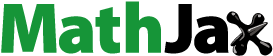
ABSTRACT
Bio-nanocomposite attracts a lot of attention in composite studies and in this article is observed the composite with cellulose nanofiber (CNF) reinforcement. Several types of potential fiber as reinforcement have been published and there is one type of interesting fiber due to its large population, namely Muntingia calabura, which is considered as agricultural waste. Muntingia stems also have the characteristics of being easy to dry, elastic, and soft which are potential to be used as a composite. In order to have high fiber performance, the manufacture of cellulose nanofibers needs to be analyzed for their characteristics. The characteristics of Muntingia fiber were enhanced by applying the chemical treatment using 8% of NaOH and 0.5% of NaClO. Next, mechanical treatment using an ultra-fine-friction grinder was performed to derive the CNF from the fiber. The chemical treatment roughened the fiber surface and decreased the impurities, lignin, and hemicellulose in the fiber. It was proven by the lignin bond chain (C-C) with the smallest intensity of 31.03% and the surface morphology was observed through SEM. The highest crystallinity index of Muntingia fiber was obtained from bleaching-treated Muntingia of 83.29%, affecting the percentage of total fiber weight lost by 28.75%. The lower the percentage of fiber weight loss, the higher the thermal resistance. This study showed that Muntingia fiber is potential to be used as one of the alternative fibers for bio-nano composite.
摘要
生物纳米复合材料在复合材料研究中引起了广泛的关注,本文观察了具有纤维素纳米纤维(CNF)增强的复合材料. 已经发表了几种可能用作增强材料的纤维,其中有一种因其人口众多而引起关注的纤维,即Muntingia calabura,被认为是农业废弃物. Muntingia茎还具有易于干燥、弹性和柔软的特点,有潜力用作复合材料. 为了获得高纤维性能,需要分析纤维素纳米纤维的制造过程中的特性. 通过使用8%的NaOH和0.5%的NaClO进行化学处理,增强了Muntingia纤维的特性. 接下来,使用超细摩擦研磨机进行机械处理以从纤维中获得CNF. 化学处理使纤维表面粗糙化,减少了纤维中的杂质、木质素和半纤维素. 木质素键链(C-C)的最小强度为31.03%,并通过SEM观察表面形貌. 漂白处理后的Muntingia纤维结晶度最高,达83.29%,影响纤维总重量损失28.75%. 纤维重量损失百分比越低,热阻越高. 这项研究表明,Muntingia纤维有潜力用作生物纳米复合材料的替代纤维之一.
Introduction
Nowadays, the use of biodegradable materials is increasing due to high environmental problems. Bio-nanocomposite is one of the most attractive materials, where the filler has a nanometer size, which is 100 nm or less. The bio-nanocomposite filler comes from organic or inorganic materials, while the matrix is a natural polymer (Darder, Aranda, and Ruiz-Hitzky Citation2007). The filler that is currently being developed in the manufacture of bio-nanocomposite materials is Cellulose Nanofiber (CNF). Cellulose in CNF has main characteristics, namely, low density and biodegradable. In addition, CNF high crystallinity, high specific surface area, and good rheological properties compared to inorganic reinforcement (Yang et al. Citation2019).
CNF contains amorphous and crystalline cellulose, which is composed of separated fibril or fibril bundles. The fiber formed from CNF is more flexible and longer with fibril diameter similar to or larger than cellulose nanocrystal (CNC). CNF has a morphology and dimension that vary substantially, depending on the fibrillation degree and initial treatment given. The structure shown in CNF is like a complex net (Xu et al. Citation2013). CNF has a diameter ranging from 5 to 30 nm with a length in microns and is produced through mechanical and chemical processes. The previous studies have used CNF as reinforcement material in bio-nanocomposite. Some of them used sisal (Santana et al. Citation2017), bamboo (Visakh et al. Citation2012), aloe vera (Kakroodi et al. Citation2014), kenaf (Sulaiman et al. Citation2020), and palm fiber (Supramaniam et al. Citation2020). The processes commonly used to make CNF include refining, grinding, high pressure homogenizers, high intensity ultrasonication, microfluidizers, and enzymatic methods. One of the simple processes is grinding process using a grinder to isolate the fiber cellulose (Nechyporchuk, Belgacem, and Bras Citation2016). However, there has been no study on Muntingia fiber.
Muntingia calabura is a tree that commonly grows on roadsides or on agricultural land. It can grow quite fast in hot or warm environmental conditions (Rahman, Fakir, and Rahman Citation2010). Due to its abundance, this plant adds too much agricultural waste (Vinod et al. Citation2021). The bark of the tree can be used to make ropes due to its strong and elastic characteristics. It is also antibacterial and antioxidant (Isnarianti, Wahyudi, and Puspita Citation2013). This study discusses the production, isolation, and characterization process of Muntingia fiber using ultra-fine grinding to get the reference of new fiber for bio-nano composite. This will reduce the abundance of waste of Muntingia.
This research began with the process of alkalization and bleaching on the bark of Muntingia stems. Next, an ultra-fine friction grinding process was carried out to obtain a smaller cellulose size. Then, it was characterized by Scanning Electron Microscopy (SEM), X-ray Diffraction (XRD), Fourier Transform Infrared (FTIR), and Thermogravimetric Analysis (TGA).
Materials
The CNF in the study used the fiber of Muntingia tree bark. The tree bark was collected from the forest in Malang, East Java, Indonesia. The chemical materials for alkalization and bleaching were sodium hydroxide (NaOH) pellets (Merck) and sodium hypochlorite (NaClO), were acquired from Sigma-Aldrich,Indonesia
Fiber extract and preparation of CNF
The alkalization process used 8% of NaOH. This amount of NaOH produced an optimum result on the fiber before being bleached. Chemical treatment was done to get better fiber characteristics and remove the impurities from the fiber (Naili et al. Citation2017). Previously, Muntingia was divided into untreated fiber and 8% NaOH treated. 1000 ml of aquades was used as a dissolvent for 80 g of NaOH. At room temperature, dry Muntingia fiber which had been previously soaked for 10 days was immersed in 8% NaOH solution for 2 h. Then, the fiber was dried at room temperature (23–30°C) for 24 h.
After alkalizing treatment, the fiber was bleached using 0.5% of NaClO. 966 ml of aquades was used to dissolve 42 ml NaClO. Then the fiber was immersed in 8% NaOH at room temperature condition for 2 h. The last step was drying the fiber for 24 h at room temperature (23–30°C).
Next, the bleached Muntingia fiber was mechanically processed using the ultra-fine grinding MKCA6–3 (Masuko Sangyo Co., Ltd., Japan) with an open gap (10 μm) for 1 min to pre-dispersed the material, which make slurry fibers with 1% cellulose and 99% wt% water. The material was prepared by providing 30 g Muntingia fiber as the source of cellulose and 2000 ml aquades as the dissolvent. Next, the fiber was immersed in aquades before the grinding process. The grinding process was performed in stages with gaps of 30, 50, 70, 90, and 110 with 10 cycled-repetition conducted for each gap. The CNF is successfully formed if there are no deposits and the fiber will transform into a gel (Xu et al. Citation2013). The extraction and isolation process of Muntingia CNF can be seen in .
Composition test
Composition analysis of Muntingia fiber was carried out using the TAPPI method (Ma et al. Citation2014). The fiber analysis performed in the study covered analysis of Neutral Detergent Fibers (NDF), acid detergent fibers (ADF) (Wali, Haneda, and Maryana Citation2014), cellulose, and lignin. The results were displayed in the form of a percentage of cellulose content, hemicellulose, and lignin as seen in .
Table 1. Muntingia calabura fiber composition test.
Scanning electron microscope (SEM)
The morphology of fiber surface was analyzed using FE-SEM (FEI Type: Quanta FEG 650). The image used 1000× magnification with an electron beam acceleration potential of 3 kV. The surface morphology was observed in two different planes: longitudinal plane and cross-sectional area.
X-Ray diffraction (XRD)
The crystallinity index was analyzed using XRD test. The tool used was PAN analytical type X’Pert3 Powder with a radiation source of Cu, 40 kV, and 30 mA. The crystallinity index (CI) was calculated using EquationEquation (1)(1)
(1) :
is the greatest peak intensity and
is the diffraction intensity of the crystalline (Segal et al. Citation1959).
Fourier transform infrared (FTIR)
Test specifications according to ASTM E1252 (Hashim et al. Citation2016). FTIR spectrometer was used Nicolet Avatar 360 IR. Using KBr powder, the spectrometer used a wavelength range of 4000 cm−1 to 450 cm−1 with a scan rate of 10 per minute.
Thermogravimetric analysis (TGA)
TGA test was used Hitachi STA-200RV type. Samples weight varied from 5.9 mg to 6.8 mg. Later, the samples were heated at a temperature of room temperature until 500°C (using nitrogen gas). Changes in mass would have been later detected by a tool and recorded by computer software.
Result and discussion
The chemical composition of Muntingia fiber
The chemical composition of the fiber before and after treatment can be seen in . The analysis shows that there is a decrease in lignin and hemicellulose content due to the alkalizing treatment on the fiber. The alkalization process can clean fiber from impurities, lignin, and hemicellulose because the hydrogen bonds in the lignin are broken by the OH- compound in NaOH (Sood and Dwivedi Citation2018). The table shows that the lignin content of 17.05 decreased by 5.18%. The lowest lignin content was found in the 0.5% NaClO treated fiber. However, the cellulose content in the fiber decreased because the cellulose in the fiber was decomposed during the chemical treatment. The highest cellulose (40.41%) was found in the untreated fiber. The extractives content of CNF’s Muntingia fiber was 8.9% while the ash content was 6.1%.
Morphology
The SEM image shows the difference in the surface structure of the chemically treated and untreated fiber. As seen in , the untreated fiber surface tends to be smoother because it is still covered by impurities, wax, lignin, and hemicellulose (Mouhoubi et al. Citation2017). On the contrary, the alkalized and bleached fiber looks rougher (). The chemical treatment has roughened the fiber. This will affect the tensile strength of the fiber. If the image in is compared with the image in , it is seen that the impurities have been reduced in the fiber (Wong, Yousif, and Low Citation2010).
FTIR analysis
The fiber spectrum of Muntingia fiber is shown in . The spectrum is useful to identify the functional group of the Muntingia fiber before and after treatment. The peak of 3200–3344 cm−1 corresponds to the stretching of the hydroxyl (−OH) in cellulose. In this conversion, several things happened such as changes in hydroxyl, carboxyl, and the area around lignin. An expansion occurs at the peak area of 3200–3600 cm−1. This affected the increase in the hydrogen bonds in the cellulose chain due to the shift in the hydroxyl group. The Hydroxyl group increased after it lost the amorphous components (Pandey et al. Citation2008). The intensification of these peaks presented an increase in the cellulose content and the removal of amorphous components increased the hydrogen bonds between the cellulose chains (Syafri et al. Citation2022).
The peak of 2923–2925 cm−1 is related to the C-H strain, but it is not detected in the alkali treatment spectrum. This may indicate that the treatment is appropriate in removing most of the hemicellulose and lignin from the fiber. The peak of 1611–1647 cm−1 is related to the strain of C=O in the hemicellulose, water adsorption, C-O, C-H group from an aromatic ring, and the C-O strain in the lignin (Jonoobi et al. Citation2010). These results could also indicate that alkali treatment was more efficient in removing hemicellulose in the fiber (Syafri et al. Citation2022). The peak of 1389–1409 cm−1 corresponds to the strain of CH2 and OH groups. The peak of 1022–1028 cm−1 is associated with the strain of C-O, the asymmetrical strain of C-OC, and oscillatory vibration in cellulose (Ilyas, Sapuan, and Ishak Citation2018).
XRD analysis
XRD analysis is one of the parameters used to observe the influence of Muntingia fiber crystallinity index before and after alkalizing and bleaching treatment. shows the XRD curve of muntingia fiber before and after the treatment. The XRD curve analysis was performed using the Segal method (Segal et al. Citation1959). The result of the crystallinity index is shown in . The diffraction pattern seen in the image displays the peak intensity which is indicated from the angle of 2 theta, including the low angle of 15.4° which shows the amorphous fiber component or noncellulose component. The high angle of 22.45° expresses the crystallinity of the fiber. The significant difference of the spectrum in the comparison exposes a difference of crystallinity and semi-crystallinity contents (Jayaramudu, Guduri, and Rajulu Citation2010).
Figure 4. (a) XRD curve and (b) crystallinity index of Muntingia fiber without treatment, alkalized, bleached and CNF treated.
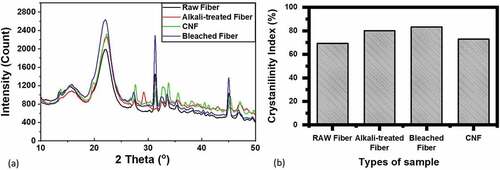
The result of the crystallinity index of raw Muntingia fiber is 69.31% (displayed in the table above). The number is higher than the crystallinity index of other natural fibers such as Cissus quadrangularis (47.15%) (Indran and Raj Citation2015), Agave gigantea (48.29%) (Syafri et al. Citation2022), corn husk fiber (59.49%) (Herlina Sari et al. Citation2018), and Cyrtostachysrenda fiber (56%) (Loganathan et al. Citation2022). After the Muntingia calabura fiber was alkalized, its crystallinity index became 79.99%. After bleaching, the maximum crystallinity index was 83.29%. This was because the bleaching process was effective to remove the amorphous component from Muntingia fiber. However, their number decreased to 72.85% after mechanical treatment (CNF) due to the damage in the cellulose chain caused by the mechanical treatment (Jonoobi, Mathew, and Oksman Citation2012).
TGA analysis
The thermal degradation of Muntingia fiber was analyzed using the curve of Thermogravimetric (TG) and Difference Thermogravimetric (DTG) shown in . Thermal degradation was calculated to measure the loss of weight due to temperature change. The TG curve presents the three regions of fiber degradation temperature starting from the moisture evaporation in the fiber in the temperature range of 27°C to 87°C, cellulose degradation in region two in the temperature range of 181°C to 188°C, and region three in the temperature range of 300°C to 489°C showing residual substances in the form of ash (Mahardika et al. Citation2018). The total percentage of weight loss from the Muntingia fiber without treatment and with alkalizing, bleaching, and CNF treatment along with the temperature increase is 84. 97%, 31.92%, 28. 75%, and 38.97%. It can be seen that the percentage of total weight lost to the heating temperature of the fiber gets lower. The decreasing weight loss is inversely proportional to the thermal resistance of the fiber, because the lower the weight loss, the more resistant the fiber is to heating. Fiber resistance to heating is called the thermal resistance of the fiber. The thermal resistance of the fiber is directly proportional to the crystallinity index of the fiber (Andoko et al. Citation2022; Suryanto et al., Citation2014). So, when the crystallinity index is high, the thermal resistance of the fiber is high too. Because more crystalline phases in the fiber means stronger thermal resistance (Hajiha, Sain, and Mei Citation2014). The percentage of the weight loss indicates that the higher the crystallinity index of the fiber (), the higher the thermal resistance of the fiber ().
Conclusion
This study introduces and characterizes the insulation results of Muntingia fiber as an innovation in the newest bio-nano composite reinforcement. Characterization was carried out by looking at the composition, crystallinity index, functional groups and thermal resistance of CNF Muntingia fiber. Muntingia fiber that has been bleached for 2 h has shown very low lignin content (5.18%). The crystallinity index of the bleached Muntingia fiber is 83.29%. This number is higher than that of untreated fiber. The result of the crystallinity index is associated with the thermal resistance of the fiber. The bleached Muntingia fiber had the highest thermal resistance with a weight lost a percentage of only 28.75%. Bleaching using NaClO is the chemical treatment that is recommended to obtain the purity of cellulose in producing nanocellulose fiber. The characteristic revealed that Muntingia fiber is potential as light and environmentally friendly bio-nano composite.
Highlights
Bio-nanocomposite attracts a lot of attention in composite studies
Characteristics of Muntingia fiber were enhanced by applying the chemical treatment
Chemical treatment roughened the fiber surface and decreased the impurities, lignin, and hemicellulose in the fiber.
Muntingia fiber is potential to be used as one of the alternative fibers for bio-nano composite.
Acknowledgments
This research is a collaboration between Materials Compartment, Mechanical Engineering Department , Faculty of Engineering, UB and Natural Composites Research Group Lab, Department of Materials and Production Engineering, KMUTNB. This research was partially funded by the Hibah Doktor LK FT-UB, grant number : 20/UN.10.F07/H.PN/2022 and partly by the National Science, Research and Innovation Fund (NSRF), and King Mongkut’s University of Technology North Bangkok with Contract no. KMUTNB-FF- 66-01.
Disclosure statement
No potential conflict of interest was reported by the author(s).
References
- Andoko, A., F. Gapsari, K. Diharjo, M. R. Sanjay, and S. Siengchin. 2022. Isolation of microcellulose from timoho fiber using the process of delinigfication and maceration: Evaluation of physical, chemical, structural, and thermal properties. International Journal of Biological Macromolecules 14 (22):8130–10. doi:10.1016/j.ijbiomac.2022.10.225.
- Darder, B. M., P. Aranda, and E. Ruiz-Hitzky. 2007. Bionanocomposites: A new concept of ecological, bioinspired, and functional hybrid materials. Advanced Materials 19 (10):1309–19. doi:10.1002/adma.200602328.
- Hajiha, H., M. Sain, and L. H. Mei. 2014. Modification and characterization of hemp and sisal fibers. Journal of Natural Fibers 11 (2):144–68. doi:10.1080/15440478.2013.861779.
- Hashim, M. Y., M. N. Roslan, O. M. F. Marwah, S. Mahzan, M. Zin, and S. Ariffin. 2016. The effect of alkali treatment conditions on tensile strength of kenaf fiber. ARPN Journal of Engineering and Applied Sciences 11 (14):8658–62.
- Herlina Sari, N., I. N. G. Wardana, Y. S. Irawan, and E. Siswanto. 2018. Characterization of the chemical, physical, and mechanical properties of NaOH-treated natural cellulosic fibers from corn husks. Journal of Natural Fibers 15 (4):545–58. doi:10.1080/15440478.2017.1349707.
- Ilyas, R. A., S. M. Sapuan, and M. R. Ishak. 2018. Isolation and characterization of nanocrystalline cellulose from sugar palm fibres (Arenga Pinnata). Carbohydrate Polymers 181:1038–51. doi:10.1016/j.carbpol.2017.11.045.
- Indran, S., and R. E. Raj. 2015. Characterization of new natural cellulosic fiber from Cissus quadrangularis stem. Carbohydrate Polymers 117:392–99. doi:10.1016/j.carbpol.2014.09.072.
- Isnarianti, R., I. A. Wahyudi, and R. M. Puspita. 2013. Muntingia calabura L leaves extract inhibits glucosyltransferase activity of Streptococcus mutans. Journal of Dentistry Indonesia 20 (3):59–63. doi:10.14693/jdi.v20i3.195.
- Jayaramudu, J., B. R. Guduri, and A. V. Rajulu. 2010. Characterization of new natural cellulosic fabric Grewia tilifolia. Carbohydrate Polymers 79 (4):847–51. doi:10.1016/j.carbpol.2009.10.046.
- Jonoobi, M., J. Harun, A. P. Mathew, and K. Oksman. 2010. Mechanical properties of cellulose nanofiber (CNF) reinforced polylactic acid (PLA) prepared by twin screw extrusion. Composites Science and Technology 70 (12):1742–47. doi:10.1016/j.compscitech.2010.07.005.
- Jonoobi, M., A. P. Mathew, and K. Oksman. 2012. Producing low-cost cellulose nanofiber from sludge as new source of raw materials. Industrial Crops and Products 40 (1):232–38. doi:10.1016/j.indcrop.2012.03.018.
- Kakroodi, A. R., S. Cheng, M. Sain, and A. Asiri. 2014. Mechanical, thermal, and morphological properties of nanocomposites based on polyvinyl alcohol and cellulose nanofiber from Aloe vera rind. Journal of Nanomaterials 2014 (i):12–18. doi:10.1155/2014/903498.
- Loganathan, T. M., M. T. H. Sultan, M. Jawaid, Q. Ahsan, J. Naveen, and V. Perumal. 2022. Characterization of new cellulosic Cyrtostachys renda and Ptychosperma macarthurii fibers from landscaping plants. Journal of Natural Fibers 19 (2):669–84. doi:10.1080/15440478.2020.1758865.
- Ma, X. J., S. L. Cao, X. F. Yang, L. Lin, L. H. Chen, and L. L. Huang. 2014. Lignin removal and benzene-alcohol extraction effects on lignin measurements of the hydrothermal pretreated bamboo substrate. Bioresource Technology 151:244–48. doi:10.1016/j.biortech.2013.10.078.
- Mahardika, M., H. Abral, A. Kasim, S. Arief, and M. Asrofi. 2018. Production of nanocellulose from pineapple leaf fibers via high-shear homogenization and ultrasonication. Fibers 6 (2):1–12. doi:10.3390/fib6020028.
- Mouhoubi, S., M. E. H. Bourahli, H. Osmani, and S. Abdeslam. 2017. Effect of alkali treatment on alfa fibers behavior. Journal of Natural Fibers 14 (2):239–49. doi:10.1080/15440478.2016.1193088.
- Naili, H., A. Jelidi, O. Limam, and R. Khiari. 2017. Extraction process optimization of Juncus plant fibers for its use in a green composite. Industrial Crops and Products 107:172–83. doi:10.1016/j.indcrop.2017.05.006.
- Nechyporchuk, O., M. N. Belgacem, and J. Bras. 2016. Production of cellulose anofibrils: A review of recent advances. Industrial Crops and Products 93:2–25. doi:10.1016/j.indcrop.2016.02.016.
- Pandey, J. K., J. W. Lee, W. S. Chu, C. S. Kim, S. H. Ahn, and C. S. Lee. 2008. Cellulose nano whiskers from grass of Korea. Macromolecular Research 16 (5):396–98. doi:10.1007/BF03218535.
- Rahman, M. M., M. S. A. Fakir, and M. M. Rahman. 2010. Fruit growth of China Cherry (Muntingia calabura). Botany Research International 3 (2):56–60.
- Santana, J. S., J. M. Do Rosário, C. C. Pola, C. G. Otoni, N. de Fátima Ferreira Soares, G. P. Camilloto, and R. S. Cruz. 2017. Cassava starch-based nanocomposites reinforced with cellulose nanofibers extracted from sisal. Journal of Applied Polymer Science 134 (12):1–9. doi:10.1002/app.44637.
- Segal, L., J. J. Creely, A. E. Martin, and C. M. Conrad. 1959. An empirical method for estimating the degree of crystallinity of native cellulose using the X-ray diffractometer. Textile Research Journal 29 (10):786–94. doi:10.1177/004051755902901003.
- Sood, M., and G. Dwivedi. 2018. Effect of fiber treatment on flexural properties of natural fiber reinforced composites: A review. Egyptian Journal of Petroleum 27 (4):775–83. doi:10.1016/j.ejpe.2017.11.005.
- Sulaiman, S., N. S. Sahat, F. N. Omar, M. N. Mokhtar, M. N. Naim, A. S. Baharuddin, and M. A. M. Salleh. 2020. Chemical-physical treatment for production of cellulose nanofiber from Kenaf Bast fiber. Journal of Natural Fibers 19 (12):4403–14. doi:10.1080/15440478.2020.1863288.
- Supramaniam, J., S. Kiat Wong, B. Fen Leo, L. Teng Hern Tan, B. Hing Goh, and S. Ying Tang. 2020. Unravelling the swelling behaviour and antibacterial activity of palm cellulose nanofiber-based metallic nanocomposites. IOP Conference Series: Materials Science and Engineering 778 (1):012027. doi:10.1088/1757-899X/778/1/012027.
- Suryanto, H., E. Marsyahyo, Y. S. Irawan, and R. Soenoko. 2014. Morphology, Structure, and Mechanical Properties of Natural Cellulose Fiber from Mendong Grass (Fimbristylis globulosa). Journal of Natural Fibers. doi:10.1080/15440478.2013.879087.
- Syafri, E., N. H. Sari, M. Mahardika, P. Amanda, and R. A. Ilyas. 2022. Isolation and characterization of cellulose nanofibers from Agave gigantea by chemical-mechanical treatment. International Journal of Biological Macromolecules 200:25–33. doi:10.1016/j.ijbiomac.2021.12.111.
- Vinod, A., T. G. Yashas Gowda, R. Vijay, M. R. Sanjay, M. K. Gupta, M. Jamil, V. Kushvaha, and S. Siengchin. 2021. Novel Muntingia Calabura bark fiber reinforced green-epoxy composite: A sustainable and green material for cleaner production. Journal of Cleaner Production 294:126337. doi:10.1016/j.jclepro.2021.126337.
- Visakh, P. M., S. Thomas, K. Oksman, and A. P. Mathew. 2012. Effect of cellulose nanofibers isolated from bamboo pulp residue on vulcanized natural rubber. BioResources 7 (2):2156–68. doi:10.15376/biores.7.2.2156-2168.
- Wali, M., F. Haneda, and N. Maryana. 2014. Identifikasi Kandungan Kimia Bermanfaat pada Daun Jabon Merah dan Putih (Anthocephalus spp.). Jurnal Silvikultur Tropika Agustus 05 (2):77–83.
- Wong, K. J., B. F. Yousif, and K. O. Low. 2010. The effects of alkali treatment on the interfacial adhesion of bamboo fibres. Proceedings of the Institution of Mechanical Engineers, Part L: Journal of Materials: Design and Applications. doi:10.1243/14644207JMDA304
- Xu, X., F. Liu, L. Jiang, J. Y. Zhu, D. Haagenson, and D. P. Wiesenborn. 2013. Cellulose nanocrystals vs. Cellulose nanofibrils: A comparative study on their microstructures and effects as polymer reinforcing agents. ACS Applied Materials & Interfaces 5 (8):2999–3009. doi:10.1021/am302624t.
- Yang, B., M. Zhang, Z. Lu, J. Tan, J. J. Luo, S. Song, X. Ding, L. Wang, P. Lu, and Q. Zhang. 2019. Comparative study of aramid nanofiber (ANF) and cellulose nanofiber (CNF). Carbohydrate polymers 208:372–81. doi:10.1016/j.carbpol.2018.12.086.