ABSTRACT
A new chemical treatment method to extract rich cellulosic fibers from date palm agro-residues is developed. The method yielded high-performance natural date palm fibers based on multistep process, which is efficient, sustainable, and unique. The proposed method consists of three steps: dewaxing, acetylation, and mercerization, which are unique in terms of time control and their sequence resulting in optimal properties of extracted fiber. Each step is strictly time-controlled and designed to achieve specific objectives in preparation for the next step. Optimization techniques including design of experiment are used to adjust input parameters so as to obtain optimized output from the treatment method. Two approaches are used for supplying heat during the fiber extraction procedure i.e. conventional heat source and microwave heat source. Experimental characterization of extracted fibers is carried out to determine its mechanical and physical properties. Results showed 32% increase in crystallinity degree of the treated fiber over the untreated one. The new method achieved around five-fold increase in ultimate tensile strength and three-fold increase in elastic modulus. The significant enhancement in properties of treated fibers over untreated counterparts confirms the effectiveness of the new process.
摘要
开发了一种新的化学处理方法,从枣树农产品残渣中提取丰富的纤维素纤维. 该方法基于多步骤工艺生产出高性能天然椰枣纤维,具有高效、可持续和独特性. 提出的方法包括三个步骤: 脱蜡、乙酰化和丝光,这在时间控制和它们的顺序方面是独特的,导致提取纤维的最佳性能. 每一步都经过严格的时间控制,旨在为下一步做好准备,实现具体目标. 包括实验设计在内的优化技术用于调整输入参数,以从处理方法获得优化的输出. 在纤维提取过程中使用两种方法来供热,即传统热源和微波热源. 对提取的纤维进行了实验表征,以确定其机械和物理性能. 结果表明,经处理的纤维的结晶度比未经处理的提高了32%. 新方法使极限抗拉强度提高了约5倍,弹性模量提高了3倍. 与未经处理的纤维相比,经处理纤维的性能显著提高,这证实了新工艺的有效性.
Introduction
Researchers over two decades put extensive efforts to utilize agro-residues to extract alternate fibrous material that can be used to produce consumer goods (Moraczewski et al. Citation2021; Nassar et al. Citation2021). Significant amount of research works have been reported on extraction of natural fibers including flax, cotton, jute, hemp, sisal, date palm, rami, kenaf, banana, coir, and its successful adoption to manufacture bio-composites (Al-Jarrah and Al-Oqla Citation2022). However, a limited research work is carried out to address the residues of date-palm that originates from leaves, branches, and stem (Al-Oqla and Sapuan Citation2014; Alhudaib et al. Citation2022). Developing bio-composites from lignocellulosic waste and recycled polymers contributed to minimize synthetic polymer consumption and its impact on environment (Hayajneh, Al-Shrida, and Al-Oqla Citation2022). Furthermore, the synergy of the materials’ features, productivity, and renewability is essential for the correct design of environmental-friendly goods in order to improve sustainable development and customer satisfaction (Al-Oqla and El-Shekeil Citation2019). Currently, few commercial lignocellulosic fibers are employed in industrial applications, and many more are not fully examined (Al-Oqla, Hayajneh, and Fares Citation2019).
As reported in literature, a closer look at the fiber extraction method revealed that the issue of surface treatment of natural fibers takes a prime role in determining the ultimate properties of fiber whether it be strength or interaction with environment. Almost in all cases, the surface treatment techniques played a critical role in order to achieve sustainable and efficient fibers from natural resources in manufacturing bio-composites that is economical in designing industrial components (Das et al. Citation2022; Nassar and Sider Citation2021). Alshammari et al. (Citation2019) studied the properties of epoxy reinforced with fillers extracted from fruit bunch stalk of date palm tree. It was found that reinforced epoxy matrix effectively doubled the strength properties of the developed bio-composite. Besides the natural fibers, it is also necessary to select the best resin to rightly tailor the performance of natural fiber bio-composites (Hayajneh, Al-Shrida, and Al-Oqla Citation2022). A recent study reported on the mechanical performance of different resins systems showed that bio-epoxy resin demonstrates comparable performance to epoxy and polyester resins for use in semistructural bio-composites (Sarkar, Akonda, and Shah Citation2020). Various chemical treatment methods such as mercerization (alkali treatment), silane, malleated and isocyanates coupling agents, permanganates, acetylation, benzoylation, and acylation are adopted to modify surface of fiber to enhance its characteristics as reinforcing agent in polymers (Alzebdeh and Nassar Citation2021; Tanasă et al. Citation2020). The modification processes aimed to eliminate contaminants and impurities as well as increase the crystalline biomass structure of the fiber i.e., cellulose. The crystalline content and rough surface are required characteristics of natural fibers that play a critical role in developing bio-composites (Bendourou et al. Citation2021; Yusriah et al. Citation2014).
The fiber treatment methods reported in the literature focused on either modifying fiber surface to achieve better compatibility between fiber and polymers or enhancing a set of properties related to strength or thermal stability. This research study developed a new chemical treatment method that is unique and comprehensive in terms of reaction sequence and time control. The developed method is systematic and involves thermal and chemical agents in strict sequential order that resulted in improvement of fiber overall characteristics including its surface modification. The processing of untreated fiber using microwave-electrical power accelerates modifications in fiber, results in significant enhancement in tensile strength and modulus. The paper describes the treatment method followed by characterization and concluding with results and discussions.
Material and Methods
Materials
Date palm agro-residues generated from the pedicle part of Khalas date palm tree (Phoenix dactylifera) of 20-year-old were collected for processing. Initially, water retting was performed by immersing the cut pieces (using electric saw) in water for a week after removing its bark. This allows the pedicel bundles to absorb water, making it easier to be separated into individual date palm fiber(s) (DPF). Next, the fibers were extracted manually from the retted pedicels and heated in an oven at 105°C for 24 hours to evaporate moisture.
Multistep Chemical Treatment
In all designated steps of the current treatment method (Nassar et al. Citation2020, Citation2021), a mixture of solid to liquid (solvents) (S:L) ratio (1:20) was used to ensure sufficient chemical reaction taking place at the fiber’s surface. This ratio is commonly used in the natural fiber treatment to secure a sufficient chemical accessibility to the fiber in order to maximize the extraction yield (Bachtiar et al. Citation2011; Leyton et al. Citation2017). The treatment process comprises three phases: dewaxing, acetylation, and mercerization (alkalization) of the fiber assisted by either conventional heating (CH) or accelerated heating (AH) source. The following subsections expand these steps in more details.
Step 1: Surface Dewaxing
The main purpose is to eliminate impurities and contaminants like wax, pectin, and others residing on the surface of untreated fiber. The untreated fibers were dewaxed with ethanol/water (1:1, v/v) in a Soxhlet apparatus. In case of conventional heating, the procedure was conducted at 75°C for 4 hours. The dewaxed fibers were then dried at 105°C for at least 24 hours. In the accelerated heating form, a microwave heat source is used. The method of weight loss and FTIR analysis was used to optimize the microwave power and time variables. To achieve this, three samples, each subjected to one of three microwave power levels (low 250 W, medium 450 W, and high 900 W) at a constant temperature of 75 ± 2°C, were analyzed. After completion, the average weight loss was recorded after being verified by FTIR at an incremental time step of 10 minutes. Thus, the optimal time and microwave power that achieve the highest wax and impurities removal are determined.
Step 2: Acetylation
This step aims to bleach and sanitize the fibers to further improve its processability and anti-microbial properties. For CH option, fibers were soaked in acidified sodium chloride solution (30% acetic acid, 5% sodium chloride) in Soxhlet at 105°C for 2 hours. For AH option, microwave power and time were optimized against the acetylation degree as shown in . Acetylation degree (r) is defined as the ratio of peak intensity (A) at 1724 cm−1 (acetyl group) to the peak intensity (B) at 1026 cm−1 (cellulose backbone). Measurements were taken every 5 minutes and the acetylation degree was recorded, based on the average of three replications.
Step 3: Mercerization (alkalization)
In case of mercerization using conventional heating, an alkali solution of 5% NaOH was prepared, and the acetylated fibers were soaked in the boiling solution at 100°C for 45 minutes. In case of microwave-assisted mercerization, processing parameters were first selected based on the literature and preliminary experimental runs. Then, the parameters were designed and optimized using Design of Experiment (DoE). The selected output in the design is crystallinity degree of fibers (Cr.%) and the independent variables are NaOH concentration (wt. %), microwave power (W), and treatment time (min) at constant temperature (80°C) for all experimental runs. The analysis was carried out using Full Spherical Central Composite Design option within Stat-Ease Design-Expert® software (v 12.0.3.0) including six replicates of central levels to evaluate the reliability and repeatability of outputs. Since microwave accelerates the elimination of amorphous biomass from the fiber, preliminary trials were performed to evaluate the process factors to avoid disruption of fiber and retain its integrity. Otherwise, over extraction of hemicellulose and lignin would weaken the structural integrity of fiber and generate a pulp that is rich in cellulose. Consequently, the levels of the design parameters were selected as shown in . After each experimental run, treated fibers were washed using distilled water several times until pH neutral was attained. outlines a graphical summary of underlying steps within the treatment method along with the impact of each step on microstructure of fiber as shown in .
Figure 2. (a)Graphical presentation of the chemical treatment process, and (b) Process effect on DPF microstructure.
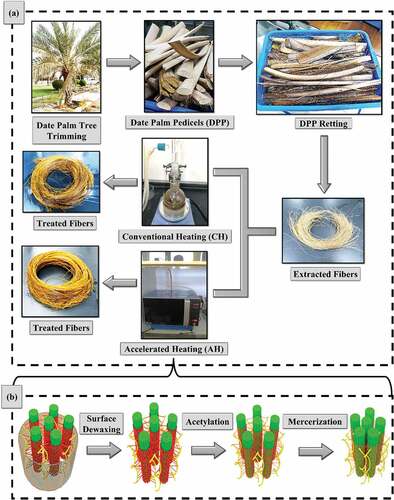
Table 1. Range of levels for parameters used in microwave-assisted mercerization.
Characterization
The analysis of functional groups of the chemical changes of the fibers was obtained by FTIR spectrometer. Samples were scanned over the range 400 to 4000 cm −1 with a total of 64 scans at a resolution of 4 cm −1 at an ambient temperature (25°C).
Soxhlet extraction method and GB/T-5889–1986 standards were used to determine the fiber chemical composition as also reported in the literature (Jiang et al. Citation2010; Wang et al. Citation2015; Watkins et al. Citation2015). First, the untreated and treated fibers were dried at 105°C for 24 hours. After that, the samples, each sample weighs approximately 2 g, were prepared independently for the biomass composition analysis. The untreated fiber was firstly dewaxed using benzene/ethanol. Boiling water was used for further decomposition of water-soluble substances. Diluted ammonium oxalate solution assisted in extraction of pectin. Further, boiling Potassium hydroxide solution was responsible for separating the hemicellulose. Lignin was extracted by boiling Hydrogen Peroxide (H2O2) solution. Eventually, the volume of cellulose was determined by subtracting the total measured chemical composition from 100%. The method was performed on three samples in each step and the average value was recorded.
To evaluate crystallinity of the untreated and treated fibers, chopped fibers were examined at an ambient temperature through step scanning with an X-ray powder diffractometer. Measurements were carried out at 40 kV and 20 mA, with a detector mounted on a goniometer scanning scale from 5° to 60°, at a scanning speed of 5° min−1 using monochromatic CuKα radiation (λ = 1.5406 nm). The crystallinity degree was measured using an empirical method which is explained in (Madhushani et al. Citation2021). For mechanical characterization, estimation of cross-sectional area of fiber was accomplished using an optical microscope with a magnification power of 300-1000×. Then, tensile test was carried out according to ASTM-C155 using a universal testing machine with a 5 kN load cell at a constant speed of 1 mm/s and gauge length of 28. Five samples of each category (UT, CH, AH) were tested, and average values along with standard deviations were recorded. The morphological observations of the fiber surface and cross-section were obtained using scanning electron microscopy JEOL (JSM-7600F). Prior to investigation, the samples were coated with gold.
Results and Discussion
Process Optimization
Fiber Surface Purification
Microwave-assisted dewaxing has been configured based on wax and impurities extraction rate as verified using FTIR. shows that rate of dewaxing is directly proportional to the microwave power, and as such medium and high microwave powers are recommended for higher rate of wax extraction. The low power is also capable to extract wax but at a lower rate. Therefore, a medium power was selected as it is sufficient to improve the rate of wax removal with lower energy consumption while maintaining fiber structure and preventing damage that could occur from excessive microwave power. Overall, it is found that the optimal time which maximizes fiber dewaxing is 60 minutes.
Also, FTIR as shown in indicates that the major internal chemical composition of the fiber was not altered because of dewaxing which preserved the fiber structural integrity. FTIR spectra for all experiments were almost consistent, confirming that no additional absorption bands were applied to the fiber. The characteristic peaks refer to an individual component of natural fiber such as wax, cellulose, hemicellulose, lignin, pectin, and water molecules. The peak at around 1730 cm−1 is due to carbonyl (C=O) stretching of acetyl groups in hemicellulose and ester bonds of carboxyl groups in lignin and hemicellulose. The complete dewaxing is verified by the disappearance of the (C=O) after one hour of treatment time using microwave-assisted heating. The same process requires 4 hours in case of conventional heating-assisted dewaxing. The use of Hydroxyl group (OH) is substantial for modifying the reactivity of fiber surface for further chemical crosslinking with matrix material.
Effect of Fiber Acetylation
The acidified sodium chloride solution is used to sterilize, purify, and bleach the dewaxed fibers. displays the degree of acetylation as a function of time at three microwave power levels. It is noted that the maximum degree of acetylation is attained at high microwave power after 20 minutes of reaction time. However, medium heating power was adopted for this analysis as it has an acceptable degree of acetylation that would not weaken the structural integrity of the fiber as opposed to the use of high power. Acetylation decreases the hygroscopic characteristic of natural fiber and becomes more stable due to the replacement of OH groups in DPF by acetyl groups and thus enhance hydrophobicity. This also can be indicated by OH group intensity reduction as shown in . Based on the FTIR of AH option, it is also found that the spectra were not potentially changed after treatment except for intensity reduction of the peak at 2855 cm−1 which is related to hemicellulose content (Bezazi et al. Citation2014). Thus, the aim of acylation to bleach fibers and remove portion of amorphous biomass is confirmed. This finding was not observed in the case of CH that indicate superiority of using microwave to bleach the fiber and achieve higher yield in a short time.
Analysis of Mercerization Effect on the Fiber
After applying DoE analysis, the optimal conditions to maximize the crystallinity degree were found at lower concentrations of NaOH and medium levels of microwave power for a time of 20 minutes. Results indicate that high concentrations of NaOH and high microwave power tend to degrade the crystallinity degree. This was reflected by massive damage to the cellulose structure due to the increased removal rate of non-cellulosic biomass. The FTIR spectra for final yield of the treatment method is presented in . Bands 1336 and 1316 cm−1 show significant differences in their absorbances. These are the bands assigned to both crystalline celluloses (Cel I and Cel II), and after treatment those band became more intense in the treated DPF than in the untreated counterpart especially in the case of microwave assisted heating. In addition, the absorption peaks at 3328 cm−1 attributed to OH stretching vibration, 2900 cm−1 attributed to CH stretching vibration, 1430 cm−1 attributed to CH2 and OCH plane bending vibration, 1370 cm−1 attributed to CH deformation vibration, and 896 cm−1 attributed to anomeric carbon vibration can be observed in the spectra of treated DPF. All these are characteristic peaks of cellulose (brown shaded in ), indicating extraction of highly rich cellulose fiber (Zhao et al. Citation2015). The differences between microwave and conventional heat assisted treatments can be depicted as the higher intensity of the cellulose backbone (1030 cm−1) and OH group (around 3325 cm1), the lower intensity of hemicellulose peak (2855 cm−1). Therefore, the modified DPF using microwave power is anticipated to be more compatible with the base polymer resulting in improved bio-composite.
In summary, the current technique consists of three steps that should be applied in the specified sequence to achieve an optimal performance, including configured and optimized input variables. Each step is taken to accomplish a particular objective in preparation for the next step; surface dewaxing is used to extract both wax and impurities to expose the wall cell to react with imposed functional groups; acetylation is conducted to bleach and sanitize the fiber to improve its processability in the mercerization step and removes the amorphous cellulose. Mercerization is used to further remove/alleviate amorphous biomass and regulate the penetration level of NaOH-based ionic solution to react with OH group in hemicellulose and lignin to change fiber surface characteristics and increase the content of crystalline cellulose. However, considering the processing time and yield it is found that AH treatment produces better bleached and purified DPF in a shorter time (1.5 hr.) with a reduction of (80%) compared to the CH treatment. It is worthwhile to emphasize that the mercerization (alkalization) seems to be the most effective step in the process as it is optimized (by DoE) to effectively removes lignin and hemicellulose and increase the content of cellulosic fibrils with rearrangement of chains in a unidirectional order direction, thereby improving the fiber’s strength. Furthermore, alkalization with NaOH exposes the OH hydroxyl groups attached to the surface which promotes crosslinking (i.e., chemical reactivity) between the fibers and the matrix in composites. The disruption of hydrogen bonding in the network structure changes the surface morphology by making it rough promoting a strong interfacial bonding between the fibers and the matrix through mechanical interlocking. portrays a flow-chart illustrating the multi-step chemical treatment method of DPF using CH and AH routes.
Biomass Composition
Biomass composition (%) of both untreated and treated fibers after each step using both CH and AH procedures are shown in . The untreated DPF contains mainly cellulose, lignin, and hemicellulose and small quantities of wax, impurities, and pectin. After dewaxing, it is found that mostly wax, impurities, and pectin are removed from DPF in both CH and AH with slightly larger removal in case of AH as indicated by the higher percentage of remaining biomass after dewaxing. Due to acetylation, cellulose content is further increased because of the partial extraction of amorphous biomass which is mainly lignin. The most crucial step is mercerization in which NaOH is used to remove the optimal percentage of amorphous biomass without affecting fiber integrity. After biomass composition analysis, it is shown that cellulose content is increased and DPF became rich in cellulose because of reduction of the extractives and amorphous biomass removal. Moreover, removal of the amorphous material is more evident in the case of AH due to the ability of alkali solution to penetrate inside fiber subsurface.
Morphological
Scanning Electron Microscope (SEM) micrographs were obtained and interpreted to evaluate the effect of biomass composition on fiber morphology and internal structure in each treatment step. The untreated surface in clearly shows a cover of wax layer and other impurities. After dewaxing, thickness of this outer layer is reduced due to wax and impurities removal as confirmed by FTIR. A major removal of impurities and less rough surface are observed in the case of AH compared to CH case, which indicates a higher efficiency of the microwave power to clean the fiber surface. On the other hand, dewaxing did not result in any fiber damage or deterioration, as it only took place at the fiber surface.
demonstrates the surface morphology and cross section of the acetylated fibers. Due to acetylation, cellulose content is further increased because of the partial extraction of amorphous biomass. The microwave power stimulated acetylation to bleach surface and extract further amorphous biomass including pectin and lignin. Whereas CH-acetylation showed no major effect to the dewaxed surface. Similarly, the magnified micrographs of cross-section show a minor change in case of AH to the fiber interior subsurface where the elementary fiber become stuffed and squeezed which is attributed to the biomass removal. This action was not clearly observed in the case of CH, as the microwave power forced the functional groups to penetrate the fiber interior structure.
shows images of the fiber surface and cross section of treated DPF in comparison to untreated DPF after implementation of mercerization, which is the final step of the developed process. It is evident from these micrographs that the surface topography of DPF looks rougher and cleaner in this step of treatment compared to the previous steps. This is because mercerization eliminates a substantial amount of amorphous biomass mainly lignin and hemicellulose. In addition, the fiber backbone structure is preserved, and the fiber surface becomes fibrillated supporting compatibility with synthetic polymer thereby improving fiber/polymer interfacial adhesion. It is worthwhile to mention that the treatment process carefully controls the removal of hemicellulose and lignin to prevent fiber pulping (pure dissimilated cellulose) and maintain fiber structural integrity. In this regard, SEM micrographs confirmed the potency of developed method to enhance the surface topography and preserves the fiber integrity. SEM of cross-section morphology reveals that circular bundles which form structural strength/integrity of fiber were potentially affected by the treatment method. As clearly shown in the corresponding micrographs in , the holes are collapsed and closed due to full removal of amorphous biomass. As lignin was removed, the middle lamella became more packed which cause a gradual elimination of micro-voids as indicated in the square in the magnified images.
Crystallinity Degree
displays XRD patterns of untreated and treated DPF taken after completion of entire treatment process. Results show that both CH and AH procedures did not adversely influence the physical structure of DPF, since both XRD patterns show identical peaks at 21° and 18° for I002 and Iam, respectively. Clearly, the crystallinity degree has been increased owing to the treatment process which partially remove the amorphous biomass, mostly hemicellulose and lignin and promote the crystalline cellulosic content. In specific, crystallinity degree is increased by 32% when microwave is used as a heating source, whereas conventional heating improves crystallinity by 19%. Such a difference is due to the higher removal rate of non-cellulosic biomass in AH technique.
Tensile Properties
Among mechanical properties of interest are the tensile strength, modulus, and elongation at break of DPF, which were substantially increased in case of treated fibers owing to the treatment effect. In the untreated date palm fiber, hemicellulose remains dispersed in the interfibrillar area separating the cellular chains from one another, which makes them always to be in a state of deformation. When a reasonable amount of hemicellulose is removed by the chemical treatment, the interfibrillar region is likely to be less rigid and less dense, thereby making the fibrils more capable of rearranging themselves along the direction of tensile deformation. A dilute content of lignin acts as a bonding medium between cellulose and hemicellulose which is responsible for preserving the structural integrity of the fiber. The overall result of the treatment is a close packing of the cellular chains, which leads to higher tensile strength of the fiber. exhibits stress-strain diagrams for the untreated and treated fibers. The elastic modulus, tensile strength and elongation at break can be extracted from the plot. It is evident from the figure that fiber processed by AH option yielded the maximum strength, but with a reduced ductility. Maximum ductility is achieved in the CH-derived fiber case, but its strength is roughly 33% less than the AH-derived fiber. The trade-off between strength and ductility is a typical material behavior which is observed in this work. Clearly, the AH-based fiber is more brittle compared to the CH-based fiber as modified microstructure contribute to less ductility and high strength.
summarizes the average values of physical and mechanical properties of untreated and treated fibers. The results presented in the table confirm that the multi-step chemical treatment process with microwave-assisted heating results in a major increase in elastic modulus and tensile strength. The tensile strength improved by around 5.5- fold compared to the untreated fibers when AH is used and by 3.7-fold compared to the untreated fiber when CH is used. Similarly, the elastic modulus of treated fiber increased by 3.4 factor in relative to the untreated fiber when AH is used and 86% increase in the case of CH option. A substantial improvement in strength and modulus is highly valuable for the manufacture of polymer-based bio-composites. Thanks to optimized content of ingredients (cellulose, lignin, hemicellulose) and the efficient elimination of nonbeneficial components (wax, impurities), as verified by SEM images (Section 3.3). The elimination of such unfavorable surface contaminants further decreases the discontinuity and structural defects of the fiber. The successful completion of the current treatment process with the aid of heating, the fibrils are rearranged along the main axis, resulting in an improved resistance to deformation along the fiber axis. The experimental findings suggest that the inclusion of hemicellulose and other forms of waxy compounds up to a certain threshold will expand fiber ductility.
Table 2. Summary of average values of physical and mechanical propertied of DPF before and after treatment.
Conclusion
The paper reports a new chemical method to modify natural fibers derived from date palm pedicels agro-residues aiming to extract high-performance fibers. The multistep method is unique in terms of time control and sequencing that effectively integrates processing steps i.e., dewaxing, acetylation, alkalization through optimization of input parameters based on design of experiment. The objective is to control reaction of chemical agents with hydroxyl groups and thereby adjust the contents of cellulose, hemicellulose, and lignin of the fiber. Dewaxing purifies the fiber’s wall cell from wax, impurity, and completely removes pectin. Acetylation eliminates a small amount of amorphous cellulose in acetic acid solution mobilized by sodium chloride, thereby, amend the properties of fiber to become hydrophobic. Alkalization with NaOH facilitated further removal of lignin and amorphous hemicellulose that enhanced the crystalline cellulose backbone. The successful use of chemical agents increased the fiber surface roughness and exposed the OH hydroxyl group that facilitate its application as reinforcing component to polymers. This is a significant contribution in synthesis of high-performance bio-composites, which will ultimately help in exploring new opportunities to develop value-added products using natural fibers sourced from date palm waste.
Highlights
A new treatment method to extract fibers from date palm agro-waste is reported.
The process is unique, efficient, sustainable and improves performance of fibers.
The method effectively uses microwave-assisted heat to modify fibers.
Findings will facilitate the use of modified fibers in making products.
Disclosure statement
No potential conflict of interest was reported by the author(s).
References
- Al-Jarrah, R., and F. M. Al-Oqla. 2022. A novel integrated BPNN/SNN artificial neural network for predicting the mechanical performance of green fibers for better composite manufacturing. Composite Structures 289 (January):115475. Elsevier Ltd. doi:10.1016/j.compstruct.2022.115475.
- Al-Oqla, F. M., and Y. A. El-Shekeil. 2019. Investigating and predicting the performance deteriorations and trends of polyurethane bio-composites for more realistic sustainable design possibilities. Journal of Cleaner Production 222:865–17. Elsevier Ltd. doi:10.1016/j.jclepro.2019.03.042.
- Al-Oqla, F. M., M. Hayajneh, and O. Fares. 2019. Investigating the mechanical thermal and polymer interfacial characteristics of jordanian lignocellulosic fibers to demonstrate their capabilities for sustainable green materials. Journal of Cleaner Production 241:118256. Elsevier Ltd. doi:10.1016/j.jclepro.2019.118256.
- Al-Oqla, F. M., and S. M. Sapuan. 2014. Natural fiber reinforced polymer composites in industrial applications: Feasibility of date palm fibers for sustainable automotive industry. Journal of Cleaner Production 66:347–54. Elsevier Ltd. doi:10.1016/j.jclepro.2013.10.050.
- Alhudaib, K., S. M. El-Ganainy, M. Almaghasla, and M. Sattar. 2022. Characterization and control of thielaviopsis punctulata on date palm in Saudi Arabia. Plants 11 (3):250. doi:10.3390/plants11030250.
- Alshammari, B., N. Saba, M. Alotaibi, M. Alotibi, M. Jawaid, and O. Alothman. 2019. Evaluation of mechanical, physical, and morphological properties of epoxy composites reinforced with different date palm fillers. Materials 12 (13):2145. doi:10.3390/ma12132145.
- Alzebdeh, K., and M. Nassar. 2021. Polymer blend natural fiber based composites. In Fiber reinforced composites constituents, compatibility, perspectives, and applications, 214–38. Woodhead Publishing Series in Composites Science and Engineering. doi:10.1016/B978-0-12-821090-1.00011-9.
- Bachtiar, D., M. Sapuan Salit, E. Zainudin, K. Abdan, and K. Zaman Haji Mohd Dahlan. 2011. Effects of alkaline treatment and a compatibilizing agent on tensile properties of sugar palm fibre reinforced high impact polystyrene composites. BioResources 6 (4):4815–23.
- Bendourou, F., G. Suresh, M. Laadila, P. Kumar, T. Rouissi, G. Dhillon, K. Zied, S. Brar, and R. Galvez. 2021. Feasibility of the use of different types of enzymatically treated cellulosic fibres for polylactic acid (PLA) recycling. Waste Management 121:237–47. Elsevier Ltd. doi:10.1016/j.wasman.2020.11.058.
- Bezazi, A., A. Belaadi, M. Bourchak, F. Scarpa, and K. Boba. 2014. Novel extraction techniques, chemical and mechanical characterization of agave Americana L. natural fibres. Composites Part B: Engineering 66: 194–203. Elsevier Ltd. doi:10.1016/j.compositesb.2014.05.014.
- Das, O., K. Babu, V. Shanmugam, K. Sykam, M. Tebyetekerwa, R. Neisiany, M. Försth, G. Sas, J. Gonzalez-Libreros, A. Capezza, et al. 2022. Natural and industrial wastes for sustainable and renewable polymer composites. Renewable and Sustainable Energy Reviews 158 (January):1–22. doi:10.1016/j.rser.2021.112054.
- Hayajneh, M. T., M. M. Al-Shrida, and F. M. Al-Oqla. 2022. Mechanical, thermal, and tribological characterization of bio-polymeric composites: A comprehensive review. E-Polymers 22 (1):641–63. doi:10.1515/epoly-2022-0062.
- Jiang, W., G. Han, Y. Zhang, and M. Wang. 2010. Fast compositional analysis of ramie using near-infrared spectroscopy. Carbohydrate Polymers 81 (4):937–41. Elsevier Ltd. doi:10.1016/j.carbpol.2010.04.009.
- Leyton, A., R. Pezoa-Conte, P. Mäki-Arvela, J.-P. Mikkola, and M. E. Lienqueo. 2017. Improvement in carbohydrate and phlorotannin extraction from macrocystis pyrifera using carbohydrate active enzyme from marine alternaria sp. as pretreatment. Journal of Applied Phycology 29 (4):2039–48. doi:10.1007/s10811-017-1141-3.
- Madhushani, W., R. Priyadarshana, S. Ranawana, K. Senarathna, and P. Kaliyadasa. 2021. Determining the crystallinity index of cellulose in chemically and mechanically extracted banana fiber for the synthesis of nanocellulose. Journal of Natural Fibers 00(00): 1–9. Taylor & Francis. doi:10.1080/15440478.2021.1958428.
- Moraczewski, K., R. Malinowski, D. Łączny, and M. Macko. 2021. Surface modification of maize stem with polydopamine and tannic acid coatings. Surfaces and Interfaces 26:26. doi:10.1016/j.surfin.2021.101319.
- Nassar, M., K. Alzebdeh, N. Al-Hinai, and T. Pervez. 2021. A new treatment method for cellulose-rich fibers toward high performance bio-composite applications.
- Nassar, M., K. Alzebdeh, A. Munam, N. Al-Hinai, T. Pervez, and F. Al-Jahwari. 2020. Preparation of high-performance fiber from natural fiber (date palm).
- Nassar, M., K. Alzebdeh, T. Pervez, N. Al‐hinai, and A. Munam. 2021. Progress and challenges in sustainability, compatibility, and production of eco-composites: A state-of-art review. Journal of Applied Polymer Science 138 (April):51284. doi:10.1002/app.51284.
- Nassar, M., and I. Sider. 2021. Evaluation of novel compatibility strategies for improving the performance of recycled low-density polyethylene based biocomposites. Polymers 13 (20):20. doi:10.3390/polym13203486.
- Sarkar, F., M. Akonda, and U. Shah. 2020. Mechanical properties of flax tape-reinforced. Materials 13 (23):5485. doi:10.3390/ma13235485.
- Tanasă, F., M. Zănoagă, C. Teacă, M. Nechifor, and A. Shahzad. 2020. Modified hemp fibers intended for fiber-reinforced polymer composites used in structural applications—a review. I. methods of modification. Polymer Composites 41 (1):5–31. doi:10.1002/pc.25354.
- Wang, H., X. Yao, G. Sui, L. Yin, and L. Wang. 2015. Properties of xanthoceras sorbifolia husk fibers with chemical treatment for applications in polymer composites. Journal of Materials Science and Technology 31 (2):164–70. Elsevier Ltd. doi:10.1016/j.jmst.2014.07.004.
- Watkins, D., M. Nuruddin, M. Hosur, A. Tcherbi-Narteh, and S. Jeelani. 2015. Extraction and characterization of lignin from different biomass resources. Journal of Materials Research and Technology 4 (1):26–32. Korea Institute of Oriental Medicine. doi:10.1016/j.jmrt.2014.10.009.
- Yusriah, L., S. Sapuan, E. Zainudin, and M. Mariatti. 2014. Characterization of physical, mechanical, thermal and morphological properties of agro-waste betel nut (areca catechu) husk fibre. Journal of Cleaner Production 72:174–80. Elsevier Ltd. doi:10.1016/j.jclepro.2014.02.025.
- Zhao, Y., C. Xu, C. Xing, X. Shi, M. Matuana, H. Zhou, X. Ma, L. Matuana, H. Zhou, and X. Ma. 2015. Fabrication and characteristics of cellulose nanofibril films from coconut palm petiole prepared by different mechanical processing. Industrial Crops and Products 65(November): 96–101. Elsevier B.V. doi:10.1016/j.indcrop.2014.11.057.