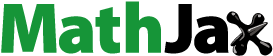
ABSTRACT
With the increase in environmental pollution, studies on the use of sustainable resources are increasing day by day. For this purpose, the use of natural fiber-reinforced polymer composites is encouraged in many areas such as automotive, transportation, construction, and home textiles. However, they are flammable and therefore seriously threaten the safety of people and property. Various flame retardant additives have been used to improve the flame retardancy properties of these composites. In this study, silicon dioxide (SD) and zinc borate (ZB) microparticles in different weight percentages (3, 5, 7, and 10%) were reinforced to give flame retardant properties to jute-epoxy composites. In addition, composites containing both SD and ZB microparticles were produced and they were labeled as HB. Then, thermal conductivity, flammability, water absorption, and mechanical properties of these composites were investigated. The burning rate of the composites decreased as the amount of microparticle increased. 5ZB5SD, including %5 SD and %5 SD microparticles, showed 36.60% less burning rate than the neat jute-epoxy composite. 5ZB showed 10.84% higher tensile strength than the neat jute-epoxy. The impact strength of the specimens increased with the increase in the filling ratio, and 5ZB5SD showed approximately 2.50 times the impact strength of the jute-epoxy composite.
摘要
随着环境污染的加剧,对可持续资源利用的研究日益增多. 为此,鼓励在汽车、交通、建筑和家纺等许多领域使用天然纤维增强聚合物复合材料. 然而,它们是易燃的,因此严重威胁人身和财产的安全. 各种阻燃添加剂已被用于改善这些复合材料的阻燃性能. 在本研究中,以不同重量百分比(3、5、7和10%)增强二氧化硅(SD)和硼酸锌(ZB)微粒,使黄麻环氧复合材料具有阻燃性能. 此外,还生产了含有SD和ZB微粒的复合材料,并将其标记为HB. 然后,研究了这些复合材料的导热性、可燃性、吸水性和力学性能. 随着微粒数量的增加,复合材料的燃烧速率降低。5ZB5SD,包括%5SD和%5SD微粒,比纯黄麻环氧复合材料的燃烧率低36.60%. 5ZB的拉伸强度比纯黄麻环氧树脂高10.84%. 试样的冲击强度随着填充率的增加而增加,5ZB5SD的冲击强度约为黄麻环氧复合材料的2.50倍.
Introduction
Today, while environmental pollution has increased tremendously, most sectors have been turning to products obtained from sustainable natural resources. For this purpose, it is seen that natural fibers have been used intensively as reinforcement elements due to superior properties such as low cost, ecofriendly nature, fewer health hazards, and low density in composite studies conducted in recent years (Kumar et al. Citation2022; Neto et al. Citation2022; Sajin et al. Citation2022Citation2022). Jute fiber, which has a light brown color, is one of the most widely used natural fibers because it is relatively cheaper and commercially accessible. It has high tensile strength but low flexibility (Suresha, Guggare, and Raghavendra Citation2016). Also, these fibers have a relatively lower density and higher strength than plastic (Gowda, Naidu, and Chhaya Citation1999). Materials having a heat transmission coefficient value of less than 0.065W/mK are defined as thermal insulation materials according to ISO and CEN standards (Kulaksızoğlu Citation2006). Since the thermal conductivity coefficient of jute fiber is between 0.038–0.040 W/mK, it can also be used as an insulation material (Ghosh et al. Citation2016). Jute fibers are used as reinforcement elements in polymer composites due to their superior properties. Substances such as lignin and hemicellulose on the surfaces of natural fibers restrict the OH groups of the fibers from reacting with the polymer matrix (Gogna et al. Citation2019). That’s why jute reinforced polymer composites have relatively weak interfacial bonding between fiber and matrix. So, surface treatments are generally applied to the fibers to provide better adhesion and improve interfacial bonding (E. Kapatel Citation2021; Owen Citation2014; Sinha and Rout Citation2009). The surface improvement methods on natural fibers are generally applied in three different ways: physical, physico-chemical, and chemical. Natural fibers are chemically treated to remove lignin, pectin, waxy substances, and natural oils that coat the outer surface of the fiber cell wall (Sanjay and Yogesha Citation2017). These processes include alkalization (Santulli Citation2007), acetylation (Sanjay and Yogesha Citation2017), silane, isocyanate, titanium-based compounds (John and Anandjiwala Citation2008), benzoylation, peroxide, sodium chloride, and permanganate treatment (Kabir et al. Citation2012). When the coir fiber was exposed to chemical treatment with 5% NaOH solution for 1 hour, the tensile strength increased by 17.8% and the flexural strength increased by 16.7% (Yan et al. Citation2016). In the study carried out by Amjad et al., composites produced with alkali-treated jute showed higher compression and interlaminar shear properties (Amjad, Anjang Ab Rahman, and Shukur Zainol Abidin Citation2022). In a similar study, the interfacial adhesion between jute and polypropylene was improved with 4% NaOH treatment (Karaduman et al. Citation2014). It was observed that the impurities on the banana fiber were removed with acetylation of 2-4-6-8-10% for 4 hours (Kivade et al. Citation2022). Composites were produced with jute and coil fibers treated with NaOH at different concentrations (2–8%), and the best mechanical properties were observed in a 2% NaOH-treated composite (Hai, Kim, and Lee Citation2009). As can be seen from the above studies, alkali treatment significantly affects both the mechanical and thermal properties of composites as it easily removes organic contents such as lignin and cellulose in natural fibers (Parkunam, Ramesh, and Saravanakumar Citation2022). However, over-treatment of the natural fibers can also cause a decrease in strength by breaking the fiber bonds (Symington et al. Citation2009).
Natural fibers have low fire resistance. So, in natural fiber-reinforced polymer composites, flame retardants are used to improve the fire properties of the composites. The flame retardants aim to increase the ignition resistance and reduce the spread of flame. Nitrogen, phosphorus, halogens, and inorganic flame retardants are used to impart flame retardant properties to materials (Bachtiar et al. Citation2019; Shi et al. Citation2022). The most widely used flame retardant microparticles in natural fiber reinforced polymer composites are nanoclays (Delhom, White-Ghoorahoo, and Pang Citation2010), magnesium hydroxide (Sain et al. Citation2004), ammonium polyphosphate, alumina trihydrate (Khalili et al. Citation2019) and so on. In this study, zinc borate (ZB) and silicon dioxide (SD) microparticles with flame retardant property were used. Zinc borate becomes more advantageous than other flame retardants because they produce less smoke and maintain their stability up to high temperatures, as well as show the most effective results in terms of price/efficiency ratio (Yüce Citation2009). If we look at the studies on the effect of ZB reinforcement on the flame retardancy, mechanical properties, and thermal properties of composites: Kristina and coworkers (2010) investigated the smoke suppressant and fire properties of zinc-based fillers in epoxy. They found that zinc borate and zinc hydroxystannate reduced heat release and heat release capacity (Formicola et al. Citation2011). Durrani and co-workers (2020) investigated the fire behavior of cellulosic fabric using zinc borate particles. Zinc borate-cotton fabric showed a lower heat release than untreated cotton (Durrani et al. Citation2020). In another study, aerogel with waste cotton fabric-zinc borate was produced. They stated that ZB improved the mechanical properties, thermal stability, flame retardancy, and even self-extinguishing ability of the aerogel (Qin et al. Citation2020). In another study, zinc borate, zinc borate/ammonium polyphosphate (ZB/APP), and zinc borate/aluminum trihydrate (ZB/ATH) in different weight percentages (5, 10, 15%) were used as a reinforcing elements. They stated that composite specimens containing 10% APP and 5% ZB showed the highest flame retardant effect (Khalili et al. Citation2019). Another material having flame retardant properties used in this study is silicon dioxide (SD), which consists of oxygen and silica atoms (SiO2) (Ateşer Citation2010). When SD is used as a filler material, properties such as strength and modulus, sound insulation, vibration damping ability, abrasion resistance, chemical resistance, thermal expansion coefficient, thermal conductivity and dielectric constant of composites can be improved (Sinha et al. Citation2020; Yadav et al. Citation2021;Sinha et al., Citation2020; CitationJiao and Chen Citation2011). It also can provide high toughness and strength to the composite (Qian, Zhou, and Chen Citation2018). Yi et al. investigated the flame retardant properties of double-layered hydroxides and nanosilicon dioxides in EVA. They found that composites containing silicon dioxide had a higher LOI value. They also determined that they have reducing effects on the heat release rate, total heat release, mass loss, smoke production rate, and total smoke release (Qian, Zhou, and Chen Citation2018). Pan and co-workers produced wood fiber/PE composites using nano silicon dioxide at different weight percentages (2, 4, 6, 8 and 10%). Composite produced with 8% SD has the lowest heat release rate (Mingzhu, Hailan, and Changtong Citation2013).
In the literature, there are studies in which various flame retardant additives are added to natural fiber reinforced polymer composites to provide flame retardant properties (Azad et al. Citation2022; George et al. Citation2022; Parkunam, Ramesh, and Saravanakumar Citation2022; Shi et al. Citation2022). However, no study was found in which zinc borate and/or silicon dioxide fillers were used to achieve flame retardant properties to jute fiber-epoxy composites. Therefore, this study aimed to investigate flammability, mechanical and thermal properties of jute/epoxy composite by using zinc borate and silicon dioxide microparticles. Laminated jute-epoxy composites containing different weight percentages of zinc borate (3, 5, 7, 10%) and silicon dioxide (3, 5, 7, 10%) microparticles were produced using the vacuum infusion method. The composites containing hybrid microparticles (both zinc borate and silicon dioxide) were also produced. Then, thermal conductivity, flammability (horizontal burning), water absorption, and mechanical tests were performed on each composite specimen and the results were evaluated. After the mechanical tests, the fracture surfaces of the composite specimens were investigated by Scanning Electron Microscopy (SEM) and fiber pull-out, debonding, matrix cracks, fiber breakage, and failures were observed.
Materials and methods
Materials
340 g/m2 plain woven jute fabric was purchased from RNGROUP (Turkey). The density and thickness of jute fabric are 1.68 g/cm3 and 0.96 mm, respectively. Zinc borate (ZB) was supplied from Melos Kimya (Turkey). The average particle diameter of ZB is 3.2 μm. Silicon dioxide (SD) microparticles (10 μm) were bought from Nanokar (Turkey). D.T.E 1200 epoxy and D.T.S 1151 hardener were purchased from Duratek (Turkey). For surface treatment processes, sodium hydroxide (NaOH) and acetic acid were purchased from Alev Kimya. The materials (wax, peel ply, flow mesh, vacuum bagging, sealant tape) required for the vacuum infusion process were provided by SAZCILAR A.S.
Surface treatment of jute fabrics
In this study, alkalization, which is one of the most common methods, was used to improve the fiber surface and increase the interfacial bond strength between fiber and matrix as well as the mechanical and thermal properties of the composite. The alkalization treatment was carried out according to the articles (Ray and Sarkar Citation2001), (Yadav Citation2013) and (Hai, Kim, and Lee Citation2009). First, the plain woven jute fabric was soaked in 2% NaOH solution () and waited for 3 hours (). 3 hours later, the jute fabric was removed from the solution and washed 4–5 times with distilled water (). Then, 2% acetic acid solution () was prepared and the jute fabric was soaked in this solution (). The steps here proceeded as in the NaOH treatment. After 3 hours, washing was continued with distilled water until the PH of the fabric was about 7 (). Finally, the neutralized jute fabric was laid on a suitable surface (smooth surface such as glass) and dried (). In this process, the fibers were not exposed to direct sunlight.
Figure 1. Demonstration of surface treatment steps of jute fabric: (a) preparation of 2% NaOH solution, (b) soaking the jute fabric in the NaOH solution, (c) washing process, (d) preparation of 2% acedic acid solution, (e) soaking the jute fabric in the acetic acid solution, (f) measure pH value, (g) drying process.
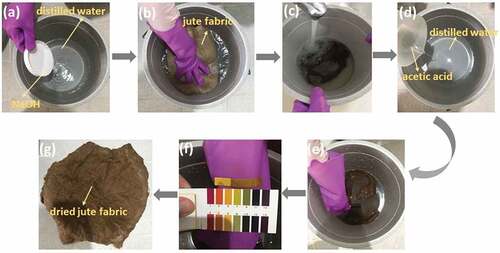
Preparation of resin containing microparticles
In this step, it was aimed to mix the microparticles with the epoxy homogeneously without clumping (agglomeration). By weight 3%, 5%, 7% and 10% zinc borate, 3%, 5%, 7% and 10% silicon dioxide and 1.5–1.5%, 2.5–2.5%, 3.5–3.5%, 5–5% zinc borate/silicon dioxide hybrid fillers were added to the epoxy resin and mixed with the help of a hand mixer until a homogeneous distribution was formed. In other words, a total of 12 different microparticle-epoxy mixtures were obtained. The amount of microparticles in epoxy was calculated by taking 3, 5, 7 and 10% of the weight of jute fiber used in composite production. These rates were determined by considering the studies in the literature.
Production of laminated hybrid composites
Composite specimens were produced using the vacuum infusion method. In this method, first of all, liquid wax was applied on the glass of approximately 70 × 70 cm2, which allows the sample to be easily separated from the glass. Then, the jute fabrics cut in approximately 45 × 45 cm2 dimensions were placed on top of each other in 3 layers (). After placing the peel-ply and flow mesh on the top of the fabric, the sample was closed with a vacuum bagging with the help of sealant tape (). Before starting the vacuum, that is, impregnating the resin, the microparticle and epoxy mixture prepared (section 2.3). After this step, epoxy was mixed with hardener in the specified ratio (79:21). Then, jute fabrics were wetted with microparticle reinforced-epoxy by applying a vacuum of 400 mm/H (). After complete wetting, the specimen was wait to cure at room conditions for 1 day and in an oven at 80°C for 2–3 hours. Then the cured material was removed from the mold (). The composites produced contain 30% jute fiber by weight. The reason for choosing this ratio is that it is observed jute fibers are well wetted with epoxy during production by vacuum infusion method. When higher fiber content (40%) was used, voids and pores were observed in the composite. The weight percentages of zinc borate and silicon dioxide in the produced composites are indicated by numbers in front of the words “ZB” and “SD,” respectively. For example: 3ZB for 3% zinc borate containing composite, 3SD for 3% silicon dioxide containing composite and 1.5ZB1.5SD for hybrid composite (HB) containing 1.5% zinc borate and 1.5% silicon dioxide. The names of the composite specimens produced are: N, 3ZB, 5ZB, 7ZB, 10ZB, 3SD, 5SD, 7SD, 10SD, 1.5ZB1.5SD, 2.5 ZB2.5SD, 3.5ZB3.5SD.
Test procedure
Fourier transform infrared spectroscopy measurement (FTIR)
The IR spectra of raw and treated jute fibers were performed using a Thermo Fisher Nicolet IS50 Fourier Transform Infrared (FTIR) spectrometer. These measurements were conducted between a wavelength range of 4000–400 cm −1.
Thermal conductivity test
The thermal conductivity test was carried out according to ASTM C518–15 (ASTM Citation2017) and the specimen dimensions were adjusted to be 30 × 30 cm2. The upper and lower plate temperatures are 10°C and 30°C. The specimen to be measured was placed between the two plates and controlled to heat flow from hot to cold plate, which was measured by the transducers. The thermal conductivity was calculated with the help of EquationEquation (1)(2)
(2) .
λ= S. E. (L/∆T)(1)
Where λ, S, E, L and ΔT indicate thermal conductivity (W/(mK)), calibration factor ((W/m2)/V), heat flux transducer output (V), separation between the hot and cold plate (m) and temperature difference (K), respectively.
Flammability test (horizontal burning)
The flammability test of composite specimens was carried out horizontally according to UL-94 standard using a fire test cabin. Test specimens were cut length of 125 mm and width of 13 mm. Each specimen was marked with two lines 25 ± 1 mm and 100 ± 1 mm from the tip to be ignited and was fixed in the horizontal position with the help of a clamp. A flame having a length of 20 mm was applied (30 seconds) to one end of the sample with a Bunsen burner at an angle of 45° as shown . After the flame was extinguished, the length of the burned area was measured. The burning rate was calculated with the help of Equation (2). The tests were repeated 5 times for the composite specimens in each set and the average was taken. The setup is shown in .
Where V, L, and t indicate linear burning rate (mm/min), damaged length (mm), and times (second), respectively.
Water absorption test
Natural fiber-reinforced polymer composites absorb moisture in a humid environment or when immersed in water. Moisture absorption causes deterioration of the fiber-matrix interface area, resulting in low-stress transfer efficiency and a loss in mechanical characteristics (Gupta and Srivastava Citation2016). Water absorption tests of layered composites were performed according to ASTM D 570–98 (ASTM Citation2006) standard using SR 13-C device. Dimensions of specimens were 76.2x25.4 mm2. Firstly, the samples were dried at 50 ± 3°C for 24 hours, cooled in a desiccator and weighed. The conditioned specimens are placed in a container of distilled water maintained at a temperature of 23 ± 1°C, and entirely immersed. At the end of 2 hours, the specimen was wiped with a dry cloth and weighed immediately. After being weighed specimens were placed in the water again. This step was repeated end of 24, 48, 72, and 96 hours, and values of weight were recorded. For each set, 3 repetitive tests were performed and the average was taken. The water absorption ratio was calculated with the help of Equation (3):
Where W is the water absorption ratio (%), w1 is the weight of the specimen before the test (g) and w2 is the weight of the specimen after the test (g).
Mechanical tests
The tensile test was realized according to ASTM D 3039 (-ASTM Citation2017) and the specimen dimensions were 250 × 25 mm2. The distance between the jaws, test speed, and device capacity were 200 mm and 2 mm/min and 20 kN, respectively. The flexural test was conducted according to EN ISO 14125 (ISO Citation1998) and the specimen dimensions (length and wide) and the distance between the supports were adjusted by calculating from the standard according to the thickness of the specimens. The test speed was applied as 2 mm/min. The impact test was applied to the sample from the front side according to the ISO 179–1 (ISO Citation2010) standard and the specimen dimensions were determined by calculating the thickness from the formulas in the standard. For this test, Devotrans CD-I device from the SAZCILAR AŞ company was used. The mechanical tests were repeated at least 3 times for the composite samples in each set and the average was taken.
Morphology characterization
Morphological analysis of the fracture surfaces after the tensile test was performed using a Carl Zeiss Gemini 300 scanning electron microscope (SEM) at 5 kV accelerating voltage. Before scanning, the surfaces to be observed were coated with a thin layer of gold/palladium to make the samples conductive and prevent electrostatic charging.
Results and discussion
Fourier transform infrared spectroscopy
To see the effect of alkalization treatment on the surface of the jute fabric, FTIR analyses of both raw and treated jute fibers were performed. shows the FTIR spectra of untreated jute and alkalized jute. The bond seen at 3339.48 cm−1 in the spectrum of raw jute is attributed to the O-H stretching vibration (Seki Citation2009; Silva et al. Citation2016). This stretching can be caused by absorbing water or by alcohols present in cellulose, lignin, and hemicellulose (Gopal et al. Citation1985). It is seen that this band decreases to 3331.80 cm−1 in the alkali-treated fibers. The band resulting from the C-H stretching vibration found in cellulose and hemicellulose is observed at 2916.07 cm−1 (Ray and Sarkar Citation2001). A decrease was observed in this peak (2895.88 cm−1) after alkali treatment and it was stated by Seki that this could be due to weak attractions (Seki Citation2009). The band resulting from the axial deformation of C=O was observed at 1731.89 cm−1 in the raw jute. In the studies in the literature, it has been stated that this bond cannot be seen after the alkalization process (R. Ahmed et al. Citation2014; E. Kumar et al. Citation2020; A. S. Sinha and Rout Citation2009). In the FTIR results are examined, it is seen that hemicellulose and lignin were partially removed from the jute fiber and the alkalization process was successfully carried out.
Thermal conductivity test results
Thermal conductivity values of microparticles (SD/ZB/HB) reinforced jute-epoxy composites are given . Among the ZB reinforced composites, the thermal conductivity of composites increased by increasing microparticle content and 7ZB showed the highest conductivity with a value of 0.0506 W/mK. This value is approximately 38.63% higher than the thermal conductivity value of N coded sample. However, 10% ZB reinforced composite showed a slightly lower conductivity value (0.0482 W/mK) than 7% ZB reinforced composite. The thermal conductivity of the jute-epoxy composite increased from 0.0365 W/mK to 0.0512 W/mK with %5 SD particle reinforcement. A slight decrease was observed in the conductivity value of the specimens in which the microparticle reinforcement ratio was increased to 7% and 10% by weight. In composite samples containing both SD and ZB microparticles, the highest thermal conductivity was measured as 0.0505 in the 1.5SD1.5 ZB. In composite specimens (2.5SD2.5 ZB, 3.5SD3.5 ZB, 5SD5ZB) containing reinforcement above 3% reinforcement ratio, a decrease in conductivity value was observed with the increase of reinforcement ratio. 2.5SD2.5ZB, 3.5SD3.5ZB and 5SD5ZB showed thermal conductivity values of 0.0458 W/mK, 0.0437 W/mK and 0.0407 W/mK, respectively.
Figure 5. Thermal conductivity results of (a) ZB, (b) SD and (c) HB microparticles reinforced jute/epoxy composite specimens.
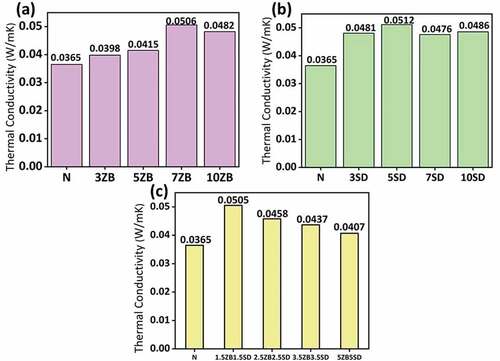
In literature studies, it is seen that thermal conductivity decreases with increasing the percentage of natural fibers in polymer matrix composites (Devireddy and Biswas Citation2016; Pujari, Ramakrishna, and Tulasi Balaram Padal Citation2017; Zakriya et al. Citation2017). Since the ratio of jute fabric was kept constant in the produced composite specimens, a linear increase or decrease was not observed in the thermal conductivity values. The thermal conductivity of polymer composites depends on many factors such as the shape and size of the added particles, aspect ratio, diameter, distribution of particles in the matrix, interface, and percentage of reinforcement loading (Burger et al. Citation2016). The conductivity values of SD and ZB microparticle reinforced composites increased up to a point and then decreased slightly. The reason for this decrease is the decrease in the homogeneous distribution of the particles with the increasing percentage amount. Similarly, in the study conducted by Evseeva and Tanaeva, nanomaterials in different weight percentages were added to the epoxy and the thermal conductivity value increased up to a certain percentage, while the conductivity value decreased with the further increase in the amount of additive. This decrease was explained by the worsening of the dispersion of the additive in the epoxy at higher concentrations (Evseeva and Tanaeva Citation2008). In HB reinforced composites, on the other hand, when the reinforcement ratio exceeded 3%, a more significant decrease was observed in the thermal conductivity value compared to the other samples. The reason for this is thought to be due to the heterogeneous structure of the composites containing ZB and SD microparticles of different sizes (3.2 μm and 10 μm) and the epoxy and microparticle interface. A material to be used as a thermal insulation material, the heat transmission coefficient value must be less than 0.065 W/mK according to ISO and CEN standards (Kulaksızoğlu Citation2006). SD and ZB particles reinforced as flame retardant did not compromise the thermal insulation performance of the composites, and thermal conductivity values lower than 0.065W/mK were obtained in all specimens.
Flammability test (horizontal burning) results
Flammability test results of composite specimens are summarized in . Jute/epoxy composite without microparticles was used as a control sample. According to the test results, it was observed that the burning rate decreased with the increase in the amount of microparticles in ZB, SD and HB reinforced composite sets. This decrease is clearly seen in the graph given in , and images of 5% micro particle reinforced composite specimens (5ZB, 5SD and 2.5 ZB2.5SD) after the flammability test are also given. The 10ZB, 10SD specimens showed 31.57% and 26.44% less burning rate than the jute epoxy composite (N), respectively. 5ZB5SD showed the best (lowest) burning rate among all specimens and the burning rate of these composite reached 18.17 mm/min. It was also stated by Ribeiro et al. that polymer composites produced using hybrid flame retardant showed better non-flammability characteristics than composites produced with a single flame retardant (Ribeiro, Sousa, and Nóvoa Citation2015). Similarly, there are studies in the literature in which zinc borate and silicon dioxide improve the flame retardant properties of polymer composites (Khalili et al. Citation2019; Suppakarn and Jarukumjorn Citation2009; Yurddaskal and Celik Citation2018).
Figure 6. Flammability test results of (a) ZB, (b) SD and (c) HB microparticles reinforced jute/epoxy composite specimens.
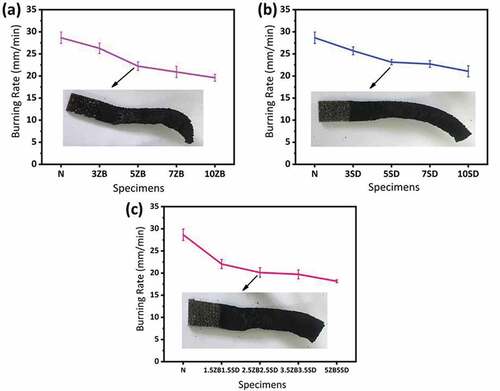
Table 1. Flammability test results of composite specimes.
Water absorption behaviour
shows water absorption values for microparticle-reinforced jute/epoxy hybrid composite specimens. It was observed that the water absorption curve increased with the increase in immersion time of the sample. The percentage water absorption of composites N, 10ZB, 10SD and 5ZB5SD are found 6.81, 6.15, 7.27 and 8.75, respectively at the end of 96 hours. 7ZB (7% zinc borate microparticles reinforced jute/epoxy) composite shows the lowest water absorption value (5.72%), 5ZB5SD (10% zinc borate/silicon dioxide hybrid microparticles added jute/epoxy) composite shows the highest water absorption value (8.75%). Similar results are seen in the studies of the water absorption property of natural fiber composites. Nath et al. showed that the water absorption behavior of the natural fiber-reinforced polymer composites was directly proportional to the immersion time. Since the cellulose in natural fibers absorbs moisture, the water absorption amount of composites increases with increasing immersion time (Ankush et al. Citation2021; Nath et al. Citation2019). In another study, it was declared that zinc borate could dissolve during the water absorption test and create microvoids in the composite, which could increase the moisture absorption rate of the composite (Yeh et al. Citation2021). In another study, different weight percentages (0–15 wt.%) of silicon carbide were added to the jute-epoxy matrix composites and the effects of the amount of additive on the water absorption properties of the composites were investigated. The water absorption of jute epoxy composites increases with increasing the silicon carbide filler content. This increase is explained by two important factors: the composite contains more voids with the increase in the amount of silicon carbide, and the jute fiber has a hydroxyl group that absorbs moisture from the environment (Patnaik and Nayak Citation2018; Pavlidou, Krassa, and Papaspyrides Citation2005).
Mechanical test results
Tensile, flexural, and impact test results of composite specimens are summarized in , and images of composite specimens containing 5% zinc borate after these tests are given in . In tensile test results, it was observed that the ultimate tensile strength of ZB reinforced composites increased up to 5% with the increase in the filler ratio, and when this ratio was exceeded the ultimate tensile strength decreased (). It was found that the tensile strength of the unfilled jute/epoxy composite (N) increased by 10.84% with the addition of 5% by weight ZB fillers (5ZB). In SD-reinforced composite specimens, the composite containing 3% by weight SD showed approximately 4.85% higher ultimate tensile strength than the jute-epoxy composite. A decrease in tensile strength was observed when the 3% microparticle filler ratio was exceeded. In HB-reinforced composite specimens, 1.5ZB1.5SD, 2.5ZB2.5SD and 3.5ZB3.5SD specimens showed close tensile strength values to each other. These values are 37.83, 37.90 and 37.98, respectively. While the highest tensile strength was seen in 3.5ZB3.5SD, with increasing the amount of reinforcement, the tensile strength decreased and the sample coded 5ZB5SD showed approximately 3.50% less strength than 3.5ZB3.5SD.
Figure 8. Images of composite specimens containing 5% zinc borate (ZB), after the (a) tensile, (b) flexural and (c) impact test.
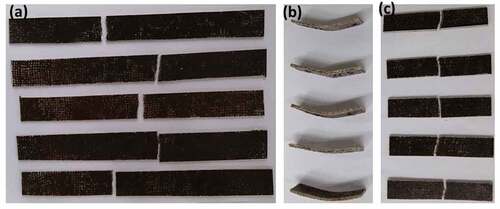
Figure 9. Tensile strength values of (a) ZB, (b) SD and (c) HB microparticles reinforced jute/epoxy composite specimens.
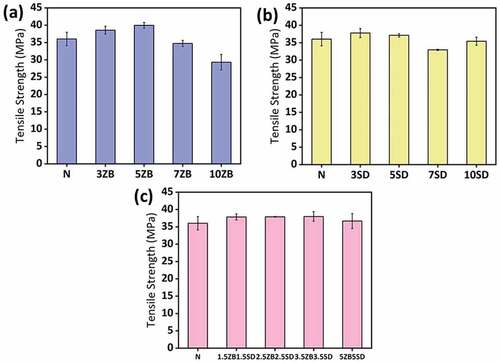
Table 2. Mechanical test results of microparticle reinforced jute-epoxy laminated composite specimens.
In particle-reinforced composites, one of the most important factors affecting the mechanical properties of the composite is the interfacial bonding between the matrix and the reinforcement element (Ahmed, Mallinatha, and Amith Citation2011; Gwon et al. Citation2010). Weak interfacial bonding causes the tensile strength of the composite to decrease, while strong interfacial bonding increases the tensile strength and toughness of the composite (S. Ahmed and Jones Citation1990; Rong et al. Citation2001). In this study, similar situations were observed in all of the SD, ZB and HB particle reinforced composite specimens. According to this, the tensile strength of the composite specimens increased up to a certain percentage of microparticle (%wt.), and after this rate was exceeded, a decrease was observed in the tensile strength. Similar results were observed in the study by Sushil et al. (Singh, Kumar, and Jain Citation2018). At a high rate of fillers, the weak interfacial bonding between the epoxy matrix and the reinforcement may have caused a decrease in tensile strength. In addition, the use of high micro-filler content during composite production (vacuum infusion method) caused the flow to be more viscous, which made it difficult to distribute the particles homogeneously in the epoxy. Agglomeration can lead to porosity and voids, which adversely affects the mechanical properties of composites (Asi Citation2009).
Flexural test results of composite specimens are given . In ZB reinforced composites, 10% ZB reinforced composite (10ZB) showed the highest flexural strength, and this value was 3.92% higher than the jute-epoxy composite (N). Among the composite specimens containing SD particles, 5SD showed the highest flexural strength with a value of 102.67 MPa. This value is 15.11% higher than jute-epoxy composite. The flexural strength of the composites decreased by increasing the amount of microparticle reinforcement above 5%. While similar behavior was observed in HB reinforced composites compared to SD reinforced composites, 2.5ZB2.5SD showed the highest flexural strength (97.20 MPa) and when the filler ratio exceeded 5%, the flexural strength of the composites decreased. During the flexural test, more than one mechanism such as tensile, compression and slip occur simultaneously. The reason for the decrease in flexural strength in SD and HB reinforced composites after 5 wt% is the shear failure (K. S. Ahmed, Mallinatha, and Amith Citation2011; Asi Citation2009).
Figure 10. Flexural strength values of (a) ZB, (b) SD and (c) HB microparticles reinforced jute/epoxy composite specimens.
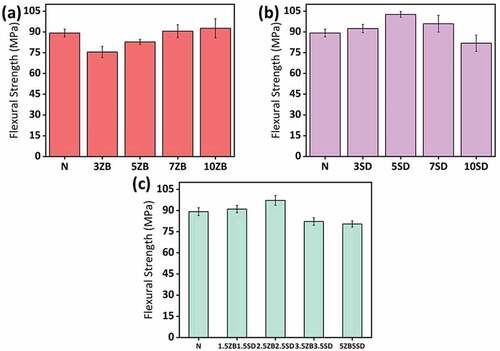
The impact strength of composite materials is affected by many factors such as the toughness of the constituent materials, the matrix fiber interface bonding, the type and size of the fillers (Ejaz et al. Citation2020; Jawaid, Abdul Khalil, and Abu Bakar Citation2010). shows the impact test results of composite specimens. It is clearly seen that the impact strength increases as the amount of micro particle filler increases in all of the SD, ZB and HB reinforced composites. When the composite material is subjected to impact load, sudden crack propagation occurs in the material. In particle-reinforced composites, the particles show resistance to crack propagation and more energy is absorbed by the materials (S. Ahmed and Jones Citation1990; K. S. Ahmed, Mallinatha, and Amith Citation2011). In this study, the increase in impact strength as the amount of filler increases, is consistent with this theory. The 10ZB, 10SD and 5ZB5SD composite specimens showed approximately 1.80, 2.20 and 2.50 times the impact strength of the jute-epoxy composite (N), respectively. It was observed that SD-reinforced composites showed higher impact strength than ZB-reinforced composites. The reason for this is thought to be related to the particle sizes. Silicon dioxide showed higher strength due to its larger particle size than zinc borate. Also, HB reinforced composites showed higher strength than both SD and ZB-reinforced composites. 10 HB composite samples showed an impact strength value of 16.94 kJ/m2 (the highest in among all samples). The amount of energy required to break the composite has been increased by adding hybrid microparticles to the jute-epoxy composite (Ejaz et al. Citation2020, Citation2022; Mutalikdesai et al. Citation2018).
Morphology characterization
The composite specimens subjected to tensile test are examined using SEM, and images of fracture surfaces are shown in (Neat, 5ZB and 10ZB). Common failures seen in fiber reinforced polymer composites under tensile loading are fiber breakage, fiber pull-out, delamination, debonding and matrix cracking (Ejaz et al. Citation2022; Yuksel Yilmaz, Yunus, and Celik Bedeloglu 2022). Fiber breakage, matrix cracking and debonding failures were observed in the produced samples. The absence of delamination between the layers indicates that there is a good interfacial bonding between the jute fabric and epoxy. The fiber breakage and matrix cracking in shows a relatively poor interfacial bonding between jute and epoxy composites. It is seen that with the addition of 5% by weight of zinc borate to the jute-epoxy composite, the jute fibers are better covered (wetted) by the epoxy (). The minimum fiber pull-out failure in 5ZB coded composites is another factor that shows a good interfacial adhesion (Amjad, Anjang Ab Rahman, and Shukur Zainol Abidin Citation2022). A good interfacial bonding contributes to the transfer of load from the epoxy to the jute fiber, which results in higher tensile strength of the composite. The presence of zinc borate agglomerations was clearly observed in the composite sample containing 10% zinc borate (). ZB agglomerations create stress concentration zones and these zones reduce the interfacial bonding between epoxy and jute fiber (Abdi, Eslami-Farsani, and Khosravi Citation2018; Feiz and Khosravi Citation2019) In similar studies, it was stated that agglomeration was observed with increasing the amount of particles added into the polymer matrix (Amjad, Anjang Ab Rahman, and Shukur Zainol Abidin Citation2022; Balakrishnan, Krishnaraj, and Raajeshkrishna Citation2019). The weakening of the interfacial bond can also be seen in with the failure of debonding. The voids, fiber breakage, agglomeration, fiber pull-out, and debonding failures that were seen in the 10ZB coded sample decreased the tensile strength of the composite (Sumesh and Kanthavel Citation2019; Zaer-Miri and Khosravi Citation2022).
Conclusions
Jute fiber is one of the most widely available natural fibers. It has a low thermal conductivity, high tensile strength and low cos. The most important disadvantage of natural fibers is that they are not fire resistant. In this study, it was aimed to improve the flame retardant properties of composites by adding silicon dioxide (SD) and zinc borate (ZB) microparticles at different weight percentages (3, 5, 7 and 10%) to the jute/epoxy composite. Before producing the composite, some processes were applied to remove the impurities on the jute fiber and to improve the interface. These processes are alkalization and acetylation. Then, laminated jute-epoxy composites containing SD, ZB, and HB particles in different weight percentages were produced using the vacuum infusion method.
Some important results obtained from this study can be listed as follows:
The thermal conductivity value of all produced composites is less than 0.065 W/mK. Therefore, ZB/SD/HB reinforced jute/epoxy composites can be used as thermal insulation materials.
When the flammability test results of the composites were examined, similar results were seen in all of the composite samples reinforced with SD, ZB and HB. As the amount of microparticle reinforcement increased, the burning rate of the composites decreased. The 10ZB, 10SD, 5ZB5SD specimens showed 31.57%, 26.44% and 36.60% less burning rate than the jute-epoxy composite (N), respectively.
In the water absorption test, as the immersion time increased, the amount of water absorption of the composite specimens increased. N, 10ZB, 10SD and 5ZB5SD showed water absorption values of 6.81, 6.15, 7.27 and 8.75% respectively at the end of 96 hours.
The tensile strength of composite specimens increased up to a particular percentage of the microparticle, but when this rate was exceeded, the tensile strength decreased. The 5ZB, 3SD, 3.5ZB3.5SD specimens showed 10.84%, 4.85% and 5.38% higher tensile strength than the jute-epoxy composite (N), respectively.
Among the composite specimens, 5SD showed the highest flexural strength. This value (102.67 MPa) is 15.11% higher than that of the jute-epoxy composite without fillers.
When the impact test results were compared, it was observed that the impact strength of the samples increased with the increase in the additive ratio. As the additive ratio increased, the composites absorbed more energy. Composites including hybrid microparticles showed higher impact strength than those containing only SD and ZB. 5ZB5SD, containing 10% hybrid fillers by weight, showed approximately 2.50 times the impact strength of the jute-epoxy composite (N).
This study shows the reader that the flammability, thermal and mechanical properties of jute-epoxy composites can be improved with zinc borate, silicon dioxide and hybrid microparticle reinforcement.
If it is desired to study the flammability of composites by using similar flame retardant additives, the amount of additives can be increased to achieve better non-flammability. However, since it is difficult to work with high amount of microparticle additives in the vacuum infusion method, it is recommended to produce particle-reinforced composites by a different method (such as hand lay-up).
Acknowledgement
The authors would like to thank for the financial support of this research to the TUBITAK (Scientific and Technological Research Council of Turkey) 2209-A University Students Research Projects Support Program (project no: 1919B012001280). In addition, the authors thank the SAZCILAR Inc. for supplying materials for the vacuum infusion process and MELOS Inc. for providing Zinc borate microparticles.
Disclosure statement
The authors declare that they have no known competing financial interests or personal relationships that could have appeared to influence the work reported in this paper.
Additional information
Funding
References
- Abdi, A., R. Eslami-Farsani, and H. Khosravi. 2018. Evaluating the mechanical behavior of basalt fibers/epoxy composites containing surface-modified CaCo3 nanoparticles. Fibers and Polymers. 19 (3):635–20. Springer. doi:10.1007/s12221-018-7755-x.
- Ahmed, A. S., M. Islam, M. K. M. H. Azman Hassan, K. Islam, R. Arjmandi, and R. Arjmandi. 2014. Impact of succinic anhydride on the properties of jute fiber/polypropylene biocomposites. Fibers and Polymers Springer. 15 (2):307–14. doi:10.1007/s12221-014-0307-8.
- Ahmed, S., and F. R. Jones. 1990. A review oF particulate reinforcement theories for polymer composites. Journal of Materials Science Springer. 25 (12):4933–42. doi:10.1007/BF00580110.
- Ahmed, K. S., V. Mallinatha, and S. J. Amith. 2011. Effect of ceramic fillers on mechanical properties of woven jute fabric reinforced epoxy composites. Journal of Reinforced Plastics and Composites SAGE Publications Sage UK: London, England. 30 (15):1315–26. doi:10.1177/0731684411420606.
- Amjad, A., A. Anjang Ab Rahman, and M. Shukur Zainol Abidin. 2022. Effect of nanofillers on mechanical and water absorption properties of alkaline treated jute fiber reinforced epoxy bio nanocomposites. Taylor & Francis. Journal of Natural FibersJournal of Natural Fibers. 1–17. doi:10.1080/15440478.2022.2068171.
- Ankush, S., M. Choudhary, P. Agarwal, S. K. B. Shivam Joshi, A. Patnaik, and A. Patnaik. 2021. Mechanical, thermal and thermomechanical properties of sponge iron slag filled needle-punched nonwoven jute epoxy hybrid composites. Fibers and Polymers Springer. 22 (4):1082–98. doi:10.1007/s12221-021-0578-9.
- Asi, O. 2009. Mechanical properties of glass-fiber reinforced epoxy composites filled with al 2O3 particles. Journal of Reinforced Plastics and Composites Sage Publications Sage UK: London, England. 28 (23):2861–67. doi:10.1177/0731684408093975.
- ASTM, A.M. 2006. ASTM D570-98: standard test method for water absorption of plastics. doi:10.1520/D0570-98R05.
- ASTM, A. M. 2017. ASTM D3039-standard test method for tensile properties of polymer matrix composite materials. doi:10.1520/D3039_D3039M-00R06.
- ASTM, C. 2017. 518, standard test method for steady-state thermal transmission properties by means of the heat flow meter apparatus. Annual Book of ASTM Standards.
- Ateşer, H. O. 2010. Amorf silika seramiklerin andaluzit katkısıyla sinterlenme ve mekanik özelliklerinin incelenmesi. PhD diss., Fen Bilimleri Enstitüsü.
- Azad, M. M., S. K. A. Mohsin Ejaz, J.-I. Song, S. K. Afaq, and J.-I. Song. 2022. A bio-based approach to simultaneously improve flame retardancy, thermal stability and mechanical properties of nano-silica filled jute/thermoplastic starch composite. Materials Chemistry and Physics 126485:126485. doi:10.1016/j.matchemphys.2022.126485.
- Bachtiar, E. V., K. Kurkowiak, L. Yan, B. Kasal, and T. Kolb. 2019. Thermal stability, fire performance, and mechanical properties of natural fibre fabric-reinforced polymer composites with different fire retardants. Polymers 11:4. Multidisciplinary Digital Publishing Institute: 699. doi:10.3390/polym11040699.
- Balakrishnan, S., C. Krishnaraj, and C. R. Raajeshkrishna. 2019. Mechanical characterization of pineapple, watermelon peel nanoparticles reinforced carbon, jute fabric, and its hybrid epoxy composites. Materials Research Express IOP Publishing. 6 (10):105356. doi:10.1088/2053-1591/ab403f.
- Burger, N., A. Laachachi, M. Ferriol, M. Lutz, V. Toniazzo, and D. Ruch. 2016. Review of thermal conductivity in composites: mechanisms, parameters and theory. Progress in Polymer Science 61:1–28. Elsevier. doi:10.1016/j.progpolymsci.2016.05.001.
- Delhom, C. D., L. A. White-Ghoorahoo, and S. S. Pang. 2010. Development and characterization of cellulose/clay nanocomposites. Composites Part B: Engineering Elsevier. 41 (6):475–81. doi:10.1016/j.compositesb.2009.10.007.
- Devireddy, S. B. R., and S. Biswas. 2016. Physical and thermal properties of unidirectional banana–jute hybrid fiber-reinforced epoxy composites. Journal of Reinforced Plastics and Composites SAGE Publications Sage UK: London, England. 35 (15):1157–72. doi:10.1177/0731684416642877.
- Durrani, H., V. Sharma, D. Bamboria, A. Shukla, S. Basak, and W. Ali. 2020. Exploration of flame retardant efficacy of cellulosic fabric using in-situ synthesized zinc borate particles. Cellulose Springer. 27 (15):9061–73. doi:10.1007/s10570-020-03383-4.
- Ejaz, M., S. K. A. Muhammad Muzammil Azad, J.-I. Song, S. K. Afaq, and J.-I. Song. 2022. Synergistic effect of aluminum trihydrate and zirconium hydroxide nanoparticles on mechanical properties, flammability, and thermal degradation of polyester/jute fiber composite. Cellulose Springer. 29 (3):1775–90. doi:10.1007/s10570-022-04417-9.
- Ejaz, M., M. Muzammil Azad, S. K. A. Atta Ur Rehman Shah, J.-I. Song, and J.-I. Song. 2020. Mechanical and biodegradable properties oF jute/flax reinforced PLA composites. Fibers and Polymers Springer. 21 (11):2635–41. doi:10.1007/s12221-020-1370-y.
- Evseeva, L. E., and S. A. Tanaeva. 2008. Thermal conductivity of micro-and nanostructural epoxy composites at low temperatures. Mechanics of Composite Materials Springer. 44 (1):87–92. doi:10.1007/s11029-008-0010-1.
- Feiz, A., and H. Khosravi. 2019. Multiscale composites based on a nanoclay-enhanced matrix and e-glass chopped strand mat. Journal of Reinforced Plastics and Composites SAGE Publications Sage UK: London, England. 38 (13):591–600. doi:10.1177/0731684419836219.
- Formicola, C., A. De Fenzo, M. Zarrelli, M. Giordano, and V. Antonucci. 2011. Zinc‐based compounds as smoke suppressant agents for an aerospace epoxy matrix. Polymer International Wiley Online Library. 60 (2):304–11. doi:10.1002/pi.2949.
- George, K., S. Mohanty, M. Biswal, and S. K. Nayak. 2022. Flame retardancy of EPDM/KevlaR fibre composites with zinc borate, magnesium hydroxide and ammonium polyphosphate. Journal of Thermal Analysis and Calorimetry Springer. 147 (15):8189–98. doi:10.1007/s10973-021-11148-9.
- Ghosh, S. K., S. Bairagi, M. Rajib Bhattacharyya, and M. Murari Mohan Mondal. 2016. Study on potential application of natural fibre made fabrics as thermal insulation medium. American International Journal of Research in Science, Technology, Engineering & Mathematics 16 (203):8–13.
- Gogna, E., R. Kumar, A. Kumar Sahoo, and A. Panda. 2019. A comprehensive review on jute fiber reinforced composites. In Shanker, K., Shankar, R., Sindhwani, R. eds. Advances in Industrial and Production Engineering. Lecture Notes in Mechanical Engineering, 459–67. Singapore: Springer.
- Gopal, M., S. K. Bhaduri, S. K. Banerjee, and K. P. Sao. 1985. Acetylation of Jute and Infrared Spectra of Acetylated Jute. India: NISCAIR-CSIR.
- Gowda, T. M., A. C. B. Naidu, and R. Chhaya. 1999. Some mechanical properties of untreated jute fabric-reinforced polyester composites. Composites Part A, Applied Science and Manufacturing Elsevier. 30 (3):277–84. doi:10.1016/S1359-835X(98)00157-2.
- Gupta, M. K., and R. K. Srivastava. 2016. Mechanical, thermal and water absorption properties of hybrid sisal/jute fiber reinforced polymer composite. India: NISCAIR-CSIR.
- Gwon, J. G., S. Young Lee, S. Jin Chun, G. Hyun Doh, and J. Hyeun Kim. 2010. “Effects of chemical treatments of hybrid fillers on the physical and thermal properties of wood plastic composites.” Composites Part A: Applied Science and Manufacturing 41 (10). Elsevier: 1491–97.
- Hai, N. M., B.-S. Kim, and S. Lee. 2009. Effect of NaOH treatments on jute and coir fiber PP composites. Advanced Composite Materials Taylor &Francis. 18 (3):197–208. doi:10.1163/156855109X428754.
- ISO, E. N. 1998. ISO 14125, fibre-reinforced plastic composite-determination of flexural properties.
- ISO-Committee. 2010. Plastics—determination oF charpy impact properties (ISO 179-1). Geneva, Switzerland: ISO-Committee.
- Jawaid, M., H. P. S. Abdul Khalil, and A. Abu Bakar. 2010. Mechanical performance of oil palm empty fruit bunches/jute fibres reinforced epoxy hybrid composites. Materials Science and Engineering: A Elsevier. 527 (29–30):7944–49. doi:10.1016/j.msea.2010.09.005.
- Jiao, C., and X. Chen. 2011. Influence of fumed silica on the flame‐retardant properties of ethylene vinyl acetate/aluminum hydroxide composites. Journal of Applied Polymer Science Wiley Online Library. 120 (3):1285–89. doi:10.1002/app.33126.
- John, M. J., and R. D. Anandjiwala. 2008. Recent developments in chemical modification and characterization of natural fiber‐reinforced composites. Polymer Composites Wiley Online Library. 29 (2):187–207. doi:10.1002/pc.20461.
- Kabir, M. M., K. T. L. Hao Wang, F. Cardona, and F. Cardona. 2012. Chemical treatments on plant-based natural fibre reinforced polymer composites: an overview. Composites Part B: Engineering Elsevier. 43 (7):2883–92. doi:10.1016/j.compositesb.2012.04.053.
- Kapatel, P. M. 2021. Investigation oF green composite: preparation and characterization of alkali-treated jute fabric-reinforced polymer matrix composites. Journal of Natural Fibers Taylor & Francis. 18 (4):510–19. doi:10.1080/15440478.2019.1636738.
- Karaduman, Y.E.K.T.A., M. M. A. Sayeed, L. Onal, and A. Rawal. 2014. Viscoelastic properties of surface modified jute fiber/polypropylene nonwoven composites. Composites Part B: Engineering 67:111–18. Elsevier. doi:10.1016/j.compositesb.2014.06.019.
- Khalili, P., X. Liu, K. Yeow Tshai, C. Rudd, X. Yi, and I. Kong. 2019. Development of fire retardancy of natural fiber composite encouraged by a synergy between zinc borate and ammonium polyphosphate. Composites Part B: Engineering 159:165–72. Elsevier. doi:10.1016/j.compositesb.2018.09.036.
- Kivade, S. B., M. N. Amaresh Gunge, S. Rajole, and S. Rajole. 2022. Mechanical and dynamic mechanical behavior of acetylation-treated plain woven banana reinforced biodegradable composites. Advanced Composites and Hybrid Materials Springer. 5 (1):144–58. doi:10.1007/s42114-021-00247-8.
- Kulaksızoğlu, Z. 2006. Isı Yalıtım Sektör Araştırması. 1.
- Kumar, G. C., S. M. Baligidad, A. C. Maharudresh, N. Dayanand, and T. N. Chetan. 2022. “Development and investigation of the mechanical properties of natural fiber reinforced polymer composite.” Materials Today: Proceedings. 50. Phagwara, India: Elsevier: 1626–31.
- Kumar, R., S. Kumari, B. Rai, R. Kumar, S. Sirohi, and G. Kumar. 2020. A facile chemical approach to isolate cellulose nanofibers from jute fibers. Journal of Polymers and the Environment Springer. 28 (10):2761–70. doi:10.1007/s10924-020-01808-6.
- Mingzhu, P., L. Hailan, and M. Changtong. 2013. Flammability of nano silicon dioxide–wood fiber–polyethylene composites. Journal of Composite Materials Sage Publications Sage UK: London, England. 47 (12):1471–77. doi:10.1177/0021998312448499.
- Mutalikdesai, S., A. Hadapad, S. Patole, and G. Hatti. 2018. “Fabrication and mechanical characterization of glass fibre reinforced epoxy hybrid composites using fly ash/nano clay/zinc oxide as filler.” In IOP Conference Series: Materials Science and Engineering. Moodbidri, India, 376:12061. IOP Publishing.
- Nath, S., H. Jena, D. Sahini, and D. Sahini. 2019. Analysis of mechanical properties of jute epoxy composite with cenosphere filler. Silicon Springer. 11 (2):659–71. doi:10.1007/s12633-018-9941-x.
- Neto, J., H. Queiroz, R. Aguiar, R. Lima, D. Cavalcanti, and M. Doina Banea. 2022. A review oF recent advances in hybrid natural fiber reinforced polymer composites. Journal of Renewable Materials 10(3): Tech Science Press: 561. doi:10.32604/jrm.2022.017434.
- Owen, M. M. 2014. The effects of alkali treatment on the mechanical properties of jute fabric reinforced epoxy composites. International Journal of Fiber and Textile Research 4 (2):32–40.
- Parkunam, N., M. Ramesh, and S. Saravanakumar. 2022. “A review on thermo-mechanical properties of natural fibre reinforced polymer composites incorporated with fire retardants.” Materials Today: Proceedings. Elsevier.
- Patnaik, T. K., and S. S. Nayak. 2018. Development of silicon carbide reinforced jute epoxy composites: physical, mechanical and thermo-mechanical characterizations. Silicon Springer. 10 (1):137–45. doi:10.1007/s12633-015-9393-5.
- Pavlidou, S., K. Krassa, and C. D. Papaspyrides. 2005. Woven glass fabric/polyester composites: effect of interface tailoring on water absorption. Journal of Applied Polymer Science Wiley Online Library. 98 (2):843–51. doi:10.1002/app.22179.
- Pujari, S., A. Ramakrishna, and K. Tulasi Balaram Padal. 2017. Investigations on thermal conductivities of jute and banana fiber reinforced epoxy composites. Journal of the Institution of Engineers (India): Series D Springer. 98 (1):79–83. doi:10.1007/s40033-015-0102-8.
- Qian, Y., S. Zhou, and X. Chen. 2018. Synergistic flame retardant effect between nano-silicon dioxide and layered double hydroxides in ethylene vinyl acetate composites. Journal of Thermoplastic Composite Materials SAGE Publications Sage UK: London, England. 31 (10):1295–309. doi:10.1177/0892705717738287.
- Qin, Q., R. Guo, E. Ren, X. Lai, C. Cui, H. Xiao, M. Zhou, G. Yao, S. Jiang, and J. Lan. 2020. Waste cotton fabric/Zinc borate composite aerogel with excellent flame retardancy. ACS Sustainable Chemistry & Engineering ACS Publications. 8 (28):10335–44. doi:10.1021/acssuschemeng.0c00210.
- Ray, D., and B. K. Sarkar. 2001. Characterization oF alkali‐treated jute fibers for physical and mechanical properties. Journal of Applied Polymer Science 80(7): Wiley Online Library: 1013–20. doi:10.1002/app.1184.
- Ribeiro, M. C. S., S. P. B. Sousa, and P. R. O. Nóvoa. 2015. An Investigation on fire and flexural mechanical behaviors of nano and micro polyester composites filled with SiO2 and Al2O3 particles. Materials Today: Proceedings Elsevier. 2 (1):8–19. doi:10.1016/j.matpr.2015.04.002.
- Rong, M. Z., M. Qiu Zhang, Y. Xiang Zheng, H. Min Zeng, and K. Friedrich. 2001. Improvement of tensile properties of Nano-SiO2/PP composites in relation to percolation mechanism. Polymer Elsevier. 42 (7):3301–04. doi:10.1016/S0032-3861(00)00741-2.
- Sain, M., S. H. Park, F. Suhara, and S. Law. 2004. Flame retardant and mechanical properties of natural fibre–pp composites containing magnesium hydroxide. Polymer Degradation and Stability Elsevier. 83 (2):363–67. doi:10.1016/S0141-3910(03)00280-5.
- Sajin, J. B., R. Christu Paul, J. S. Binoj, B. Brailson Mansingh, M. Gerald Arul Selvan, R. S. R. I. Kheng Lim Goh, and M. S. Senthil Saravanan. 2022. Impact of fiber length on mechanical, morphological and thermal analysis of chemical treated jute fiber polymer composites for sustainable applications. Elsevier: 100241. Current Research in Green and Sustainable Chemistry. 5: 100241.
- Sanjay, M. R., and B. Yogesha. 2017. Studies on natural/glass fiber reinforced polymer hybrid composites: an evolution. Materials Today: Proceedings Elsevier. 4 (2):2739–47. doi:10.1016/j.matpr.2017.02.151.
- Santulli, C. 2007. Impact properties of glass/plant fibre hybrid laminates. Journal of Materials Science Springer. 42 (11):3699–707. doi:10.1007/s10853-006-0662-y.
- Seki, Y. 2009. Innovative multifunctional siloxane treatment of jute fiber surface and its effect on the mechanical properties of jute/thermoset composites. Materials Science and Engineering: A Elsevier. 508 (1–2):247–52. doi:10.1016/j.msea.2009.01.043.
- Shi, X.-H., L. Xue-Lin, L. Ying-Ming, Z. Li, and D.-Y. Wang. 2022. Flame-retardant strategy and mechanism of fiber reinforced polymeric composite: a review. Composites Part B: Engineering Elsevier 109663:109663. doi:10.1016/j.compositesb.2022.109663.
- Silva, I. L. A. D., A. Barreto Bevitori, L. Araujo Rohen, F. Muylaert Margem, F. de Oliveira Braga, and S. Neves Monteiro. 2016. Characterization by fourier transform ‘nfrared (FTIR) analysis for natural jute fiber. Materials science forum, Vol. 869, 283–87. Trans Tech Publications Ltd. https://doi.org/10.4028/www.scientific.net/MSF.869.283
- Singh, S. K., A. Kumar, and A. Jain. 2018. Improving tensile and flexural properties of SiO2-Epoxy polymer nanocomposite. Materials Today: Proceedings 5 (2):6339–44. Elsevier.
- Sinha, E., and S. K. Rout. 2009. Influence oF fibre-surface treatment on structural, thermal and mechanical properties of jute fibre and its composite. Bulletin of Materials Science Springer. 32 (1):65–76. doi:10.1007/s12034-009-0010-3.
- Sinha, R. K., K. Sridhar, R. Purohit, and R. Kumar Malviya. 2020. “Effect of Nano SiO2 on properties of natural fiber reinforced epoxy hybrid composite: a review.” Materials Today: Proceedings. U.P. India. 26. Elsevier: 3183–86.
- Sumesh, K. R., and K. Kanthavel. 2019. Green synthesis of aluminium oxide nanoparticles and its applications in mechanical and thermal stability of hybrid natural composites. Journal of Polymers and the Environment Springer. 27 (10):2189–200. doi:10.1007/s10924-019-01506-y.
- Suppakarn, N., and K. Jarukumjorn. 2009. Mechanical properties and flammability of sisal/PP composites: effect of flame retardant type and content. Composites Part B: Engineering Elsevier. 40 (7):613–18. doi:10.1016/j.compositesb.2009.04.005.
- Suresha, B., S. L. Guggare, and N. V. Raghavendra. 2016. Effect of TiO2 filler loading on physico-mechanical properties and abrasion of jute fabric reinforced epoxy composites. Materials Sciences and Applications Scientific Research Publishing. 7 (9):510–26. doi:10.4236/msa.2016.79044.
- Symington, M. C., W. M. Banks, O. David West, and R. A. Pethrick. 2009. Tensile testing of cellulose based natural fibers for structural composite applications. Journal of Composite Materials Sage Publications Sage UK: London, England. 43 (9):1083–108. doi:10.1177/0021998308097740.
- Yadav, R. K. 2013. A study on mechanical behavior of surface modified jute fiber reinforced epoxy composites, PhD diss. Engineering and Technology.
- Yadav, P. S., R. Purohit, A. Kothari, and R. S. Rajput. 2021. Effect of Nano SiO2on mechanical and thermal properties of polymer matrix nanocomposites. Taylor & Francis. Advances in Materials and Processing Technologies 1–17.
- Yan, L., N. Chouw, L. Huang, and B. Kasal. 2016. Effect of alkali treatment on microstructure and mechanical properties of coir fibres, coir fibre reinforced-polymer composites and reinforced-cementitious composites. Construction and Building Materials 112:168–82. Elsevier. doi:10.1016/j.conbuildmat.2016.02.182.
- Yeh, S.-K., H. Chun-Ruei, M. Bangun Rizkiana, and C.-H. Kuo. 2021. Effect of fiber size, cyclic moisture absorption and fungal decay on the durability of natural fiber composites. Construction and Building Materials 286:122819. Elsevier. doi:10.1016/j.conbuildmat.2021.122819.
- Yüce, S. 2009. Çinko borat üretimi. PhD diss., Fen Bilimleri Enstitüsü.
- Yuksel Yilmaz, A.N., Yunus, D.E.,and Celik Bedeloglu, A. Investigation of mechanical properties of hybrid stainless steel/acrylic and carbon fiber reinforced epoxy composite.Journal of Composite Materials. 56 (18): 2855–2866. doi:10.1177/00219983221106249. SAGE Publications Sage UK: London.
- Yurddaskal, M., and E. Celik. 2018. Effect of halogen-free nanoparticles on the mechanical, structural, thermal and flame retardant properties of polymer matrix composite. Composite Structures 183:381–88. Elsevier. doi:10.1016/j.compstruct.2017.03.093.
- Zaer-Miri, S., and H. Khosravi. 2022. Assessment of the wear behavior and interlaminar shear properties of modified nano-TiO2/jute fiber/epoxy multiscale composites. Journal of Industrial Textiles SAGE Publications Sage UK: London, England. 51 (7):1084–99. doi:10.1177/1528083719893718.
- Zakriya, M., G. Ramakrishnan, N. Gobi, N. K. Palaniswamy, and J. Srinivasan. 2017. “Jute-reinforced non-woven composites as a thermal insulator and sound absorber–a review. Journal of Reinforced Plastics and Composites SAGE Publications Sage UK: London, England. 36 (3):206–13. doi:10.1177/0731684416679745.