ABSTRACT
Nanofibers electrospun from cellulose sources have received substantial attention. Using trifluoro acetic acid (TFA) as the solvent, dissolved cotton and jute were comparatively electrospun to cotton nanofibers (CNFs) and jute nanofibers (JNFs), respectively. The viscosity and conductivity of the as-prepared polymer solutions were measured. The morphology, chemical structure, thermal stability and decomposition pattern together with the crystallinity index of the JNFs and CNFs were characterized by scanning electron microscopy (SEM), Fourier transform infrared (FTIR) analysis, thermogravimetric analysis (TGA) and X-ray diffraction (XRD), respectively. SEM analysis showed no major differences in surface morphology between JNFs and CNFs. The TGA results confirmed that the as-spun nanofibers have excellent thermal stability up to 210 ºC temperature before cellulose decomposition. The JNFs showed a similar degradation pattern as the CNFs. The results of this work will contribute to proposing appropriate applications of electrospun nanofibers from jute.
摘要
纤维素来源的纳米纤维静电纺丝已受到广泛关注. 以三氟乙酸(TFA)为溶剂,将溶解棉和黄麻分别与棉纳米纤维(CNFs)和黄麻纳米纤维(JNFs)进行比较电纺. 测量了制备的聚合物溶液的粘度和电导率. 分别用扫描电子显微镜(SEM)、傅里叶变换红外(FTIR)分析、热重分析(TGA)和X射线衍射(XRD)对JNF和CNF的形貌、化学结构、热稳定性和分解模式以及结晶度指数进行了表征. SEM分析表明,JNF和CNF的表面形貌没有重大差异. TGA结果证实,纺丝态纳米纤维在纤维素分解前的210ºC温度下具有优异的热稳定性. JNF的降解模式与CNF相似. 这项工作的结果将有助于提出黄麻静电纺纳米纤维的适当应用.
Introduction
Nanocrystals and nanofibers from cellulose have gained considerable attention in recent years for applications in the environmental remediation and pharmaceutical formulations. Cellulose nanofibers are proven to be ideal for several applications because of their ultralow density, tunable porous architecture and outstanding mechanical properties (Trilokesh and Uppuluri Citation2019). Nanocelluloses have been used in the preparation of optical functional materials, such as chiral nematic (liquid crystal), iridescent films, greenhouse plastics, anti-counterfeit technologies and particle packing (Nevo et al. Citation2015). They were also explored as ultralight, durable and flexible foams/aerogels (Lavoine and Bergström Citation2017). Nanocelluloses have been extensively used as natural fillers in composites due to its high mechanical strength, modulus (138–150 GPa), and tensile strength (10 GPa) (Šturcová, Davies, and Eichhorn Citation2005). Nanocelluloses have also been a promising candidate for applications in fields, such as biomedical, pharmaceuticals, electronics, barrier films, nanocomposites, membranes and supercapacitors (Tian and He Citation2016; Trache et al. Citation2017).
Growing efforts have recently been put into the development of high-performance nanofibers/nanocomposites/nanocrystals from natural cellulose resources other than cotton, such as banana, pineapple leaf, jute, sugar palm, sisal, sugarcane straw, and jackfruit peel (Abraham et al. Citation2011; Bilatto et al. Citation2020; Ilyas et al. Citation2018; Morán et al. Citation2007; Rodrigues et al. Citation2015; Thomas et al. Citation2015; Trilokesh and Uppuluri Citation2019). These plants contain mainly cellulose, but also hemicellulose, lignin and some other extractives and inorganic salts (Ara et al. Citation2021; Nechyporchuk, Belgacem, and Bras Citation2016). Among these, jute is the most abundant biodegradable lignocellulosic natural bast fiber, which holds the second position (8.5%) in terms of natural fiber production globally (Wang et al. Citation2009) next to cotton (78.8%) (Siqueira, Bras, and Dufresne Citation2010). Jute consists of celluloses (58 63 wt.%), hemicelluloses (20 24 wt.%), lignin (12 15 wt.%) and small quantities of fats, pectin, and aqueous extracts (Wang, Cai and Yu Citation2008). Regeneration of cotton fibers into nanofibers has achieved a great success. However, regeneration of jute fibers into high-performance technical fibers, i.e., nanofibers, is still in the beginning stage. Ideally, a proper solvent to dissolve jute fibers will grant the possibility of electrospinning nanofibers from the dissolved jute. Trifluoro acetic acid (TFA) has been potentially utilized for dissolving cellulosic fibers for electrospinning (Ohkawa Citation2015; Ohkawa et al. Citation2009; Rodrigues et al. Citation2015; Santos et al. Citation2015; Uthandi, Marimuthu, and Tilak Citation2019) due to its high acid strength, semi-conductivity with a moderate charge capacity (Ohkawa et al. Citation2009), high volatility, and miscibility with many organic solvents (Guzman-Puyol et al. Citation2015). TFA can be recycled (up to 97%) by distillation (Mahajan et al. Citation2008). Recently, dissolved jute using TFA as the solvent has been successfully electrospun into nanofibers (Ara et al. Citation2021).
Both cotton and jute are naturally abundant cellulose fibers, and nanofibers can be regenerated from dissolved polymer solution from them. However, their chemical components except for cellulose are different. Thus, their regenerated nanofibers may exhibit different properties. This work reports on a comparative study of the structure and properties between electrospun cotton nanofibers (CNFs) and jute nanofibers (JNFs) using the TFA solvent. The solution viscosity and conductivity, spinnability, chemical components, morphology, thermal stability and crystalline structure were tested/characterized and compared. The findings of this work will shed a light on the potential applications of JNFs in the same application areas of CNFs.
Experimental
Materials
Jute fibers (Bangla Tossa C grade) were collected from Khulna jute mills, Bangladesh. Cotton fibers were collected from local market. Both fibers were used without any pre-treatment. TFA was bought from Sigma Aldrich. TFA was of analytical grade and used without further purification.
Fabrication
The schematics of the experiments are shown in . Dissolution of cotton fibers into TFA solution was the same as reported in our previous work (Ara et al. Citation2021). Briefly, cotton fiber pieces (1–5 mm) were directly added into TFA solution with different concentrations (1, 1.5, 2, 2.5, 3, 3.5, 4, 4.5 & 5 cotton wt.%) under magnetic stirring at room temperature. The stirring process lasted for 72 h to make a completely dissolved cotton-TFA solution. The raw jute was dissolved in TFA using the same process as reported previously (Ara et al. Citation2021). Raw jute took 120 h to fully dissolve under continuous magnetic stirring. It also took almost 7–8 days to fully dissolve the 5 wt.% jute fibers into a highly viscous solution. Both solutions were used as the polymer solution to perform electrospinning, as shown in . A conventional needle-based electrospinning setup was used with experimental parameters listed in . Proper experimental parameters for electrospinning were chosen after a few trials, and electrospun nanofibers were collected on the aluminum foil collector for further characterization and measurements.
Table 1. Experimental parameters of electrospinning (needle gauge 16).
Characterization and measurements
Solution conductivity was measured by a Palintest 146 Waterproof 800 pH/Conductivity/TDS Meter. The conductive electrode was completely immersed in the solution at room temperature, while the displayed readings were recorded. Viscosity was measured by a Brookfield KF40 falling ball viscometer at a temperature of 25°C.
The Fourier transform Infrared (FTIR) spectra were measured by a Perkin Elmer Spectroscopy (400 series, UK) device with a universal attenuated total reflectance (ATR) sampling accessory. The spectra were collected in the range of 650–4000 cm−1. Peak heights of absorptions band were measured by the software OriginPro70.
A Hitachi tabletop scanning electron microscope (TM4000 series) was used to observe the surface morphology of as-collected nanofibers with an accelerating voltage of 15 kV (in the case of JNFs) and 5 KV (in the case of CNFs) under mixed vacuum mode. Samples were coated for 75 s (3.75 nm) with gold by a SC7620 mini sputter coater before observation. The fiber diameter and surface area were measured from the SEM images using ImageJ 1.46 image analysis software.
Thermogravimetric analysis (TGA) was performed with a Perkin Elmer TGA Pyris 1 instrument to measure the thermal stability and decomposition patterns of JNFs and CNFs. Approximately 3 mg of nanofibers were used for each measurement. The samples were heated from 30°C to 800°C at a heating rate of 10°C/min under nitrogen protection.
The X-ray diffraction patterns of as-spun nanofibers were measured by a Bruker D4 Endeavor powder X-ray diffractometer using Mo/Cu radiation source at 40 kV and 30 mA over the scanning angle range 2θ of 5°–50° at a scanning speed of 0.5°/min.
Results and discussion
Viscosity and conductivity
Viscosity and conductivity were measured to determine the suitability of the as-prepared solutions for electrospinning. The jute-TFA solutions of 4.5 wt.% and 5 wt.% were too dark due to the presence of lignin, hence the falling ball was not visible to measure their viscosity accurately. For both cotton and jute, a highly viscous solution can be obtained when dissolved in TFA due to their high molecular weight. shows that the viscosity value of polymer solutions increases with the increase in concentration for both jute and cotton. The jute-TFA solution shows a slightly higher viscosity than the cotton-TFA solution due to the presence of lignin and hemicellulose.
Table 2. Viscosity and conductivity values of jute- and cotton-TFA solutions.
The conductivity of both solutions suggests the feasibility of electrospinning (). The relationship between the concentration and conductivity is not clear as seen from . Electrospinning involves stretching of a solution caused by repulsion of charges at its surface, and more charges can be carried by the electrospinning jet if the conductivity of the solution is increased (Ramakrishna Citation2005). Hence, a small amount of salt or co-solvents can be added to increase the conductivity of the cotton-TFA and jute-TFA solutions to gain more stable electrospinning jets.
Spinnability
For cotton fiber dissolved in TFA solvent, up to 5 wt.% solution can be made. Cotton-TFA solution with the concentration of 1.5, 2, 3.5 and 5 wt.% can produce visible nanofibers through electrospinning. Difficulties were experienced during electrospinning of 2.5, 3 and 4 wt.% solutions, as no jets were found and there were no nanofibers obtained on the aluminum foil from the collector. This may be due to the low conductivity of 2.5 and 3 wt.% solution. During electrospinning of 5 wt.% solution, droplets and discontinuous jets were formed. Only 1.5, 2, 3.5 and 5 wt.% solutions could be electrospun properly with nanofibers deposited on the collector for further characterization. In both cases of JNF and CNF electrospinning, the spinning became difficult with the increase in solution concentration. This might be due to the presence of lignin in jute fiber and the increased viscosity of the jute and cotton solutions.
Chemical components
shows the FTIR spectra of dissolved cotton and jute solutions together with their resultant nanofibers. In , the spectral bands of 3499 cm−1 in cotton-TFA solution and 3131 cm−1 in jute-TFA solution are ascribed to alcoholic O-H stretching from the vibrations of the hydrogen-bonded hydroxyl group (Lakshmanan and Chakraborty Citation2017). Peaks at 1150 cm−1 and 1149 cm−1 represent C=C ring stretching bands respectively for cotton and jute solutions (Soni, Hassan, and Mahmoud Citation2015). The spectral bands of 1778 cm−1 and 1776 cm−1 are due to the absorption of the carbonyl of trifluoroacetyl group resulting from the esterification of -OH group of cellulose, hemicellulose, and lignin (Hasegawa et al. Citation1992). Absorption bands around 811 cm−1 in jute-TFA solution, 810 cm−1 and 782 cm−1 in cotton-TFA also show the presence of trifluoroacetic acid (Hasegawa et al. 1992).
Figure 2. FTIR spectra of (a) cotton-TFA and jute-TFA solutions (1.5 wt%) and (b) CNFs and JNFs with different concentrations.
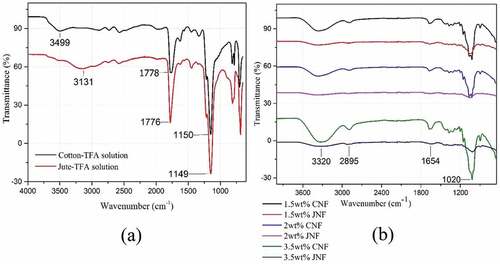
In , it can be clearly seen that strong absorption peaks appear at 3320 cm−1 and 2895 cm−1, corresponding to the O-H stretching in the carboxylic acid group and C-H stretching of cellulose, respectively (Mayandi et al. Citation2016). O ̶H bending of adsorbed water at 1654 cm−1 and C-O stretching vibration of the cellulose backbone at 1020 cm−1 are also observed (Rodrigues et al. Citation2015). The absence of peaks at 1778 cm−1, 1776 cm−1 and in the range 810–782 cm−1 clearly proves the evaporation of TFA from both CNFs and JNFs. distinctly shows no prominent peaks of lignin or hemicellulose, indicating that there are some minor differences in the chemical structure of cotton and jute nanofibers.
Morphology
shows the SEM images of JNFs and CNFs with different concentrations. The associated statistics on fiber diameter are shown in . In 1.5 wt.% JNFs, the as-collected sample shows a visible nanofibrous web with an average fiber diameter of 118 ± 27 nm, but beads can be observed occasionally. On the other hand, well-separated and web-like nanofibrous membrane with an average fiber diameter of 215 ± 43 nm can be seen from 1.5 wt.% CNFs. It was also observed that regenerated cotton is more spinnable than regenerated jute under a low concentration.
Table 3. Statistics of the diameter of JNFs and CNFs.
About 2 wt.% JNFs exhibit an even nanofibrous web with an average diameter of 123 ± 57 nm. Similarly, nanofibrous web can be seen for 2 wt.% and 3.5 wt.% CNFs with an average diameter of 178 ± 41 nm and 269 ± 82 nm, respectively. As shown in , the average diameter of JNFs is lower than that of CNFs under the same concentration. In the spinnable concentration range, e.g., 2–3.5 wt.%, uniform nanofibers can be electrospun with a relatively low standard deviation in fiber diameter, suggesting that electrospinning of regenerated jute is comparable to that of regenerated cotton.
The SEM image of 5 wt.% JNFs shows no obvious nanofibrous structure because the jet emission failed. Similarly, no visible nanofibers can be observed in the case of 5 wt.% CNFs, and this may be due to the high viscosity of the solutions. It is obvious that both solutions are not spinnable when the concentration is 5 wt.% or higher.
Thermal stability
TGA was used to characterize the decomposition rate and thermal stability of materials during controlled heating (Lakshmanan and Chakraborty Citation2017). shows the thermogravimetric (TG) and derivative thermogravimetric (DTG) curves of JNFs and CNFs under different concentrations. The JNF curves show a similar weight loss profile with four major weight loss stages in response to moisture evaporation, hemicellulose decomposition, cellulose decomposition, and lignin decomposition, respectively (Rangan et al. Citation2017). The earliest average weight loss of 3.99% due to the water evaporation occurred in JNFs between 30°C and 126°C. All tested CNFs showed an average 8.31% weight loss in the temperature range 30–126ºC due to evaporation of absorbed and intermolecular water. In the first weight loss stage, JNFs show less weight loss than that of CNFs, as seen from .
A large weight loss appears in the temperature range 210–300ºC for JNFs, and this is due to the thermal depolymerization of hemicellulose and the degradation of cellulose (which usually takes place between 275 and 400ºC) (Deepa et al. Citation2015). Lignin decomposition took place between 397 and 713ºC for all JNF samples with an average weight loss of 7.45%. The amounts of char residues at 800ºC from the three JNF samples are 19.49%, 19.20% and 16.83%, respectively. According to , a sudden weight loss of 32% in CNF samples started at around 170–210ºC and 258–270ºC due to the decomposition of hemicellulose. Cellulose decomposition occurred in the temperature range 210–415ºC with a major weight loss of around 56%. There was very little (1.17%, 0.17% and 0.66%, respectively) residue left at 800ºC. Complete pyrolysis occurred at around 560 ºC for all CNF samples.
The TGA results show that both JNFs and CNFs have excellent thermal stability. The tested JNFs show a degradation pattern like CNFs. The nanofibers can be utilized in the application areas up to 210ºC temperature before cellulose decomposition.
XRD analysis
To assess the crystalline and amorphous regions before and after electrospinning, X-ray diffraction studies were carried out for raw cotton and jute fibers and for the as spun JNFs and CNFs with different concentrations. The XRD curves are shown in and the crystallinity and amorphous percentages are statistically listed in .
Figure 5. X-ray diffraction patterns of (a) raw cotton and jute fibers; (b) 1.5, (c) 2 and (d) 3.5 wt% JNFs and CNFs.
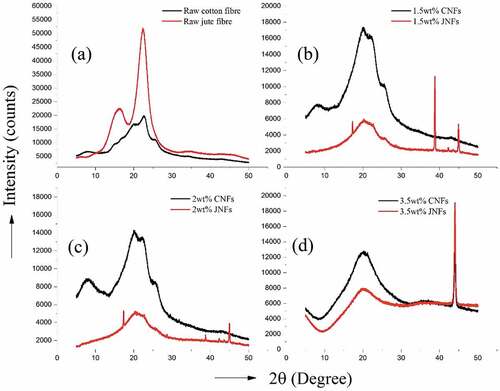
Table 4. Crystallinity index values for different tested JNFs and CNFs.
X-ray diffraction peaks were observed at 2θ = 22–23° and 15–17° for all tested samples, which are the characteristic peaks of cellulose indicating the existence of crystalline regions. Some sharp peaks at 2θ = 20.1°, 38.6°, 44.3° and 44.9°, and 44.1° represents the presence of aluminum foil in the tested sample, which is a major drawback while collecting nanofibers from aluminum foil. Due to this drawback, the results collected for the JNF and CNF samples are not sufficiently clear for comparative analysis.
Nevertheless, from the crystallinity index given in , there is an increase in crystallinity from raw cotton (57.5%) to 2 wt.% CNFs (66.3%), but a decreasing pattern can be observed from raw jute (67.8%) to 3.5 wt.% JNFs (28.6%). Regeneration of jute by dissolution in TFA may have transformed the crystalline structure from cellulose I to cellulose II with a large amount of amorphous region.
Conclusions
Nanofibers can be electrospun from both dissolved cotton and jute solution using TFA as the solvent. TFA facilitated the dissolution of cellulose and lignocellulose in jute by esterifying the cellulose, lignin, and hemicelluloses to trifluoroacetyl esters, as confirmed in the FTIR analysis. The jute-TFA solution showed a slightly higher viscosity than the cotton-TFA solution due to the presence of lignin and hemicellulose. The FTIR spectra of JNFs and CNFs showed no major differences in chemical composition between the nanofibers and their raw materials. An average diameter of 125 ± 35 nm JNFs was obtained for raw jute, whereas for cotton 220 ± 55 nm CNFs were collected. The SEM images showed no significant difference between CNFs and JNFs with a spinnable range of 1.5–3.5 wt.%, but the average diameter of JNFs was lower than that of CNFs under a given concentration. The TGA results showed that both the JNFs and CNFs have excellent thermal stability up to 210 ºC temperature before cellulose decomposition, and the JNFs showed a degradation pattern almost identical to the CNFs. The present results as obtained from this work indicate that JNFs have the potential to be applied as regenerated cellulose nanofibers with structure and properties similar to CNFs. The as-spun nanofibers from jute could find applications in several areas, such as biomedical, pharmaceuticals, electronics, barrier films, nanocomposites, membranes for water and wastewater treatment and supercapacitors.
Supplemental Material
Download MS Word (20.2 KB)Disclosure statement
No potential conflict of interest was reported by the author(s).
Supplementary material
Supplemental data for this article can be accessed online at https://doi.org/10.1080/15440478.2022.2131307
References
- Abraham, E., B. Deepa, L. A. Pothan, M. Jacob, S. Thomas, U. Cvelbar, and R. Anandjiwala. 2011. Extraction of nanocellulose fibrils from lignocellulosic fibres: A novel approach. Carbohydrate Polymers 86 (4):1468–11. doi:10.1016/j.carbpol.2011.06.034.
- Ara, Z. A., L. Wang, R. Padhye, and X. Wang. 2021. Electrospinning of lignocellulose nanofibers from dissolved jute. Journal of Natural Fibers 1–13. doi:10.1080/15440478.2021.1921662.
- Bilatto, S., J. M. Marconcini, L. H. Mattoso, and C. S. Farinas. 2020. Lignocellulose nanocrystals from sugarcane straw. Industrial Crops and Products 157:112938. doi:10.1016/j.indcrop.2020.112938.
- Deepa, B., E. Abraham, R. R. Koshy, L. A. Pothan, and S. Thomas. 2015. Extraction and characterization of cellulose nanofibers from banana plant. Handbook of Polymer Nanocomposites Processing, Performance and Application Volume C: 65–80.
- Guzman-Puyol, S., L. Ceseracciu, J. A. Heredia-Guerrero, G. C. Anyfantis, R. Cingolani, A. Athanassiou, and I. S. Bayer. 2015. Effect of trifluoroacetic acid on the properties of polyvinyl alcohol and polyvinyl alcohol–cellulose composites. Chemical Engineering Journal 277:242–51. doi:10.1016/j.cej.2015.04.092.
- Hasegawa, M., A. Isogai, F. Onabe, and M. Usuda. 1992a. 'Dissolving states of cellulose and chitosan in trifluoroacetic acid'. Journal of Applied Polymer Science 45 (10):1857–63. doi:10.1002/app.1992.070451020.
- Ilyas, R. A., S. M. Sapuan, M. R. Ishak, and E. S. Zainudin. 2018. Water transport properties of bio-nanocomposites reinforced by sugar palm (Arenga Pinnata) nanofibrillated cellulose. Journal of Advanced Research in Fluid Mechanics and Thermal Sciences 51 (2):234–46.
- Lakshmanan, A., and S. Chakraborty. 2017. Coating of silver nanoparticles on jute fibre by in situ synthesis. Cellulose 24 (3):1563–77. doi:10.1007/s10570-017-1204-2.
- Lavoine, N., and L. Bergström. 2017. Nanocellulose-based foams and aerogels: Processing, properties, and applications. Journal of Materials Chemistry A 5 (31):16105–17. doi:10.1039/C7TA02807E.
- Mahajan, Y. S., A. K. Shah, R. S. Kamath, N. V. Salve, and S. M. Mahajani. 2008. Recovery of trifluoroacetic acid from dilute aqueous solutions by reactive distillation. Separation and Purification Technology 59 (1):58–66. doi:10.1016/j.seppur.2007.05.027.
- Mayandi, K., N. Rajini, P. Pitchipoo, J. W. Jappes, and A. V. Rajulu. 2016. Extraction and characterization of new natural lignocellulosic fiber Cyperus pangorei. International Journal of Polymer Analysis and Characterization 21 (2):175–83. doi:10.1080/1023666X.2016.1132064.
- Morán, J. I., V. A. Alvarez, V. P. Cyras, and A. Vázquez. 2007. Extraction of cellulose and preparation of nanocellulose from sisal fibers. Cellulose 15 (1):149–59. doi:10.1007/s10570-007-9145-9.
- Nechyporchuk, O., M. N. Belgacem, and J. Bras. 2016. Production of cellulose nanofibrils: A review of recent advances. Industrial Crops and Products 93:2–25. doi:10.1016/j.indcrop.2016.02.016.
- Nevo, Y., N. Peer, S. Yochelis, M. Igbaria, S. Meirovitch, O. Shoseyov, and Y. Paltiel. 2015. Nano bio optically tunable composite nanocrystalline cellulose films. RSC Advances 5 (10):7713–19. doi:10.1039/C4RA11840E.
- Ohkawa, K. 2015. Nanofibers of cellulose and its derivatives fabricated using direct electrospinning. Molecules 20 (5):9139–54. doi:10.3390/molecules20059139.
- Ohkawa, K., S. Hayashi, A. Nishida, H. Yamamoto, and J. Ducreux. 2009. Preparation of pure cellulose nanofiber via electrospinning. Textile Research Journal 79 (15):1396–401.
- Ramakrishna, S., K. Fujihara, W.-E. Teo, T.-C. Lim, and Z. Ma. 2005. An Introduction to Electrospinning and Nanofibers, 9812564152. World Scientific.
- Rangan, A., M.V. Manchiganti, R.M. Thilaividankan, S.G. Kestur, and R. Menon. 2017. 'Novel method for the preparation of lignin-rich nanoparticles from lignocellulosic fibers'. Industrial Crops and Products 103:152–60. doi:10.1016/j.indcrop.2017.03.037.
- Rodrigues, B. V. M., E. C. Ramires, R. P. O. Santos, and E. Frollini. 2015. Ultrathin and nanofibers via room temperature electrospinning from trifluoroacetic acid solutions of untreated lignocellulosic sisal fiber or sisal pulp. Journal of Applied Polymer Science 132 (16):41826. doi:10.1002/app.41826.
- Santos, R. P. O., B. V. M. Rodrigues, E. C. Ramires, A. C. Ruvolo-Filho, and E. Frollini. 2015. Bio-based materials from the electrospinning of lignocellulosic sisal fibers and recycled PET. Industrial Crops and Products 72:69–76. doi:10.1016/j.indcrop.2015.01.024.
- Siqueira, G., J. Bras, and A. Dufresne. 2010. Cellulosic bionanocomposites: A review of preparation, properties and applications. Polymers 2 (4):728–65. doi:10.3390/polym2040728.
- Soni, B., E. B. Hassan, and B. Mahmoud. 2015. Chemical isolation and characterization of different cellulose nanofibers from cotton stalks. Carbohydrate Polymmers 134:581–89. doi:10.1016/j.carbpol.2015.08.031.
- Šturcová, A., G. R. Davies, and S. J. Eichhorn. 2005. Elastic modulus and stress-transfer properties of tunicate cellulose whiskers. Biomacromolecules 6 (2):1055–61. doi:10.1021/bm049291k.
- Thomas, M. G., E. Abraham, P. Jyotishkumar, H. J. Maria, L. A. Pothen, and S. Thomas. 2015. Nanocelluloses from jute fibers and their nanocomposites with natural rubber: Preparation and characterization. International Journal of Biological Macromolecules 81:768–77. doi:10.1016/j.ijbiomac.2015.08.053.
- Tian, H., and J. He. 2016. Cellulose as a scaffold for self-assembly: From basic research to real applications. Langmuir 32 (47):12269–82. doi:10.1021/acs.langmuir.6b02033.
- Trache, D., M. H. Hussin, M. K. Haafiz, and V. K. Thakur. 2017. Recent progress in cellulose nanocrystals: Sources and production. Nanoscale 9 (5):1763–86. doi:10.1039/C6NR09494E.
- Trilokesh, C., and K. B. Uppuluri. 2019. Isolation and characterization of cellulose nanocrystals from jackfruit peel. Scientific Reports 9 (1):16709. doi:10.1038/s41598-019-53412-x.
- Uthandi, S., S. Marimuthu, and J. Tilak. 2019. Bacterial cellulose dissolution for high-value nano fibre application. Madras Agricultural Journal 106 (Spl.):199–204.
- Wang, W.-M., Z.-S. Cai, and Y. J-Y. 2008. 'Study on the chemical modification process of jute fiber'. Journal of Engineered Fibers and Fabrics 3 (2).
- Wang, X., H. Niu, T. Lin, and X. Wang. 2009. 'Needleless electrospinning of nanofibers with a conical wire coil'. Polymer Engineering & Science 49 (8):1582–86.