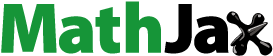
ABSTRACT
In order to investigate the feasibility of developing a new material to substitute disposable plastics to reduce environmental pollution, four kinds of plant leaf fibers (lotus leaf, reed leaf, bamboo leaf and ginkgo leaf) were selected to combined with agar to prepare fully degradable composites (referred as LAC, RAC, BAC and GAC, respectively). The chemical composition, functional groups and thermal properties of plant leaf fibers were analyzed. The morphology of the tensile cross section of the composites was observed, and the mechanical properties, moisture absorption profile and thermal conductivity of the composites were studied. The cellulose content in the plant leaf fibers was relatively high, among which the reed leaf fiber had the highest one, which was 27.75%. The thermal stability of lotus, reed and ginkgo leaf fiber was close, while that of bamboo leaf fiber was poor. Among the four kinds of plant leaf fiber composites, reed leaf fiber/agar composite has the best mechanical properties, and its tensile, flexural and impact strength were 1.81 MPa, 6.59 MPa and 5.09 kJ/m2, respectively. The BAC had a poor internal combination with many internal defects leading to its poor mechanical properties.
摘要
为了研究开发一种替代一次性塑料以减少环境污染的新材料的可行性,选择了四种植物叶纤维(荷叶、芦苇叶、竹叶和银杏叶)与琼脂结合,制备可完全降解的复合材料(分别称为LAC、RAC、BAC和GAC). 分析了植物叶纤维的化学成分、官能团和热性质. 观察了复合材料的拉伸截面形貌,研究了复合材料力学性能、吸湿性和导热性. 植物叶纤维中纤维素含量较高,其中芦苇叶纤维含量最高,为27.75%. 荷叶、芦苇叶和银杏叶纤维的热稳定性接近,而竹叶纤维的热稳定较差. 在四种植物叶纤维复合材料中,芦苇叶纤维/琼脂复合材料的力学性能最好,其拉伸强度、弯曲强度和冲击强度分别为1.81MPa、6.59MPa和5.09 kJ/m2. BAC内部结合较差,内部缺陷较多,导致其机械性能较差.
Introduction
Plastic products have brought great convenience to people in modern daily life, and the consumption of plastic products is huge (Ali et al. Citation2021; Groh et al. Citation2019; Skoczinski et al. Citation2021). In recent years, the pollution and harm caused by plastic waste have gradually become prominent, and the pollution of plastics to the environment has attracted extensive attention all over the world (Xu, Xiang, and Ko. Citation2020; Dessi et al. Citation2021; Schymanski et al. Citation2018; Willis, Hardest, and Wilcox Citation2021). Since the 1990s, various countries have taken a series of environmental protection measures and formulated corresponding legal measures to reduce the environmental pollution caused by plastics. China has also issued a series of “plastic prohibition orders” to improve environmental quality (Charitou et al. Citation2021; Chowdhury et al. Citation2021; Li et al. Citation2021; Manfra et al. Citation2021). Reducing the impact of plastics on environmental pollution not only needs the constraints of laws and regulations, but also needs to find out the materials that can replace plastics through relevant technical research.
Biomass composites are widely favored by researchers because of their green and degradable characteristics (Sanjay et al. Citation2019; Safri Citation2018 Sarasini and Fiore Citation2018). As a substitute for plastics, biomass composites are not inferior to traditional polymer materials in comprehensive performance (Rizal et al. Citation2018; Todkar and Patil Citation2019; Vivek and Kanthavel Citation2019). Al-Oqla (Citation2020) studied the properties of with different content of olive leaf fiber reinforced LDPE composites. When the fiber content was 40 wt%, the flexural strength, flexural modulus and impact fracture stress properties of the composites were significantly improved, and the composite had the largest flexural strength, which was 34.6 MPa. Dehghani et al. (Citation2013) grafted the palm leaf fiber with maleic anhydride, then prepared the composite by injection molding with the treated fiber and PET plastic. The modified palm leaf fiber dimension can improve the tensile strength, bending strength and impact strength of the composite, And it can improve the overall crystallinity of the composite. The mechanical properties of the composite can meet the application in some indoor scenes. Asumani, Reid, and Paskaramoorthy (Citation2012) studied kenaf fiber reinforced PP composites treated with alkali and silane. When the concentration of alkali solution was 5%, the mechanical properties of the composites were significantly improved, and their tensile strength and tensile modulus were increased by 25% and 11% respectively. Kuciel, Mazur, and Hebda (Citation2020) prepared the wood fiber/PLA composite by injection molding process, and studied the reinforcing effect of wood fiber on PLA performance. The addition of wood fiber increases the dimensional stability and crystallinity of the composite, and the increase of wood fiber content will increase the flexural strength of the composite, which can be used in engineering fields. Yaacab, Ismail, and Ting (Citation2016) prepared rice straw/PLA composites by hot pressing method, and studied the effect of rice straw content on the properties of the composites. It was found that when the content of rice straw is less than 20%, the tensile strength and thermal stability of the composites decrease with the increase of rice straw content, The elastic modulus of the composite increased with the increase of rice straw content.
Plant leaves are a common green, cheap and degradable biomass resource, but most of them will be regarded as domestic waste or made into feed (Jiang et al. Citation2018). Gelatin is the product of partial hydrolysis of collagen in animal body or skin. It is a hydrophilic macromolecular colloid with completely degradable characteristics (Oustadi et al. Citation2020; Yang et al. Citation2020). The composites. prepared from plant leaves and gelatin can be completely degraded and have the potential to replace plastic products.
In this paper, four kinds of plant leaf fibers (lotus leaf, reed leaf, bamboo leaf and ginkgo leaf) and agar were used as raw materials to prepare the composites by compression molding technique. The characteristic functional groups and the thermal stability of fibers were investigated by Fourier-transform infrared spectroscopy (FTIR) and Thermogravimetric analysis (TGA). The tensile cross section morphology of the composites were observed through scanning electron microscopy (SEM). The mechanical and moisture absorption properties of the composites were analyzed.
Experimental
Materials
The lotus leaves, and bamboo leaves were obtained from Bozhou in the Anhui Province of China. The reed leaves were obtained from Lianyungang in the Jiangsu Province of China. The ginkgo leaves were obtained from Qingdao in the Shandong Province. Edible grade agar was obtained from the Zhejiang Yinuo Biology Science and Technology company (Zhejiang, China). Glycerin was obtained from the Tianjin Zhiyuan Chemical Agent Company (Tianjin, China).
Preparation of fibers
The fresh plant leaves were washed and cleaned with running water and then dried at room temperature naturally. The dry leaves were crushed and screened into 0.15 mm to get the plant leaf fiber. shows the process of fibers (lotus leaf fibers as an example).
Preparation of composites
Weigh the plant leaf fibers and agar respectively, and the mass of agar was 20 wt%, 10 wt% of the total weight glycerol was added as the waterproof agent, and then mixed evenly. The mixture was well distributed in a 100 × 100 mm metal mold and then use a XLB-D400 × 400 × 2-Z flat vulcanizer (Shanghai Qicai Hydraulic Machinery Company, Shanghai, China) compressed at 120°C under 10 MPa of pressure for 30 min. shows the composite and test samples.
Characterization
Chemical composition analysis
The chemical composition of plant leaf fibers were test according to the NREL standard.
Fourier-Transform Infrared Spectroscopy (FTIR)
The characteristic functional groups of plant leaves and the composites were analyzed by a Nicolet iS-10 spectrometer (Thermo Fischer Scientific, Waltham, MA) at room temperature. The FTIR transmittance spectra were recorded after an average of 16 scans from 4000 cm −1 to 500 cm −1 with a resolution of 4 cm −1.
Thermogravimetric Analysis (TGA)
The thermal stability of the composites were studied by using an STA 449 F3 Jupiter simultaneous thermal analyzer (NETZSCH, Selb, Germany). 10 mg of weight were taken in each sample, and the tests were carried out in argon atmosphere from 35°C to 800°C at a rate of 20°C/min and a flow rate of 20 mL/min.
Morphology studies
The tensile cross section morphology of plant leaves and the interface images of the composites were investigated by a Hitachi S-4800 scanning electron microscope (Tokyo, Japan).
Mechanical properties
The tensile strength and flexural strength properties were determined according to the GB/T standards 1040.1–2006 and 9341–2008, respectively. A universal testing machine (CMT6104, Metz Industrial System (China) Co., Ltd., Shanghai, China) was used to measure the mechanical properties of the composites. The test rate was set at 2 mm/min, and each specimen was tested three times to obtain the average value. The impact strength was tested according to the GB/T 1043.1–2008 by using a XJJ-5 simply supported beam impact testing machine (Chengde Jinjian Testing Instrument Company, Chengde, China).
Moisture absorption performance
The moisture absorption test was carried out in a HZ-2004 G constant temperature and humidity box (Dongguan Hengzhun (Lixian) Instrument Scientific Company, Dongguan, China) according to the GB/T standard 20,312–2006. The dried samples were placed in the box and the temperature was set to (23 ± 0.5) °C and the relative humidity was 85%. The samples were removed and weighed at time intervals of 6, 24, 48, 72, 96, 120, 144, and 168 h. The moisture absorption balance was achieved when the mass of the sample did not change between drying intervals. The moisture absorption rate of the composites was calculated according to the following equation:
where W1 is the mass of the specimen at a certain time and W0 is the initial mass of the specimen.
Thermal conductivity
A D300FX-D15 thermal conductivity tester (Tianjin Foruide Technology Company, Tianjin, China) was used to test the thermal conductivity. Every samples was tested three times to get the average value.
Results and discussion
Chemical composition analysis
is the main composition of plant leaf fibers. It can be seen from the table, for each plant leaf fiber, lignin content is higher, followed by cellulose. In plant leaf fiber, lignin provides rigidity for cell wall, while cellulose plays a supporting role, which is the main reason for providing mechanical properties for fiber, hemicellulose is distributed between them and plays a bonding role (Ortega-Toro et al. Citation2015).
Table 1. The content of main components in plant leaf fibers.
There was a big difference in composition content among different plant leaf fibers. As far as cellulose was concerned, the content of reed leaf fiber was higher, followed by bamboo leaf fiber and ginkgo leaf fiber, and the content of lotus leaf fiber was lower. This showed that among the four plant leaf fibers, reed leaf fiber may has better mechanical properties
Ash is an inorganic component in plant leaf fiber, and its main components are SiO2, Al2O3, etc, which affects the wettability and bonding degree of materials. The ash content of lotus, reed, ginkgo and bamboo leaf fiber decreased in turn.
FTIR analysis
is the FTIR spectra of plant leaf fibers. It can be seen that the characteristic absorption peaks of the main functional groups of the leaf fibers of four plants were the same, and the difference is mainly concentrated on the absorption peak intensity of each functional group. There was an absorption peak of -OH stretching vibration near 3430 cm−1 (Almaadeed et al. Citation2013; Sun, and Wu. Citation2019), and the absorption peak of reed and ginkgo leaf fiber was stronger here indicating that reed and ginkgo leaf fiber contain more -OH. In the composite, -OH in plant leaf fiber can form hydrogen bond with polar groups in agar, while reed and ginkgo leaf fiber had higher -OH content, which was more conducive to hydrogen bond formation when compounded with agar. The peak at 2919 cm−1 is related to C-H stretching vibration in lignin (Wang et al. Citation2020). The peak at 1635 cm−1 is associated with aromatic hydrocarbon skeleton in lignin. The peaks at 1385 cm−1 and 1349 cm−1 present the asymmetric stretching vibration of -C(CH3)3 hydrocarbon bond in lignin. The peak at 1074 cm−1 is attributes to C-O stretching vibration absorption in lignin (Senthilkumar et al. Citation2019).
is the hydroxyl index of plant leaf fibers. The hydroxyl index is the ratio of the intensity of the hydroxyl absorption peak (3430 cm−1) to the intensity of the internal standard peak, which is the absorption peak of the group not affected by the action. The C=C absorption peak at 1598 cm−1 can be used as the internal standard peak. The hydroxyl index can reflect the proportion of -OH in plant leaf fiber. It can be seen from the table that the hydroxyl index of bamboo leaf fiber was higher, indicating that its had a more -OH proportion. -OH is a hydrophilic group, so bamboo leaf fiber and its composites may have a higher moisture absorption rate.
Table 2. Hydroxyl index of plant leaf fibers.
TG analysis
is the TG curves of plant leaf fibers. The degradation process of plant leaf fiber can be divided into three stages. The first stage of temperature range was 40–120°C, which was caused by the evaporation of water inside the plant leaf fiber, this phenomenon generally exists in natural plant fibers (Shanmugasundaram, Rajendran, and Ramkumar Citation2018). The second stage was the temperature range of 200–300°C, this is the stage of the degradation of non-cellulose components such as hemicellulose and lignin in plant leaf fibers, and it was the main stage of plant leaf degradation. The third stage was related to the thermal decomposition of cellulose in plant leaf fiber. The final residue of plant leaf fiber after degradation was mainly ash from plant leaf fiber, and the contents of these residues were lotus, reed, ginkgo and bamboo leaf fiber from high to low, which was consistent with the analysis results of plant leaf fiber composition.
From the DTG curves of plant leaf fibers, it can be seen that the degradation rate of four plant leaf fibers was fast in the second stage, most of the components in plant leaf fibers were rapidly decomposed in this stage. Comprehensive analysis of TGA and DTG curves of plant leaf fibers showed that the degradation rate of bamboo leaf fiber in the second stage was the fastest, and the final residue of was the least, which indicates that the thermal stability of bamboo leaf fiber was the worst.
Morphology studies
shows the SEM image of tensile cross section of the composites. It can be seen from the figure, in LAC, RAC and GAC, the interface between fiber and agar was not obvious, and it was difficult to distinguish displays the tensile, flexural and impact strength between fibers and agar, both of them were well combined into a whole. There were a few holes left by fiber pulling out in the tensile section of the composites and presented a relatively flat step shape indicating that the combination effect between fiber and agar was good, which was beneficial to the stress transmission when under stress. In the tensile section of BAC, independent fibers can be obviously observed, and existed a large number of holes and gaps indicating that the bonding effect between bamboo leaf fibers and agar was poor. The bonding mechanism between plant leaf fibers and agar was that the polar groups of plant leaf fibers and agar can form hydrogen bonds. According to the FTIR results, the content of polar group -OH in bamboo leaf fiber was obviously lower, so its ability to form hydrogen bond with agar was weaker than that of other three plant leaf fibers. The content of polar group -OH in lotus, reed and ginkgo leaf fiber was more and has small difference, so the combination effect of these three plant leaf fibers with agar was relatively good.
Mechanical properties
displays the tensile, flexural and impact strength of the composites. It can be seen from the figure that the tensile strength of LAC, RAC, BAC and GAC were 2.05 MPa, 1.81 MPa, 0.98 MPa and 1.95 MPa, respectively, the flexural strength were 5.9 MPa, 6.59 MPa, 3.27 MPa and 6.58 MPa, respectively, and the impact strength were 4.29 kJ/m2、5.09 kJ/m2、1.11 kJ/m2 and 3.18 kJ/m2, respectively. The mechanical properties of LAC, RAC and GAC were similar, among which the flexural and the impact strength of RAC were the highest, while the mechanical properties of BAC were poor. Overall, the RAC composite had the best mechanical properties.
The hydrogen bond formed between plant leaf fibers and polar groups in agar was the main reason for their combination into composite. Lotus leaf fiber, reed leaf fiber and ginkgo leaf fiber contain more polar groups, so these three plant leaf fibers can combine well with agar. The combination of plant leaf fiber and agar in the composite material had an important influence on the mechanical properties of the composite. A good interface combination will make the composite material transfer stress better when it was stressed showing good mechanical properties. Among the four composites, LAC, RAC and GAC had better interface bonding, so the mechanical properties of these three composites were better, while the interface bonding of BAC was poor, leading to its poor mechanical properties.
shows the tensile force-displacement curves of four kinds of composites. The test load increased with the increase of displacement. When the load reached the peak value, the sample made a cracking sound, and then the load decreased, and the test was finished. The breaking forces of LAC, RAC, GAC and BAC were 33.33 N, 39.36 N, 22.34 N and 10.29 N, respectively. It can be seen that LAC, RAC and GAC had good mechanical properties, while BAC composites had poor mechanical properties, which was consistent with the above analysis.
Moisture absorption performance
is the moisture absorption rate curves of the composites. It can be seen that the characteristics of the moisture absorption rate of the composites were similar, with the moisture absorption rate curves rising rapidly within 0–24 h, slowing down slightly after 24 h, and gradually stabilizing after 72 h, reaching moisture absorption balance. The equilibrium moisture absorption rate of the composites were close, among which, BAC had the largest one, which was 36.36%. The equilibrium moisture absorption rate of LAC was the lowest, which was 32.32%, lower than that combined with other bio-adhesives we studied before (Shi et al. Citation2022)
There are two main reasons for the moisture absorption of composites. First, there were numerous of hydrophilic groups in plant leaf fibers and agar, which will combine with water molecules in the air. Another reason is that the combination effect inside the composite had an important influence on its moisture absorption. A better combination of plant leaf fibers and agar in the composite can lead to a better internal bonding with few defects such as holes and gaps which was not easy to gather water vapor and was beneficial to decrease the moisture absorption rate, while on the contrary, the moisture absorption rate increased. The internal bonding of bamboo leaf fiber/agar composite was poor, so its moisture absorption rate was high.
is the schematic diagram of fiber moisture absorption. Hydrophilic groups directly absorb water by forming hydrogen bonds with water molecules, and the adsorbed water molecules can also connect with water molecules due to their polarity. When the humidity is high, excess indirect water molecules will fill in the gaps inside the fiber and the composite. According to the FTIR analysis, the hydroxyl index of bamboo fiber was high, many hydrophilic groups that can combine with water vapor, so the moisture absorption performance of bamboo fiber in the composite was high. In addition, the internal bonding of BAC was poor among the four composites, and there were many internal voids and holes for indirect water molecules to fill in. On the whole, the BAC had a high moisture absorption rate.
Thermal conductivity analysis
shows the thermal conductivity of the composites. The thermal conductivity of LAC, GAC, RAC and BAC decreased in turn, which were 0.092 W/(m·k), 0.083 W/(m·k), 0.078 W/(m·k) and 0.044 W/(m·k), respectively, all less than 0.23 W/(m·k) which were thermal insulating, this was similar to Benallel’s research (Benallel et al. Citation2021).
The main factor that affects the thermal conductivity of composites was the internal structure. The gaps and holes in composites can collect air, which was a good insulation medium. The air content in the composites seriously affects its thermal conductivity. The combination of fiber and agar in the BAC was poor, and there were many holes and gaps in the composite, which provide a good condition for air gathering. Therefore, the thermal conductivity of the composite was weak and the thermal conductivity was small. However, the other three composites have good internal bonding, so their thermal conductivity was relatively strong and the thermal conductivity was relatively high.
Conclusions
The cellulose content in the four plant leaf fibers was relatively high, among which the reed leaf fiber was the highest, which was 27.75%. The plant leaf fibers had similar functional groups, among which, the content of -OH in bamboo leaf fiber was less, which was not conducive to hydrogen bonding when it was combined with agar. The thermal stability of lotus, reed and ginkgo leaf fiber was close, while that of bamboo leaf fiber was poor.
Among the four kinds of composites, LAC, RAC and GAC had a well combination with few internal defects. The internal bonding of the composite had great influence on its mechanical properties, on the whole, the RAC had the best mechanical properties, and its tensile, flexural and impact strength were 1.81 MPa, 6.59 MPa and 5.09 kJ/m2, respectively.
The thermal conductivity of the composites was less than 0.23 W·m −1·k −1, which were thermal insulating materials.
Highlights
The composites made of natural plant leaf fibers and agar can be completely degraded which were beneficial for reducing environmental pollution, and can be used to substitute plastic products.
The physical and chemical properties of different plant leaf fibers were analyzed.
The hygroscopicity of the composites was explained from the microscopic point of view.
The composites studied in this paper were heat-insulating and nontoxic which have the potential to be used in food packaging field.
Disclosure statement
No potential conflict of interest was reported by the author(s)
Additional information
Funding
References
- Ali, S. S., E. Koutra, M. Kornaros, M. El-Sheekh, E. A. Abdelkarim, D. Zhu and J. Sun. 2021. Degradation of conventional plastic wastes in the environment: A review on current status of knowledge and future perspectives of disposal. The Science of the Total Environment 771:144719. doi:10.1016/j.scitotenv.2020.144719.
- Al-Maadeed, M. A., R. Kahraman, P. N. Khanam and S. Al-Maadeed. 2013. Characterization of untreated and treated male and female date palm leaves. Materials & Design 43:526–13. doi:10.1016/j.matdes.2012.07.028.
- Al-Oqla, F. M. 2020. Flexural characteristics and impact rupture stress investigations of sustainable green olive leaves bio-composite materials. Journal of Polymers and the Environment 29 (3):1–8. doi:10.1007/s10924-020-01889-3.
- Asumani, O. M. L., R. G. Reid and R. Paskaramoorthy. 2012. The effects of alkali–silane treatment on the tensile and flexural properties of short fibre non-woven kenaf reinforced polypropylene composites. Composites Part A: Applied Science & Manufacturing 43 (9):1431–40. doi:10.1016/j.compositesa.2012.04.007.
- Benallel, A., A. Tilioua, M. Ettakni, M. Ouakarrouch, M. Garoum and M. A. A. Hamdi. 2021. Design and thermophysical characterization of new thermal insulation panels based on cardboard waste and vegetable fibers. Sustainable Energy Technologies and Assessments 48:101639. doi:10.1016/J.SETA.2021.101639.
- Charitou, A., R. N. Aga-Spyridopoulou, Z. Mylona, R. Beck and A. M. Addamo. 2021. Investigating the knowledge and attitude of the Greek public towards marine plastic pollution and the EU Single-Use Plastics Directive. Marine pollution bulletin 166:112182. doi:10.1016/j.marpolbul.2021.112182.
- Chowdhury, G. W., H. J. Koldewey, E. Duncan, I. E. Napper, S. E. Nelms, S. Sarker, S. Bhola and B. Nishat. 2021. Plastic pollution in aquatic systems in Bangladesh: A review of current knowledge. Science of the Total Envinorment 761:143285. doi:10.1016/j.scitotenv.2020.143285.
- Dehghani, A., S. M. Ardekani, M. A. Al-Maadeed, A. Hassan and M. U. Wahit. 2013. Mechanical and thermal properties of date palm leaf fiber reinforced recycled poly (ethylene terephthalate) composites. Materials & Design (1980-2015) 52:841–48. doi:10.1016/j.matdes.2013.06.022.
- Dessi, C., E. D. Okoffo, J. W. O’Brien, M. Gallen, S. Kaserzon, C. Rauert, X. Wang and K. V. Thomas. 2021. Plastics contamination of store-bought rice. Journal of Hazardous Materials 416:125778. doi:10.1016/j.jhazmat.2021.125778.
- Groh, K. J., T. Backhaus, B. Carney-Almroth, B. Geueke, P. A. Inostroza, A. Lennquist, H. A. Leslie, M. Maffini, D. Slunge, L. Trasande, et al. 2019. Overview of known plastic packaging-associated chemicals and their hazards. The Science of the Total Environment 651 (9):3253–68. doi:10.1016/j.scitotenv.2018.10.015.
- Jiang, D. M., P. H. An, S. P. Cui, F. Xu, T. F. Tuo, J. Z. Zhang and H. Jiang. 2018. Effect of leaf fiber modification methods on mechanical and heat-insulating properties of leaf fiber cement-based composite materials. Journal of Building Engineering 19:573–83. doi:10.1016/j.jobe.2018.05.028.
- Kuciel, S., K. Mazur and M. Hebda. 2020. The influence of wood and basalt fibres on mechanical, thermal and hydrothermal properties of pla composites. Journal of Polymers and the Environment 28 (4):1204–15. doi:10.1007/s10924-020-01677-z.
- Li, C., M. Sun, X. Xu, L. Zhang and Y. Ye. 2021. Environmental village regulations matter: Mulch film recycling in rural China. Journal of Cleaner Production 299:126796. doi:10.1016/j.jclepro.2021.126796.
- Manfra, L., V. Marengo, G. Libralato, M. Costantini and M. Cocca. 2021. Biodegradable polymers: A real opportunity to solve marine plastic pollution?. Journal of Hazardous Materials 41:125763. doi:10.1016/j.jhazmat.2021.125763.
- Ortega-Toro, R., J. Contreras, P. Talens and A. Chiralt. 2015. Physical and structural properties and thermal behaviour of starch-poly (ɛ-caprolactone) blend films for food packaging. Food Packaging and Shelf Life 5:10–20. doi:10.1016/j.fpsl.2015.04.001.
- Oustadi, F., R. Imani, M. H. Nazarpak and A. M. Sharifi. 2020. Genipin-crosslinked gelatin hydrogel incorporated with PLLA-nanocylinders as a bone scaffold: Synthesis, characterization, and mechanical properties evaluation. Polymers for Advanced Technologies 31 (8):1783–92. doi:10.1002/pat.4905.
- Rizal, S., Ikramullah, D. A. Gopakumar, S. Thalib, S. Huzni and H. P. S. A. Khalil. 2018. Interfacial compatibility evaluation on the fiber treatment in the Typha fiber reinforced epoxy composites and their effect on the chemical and mechanical properties. Polymers 10 (12):1316–29. doi:10.3390/polym10121316.
- Safri, S. N. A., M. T. H. Sultan, M. Jawaid and K. Jayakrishna. 2018. Impact behaviour of hybrid composites for structural applications: A review. Composites Part B: Engineering 133:112–21. doi:10.1016/j.compositesb.2017.09.008.
- Sanjay, M. R.S., S. Siengchin, J. Parameswaranpillai, M. Jawaid, C. I. Pruncu and A. Khan. 2019. A comprehensive review of techniques for natural fibers as reinforcement in composites: Preparation, processing and characterization. Carbohydrate Polymers 207:108–21. doi:10.1016/j.carbpol.2018.11.083.
- Sarasini, E. and V. Fiore. 2018. A systematic literature review on less common natural fibres and their biocomposites. Journal of Cleaner Production 195:240–67. doi:10.1016/j.jclepro.2018.05.197.
- Schymanski, D., C. Goldbeck, H. U. Humpf and P. Furst. 2018. Analysis of microplastics in water by micro-Raman spectroscopy: Release of plastic particles from different packaging into mineral water. Water Research 129:154–62. doi:10.1016/j.watres.2017.11.011.
- Senthilkumar, K., N. Rajini, N. Saba, M. Chandrasekar, M. Jawaid and S. Siengchin. 2019. Effect of alkali treatment on mechanical and morphological properties of pineapple leaf fiber/polyester composites. Journal of Polymers and the Environment 27 (6):1191–201. doi:10.1007/s10924-019-01418-x.
- Shanmugasundaram, N., I. Rajendran and T. Ramkumar. 2018. Characterization of untreated and alkali treated new cellulosic fiber from an Areca palm leaf stalk as potential reinforcement in polymer composites. Carbohydrate Polymers 195:566–75. doi:10.1016/j.carbpol.2018.04.127.
- Shi, K., L. Wang, R. Qi and C. He. 2022. Bio-Adhesives Combined with Lotus Leaf Fiber to Prepare Bio-Composites for Substituting the Plastic Packaging Materials. Journal of Renewable Materials 10 (5):1257–68. doi:10.32604/JRM.2022.017891.
- Skoczinski, P., L. Krause, A. Raschka, L. Dammer and M. Carus. 2021. Current status and future development of plastics: Solutions for a circular economy and limitations of environmental degradation. Method in Enzymology 64:1–26. doi:10.1016/bs.mie.2020.11.001.
- Sun, Z. and M. Wu. 2019. Effects of sol-gel modification on the interfacial and mechanical properties of sisal fiber reinforced polypropylene composites. Industrial Crops and Products 137:89–97. doi:10.1016/j.indcrop.2019.05.021.
- Todkar, S. S. and S. A. Patil. 2019. Review on mechanical properties evaluation of pineapple leaf fibre (PALF) reinforced polymer composites. Composites Part B: Engineering 174:106927. doi:10.1016/j.compositesb.2019.106927.
- Vivek, S. and K. Kanthavel. 2019. Effect of bagasse ash filled epoxy composites reinforced with hybrid plant fibres for mechanical and thermal properties. Composites Part B: Engineering 160:170–76. doi:10.1016/j.compositesb.2018.10.038.
- Wang, Y., J. Wu, Q. Wan, L. Zhang and H. Lei. 2020. Preparation of chitosan/polyvinyl alcohol electrospinning nano-membranes using the green solvent, plasma acid. Journal of Macromolecular Science, Part B: Physics 59 (11):731–46. doi:10.1080/00222348.2020.1800921.
- Willis, K. A., B. D. Hardest and C. Wilcox. 2021. State and local pressures drive plastic pollution compliance strategies. Journal of Environmental Management 287:112281. doi:10.1016/j.jenvman.2021.112281.
- Xu, Q., J. Xian and J. H. Ko. 2020. Municipal plastic recycling at two areas in China and heavy metal leachability of plastic in municipal solid waste. Environmental Pollution 260:114074. doi:10.1016/j.envpol.2020.114074.
- Yaacab, N. D., H. Ismail and S. S. Ting. 2016. Potential use of paddy straw as filler in poly lactic acid/paddy straw powder biocomposite: Thermal and thermal properties. Procedia Chemistry 19:757–62. doi:10.1016/j.proche.2016.03.081.
- Yang, N., H. Chen, Z. Jin, J. Hou, H. Han, Y. Shen and S. Guo. 2020. Moisture sorption and desorption properties of gelatin, HPMC and pullulan hard capsules. International Journal of Biological Macromolecules 159:659–66. doi:10.1016/j.ijbiomac.2020.05.110.