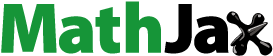
ABSTRACT
As the resources are declining globally, researchers are constantly looking for the development of new materials. The composite materials using natural fibers are one of the best solutions nowadays in this regard. In third-world countries, jute is produced abundantly. Moreover, banana is widely available due to their reproduction ability from an existing plant. This study involves the use of jute-glass fiber laminas and banana-glass fiber laminas with epoxy resin, individually, to produce hybrid laminated composites. Different Stacking orientations such as [0°/G/G/0°], [0°/G/G/30°], and [30°/G/G/30°] have been utilized for both jute and banana fibers to find the best hybrid laminated composite. The mechanical properties such as tensile, flexural, impact, hardness, and heat reversion properties along with some physical properties like density, specific gravity, and water absorption of these hybrid laminated composites have been tested according to the ASTM standards. The fracture surface has been examined using scanning electron microscopy (SEM) for microscopic visualization. It has been found from the experimental results that the jute-glass fiber composite shows better mechanical and physical properties, and among all the stacking orientations, [0°/G/G/0°] orientation provides higher tensile strength, flexural strength, and physical properties, whereas [0°/G/G/30°] orientation shows the better impact and hardness properties.
摘要
随着全球资源的减少,研究人员不断寻找新材料的开发. 使用天然纤维的复合材料是目前这方面的最佳解决方案之一. 在第三世界国家,黄麻产量丰富. 此外,香蕉由于其从现有植物中繁殖的能力而被广泛使用. 本研究涉及使用黄麻玻璃纤维薄板和香蕉玻璃纤维薄板与环氧树脂分别生产混合层压复合材料. 黄麻纤维和香蕉纤维都采用了不同的堆叠方向,如[0°/G/G/0°]、[0°/G/G/30°]和[30°/G/G/30°C],以找到最佳的混合层压复合材料. 根据ASTM标准测试了这些混合层压复合材料的力学性能,如拉伸、弯曲、冲击、硬度和热回复性能,以及一些物理性能,如密度、比重和吸水率. 使用扫描电子显微镜(SEM)对断裂表面进行了微观观察. 从实验结果中发现,黄麻玻璃纤维复合材料显示出更好的机械和物理性能,在所有粘结取向中,[0°/G/G/0°]取向提供了更高的拉伸强度、弯曲强度和物理特性,而[0°/G/G/30°]取向显示了更好的冲击和硬度性能.
Introduction
For a long time, specialists and researchers have been persistently trying to identify more novel materials that may accelerate the pace of advancement. Furthermore, nature consciousness is a seriously considered phenomenon right now. The natural fiber reinforced composite material is a progressive result of this inquiry because of the advantages of natural fibers over synthetic fibers. Natural fibers are getting more attention because, compared to synthetic fibers, the natural filaments offer lower thickness, accessibility, sustainability, recyclability, low handling use, excellent mechanical properties, and the simplicity of assortment and creation (Chandekar, Chaudhari, and Waigaonkar Citation2020; Chou Citation1992; Jawaid, Abdul Khalil, and Abu Bakar Citation2011; Leman et al. Citation2008; Rafiquzzaman, Abdullah, and Arifin Citation2015; Sapuan, Harimiand, and Maleque Citation2003; Schwartz Citation1997). Jute is plentiful in asian countries like Bangladesh, India, China, etc. Due to its good availability, it is now widely used in the composite field. Jute is being utilized in lieu of artificial fibers such as Kevlar, glass, etc., because of its cost-effectiveness, eco-friendly behavior, great versatility, adequate mechanical properties, etc. (Hossain et al. Citation2013; Rafiquzzaman et al. Citation2016). The banana is also one of the most ubiquitous plants on the planet. It is a part of the Musaceae family, and there are around 300 species, yet just 20 assortments are utilized for human welfare. Around 70 million metric tons of bananas are produced each year by the tropical and subtropical areas of the world (Anwar et al. Citation2009; Liu and Dai Citation2007; Umair Citation2006). Similar to most natural fibers, the jute and banana fibers show some drawbacks, such as a poor bonding between the matrix and fibers because of their hydrophilic properties and moisture-absorbing characteristics (Furtos et al. Citation2021; Mueller and Krobjilowski Citation2003; Reddy, Mohana Krishnudu, and Rajendra Prasad Citation2021). One of the serious issues related to the utilization of natural untreated fibers in the composites is their great moisture sensitivity, prompting an extreme decrease in the mechanical properties and delamination (Joshi et al. Citation2004). The lower mechanical properties might be because of the poor interfacial bonding between the matrix and fibers. Therefore, it is of great importance to change the fiber surface to render it progressively hydrophobic for better bonding with the resin matrix. For this reason, Mercerization and Acetylation are considered to be the best approaches to observing the hydrophobic characteristics of natural fibers (Panwar and Neelakrishnan Citation2021). Again, copolymerization is also widely used for the fibers to be more hydrophobic (Astorga-Rodríguez et al. Citation2018). Again, Natural fiber’s surface roughness, crystallinity, and wear resistance are greatly influenced by Mercerization and Acetylation effect (Behera et al. Citation2021; Leman, Syams Zainudin, and Ridzwan Ishak Citation2018; Matykiewicz et al. Citation2021; Pitchayya Pillai, Manimaran, and Vignesh Citation2021). Optimum solution determination is the predominant criterion for the Acetylation and Mercerization process as tensile strength and Young Modulus might show decreasing phenomena with the excessive addition of alkali solution(Aly et al. Citation2012). Similarly, fiber crystallinity can deteriorate without the use of appropriate perchloric acid solution in the Acetylation process which leads to a negative effect on the hardness properties of composites (Silva, Faria Maia, and Regina Mulinari Citation2021; Zhang et al. Citation2008).
Under the action of compression, tension, and bending, the polymeric composites encounter mechanical damage (Taj, Ali Munawar, and Khan Citation2007). So, it is crucial to use materials that provide high-scale damage tolerance and show better mechanical properties. The epoxy-based polymer composites provide great damage tolerance by using a tough matrix (Furtos, Baldea, and Silaghi-Dumitrescu Citation2016; Salih, Subhi Jasim, and Mousa Hasan Citation2015), supporting bi-directional woven textures (Kim et al. Citation2004), and sewing of fibers (Sela and Ishai Citation1989). Nevertheless, the hybrid composites are more developed compared to the traditional FRP composites because natural fibers exhibit different types of drawbacks such as poor interfacial bonding with matrix phase, high flammability as well as high moisture and water uptake phenomena compared with synthetic fibers which limit the idiosyncratic application of natural fibers in different industries such as Automobile. (Nurazzi et al. Citation2021; Syduzzaman et al. Citation2020). Whereas hybrid composites offer the most desirable properties as it acts as a single component comprising a weighted sum of different fibers with low and high moduli (Thwe and Liao Citation2002). Hybrid composites containing natural and synthetic fibers become popular among researchers over sole natural fibers oriented hybrid composites because of having different applicability and higher mechanical properties (Atmakuri et al. Citation2020). For instance, (Zhou et al. Citation2022) worked on the hybridization effect of glass fibers on bamboo fibers and found impact strength increased up to 370%. Similarly, sisal/glass hybrid composites showed an increasing trend for tensile strength with the increasing glass volume fraction (Arumugam et al. Citation2020). Natural fibers are mostly hybridized with glass fibers for application in numerous field because glass fibers offer a low-cost solution than carbon, aramid, etc. fibers as well as has compatible properties with natural fibers which ensure better hybridization (Shahzad and Ullah Nasir Citation2017; Vigneshwaran et al. Citation2020). Furthermore, different orientations of fibers or different plies and different volume fractions of the fibers are responsible for the variation in mechanical properties (Shahzad Citation2019). (Sujon, Habib, and Abedin Sujon, Ahsan Habib, and Zoynal Abedin Citation2020) experimented on the jute fiber at a constant volume fraction (25%) with different stacking orientations to evaluate the variation in tensile strength. Subsequently, the thickness also plays a vital role along with orientations according to (Banakar, Shivananda, and Niranjan Citation2012) as they evaluated the impact of thickness and fiber orientations on the glass/epoxy resin composite. They took three different orientations for each of the 2 mm and 3 mm thicknesses, and it has been observed that the tensile strength decreases with the increasing thickness. In addition, similar to the tensile strength, the orientation also affects the flexural strength (Sandeep et al. Citation2014). (Shuvescha, Parvin, and Rafiquzzaman Citation2017) analyzed the coconut midrib epoxy composite at different fiber orientations to identify the variation in hardness and impact strength along with flexural variation. In addition to the fiber orientations, different fiber contents or volume fractions of fibers may have effects on the mechanical properties of the hybrid composites (Kaleemulla and Siddeswarappa Citation2010). (Ramesh, Palanikumar, and Reddy Ramesh, Palanikumar, and Hemachandra Reddy Citation2016) worked on the jute-sisal-glass hybrid composite with volume of 40:0:60,0:40:60 and 20:20:60 to evaluate the mechanical properties like tensile, flexural, impact, etc. with two different orientations by modulating the volume fraction. It has been found that the 0 oriented hybrid composite provides better mechanical properties than the 90
oriented composite, and Jute-sisal-glass hybrid composite with a volume ratio of 0:40:60 provides the lowest strength where jute was absent. Following these, (Shuib et al. Citation2019) made a compression plate for the healing purpose of tibia fracture by maintaining the same stacking sequences between the bamboo fiber and glass fiber where only the orientation played a variable role. They analyzed different fiber orientations of the bamboo fiber to find out better tensile and flexural strength. Due to the fiber length variation, the mechanical properties of the banana-glass fiber composites change with the variation of fiber loading or volume fraction (Joseph et al. Citation2002).
Though researchers put great attention on hybrid composites with different stacking sequences using Jute/Glass and Banana/Glass individually, no work done regarding Jute/Glass or Banana/Glass where the different orientation of natural fibers (jute or Banana) plays a significant role in a constant stacking sequence. This novel work consists of 4 layers of hybrid composites fabrication following [0°J/G/G/0°J], [0°J/G/G/30°J], [30°J/G/G/30°J], [0°B/G/G/0°B], [0°B/G/G/30°B], and [30°B/G/G/30°B] arrangements and characterization of mechanical and physical properties to determine the best-oriented material as well comparing the hybridization effect of Jute and Banana fibers individually within identical arrangements. Consequently, composites were tested to evaluate their mechanical properties (e.g., tensile, flexural, impact, heat reversion, and hardness properties) and physical properties (e.g., density, specific gravity, and water absorption properties). The fracture surfaces were also investigated using scanning electron microscopy (SEM).
Experimental methodology
Materials collection
For preparing the jute-glass fiber and banana-glass fiber hybrid composites, the natural jute fiber was collected from a local jute mill situated in Khulna, Bangladesh. The natural banana fiber was collected from the “Eco-banana fiber extraction plant” in Shivganj, Bogura, Bangladesh. Bi-directional E-Glass fibers were obtained from local suppliers “Real Fibre Glass Industries,” Dhaka, Bangladesh. For binding purposes, the epoxy ly556 and hy951 were used and purchased from “Herenba Instruments and Engineering” located in Chennai, India. A handloom was utilized for unidirectional fiber-making purposes. The handloom bar was made from an ebonite material cutting shop in Khulna, Bangladesh. The mechanical and physical properties of the usable materials are listed in .
Table 1. The typical properties of the materials.
Materials preparation and fabrication process
In order to fabricate Jute-Glass and Banana-Glass hybrid composites, first assignment was unidirectional mat preparation using Jute and Banana individually. For that reason, a handloom was used to incorporate the fibers in straight direction for ensuring 0° parallel fibers. illustrates the unidirectional fiber materials and utilized handloom structure.
Figure 1. (a) Hand-loom, (b) jute fiber material, (c) banana fiber material, and (d) woven glass fiber.
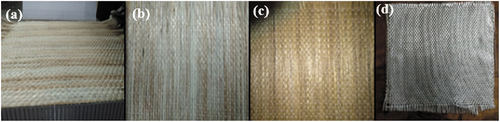
After completing the mat preparation, the unidirectional jute and banana fiber materials were cut into 19 cm × 25 cm size, weighted, and mixed with resin and hardener following 30:70 constant volume fraction shown in . Again, according to stoichiometric consideration, 11:1 ratio between epoxy resin and hardener was maintained. hand lay up technique was followed to fabricate the hybrid laminated composites. For both jute and banana fiber composites, the stacking sequences were the same. shows that the woven glass fiber was fixed between jute fiber or banana fiber materials. Here, three stacking sequences were common for both jute and banana fiber hybrid composites. Thereby, six laminates of hybrid composites: [0°J/G/G/0°J], [0°J/G/G/30°J], [30°J/G/G/30°J], [0°B/G/G/0°B], [0°B/G/G/30°B], and [30°B/G/G/30°B] were fabricated.
Figure 2. Stacking sequences of hybrid composites; (a) [0°/G/G/0°], (b) [0°/G/G/30°], and (c) [30°/G/G/30°].
![Figure 2. Stacking sequences of hybrid composites; (a) [0°/G/G/0°], (b) [0°/G/G/30°], and (c) [30°/G/G/30°].](/cms/asset/3e5d24de-1f4e-490a-b416-c9c6fdbfa8fe/wjnf_a_2143981_f0002_b.gif)
Table 2. Volume fraction control of all composite types.
Experimental testing procedures
Tensile testing
A dog-bone-shaped specimens were used for the tensile tests. To perform the tensile test, the ASTM D3039 was followed along with the dimension of the specimen was taken as 150 mm × 30 mm. Moreover, 300KN Shimadzu AGS-X universal testing machine (UTM) was used with 10 mm/min crosshead speed. The workpiece was exposed to an axial load while it was clamped on both sides of the jaws of the testing machine. Before the load was applied, a gauge length 30 mm was selected according to the composite material standard for the strain calculation. Furthermore, the ultimate force was recorded depending on the gauge length variation.
SEM analysis
The tensile strength difference between the jute-glass fiber and banana-glass fiber hybrid composite was illustrated utilizing the morphological view of their fracture surface by using the ZEISS EVO/18 Research Scanning Electron Microscope, Germany. Each sample was cut 10 mm above the fractured zone after the tensile test. The fractured surface was viewed at 50x, 100x, 150x, 250x, and 500x magnifications.
Flexural testing
The flexural properties of the hybrid composites were tested by a three-point loading framework, where the distance between the two static points was 110 mm, and the loading point applied force on the center of the specimen length. 135 mm × 20 mm dimension was maintained for each type of specimen according to the ASTM D790. A computerized INSTRON universal testing machine was used for the three-point bending test. A 10 KN load cell with a 2 mm/min cross-head speed was used to ensure continuous loading. Furthermore, the span length of the specimens was 80% of their original length following the ASTM instruction.
Impact testing
The impact strength of the jute-glass fiber and banana-glass fiber hybrid composites was tested using the “Semi-Automatic Digital ASTM Charpy Impact Testing Machine, Model: TFIT (ASTM).” For the impact test, the ASTM-A370 was followed. The specimen was gripped in an impact tester horizontally so that the pendulum strikes at the specimen’s v-nose with sufficient kinetic energy. The capacity of the Charpy impact tester was 400J.
Hardness testing
Rockwell hardness tests were carried out. In the Rockwell testing machine, a minor or primary force was delivered to the specimen using a ball indenter. But the Rockwell hardness value was derived from the initial and final depth conditions. The Rockwell hardness technique determines the permanent depth of the surface created by the ball indenter. For the Rockwell hardness method, the ASTM E-18 was followed. The specimen size was 10 mm × 10 mm.
Heat reversion testing
The heat reversion method is usually applied to determine the thermal resistance of a material against a high temperature. An electric oven was used for heating the composite materials and heat reversion (%) was calculated following Equationequation (1)(1)
(1) . Before putting into the oven, the composite specimen was marked at two points at a distance of 40 mm between them. Then the specimen was submerged into the diesel oil that had a flashing point of 85°C. After 15 minutes of heating, the specimen was removed from the oven, and the length between the marked points was measured.
Where, =
- L; L is the distance between marked points after test and
is the distance between marked points before test.
Density testing
For the determination of density, the dry weight of all specimens was measured using a 4-digit weight balance machine. Besides, the thickness of all specimens was measured by using digital slide calipers. Then the mass of each specimen was divided by its volume to find the density. It is noted that the density of the specimen means the apparent density of the specimen as the internal void was not considered.
Specific gravity testing
For the specific gravity measurement, the dry weight of each specimen was measured by a 4-digit weight balance machine. A 250 mL beaker full of water was employed, where each type of specimen was immersed with a fixed thread. Moreover, the weight of the specimen was determined cautiously so that the specimen was not in contact with the beaker’s sidewall. The following formula was followed for determining the specific gravity of all specimens:
Water absorption testing
The water absorption test was carried out to determine the exact moisture affinity of the jute-glass fiber and banana-glass fiber hybrid composites. A 120 mm × 20 mm sized rectangle specimen was used according to the ASTM-570. The dry weight of all specimens was measured by a 4-digit weight machine before immersing them into normal water. After a week, the weight gain of the submerged specimen was determined by percentage using the following equation:
Where, is the dry weight of the specimen, and
is the weight of the specimen after immersion.
Results and discussion
Tensile properties
The results of the tensile test for all hybrid laminates are recorded in . From the tensile test results, it was apparent that the jute-glass fibers-oriented hybrid composites possessed higher tensile strength than the banana-glass fiber-oriented hybrid composites for the same orientation. The comparative stress vs strain curves developed from the UTM for all types of hybrid laminates are exhibited in
Table 3. Tensile test results for all specimens.
The modulus of elasticity of all specimens was determined utilizing the linear portion of the stress-strain graph. When a specimen arrived at its yield quality, it began to act as a fragile material and started to break. illustrates the comparisons between all types of hybrid-oriented composites. It was observed that the [0°J/G/G/0°J] orientation provided the highest tensile strength of 106.50 MPa, whereas the [30°J/G/G/30°J] orientation delivered 80.21 MPa tensile strength only. The huge difference between these two tensile strengths was because of the different fiber orientations. For both jute and banana fibers, the 0 fibers at both upper and lower surfaces provided the highest tensile strength. But when the 0
fiber was replaced by 30
fiber, the tensile strength declined, and the strength was lowest when both of the upper and lower surface fibers were replaced by 30
fibers. As a result, the [0°J/G/G/0°J] orientation showed 106.5 MPa tensile strength but in the case of [0°J/G/G/30°J] and [30°J/G/G/30°J] orientations, the strength reduced by 13.33% and 24.67%, respectively. Similarly, this decreasing trend was followed by banana-glass fiber composite. The [0°B/G/G/0°B] orientation provided 84.82 MPa tensile strength, whereas the strength deteriorated by 19.02% and 48.96% for the [0°B/G/G/30°B] and [30°B/G/G/30°B] orientations, respectively. It was also noted that [0°B/G/G/0°B] orientation had higher tensile strength than the [30°J/G/G/30°J] orientation. The modulus of elasticity of the fiber was also affected by fiber orientation as the [0°J/G/G/0°J] orientation provided 12.22 GPa Young’s modulus but the [30°J/G/G/30°J] orientation delivered only 4.07 GPa. The banana-glass fiber composite also maintained this diminishing trend. Though normally, banana fiber shows very less but higher strength than the jute fiber. However, in this study jute-glass fiber composite shows higher strength than the banana-glass fiber composite. Similar to the tensile strength, the jute-glass fibers-oriented hybrid composites exhibited a superior modulus of elasticity compared to the banana-glass fiber-oriented hybrid composites for the same orientation.
SEM observation
The fractured surfaces were investigated extensively by Scanning Electron Microscope (SEM) to determine and characterize the microscopic mode of fractures as shown in . Generally, up to the elastic limit, the bonding between the matrix phase and fibers remains very strong. However, after the elastic limit, the adhesion characteristics become very weak. That’s why the matrix phase starts to crack with the increasing load. Usually, the fibers show higher strength than the matrix phase, which is the reason behind the cracking of the matrix phase before the fibers (Furtos et al. Citation2013; Jacob et al. Citation2005).
Figure 5. Morphological view of the [0b/G/G/
b] orientation; (i) (a) debonding, (b) banana fiber fracture, and (c) air void; (ii) (a) fiber failure and (b) debonding.
![Figure 5. Morphological view of the [0 ∘b/G/G/0∘b] orientation; (i) (a) debonding, (b) banana fiber fracture, and (c) air void; (ii) (a) fiber failure and (b) debonding.](/cms/asset/869a649f-f9dd-4213-9885-9b1e591d0acc/wjnf_a_2143981_f0005_oc.jpg)
Figure 6. Morphological view of the [30b/G/G/
b] orientation; (i) (a) matrix fracture, (b) banana fiber failure, and (c) air void; (ii) (a) fibers pull-out and (b) debonding.
![Figure 6. Morphological view of the [30 ∘b/G/G/30∘b] orientation; (i) (a) matrix fracture, (b) banana fiber failure, and (c) air void; (ii) (a) fibers pull-out and (b) debonding.](/cms/asset/9ebe7bb1-3b25-44e0-9a20-a8a1c39bfadd/wjnf_a_2143981_f0006_oc.jpg)
Figure 7. Morphological view of the [0j/G/G/0
j] orientation; (i) (a) delamination and (b) jute fibers pull-out; (ii) (a) jute fibers failure and (b) glass fibers debonding.
![Figure 7. Morphological view of the [0 ∘j/G/G/0 ∘j] orientation; (i) (a) delamination and (b) jute fibers pull-out; (ii) (a) jute fibers failure and (b) glass fibers debonding.](/cms/asset/3a9514c2-99a5-4fac-a76e-62ce9c49f4be/wjnf_a_2143981_f0007_oc.jpg)
Figure 8. Morphological view of the [30j/G/G/
j] orientation; (i) (a) delamination and (b) glass fibers pull-out and misalignment; (ii) (a) debris.
![Figure 8. Morphological view of the [30 ∘j/G/G/30∘j] orientation; (i) (a) delamination and (b) glass fibers pull-out and misalignment; (ii) (a) debris.](/cms/asset/d6642147-4e4c-4c26-93b9-7e5aba629e9e/wjnf_a_2143981_f0008_oc.jpg)
There are many factors for reducing strength, such as air voids, fiber orientations, adhesion or bonding, agglomeration, etc. It was observed that the matrix phase-fibers bonding started to loosen due to the applied load that affected the cracking of the banana fibers. At the high strength, the glass fibers initiated to break after ensuring the banana fibers pull-out due to the uneven transfer of stress between the fibers. This was the result of agglomeration that happened due to the fibers compacting together in the matrix phase. By comparing , it could be concluded that, as the matrix phase broke drastically in the [30°B/G/G/30°B] orientation, its fibers pull-out occurred at a lower strength than the [0°B/G/G/0°B] orientation. Concurrently, the 30° banana fibers were not sufficiently strong to hold against the crack propagation because the load-bearing fibers were too weak compared to the 0° banana fibers. Furthermore, the matrix and fibers delamination were a big issue for the fracture before a considerable load. But the [0°B/G/G/0°B] orientation delivered a great tensile strength because of its availability of high load-carrying fibers, even after its matrix phase got broken after debonding. (Braga and Magalhaes Citation2015) observed the microstructure of Jute-Glass hybrid composites using SEM and saw a few voids between matrix and jute fibers because of having random fibers pullout. Similarly, we observed the pull-out of jute fibers and glass fibers occurred at the rear side as shown in respectively.
Nevertheless, adequate interfacial bonding between matrix phase and fibers can reduce the possibility of earlier cracking as matrix can transfer stress toward high load carrying fibers (Furtos et al. Citation2012). It was clearly observed from that the pull-out of jute fibers and glass fibers occurred at the rear side in the [0°J/G/G/0°J] orientation. The matrix-phase bonded with the fibers comparatively better than other combinations. As the strong fibers were capable to carry a high-scale load, the fibers were able to withstand the increasing load. But shows that the [30
J/G/G/
J] orientation had high delamination and pull-out of fibers. On its upper surface, some debris was visible, which influenced the reduction of its strength. Besides, more delamination had been found in the
jute fibers compared to the 0° jute fibers. As high stress acted on the small concentrated surface of [30
J/G/G/
J] orientation, the high-scale delamination happened. Therefore, its weak fibers were unable to carry high loads.
Flexural properties
The flexural properties of the six different types of hybrid laminates were estimated with the UTM. The flexural test results are summed up in . The results revealed that similar to the tensile strength, the jute-glass fiber hybrid composites showed superior flexural strength than the banana-glass fiber hybrid composites for the same orientation.
Table 4. Flexural test results for all specimens.
Before the load reaches its capacity it is distributed evenly between the fibers and matrix in the laminates. The crack starts where the fiber-matrix adhesion is poor and begins to spread over the entire length of the laminate section. The density of all specimens was between 990 and 1350 kg/m3, but the jute-glass hybrid composite had higher density than the banana-glass hybrid composite for the same orientation. For both jute-glass fiber and banana-glass fiber hybrid composites, the [0°J/G/G/0°J] and [0°B/G/G/0°B] orientations had the highest densities of 1347.6 kg/m3 and 1191.85 kg/m3, respectively. However, the [0°J/G/G/30°J] and [0°B/G/G/30°B] orientations showed the least densities of 1115.4 kg/m3 and 994.209 kg/m3, respectively, because of the dissimilarly oriented fibers. The comparative stress vs strain curves developed from the UTM for all types of hybrid laminates are illustrated in . The flexural modulus of all specimens was determined using the linear portion of the stress-strain graph. The flexural strength varied with the change of orientation for both jute and banana fibers. The comparison between the jute-glass fiber and banana-glass fiber hybrid laminates in terms of flexural behavior is shown in , where it was apparent that the [0°J/G/G/0°J] orientation provided the highest flexural strength of 118.022 MPa, whereas the [30°B/G/G/30°B] orientation delivered only 53.723 MPa. Moreover, the difference between the [0°J/G/G/0°J] and [0°B/G/G/0°B] orientations was 19.668 MPa, whereas, for the [0°J/G/G/30°J] and [0°B/G/G/30°B] orientations, the difference was only 7.284 MPa in terms of flexural strength. With the change of orientation, the jute-glass fiber and banana-glass fiber hybrid laminates showed similar alteration patterns in terms of strength. When the [0°J/G/G/0°J] orientation was replaced by [0°J/G/G/30°J] and [30°J/G/G/30°J] orientations, the flexural strength decreased by 24.8% and 34%, respectively. But when the [0°B/G/G/0°B] orientation was supplanted by [0°B/G/G/30°B] and [30°B/G/G/30°B] orientations, the strength reduced by 17.17% and 45.38%, respectively. Moreover, the [0°J/G/G/0°J] orientation showed Young’s modulus of 14.586 GPa, whereas the [0°B/G/G/0°B] orientation exhibited 8.0031 GPa only. However, Young’s modulus did not follow any specific pattern with the change of orientation in the bending test.
Impact properties
The impact test was carried out for the six different hybrid laminates, where the energy loss was detected by the Charpy impact tester. It was observed that the impact test result was different from the previous flexural and tensile tests in terms of orientation. The diverse stacking sequences can alter the distinctive strength parameters such as the dissipation energy, initiation energy, and total energy (Pothan, Thomas, and George Citation1999). Due to the pendulum tip’s striking on the composite, the crack initiated to propagate; but before cracking, some amount of energy got absorbed in the fiber. The crack could not propagate linearly as the resin acted as a matrix phase in between the fibers. In order to compare the impact values of jute-glass fiber and banana-glass fiber hybrid composites, has been developed. It was observed that the [0°J/G/G/30°J] orientation had a higher impact strength than the [0°J/G/G/0°J] orientation. Because when the 0° fiber of the lower surface was replaced by 30° fibers, the crack experienced different types of surfaces on the upper and lower surfaces of the specimen. Therefore, the crack covered more specimen surface area and took more time to propagate, thus enhancing the energy absorption (Navaneethakrishnan et al. Citation2019). Similarly, the [30J/G/G/30
J] orientation had an average impact strength of 309.469 kJ/m2 because of having the same 30
fibers on both sides. A similar phenomenon happened in the banana-glass fiber hybrid composite. The [0
B/G/G/30
B] orientation absorbed an average impact strength of 431.034 kJ/m2, whereas the [0
B/G/G/0
B] and [30
B/G/G/30
B] orientations absorbed only 404.103 kJ/m2 and 346.119 kJ/m2, respectively. Moreover, the [0
J/G/G/
J] orientation absorbed average impact energy of 12.209 J but the [0
B/G/G/0
B] orientation absorbed 14.514J. The composite thickness and volume fraction are the major influencing factors for the variation in impact strength.
When the thickness and fiber volume fraction amplify, the adjusted fibers require high energy to break down (Jiyas, Kumar, and John Citation2016). It is apparent that the banana-glass hybrid composite always had a slightly higher thickness than the jute-glass hybrid composite, even though the same volume fraction was maintained for both of them. Therefore, all banana-glass fiber hybrid composite orientations showed higher impact energy than the jute-glass fiber hybrid composite because of their difference in thickness only.
Hardness properties
The comparison among their average hardness numbers is shown in . The experimental results showed that the jute-glass fiber hybrid composite exhibited a higher hardness value than the banana-glass fiber hybrid composite for the same orientation. The [0°J/G/G/0°J] orientation had an average hardness number of 96.5 HRB, whereas the [0°B/G/G/0°B] orientation showed only 77.166 HRB. Similarly, the [0°J/G/G/30°J] and [30°J/G/G/30°J] orientations had larger HRB values than the [0°B/G/G/30°B] and [30°B/G/G/30°B] orientations, respectively. So, the jute-glass fiber hybrid composite was harder than the banana-glass fiber hybrid composite. Moreover, the fiber orientation greatly influenced the hardness of the composite surface. The [0°J/G/G/30°J] orientation had higher hardness than the [0°J/G/G/0°J] and [30°J/G/G/30°J] orientations. Similarly, the [0°B/G/G/30°B] orientation was harder than the [0°B/G/G/0°B] and [30°B/G/G/30°B] orientations. So, similar to the impact strength, the dissimilarly oriented fibers on the upper and lower surfaces of the composites exhibited higher hardness than the similarly oriented fibers. Although the value of HRB greatly fluctuated among the banana-glass fiber hybrid composite orientations, the various orientations of jute-glass fiber hybrid composite showed slight differences.
Heat reversion properties
For determining the ability of the composites to withstand heat, the heat reversion test was carried out at 60°C, 80°C, 100°C, 120°C, 140°C, and 150°C temperatures. When the temperature goes down to room temperature residual stress formed on composites structures which has significant impact on materials properties. But the level of residual stress mostly depends on the temperature difference between heated specimen and exposed room temperature, expansion or shrinkage thermal co-efficient, volume fraction and elastic co-efficient of materials inside fibers (Parlevliet, Bersee, and Beukers Citation2007). Consequently, (Butylina, Martikka, and Kärki Citation2013) conducted the heat reversion analysis on wood reinforced composites and found that with the increasing volume fraction of fibers, linear thermal expansion/shrinkage decreased. Again, heat reversion value of different volume fractioned composites showed an abrupt change without any clear trend. Though in our experiment, we kept a constant volume fraction for all considerations, two different fibers stacked with matrix at different orientation. Where gap between oriented fibers, dissimilar orientation in [0B/G/G/30°B], [0
J/G/G/30°J] combinations and elastic and thermal co-efficient difference between fibers might have great influence on heat reversion results shown in . It was obvious that the temperature effect on the jute-glass fiber and banana fiber hybrid composites was very low. Up to 100°C, all the specimens had constant length. The [30
J/G/G/
J] orientation showed no fluctuation in length due to the temperature variation, whereas the [0
B/G/G/0°B] orientation showed higher sensibity i.g. 3.75% heat reversion up to 140°C but it again reduced to 1.25% at 150°C shown in . Similarly when the temperature was modulated from 140°C to 150°C, [0
B/G/G/
B] composite showed 2.5% contraction characteristics, whereas the jute-glass fiber composite orientations remained unaltered in length. Among all the orientations, the [30
J/G/G/30°J] and [0
B/G/G/30°B] orientations showed slightly better resistance against the thermal change.
Table 5. Heat Reversion (%) value for all specimens.
Density properties
Generally, density of a composite depends on the relative proportion of matrix and reinforcing materials and this is one of the most important factors determining the properties of the composites. The densities obtained for all hybrid composites are presented in . The density of all specimens was between 990 kg/m3 and 1350 kg/m3, but the jute-glass hybrid composite had a higher density than the banana-glass hybrid composite for the same orientation. For both jute-glass fiber and banana-glass fiber hybrid composites, the [0°J/G/G/0°J] and [0°B/G/G/0°B] orientations had the highest densities of 1347.594 kg/m3 and 1191.846 kg/m3, respectively. However, the [0°J/G/G/30°J] and [0°B/G/G/30°B] orientations showed the least densities of 1115.4 kg/m3 and 994.209 kg/m3, respectively, because of the dissimilarly oriented fibers.
Table 6. Density values for all specimens.
Specific gravity properties
The specific gravity was evaluated for all hybrid laminated composites as listed in . Though the difference was marginal for different orientations, the jute-glass fiber hybrid composite had higher specific gravity than the banana-glass fiber hybrid composite. The [0°J/G/G/30°J] orientation had the highest specific gravity, whereas the [0°B/G/G/30°B] orientation had the least specific gravity.
Table 7. Specific gravity values for all specimens.
Water absorption properties
The water absorption behavior of the different orientations of hybrid composites was examined against the periodical time-frame. It could be easily concluded that the banana-glass fiber hybrid composite exhibited better water absorption capability than the jute-glass fiber hybrid composite at any orientation. The water absorption ability can be significantly affected due to the compatibility between the fibers, and the absorption of the polymer composite improves due to the voids and flaws of the fibers (Kulkarni et al. Citation2008). In , the water absorption percentage vs immersion time has been shown to explore the water affinity behavior of different orientations of composites. The highest absorption for the [0°J/G/G/0°J] orientation was 10.218% at the end of 11th week, whereas the percentage of absorption by the [0°B/G/G/0°B] orientation was 18.268% at the same time period. After 11th week, both hybrid composites began to lose their moisture contents. But there was a distinction between the [0°J/G/G/30°J] and [0°B/G/G/30°B] orientations. After 11th week, the [0°J/G/G/30°J] orientation started to release water but even then, the [0°B/G/G/30°B] orientation continued to absorb water until 12th week. After that, it started to release water. Here, the fiber orientations played a great role in water absorption. After 4 weeks, the [0°J/G/G/0°J] orientation absorbed 6.289% water. When both upper and lower surfaces had 0° fibers, the water permeability was the same on both sides. But when one of the surfaces was substituted by a 30° fiber, e.g., the [0°J/G/G/30°J] orientation, the water entering path got reduced because the two sides provided different characteristics paths for water. So, the absorption percentage got reduced to 1.763% only. Again, when the 0° fibers of the both surfaces of the hybrid composite were replaced by 30° fibers, e.g., the [30°J/G/G/30°J] orientation, both sides exhibited the same characteristics for the water molecule entrance. Therefore, its absorption percentage got increased to 6.196% after 4 weeks. A similar tendency was shown by the banana-glass hybrid composite, where the [0°B/G/G/30°B] orientation had a lower
water absorption compared to the [0°B/G/G/0°B] and [30°B/G/G/30°B] orientations. Furthermore, along with the water absorption, the thickness of the hybrid composites got altered. The variation of thickness with the immersion time has been presented in . The thickness showed a proportional relationship with the water absorption. When the moisture content increased, the thickness of all specimens gradually enhanced. Similarly, the releasing of the moisture content lowered their thickness.
Conclusion
This paper evaluated the physical and mechanical properties of the jute-glass fiber and banana-glass fiber hybrid composites by employing the appropriate standard testing methods. The specimen size was precisely maintained for all experiments. For all orientations, the same volume fraction of the fibers and resin was effectively maintained for ensuring less void fraction. The experimental results showed that the orientation played a vital role in determining the physical properties. The [0°J/G/G/0°J] and [0°B/G/G/0°B] orientations showed higher tensile and flexural strength compared to the other orientations of the same hybrid composite. In addition, the decreasing characteristics were shown by both jute-glass fiber and banana-glass fiber hybrid composites when the 0° fibers got replaced by 30° fibers. However, in the impact and hardness tests, the [0°J/G/G/30°J] and [0°B/G/G/30°B] orientations provided higher strength than the other orientations due to their crack propagation mechanism. But by SEM fracture mode analysis and from the physical performance tests, we concluded that the [0°J/G/G/0°J] and [0°B/G/G/0°B] orientations had remarkable properties and internal structures.
Highlights
A novel natural fiber composite which is sustainable and possesses excellent mechanical properties
High fracture strength as well as other mechanical properties such as tensile, flexural and impact
Fiber orientation has a significant effect on physical and mechanical properties
Ethical approval
There are no human subjects in this article and informed consent is not applicable.
Ethical statement
This is the original work of the authors and has never been published anywhere else. The paper is not being looked at for publication anywhere else at the moment. Previous works are cited in the text and references are maintained appropriately.
Acknowledgments
We thank all the staff of the Solid Mechanics Laboratory, Department of Mechanical Engineering at Khulna University of Engineering and Technology for their assistance in completing the mission.
Disclosure statement
No potential conflict of interest was reported by the author(s).
Data availability statement
The data required to reproduce these findings can be shared upon request.
Additional information
Funding
References
- Aly, M., M.S.J. Hashmi, A.G. Olabi, K.Y. Benyounis, M. Messeiry, A.I. Hussain, and E.F. Abadir. 2012. Optimization of alkaline treatment conditions of flax fiber using Box–Behnken method. Journal of Natural Fibers 9 (4):256–20. doi:10.1080/15440478.2012.738036.
- Anwar, U.M.K., M.T. Paridah, H. Hamdan, S. M. Sapuan, and E.S. Bakar. 2009. Effect of curing time on physical and mechanical properties of phenolic-treated bamboo strips. Industrial Crops and Products 29 (1):214–19. doi:10.1016/j.indcrop.2008.05.003.
- Arumugam, S., J. Kandasamy, A. U. Shah, M. T. Hameed Sultan, S. N. A. Safri, M. Shukry Abdul Majid, A. Azriff Basri, and F. Mustapha. 2020. Investigations on the mechanical properties of glass fiber/sisal fiber/chitosan reinforced hybrid polymer sandwich composite scaffolds for bone fracture fixation applications. Polymers 12 (7):1501. doi:10.3390/polym12071501.
- Astorga-Rodríguez, J. E., I. Eugenia Martínez-Rodríguez, L. M. García-de la Parra, M. Betancourt-Lozano, R. C. Vanegas-Pérez, C. A. P. de León-Hill, and J. Ruelas-Inzunza. 2018. Lead and cadmium levels in mussels and fishes from three coastal ecosystems of NW Mexico and its potential risk due to fish and seafood consumption. Toxicology and Environmental Health Sciences 10 (3):203–11. doi:10.1007/s13530-018-0365-1.
- Atmakuri, A., A. Palevicius, A. Vilkauskas, and G. Janusas. 2020. Review of hybrid fiber based composites with nano particles—material properties and applications. Polymers 12 (9):2088. doi:10.3390/polym12092088.
- Banakar, P., H.K. Shivananda, and H.B. Niranjan. 2012. Influence of fiber orientation and thickness on tensile properties of laminated polymer composites. International Journal of Pure and Applied Sciences and Technology 9 (1):61. https://citeseerx.ist.psu.edu/viewdoc/download?doi=10.1.1.419.7778&rep=rep1&type=pdf.
- Behera, S., R. Kumar Gautam, S. Mohan, and A. Chattopadhyay. 2021. Dry sliding wear behavior of chemically treated sisal fiber reinforced epoxy composites. Journal of Natural Fibers 1–14. doi:10.1080/15440478.2021.1904483.
- Braga, R.A., and P.A.A. Magalhaes Jr. 2015. Analysis of the mechanical and thermal properties of jute and glass fiber as reinforcement epoxy hybrid composites. Materials Science and Engineering: C 56:269–73. doi:10.1016/j.msec.2015.06.031.
- Butylina, S., O. Martikka, and T. Kärki. 2013. Thermal performance and optical properties of wood–polymer composites. Journal of Thermoplastic Composite Materials 26 (1):60–73. doi:10.1177/0892705711419694.
- Chandekar, H., V. Chaudhari, and S. Waigaonkar. 2020. A review of jute fiber reinforced polymer composites. Materials Today: Proceedings 26:2079–82. doi:10.1016/j.matpr.2020.02.449.
- Chou, T.-W. 1992. Microstructural design of fiber composites. NASA STI/Recon Technical Report A 92:50452. doi:10.1016/0266-3538(93)90101-L.
- Furtos, G., B. Baldea, and L. Silaghi-Dumitrescu. 2016. Development of new radiopaque glass fiber posts. Materials Science and Engineering: C 59:855–62. doi:10.1016/j.msec.2015.10.091.
- Furtos, G., L. Molnar, L. Silaghi-Dumitrescu, P. Pascuta, and K. Korniejenko. 2021. Mechanical and thermal properties of wood fiber reinforced geopolymer composites. Journal of Natural Fibers 1–16. doi:10.1080/15440478.2021.1929655.
- Furtos, G., L. Silaghi-Dumitrescu, M. Moldovan, B. Baldea, R. Trusca, and C. Prejmerean. 2012. Influence of filler/reinforcing agent and post-curing on the flexural properties of woven and unidirectional glass fiber-reinforced composites. Journal of Materials Science 47 (7):3305–14. doi:10.1007/s10853-011-6169-1.
- Furtos, G., M. Tomoaia‐cotisel, B. Baldea, and C. Prejmerean. 2013. Development and characterization of new AR glass fiber‐reinforced cements with potential medical applications. Journal of Applied Polymer Science 128 (2):1266–73. doi:10.1002/app.38508.
- Hossain, R.M., A. Islam, A.W. Van Vuure, and V. Ignaas. 2013. Effect of fiber orientation on the tensile properties of jute epoxy laminated composite. Journal of Scientific Research 5 (1):43–54. doi:10.3329/jsr.v5i1.10519.
- Jacob, M., S. Joseph, L. A. Pothan, and S. Thomas. 2005. A study of advances in characterization of interfaces and fiber surfaces in lignocellulosic fiber-reinforced composites. Composite Interfaces 12 (1–2):95–124. doi:10.1163/1568554053542115.
- Jawaid, M., H.P.S. Abdul Khalil, and A. Abu Bakar. 2011. Woven hybrid composites: Tensile and flexural properties of oil palm-woven jute fibres based epoxy composites. Materials Science and Engineering: A 528 (15):5190–95. doi:10.1016/j.msea.2011.03.047.
- Jiyas, N., B. Kumar, and M. John. 2016. Synthesis and mechanical characterization of woven banana and glass fiber reinforced epoxy composites. IJSER 7:32–38.
- Joseph, S., M.S. Sreekala, P. K. Zachariah Oommen, and S. Thomas. 2002. A comparison of the mechanical properties of phenol formaldehyde composites reinforced with banana fibres and glass fibres. Composites Science and Technology 62 (14):1857–68. doi:10.1016/S0266-3538(02)00098-2.
- Joshi, S. V., L.T. Drzal, A.K. Mohanty, and S. Arora. 2004. Are natural fiber composites environmentally superior to glass fiber reinforced composites? Composites: Part A, Applied Science and Manufacturing 35 (3):371–76. doi:10.1016/j.compositesa.2003.09.016.
- Kaleemulla, K. M., and B. Siddeswarappa. 2010. Influence of fiber orientation on the in-plane mechanical properties of laminated hybrid polymer composites. Journal of Reinforced Plastics and Composites 29 (12):1900–14. doi:10.1177/0731684409340806.
- Kim, J., M. Shioya, H. Kobayashi, J. Kaneko, and M. Kido. 2004. Mechanical properties of woven laminates and felt composites using carbon fibers. Part 1: In-plane properties. Composites Science and Technology 64 (13–14):2221–29. doi:10.1016/j.compscitech.2004.03.012.
- Kulkarni, R.R., K.K. Chawla, U.K. Vaidya, M.C. Koopman, and A.W. Eberhardt. 2008. Characterization of long fiber thermoplastic/metal laminates. Journal of Materials Science 43 (13):4391–98. doi:10.1007/s10853-007-2437-5.
- Leman, Z., S.M. Sapuan, M.M.H.M. Azwan, M. Mohamad Hamdan Megat Ahmad, and M.A. Maleque. 2008. The effect of environmental treatments on fiber surface properties and tensile strength of sugar palm fiber-reinforced epoxy composites. Polymer-Plastics Technology and Engineering 47 (6):606–12. doi:10.1080/03602550802059451.
- Leman, Z., E. Syams Zainudin, and M. Ridzwan Ishak. 2018. Effectiveness of alkali and sodium bicarbonate treatments on sugar palm fiber: Mechanical, thermal, and chemical investigations. Journal of Natural Fibers. doi:10.1080/15440478.2018.1537872.
- Liu, X.Y., and G.C. Dai. 2007. Surface modification and micromechanical properties of jute fiber mat reinforced polypropylene composites. Express Polymer Letters 1 (5):299–307. doi:10.3144/expresspolymlett.2007.43.
- Matykiewicz, D., M. Barczewski, O. Mysiukiewicz, and K. Skórczewska. 2021. Comparison of various chemical treatments efficiency in relation to the properties of flax, hemp fibers and cotton trichomes. Journal of Natural Fibers 18 (5):735–51. doi:10.1080/15440478.2019.1645792.
- Mueller, D. H., and A. Krobjilowski. 2003. New discovery in the properties of composites reinforced with natural fibers. Journal of Industrial Textiles 33 (2):111–30. doi:10.1177/152808303039248.
- Navaneethakrishnan, G., T. Karthikeyan, S. Saravanan, V. Selvam, N. Parkunam, G. Sathishkumar, and S. Jayakrishnan. 2019. Structural analysis of natural fiber reinforced polymer matrix composite. Materials Today: Proceedings 21 (1):7–9. doi:10.1016/j.matpr.2019.05.295.
- Nurazzi, N.M., M.R.M. Asyraf, S. Fatimah Athiyah, S.S. Shazleen, S. Ayu Rafiqah, M.M. Harussani, S.H. Kamarudin, M.R. Razman, M. Rahmah, and E.S. Zainudin. 2021. A review on mechanical performance of hybrid natural fiber polymer composites for structural applications. Polymers 13 (13):2170. doi:10.3390/polym13132170.
- Panwar, A., and S. Neelakrishnan. 2021. An experimental study on the effect of mercerization parameters on the variation in the chemical composition and mechanical properties of natural fibers: Coir. Journal of Natural Fibers 1–11. doi:10.1080/15440478.2021.1993505.
- Parlevliet, P. P., H. E. Bersee, and A. Beukers. 2007. Residual stresses in thermoplastic composites–a study of the literature. Part III: Effects of thermal residual stresses. Composites: Part A, Applied Science and Manufacturing 38 (6):1581–96. doi:10.1016/j.compositesa.2006.12.005.
- Pitchayya Pillai, G., P. Manimaran, and V. Vignesh. 2021. Physico-chemical and mechanical properties of alkali-treated red banana peduncle fiber. Journal of Natural Fibers 18 (12):2102–11. doi:10.1080/15440478.2020.1723777.
- Pothan, L. A., S. Thomas, and J. George. 1999. “Tensile and impact properties of banana fiber/glass fiber hybrid polyester composites.” 12th International Conference on Composite Materials, Paris, France.
- Rafiquzzaman, M., S. Abdullah, and A.M.T. Arifin. 2015. Behavioural observation of laminated polymer composite under uniaxial quasi-static and cyclic loads. Fibers and Polymers 16 (3):640–49. doi:10.1007/s12221-015-0640-6.
- Rafiquzzaman, M., M. Islam, H. Rahman, S. Talukdar, and N. Hasan. 2016. Mechanical property evaluation of glass–jute fiber reinforced polymer composites. Polymers for Advanced Technologies 27 (10):1308–16. doi:10.1002/pat.3798.
- Ramesh, M., K. Palanikumar, and K. Hemachandra Reddy. 2016. Influence of fiber orientation and fiber content on properties of sisal‐jute‐glass fiber‐reinforced polyester composites. Journal of Applied Polymer Science 133 (6). doi: 10.1002/app.42968.
- Reddy, P. V., D. Mohana Krishnudu, and P. Rajendra Prasad. 2021. A study on alkali treatment influence on prosopis juliflora fiber-reinforced epoxy composites. Journal of Natural Fibers 18 (8):1094–106. doi:10.1080/15440478.2019.1687063.
- Salih, S. I., A. Subhi Jasim, and A. Mousa Hasan. 2015. Investigation on mechanical properties of hybrid polymer composite reinforced by rice husks and date palm fibers as a construction material. Al-Nahrain Journal of Science 18 (3):89–97. doi:10.22401/JNUS.18.3.13.
- Sandeep, M.B., D. Choudhary, M. N. Inamdar, and M. Q. Rahaman. 2014. Experimental study of effect of fiber orientation on the flexural strength of glass/epoxy composite material. International Journal of Research in Engineering and Technology 3 (9):208–11. doi:10.15623/ijret.2014.0309032.
- Sapuan, S.M., M. Harimiand, and M.A. Maleque. 2003. Mechanical properties of epoxy/coconut shell filler particle composites. Arabian Journal for Science and Engineering 28 (2):171–82.
- Schwartz, M. M. 1997. Composite materials: Properties, nondestructive testing, and repair. Vol. 1. Prentice Hall. https://www.osti.gov/biblio/293032
- Sela, N., and O. Ishai. 1989. Interlaminar fracture toughness and toughening of laminated composite materials: A review. Composites 20 (5):423–35. doi:10.1016/0010-4361(89)90211-5.
- Shahzad, A. 2019. Investigation into fatigue strength of natural/synthetic fiber-based composite materials. In Mechanical and physical testing of biocomposites, fibre-reinforced composites and hybrid composites, 215–39. Elsevier. doi:10.1016/B978-0-08-102292-4.00012-6.
- Shahzad, A., and S. Ullah Nasir. 2017. Mechanical properties of natural fiber/synthetic fiber reinforced polymer hybrid composites. In Green biocomposites, 355–96. Springer. doi:10.1007/978-3-319-46610-1_15.
- Shuib, S., N. F. Ismail, M. N. Nazri, and A. Z. Romli. 2019. Bamboo and glass fibre hybrid laminated composites as Locking Compression Plate (LCP) for tibia fracture treatment. Journal of Physics: Conference Series 1150: 012028.doi: 10.1088/1742-6596/1150/1/012028.
- Shuvescha, D., R. Parvin, and M.D. Rafiquzzaman. 2017. Fibre orientation effect on mechanical properties of coconut leaf midrib reinforced polymer composite. European Journal of Advances in Engineering and Technology 4 (12):914–19.
- Silva, N. G., T. Faria Maia, and D. Regina Mulinari. 2021. Effect of acetylation with perchloric acid as catalyst in sugarcane bagasse waste. Journal of Natural Fibers 1–15. doi:10.1080/15440478.2021.1875352.
- Sujon, M. A. S., M. Ahsan Habib, and M. Zoynal Abedin. 2020. Experimental investigation of the mechanical and water absorption properties on fiber stacking sequence and orientation of jute/carbon epoxy hybrid composites. Journal of Materials Research and Technology 9 (5):10970–81. doi:10.1016/j.jmrt.2020.07.079.
- Syduzzaman, M., M. Abdullah Al Faruque, K. Bilisik, and M. Naebe. 2020. Plant-based natural fibre reinforced composites: A review on fabrication, properties and applications. Coatings 10 (10):973. doi:10.3390/coatings10100973.
- Taj, S., M. Ali Munawar, and S. Khan. 2007. Natural fiber-reinforced polymer composites. Proceedings-Pakistan Academy of Sciences 44 (2):129.
- Thwe, M. M., and K. Liao. 2002. Effects of environmental aging on the mechanical properties of bamboo–glass fiber reinforced polymer matrix hybrid composites. Composites: Part A, Applied Science and Manufacturing 33 (1):43–52. doi:10.1016/S1359-835X(01)00071-9.
- Umair, S. 2006. “Environmental effect of fiber composite materials-study of life cycle assessment of materials used for ship structure.” MS Thesis Dissertation, Royal Institute of Technology, Stockholm. http://urn.kb.se/resolve?urn=urn:nbn:se:kth:diva-46483
- Vigneshwaran, S., R. Sundarakannan, K.M. John, R. Deepak Joel Johnson, K. Arun Prasath, S. Ajith, V. Arumugaprabu, and M. Uthayakumar. 2020. Recent advancement in the natural fiber polymer composites: A comprehensive review. Journal of Cleaner Production 277:124109. doi:10.1016/j.jclepro.2020.124109.
- Zhang, W., X. Zhang, M. Liang, and C. Lu. 2008. Mechanochemical preparation of surface-acetylated cellulose powder to enhance mechanical properties of cellulose-filler-reinforced NR vulcanizates. Composites Science and Technology 68 (12):2479–84. doi:10.1016/j.compscitech.2008.05.005.
- Zhou, S., J. Li, S. Kang, D. Zhang, Y. Han, and P. Ma. 2022. Impact properties analysis of bamboo/glass fiber hybrid composites. Journal of Natural Fibers 19 (1):329–38. doi:10.1080/15440478.2020.1745114.