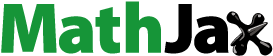
ABSTRACT
This work aims to examine the feasibility of using poly(ethylene glycol) (PEG)-based reverse micellar dyeing system for dyeing cotton fabric with the use of hot type trichloropyrimidine (TCP)-based reactive dyes and to evaluate the possibility of saving the dyeing energy used during the dyeing process. Experimental results show that fabrics dyed in reverse micellar system at 90°C can achieve higher color yield than the conventional water-based system at the same temperature. Further experiments using reverse micellar system for dyeing cotton at 80°C (a reduction of working temperature of 10°C) provided color yield comparable to that of conventional water-based system except the use of yellow dye. Both water-dyed and octane-dyed samples had good to excellent levelness, washing and rubbing fastness and 98.5% of octane could be recycled after distillation. Reflectance curves were identical in shape and the SEM images showed neither of the dyeing systems caused any significant damage to cotton fibers. These findings validated the possibility of using reverse micellar dyeing system for hot type TCP-based reactive dyeing of cotton fabrics at lower coloration temperature and energy consumption.
摘要
本工作旨在检验基于聚乙二醇(PEG)的反胶团染色系统用于热型三氯嘧啶(TCP)活性染料对棉织物染色的可行性,并评估在染色过程中节省染色能量的可能性. 实验结果表明,织物在90°C的反胶束体系中染色,在相同温度下比传统的水基体系获得更高的显色率. 使用反胶束体系在80°C(工作温度降低10°C)下对棉花进行染色的进一步实验,除使用黄色染料外,其显色率与传统水基体系相当. 水色和辛烷染色样品均具有良好的匀染性、洗涤和摩擦牢度,蒸馏后辛烷可回收98.5%. 反射曲线形状相同,SEM图像显示,两种染色系统均未对棉纤维造成任何显著损伤. 这些发现验证了在较低染色温度和能耗下,使用反胶团染色系统对棉织物进行热型TCP活性染色的可能性.
Introduction
Textile dyes used for dyeing of cotton fibers can be primarily classified according to the application class: (a) direct dyes; (b) reactive dyes; (c) sulfur dyes; (d) vat dyes; and (e) azoic dyes. Among these, reactive dyes, first introduced by ICI in 1956, are the most common dye class for coloration of cotton fibers since they have unique characteristics to react and form dye-fiber covalent bonds with cotton fibers (Ahmed Citation1995; Aspland Citation1992).
Reactive dyes of various reactive groups show different reactivity and are applied at different exhaust dyeing temperatures with different amounts of salt and alkali so as to achieve the optimum dyeing effect. Dyes with relatively high reactivity (cold-type) to cotton fibers are generally alkali controllable. They are mostly applied at relatively low temperatures (25-40°C) and require careful control of alkali addition for level dyeing. Dichlorotriazine (DCT) and difluorochloropyrimidine (DFCP) are the best examples of cold type reactive dyes. On the contrary, dyes with relatively low reactivity to cotton fibers are salt controllable. They are commonly applied at relatively high temperatures (80-95°C) and require careful control of salt addition, promoting exhaustion for level dyeing. Trichloropyrimidine (TCP) and monochlorotriazine (MCT) are the best examples of hot type reactive dyes (Broadbent Citation2001).
Dyeing of cotton fibers with reactive dyes with conventional water-based approach, on the one hand, consumes large amounts of water and auxiliaries. On the other hand, it generates substantial amounts of effluent which results in high cost of post-treatment and poses threats to the living environment and the ecosystem (Dong et al. Citation2007; Hossain et al. Citation2021). To alleviate the environmental pressure, new dyeing technologies which are more environment-friendly and need less water, energy, chemicals and auxiliaries and generate less effluent (a greener approach) are being explored constantly.
To follow a greener approach to dyeing of cotton fibers, different attempts, such as supercritical carbon dioxide (Abou Elmaaty et al. Citation2020, Citation2022, Citation2022; Baaka et al. Citation2022; Luo et al. Citation2018; Zaghloul et al. Citation2021; Zhang, Zheng, and Zheng Citation2018), clay nano-adsorbent (Parvinzadeh Gashti et al. Citation2013), D5 microemulsion (Hossain et al. Citation2022; Pei, Gu, and Wang Citation2021), natural dye extracts (Arroyo Figueroa et al. Citation2021; Dhanania, Singhee, and Samanta Citation2021; Diarsa and Gupte Citation2020; Hossain et al. Citation2021; Kumizhi Kizhakkinayil and Nair Citation2021; Naveed et al. Citation2022), and cationization (Giacomini, de Souza, and de Barros Citation2020; Teklemedhin Citation2018), have been made. One of the alternative methods is to replace the conventional aqueous dyeing media with non-aqueous media with the aid of reverse micelles self-assembled by the use of surfactant and solvent, forming a water-pool capable of solubilizing water in their polar cores (De and Maitra Citation1995; Pileni Citation1993; Sawada and Ueda Citation2003c). To form stable reverse micelles, surfactant with proper Hydrophilic-Lipophilic Balance (HLB) value is crucial (Tang et al. Citation2018). Sawada and Ueda (Citation2003a) used anionic surfactant, Aerosol-OT, as the building block for reverse micelle formation. However, the problem of uneven micro-environment is encountered in which the water-pool region of reverse micelles is adversely affected by the ionic head groups of surfactant molecules, shifting the research direction toward the use of nonionic surfactant (Sawada and Ueda Citation2004; Yi et al. Citation2015).
Our series of systematic studies have focused on investigating the application of reverse micelle as a function of dye carrier and as an alternative coloration technology for dyeing of cotton in non-aqueous organic solvent media based on the use of polyethylene glycol (PEG) nonionic surfactant (Tang and Kan Citation2020; Wang et al. Citation2016). In contrast to most of our previous works that primarily used Levafix CA series (Tang et al. Citation2019a) and other vinyl sulfone (VS)-based warm type reactive dyes (Tang et al. Citation2019b), this study uses trichloropyrimidine (TCP)-based hot type reactive dyes to investigate the feasibility of using polyethylene glycol (PEG)-based reverse micellar approach for hot type reactive dyeing of cotton fabrics in high temperature (80 and 90°C) and compare its dyeing performance, effectiveness, and efficiency with conventional water-based dyeing approach (90°C) in terms of (a) color yield (K/Ssum value); (b) color space coordinates (CIE L*a*b* values); (c) color levelness (Relative Unlevelness Indices); (d) color reflectance (Reflectance curves); (e) washing and crocking colorfastness (Greyscale); and (f) fiber damage (Scanning electron microscopy). In addition, the recovery of octane solvent is studied through the use of simple distillation.
Experimental
Materials and reagents
Interlock 100% cotton bleached fabric (fabric density: 16 wales and 20 courses per cm, fabric weight: 148 g/m2), obtained from Fountain Set (Holdings) Limited, Hong Kong, was washed (washing condition: 2 g/L detergent, 49°C, 45 min), tumble dried and conditioned in a standard environment (65 ± 2% relative humidity (RH), 20 ± 2ºC). Nonionic surfactant (polyethylene glycol (12) tridecylether) (PEG-12) (Sigma-Aldrich, St. Louis, MO, USA), co-surfactant (n-octanol) (Acros Organics, Geel, Belgium) and octane solvent (Acros Organics, Geel, Belgium) were of regent grade, facilitating the assembly process of PEG-based reverse micelles. Sodium chloride (reagent grade) (VWR Chemicals, Leuven, Belgium) was used for conventional dyeing approach only whereas sodium carbonate (reagent grade) (Sigma-Aldrich, St. Louis, MO, USA) was used for both conventional and PEG-based reverse micellar dyeing approach. Trichloropyrimidine (TCP)-based, reactive dyes () were obtained from Clariant (China) and used without further purification. illustrates chemical structure of the TCP-based reactive dye.
Table 1. TCP-based dyestuff used in the experiment.
Instruments
Dyeing of cotton fabric was conducted in BS-21 shaking and heating bath (JeioTech, South Korea). DataColor SF650 Spectrophotometer (DataColor Inc., USA) was used for measurement of color yield, CIE L*a*b* values, reflectance percentage and color levelness of water-dyed and PEG-dyed fabrics. SDL ATLAS Launderometer (SDL, USA) was used to conduct colourfastness to washing test. Colourfastness to rubbing test was launched by the use of SDL ATLAS Crockmeter (SDL, USA). The surface morphology of the cotton fiber was observed by using TM3000 tabletop scanning electron microscope (Hitachi, Japan).
Methods
Conventional hot type water dyeing of cotton fabric (sodium chloride)
Conventional dyeing of cotton fabric in aqueous media was conducted in accordance with the recipe advised by the dye supplier and the liquor-to-goods ratio (LR) was 50:1 (ensuring level dyeing). shows the profile of hot type process for reactive dyeing of cotton fabric. The fabric was immersed in the dye liquor, prepared with sodium chloride () and the dye solution, in water bath (30°C) with shaking (10 min), followed by raising the bath temperature to 90°C for dyeing (40 min). Sodium carbonate () was then added to promote dye fixation carried out for another 60 min. The bath temperature was finally lowered to 50°C and the fabric was rinsed with detergent (2 g/L) twice. The rinsed fabric was then drip-dried and conditioned (65 ± 2% RH, 20 ± 2 ºC) for 24 hours before measurements were taken.
Figure 2. Flow diagram for conventional hot type reactive dyeing of cotton fabric in water media (sodium chloride).
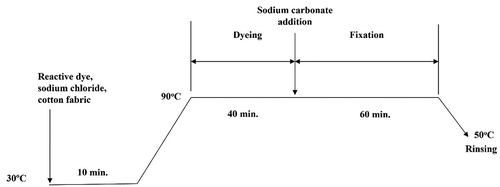
Table 2. Sodium chloride and sodium carbonate for various dye concentrations.
PEG-based reverse micellar dye encapsulation
exhibits the recipe for preparation of PEG-based dye-encapsulated reverse micelles. To promote the self-assembling process of PEG-based reverse micelles, simple injection of mixtures of nonionic surfactant (PEG-12), co-surfactant (n-octanol) and octane solvent was carried out at ambient environment with continuous stirring. Reactive dye solution was then added into the prepared reverse micellar solution. Dye encapsulation process was then accelerated by continuous stirring, ensuring good dispersion of dye encapsulated reverse micellar solution for subsequent dyeing of cotton fabrics ().
Table 3. Recipe for PEG-based dye-encapsulated reverse micelle preparation.
PEG-based hot type reverse micellar dyeing of cotton (no sodium chloride)
demonstrates the workflow for preparation of PEG-based reverse micellar dyeing of cotton fabric with the use of hot type TCP-based reactive dyes in octane media. Cotton fabric was immersed in the prepared dye liquor (Section 2.3) at 30°C (10 min), followed by increasing the temperature to 80 or 90°C for dyeing (40 min), and adding sodium carbonate () for fixation (60 min). The temperature of the bath was then lowered to 50°C to allow rinsing of the fabric with detergent solution (2 g/L) twice (20 min). The washed fabric was drip-dried and then conditioned in a standard environment (65 ± 2% RH, 20 ± 2 ºC) for 24 hours before subsequent measurements.
Color yield (K/Ssum value)
DataColor SF650 Spectrophotometer (USA) was used to obtain the color yield of both conventional and reverse micellar dyed fabric samples. The dyed fabrics were folded twice to ensure opacity on the face side. K/Ssum value was calculated by summing K/S values of the dyed samples from 400 to 700 nm wavelength (visible light spectrum). The parameters included: (a) light source (illuminant D65); (b) standard observer (10°); (c) medium aperture (20 mm diameters); (d) 10 nm data interval; and (e) four measurements (average) per sample. The calculation of K/S value was as in Equation (1) and it can be interpreted that higher K/S value means better color yield:
Where K: absorption coefficient (colorant concentration), S: scattering coefficient (dyed samples), and R: reflectance (dyed samples).
CIE L*a*b* value
CIE L*a*b* values of water-dyed and octane-dyed samples were obtained by the same apparatus and parameters (Sub-section of color yield).
Relative Unlevelness Indices (RUI)
Relative Unlevelness Indices (RUI), proposed by Chong, Li, and Yeung (Citation1992), were used to evaluate the color levelness of water-dyed and octane-dyed fabric samples (dye concentrations of 0.1% to 3.5% o.w.f.). Each sample was measured at four randomly selected spots using the same apparatus and parameters (Sub-section of color yield). RUI values were then calculated with the use of Equation (2).
Where : standard deviation of reflectance (specified wavelength);
: reflectance (specific wavelength);
: photopic relative luminous efficiency function.
Washing fastness assessment
AATCC Test Method 61–2013, Test No. 2A, was conducted and gray scale was used to assess washing fastness (in terms of color change and color staining) of the dyed samples (dye concentrations from 0.1 to 3.5% o.w.f.) and the attached multifiber fabrics.
Rubbing fastness assessment
AATCC Test Method 8–2013 was conducted, and gray scale was used to assess dry and wet crocking fastness (in terms of color staining) of the dyed samples (dye concentrations from 0.1 to 3.5% o.w.f.) and the white crock cloth.
Scanning Electron Microscopy (SEM)
TM3000 tabletop scanning electron microscope (Hitachi, Japan) was used to capture surface morphology images of the undyed, water-dyed, and octane-dyed cotton fabrics.
Solvent recovery
Post-dyeing solution (40 ml) was placed in round-bottom flask with magnetic stirring for recovery of solvent through distillation. The flask was immersed in oil bath and connected with a thermometer and a condenser tube via a three-way adaptor. The distillation process was controlled at a rate of 1 drop per second at 125°C. The collected distillates were then transferred to a separatory funnel for observation.
Results and discussion
Color yield
shows color yield (K/Ssum value) of cotton fabrics dyed with TCP-based reactive dyes using conventional water-based approach and reverse micellar octane-based approach at different temperatures. Fabric samples dyed with TCP dyes of blue, rubine, yellow and violet colors in octane media (90°C) obtain the highest K/Ssum values compared with those dyed in conventional water-based media (90°C) and octane media (80°C). Most Fabrics dyed in octane media (90°C) can achieve a percentage increase of color yield ranged from 0.55% to 36.70% when compared with those dyed in water media. This indicates that PEG-based reverse micellar approach for dyeing of cotton fabrics with hot type TCP-based reactive dyes in octane media is feasible and can be superior and more effective and efficient than that in water media at the same dyeing temperature (90°C) owing to the reduced ionization effect between dye molecules and cotton fiber, improved swelling of fiber and enhanced dye molecule absorption (Liu et al. Citation1998; Sawada and Ueda Citation2003b; Tang et al. Citation2017).
Table 4. The K/Ssum value of water-dyed and PEG reverse micellar-dyed samples with various TCP-based reactive dyes.
With regard to rubine color (), fabrics dyed in octane media (80°C) exhibit significantly higher color yield than those dyed in water media (90°C). Fabrics dyed in octane media at 80°C obtain a percentage increase of color yield between 15.77% and 26.86% when compared with that in conventional water media. This means that lower dyeing temperature (10°C lesser) can be used for dyeing cotton with rubine color by using reverse micellar approach in octane media and the parameters used in this study (Section 2.3 ) are particularly favorable for hot type reactive dyeing cotton fabric with RR55.
Concerning blue (RB52) and violet (RV6) colors (), color yield of water-dyed and octane-dyed samples is close. Blue-dyed samples in octane media gain slightly higher color yield (0.44% to 7.44%) than those dyed in water media whereas violet-dyed samples in octane media attain slightly lower color yield (−6.81% to −18.29%) than those dyed in water media. This suggests that reverse micellar approach (80°C) for dyeing of cotton fabrics with hot type TCP-based blue and violet dyes can also achieve lower dyeing temperature (10°C lesser) while maintaining dyeing properties similar to conventional water-based approach (90°C).
In case of yellow color (RY41), reverse micellar dyeing approach (80°C) obtains noticeably lower color yield (−10.94% to −32.58%) than the conventional water-based approach (90°C). This implies that reverse micellar dyeing approach (80°C) is unable to match the color yield of conventional water-based approach (90°C) and higher temperature, such as 85°C, is needed in order to acquire color yield comparable to conventional water-based approach (90°C). The possible reason is related to the cross effect of factors between compatibility and reactivity of dye, working temperature and dyeing system (Tang et al. Citation2019b).
Color reflectance
presents reflectance curves of cotton samples dyed in conventional water-based media and reverse micellar octane media with hot type TCP-based reactive dyes. Higher reflectance percentage (%) means lower dye absorption and lighter shade. From , it is apparent that fabrics dyed in conventional aqueous media (90°C) with blue, rubine and violet colors exhibit the highest reflectance percentage (lightest shade), followed by those dyed in reverse micellar octane media (80°C) (medium shade), while fabrics dyed in reverse micellar octane media (90°C) obtain the lowest reflectance percentage (darkest shade). This reveals that using reverse micellar octane media (80°C) is adequate to achieve blue, rubine and violet shades comparable to the conventional aqueous media (90°C).
Figure 5. Reflectance curves of water-dyed and reverse micellar-dyed samples with various TCP-based reactive dyes (80D and 90D are dyed at 80°C and 90°C respectively): (a) blue color (Drimarene Blue X-3LR); (b) rubine color (Drimarene Rubine X-3LR); (c) yellow color (Drimarene Golden Yellow X-2 R); and (d) violet color (Drimarene Violet X-2RL).
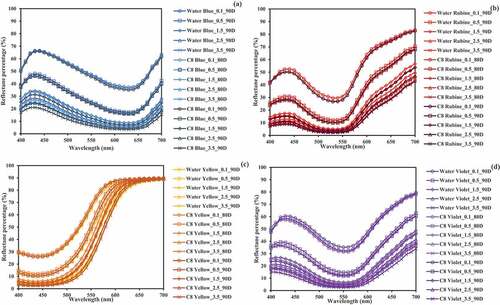
In case of yellow color (), the result is slightly different. Fabrics dyed in reverse micellar octane media (80°C) obtain the highest reflectance percentage, followed by water media (90°C), whereas fabrics dyed in reverse micellar octane media (90°C) gain the lowest reflectance percentage. Therefore, higher dyeing temperature of reverse micellar system (above 80°C) is recommended in order to achieve yellow shade comparable to the conventional water-based system.
As illustrated in , reflectance curves of cotton fabrics dyed in conventional aqueous media and reverse micellar octane media are identical in shape, without any peak shifting. This indicates that the use of reverse micellar octane media (80 or 90°C) does not affect color quality of the TCP-based reactive dyes and is thus applicable for hot type reactive dyeing of cotton fabrics.
Levelness
displays RUI values of water-dyed and reverse micellar octane-dyed cotton samples with TCP-based reactive dyes. It is observed that both water-dyed and octane-dyed samples can achieve good to excellent levelness with RUI values less than 0.5. Among the four colors, both water-dyed and octane-dyed samples in yellow color (RY41) obtain excellent levelness (RUI values less than 0.2) for all the five dye concentrations (0.1 to 3.5%) and their RUI values are relatively constant (0.7 to 0.12) when compared with blue (0.13 to 0.39), rubine (0.05 to 0.48), and violet (0.06 to 0.47) colors.
Table 5. Relative Unlevelness Indices (RUI) of water-dyed and octane-dyed samples with various TCP-based reactive dyes.
Among the three dyeing conditions, conventional water-based method has the best levelness (RUI values: 0.05 to 0.24), followed by reverse micellar method (80°C) (RUI values: 0.03 to 0.45), and reverse micellar method (90°C) (RUI values: 0.07 to 0.47). The possible reason for water-based method having the best levelness is due to the use of liquor-to-goods ratio of 50:1 while the solvent to cotton ratio for reverse micellar method is only 8:1. In addition, it is observed that even though a higher temperature of reverse micellar method (90°C) can achieve a higher color yield, levelness is poorer compared with reverse micellar method (80°C).
CIE L*a*b* values
manifests CIE L*a*b* values of water-dyed and octane-dyed samples, dyed with TCP-based reactive dyes. The L* value represents the lightness of the sample. The higher the L* value, the lighter is the shade of the sample. From , L* values of all colors generally reveal a negative relationship with dye concentration. When dye concentration increases, the L* value decreases, indicating darker shade of the fabric.
Table 6. The CIE L*a*b* values of water-dyed and octane-dyed samples with various TCP-based reactive dyes.
The a* value represents red (+a) and green (−a). The results () exhibit that a* values of all colors have a positive relationship with dye concentration. When dye concentration increases, the a* value increases and both water-dyed and octane dyed samples become redder in shade. The b* value representing yellow (+b) and blue (−b) varies, relative to different colors. Blue and violet colors show a decrease of b* value when dye concentration increases. This means that both water-dyed and octane-dyed samples become bluer in shade. However, red and yellow colors reveal an increase of b* value when dye concentration increases. This indicates that both water-dyed and octane-dyed samples become yellower in shade when dye concentration increases from 0.1 to 3.5%.
Washing fastness
shows the color change and staining ratings of water-dyed and reverse micellar octane-dyed fabrics after testing by AATCC Test Method 61. With regard to color change, both water-dyed and reverse micellar-dyed samples obtain excellent ratings between 4–5 and 5 for all the four colors. Regarding color staining, nearly all water-dyed and reverse micellar-dyed samples can achieve ratings between 4–5 and 5 except those dyed in reverse micellar octane media (90°C) with 3.5% dye concentration for blue, red and violet colors which can achieve rating of only 4. In addition, both water-dyed and octane-dyed samples can attain excellent washing fastness toward yellow color (rating of 5). These results indicate that both water-dyed and reverse micellar octane-dyed samples are adequately washed after the dyeing process. No unfixed dye or chemical residue was found on the surface of the fabrics.
Table 7. Color change and staining ratings of water-dyed and reverse micellar octane-dyed cotton substrates with various TCP-based reactive dyes.
Rubbing fastness
depicts color staining ratings of dry and wet crocking fastness of water-dyed and octane-dyed cotton fabrics. It is evident that both water-dyed and octane-dyed samples obtain good to excellent dry and wet rubbing fastness with ratings ranging from 4 to 5. This indicates that TCP-based dyes used in this study can achieve good fixation to the fabrics.
Table 8. Color staining ratings of water-dyed and reverse micellar octane-dyed cotton substrates with various TCP-based reactive dyes.
SEM images
presents SEM images of undyed, water-dyed (90°C), octane-dyed (80°C) and octane-dyed (90°C) cotton fabrics using 3.5% concentration of RB52 reactive dye with 1000x magnification. The images reveal that both water-dyed and octane-dyed cotton have only a few short microfibrils on the fiber surface after the high temperature dyeing process. This means that neither the conventional water-based dyeing approach nor the reverse micellar dyeing approach causes any significant damage to cotton fibers, validating the possibility of using reverse micellar dyeing system for hot type TCP-based reactive dyeing of cotton fabrics at a lower temperature.
Solvent recovery
After the distillation process, the collected distillate consists of two layers in which the bottom layer and the upper layer are composed of a small amount of water and the recycled solvent respectively. The percentage of solvent recovery is calculated based on the ratio of recycled solvent volume to the theoretical prediction of solvent volume used before the dyeing process and the result reveals that about 98.5% of octane can be recovered for further use after the reverse micellar dyeing process.
Conclusion
The feasibility of using PEG-based reverse micellar dyeing system for hot type reactive dyeing of cotton fabrics with TCP-based reactive dyes is investigated and compared with conventional water-based dyeing system. Experimental results manifest that fabric samples dyed in reverse micellar system at temperature of 90°C obtain higher color yield (K/Ssum value) than those dyed with the conventional water-based dyeing system at the same temperature.
Further experiment was then conducted to examine the use of reverse micellar system for dyeing of cotton fabrics at a lower temperature of 80°C. Experimental results exhibit that fabric dyed with RB52, and RV6 in reverse micellar system can achieve color yield comparable to that in the conventional system. Fabrics dyed with RR55 in reverse micellar system can even attain a higher color yield when compared with the conventional system. However, fabrics dyed with RY41 in reverse micellar system are unable to match color yield of conventional water-based system and higher temperature (above 80°C) is needed.
Reflectance curves of water-dyed and reverse micellar-dyed samples are identical in shape and no peak shifting is found. Generally speaking, fabrics dyed in conventional water-based system show higher reflectance percentage than in reverse micellar system except those dyed with RY41 at 80°C. Good to excellent levelness, washing and rubbing fastness are obtained for both water-dyed and reverse micellar-dyed samples. The SEM images reveal that neither the conventional water-based dyeing approach nor the reverse micellar dyeing approach cause any significant damage to cotton fibers and the use of simple distillation method can recycle about 98.5% of octane solvent used in the reverse micellar system, validating the possibility of using reverse micellar dyeing system for hot type TCP-based reactive dyeing of cotton fabrics at a lower temperature and good solvent recovery.
Supplemental Material
Download MS Word (15.2 KB)Disclosure statement
No potential conflict of interest was reported by the author(s).
Supplementary material
Supplemental data for this article can be accessed online at https://doi.org/10.1080/15440478.2022.2131689
Additional information
Funding
References
- Abou Elmaaty, T., H. Elsisi, E. Negm, S. Ayad, and M. Sofan. 2022. Novel nano silica assisted synthesis of azo pyrazole for the sustainable dyeing and antimicrobial finishing of cotton fabrics in supercritical carbon dioxide. The Journal of Supercritical Fluids 179:105354. doi:10.1016/j.supflu.2021.105354.
- Abou Elmaaty, T., H. Kazumasa, H. Elsisi, A. Mousa, H. Sorour, H. Gaffer, T. Hori, A. Hebeish, I. Tabata, and R. Farouk. 2020. Pilot scale water free dyeing of pure cotton under supercritical carbon dioxide. Carbohydrate Polymer Technologies and Applications 1:100010. doi:10.1016/j.carpta.2020.100010.
- Abou Elmaaty, T., M. Sofan, S. Ayad, E. Negm, and H. Elsisi. 2022. Novel synthesis of reactive disperse dyes for dyeing and antibacterial finishing of cotton fabric under scCO2. Journal of CO2 Utilization 61:102053. doi:10.1016/j.jcou.2022.102053.
- Ahmed, A. I. 1995. Reactive dyes development: A review. Textile Dyer and Printer 28:19–14.
- Arroyo Figueroa, G., J. G. Dzul Cauich, T. M. Saavedra, and M. I. García Vieyra. 2021. Dyeing and colour fastness in cotton and wool, using natural extracts of sunflower petals, onion peel and cocoa shell. Journal of Natural Fibers 1–10. doi:10.1080/15440478.2021.1950097.
- Aspland, J. R. 1992. Reactive dyes and their application. Textile Chemists and Colorists 24 (5):31–36.
- Baaka, N., N. Dhouibi, S. Dridi-Dhaouadi, and H. Dhaouadi. 2022. Comparative study between supercritical carbondioxide fluid technology and conventional water-based processing to dye minor elastin containing cotton fabrics. Journal of Natural Fibers 19 (5):1681–89. doi:10.1080/15440478.2020.1787922.
- Broadbent, A. D. 2001. Reactive dyes. In Basic principles of textile coloration, 332–57. Bradford, England: Society of Dyers and Colorists.
- Chong, C. L., S. Q. Li, and K. W. Yeung. 1992. An objective method for the assessment of levelness of dyed materials. Journal of the Society of Dyers and Colourists 108 (12):528–30. doi:10.1111/j.1478-4408.1992.tb01405.x.
- De, T. K., and A. Maitra. 1995. Solution behaviour of Aerosol OT in non-polar solvents. Advances in Colloid and Interface Science 59:95–193. doi:10.1016/0001-8686(95)80005-N.
- Dhanania, Y., D. Singhee, and A. K. Samanta. 2021. Optimization of dyeing process variables for eco-friendly dyeing of cotton fabric with babul bark extract as a natural dye and gallnut extract as a bio-mordant. Journal of Natural Fibers 1–18. doi:10.1080/15440478.2021.1875955.
- Diarsa, M., and A. Gupte. 2020. Optimization and extraction of natural dye from tagetes erecta and dyeing of cotton and silk fabric using banana (Musa Sp.) pseudo stem sap. Journal of Natural Fibers 19: 1–13. doi:10.1080/15440478.2020.1863291.
- Dong, Y., J. Chen, C. Li, and H. Zhu. 2007. Decoloration of three azo dyes in water by photocatalysis of Fe (Iii)–oxalate complexes/H2O2 in the presence of inorganic salts. Dyes and Pigments 73 (2):261–68. doi:10.1016/j.dyepig.2005.12.007.
- Giacomini, F., A. A. U. de Souza, and M. A. S. D. de Barros. 2020. Comparative study of dyeing with cochineal dye in cationized cotton with various proteins. Journal of Natural Fibers 19: 1–13. doi:10.1080/15440478.2020.1856275.
- Hossain, S., M. A. Jalil, A. Kader, and S. A. B. Kamal. 2021. Excellent dyeing properties of a natural dye extracted from the leaves of phoenix dactylifera linn on cotton and silk fabrics. Journal of Natural Fibers 1–10. doi:10.1080/15440478.2021.1993410.
- Hossain, M. Y., T. Jiang, W. Zhu, S. Sarker, M. N. Pervez, M. I. U. Hoque, Y. Cai, and V. Naddeo. 2022. Green and sustainable method to improve fixation of a natural functional dye onto cotton fabric using cationic dye-fixing agent/D5 microemulsion. Journal of Natural Fibers 1–16. doi:10.1080/15440478.2021.2024933.
- Hossain, M. Y., Y. Liang, M. N. Pervez, X. Ye, X. Dong, M. M. Hassan, and Y. Cai. 2021. Effluent-free deep dyeing of cotton fabric with cacao husk extracts using the Taguchi optimization method. Cellulose 28 (1):517–32. doi:10.1007/s10570-020-03525-8.
- Kumizhi Kizhakkinayil, M., and B. R. Nair. 2021. Extraction of an eco-friendly natural dye from eleutherine bulbosa (Miller) Urban bulbs, its application as a cotton fabric colorant and chemical characterization. Journal of Natural Fibers 1–13. doi:10.1080/15440478.2021.1982109.
- Liu, D., J. Ma, H. Cheng, and Z. Zhao. 1998. Investigation on the conductivity and microstructure of AOT/non-ionic surfactants/water/n-heptane mixed reverse micelles. Colloids and Surfaces A, Physicochemical and Engineering Aspects 135 (1):157–64. doi:10.1016/S0927-7757(97)00239-2.
- Luo, X., J. White, R. Thompson, C. Rayner, B. Kulik, A. Kazlauciunas, W. He, and L. Lin. 2018. Novel sustainable synthesis of dyes for clean dyeing of wool and cotton fibres in supercritical carbon dioxide. Journal of Cleaner Production 199:1–10. doi:10.1016/j.jclepro.2018.07.158.
- Naveed, R., I. A. Bhatti, S. Adeel, A. Ashar, I. Sohail, M. U. H. Khan, N. Masood, M. Iqbal, and A. Nazir. 2022. Microwave assisted extraction and dyeing of cotton fabric with mixed natural dye from pomegranate rind (Punica granatum L.) and turmeric rhizome (Curcuma longa L.). Journal of Natural Fibers 19 (1):248–55. doi:10.1080/15440478.2020.1738309.
- Parvinzadeh Gashti, M., R. Rashidian, A. Almasian, and A. B. Zohouri. 2013. A novel method for colouration of cotton using clay nano-adsorbent treatment. Pigment & Resin Technology 42 (3):175–85. doi:10.1108/03699421311317343.
- Pei, L., X. Gu, and J. Wang. 2021. Sustainable dyeing of cotton fabric with reactive dye in silicone oil emulsion for improving dye uptake and reducing wastewater. Cellulose 28 (4):2537–50. doi:10.1007/s10570-020-03673-x.
- Pileni, M. P. 1993. Reverse micelles as microreactors. The Journal of Physical Chemistry 97 (27):6961–73. doi:10.1021/j100129a008.
- Sawada, K., and M. Ueda. 2003a. Adsorption behavior of direct dye on cotton in non-aqueous media. Dyes and Pigments 58 (1):37–40. doi:10.1016/S0143-7208(03)00027-5.
- Sawada, K., and M. Ueda. 2003b. Dyeing of protein fiber in a reverse micellar system. Dyes and Pigments 58 (2):99–103. doi:10.1016/S0143-7208(03)00048-2.
- Sawada, K., and M. Ueda. 2003c. Adsorption and fixation of a reactive dye on cotton in non-aqueous systems. Coloration Technology 119 (3):182–86. doi:10.1111/j.1478-4408.2003.tb00170.x.
- Sawada, K., and M. Ueda. 2004. Characteristics of aqueous microenvironments in non‐ionic surfactant reverse micelles and their use for enzyme reactions in non‐aqueous media. Journal of Chemical Technology and Biotechnology 79 (4):369–75. doi:10.1002/jctb.984.
- Tang, A. Y. L., and C. W. Kan. 2020. Non-aqueous dyeing of cotton fibre with reactive dyes: A review. Coloration Technology 136 (3):214–23. doi:10.1111/cote.12459.
- Tang, A. Y. L., C. H. Lee, Y. Wang, and C. W. Kan. 2017. Octane-assisted reverse micellar dyeing of cotton with reactive dyes. Polymers 9 (12):678. doi:10.3390/polym9120678.
- Tang, A. Y. L., C. H. Lee, Y. M. Wang, and C. W. Kan. 2018. Effect of hydrophilic-lipophilic balance (HLB) values of PEG-based non-ionic surfactant on reverse micellar dyeing of cotton fibre with reactive dyes in non-aqueous medium. Fibers and Polymers 19 (4):894–904. doi:10.1007/s12221-018-8061-y.
- Tang, A. Y. L., C. H. Lee, Y. M. Wang, and C. W. Kan. 2019a. Dyeing cotton with reactive dyes: A comparison between conventional water-based and solvent-assisted PEG-based reverse micellar dyeing systems. Cellulose 26 (2):1399–408. doi:10.1007/s10570-018-2150-3.
- Tang, A. Y. L., C. H. Lee, Y. M. Wang, and C. W. Kan. 2019b. A study of PEG-based reverse micellar dyeing of cotton fabric: Reactive dyes with different reactive groups. Cellulose 26 (6):4159–73. doi:10.1007/s10570-019-02340-0.
- Teklemedhin, B. T. 2018. Cationization of cotton using extracted keratin from ethiopian sheep wool waste for salt free dyeing with reactive dye. Journal of Textile Science & Engineering 8:365. doi:10.4172/2165-8064.1000365.
- Wang, Y. M., C. H. Lee, Y. L. Tang, and C. W. Kan. 2016. Dyeing cotton in alkane solvent using polyethylene glycol-based reverse micelle as reactive dye carrier. Cellulose 23 (1):965–80. doi:10.1007/s10570-015-0831-8.
- Yi, S., X. Tong, S. Sun, and F. Dai. 2015. Dyeing properties of CI reactive violet 2 on cotton fabric in non-ionic TX-100/span40 mixed reverse micelles. Fibers and Polymers 16 (8):1663–70. doi:10.1007/s12221-015-5386-7.
- Zaghloul, D. N., T. Abou Elmaaty, K. Nakamura, I. Tabata, T. Hori, and K. Hirogaki. 2021. Influence of additive organic base on dyeing of cotton fabric under supercritical carbon dioxide using fluorotriazine reactive disperse dye and investigation of optimal dyeing conditions. The Journal of Supercritical Fluids 174:105243. doi:10.1016/j.supflu.2021.105243.
- Zhang, J., H. Zheng, and L. Zheng. 2018. Optimization of eco-friendly reactive dyeing of cellulose fabrics using supercritical carbon dioxide fluid with different humidity. Journal of Natural Fibers 15 (1):1–10. doi:10.1080/15440478.2017.1302385.