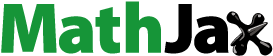
ABSTRACT
The thermal comfort properties of fabrics produced from bamboo, lotus, and their blends were tested to find the ability of the fabric to manage the body heat generated. To assess the thermal comfort properties of the fabrics, the air permeability, water vapor permeability, thermal conductivity, and thermal resistance were evaluated. It is observed from the results that the thickness and mass per square meter of the fabrics reduced as the blend proportion of lotus fiber increased in the yarn. Also, from the results, it could be clearly noted that air permeability, water vapor permeability, and thermal conductivity increased, and the thermal resistance got reduced as the proportion of lotus component increased. Hence, lotus-blended fabrics are more suitable for thermal management summer wear.
摘要
测试了由竹子、莲花及其混合物制成的织物的热舒适性,以发现织物管理身体产生的热量的能力. 为了评估织物的热舒适性,评估了织物的透气性、水蒸气渗透性、导热性和耐热性. 从结果中观察到,织物的厚度和每平方米的质量随着纱线中莲花纤维的混合比例的增加而减小. 此外,从结果中可以清楚地注意到,随着莲花成分的比例增加,空气渗透性、水蒸气渗透性和导热性增加,热阻降低. 因此,莲花混纺织物更适合夏季穿着.
Introduction
Many factors influence clothing comfort, including raw material type, fabric, finish, construction, garment fit, and so on. The combined effect of all these factors will determine the level of comfort felt. The comfort feel is again a combination of parameters such as sensorial comfort, thermal comfort, moisture comfort, fit comfort, etc. To attain maximum comfort considering many varying parameters such as type of fiber, yarn, fabric, finishes, and so on, the selection of raw material and its blend is the first choice in the process of new product development.
The properties of the resultant garment or fabric would be majorly based on the raw material. In general, textile materials are blended in the fiber stage to achieve the required properties to meet the specific end use, and it is a very common practice of spinning (Gupta and Shiekl Citation1975). The blending of fibers of different properties in different proportions is the most common practice of spinning, which is followed to obtain desired yarn properties.
The blending of two different fibers can be carried out to utilize the beneficiary properties of both fibers like improved performance, without sacrificing comfort and esthetic properties of the end product. These benefits also provide opportunities to produce increased and improved ranges of products to expand the market potential (Pan et al. Citation2000). The factors influencing the resultant properties of blended yarns are primarily dependent on the properties of the individual fibers, and it has been discovered that the blended material exhibits superior properties such as quick moisture absorption, fast drying properties, a cool feel to the wearer, a comfortable and soft texture, and protection against microbes and the outside environment. These types are generally used for all kinds of applications, such as clothing, sports textiles, geo textiles, medical textiles, agro textiles, automotive textiles, and so on.
The clothing designed and developed is aimed at providing good comfort to the wearer by way of managing the generated heat and moisture through the fabric material (Özdemir Citation2017a, Citation2017b). The properties of bamboo and lotus are similar in many features. Bamboo products have soft and cool-feeling antibacterial properties, moisture absorption characteristics, UV productive capability, and biodegradability. Lotus fiber is extracted from lotus peduncles, after removing flowers, which does not generate toxic waste, biodegradable, and sustainable (Aishwariya and Thamima Citation2019; Pan et al. Citation2011; Zhang and Guo Citation2014). Lotus fibers come as bundles during extraction, and each microfiber has an essential crimp for textile applications; this crimp provides elastic property, softness, and other required textile properties (Cheng et al. Citation2018; Karthik, Rathinamoorthy, and Ganesan Citation2015; Pandey, Sinha, and Dubey Citation2020). The lotus fibers are longer, finer, and light in weight and have cohesiveness, uniformity, lustrousness, greater tenacity, elongation, and wrinkle free. As the lotus fiber possesses these characteristics, it can be a choice for developing clothing with comfort and a luxurious feel (Zhang and Li Citation2011).
In this research work, bamboo- and lotus-blended yarns were produced in five different blend proportions. To utilize the properties of both fibers and to confirm the suitability to attain thermal comfort, knitted fabric with a honeycomb structure was produced with the blended yarn samples, and a study has been conducted to analyze the thermal comfort properties of lotus fiber blended with bamboo fiber.
Materials and methods
Materials
In this study, basic raw materials, bamboo and lotus fibers were purchased from a local supplier, and the fiber parameters are given in .
Table 1. Technical details of fibers.
The 30s Ne of 100% bamboo, 67% bamboo-33% lotus, 50% bamboo-50% lotus, 33% bamboo-67% lotus, and 100% lotus yarns were used for producing the samples. The technical details of the yarn procured are given in .
Table 2. Technical details of yarns.
Honey comb-knitted fabrics produced from five different yarn samples, namely the two types of fibers and their three blend proportions, were used to assess the thermal comfort properties of bamboo- and lotus-blended fabrics. The knitted fabrics were produced using Mayer and Cie knitting machines, available locally. Its diameter is 24 inch; gauge is 24 inch, and it has 72 feeders for assessing the thermal comfort properties of the fabrics. The fabric samples manufactured were allowed to relax for 24 h in standard atmospheric conditions and were used for this investigation.
Methods
The fabric samples were relaxed, conditioned, and prepared for investigation were taken to test their physical properties. The thickness of the fabric was tested by following the standard testing procedure prescribed by the ASTM D 1777, and similarly, the areal density was measured as per the ASTM D 3776, wales and courses per unit length as per the ASTM D 3887: 1996 (RA 2008) and loop length as per the ASTM D 3887. The technical details of the fabric produced are given in .
Table 3. Technical details of fabrics.
Measurement of air permeability
Air permeability is a very familiar test, which measures the potential passage of air through the fabric, and it directly indicates the breathability of fabric. The evaluation of air permeability is an important parameter to be considered in the decision of thermal comfort since it deals with the flow of vapor from the skin to the outer environment and vice versa. The air permeability of the samples was measured by following the ASTM D737 standard procedure using a Textest F× 3300 air permeability tester.
Measurement of relative water permeability
The ability of a fabric to transport water vapor from the skin to the outside environment is known as relative water vapor permeability. If the fabric resists transferring water vapor, it directly influences the thermal comfort of the fabric. The permeability of water vapor was measured on a Textest F× 3300 air permeability tester. The instrument operates on the basis of heat flux sensing. The temperature of the head is maintained at room temperature, and the head loss through the head is a measure of air permeability when the evaporation of moisture takes place in a dry environment. The curve and porous measuring head are wet and show airflow of 1.5 to 3.0 m/s. The sample to be tested is positioned at a distance of 1 to 1.5 cm and assessed by its thermal conductivity for 2 min. This instrument measures the relative water vapor permeability of the fabric using a sensor positioned at the measuring head. The heat provided to sustain even temperature was measured by placing the sample on the head and measuring the heat provided to sustain even temperature. The relative water vapor permeability is calculated using the formula given below:
Measurement of thermal properties
The properties, particularly thermal conduction and thermal resistance, are the two indices used to measure the thermal comfort properties of the clothing. Thermal conductivity is one of the essential properties of a clothing material that has the capability to conduct heat. This property is very essential in the case of designing sports or active wear. This thermal conductivity directly affects the comfort of the clothing and plays a vital factor in deciding the suitability of the clothing. Thermal conductivity is a property of materials that shows the heat flux that will flow through the fabric samples when a constant heat gradient flows through the material.
Thermal resistance is the ability to prevent the passage of heat through the fabric. Thermal resistance is greatly influenced by its fabric structure, thickness, and mass per square meter. The air layer inside the garment with resisted heat acts as an insulator and tends to maintain the body heat inside the clothing and make the wearer warmer.
The thermal comfort properties, particularly thermal conduction and thermal resistance, of the samples were evaluated by utilizing the Alambeta instrument. This instrument measures the heat flow by following the test procedure as per ISO 11,092 by placing the samples between a hot plate, which resembles human skin, and a cold plate as the outer environment. By using the sensor, which is capable of sensing the heat flux, it measures the heat flow in a time span of 30–50 s.
Thermal resistance is a sign of the effectiveness of the insulation properties of the fabric samples. It can be calculated using the formula given below;
R = h/λ (m2K/W)
where, R = Thermal resistance,
h = fabric thickness (m) and λ = thermal conductivity (W/mK).
Results and discussion
The study discussed in this article has been carried out to confirm the suitability of lotus fiber and its blends with bamboo fiber in the fabrics for achieving thermal comfort. Lotus fibers are very soft, very lightweight, highly breathable, and capable of absorbing moisture effectively (Chen, Gan, and Yuan Citation2012). Also, many researchers have been carried out by many researchers and manufacturers to assess the thermal comfort of the bamboo fiber and confirm that bamboo fiber has better dyeability, high elasticity, excellent air permeability, and good moisture absorption. To utilize the benefits of both the fibers, a systematic analysis has been carried out to confirm the suitability of lotus fiber and its blends with bamboo fiber for providing thermal comfort.
Honeycomb-knitted fabrics are produced from five different yarn samples as mentioned in . Honeycomb fabrics are thicker, heavier, and stronger than the other two structures of the fabrics produced and have decided to take this for understanding the influence of blend ratio of lotus/bamboo-blended knitted fabrics.
Influence of blend proportion on air permeability
The results of air permeability tests of honeycomb-knitted fabric samples are presented in . From the total observation, it is noted that the air permeability increases as the proportion of lotus fiber in the fabric increases.
The results show that the 100% lotus fabric has the highest values in air permeability tests. It is further supported by the findings about the thickness of the manufactured fabrics. The thickness of the lotus-blended fabric reduces as the amount of lotus fiber in the fabric rises.
When comparing between the 100% bamboo- and 100% lotus-knitted fabrics, the air permeable character of the 100% lotus-knitted fabrics is almost double the time of 100% bamboo-knitted fabric. This indicates the positive sign of the suitability of lotus fibers in achieving thermal comfort.
Influence of blend proportion on relative water vapor permeability
represents the relative water vapor permeability of the honeycomb-knitted fabric samples produced. The results show that as the proportion of lotus fibers increases, the relative water vapor permeability increases.
The trend of relative water vapor permeability is similar to the air permeability of the samples evaluated. The higher water vapor permeability of lotus-blended fabrics is the result of the low thickness and fabric mass per square meter. This creates a fabric structure that allows the passage of vapor easily through the fabric (Bivainytė and Mikučionienė Citation2011). The result of 100% lotus fabric, which is comparatively tight-structured honeycomb fabric, has shown maximum water vapor permeability, which is evidence for the suitability of lotus fiber in achieving thermal comfort (Chen, Gan, and Yuan Citation2012; Ozdemir 2017).
Influence of blend proportion on thermal conductivity
illustrates the trend in the thermal conductivity of knitted fabrics, which decreases as the percentage of lotus fiber increases. When comparing the results of air and vapor permeability of the samples evaluated, it demonstrates the opposite tendency.
The thermal conductivity of the fabric increases as the lotus fiber content increases. It is observed that fabric thickness plays a main role in thermal conduction and thermal insulation (Prakash, Ramakrishnan, and Koushik Citation2013). It influences the circulation of air across the fabric, which facilitates the carrying of heat generated and stored and ultimately leads to keeping the body cool and results in thermal comfort (Shoshani and Shaltiel Citation1989; Ozdemir Citation2017a).
Influence of blend proportion on thermal resistance
Thermal resistance is the capability of fabric, which prevents or resists the passage of heat through it (Majumdar, Mukhopadhyay, and Yadav Citation2010). Thermal resistance is one of the vital characteristics of the fabric, which is intended for clothing purposes and is greatly influenced by its fabric thickness, mass per square meter, and structure. This directly acts as an insulator and tends to maintain the body heat inside the clothing and make the wearer warmer.
Generally, thermal conductivity is inversely proportional to the thermal resistance, and the results obtained for the samples produced are in line with the concept. From , it is clearly seen that the thermal resistance reduces with the increase in lotus fiber content, which is the result of high fabric thickness and mass per square meter (Chidambaram, Govindan, and Venkatraman Citation2012).
Conclusions
The thermal comfort properties of honeycomb fabrics produced from 100% bamboo-, 67:33 bamboo/lotus-, 50:50 bamboo/lotus-, 33:67 bamboo/lotus-, and 100% lotus-blended yarns were investigated. The air permeability, thermal resistance, relative water vapor permeability, and thermal conductivity were assessed to evaluate the thermal comfort properties of the fabrics. From the results obtained, it is clearly observed that as the content of the lotus fiber increases, air permeability, water vapor permeability, and thermal conductivity increase, while thermal resistance reduces. The fabric with higher lotus content improves thermal comfort properties. The thickness and mass per square meter reduced as the proportion of lotus fiber increased in the yarn.
Highlights
To assess the thermal comfort properties of the fabrics
Fabrics produced from bamboo, lotus, and their blends were tested to find the ability of the fabric to manage the body heat generated
Thickness and mass per square meter of the fabrics reduced as the blend proportion of lotus fiber increased in the yarn.
Lotus-blended fabrics are more suitable for thermal management summer wear.
Ethical approval
We confirm that all the research meets ethical guidelines and adheres to the legal requirements of the study country. The research does not involve any human or animal welfare-related issues.
Disclosure statement
No potential conflict of interest was reported by the author(s).
References
- Aishwariya, S., and S. Thamima. 2019. Sustainable textiles from lotus. Asian Textile 28 (10):56–8.
- Bivainytė, A., and D. Mikučionienė. 2011. Investigation on the Air and Water Vapour Permeability of Double-Layered Weft Knitted Fabrics. Fibres & Textiles in Eastern Europe 19 (3(86)):69–73. doi:10.5755/j01.ms.18.3.2438.
- Chen, D. S., Y. J. Gan, and X. H. Yuan. 2012. Research on Structure and Properties of Lotus Fibers. Advanced Materials Research 476:1948–54. doi:10.4028/scientific.net/AMR.476-478.1948.
- Cheng, C., R. Guo, J. Lan, S. Jiang, Z. Du, L. Zhao, and L. Peng. 2018. Preparation and characterization of lotus fibers from lotus stems. The Journal of the Textile Institute 109 (10):1322–28. doi:10.1080/00405000.2018.1423898.
- Chidambaram, P., R. Govindan, and K. C. Venkatraman. 2012. Study of thermal comfort properties of cotton/regenerated bamboo knitted fabrics. African Journal of Basic & Applied Sciences 4 (2):60–66. doi:10.5829/idosi.ajbas.2012.4.2.1032.
- Gupta, D. K., and A. E. Shiekl. 1975. The Mechanics of Blended Yams. Applied Polymer Symposia 27:295–315.
- Karthik, T., R. Rathinamoorthy, and P. Ganesan. 2015. Sustainable luxury natural fibers—production, properties, and prospects. In Handbook of Sustainable Luxury Textiles and Fashion, ed. M. A. Gardetti and S. S. Muthu, 59–98. Singapore: Springer.
- Majumdar, A., S. Mukhopadhyay, and R. Yadav. 2010. Thermal properties of knitted fabrics made from cotton and regenerated bamboo cellulosic fibres. International Journal of Thermal Sciences 49 (10):2042–48. doi:10.1016/j.ijthermalsci.2010.05.017.
- Özdemir, H. 2017a. Permeability and wicking properties of modal and lyocell woven fabrics used for clothing. Journal of Engineered Fibers and Fabrics 12 (1):12–21. doi:10.1177/155892501701200102.
- Özdemir, H. 2017b. Thermal comfort properties of clothing fabrics woven with polyester/cotton blend yarns. AUTEX Research Journal 17 (2):135–41. doi:10.1515/aut-2016-0012.
- Pan, N., K. Chen, C. J. Monego, and S. Backer. 2000. Studying the mechanical properties of blended fibrous structures using a simple model. Textile Research Journal 70 (6):502–07. doi:10.1177/004051750007000606.
- Pandey, R., M. K. Sinha, and A. Dubey. 2020. Cellulosic fibers from Lotus (Nelumbo nucifera) peduncle. Journal of Natural Fibers 17 (2):298–309. doi:10.1080/15440478.2018.1492486.
- Pan, Y., G. Han, Z. Mao, Y. Zhang, H. Duan, J. Huang, and L. Qu. 2011. Structural characteristics and physical properties of lotus fibers obtained from Nelumbo nucifera petioles. Carbohydrate polymers 85 (1):188–95. doi:10.1016/j.carbpol.2011.02.013.
- Prakash, C., G. Ramakrishnan, and C. V. Koushik. 2013. A study of the thermal properties of bamboo knitted fabrics. Journal of Thermal Analysis and Calorimetry 111 (1):101–05. doi:10.1007/s10973-011-2166-5.
- Shoshani, Y., and S. Shaltiel. 1989. Heat resistance characteristics of weft knit single jersey inlay fabrics. Knitting Times 4 (3):70–72.
- Zhang, Y., and Z. Guo. 2014. Micromechanics of lotus fibers. Chemistry Letters 43 (7):1137–39. doi:10.1246/cl.140345.
- Zhang, H. W., and Y. L. Li. 2011. Lotus fiber production and its property. Advanced Materials Research 146:93–96. doi:10.4028/scientific.net/AMR.146-147.93.