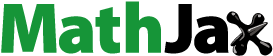
ABSTRACT
Agriculture biomass is a widely known renewable source that has a high possibility of recycling. The present investigation deals with the extraction, pre-treatment, dyeing, and characterization of natural fiber obtained from agricultural residues of corn husk. Water retted corn husk fibers were subjected to two steps of scouring and bleaching with hydrogen peroxide. The process effectively reduced non-cellulosic impurities, increased cellulose content to almost 79%, enhanced water absorption (431.5%), and increased fiber whiteness (54) with minimal impact on breaking tenacity (17.17 CN/tex). Natural dyeing was performed by using dye extracted from Sappan wood, and it was observed that fiber dyed without mordant exhibits a good color strength (K/S) of 13.21. Optimum dyeing conditions were determined by the response surface methodology, where K/S was kept as the main response. Modern spectroscopic characterization techniques were used for confirmatory analysis. The optimized recipe for natural dyeing is a 20% liquid dye concentration at 70°C for 1 hour, which achieved a K/S of 10.2–10.5 with adequate wash and light fastness properties in the range of 3–4 and 7–8, respectively. The current study will pave the way for the efficient textile application of this abundant but unnecessarily wasted biomass.
摘要
农业生物质是一种广为人知的可再生资源,具有很高的回收利用可能性本研究涉及从玉米壳的农业残留物中获得的天然纤维的提取、预处理、染色和表征. 对水沤玉米壳纤维进行两步精练和过氧化氢漂白. 该方法有效地减少了非纤维素杂质,将纤维素含量提高到几乎79%,提高了吸水率(431.5%),并提高了纤维白度(54),对断裂韧性的影响最小(17.17 CN/tex). 使用从Sappan木材提取的染料进行自然染色,观察到未经媒染剂染色的纤维显示出13.21的良好色强度(K/S). 通过响应面法确定最佳染色条件,其中K/S作为主要响应. 现代光谱表征技术用于验证分析. 天然染色的最佳配方是在700C下保持1小时20%的液体染料浓度,其K/S达到10.2-10.5,具有足够的洗涤牢度和耐光牢度,分别为3-4和7-8. 目前的研究将为这种丰富但不必要浪费的生物质的有效纺织应用铺平道路.
Introduction
Increasing concern about environmental pollution due to the use of synthetic materials has motivated researchers to look for natural or eco-friendly resources. The utilization of natural resources instead of synthetic fibers, dyes, and chemicals is the best strategy to reduce the environmental impact of textiles. Natural components obtained from plants, animals, and microbes are sustainable bio-resources with minimal ecological impact (Repon, Reazuddin, and Al Mamun Citation2016).
Corn is a well-known crop and is popular due to its production in different climatic conditions (Shaw Citation1988). Corn is used as raw material for various sectors, such as food processing, starch production, ethanol generation, animal feed, and pharmaceutical (Kazerooni et al. Citation2019). Corn crops that produce huge amounts of biomass typically consist of 15% husk, 35% leaves, and 50% cobs (N. Reddy and Yang Citation2015). Researchers around the world are exploring the utilization of corn husk waste for value-added end applications, such as making biodegradable pots (Fuentes et al. Citation2021), organic fertilizers (Anwar et al. Citation2015), porous carbon for the detection of cancer (Pandey et al. Citation2021), corn husk fiber (CHF) reinforced polymeric composite for acoustic applications (Sekar et al. Citation2019), and utilization in technical textile applications (Archana et al. Citation2017).
Traditionally, indigenous microorganism-based dew and water retting are used to extract bast fibers (Paridah, Amel Basher Ahmed Basher, and Zakia Citation2011). Sequential extraction using water retting, enzyme retting, and alkaline treatment are also tried by various researchers (Hanana et al. Citation2015). The raw CHF has 60–65% cellulose, 12–15% lignin, 18–22% hemicellulose, and 5–10% other impurities (Khan, Yilmaz, and Yilmaz Citation2020; Yilmaz et al. Citation2016). The presence of these hydrophobic impurities hinders water absorption into the fiber. Removal of such impurities from fiber helps to improve the ability of moisture absorption and makes it suitable for textile coloration (Luxbacher et al. Citation2014). Many researchers have reported alkaline boiling as an efficient method for scouring bast fibers (Reddy et al. Citation2014; Yilmaz et al. Citation2016). Researchers have studied different oxidative bleaching agents such as hydrogen peroxide, sodium hypochlorite, and peracetic acid (Chattopadhyay et al. Citation2021; Marc et al. Citation2018). Enzymatic pre-treatment for removal of lignin, hemicellulose, and pectin by using enzymes such as cellulase, xylanase, pectinase, and laccase were also studied (Batog et al. Citation2006). Researchers also tried using ultrasound and microwave energy for the pretreatment of bast fibers (Hassan and Saifullah Citation2018; Syrén, Peterson, and Kadi Citation2021).
Natural dyeing of textile fibers is a green approach appreciated worldwide to make sustainable clothing. The dyeing of jute, hemp, banana, and other bast fibers with different natural dyes, such as catechu, marigold (Pan, Chattopadhyay, and Day Citation2004), henna, myrobalan (Singh, Fatima, and Sharma Citation2010), dwarf elder (Chattopadhyay et al. Citation2013), jackfruit leaf, manjistha, red sandalwood, sappan wood, and babool (Samanta, Agarwal, and Datta Citation2008) have also been reported by researchers.
As with any other plant fibers, the extraction, pretreatment, and coloration of CHF by natural methods is an exciting and challenging area for research. The pretreatment and dyeing of this biomass provide the possibility of finding a new approach to CHF utilization and open the way for effective consumption of this naturally dyed fiber for textile applications. Moreover, to the best of our knowledge, based on the exhaustive literature survey done in this study, no researchers globally have attempted and reported effective coloration of un-mordanted CHF with natural dyes. Therefore, this research was aimed to extract lignocellulosic fiber from corn husk by water retting method, develop a pretreatment process for natural coloration and investigate the mechanical, morphological, and chemical properties. In addition, the optimization of natural dyeing parameters was carried out by a response surface statistical tool to get optimized conditions for the dyeing of corn husk fiber.
Materials and methods
Materials
Corn husks were obtained from Dhule, a district of Maharashtra, India. Sappan wood powder was procured from the local market in Mumbai. Sodium hydroxide flakes, glacial acetic acid, and tannic acid were obtained from SD fine chemicals, Mumbai; hydrogen peroxide (50%) was purchased from Merck Life Science, Mumbai. Nonionic wetting agent (Kleenox WLF Liq), peroxide stabilizer (Zystab C Liq), and soaping agent (Greenwash EC Liq) were procured from Rossari Biotech Ltd, Mumbai.
Methods
Extraction of fiber
CHF was extracted by water retting described by (Singh et al. Citation2020) with a minor modification. The corn husks were soaked in water for 20 days to allow biological degradation. The material-to-liquor ratio was maintained at 1:50. After 20 days, the retted fibers were washed thoroughly with fresh water and combed with a plastic comb to separate the fibers by removing degraded residual particles present in between the surface of the fibers and making a parallel aligned fiber bundle. The retained bundles of fibers were dried at 40°C for 6 hours. The dried fiber bundle was further crushed and beaten manually to remove residual particles from the fiber surface. These fibers were then used for further study.
Pre-treatment of CHF
Scouring – Retted CHF was scoured by a two-step process: the first step involved treatment with 3% (w/w) sodium hydroxide and 0.5% (w/w) nonionic wetting agent for 30 minutes at 95°C. The material-to-liquor ratio was 1:20. The partially scoured fibers were again finally scoured in the second step with 2% (w/w) sodium hydroxide and 0.5% (w/w) nonionic wetting agent, keeping other parameters the same as in the first step. After scouring, fibers were subjected to after-treatment of hot wash, cold wash, and then dried.
Bleaching – Scoured CHF was bleached with a recipe consisting 3% (w/w) hydrogen peroxide (50%), 1% (w/w) sodium hydroxide, 0.5% (w/w) peroxide stabilizer and 0.5% (w/w) nonionic wetting agent for 30 minutes at 95°C. The material-to-liquor ratio was maintained at 1:20. After bleaching, the fiber was cold rinsed, hot washed, and neutralized with 0.2% (w/w) acetic acid. The neutralized fiber was washed with cold water and dried.
Extraction of dye and dyeing - Natural colorant from sappan wood powder was extracted by an aqueous method. The sappan wood powder of concentrations of 10, 20, and 30% (w/v) was taken for extraction. The extraction process was carried out at 90°C for 1 hour. Then, the extracted liquor was cooled and filtered with a vacuum filter. The filtrate obtained was considered as a stock solution of 10, 20, and 30% and directly used for CHF dyeing. Natural dyeing of CHF was performed using sappan wood extracted dye solution. Dyeing was carried out with and without mordanting of CHF. 10% (w/w) tannic acid was used for mordanting CHF at 90°C for 1 hour. The MLR was set as 1:10, and the pH of the dye bath was maintained between 4.5 and 5.5 by using 0.5% acetic acid. The preliminary experiments indicated that higher color strength was obtained on un-mordanted CHF; therefore, further dyeing experiments were performed without moderating CHF. Process parameters were optimized using the design of expert (DOE) software. At the start, 17 trials were conducted to optimize dye concentration, time, and dyeing temperature. The MLR was set to 1:10 for all dyeing experiments. Further, after treatment was carried out with a 1% (w/w) soaping agent at 60°C for 20 minutes, washed with cold water, and dried.
Box-Behnken design
Process parameters like dye concentration, time, and temperature were optimized using the Box-Behnken design (BBD). Linear process order and ANOVA model were used. The lower and upper limits of the process parameters for dyeing are shown in .
Table 1. Process parameters with range for natural dyeing of CHF.
Characterizations
Weight loss, chemical composition, water absorption capacity, optical properties, color fastness, mechanical properties, structural and morphological properties were investigated, before characterization, samples were preconditioned for at least 24 hours at 21°C and 65% relative humidity.
Weight loss of the CHF was measured by the gravimetric method as per ISO: 1383–1977 (BIS, 1982). The weight loss percentage was calculated using EquationEquation 1(1)
(1) .
where Wa and Wb are the weight of fiber before the process and weight of fiber after the process, respectively.
The chemical constituent (cellulose, hemicellulose, lignin, and ash) analysis of CHF was determined using the standard procedures described by (Kale, Taye, and Chaudhary Citation2019). The moisture content of CHF was determined as per the ASTM D 2654–76 method. Before moisture content analysis, fiber was conditioned in sodium nitrite desiccators at 65 ± 2% relative humidity and 27 ± 2°C temperature (BIS 6359: 1971, 1972). The amount of fat and wax composition in CHF was determined as per TAPPI T204 cm-97 method by extracting the fiber in ethanol: benzene mixture 1:2 (v/v) using the soxhlet apparatus for 6 hours.
The water absorption capacity of CHF was calculated as per the (ASTM Standard D2402–07 Citation2012) method. The 0.5 gm of CHF was thoroughly wetted-out by immersion in distilled water for 5 minutes, after that centrifuged for 5 minutes at an acceleration of 9800 m/s2. After centrifuging CHF was weighed and dried at 110°C for 90 minutes, then the dried CHF was reweighed for calculating the water absorption capacity by EquationEquation 2(2)
(2)
where Wa and Wb stand for weight of fiber after centrifuged and weight of fiber after drying, respectively.
The whiteness, yellowness, and brightness index of bleached and K/S, L, a, b values of dyed CHF were measured by the Spectrascan-5100+ (Data Color International, USA) computerized color matching system. Hunter, ASTM D1925, and TAPPI T452 scales were used to calculate whiteness, yellowness, and brightness index, respectively. K/S value was measured under the illuminant D65 using 10° standard observer, and Kubelka Munk EquationEquation 4(4)
(4) was used for K/S calculation.
where K, S and R stand for the absorption coefficient, scattering coefficient, and reflectance, respectively, at the complete opacity of the dyed sample.
The wash fastness of the dyed fiber samples was tested according to ISO 105 C10 method using Launderometer. The lightfastness was assessed by the ISO 105 B02 (Ferus-Comelo et al. Citation2020) method using a xenon test chamber (Q-LAB) with a xenon-Arc lamp as a light source.
The FTIR spectra of the fabric samples were assessed in the range of 4000–500 cm−1 by Bruker ATR spectrophotometer, USA. Microscopic images were taken with the Laser Image analyzer Optical microscope (OLS5100 laser microscope). CHF’s tensile properties were tested using an Instron universal tensile tester as per the ASTM D3822 (ASTM Citation2012) standard.
Result and discussion
Chemical composition of CHF
displays the chemical components of the CHF at each of the three stages. It is evident that after scouring and bleaching, the CHF contains less lignin, hemicellulose, and other non-cellulosic elements. After scouring and bleaching, CHF has a cellulose content of about 79%. The increase in water-loving sites following the removal of lignin, waxes, and hydrophobic contaminants may be the cause of the CHF’s increased moisture content. The increase in the number of hydroxyl groups (OH) in cellulose is another factor that affects the moisture content (Luxbacher et al. Citation2014). Hemicelluloses have various sugar units that tend to build physical barriers around the cellulose fibers. Therefore, during the hemicellulose removal process, more of the cellulose’s hydrophilic hydroxyl groups get exposed (Bazargan et al. Citation2014).
Table 2. Pre-treatment performance of retted, scoured and bleached CHF.
Effect of pre-treatment on physical and chemical properties of CHF
displays the impact of pre-treatment on CHF. After scouring, the ability of the fiber to absorb water rises dramatically; after bleaching, just a slight increase is observed. As seen in , the decrease in lignin and other hydrophobic contaminants has increased the capacity of CHF to absorb water (Bazargan et al. Citation2014). Scouring and bleaching significantly impacted the breaking strength and elongation of CHF. After scouring, a decrease in breaking tenacity was seen. Possible causes include slight cellulose chain breakage or the conversion of cellulose I to cellulose II after high-temperature alkaline treatment (G. Singh et al. Citation2020) and excessive removal of non-cellulosic materials (Wang, Sheng Cai, and Jian Yong Citation2010). After scouring and bleaching, a modest increase in elongation percentage is also seen. Due to the elimination of lignin, hemicellulose, and other non-cellulosic impurities during scouring and bleaching, it was found that the weight of CHF fell by around 20%. The whiteness and brightness of bleached CHF increased as a result of the removal of contaminants and natural coloring material . There is a slight increase in yellowness after bleaching, which may be caused by the lignin’s oxidation and decay of hemicelluloses and other unstable polysaccharide chains to low molecular weight carbohydrate molecules after drying (Ahn et al. Citation2019; Beyer, Koch, and Fischer Citation2005). After scouring and bleaching, the laser micrograph in reveals regularities on the surface of the CHF; these regularities may be the result of the removal of surface-adhered detritus of non-cellulosic material (K. O. Reddy et al. Citation2014).
Microscopic analysis
FTIR spectra
In , the CHF’s FTIR spectroscopy is displayed. The O-H stretching vibration and the hydrogen bond of cellulose and hemicellulose are to blame for the broadband absorbance peak at 3400 cm−1. The typical C-H stretching in CH and CH2 of hemicellulose and cellulose was attributed to a peak of about 2900 cm−1. The C=O stretching vibration of the ester groups in hemicellulose or the carboxylic acid of lignin is indicated by the peak at 1740 cm−1 (Biswas et al. Citation2017). The C-O stretching vibration of the acetyl group in lignin and hemicellulose is linked to the absorbance peak at 1240 cm−1 (Luxbacher et al. Citation2014). The polysaccharide’s C-O and O-H stretching vibration in cellulose is responsible for a strong peak at about 1030 cm−1. The absorbance at 896 cm−1 is caused by β -glycosidic linkages between monosaccharides (Portella et al. Citation2016). After scouring and bleaching of CHF, the width of a band at 1740 cm−1 and 1240 cm−1 shrank, indicating that the amount of lignin and hemicellulose had decreased. Following pretreatment of CHF, the increase in peak at 896 cm−1 indicates an increase in cellulose content (Luxbacher et al. Citation2014).
Effect of mordanting on natural dyeing of corn husk fiber
displays the impact of mordanting on the color strength (K/S) of naturally colored CHF. It has been noted that CHF that has not been pre-mordanted with tannic acid has greater color strength. Magnesium and calcium metal ions exhibit the power to boost maximum color depth, and their inherent availability in CHF may be beneficial in obtaining adequate depth without the use of mordants (Erdogan, Karadag, and Eler Citation2010; Nishant et al. Citation2016). Both of the dyed fibers have nearly identical washing and light resistance.
Table 3. K/S and fastness properties of CHF dyed with and without mordant.
Optimization of dyeing conditions using response surface methodology
With the aid of design expert software, the dyeing conditions of CHF natural dyeing were adjusted. The Box-Benhken methodology was applied to the natural dyeing of CHF in order to improve color strength (K/S). 17 experiments were conducted to optimize the CHF dyeing process settings. illustrates the results of further analysis of natural dyed CHF findings in terms of color strength (K/S).
Table 4. Design matrix and dyeing performance of natural dyed CHF.
The statistical analysis of the data using the ANOVA model is shown in . A model term is suggested to be significant by a P-Value of 0.0251, which is less than 0.0500, whereas values of P greater than 0.1000 show that the model term is not significant. The ANOVA model’s F-value is 4.34, which suggests that it is significant. The F-value for the ANOVA model is 1.25, indicating that the lack of fit is insignificant. The F-value suggests a 44.38% risk of a lack of fit since there is a lot of noise. Here, we only care that the model is to be fit and the lack of fit to be insignificant (Pawar, Athalye, and Adivarekar Citation2021).
Table 5. ANOVA model results of CHF natural dyeing.
Regression analysis
The implementation of the design expert could be calculated using EquationEquation 4(4)
(4) . The color strength (K/S) of dyed CHF may be predicted for each process variable, such as dye concentration, temperature, and time, using the equation below, which is presented in a coded form.
Where A, B and C stand for dye concentration, temperature and time, respectively
Response surface plot
To get the highest color strength with the least amount of energy, dyes, and dyeing chemicals over the shortest amount of time, the dyeing process must be optimized. Temperature, dye concentration, and time are all important considerations during dyeing. Dye absorption is decreased and the chance of dye degradation is increased by an inadequate dyeing process (Haji and Rahimi Citation2020). illustrates the impact of dye concentration and dyeing temperature on the color intensity of dyed CHF with a set dyeing time. The dyeing had a set time limit of 60 minutes. As the temperature and dye bath concentration increases, so does the color strength of the dyed CHF. This is because the concentration of the dye in the solution at high temperature causes an increase in the adsorption of dye molecules from the dyebath to the surface of corn husk fibers (Haji and Rahimi Citation2020). Maximum color strength on dyed CHF was achieved in the temperature range of 70–90°C with a dye concentration of 20–30%. depicts the color strength of colored CHF with a 20% liquid dye concentration as a function of time and temperature during the dyeing process. demonstrates that the color strength of dyed CHF increases as temperature and dyeing time rise. The strongest color on dyed CHF was achieved between 70 and 90°C for 60–80 minutes. illustrates the impact of dye concentration and dyeing time on the color intensity of dyed CHF at a constant dyeing temperature of 70°C. shows that the color strength of dyed CHF rises with dye concentration and dyeing time. Maximum color strength on dyed CHF was achieved at a 20–30% dye concentration for 60–80 minutes.
Optimization of responses
displays the range of process parameters and their outcome (color strength). Desired weightage was given to all process conditions and worked to achieve maximum color strength on natural dyed CHF.
Table 6. Ranges of process parameters and their outputs.
Fastness properties of natural dyed CHF
presents the data for fastness. Naturally, colored CHF showed excellent lightfastness. When tested for washing fastness, naturally dyed CHF bleeds more color when washed. As a result, there is more staining on nearby cotton, while there is comparably slight staining on adjacent wool. Additionally, dyed CHF had a color change. Natural colored CHF has moderate ratings for washing fastness.
Conclusion
CHF has been successfully extracted, pretreated, and dyed with sappan wood natural dye. The two-step scouring with sodium hydroxide gives better absorbency, and further treatment with hydrogen peroxide improves the whiteness of CHF. Slight damage in the mechanical properties of CHF is observed after scouring and bleaching. The FTIR spectra and chemical composition confirm the reduced non-cellulosic impurities from CHF. The laser micrograph shows the regularities on the CHF surface after scouring and bleaching. Sappan wood natural dyeing without mordanting exhibits higher color strength than mordanted CHF. Based on BBD, the optimum conditions for dyeing the CHF using sappan wood natural dye were determined using the RSM. The results suggested that dye concentration, temperature, and time of dyeing affected the color strength of dyed CHF. Based on the numerical optimization model, the dye concentration 20%, temperature 70°C, and time of 60 minutes gave optimum color strength (K/S) with adequate fastness performance. This optimized method of pre-treatment and natural dyeing of CHF can be considered a possible way to utilize CHF in textile by blending it with other commercial natural fibers.
Highlights
Valorising agro-waste which otherwise goes for landfilling or burnt
Optimising parameters of extraction, pre-treatment and dyeing of corn husk fiber
Utilising sophisticated characterisation techniques to determine claimed effect
Developing process for application of natural colorant without the use of a mordant
Incorporating statistical modules for ascertaining response surface methodology.
Disclosure statement
No potential conflict of interest was reported by the authors.
References
- Ahn, K., S. Zaccaron, N. S. Zwirchmayr, H. Hettegger, A. Hofinger, M. Bacher, U. Henniges, T. Hosoya, A. Potthast, and T. Rosenau. 2019. Yellowing and brightness reversion of celluloses: CO or COOH, who is the culprit? Cellulose 26 (1):429–12. doi:10.1007/s10570-018-2200-x.
- Anwar, Z., M. Irshad, I. Fareed, and A. Saleem. 2015. Characterization and recycling of organic waste after co-composting - a review. The Journal of Agricultural Science 7:4. doi:10.5539/jas.v7n4p68.
- Archana, J., D. Rastogi, M. S. P. Bhawana Chanana, A. Dhama, and A. Dhama. 2017. Extraction of cornhusk fibres for textile usages. IOSR Journal of Polymer and Textile Engineering 04 (01):29–34. doi:https://doi.org/10.9790/019X-04012934.
- ASTM standard D2402-07. 2012. “Standard Test Method for Water Retention of Textile Fibers (Centrifuge Procedure).” ASTM Internal.
- Batog, J., W. Konczewicz, R. Kozlowski, M. Muzyczek, N. Sedelnik, and B. Tanska. 2006. Survey and recent report on enzymatic processing of bast fibers. Journal of Natural Fibers 3 (2–3):113–29. doi:10.1300/J395v03n02_08.
- Bazargan, A., T. Gebreegziabher, C. Wai Hui, and G. McKay. 2014. The effect of alkali treatment on rice husk moisture content and drying kinetics. Biomass & bioenergy 70:70. doi:https://doi.org/10.1016/j.biombioe.2014.08.018.
- Beyer, M., H. Koch, and K. Fischer. 2005.Role of hemicelluloses in the formation of chromophores during heat treatment of bleached chemical pulps. Macromolecular symposiaVol. 232 10.1002/masy.200551412
- Biswas, B., N. Pandey, Y. Bisht, R. Singh, J. Kumar, and T. Bhaskar. 2017. Pyrolysis of agricultural biomass residues: comparative study of corn cob, wheat straw, rice straw and rice husk. Bioresource Technology 237 (August):57–63. doi:10.1016/j.biortech.2017.02.046.
- Chattopadhyay, S. N., C. Pan, A. N. Roy, K. K. Samanta, and A. Khan. 2021. Hybrid bleaching of jute yarn using hydrogen peroxide and peracetic acid. Indian Journal of Fibre & Textile Research 46:78–82.
- Chattopadhyay, S. N., N. C. Pan, A. K. Roy, S. Saxena, and A. Khan. 2013. Development of natural dyed jute fabric with improved colour yield and Uv protection characteristics. The Journal of the Textile Institute 104 (8):808–18. doi:10.1080/00405000.2012.758352.
- Erdogan, G., R. Karadag, and A. Eler. 2010. Aluminium(iii), Fe(Ii) Complexes and dyeing properties of apigenin (5,7,4’-Trihydroxy Flavone). Reviews in Analytical Chemistry 29:3–4. doi:10.1515/REVAC.2010.29.3-4.211.
- Ferus-Comelo, M., H. Meister, A. Sick, and A. Wagner-Suettner. 2020. Instrumental ISO blue wool lightfastness assessments. Melliand International 3:26–28.
- Fuentes, R. A., J. A. Berthe, S. E. Barbosa, and L. A. Castillo. 2021. Development of biodegradable pots from different agroindustrial wastes and by products. Sustainable Materials and Technologies 30 (December):e00338. doi:10.1016/j.susmat.2021.e00338.
- Haji, A., and M. Rahimi. 2020. RSM optimization of wool dyeing with berberis thunbergii DC leaves as a new source of natural dye. Journal of Natural Fibers 19:2785–98. doi:https://doi.org/10.1080/15440478.2020.1821293.
- Hanana, S., A. Elloumi, V. Placet, H. Tounsi, H. Belghith, and C. Bradai. 2015. An efficient enzymatic-based process for the extraction of high-mechanical properties alfa fibres. Industrial Crops and Products 70 (August):190–200. doi:10.1016/j.indcrop.2015.03.018.
- Hassan, M. M., and K. Saifullah. 2018. Ultrasound-assisted pre-treatment and dyeing of jute fabrics with reactive and basic dyes. Ultrasonics Sonochemistry 40 (January):488–96. doi:10.1016/j.ultsonch.2017.07.037.
- Kale, R. D., M. Taye, and B. Chaudhary. 2019. Extraction and characterization of cellulose single fiber from native Ethiopian Serte (Dracaena Steudneri Egler) plant leaf. Journal of Macromolecular Science, Part A 56 (9):837–44. doi:10.1080/10601325.2019.1612252.
- Kazerooni, E., A. Sharif, H. Nawaz, R. Rehman, and S. Nisar. 2019. Maize (corn)-A useful source of human nutrition and health: A critical review. IJCBS 15:35–41.
- Khan, G. M. A., N. D. Yilmaz, and K. Yilmaz. 2020 August. Effects of Alkalization on physical and mechanical properties of biologically degummed okra bast and corn husk fibers. Journal of Natural Fibers 1–11. doi:10.1080/15440478.2020.1798840.
- Luxbacher, T., M. Čurlin, I. Petrinić, H. Bukšek, and T. Pušić. 2014. Assessing the quality of raw cotton knitted fabrics by their streaming potential coefficients. Cellulose 21 (5):3829–39. doi:10.1007/s10570-014-0388-y.
- Marc, D.A., J. A. M. Helena Oliver-Ortega, F. X. E. Jaume Camps, P. Mutjé, F. X. Espinach, and P. Mutjé. 2018. The role of lignin on the mechanical performance of polylactic acid and jute composites. International Journal of Biological Macromolecules 116 (September):299–304. doi:10.1016/j.ijbiomac.2018.04.124.
- Nishant, K., S. Basak, K. K. Samanta, and R. R. Deshmukh. 2016. Extraction of natural cellulosic fibers from cornhusk and its physico-chemical properties. Fibers and Polymers 17 (5):687–94. doi:10.1007/s12221-016-5416-0.
- Pan, N. C., S. N. Chattopadhyay, and A. Day. 2004. Dyeing of jute fabric with natural dye extracted from marigold flower. Asian Textile Journal 13 (January):80–82.
- Pandey, U., M. Usha Rani, A. Suresh Deshpande, S. Govind Singh, and A. Agrawal. 2021. Sweetcorn husk derived porous carbon with inherent silica for ultrasensitive detection of ovarian cancer in blood plasma. Electrochimica acta 397 (November):139258. doi:10.1016/j.electacta.2021.139258.
- Paridah, M. T., S. O. A. S. Amel Basher Ahmed Basher, and A. M. A. Zakia. 2011. Retting process of some bast plant fibres and its effect on fibre quality: A review. Bioresources 6:5260–81.
- Pawar, S. S., A. Athalye, and R. V. Adivarekar. 2021. Solvent assisted dyeing of silk fabric using deep eutectic solvent as a swelling agent. Fibers and Polymers 22 (2):405–11. doi:10.1007/s12221-021-0142-7.
- Portella, E. H., D. Romanzini, C. Coussirat Angrizani, S. Campos Amico, and A. José Zattera. 2016. Influence oF stacking sequence on the mechanical and dynamic mechanical properties of cotton/glass fiber reinforced polyester composites. Materials Research 19 (3):542–47. doi:10.1590/1980-5373-MR-2016-0058.
- Reddy, K. O., B. Ashok, K. R. N. Reddy, Y. E. Feng, J. Zhang, and A. V. Rajulu. 2014. Extraction and characterization of novel lignocellulosic fibers from Thespesia Lampas plant. International Journal of Polymer Analysis and Characterization 19 (1):48–61. doi:10.1080/1023666X.2014.854520.
- Reddy, N., and Y. Yang. 2015. Innovative bIofibers from renewable resources. Berlin, Heidelberg: Springer Berlin Heidelberg. doi:10.1007/978-3-662-45136-6.
- Repon, M., M. Reazuddin, and A. Al Mamun. 2016. Optimization of dyeing time of eco-friendly cotton coloration using banana (Musa Sapientum) floral stem sap. Chemical and Materials Engineering 4 (2):26–31. doi:10.13189/cme.2016.040203.
- Samanta, A., P. Agarwal, and S. Datta. 2008. Dyeing of jute with binary mixtures of jackfruit wood and other natural dyes - study on colour performance and dye compatibility. Indian Journal of Fibre and Textile Research 33 (January):171–180.
- Sekar, V., M. Hosseini Fouladi, S. Narayana Namasivayam, and S. Sivanesan. 2019. Additive manufacturing: A novel method for developing an acoustic panel made of natural fiber-reinforced composites with enhanced mechanical and acoustical properties. Journal of Engineering 2019 (September):1–19. doi:10.1155/2019/4546863.
- Shaw, R. H. 1988. Corn and corn improvement. ed. G. F. Sprague and J. W. DudleyMadison, WI, USA:American Society of Agronomy, Crop Science Society of America, Soil Science Society of America. 10.2134/agronmonogr18.3ed
- Singh, R., N. Fatima, and E. Sharma. 2010. Dyeing of banana blended fabric with natural dyes. Man-Made Textiles in India 53 (January):10–14.
- Singh, G., S. Jose, D. Kaur, and B. Soun. 2020 July. Extraction and characterization of corn leaf fiber. Journal of Natural Fibers 1–11. doi:10.1080/15440478.2020.1787914.
- Syrén, F., J. Peterson, and N. Kadi. 2021. Effects of microwave treatment in immersed conditions on the mechanical properties of jute yarn. Fibers 9 (7):40. doi:10.3390/fib9070040.
- Wang, W. M., Z. Sheng Cai, and Y. Jian Yong. 2010. Study on thE chemical modification process of jute fiber. Tappi Journal 9:2. doi:10.32964/tj9.2.23.
- Yilmaz, N. D., M. Sulak, K. Yilmaz, and F. Kalin. 2016. Physical and chemical properties of water-retted fibers extracted from different locations in corn husks. Journal of Natural Fibers 13 (4):397–409. doi:10.1080/15440478.2015.1029201.