ABSTRACT
Natural fiber reinforced hybrid polymer composites have attracted many researchers’ attention compared to synthetic fiber composites due to their better mechanical properties. Besides being inexpensive, natural fibers are eco-friendly. In the literature, kenaf fiber has shown an enormous future for its suitability in technical applications. The present studies explore the mechanical properties of kenaf and kapok fiber reinforced hybrid polyester composites. The composites are prepared by simple hand lay-up technique. The test specimens were prepared according to ASTM standards and the tensile, bending, and impact strength was evaluated experimentally. The result shows that composite with equal contribution of kenaf and kapok fiber reinforcement has tensile and impact strength of 25.25 ± 4.29 MPa and 46.65 ± 0.01 KJ/m2 respectively. As the kapok fiber content increases the bending strength and bending modulus of composites decrease. The results show that the tensile and impact strength of hybrid composites has improved considerably compared to neat kapok composites. Scanning electron microscopy (SEM) was carried out to examine the fractured surfaces of tested specimens.
摘要
与合成纤维复合材料相比,天然纤维增强混杂聚合物复合材料由于其更好的机械性能而引起了许多研究人员的关注. 天然纤维不仅价格便宜,而且对环境友好. 在文献中,红麻纤维因其在技术应用中的适用性而显示出巨大的前景. 本研究探讨了红麻和木棉纤维增强混杂聚酯复合材料的力学性能. 复合材料通过简单的手工叠层技术制备. 根据ASTM标准制备试样,并通过实验评估拉伸、弯曲和冲击强度。结果表明,红麻和木棉纤维增强材料的拉伸强度和冲击强度分别为25.25 ± 4.29MPa和46.65 ± 0.01 KJ/m2. 随着木棉纤维含量的增加,复合材料的弯曲强度和弯曲模量降低. 结果表明,与纯木棉复合材料相比,混杂复合材料的拉伸和冲击强度显著提高. 进行扫描电子显微镜(SEM)检查测试样品的断裂表面。.
Introduction
Glass, carbon, and aramid fibers are commonly used materials in the automotive, aeronautical and industrial sectors. However, these synthetic fibers have severe disadvantages including the high energy required for manufacturing, non-recyclability, non-biodegradability, and health risks when inhaling (Mokhtar et al. Citation2013). Natural fibers are used as reinforcement with polymer resins to overcome these drawbacks. Natural fibers are extracted from plants, stems, seeds, bark, and leaves. Many researchers have studied the suitability of these natural fibers as reinforcing material in the polymer matrix to meet today’s industry demands (Reddy et al. Citation2021). Natural fibers are cheaper and available in ample amounts. Many research works have been carried out on the mechanical characterization of natural fiber reinforced polymer composites (Sinha, Bhattacharya, and Kumar Narang Citation2019). Since the 1990s, natural fiber composites have been in demand and emerging as realistic alternatives to conventional materials in many applications (Tiber and Ersen Balcıoğlu Citation2019). Attractive characteristics of natural fibers such as flexibility, nontoxicity, biodegradability, lightweight, and lower energy consumption during processing make them a better alternative to synthetic fibers (Rajeshkumar Citation2020a; Ravikumar, Suresh, and Rajeshkumar Citation2020). Though natural fiber reinforced composites (NFRCs) have given many benefits compared to glass fiber reinforced composites, some technical deliberations must be addressed to develop parts for high value applications, such as aerospace and automotive (Pandey et al. Citation2010). The development of natural fiber composites lead to the progress of hybrid composites whose properties can be modified by properties of matrix and reinforcements (Nagarjun, Kanchana, and Rajesh Kumar Citation2022).
Hybrid composites are considered for tailoring materials of specific properties when single reinforcement alone is not enough to satisfy the end property. The hybridization process uses two or more different reinforcing fibers in a polymer matrix to provide good mechanical and physical properties for specific engineering applications (Cavalcanti et al. Citation2020; Haneefa et al. Citation2008). Composites are commonly used in industrial applications where mechanical strength is one of the essential parameters. Compared to glass fiber composites use of natural fiber reduces the weight of the composite by 10% (Rajeshkumar Citation2020b). R. Yahaya et al. prepared kenaf – aramid reinforced epoxy hybrid composites for military vehicle’s spall liner application with kenaf fiber as woven, non-woven unidirectional, and non-woven mat. They concluded that the tensile strength of woven kenaf hybrid composite is almost 20.78% and 43.55% higher and Charpy impact strength is 19.78% and 52.07% higher than that of unidirectional and mat samples respectively (Yahaya et al. Citation2016). shows the comparison of the cost and energy required to produce glass, carbon, and natural fibers (Peças et al. Citation2018).
Table 1. Cost and energy of different fibers (Peças et al. Citation2018).
Kenaf (Hibiscus cannabinus) is a herbaceous annual plant and rises up 4–5 m in 4–5 months of the growing season (Rashdi et al. Citation2010). It is composed of cellulose, hemicellulose, lignin, and other compounds such as pectin and waxes (Mokhtar et al. Citation2013). Kapok (Ceiba pentandra) fiber is a cellulose fiber that comes from the kapok tree fruit – a tree that grows in the rainforest, in the sub and tropical zones like South America, Africa, and Asia. It can reach a height of 100 m, have a trunk of 3 m in diameter, and lives to 300 years old. Kapok fiber is eight times lighter than cotton fiber and has the lowest specific gravity among all-natural fibers. Raw kapok fibers are hydrophobic because the outer surface of fibers contains a thin layer of wax. Due to its hollowness in nature, kapok fiber has good insulating properties.
During the literature review, it was observed that no work has been reported so far on a composite prepared with a blend of hollow and waxy surface kapok fiber and long, coarse kenaf bast fiber. So, in this work kenaf and kapok fiber reinforced hybrid composites were fabricated and their mechanical properties were compared with neat kenaf and kapok fiber reinforced composite. Also, morphological studies were carried out to investigate fractured surfaces using scanning electron microscopy (SEM). The chemical composition and mechanical properties of kenaf and kapok fibers are given in respectively (Hestiawan and Kusmono Citation2018) Omrani, Menezes, and Rohatgi (Citation2016) and Purnawati et al. (Citation2018), (Sekar et al. Citation2019).
Table 2. Chemical composition of kenaf and kapok fibers (Hestiawan and Kusmono Citation2018; Omrani, Menezes, and Rohatgi Citation2016; Purnawati et al. Citation2018).
Table 3. Mechanical properties of kenaf and kapok fiber (Sekar et al. Citation2019).
Materials and method
Kenaf and kapok fibers are used as reinforcement in this experimental work. Kenaf fibers were purchased from Yavatmal district, Maharashtra, India, and kapok fiber from Mumbai, India. The matrix used is unsaturated polyester resin (GP resin) with catalyst methyl ethyl ketone peroxide (MEKP) and cobalt oxide as an accelerator. The catalyst initiates the polymerization process, and the accelerator speeds up this process. The resin, accelerator and catalyst were procured from Manish Resins & Polymers Pvt. Ltd, Mumbai, India.
Experimental details
Hand lay-up is the most cost-effective and straightforward technique used to fabricate polymer composites. A steel mold with the dimension of 250 × 250 × 3 mm (Length x width x Thickness) was used to prepare the composite sheets. The releasing agent was applied to the mold to remove composite samples easily. Thin thermoplastic polyester sheets were used at the top and bottom of the mold plate to get a good surface finish and ease of demolding. The kenaf fibers were cut to the 10 cm length and the composites were prepared with a constant 6 wt% weight fraction. The composites are named kenaf (6), and kapok (6) for neat kenaf and kapok composites. The kenaf & kapok hybrid composite are named as 5&1(90%Kenaf & 10%Kapok), 4&2(80%Kenaf & 20%Kapok), 3&3(50%Kenaf & 50%Kapok), 2&4(20%Kenaf & 80%Kapok) and 1&5 (10%Kenaf & 90%Kapok) for 6 wt% distribution. The kenaf and kapok fibers were placed layer by layer in the mold. The unsaturated polyester resin was mixed with 3% each of catalyst-MEKP and accelerator-cobalt oxide. The accelerator was added with resin in the first step to make it ready to react with the catalyst. In the second step, the required amount of catalyst was added, and stirring was done. The mixture was then poured slowly over the fibers and covered the entire sandwich with the polyester sheet. The hand roller was used for removing trapped air voids if any. The mold plate was then closed with a top plate and allowed to cure at room temperature of 28 ± 2°C for 24 h by putting a dead weight of 25 kg over it. After the curing process, the composite samples were post-cured in a hot air oven at 80°C for 5 h. A similar procedure was continued to fabricate the remaining composites.
Mechanical testing
The main objective was to determine three important mechanical properties of composite by conducting the following tests. All tests were performed at a room temperature of 28 ± 2°C. In each case, five samples were tested, and average values were tabulated.
Tensile test
The tensile test specimens were cut to dog bone shape according to ASTM D638 Type IV standard. The Tinius Olsen testing machine of 5KN capacity was used to analyze tensile strength. All the specimens were tested with a gauge length of 65 mm and 5 mm/min crosshead speed. The tensile strength was reported in MPa.
Flexural test
A flexural test was carried out through a three-point bending test using the Tinius Olsen testing machine. The bending test specimen were prepared according to ASTM D790 and tested with a crosshead speed of 5 mm/min. An 80 mm span beam freely supported the sample, and the point load was applied in the middle of the specimen.
Impact test
Impact test was carried out on the Izod impact testing machine. Impact test specimens were prepared as per the ASTM D256. It evaluates the maximum energy absorbed by the composite test specimens when a high magnitude of force was applied briefly.
Morphology analysis
The morphological characteristics of raw kenaf and kapok fiber were studied. Also, the fractured surfaces of the composite specimen subjected to tensile, flexural and impact load were observed via scanning electron microscopic machine (Model: HITACHI S-3400N). SEM instrument was used at an emission current of 58 μA and acceleration voltage of 5.0kV with a working distance of 6.2 mm. Before performing the SEM analysis, the samples were coated with gold.
Results and discussion
Morphology analysis by scanning electron microscopy (SEM)
All micrographs were taken with 500 times (500×) magnification. shows the SEM micrograph of raw kenaf (Bhambure, Rao, and Senthilkumar Citation2021) and raw kapok fiber. Kenaf fiber shows a multicellular structure with many impurities on the surface, whereas the kapok fiber micrograph shows a hollow tube-like structure reported in existing literature (Purnawati et al. Citation2018). shows an SEM micrograph for the fractured surface of kenaf fiber, kapok fiber, and hybrid composite tensile test specimen. It shows the presence of voids and failure of a matrix which indicates the brittle nature of the specimen. Kenaf fibers were broken, and kapok fibers were pulled out, lacking fiber-matrix adhesion. Kenaf fibers are very short in length, and kapok fibers are long. shows the fractured surface of kenaf fiber, kapok fiber, and hybrid composite bending test specimen. In bending SEM micrograph of kenaf fiber composite crack observed at the top side with protruded broken fibers at the bottom side with small cavities. shows very long pulled-out kenaf fibers with essentially naked surfaces, indicating easy slipping from the surrounding crosslinked matrix. shows extruded kapok fibers due to fiber pull out, which caused matrix cracking and fiber debonding. In hybrid composite SEM image shows broken kenaf fiber, fiber accumulation, and long protruded kapok fiber with matrix voids. shows kenaf fiber, kapok fiber, and hybrid composite fractured surfaces of the impact test specimens. SEM image of kenaf fiber composite shows maximum fiber breakage with fiber pull out. The multicellular structure of kenaf fiber was seen in pulled broken fiber. Kapok fiber composite SEM micrograph indicates a much smoother surface than other samples and matrix cracking due to poor bonding between fiber and matrix. SEM of hybrid composite shows long protruded kapok fibers and short-length fractured kenaf fiber with matrix rupture.
Figure 2. SEM micrograph of a fractured tensile test specimen of a) kenaf, b) kapok, and c) kenaf & kapok hybrid composite.
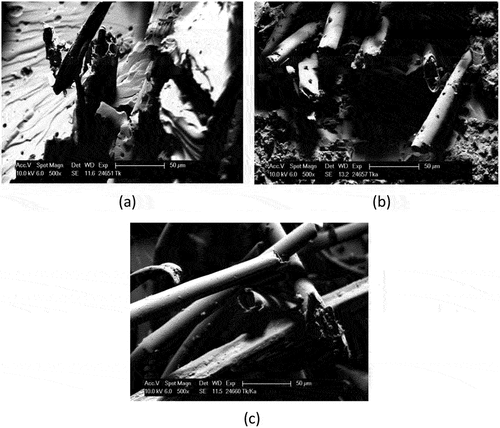
Mechanical properties of composites
Tensile test
shows the tensile strength of neat kenaf composite as 40.6 ± 2.16 MPa and neat kapok composite as 15.27 ± 1.13 MPa. The maximum tensile strength of 25.25 ± 4.29 MPa is observed in 3&3 (50% kenaf and 50% Kapok) because the load sharing of both the kenaf and kapok fibers is improved compared to other combinations. The kenaf fiber is coarse and has quite high breaking strength compared to kapok fiber which is contributing an increase in tensile strength. Kapok fiber waxy surface and hollow structure is responsible for its low strength. Hybrid composites show increase in tensile strength up to 50/50 fiber ratio and decreases further with increase in kapok content. Venkateshwaran N. et al (Venkateshwaran, Elayaperumal, and Sathiya Citation2012) and Boopalan et al (Boopalan, Niranjanaa, and Umapathy Citation2013) fabricated hybrid composites and concluded that composite with 50/50 fiber content shows maximum mechanical properties compared to all other compositions.
Bending test
The bending strength and bending modulus of neat kenaf, kapok ,and hybrid composite were evaluated. shows the bending strength and bending modulus of kenaf, kapok ,and hybrid composite specimen. Experimental results show bending strength of neat kenaf and kapok fiber reinforced composites are 54.02 ± 0.07 MPa and 12.45 ± 0.25 MPa and the bending modulus of neat kenaf and kapok fiber reinforced composites is 2251.03 ± 0.07 MPa, 161.58 ± 0.25 MPa respectively. The bending strength and bending modulus of the hybrid composite with 3&3 combination is better than the neat kapok composite. This is due to higher kenaf fiber strength and strong fiber-resin interlocking due to the coarse nature of kenaf fiber. The higher cellulose content and longer fiber properties of kenaf compared to kapok fiber result in an increase in interfacial properties of the composite, indicating good bending strength and modulus. Compared to neat kapok fiber composites hybrid composites exhibited good bending strength and bending modulus.
Impact test
For conducting impact tests, the specimen was fixed in the vice of the testing machine. When the pendulum was released, the amount of energy absorbed by the material was observed, and the impact strength was calculated. In , the neat kenaf and kapok fiber composite show impact strength of 44.95 ± 1.85 KJ/m2 and 32.97 ± 0.02 KJ/m2 respectively. Kenaf & kapok hybrid composite with equal contribution shows good impact strength of 46.65 ± 0.01 KJ/m2, which is highest among all wt% combinations. The hybridization of kenaf & kapok fiber has increased the impact strength by 29% compared to neat kapok fiber reinforced composite. This could be because of the fact that the synergistic effect of kenaf fibers along with kapok fiber produced a good shear force resistance, which was responsible for the increase in impact strength. Rana et al. (Citation2017), in their research work, mentioned that the impact strength of the hybrid composite is first increased and then decreased. This trend is followed by all mechanical properties of sisal, glass fiber reinforced epoxy composite of different composition. Similar kinds of results were found in literature with (Vinayaka et al. Citation2017). This is also reported in the existing literature that 50/50 ratio composites show better mechanical properties in most of the hybrid composites. The main reason of decreasing all the properties after 50:50 ratios is poor bonding between the reinforcement and matrix material with increase in kapok fiber content. As the kapok fibers are fragile and have waxy surface it will result in decreasing properties with increase in its content.
Conclusion
In the present study, hybrid biocomposite are prepared with kenaf bast fiber and kapok seed fiber. The mechanical properties evaluated through experimental results are compared with neat kenaf and kapok fiber-reinforced composites. Hybrid composite with 3&3 combinations showed a significant increase in tensile and impact strength by 39% and 29% respectively, compared to neat kapok fiber reinforced composite. Hybrid composite with 3&3 combinations showed 38% decrease in tensile strength 4% increase in impact strength to neat kenaf fiber composite. The SEM images of the fractured test specimens of composite show the mode of failure and damages of natural fibers and matrix during tensile, flexural, and impact testing.
HIGHLIGHTS
Prepared bio composite with neat kenaf, neat kapok and kenaf & kapok reinforced hybrid polyester composite by simple hand lay-up technique.
Hybrid composite with 50/50 ratio (in this paper 3&3) shows significant increase in tensile and impact strength.
Neat kenaf fiber reinforced composite shows better bending strength and bending modulus compared to neat kapok and all combination of hybrid composite.
Morphological analysis shows multicellular structure of kenaf fiber and hollow tube like structure of kapok fiber.
Unique of Study
As natural fibers are cheap and available in ample amount natural fiber composites have been in demand and emerging as realistic alternatives to conventional materials. In view of this kenaf fiber and kapok fiber reinforced bio composites are prepared.
Existing literature shows hybridization is one of the methods to improve the mechanical properties of natural fiber reinforced composites. But no work has been reported so far on composite prepared with a blend of seed fiber (like kapok) and plant fiber (kenaf). So, this work attempts to fabricate kenaf & kapok fiber reinforced hybrid polyester composite and evaluate its mechanical properties.
Disclosure statement
The authors have no conflicts of interest to declare.
References
- Bhambure, S. S., A. S. Rao, and T. Senthilkumar. 2021. Characterization of control and chemically modified kenaf fiber. Journal of Natural Fibers 00 (00):1–10. doi:10.1080/15440478.2021.1993500.
- Boopalan, M., M. Niranjanaa, and M. J. Umapathy. 2013. Study on the mechanical properties and thermal properties of jute and banana fiber reinforced epoxy hybrid composites. Composites Part B: Engineering 51:54–57. doi:10.1016/j.compositesb.2013.02.033.
- Cavalcanti, D. K. K., M. D. Banea, J. S. S. Neto, and R. A. A. Lima. 2020. Comparative analysis of the mechanical and thermal properties of polyester and epoxy natural fibre-reinforced hybrid composites. Journal of Composite Materials 55 (12):1683–92. doi:10.1177/0021998320976811.
- Haneefa, A., P. Bindu, I. Aravind, and S. Thomas. 2008. Studies on tensile and flexural properties of short banana/glass hybrid fiber reinforced polystyrene composites. Journal of Composite Materials 42 (15):1471–89. doi:10.1177/0021998308092194.
- Hestiawan, H., and J. Kusmono. 2018. Effect of chemical treatments on tensile properties and interfacial shear strength of unsaturated polyester/fan palm fibers. Journal of Natural Fibers 15 (5):762–75. doi:10.1080/15440478.2017.1364203.
- Mokhtar, I., M. Yazid Yahya, M. R. Abdul Kadir, and M. Faisal Kambali. 2013. Effect on mechanical performance of UHMWPE/HDPE-blend reinforced with kenaf, basalt and hybrid kenaf/basalt fiber. Polymer - Plastics Technology and Engineering 52 (11):1140–46. doi:10.1080/03602559.2013.798814.
- Nagarjun, J., J. Kanchana, and G. Rajesh Kumar. 2022. Improvement of mechanical properties of coir/epoxy composites through hybridization with sisal and palmyra palm fibers. Journal of Natural Fibers 19 (2):475–84. doi:10.1080/15440478.2020.1745126.
- Omrani, E., P. L. Menezes, and P. K. Rohatgi. 2016. State of the art on tribological behavior of polymer matrix composites reinforced with natural fibers in the green materials world. Engineering Science and Technology, an International Journal 19 (2):717–36. doi:10.1016/j.jestch.2015.10.007.
- Pandey, J. K., S. H. Ahn, C. S. Lee, A. K. Mohanty, and M. Misra. 2010. Recent advances in the application of natural fiber based composites. Macromolecular Materials and Engineering 295 (11):975–89. doi:10.1002/mame.201000095.
- Peças, P., H. Carvalho, H. Salman, and M. Leite. 2018. Natural fibre composites and their applications: A review. Journal of Composites Science 2 (4):66. doi:10.3390/jcs2040066.
- Purnawati, R., F. Febrianto, I. Nyoman, J. Wistara, S. Nikmatin, W. Hidayat, S. Hwan Lee, and N. Hun Kim. 2018. Physical and chemical properties of kapok (Ceiba pentandra) and balsa (Ochroma pyramidale) fibers. Journal of the Korean Wood Science and Technology 46 (4):393–401. doi:10.5658/WOOD.2018.46.4.393.
- Rajeshkumar, G. 2020a. A new study on tribological performance of phoenix sp. Fiber-reinforced epoxy composites. Journal of Natural Fibers 18 (12):2208–19. doi:10.1080/15440478.2020.1724235.
- Rajeshkumar, G. 2020b. Characterization of surface modified phoenix sp. Fibers for composite reinforcement. Journal of Natural Fibers 18 (12):2033–44. doi:10.1080/15440478.2019.1711284.
- Rana, R. S., A. Kumre, S. Rana, and R. Purohit. 2017. Characterization of properties of epoxy sisal/glass fiber reinforced hybrid composite. Materials Today: Proceedings 4 (4):5445–51. doi:10.1016/j.matpr.2017.05.056.
- Rashdi, A. A. A., M. Sapuan Salit, K. Abdan, and M. M. Hamdan Megat. 2010. Water absorption behaviour of kenaf reinforced unsaturated polyester composites and its influence on their mechanical properties. Pertanika Journal of Science and Technology 18 (2):433–40.
- Ravikumar, P., A. R. Suresh, and G. Rajeshkumar. 2020. An investigation into the tribological properties of bidirectional jute/carbon fiber reinforced polyester hybrid composites. Journal of Natural Fibers 00 (00):1–11. doi:10.1080/15440478.2020.1764444.
- Reddy, B. M., Y. V. Mohana Reddy, B. C. Mohan Reddy, G. Suresh Kumar, P. Venkateshwar Reddy, and H. Raghavendra Rao. 2021. A study on mechanical, structural, morphological, and thermal properties of raw and alkali treated cordia dichotoma-polyester composite. Polymer Composites 42 (1):309–19. doi:10.1002/pc.25826.
- Sekar, V., M. Hosseini Fouladi, S. Narayana Namasivayam, and S. Sivanesan. 2019. Additive manufacturing: A novel method for developing an acoustic panel made of natural fiber-reinforced composites with enhanced mechanical and acoustical properties. Journal of Engineering (United Kingdom) 2019. doi:10.1155/2019/4546863.
- Sinha, A. K., S. Bhattacharya, and H. Kumar Narang. 2019. Experimental determination and modelling of the mechanical properties of hybrid abaca-reinforced polymer composite using RSM. Polymers and Polymer Composites 27 (9):597–608. doi:10.1177/0967391119855843.
- Tiber, B., and H. Ersen Balcıoğlu. 2019. Flexural and fracture behavior of natural fiber knitted fabric reinforced composites. Polymer Composites 40 (1):217–28. doi:10.1002/pc.24635.
- Venkateshwaran, N., A. Elayaperumal, and G. K. Sathiya. 2012. Prediction of tensile properties of hybrid-natural fiber composites. Composites Part B: Engineering 43 (2):793–96. doi:10.1016/j.compositesb.2011.08.023.
- Vinayaka, D. L., V. Guna, D. Madhavi, M. Arpitha, and N. Reddy. 2017. Ricinus communis plant residues as a source for natural cellulose fibers potentially exploitable in polymer composites. Industrial Crops and Products 100:126–31. doi:10.1016/j.indcrop.2017.02.019.
- Yahaya, R., S. M. Sapuan, M. Jawaid, Z. Leman, and E. S. Zainudin. 2016. Effect of fibre orientations on the mechanical properties of kenaf–aramid hybrid composites for spall-liner application. Defence Technology 12 (1):52–58. doi:10.1016/j.dt.2015.08.005.