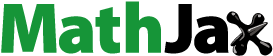
ABSTRACT
The purpose of this study is to characterize alkali-treated fibers from the prop root of fragrant screw pine (FSP) plant in order to determine their suitability as a substitute for man-made fiber in preparation of lightweight bio-based composite materials. The physical, chemical, mechanical, morphological, and thermal properties of alkali-treated FSP fibers (AFSPF) were reported and compared to those of other natural fibers used as reinforcement in polymer composites. Cellulose content (80.53 wt.%), wax content (0.21 wt.%), density (1.41 g/cm3), tensile strength (619–1038 MPa), and young’s modulus (23–41 GPa) of AFSPF were determined. Thermal analysis (TGA and DTG) confirms the thermal stability of these fibers up to 257°C. The characterized properties demonstrate that AFSPF can be used as reinforcement in the preparation of polymer-based bio-composites for applications requiring low weight and high specific strength that meet technical and environmental requirements.
摘要
本研究的目的是对香松(FSP)植物支柱根的碱处理纤维进行表征,以确定其作为人造纤维的替代品在制备轻质生物基复合材料中的适用性. 报道了碱处理的FSP纤维(AFSPF)的物理、化学、力学、形态和热性能,并与聚合物复合材料中用作增强材料的其他天然纤维进行了比较. 测定了AFSPF的纤维素含量(80.53 wt.%)、蜡含量(0.21 wt.%)、密度(1.41 g/cm3)、拉伸强度(619-1038 MPa)和杨氏模量(23-41 GPa). 热分析(TGA和DTG)证实了这些纤维在257°C以下的热稳定性. 所表征的特性表明,AFSPF可以用作制备聚合物基生物复合材料的增强材料,以满足满足技术和环境要求的低重量和高比强度应用.
Introduction
In recent years, the majority of researchers have focused their efforts on developing eco-friendly and sustainable materials derived from renewable natural resources. Natural fibers are a type of material that is environmentally safe, biodegradable, and inexpensive. They are derived from the stem, bast, leaves, and roots of plants (Demircan et al. Citation2020; Ilaiya Perumal and Sarala Citation2020). Natural fibers are preferable to synthetic fibers when reinforcing polymer-based composite materials. At the moment, natural fiber reinforced polymer composites are used in a variety of industries, including automotive, aerospace, construction, military, and industrial (Brailson Mansingh et al. Citation2021).
When natural fibers are used to reinforce polymer composites, their hydrophilicity results in insufficient bonding between the reinforcement and matrix (Arul Marcel Moshi et al. Citation2020a). This will deteriorate the polymer composites’ mechanical and thermal properties. Additionally, when these polymer composites are used in aquatic applications, the natural fibers used as reinforcement absorb water and cause the composite to swell, which is not desirable (Ozen et al. Citation2022). This also limits the use of composite materials developed for aquatic applications.
To address these issues, natural fibers were surface modified via chemical treatment, sea water treatment, and radiation treatment prior to reinforcement (Zhou et al. Citation2021). These surface modification techniques were exposed to decrease the hydrophilicity of natural fibers, resulting in a more crest and trough pattern on the natural fiber’s surface. When these natural fibers are used as reinforcement in polymer composites, the developed polymer composites exhibit improved mechanical, thermal, and aquatic properties (Arul Marcel Moshi et al. Citation2020b).
The scientific name for the fragrant screw pine (FSP) plant is Pandanus fascicularis lam. It is a member of the pandanaceae family and is used in weaving and traditional medicine. FSP is an abundant source of natural resources that can be used in a variety of industrial applications. The FSP plant is found in tropical regions, particularly Asian countries. The stem of this plant is long and tenacious, embedded with thorny leaves. The prop roots of the FSP plant penetrate deeply into the ground, enhancing the fiber’s quality and quantity.
In this work, the fibers were extracted from the prop root of FSP plant for investigation. Alkali treatment of these fragrant screw pine root fibers (FSPRFs) improved their hydrophobic and surface properties. The comprehensive characterization of alkali-treated FSPRFs (AFSPRFs) in terms of mechanical, thermal, and chemical analysis was investigated in order to predict the application of polymer composites when used as reinforcement. Additionally, Fourier transform infrared spectroscopy (FTIR), X-ray diffraction (×RD), and scanning electron microscopy (SEM) were examined to determine the functional group, crystal structure, and surface properties of the fiber. The above findings indicate that when AFSPRFs are used as a reinforcement in polymer composites, it significantly improves the thermomechanical properties of bio-based polymer matrix composites.
Materials and methods
The step-by-step process involved in harvesting, extraction, and chemical treatment of FSPRFs is as shown in .
Figure 1. From extraction to alkali treatment of FSPRF (a) FSP plant (b) Prop roots (c) Prop roots cut into thin sheet (d) Water retting of prop roots (e) Chemical treatment of FSPRF (f) AFSPRF dried under sunlight.

Extraction of FSPRF
As illustrated in , a fragrant screw pine plant was harvested in Derisanamcope village near Nagercoil, Tamilnadu, India (). The prop roots were separated from the harvested plants and sliced into sheets of approximately 4–5 mm thickness (). They were exposed to sunlight for seven days to dry and the dried prop roots were then water retted for 14 days as shown in (Hassan et al. Citation2022). The mechanical combing method was adapted to extract the FSPRFs using a metal comb, sun-dried for three days and stored for further processing (Sathishkumar et al. Citation2013).
Alkali treatment of FSPRF
FSPRFs were treated with a 3% (w/v) solution of aqueous sodium hydroxide (NaOH) for 3 h at room temperature as shown in (Rajkumar, Manikandan, and Saravankumar Citation2016). Subsequently, the fibers were washed several times with distilled water to remove any remaining alkali moieties on their surface. Following that, the treated fibers were neutralized with a 1% (w/v) solution of hydrochloric acid (HCL) to remove any excess NaOH on the fiber surface. Finally, the fibers were dried for 5 h at 70°C in an air oven and the AFSPRFs are depicted in .
Characterization of AFSPRF
The chemical composition of AFSPRF was determined using standard test procedures described elsewhere in literature including cellulose, hemicellulose, lignin, and wax content (Sudhir Chakravarthy et al. Citation2020). AFSPRF density was determined using Mettler Toledo XS205 balance method and the moisture content of AFSPRF was determined using standard weight loss method (Brailson Mansingh et al. Citation2021b). The ASTM D3822–07 standard was used to conduct the single fiber tensile test and the functional groups present in AFSPRF were determined using Fourier Transform Infrared (FTIR) Spectroscopy at a scan rate of 32 scans per minute and a resolution of 4 cm-1 (Narayanasamy et al. Citation2020). The powdered AFSPRF was XRD analyzed in the 2 theta range of 10° to 70° with a goniometer speed of 5°/min. Thermogravimetric analysis (TG & DTA) was carried out in the temperature range of 30°C to 1000°C at a heating rate of 10°C/min (Siva et al. Citation2020). Moreover, the Differential Scanning Calorimetry (DSC) analysis was carried out in the temperature range of 30°C to 500°C at a heating rate of 10°C/min. In addition, the AFSPRF’s surface morphology was investigated using a scanning electron microscope (SUPRA 55, Zeiss, Oberkochen, Germany) set to a 21 kV accelerating voltage.
Results and discussion
Chemical analysis of AFSPRF
The chemical properties of natural fibers vary according to the geographical and climate conditions in which the plants grow, as well as the plant’s maturity (Thooyavan et al. Citation2022). Natural fiber characteristics such as fiber structure, morphology, thermal degradation, bonding, and mechanical properties are primarily determined by the fiber’s cellulose, hemicelluloses, lignin, and wax content. The following summarizes the biochemical composition of AFSPRF. AFSPRF has a cellulose content of 80.53 wt.%, which is higher than the FSPRF (73.10 wt.%) and addition of cellulose improves the mechanical properties of fiber. Hemicellulose content of treated FSPRF is 7.45 wt.%, which is less than the FSPRF content (12.58 wt.%) and responsible for the fiber’s moisture absorption, disintegration, and thermal stability. AFSPRF contains 5.24 wt.% lignin, which contributes to the cell wall texture. Also, the low wax content 0.21 wt.% in AFSPRF contributes better in fiber bonding characteristics when used with polymer matrix. Additionally, the moisture content of AFSPRF was determined following % moisture content by weight method after drying the sample in an oven at 104 °C for 4 h. The moisture content of AFSPRF is determined to be 5.43 wt.% which is less compared to the untreated fibers (8.28 wt.%) and also it is observed that the alkali treatment had removed a portion of hemicellulose, lignin, and wax from the FSPRF enhancing the mechanical and bonding properties (Brailson Mansingh et al. Citation2021a).
Table 1. Comparison of physico-chemical and mechanical properties of AFSPRF with other fibers. (Arthanarieswaran, Kumaravel, and Saravanakumar Citation2015; Demircan et al. Citation2020a; Manimaran et al. Citation2018; Raju, Depoures, and Kumaran Citation2021; Saravanakumar et al. Citation2013).
FTIR analysis of AFSPRF
illustrates the FTIR spectrum of both FSPRF and AFSPRF for comparison and the major functional group present in the fibers were analyzed using FTIR spectroscopy (Sajin et al. Citation2022). The broad peak at 3330 cm−1 is due to OH stretching resulting in the presence of cellulose. Due to the presence of CH in the cellulose component, the peak at 2919 cm−1 is attributed to C-H stretching vibration. A small absorption peak at 2850 cm−1 corresponds to the alkaline functional group’s C-H symmetric bending. Another small peak at 1601 cm−1 and 1417 cm−1 corresponds to the C-O stretching of AFSPRF’s carbonyl functional group. At 1029 cm−1, a distinct peak is observed due to the presence of an alkyl halide functional group. The FTIR spectrum peaks confirm the presence of biochemical components identified in the AFSPRF.
Morphological analysis of AFSPRF
depicts the scanning electron microscopy (SEM) image of FSPRF and AFSPRF. It is well known that natural fibers derived from plants are impregnated with pectin, lignin, and other impurities (Arthanarieswaran, Kumaravel, and Saravanakumar Citation2015). However, the AFSPRF surface is rougher with more crests and troughs due to the removal of non-cellulosic material and wax from the fiber during alkali treatment, as illustrated in . The AFSPRF’s rough surface may facilitate interfacial bonding between fibers and matrix in polymer composites (Raju, Depoures, and Kumaran Citation2021). Microfibrillar structures and agglomeration of alkali powder on AFSPRF surface were also observed in . Moreover, the presence of alkali powder on the surface of AFSPRF is a result of insufficient neutralization with HCL after alkali treatment.
Micro fibril angle plays an important role in the mechanical properties of fiber. The microfibril angle (α) of AFSPRF was calculated from the following global EquationEquation (1)(1)
(1) (Brailson Mansingh et al. Citation2021b).
where ε is the strain, α is the microfibril angle (degree), ΔL is the Elongation at break (mm) and Lo is the gauge length (mm). The calculated microfibril angle of the AFSPRF was in the range of 6.9° − 9.2° whereas FSPRF had a microfibril angle of 7.2°. However, similarly microfibril angles of the other natural fibers reported in the literature are Flax, 5°, Hemp, 6.2°, Jute 8.1°, Banana 11° − 12° and Prosopis juliflora, 10.64° (Raju, Depoures, and Kumaran Citation2021). The microfibril angle is also computed from the SEM image using image analysis techniques using Image J software as 9.238° as shown in . Minimum microfibril angle facilitates better stress transfer from the matrix phase to the fiber phase when reinforced in polymer composites.
XRD analysis of AFSPRF
The X-ray diffractogram of FSPRF and AFSPRF is shown in It demonstrates unequivocally two distinct peaks occurred at 2ϴ = 15.71° and 2ϴ = 22.43°. These two peaks indicate that the AFSPRF is naturally semi-crystalline in nature (Selvan et al. Citation2021). The first peak at 15.71° is attributed to the (1 1 0) crystallographic plane, indicating that AFSPRF is amorphous (Iam). The second peak at 22.43° corresponds to the (2 0 0) crystallographic plane, indicating the fiber’s crystalline nature. The remaining small peaks in the spectrum indicate the presence of impurities in the AFSPRF. The AFSPRF’s calculated crystalline index (CI) was 64.8%, which is higher than that of Prosopis juliflora (46%), Sansevieria ehrenbergii (52.27%), Acacia leucophloea (51%), and Cotton shell (48.96%), but lower than that of Jute (71%) and Hemp (88%) (Manimaran et al. Citation2018).
The crystallinity index (C.I) of the FSP fiber was calculated by Segal empirical EquationEquation (2)(2)
(2) (Segal et al. Citation1958).
where Ic is the maximum intensity of crystalline peak at 2θ = 22.43° and Iam is the intensity of amorphous peak at 2θ = 15.71°. By using Scherrer’s EquationEquation (3)(3)
(3) , the crystallite size (CS) of AFSPRF was found to be 25.71 nm which is 17.07% higher than FSPRF which reduces the hydrophilic nature of the fiber (Brailson Mansingh et al. Citation2021b).
where K = 0.89 is scherrer’s constant, λ is the wave length of the radiation, β is the peak’s full-width at half-maximum (FWHM) and θ is the Bragg’s diffraction angle.
Physico-mechanical analysis of AFSPRF
The AFSPRF’s physico-mechanical properties were compared to those of other natural fibers as listed in . The diameter of AFSPRF was determined using an optical microscope and found to be between 121 µm and 343 µm. As shown in , a contour line was drawn to delineate the fiber cross-section and the area was calculated using image J software. Image analysis is a highly precise method for determining the fiber’s cross-sectional area. Generally, measuring the diameter of natural fibers is difficult, as the shape of the fiber varies in nature (Demircan et al. Citation2020a). However, for the purpose of estimating the tensile properties it is assumed to be circular in shape and the diameter of the fiber was calculated by the following EquationEquation (4)(4)
(4) .
where Df denotes the diameter of the fiber and Lf denotes the linear mass density of fiber in denier (mass in grams per 9000 m length of fiber). It was the measure of fineness of the fiber and is determined as per ASTM D1577–07 standard by weighing 100 fibers, each with 60 mm in length. Md represents the mass density (g/cm3) (Saravanakumar et al. Citation2014). Selected fiber samples are powdered and filled into a cylindrical shape container of known volume and weighed to determine the mass density; the density was determined to be 1.41 g/cm3. The linear mass density of the given sample is 730 g per 9000 m fiber length. The fiber diameter was estimated for cross verification using EquationEquation (4)(4)
(4) and noted as 250.1 µm.
The AFSPRF exhibited highest tensile strength (619–1038 MPa), young’s modulus (23–41 GPa) and elongation at break (3.84–9.91%), whereas the FSPRF exhibited lowest tensile strength (531–915 MPa, 21–33 GPa, and 3.36–8.85%, respectively. These properties are significantly superior to those of other natural fibers including Sisal, Hemp, Bagasse, Kenaf, and Jute as listed in . As a result of partial removal of amorphous contents and the enrichment of cellulose wt.%, AFSPRF exhibits superior mechanical properties in relation to FSPRF.
TGA analysis of AFSPRF
illustrates the thermal behavior of FSPRF and AFSPRF. At 80.4°C, the fiber began to lose weight, which is attributed to the loss of moisture content. At around 160°C, a second minor weight loss was observed due to lignin decomposition. At approximately 257°C, AFSPRF was found to be thermally stable, whereas between 257°C and 370°C the next degradation peak was observed associated to thermal depolymerization of hemicelluloses (Karthik et al. Citation2022). A prominent peak with a mass change of 62.59% was observed at 341.8°C in the DTG curve, indicating the possible decomposition of cellulose caused by the disintegration of its molecular structure. A similar peak was also observed for Jute, Hemp, Kenaf, and Bamboo fibers at temperatures of 298.2°C, 308.2°C, 309.2°C, and 321°C, respectively (Manimaran et al. Citation2018). At 999.7°C, 19.27% of residual char content was discovered at the end of the process.
DSC analysis of AFSPRF
illustrates the DSC curve of FSPRF and AFSPRF, which exhibits a series of endothermic and exothermic reactions at various temperatures. Heat is absorbed in the endothermic region of the natural fiber as a result of moisture evaporation in the intercellular region (Saravanakumar et al. Citation2013). Generally, free water is more easily removed than water that is linked to the cellulose. To remove the linked water, a higher temperature of around 100°C is required. In AFSPRF, the endothermic peak for evaporating water is around 88°C, whereas in FSPRF, it is around 83°C. This demonstrates that 3% alkali solution was insufficient to completely dissolve the hemicellulose in the fiber (Cheng et al. Citation2020). On AFSPRF, the exothermic peak terminates at 360°C, indicating that the hemicellulose and cellulose contents have been completely decomposed. The endothermic and exothermic peaks of AFSPRF are compared to those of other natural fibers in . The endothermic and exothermic reactions of AFSPRF indicate that it is well suited for reinforcement in polymer composites.
Table 2. Endothermic and Exothermic Peak of AFSPRF in comparison with other natural Fibers (Narayanasamy et al. Citation2020; Sudhir Chakravarthy et al. Citation2020; Arthanarieswaran, Kumaravel, and Saravanakumar Citation2015; Arthanarieswaran, Kumaravel, and Saravanakumar Citation2015).
Conclusions
The characterization results of AFSPRF show that it can be used as reinforcement in polymer composite and can contribute to the sustainability of composite industry. The specific outcomes over the comprehensive characterization of AFSPRF is as follows:
High cellulose content (80.53 wt.%) with rough surface morphology ensures better mechanical and bonding characteristics of AFSPRF when reinforced in polymer composites.
Low density (1.41 (g/cm3)) and sufficient tensile strength (1038 MPa) of AFSPRF enhances the specific strength of polymer composite when used as a reinforcement. Also, the materials with high specific strength are required for lightweight applications.
Hydrophilic nature of AFSPRF is well within the limit to be used as a reinforcement in polymer composites used for aquatic applications, which is confirmed through XRD analysis.
Thermal stability of AFSPRF to withstand the polymerization temperature verified through TGA and DSC analysis adds value to the fiber for use in multiple industrial applications.
Disclosure statement
No potential conflict of interest was reported by the author(s).
Data availability statement
This is an ongoing research work and hence the data cannot be shared at this moment.
Additional information
Funding
References
- Arthanarieswaran, V. P., A. Kumaravel, and S. S. Saravanakumar. 2015. Physico-chemical properties of alkali treated Acacia leucophloea fibers. International Journal of Polymer Analysis and Characterization 20 (1):704–14. doi:10.1080/1023666X.2015.1081133.
- Arul Marcel Moshi, A., D. Ravindran, S. R. Sundara Bharathi, S. Indran, and G. Suganya Priyadharshini. 2020a. Characterization of surface-modified natural cellulosic fiber extracted from the root of Ficus religiosa tree. International Journal of Biological Macromolecules 156 (1):997–1006. doi:10.1016/j.ijbiomac.2020.04.117.
- Arul Marcel Moshi, A., D. Ravindran, S. R. Sundara Bharathi, S. R. Padma, S. Indran, and D. Divya. 2020b. Characterization of natural cellulosic fiber extracted from Grewia damine flowering plant’s stem. International Journal of Biological Macromolecules 154 (1):1246–55. doi:10.1016/j.ijbiomac.2020.07.225.
- Brailson Mansingh, B., J. S. Binoj, S. A. Hassan, M. Mariatti, S. Siengchin, M. R. Sanjay, and K. N. Bharath. 2021b. Characterization of natural cellulosic fiber from cocos nucifera peduncle for sustainable biocomposites. Journal of Natural Fibers. doi:10.1080/15440478.2021.1982827.
- Brailson Mansingh, B., J. S. Binoj, S. A. Hassan, M. Mariatti, S. Siengchin, M. R. Sanjay, Y. C. Liu, and P. Saji Raveendran. 2021a. Characterization of chemically treated new natural cellulosic fibers from peduncle of Cocos nucifera L. Var typica. Polymer Composites. doi:10.1002/pc.26307.
- Brailson Mansingh, B., J. S. Binoj, N. Prem Sai, S. A. Hassan, S. Siengchin, M. R. Sanjay, and L. Y. Cheng. 2021. Sustainable development in utilization of Tamarindus indica L. and its by-products in industries: A review. Current Research in Green and Sustainable Chemistry 4 (1):e100207. doi:10.1016/j.crgsc.2021.100207.
- Cheng, D., B. Weng, Y. Chen, S. Zhai, C. Wang, R. Xua, J. Guo, Y. Lv, L. Shi, and Y. Guo. 2020. Characterization of potential cellulose fiber from Luffa vine: A study on physicochemical and structural properties. International Journal of Biological Macromolecules 164 (1):2247–57. doi:10.1016/j.ijbiomac.2020.08.098.
- Demircan, G., M. Kisa, M. Özen, A. Açikgöz, B. Aktaş, and M. Ali Kurt. 2020a. A bio-based epoxy resin from rosin powder with improved mechanical performance. Emerging Materials Research 9 (4):1076–81. doi:10.1680/jemmr.20.00001.
- Demircan, G., M. Kisa, M. Ozen, and B. Aktas. 2020. Surface-modified alumina nanoparticles-filled aramid fiber-reinforced epoxy nanocomposites: Preparation and mechanical properties. Iranian Polymer Journal 29 (1):253–64. doi:10.1007/s13726-020-00790-z.
- Hassan, S. A., J. S. Binoj, K. L. Goh, B. B. Mansingh, K. C. Varaprasad, M. Y. Yahya, F. E. C. Othman, U. Ahmed, D. Nurhadiyanto, Mujiyono, et al. 2022. Effect of fiber stacking sequence and orientation on quasi- static indentation properties of sustainable hybrid carbon/ramie fiber epoxy composites. Current Research in Green and Sustainable Chemistry 5 (1):e100284. doi:10.1016/j.crgsc.2022.100284.
- Ilaiya Perumal, C., and R. Sarala. 2020. Characterization of a new natural cellulosic fiber extracted from Derris scandens stem. International Journal of Biological Macromolecules 165 (1):2303–13. doi:10.1016/j.ijbiomac.2020.10.086.
- Karthik, K., J. U. Prakash, J. S. Binoj, and B. B. Mansingh. 2022. Effect of stacking sequence and SiC nanoparticles on properties of carbon/glass/kevlar fiber reinforced hybrid polymer composites. Polymer Composites. doi:10.1002/pc.26912.
- Manimaran, P., P. Senthamaraikannan, M. R. Sanjay, M. K. Marichelvam, and M. Jawaid. 2018. Study on characterization of Furcraea foetida new natural fiber as composite reinforcement for lightweight applications. Carbohydrate Polymers 181 (1):650–58. doi:10.1016/j.carbpol.2017.11.099.
- Narayanasamy, P., P. Balasundar, S. Senthil, M. R. Sanjay, S. Siengchin, A. Khan, and A. M. Asiri. 2020. Characterization of a novel natural cellulosic fiber from Calotropis gigantea fruit bunch for ecofriendly polymer composites. International Journal of Biological Macromolecules 150 (1):793–801. doi:10.1016/j.ijbiomac.2020.02.134.
- Ozen, M., G. Demircan, M. Kisa, A. Acikgoz, G. Ceyhan, and Y. Işıker. 2022. Thermal properties of surface-modified nano-Al2O3/Kevlar fiber/epoxy composites. Materials Chemistry and Physics 278 (1):125689. doi:10.1016/j.matchemphys.2021.125689.
- Rajkumar, R., A. Manikandan, and S. S. Saravankumar. 2016. Physicochemical properties of alkali-treated new cellulosic fiber from cotton shell. International Journal of Polymer Analysis and Characterization 21 (1):359–64. doi:10.1080/1023666X.2016.1160509.
- Raju, J. S. N., M. V. Depoures, and P. Kumaran. 2021. Comprehensive characterization of raw and alkali (NaOH) treated natural fibers from Symphirema involucratum stem. International Journal of Biological Macromolecules 186 (1):886–96. doi:10.1016/j.ijbiomac.2021.07.061.
- Sajin, J. B., R. C. Paul, J. S. Binoj, B. B. Mansingh, M. G. A. Selvan, K. L. Goh, R. S. R. Isaac, and M. S. S. Saravanan. 2022. Impact of fiber length on mechanical, morphological and thermal analysis of chemical treated jute fiber polymer composites for sustainable applications. Current Research in Green and Sustainable Chemistry 5 (1):e100241. doi:10.1016/j.crgsc.2021.100241.
- Saravanakumar, S. S., A. Kumaravel, T. Nagarajan, and I. Ganesh Moorthy. 2014. Investigation of physico-chemical properties of alkali-treated Prosopis juliflora fibers. International Journal of Polymer Analysis and Characterization 19 (4):309–17. doi:10.1080/1023666X.2014.902527.
- Saravanakumar, S. S., A. Kumaravel, T. Nagarajan, P. Sudhakar, and R. Baskaran. 2013. Characterization of a novel natural cellulosic fiber from Prosopis juliflora bark. Carbohydrate Polymerss 92 (1):1928–33. doi:10.1016/j.carbpol.2012.11.064.
- Sathishkumar, T. P., P. Navaneethakrishnan, S. Shankar, and R. Rajasekar. 2013. Characterization of new cellulose Sansevieria ehrenbergii fibers for polymer composites. Composite Interface 20 (80):575–93. doi:10.1080/15685543.2013.816652.
- Segal, L., J.J. Creely, A.E. Martin, and C.M. Conrad. 1959. An Empirical Method for Estimating the Degree of Crystallinity of Native Cellulose Using the X-Ray Diffractometer. Textile Research Journal 29 (10):786–94. doi:10.1177/004051755902901003.
- Selvan, M. T. G. A., J. S. Binoj, J. T. E. J. Moses, N. P. Sai, S. Siengchin, M. R. Sanjay, and Y. Liu. 2021. Extraction and characterization of natural cellulosic fiber from fragrant screw pine prop roots as potential reinforcement for polymer composites. Polymer Composites. doi:10.1002/pc.26376.
- Siva, R., T. N. Valarmathi, K. Palanikumar, and V. S. Antony. 2020. Study on a novel natural cellulosic fiber from Kigelia africana fruit: Characterization and analysis. Carbohydrate Polymers 244 (1):116494. doi:10.1016/j.carbpol.2020.116494.
- Sudhir Chakravarthy, K., S. Madhu, J. S. N. Raju, and J. S. Md. 2020. Characterization of novel natural cellulosic fiber extracted from the stem of Cissus vitiginea plant. International Journal of Biological Macromolecules 161 (1):1358–70. doi:10.1016/j.ijbiomac.2020.07.230.
- Thooyavan, Y., L. A. Kumaraswamidhas, R. E. Raj, J. S. Binoj, and B. B. Mansingh. 2022. Failure analysis of basalt bidirectional mat reinforced micro/nano Sic particle filled vinyl ester polymer composites. Engineering Failure Analysis 136 (1):106227. doi:10.1016/j.engfailanal.2022.106227.
- Zhou, S., L. Xia, K. Zhang, Z. Fu, Y. Wang, Q. Zhang, L. Zhai, Y. Mao, and W. Xu. 2021. Titanium dioxide decorated natural cellulosic Juncus effusus fiber for highly efficient photo-degradation towards dyes. Carbohydrate Polymers 232 (1):115830. doi:10.1016/j.carbpol.2020.115830.