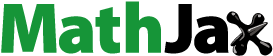
ABSTRACT
Improvement in mechanical properties of the natural fiber reinforcement for potential use in the composite for mechanical performance is a key focus of researchers in recent years. However, few studies are available in the literature on the mechanical performance of hybrid-woven fabrics. In this article, the effect of the weave structure of reinforcing fabric on mechanical performance has been investigated. Jute-based woven fabrics having four different weave structures (matt, sateen, and hybrid-weave A/B) were developed in the in-house lab using a shuttle dobby weaving machine. The tensile test and puncture tests were performed to evaluate the mechanical performance by varying the weave architecture. The sateen weave exhibited maximum penetration load during a puncture test. The results demonstrated a significant improvement in the tensile strength by using a hybrid weave in the warp direction. However, sateen woven fabric demonstrated enhancement in the tensile attributes in the weft-wise direction. Similarly, a hybrid weave consisting of a combination of sateen and matt weave exhibited a maximum stiffness value. To check the statistical significance of the results, ANOVA analysis was performed. The findings of ANOVA suggest that the results are statistically significant. This research will open a new avenue in the field of reinforcement composite material.
摘要
近年来,提高天然纤维增强材料的力学性能是研究人员关注的一个重点. 然而,文献中很少有关于混合机织物机械性能的研究。本文研究了增强织物的组织结构对力学性能的影响. 使用梭式多臂织机在室内实验室开发了具有四种不同组织结构(亚光、缎面、混合组织A/B)的黄麻基机织物. 通过改变组织结构,进行拉伸试验和穿刺试验以评估机械性能. 棉缎织物在穿刺试验中表现出最大的穿透载荷. 结果表明,通过在经纱方向上使用混合组织,拉伸强度显著提高. 而棉缎机织物在纬纱方向上的拉伸特性增强。类似地,由棉缎和亚光织物组合而成的混合织物表现出最大的刚度值. 为了检查结果的统计意义,进行了方差分析. 方差分析的结果表明,结果具有统计学意义. 该研究将为增强复合材料领域开辟一条新的途径.
Introduction
The fabric can be of different types based on the design and construction parameters. The basic types of fabric can be categorized as woven, braided, knitted, and non-woven (Grosberg Citation1966). The variation in the fabric architecture affects the mechanical properties of the woven fabric (Booth Citation1961). The mechanical properties also differ with the direction of the load and tension forces applied. The mechanical attributes play a crucial role in resisting permanent deformation under the applied stress in designing a fabric (Dolatabadi and Kovar Citation2012). The tensile strength and elongation are the most important fabric mechanical performance parameters. The end application of studying the mechanical properties can be woven preforms of composites, protective clothing, cut-resistant gloves, and high-performance applications (Alessa and Sosa Citation2022; Aliabadi Citation2015; Bilisik and Syduzzaman Citation2022). The mechanical properties of the woven fabrics such as tensile, tearing strength and puncture have been reported in the literature. Literature reported the cotton woven fabric from different weave structures by keeping the construction parameters constant. The mechanical properties studied were tensile strength, tearing strength, abrasion resistance, pilling resistance, and stiffness. The tensile strength of the plain weave was higher as compared to that of the twill weave because of less porosity and the number of interlacement points. The plain weave also exhibited high stiffness and pilling resistance as compared to the twill weave (Jahan Citation2017; Realff et al. Citation1991)
Studies show that the construction parameters also have an effect on the mechanical properties of the fabric to a great extent. The fabric construction such as thread density and grams per square meter (GSM) is also affected by improper yarn tension, consequently affecting the mechanical properties (Realff et al. Citation1991). It is reported that the strength of plain weave is higher than the 2/1 twill, and the strength of twill 2/1 is higher than the twill 2/2. The tensile stress–strain properties are the most common mechanical measurement in a fabric. The result of these tests depends on the geometry, construction and fabric type, arrangement, and fabric structure. The axial stretching of the fabric yields the breaking load and elongation of the fabric (Jahan Citation2017). The mechanical properties such as strength and stiffness of plain, 2/2 twill, and 5 end sateen were investigated based on two factors such as crossing over factor (COF) and floating yarn factor (FYF). The COF and FYF were found more in the plain and sateen weave, respectively, when the comparison is done between plain, sateen, and twill weave. It can be found that the greater the difference in warp and weft yarn density, the greater the difference in the tearing resistance (Triki, Dolez, and Vu-Khanh Citation2011; Witkowska and Frydrych Citation2008)
The gradual removal of the fibers from the yarns leads to a change in the abrasion property. The float of the yarn in the woven fabrics also affects its abrasion resistance. The longer floats in a weave structure will steer an unusual breaking of yarns and high abrasion. Therefore, the sateen weave shows high abrasion as compared to the twill and the plain weave due to longer floats (Doustaneh et al. Citation2013; Göktepe Citation2002). The pills that protrude from the fabric surface also have an effect on mechanical properties, which can be formed due to the rubbing action of wearing and washing by the entanglement of fibers (Göktepe Citation2002). The stiffness of a fabric depends on the bending length of the fabric. The more the bending length of the fabric, the higher the stiffness and the lower the draping of the fabric (Lomov, Truevtzev, and Cassidy Citation2000). The stiffness of fabric generally increases with an increase in interlacement points. The plain fabric with more interlacement points is stiffer than the 2/1 twill and similarly, the 2/1 weave structure is more stiffer than the 2/2 twill weave (Lomov, Truevtzev, and Cassidy Citation2000). The migratory tendency of fibers from the constituent yarn is less in the plain weave as compared to the twill weave resulting in less pill formation in the plain weave (Saville Citation1999).
The crimp of the weave structure is also pivotal in deciding the tensile strength. Theoretically, the plain weave has a high crimp as compared to the sateen weave. The more the crimp amplitude in the fabric, the less will be the tensile strength. This causes less contribution toward the tensile force and the inter-yarns get more entangled (Saiman, Wahab, and Wahit Citation2014). This is contradictory to what was reported in (Ganesh and Ankita Citation2018; Jahan Citation2017). Ganesh and Ankita (Citation2018) reported that plain-woven fabrics have more interlacement points and provide a higher contact area. Consequently, there is an increase in the resistance to the yarn slippage and a higher frictional force during a tensile load. Therefore, the tensile strength of the plain-woven fabric is more compared to the twill weave. The twill weave and matt weave show less tensile strength due to the fewer binding points present in its structure (Saiman, Wahab, and Wahit Citation2014). However, the tear strength of a woven structure depends on the mobility of the yarn. The plain weave has less tearing strength due to the loss of mobility because of its weave structure (Eryuruk and Kalaoğlu Citation2015). In the case of application of the tensile loading, all the yarns are in the direction of loading, so they all share the load (Eryuruk and Kalaoğlu Citation2015). Morton investigated fabric strength in relation to the yarn properties and the density of structure and concluded that an increase in cover factor gradually increases the tensile and the tearing strength (Morton Citation1934). The tensile strength is defined as the maximum load that a material can withstand divided by the original cross-sectional area of the material when stretched or elongation force is applied (Asaduzzaman et al. Citation2020). Apart from this, many studies on puncture resistance of fabrics have been reported in the literature. The puncture resistance of pure leno and hybrid leno weaves made up of multifilament polyester yarn was studied, and it was found that hybrid leno fabrics offer less penetration resistance as compared to leno weaves (Shaker et al. Citation2020). The puncture resistance of double-face fabrics with the variation of thickness was studied and compared to the conventional weaves. It was found that a 2/2 matt weave is better in response to puncture force as compared to double face fabrics (Hameed et al. Citation2022). Therefore, fabric testing is necessary for gauging the performance of the fabric and ensuring the quality of fabric and solving compliance-related issues and thus providing mechanical properties at various fabric conditions (Grosberg Citation1966; Realff et al. Citation1991). Hence, the aforementioned literature establishes the significance of investigating the mechanical performance of different woven fabrics by varying the weave architecture.
Hybridization of yarns in a weave structure by using different fibers can be beneficial in obtaining optimum mechanical performance structures to save cost (Andrew and Arumugam Citation2017). Furthermore, under the low-velocity impact, it was observed that the intra-layered hybrid structure has better performance as compared to the interlayered hybrid structure (Pegoretti et al. Citation2004). Umair et al. studied the hybrid reinforcement composites reinforced with glass microsphere fillers and investigated the low-velocity impact response for the first time (Umair et al. Citation2021). From the literature, it is evident that most of the research available in the open literature is on textile-based reinforced composites. There exists little literature according to the author’s knowledge on the mechanical performance of the hybrid woven fabric alone. The hybrid natural woven fabric can potentially be used in the composite for aerospace and construction and low-velocity impact applications.
In this article, the porosity, puncture resistance, tensile, and stiffness properties of natural fiber-based woven fabrics from two different novel hybrid woven fabrics, developed for the first time with the combination of longer and shorter yarn floats, and two (2) basic woven structures are studied. Natural fiber-based Jute (fiber) is used to produce these woven fabrics. The results showed a significant effect of weave structure on the mechanical properties of developed fabrics.
Materials and methods
This section delineates the comprehensive overview of the materials and methods that have been used for the fabrication and the testing of the woven samples.
Development of woven fabric
In this work, the Jute yarn of count (1.6/1 Ne or 368.75 tex) is used as a warp and weft for the development of the fabric. The warp yarn was singed using a locally produced setup to remove the fibers and make the surface even. The singeing process not only increases the tensile strength of the yarn but also makes the weaving process easy (Asghar et al. Citation2021).
The woven fabrics with four different weaving patterns were produced on the NORTHROP shuttle manual dobby weaving machine present in our lab as shown in . The machine consists of a double lifting frame mechanism and a positive shedding tappet mechanism. The lattice preparation of the manual dobby machine and the peg plan were fed according to the weave design. The minimum number of shedding frames used was according to the weave repeat and pattern. The pegs in the lattice decide which frames to shed according to the design pattern. The fabric construction parameters such as the cover factor of the fabric and the reed count used to develop the fabric were 37 and 4 yarns/dent, respectively. This includes 3/3 matt, 6 ends sateen, hybrid weave A and hybrid weave B as shown in . These designs were chosen to study the effect of the float length on mechanical properties and the inclusion of tight part in the fabric. Hybrid weave A was designed as a combination of a longer float design (6 end sateen) with the closing of 3/3 matt weave. Similarly, hybrid weave B was designed as a combination of a longer float weave design (6 end sateen) with the closing of a tight 3/3 warp rib structure. Two basic woven structures 6 end sateen and 3/3 matt weave were also studied. The weave type, areal density, warp, and weft-wise crimp percentages of the four different woven fabrics are given in . Within a weave design repeat, the sateen yarns were combined with the rib and matt yarns to achieve hybrid weaving patterns. Hybridization of sateen woven fabric was done to add structural stability, as the sateen fabric alone has a longer float length and open structure. consists of the design of the experiment (DOE) and specifications such as end/in, picks/in, areal density, and warp/weft crimp of developed woven fabrics. The areal density of the sample S1 (i.e., weave with a combination of sateen and matt pattern) is the highest which is justified by the theoretical calculation of the areal density (GSM) using EquationEquation 1(1)
(1) , Equation2
(2)
(2) and (Equation3
(3)
(3) ) respectively. In EquationEquations 1
(1)
(1) and Equation2
(2)
(2) , epc, ppc, Cw, and Cf are ends per cm, picks per cm, and crimp in warp and weft directions, respectively.
Table 1. Specifications of four different woven fabrics.
The areal densities of samples S3 and S4 are comparable. Sample S2 (i.e., matt weave) has the least areal density.
Testing
The magnified view of the fabric structure of the woven samples has been examined with an optical microscope (Olympus-BX51 M), as shown in . The scaling factor for the optical microscope was kept at 35 X. After the fabrication of the samples, mechanical testing such as puncture, tensile, and stiffness has been done under a standard humidity level of 65% and temperature of 21°C. The tensile test was investigated by a universal testing machine as shown in having sample dimensions, i.e., 150 mm long and 100 mm wide as per ASTM-D5034. The tensile test was performed at a rate of 100 mm/min. The puncture resistance test was also performed on a universal testing machine as per EN388:2016 standard. The stylus used for the puncture test is made of Steel 60 HRC Rockwell with a 4.5 mm cylindrical diameter and tapered 30 degrees to produce 1 mm spherical diameter from the striking face. The speed of the puncture test was 25 mm/min, and the diameter of the stylus of the puncture test used was 1 cm. The puncture test setup is shown in . The stiffness test was performed using the stiffness of fabrics machine by the circular bend procedure ASTM-D4032, as shown in . All the tests were repeated three times, and the average result is reported in the article. Furthermore, Minitab 18 software was used for statistical analysis of the results.
Results and discussion
The porosity of the samples was theoretically calculated, and the results are presented in this section. The results of puncture, tensile (warp and weft directions), and stiffness of fabricated woven fabrics are also presented in this section.
Porosity
The porosity of the samples was calculated theoretically using the Equation 4 and is presented in where Wa is the areal density in kg/m2, Pf is the fiber density in kg/m3, and t is the thickness of fabric in m.
Table 2. Porosity of different weave structures using experimental data.
It is found that the porosity is directly linked to the areal density of the fabric. The sample with the least density is porous having a porosity of 82.5% and sample with the highest areal density reveals the least porosity of 76.2%. Therefore, the resulting porosity of sample S2 is the highest as given in and can also be observed in .
Puncture test
This subsection concludes the discussion on the experimental results of the puncture test that has been performed to test the mechanical strength of the fabricated samples. The graphical representation of the low-velocity puncture test result of all the fabricated samples has been given in . S1 sample shows the highest resistance against penetration, followed by sample S3 (hybrid weave B) and sateen weave, as shown in . The matt weave exhibited the least penetration resistance and lowest Fmax value, which can be linked to the highest porous structure and loose float structure. However, the penetration load results of different weaves reveal that the Sateen weave sample (S4), with the highest float length, shows the maximum penetration load. It should be noted that the Sateen weave has closely spaced interlacement points and least porosity. There are several other factors, which can play a role in the puncture resistance load of the fabrics such as friction between warp and weft yarns, unevenness of yarn or protrude pills, the strength of fiber (Realff et al. Citation1991), and the falling of stylus on the tight or loose part and needs to be investigated. However, the puncture loads of all the chosen fabrics except matt weave are close to each other, and porosity is a major contributor to the penetration of the stylus. It is difficult to push away yarns in a fabric in a tight weave and easier in a loose fabric as depicted in the results. In the load extension curve, multiple load peaks are present which can be correlated with the breaking of filaments during penetration. However, the absence of the multiple peaks in the penetration testing of the matt weave sample can be linked to the highly porous structure of the sample S2. In sample S2, after the maximum peak force is obtained, the nonlinearity in the curve indicates the fiber pull out from the woven fabric as indicated in . The reason for non-linearity could be that in the case of matt weave the pull out is more as the three yarns of 3/3 matt weave collectively offer more resistance to pull out. However, the curve is straight for the rest of the samples. Multiple load peaks can be observed for S3 and S4, as shown in . The trend followed by samples S3 and S4 is similar to the trend observed in sample S1. The puncture load of 6 end Sateen weave made of Jute yarn is comparable to the puncture load of multifilament Kevlar-29 5 end Sateen weave fabric of thickness 0.4 mm (Hameed et al. Citation2022). However, it should be noted that the yarns or filaments are broken in the case of the current study, whereas in the case of Kevlar-29 woven fabric, the yarns are displaced outwards.
Tensile test
This subsection includes a discussion about the experimental results of the tensile test that has been performed using the universal tensile testing machine. The experimental results of tensile load and extension in the warp-wise direction have been shown in . Sample S1 (i.e., a combination of the sateen weave and matt weave) exhibits the maximum load-bearing capacity with an increase in the applied tensile load in the warp direction due to the presence of a compact weave structure (matt weave) and a longer float structure in the fabric in the warp-wise direction. It should be noted that the areal density and picks/inch of this fabric is higher as compared to other fabrics. A similar trend is observed for the S3 sample (i.e., a combination of the sateen and the rib structure) and the load-bearing capacity is less than that of sample S1. This is followed by the sateen woven fabric (S4) and the matt woven fabric (S2). These weaves show the least load-bearing capacity, which can be associated with the crimped structure of the matt and the sateen weave. The extension in the warp-wise direction of sample S2 is less as compared to the other samples S1, S3, S4.
This section discusses the response of tensile load in the weft-wise direction of the developed samples. The results of the tensile load and extension in the weft-wise direction are given in . Sample S3 (i.e., a combination of sateen and rib weave) and sample S2 (i.e., matt weave) show the minimum peak load and an almost similar trend of weft-wise tensile load results. The tensile strength of samples S2 and S3 is 785 N, and sample S1 (i.e., a combination of sateen and matt weave) shows a peak tensile load of 891 N. This can be associated with the high crimp amplitudes present in these weave structures. The sample S4 (i.e., sateen weave) shows the least crimp amplitude and, hence, maximum tensile strength and load-bearing capacity. Sample S1 has the next highest peak of load-bearing capacity. Samples S2 and S3 have the lowest crimp amplitude and hence the least interlacement points. The results of samples S2 and S3 show comparable peaks of maximum load.
Stiffness
The stiffness results for the developed fabric using the circular bend procedure are shown in . The result of stiffness of sample S1 (i.e., hybrid weave with a combination of matt and sateen weave) depicts the maximum stiffness value. This can be represented by the presence of the tight part (i.e., matt weave) in the weave structure. At the start of the test in , the slope of the curve shows a stiffness response of different weaves during a puncture test. The stiffness response in the results of the puncture test () shows a similar trend that has been observed in the results of the stiffness test. The sample (S2) consisting of matt weave and the sample (S3) consisting of sateen and rib weave combination shows the next lowest value of stiffness. The sample (S4) shows the least value of stiffness associated with the slack structure of the weave.
Table 3. Stiffness response of the developed samples using circular bend procedure.
Statistical analysis
The normal probability plots and Tukey plots for puncture resistance, tensile strength (warp and weft wise), and stiffness of fabric are shown in , respectively. The probability normal plots are used to test whether the data collected is normally distributed or not. It is found from the results that the data is normally distributed as shown in The Tukey is used to formally test whether the difference between a pair of groups is statistically significant.
Figure 8. Puncture test statistical plots: (a) Normal probability plot and (b) Tukey simultaneous plot.
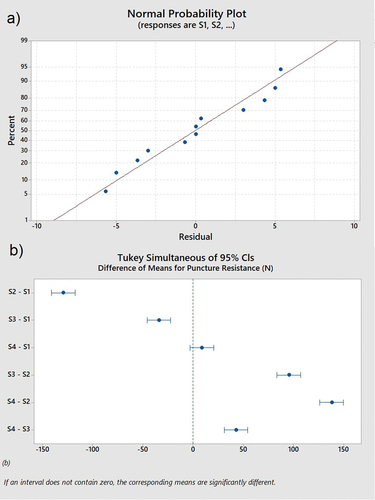
Figure 9. Tensile test statistical plots: warp wise (a) Normal probability plot (b) Tukey simultaneous plot, and weft wise (c) Normal probability plot (d) Tukey simultaneous plot.
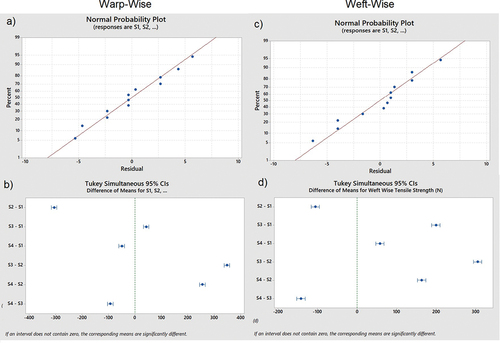
One-way ANOVA (Tukey plots)
The Tukey plot of the puncture resistance test showed that the confidence intervals for those variations between the means, which do not include zero in their range, are considerable. In , only one value includes zero in the mean values of their confidence intervals, as shown in , which showed that the differences between the means of these pairs were not substantial. All remaining confidence intervals did not include zero in their pair of means, showing that the differences between the pair of means are statistically significant.
The Tukey plot of the tensile strength test for both tests in the warp and wise direction showed that the confidence intervals for those variations between the means, which do not include zero in their range, are significant. In , no value includes zero in the mean values of their confidence intervals, as shown in , which showed that the variations between the means of these pairs were not significant. All the values of the confidence gaps did not include zero in the pair of means, which revealed that the differences between the pair of means were considerable. The samples are tightly held in the jaws during the puncture and tensile tests, and there are fewer chances of variation in data as depicted in the results.
Similarly, the Tukey plot of stiffness in the warp direction showed that the confidence gaps for those differences between the means, which do not include zero in their range, are significant. In , one value includes zero in the mean values of their confidence gaps as shown in , which showed that the differences between the means of these pairs were not significant. Rest all the values of the confidence intervals did not include zero in the pair of means, which showed that the differences between the pair of means were significant. There is a lot of variation in data in stiffness test results and can be associated with loosely held samples during a stiffness test due to the sensitivity of the machine.
Conclusion
Four woven fabrics were developed and the mechanical performance such as puncture, tensile, stiffness, and porosity has been investigated. The matt weave showed the highest porosity of 82.5% and the least areal density of 0.598 kg/m2. The puncture test shows that the sateen weave has the maximum peak force as compared to that of the hybrid and matt woven fabrics because of its loose fabric structure and highest areal density. It is concluded that a loosely woven fabric disperses the yarns more during a puncture test and has less penetration resistance due to more porosity as compared to the tight weave. The tensile results of load versus extension show that a hybrid woven structure consisting of a combination of sateen and matt weave shows the maximum peak force due to the presence of loose and tight part in the warp-wise direction. The weft-wise tensile results consisting of sateen weave show maximum peak load as compared to other developed fabrics. This is due to the presence of fewer crimp amplitudes in the woven fabric as compared to other weaves. The stiffness of the hybrid weave developed using a combination of sateen and matt weave is the highest, while the stiffness of sateen woven fabric is the lowest due to loose fabric structure. The results are also statistically studied and show a significant impact on the mechanical properties analyzed.
Highlights
Four jute-based woven fabrics with different weave architectures (matt, satin, and hybrid weave A and B) were developed in an inhouse lab using shuttle NORTHROP dobby machine.
The porosity, puncture tests, tensile tests, and stiffness tests of the developed fabrics were performed to evaluate the mechanical performance by varying the weave architecture.
The satin weave (S4) exhibited maximum penetration load of 275 N during a puncture test. The results demonstrated a significant improvement in the tensile strength by using a hybrid weave A (S1) in warp-wise direction. However, the satin woven fabric (S4) demonstrated enhancement in tensile attributes in weft-wise direction. The warp-wise tensile strength is in general more as compared to the weft-wise tensile strength.
Similarly, hybrid weave A (S1) consisting of a combination of satin and matt weave exhibited a maximum stiffness value of
gm during a stiffness test using circular bend procedure.
This research concludes that hybridization is an easy and effective method to increase the stiffness and tensile performance of fabrics. Moreover, there is a less extension in fabric during a load test using hybrid weaves.
Disclosure statement
No potential conflict of interest was reported by the author(s).
References
- Alessa, F.M., and E.M. Sosa. 2022, April 1–13. Experimental evaluation of impact-resistant gloves using surrogate hands. International Journal of Occupational Safety and Ergonomics. doi:10.1080/10803548.2022.2051865.
- Aliabadi, M.H. 2015. Woven composites. 6 vols. World Scientific Publishing: Imperial College Press.
- Andrew, J.J., and V. Arumugam. 2017. Effect of patch hybridization on the tensile behavior of patch repaired glass/epoxy composite laminates using acoustic emission monitoring. International international Journal of Adhesion and Adhesives 74:155–14. doi:10.1016/j.ijadhadh.2017.01.014.
- Asaduzzaman, M., A. Mukibul Hasan, M. Mohsin Patwary, S. Mahmud, M. Ariful Islam, T. Hossain Raju, and A. Hossen. 2020. Effect of weave type variation on tensile and tearing strength of woven fabric. Technium 2(6): 35–40. doi:10.47577/technium.v2i6.1409.
- Asghar, M.A., A. Imad, Y. Nawab, M. Hussain, and A. Saouab. 2021. Effect of yarn singeing and commingling on the mechanical properties of jute/polypropylene composites. Polymer Composites 42 (2):828–41. doi:10.1002/pc.25868.
- Bilisik, K., and M. Syduzzaman. 2022. Protective textiles in defence and ballistic protective clothing. In Protective textiles from natural resources, 689–749. Elsevier. doi:10.1016/B978-0-323-90477-3.00027-4.
- Booth, J. 1961. Principles of textile testing: An introduction to physical methods of testing textile fibres, yarns and fabrics.
- Dolatabadi, M.K., and R. Kovar. 2012. Anisotropy in tensile properties of plain weave fabric – Part I: The meso-scale model. Textile Research Journal 82 (16):1666–76. doi:10.1177/0040517511435003.
- Doustaneh, A.H., S. Mahmoudian, M. Mohammadian, and A. Jahangir. 2013. The effects of weave structure and yarn fiber specification on pilling of woven fabrics. World Applied Science Journal 24 (4):503–06.
- Eryuruk, S.H., and F. Kalaoğlu. 2015. The effect of weave construction on tear strength of woven fabrics. Autex Research Journal 15 (3):207–14. doi:10.1515/aut-2015-0004.
- Ganesh, J., and K. Ankita. 2018. Impact of weave on functional properties of fabric. Textile Value Chain.
- Göktepe, Ö. 2002. Fabric pilling performance and sensitivity of several pilling testers. Textile Research Journal 72 (7):625–30. doi:10.1177/004051750207200710.
- Grosberg, P. 1966. The mechanical properties of woven fabrics Part II: The bending of woven fabrics. Textile Research Journal 36 (3):205–11. doi:10.1177/004051756603600301.
- Hameed, M.N., Y. Nawab, M. Zubair, M. Umair, Z. Ahmad, and K. Shaker. 2022. Double face fabrics: A tailorable solution for puncture resistant applications. The Journal of the Textile Institute 113 (6):1197–205. doi:10.1080/00405000.2021.1918882.
- Jahan, I. 2017. Effect of fabric structure on the mechanical properties of woven fabrics. Advance Research in Textile Engineering 2 (2):1018. doi:10.26420/advrestexteng.2017.1018.
- Lomov, S.S., A.V. Truevtzev, and C. Cassidy. 2000. A predictive model for the fabric-to-yarn bending stiffness ratio of a plain-woven set fabric. Textile Research Journal 70 (12):1088–96. doi:10.1177/004051750007001208.
- Morton, W.E. 1934. Some observations on fabric strength in relation to yarn properties and density of structure. Journal of the Textile Institute Proceedings 25 (6):262–65. doi:10.1080/19447013408663446.
- Pegoretti, A., E. Fabbri, C. Migliaresi, and F. Pilati. 2004. Intraply and interply hybrid composites based on E-glass and poly(vinyl alcohol) woven fabrics: Tensile and impact properties. Polymer International 53 (9):1290–97. doi:10.1002/pi.1514.
- Realff, M. L., M.H. Seo, M.C. Boyce, P. Schwartz, and S. Backer. 1991. Mechanical properties of fabrics woven from yarns produced by different spinning technologies: Yarn failure as a function of gauge length. Textile Research Journal 61 (9):517–30. doi:10.1177/004051759106100904.
- Saiman, M.P., M.S. Wahab, and M.U. Wahit. 2014. The effect of fabric weave on the tensile strength of woven kenaf reinforced unsaturated polyester composite. In Proceedings of the International Colloquium in Textile Engineering, Fashion, Apparel and Design 2014 (ICTEFAD 2014), 25–29. Singapore: Springer. 10.1007/978-981-287-011-7_5.
- Saville, B.P. 1999. Physical testing of textiles. Boston NewYork Washington, DC: Woodhead Publishing Limited, Elsevier.
- Shaker, K., Y. Nawab, M.A. Asghar, A. Nasreen, and M. Jabbar. 2020. Tailoring the properties of leno woven fabrics by varying the structure. Mechanics of Advanced Materials and Structures 27 (22):1865–72. doi:10.1080/15376494.2018.1527964.
- Triki, E., P. Dolez, and T. Vu-Khanh. 2011. Tear resistance of woven textiles – Criterion and mechanisms. Composites Part B: Engineering 42 (7):1851–59. doi:10.1016/j.compositesb.2011.06.015.
- Umair, M., M. Hussain, Z. Abbas, K. Shaker, and Y. Nawab. 2021. Effect of weave architecture and glass microspheres percentage on the low velocity impact response of hemp/green epoxy composites. Journal of Composite Materials 55 (16):2179–95. doi:10.1177/0021998320987605.
- Witkowska, B., and I. Frydrych. 2008. Static tearing, Part II: Analysis of stages of static tearing in cotton fabrics for wing-shaped test specimens. Textile Research Journal 78 (11):977–87. doi:10.1177/0040517507081310.