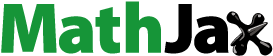
ABSTRACT
Processing parameters and manufacturing techniques of composite materials have a considerable impact on the physicomechanical properties of a final product. The innovative contribution of the current work was to optimize the preparation process of composite materials to obtain the best physicomechanical properties. The mechanical characteristics and the water absorption uptake of mortar/unidirectional Agave americana fibers composite were optimized using an experimental design approach (statistical analysis). A central composite design was considered to determine the optimum preparation conditions of the mortar/A. americana composite to ensure the highest mechanical properties and lowest moisture effect. A second-order polynomial model was developed. The results show that both parameters and their interactions significantly affect the composite’s compressive strength, water absorption uptake, and stress strain. However, only the two studied parameters have a significant effect on flexural strength response. The optimal properties of the composite are 11.14 MPa, 2.03 mm, 3.88 MPa, 0.93 mm, and 14.6%, respectively, for compressive strength, stress strain, flexural strength, displacement, and water absorption. These properties are obtained at specific processing parameters, respectively, 17.6Ve% of agave fibers loading and 4.2% sodium hydroxide fibers treatment solution concentration. The adequate treatment process was proven when testing fibers morphology (Scanning electron microscopy) and their crystallinity index (X-ray diffraction).
摘要
复合材料的加工参数和制造技术对最终产品的物理机械性能有相当大的影响. 当前工作的创新贡献是优化复合材料的制备工艺,以获得最佳的物理力学性能. 采用实验设计方法(统计分析)优化了砂浆/单向龙舌兰纤维复合材料的力学特性和吸水率. 考虑采用中心复合设计来确定砂浆/龙舌兰复合材料的最佳制备条件,以确保最高的机械性能和最低的水分效应. 建立了二阶多项式模型. 结果表明,这两个参数及其相互作用显著影响复合材料的抗压强度、吸水率和应力应变. 然而,只有两个研究参数对弯曲强度响应有显著影响. 对于抗压强度、应力应变、弯曲强度、位移和吸水率,复合材料的最佳性能分别为11.14MPa、2.03 mm、3.88 MPa、0.93 mm和14.6%. 这些性能分别在特定的工艺参数下获得,即17.6Ve%的龙舌兰纤维负载和4.2%NaOH纤维处理溶液浓度. 在测试纤维形态(MEB)和结晶度指数(XRD)时,证明了适当的处理工艺.
Introduction
Many plant fibers’ structures and qualities have been investigated in recent years as part of major efforts to build composites reinforced with plant materials. Composites reinforced with natural fiber presented a low-density, a long-lasting alternative to synthetic fiber composites, a more efficient, and an adaptive solution to environmental and economic challenges (Langhorst et al. Citation2021; Mehrez et al. Citation2022a; Mehrez et al. Citation2022b). As people become more conscious of the necessity of conserving and recycling natural resources, the range of plant fiber resources available for such purposes has grown (Kumara et al. Citation2021; Mancino, Marannano, and Zuccarello Citation2018; Sakuri et al. Citation2020; Sathiamurthi et al. Citation2021).
Biocomposites reinforced with Agave fibers are environmentally friendly or recycled materials that have already been used in the automobile industry (Ali et al. Citation2021), construction (Langhorst et al. Citation2019), and other fields (Mancino, Marannano, and Zuccarello Citation2018). Agave fibers are mixed with polyester (Kumara et al. Citation2021; Sakuri et al. Citation2020), epoxy (Sathiamurthi et al. Citation2021), biopolymers (Torres-Tello et al. Citation2017), and cement (Zhu et al. Citation1994) matrix. However, Agave fibers offer good mechanical properties, such as high toughness, strong fiber-matrix adhesion, and low damageability. These qualities can be enhanced with the right-treatment process. Many researches in the literature review focus on the treatment effects of raw natural fibers. Interfacial adhesion between plant fibers and matrix is a real challenge. This determines the final qualities of the composites and claims the review study (Ramesh, Palanikumar, and Reddy Citation2017) on the relevance of the interface, the impact of various types of surface alterations, and numerous types of composite matrices.
Another review study (Ramesh et al. Citation2020) focused on the overall environmental impact of fiber reinforced materials products and processes. Plant fiber-based biocomposites, with current technology, require significantly more polymers, which somehow balances the environmental damage avoided by fibers and composites (Ramesh, Rajeshkumar, and Bhuvaneswari Citation2021). When comparing the methods for extracting various leaf-based fibers, it was discovered that water retting and decortication result in higher productivity, according to Ramesh, Rajeshkumar, and Bhuvaneswari (Citation2021). To create composites using leaf fibers reinforcements, compression molding or hot pressing was often utilized. In other instances, dual-screw extrusion was used (Ramesh, Rajeshkumar, and Bhuvaneswari Citation2021).
Fibers can significantly improve the mechanical characteristics of a cement-based matrix (Shah and Ouyang Citation1991). Understanding the interaction between various fibers and cement-based matrices is essential for future developments. Cement-based materials have a low fracture strength and a low value of strain relative to their tensile strength. The inclusion of fibers can significantly increase the tensile strain capacity of cement-based materials. According to Sathiamurthi et al. (Citation2021), the composite with 20% of Agave americana/kenaf fibers reinforced with epoxy hybrid composites had the highest flexural strength. Sakuri et al. (Citation2020) investigated the mechanical strength of composites made from Agave cantala with an unsaturated polyester matrix and microcrystalline cellulose. They tested the treatment with 6% sodium hydroxide (NaOH) of cantala fiber with different immersion times (0 h, 3 h, 6 h, 9 h, and 12 h). They discovered that cantala fiber had a crystallinity index of 73.65% after 6 h of alkali treatment. They investigated the morphology of fibers following different alkali treatments using scanning electron microscopy (SEM). Its experimental results show that hemicellulose, wax, and other contaminants were eliminated. According to Huerta-Cardoso et al. (Citation2020), Agave fibers were immersed in four different surface treatments: alkali, acetylation, enzymatic, and silane treatments to improve their morphology and compatibility with polylactic acid. Jani et al. (Citation2020) studied experimentally the thermal and mechanical properties of A. americana fibers (AAFs) with 7.5 wt% and 10 wt% alkali treatment. Their results demonstrated that the treated fiber with 10 wt% NaOH has good mechanical and thermal properties when compared to 7.5 wt% NaOH. Jacob et al. (Citation2004) investigated the effects of different NaOH concentrations (0.5%, 1%, 2%, 4%, and 10%) on sisal fiber-reinforced composites. They found that the 4% of NaOH treatment, at room temperature, gives the highest tensile strength. Sisal fiber-reinforced polyester composites treated with 5% NaOH showed higher tensile strength than composites treated with 10% NaOH solution concentration, according to Mishra et al. (Citation2003). Natural fibers undergo more delignification at higher alkali concentrations, resulting in weaker or broken fibers.
Kumar et al. (Citation2022) applied a variety of natural fiber surface treatment techniques, to improve its physicomechanical properties. The Himalayan agave fibers were chemically treated at different concentrations of 5%, 10%, and 15% for 24 h and reinforced at 10 wt% of fiber loading into ceramic composites. Their SEM results (Kumara et al. Citation2021). show that fiber breaking, debonding, debris, crack surface, and microplowing are responsible for weak mechanical behavior of composites. Kumar et al. (Citation2020) demonstrate that debonding, fracture surfaces, and microplowing are evident in the SEM investigation of worn treated surfaces of Himalayan agave fiber with alkali-treated 2% NaOH.
Tensile and flexural properties of A. americana/kenaf fibers reinforced epoxy composites are investigated in Sathiamurthi et al. (Citation2021). The length of fibers is varied from 1 cm to 4 cm, and its relative fiber weight fraction is varied between 10% and 25%. Their results show that the composite constructed from fibers with a length of 3 cm and a relative loading of 20% had the maximum tensile strength and tensile modulus. Madhu et al. (Citation2020) focus on the use of A. americana plant as potential reinforcement in polymeric composites. NaOH, stearic acid, benzoyl peroxide, and potassium permanganate were used to chemically treat the extracted fibers. Jain et al. (Citation2019) studied the effect of fiber pretreatment on alkaline horrnification. They analyzed the moisture uptake behavior of Agave fiber composites. It was observed that water retention value, which is a measure of affinity toward moisture, decreases with each subsequent hornification cycle. The tests demonstrated a significant influence of alkaline hornification on the improvement of the hydrothermal durability of the Agave fibers. Kumara et al. (Citation2021) investigated experimentally the physicomechanical and Taguchi-designed sliding wear properties of novel Himalayan agave fiber (fiber’s sizes of 3 mm, 5 mm, and 7 mm and fiber’s loading of 5 wt.%, 7 wt.%, and 9 wt.%). They showed that polyester composites with a 7 wt.% agave fiber loading can achieve maximum flexural strength (47.02 MPa) and hardness (48.01 Hv).
Most researchers commonly use classical experimental method, which involves changing one parameter at a time while leaving others constant. Response surface methodology (RSM) has been identified as an efficient statistical tool due to its time-consuming nature and cost difficulties. In fact, fewer experiments are necessary, and studies are faster and more reliable. Kandar and Akil (Citation2016) used one of the several experimental strategies, the Box-Behnken Design (BBD) approach, to enhance the mechanical properties of woven flax/polylactic-acid (PLA) by using Minitab 16 to optimize a set of compression molding variables. Tharazi et al. (Citation2017) used the same BBD design to optimize hot press parameters on tensile properties of unidirectional kernel fibers reinforced PLA composite. Kiran et al. (Citation2011) used the Taguchi approach to discover that the press forming temperature had the greatest impact on the mechanical properties of the composite. Molding temperature and dwell time length are the optimal parameters for molding conditions for foam material and cup depths of mold, according to Wu et al. (Citation2012).
This paper deals with an experimental design to optimize a novel biocomposite behavior. The research goal is to optimize the composite material preparation process to get the best physicomechanical properties. Suitable procedures to prepare biocomposites are described. The corresponding experimental design guidelines are given. The results are evaluated, and the effect of NaOH concentration and fibers volume percentage on the composite’s physicomechanical properties are discussed.
Materials and methods
Reinforcement and matrix materials
The studied composite samples were made with cement, sand, and AAFs. The mortar was prepared from the Portland cement (1/3 mass ratio) mixed with grains sand having a maximum granulometry distribution of 1 mm (2/3 mass ratio). For all composites, the weight ratio of water to cement, W/C, was set at 0.8. The chemical combinations of cement CEMII/A-L32.5 R is shown in .
Table 1. Chemical properties of Portland cement CEMII/A-L 32.5 R.
Extraction of the Agave fiber
The extraction of rigid lignocellulosic fibers (such as Agave fibers) from perennials growing on Tunisian soil is both scientifically and economically interesting. In this experimental study, fibers are removed in the open air using water retting. This sort of retting follows the same microbe development concept as air retting, with the exception that the leaves (of Agave, for example) are submerged in water for many days (between 15 and 20 days until fibers are delignified and nonadherent). Water retting is done in a tank with 37°C water. Anaerobic bacteria are used to treat around 5–7 kg of Agave leaves cut into strips ().
In this work, the same extraction procedure as done by Bezazi et al. (Citation2014) was used. The leaves were immersed in a barrel for 10–13 days, according to the method utilized. Due to the rapid development of bacteria in a confined environment with low water vaporization, using a closed barrel speeds up the biodegradation of the leaves matrix. Before testing, the washed A. americana was dried in the sun for 72 h and then stored in vacuum-sealed plastic containers. enumerates the chemical composition of raw AAF (Jani et al. Citation2020). When agave fibers are compared to other fibers, we may deduce that they belong to the family of hard fibers extracted from the leaves of certain plants. These fiber characteristics distinguish them from other fibers in terms of morphology, physical properties, mechanical properties, and chemical composition.
Table 2. Chemical composition of raw AAFs (Jani et al. Citation2020).
Sodium hydroxide surface treatment of Agave americana fiber
The hydrophilic character of natural fibers and especially AAFs is the main disadvantage of using them in building materials. In the present study, NaOH is used to chemically preserve the AAFs, to reduce their water uptake, and to improve the interfacial adhesion between AAFs and the mortar matrix. The alkali solution is used to treat fibers with five concentrations: 4.2 wt%, 5 wt%, 7 wt%, 9 wt%, and 9.8 wt%. Fibers are dipped in NaOH treatment for 12 h at room temperature (Jani et al. Citation2020). The treated fibers are rinsed with ordinary water and sun-dried for 2 days. NaOH treatment aims to remove lignin, wax, and hemicellulose. It cleanses the outer surface of the natural fiber and increases its strength (Ben Sghaier et al. Citation2012; Bessadok et al. Citation2008Mehrez et al. Citation2022c; Santana et al. Citation2021).
Volume fraction of fibers
For the preparation of composite samples, AAFs were used to replace a fraction of the cement and sand in the mixture. The fiber volume content was varied to create composite samples. 10.8Ve%, 15 Ve%, 25 Ve%, 35 Ve%, and 39.1Ve% are the percentage of A. americana in the composite’s samples.
Composite material preparation
The obtained dry fibers were cut manually into bundles of 12 cm in length. (a) Cement and sand were mixed for 3 min, (b) Agave fibers were added, and the three constituents were mixed for 2 min, (c) water was gradually added and mixed continually for 4 min, and (d) the prepared blending was quickly versed in the molds to ensure excellent homogenization of the different components of the prepared samples ().
Mechanical testing was performed on samples with a dimension of V = 16 × 16 × 4 cm3. After 24 h, all the samples were demolded and stored in the laboratory for 28 days. The temperature was around 25°C, with a relative humidity of around 50%.
Flexural tests
According to ASTM D790–Citation10, the flexural test was performed by a three-point bending method with the electronic Universal Testing Machine (EZ 50 kN capacity machine) with a cross-head speed of 5 mm/min at room temperature. The specimen was freely supported by two supports in a span of 100 mm. The load was applied in the middle of the top surface of the specimen, which develops a crack and the specimen deforms. The obtained load versus displacement curves were used to calculate the flexural strength and modulus.
Compressive tests
In the compressive test, the six half prisms of the sample produced after the rupture in the flexural test were employed. A steel plate of a cross-section of 4 × 4 cm2 is placed on the half of the sample after the flexural test. The compressive tests were done at a crosshead speed of 5 mm/min.
Water absorption at saturation
Water absorption was determined by immersion. Samples composed of bundles of treated fibers were dried at 60°C for 24 h, weighed in a numerical balance with a precision of 10−4 g, and placed inside a beaker containing distilled water at room temperature (25°C). The weight difference was measured every hour until saturation and moisture content.
X-ray diffraction
The crystallinity of natural AAFs is measured using the X-ray diffraction (XRD) method and compared with treated ones. A Bruker D8 advance diffractometer with CuKα (λ = 1.541 Ǻ) was used to identify these fibers. Cu-Kα radiation at 40 KV and 40 mA was used to scan both fibers in the 2 range from 10° to 50° at room temperature, with a step size of 0.020°. Wang, Ding, and Cheng (Citation2007) presented the following technique for determining the crystallinity index of natural AAFs:
where is the sum of the areas under all the diffraction peaks and
is the sum of the areas corresponding to the major important crystalline peaks from cellulose I.
Scanning electron microscope analysis
The morphology of the fibers is investigated using an SEM JEOL JSM 5400. To fix the fibers, silver plates were employed. They were then coated with a thin coating of gold in a vacuum chamber to make them conductive and allow accurate examination. The SEM is used to compare morphological views of natural A. americana-treated and -untreated fibers in order to investigate the impact of treatment on the porosity of composite samples.
Results and discussions
The volume fraction of fibers and concentration of alkali treatment solution are typically, the most critical processing parameters. The effect of these two parameters on the physicomechanical properties of the composite made with AAFs was discussed. For this purpose, five levels were considered for each parameter based on an experimental design.
Experimental design methodology
Most researchers use the traditional experimental approach, which entails changing one parameter at a time while maintaining others at constant levels (Chen et al. Citation2013). The conventional method requires a lot of time and resources. The RSM has been identified to be an efficient statistical tool. It needs lower number of experiments. Thus, experiments are faster and more effective (Chang et al. Citation2014). A total of 13 experimental runs including 5 replicates of the central point were performed. The settings of the parameters are as depicted in . These parameter settings were considered based on a preliminary study.
Table 3. List of parameters and levels.
Results and discussion
The results of the 13 runs to determine mechanical properties and the water absorption uptake of composites are illustrated in . The two factors tested in this study are fibers’ volume fraction and the concentration of fibers treatment solution. The average compressive strength response ranged from a minimum of 1.54 MPa to a maximum of 10.5 MPa, while for flexural strength the response ranged between 1.58 MPa and 3.88 MPa. The average displacement response ranged from a minimum of 0.32 mm to a maximum of 1.14 mm while the obtained values of stress response ranged between 0.43 mm and 1.9 mm. And the water absorption uptake response ranged from a minimum of 14.32% to a maximum of 19.58%.
Table 4. Arrangement of experimental design.
Determination of the significant parameter on the studied responses
The Pareto graph allows the detection of the most relevant variables, and their interactions impact on the studied response. The lengths of each bar in this chart are proportional to the absolute value of the estimated effects (Gheith, Aloui, and Ben Nasrallah Citation2012). Effects that cross the vertical line (y=α) are statistically significant at 95% confidence level. The value of α is calculated based on the t-test expression:
The Pareto chart depicted in can be used to describe the single effect of all studied factors as well as their interactions.
The performance of the mortar/AAFs bioreinforced composites, studied in this work, has been evaluated via mechanical testing and water absorption uptake approaches. An optimization formulation of a composite material with two parameters was targeted for which a mixture design of experiment was adopted. Pareto charts of five different responses are presented in . For such an experimental design, one practical way of understanding the effect of each parameter is by studying the main effect charts. It was observed that the variation of AAFs’ volume fraction (A) affects, significantly, the mechanical proprieties as well as the water absorption uptake. It was also found that the varying concentration of NaOH solution for fibers treatment (B), did not affect the displacement of the studied mortar composites. The conjugate effect of fibers volume fraction (AA) is more significant on compressive strength, stress strain, and displacement responses. For water absorption response, the conjugate effect of fiber treatment solution’s concentration (BB) has the most significant effect. However, the interaction (AB) between fibers volume fraction (A) and fibers treatment solution’s concentration (B) is not significant for all studied responses.
ISO-surface response
The ISO-response surfaces were plotted to determine optimum conditions for the preparation of composites (). There were two factors for a goal to construct desirability indices: fibers volume faction and fibers treatment solution’s concentration. The goal of the present experimental design was, on the one hand, to maximize the strengths of the studied composites and, on the other hand, to minimize moisture uptake behavior. Therefore, the target value of compressive strength, typical stress strain, flexural strength, and displacement responses were the highest values, and the target value of the water uptake response was the lowest value from the obtained experimental results. In this study, the flexural and compressive properties of the biocomposite compromised with level of −1.414 and level of −1 on fibers volume fraction and fibers treatment solution’s concentration. These levels of the independent variables yield the highest responses of flexural and compressive strengths, respectively, 3.9 MPa and 10.6 MPa. The present results show that the addition of AAFs decreases flexural and compressive strengths. However, the fibers treatment solution’s concentration increases leading to a rise in displacement as well as in stress strain. To minimize the moisture behavior of the composite, the water absorption uptake response must be minimized. Obtained results agree with previously published results: Rojas Clemente (Citation2021) tested the geopolymers reinforced by AAFs on compressive and flexural loads of 7 days of age. He observed that the compressive strength increased by 12% at 0.75 (wt.%) and the modulus of elasticity in compression by 13% at 1% (wt.%). The flexural modulus increased up to 21%, and the flexural strength did not change significantly. When the agave fibers reinforced polymer composite, an increase in several mechanical properties (impact, tensile and flexural strength, and tensile and flexural modulus) was reported (Cisneros‐López et al. Citation2017; Corral et al. Citation2016). According to , the AAFs loading should be in the range of 15% to 20%Ve%, and the NaOH concentration in the fibers treatment solution should be in the range of 5% to 7% to ensure minimal water absorption uptake. The porous structure of AAFs is mainly responsible for the composite’s hydrophobic character. Mehrez et al. (Citation2022a) showed the evolution of water absorption uptake for both considered composites reinforced wood and cereal fibers vs. fibers concentration. They approved that the water absorption decreases with increasing fiber concentration. Mehrez et al. (Citation2022c) showed that the water absorption of the composite material increases significantly with fiber inclusion and slightly decreases with fiber chemical treatment.
Regression model
The models generated from the regression based on analysis of variance and their goodness-of-fit statistics are summarized in . The fitting method of backward elimination used here resulted in a combination of interaction terms in the regression that are statistically significant to the studied response. The goodness-of-fit statistics showed that all models generated exhibit a high R2 and therefore the models fit the experimental data very well. In addition, S (in the units of the response) is the standard deviation of the distance between the data values and the fitted values, which are reported to be in an acceptable low range for all models. R2pred (predicted R2) represents how well the model predicts the response for new observations and the values obtained here demonstrate that the models have good predictability of the fitted values. The R2 was above 89%, 95%, 86%, and 95% of the investigated parameters of compressive strength, stress strain, displacement, and water absorption, respectively. As shown by Gheith, Aloui, and Ben Nasrallah (Citation2013), the regression coefficient is higher enough to conclude that the predicted value is close to experimental values, proving that the model is fully applicable. A higher value of regression coefficients can be directly translated to a greater effect of the independent variables on the responses (Chang et al. Citation2014).
Table 5. Regression models and their goodness-of-fit statistics developed for the studied responses.
The volume fraction of fibers showed the highest regression coefficient value for all responses. Therefore, it can be said that fibers volume fraction, compared to fibers treatment solution’s concentration, had the greatest effect on mechanical properties as well as water absorption uptake. Moreover, the positive coefficients for the independent variables indicated a favorable effect on the physicomechanical properties. The negative coefficients among the three independent variables indicate a partitioning favorable effect on the physicomechanical properties.
The probability values P for each response are summarized in . It was found that major terms in the model had a significant effect on studied responses. For all composite responses, the interaction (AB) between fibers volume fraction and fibers treatment solution’s concentration was not significant (P > .05). The volume fraction of fibers (A), the concentration of fibers treatment solution (B), the two-level interaction of fibers volume fraction (AA), and the two-level interaction of fibers treatment NaOH solution concentration (BB) were all significant (P < .05) for flexural strength, typical stress strain, and water absorption uptake composite responses. The volume fraction of fibers (A) and the fibers treatment solution’s concentration (B) were significant for the flexural strength response. All other model terms were determined to be not significant. However, for displacement, the volume fraction of fibers (A) and the two-level interaction of fibers volume fraction (AA) were significant. A higher value of regression coefficients can be directly translated to a greater effect on the independent variables of the responses.
Table 6. Probability values of approximate polynomials for response variables in experimental design.
Optimization of parameters
In this section, the formulation was done to find a combination of both variables, namely, fibers volume fraction and fibers treatment solution’s concentration, which resulted in the desired combination of several responses (mechanical properties and water absorption uptake studied). Due to the number of variables involved and the responses studied, the common approach of iso-surface response and Pareto charts, followed by overlaying the contours of all responses would be too complicated to find an optimized formulation. It would not be reasonable, either, to draw conclusions based on individual trace plots of responses. Therefore, the “response optimization” was employed to identify a combination of mixture components yielding properties targeted for a particular application. The maximum predicted values for mechanical proprieties and minimum value of water absorption uptake as well as experimental optimum values for maximizing mechanical responses and minimizing water absorption responses could be gained from the model equations (). By using point prediction from the numerical optimization available, the optimal parameter setting is 17.6Ve% of fibers loading, 4.2% of NaOH concentration solution for fibers treatment with the desirability of 0.93. Confirmation runs were conducted to verify whether the predictions were accurate. These values were compared to those of the mortar composite. The mechanical property values are higher than mortar composite without fibers. Rojas Clemente (Citation2021) demonstrated that 1% NaOH concentration over 1 h was chosen as the optimum condition to prepare a composite material from AAFs on the mechanical properties of fly ash-based geopolymer. The optimal concentration is 7.5% alkali-treated AAF-reinforced epoxy composite. Higher alkali concentrations increase delignification in natural fibers, which results in weaker or damaged strands (Mishra et al. Citation2003 and Jacob et al. Citation2004). Based on the experimental design methodology, the obtained optimal parameters are shown in .
Table 7. Properties of the optimal parameter.
shows the strain stress diagram of reference mortar and run 9 (optimal of NaOH concentration). The experimental results obtained in the study indicated that the addition of 25% Ve of treated AAFs with 4.2% NaOH (run 9) to cement mortar tends to increase peak stress and strain.
X-ray diffraction
To approve the obtained results from the previous numerical optimization, the XRD patterns of A. americana-treated fibers at different NaOH concentration solutions were collected. The results are presented in . The patterns exhibited an intense peak when 2θ = 22° (I002) for treated and untreated fibers. This peak corresponds to the crystallinity region in the fiber. The non-crystalline region of the fiber is due to the valley between the peaks which was assigned as Inon-Cr when 2θ = 18°. It is clearly seen that the treated fibers with 4.2% NaOH peak at the 2θ = 22° are more intense and narrower, which indicated a higher degree of crystallinity in these fibers compared to other treated and untreated fibers. The calculation of the crystallinity index results (EquationEquation 1(1)
(1) ), is shown in . This phenomenon was approved by the authors Ben Sghaier et al. (Citation2012) and Joonabi et al. 2010. Mehrez et al. (Citation2022c) also observed a rise in the crystallinity index of wood aggregates for small NaOH concentration (1% and 2%) and a decrease for higher NaOH concentration (6% and 10%). Gu (Citation2009) demonstrates that the use of 10% NaOH concentration decreases the tensile strength of treated coir fiber at room temperature 20°C for 48 h when compared to the use of 2%, 4%, 6%, and 8% NaOH concentration. It showed how bad the fiber degradation was in the 10% case. The crystallinity index of AAFs increases for alkali treatments not exceeding 2% NaOH solution at 30°C for 1 h, as shown by Oudiani et al. (Citation2011), whereas higher NaOH concentrations (>2%) result in a considerable decrease in the crystallinity index.
Table 8. Crystallinity index of AAFs.
SEM
MEB assessment is a powerful tool for examining the morphology of fiber surfaces. reveals the difference between raw, 4.2%NaOH-treated and 9.8%NaOH-treated AAFs’ surfaces. AAF has a cylindrical shape and is composed of a straight set of microfibrils, as can be observed on . Waxes, oils, and other significant impurities are also present on the fiber’s surface. Given that, chemical treatments, in general, are thought to remove impurities and contaminants from the fiber’s surface. From the morphology of 4.2%NaOH-treated AAF (). It is clearly seen at this solution concentration, the surface of AAF becomes cleaner and smoother compared to raw AAF. In addition, some pores appeared on the surface of the treated fibers which will promote interlocking bonding between the fiber and the cement matrix which explains previously obtained mechanical results. After treatment with a higher NaOH concentration (9.8% NaOH), the morphology of AAF () changed significantly. The AAF was totally destroyed and a lot of tears appeared on its surface. This explains the high sensitivity of 9.8% NaOH treated fibers to water absorption, which is by consequence causing probably a weak adhesion between the fibers and the cement matrix. According to Kumar et al. (Citation2020), debonding, fracture surfaces, and microplowing are evident in the SEM investigation of worn treated surfaces of Himalayan agave fiber with alkali-treated 2% NaOH. The same observation (destruction of the fiber surface after microscopic observation) was made by Mehrez et al. (Citation2022c), when increasing the concentration of the NaOH-treated solution of wood aggregates.
Conclusion
The present study proposes an experimental design approach to predict the physical and mechanical behaviors of mortar/A. americana composite. The studied biocomposites show that the compressive strength ranged from 1.02 to 15.96 MPa, typical stress-strain ranged from 0.457 to 2.781 mm, flexural strength ranged from 2.707 to 5.010 MPa, displacement ranged from 0.465 to 1.520 mm and water absorption uptake from 14.252 to 13.96%. The regression model was selected for modeling the mechanical properties and water absorption uptake due to its high significance level. The R2 values of the model for compressive strength, stress, flexural strength, displacement, and water absorption were 89.4%, 95.16%, 63.4%, 86.09%, and 95.85%, respectively. The influence of two dependent parameters (A) and (B) on mechanical properties and water absorption uptake of the mortar/AAF composites were investigated through iso-surfaces. Parameters (A), (B), (AA), and (BB) and their interactions (AB) were found to have a significant effect on mechanical proprieties and water absorption uptake. The optimum area in the designated range of process parameters was found using iso-surface plots and optimum parameters were achieved at a fibers volume fraction of 17.6Ve%, and 4.2% NaOH concentration of fibers treatment solution. The performed MEB and XRD analysis of treated and untreated fibers comparison confirm the optimum result obtained from the established experimental design.
Highlights
Mechanical properties of Agave americana reinforced cement mortar are studied.
Extraction and different pretreatment processes of A. americana fibers reinforced cement mortar are described.
An experimental design was developed to detect the optimum fibers content as well as the adequate concentration of the used treatment solution that allows higher mechanical properties and lower water uptake of the proposed composite.
The morphology and the crystallinity index of raw and treated Agave fibers were compared.
Abbreviations
DOE | = | : Design of Experiments |
Ve% | = | : Volume fraction |
RSM | = | : Response Surface Methodology |
SEM | = | : Scanning Electron Microscope |
XRD | = | : X-ray diffraction |
Acknowledgments
This work has been performed in partnership with the Research and Technology Center of Energy CRTEn (Borj Cedria, Tunisia) and the LESTE laboratory (Monastir, Tunisia). Financial support has been provided by the Tunisian Ministry of Higher Education and Scientific Research (doctoral scholarship). This support is gratefully acknowledged.
Disclosure statement
The authors declare that they have no known competing financial interests or personal relationships that could have appeared to influence the work reported in this paper.
References
- Ali, M., A. Alabdulkarem, A. Nuhait, K. Al-Salem, R. Almuzaiqer, O. Bayaquob, and Z. Algafri. 2021. Thermal analyses of loose agave, wheat straw fibers and agave/wheat straw as new hybrid thermal insulating materials for buildings. Journal of Natural Fibers 18 (12):1–17. doi:10.1080/15440478.2020.1724232.
- ASTM D790 – 10. Standard Test Methods for Flexural Properties of Unreinforced and Reinforced Plastics and Electrical Insulating Materials
- Ben Sghaier, A. E. O., Y. Chaabouni, S. Msahli, and F. Sakli. 2012. Morphological and crystalline characterization of NaOH and NaOcl treated agave americana L. fiber. Industrial Crops and Products 36 (1):257–66. doi:10.1016/j.indcrop.2011.09.012.
- Bessadok, A., S. Marais, S. Roudesli, C. Lixon, and M. Métayer. 2008. Influence of chemical modifications on water-sorption and mechanical properties of agave fibres. Composites Part A, Applied Science and Manufacturing 39 (1):29–45. doi:10.1016/j.compositesa.2007.09.007.
- Bezazi, A., A. Belaadi, M. Bourchak, F. Scarpa, and K. Boba. 2014. Novel extraction techniques, chemical and mechanical characterisation of agave americana L. natural fibres. Composites Part B: Engineering 66:194–203. doi:10.1016/j.compositesb.2014.05.014.
- Chang, B. P., H. M. Akil, M. G. Affendy, A. Khan, and R. B. M. Nasir. 2014. Comparative study of wear performance of particulate and fiber-reinforced nano-ZnO/ultra-high molecular weight polyethylene hybrid composites using response surface methodology. Materials & Design 63:805–19. doi:10.1016/j.matdes.2014.06.031.
- Chen, Y. D., W. Q. Chen, B. Huang, and M. J. Huang. 2013. Process optimization of K2C2O4-activated carbon from kenaf core using Box–Behnken design. Chemical Engineering Research & Design 91 (9):1783–89. doi:10.1016/j.cherd.2013.02.024.
- Cisneros‐López, E. O., J. Anzaldo, F. J. Fuentes‐talavera, R. González‐núñez, J. R. Robledo‐ortíz, and D. Rodrigue. 2017. Effect of agave fiber surface treatment on the properties of polyethylene composites produced by dry‐blending and compression molding. Polymer Composites 38 (1):96–104. doi:10.1002/pc.23564.
- Corral, F. S., L. A. C. Nava, E. H. Hernández, J. F. H. Gámez, M. G. N. Velázquez, and M. I. M. Sierra, … R. E. D. D. L. Gómez, R. E. D. D. L. Gómez. 2016. Plasma treatment of agave fiber powder and its effect on the mechanical and thermal properties of composites based on polyethylene. International Journal of Polymer Science 2016:1–7. doi:10.1155/2016/2807915.
- El Oudiani, A., Y. Chaabouni, S. Msahli, and F. Sakli. 2011. Crystal transition from cellulose I to cellulose II in NaOH treated Agave americana L. fibre. Carbohydrate Polymers 86 (3):1221–1229. doi:10.1016/j.carbpol.2011.06.037.
- Gheith, R., F. Aloui, and S. Ben Nasrallah. 2012. Optimization of a stirling engine performances: A study based on experiments design approach. Vol. 1. Symposia, Parts A and B. doi:10.1115/fedsm2012-72239.
- Gheith, R., F. Aloui, and S. Ben Nasrallah. 2013. Optimization of stirling engine performance based on an experimental design approach. International Journal of Energy Research 37 (12):1519–28. doi:10.1002/er.2964.
- Gu, H. 2009. Tensile behaviours of the coir fibre and related composites after NaOH treatment. Materials & Design 30 (9):3931–34. doi:10.1016/j.matdes.2009.01.035.
- Huerta-Cardoso, O., I. Durazo-Cardenas, V. Merchante-Rodriguez, P. Longhurst, F. Coulon, and A. Encinas-Oropesa. 2020. Up-cycling of agave tequilana bagasse-fibres: A study on the effect of fibre-surface treatments on interfacial bonding and mechanical properties. Results in Materials 8:100158. doi:10.1016/j.rinma.2020.100158.
- Jacob.M., S. T., and K. T. Varughese. 2004. Mechanical properties of sisal/oil palm hybrid fiber reinforced natural rubber composites.Composites Science and Technology. 64:7–87–8. doi:10.1016/S0266-3538(03)00261-6.
- Jain, D., I. Kamboj, T. K. Bera, A. S. Kang, and R. K. Singla. 2019. Experimental and numerical investigations on the effect of alkaline hornification on the hydrothermal ageing of agave natural fiber composites. International Journal of Heat and Mass Transfer 130:431–39. doi:10.1016/j.ijheatmasstransfer.2018.10.106.
- Jani, S. P., S. Sajith, C. Rajaganapathy, and M. Adam Khan. 2020. Mechanical and thermal insulation properties of surface-modified agave Americana/carbon fibre hybrid reinforced epoxy composites. Materials Today: Proceedings 37:1648–53. doi:10.1016/j.matpr.2020.07.180.
- Kandar, M. I. M., and H. M. Akil. 2016. Application of design of experiment (DoE) for parameters optimization in compression moulding for flax reinforced biocomposites. Procedia Chemistry 19:433–40. doi:10.1016/j.proche.2016.03.035.
- Kiran, G. B., K. N. S. Suman, N. M. Rao, and R. U. M. Rao. 2011. A study on the influence of hot press forming process parameters on mechanical properties of green composites using Taguchi experimental design. International Journal of Engineering Science Technology 3 (4):253–63. doi:10.4314/ijest.v3i4.68557.
- Kumara, S., L. Prasad, V. K. Patel, V. Kumar Patel, A. Kumar, and A. Yadav. 2021. Physico-mechanical and Taguchi-designed sliding wear properties of Himalayan agave fiber reinforced polyester composite. Journal of Natural Fibers. doi:10.1080/15440478.2021.1982818.
- Kumar, S., L. Prasad, S. Kumar, and V. K. Patel. 2020. Materials Research Express 6: 12. doi: 10.1088/2053-1591/ab6387.
- Kumar, S., L. Prasad, S. Kumar, and V. K. Patel. 2020. Physicomechanical and Taguchi optimized abrasive wear behaviour of KOH/KMnO4/NaHCO3 treated Himalayan Agave fiber reinforced polyester composite. Materials Research Express 6 (12):125353. doi:10.1088/2053-1591/ab6387.
- Kumar, S., R. K. Verma, A. Kumar, and V. K. Patel. 2022. Importance of chemically treated natural fibers in the fabrication of natural fiber reinforced polymer composites. Trends in Fabrication of Polymers and Polymer Composites 10–11. doi:10.1063/9780735423916_010.
- Langhorst, A., W. Paxton, S. Bollin, D. Frantz, J. Burkholder, A. Kiziltasand, and D. Mielewski. 2019. Heat-treated blue agave fiber composites. Composites Part B: Engineering 165:712–24. doi:10.1016/j.compositesb.2019.02.035.
- Langhorst, A., M. Ravandi, D. Mielewski, and M. Banu. 2021. Technical agave fiber tensile performance: The effects of fiber heat-treatment. Industrial Crops and Products 171:113832. doi:10.1016/j.indcrop.2021.113832.
- Madhu, P., M. R. Sanjay, M. Jawaid, S. Siengchin, A. Khan, and C. I. Pruncu. 2020. A new study on effect of various chemical treatments on Agave Americana fiber for composite reinforcement: Physico-chemical, thermal, mechanical and morphological properties. Polymer Testing 85:106437. doi:10.1016/j.polymertesting.2020.
- Mancino, A., G. Marannano, and B. Zuccarello. 2018. Implementation of eco-sustainable bio-composite materials reinforced by optimized agave fibers. Procedia Structural Integrity 8:526–38. doi:10.1016/j.prostr.2017.12.052.
- Mehrez, I., H. Hachem, R. Gheith, and A. Jemni. 2022a. Valorization of Posidonia-Oceanica leaves for the building insulation sector. Journal of Composite Materials 56 (13):00219983221087793. doi:10.1177/00219983221087793.
- Mehrez, I., H. Hachem, and A. Jemni. 2022b. Thermal insulation potential of wood-cereal straws/plaster composite. Case Studies in Construction Materials 17:e01353. doi:10.1016/j.cscm.2022.e01353.
- Mehrez, I., H. Hachem, R. Gheith, and A. Jemni. 2022c. Effect of the incorporation of NaOH-treated wood aggregates on thermal and mechanical properties of plaster mortar. European Journal of Wood and Wood Products 1–10. doi:10.1007/s00107-022-01877-5.
- Mishra, S., A. K. Mohanty, L. T. Drzal, M. Misra, S. Parija, S. K. Nayak, and S. S. Tipathy. 2003. Studies on mechanical performance of biofibre/glass reinforced polyester hybrid composites”. Composites Science and Technology 63 (10):1377–85. doi:10.1016/S0266-3538(03)00084-8.
- Ramesh, M., C. Deepa, L. R. Kumar, M. R. Sanjay, and S. Siengchin. 2020. Life-cycle and environmental impact assessments on processing of plant fibres and its bio-composites: A critical review. Journal of Industrial Textiles 51:5518S–42S. doi:10.1177/1528083720924730.
- Ramesh, M., K. Palanikumar, and K. H. Reddy. 2017. Plant fibre based bio-composites: Sustainable and renewable green materials. Renewable and Sustainable Energy Reviews 79:558–84. doi:10.1016/j.rser.2017.05.094.
- Ramesh, M., L. Rajeshkumar, and V. Bhuvaneswari. 2021. Leaf fibres as reinforcements in green composites: A review on processing, properties and applications. Emergent Materials 5 (3):1–25. doi:10.1007/s42247-021-00310-6.
- Rojas Clemente, S. M. 2021. Optimization of the alkaline treatment for Agave americana fiber and its influence on the mechanical properties of fly ash-based geopolymer. http://hdl.handle.net/20.500.12404/20157
- Sakuri, S., E. Surojob, D. Ariawanb, and A. Rio Prabowo. 2020. Investigation of Agave cantala-based composite fibers as prosthetic socket materials accounting for a variety of alkali and microcrystalline cellulose treatments. Theoretical and Applied Mechanics Letters 10 (6):405–11. doi:10.1016/j.taml.2020.01.052.
- Santana, H. A., N. S. Amorim Júnior, D. V. Ribeiro, M. S. Cilla, and C. M. R. Dias. 2021. Vegetable fibers behavior in geo-polymers and alkali-activated cement based matrices: A review. Journal of Building Engineering 44:103291. doi:10.1016/j.jobe.2021.103291.
- Sathiamurthi, P., K. S. KarthiVinith, T. P. Sathishkumar, S. Arunkumar, and A. S. Anaamalaai. 2021. Fiber extraction and mechanical properties of Agave Americana/Kenaf fiber reinforced hybrid epoxy composite. Materials Today: Proceedings 46 (17):8594–601. doi:10.1016/j.matpr.2021.03.571.
- Shah, S. P., and C. Ouyang. 1991. Mechanical behavior of fiber-reinforced cement-based composites. Journal of the American Ceramic Society 74 (11):2727–953. doi:10.1111/j.1151-2916.1991.tb06836.x.
- Tharazi, I., A. Sulong, N. Muhamad, C. Haron, D. Tholibon, N. Ismail, M. K. F. Radzi, and Z. Razak. 2017. Optimization of Hot Press Parameters on Tensile Strength for Unidirectional Long Kenaf Fiber Reinforced Polylactic-Acid Composite. Procedia Engineering 184:478–485.
- Torres-Tello, E. V., J. R. Robledo-Ortíz, Y. González-García, A. A. Pérez-Fonseca, C. F. Jasso-Gastinel, and E. Mendizábal. 2017. Effect of agave fiber content in the thermal and mechanical properties of green composites based on polyhydroxybutyrate or poly(hydroxybutyrate-co-hydroxyvalerate). Industrial Crops and Products 99:117–25. doi:10.1016/j.indcrop.2017.01.035.
- Wang, N., E. Ding, and R. Cheng. 2007. Thermal degradation behaviors of spherical cellulose nanocrystals with sulfate groups. Polymer 48 (12):3486–93. doi:10.1016/j.polymer.2007.03.062.
- Wu, L., K. L. Yick, S. Ng, and J. Yip. 2012. Application of the Box Behnken design to the optimization of process parameters in foam cup molding. Expert Systems with Application 39 (9):8059–65. doi:10.1016/j.eswa.2012.01.137.
- Zhu, W. H., B. C. Tobias, R. S. P. Coutts, and G. Langfors. 1994. Air-cured banana-fiber reinforced cement composites. Cement and Concrete Composites 16 (1):3–8. 1994. doi:10.1016/0958-9465(94)90024-8.