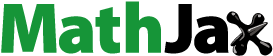
ABSTRACT
The present world faces critical issues such as global warming, sea-level rise, and drastic change in the climate pattern due to the emission of greenhouse gases. Large-scale use and disposal of hazardous plastics contribute significantly to the present scenario and it becomes essential to use naturally derived materials for making plastics. Natural fibers were found to possess the inherent characteristics required for reinforcing the polymer. In this work, one such novel cellulosic fiber derived from the bast of Leucaena leucocephala was identified and characterized using tests such as chemical, tensile, X-ray diffraction, Fourier transform infrared spectroscopy, Thermogravimetric, Differential scanning calorimetry, Energy-dispersive X-ray spectroscopy, and Field emission scanning electron microscopy. The presence of high cellulose (59.03 wt.%) with high crystallinity index (63.10%) contributes to high tensile strength(415–693 MPa) and high tensile modulus (9.90–13.10 GPa) of the Leucaena leucocephala fiber (LLF). From thermogravimetric analysis, LLF was observed to be thermally stable up to 188.20°C and activation energy of 64.22 kJ/mol. The morphological analysis of LLF revealed the existence of honeycombed porous surface characterized with serrations, and this facilitates better bonding characteristics with polymer. Lower density, mechanical properties, and better thermal stability make LLF a suitable alternate for synthetic fibers while making composites.
摘要
当今世界面临着全球变暖、海平面上升以及温室气体排放导致的气候格局剧烈变化等关键问题. 大规模使用和处置有害塑料对目前的情况有很大贡献,使用天然衍生材料制造塑料变得至关重要. 发现天然纤维具有增强聚合物所需的固有特性. 在这项工作中,通过化学、拉伸、X射线衍射、傅里叶变换红外光谱、热重分析、差示扫描量热法、能量色散X射线光谱和场发射扫描电子显微镜等测试,鉴定并表征了一种源自银合欢韧皮部的新型纤维素纤维. 具有高结晶指数(63.10%)的高纤维素(59.03重量%)的存在有助于银合欢纤维(LLF)的高拉伸强度(415-693 MPa)和高拉伸模量(9.90-13.10 GPa). 通过热重分析,观察到LLF在188.20°C时热稳定,活化能为64.22 kJ/mol. LLF的形态分析表明,存在以锯齿为特征的蜂窝状多孔表面,这有助于更好地与聚合物结合. 低密度、机械性能和更好的热稳定性使LLF在制造复合材料时成为合成纤维的合适替代品.
Introduction
Rapid depletion of fossil fuel resources and abrupt change in pollution level due to the manufacturing and disposal of conventional plastics has necessitated the use of eco-friendly materials for composite making. Natural fibers obtained from plants possess the desired characteristics such as high specific modulus, good damping properties, and better thermal stability required for reinforcing polymer matrices. Recently, the global market for natural fiber-reinforced composites has been observed to steadily increase and is estimated to reach $10.89 billion by 2024 (Li et al. Citation2020). Natural fibers find extensive application in making non-structural components for automotive, infrastructure, and sports applications (Jawaid and Abdul Khalil Citation2011). Hydrophilic character and poor thermal stability limit the extent of the application of natural fibers in the composite making. Various physical, chemical, and thermal treatments are adopted to improve the properties of natural fibers and overcome their drawbacks. The major chemical constituents of plant fibers include cellulose, hemicelluloses, lignin, pectin, wax, and other impurities. Cellulose is a semi-crystalline polymer made up of repeating units of D-anhydroglucose (C6H11O5) linked together by β-1, 4-glycosidic linkages. The presence of hydroxyl groups in each repeating unit of cellulose and their ability to bond with hydrogen makes them hydrophilic and influences their physical properties (Sjostrom Citation1993). The rigidity of natural fibers is mainly governed by the ratio of the crystalline and amorphous fraction of cellulose. When the fraction of crystalline cellulose is high, the plant fibers tend to possess high strength and more rigidity (Djafari Petroudy Citation2017). Cellulose microfibrils are embedded in matrix elements such as hemicelluloses and lignin and when a load has been applied the microfibrils orients themselves in the direction of load. The fiber fails when the matrix loses its bond with the microfibrils and hydrogen bonding in microfibrils breaks (Komuraiah, Shyam Kumar, and Durga Prasad Citation2014). The orientation of cellulose microfibrils with respect to the fiber axis has a profound influence on the type of deformation. Fibers with spiral orientation tend to exhibit ductile behavior and fibers with parallel orientation show rigid behavior (John and Thomas Citation2008). Hemicelluloses are made up of 5- and 6- carbon ring sugars in combined form, the polymeric chain of hemicelluloses extends to relatively short lengths due to a low degree of polymerization (Samanta, Mukhopadhyay, and Kumar Ghosh Citation2020). Acid residue present in hemicelluloses makes it hydrophilic and susceptible to biological degradation under the action of microbes (Patel et al. Citation2020). The amorphous form, branched structure and lower molecular weight make hemicelluloses undergo thermal decomposition earlier than cellulose and lignin (Zhou, Saini, and Kastiukas Citation2017). Lignin is a highly branched polymer with complex structures built up of phenyl propane units linked through various types of carbon-carbon and ether bonds (Thakur and Kumari Thakur Citation2014). Lignin acts as gluing material, binds up cellulose microfibrils firmly together thereby enables plants to grow the bigger size and also serves various functions such as transport of water throughout the body of the plant and enhances resistance against biological attack (Janusz et al. Citation2017). Wax consists of different types of alcohols and the presence of wax in higher quantity adversely influences the interfacial adhesion between fiber and polymer matrix. Although plant fibers can be obtained from their different parts such as leaves, fruits, flowers, and roots, the fibers extracted from stem or bast possess superior mechanical properties due to a high degree of polymerization and uniform quality (Venugopal and Kumar Boominathan Citation2020). Some of the bark fibers recently reported include Leucaena leucocephala (LL) which is a thorn less shrub or tree native to Central America and Mexico grows to a height of 7-18 m. It belongs to the family Fabaceae and genus Leucaena which comprises 50 species (Pramod, Rao, and Sundberg Citation2013). It is a long-lived tree with high nutritious value, offers multi-benefits such as firewood, timber, medicines, manure, shade, and erosion control (Díaz et al. Citation2007). This species is widely distributed in tropical and subtropical regions of the world. In India, it is commonly known as Subabul (Chaturvedi Citation1985). It grows well in well-drained soils which are moderate alkaline (pH-7.5) to slightly acidic (pH-6.0). The tree is planted in areas where soil improvement is required, as it supplies abundant nitrogen to upper soil horizons (Burleigh and Yamoah Citation1997). In this paper, an attempt has been made to investigate the physico chemical, tensile, thermal and morphological characteristics of novel cellulosic fiber obtained from the bark of the Leucaena leucocephala tree through various characterization tests such as chemical, X-ray diffraction (XRD), Fourier transform infrared spectroscopy (FTIR), Thermo gravimetric analysis (TGA), Differential Scanning Calorimetry (DSC), Energy Dispersive X-ray Spectroscopy (EDS) and Field Emission Scanning Microscopy (FESEM).The ultimate aim in Characterization of this novel fiber is to prove that it is a potential reinforcement toward making of polymer composites replacing the conventional fibers.
Materials and methods
In the present study, Leucaena leucocephala tree identified in Tirukovilur town, Villupuram district, TamilNadu, India was used for the investigation. The height and trunk diameter of the tree was found to be 7.5 m approx. and 0.15 m, respectively. The age of the tree calculated through noninvasive method was found to be approximately 35 years. The tree can be identified from their bipinnate leaves and cream colored globular-shaped flowers as shown in . The barks were collected from the upper trunk branch and were cut using a sharp-edged knife (as shown in (b)) and completely immersed in water for two weeks as shown in . During this period, microbes act upon the barks and break the chemical bonds that hold the layers of barks together (Fan and Feng Citation2016). The inner fibrous layers were separated from the outer layer of bark manually using a hand. The moist fibers were then allowed to dry under hot sunlight for a period of 24hrs (as shown in ).
Figure 1. Fiber extraction stages (a) Leucaena leucocephala tree (b) Extracted bark (c) Water retting (d) Extracted fibers.
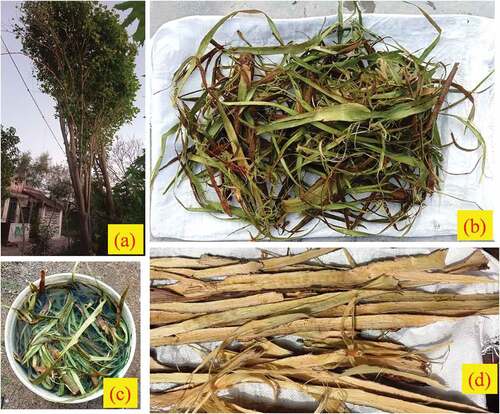
Chemical analysis
The quantity of cellulose present in Leucaena leucocephala fiber (LLF) was determined by adopting Kurschner and Hoffer method (Kurschner et al. Citation1993). Hemicellulose content in LLFs was determined as per the NFT standard 12–008 method. The lignin content in LLF was determined through APPITA P11S–78 method. The wax content in LLFs was determined using the Soxhlet extraction process developed by Conrad (Conrad Citation1944). The ash content of LLFs was determined as per ASTM E 1755–01 standard.
Density of LLFs
The density of LLFs was determined through Mettler Toledo xsz05 balance method (Gopinath, Billigraham, and Sathishkumar Citation2021).
Linear density of LLF
The fineness or linear density of LLF in terms of Tex was determined as per ASTM D1577-07(2018). Linear density represents the mass in grams of 1000 m length of fibers. Twenty fiber samples of 120 mm length were weighed using an electronic weighing balance (Model: KINGLAB) with an accuracy of 0.01 mg.
Fourier transform infrared spectroscopy (FTIR)
The functional groups present in the chemical constituents of natural fibers can be identified from the various kinds of motion such as stretching, bending, twisting, and rocking exhibited by them when exposed to infrared radiation. The FTIR spectra of LLF over the range of wavelength 4000 cm−1-500 cm−1 were generated using an FTIR spectrometer (Model: 8400 S, Shimadzu, Japan). The scanning rate and resolution were maintained at 32 scans/min and at 2 cm−1.
X-ray diffraction (XRD)
The relative fraction of crystalline cellulose and size of cellulose crystals of LLF was evaluated by examining their X-ray diffraction pattern. For this purpose, a PAN alytical X’pert Pro diffractometer with CuKα radiation source and capable of generating monochromatic X-rays of wavelength 0.1542 nm was used. The intensity of X-ray diffraction over the 2θ range between 10° and 80° and step size of 0.05° was recorded by maintaining the scan rate at 5°/min. The amount of crystalline cellulose present in the total cellulose of natural fibers is commonly referred to as crystallinity index (CI). Peak deconvolution method was adopted for evaluating the CI value of LLF. The area of crystalline peaks and total area of diffractogram was measured using Origin Pro software and the CI value is given by the ratio of area of crystalline peaks and total area of diffractogram.The crystallite size (CS) of LLFs was evaluated using Scherrer’s equation given in (1).
Where, K = 0.89 is Scherer’s constant, β is the peak’s full-width at half-maximum, and λ is the wavelength of X-rays.
Thermal analysis
The suitability of natural fibers for reinforcing polymer matrices with high processing temperature depends upon their thermal stability. The thermal degradation behaviors of natural fibers are commonly investigated through various conventional techniques such as Thermogravimetric (TG), Derivative thermogravimetric (DTG), and Differential Scanning Calorimetry (DSC). TG and DTG analyses are performed to study the change in mass and rate of change of mass with the gradual increase in temperature. TG and DSC analysis of LLF was performed using Jupiter simultaneous thermal analyzer (Model: STA 449 F3, NETZSCH, Germany) in which the fiber sample was subjected to a gradual rise of temperature from room temperature to 1000°C with the rate of heating maintained at 10°C/min. The process of heating was carried out in a nitrogen atmosphere to overcome oxidation effects and high purity nitrogen gas was continuously passed into the furnace at a flow rate of 20 mL/min.
Tensile tests on LLFs
The tensile strength offered by LLFs was determined by performing single fiber tensile test as per ASTM 3822–07 on randomly selected fiber samples of twenty numbers of fiber samples of gauge length 75 mm using INSTRON universal testing machine with 5 kN load cell. During the test, the cross head speed was maintained at 0.1 mm/min.
Surface morphology
The morphology of fiber surface was examined through high resolution scanning electron microscope images obtained using Schotty Emitter field emission scanning electron microscope (FESEM) (Model: Thermo Scientific Apreo S). The powdered fiber samples were coated with thin layer of gold so as to avoid charging effects due to electron beam. During the course of examination, accelerating voltage of 30 kV was maintained.
Energy-dispersive X-ray spectroscopy (EDS)
EDS analysis enables the identification of various types of elements present on the fiber surface, by using a high-energy electromagnetic spectrum. Energy dispersive spectrometer (EDS) analyzer (BRUKER (German), Model: Nano X flash detector with the magnification of 1000× was used for performing analysis on LLF. The accelerating voltage and working distance maintained during the examination were 20.0 kV and 11.6 mm.
Results and discussion
Chemical analysis
The chemical composition of LLF and other natural fibers are provided in . Cellulose content (59.03 wt.%) in LLF was found to be comparatively higher than that present in other natural fibers such as piassava (28 wt.%), kudzu (33 wt.%), Carica papaya (38.71 wt.%), Cocos nucifera (43 wt.%), Althae officinalis (44.6 wt.%), Parthenium hysterophorus (51.5 wt.%) and Ferula communis (53.3 wt.%) (Sudhir Chakravarthy et al. Citation2020). The presence of higher cellulose indicates the higher strength and stability of fibers which is a favorable property for reinforcement with polymers. The quantity of hemicellulose (36.02 wt.%) present in LLF is higher than that present in fibers such as jute (12 wt.%), ramie (13.1 wt.%), flax (16.7 wt.%), hemp (17.9 wt.%), banana (19 wt.%), and kenaf (33.9 wt.%) (Jawaid and Abdul Khalil Citation2011). Presence of high fraction of hemicellulose indicates higher moisture absorption, greater microbial attack, and lower thermal stability in LLF (Karimah et al. Citation2021). However, before reinforcing with polymer matrices, LLF should be subjected to chemical modification to make them hydrophobic and during this process, the amorphous constituent such as hemicellulose is removed completely which in turn can be reinforced with polymers. Higher lignin content (17.37 wt. %) in LLF contributes to the structural properties such as high rigidity and stiffness of fibers which are very favorable for reinforcement with polymers when compared to other bark fibers such as ramie (1 wt. %), flax (3 wt.%), hemp (4 wt. %), kenaf (8.18 wt. %) and jute (13 wt. %) (Saravanakumar et al. Citation2014). The wax content (1.00 wt.%) in LLF is higher than that present in other bark fibers such as ramie (0.3 wt.%), Jute (0.7 wt.%), and hemp (0.8 wt.%) and the higher wax presence adversely affects the interfacial adhesion between the fiber and the polymer matrix (Indran and Edwin Raj Citation2015). The moisture content (6.60 wt.%) in LLF is comparatively lower than that present in fibers such as Cissus quadrangularis root (7.3 wt.%), Coccinia grandis stem (9.14 wt.%), Albizia samara (9.34 wt.%), and Kigelia Africana (10.12 wt.%) (Siva et al. Citation2020) and this improves the bonding strength between fiber and matrix of LLF reinforced polymer composites.
Table 1. Fiber classification, chemical compositions and density of raw LLFs and various natural fibers.
Fineness and density of LLFs
The average linear density of LLF evaluated using the results of 20 fiber samples was found to be 22.4 Tex with CV as 7.95%.The density of LLF was found to be 1470 kg/m3 and it is found to be comparatively lower than natural fibers such as flax (1500 kg/m3), ramie (1500 kg/m3) and jute (1510 kg/m3) respectively (Arthanarieswaran, Kumaravel, and Saravanakumar Citation2015). The presence of honeycombed porous cells could be the possible reason for the lower density of LLF.
Fourier transform infrared spectroscopy (FTIR)
The FTIR spectrum of LLF is provided in . The broad band at 3281 cm−1 corresponds to stretching vibration of hydroxyl groups which are present in cellulose, hemicelluloses, polysaccharides and monosaccharide molecules (Cheng et al. Citation2020). The band at 2874 cm−1 indicates the symmetrical stretching vibration of CH bonds present in cellulose and hemicelluloses (Shaker et al. Citation2020). The sharp peak at 1630 cm−1 is attributed to CO stretching of lignin (Jayaramudu, Guduri, and Varada Rajulu Citation2010). The minor peak at 1524 cm−1 corresponds to C=C groups of lignin (Belouadah et al. Citation2021). The peak at 1360 cm−1 is mainly due to CH2 symmetric bending vibration (Sreenivasan et al. Citation2011). The peak at 1244 cm−1 is attributed to C-O stretching vibration of the acetyl group in lignin (Bezazi et al. Citation2014). The band at 1017 cm−1 represents C-OH stretching vibration of cellulose. The minor peak at 847 cm−1 indicates the presence of β-glycosidic linkages existing between monosaccharides (Maache et al. Citation2017). The sharp peak at 687 cm−1 represents C-OH out of plane bending motion (Liu and Kim Citation2017).
X-ray diffraction analysis (XRD)
The X-ray diffractogram of LLF is shown in . In the diffractogram, four distinct crystalline peaks at 2θ = 15.29°, 23.00°, 24.57°, and 38.52° were observed. The peaks at 2θ = 15.29° and 2θ = 23.00° attributed to crystallographic planes (110) and (002) of cellulose I crystals with monoclinic structure. Existence of peaks at 24.57° and 38.52°Confirms the existence of amorphous regions in cellulose (Spinacé et al. Citation2009). The strength and stiffness of natural fibers are mainly governed by the fraction of crystalline cellulose present in them (Djafari Petroudy Citation2017). The ratio of crystalline cellulose and total cellulose content is known as crystallinity index (CI). Natural fibers with high CI value exhibit superior mechanical properties and better thermal stability (Poletto, Ornaghi, and Zattera Citation2014). This is mainly attributed to the presence of long-range, ordered cross-linked molecular structure in crystalline cellulose. The crystallinity index (CI) of LLF was determined using the peak deconvolution method in which CI is defined as the ratio of the area of crystalline peaks and total area of crystalline and amorphous peaks. The value of CI thus obtained was found to be 63.10%. The crystallite size of LLF determined using Scherrer’s EquationEquation (1)(1)
(1) was found to be 2.33 nm. Crystallinity index and Crystal size of raw LLFs and various natural fibers are provided in .The crystallite size of some of the bast fibers includes Ferula communis (1.6 nm), Markhamia lutea (2.07 nm), Althaea officinalis (2.4 nm) and flax (2.8 nm), (Sarikanat et al. Citation2014; Seki et al. Citation2013). Higher crystallite size enables reduced chemical reactivity and lower absorption in natural fibers (Gopinath, Billigraham, and Sathishkumar Citation2021).
Table 2. Crystallinity index and crystal size of raw LLFs and various natural fibers.
Thermal properties of LLFs
Thermal degradation behavior of LLF was studied through thermogravimetric and differential scanning calorimetry tests. Thermogravimetric (TG) and Derivative Thermogravimetric (DTG) curves of LLF are shown in . It can be inferred from the TG curve that thermal degradation of LLF occurs in three different stages. Initially, the fiber sample suffers a mass loss of 6.62% within the temperature 28.38°C and 130.25°C of TG curve which is attributed to the loss of moisture through evaporation, and this fact is also confirmed from the peak in DTG curve at 93.04°C. The mild sloped region prevailing within 130.25°C to 188.20°C of TG curve represents the thermally stable region wherein the sample suffers a minimal mass loss of 2.96%. During the first stage of thermal degradation, thermal depolymerization of hemicellulose occurs and for LLF sample, it occurs within the temperature range 188.20°C and 285.80°C of TG curve accompanied with a mass loss of 40.78% and this is evident from the peak in DTG curve at 224.19°C. In the second stage, the thermal degradation of cellulose was observed to occur within the temperature range between 285.80°C and 341.31°C of TG curve and it is associated with a mass loss of 19.95%. The peak in DTG curve at 312.64°C corresponds to cellulose degradation. The presence of cross-linked aromatic rings and charring ability makes lignin more thermally stable than the other constituents of fiber. The thermal degradation of lignin forms the third stage and for LLF, it was observed to occur within temperature 341.31°C and 632.89°C of TG curve and the peak at 494.42°C in DTG curve confirms the lignin degradation. The presence of a broad exothermic peak in DSC curve was observed in within temperatures 379.84°C and 661.54°C and with a peak at 523.09°C corresponds to thermal degradation of lignin which occurs over a wide range of temperature. The thermal stability of LLF can be quantified by assessing its activation energy which represents the amount of energy required to thermally decompose one mole of the fiber sample. Broido’s empirical EquationEquation (2)(2)
(2) was used to determine the activation energy of LLF. The procedure involves finding out the slope of ln(ln(1/y) vs. 1/T plot (shown in ) and substituting it in EquationEquation (2)
(2)
(2) . The activation energy of LLF thus determined was found to be 64.22 kJ/mol. The activation energy of natural fibers used for reinforcing polymer composites lies mostly within the range of 60-120 kJ/mol.
where R = 8.32 J/mol K denotes the universal gas constant, T represents the temperature in Kelvin, y denotes the fraction of initial molecules which remains stable without suffering thermal decomposition (wt/wo), wt represents the weight of the fiber sample remaining at any time t, and wo represents the initial weight of the fiber sample taken.
Tensile properties
The single fiber stress vs. strain curves of five LLF samples among the 25 samples tested are shown in . The maximum resistance offered by the single fiber against the tensile load is noted down from the stress vs. strain plot and this value represents the tensile strength of the fiber sample. The tensile strength of LLF thus determined was found to be 415–693 MPa with strain as 4.33–5.51%. It is worth noting the tensile strength of some of the natural fibers such as Acacia leucophloea, Albizia saman, Prosopis juliflora, Sida cordifolia, and Sida rhombifolia are 317–1608 MPa, 381–1092 MPa, 558 MPa, 703.95 ± 23.73 MPa, and 673 ± 14 MPa, respectively (Gopinath, Billigraham, and Sathishkumar Citation2021). The tensile modulus of the fiber sample was obtained by determining the slope of the linear portion of the stress-strain plot. The tensile modulus of LLF thus determined was found to be 9.90–13.10 GPa. Another parameter that significantly influences the mechanical properties of fiber is the angle at which the microfibrils are wound with respect to the fiber axis which is otherwise termed as Microfibrillar angle. Higher the microfibrillar angle, the fiber tends to exhibit high ductility and fibers with lower microfibrillar angle tend to possess high strength. The microfibrillar angle of LLF determined using the global deformation EquationEquation (3)(3)
(3) was found to be 16.74°-18.85°. Mechanical properties of raw LLFs and various natural fibers are provided in .
Table 3. Mechanical properties of raw LLFs and various natural fibers.
Morphological analysis of LLFs
The morphology of LLFs surfaces obtained using high-resolution FESEM at different magnifications are provided in . The FESEM micrographs of LLF revealed the presence of rough surfaces characterized with serrations and minor cracks. Honeycomb-shaped porous cells are clearly visible in the micrograph provided in . The existence of rough surface and porous channels enables better wettability and bonding characteristics with polymer matrix.
Energy-dispersive X-ray spectroscopy (EDS)
The EDS spectrum showing the distribution of various elements present on the surface of LLF shown in . The elements present on the fiber surface in terms of atomic and weight percentage are summarized in . The spectrum reveals the existence of high-intensity peaks of carbon and oxygen which are mainly due to the fact that cellulose is primarily built up of these elements. The carbon and oxygen peaks were observed at 0.25 and 0.55 keV. The presence of non-cellulosic components such as hemicellulose (36.02 wt.%) and lignin (17.37 wt. %) in higher fractions could be confirmed from the relatively higher fraction of carbon (61.65 at.%) compared to oxygen (35.87 at.%) respectively. The other elements such as calcium and potassium which have visible peaks represent the amorphous constituents of fiber such as wax, lignin, and other impurities.
Table 4. Comparison of various elements scattered on the surface of LLF with other natural fibers (Manimaran et al. Citation2018).
Conclusion
In this study, the physical, chemical, mechanical, and thermal properties of cellulosic fiber extracted from LL were investigated through various characterization tests. From the test results, the fiber was found to possess high cellulose content (59.03 wt.%) and high amorphous constituents such as hemicelluloses (36.02 wt.%) and lignin (17.37 wt. %). Hydrophilicity, low thermal stability, and poor resistance to biological attack due to the presence of high hemicelluloses can be overcome by eliminating them through chemical modifications adopted for enhancing the adhesion between fiber and fiber and make them hydrophobic. The higher crystallinity index (63.10%) contributes to the high tensile strength (415–693 MPa) and high tensile modulus (9.90–13.10 GPa) of LLF. In addition to strength, LLF was found to offer high ductility which is confirmed from its high microfibrillar angle (16.74°-18.85°). Lower density and better thermal stability validate that LLF as a promising reinforcement with matrix in making of polymer composites for various non-structural applications such as partition boards in buildings, interior body panels in automobiles, and for making sports goods. In future, with appropriate chemical treatments the amorphous compounds found on surface of LLF can be completely removed and can be further characterized toward making of effective polymer composite reinforcements.
Highlights
Higher cellulose content (59.03 wt. %).
The average linear density of LLF found to be 22.4 Tex with CV as 7.95%.
Crystallinity index (CI) of 63.10% determined using the peak deconvolution method.
Microfibrillar angle of 16.74°-18.85° exhibits high ductility of LLF.
EDX reveals existence of high-intensity peaks of carbon and oxygen.
Disclosure statement
No potential conflict of interest was reported by the author(s).
References
- Arthanarieswaran, V. P., A. Kumaravel, and S. S. Saravanakumar. 2015. Characterization of new natural cellulosic fiber from acacia leucophloea bark. International Journal of Polymer Analysis and Characterization 20 (4):367–16. Taylor & Francis. doi:10.1080/1023666X.2015.1018737.
- Azeez, T. O., D. O. Okechukwu Onukwuli, J. T. Tagbo Nwabanne, and A. T. Tamunonengiofori Banigo. 2020. Cissus populnea fiber - unsaturated polyester composites: Mechanical properties and interfacial adhesion. Journal of Natural Fibers 17 (9):1281–94. Taylor & Francis. doi:10.1080/15440478.2018.1558159.
- Baskaran, P. G., M. Kathiresan, P. Senthamaraikannan, and S. S. Saravanakumar. 2018. Characterization of new natural cellulosic fiber from the bark of dichrostachys cinerea. Journal of Natural Fibers 15 (1):62–68. Taylor & Francis. doi:10.1080/15440478.2017.1304314.
- Belouadah, Z., L. Toubal, N. Belhaneche-Bensemra, and A. Ati. 2021. Characterization of ligno-cellulosic fiber extracted from atriplex Halimus L. plant. International Journal of Biological Macromolecules 168 (January):806–15. doi:10.1016/j.ijbiomac.2020.11.142.
- Bezazi, A., A. Belaadi, M. Bourchak, F. Scarpa, and K. Boba. 2014. Novel extraction techniques, chemical and mechanical characterisation of agave Americana L. natural fibres. Composites Part B: Engineering 66 (November):194–203. doi:10.1016/j.compositesb.2014.05.014.
- Burleigh, J. R., and C. F. Yamoah. 1997. Site factors associated with the performance of Leucaena Leucocephala (Lam.) de wit and Sesbania Sesban (L.) merill in pure and mixed stands in the northern highlands of Rwanda. Agroforestry Systems 37 (2):121–31. doi:10.1023/A:1005861821739.
- Chaturvedi, A. N. 1985. Biomass production on Saline-Alkalinesoils. Nitrogen Fixing Tree Research Reports 3:7–8.
- Cheng, D., B. Weng, Y. Chen, S. Zhai, C. Wang, R. Xu, J. Guo, Y. Lv, L. Shi, and Y. Guo. 2020. Characterization of potential cellulose fiber from Luffa Vine: A study on physicochemical and structural properties. International Journal of Biological Macromolecules 164 (December):2247–57. doi:10.1016/j.ijbiomac.2020.08.098.
- Conrad, C. M. 1944, May 1. Determination of wax in cotton fiber a new alcohol extraction method. Research-Article American Chemical Society World. doi:10.1021/i560136a007.
- Díaz, M. J., M. M. García, M. E. Eugenio, R. Tapias, M. Fernández, and F. López. 2007. Variations in fiber length and some pulp chemical properties of Leucaena varieties. Industrial Crops and Products 26 (2):142–50. doi:10.1016/j.indcrop.2007.02.003.
- Djafari Petroudy, S. R. 2017. Physical and mechanical properties of natural fibers. In Advanced high strength natural fibre composites in construction, ed. M. Fan and F. Fu, 59–83. Woodhead Publishing. doi:10.1016/B978-0-08-100411-1.00003-0.
- Fan, M., and F. Feng. 2016. Advanced high strength natural fibre composites in construction. Woodhead Publishing.
- Gopinath, R., P. Billigraham, and T. P. Sathishkumar. 2021. Investigation of physico-chemical, mechanical, and thermal properties of new cellulosic bast fiber extracted from the bark of Bauhinia Purpurea. Journal of Natural Fibers 0 (0):1–18. Taylor & Francis. doi:10.1080/15440478.2021.1990180.
- Gopinath, R., K. Ganesan, S. S. Saravanakumar, and R. Poopathi. 2016. Characterization of new cellulosic fiber from the stem of Sida Rhombifolia. International Journal of Polymer Analysis and Characterization 21 (2):123–29. Taylor & Francis. doi:10.1080/1023666X.2016.1117712.
- Hamideh, H., M. Sain, and L. H. Mei. 2014. Modification and characterization of Hemp and Sisal fibers. Journal of Natural Fibers 11 (2):144–68. Taylor & Francis. doi:10.1080/15440478.2013.861779.
- Indran, S., and R. Edwin Raj. 2015. Characterization of new natural cellulosic fiber from Cissus Quadrangularis stem. Carbohydrate Polymers 117 (March):392–99. doi:10.1016/j.carbpol.2014.09.072.
- Ishak, M. R., Z. Leman, S. M. Sapuan, A. M. M. Edeerozey, and I. S. Othman. 2010, May. Mechanical properties of Kenaf Bast and Core Fibre reinforced unsaturated polyester composites. IOP Conference Series: Materials Science and Engineering, 11, 012006. IOP Publishing. doi:10.1088/1757-899X/11/1/012006.
- Janusz, G., A. Pawlik, J. Sulej, U. Świderska-Burek, A. Jarosz-Wilkołazka, and A. Paszczyński. 2017. Lignin degradation: Microorganisms, enzymes involved, genomes analysis and evolution. FEMS Microbiology Reviews 41 (6):941–62. doi:10.1093/femsre/fux049.
- Jawaid, M., and H. P. S. Abdul Khalil. 2011. Cellulosic/Synthetic fibre reinforced polymer hybrid composites: A Review. Carbohydrate Polymers 86 (1):1–18. doi:10.1016/j.carbpol.2011.04.043.
- Jayaramudu, J., B. R. Guduri, and A. Varada Rajulu. 2010. Characterization of new natural cellulosic fabric Grewia Tilifolia. Carbohydrate Polymers 79 (4):847–51. doi:10.1016/j.carbpol.2009.10.046.
- John, M. J., and S. Thomas. 2008. Biofibres and Biocomposites. Carbohydrate Polymers 71 (3):343–64. doi:10.1016/j.carbpol.2007.05.040.
- Karimah, A., M. R. Rasyidur Ridho, S. S. Sofyan Munawar, D. S. Sudarwoko Adi, I. Ismadi, R. Damayanti, B. Subiyanto, W. Fatriasari, and A. Fudholi. 2021. A review on natural fibers for development of eco-friendly bio-composite: characteristics, and utilizations. Journal of Materials Research and Technology 13 (July):2442–58. doi:10.1016/j.jmrt.2021.06.014.
- Khan, A., V. Vijay Raghunathan, D. L. Singaravelu, M. R. Sanjay, S. Siengchin, M. Jawaid, K. A. Alamry, and A. M. Asiri. 2020, August. Extraction and characterization of cellulose fibers from the stem of Momordica Charantia. Journal of Natural Fibers 19(6):1–11. doi: 10.1080/15440478.2020.1807442.
- Komuraiah, A., N. Shyam Kumar, and B. Durga Prasad. 2014. Chemical composition of natural fibers and its influence on their mechanical properties. Mechanics of Composite Materials 50 (3):359–76. doi:10.1007/s11029-014-9422-2.
- Kumar, R., N. Rajesh Jesudoss Hynes, P. Senthamaraikannan, S. Saravanakumar, and M. R. Sanjay. 2018. Physicochemical and thermal properties of Ceiba Pentandra bark fiber. Journal of Natural Fibers 15 (6):822–29. doi:10.1080/15440478.2017.1369208.
- Kumar, R., S. Sivaganesan, P. Senthamaraikannan, S. S. Saravanakumar, A. Khan, S. Ajith Arul Daniel, and L. Loganathan. 2020, March. Characterization of new cellulosic fiber from the bark of Acacia Nilotica L. plant. Journal of Natural Fibers 19(1):1–10. doi: 10.1080/15440478.2020.1738305.
- Kurschner, K., A. Hoffer, S. H. Jenkins, W. Vieweg, O. Schwarzkopf, W. Schramek, C. Schubert, H. Velten, K. Hess, C. Trogus, et al. 1993. Cellulose and cellulose derivative. Zeitschrift für Analytische Chemie 92 (3–4):145–54. doi:10.1007/BF01354736.
- Li, M., Y. Pu, V. M. Thomas, C. G. Geun Yoo, S. Ozcan, Y. Deng, K. Nelson, and A. J. Ragauskas. 2020. Recent advancements of plant-based natural fiber–reinforced composites and their applications. Composites Part B: Engineering 200 (November):108254. doi:10.1016/j.compositesb.2020.108254.
- Li, X., L. G. Tabil, and S. Panigrahi. 2007. Chemical treatments of natural fiber for use in natural fiber-reinforced composites: A review. Journal of Polymers and the Environment 15 (1):25–33. doi:10.1007/s10924-006-0042-3.
- Liu, Y., and H. -J. Kim. 2017. Fourier transform infrared spectroscopy (FT-IR) and simple algorithm analysis for rapid and non-destructive assessment of developmental cotton fibers. Sensors 17 (7):7. Multidisciplinary Digital Publishing Institute: 1469. doi:10.3390/s17071469.
- Maache, M., A. Bezazi, S. Amroune, F. Scarpa, and A. Dufresne. 2017. Characterization of a novel natural cellulosic fiber from Juncus Effusus L. Carbohydrate Polymers 171 (September):163–72. doi:10.1016/j.carbpol.2017.04.096.
- Manimaran, S. P. S., and M. Prithiviraj. 2019, June. Investigation of physico chemical properties and characterization of new natural cellulosic fibers from the bark of Ficus Racemosa. Journal of Natural Fibers 18(2):1–11. doi: 10.1080/15440478.2019.1621233.
- Manimaran, P., M. R. Sanjay, P. Senthamaraikannan, S. S. Saravanakumar, S. Siengchin, G. Pitchayyapillai, and A. Khan. 2019. Physico-chemical properties of fiber extracted from the flower of Celosia Argentea plant. Journal of Natural Fibers 18 (3):464–73. Taylor & Francis. doi:10.1080/15440478.2019.1629149.
- Manimaran, P., M. R. Sanjay, P. Senthamaraikannan, B. Yogesha, C. Barile, and S. Siengchin. 2020. A new study on characterization of Pithecellobium Dulce fiber as composite reinforcement for light-weight applications. Journal of Natural Fibers 17 (3):359–70. Taylor & Francis. doi:10.1080/15440478.2018.1492491.
- Manimaran, M. P., S. S. Saravanakumar, V. P. Arthanarieswaran, and P. Senthamaraikannan. 2018. Physicochemical, tensile, and thermal characterization of new natural cellulosic fibers from the stems of Sida Cordifolia. Journal of Natural Fibers 15 (6):860–69. doi:10.1080/15440478.2017.1376301.
- Manimaran, P., K. Solai Senthil Kumar, and M. Prithiviraj. 2019, November. Investigation of physico chemical, mechanical and thermal properties of the Albizia Lebbeck bark fibers. Journal of Natural Fibers 18(8):1–12. doi: 10.1080/15440478.2019.1687068.
- Mayandi, K., N. Rajini, P. Pitchipoo, J. T. Winowlin Jappes, and A. Varada Rajulu. 2016. Extraction and characterization of new natural Lignocellulosic Fiber Cyperus Pangorei. International Journal of Polymer Analysis and Characterization 21 (2):175–83. doi:10.1080/1023666X.2016.1132064.
- Patel, U., R. Ray, A. Mohapatra, S. N. Narayan Das, and H. C. Chandra Das. 2020. Effect of different chemical treatments on surface morphology, thermal and tensile strength of Bauhinia Vahlii (BV) stem fibers. Journal of Natural Fibers 19 (1):1–12. Taylor & Francis. doi:10.1080/15440478.2020.1739591.
- Poletto, M., H. L. Ornaghi, and A. J. Zattera. 2014. Native cellulose: Structure, characterization and thermal properties. Materials 7 (9):6105–19. Multidisciplinary Digital Publishing Institute. doi:10.3390/ma7096105.
- Pramod, S., K. S. Rao, and A. Sundberg. 2013. Structural, histochemical and chemical characterization of normal, tension and opposite wood of Subabul (Leucaena Leucocephala (Lam.) De Wit.). Wood Science and Technology 47 (4):777–96. doi:10.1007/s00226-013-0528-9.
- Raghavendra, G., S. A. Shakuntala Ojha, S. K. Acharya, and S. K. Pal. 2014. Jute fiber reinforced epoxy composites and comparison with the Glass and Neat Epoxy composites. Journal of Composite Materials 48 (20):2537–47. SAGE Publications Ltd STM. doi:10.1177/0021998313499955.
- Samanta, A. K., A. Mukhopadhyay, and S. Kumar Ghosh. 2020. 2 - processing of jute fibres and its applications. In Handbook of natural fibres, 2nd ed. R. M. Kozłowski and M. Mackiewicz-Talarczyk, 49–120. The Textile Institute Book Series. Woodhead Publishing. doi: 10.1016/B978-0-12-818782-1.00002-X.
- Sanjay, M. R., G. R. Arpitha, and B. Yogesha. 2015. Study on mechanical properties of natural - glass fibre reinforced polymer hybrid composites: A review. Materials Today: Proceedings 2 (4):2959–67. doi:10.1016/j.matpr.2015.07.264.
- Saravana Kumaar, A., A. Senthilkumar, T. Sornakumar, S. S. Saravanakumar, and V. P. Arthanariesewaran. 2019. Physicochemical properties of new cellulosic fiber extracted from Carica Papaya Bark. Journal of Natural Fibers 16 (2):175–84. doi:10.1080/15440478.2017.1410514.
- Saravanakumar, S. S., A. Kumaravel, T. Nagarajan, and I. Ganesh Moorthy. 2014. Investigation of physico-chemical properties of Alkali-treated Prosopis Juliflora fibers. International Journal of Polymer Analysis and Characterization 19 (4):309–17. Taylor & Francis. doi:10.1080/1023666X.2014.902527.
- Saravanakumar, S. S., A. Kumaravel, T. Nagarajan, P. Sudhakar, and R. Baskaran. 2013. Characterization of a novel natural cellulosic fiber from Prosopis Juliflora Bark. Carbohydrate polymers 92 (2):1928–33. doi:10.1016/j.carbpol.2012.11.064.
- Sarikanat, M., Y. Seki, K. Sever, and C. Durmuşkahya. 2014. Determination of properties of Althaea Officinalis L. (Marshmallow) fibres as a potential plant fibre in polymeric composite materials. Composites Part B: Engineering 57 (February):180–86. doi:10.1016/j.compositesb.2013.09.041.
- Seki, Y., M. Sarikanat, K. Sever, and C. Durmuşkahya. 2013. Extraction and properties of Ferula Communis (Chakshir) fibers as novel reinforcement for composites materials. Composites Part B: Engineering 44 (1):517–23. doi:10.1016/j.compositesb.2012.03.013.
- Senthamaraikannan, P., S. S. Saravanakumar, V. P. Arthanarieswaran, and P. Sugumaran. 2016. Physico-chemical properties of new cellulosic fibers from the bark of Acacia Planifrons. International Journal of Polymer Analysis and Characterization 21 (3):207–13. doi:10.1080/1023666X.2016.1133138.
- Shaker, K., R. M. Muhammad Waseem Ullah Khan, M. Jabbar, M. Umair, A. Tariq, M. Kashif, and Y. Nawab. 2020. Extraction and characterization of novel fibers from Vernonia Elaeagnifolia as a potential textile fiber. Industrial Crops and Products 152 (September):112518. doi:10.1016/j.indcrop.2020.112518.
- Siva, R., T. N. Valarmathi, K. Palanikumar, and A. V. Samrot. 2020. Study on a novel natural cellulosic fiber from Kigelia Africana Fruit: Characterization and analysis. Carbohydrate polymers 244 (September):116494. doi:10.1016/j.carbpol.2020.116494.
- Sjostrom, E. 1993. Wood chemistry: Fundamentals and applications. Gulf Professional Publishing.
- Spinacé, M. A. S., C. S. Lambert, K. K. G. Fermoselli, and M. -A. De Paoli. 2009. Characterization of Lignocellulosic Curaua Fibres. Carbohydrate Polymers 77 (1):47–53. doi:10.1016/j.carbpol.2008.12.005.
- Sreenivasan, V. S., S. Somasundaram, D. Ravindran, V. Manikandan, and R. Narayanasamy. 2011. Microstructural, physico-chemical and mechanical characterisation of Sansevieria cylindrica fibres – an exploratory investigation. Materials & Design 32 (1):453–61. doi:10.1016/j.matdes.2010.06.004.
- Sudhir Chakravarthy, S. C., M. S, J. Siva Naga Raju, and J. S. Md. 2020. Characterization of novel natural cellulosic fiber extracted from the stem of Cissus Vitiginea Plant. International Journal of Biological Macromolecules 161 (October):1358–70. doi:10.1016/j.ijbiomac.2020.07.230.
- Thakur, V. K., and M. K. Kumari Thakur. 2014. Processing and characterization of natural cellulose fibers/thermoset polymer composites. Carbohydrate Polymers 109 (August):102–17. doi:10.1016/j.carbpol.2014.03.039.
- Venkatachalam, N., P. Navaneethakrishnan, and T. Sathishkumar. 2016, December. Characterization of novel Passiflora Foetida natural fibers for paper board industry. Journal of Industrial Textiles 152808371668292. doi:10.1177/1528083716682923.
- Venugopal, A., and S. Kumar Boominathan. 2020. Physico-chemical, thermal and tensile properties of Alkali-Treated Acacia Concinna fiber. Journal of Natural Fibers 0 (0):1–16. Taylor & Francis. doi:10.1080/15440478.2020.1838998.
- Vignesh, V., A. N. Balaji, and M. K. V. Karthikeyan. 2016. Extraction and characterization of new cellulosic fibers from Indian mallow stem: An exploratory investigation. International Journal of Polymer Analysis and Characterization 21 (6):504–12. doi:10.1080/1023666X.2016.1175206.
- Vinod, A., R. Vijay, D. Lenin Singaravelu, M. R. Sanjay, S. Suchart Siengchin, Y. Yagnaraj, and S. Khan. 2019, September. Extraction and characterization of natural fiber from stem of Cardiospermum Halicababum. Journal of Natural Fibers 18(6):1–11. doi: 10.1080/15440478.2019.1669514.
- Yoganandam, K., P. Ganeshan, B. NagarajaGanesh, and K. Raja. 2020. Characterization studies on Calotropis Procera fibers and their performance as reinforcements in epoxy matrix. Journal of Natural Fibers 17 (12):1706–18. Taylor & Francis. doi:10.1080/15440478.2019.1588831.
- Zhou, X., H. Saini, and G. Kastiukas. 2017. Engineering properties of treated natural hemp fiber-reinforced concrete. Frontiers in Built Environment 3:33. doi:10.3389/fbuil.2017.00033.