ABSTRACT
The natural, glass, and carbon fiber reinforced polymer composites are currently being replaced conventional materials due to their lower specific weight and superior strength properties. Natural fiber-reinforced polymer composites (NFRPCs) have grown in importance in real world applications recently due to a growing focus on the environmental and sustainability elements of engineering materials. The difficulty of machining FRP composites, which results in dimensional errors, poor product quality, and material damage, is due to their inhomogeneity, ease of deformation, and anisotropic nature. Moreover, this review gives an insight regarding recent developments and challenges that will help for upcoming researchers. The non-homogeneous properties and insufficient ductility of natural and synthetic fiber-reinforced composites have produced fracturing and discontinuous chips during the machining operations. The machinability of FRP composites depends on the constituents present in the composites. More delaminations were found in the natural fiber composites due to improper bonding and less compatibility with the polymer matrices, also the lower heat resistant property of the natural fibers causes serious problems during the machining process. Hence more studies are needed to decrease the thrust force and delamination damages in carbon, glass, and natural fiber reinforced polymer composites.
摘要
天然、玻璃和碳纤维增强聚合物复合材料由于其较低的比重和优异的强度特性,目前正在取代传统材料由于人们越来越关注工程材料的环境和可持续性元素,天然纤维增强聚合物复合材料 (NFRPC) 最近在现实世界的应用中变得越来越重要. FRP 复合材料. 的加工困难,导致尺寸误差、产品质量差和材料损坏,这是由于它们的不均匀性、易于变形和各向异性的性质. 此外,这篇综述提供了有关近期发展和挑战的见解,这将有助于即将到来的研究人员. 天然和合成纤维增强复合材料的不均匀性能和延展性不足在加工操作过程中产生了断裂和不连续的切屑. FRP 复合材料的可加工性取决于复合材料中存在的成分. 由于不适当的粘合和与聚合物基体的相容性较低,在天然纤维复合材料中发现更多的分层,而且天然纤维较低的耐热性能在加工过程中导致严重的问题. 因此,需要更多的研究来降低碳、玻璃和天然纤维增强聚合物复合材料的推力和分层损伤.
Introduction
Polymer composites are a type of versatile and high-performance materials formed with a combination of various material phases, in that at least one of the phases, and normally a matrix is made of polymer. The assembly of all these components gives unique mechanical, conductive, and thermal properties, which are slightly inconvenient to get using a single material. The reinforcement and matrix are the two essential phases of developing polymer composite (Correia, Bai, and Keller Citation2015; Jagadeesh et al. Citation2020; Praveenkumara et al. Citation2021). The fiber-reinforced polymer (FRP) composites have been a center of attraction for research and industries alike and are popular in various sectors like construction, aerospace, sports, automotive, and small-scale industries as a structural material (Alarifi Citation2021; Jagadeesh et al. Citation2021a, Citation2022, Citation2022). The fibers are preferred in various polymer compositions to enhance their overall mechanical properties. Both natural fibers and synthetic fibers are preferred for the purpose, although the natural fiber reinforcement with different polymer matrices have gained much considerable attention as per the recent literature and in practical applications because of sustainability, processing advantages, low cost, and nature-friendly aspects (Jagadeesh et al. Citation2021b; Liu, Tang, and Cong Citation2012; Malik, Ahmad, and Gunister Citation2021). The performance of advanced FRP composites depends on the properties of individual fibers, individual matrix, and the geometry of the fibers, fibers orientation, and fiber to matrix volume ratio. The glass fiber reinforced polymer (GFRP) composites are economically the best alternatives to metals and stainless steel, even in highly corrosive environments (Karataş and Gökkaya Citation2018). The carbon fiber-reinforced polymer (CFRP) composites show excellent properties such as outstanding mechanical properties, good chemical resistance, low density, and high strength characteristics that could be tailor-made for the specified load (Jagadeesh et al. Citation2021, Citation2022; Vinayagamoorthy Citation2018). The natural fiber-reinforced composites show lower mechanical, electrical, and thermal properties than CFRP and GFRP. However, these natural fiber composites possess unique advantages like biodegradability, low cost, ease of availability, nature friendly, and fire-resistant properties. These natural fibers are reinforced with various polymer matrices to increase the material properties, and sometimes additives or filler materials are incorporated for further properties enhancement. The hybridization technique is popular nowadays for both natural and synthetic fibers reinforced polymer composites. Adding two or more reinforcements with a single matrix material causes balanced stiffness, strength, machinability, thermal distortion stability, notch sensitivity and improves fatigue resistance (Jagadeesh et al. Citation2021; Panchagnula and Palaniyandi Citation2018). During the fabrication of polymer composites, it is difficult and complex to get slots or holes in the composites without affecting reinforcements; in such circumstances, machining is preferred to execute complex shapes by fulfilling design requirements. During the machining, the polymer composites exhibit significant variations compared to conventional materials due to their non-homogeneous nature, fiber orientations, and diverse matrix, fiber properties (Jagadeesh et al. Citation2022; Lopresto, Caggiano, and Teti Citation2016). Also, the cutting mechanism of these materials is difficult, hence analysis of machining performance is difficult in the case of polymer composites. Due to the complexity of many of the production procedures used to create composite structures, efforts at modeling or optimization are typically insufficient in both potential and applicability. Many physics-based manufacturing strategies should take into consideration sufficient systems as well as a variety of changeable properties. Controlling manufacturing precision and producing high-quality goods is quite difficult (Priyadharshini et al. Citation2022). The machining of FRP composites causes material surface damage through fiber cracks, interlaminar delamination, fiber breakage, matrix flow, and intralaminar delamination. The typical FRP composites failure modes are illustrated in . The utilization of most conventional machining techniques is not economical for FRP composites. Sometimes the performance and life of FRP composites may be affected by machining conditions or machining parameters (Cepero-Mejías et al. Citation2020; Melentiev et al. Citation2016; Vigneshwaran et al. Citation2021). A good surface finish through FRP composites machining is a serious problem nowadays while subjecting the FRP composites to aesthetic requirements; precision fits, fatigue loads, and fastener hole applications. Overall, the damages that occur during machining are due to factors like the fibers’ nature, fibers orientation, mechanical properties of fibers, machining mode, tool materials, tool geometry, machining parameters, compatibility, and bonding between matrix/fibers. It is the fact that the FRP composites show inhomogeneity, ease of deformation, and anisotropic nature, which makes the process of machining difficult, and it leads to dimensional inaccuracy, poor product quality, material damage and results in a higher scrap rate (Thakur and Singh Citation2021; Wang et al. Citation2021). The material removal phenomenon of FRP composites is different from those of alloys and metals process mechanisms, and the FRP materials machining is found to be less in the literature the metals and alloys machining. Compared to the metals, the long fibers reinforced polymer composites have a maximum layered structure, with unique properties and their thickness. During the drilling of these layered structures, internal defects occur due to drilling loads and these loads’ uneven distributions along with the fiber layers. It was observed that very few review works were found in the literature related to the machinability of FRP composites (Kalla, Sheikh-Ahmad, and Twomey Citation2010; Sheikh-Ahmad, Urban, and Cheraghi Citation2012). Hence, this review comprehensively discusses the basic studies on FRP composites machining, the quality aspects of FRP composites machinability, and collects previous literature on the machinability of natural fiber reinforced hybrid polymer composites and synthetic fiber reinforced polymer composites. Also, this review includes the unconventional machining process utilized in FRP composites machining.
Figure 1. Typical FRP composites failure modes: fiber failures (a), matrix-fiber debonding (b), delamination (c), fiber pull-outs (d), sub-surface damages (e) (Cepero-Mejías et al. Citation2020).
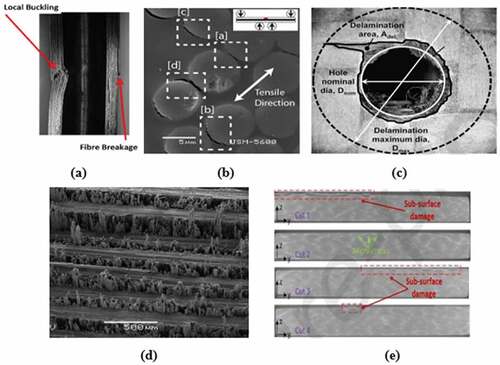
Studies on FRP composites machining
The non-traditional machining processes are capable of solving many problems that exist in FRP composites machining, whereas the conventional processes are highly preferred for the reasons of time and cost. However, more research is needed to optimize the machining process to get adequate machining quality results. The failure stress analysis of carbon/epoxy composite indicates the significant effect of cutting speed on the failure stress. The maximum failure stresses were observed with the lower cutting speeds, which does not correlate with microscopic observations (Thakur and Singh Citation2021). However, surfaces cut at lower rates have rougher surfaces than those cut at high speeds. These surface observations clearly show the roughness measurement alone is not sufficient to analyze the machining damages, and inside propagated damages cause a reduction in mechanical performance (Poór et al. Citation2021; Thakur and Singh Citation2021). The key factor fiber orientation decides the structural integrity of machined epoxy/carbon composites, and subsurface damage will not occur beyond the critical angle of 90°. Usually, the FRP composites offer a bouncing back phenomenon after the machining process, which is attributed to the elastic bending nature of reinforcement fibers. When the orientation of the fibers exists with ≤90° the three deformation zones occur, namely chipping, pressing, and bouncing. If the angle is >90°, more significant fiber bending is observed during cutting. Hence this involves a complicated cutting mechanism. The curing conditions while fabricating FRP composites in the transverse direction significantly affect the mechanical properties, influencing the changing cutting forces in smaller amounts (Kalla, Sheikh-Ahmad, and Twomey Citation2010; Kangokar Mukesh et al. Citation2022; Wang et al. Citation2021). The machinability evaluation phenomenon with cemented carbide tool reveals the better machinability of PEEK material with 30% carbon fiber reinforced composites and unreinforced PEEK than the 30% glass fiber reinforced PEEK composites. The overall evaluation factors indicate the higher machinability of unreinforced PEEK material than the reinforcement with glass and carbon fibers (Davim et al. Citation2010). The alkaline treated sisal/roselle/polyester composites show better machinability against abrasive wheels than the untreated composites. This was due to forming a strong interfacial bond with higher strength among matrix and reinforcements with the removal of moisture from the lignocellulose fibers. The 5 wt% fiber-reinforced composites with 2 hours of chemical treatment re-bounces in smaller amounts during machining. After the machining process, the 30 wt% fiber contents with 8 hours of treatment show more dimensional accuracy than other combinations (Navaneethakrishnan and Athijayamani Citation2016). Khashaba et al. (Citation2010) analyzed the influence of drill wear on the machinability of glass fiber/epoxy composites. The machinability parameters were characterized using toque, thrust force, fiber push-outs, peel-ups, and roughness of the drilled hole. The results reveal that the thrust force behavior during drilling was highly affected by the pre-wear drill. This effect was more at a higher feed and cutting speed, which causes an increment in roughness and fibers delamination. The influence of drill wear on thrust force with different feeds and speeds is shown in . The thrust force was elevated with higher drill pre-wear and feed; even with the smaller increment in drill pre-wear causes more amount of thrust force which is shown in the graph. When utilizing a pre-wear drill for GFRP composites, the effect is greatest. The thrust force was unaffected by cutting speed when using a new drill. The 30 wt% of glass fibers reinforcement with polyamide (PA66) significantly affected the tooling performance as compared to without reinforcement of materials. Using polycrystalline diamond (PCD) tool for the turning of glass/PA66 and neat PA66 gives the lowest forces and slightly higher force values by K15 carbide tools. During the cutting of PA66 material, the K15-KF carbide tool promotes higher forces, and diamond coated tool exhibits maximum forces while machining glass/PA66 composite. The specific cutting forces were decreased with increasing feed rate (Paulo Davim et al. Citation2009). The experimental machinability analysis of short glass/nylon-6 composite shows that the drill bit tool wear increases with increasing the glass fibers percentage. It is shown that the nylon-6/glass composite offers higher resistance to the drill bit movement with increasing the high modulus glass fibers in the soft nylon-6 matrix. This resistance to drilling bit movement causes tool wear, resulting in the machined composite’s dimensional inaccuracy. The observations made from total rig down count (TRDC) against time show the lowest level of cutting forces for 15% glass fiber reinforced nylon-6 composite as compared to the other combinations with 30%, 40%, and 50% glass fibers reinforcement (Jawali et al. Citation2006). The fiber’s contents volume and primary processing were the major contributing parameters that influenced the cutting forces while machining randomly oriented glass fiber reinforced polymer composites. The cutting forces were increased with increasing fiber contents and the depth of the cut. During the composite cutting, an enormous amount of energy was found at higher frequency regions due to burst kinds of cutting force signals due to fiber pull-outs and matrix damage. The stable flank wear was found after hardly one or two minutes of a short GFRP composite cutting process (Kim et al. Citation2010). ()
Figure 2. Drill pre-wear effect on thrust force at: (a) different feeds, (b) different speeds (Khashaba et al. Citation2010).
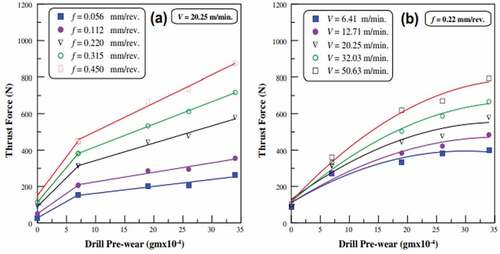
Table 1. Studies on machinability of fiber-reinforced composites.
Factors affecting machinability/quality aspects
The FRP composites are currently promising materials for developing structural elements in various industries. Even though the FRP composite parts are being fabricated with near-net shape, machining operations such as drilling and trimming are still required to achieve finalized part sizes and fit tolerances. The machining of FRP composite is significantly more varied than that of the traditional metal and alloys machining. The cutting mechanism of most of the homogeneous materials was characterized by bulk materials plastic deformation with the continuous chips, whereas FRP composites cutting mechanism was characterized by non-homogeneity and anisotropic nature (Gao et al. Citation2016; Wang and Melly Citation2018; Wang et al. Citation2021). This anisotropy and inhomogeneity affect the machining process of FRP composites through fibers delamination, pull-outs/peel-ups, and machining parameters. The integrity offered by the machined surface is a basic aspect while determining an FRP composites machinability. Usually, this structural integrity was affected by machined surfaces due to the presence of internal defects in the FRP composites. Therefore, many extensive research works have been done to analyze factors responsible for the machining process and to study the quality aspects of machining (Shahabaz et al. Citation2021; Thakur and Singh Citation2021; Zhu et al. Citation2022). The stiffness and strength of the polymer composites were reduced due to the effect of delamination, which further led to materials failure. The turning, drilling, milling, and other machining operations are more critical due to the delamination factor in polymer composites. This delamination occurs through removal or separation of composite plies, and it is attributed to interlaminar cracks development in the materials. This delamination causes an improper machining process through dimensional inaccuracies, material wastage, and difficulty getting a good surface finish. The damage occurrence during machining depended on cutting parameters and drilling geometry. The geometry of the fresh tools will change along with cutting time because of wear progression, which affects the quality and process of machining (Helmi Abdul Kudus, Ratnam, and Akil Citation2021; Vigneshwaran et al. Citation2021).
Properties and machining of fiber-reinforced composites using conventional techniques
Usually, the failure behavior polymer composite occurs not only with anisotropic and heterogeneous structure but also due to the tool’s interactions with the materials and machining methods. This heterogeneous structure of polymer composites causes health-related and structural issues such as matrix smearing, delamination, tool life reduction, fiber pull-out, and formation of unhealthy dust during machining (Hwang et al. Citation2015; Saoudi et al. Citation2018). The conventional tools have higher hardness and abrasiveness, leading to fiber crushing during machining. Sometimes the machining of complex polymer composite causes the tool’s plastic deformation. In the aerospace industry, the components rejection rate was raised to 60% due to delamination failures, and it was reported in the literature. Moreover, the machining at narrow workspace was difficult with conventional tools because of tools spindle size and machining time increment with tool changing duration for worn-out drilling and milling tools (Altin Karataş and Gökkaya Citation2018; Katnam, Da Silva, and Young Citation2013).
Synthetic fiber reinforced polymer composites
The surface integrity and finishing-related problems are generally encountered while CFRP composites machining using conventional machining tools (Geier et al. Citation2021). Due to lower machinability, the CFRP composites machining exhibits various failures, including burrs, sub-surface failure, and delamination (Xu et al. Citation2022). The lower feed rate reduces the axial forces, which reduces risk that occurs from delamination initiation, which proves better machinability while drilling CFRP composite layers. The influence of tool geometry on the delamination results was also reported, and accordingly, the minimum delamination was obtained for twist drill with a point angle of 120° (Geier, Davim, and Szalay Citation2019; Shunmugesh and Panneerselvam Citation2016). The GFRP composites are extensively popular in various industries because of their higher mechanical properties, less weight, and low cost as compared to other synthetic materials. Even with good control over the composites manufacturing process and capable of producing near net shapes, many machining operations are required to complete the manufacturing process. The employment of various machining operations is difficult in the case of GFRP composites due to anisotropic and heterogeneous character (Saoudi et al. Citation2018; Thakur and Singh Citation2021). A finite element model was developed by Calzada et al. to analyze failure mechanism in the machining of CFRP composite, and the failure mechanism was analyzed throughout the formation of the chipping process. This model was able to predict failure mode, machining forces, and characteristics of chipped fibers with the microstructure of fibers orientation. To validate this model, an orthogonal machining experiment was conducted to record the machining response. This comparison reveals the model’s accuracy in determining failure mode with fiber characteristics and the machining forces. This model was demonstrated the failure mode of 135° fibers oriented CFRP composite, where the failure mode was changed to crushing from the bending mode. This failure mode simulation is illustrated in . When the tool enters the workpiece, it peels the fibers where the matrix-fiber adhesion is less due to interfacial failures under the cutting planes. After peeling, the bending stresses were developed below the cuts, affecting the rest of the workpiece (Calzada et al. Citation2012). The addition of boron nitride (BN) nanoparticles into carbon/epoxy composite improves the drilling performance and properties of the resultant nanocomposite. The addition of BN particles increases the thrust force and reduces the delamination factor of the nanocomposite. The hole surface finish was good in BN reinforced composite due to improved bending and shear strength between the composite layers. The optimum parameters for these nanocomposites are 90 m/min of cutting speed and 0.005 mm/rev of feed rate (Burak Kaybal et al. Citation2020).
Figure 3. Simulation results of 135° fiber oriented CFRP composite, (a) 135° failure nodes, (b) 15 µ m DOC and (c) 30 µ m DOC (Calzada et al. Citation2012).
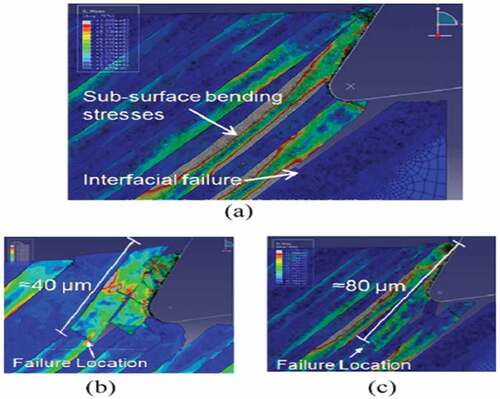
The thrust force on unidirectional CFRP composite was significantly varied with drill rotational positions, and the lower thrust force values were observed at 135° and 315° rotational angles. The rough surface was observed along the drilled hole and throughout the depth. The fiber pull-outs were observed majorly in two regions where the interaction angle between fiber orientation and cutting angle was from 135° − 175° and 315° − 355°. The quality of the whole surface was better at a low feed rate and high cutting speed (Eneyew and Ramulu Citation2014). The 3D printed CFRP composite shows maximum tool wear at a low feed rate of 23.64 IPM when subjected to the end milling process. The low feed rate machining allows the workpiece to adhere to the tool, and it causes the tool to material upset instead of shear it. To improve the machining performance and to reduce the burr formation, it was suggested to adopt the minimum quantity lubrication technique (MQL). Under the MQL conditions, both tool wear and surface finish were improved. The utilization of post-process machining gives maximum surface finish quality and could be used in end applications (Cococcetta et al. Citation2020). The decrement in the latter force was the most effective thing while reducing the increment rate of cutting forces owing to tool wear progress during the CFRP composite down-milling process. This consideration is possible through the usage of a two-layer cutting tool, where it reduces the pressing forces and distributes the wear rate at the tool edge, which leads to overall cutting force decrement (Maegawa et al. Citation2016). The machining of CFRP composites causes flank wear on the carbide tool due to carbon fiber’s abrasive and hard structures. The more hardness of fiber causes an increment in cutting forces and results in the wear of uncoated tools during machining. To get the required wear resistance in carbide tools, the diamond coating was done on the carbide tool surface for sufficient wear resistance. By considering the tool life, the carbide tools are in the first position for machining of CFRP composites, especially with fine grain size carbide grades. For getting the higher cutting performance, the polycrystalline diamond tools are preferred or milling of CFRP composites (Ozkan et al. Citation2019). A different machining approach was done on the CFRP composites under cryogenic conditions. The CFRP composites were subjected to cold temperature while machining for 30 minutes. The cryogenic heat treatment positively affects the CFRPs tensile properties, which is about 3.04% and 3.65%, respectively, for elastic modulus and tensile strength. Hence, the cryogenic approach’s cutting forces were higher than other machining approaches. Although, the formation of higher forces under cryogenic machining has lower delaminations. This was owing to chip breakability improvement and the formation of low forces in the axial direction because of cryogenic coolant. These coolants make the workpiece brittle and avoid thermal damages on machined surfaces (Morkavuk et al. Citation2018). The comparison of delamination factors for CFRP composite under dry, cryogenic, and MQL conditions reveals that the cryogenic drilling has maximum delamination at the hole entry and exit sides. The comparison of delamination factors under these three conditions at the entry and exit sides of the hole is illustrated in . In comparison to dry drilling, the cryogenic drilling exhibit below 10% delamination at the hole entrance. In the case of the MQL condition, the delamination was 2% higher than the measured values at dry conditions at the hole entrance. When the delamination at the exit side was concerned, the delamination magnitude was found to be 16% higher in cryogenic conditions than the dry drilling due to a higher magnitude of forces (Nagaraj, Uysal, and Jawahir Citation2020).
Figure 4. The delamination factor compares the drilled hole at entry and exit under dry, cryogenic, and MQL conditions (Nagaraj, Uysal, and Jawahir Citation2020).
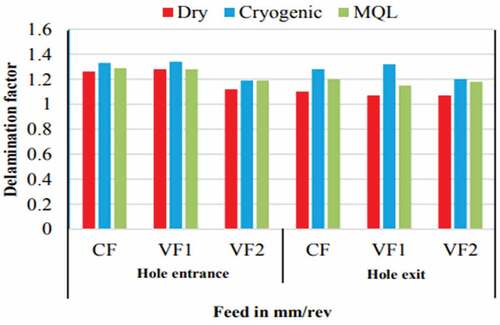
During the machining of flax fiber-reinforced polymer composites, the flax fiber orientations significantly affect the machined surface state. The fiber orientation with an angle of 45° gives the best machinability with low surface roughness, effective fibers shearing, and lower cutting energies due to friction and shearing. This could be related to the higher shear stiffness involved in 45° fiber-oriented samples. The 90°-fiber orientation shows maximum cutting energies due to flax fibers transverse deformation during machining. Whereas the 0° fibers-oriented composite has maximum surface roughness because of random contact position among flax fibers and cutting tool edge within the composite (Chegdani et al. Citation2020). Irrespective of radial and axial force during the helical milling of CFRP composites, the cutting forces increased with the depth of cut and feed rate. The radial forces were high at higher rotational speeds. The tool wear was obvious during helical milling of CFRP composite due to higher cutting forces; additionally, the cutting forces are higher in multidirectional CFRP milling than unidirectional CFRP milling. The entry delamination is less while using the sharp cutting tool, and the delamination was enlarged with reduction of tool sharpness (Wang, Qin, and Li Citation2015). With the increase of MWCNTs loading in CFRP composite, both torque and thrust forces were decreased due to stiffness improvement in MWCNTs loaded CFRP nanocomposite. The surface roughness value of the hole was increased due to more severe damages with higher feed rates. However, the roughness decreased with increasing spindle speed due to matrix softening at high temperatures generated between chip-tool interfaces. Moreover, the addition of MWCNTs into the polymer matrix reduces surface roughness due to the lubrication behavior of MWCNTs at the chip-tool interface, also minimizes fibers debonding and matrix pull-out (Kumar and Singh Citation2019). The depth of cut was the most significant influencing factor on the CFRP laminate machinability. The low-level cutting temperature, cutting force, surface roughness, and cutting energy were attained at a small depth of cut (equivalent to chip thickness) and higher cutting speed. The cutting temperature was exceeded the glass transition temperature at full diameter tool usage, which causes machining ineffectiveness without coolant use in these conditions. Due to lower cutting conditions, the internal damage and delaminations were absent at the machined edge (Sheikh-Ahmad and Mohammed Citation2014).
The machining of GFRP composite generates enough heat required to cause thermal damages to the epoxy matrix. The 300 mm cutting length produces a cutting temperature of more than 160°C. With the generation of lower cutting forces and increased thermal conductivity, the graphene-filled GFRP composite laminate generates lesser heat during milling and leads to lower cutting temperature. The modified GFRP laminate has lower cutting forces and decreases the roughness through the grooves making happened due to the chip removal process. Overall, the addition of graphene improves the machinability of GFRP composites (El-Ghaoui, Chatelain, and Ouellet-Plamondon Citation2019). The 3000-rpm spindle speed reduces the thrust force than 2000 and 1000 rpm during the sisal/glass polymer composite drilling. The increment in feed rate results in a higher load on the drill bit, which causes more thrust forces during the machining process. Moreover, the drill diameter also shows an increment trend as like of feed rate. Hence the higher spindle speed, lower drill diameter, and feed rate are the best optimum conditions for drilling the sisal/glass polymer composite (Manickam and Gopinath Citation2017). The maximum thrust force of 55 to 70 N was observed while drilling glass/PP composite using HSS drill compared to solid carbide (SC) and tipped carbide (TC) drill, which was due to more tool wear and less hardness of HSS drill. The marginal thrust force variation was observed at solid carbide and tipped carbide tool performance. The delamination factor value varied between 1.8–1.9 for the HSS drill at 0.15 mm/rev of feed rate, whereas for solid carbide and tipped carbide tools it was recorded between 1.6–1.8. This delamination factor reduction was attributed to the drilling process constrained with thrust forces, also it might be due to high working temperature with carbide drill tools. The detailed comparison of delamination factor and thrust force is illustrated in the graphs shown in (Mudhukrishnan, Hariharan, and Palanikumar Citation2020).
Figure 5. The thrust force and delamination factor were compared to different drill tools (Mudhukrishnan, Hariharan, and Palanikumar Citation2020).
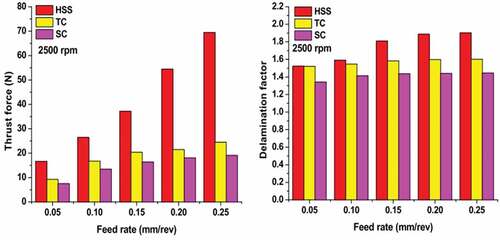
The drilling work was conducted for glass/polyphthalamide (PPA) composite demonstrating the delamination factor increment at low feed rate and high cutting speeds. The best-drilled surface quality was obtained at a 0.05 mm/rev feed rate. The GFRP composite surface roughness at lower feeds was affected by glass fibers pullout or fracture; however, it could be controlled with feed rate at high feeds. The SEM observation of drilled surface confirms the existence of fibers pull out, cracks, shearing, and crushing of fibers (Ficici, Ayparcasi, and Unal Citation2017). When end milling GFRP composite, increasing the feed rate or cutting speed speeds up tool wear and leads to fast cutting tool failure. The machining of 90° fibers-oriented sample makes wear easy to grow and prolongs the tool life as compared to the 0° fibers-oriented sample. The more tool wear in 90° orientation was due to inherent tool/fiber contact. This tool wear progression was effectively monitored with neuro-fuzzy and multiple regression analysis modeling. This modeling shows an acceptable accuracy while predicting the tool wear compared to experimental data (A. I. Azmi, Lin, and Bhattacharyya Citation2013). illustrates the graph of thrust force v/s time variation with depth of cut during the woven GFRP composite drilling process at 16.3 m/min and a feed of 0.025 mm/rev. At the first stage, the linear increment of thrust force was observed with the entry of the tool edge onto the workpiece. This stage represents the workpiece’s elastic loading due to the tool edge’s negative rake angle and its zero-center speed. Hence the tool edge extrudes the workpiece material instead of cutting. The second stage involves the entry of the tool edge inside the surface layer. At this point, the peaks are observed due to the stiffness reduction in the composites. The peaks are further increased due to the cutting-edge entry into a new layer and the left uncut layers are observed in decreased trend. The decrement of stiffness owing to the overall cutting of 53% thickness with temperature results in a drop of thrust force by 60% of their maximum peak. Finally, at the fourth stage, the cutting edges exit layer by layer in the workpiece, decreasing thrust force gradually over the tool length (Khashaba and El-Keran Citation2017). The GFRP composites were subjected to ANOVA, DFA (Desirability Function Analysis), and GRA (Grey Relational Analysis) analysis to study the turning machinability using TiCN/TiN coated tool. The findings of the ANOVA show that the depth of cut, followed by feed rate, had the greatest significant impact on surface roughness, while cutting rates had the greatest impact on tool wear. The GFRP turning process was subjected to multi-response optimization by using GRA to analyze the optimum parameters, and it was found to be 0.08 mm/rev of feed and 50 m/min of cutting speed. To overcome the problems that occurred in optimized multi-response during the GFRP turning process, the DFA was a very powerful tool while setting the optimal parameters to reduce roughness and tool wear, and those are 0.5 mm depth of cut, 100 m/min of cutting speed and 0.08 mm/rev of feed (Raveendran and Marimuthu Citation2015).
Figure 6. Drilling cycle of GFRE composite at 16.3 m/min and a feed of 0.025 mm/rev (Khashaba and El-Keran Citation2017).
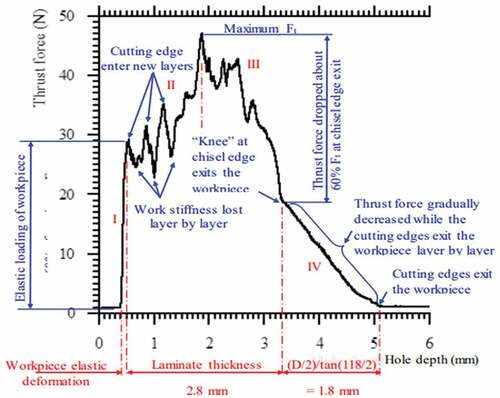
The fiber reinforcement causes a micro-abrasion on the grains of the uncoated tungsten carbide tool during the end milling of the GFRP composite. Severe delamination damages and uncut fibers have offset the tool wear performance across fibers orientation during machining. The end mill cutter tool life was analyzed through Taylor’s equation, and it confirms the cutting speed as a governing factor that affects the tool life of the end mill cutter (A. I. Azmi, Lin, and Bhattacharyya Citation2012). An experimental investigation on drilling glass/PP composite using the “Brad and Spur” tool reveals the major influencing factor on the cutting process: feed rate followed by drill diameter. These two parameters increment causes more thrust forces and increases in spindle speed have no significant variations on thrust forces. The empirical model was employed for thrust force prediction, and this model was best suited for predicting the thrust induced during cutting of glass/PP composite (Palanikumar et al. Citation2016). The artificial neural network (ANN) model for glass/PA66 composite reveals the higher impact of feed rate on the process outputs. The influencing percentage was over 80% for measured responses, which implies that low feed rate values cause smooth machining operation during longitudinal turning. The cutting speed has a low impact on measured responses, and it gives low cutting forces when used with low levels as compared to the feed rate. The machining parameters interactions were also noticeable when the influencing percentage of measured outputs reached 4% (Fountas et al. Citation2013). The insertion of CNT buckypaper into glass/epoxy composite shows a good milling performance with lower axial forces. The composite specimen without CNT insertion exhibits 3% higher axial forces than the filled composite. This CNT buckypaper improves the interlaminar strength between the epoxy and glass fibers, which results in lower delaminations during the milling process. Moreover, the CNT buckypaper in glass/epoxy improves the interlaminar shear stress by 25% more than the unfilled composite. Hence, it helps get a good surface finish with optimum machining performance (Wang et al. Citation2020).
Natural fiber-reinforced composites (NFRCs)
The NFRCs machinability is strongly dependent on the fiber type in the composite and their mechanical, thermal properties. Hence, care must be taken while selecting cutting tools and machining parameters for natural fiber or filler reinforced composite. The relevant parameters selection gives desired integrity and surface quality in the machined NFRC component (Abd-Elhady et al. Citation2020; Nassar, Arunachalam, and Alzebdeh Citation2017). Franke (Citation2011) investigated how the cutting edge affected the quality of the drilled holes while lengthy fiber-reinforced thermoplastic composites were being machined. The significant key factors during the drilling of long fibers reinforced thermoplastics were discovered to be feed force and fiber breakup. Bajpai and Singh (Citation2013) studied the drilling behavior of sisal/PP thermoplastic composite. When fibers are under tension while being cut, cutting is made easier and a high-quality surface is produced at the hole wall. Just after drilling procedure, the area of the hole wall that was created was visually inspected; neither uncut nor loose fibers were discovered, and the hole wall’s surface quality was satisfactory. When physical and mechanical qualities are not as crucial, it is vital to select the fibers kind which results in drilling-friendly NFRPCs. Different forms of cellulose are found in different types of fibers, and the various characteristics of fibers rely on the fiber plant parameters, including the maturity of the plant, the period of harvest, the weather, its soil, etc. The brittleness and ductility of fibers also affect the quality of drilled hole (Helmi Abdul Kudus, Ratnam, and Akil Citation2021). The NFRCs possess lower mechanical properties, and their unique characteristics with polymer material led to internal defects (cracks, improper bonding, blisters, and voids) in the composites. Hence these will cause problems when NFRCs are employed for machining processes (Chegdani and El Mansori Citation2019; Madhu et al. Citation2022). The orthogonal cutting of flax fiber reinforced PP composite reveals the generation of continuous chips at all cutting conditions. This was inherently correlated to the specific mechanical action of flax fiber within the PP matrix undercutting solicitations. This cutting behavior causes consequent surface damage through uncut fibers extremities and debonding zones. The influence of cutting depth was more on the machined surface, where the cutting forces were increased with increasing depth of cut. The cutting speed effect was significantly reduced because of thermal influence by plastic deformation and friction (Chegdani and El Mansori Citation2018a). The drilling and tribological behavior of flax/PP composite was affected by coated tool materials (diamond coated, titanium diboride coated, and uncoated tungsten carbide tool). The diamond coating leads to increment in thickness with cutting edge radius and also the intrinsic friction behavior of cutting tool by the alteration of surface morphology. The diamond-coated drill’s even though with the maximum response of intrinsic friction by diamond coating. This was due to the multiscale friction mechanism at the tool-workpiece interface and also due to coated surface morphology. This diamond coating declines the flax/PP composite machinability more than TiB2 coating. illustrates the comparison of machined surface SEM images using three types of tools. In that, the uncoated tool shows better machinability than other coated tools, preferably at a higher feed rate. Thus, the elemental flax fibers clear cut was observed on the machined surface, shown in . The torn-off fibers without cutting are observed on the machined surface ( due to higher specific cutting energy induced by diamond-coated tools (Chegdani and El Mansori Citation2018a). The cutting tool geometries significantly affect machined surface quality in the case of drilled flax/PLA composite. The changes in drill point angle lead to variations in thrust forces and cause various types of damages in the biodegradable composite. The usage of acute drill geometry improves the drill weakness and wear rates. At higher feeds, the damage caused by the drill point angle at entry and exit of the hole was reduced by 1.93% and 0.76%, respectively (Díaz-Álvarez et al. Citation2019). The delamination factor was elevated with both feed and speed parameters while drilling banana/epoxy composite. ANOVA analysis of this composite reveals more influence of feed on the delamination factor than the speed, with a significance of 51.73 and 53.13 at entry and exit, respectively. As compared to experimental analysis, the prediction of delamination factor using regression model has an error of 0.678 and 0.357 respectively at entry and exit (Venkateshwaran and ElayaPerumal Citation2012).
Figure 7. SEM images of machined surfaces which are drilled using three types of tools at 300 mm/min of feed rate, LUF-Long uncut fiber, SUF-Short uncut fiber, EF-Elementary fiber, DB-Debris, MX-Matrix (Chegdani, and El Mansori Citation2018b).
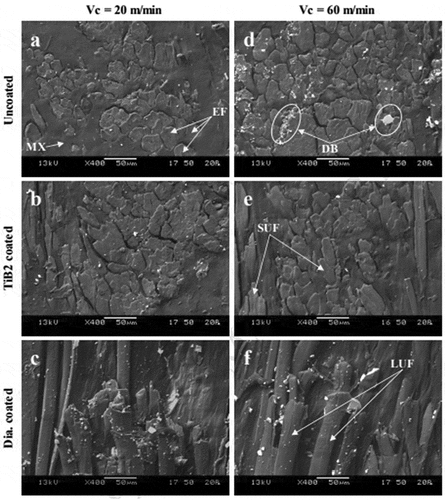
The alkaline treated jute fiber-reinforced composite exhibits reduced push-down delaminations more than the peel-up delaminations during the machining process. The delamination was increased with an increasing feed rate. The GRA Model evaluation was subjected to 16 experiments for the analysis of treated jute composite; out of 16, the 10 experiments gave better machining performance than the untreated composite. As per ANOVA suggestion, the delamination factor was slightly reduced due to alkali treatment, but the fiber treatment influence on the delamination factor was insignificant. The optimum feed rate and speed values are 0.03 mm/rev and 9.42 m/min, respectively, for jute/polyester composite (Sridharan and Muthukrishnan Citation2013). The machinability studies on kenaf reinforced plastic composite milling report the influence of milling parameters on delamination factor and surface roughness. The optimum parameter values are 500 rpm, 200 mm/min, and 2 mm, respectively, for spindle speed, feed rate, and depth of cut for kenaf reinforced composites. However, the spindle speed does not significantly affect surface roughness, but high spindle speed gives a good, machined surface. Whereas the influence of depth cut was not reported clearly, hence it was assumed to be a good surface finish with a deeper depth of cut (Azmi et al. Citation2018). An experimental study related to the drilling of rice husk reinforced composite reveals a lower delamination value as compared to glass fiber composite. The minimized delamination value was obtained for 118° drills, and it was well adapted for drilling rice husk/polyester composite. The drilling process with Brad drill causes maximum delamination value than the end mill and twist mill (Syed Azuan, Juraidi, and Wan Muhamad Citation2012). A new experimental study was conducted by Tran et al. to analyze machinability in polypropylene reinforced with biochar and miscanthus fiber composite. The study reveals that the drill diameter, spindle speed, and feed rate significantly affect the roughness, thrust force, and cutting energy of biocomposites. The emission of ultrafine particles was not affected significantly by drill diameter and machining parameters, while the feed rate has a much more significant effect on particles emission and thrust force as compared to other parameters. The cutting energy was decreased with increasing drill diameter and feed rate, while it was increased with increasing spindle speed. During the drilling process, the concentration of fine particles was reached up to 1300 #/cm3 and it was recorded 9000 #/cm3 for ultrafine particles concentration (Tran et al. Citation2020). The experimental studies on milling of jute and flax fiber-reinforced composite reveal the lower values of roughness, delamination factor, and cutting force for tungsten carbide mill, and these values are higher for HSS end mill. FFRP and JFRP composite milling show a low delamination factor at 0.01 mm/rev of feed rate and 2500 rpm of spindle speed, while maximum delamination factor was obtained for 0.02 mm/rev of feed rate 7500 rpm of spindle speed parameters. Similarly, the lower cutting force and surface roughness values were obtained at 0.01 mm/rev of feed rate and 7500 rpm of spindle speed, while the highest value was found at 0.02 mm/rev of feed rate and 2500 rpm of spindle speed. The closer values of tool vibration amplitudes (Çelik and Alp Citation2022). The effect of compatibilizer over natural fiber reinforced thermoplastic composite (jute/PP) was reported by Pailoor, Murthy, and Sreenivasa (Citation2021). Regarding fiber orientation and fiber type, compatibilizer had no effect on delamination during drilling process. However, throughout the composites without such a compatibilizer, delamination grew as fiber content did. Thrust force in the longitudinal axis was reduced in composites containing coupling agents. Increased velocity and feed in the composite without a compatibilizer were correlated with thicker, longer, and less curled chips. One of the best methods for enhancing interfacial bonding among bio-fibers and thermoplastics is considered to be the use of a compatibilizer. As a compatibilizer, a wide range of compounds including silanes, isocyanates, and maleated polyolefin have already been investigated. More delamination and decreased thrust force were the results of the compatibilizer addition. The creation of covalent and hydrogen linking with the -OH of jute fiber is responsible for the increased delamination (Aggarwal et al. Citation2013).
Challenges and future scope
Similar to the abundance of tool materials, the abundance of natural fibers also presents a difficulty when it comes to machining NFRCs since each natural fiber may have a distinct set of machining properties. This is further exacerbated by variations in the binding of the fiber matrix. The heat produced while milling is another important difficulty. Even while it can lessen the thrust force, the heat created leads to melt the polymers and scorch the fiber, which leads to structural failure and fiber peeling. Coolant might be used to lower the heat produced, but this would cause additional issues including moisture uptake by natural fibers, which will cause them to lose some of their qualities. The majority of investigations on CFRP composite machining have demonstrated that it is very difficult to reduce surface roughness. Hence, more analytical modeling and machine learning techniques needs to optimize the machining parameters.
Conclusions
This review article outlined the comprehensive studies on machinability of FRP composites, the factors/quality aspects of machinability, properties, and machining of fiber-reinforced composites using conventional techniques. A lot of research work going on in recent years to increase the machinability of polymer composite to the level of metal-based composites machinability. The cutting forces and damages that occurred in the sub-surface and surface of the composite were dependent on individual characteristics of reinforcements and matrix materials. Normally a higher spindle revolution speed, low drill diameter, a point angle nearer to 1000, lower tool traverse rate, and preferred parabolic tool drill are found to be effective for the drilling process. The maximum machinability for the end milling process may be obtained at a lower tool traverse rate, low cutting depth, and higher spindle speed. The non-homogeneous properties and insufficient ductility of GFRP, NFRC, and CFRP composites have produced fracturing and discontinuous chips during the machining operations. Additionally, research into high speed milling is a potential area since recent experimental findings indicated that faster cutting speeds produce lower process forces, extending tool life, or enabling faster feed rates. A further intriguing possibility is the use of minimal amount lubrication, which may enable increasing the intensity of the use of cutting fluids while potentially extending tool life and minimizing environmental effect. The different materials fracture or failure modes seem to have occurred randomly along the machined surfaces. Recent advancements in drilling of FRP composites are characterized by the advent of orbital drilling procedures, which require longer processing periods but can decrease or eradicate the delamination and heat damaging flaws caused while drilling composites. The tool selection and processing parameters are required to be optimized to get a better-machined surface. To improve the machining parameters, further research has to be done on utilizing analytical modeling and machine learning approach.
Highlights
Study on machinability of FRP composites, the factors/quality aspects of machinability, properties, and machining of fiber-reinforced composites using conventional techniques.
Machinability of FRP composites depends on the constituents present in the composites.
Delaminations were found in the natural fiber composites due to improper bonding and less compatibility with the polymer matrices.
Lower heat resistant property of the natural fibers causes serious problems during the machining process.
The maximum machinability for the end milling process may be obtained at a lower tool traverse rate.
Acknowledgment
The author extends their appreciation to the Deanship of Scientific Research at Majmaah University for funding this work under project No. R-2022-26.
Disclosure statement
No potential conflict of interest was reported by the authors.
Data availability statement
The data used to support the findings of this study are available from the corresponding author upon request.
References
- Abd-Elhady, A. A., H. E. D. M. Sallam, I. M. Alarifi, R. A. Malik, and T. M. A. A. EL-Bagory. 2020. Investigation of fatigue crack propagation in steel pipeline repaired by glass fiber reinforced polymer. Composite Structures 242 (April):112189. doi:10.1016/j.compstruct.2020.112189.
- Aggarwal, P. K., N. Raghu, A. Karmarkar, and S. Chuahan. 2013. Jute-polypropylene composites using m-TMI-grafted-polypropylene as a coupling agent. Materials & Design 43:112–21. doi:http://dx.doi.org/10.1016/j.matdes.2012.06.026.
- Alarifi, I. M. 2021. Investigation into the morphological and mechanical properties of date palm fiber-reinforced epoxy structural composites. Journal of Vinyl and Additive Technology 27 (1):77–88. doi:10.1002/vnl.21785.
- Altin Karataş, M., and H. Gökkaya. 2018. A review on machinability of carbon fiber reinforced polymer (CFRP) and glass fiber reinforced polymer (GFRP) composite materials. Defence Technology 14 (4):318–26. doi:10.1016/j.dt.2018.02.001.
- Azmi, H., C. H. C. Haron, J. A. Ghani, M. Suhaily, and A. R. Yuzairi. 2018. Machinability study on milling kenaf fiber reinforced plastic composite materials using design of experiments. IOP Conference Series: Materials Science and Engineering 344 (1).
- Azmi, A. I., R. J. T. Lin, and D. Bhattacharyya. 2012. Experimental study of machinability of GFRP composites by end milling. Materials and Manufacturing Processes 27 (10):1045–50. doi:10.1080/10426914.2012.677917.
- Azmi, A. I., R. J. T. Lin, and D. Bhattacharyya. 2013. Tool wear prediction models during end milling of glass fibre-reinforced polymer composites. International Journal of Advanced Manufacturing Technology 67 (1–4):701–18. doi:10.1007/s00170-012-4516-2.
- Bajpai, P. K., and I. Singh. 2013. Drilling behavior of sisal fiber-reinforced polypropylene composite laminates. Journal of Reinforced Plastics and Composites 32 (20):1569–76. doi:10.1177/0731684413492866.
- Burak Kaybal, H., A. Unuvar, Y. Kaynak, and A. Avcı. 2020. Evaluation of boron nitride nanoparticles on delamination in drilling carbon fiber epoxy nanocomposite materials. Journal of Composite Materials 54 (2):215–27. doi:10.1177/0021998319860245.
- Calzada, K. A., S. G. Kapoor, R. E. Devor, J. Samuel, and A. K. Srivastava. 2012. Modeling and interpretation of fiber orientation-based failure mechanisms in machining of carbon fiber-reinforced polymer composites. Journal of Manufacturing Processes 14 (2):141–49. doi:http://dx.doi.org/10.1016/j.jmapro.2011.09.005.
- Çelik, Y. H., and M. S. Alp. 2022. Determination of milling performance of jute and flax fiber reinforced composites. Journal of Natural Fibers 19 (2):782–96. doi:10.1080/15440478.2020.1764435.
- Cepero-Mejías, F., J. L. Curiel-Sosa, A. Blázquez, T. T. Yu, K. Kerrigan, and V. A. Phadnis. 2020. Review of recent developments and induced damage assessment in the modelling of the machining of long fibre reinforced polymer composites. Composite Structures 240:240. doi:10.1016/j.compstruct.2020.112006.
- Chegdani, F., and M. El Mansori. 2018a. Friction scale effect in drilling natural fiber composites. Tribology International 119:622–30. doi:10.1016/j.triboint.2017.12.006.
- Chegdani, F., and M. El Mansori. 2018b. Mechanics of material removal when cutting natural fiber reinforced thermoplastic composites. Polymer Testing 67:275–83. doi:10.1016/j.polymertesting.2018.03.016.
- Chegdani, F., and M. El Mansori. 2019. New multiscale approach for machining analysis of natural fiber reinforced bio-composites. Journal of Manufacturing Science and Engineering, Transactions of the ASME 141 (1):1–24. doi:10.1115/1.4041326.
- Chegdani, F., B. Takabi, M. El Mansori, B. L. Tai, and S. T. S. Bukkapatnam. 2020. Effect of flax fiber orientation on machining behavior and surface finish of natural fiber reinforced polymer composites. Journal of Manufacturing Processes 54 (November 2018):337–46. doi:10.1016/j.jmapro.2020.03.025.
- Cococcetta, N. M., D. Pearl, M. P. Jahan, and J. Ma. 2020. Investigating surface finish, burr formation, and tool wear during machining of 3D printed carbon fiber reinforced polymer composite. Journal of Manufacturing Processes 56 (December 2019):1304–16. doi:10.1016/j.jmapro.2020.04.025.
- Correia, J. R., Y. Bai, and T. Keller. 2015. A review of the fire behaviour of pultruded GFRP structural profiles for civil engineering applications. Composite Structures 127:267–87. doi:http://dx.doi.org/10.1016/j.compstruct.2015.03.006.
- Davim, J. P., F. Mata, V. N. Gaitonde, and S. R. Karnik. 2010. Machinability evaluation in unreinforced and reinforced PEEK composites using response surface models. Journal of Thermoplastic Composite Materials 23 (1):5–18. doi:10.1177/0892705709093503.
- Debnath, K., I. Singh, and A. Dvivedi. 2014. Drilling characteristics of sisal fiber-reinforced epoxy and polypropylene composites. Materials and Manufacturing Processes 29 (11–12):1401–09. doi:10.1080/10426914.2014.941870.
- Díaz-Álvarez, A., J. Díaz-Álvarez, C. Santiuste, and M. H. Miguélez. 2019. Experimental and numerical analysis of the influence of drill point angle when drilling biocomposites. Composite Structures 209:700–09. doi:10.1016/j.compstruct.2018.11.018.
- El-Ghaoui, K., J. F. Chatelain, and C. Ouellet-Plamondon. 2019. Effect of graphene on machinability of Glass Fiber Reinforced Polymer (GFRP). Journal of Manufacturing and Materials Processing 3 (3):1–12. doi:10.3390/jmmp3030078.
- Eneyew, E. D., and M. Ramulu. 2014. Experimental study of surface quality and damage when drilling unidirectional CFRP composites. Journal of Materials Research and Technology 3 (4):354–62. doi:http://dx.doi.org/10.1016/j.jmrt.2014.10.003.
- Ficici, F., Z. Ayparcasi, and H. Unal. 2017. Influence of cutting tool and conditions on machinability aspects of Polyphthalamide (PPA) matrix composite materials with 30 % glass fiber reinforced. International Journal of Advanced Manufacturing Technology 90 (9–12):3067–73. doi:http://dx.doi.org/10.1007/s00170-016-9626-9.
- Fountas, N. A., I. Ntziantzias, J. Kechagias, A. Koutsomichalis, J. P. Davim, and N. M. Vaxevanidis. 2013. Prediction of cutting forces during turning PA66 GF-30 glass fiber reinforced polyamide by soft computing techniques. Materials Science Forum 766:37–58. doi:10.4028/scientific.net/MSF.766.37.
- Franke, V. 2011. Drilling of long fiber reinforced thermoplastics - Influence of the cutting edge on the machining results. CIRP Annals - Manufacturing Technology 60 (1):65–68. doi:10.1016/j.cirp.2011.03.078.
- Gaitonde, V. N., S. R. Karnik, J. C. Rubio, A. E. Correia, A. M. Abrão, and J. P. Davim. 2008. Analysis of parametric influence on delamination in high-speed drilling of carbon fiber reinforced plastic composites. Journal of Materials Processing Technology 203 (1–3):431–38. doi:10.1016/j.jmatprotec.2007.10.050.
- Gao, C., J. Xiao, J. Xu, and Y. Ke. 2016. Factor analysis of machining parameters of fiber-reinforced polymer composites based on finite element simulation with experimental investigation. International Journal of Advanced Manufacturing Technology 83 (5–8):1113–25. doi:10.1007/s00170-015-7592-2.
- Geier, N., J. P. Davim, and T. Szalay. 2019. Advanced cutting tools and technologies for Drilling Carbon Fibre Reinforced Polymer (CFRP) composites: A review. Composites Part A: Applied Science and Manufacturing 125:105552. doi:10.1016/j.compositesa.2019.105552.
- Geier, N., J. Xu, C. Pereszlai, D. I. Poór, and J. P. Davim. 2021. Drilling of carbon fibre reinforced polymer (CFRP) composites: Difficulties, challenges and expectations. Procedia Manufacturing 54:284–89. doi:10.1016/j.promfg.2021.07.045.
- Helmi Abdul Kudus, M., M. M. Ratnam, and H. M. Akil. 2021. Factors affecting hole quality during drilling of natural fiber-reinforced composites: A comprehensive review. Journal of Reinforced Plastics and Composites 40 (9–10):391–405. doi:10.1177/0731684420970650.
- Hwang, H. S., M. H. Malakooti, B. A. Patterson, and H. A. Sodano. 2015. Increased interyarn friction through ZnO nanowire arrays grown on aramid fabric. Composites Science and Technology 107:75–81. doi:http://dx.doi.org/10.1016/j.compscitech.2014.12.001.
- Jagadeesh, P., V. S. H. Ningappa, M. Puttegowda, Y. G. T. Girijappa, S. M. Rangappa, M. R. Khan, I. Khan, and S. Siengchin. 2021. Pongamia pinnata shell powder filled sisal/kevlar hybrid composites: Physicomechanical and morphological characteristics. Polymer Composites 42 (9):4434–47. doi:10.1002/pc.26160.
- Jagadeesh, P., M. Puttegowda, P. Boonyasopon, S. M. Rangappa, A. Khan, and S. Siengchin. 2022. Recent developments and challenges in natural fiber composites: A review. Polymer Composites 43 (5):2545–61. doi:10.1002/pc.26619.
- Jagadeesh, P., M. Puttegowda, Y. G. T. Girijappa, S. M. Rangappa, M. K. Gupta, and S. Siengchin. 2021. Mechanical, electrical and thermal behaviour of additively manufactured thermoplastic composites for high performance applications.
- Jagadeesh, P., M. Puttegowda, Y. G. T. Girijappa, S. M. Rangappa, and S. Siengchin. 2022. Carbon fiber reinforced areca/sisal hybrid composites for railway interior applications: Mechanical and morphological properties. Polymer Composites 43 (1):160–72. doi:10.1002/pc.26364.
- Jagadeesh, P., M. Puttegowda, S. Mavinkere Rangappa, and S. Siengchin. 2021a. A review on extraction, chemical treatment, characterization of natural fibers and its composites for potential applications. Polymer Composites 42 (12):6239–64. doi:10.1002/pc.26312.
- Jagadeesh, P., M. Puttegowda, S. Mavinkere Rangappa, and S. Siengchin. 2021b. Influence of nanofillers on biodegradable composites: A comprehensive review. Polymer Composites 42 (11):5691–711. doi:10.1002/pc.26291.
- Jagadeesh, P., M. Puttegowda, O. P. Oladijo, C. W. Lai, S. Gorbatyuk, D. Matykiewicz, S. M. Rangappa, and S. Siengchin. 2022. A comprehensive review on polymer composites in railway applications. Polymer Composites 43 (3):1238–51. doi:10.1002/pc.26478.
- Jagadeesh, P., M. Puttegowda, S. M. Rangappa, and S. Siengchin. 2022. Role of polymer composites in railway sector: An overview. Applied Science and Engineering Progress 15 (2):1–8. doi:10.14416/j.asep.2022.02.005.
- Jagadeesh, P., Y. G. Thyavihalli Girijappa, M. Puttegowda, S. M. Rangappa, and S. Siengchin. 2020. Effect of natural filler materials on fiber reinforced hybrid polymer composites: An overview. Journal of Natural Fibers:1–16. doi:10.1080/15440478.2020.1854145.
- Jawali, N. D., B. Siddeswarappa, and Siddaramaiah. 2006. Physicomechanical properties, machinability, and morphological behavior of short glass fiber-reinforced Nylon 6 composites. Journal of Reinforced Plastics and Composites 25 (13):1409–18. doi:10.1177/0731684406066675.
- Jayabal, S., S. Velumani, P. Navaneethakrishnan, and K. Palanikumar. 2013. Mechanical and machinability behaviors of woven coir fiber-reinforced polyester composite. Fibers and Polymers 14 (9):1505–14. doi:10.1007/s12221-013-1505-5.
- Kalla, D., J. Sheikh-Ahmad, and J. Twomey. 2010. Prediction of cutting forces in helical end milling fiber reinforced polymers. International Journal of Machine Tools & Manufacture 50 (10):882–91. doi:http://dx.doi.org/10.1016/j.ijmachtools.2010.06.005.
- Kangokar Mukesh, S., N. Bettagowda, J. Praveenkumara, Y. G. Thyavihalli Girijappa, M. Puttegowda, S. Mavinkere Rangappa, S. Siengchin, and S. Gorbatyuk. 2022. Influence of stacking sequence on flax/kevlar hybrid epoxy composites: Mechanical and morphological studies. Polymer Composites 43 (6):3782–93. doi:10.1002/pc.26655.
- Karataş, M. A., and H. Gökkaya. 2018. A review on machinability of carbon fiber reinforced polymer (CFRP) and glass fiber reinforced polymer (GFRP) composite materials. Defence Technology 14 (4):318–26. doi:10.1016/j.dt.2018.02.001.
- Katnam, K. B., L. F. M. Da Silva, and T. M. Young. 2013. Bonded repair of composite aircraft structures: A review of scientific challenges and opportunities. Progress in Aerospace Sciences 61:26–42. doi:10.1016/j.paerosci.2013.03.003.
- Kechagias, J., G. Petropoulos, V. Iakovakis, and S. Maropoulos. 2009. An investigation of surface texture parameters during turning of a reinforced polymer composite using design of experiments and analysis. International Journal of Experimental Design and Process Optimisation 1 (2/3):164. doi:10.1504/IJEDPO.2009.030317.
- Khashaba, U. A., and A. A. El-Keran. 2017. Drilling analysis of thin woven glass-fiber reinforced epoxy composites. Journal of Materials Processing Technology 249:415–25. doi:http://dx.doi.org/10.1016/j.jmatprotec.2017.06.011.
- Khashaba, U. A., I. A. El-Sonbaty, A. I. Selmy, and A. A. Megahed. 2010. Machinability analysis in drilling woven GFR/epoxy composites: Part I - effect of machining parameters. Composites Part A: Applied Science and Manufacturing 41 (3):391–400. doi:http://dx.doi.org/10.1016/j.compositesa.2009.11.006.
- Kim, D., Y. H. Kim, S. Gururaja, and M. Ramulu. 2010. Processing and fiber content effects on the machinability of compression moulded random direction short GFRP composites. International Journal of Automotive Technology 11 (6 (December 1)):849–55. doi:10.1007/s12239-010-0101-6.
- Kumar, D., and K. K. Singh. 2019. Investigation of delamination and surface quality of machined holes in drilling of multiwalled carbon nanotube doped epoxy/carbon fiber reinforced polymer nanocomposite. Proceedings of the Institution of Mechanical Engineers, Part L: Journal of Materials: Design and Applications 233 (4):647–63.
- Kuzu, A. T., and M. Bakkal. 2016. The effect of cutting parameters and tool geometry on machinability of cotton-fiber reinforced polymer composites: Cutting forces, burr formation, and chip morphology. Journal of Industrial Textiles 45 (6):1364–82. doi:10.1177/1528083714560253.
- Liu, D. F., Y. J. Tang, and W. L. Cong. 2012. A review of mechanical drilling for composite laminates. Composite Structures 94 (4):1265–79. doi:http://dx.doi.org/10.1016/j.compstruct.2011.11.024.
- Lopresto, V., A. Caggiano, and R. Teti. 2016. High performance cutting of fibre reinforced plastic composite materials. Procedia CIRP 46:71–82. doi:http://dx.doi.org/10.1016/j.procir.2016.05.079.
- Madhu, P., J. Praveenkumara, M. R. Sanjay, S. Siengchin, and S. Gorbatyuk. 2022. Introduction to bio-based fibers and their composites. Advances in Bio-Based Fiber 2022(January):1–20.
- Maegawa, S., Y. Morikawa, S. Hayakawa, F. Itoigawa, and T. Nakamura. 2016. Mechanism for changes in cutting forces for down-milling of unidirectional carbon fiber reinforced polymer laminates: Modeling and experimentation. International Journal of Machine Tools & Manufacture 100:7–13. doi:http://dx.doi.org/10.1016/j.ijmachtools.2015.10.003.
- Malik, K., F. Ahmad, and E. Gunister. 2021. Drilling performance of natural fiber reinforced polymer composites: A review. Journal of Natural Fibers 19 (12):1–19. doi:10.1080/15440478.2020.1870624.
- Manickam, R., and A. Gopinath. 2017. Measurement and analysis of thrust force in drilling sisal-glass fiber reinforced polymer composites. IOP Conference Series: Materials Science and Engineering 197 (1).
- Manna, A., V. Mohindra, S. Patra, and M. Sandeep. 2008. Drilling of E-glass fibre reinforced polymer composite. International Journal of Machining and Machinability of Materials 3 (3–4):343–55. doi:10.1504/IJMMM.2008.020968.
- Melentiev, R., P. C. Priarone, M. Robiglio, and L. Settineri. 2016. Effects of tool geometry and process parameters on delamination in CFRP drilling: An overview. Procedia CIRP 45:31–34. doi:10.1016/j.procir.2016.02.255.
- Morkavuk, S., U. Köklü, M. Bağcı, and L. Gemi. 2018. Cryogenic machining of Carbon Fiber Reinforced Plastic (CFRP) composites and the effects of cryogenic treatment on tensile properties: A comparative study. Composites Part B: Engineering 147:1–11. doi:10.1016/j.compositesb.2018.04.024.
- Mudhukrishnan, M., P. Hariharan, and K. Palanikumar. 2020. Measurement and analysis of thrust force and delamination in drilling glass fiber reinforced polypropylene composites using different drills. Measurement: Journal of the International Measurement Confederation 149:106973. doi:10.1016/j.measurement.2019.106973.
- Nagaraj, A., A. Uysal, and I. S. Jawahir. 2020. An investigation of process performance when drilling carbon fiber reinforced polymer (CFRP) composite under dry, cryogenic and MQL environments. Procedia Manufacturing 43:551–58. doi:10.1016/j.promfg.2020.02.165.
- Nassar, M. M. A., R. Arunachalam, and K. I. Alzebdeh. 2017. Machinability of natural fiber reinforced composites: A review. International Journal of Advanced Manufacturing Technology 88 (9–12):2985–3004. doi:http://dx.doi.org/10.1007/s00170-016-9010-9.
- Navaneethakrishnan, S., and A. Athijayamani. 2016. Measurement and analysis of thrust force and torque in drilling of sisal fiber polymer composites filled with coconut shell powder. International Journal of Plastics Technology 20 (1):42–56. doi:10.1007/s12588-016-9139-2.
- Ozkan, D., M. Sabri Gok, M. Oge, and A. Cahit Karaoglanli. 2019. Milling behavior analysis of carbon fiber-reinforced polymer (CFRP) composites. Materials Today: Proceedings 11:526–33. doi:10.1016/j.matpr.2019.01.024.
- Pailoor, S., H. N. N. Murthy, and T. N. Sreenivasa. 2021. Drilling of in-line compression molded jute/polypropylene composites. Journal of Natural Fibers 18 (1):91–104. doi:10.1080/15440478.2019.1612309.
- Palanikumar, K., L. Karunamoorthy, and R. Karthikeyan. 2006. Assessment of factors influencing surface roughness on the machining of glass fiber-reinforced polymer composites. Materials & Design 27 (10):862–71. doi:10.1016/j.matdes.2005.03.011.
- Palanikumar, K., T. Srinivasan, K. Rajagopal, and B. Latha. 2016. Thrust force analysis in drilling glass fiber reinforced/polypropylene (GFR/PP) composites. Materials and Manufacturing Processes 31 (5):581–86. doi:10.1080/10426914.2014.961478.
- Panchagnula, K. K., and K. Palaniyandi. 2018. Drilling on fiber reinforced polymer/nanopolymer composite laminates: A review. Journal of Materials Research and Technology 7 (2):180–89. doi:http://dx.doi.org/10.1016/j.jmrt.2017.06.003.
- Paulo Davim, J., L. R. Silva, A. Festas, and A. M. Abrão. 2009. Machinability study on precision turning of PA66 polyamide with and without glass fiber reinforcing. Materials & Design 30 (2):228–34. doi:10.1016/j.matdes.2008.05.003.
- Petropoulos, G., I. Ntziantzias, P. Reis, and J. P. Davim. 2008. Predicting machinability parameters on drilling glass fibre reinforced plastics using response surface methodology. International Journal of Materials & Product Technology 32 (2–3):243–63. doi:10.1504/IJMPT.2008.018984.
- Poór, D. I., N. Geier, C. Pereszlai, and J. Xu. 2021. A critical review of the drilling of CFRP composites: Burr formation, characterisation and challenges. Composites Part B: Engineering: Engineering 223:109155. doi:10.1016/j.compositesb.2021.109155.
- Praveenkumara, J., P. Madhu, T. G. Yashas Gowda, M. R. Sanjay, and S. Siengchin. 2021. A comprehensive review on the effect of synthetic filler materials on fiber-reinforced hybrid polymer composites. The Journal of the Textile Institute 113 (7):1–9. doi:https://doi.org/10.1080/00405000.2021.1920151.
- Priyadharshini, M., D. Balaji, V. Bhuvaneswari, L. Rajeshkumar, M. R. Sanjay, and S. Siengchin. 2022. Fiber reinforced composite manufacturing with the aid of artificial intelligence – A state-of-the-art review. Archives of Computational Methods in Engineering 29 (7):5511–24. doi:10.1007/s11831-022-09775-y.
- Ramesh, M., K. Palanikumar, and K. H. Reddy. 2014. Influence of tool materials on thrust force and delamination in drilling sisal-glass fiber reinforced polymer (S-GFRP) composites. Procedia Materials Science 5:1915–21. doi:10.1016/j.mspro.2014.07.513.
- Raveendran, P., and P. Marimuthu. 2015. Multi-response optimization of turning parameters for machining glass fiber-reinforced plastic composite rod. Advances in Mechanical Engineering 7 (12):1–10. doi:10.1177/1687814015620109.
- Saoudi, J., R. Zitoune, S. Gururaja, M. Salem, and S. Mezleni. 2018. Analytical and experimental investigation of the delamination during drilling of composite structures with core drill made of diamond grits: X-Ray tomography analysis. Journal of Composite Materials 52 (10):1281–94. doi:10.1177/0021998317724591.
- Shahabaz, S. M., S. Sharma, N. Shetty, S. D. Shetty, and M. C. Gowrishankar. 2021. Influence of temperature on mechanical properties and machining of fibre reinforced polymer composites: A review. Engineered Science 16:26–46. doi:10.30919/es8d553.
- Sheikh-Ahmad, J., and J. Mohammed. 2014. Optimization of process parameters in diamond abrasive machining of carbon fiber-reinforced epoxy. Materials and Manufacturing Processes 29 (11–12):1361–66. doi:10.1080/10426914.2014.941869.
- Sheikh-Ahmad, J., N. Urban, and H. Cheraghi. 2012. Machining damage in edge trimming of CFRP. Materials and Manufacturing Processes 27 (7):802–08. doi:10.1080/10426914.2011.648253.
- Shunmugesh, K., and K. Panneerselvam. 2016. Machinability study of carbon fiber reinforced polymer in the longitudinal and transverse direction and optimization of process parameters using PSO–GSA. Engineering Science and Technology, an International Journal 19 (3):1552–63. doi:http://dx.doi.org/10.1016/j.jestch.2016.04.012.
- Sridharan, V., and N. Muthukrishnan. 2013. Optimization of machinability of polyester/modified jute fabric composite using grey relational analysis (GRA). Procedia Engineering 64:1003–12. doi:http://dx.doi.org/10.1016/j.proeng.2013.09.177.
- Syed Azuan, S. A., J. M. Juraidi, and W. M. Wan Muhamad. 2012. Evaluation of delamination in drilling rice husk reinforced polyester composites. Applied Mechanics and Materials 232:106–10. doi:10.4028/scientific.net/AMM.232.106.
- Thakur, R. K., and K. K. Singh. 2021. Influence of fillers on polymeric composite during conventional machining processes: A review. Journal of the Brazilian Society of Mechanical Sciences and Engineering 43 (2):1–20. doi:10.1007/s40430-021-02813-z.
- Tran, D. S., V. Songmene, A. D. Ngo, J. Kouam, A. Rodriguez-Uribe, M. Misra, and A. K. Mohanty. 2020. Experimental investigation on machinability of polypropylene reinforced with miscanthus fibers and biochar. Materials 13 (5):1181. doi:10.3390/ma13051181.
- Venkateshwaran, N., and A. ElayaPerumal. 2012. Hole quality evaluation of natural fiber composite using image analysis technique. Journal of Reinforced Plastics and Composites 32 (16):1188–97. doi:10.1177/0731684413486847.
- Vigneshwaran, S., K. M. John, R. Deepak Joel Johnson, M. Uthayakumar, V. Arumugaprabu, and S. T. Kumaran. 2021. Conventional and unconventional machining performance of natural fibre-reinforced polymer composites: A review. Journal of Reinforced Plastics and Composites 40 (15–16):553–67. doi:10.1177/0731684420958103.
- Vinayagamoorthy, R. 2018. A review on the machining of fiber-reinforced polymeric laminates. Journal of Reinforced Plastics and Composites 37 (1):49–59. doi:10.1177/0731684417731530.
- Wang, G. D., and S. K. Melly. 2018. Three-dimensional finite element modeling of drilling CFRP composites using Abaqus/CAE: A review. International Journal of Advanced Manufacturing Technology 94 (1):599–614. doi:10.1007/s00170-017-0754-7.
- Wang, X., S. K. Melly, N. Li, G. D. Wang, T. Peng, Y. Li, and Q. Di Zhao. 2020. Helical milling response of glass fiber-reinforced polymer composite with carbon nanotube buckypaper interlayer. Polymers and Polymer Composites 28 (6):378–87. doi:10.1177/0967391119879296.
- Wang, H., X. Qin, and H. Li. 2015. Machinability analysis on helical milling of carbon fiber reinforced polymer. Journal of Advanced Mechanical Design, Systems and Manufacturing 9 (5):1–11. doi:10.1299/jamdsm.2015jamdsm0057.
- Wang, X., F. Wang, T. Gu, Z. Jia, and Y. Shi. 2021. Computational simulation of the damage response for machining long fibre reinforced plastic (LFRP) composite parts: A review. Composites Part A: Applied Science and Manufacturing 143 (October 2020):106296. doi:10.1016/j.compositesa.2021.106296.
- Xu, J., Y. Yin, J. P. Davim, L. Li, M. Ji, N. Geier, and M. Chen. 2022. A critical review addressing drilling-induced damage of CFRP composites. Composite Structures 294:115594. doi:10.1016/j.compstruct.2022.115594.
- Zhu, W., H. Fu, F. Li, X. Ji, Y. Li, and F. Bai. 2022. Optimization of CFRP drilling process: A review. International Journal of Advanced Manufacturing Technology 123:1–30.