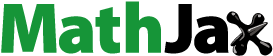
ABSTRACT
Natural fiber reinforced composites are attracting the attention of industries toward a sustainable and environment-friendly material for the future demands. The main drawback pertaining to the use of natural fiber composites lies in its inferior strength in comparison to its counterpart synthetic fibers. This research focuses on improving the fracture toughness of woven jute fabric mat with different orientations (0°, 30° and 45°) in epoxy resin by incorporating fillers and tested in universal tensile testing machine. Silicon carbide (SiC) particles of three sizes 26 µm, 54 µm and 72 µm were incorporated in the matrix in different weight ratios (5%, 10% and 15%). The fracture toughness of the jute/epoxy composites increases with the increase in the amount of SiC particles up to 10% addition and then it shows decreasing trend with further addition. The fracture toughness values show upward trend when the fiber orientation changed from 0° to 45°. Fractography of the tested specimen captured by scanning electron microscope which reveals the fracture of fibers and micro cracks in the epoxy matrix due to the applied load. Analysis of variance (ANOVA) is also conducted for predicting the most influencing parameters on the fracture toughness.
摘要
天然纤维增强复合材料正吸引着工业界的注意力,成为一种可持续和环保的材料,以满足未来的需求. 与使用天然纤维复合材料有关的主要缺点在于其强度低于相应的合成纤维. 本研究旨在通过添加填料并在万能拉伸试验机上进行试验,提高环氧树脂中不同取向(0°、30°和45°)的编织黄麻织物垫的断裂韧性. 三种尺寸为26 µm、54 µm和72 µm的碳化硅(SiC)颗粒以不同的重量比(5%、10%和15%)加入基体中. 黄麻/环氧复合材料的断裂韧性随着SiC颗粒添加量的增加而增加,添加量达到10%,然后随着添加量的进一步增加,断裂韧性呈下降趋势. 当纤维取向从0°变为45°时,断裂韧性值呈上升趋势. 扫描电子显微镜捕获的测试样品的断口,显示了由于施加的载荷导致的纤维断裂和环氧树脂基体中的微裂纹. 还进行了方差分析(ANOVA),以预测对断裂韧性影响最大的参数.
Introduction
The growing environmental awareness and ecological sustainability made the researchers to turn their attention toward usage of the environmental-friendly materials in engineering applications (Mohammed et al. Citation2015). The common synthetic fibers used in reinforced composites are carbon, glass and Kevlar which are posing environmental challenges and necessitated the researchers around the world to turn their attention toward environmentally pollution free fibers such as natural fibers. Natural fibers are mainly obtained from plants and animals. The widely used fibers are acquired from plants like sisal, jute, flax, coconut, oil palm, etc. The plants offer fibers from bast, seed covering and grass and reeds (Faruk et al. Citation2012). The variation in the fiber due to growing condition and varieties in plant reflects in the mechanical behavior of the fiber composites. This challenge has been addressed by many researchers by implementing different methods in the preparation of natural composite in an efficient way for the optimal mechanical strength. Sarikaya, Çallioğlu, and Demirel (Citation2019) investigated the performance of composite materials with birch, palm and eucalyptus fibers and epoxy resins by resin transfer molding method and molded fiber production method. The outcome of the investigations revealed that these methods will have more scope in the future for the fabrication of natural fiber reinforced composites. The mechanical performance of the natural fiber reinforced composites is enhanced by different methods which include fiber treatments, filler addition into the matrix and alignment of fibers in relation to the loading direction. One of the important mechanical properties of the composite is its fracture toughness. The fracture toughness of the natural fiber reinforced composites are inferior than its counterparts made from synthetic fiber reinforced composites (Sebe et al. Citation2000). The epoxy resin plates has lower fracture toughness due to its low load bearing ability. In general, the fracture toughness of epoxy resin can be increased by incorporating fibers into the resin matrix. Wong et al (Wong et al. Citation2010) have reported that the toughness can be improved by reinforcing the bamboo fiber into the neat polyester resin. The study exposed that there is an increase of 340% than neat polyester resin due to the addition of bamboo fibers into the neat resin. Bahar Tiber and Ersen Balcıoglu (Tiber and Balcıoğlu Citation2019) conducted studies using hybrid composites involving bamboo/cotton, modal/cotton and viscose/cotton fiber mate with epoxy. The fracture toughness of the modal/cotton composites appeared to be better than the other combination. Silva et al (Silva et al. Citation2006) studied the fracture behavior of (sisal/coconut fiber)/castor oil polyurethane composites. Further it was also suggested that the toughness can even be increased by giving chemical treatments to the fibers which increases the bonding strength between fiber and resin matrix. Khan et al (Khan et al. Citation2021) have conducted experiments by changing the arrangement of jute and kenaf mat layers to estimate the mechanical property variation due to the arrangement method. Kenaf/jute/kenaf (K/J/K), jute/kenaf/jute (J/K/J) and neat epoxy (EP) composites were fabricated and tested for mechanical properties. The study concluded that the K/J/K hybrid composites showed better mechanical properties which may be attributed to the better bonding between fiber/matrix. Dilip raja and Ananda kumar (Dilip Raja and Anand Kumar Citation2022) have analyzed the interwoven fibers of jute and Kevlar with epoxy matrix. Weaving patterns such as plain weave, basket weave, twill weave and satin weave were considered for experiments. Composites prepared out of these combinations were tested for mechanical properties. The observation revealed that plain weave and basket weave distributed the applied load in isotropic configuration. The satin weave showed the micro cracks in the matrix.
Stocchi et al. (Citation2007) imposed different fiber treatments and found some improvement in the toughness property when the fibers were treated with silicone and alkali treatments. Another method of getting good mechanical strength is powder filling into the matrix. Many researchers obtained better mechanical properties in natural fiber reinforced composites by powder filling or hybridization methods. The improved property is the result of increase in rigidity of the composite due to particle addition into the matrix. The addition of filler particles in the composites produced higher modulus and reduction in material cost (Balcıoğlu and Yalçın Citation2020; Liu and Dai Citation2007). Ojha and Biswal (Citation2019) observed the increase in tensile strength and impact load of palm stalk reinforced composite with the granite powder addition. Satapathy et al. (Citation2010) used SiC Particles as a reinforcement filler which was derived from rice husk by plasma-processing method. It was observed that the addition of SiC particles enhanced the mechanical properties of the jute-epoxy composites. Determination of fracture toughness for the polymer composites with natural fibers and fillers is critical to understand the fatigue service life of the component. Razavi et al (Razavi et al. Citation2021) have investigated the influence of the functionalized polyacrylonitrile (PAN) nanofibers in the carbon fiber epoxy matrix. When compared the functionalized and non-functionalized composite, the former had an increase in fracture energy by 50% than the latter. The sample with functionalized polyacrylonitrile showed an improvement in the inter-laminar strength by 27%. Researchers have also analyzed the fracture toughness characteristics of jute epoxy composites with the addition of rubber particles. Mahesh and Mahesh (Citation2022) presented abrasive test of Jute epoxy rubber composite for different filler combinations, load and distance and found that rubber additives results in increased resistance to abrasion. Mahesh et al. Citation2022a, Citation2022b) devised a systematic study method which efficiently uses the waste rubber crumb as an alternative filler material for epoxy matrix for low velocity impact applications. Mahesh, Harursampath, and Mahesh (Citation2022) studied the ballistic impact performance of jute reinforced polyethylene composite with nano-silica thickening agent and found that the composite can have high specific energy absorption characteristics with the high inclusion of nano-silica. Based on the literature review, natural fiber composites with reinforcement fillers are studied extensively with the certain limitations on the influence of fiber laminates and reinforcement particles on the fracture characteristics. Bisaria et al. (Citation2015) studied the mechanical properties of short jute fiber reinforced composites with different fiber length of 5,10,15 and 20 mm. It was found that the composites prepared with 15 mm fiber length showed better mechanical properties. The composites with fiber length of 5 mm and 10 mm were having less interfacial bonding between matrixes and produced inferior mechanical properties. Since jute fiber mat has better interfacial bonding with the matrix it is preferred for composite preparation in industries. This research article mainly focuses on the improvement of the fracture characteristics for a woven jute Fabric mat epoxy composites reinforced with SiC filler in different particle size, various addition percentage and different orientation of the laminates.
Materials and methods
Materials
Plain woven jute fabric mat with areal weight of 330 g/m2 and commercial grade epoxy resin was procured from local market. The selected woven jute fabric mat is having 12 EPI and 10 PPI. The metal die of 80 × 80x10 mm size was machined and used for the preparation of the composites. gives the properties of the epoxy material used in this investigation. depicts the jute fiber mat used in this study. The reinforcement material selected as filler is Silicon carbide with sizes 26 µm, 54 µm and 72 µm.
Table 1. Epoxy resin property.
Methods
Fabrication of composites specimen
The specimen for compact tension test was prepared by hand layup method. The required number of fabric mats were cut with the size of 80 mm x 80 mm. Totally 8 layers were used for the preparation of the composite specimen. All layers were stacked one after another in metal die. Epoxy resin was mixed with reinforcement of SiC in the following weight percentage 5%, 10% and 15%. Epoxy resin with hardener in the ratio of 10:1 was poured between all the layers. Finally enough pressure has been given for 24 hours and the specimen was taken out after curing period. gives the stacking method followed in preparing the composite specimen of 0/90, 30/60 and 45/45. The compact tension specimens were cut according to ASTM E D5045 standard (Liu and Dai Citation2007; Silva et al. Citation2006). illustrates the compact tension parameters of the research. displays the prepared compact tension specimen in this study. The effective width of the specimen was taken as 50 mm. The specimen were given a precut of 25 mm.
Compact tension test
The fracture toughness of the jute fiber laminate composites was predicted by conducting Mode-I Fracture according the ASTM Standard ASTM E D5045 at normal room temperature condition using Deepak universal testing machine. The fracture test was conducted in plane-strain condition. The following equations are applied for predicting the Critical stress intensity factor (or) fracture toughness (KIC). depicts the fracture testing of composites. The test was carried out at temperature of 30°C and with humidity of 60%. The cross-head speed of 1 m/sec was maintained for all the experiments. The load against the elongation data was obtained from the fracture test for predicting the fracture toughness of the composites.
Figure 5. Experimental set up used for fracture study (a) Testing equipment (b) Close up view of crack initiation.
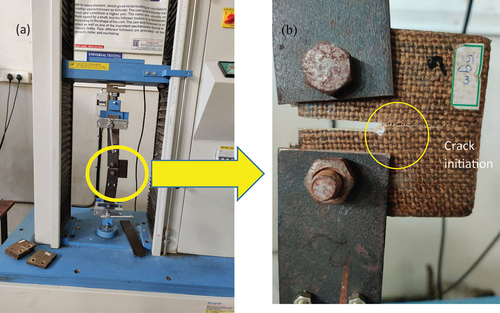
Critical stress intensity factor (or) facture toughness
Where B=Specimen thickness in mm; H=specimen width in mm; c= crack length in mm; P=Peak Load in test.
For CT specimen, the geometry factor, is given by
where relevant parameters are depicted in
Also, in order to satisfy plane strain condition, the following conditions must be satisfied
Where is the yield strength of the material determined from tensile test. Plastic zone can be calculated by
Where is radius of plastic zone
Three tests were carried out for each variation of fiber angle. Fracture toughness plots of the specimens were obtained from load-displacement curves. The obtained results depicted were calculated average of the three tests conducted.
Scanning electron microscopic study
The fractured surfaces were analyzed using scanning electron microscopy. The surfaces were scanned with magnification of 200 µm.
Results and discussion
Effect of fiber orientation on the fracture toughness
gives the effect of fiber orientation on the fracture toughness of the jute-epoxy composites. provides the effect of orientation angle on fracture toughness when 5% of the filler materials were added. For the arrangement of fiber in 0/90 composite specimen with 5% filler addition, the fracture toughness varies from 16.64 MPa√m to 19.74 Mpa√m while the particle size decreased from 26 µm to 72 µm. In the case of 30/60 fiber orientation set up, the fracture toughness increases from 21.53 MPa√m to 24.63 MPa√m for the particle size variation of 26 µm to 72 µm. The third variation of fiber orientation i.e 45/45 provided the fracture toughness of 26.41 MPa√mto 28.86 MPa√m. It was also clearly noted that the variation of fiber arrangements from 0/90 to 45/45 had an increasing trend of fracture toughness. The fracture toughness of the unfilled arrangements was also given for comparisons. This varies from 14.9 MPa√m to 24.53 MPa√m . This could be attributed to the fact that the alignment of the fibers in relation to the loading direction mainly alters its load bearing capability. The 0/90 arrangement possesses the less load bearing capability. While 45/45 arrangement of fibers carries more load due to equal load sharing between warp and weft fibers.
Figure 6. Effect of particle size on fracture toughness for various fiber orientation with varying filler percentages.
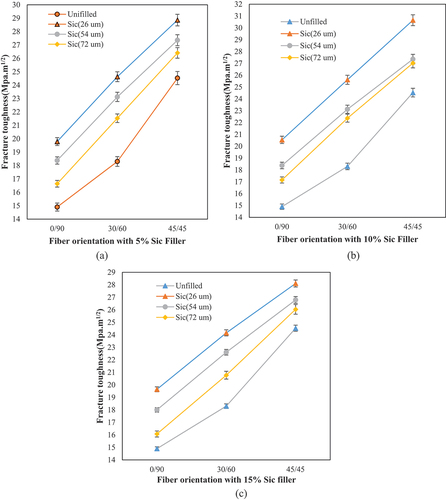
Among all combination lay out arrangements 45/45 showed better fracture toughness behavior. depicts the variation of the fracture toughness for 10% Filler addition in three types of fiber orientation respectively. The fracture toughness values range from 17.15 MPa to 20.53 MPa
, 22.3 MPa
to 25.6 MPa
and 27.02 MPa
to 30.64 MPa
for filler size varying from 72 µm to 26 µm. displays the variation of the fracture toughness for 10% Filler addition in three types of fiber orientation respectively. The fracture toughness values range from 16.07 MPa
to 19.64 MPa
, 20.77 MPa
to 24.14 MPa
and 26.04 MPa
to 28.1 MPa
for filler size varying from 72 µm to 26 µm.
Effect of the filler material addition on the fracture toughness
The filler materials added into the matrix enhanced the load bearing ability of the composite and also resisted the crack formation to certain extent so that the part of the load is borne by this particle. The following shows the effect of filler materials addition on the fracture toughness of the composite specimen. The addition of filler was varied from 5% to 15%. In all the figures, it was evident that the fracture toughness increased up to 10% addition afterward it took decreasing trend. The reason for the decrease could be related to the fact that more amount of particles get agglomerated and forms more cleavage sites for fracture initiation. From the graphs it can be seen that the composite with 10% filling percentage possessed better fracture toughness 30.64 MPa among all the combinations. This can be considered due to the pinning effect of the particles included in the matrix material. Crack pinning is created due to the obstruction of hard filler particles to the propagation of the crack (Garg and Mai Citation1988). Similar conclusions have also been drawn previously (Srivastava and Shembekar Citation1990).The fracture surface energy of the composites filled with Sic particles of 10% is maximum due to the pinning of crack and halts the crack propagation. The more amount of surface area of fracture faces increases the fracture surface energy.
Effect of the filler material size on the fracture toughness
The relation between the filler material size and fracture toughness of specimens is shown in . The filler materials size greatly influences the fracture toughness values of the composites. Addition of large particles (72 µm) deteriorates the fracture toughness capacity of the composites. However, small particles such as 26 µm enhance the load bearing capability of the composites which also increase the fracture toughness of the composites. The maximum value of the fracture toughness 30.64Mpa was seen for composite with filler materials size of 26 µm. The minimum value 16.07 MPa
were observed for composites with 72 µm filler material. Fracture toughness of composites depends on the surface area of fracture faces. When the size of the filler particles gets increased the load distribution between matrixes is reduced. It paves the way for the crack formation easily. The may be attributed the less fracture toughness of the composites of 72 µm combination.
Influence of the parameters on the fracture toughness
Taguchi’s orthogonal array was used to frame mathematical expression to achieve better fracture toughness by selecting suitable combination of process parameters such as orientation angle, filler particle size and filling percentage. shows the factors and their levels. shows the 27 experiments conducted to form mathematical correlation between input variables and fracture toughness. The table lists the experimental results of all the studies performed and also predicted responses of the corresponding input variables. It also lists the error between experimental and predicted responses.
Table 2. Factors and their levels.
Table 3. Design of experiments for fracture toughness of L27 experiments conducted.
Analysis of variance (ANOVA)
Analysis of Variance (ANOVA) is used to identify the variation of an output parameters to various inputs parameters. The purpose of the analysis of variance is to analyze which experimental parameters significantly influence the strength characteristics of composites prepared. In order to estimate the contribution of three parameters on the fracture toughness of composites ANOVA was performed using MINITAB 16.0. The optimum values for the influencing factors on fracture toughness can be obtained by this study. . presents the ANOVA results relative performance of composites of the study conducted for fracture toughness with a confidence level of 95%. The statistical significance was achieved for particular response with low value indication of p. The ANOVA analysis revealed that orientation angle (85.3%) had major effect on the fracture toughness of composites followed by filler material size (9.6) and filling percentage (0.2%). The table also shows the interaction factors effect of the responses. The interaction effect of the parameters appeared to be low in relation to the individual parameters effect.
Table 4. ANOVA results.
The relationship among the process parameters were correlated by a mathematical equation given in equation (5). This equation can be used to estimate the theoretical fracture toughness of the composites.
Fracture Toughness (FT) = 17.802 + 0.0555211 A − 0.0254747 B + 0.838528 C + 0.00321855 A*A +0.000242839 A*B − 0.000492398 A*C − 0.000468088 B*B − 0.000227427 B*C −0.0432415 C*C … .(5)
Where A=Orientation angle; B=Particle size; C=Filling percentage
Morphology of fractures surface
Micro-cracks were observed in the unfilled and filled composites during test. As the load increased these cracks become macro in size tending to cause the specimen to fail by breaking. The damage conditions need to be analyzed both in micro and macro size for understanding the fracture mechanism. shows the macro-level crack initiation. shows the crack opening which will be unsafe situation for both filled and unfilled jute/epoxy composite specimen. shows the macro and micro magnification of the tested specimen under scanning electron microscope. The fracture damages like matrix crack, matrix deformation, debonding of fiber, fiber pullout and fracture are evident from the micro level examination. Further, it can be anticipated that the transverse crack also leads to an effect called fiber-bridging. In the woven jut mat arrangement of 0/90 orientation in which the fibers are arranged parallel to the loading direction, matrix bonding with fiber interface is weaker which augments the fiber pulled out and hence this combination withstands lesser load. Whereas 45/45 arrangement possesses better the bonding between fiber and matrix and is able to withstand more load. The occurrence of the smaller deformation in the SiC filled composite may be due to the decrease in ductility of the composite. The fillers materials tend to arrest the deformations of the matrix materials during loading condition.
Conclusion
The fracture characteristics of woven jute composites with SiC loading have been studied in this research experimentally. The effect of the three parameters such as fiber orientation, filler material size and filler material loading was also analyzed.
Specimens with different variations such as particle filling, fiber orientation have been fabricated to study the fracture toughness characteristics of woven jute fabric mate composites.
ANOVA was performed using MINITAB 16.0 to obtain the optimum values for the influencing factors on fracture toughness.
Fracture toughness values were improved with the introduction of SiC particles into the matrix of the woven jute fabric mat reinforced composite. The unfilled woven jute fabric mat composites fracture toughness values vary from 14.9 MPa
to 24.53 MPa
.
The fracture toughness values increased proportionally in relation to the decrease in particle size. The maximum value of the fracture toughness 30.64 MPa
was seen for composite with filler materials size of 26 µm. The minimum value 16.07 MPa
was observed for composites with 72 µm filler material.
The maximum value of the fracture toughness obtained in this study is for 45/45 arrangement of woven jute fabric mat with 8 layers is 30.45 MPa
and 10% filling with 26 µm size of the particles.
The fracture toughness values are seen to improve on the upside with the gradual loading of the SiC particles. The fracture toughness values increased gradually and obtained maximum value at 10% loading afterward it started decreasing.
A correlation equation has been formulated to predict the influence of input process parameters on the desired output i.e fracture toughness.
The damages such as agglomeration of fillers, matrix micro cracks, pull out of fibers and fiber breakages were revealed by the Scanning Electron Micrographs.
Highlights
It brings out the detailed study of fracture toughness of natural fiber composites by incorporating SiC fillers.
It also describes the prime phenomenal reasons behind the enhancement of toughness of the woven jute fabric mat reinforced epoxy composites.
It specially elaborates the influence of fiber orientation, volume of filler material and size of filler material, which has not been studied in detail elsewhere in the literature.
The better process parameter (fiber orientation, filler volume and size) obtained by using Taghuchi’s method.
Disclosure statement
No potential conflict of interest was reported by the author(s).
References
- Balcıoğlu, H. E., and D. Yalçın. 2020. The determination of fracture characterization of knitted fabric reinforced composites using arcan test. Fibers and Polymers 21 (4):849–14. doi:10.1007/s12221-020-9619-z.
- Bisaria, H., M. Gupta, P. A. Shandilya, and R. Srivastava. 2015. Effect of fibre length on mechanical properties of randomly oriented short jute fibre reinforced epoxy composite. Materials Today: Proceedings 2 (4–5):1193–99. doi:10.1016/j.matpr.2015.07.031.
- Dilip Raja, N., and K. V. Anand Kumar. 2022. Effect of weaving pattern on the mechanical properties of 2D interwoven kevlar-jute hybrid laminates. Journal of Natural Fibers 1–12. doi:10.1080/15440478.2022.2085226.
- Faruk, O., A. K. Bledzki, H.-P. Fink, and M. Sain. 2012. Biocomposites reinforced with natural fibers: 2000–2010. Progress in Polymer Science 37 (11):1552–96. doi:10.1016/j.progpolymsci.2012.04.003.
- Garg, A. C., and Y.-W. Mai. 1988. Failure mechanisms in toughened epoxy resins—a review. Composites Science and Technology 31 (3):179–223. doi:10.1016/0266-3538(88)90009-7.
- Khan, T., M. Sultan, A. Shah, A. Ariffin, and M. Jawaid. 2021. The effects of stacking sequence on the tensile and flexural properties of kenaf/jute fibre hybrid composites. Journal of Natural Fibers 18 (3):452–63. doi:10.1080/15440478.2019.1629148.
- Liu, X., and G. Dai. 2007. Surface modification and micromechanical properties of jute fiber mat reinforced polypropylene composites. Express Polymer Letters 1 (5):299–307. doi:10.3144/expresspolymlett.2007.43.
- Mahesh, V., D. Harursampath, and V. Mahesh. 2022. An experimental study on ballistic impact response of jute reinforced polyethylene glycol and nano silica based shear thickening fluid composite. Defence Technology 18 (3):401–09. doi:10.1016/j.dt.2021.03.013.
- Mahesh, V., and V. Mahesh. (2022). Tribological characterization of sustainable jute-epoxy-rubber crumb hybrid composite. Proceedings of the Institution of Mechanical Engineers, Part C: Journal of Mechanical Engineering Science: 09544062221103941.
- Mahesh, V., V. Mahesh, D. Harursampath, S. Joladarashi, and S. Kulkarni. 2022a. Development of sustainable jute/epoxy composite and assessing the effect of rubber crumb on low velocity impact response. Journal of Natural Fibers 1–12. doi:10.1080/15440478.2022.2054897.
- Mahesh, V., V. Mahesh, S. M. Nagaraj, P. Subhashaya, and G. S. T. Shambu Singh. (2022b). Physio-mechanical and thermal characterization of jute/rubber crumb hybrid composites and selection of optimal configuration using the MADM approach. Proceedings of the Institution of Mechanical Engineers, Part C: Journal of Mechanical Engineering Science: 09544062221079166.
- Mohammed, L., M. N. Ansari, G. Pua, M. Jawaid, and M. S. Islam. 2015. A review on natural fiber reinforced polymer composite and its applications. International Journal of Polymer Science 2015:1–15. doi:10.1155/2015/243947.
- Ojha, A. R., and S. K. Biswal. 2019. Thermo physico-mechanical behavior of palm stalk fiber reinforced epoxy composites filled with granite powder. Composites Communications 16:158–61. doi:10.1016/j.coco.2019.10.003.
- Razavi, S. M. J., R. E. Neisiany, M. Razavi, A. Fakhar, V. Shanmugam, V. Alagumalai, M. Försth, G. Sas, and O. Das. 2021. Efficient improvement in fracture toughness of laminated composite by interleaving functionalized nanofibers. Polymers 13 (15):2509. doi:10.3390/polym13152509.
- Sarikaya, E., H. Çallioğlu, and H. Demirel. 2019. Production of epoxy composites reinforced by different natural fibers and their mechanical properties. Composites Part B: Engineering 167:461–66. doi:10.1016/j.compositesb.2019.03.020.
- Satapathy, A., A. K. Jha, S. Mantry, S. Singh, and A. Patnaik. 2010. Processing and characterization of jute-epoxy composites reinforced with SiC derived from rice husk. Journal of Reinforced Plastics and Composites 29 (18):2869–78. doi:10.1177/0731684409341757.
- Sebe, G., N. S. Cetin, C. A. Hill, and M. Hughes. 2000. RTM hemp fibre-reinforced polyester composites. Applied Composite Materials 7 (5):341–49. doi:10.1023/A:1026538107200.
- Silva, R., D. Spinelli, W. Bose Filho, S. C. Neto, G. Chierice, and J. Tarpani. 2006. Fracture toughness of natural fibers/castor oil polyurethane composites. Composites Science and Technology 66 (10):1328–35. doi:10.1016/j.compscitech.2005.10.012.
- Srivastava, V., and P. Shembekar. 1990. Tensile and fracture properties of epoxy resin filled with flyash particles. Journal of Materials Science 25 (8):3513–16. doi:10.1007/BF00575379.
- Stocchi, A., C. Bernal, A. Vázquez, J. Biagotti, and J. Kenny. 2007. A silicone treatment compared to traditional natural fiber treatments: Effect on the mechanical and viscoelastic properties of jute—vinylester laminates. Journal of Composite Materials 41 (16):2005–24. doi:10.1177/0021998307074108.
- Tiber, B., and H. E. Balcıoğlu. 2019. Flexural and fracture behavior of natural fiber knitted fabric reinforced composites. Polymer Composites 40 (1):217–28. doi:10.1002/pc.24635.
- Wong, K., S. Zahi, K. Low, and C. Lim. 2010. Fracture characterisation of short bamboo fibre reinforced polyester composites. Materials & Design 31 (9):4147–54. doi:10.1016/j.matdes.2010.04.029.