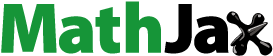
ABSTRACT
This study investigated the comparative influence of different compositions (3 wt. %, 6 wt. %, 9 wt. %, 12 wt.%, and 15 wt. %) of treated plantain stem fiber (PSF) and plantain leaf fiber (PLF) on selected properties of the epoxy-based composite. These plantain fibers and epoxy resin were mixed based on predetermined compositions and stirred using a stirrer at an ambient temperature for 3 minutes before pouring into a mold using a hand layup process. The composites were allowed to cure within 2–3 hours. Mechanical (tensile, flexural, impact, and hardness), wear, thermal conductivity and water absorption properties, and surface morphologies of the developed composites were investigated. The study revealed that the optimum properties were attained at 9 wt.% and 12 wt.% PSF and PLF except for wear and water absorption that occurred at 15 wt.%. The PSF gave more enhancement in all the properties except for impact strength. Hence, from the combination of properties obtained, these bio-based fibers can be used to improve the conductivity of eco-friendly and biodegradable polymer-based composites for electrical/electronics, biomedical, automobile, and building applications.
摘要
本研究比较了经处理的车前草茎纤维 (PSF) 和车前草叶纤维 (PLF) 的不同成分 (3wt.%、6wt.%, 9wt.%和12wt.%) 对环氧基复合材料选定性能的影响. 根据预定成分混合这些车前草纤维和环氧树脂, 并使用搅拌器在环境温度下搅拌3分钟, 然后使用手糊工艺将其倒入模具中. 允许复合材料在2-3小时内固化。研究了所开发复合材料的机械 (拉伸、弯曲、冲击和硬度) 、磨损、导热性和吸水性能以及表面形貌. 研究表明, 除磨损和吸水率为15%外, PSF和PLF的质量分数分别为9%和12%时, 其性能最佳. 除冲击强度外, PSF在所有性能上都有较大的增强。因此, 从所获得的性能组合来看, 这些生物基纤维可用于提高电气/电子、生物医学、汽车和建筑应用中生态友好和可生物降解聚合物基复合材料的导电性.
Introduction
Polymer composites reinforced with natural fibers have sparked a lot of research interest owing to their incredible versatility in terms of ultimate product qualities, design, availability, cost-effectiveness, and ever-evolving synthesis procedures (Arpitha et al. Citation2022; Gouda et al. Citation2014; Paul, Kanny, and Redhi Citation2015; Rastogi, Verma, and Singh Citation2020). They are considered excellent alternatives to traditional materials. They have found applications in critical areas such as aerospace, automotive, and medical devices because of their excellent strength-to-weight ratio, highly configurable product qualities, flexible production processes, and strong corrosion resistance capabilities (Oladele et al. Citation2021b; Rajak et al. Citation2019; Verma, Gaur, and Singh Citation2017). Among thermoset polymer materials used as a matrix in composite fabrication, epoxy is a polymer of choice due to its good chemical and corrosion resistance. Its rigidity after curing through the cross-linking structures is also responsible for the strengths and high-temperature versatility. Based on its strength and durability, epoxy has wide applications in automobiles and construction. The combination of epoxy resin with agro-waste products has engendered structural modification, resulting in the base material’s property enhancement (Oladele et al. Citation2020a).
Using natural fibers as reinforcement has attracted the attention of researchers because of their advantages over other established materials. They are environmentally friendly, fully biodegradable, abundantly available, renewable, cheap, and low-density. These fibers are used in place of synthetic fibers in structural applications. Several automotive components made with glass fiber are now manufactured using environmentally friendly composites attributed to the fibers’ low weight and reasonable maintenance (Ballo and Närhi Citation2017; Vinayagamoorthy Citation2020). Automotive companies such as German auto companies (BMW, Audi Group, Ford, Opel, Volkswagen, Daimler Chrysler, and Mercedes), Proton company (Malaysian national carmaker), and Cambridge industry (an auto industry in the USA) now adopt the use of natural fibers in the production of automotive components (Shinoj et al. Citation2011). Recently, the application of natural fibers extended to other industries such as building and construction, structural, and aerospace (Oladele, Omotosho, and Adediran Citation2020b).
Recently, interest in natural fibers has made plants waste a helpful substance in the environment. Fibers extracted from stems and leaves are applied in different applications such as textile, structural, and engineering (Jenish et al. Citation2022a, Citation2022b). Researchers have attempted to use natural fibers from plants, such as bananas, bamboo, sisal, raffia, coir, hemp, and many more, to optimize polymer composites’ mechanical, wear, and physical properties. Of these plants, plantain (Musa Paradisiaca) contains a high proportion of nutrients and has been used for food, beverages, and medicine (Paul and John Citation2018). Despite the plant’s potential, its stem and leaf are considered waste materials. These wastes are tremendous; their disposal is challenging and constitutes environmental pollution.
However, despite the advantages of using natural fibers, its high cellulose content is a drawback in achieving high strength properties and good compatibility between fiber and polymer matrix. Physically or chemically modification is a solution to improve the surface and interfacial adhesion between the natural fiber and the matrix. Chemical modifications such as alkali, silane, and acetylation treatment are used to remove impurities and cause surface roughness of the fiber (Bakri, Jayamani, and Hamdan Citation2017; Naidu, Kona, and Bahubalendruni Citation2019; Oladele, Omokafe, and Olusegun Citation2016).
This study added value to plantain stem and leaf waste by using them as reinforcement in an epoxy polymer matrix. This research evaluates the influence of chemically modified plantain fiber from stem and leaves on the properties of reinforced epoxy composites developed for structural applications.
Materials and methods
Materials
The materials used in this research were plantain fibers processed from its stem and leaf, epoxy resin LY556 (bisphenol A), hardener HY951 (Araldite), and sodium hydroxide used for alkali treatment. The plantain stem and leaves were obtained from a farm settlement in Akure, Ondo State, Nigeria. The epoxy and hardener were used as the matrix and purchased from a supplier in Lagos State, Nigeria. reveal the plantain plant and the fiber extracted.
Experimental procedure
Preparation of plantain fiber
The extracted plantain fibers for the stem and leaves were sun-dried for 3 days to reduce the moisture content. The dried stem and leaf fibers are chopped into short lengths of between 5–7 mm and treated in water bathe (UNISCOPE SM101) with 1 M of Sodium Hydroxide (NaOH) for 2 hours at 50°C. The treatment aided in increasing the surface roughness of the plantain fibers. The treated fibers were washed with tap water and rinsed thoroughly with distilled water to ensure neutrality, as confirmed with litmus paper. Further processing was carried out using an oven to dry the fibers for 8 hrs at 60°C. The treated fiber is as shown in .
Preparation of plantain fiber composites
The epoxy resin and hardener were mixed in a ratio of 2:1, respectively (Golestaneh et al. Citation2010). Varying fiber weight fractions of 3, 6, 9, 12, and 15 wt% were measured, introduced into the matrix, and mixed thoroughly in a plastic container for 3 minutes until the fibers were uniformly dispersed. The mixture was poured into the mold using a hand layup process. The composites cure within 2–3 hours based on fiber content. A curing time of 2 hours occurred with low fiber content, while a higher weight fraction resulted in more curing time. The real-time composite material is presented in .
Mechanical, wear, and physical properties tests
The tensile test of the produced samples was carried out according to the ASTM C1557 standard. The test was performed using Universal Testing Machine (Model: Instron series 3369). Dumbbell-shaped samples with dimensions 90 × 10 × 5 mm were adopted, and the test was conducted at a crosshead speed of 5 mm/min using a 10 kg load cell. The flexural properties of the developed composites were evaluated using three points blending test. The configuration was done following ASTM D790. Three samples were tested for each composite, and the average value was estimated.
An impact test was carried out on the produced samples using a Charpy V-Notch impact testing machine (Instron CEAST 9050) following ISO 179. The impact test dimension of 64 × 11 × 3 mm was notched at the center. The hardness test was conducted on the specimen using a Shore D hardness tester. A 15 kgf was applied to each composite sample with a 15 s dwell time. Five values were obtained by indenting the composite in five different places, and the average value was used for analysis.
The wear loss index was evaluated using a Taber abraser (TSC-A016). The machine was operated at a constant speed of 500rpm. This test was carried out to ascertain the material’s vulnerability to abrasion. The initial weights of the samples were recorded as Wi, while the final weight after the abrasion test is Wf measured on the electronic weighing machine for accuracy. The wear indices were calculated based on the sample weight loss, as shown in EquationEquation (1)(1)
(1) .
where, Wi, Wf, and C are initial weight, final weight, and the number of test cycles, respectively.
Thermal conductivity was examined to determine heat flow from one end of the polymeric material to the other using Holmarc lee Disc Apparatus. The thermal conductivity was determined using EquationEquation (2)(2)
(2)
where K is the thermal conductivity; M is the mass of the disk; Cp is the specific heat capacity of the disk; Ø1 − Ø2 initial and final temperature of disc B; D diameter of the sample; X thickness of the sample; T1, T2 is the temperature of disk A and B in Kelvin.
Water absorption tests were carried out per ASTM D5229 M–12 (2012). A 250 cl of water was poured into clean plastic containers to conduct the test. Each composite’s initial weight was taken using a weighing balance, and readings were taken every day for 30 days. The samples were removed, cleaned, and weighed. The data collected were used to determine the weight gained using the EquationEquation (3)(3)
(3) formula.
where W (g) is weight gain per day, Wo is the initial dry weight, and Wt is the sample’s weight at time (t).
Microstructural examination
The surfaces of the produced samples were examined directly by Scanning Electron Microscope (Model: JEOL JSM-6480LV). The samples were mounted on stubs with silver paste. To enhance the conductivity of the composite samples, a thin film of platinum was vacuum evaporated onto the surface before the photomicrographs were taken at a voltage of 15 kV.
Results and discussion
Maximum tensile strength
The result in features an uptrend in the maximum tensile strength of the composite materials from 3 wt. % to 6 wt.% for PLF-based composites and 3 wt.% to 9 wt. % for PSF-based composites, respectively, followed by gradual reduction. This enhancement in strength with an increase in reinforcement content followed by a decrease has been reported in composite development (Oladele et al. Citation2018). The results revealed that the composite with 6 wt. % PLF had 40.60 MPa, while 9 wt.% PSF had 47.65 MPa tensile strength compared to the 31.92 MPa of the control. These results infer the presence of proper adhesion and stress distribution between the plantain fibers and the epoxy matrix, culminating in about 49% enhancement from PSF-based composite. Further addition of PLF and PSF beyond these fiber loadings results in a progressive declination in tensile strengths. This progressive degradation can be attributed to improper bonding at the fiber/matrix interface, thereby reducing the bonding strength of the composite (Jenish et al. Citation2022a). PSF-based composites possess the highest maximum tensile strength in all the compositions studied, which showed that PSF is stronger than PLF and impact better strength property to the developed composites than the PLF.
Tensile modulus
presents the response of plantain fiber reinforced epoxy composite in terms of tensile modulus. A similar trend to was observed except for the optima fiber contents shifting to 9 wt.% for PLF and 12 wt.% for PSF-based composites, respectively. Hence, their values were 314 MPa and 322 MPa compared to the control, which had 242 MPa. This produces an enhancement of about 33% from PSF-based composite. It was noticed that the tensile modulus was improved in all the developed composites compared to the control sample. This implies that 3–15 wt.% reinforcement contents are still an acceptable range of values for enhancing the tensile modulus of the epoxy-based composite. The improvement can be attributed to proper adhesion between the PSF/PLF and the epoxy.
Maximum flexural strength
featured the relationship between the maximum flexural strength at the various PSF/PLF loading and the control. There was an improvement in the flexural strength of both PSF and PLF composites from 3 to 9 wt. % with 9 wt. % having the highest flexural strengths of 64.83 MPa and 61.42 MPa, respectively, compared to 39.54 MPa of epoxy material that serves as the control. The observed trend revealed that these bio-based fibers in the epoxy matrix within 3–12 wt.% aided better flexural strengths in both constituents. Alkaline treatment also helped improve the mechanical properties of polymer composites (Omotoyinbo et al. Citation2022). It could also be deduced that even stress distribution and interlocking structure of the fibers in the matrix contributed to the property enhancements. From the plot, PSF reinforced epoxy showed a better enhancement than PLF reinforced epoxy composites. The enhancement may be due to the higher chemical properties, rigidity, and stiffness possessed by the stem, which made them offer structural support for the plant (Gibson Citation2012; Shah, Reynolds, and Ramage Citation2017). Some authors claimed that plant geometrics such as cross-sectional (circular, elliptical, square cross-sections, etc.) could influence the flexural properties of the fiber. Etnier and Vogel Citation2000 concluded in his study of plant strength that noncircular stem has a higher twist-to-bend ratio and is more strengthening materials than other parts causing them to possess better flexural strength. The system produced about 64% enhancement from PSF-based composite with optimum value.
Flexural modulus
highlights the relationship between flexural modulus, PSF/PFL loading, and the control. The flexural modulus agrees with the tensile modulus obtained in , where all the developed composites possess improved properties than the control sample. The response of the composites to tensile and flexural properties was comparable in the evaluations. Also, the optimal values for the composites shifted from 9 wt.% reinforced epoxy composites for flexural strengths to 12 wt.% reinforcements in flexural modulus. Hence, the optima values from PSF and PLF-based composites were 374 MPa and 353 MPa, respectively. Compared to the unreinforced epoxy with a value of 262 MPa, this culminated in about 43% enhancement from the PSF-based composite. This feat owes to the strong interlink between the bio fibers and epoxy matrix. Further fiber inclusion resulted in a slight reduction of flexural modulus at 15 wt. %; this is attributed to higher fiber loading in the matrix. This reduction can also be because of fiber entanglement and agglomeration, causing the materials’ crack initiation and stress concentration. (Gopinath, Kumar, and Elayaperumal Citation2014) reported a similar result in their study on the mechanical behavior of banana fiber-reinforced epoxy composites; they reported that the flexural strength increases up to 15% fiber loading, followed by a decrease.
Impact strength
The effect of variations of plantain fiber from stem and leaf and variation in fiber loading (3, 6, 9, 12, and 15 wt. %) on the impact strength of plantain fiber/epoxy composites are presented in . Similar trends were observed in the other mechanical properties (). The developed composites possess improved impact strengths compared to the control, with optimal values at 9 wt.% and 12 wt.% for PLF and PSF-based composites, respectively. At these respective fiber loadings, the impact strengths are 43.25 kJ/m2 and 40.82 kJ/m2, culminating in about a 70% increment compared to the epoxy matrix. The results showed proper interfacial adhesion between the treated bio fibers and epoxy matrix. The enhancement could be attributed to the surface modification of the bio fibers (Agbabiaka, Oladele, and Daramola Citation2015). However, contrary to the results from the other mechanical properties (), PLF enhances the impact strengths in all the compositions considered more than the PSF-based composites. This trend showed that the addition and presence of these bio fibers increase the impact strength of the composites, as reported in the literature (Adekomaya et al. Citation2016).
Hardness
shows the variation in plantain fiber loading versus the hardness of the composites and the control. The hardness increased with increasing PSF and PLF loading, having the peak values at 12 wt.% for both fibers with a value of 50 HS for PSF and 46 HS for PLF compared to 27 HS for epoxy matrix. In the same mode as , the hardness of all the composites was improved compared to the control. The proper interfacial bond between the treated fiber and matrix promotes the hardness property. (Dehury et al. Citation2017) affirmed hardness enhancement by adding jute fiber reinforced epoxy/polystyrene up to 40 wt% fiber loading. The increase in hardness can be linked to increased stiffness and interlocking of fibers (Rahman Citation2009). Further addition of PSF and PLF insinuated the declination of the hardness, which is similar to an investigation done by (Özturk Citation2010) in which the addition of 19%, 43%, and 52% volume of kenaf fiber/phenol-formaldehyde composite resulted in a linear increase in hardness with increasing fiber volume until 43 vol. % and followed by a progressive decrease.
Wear
presents the relationship between the wear loss index, plantain fiber-reinforced epoxy matrix, and the control. The composites exhibited an increment in the wear loss index with enhancement from 6 wt. % to 15 w.t%. No improvement occurred when 3 wt.% bio fibers from PSF/PLF were used compared to the control sample, which showed that higher quantities of the bio fibers are needed to improve wear resistance, as shown in the plots. A similar result was reported in an experiment by (B Laxshaman Rao et al. Citation2021) in which banana fiber was used to reinforce epoxy resin. The wear resistance of the composite improves with increased banana proportion. The result also showed that PSF gave improved wear properties than PLF-based composites. For PSF-based composites, the optimum increment was achieved at 15 wt. %, given 0.5% wear loss. The addition of PSF loading in the matrix led to a gradual increase in the wear properties, which could be attributed to the proper bonding between the stem fibers within the epoxy resin. (CH Chandra Rao et al. Citation2012) reported a similar result in their investigation on coir fiber reinforce epoxy resin.
Thermal conductivity
The effect of the PSF and PFL addition to epoxy composites on thermal conductivity is presented in . The result showed that the thermal conductivity of the samples increases as the weight percentage of the reinforcement increases for all specimens. However, PSF better enhanced thermal conductivity than PFL, which corroborates the submission that morphology and fiber composition (strength) significantly influence the thermal conductivity of polymer materials. The conductivity increased from 3 wt.% to 12 wt.%, followed by a decrease at 15 wt%, with a value that is still higher than that of the control sample. The thermal conductivity of epoxy is 1.13 W/mK, while thermal conductivity at the highest point was obtained at 12 wt. % reinforcements which are 2.61 W/mK for PSF and 2.3 W/mK for PLF. The observed enhanced conductivity is due to the fiber’s network nature, which encourages easy heat flow within the materials compared to the epoxy. Hence, these bio-based fibers can be used to improve the conductivity of eco-friendly and biodegradable polymer-based composites for electrical/electronics, biomedical, automobile, and building applications.
Water absorption
shows the water absorption behavior of all composites against the immersion time of 96 hours. It is evident from the plots that the percentage of water absorption increased with an increase in plantain fiber loading. This behavior could be explained since natural fibers are hydrophilic (Alaneme and Oke Citation2013; Oladele et al. Citation2021a). As expected, the water absorption capacity of all the composite samples is high in the early stages of the exposure from 0 to 20 hours, after which it increases until it reaches equilibrium level after 84 hours. At this stage, the composites have attained saturation point and can no longer absorb water. A 15 wt. % of PSF composition has maximum water absorptivity of up to 0.53% compared to the 15 wt. % PLF of 0.44% weight gain. This implies that samples developed with low fiber contents were more resistant to water absorption than samples of higher weight fractions.
Microstructural analysis
The surface morphology of the developed composites was examined using a scanning electron microscope (SEM), and the image for the various compositions of 3 wt.%, 9 wt.%, and 12 wt.% plantain leaf fiber (PLF) to epoxy is shown in , while the image for the various compositions of 3 wt.%, 9 wt.%, and 12 wt.% plantain stem fiber (PSF) to the epoxy is shown in . The microstructure reveals the epoxy polymer’s intrinsic coalescence and adhesion to the plantain leaf fiber (PLF). The surface pattern demonstrates that the PLF has created a homogeneous matrix in the host resin. This homogeneity led to an improvement in the tensile strength and flexural modulus of the composite. The fibers are well dispersed in the composite matrix, as observed in the 9 wt% (PLF). The homogeneity of the composition increases with an increase in fiber fraction. However, above 9 wt.%, an agglomerated character is visible on the surface, as seen in . A similar trend was observed in the SEM images of plantain stem fiber (PSF) reinforced epoxy composites in . The good interfacial bonding between the plantain stem fiber and the epoxy matrix contributed, and the stiffness of the PSF contributed to the improvement observed in the composite’s tensile, impact, and hardness properties.
Conclusion
The influence of treated plantain stem fiber (PSF) and plantain leaf fiber (PLF) on specific selected properties of epoxy composites has been investigated, and the following conclusions were drawn:
The chemical treatment adopted to modify the surface of the plantain fibers improves the surface morphology and contributes to good interfacial adhesion between the fiber and the matrix.
The composite with 6 wt. % PLF had 40.60 MPa while 9 wt.% PSF had 47.65 MPa tensile strength compared to the 31.92 MPa of the control.
There was an improvement in the flexural strength of both PSF and PLF composites with 9 wt. % having the highest flexural strengths of 64.83 MPa and 61.42 MPa, respectively, compared to 39.54 MPa of the control.
The hardness increased with 12 wt.% for both fibers with a value of 50 HS for PSF and 46 HS for PLF compared to 27 HS for epoxy matrix.
The composites exhibited an increment in the impact strength and wear loss index with enhancement from 6 wt. % to 15 w.t%.
The water absorption properties of PLF were enhanced with water absorptivity of up to 0.44% compared to 0.53% for PSF.
Highlights
Plantain stem and leaf were chemically treated to extract their fibers
Epoxy-based composite containing plantain stem and leaf fibers were prepared using a hand layup process.
Chemical treatment enhanced the interfacial adhesions between the fibers and the matrix.
The properties of the epoxy composites were enhanced with the fiber addition
Stem fiber gave more enhanced properties than the leaf fiber except for impact strength
Ethical approval
The authors have no conflicts of interest to declare that are relevant to the content of this article.
Disclosure statement
No potential conflict of interest was reported by the author(s).
Additional information
Funding
References
- Adekomaya, O., T. Jamiru, R. Sadiku, and Z. Huan. 2016. A review on the sustainability of natural fiber in matrix reinforcement–a practical perspective. Journal of Reinforced Plastics and Composites 35 (1):3–14. doi:10.1177/0731684415611974.
- Agbabiaka, O. G., I. O. Oladele, and O. O. Daramola. 2015. Mechanical and water absorption properties of alkaline treated coconut (Cocos nucifera) and sponge (Acanthus montanus) fibers reinforced polypropylene composites. American Journal of Materials Science and Technology 4 (2):84–92. doi:10.7726/ajmst.2015.1007.
- Alaneme, K., and S. Oke. 2013. Water absorption characteristics of polyester matrix composites reinforced with oil palm ash and oil palm fibre. Usak University Journal of Material Sciences 2 (2):109–20. doi:10.12748/uujms.201324253.
- Arpitha, G., A. Verma, S. Mr, S. Gorbatyuk, A. Khan, T. R. Sobahi, A. M. Asiri, and S. Siengchin. 2022. Bio-composite film from corn starch based vetiver cellulose. Journal of Natural Fibers 1–11. doi:10.1080/15440478.2022.2068174.
- Bakri, M. K. B., E. Jayamani, and S. Hamdan. 2017. Processing and characterization of banana fiber/epoxy composites: Effect of alkaline treatment. Materials Today: Proceedings 4 (2):2871–78. doi:10.1016/j.matpr.2017.02.167.
- Ballo, A., and T. Närhi. 2017. Biocompatibility of fiber-reinforced composites for dental applications. In Biocompatibility of dental biomaterials, 23–39. Elsevier. doi:10.1016/B978-0-08-100884-3.00003-5
- Dehury, J., J. Mohanty, S. Biswas, and V. Bhagat. 2017. Physical, mechanical and water absorption behavior of bi-directional jute/glass fiber reinforced epoxy composites. International Journal of Engineering Research 6:1–6.
- Etnier, S. A., and S. Vogel. 2000. Reorientation of daffodil (narcissus: Amaryllidaceae) flowers in wind: Drag reduction and torsional flexibility. American Journal of Botany 87 (1):29–32. doi:10.2307/2656682.
- Gibson, L. J. 2012. The hierarchical structure and mechanics of plant materials. Journal of the Royal Society Interface 9 (76):2749–66. doi:10.1098/rsif.2012.0341.
- Golestaneh, M., G. Amini, G. Najafpour, and M. Beygi. 2010. Evaluation of mechanical strength of epoxy polymer concrete with silica powder as filler. World Applied Sciences Journal 9 (2):216–20.
- Gopinath, A., M. S. Kumar, and A. Elayaperumal. 2014. Experimental investigations on mechanical properties of jute fiber reinforced composites with polyester and epoxy resin matrices. Procedia Engineering 97:2052–63. doi:10.1016/j.proeng.2014.12.448.
- Gouda, P. S., V. Chatterjee, P. Barhai, D. Jawali, S. Rahatekar, and M. Wisnom. 2014. Improved fracture toughness in carbon fibre epoxy composite through novel pre-preg coating method using epoxy terminated butadiene nitrile rubber. Materials & Design (1980-2015) 62:320–26. doi:10.1016/j.matdes.2014.05.018.
- Jenish, I., A. F. Sahayaraj, M. Appadurai, E. F. Irudaya Raj, and P. Suresh. 2022a. Sea sand abrasive wear of red mud micro particle reinforced cissus quadrangularis stem fiber/epoxy composite. Journal of Natural Fibers 1–16. doi:10.1080/15440478.2022.2087131.
- Jenish, I., S. G. Veeramalai Chinnasamy, S. Basavarajappa, S. Indran, D. Divya, Y. Liu, M. Sanjay, and S. Siengchin. 2022b. Tribo-mechanical characterization of carbonized coconut shell micro particle reinforced with cissus quadrangularis stem fiber/epoxy novel composite for structural application. Journal of Natural Fibers 19 (8):2963–79. doi:10.1080/15440478.2020.1838988.
- Naidu, A. L., S. Kona, and M. R. Bahubalendruni. 2019. Mechanical behaviour of layered silicate composites from nagavali river clay. Materials Today: Proceedings 18:109–13. doi:10.1016/j.matpr.2019.06.283.
- Oladele, I., J. Ajileye, S. Oke, O. Daramola, and O. Adewumi. 2021a. Thermal and water absorption properties of bio-synthetic hybrid reinforced polypropylene composites. Materials Today: Proceedings 38:994–98. doi:10.1016/j.matpr.2020.05.580.
- Oladele, I., I. Ibrahim, A. Adediran, A. Akinwekomi, Y. Adetula, and T. Olayanju. 2020a. Modified palm kernel shell fiber/particulate cassava peel hybrid reinforced epoxy composites. Results in Materials 5:100053. doi:10.1016/j.rinma.2019.100053.
- Oladele, I. O., A. M. Okoro, J. A. Omotoyinbo, and M. C. Khoathane. 2018. Evaluation of the mechanical properties of chemically modified chicken feather fibres reinforced high density polyethylene composites. Journal of Taibah University for Science 12 (1):56–63. doi:10.1080/16583655.2018.1451103.
- Oladele, I. O., M. S. Omokafe, and S. J. Olusegun. 2016. Influence of chemical treatment on the constituents and tensile properties of selected agro-fibres. West Indian Journal of Engineering 38 (2): 4-12.
- Oladele, I. O., T. F. Omotosho, and A. A. Adediran. 2020b. Polymer-based composites: An indispensable material for present and future applications. International Journal of Polymer Science 2020 :1–12. doi:10.1155/2020/8834518.
- Oladele, I. O., T. F. Omotosho, G. S. Ogunwande, and F. A. Owa. 2021b. A review on the philosophies for the advancement of polymer-based composites: Past, present and future perspective. Applied Science and Engineering Progress 14 (4):553–79. doi:10.14416/j.asep.2021.08.003.
- Omotoyinbo, J., I. Oladele, J. Jabar, J. Borode, K. Alaname, S. Oke, T. Omotosho, F. Atilola, and L. Saliu. 2022. Microstructural characterisation, rheological and water absorption properties of filled polyurethane foam. Futa Journal of Engineering and Engineering Technology 16 (1):33–43.
- Özturk, S. 2010. Effect of fiber loading on the mechanical properties of kenaf and fiberfrax fiber-reinforced phenol-formaldehyde composites. Journal of Composite Materials 44 (19):2265–88. doi:10.1177/0021998310364265.
- Paul, V., and M. J. John. 2018. Composites from natural fibers and bio-resins. In Biocomposites, 1–25. Jenny Stanford Publishing. DOI: 10.1201/9781315110806.
- Paul, V., K. Kanny, and G. G. Redhi. 2015. Mechanical, thermal and morphological properties of a bio-based composite derived from banana plant source. Composites: Part A, Applied Science and Manufacturing 68:90–100. doi:10.1016/j.compositesa.2014.08.032.
- Rahman, M. M. 2009. UV-cured henequen fibers as polymeric matrix reinforcement: Studies of physico-mechanical and degradable properties. Materials & Design 30 (6):2191–97. doi:10.1016/j.matdes.2008.08.022.
- Rajak, D. K., D. D. Pagar, P. L. Menezes, and E. Linul. 2019. Fiber-reinforced polymer composites: Manufacturing, properties, and applications. Polymers 11 (10):1667. doi:10.3390/polym11101667.
- Rao, C. C., S. Madhusudan, G. Raghavendra, and E. V. Rao. 2012. Investigation in to wear behavior of coir fiber reinforced epoxy composites with the Taguchi method. International Journal of Engineering Research and Applications 2:2248–9622.
- Rao, B. L., Y. Makode, A. Tiwari, O. Dubey, S. Sharma, and V. Mishra. 2021. Review on properties of banana fiber reinforced polymer composites. Materials Today: Proceedings 47:2825–29. doi:10.1016/j.matpr.2021.03.558.
- Rastogi, S., A. Verma, and V. Singh. 2020. Experimental response of nonwoven waste cellulose fabric–reinforced epoxy composites for high toughness and coating applications. Materials Performance and Characterization 9 (1):151–72. doi:10.1520/MPC20190251.
- Shah, D. U., T. P. Reynolds, and M. H. Ramage. 2017. The strength of plants: Theory and experimental methods to measure the mechanical properties of stems. Journal of Experimental Botany 68 (16):4497–516. doi:10.1093/jxb/erx245.
- Shinoj, S., R. Visvanathan, S. Panigrahi, and M. Kochubabu. 2011. Oil palm fiber (opf) and its composites: A review. Industrial Crops and Products 33 (1):7–22. doi:10.1016/j.indcrop.2010.09.009.
- Verma, A., A. Gaur, and V. Singh. 2017. Mechanical properties and microstructure of starch and sisal fiber biocomposite modified with epoxy resin. Materials Performance and Characterization 6 (1):500–20. doi:10.1520/MPC20170069.
- Vinayagamoorthy, R. 2020. Trends and challenges on the development of hybridized natural fiber composites. Journal of Natural Fibers 17(12):1757-1774. doi:10.1080/15440478.2019.1598916.