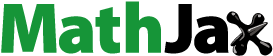
ABSTRACT
The goal of this study is to thoroughly comprehend the advantages of rattan (Calamus beccarii) as potential reinforcement in polymeric composites. The influence of various chemical treatments on thermal, morphological, mechanical and water absorption characteristics of natural rattan (RA) stem fiber were investigated. In this research, RA fiber surface was modified through different chemical treatments such as alkalization, bleaching, and benzoylation. The presence of voids and rough surfaces was investigated on SEM micrographs which are due to removal of lignin, wax, and oils from the fiber surface to a large extent. The results obtained from Fourier transform infrared may indicate the presence of cellulose, hemicellulose, and lignin compounds in the case of untreated and treated RA fiber. The increase in tensile strength and Young’s modulus confirms improvement in the mechanical properties of the RA fiber after chemical treatment. It was observed that alkali-treated RA fibers exhibit highest mechanical properties (295.28 MPa tensile strength, 8.23 GPa Young’s modulus). Also, X-ray diffraction analysis gives a higher crystallinity index (62.50%) for treated RA fiber. Thermogravimetric analysis confirms that there was an increase in the thermal stability of the fiber after chemical treatment. Overall results confirm that the RA fiber is appropriate for use as a reinforcing phase in composite materials for prospective engineering semi-structural applications such as roofing sheets, bricks, door panels, furniture panels, interior paneling, storage tanks, and pipelines.
摘要
本研究的目的是全面了解藤条(Calamus beccarii)作为聚合物复合材料潜在增强体的优势. 化学处理对天然藤茎纤维的热、形态、力学和吸水特性的影响. 在本研究中,RA纤维表面通过不同的化学处理进行了改性,如碱化、漂白和苯甲酰化. 通过SEM显微照片研究了空隙和粗糙表面的存在,这在很大程度上是由于从纤维表面去除了木质素、蜡和油. 傅里叶变换红外光谱的结果可能表明未经处理和处理的RA纤维中存在纤维素、半纤维素和木质素化合物. 拉伸强度和杨氏模量的增加证实了化学处理后RA纤维的机械性能的改善. 据观察,碱处理的RA纤维具有最高的机械性能(295.28 MPa拉伸强度,8.23 GPa杨氏模量). 此外,X射线衍射分析表明,经处理的RA纤维结晶度指数较高(62.50%). 热重分析证实,经过化学处理后,纤维的热稳定性有所提高. 总体结果证实,RA纤维适合用作复合材料的增强相,用于未来的工程半结构应用,如屋顶板、砖、门板、家具板、室内镶板、储罐和管道.
Introduction
Growing concern toward environmental safety has encouraged the researcher to synthesize new green materials. Eco-friendly, bio-degradability, and lightweight have become vital considerations in the fabrication of new material (Graupner, Herrmann, and Mussig Citation2009). Currently, synthetic fibers like glass, carbon, and aramid are widely being used in polymer-based composites because of their high stiffness and strength properties (Rout et al. Citation2001). However, these fibers have serious drawbacks in terms of their biodegradability, initial processing costs, recyclability, energy consumption machine abrasion, health hazards, etc. (Bledzki and Gassan Citation1999).
Natural fibers can eliminate these drawbacks of synthetic fibers. Natural fibers have several tailor made properties like lightweight, renewable, low cost, high specific modulus, high cellulose content, low density, nontoxic, easy fiber surface modification, relative nonabrasiveness, and easy for processing (Natarajan, Kumaravel, and Palanivelu Citation2016; Santhanam et al. Citation2016).
Natural fibers are classified based on their origins, coming from plants, animals, or minerals. Commonly, natural fibers, that is, extracted from fruits, seeds, stems, and roots of the plant known as plant fibers have been used as reinforcement in composite material. Also, these plant fibers have many traditional applications such as making of ropes, cords, hats, mats, and strings. Plant fibers are lignocellulosic fibers in which cellulose is the principal constituent, which is bounded by hemicellulose and lignin compound (Bledzki and Gassan Citation1999).
Besides all the benchmarking properties of the plant fiber, it has few limitations like poor adhesion at the fiber-matrix interface, weak thermal stability, and moisture sensitive. The morphological changes by different chemical treatments can eliminate the deficiencies (Kabir et al. Citation2012). Chemical treatments can clean the fiber surface, chemically modify the surface, stop the moisture absorption process, and increase surface roughness to be more compatible with hydrophobic polymers. Chemical treatment increases the surface roughness of the fiber surface by removing the amorphous constituents that surrounds the external surface of the fiber thus improving the fiber and matrix bonding. Many researchers have experimented with different chemical treatments on the fiber surface. Surface modification results in increase in the thermal stability of the fiber and enhancement of mechanical properties (Dehury, Nayak, and Mohanty Citation2021). Manimaran and coauthors (Manimaran et al. Citation2020) successfully extracted Aristida adscensionis fibers and studied their various properties. They found high cellulose content of 70.78%, whereas the contents of lignin and wax were equal to 8.9% and 2.26%, respectively. Moreover, the fiber has a low density equal of 790 kg/m3, whereas fiber diameter is equal to about 46 μm. The tensile strength and modulus were approximately 15.25 MPa and 0.78 GPa, respectively.
Oladele and Agbabiaka investigated the effect of mercerization treatment (KOH and NaOH) on sisal fiber (Oladele and Agbabiaka Citation2015). They found that KOH-treated sisal fiber-reinforced polypropylene composites gave the best flexural and tensile properties when compared to NaOH treatment. Madhu and co-authors studied the effect of various chemical treatments on Agave Americana fiber (Madhu et al. Citation2020). They found that the chemical treatments on the fibers brought a significant reduction in the amorphous contents like hemicellulose, lignin, and other impurities, and made them less resistant to water molecules. In addition, the thermal properties of the fibers were enhanced after surface modification. Al-Oqla et al. investigated the mechanical, thermal, and interfacial characteristics of Jordanian lignocellulosic fibers. They found that palm fiber type shows highest mechanical properties followed by olive fiber. Lemon and loquat fibers were the best in thermal stability (Al-Oqla, Hayajneh, and Fares Citation2019). Kabir et al. reported that benzoylation treatment reduces the hydrophilic nature of the fiber, thereby increasing the strength of the composite (Kabir et al. Citation2012). Nayak and Mohanty found that benzoylation enhances the thermal stability of the fiber (Nayak and Mohanty Citation2019). Sodium chlorite-treated sisal fiber gave higher tensile strength and also there was decline in the moisture absorption rate reported by Li and coauthors (Li, Panigrahi, and Tabil Citation2009). Szczepanowska (Szczepanowska Citation2017) described various types of rattan and epidermis morphology, topography, and cellular structure were characterized by a multi-scale and a multi-sensory approach using optical microscopy, confocal laser scanning microscopy, and field-emission scanning electron microscopy (FESEM).
In this present research work, the natural fiber, that is, obtained from the plant rattan (RA) belongs to the subfamily “Calamoideae” and is widely used in making chairs, clothing, medicines, handicraft, and arts and also its fruit is edible. Rattan fibers contain 73.83% of cellulose, 12.49 of hemi-cellulose, 10.15% of lignin, 3.15% of aqueous extract, and 0.37% of pectin (Sahoo et al. Citation2019). However, in the composite field of application, literatures about the rattan stem fiber are very scanty. Hence, the present work aims to modify the surface of the rattan fiber by various chemical treatments to enhance the fiber-matrix adhesion during composite fabrication in future. This also aims to find out the effects of chemical treatment on various properties like mechanical, thermal, morphological, and water absorption property of rattan fibers.
Materials and methods
Materials
Rattans are categorized as a member of the palm family (Palmae or Arecaceae) which has roughly around 600 species among which Calamus beccarii is one of them. It has spiny, brown stems, 50 m tall, 4 cm diameter. Rattan has significant properties that make them popular in industries such as furniture, handicraft, and other relevant industries for being durable, light weight, elastic, and flexible (Olawale and Wasiu Citation2013). Rattan consists of lignin, cellulose, and hemicellulose. The raw material for the present study, rattan stems from a species named Calamus beccarii (), was collected from local places of Bhubaneswar, Odisha, India. Chemicals like sodium hydroxide, sodium chlorite, and benzyl chloride of analytical grades were purchased from Mohapatra Chemicals, Bhubaneswar, and used without any further purification.
Methods
Fiber extraction process
The rattan fiber was collected from rattan plant (). Rattan cane was then separated from the plant as shown in . The rattan cane between inter-nodes was sliced using a slicer. The sliced rattan was then immersed in water for 5 days. The fibers were extracted from the rattan cane and thoroughly washed with distilled water to remove any impurities and dried in sunlight to remove moisture from the fiber. The fibers extracted at this stage were designated as untreated (raw) fibers ().
Surface treatment of fibers
Chemical modification of fibers is a common method for modifying the fiber surface which enhances the bonding between a natural fiber and a polymeric matrix. The most serious concerned problem with natural fibers is its hydrophilic nature, which causes the fiber to swell and ultimately rotting takes place through attack by fungi. Natural fibers are hydrophilic as they are derived from lignocellulose, which contain strongly polarized hydroxyl groups. Chemical treatment helps in removing excess amorphous constituents thereby exposing more cellulose on the surface of the fiber. The strength and stiffness of the plant and plant fibers depended on the cellulose content. It also enhances the surface roughness and crystallinity of the fibers with decrease in diameters. To enhance the properties of the fiber, various chemical treatments were applied on the fiber. A chemical treatment not only reduces the hydrophilicity of the fiber but also removes amorphous materials from the fiber surface thereby increasing their mechanical and thermal properties. This makes them suitable for various outdoor applications. In this research, the RA fibers were subjected to following chemical treatments for modifying the surface of the fibers.
Alkalization
Alkalization is widely used as the basic chemical treatment required for surface modification of natural fibers. During alkalization, the fibers were exposed to sodium hydroxide (NaOH) solution. This treatment disrupts the hydrogen bond (OH) present in the fibers and takes out water molecule (H2O) thus reduces the hydrophilic nature of fibers as per Eq 1. In this process, the untreated RA fibers were treated in 5% sodium hydroxide (NaOH) solution for 1 h at a temperature of 80°C. Then, the fibers were cooled to room temperature and washed in running water to remove any traces of sodium hydroxide solution adhered to the surface of the fibers so that the pH level of fiber is approximately 7 (neutral). Then, they were dried in an oven at a temperature of 60°C for 24 h (Dehury, Nayak, and Mohanty Citation2021). The fibers obtained at this stage were designated as alkaline-treated fibers.
Benzoylation
During benzoylation treatment alkali pre-treatment is used. At this stage, extractable materials such as lignin, waxes, and oil covering materials were removed and more reactive hydroxyl (OH) groups were exposed on the fiber surface. Then, the fibers were treated with benzoyl chloride. OH groups of the fiber are further replaced by benzoyl group and it attached on the cellulose backbone. This results in more hydrophobic nature of the fiber and improves adhesion with the matrix.
The alkaline-pretreated RA fibers were treated with 10% NaOH and benzoyl chloride solution for 15 min. The resulting fibers were dipped in ethanol for 1 h to remove benzoyl chloride sticky to the fiber surface. Then, the fibers were washed with distilled water and put in an oven maintaining 80°C temperature for 24 h for drying purpose (Mobarak et al. Citation2018).
Bleaching
Bleaching of RA fiber was carried out in sodium chlorite (NaClO2) treatment. Sodium chlorite is acidified and forms chlorine dioxide (ClO2) by oxidation reaction. This bleaching effect releases oxygen, which in turn, oxidizes the fiber impurities. In this process, first the RA fibers were soaked in a 5% NaOH solution. Then, the pretreated RA fibers were treated with the solution of sodium chlorite: water in the ratio 1:25 at 70°C for 3 hours. Then, the treated fibers were thoroughly washed with distilled water and finally dried in oven at 60°C for 5 hours.
Characterization of RA fiber
Physical characterization
The density of RA fiber was determined by pycnometer using standard ASTM D-792. In this method, kerosene was taken as the immersion liquid (Subramaniam et al. Citation2016; Vijay et al. Citation2019). Then, the density of RA fiber is calculated by the Eq (2) given below:
where ρ is the density of RA fiber (g/cm3), ρk is the density of kerosene (0.816 g/cm3), m1 is the mass of the empty pycnometer (kg), m2 is the mass of the pycnometer filled with chopped RA fibers (kg), m3 is the mass of the pycnometer filled with chopped RA fibers, and kerosene (kg) and m4 is mass of the pycnometer filled with kerosene (kg) (Jebadurai et al. Citation2019).
Fourier transform infrared spectroscopy
The Fourier transform infrared (FTIR) spectroscopy of the RA fiber was carried out to examine the constituents of the fiber. The FTIR spectra of all the samples of RA fibers were recorded, analyzed, and presented in a common scale. A total number of 14,000 scans for each of untreated and treated fibers were collected for the analysis. A spectral range (wavenumber) of 4000 to 500 cm −1 with a resolution of 4 cm −1 was maintained throughout the process. The spectra were recorded in Potassium bromide pellets on Nicolet AVATAR 360 spectrophotometer. The sample testing apparatus was equipped with Germanium Attenuated Total Reflectance (ATR).
X-ray diffraction
The X-ray diffraction (×RD) of the RA fiber was carried out to determine the crystallinity and amorphous region of the fiber. Cu-Kα radiation in reflection mode operating at 40 kV and 150 mA was used to record the XRD patterns. The angle (2θ) was varied from 10° to 30° at a rate of 0.05° step with 1 s of counting time. The Crystallinity index was determined using Eq. (3)
where I002 represents maximum intensity of diffraction of the (002) lattice peak at a 2θ angle between 21° and 23° due to crystalline region and I101 represents minimum intensity of diffraction of the (101) lattice peak at a 2θ angle between 16° and 18° due to amorphous region (Kabir et al. Citation2012).
The crystallite size of Calamus beccarii rattan fiber (L) was calculated through the next expression (Indran and Raj Citation2015):
where K is the Sherrer’s constant of 0.89, λ is the wavelength of the radiation, β is the peak’s full-width at half-maximum (FWHM) in radians, and θ is the corresponding Bragg angle.
Tensile properties
A Universal Testing Machine (Instron 3369 UTM) was used to measure the tensile strength of the RA fibers. Single fiber of all treated and untreated RA fibers were analyzed for their tensile strength and Young’s modulus as per ASTM D 3379–75. A thick sheet of paper frame was prepared which hold the specimen in the machine. A slot was cut in the center of the paper frame having length equal to the gage length of the specimen. A single filament of RA fiber was attached to both the ends of the slot in the paper using glue. The actual gage length of the fiber was measured using a Vernier caliper to be 50 mm. During the test, a full-scale load of 1 N and feed rate of 0.5 mm/min were maintained. Both sides of the frames were cut carefully without disturbing the set-up as a whole. The environmental conditions were maintained at 23°C temperature and 54% humidity. In total, 10 samples were tested and their average value was recorded.
Thermogravimetric analysis (TGA)
The thermal stability of RA fibers was characterized using a thermogravimetric analyzer (TA, Q50 V20.13 Build 39). About 10 mg of fibers are exposed to atmospheric air with a heating rate of 10°C min −1 from room temperature to 700°C.
Water absorption
Water absorption test of untreated and all treated RA fibers was carried out by taking a small amount of each set of fibers. Fiber samples were first dried in a hot air oven at 60°C for about 2 hours, weighed in a balance accurate to 4 decimal places (±0.1 mg), and then immersed in borewell water (whose pH value is 7.3) at room temperature (Dehury, Nayak, and Mohanty Citation2021). The fiber samples were removed from water at various intervals, dried in cotton, and weighed once again. The percentage of water absorption was calculated as follows:
where Wt is the weight of fiber in g after immersion and Wo is the weight of fiber in g before immersion.
Morphological characterization
Scanning electron microscope (SEM) of the RA fibers was performed to observe the surface morphological changes in the fiber. Totally, 10 nm of gold layer coating was applied on all the treated and untreated samples before the graphs were taken. Then, the surface morphology of fibers was obtained using the Leo Supra 35VP SEM operating at 20 kV generated the Scanning Electron graphs.
Results and discussion
Density of fibers
The apparent densities of untreated and treated rattan fibers were measured and noted. Apparent density is the density of natural fiber including voids which are inherent in the plant fibers. Generally, the natural fibers consist of pores and voids. Hence, finding out the reliable value of density depends upon its porous nature. Batra (Batra Citation1998) has measured an apparent density of fibers as 1.38 g/cm3 and a true density as 1.54 g/cm3. So, the apparent densities were measured for both treated and untreated fibers to have an overview of the change in densities, if any, after the chemical treatments. The apparent densities were found to be 0.98, 1.01, 1.10, and 1.12 g/cm3 for untreated, alkali-treated, sodium chlorite and benzoylation-treated rattan fibers, respectively. It is observed that the densities are little affected by the chemical treatments. However, the density increases after chemical treatment due to the destruction of the cellular structure of fibers which reduces the void contents and fiber diameter. In addition, the diameter of untreated, alkali-treated, sodium chlorite and benzoylation-treated rattan fibers were found to be 15.2 μm, 14.2 μm, 14.6 μm, 14.4 μm, and 14.3 μm, respectively.
Fourier transform infrared (FTIR) spectroscopy analysis
The FTIR spectra of untreated and all treated fibers are presented in . Alkalization treatment on RA fiber gives higher intensity values than benzoylation and bleaching treatment. presents the possible vibration of the infrared wave number. Spectra of the untreated fiber and all treated fiber show stretching of the aromatic ring of lignin at around 3600 to 4000 cm−1 and 1630 cm−1 (Maache et al. Citation2017). This band describes that RA fiber has more lignin, which provides structural integrity to fiber. The intensity of the band at around 3000 to 3500 cm−1 corresponds to hydrogen-bonded O-H stretching, and at around 2800 to 3000 cm−1 corresponds to the C-H stretching vibration of cellulose (Sari, Rahman, and Syafri Citation2019). However, no such band intensities can be visible in the case of untreated RA fiber. Also, fiber treated with sodium chlorite does not show any significant changes in their chemical composition (Rosa et al. Citation2011). But fiber treated with NaOH and benzoyl chloride has broadband of intensity at around 3300 to 3500 cm−1 showing O-H stretching of cellulose. Further, NaOH-treated fiber has a strong intensity band at 2850 cm−1 indicating an increased exposure of cellulose on fiber surface that results in an improvement in mechanical properties (Sari, Rahman, and Syafri Citation2019). The C-C alkynes groups were seen at two shoulder peaks at 2352 and 2300 cm−1 in case of NaOH-treated fiber. Spectra of untreated fiber show band at 1750 cm−1 attributed to C-O stretching of hemicellulose. But this band is nearly absent in the case of all treated fiber indicating the disappearance of hemicellulose after chemical treatment. NaOH-treated fiber shows broad band between 1000 and 1100 cm−1 presenting C-O stretching modes of hydrogen and ether group in cellulose, while these bands remain absent in untreated fiber (Sathishkumar et al. Citation2013).
Table 1. Infrared main transitions for rattan fiber.
X-ray diffraction analysis
The X-ray diffraction patterns of untreated and chemically treated RA fibers are shown in . It represents two intense peaks which are close to 2θ = 16° and 2θ = 22°. The two peaks represent cellulose crystallographic planes I101 and I002. The peaks for the untreated RA fibers were obtained at 15.84 °and at 22.92° but the treated fibers deviate slightly and the peaks were produced slightly toward right. The X-ray diffraction pattern suggests that amorphous parts of the fiber were removed by the chemical treatment which leads to the exposure of crystalline structure (Reddy et al. Citation2012).
The crystallinity indexes (CI) and crystal size (L) of the fibers are presented in . From the table, it was observed that crystallinity index of all treated fibers are higher than untreated one. The CI gives the quantitative measure of orientation of cellulose crystals in the fibers with respect to the fiber axis. This could be due to the removal of waxy materials, lignin, pectins, cementing materials, and hemicelluloses, which lead to the interfibrillar regions to be less dense and less rigid and better packing of the cellulose chains (Bledzki and Gassan Citation1999). The CI value of alkali treated rattan fiber was found to be 62.5%. The obtained CI of Calamus beccarii rattan fiber was higher than Aristida adscensionis (58.9%) (Manimaran et al. Citation2020); Furcraea foetida (52.6%) (Manimaran et al. Citation2018); Prosopis Juliflora Bark (46%) (Saravanakumar et al. Citation2013) and lower than Azadirachta indica (65.04%) (Manimaran et al. Citation2018); and Althaea officinalis L. (68%) (Sarikanat et al. Citation2014). The crystallite size was found to be 1.93 nm, which is higher than Ferula communis (1.6 nm) (Seki et al. Citation2013).
Table 2. Crystallinity index of untreated and treated rattan fibers.
Tensile properties
The mechanical properties of untreated and various chemically treated RA fibers are presented in . A significant increase in tensile strength and Young’s modulus of all the chemically treated RA fibers was observed in ) as compared to untreated RA fibers. The enhancement in mechanical behavior was possible due to the removal of amorphous constituents present on the surface of the fibers, which acts as a barrier in case of untreated RA fiber (Fidelis et al. Citation2013). Chemical treatment also enhances the crystallinity of the fibers which makes the fiber strong and enhances the mechanical properties. The stress transfer between the fiber cell increases due to removal of the unwanted and cemented materials and the fiber becomes more homogenous. Among all treated fibers, alkali-treated fibers exhibit highest tensile and Young’s modulus of 295.28 MPa and 8.23 GPa, respectively. The obtained tensile strength is more than alkali-treated vetiver fibers, i.e., 204.34 MPa (Jena, Mohanty, and Nayak Citation2020), Agave Americana fiber, i.e., 282 MPa (Madhu et al. Citation2020), Pennisetum orientale fiber, i.e., 98.91 MPa (Nayak Citation2022) and Jordanian palm fiber, i.e., 160 MPa (Al-Oqla, Hayajneh, and Fares Citation2019).
This increased value in NaOH (alkalization) may be due to the formation of the strong covalent bond between the cellulose chain, which results in close packing and stiffness of the fiber. In addition, it was observed that sodium chlorite–treated fibers reveal highest elongation at break as compared to other treated and untreated fibers which fractures by deforming much under the tensile load.
Thermogravimetric analysis (TGA)
The TGA curve of untreated and treated RA fiber is shown in . The thermogravimetric analysis of natural fiber is highly essential to have an idea of its response toward different temperature ranges. The cellulose, hemicellulose, and lignin degrade at different temperature. From TGA curve, it was observed that the degradation of RA fiber was associated with four-stage degradation process. The initial weight loss was observed from temperature range of 40 to 120°C which may be due to evaporation of moisture from the fibers (Brigida et al. Citation2010). Within this temperature range, weight loss of 10% was observed in case of untreated fiber showing its higher moisture content. Whereas, in case of all treated RA fiber, the weight losses was found to be 5% to 7% of the total fiber weight due to enhance moisture resistance property (Senthamaraikannan and Kathiresan Citation2018). No significant weight loss was observed in case of untreated RA fiber in the temperature range of 120 to 250°C and in case of treated RA fibers in the temperature range of 120 to 263°C. This shows increased thermal stability of RA fibers in the temperature range of 250 to 263°C due to chemical treatments. The second weight loss of 45% was observed in case of untreated fiber in the temperature range of 250 to 360°C. This weight loss corresponds to depolymerization, thermal degradation of hemicellulose and cellulose. However, in case of alkalization a second weight loss of 34% was observed in the temperature range of 250 to 360°C. This is possibly due to more cellulose crystallinity (Sathishkumar et al. Citation2013). After 360°C temperature, the lignin starts degrade slowly because of its complex structure till 700°C. At 700°C, the residual char of maximum 2–4% was found in case of treated RA fibers due to strong bonding of lignin and cellulose, whereas in case of untreated fiber, 7% char was found.
Water absorption
Because of the presence of hydroxide and other polar groups in various constituents of natural fiber, the water absorption is high which leads to poor wettability and weak interfacial bonding between the cellulosic fiber and polymer matrix. Water absorption is one of the important properties of natural fibers that indicate the degree of hydrophobicity imparted to fibers after chemical treatments. Water absorption as a function of the square root of immersion time (√t) for each immersed specimen is presented in . It was observed that the percentage of water absorption increases initially with square root of immersion time before reaching a maximum and after that it almost saturates. This may be attributed to the fact that the initial and second absorption phases are governed by the wetting of fibers and the capillary absorption process, respectively, where the water diffuses into the fibers until reaching a maximum absorption. The moisture swells the cell wall and the fiber expands until the cell wall is saturated with water, thereby reaching the saturation stage where no further absorption takes place. The saturation time for all fibers is observed to be almost same but the water absorption rate for treated fibers is found to be less as compared with untreated fiber. Further, alkali-treated fibers revealed lowest rate of water absorption as compared to other treated and untreated fibers. This may be due to exposure of more reactive hydroxyl groups in the fibers after alkalization.
Morphological analysis of RA fibers
Untreated
The SEM of untreated RA fiber is shown in . From SEM image, it was seen that the raw RA fiber is covered with fatty and waxy substances making the fiber surface smooth and shiny. Also, the white patches on raw fiber accounts for impurities present on the fiber surface due to binding of hemicellulose and lignin.
Alkalization
shows the effect of alkalization on the surface of the fiber. This treatment eliminates hemicellulose, wax, and oils covering the external surface of the fiber. As a result, the fiber surface becomes clean and more uniform due to the elimination of micro-voids. Also, there is a reduction in fiber diameter, which enhances the aspect ratio (Oladele and Agbabiaka Citation2015).
Benzoylation
The SEM image of benzoyl chloride treated RA fibers is shown in . Pin holes and rough surface is clearly visible in the figure. This is due to the removal of lignin, wax, and oil covering the fiber surface by exposing more hydroxyl (OH) group on alkali pretreatment. Additionally, OH groups were replaced by benzoyl groups after being treated with benzoyl chloride, which improved the fiber’s hydrophobic character and fiber-matrix adhesion (Mobarak et al. Citation2018).
Bleaching
The SEM of bleaching treatment is shown in . It can be seen from SEM image that the fiber surface becomes rougher on bleaching due to dissolution of lignin, wax, and pectin. This bleaching effect releases oxygen that oxidizes the fiber impurities. The fiber contains more pores and cavities. The liberation of ClO2 reacts with hydroxyl groups of hemicellulose and lignin constituents of the fiber by removing lignin from the fiber surface (Nayak and Mohanty Citation2019). These combined effects remove moisture from the fiber and enhance the water absorptivity property.
shows the fiber cross-section before and after alkali-treatment. From the figure, it can be seen that the chemical treatment not only reduces the voids content but also decreases the fiber diameter.
Conclusion
Natural fibers that possess better properties are the best alternative for fabrication of biocomposites. Different properties of RA fibers were enhanced by applying various surface modifications on it with the following findings. The low density of RA fiber proved its suitability as reinforcement in composites for light weight application. FTIR spectroscopy indicates the presence of a strong cellulose bond in case of alkalization of RA fiber. XRD graph shows more crystallinity structure of RA fiber upon alkalization treatment, which may be due to the orderly packing of cellulose. SEM reveals significant morphological changes of RA fiber due to various surface modifications. A decrease in diameter and void content can be observed in the fiber cross-section. The NaOH-treated RA fiber revealed better tensile strength (295.28MPa), which may be due to enough exposure of cellulose which is also confirmed by FTIR and XRD. The values of the crystallinity index (CI) and the crystalline size are equal to 62.5% and 1.93, respectively. TGA evidenced increase thermal stability of RA fiber upon chemical treatment. As far as water absorption property is concerned, different chemical treatments reduce the water absorption. However, alkali-treated fibers have better resistant to water absorption in comparison with other treatments. Hydrophilic nature of the RA fiber was reduced by chemical treatment. Among all treatments, NaOH (alkalization)-treated RA fiber demonstrates best result. In future, alkalized RA fibers have wide scope in the field of green composite.
Disclosure statement
No potential conflict of interest was reported by the author(s).
References
- Al-Oqla, F. M., M. T. Hayajneh, and O. Fares. 2019. Investigating the mechanical thermal and polymer interfacial characteristics of Jordanian lignocellulosic fibers to demonstrate their capabilities for sustainable green materials. Journal of Cleaner Production 241:118256. ‘Advanced online Publication’. doi:10.1016/j.jclepro.2019.118256.
- Batra, S. K. 1998. Other long vegetable fibers. In Handbook of fibre science and technology. Fibre chemistry, ed. M. Lewin and E. M. Pearce, Vol. 4, pp. 505–44. New York: Marcel Dekker.
- Bledzki, A. K., and J. Gassan. 1999. Composites reinforced with cellulose based fibres. Progress in Polymer Science 24 (2):221–74. doi:10.1016/S0079-6700(98)00018-5.
- Brigida, A. I. S., M. A. Calado, L. R. B. Gonçalves, and M. A. Z. Coelho. 2010. Effect of chemical treatments on properties of green coconut fiber. Carbohydrate Polymers 79 (4):832–38. doi:10.1016/j.carbpol.2009.10.005.
- Dehury, J., S. Nayak, and J. R. Mohanty. 2021. Comprehensive characterization of sea purslane (fiber and the effect of surface modifications on physical, mechanical and thermal properties. Journal of Natural Fibers 1–13. ‘Advanced online Publication’. doi:10.1080/15440478.2021.1904476.
- Fidelis, M. E. A., T. V. C. Pereira, O. D. F. M. Gomes, F. de a Silva, and R. D. T. Filho. 2013. The effect of fiber morphology on the tensile strength of natural fibers. Journal of Materials Research and Technology 2 (2):149–57. doi:10.1016/j.jmrt.2013.02.003.
- Graupner, N., A. S. Herrmann, and J. Mussig. 2009. Natural and man-made cellulose fibre-reinforced poly(lactic acid) (PLA) composites: An overview about mechanical characteristics and application areas. Composite Part A: Applied Science and Manufacturing 40 (6–7):810–21. doi:10.1016/j.compositesa.2009.04.003.
- Jebadurai, S. G., E. Raj, V. S. Sreenivasan, and J. S. Binoj. 2019. Comprehensive characterization of natural cellulosic fiber from Coccinia grandis stem. Carbohydrate Polymers 207:675–83. doi:10.1016/j.carbpol.2018.12.027.
- Jena, P. K., J. R. Mohanty, and S. Nayak. 2020. Effect of surface modification of vetiver fibers on their physical and thermal properties. Journal of Natural Fibers 19 (1):25–36. doi:10.1080/15440478.2020.1726249.
- Kabir, M. M., H. Wang, K. T. Lau, and F. Cardona. 2012. Chemical treatments on plant-based natural fibre reinforced polymer composites: An overview. Composite Part B: Engineering 43 (7):2883–92. doi:10.1016/j.compositesb.2012.04.053.
- Li, X., S. Panigrahi, and L. G. Tabil. 2009. A study on flax fiber-reinforced polyethylene Biocomposites. Applied engineering in agriculture 25 (4):525–31.
- Maache, M., A. Bezazi, S. Amroune, F. Scarpa, and A. Dufresne. 2017. Characterization of a novel natural cellulosic fiber from Juncus effusus. Carbohydrate Polymers 171:163–70. doi:10.1016/j.carbpol.2017.04.096.
- Madhu, P., M. R. Sanjay, M. Jawaid, S. Siengchin, A. Khan, and C. I. Pruncu. 2020. A new study on effect of various chemical treatments on Agave Americana fiber for composite reinforcement: Physico-chemical, thermal, mechanical and morphological properties. Polymer Testing 85:106437. doi:10.1016/j.polymertesting.2020.106437.
- Manimaran, P., S. P. Saravanan, M. R. Sanjay, M. Jawaid, S. Siengchin, and V. Fiore. 2020. New lignocellulosic aristida adscensionis fibers as novel reinforcement for composite materials: Extraction, characterization and weibull distribution analysis. Journal of Polymers and the Environment 28 (6):803–11. doi:10.1007/s10924-019-01640-7.
- Manimaran, P., P. Senthamaraikannan, K. Murugananthan, and M. R. Sanjay. 2018. Physicochemical properties of new cellulosic fibers from azadirachta indica plant. Journal of Natural Fibers 15 (1):29–38. doi:10.1080/15440478.2017.1302388.
- Mobarak, T. A., M. A. Gafur, A. N. Ahmed, S. A. Dhar, and S. A. Dhar. 2018. Effect of chemical modifications on surface morphological, structural, mechanical, and thermal properties of sponge-gourd natural fiber. Fibers and Polymers 19 (1):31–40. doi:10.1007/s12221-018-7199-3.
- Natarajan, T., A. Kumaravel, and R. Palanivelu. 2016. Extraction and characterization of natural cellulosic fiber from Passiflorafoetida stem. International Journal of Polymer Analysis and Characterization 21 (6):478–85. doi:10.1080/1023666X.2016.1168636.
- Nayak, S. 2022. Untreated and chemically treated Pennisetum orientale grass fiber filled vinyl ester composites: Physical, mechanical, and thermal properties analysis. Polymer Composites 43 (7):4318–26. doi:10.1002/pc.26693.
- Nayak, S., and J. R. Mohanty. 2019. Influence of chemical treatment on tensile strength, water absorption, surface morphology, and thermal analysis of areca sheath fibers. Journal of Natural Fibers 16 (4):589–99. doi:10.1080/15440478.2018.1430650.
- Oladele, I. O., and O. G. Agbabiaka. 2015. Investigating the influence of mercerization treatment of sisal fiber on the mechanical properties of reinforced polypropylene composites and modeling of the properties. Fibers and Polymers 16 (3):650–56. doi:10.1007/s12221-015-0650-4.
- Oladele, I. O., and O. G. Agbabiaka. 2017. Development of mathematical models and estimation for the mechanical properties of organic fiber reinforced polyester composites. Fibers and Polymers 18 (7):1336–45. doi:10.1007/s12221-017-1064-2.
- Olawale, A. J., and A. S. Wasiu. 2013. Structural characteristic of bamboo and rattan cane reinforced concrete struts. Physical Review & Research International 3 (4):602–11.
- Reddy, K. O., M. Shukla, C. U. Maheswari, and A. V. Rajulu. 2012. Tensile and structural characterization of alkali treated Borassus fruit fine fibers. Journal of Forestry Research 23 (4):667–74. doi:10.1007/s11676-012-0308-7.
- Rosa, I. M., J. M. Kenny, M. Maniruzzaman, D. Monti, M. Puglia, F. Santulli, C. Sarasini, and F. Sarasini. 2011. Effect of chemical treatments on the mechanical and thermal behavior of okra (abelmoschus esculentus) fibres. Composite Science and Technology 71 (2):246–54. doi:10.1016/j.compscitech.2010.11.023.
- Rout, J., M. Misra, S. Tripathy, S. K. Nayak, and A. K. Mohanty. 2001. The influence of fibre treatment on the performance of coir-polyester composites. Composite Science and Technology 61 (9):1303–10. doi:10.1016/S0266-3538(01)00021-5.
- Sahoo, S. K., J. R. Mohanty, S. Nayak, and B. Behera. 2019. Chemical treatment on rattan fibers: Durability, mechanical, thermal, and morphological properties. Journal of Natural Fibers 18 (11):1762–71. doi:10.1080/15440478.2019.1697995.
- Santhanam, K., A. Kumaravel, S. S. Saravanakumar, and V. P. Arthanarieswaran. 2016. Characterization of new natural cellulosic fiber from the Ipomoea staphylina plant. International Journal of Polymer Analysis and Characterization 21 (3):267–74. doi:10.1080/1023666X.2016.1147654.
- Saravanakumar, S. S., A. Kumaravel, T. Nagarajan, P. Sudhakar, and R. Baskaran. 2013. Characterization of a novel natural cellulosic fiber from Prosopis juliflora bark. Carbohydrate Polymers 92 (2):1928–33. doi:10.1016/j.carbpol.2012.11.064.
- Sarikanat, M., Y. Seki, K. Sever, and C. Durmuşkahya. 2014. Determination of properties of Althaea of?cinalis L. (Marshmallow) ?bres as a potential plant ?bre in polymeric composite materials. Composites B 57:180–86. doi:10.1016/j.compositesb.2013.09.041.
- Sari, N. H., A. Rahman, and E. Syafri. 2019. Characterization of musaceae and saccharum officinarum cellulose fibers for composite application. International Journal of Nanoelectronics and Materials 12 (2):193–204.
- Sathishkumar, T. P., P. Navaneethakrishnan, S. Shankar, R. Rajasekar, and N. Rajini. 2013. Characterization of natural fiber and composites – a review. Journal of Reinforced Plastics and Composites 32 (19):1457–76. doi:10.1177/0731684413495322.
- Seki, Y., M. Sarikanat, K. Sever, and C. Durmuşkahya. 2013. Extraction and properties of Ferula communis (chakshir) fibers as novel reinforcement for composites materials. Composites B 44 (1):517–23. doi:10.1016/j.compositesb.2012.03.013.
- Senthamaraikannan, P., and M. Kathiresan. 2018. Characterization of raw and alkali treated new natural cellulosic fiber from Coccinia grandis. Carbohydrate Polymers 186:332–43. doi:10.1016/j.carbpol.2018.01.072.
- Subramaniam, S., N. Venkatachalam, P. Navaneethakrishnan, and R. Rajsekar. 2016. Effect of pretreatment methods on properties of natural fiber composites: A review. Polymers and Polymer Composites 24 (7):555–66. doi:10.1177/096739111602400715.
- Suyambulingam, I., and E. Raj. 2015. Characterization of new natural cellulosic fiber from Cissus quadrangularis root. Carbohydrate Polymers 110:423–29.
- Szczepanowska, H. M. 2017. Deconstructing rattan: Morphology of biogenic silica in rattan and its impact on preservation of southeast asian art and artifacts made of rattan. Studies in Conservation 63 (6):356–74. doi:10.1080/00393630.2017.1404693.
- Vijay, R., D. L. Singaravelu, A. Vinod, M. R. Sanjay, S. Siengchin, M. Jawaid, J. Parameswaranpillai, and J. Parameswaranpillai. 2019. Characterization of raw and alkali treated new natural cellulosic fibers from tridax procumbens. International Journal of Biological Macromolecules 125:99–108. doi:10.1016/j.ijbiomac.2018.12.056.