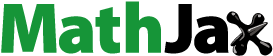
ABSTRACT
This work highlights the exploitation of fibers from a promising plant, commonly called Diss, in polymer matrix reinforcement. In this context, various untreated and treated (with acetic acid, silane, NaOH, thermal) Diss fibers were used to reinforce a thermoplastic matrix, polypropylene (PP). The effect of fiber treatments was evaluated at a ratio of 10% (by mass) of fiber, using mechanical, microstructural and physical characterization. A fiber content optimization study was carried out after choosing the fiber treatment by varying the fiber content from 10% to 40%. The microstructure observations showed a multi-layer structure for the biocomposites studied. The particular morphology of Diss fibers, with the presence of thorns, seems to improve the mechanical adhesion between the two phases. For 10% fiber content composites, the incorporation of the different fibers in the PP matrix led to improvements in most mechanical properties. The biocomposite reinforced with NaOH treated fibers (NPP-10%) showed the best mechanical performance with an improvement of 30%, 22% and 9% in tensile modulus, bending modulus and bending stress, respectively. For the fiber content variation, the NPP was retained, and an enhancement in the tensile modulus was found when the fiber content was below 20%.
摘要
这项工作突出了从一种很有前途的植物(通常称为Diss)中开发纤维,用于聚合物基体增强. 在这种情况下,使用各种未经处理和处理(使用乙酸、硅烷、NaOH、热处理)的Diss纤维来增强热塑性基体聚丙烯(PP). 使用机械、微观结构和物理特性,以10%(按质量计)的纤维比率评估纤维处理的效果. 通过将纤维含量从10%变为40%来选择纤维处理后,进行了纤维含量优化研究. 微观结构观察表明,所研究的生物复合材料具有多层结构. Diss纤维的特殊形态以及刺的存在似乎改善了两相之间的机械粘附. 对于纤维含量为10%的复合材料,在PP基体中加入不同的纤维可提高大多数机械性能. NaOH处理纤维(NPP-10%)增强的生物复合材料表现出最佳的力学性能,拉伸模量、弯曲模量和弯曲应力分别提高了30%、22%和9%. 对于纤维含量的变化,NPP被保留,当纤维含量低于20%时,拉伸模量增加.
Introduction
The use of biocomposites is increasingly adopted in industry as an alternative for conventional composites (Khalid and Arif Citation2022). The term “biocomposites” refers to polymer composites made from a biosourced or petroleum-based matrix reinforced with plant fibers (Arif et al. Citation2022). The advantages of using such materials are: ecological, by substituting synthetic fibers produced by energy-intensive processes and nonrenewable resources with renewable, degradable and less energy-intensive fibers; economic, because the production cost of natural fibers is much lower than their synthetic counterparts; structural, especially for applications that require the use of low density material, such as in the automotive, aerospace and building sectors (Khalid et al. Citation2021a, Citation2021b, Citation2021c; Nouri Citation2020).
However, atmospheric humidity, temperature, ultraviolet light as well as bacterial, fungal and insect attacks strongly influence the degradation of biocomposites when exposed to them causing damage to the bond between fibers and the polymer matrix and leading, consequently, to a decrease in the mechanical properties of biocomposites (Jagadeesh et al. Citation2020; Thyavihalli Girijappa et al. Citation2019; Vinod et al. Citation2020). This degradation occurs mainly by the deterioration of the main components of the fiber (hemicellulose, lignin and cellulose), but also by differential swelling; the fact that plant fibers are very hydrophilic compared to the matrix (usually hydrophobic) (Thyavihalli Girijappa et al. Citation2019).
On the other hand, it appears that the hydrophilic character of natural fibers could be reduced by applying treatments, such as chemical (NaOH, silane, acetic acid …) and physical (Corona, Plasma, thermal …) treatments (Madhu et al. Citation2020; Sanjay et al., Citation2019); - chemical treatments aim to change the chemical composition of the fiber, and physical treatments mainly modify the structural and interfacial properties of the plant fibers without significantly changing their chemical composition. These treatments also make it possible to provide additional improvements to the intrinsic performance of the fibers, particularly with regard to their tensile strength and thermal stability (Nouri Citation2020; Nouri et al. Citation2019).
On the other hand, the use of polypropylene (PP) matrix in biocomposites is increasingly reported in the literature (Arbelaiz et al. Citation2005; Beg and Pickering Citation2008a, Citation2008b; Chen, Guo, and Mi Citation1998; Dhanalakshmi, Ramadevi, and Basavaraju Citation2017; Doan, Brodowsky, and Mäder Citation2007; Law and Ishak Citation2011; Mishra and Verma Citation2006) due to its ability to be recycled, its low thermal conductivity (about 0.17 W/m.K), its low density and its limited environmental footprint (Chen et al. Citation2016; Tabone et al. Citation2010). In addition, it has a low fusion temperature, between 160°C and 170°C. This allows the incorporation of plant fibers without degradation.
Furthermore, there is a wide variety of plants in the world containing interesting fibers offering to manufacturers a wide choice depending on the application (Khalid et al. Citation2021d). These plants vary from one region to another, among them, that are cultivated (such as flax, hemp, miscanthus …) and others that grow wild and ready for exploitation (Jagadeesh et al. Citation2020, Citation2021; Khalid et al. Citation2021b, Citation2021b, Citation2021e; Prabhu et al. Citation2020; Puttegowda et al. Citation2020; Puttegowda et al. Citation2021; Sanjay et al. Citation2018; Thyavihalli Girijappa et al. Citation2019; Vinod et al. Citation2020). The use of these local resources, especially the last category, could also enhance the ecological context of plant fibers by eliminating the environmental cost of cultivation (Nouri Citation2020). However, a wide range of these plants are not yet exploited in industry and are not well studied in the literature.
Diss, or Ampelodesmos mauritanicus, is a plant species in the Poaceae family. This herbaceous perennial plant can grow up to two to three meters high, it is densely fibrous, very robust and it grows in tufts in more or less dry soils (Nouri et al. Citation2019). This plant represents one of the most abundant plant resources on the Mediterranean contour (Achour, Ghomari, and Belayachi Citation2017). In the past, it was used in the roofs of the oldest houses because of its mechanical and hydric properties. Currently, the use of this plant is limited to handicraft applications, notably in the manufacture of exotic umbrellas. This plant has recently started to attract the attention of researchers, notably for its exploitation as a reinforcement for cement (Achour, Ghomari, and Belayachi Citation2017) and polymer composites (Jagadeesh et al. Citation2021; Khalid et al. Citation2021b; Sarasini et al. Citation2019; Touati et al., Citation2019; Touati et al., Citation2021,) as well as for the treatment of expansive soils (Gheris and Hamrouni, Citation2020). However, compared to other natural fibers, Diss fibers are not sufficiently studied, hence their absence in industry.
The fiber extraction method can affect the mechanical properties of the plant fibers and consequently those of biocomposites. For Diss fibers, Bourahli and Osmani (Citation2013) found an average tensile strength and Young’s modulus of 149 ± 81.9 MPa and 8.7 GPa, respectively. But their extraction method was not specified. These results are close to those found by one of these authors, (Bourahli Citation2018), on fibers extracted by decortication, whose average tensile stress and Young’s modulus are 110 MPa and 7.6 GPa, respectively. Sarasini et al. (Citation2019) determined the mechanical properties of Diss fibers extracted by a combined chemical and enzymatic method. These fibers exhibited tensile strength, Young’s modulus and failure strain of 19.11 ± 9.01 MPa, 3.05 ± 0.41 GPa and 1.95% ± 0.36% respectively. Recently, Nouri et al. (Citation2019) found a tensile strength and Young’s modulus of 273 ± 36 MPa and 11.46 ± 2.2 GPa, respectively, using a mechanical extraction method based on the Diss plant morphology. The treatments’ effect was also studied. The Young’s modulus can increase significantly after different treatments (with acetic acid, silane, NaOH, thermal). For mechanical properties of Diss based biocomposites, (Sarasini et al. Citation2019) found that the incorporation of Diss fibers into a polypropylene (PP) matrix did not show any improvement in the mechanical tensile properties compared to the matrix alone. However, the use of a coupling agent (maleic anhydride (MA-g-PP)) resulted in a significant improvement in all these properties with a ratio of no more than 25% for composites with a fiber content of 15% by mass. On the other hand, Touati et al. (2018, Citation2021) found a decrease in the overall mechanical tensile properties of PP (recycled/non-recycled)/polyethylene composite with compatibilizer and 5% in weight (wt%) of Diss fibers compared to the matrix alone. Moreover, Diss fibers have a particular morphology compared to other plant fibers; Nouri et al. (Citation2019) found the presence of thorns on the surface of a large part of the manually extracted fibers. These thorns do not seem to be affected by all the chemical treatments carried out in this study. The authors concluded that this morphology could improve the adhesion between fibers and the matrix, especially when using hydrophobic matrices such as PP.
Due to the number of limited works dealing with the integration of Diss fibers in polymer composites in the literature and the low ratio of fiber introduced, this work aims to present a two-scale approach (micro/macro) in order to develop a new biocomposite material based on Diss fibers. The extraction method developed by Nouri et al. (Citation2019) was used to obtain fibers with good mechanical performance. The effects of treatments and the fiber loading rate were investigated by using fibers that have been extensively characterized in a previous work (Nouri et al. Citation2019, Citation2020, Citation2021). Particular attention was given to the state of the Diss fiber/PP interface by means of scanning electron microscope (SEM), for which the particular morphology effect of Diss fibers has been identified.
Materials and methods
Diss fibers extraction
The Diss plant leaves were harvested by hand in the north of Algeria at the end of their maturity (in 2018). Subsequently, the untreated technical fibers of Diss (UTFD) were extracted manually according to the method of Nouri et al. (Citation2019). Finally, four treatments were applied to the UTFDs as follows (Nouri et al. Citation2019):
NaOH treatment (NTFD): the UTFD were submerged in an aqueous solution containing 5% NaOH at room temperature during 5 h. Afterward the technical fibers of Diss (TFD) treated with NaOH were first cleaned by immersing them in distilled water for 24 h. Then, they were submerged in a distilled water solution containing 2% of acetic acid in order to adjust the pH to 7. Finally, the NTFD were washed several times with tap water and dried in the oven at 60°C for 3 h.
Silane treatment (STFD): Octyltriethoxysilane (2%) was dissolved in a mixture of distilled water/ethanol with a volume ratio of (0.40/0.60). This solution was adjusted using acetic acid until the pH value was equal to 4. Then the solution was stirred for 2 h. Afterward, the UTFD were submerged in the solution for 2 h at room temperature. Finally, the Silane-treated TFD were cleaned with tap water and dried in the oven at 60°C for 3 h.
Acetic acid treatment (ATFD): the UTFD were immersed in an acetic acid solution at room temperature during 90 min. Then, the acetylated TFD were treated with an ethyl acetate solution containing two drops of sulfuric acid to remove excess of acetic acid. Finally, the ATFD were cleaned with tap water and dried in the oven at 40°C for 24 h.
Thermal treatment (TTFD): the thermal treatment of UTFD was carried out in an oven at a temperature of 140°C during 14 h. Then, the thermally treated TFD were cooled down at room temperature.
Biocomposite moulding
The thermo-compression molding method was used to make plates of different Diss fiber/PP biocomposites. PP sheets of 1 mm thickness were supplied by DVPLAST.
A multilayer, composed of three PP sheets and two short Diss fiber mats (randomly dispersed), as shown in , was introduced into the mould/cover system (). Then the assembly was placed in a hydraulic press with heating plates. The mold and press were preheated at a temperature of 180°C. This temperature remained constant throughout the operation to preserve the fibers which degrade at 200°C and above. The pressure for the manufacture of the different biocomposites plates (Diss fibers/PP) and PP () was applied following the protocol presented in : the material was heated for 3 min without pressure, then the pressure was applied gradually from 2 bar to 9 bar, finally, the mold was removed and cooled in water.
Figure 1. A) Preparation of the diss fiber/PP multilayer and biocomposite molding process, b) Pressure history applied on diss fibers/PP plates.
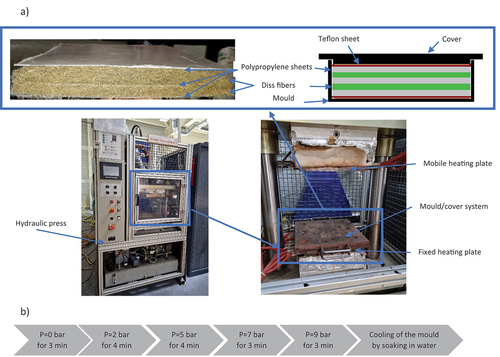
Table 1. Summary of the manufactured composite plates.
These plates have dimensions of 24 × 24 cm2 with a thickness that depends on the amount of material used and varies between 2.5 and 4 mm.
Scanning electron microscope (SEM)
The different observation planes of the biocomposites were examined using a JEOL 6060 SEM. The samples were prepared by coating. The observation surface was positioned parallel to the observation plane and then coated in a cold-coating resin (versocit-2). Finally, the observation surface was polished with a polishing machine (Jean Wirtz FT 250). On the other hand, the fracture surfaces were also examined after the tensile tests without coating.
Density
The density of the biocomposites and the PP matrix was determined by the hydrostatic weighing method. This method consists of weighing the sample in two times: once in air (A) and once in a liquid (B) with a known density (). For each biocomposite, three samples of 10 × 10 mm2 were extracted from the plate at different locations and dried for 48 h in an oven at 60°C. Ethanol was chosen as the liquid due to its low density compared to biocomposites. A Sartorius balance (1/1000) with a suspension measuring device was used for weighing. The density of ethanol was given by the provider and that of the biocomposites (ρc) was calculated by the following equation according to the international standard ISO 1183-1:
Tensile tests
Tensile tests on the biocomposites were carried out by using Instron 3356 and 5566 machines equipped with a 500N and a 1000N load cell, respectively. All tests were performed under controlled laboratory conditions, 23°C and 55%-65% relative humidity (RH). Five specimens of 1B type were obtained from each plate by a punch in accordance with ISO 527–4 (1997).
First of all, in order to determine the Young’s modulus, the 500N load cell was used and the specimens were loaded to small deformations less than 0.4%. In view of the sliding problem between the jaws and the specimens, an INSTRON extensometer with a gauge length of 50 mm was used. The deformation rate was set at 0.5 mm/min according to the recommendation of (NF EN ISO 527–4 Citation1997). Second of all, the same specimens were loaded until failure using a 1000N load cell with a loading rate of 5 mm/min.
Bending tests
The INSTRON model 3366 machine with a 500N load cell was used to perform three-point bending tests. Tests were carried out under controlled laboratory conditions (23°C and 55%-65% RH) with a loading rate of 2 mm/min and a span of 64 mm according to (NF EN ISO 14125 Citation1998).
Results and discussion
Results and discussion on the effect of treatment
Mechanical properties of biocomposites
Tensile properties
shows the mechanical properties (tensile strength (), tensile modulus (E)) of PP plate and the different 10% fiber content biocomposites plates. The PP plate has
and E values of 31.01 ± 0.37 MPa and 1.39 ± 0.08 GPa, respectively. The last one increases significantly after 10% of loading in UTFD. This phenomenon becomes more noticeable with treated fibers. NPP-10% shows the highest modulus, followed by TPP-10%, SPP-10%, APP-10% and UPP-10% with an improvement of 30%, 23%, 17%, 16% and 12.50% respectively. Nevertheless, a decrease in
is observed for these composites. This loss of resistance is more considerable for UPP-10% with a reduction of 21% compared to PP. The treated fiber-reinforced composites showed a more or less similar reduction, with 16%, 16.40%, 12.70% and 10%, respectively, for APP-10%, NPP-10%, TPP-10% and SPP-10%. Similar results are often reported in the literature with regard to the tensile strength reduction for plant fiber/PP biocomposites (Pérez-Fonseca et al. Citation2014; Stark Citation1999).
Figure 2. Tensile properties (modulus and tensile stress) of PP and biocomposites reinforced with the different diss fibers.
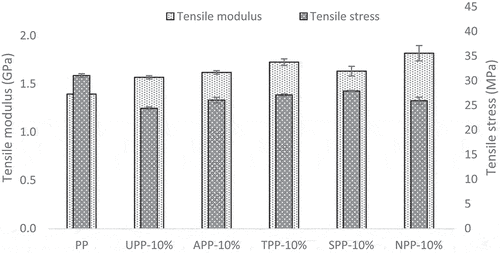
The biocomposites seem to be influenced by the intrinsic properties of fibers. Indeed, according to the work of Nouri et al. (Citation2019), NTFD and STFD show the best tensile modulus values for the Diss fibers studied, followed by ATFD and TTFD, whose difference is not significant according to the uncertainties of the results, and then UTFDs. For biocomposites, NPP-10% and UPP-10% are in first and last position respectively, similarly to what was observed for fibers. Contrary to what was expected, the STFDs do not show an improvement in the chemical adhesion in biocomposites. The choice of the silane molecule (3-Aminopropyl triethoxysilane) was made because of the compatibility of its amine functional groups with those of the PP matrix. Thi (Citation2011) found that such a coupling agent led to the highest Young’s modulus among the studied bamboo fibers/PP biocomposites, even when compared to biocomposites with MA-g-PP. The use of a coupling agent, such as the latter, may be a solution to further improve the mechanical performance of this biocomposite, particularly with regard to tensile stress.
Bending properties
shows the bending properties of PP plate and the different 10% fiber content biocomposites. The PP plate has a bending strength and bending modulus of 34.13 ± 1.95 MPa and 1.28 ± 0.02 GPa, respectively. These results are of the same order of magnitude as those obtained from the tensile test. This is due to the homogeneous nature of PP. The bending properties exhibited by the biocomposites are completely different from those in tensile. APP-10%, NPP-10%, TPP-10%, SPP-10% and UPP-10% show an increase in modulus of 22%, 20%, 13.50%, 10.50% and 7% respectively compared to the PP matrix. These results are discussed below.
By taking into account measurement uncertainties in bending stress, NPP-10% shows a significant improvement of about 9% compared to PP, while UPP-10% shows a decrease of 17%. For the other composites, the results are more or less similar to those for PP plate. These results, discussed in the next part, are still significantly higher than those obtained in tension.
Analysis of the microstructure
shows the SEM observations made on different sections of the APP-10% sample. It was observed on the cross-sectional views (Fig .4.1a) that these biocomposites have a layered structure with 3-layer: two layers of skin on the outer parts, matrix only, and a thicker middle layer (active layer) with ATFDs distributed in the PP matrix. Within this, we can also distinguish three sub-layers, two of which have a high fiber content, separated by a thin sub-layer composed only of PP. This multi-layer architecture of the composite is a consequence of the manufacturing process used. It was chosen in order to create a protective layer for the plant fibers (skin layer), especially when the material is used under changing hygrothermal conditions, which makes it possible to use this biocomposite in these conditions without any additional treatment of its outer surface. At this enlargement, no porosity was observed and fibers appear to be well surrounded by the matrix. These observations can explain the mechanical behavior of these composites in bending in particular for the modulus. Indeed, the fibers appear to be requested by only a part of the maximum applied stress, as the position of the active layer is in the middle of the biocomposite and the maximum tensile stress applied in the lower limit (lower outer part) which is mainly composed of PP. Several authors have reported similar behavior where the tensile and bending modulus are different (Le Duigou and Castro Citation2015).
Figure 4. SEM observations carried out on: 1) the cross-sectional plan of APP-10%, 2) the plane of the active layer of ATFD-10%. 3) Diss fibers. A : active layer, S : skin, PP : polypropylene, F : diss fiber, CM : coating matrix, I : fiber/matrix interfacial region, T : thorn.
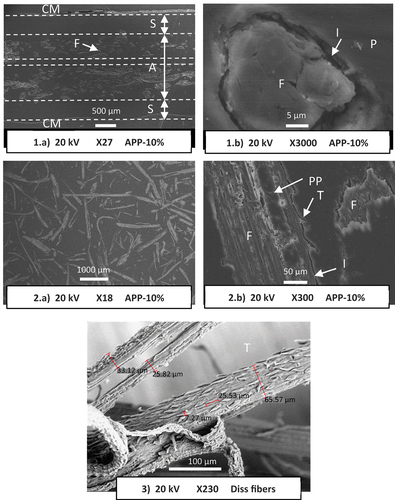
When the resolution is high, still on the same plane (fig.4.1b), a debonding between fibers and the matrix is clearly observable, indicating a poor chemical adhesion between them. The thickness of this interfacial region seems to be relative to the fibers size. These findings are often raised in the literature when using such a matrix with plant fibers (Chen, Guo, and Mi Citation1998; Law and Ishak Citation2011; Le Duigou and Castro Citation2015). The observation in plan of the active layer was also reported (fig.4.2). For an enlargement of 18 times (fig.4.2a) the fibers appear to be well surrounded by the matrix and dispersed in a homogeneous and random way without cracks or porosity within the matrix. When the enlargement is high (fig.4.2b), debonding is clearly observable. These observations could justify the decrease in the tensile stress of biocomposites due to the presence of stress concentration zones. It should be noted that the fibers are randomly oriented, which can amplify this phenomenon, particularly when the fiber is oriented perpendicular to the direction of the applied load.
We can also observe the presence of thorns in fibers (fig.4.2b) which seem to provide more mechanical adhesion with the matrix. These thorns are frequently present in the Diss fibers after extraction, depending on the initial position of the extracted fiber in the leaf (see the work of Nouri et al. Citation2019), which Figure 4.3 gives more information on their geometry. These thorns provide the fibers a good mechanical adhesion with the PP matrix, which could explain the improvement of the Young’s modulus in the case of tensile tests. The findings raised in this section were also observed for the other 10% fibers content biocomposites.
shows the SEM images of the fracture surfaces of the different biocomposites. The following findings were raised for all types of composites: (i) a debonding between fibers and the matrix with the presence of fiber imprints when fibers are oriented perpendicular to the loading direction; (ii) a break in the fibers oriented parallel to the loading direction; (iii) a combination of the two above failure modes when fibers are oriented between these two directions. However, no traces of PP were observed on the pulled fibers, indicating once again the poor chemical bonding between fibers and the matrix.
Figure 5. SEM images of fracture surfaces of different composites. AFR : Adhesive failure region, F : Fiber. TP : thorn prints. T: thorns. BF: broken fiber. TM: matrix tearing. PF: pulled fiber.
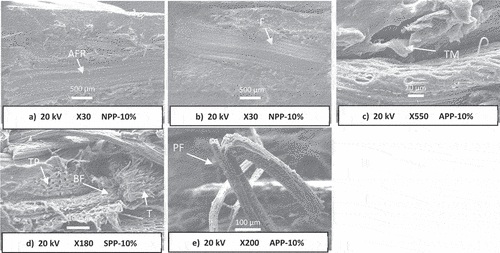
In fact, during the tensile loading of the specimen, sections containing more fibers oriented vertically to the loading direction are the most vulnerable to failure. Images (a) and (b) in show two fracture surfaces of a specimen loaded in traction where we can observe the presence of this kind of fibers on one part and its imprint on the other part. This leaves the rest of fibers and the matrix to withstand the loads in this section. At higher stresses close to the failure of PP, the matrix in this section starts to deform in a ductile manner until it is tearing (see ) leaving the rest of fibers to resist the loading. These fibers do not persist for a long time and adhesive (fibers pull-out) or cohesive (breaking of the fibers) failures occur depending on their adhesion to the matrix ( (d) and (e)). This adhesion, which can only be mechanical, is governed mainly by the presence of thorns. shows a cohesive break in the fiber due to good adhesion of the thorns to the matrix. We can also see the imprint of the thorns on the matrix.
Therefore, the conclusion is that the decrease in the composites tensile strength is mainly due to the presence of stress concentration areas caused by poor chemical adhesion. Whereas the presence of the thorns ensures the transfer of loads between fibers and the matrix and leads to an improvement of the elasticity (Young’s modulus).
Analysis of the density
The PP matrix density has been measured at 0.91 ± 0.001 g/cm3. This value is in the same order of magnitude as that of UTFD, measured at 0.93 ± 0.01 g/cm3 in the work of Nouri et al. (Citation2019).
shows the density results for the different 10% fiber content biocomposites. APP-10%, TPP-10%, SPP-10% and NPP-10% show more or less similar values higher than UPP-10%. It seems that the removal of some non-cellulosic components from fibers during their treatment has led to an increase in their density.
Indeed, Nouri et al. (Citation2019) concluded that treatment with NaOH significantly degrades the non-cellulosic components of Diss fibers, followed by silane and acetic acid treatments. The heat treatment does not significantly change the chemical composition of fibers. These degradations should be accompanied by an increase in the density of these fibers as follows: NTFD > STFD ≈ ATFD > TTFD > UTFD. The evolution of the density of the different biocomposites follows this rank with the exception of the TPP-10% plate. The latter showed a density equivalent to that of NPP-10%. Two hypotheses are possible to interpret these results for TPP-10%: samples are taken from local fiber concentration, or rearrangement of the crystalline structure during heat treatment of fibers resulted in a reduction in fiber volume.
Results analysis on the effect of fiber content in NTFD-based biocomposites (NPP)
Following the different results presented in the previous section, NPP composites were chosen to study the effect of fiber content on the mechanical properties of Diss/PP biocomposites.
Analysis of the microstructure of NTFD-based biocomposites
shows SEM images of NPP-20%, NPP-30% and NPP-40%. For each composite, images (a) and (b) are seen in the cross section of the composite, while image (c) was examined in the plane of the active layer.
Figure 7. SEM images of: a) NPP-20%, b) NPP-30% et c) NPP-40%. AR : agglomeration region. A : active layer, S : skin, PP : polypropylene, F : diss fibers, CM : coating matrix, I : fiber/matrix interface. MC : microcracks. PO : porosity.

For NPP-20%, the thickness of the active layer has significantly increased at the expense of the skin layers and the inter-fiber space appears to be significantly reduced compared to NPP-10% (. (1a) and (1b)). Furthermore, fibers are randomly distributed and well surrounded by the matrix at this enlargement (Fig.7.1c). Regions of fiber agglomerates can sometimes be observed on the active layer (Fig.7.1a). At present, no porosity has been detected in the matrix. However, debonding between fibers and the matrix is always noticed at high resolution (Fig.7.1b). For NPP-30%, the skin thickness seems to be greater than for NPP-20% and at the same time the space between fibers seems to be reduced further ( (2a) and (2c)). Microcracks can sometimes be observed due to fiber-to-fiber contact (Fig.7.2b). For NPP-40%, a significant reduction in the thickness of the skin layer compared to the other composites was observed (Fig.7.3a). Fiber-to-fiber contact seems to become much more important, as well as the presence of microcracks (Fig.7.3b). The latter appear to become larger than those observed on NPP-30%. They are even observable at low enlargement ( (3a) and (3b)). In addition, porosity in the matrix was clearly observed (Fig.7.3c).
Analysis of the density of NTFD-based biocomposites (NPP)
shows the density values of the different NPP. An increase in density as a function of fiber loading rate was observed following a linear law when the latter was below 30%. At 40%, the density has decreased, indicating the presence of significant porosity. This porosity was clearly observed on the SEM images. In addition, delamination regions were also observed on this composite with the naked eye. Indeed, when the loading rate is high, fibers are not sufficiently impregnated by the matrix, which creates fragile regions where the fiber-to-fiber contact is high, leading to the presence of voids and the delamination of the biocomposite.
Mechanical properties of NTFD-based biocomposites (NPP)
Tensile properties
shows the tensile mechanical properties of NPP based composites containing various percentages of Diss fibers. The tensile strength decreases with increasing loading by 6%, 18% and 28% for NPP-20%, NPP-30% and NPP-40%, respectively, compared to NPP-10%. The Young’s modulus improves as the loading rate increases. This is the case when the loading rate is less than 20%, above this value, no significant improvement was observed. The decrease in tensile stress could be explained, as discussed below, by the increase in stress concentration regions with increasing fiber loading rates. As regards modulus, we see an improvement when fibers are well impregnated by the matrix at 10% and 20% loading. When the fiber content reaches 30% of loading, the presence of local microcracks is observed (Fig.7.2b). This leads to a locally poor load transfer between fibers and the matrix. At the same time, the addition of fibers is also locally beneficial. Therefore, compensation between these two facts leads to a more or less stable Young’s modulus. Chen, Guo, and Mi (Citation1998) observed a similar behavior for tensile modulus when Bamboo/PP composites have a fiber content below 40%. Above this value the modulus starts to decrease. However, other authors have observed an increasing modulus evolution even if the fiber loading rate is higher than 30% (Dhanalakshmi, Ramadevi, and Basavaraju Citation2017; Pérez-Fonseca et al. Citation2014; Stark Citation1999).
Bending properties
summarizes the bending properties of NPP. The maximum bending stress is higher when the fiber content is 10% (37 MPa). At higher fiber contents the stress drops and stays similar for all remaining biocomposites, between 26 MPa and 28 MPa. These values are lower than those for PP. The bending modulus does not appear to change significantly regardless of the fiber content of the biocomposites. However, it is still higher than that of PP. In the literature, we often observe an increase in bending modulus with increasing load rate (Le Duigou and Castro Citation2015; Pérez-Fonseca et al. Citation2014). However, in our case, the multilayer structure of the composite, as explained above, seems to affect the evolution of this property. Certainly, the increase in the number of layers could improve the bending modulus of the composite.
Conclusion
In this work application of Diss fibers as reinforcement to polymer composites has been studied. The treatment effect was also examined by three chemical treatments and one thermal treatment.
The different biocomposites showed a layered structure with no porosity in the matrix. However, at the scale of the fiber/matrix interface a lack of chemical adhesion was noticed.
At 10% fiber loading, an improvement in mechanical properties (modulus and stress) in bending and tension was reported, except for tensile stress. NPP-10% showed a better improvement in these properties compared to other composites of the same loading rate, 30%, 22% and 9% for tensile modulus, bending modulus and bending stress, respectively. A combined adhesive and cohesive failure mechanism was observed depending on the orientation of fibers with respect to the loading direction which the presence of the thorns seems to improve the mechanical adhesion.
With increasing loading rate, an increase in tensile modulus was found for NPP composites when the fiber loading rate was below 20%. Above this value, this property seems to remain constant.
Studies will be carried out in the future to improve the chemical adhesion between the Diss fibers and the PP matrix in order to obtain better mechanical properties.
Acknowledgments
This research work has been conducted with the financial support of FEDER - Region Pays de la Loire in the framework of CIPTAP R&D project. Authors thank Yannick BENOIT (Centrale Nantes) for her skill and assistance in SEM observations.
Disclosure statement
No potential conflict of interest was reported by the author(s).
References
- Achour, A., F. Ghomari, and N. Belayachi. 2017. Properties of cementitious mortars reinforced with natural fibers. Journal of Adhesion Science and Technology 31:1938–15. doi:10.1080/01694243.2017.1290572.
- Arbelaiz, A., B. Fernández, J. A. Ramos, A. Retegi, R. Llano-Ponte, and I. Mondragon. 2005. Mechanical properties of short flax fibre bundle/polypropylene composites: Influence of matrix/fibre modification, fibre content, water uptake and recycling. Composites Science and Technology 65:1582–92. doi:10.1016/j.compscitech.2005.01.008.
- Arif, Z. U., M. Y. Khalid, M. F. Sheikh, A. Zolfagharian, and M. Bodaghi. 2022. Biopolymeric sustainable materials and their emerging applications. Journal of Environmental Chemical Engineering 10 (4):108159. doi:https://doi.org/10.1016/j.jece.2022.108159.
- Beg, M. D. H., and K. L. Pickering. 2008a. Mechanical performance of kraft fibre reinforced polypropylene composites: Influence of fibre length, fibre beating and hygrothermal ageing. Composites: Part A, Applied Science and Manufacturing 39 (11):1748–55. doi:https://doi.org/10.1016/j.compositesa.2008.08.003.
- Beg, M. D. H., and K. L. Pickering. 2008b. Reprocessing of wood fibre reinforced polypropylene composites. Part II: hygrothermal ageing and its effects. Composites: Part A, Applied Science and Manufacturing 39:1565–71. doi:10.1016/j.compositesa.2008.06.002.
- Bourahli, M. E. H. 2018. Uni- and bimodal Weibull distribution for analyzing the tensile strength of diss fibers. Journal of Natural Fibers 15:843–52. doi:10.1080/15440478.2017.1371094.
- Bourahli, M. E. H., and H. Osmani. 2013. Chemical and mechanical properties of diss (ampelodesmos mauritanicus) fibers. Journal of Natural Fibers 10:219–32. doi:10.1080/15440478.2012.761115.
- Chen, H., V. V. Ginzburg, J. Yang, Y. Yang, W. Liu, Y. Huang, L. Du, and B. Chen. 2016. Thermal conductivity of polymer-based composites: fundamentals and applications. Progress in Polymer Science 59:41–85. doi:10.1016/j.progpolymsci.2016.03.001.
- Chen, X., Q. Guo, and Y. Mi. 1998. Bamboo fiber-reinforced polypropylene composites: A study of the mechanical properties. Journal of Applied Polymer Science 69:1891–99
- Dhanalakshmi, S., P. Ramadevi, and B. Basavaraju. 2017. A study of the effect of chemical treatments on areca fiber reinforced polypropylene composite properties. Science and Engineering of Composite Materials 24:501–20. doi:10.1515/secm-2015-0292.
- Doan, T.-T.-L., H. Brodowsky, and E. Mäder. 2007. Jute fibre/polypropylene composites II: Thermal, hydrothermal and dynamic mechanical behaviour. Composites Science and Technology 67:2707–14. doi:10.1016/j.compscitech.2007.02.011.
- Gheris, A., and A. Hamrouni. 2020. Treatment of an Expansive Soil using Vegetable (DISS) Fibre. Innovative Infrastructure Solutions 5:1–17. 10.1007/s41062-020-0281-5
- Jagadeesh, P., V. S. H. Ningappa, M. Puttegowda, Y. G. T. Girijappa, S. M. Rangappa, M. R. Khan, I. Khan, and S. Siengchin. 2021. Pongamia pinnata shell powder filled sisal/kevlar hybrid composites: physicomechanical and morphological characteristics. Polymer Composites 42:4434–47. doi:10.1002/pc.26160.
- Jagadeesh, P., Y. G. Thyavihalli Girijappa, M. Puttegowda, S. M. Rangappa, and S. Siengchin. 2020. Effect of natural filler materials on fiber reinforced hybrid polymer composites: an overview. Journal of Natural Fibers 0:1–16. doi:10.1080/15440478.2020.1854145.
- Khalid, M. Y., A. Al Rashid, Z. U. Arif, W. Ahmed, and H. Arshad. 2021c. Recent advances in nanocellulose-based different biomaterials: Types, properties, and emerging applications. Journal of Materials Research and Technology 14:2601–23. doi:10.1016/j.jmrt.2021.07.128.
- Khalid, M. Y., A. Al Rashid, Z. U. Arif, W. Ahmed, H. Arshad, and A. A. Zaidi. 2021b. Natural fiber reinforced composites: Sustainable materials for emerging applications. Results in Engineering 11:100263. doi:10.1016/j.rineng.2021.100263.
- Khalid, M. Y., A. Al Rashid, Z. U. Arif, M. F. Sheikh, H. Arshad, and M. A. Nasir. 2021d. Tensile strength evaluation of glass/jute fibers reinforced composites: an experimental and numerical approach. Results in Engineering 10:100232. doi:10.1016/j.rineng.2021.100232.
- Khalid, M. Y., and Z. U. Arif. 2022. Novel biopolymer-based sustainable composites for food packaging applications: A narrative review. Food Packaging and Shelf Life 33:100892. doi:10.1016/j.fpsl.2022.100892.
- Khalid, M. Y., Z. U. Arif, M. F. Sheikh, and M. A. Nasir. 2021e. Mechanical characterization of glass and jute fiber-based hybrid composites fabricated through compression molding technique. International Journal of Material Forming 14:1085–95. doi:10.1007/s12289-021-01624-w.
- Khalid, M. Y., R. Imran, Z. U. Arif, N. Akram, H. Arshad, A. Al Rashid, and F. P. García Márquez. 2021a. Developments in chemical treatments, manufacturing techniques and potential applications of natural-fibers-based biodegradable composites. Coatings 11:293. doi:10.3390/coatings11030293.
- Law, T. T., and Z. A. M. Ishak. 2011. Water absorption and dimensional stability of short kenaf fiber-filled polypropylene composites treated with maleated polypropylene. Journal of Applied Polymer Science 120:563–72. doi:10.1002/app.33184.
- Le Duigou, A., and M. Castro. 2015. Moisture-induced self-shaping flax-reinforced polypropylene biocomposite actuator. Industrial Crops and Products 71:1–6. doi:10.1016/j.indcrop.2015.03.077.
- Madhu, P., M. R. Sanjay, M. Jawaid, S. Siengchin, A. Khan, and C. I. Pruncu. 2020. A new study on effect of various chemical treatments on Agave Americana fiber for composite reinforcement: physico-chemical, thermal, mechanical and morphological properties. Polymer Testing 85:106437. doi:10.1016/j.polymertesting.2020.106437.
- Mishra, S., and J. Verma. 2006. Effect of compatibilizers on water absorption kinetics of polypropylene/wood flour foamed composites. Journal of Applied Polymer Science 101:2530–37. doi:10.1002/app.23916.
- NF EN ISO 14125. (1998). Composites plastiques renforcés de fibres - Détermination des propriétés de flexion.
- NF EN ISO 527-4. (1997). Plastiques - Détermination des propriétés en traction - Partie 4 : Conditions d’essai pour les composites plastiques renforcés de fibres isotropes et orthotropes.
- Nouri, M. 2020. Développement d’éléments en biocomposite à base de fibre végétale pour la réhabilitation énergétique des bâtiments. PhD diss., Centrale Nantes.
- Nouri, M., I. Griballah, M. Tahlaiti, F. Grondin, and J. Beaugrand. 2019. Plant extraction and physicochemical characterizations of untreated and pretreated diss fibers (ampelodesmos mauritanicus). Journal of Natural Fibers 0:1–11. doi:10.1080/15440478.2019.1687062.
- Nouri, M., M. Tahlaiti, F. Grondin, and R. Belarbi. 2020. The influence of chemical and thermal treatments on the diss fiber hygroscopic behaviors. Journal of Natural Fibers 0:1–14. doi:10.1080/15440478.2020.1848733.
- Nouri, M., M. Tahlaiti, A. Meroufel, and F. Grondin. 2021. Enhanced modeling of water diffusion in natural fibers: application to diss fibers. Journal of Natural Fibers 0:1–10. doi:10.1080/15440478.2021.1982817.
- Pérez-Fonseca, A. A., J. R. Robledo-Ortíz, F. J. Moscoso-Sánchez, D. Rodrigue, and R. González-Núñez. 2014. Injection molded self-hybrid composites based on polypropylene and natural fibers. Polymer Composites 35:1798–806. doi:10.1002/pc.22834.
- Prabhu, L., V. Krishnaraj, S. Sathish, S. Gokulkumar, M. R. Sanjay, and S. Siengchin. 2020. Mechanical and acoustic properties of alkali-treated sansevieria ehrenbergii/camellia sinensis fiber–reinforced hybrid epoxy composites: incorporation of glass fiber hybridization. Applied Composite Materials 27:915–33. doi:10.1007/s10443-020-09840-4.
- Puttegowda, M., S. M. Rangappa, A. Khan, S. A. Al-Zahrani, A. Al Otaibi, P. Shivanna, M. M. Moure, and S. Siengchin. 2020. Preparation and characterization of new hybrid polymer composites from Phoenix pusilla fibers/e-glass/carbon fabrics on potential engineering applications: Effect of stacking sequence. Polymer Composites 41:4572–82. doi:10.1002/pc.25734.
- Puttegowda, M., S. M. Rangappa, A. Khan, S. A. Al-Zahrani, A. A. Otaibi, P. Shivanna, Y. Liu, and S. Siengchin. 2021. Effect of layering sequence on impact properties of alkali treated phoenix pusilla fibers-glass-carbon fabrics reinforced hybrid composite laminates. Journal of Natural Fibers 0:1–11. doi:10.1080/15440478.2021.1932683.
- Sanjay, M. R., P. Madhu, M. Jawaid, P. Senthamaraikannan, S. Senthil, and S. Pradeep. 2018. Characterization and properties of natural fiber polymer composites: A comprehensive review. Journal of Cleaner Production 172:566–81. doi:10.1016/j.jclepro.2017.10.101.
- Sanjay, M. R., S. Siengchin, J. Parameswaranpillai, M. Jawaid, C. I. Pruncu, and A. Khan. 2019. A comprehensive review of techniques for natural fibers as reinforcement in composites: Preparation, processing and characterization. Carbohydrate Polymers 207:108–21. doi:10.1016/j.carbpol.2018.11.083.
- Sarasini, F., J. Tirillò, G. Maffei, A. Zuorro, R. Lavecchia, F. Luzi, D. Puglia, L. Torre, and A. Maghchiche. 2019. Thermal and mechanical behavior of thermoplastic composites reinforced with fibers enzymatically extracted from Ampelodesmos mauritanicus. Polymer Engineering & Science Polymer Engineering & Science 59: 2418–28. doi:https://doi.org/10.1002/pen.25093.
- Stark, N. M. 1999. Wood fiber derived from scrap pallets used in polypropylene composites. Forest Products Journal 49: 39–46.
- Tabone, M. D., J. J. Cregg, E. J. Beckman, and A. E. Landis. 2010. Sustainability metrics: life cycle assessment and green design in polymers. Environmental Science & Technology 44:8264–69. doi:10.1021/es101640n.
- Thi, D. V. V. 2011, Matériaux composites à fibres naturelles / polymère biodégradables ou non. PhD diss., UNIVERSITY OF University of Gronoble.
- Thyavihalli Girijappa, Y. G., S. Mavinkere Rangappa, J. Parameswaranpillai, and S. Siengchin. 2019. Natural fibers as sustainable and renewable resource for development of eco-friendly composites: a comprehensive review. Frontiers in Materials 6. doi:10.3389/fmats.2019.00226.
- Touati, Z., H. Boulahia, N. Belhaneche-Bensemra, and V. Massardier-Nageotte. 2019. Modification of. Waste and Biomass Valorization 10: 2365–78. doi:https://doi.org/10.1007/s12649-018-0225-x.
- Touati, Z., P. L. de Hoyos-Martinez, N. Belhaneche-Bensemra, and F. Charrier- El Bouhtoury. 2021. Influence of different diss fiber treatments over the properties of poly propylene/recycled and regenerated low density polyethylene based biocomposites. Journal of Polymers and the Environment 29:291–303. doi:10.1007/s10924-020-01877-7.
- Vinod, A., M. R. Sanjay, S. Suchart, and P. Jyotishkumar. 2020. Renewable and sustainable biobased materials: an assessment on biofibers, biofilms, biopolymers and biocomposites. Journal of Cleaner Production 258. doi:10.1016/j.jclepro.2020.120978.