The FFT patterns in (c,d) were generated from particles P3 and P4, which are marked with arrows, respectively. These two patterns did not match any of the patterns for YAlO3 (JCPDS file 08–0147). The pattern in (c) matched the pattern from the Al2Y4O9 (JCPDS file 14–0475) in the zone axis of [135], which indicates that particle P3 is also the Y4Al2O9 phase. For the pattern in (d), the pattern is inconsistent with the Al2Y4O9 (JCPDS file 83–0935) and shows no better match with the patterns for the Al2Y4O9 (JCPDS file 14–0475). However, the pattern matches that from Y3Al5O12 (tetragonal P Bravais lattice with the lattice parameters a/c = 0.751/0.424 nm, JCPDS file 09-0310) in the zone axis of [132], if the Y3Al5O12 has a tetragonal-simple lattice. Therefore, particle P4 is a Y3Al5O12 phase with a tetragonal-simple crystal structure.
Figure 5. (a) TEM micrograph of carbon replica prepared from as-rolled PM2000 steel, showing nanosized Al2Y4O9 oxide particle P3 and Y3Al5O12 oxide particle P4 marked with arrows; (b) FFT image generated from particle P3; (c,d) FFT patterns generated from particles P3 and P4 in zone axes of [135] and [132], respectively.
![Figure 5. (a) TEM micrograph of carbon replica prepared from as-rolled PM2000 steel, showing nanosized Al2Y4O9 oxide particle P3 and Y3Al5O12 oxide particle P4 marked with arrows; (b) FFT image generated from particle P3; (c,d) FFT patterns generated from particles P3 and P4 in zone axes of [135] and [132], respectively.](/cms/asset/162d9c9c-c0b2-4fff-9040-0c2161ea667c/tphm_a_1979677_f0005_ob.jpg)
Shen et al. [Citation9] confirmed the presence of the Y3Al5O12 phase in the as-rolled PM2000 steel. They observed several Y3Al5O12 particles with 33–173 nm diameters and an average diameter of 80 nm in the steel matrix. They speculated that the crystal structure of Y3Al5O12 may have a tetragonal-simple lattice. Our investigation confirmed the presence of a smaller nanoscale (< 10 nm diameter) Y3Al5O12 phase in the as-rolled PM2000 steel, that is, a tetragonal-simple crystal structure.
(b) shows a FFT pattern from arrow-marked particle P5 in (a), which was also taken from the carbon replica of the as-rolled PM2000 steel. The pattern did not match those from the Al2Y4O9 (JCPDS file 14–0475/83–0935). The match did not improve when the pattern was indexed in terms of patterns from the Y3Al5O12 (JCPDS file 09-0310). The pattern could be matched better with that from the YAlO3 (JCPDS file 08–0147/33-0041) in the zone axis of , which shows that particle P5 belonged to the YAlO3 phase. Thus, except for the large YAlO3 particles (> 35 nm diameter) as observed in the investigation [Citation9], YAlO3 phase particles are smaller (∼10 nm diameter) and were present in the as-rolled PM2000 steel.
Figure 6. (a) TEM micrograph of carbon replica prepared from as-rolled PM2000 steel, showing nanosized YAlO3 oxide particle P5 marked with arrow; (b) FFT pattern generated from particle P5 in the zone axis of .
![Figure 6. (a) TEM micrograph of carbon replica prepared from as-rolled PM2000 steel, showing nanosized YAlO3 oxide particle P5 marked with arrow; (b) FFT pattern generated from particle P5 in the zone axis of [231¯].](/cms/asset/9ab9f982-cbcb-4f69-ba2d-4e6ead7344cf/tphm_a_1979677_f0006_ob.jpg)
A large amount of complex Y–Al–O/Al2O3 and Y–Al–O/TiC and pure Al2O3 inclusions that are significantly larger than ODS particles have been identified in PM2000 steel [Citation10]. In the as-rolled PM2000 steel, some YAlO3 and Y3Al5O12 (33–173 nm in diameter) and a small amount of Al2Fe2O6 and Al3FeO6 (233–374 nm in mean diameter) in addition to Al3Ti5O2 and Al2O3 (160–500 nm in diameter) were observed [Citation9]. These results indicate that during the milling of PM2000, exposure of the powder to air occurred, which led to the internal oxidation of Al, Fe and Ti. Al has a higher oxygen affinity compared with Ti, Cr and Fe, i.e. Al > Ti > Cr > Fe [Citation30]. No previous reports exist on the Cr–O and Y–Cr–O oxide phases, such as Cr2O3 and YCrO3, as identified in PM2000 steel. Besides Al2O3 oxide, Al2Fe2O6, Al3FeO6 and Al3Ti5O2 complex-oxide phases also formed in PM2000 steel. Because oxide phases larger than PM2000 steel were not the focus of this investigation, we did not study large oxide particles during this TEM examination.
To form Al2Y4O9 nanoparticles in consolidated MA/ODS steels, the following three reactions should occur: (1) Y2O3 powder particle dissolution: Y2O3→2[Y]+3[O], (2) internal oxidation reaction of Al: 2[Al]+3[O]→Al2O3 because of the higher oxygen affinity of Al, and (3) a complex-oxide formation reaction: 2Y2O3+Al2O3→Al2Y4O9, which can occur between 900°C and 1100°C [Citation28,Citation29]. In this investigation, we did not detect the Y2O3 oxide phase in the PM2000 steel, which indicates that initial Y2O3 dispersoids that were added to the starting powder dissolved or were transformed to other oxide phases during the PM2000 steel fabrication. We found no experimental evidence that initial Y2O3 particles dissolved during the process but it is possible that the Y2O3 phase transformed into other oxide phases. If nanosized Al2Y4O9 particles formed through the reaction 2Y2O3+Al2O3→Al2Y4O9, the Y2O3 and Al2O3 particles should be small. Although the size of the initial Y2O3 particles that were added to the starting powder for PM2000 steel fabrication was not available, it is believed that during mechanical alloying, the Y2O3 phase was small because of the particle fragmentation by ball milling. Through many TEM observations, we did not detect small Al2O3 particles. Instead, Al2O3 particles in PM2000 steel were confirmed to be large [Citation9,Citation10]. Therefore, nanosized Al2Y4O9 particles in PM2000 steel may not form by the reaction of fine Y2O3 with large Al2O3.
Because the identified Al2Y4O9/Y3Al5O12/YAlO3 phases in PM2000 steel have a nanoscale spherical morphology and a higher number density, and they disperse in the matrix, the formation of the Y4Al2O9 phase appears to be related to initial Y2O3 particles that are added to the starting powder. Hsiung et al. [Citation28,Citation29] investigated the formation mechanism of Y4Al2O9 or YAlO3 oxide nanoparticles in MA956 (Fe-20Cr-4.5Al-0.34Ti-0.5Y2O3) and K3 (Fe-16Cr-4.5Al-0.3Ti-2W-0.37Y2O3) ODS ferritic steels. Oxide nanoparticles with a crystalline core and an amorphous shell were observed frequently in as-fabricated K3 and MA956 ODS steels. This result indicates a three-stage oxide nanoparticle formation mechanism: (1) fragmentation of starting Y2O3 particles during the early stages of ball milling, (2) agglomeration and solid-state amorphization of Y2O3 fragment mixing with matrix constituents during the later stages of ball milling, and (3) crystallization of amorphous agglomerates larger than ∼2 nm to form oxide nanoparticles with a (complex-oxide) core/(solute-enriched) shell structure during consolidation at 1150°C. In this investigation, nanosized oxide particles with a core/shell structure were not observed in the as-rolled PM2000 steel. As an example, shows a group of FFT images that were generated from randomly selected nanosized particles on the carbon replica that was prepared from the as-rolled PM2000 steel. shows that the boundary contour of these particles is clear, and no disordered region exists on the particle edge. These nanosized particles have complete crystal characteristics, and their interior and edge do not have an amorphous structure. Therefore, the formation mechanism of nanoparticles that was proposed by Hsiung et al. [Citation28,Citation29] appears unsuitable to explain the formation of nanosized oxide particles in the as-rolled PM2000 steel.
Figure 7. FFT images generated from nanosized particles on carbon replica prepared from as-rolled PM2000 steel, showing that these particles are crystalline.
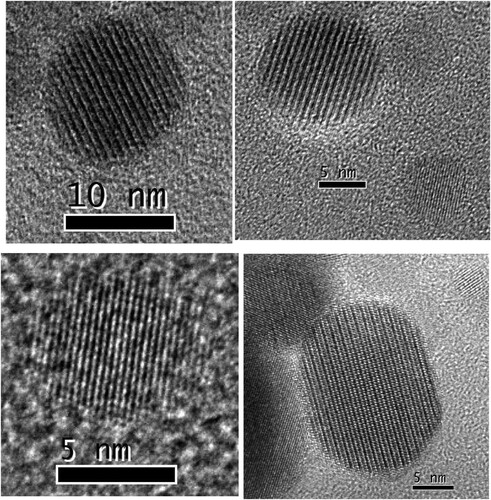
The formation of nanosized oxide phases in the as-rolled PM2000 steel may be related closely to the high-temperature diffusion of steel constituents during steel production. The nanosized Al2Y4O9/Y3Al5O12/YAlO3 particles in the PM2000 steel could be speculated to form from initial Y2O3 particle fragments that were mixed with steel constituent Al through diffusion during production. The Y–Al–O oxide phases should form in the Y–O-enriched regions during processing. Crushed fine Y2O3 particles are suitable in this context. Y2O3 particle fragments could act as nucleation sites for the Y–Al–O oxide phases. The nucleation and growth of the Al2Y4O9/Y3Al5O12/YAlO3 phases require Al solute atom diffusion to their nucleation sites and nuclei during processing.
Commercial PM2000 steel was produced by Plansee GmbH through mechanical alloying, consolidation by hot isostatic pressing (HIP), and thermomechanical processing (hot-extrusion/hot-rolling). More detailed PM2000 steel processing procedures are unavailable. The fabrication processes, such as HIP and the hot-extrusion/hot-rolling of the steel, were probably performed between 900°C and 1100°C [Citation31,Citation32]. The activation energy for self-diffusion of Al, Cr and Ti substitutional atoms in α-Fe from 900°C to 1100°C, 612°C to 901°C, and 675°C to 901°C was reported to be 246 [Citation33], 267 [Citation34], and 293 [Citation35] kJ/mol, respectively. Because the activation energy for the self-diffusion of solute Al in α-Fe at the PM2000 steel processing temperature was lower than that of solute atoms Cr and Ti, solute Al diffuses easily into the Y2O3 particle fragments compared with solute atoms Cr and Ti. With an increase in Al content to a certain critical minimum concentration of Al required for the nucleation of Al2Y4O9/Y3Al5O12/YAlO3 phases, the Y–Al–O oxide phases would nucleate inside the Y2O3 particle fragments. Subsequently, these phase nuclei would grow to Y–Al–O oxide particles through solute Al atom diffusion from the steel matrix to the particles. This behaviour may show the formation mechanism of the nanosized Al2Y4O9/Y3Al5O12/YAlO3 phases in the as-rolled PM2000 steel. The role of the Al2Y4O9/Y3Al5O12/YAlO3 phase formation in the as-rolled PM2000 steel requires further investigation.
5. Conclusions
Dispersoids in the as-rolled PM2000 steel consist of large oxides and nanosized oxide particles. Large oxides are distributed heterogeneously. Nanosized oxide particles with a 10–50-nm diameter and a mean diameter of ∼20 nm distribute uniformly in the alloy matrix. Three nanosized oxide phases that consist of Al2Y4O9, Y3Al5O12, and YAlO3 are identified in the as-rolled PM2000 steel. The identified nanoscale Al2Y4O9 oxide phase in the steel has an orthorhombic-simple crystal structure, rather than a monoclinic-simple crystal structure as reported previously in MA956 steel. The nanosized Y3Al5O12 oxide phase in the steel has a tetragonal-simple crystal structure. The probable formation mechanism of nanosized Al2Y4O9/Y3Al5O12/YAlO3 particles in the steel is as follows. During HIP and thermomechanical processing (hot-extrusion/hot-rolling) of steel, Al diffusion from the steel matrix into the Y2O3 particle fragments induces the nucleation and growth of the Al2Y4O9/Y3Al5O12/YAlO3 phases, which leads to a formation of oxide nanoparticles. The formation mechanism of the Al2Y4O9/Y3Al5O12/YAlO3 phases in the steel requires further investigation.
Acknowledgements
This work was supported by the National Natural Science Foundation of China (11805293), Key Program of National Natural Science Foundation of China (51034011), ITER-National Magnetic Confinement Fusion Program of The Department of Science and Technology of China (2011GB113001), and Shanghai Pujiang Program. The authors are grateful to Ms. Xuezhen Zhou, Shanghai University of Engineering Science, for preparing extraction carbon replicas that were used in this work. The authors thank Dr. Jinsung Jang, Nuclear Materials Research Center, Korea Atomic Energy Research Institute, for providing the steel that was used in this work.
Disclosure statement
No potential conflict of interest was reported by the author(s).
Additional information
Funding
References
- R.L. Klueh, J.P. Shingledecker, R.W. Swindeman and D.T. Hoelzer, Oxide dispersion-strengthened steels: A comparison of some commercial and experimental alloys. J. Nucl. Mater. 341(2) (2005), pp. 103–114.
- B.A. Pint and I.G. Wright, Long-term high temperature oxidation behavior of ODS ferritics. J. Nucl. Mater. 307 (2002), pp. 763–768.
- C. Capdevila, Y.L. Chen, A.R. Jones and H.K.D.H. Bhadeshia, Grain boundary mobility in Fe-base oxide dispersion strengthened PM2000 alloy. ISIJ Int. 43(5) (2003), pp. 777–783.
- T. Okuda and M. Fujiwara, Dispersion behaviour of oxide particles in mechanically alloyed ODS steel. J. Mater. Sci. Lett. 14(22) (1995), pp. 1600–1603.
- A. Kimura, R. Kasada, N. Iwata, et al., Development of Al added high-Cr ODS steels for fuel cladding of next generation nuclear systems. J. Nucl. Mater. 417(1-3) (2011), pp. 176–179.
- C.H. Zhang, A. Kimura, R. Kasada, J. Jang, H. Kishimoto and Y.T. Yang, Charac-terization of the oxide particles in Al-added high-Cr ODS ferritic steels. J. Nucl. Mater. 417(1) (2011), pp. 221–224.
- S. Ukai and M. Fujiwara, Perspective of ODS alloys application in nuclear environments. J. Nucl. Mater. 307 (2002), pp. 749–757.
- F.G. Wilson, B.R. Knott and C.D. Desforges, Preparation and properties of some ODS Fe-Cr-Al alloys. Metall. Trans. A 9(2) (1978), pp. 275–282.
- Y.Z. Shen, T.T. Zou, S. Zhang and L.Z. Sheng, Identification of oxide phases in oxide dispersion strengthened PM2000 steel. ISIJ Int. 53(2) (2013), pp. 304–310.
- M. Klimiankou, R. Lindau, A. Möslang and J. Schröder, TEM study of PM2000 steel. Powder Metall. 48(3) (2005), pp. 277–287.
- L. Zhang, S. Ukai, T. Hoshino, S. Hayashi and X. Qu, Y2o3 evolution and dispersion refinement in Co-base ODS alloys. Acta Mater. 57(12) (2009), pp. 3671–3682.
- C.-L. Chen and Y.-M. Dong, Effect of mechanical alloying and consolidation process on microstructure and hardness of nanostructured Fe–Cr–Al ODS alloys. Mater. Sci. Eng. A 528(29) (2011), pp. 8374–8380.
- H. Sakasegawa, L. Chaffron, F. Legendre, M. Brocq, L. Boulanger, S. Poissonnet, Y. De Carlan, J. Bechade, T. Cozzika and J. Malaplate, Evaluation of threshold stress of the MA957 ODS ferrtic alloy. J. Nucl. Mater. 386 (2009), pp. 511–514.
- E. Girault, P. Jacques, P. Harlet, et al., Metallographic methods for revealing the multiphase microstructure of TRIP-assisted steels. Mater. Charact. 40(2) (1998), pp. 111–118.
- Y. Shen, Z. Shang, Z. Xu, W. Liu, X. Huang and H. Liu, The nature of nano-sized precipitates in ferritic/martensitic steel P92 produced by thermomechanical treatment. Mater. Charact. 119 (2016), pp. 13–23.
- Y.Z. Shen, S.H. Kim, C.H. Han, H.D. Cho, W.S. Ryu and C.B. Lee, Vanadium nitride precipitate phase in a 9% chromium steel for nuclear power plant applications. J. Nucl. Mater. 374(3) (2008), pp. 403–412.
- S.H. Yoder and L.M. Keith, Complete substitution of aluminum for silicon: The system 3MnO· Al2O3· 3SiO2—3Y2O3· 5Al2O3. Am Min. 36(7-8) (1951), pp. 519–533.
- R. Diehl and G. Brandt, Crystal structure refinement of YAlO3, a promising laser material. Mater. Res. Bull. 10(2) (1975), pp. 85–90.
- T. Hahn, U. Shmueli and J.C. Wilson Arthur (eds.), International Tables for Crystallography. Vol. 1, Reidel, Dordrecht, 1983.
- Z. Huang, J. Feng and W. Pan, First-principles calculations of mechanical and thermodynamic properties of YAlO3. Comput. Mater. Sci. 50(10) (2011), pp. 3056–3062.
- C.Z. Wang, C. Dupas-Bruzek and S. Karato, High temperature creep of an orthorhombic perovskite–YAlO3. Phys. Earth Planet. Inter. 110(1-2) (1999), pp. 51–69.
- F. Bertaut and J. Mareshal, Un nouveau type de structure hexagonale, AlTO3 (T = Y, Eu, Gd, Tb, Dy, Ho, Er). C.R. Acad. Sci. Paris C 257 (1963), pp. 867.
- N.A. Christensen and G.R. Hazell, A comparison of three sets of diffraction data for Al2Y4O9: X-Ray synchrotron powder Data, X–Ray single Crystal Data from Ag Ka radiation, and Neutron single Crystal data from 1.01 A Neutrons. Acta Chem. Scand. 45(226) (1991), pp. 30.
- S. Geller and A.E. Wood, Crystallographic studies of perovskite-like compounds. I. Rare earth orthoferrites and YFeO3, YCrO3, YAlO3. Acta Crystallogr. 9(7) (1956), pp. 563–568.
- H. Yamane, M. Omori and T. Hirai, Thermogravimetry and Rietveld analysis for the high-temperature X-ray powder diffraction pattern of Y4Al2O9. J. Mater. Sci. Lett. 14(7) (1995), pp. 470–473.
- J.S. Schneider, S.R. Roth and L.J. Waring, Solid state reactions involving oxides of trivalent cations[J]. J. Res. Nat. Bur. Stand. A 65(4) (1961), pp. 345.
- I. Warshaw and R. Roy, A new family of rare earth compounds. Inorg. Chem. 1(3) (1962), pp. 719–720.
- L.L. Hsiung, M.J. Fluss and A. Kimura, Structure of oxide nanoparticles in Fe–16Cr MA/ODS ferritic steel. Mater. Lett. 64(16) (2010), pp. 1782–1785.
- L.L. Hsiung, M.J. Fluss, S.J. Tumey, B. William Choi, Y. Serruys, F. Willaime and A. Kimura, Formation mechanism and the role of nanoparticles in Fe-Cr ODS steels developed for radiation tolerance. Phys. Rev. B 82(18) (2010), pp. 184103.
- L.S. Darken and R.W. Gurry, Physical Chemistry of Metals, Metallurgy and Metallurgical Engineering Series, McGraw-Hill, 1953.
- A. Czyrska-Filemonowicz and B. Dubiel, Mechanically alloyed, ferritic oxide dispersion strengthened alloys: structure and properties. J. Mater. Process. Technol. 64(1-3) (1997), pp. 53–64.
- Y.L. Chen, A.R. Jones and U. Miller, Origin of porosity in oxide-dispersion-strengthened alloys produced by mechanical alloying. Metall. Mater. Trans. A 33(8) (2002), pp. 2713–2718.
- K. Nishida, T. Yamamoto and T. Nagata, On the interdiffusion in α-solid solution of the Fe–Al system in Al vapor. Trans. Jpn. Inst. Met. 12(5) (1971), pp. 310–316.
- C.-G. Lee, Y. Iijima, T. Hiratani and K.-I. Hirano, Diffu-sion of chromium in α-iron. Mater. Trans. JIM 31(4) (1990), pp. 255–261.
- P. Klugkist and C. Herzig, Tracer diffusion of titanium in α-iron. Phys. Status Solidi A 148(2) (1995), pp. 413–421.