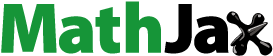
ABSTRACT
A study was conducted to develop Pashmina blended woven fabrics to enhance their functional properties by chemical processing. The samples were prepared from Pashmina, wool and nylon fibers in five blends: T1 (60:0:40); T2 (45:15:40); T3 (30:30:40); T4 (15:45:40) and T5 (0:60:40). Each blend was subjected to spun yarns of three different linear densities 246, 164, and 123 dtex. These yarns were utilized as a filling thread to form 15 different fabric samples keeping warp linear density 168.6 dtex common among all samples. All fabric samples were gently treated with HCl to dissolve nylon fiber and keep only Pashmina and wool natural protein fibers. Different functional properties were tested, including moisture management potential, water vapor transmittance, ultraviolet protection factor (UPF), porosity, and luster. Among all samples, the linear yarn density significantly affected the UPF of fabric samples. The yarn evenness increases by increasing the wool content with pashmina fiber and increases by decreasing the yarn decitex. The Lusture index of fabric increases by increasing the pashmina fibre content. The porosity of the fabric sample increases by increasing the wool fibre content and yarn fineness (dtext). The fabric made of 246 dtex in weft exhibited a maximum UPF of 40. The highest value of the overall moisture management coefficient (OMMC) was attained by sample T148. The fabric samples made of 246 dtex exhibited better functionalities than 164 and 123 dtex. The water vapor transmission rate (WVTR) increases by increasing the wool content and weft yarn fineness.
摘要
进行了一项研究,以开发帕什米纳混纺机织物,通过化学加工提高其功能性能. 样品由帕什米纳、羊毛和尼龙制成五种共混物: T1(60:0:40); T2(45:15:40); T3(30:30:40); T4(15:45:40)和T5(0:60:40). 每种共混物都经过三种不同线密度246、164和123分特的纺纱. 这些纱线被用作填充线,以形成15个不同的织物样品. 所有织物样品都用HCl轻轻处理,以溶解尼龙纤维,只保留帕什米纳和羊毛天然蛋白纤维. 测试了不同的功能性能,包括水分管理电位、水蒸气透过率、紫外线防护因子(UPF)、孔隙率和光泽. 在所有样品中,纱线线密度显著影响织物样品的UPF. 纱线均匀度随羊绒纤维中羊毛含量的增加而增加,随纱线分特数的降低而增加. 随着羊绒纤维含量的增加,织物的光泽指数增加. 织物样品的孔隙率随着羊毛纤维含量和纱线细度(dtex)的增加而增加. 由246分特纬纱制成的织物的最大UPF为40. 总水分管理系数(OMMC)的最高值由样品T148获得. 由246分特制成的织物样品表现出比164分特和123分特更好的功能. 水蒸气透过率(WVTR)随着羊毛含量和纬纱细度的增加而增加.
Introduction
Some of the rare animal fibers due to extra fineness, softness, and lusture have found an esteemed position among the group of textile fibers (Shakyawar et al. Citation2013). Cashmere fiber is one of the best, extravagant, and costliest fibrous strands on the planet, having extraordinary attributes like delicateness, perfection, whiteness, remarkable handle, warmth, strength, attractive, stylish worth, class, agelessness in design, daintiness, and capacity to retain more dampness and colors than fine wool. The guard hair in Cashmere fleeces ought to be longer than the Cashmere, to a limited extent to shield the Cashmere from weather and UV light and to help limit the vegetable matter contamination. Pashmina, a down fiber or undercoat, is sourced from local goat Capra hircus. It has received its name from the Persian word “pashm,” signifying “delicate gold,” the king of fibers (Sofi et al. Citation2018). In India, the dominant part of Pashmina is used to produce shawls in Kashmir valley, which are generally hand spun and hand woven with long life and no heap development. India produces the best quality pashmina globally, with a yearly production of around 40 tons (Ganai, Misra, and Sheikh Citation2011). Exposure of animal keratin fibres, for example, Merino wool and Mohair, to UV exposure in sunlight causes photo bleaching, followed by progressive photo yellowing. Photo bleaching can lead to “tippy dyeing” (Bumla et al. Citation2012).
Pashmina or Cashmere fiber is extremely hard to spin using machine because of its delicate, short, and slippery scales, which make lapping because of the generation of static charges during carding and spinning process (Raja et al. Citation2011). An innovative Charakha was developed to spin pashmina fiber using a hand spinning technique (Wani et al. Citation2013).
Allergies, skin aging, sunburn, and skin cancer are the consequences of upraised unmasking to sunlight. Various dermatologists advise covering maximum skin part by specially engineered clothing, applying sunscreens, avoiding exposure to the sun at its highest intensities (Das Citation2010; Gies, Roy, and Holmes Citation2000).
The desizing and bleaching were found to deteriorate the UV protection of cotton fabrics (Sarkar Citation2007). The cotton fabric samples with low air permeability exhibited a high UV protection factor in twill and plain weave (Majumdar, Kothari, and Mondal Citation2010). Few studies have been done to study the comfort and UV properties of blended woven pashmina fabrics. The fabrics derived from animal fibers have an alternate handle that changes with animal fiber type (Meena, Shakyawar, and Varshney Citation2020). The woven fabrics of Cashmere are generally popular because of drape, crease-resistance, aesthetic properties, and comfort. The comfort properties vary with fiber composition in warp and weft yarns (Meena et al. Citation2021). Pashmina/wool fibers were spun into yarn using the carrier spinning technique in which Cashmere fiber was mixed with nylon and wool and spun into yarn. After yarn manufacturing, the nylon component was dissolved from hybrid yarns as similarly performed with material to liquor ratio 1:30 (Raja et al. Citation2011; Shakyawar et al. Citation2013).The ultraviolet protection by woolen apparels is desired especially in snow regions where intensities of ultraviolet light remain high. The existence of the abundance of the aromatic skeleton and hydrogen bonds helps NLS to absorb ultraviolet radiation (Abreu, Nascimento, and Maria Citation1999). Due to the presence of the sulfonated groups, lignosulfonates get anionically charged and being water-soluble it significantly blocks UV radiations (Jancic et al. Citation2021).
Weave pattern, which basically refers to weave construction, determines the weave characteristics such as porosity and thickness, has effects on the UV protection and UVA, UVB transmittance properties of cotton/polyester blend woven fabrics used for clothing. Titanium dioxide treated fabrics show better UV protection and transmittance characteristics than the untreated fabrics because titanium dioxide absorbs UV rays. While the UPF of treated fabrics increased, UVA and UVB transmittances of these fabrics decreased significantly.The capability of titanium dioxide loaded fabrics against ultraviolet radiation was enhanced (Ozdemir Citation2017).
Some researchers investigated that the water vapor permeability of fabric samples varied according to used raw material, weave pattern of construction and filling density. Larger porosities of Lyocell fabrics have better water vapor permeability properties than modal fabrics. This is due to the fact that bonding between fibrils in Lyocell fibers is weak, resulting in easier fibrillation and a higher percentage of febrile structure than modal fibers (Hearle and Morton Citation2008). It is known that the flow of liquid through textile materials is the result of fiber-liquid molecular attraction at the surface of the fiber materials (Hsieh Citation1995). Which in turn is determined by the surface tension, effective capillary pathways and pore distribution (Ozdemir Citation2017; Zhu and Li Citation2003)?
The study’s objective was to use Pashmina fiber and wool to produce premium class fabric with enhanced functionalities like comfort, lusture, moisture management, and UV protection. To achieve the major goal of this study, the sub-objectives were to produce highly soft and air permeable Pashmina: wool yarns of varying linear densities. The Pashmina: wool hybrid yarns were processed as weft to produce various fabric samples. This research work is committed to offering high-value addition in Pashmina fabrics by product development.
Experimental
Materials and methods
Changthangi Pashmina (13µ), Australian Merino (21µ) and nylon (2.77 dtex) were procured from Indian textile market. Fifteen samples were prepared by blending three fibers Changthangi Pashmina (13µ), Australian Merino (21µ) and nylon (2.77 dtex) in five different proportion viz; T1 (60:0:40); T2 (45:15:40); T3 (30:30:40); T4 (15:45:40); T5 (0:60:40). Each blend was spun to produce three different yarns of linear densities, 246, 164 and 123 dtex on a ring frame spinning machine, making a total of 15 hybrid yarns. These yarns were used to prepare pirns for fabric manufacturing by modified handloom. A common warp beam has warp yarn 168.6 dtex was used for all fifteen fabric sample manufacturing. The weft yarns in all samples were varied by 246, 164 and 123 dtex respectively, which leads to form 15 samples. Representative fabric samples are shown in . The fabrics were scoured at 40°C for 30 minutes using a nonionic detergent, after that rinsing by Luke warm water (30°C). The samples were dried and ironed and treated with HCl of 20% concentration at 20°C for 10 minutes. The details of treated 15 samples are as depicted in , representative fabrics are shown in .
Table 1. Samples prepared with fiber proportion and (weft) count.
Dissolution of nylon fibers from fabric samples
Nylon present in the fabric samples was removed by dipping the fabric samples into 20% HCl at 20°C for 10 min. The fabrics were then washed at 40°C for 30 minutes using a nonionic detergent followed by rinsing with luke warm water (30°C) and dried (Kumar et al. Citation2020).
Treatment with sodium lignosulphonate
The samples were treated through exhaust method with NLS to improve the UPF. The samples were dipped in a solution of 1% wetting agent (Ultraon JU) in which standard solution of 5% wetting agent was prepared (Yaqoob et al. Citation2012). The samples were loaded in IR machine and machine was set for 30 minutes at 40°C. For 15% on the weight of the fabric, NLS solution was prepared keeping M: L ratio as 1:100 at 100% nip expression (samples were too light in weight), which were later dried at 80°C in the autoclave. The fabric samples were washed at 40°C for 30 minutes using a nonionic detergent in a dye bath, followed by rinsing with lukewarm water (30°C). Finally the samples were dried followed by ironing.
Testing Procedure
The yarn evenness testing was performed by Uster Evenness Tester 5 as per ASTM D 1425. The Ultraviolet protection factor of different fabric samples was tested by Gester UV transmittance analyzer as per Australian/New Zealand standard AS/NZS 4399:1996. SDL ATLAS M290 tested the moisture management attributes as per AATCC 195. The Digital three-angle gloss meter (CHN CS-390) was used to analyze the Lusture potential of fabric samples as per JJG 696 test standard. The water vapor transmissions prospective were analyzed by Gester CT-C28 water vapour transmission tester as per IS 11239-4: 1995 Test standard. The fabric porosity assessment was performed by Porometer made by PMI India as per ASTM E 1294.
Results and discussions
Physical parameters of experimental samples
The fabric sample’s analysis is presented in . The areal density of fabric (grams per square meter, GSM) was decreased by increasing the yarn linear density. By decreasing fabric areal density, warp cover, weft cover, and cloth cover were decreased, as shown in . A slight decrease in fabric thickness was also observed by decreasing cloth cover. The fabric thickness was influenced by altering the fiber blend and yarn linear densities, which is a crucial point for fabric engineering for product development. The decreasing Pashmina fiber content decreased the fabric thickness, which may be attributed mainly to the highest pashmina fiber fineness in all three pashmina, wool, and nylon fibers (Sofi et al. Citation2021). (*EPdm- ends per decimeter, PPdm- picks per decimeter)
Table 2. Fabric sample specifications.
The yarn evenness properties were measured on the Uster Evenness Tester-5, the results are as shown in . The thin places, thick places and neps increased by increasing yarn linear density or yarn fineness. However, the hybrid yarn hairiness decreased by increasing yarn fineness from 246 to 123 dtex ().
Table 3. Evenness properties of yarn samples.
The bending behaviour
The bending rigidity results () revealed that the coarser yarns have higher than finer yarns. From , it was observed that coarser linear density fabric needed more bending length. As the Pashmina content in the samples decreased, the bending length increased the bending rigidity of coarser linear density exhibited higher values and vice versa. The samples with blends of Pashmina and Australian merino in combination exhibited higher rigidity than samples containing a significant proportion of Pashmina and Australian merino. The coarser wool fiber has exhibited higher bending modulus than the finer at the fabric stage. The Pashmina fiber content was highest in T1, T6, and T11 yarn and fabric samples. The bending rigidity was decreased by increasing yarn dtex or decreasing yarn diameter. In fabric samples T1 24 to T5 24, the weft way bending rigidity was decreased by decreasing pashmina fiber content from 100 to 35%, and a similar trend was observed in fabric samples T1 36 to T5 36 and T1 48 to T5 48. The warp way bending rigidity was affected only due to the weft yarn assistance because warp yarn linear density was kept constant in all fifteen samples. The flexural modulus is an intensive characteristic computed as the ratio of stress to strain in flexural deformation or the tendency for a material to resist bending. Compared with various fabric samples, the flexural modulus decreased Pashmina fiber content in weft yarns from T1 to T5 in all three yarn dtex 246, 164, and 123. The fine Pashima fiber was replaced by coarse wool fiber from 100 to 35% (Fabric sample T1 to T5). The coarse fibers have a higher diameter and fine fibers possess higher bending rigidity than fine fibers because bending rigidity is inversely proportional to the square of the diameter of a circular fiber (Singh and Behera Citation2021a and Singh and Behera Citation2021b).
Table 4. Bending length, bending rigidity, flexural modulus, and pore size of samples.
UV protection of fabric
The UPF of fabric samples is given in . The UPF of all non-treated fabric samples was lower and non-satisfactory. With the increase in yarn fineness, the UPF rating further decreased and vice-versa. The fabric samples T2 24, T4 2), and T5 24 showed better UPF than other samples due to the higher fabric thickness than the rest of the samples. The remaining samples exhibited below satisfactory results in UPF rating in the gray state, which needed treatment to get it enhanced. The fabric samples were tested again after treating with NLS because NLS has been found to enhance the UPF of fabric samples (Gangwar et al. Citation2021). The UPF of all fabric samples increased after the treatment with NLS. The UPF enhancement was found remarkable in the samples with a higher thickness than lower thickness fabric samples. The UPF of fabric samples containing 123 doubled after the NLS treatment. The samples T2 24, T4 24, and T5 24 exhibited remarkable improvement in UPF after finishing with NLS. The fabric samples made with coarser yarns with higher areal density showed higher UPF than fabrics with finer yarns and lower areal density, and vice-versa (). The fabric areal density and thickness played a vital role in deciding UPF fabric samples (Das Citation2010). The UPF of all fabric samples decreased after washing, indicating poor NLS affinity with both protein fibers (Pashmina and wool) but still significantly higher than the grey state. This challenge must be addressed in future work in this field. The fabric samples containing 246 yarns revealed higher UPF than 164 and 123 dtex yarns-based fabric samples T1 36 to T5 36 and T1 48 to T5 48.
Comfort behavior of fabric
Evaluating the fabric porosity in terms of pore size is of great importance as it strongly affects many transmission potentials like air, moisture, and liquid water; sound, UV light transmission plays a vital role during real applications (Kostajnšek et al. Citation2021). The measurement of pore size is presented in . The pore size of Pashmina: A wool union fabric was influenced by yarn linear density and Pashmina fiber content both. The pore size was increased by increasing the yarn dtex from 246s to 123 (Fabric sample T1 24, T1 36, and T1 48) from 30.96, 32.34, and 34.32 µ. The yarn diameter was reduced by increasing the yarn linear density in the direct system, which allowed more pore size in resultant fabric samples. The pore size was increased by decreasing the Pashmina fiber content from 100 to 35% with all three 246, 164, and 123 dtex of Pashmina: wool yarns. The pore size was enhanced from 30.96 to 34.34 in fabric samples T1 24 to T5 24, where Pashmina fiber content was decreased from 100 to 35%. A similar trend was observed in the case of 35 and 123dtex Pashmina: wool hybrid yarn fabrics. The pore size was increased 24.2% when Pashmina fiber content was reduced from 100 to 35% and yarn dtex enhanced from 246 to 123dtex.
Water vapor transmission behavior of fabric
The water vapor transmission behavior of fabric samples is shown in . The water vapor transmission rate was increased by reducing the yarn diameter by increasing the linear yarn density from 246 to 123 dtex in all five different blends of Pashmina and wool fiber. The water vapor transmission was increased by decreasing pashmina fiber content by decreasing the number of capillaries between the fibers. The water vapor transmission rate among the samples T1 24, T2 24, T3 24, T4 24, and T5 24 was found in increasing order and increased by 33% from T1 24 to T5 24. However, the effect of yarn dtex (linear density) on water vapor transmission rate was more prominent than Pashmina fiber content.
Moisture management
The wetting behavior of fabric samples is presented in . The wetting time of both the top and bottom surfaces was influenced by hybrid yarn linear density and the linear density of yarns. The top wetting time was found in increasing order by an increase in yarn linear density or yarn fineness. Both top and bottom absorption rates were influenced by hybrid yarn linear density and Pashmina fiber content in weft yarns. The top absorption rate was decreased by 19% from T1 24 to T5 24, where Pashmina fiber content was decreased from 100 to 35%, and the bottom absorption rate was decreased by 21.6%. The top and bottom absorption rates were decreased by increasing the yarn linear density from 246 to 123 dtex (). The top maximum wetted radius was also decreased by increasing yarn linear density and decreasing Pashmina fiber content because wool fiber has a higher fiber diameter with considerable moisture content (16.6%) as described in cotton and casein knitted fabrics (Rathinamoorthya Citation2017).
Table 5. Wetting behavior and moisture management potential of fabric samples.
The spreading speed (SS) is expressed as accumulative SS from the center to the maximum wetted radius (MWR) and measured in mm/sec. Spreading speed (SS; mm/sec) is defined as the accumulative SS from the center to the MWR. (Hu et al. Citation2005). The spreading rate of fabric sample T1 24 was found highest of 3.80 mm/sec and reduced to 3.22 mm/sec in the case of T5 48. The Pashmina fiber content was influenced the spreading rate on the top and bottom sides of the fabric. The hybrid yarn linear density also influenced the top and bottom spreading speed, and it was reduced in all five blends when yarn dtex changed from 246 to 123, which indicated that by decreasing Pashmina fiber content with wool, the water holding capacity of yarn increased as similarly concluded in case of plasma-treated polyester fabrics (Thangavelu and Chidambaram Citation2019). The smoothness and softness of the fiber and yarn also contribute to the spreading rate. In the test period, the accumulative one-way transport index (AOTI) is the difference in moisture accumulated between the inner and outer fabric surfaces. All fabric samples showed excellent AOTI, which may be attributed to the presence of both high moisture regain protein fiber.
Here, the studied fabrics of casein and cotton have the same structural parameters, and hence the difference may be due to the yarn structural factors. First of all, cotton yarn is found to have a higher twist per inch level compared to casein. This compact nature of the yarn reduces the transport of the water inside the intra-yarn space. Secondly, higher hairiness in the case in yarn and the increase in the surface roughness lead to a faster spreading rate along the surface, which is mainly governed by the surface troughs offered by the rough surface, as the wetting angle gets reduced. This yarn structural factor must be the valid reason for the lower spreading rate in cotton.
The overall moisture management capacity (OMMC) is an indicator to indicate the vast potential of the fabric to regulate liquid moisture transmission, which covers three performance features:
one-way liquid transport capacity (OWTC)
the moisture absorption rate of the bottom side (BAR)
the spreading/drying rate of the bottom side (SSb)
The OMMC values of the fabric samples are presented in , and the values were compared with the grading scale provided by the SDL Atlas. The higher values of OMMC indicate the overall higher moisture management potential. The OMMC of sample T1 24 was found 0.68, and that was increased to 0.75. The OMMC was decreased to 0.38 by decreasing the Pashmina fiber content from 100 to 35%, which indicated that Pashmina fiber played a decisive role in moisture management. The increasing yarn linear density was enhanced by the OMMC but decreased by reducing Pashmina fiber content from T1 to T5 blend.
Luster of fabric
The luster of fabric surfaces mainly depends on the nature of the interaction of light with the surface, and it influences by various factors like fiber cross-sectional shape, fabric surface evenness, light absorption, reflection, and transmission by the surface. The gray (unwashed) samples showed lower luster values than washed fabric samples, which may be attributed to the relaxation of frozen stresses from the fabric after washing, which caused the enhancement in surface evenness (Litim et al. Citation2017). The coarse linear density yarns-based fabric samples exhibited higher value than fine linear density yarn fabric in both grey and washed conditions, as similarly reported in another study (Rao and Gupta Citation1992). The samples having a significant proportion of Pashmina fibers showed higher lusture than higher wool fiber-containing fabrics (). The highest luster value obtained in sample T1 24 consisted of the coarsest weft with 100% Pashmina fiber content. The cloth cover factor shown in found a good relationship with luster values. An increase in a cloth cover increases the luster value of fabric samples, which may be attributed to a more uniform fabric surface at a high cloth cover.
Conclusions
In this study, yarn evenness, fabric moisture management properties, ultraviolet protection potential, lusture index, porosity, moisture vapor transmission rate were tested for Pashmina: wool blended union fabrics. Initially, yarns were spun by blending nylon as the third component, which was finally dissolved before inserting as filling yarn during fabric manufacturing. The study ends with following inferences:
Yarn unevenness was increased by increasing yarn linear density and by decreasing pashmina fiber content from 100 to 35%
Cloth cover and fabric thickness were slightly decreased by increasing yarn linear density and Pashmina fiber content.
The bending rigidity of fabric samples was decreased by increasing hybrid yarn linear density, and bending rigidity increased by decreasing Pashmina fiber content.
The sodium lignosulphonate (NLS) was found effective in enhancing the UPF of fabric samples.
The Lusture index of fabric samples was highest with 100% Pashmina fiber content, which was decreased by decreasing Pashmina fiber content.
The moisture vapor transmission rate was increased by increasing the hybrid yarn linear density used as weft yarn and decreased by increasing Pashmina fiber content.
OMMC was increased by decreasing Pashmina fiber content, which was enhanced by increasing hybrid yarn content.
Statistical analysis proved the significance of Pashmina fiber content with moisture management potential, UPF, and luster index.
The Pashmina fiber was beneficial for developing premium quality fabric, which will become a pathfinder for product development.
Disclosure statement
No potential conflict of interest was reported by the author(s).
Additional information
Funding
References
- Abreu, H. S., A. M. Nascimento, and M. A. Maria. 1999. Lignin structure and wood properties. Wood and Fiber Science 31:426–12.
- Bumla, N. A., S. A. Wani, D. B. Shakyawar, A. H. Sofi, I. Yaqoob, and F. D. Sheikh. 2012. Comparative study on quality of shawls made from hand and machine spun pashmina yarns. Indian Journal of Fibre and Textile Research 37:224–30.
- Das, B. 2010. UV radiation protective clothing. The Open Textile Journal 6 (3):14–21. doi:10.2174/1876520301003010014.
- Ganai, T. A. S., S. S. Misra, and F. D. Sheikh. 2011. Characterization and evaluation of pashmina producing changthangi goat of Ladakh. The Indian Journal of Animal Sciences 81:592–99.
- Gangwar, A. K. S., D. B. Shakyawar, M. K. Singh, P. Vishnoi, and S. Jose. 2021. Optimization of sodium lignosulfonate treatment on nylon fabric using box–behnken response surface design for UV protection. Autex Research Journal 21:1–10. doi:10.2478/aut-2021-0011.
- Gies, H. P., C. R. Roy, and G. Holmes. 2000. Ultraviolet radiation protection by clothing: Comparison of in vivo and in vitro measurements. Radiation Protection Dosimetry 91 (1):247–50. doi:10.1093/oxfordjournals.rpd.a033210.
- Hearle, J. W. S, and W. E. Morton. 2008. Physical properties of textile fibres 4th Edition. Amsterdam, Netherlands: Elsevier Publication.
- Hsieh, Y. L. 1995. Liquid transport in fabric structures. Textile Research Journal 65 (5):299–307. doi:10.1177/004051759506500508.
- Hu, J., Y. Li, K. W. Yeung, A. S. W. Wong, and W. Xu. 2005. Moisture management tester: A method to characterize fabric liquid moisture management properties. Textile Research Journal 75 (1):57–62. doi:10.1177/004051750507500111.
- Jancic, U., M. Bracic, A. Ojstrsek, M. Bozic, T. Mohan, and S. Gorgieva. 2021. Consolidation of cellulose nanofibrils with lignosulphonate bio-waste into excellent flame retardant and UV blocking membranes. Carbohydrate Polymers 251:1–13. doi:10.1016/j.carbpol.2020.117126.
- Kostajnšek, K., Z. Zupin, A. Hladnik, and K. Dimitrovski. 2021. Optical assessment of porosity parameters in transparent woven fabrics polymers. 13 (408):1–16. doi:10.3390/polym13030408.
- Kumar, A., D. B. Shakyawar, N. L. Meena, and S. M. K. Naqvi. 2020. Quality improvement of Dumba fleece using dehairing technique and value addition of recovered wool. Journal of Natural Fibers 19 (4):1–11. doi:10.1080/15440478.2020.1784818.
- Litim, N., A. Baffoun, F. Khoffi, M. Hamdaoui, S. B. Abdessalem, and B. Durand. 2017. Effect of finishing resins on mechanical and surface properties of cotton Denim fabrics. Journal of Textile Institute 108 (11):1863–70. doi:10.1002/14356007.a26_227.
- Majumdar, A., V. K. Kothari, and A. K. Mondal. 2010. Engineering of cotton fabrics for maximizing in vitro ultraviolet radiation protection. Photodermatology, Photoimmunology and Photomedicine 26 (6):290–96. doi:10.1111/j.1600-0781.2010.00545.x.
- Meena, H. C., D. B. Shakyawar, and R. K. Varshney. 2020. Low-Stress mechanical properties of wool-cotton blended fabrics. Journal of Natural Fibers 17:1–15. doi:10.1080/15440478.2021.1958408.
- Meena, H. C., D. B. Shakyawar, R. K. Varshney, A. Kumar, and R. Chattopadhyaya. 2021. Productivity, quality and comfort of Siro spun wool-cotton khadi fabrics. Journal of Textile Institute 112 (5):1–10. doi:10.1080/00405000.2021.1910400.
- Ozdemir, H. 2017. Permeability and wicking properties of modal and lyocell woven fabrics used for clothing. Journal of Engineered Fibers and Fabrics 12 (1):155892501701200102. doi:10.1177/155892501701200102.
- Raja, A. S. M., L. Ammayappan, D. B. Shakyawar, and N. P. Gupta. 2011. Production and performance of Angora rabbit hair-bharat merino wool blended shawls. Indian Journal of Small Ruminants 17:79–82.
- Rao, D., and V. B. Gupta. 1992. Physical and morphological charactertics of wool fibre. Indian Journal Fibre & Textile Research 17:1–8.
- Rathinamoorthya, R. 2017. Moisture management characteristics of knitted casein fabric. Indian Journal Fibre & Textile Research 42:488–92.
- Sarkar, A. K. 2007. On the relationship between fabric processing and ultraviolet radiation transmission. Photodermatology, Photoimmunology and Photomedicine 23 (5):191–96. doi:10.1111/j.1600-0781.2007.00306.x.
- Shakyawar, D. B., A. S. M. Raja, A. Kumar, P. K. Pareek, and S. A. Wani. 2013. Pashmina fiber: Production, characteristics and utilization. Indian Journal of Fibre and Textile Research 38:207–14.
- Singh, M. K., and B. K. Behera. 2021a. The effect of denier per filament (DPF) on low-stress mechanical and transmission behaviour of polyester filament fabrics. Journal of Textile Institute 113 (7):1–10. doi:10.1080/00405000.2021.1933807.
- Singh, M. K., and B. K. Behera. 2021b. Effect of fibre cross-sectional shape on bending behaviour of yarns and fabrics; part I. Journal of Textile Institute (5):1–10. doi:10.1080/00405000.2021.1906488.
- Sofi, A. H., S. A. Wani, D. B. Shakyawar, S. R. Ahmad, M. A. Pal, T. Nazir, A. A. Khan, H. Jalal, and M. Rovida. 2021. Subjective assessment of Pashmina and Pashmina blended knitted fabrics after nylon dissolution. International Journal of Livestock Research 11:123–28. doi:10.5455/ijlr.20201013120518.
- Sofi, A. H., S. A. Wani, D. B. Shakyawar, V. K. Malhotra, S. R. Ahmad, M. A. Pal, S. Beig, and A. A. Khan. 2018. Subjective evaluation of Pashmina and Pashmina blended knitted fabrics. Journal of Pharmacognosy and Phytochemistry 7:2686–89.
- Thangavelu, V., and P. Chidambaram. 2019. Comparison of moisture management properties of plasma treated single Jersey fabric with different types of polyester yarns. Fibers and TextileIn Eastern Europe 133 (1):32–36. doi:10.5604/01.3001.0012.7505.
- Wani, S. A., A. H. Sofi, D. B. Shakyawar, I. Yaqoob, F. A. Mattoo, and A. H. Malik. 2013. Fabrication of innovative charkha for pashmina spinning and its impact assessment. Journal of Textile Institute 104 (10):1141–44. doi:10.1080/00405000.2013.779056.
- Yaqoob, I., A. H. Sofi, A. W. Sarfaraz, F. D. Sheikh, and N. A. Bumla. 2012. Pashmina Shawl - A traditional way of making in Kashmir. Indian Journal of Fibre and Textile Research 11:329–33.
- Zhu, Q., and Y. Li. 2003. Effects of pore size distribution and fiber diameter on the coupled heat and liquid moisture transfer in porous textiles. International Journal of Heat and Mass Transfer 46 (26):5099–111. doi:10.1016/S0017-9310(03)00370-3.