ABSTRACT
Biodegradable film-based packaging is a current concern to replace packaging that depends on petroleum. This is because petroleum-based packaging is very unfriendly to the environment. The bioresource-based biodegradable film has the disadvantage that its mechanical properties are still low, that it requires two or three bioresource materials to be used as polymer hybrids. As a film hybrid polymer that has superior properties such as flexibility, strength, heat resistance, and environmental resistance, it can be applied to various packaging materials and can be developed for various purposes. In this review, the authors review biomass sources as a matrix, as a filler in hybrid polymer-based packaging, the properties of the biodegradable file, and the development for the future. In addition to the raw materials as matrices and fillers, the synthesis method is also described. The properties of biodegradable hybrid polymer film include physicochemical, mechanical, and thermal. This review also summarizes the emerging aspects of bioresources for the development of sustainable and biodegradable hybrid polymer film friendly to the environment.
摘 要
可生物降解薄膜包装是替代依赖石油的包装的当前关注点. 这是因为石油包装对环境非常不友好. 基于生物源的生物降解膜的缺点是其机械性能仍然较低,需要两种或三种生物源材料用作聚合物混合物. 作为一种具有优异性能如柔韧性、强度、耐热性和耐环境性)的薄膜混合聚合物,它可应用于各种包装材料,并可用于各种用途. 在这篇综述中,作者回顾了生物质源作为基质,作为混合聚合物包装中的填料,生物可降解文件的特性,以及未来的发展. 除了作为基质和填料的原料外,还描述了合成方法. 生物可降解杂化聚合物膜的性质包括物理化学、机械和热. 该综述还总结了生物资源在开发对环境友好的可持续和可生物降解的混合聚合物膜方面的新兴方面.
Introduction
In the last decade, non-degradable polymer materials have been widely used, increasing the utilization rate. The non-biodegradable polymers have been used mostly as packaging materials because of their good physical and mechanical properties such as tensile strength and elongation, water and gas barrier, also heat and UV resistance (Siracusa et al. Citation2008). However, the use of these polymers as materials packaging has been limited recently, mostly because they are produced from nonrenewable petroleum, low biodegradability, and non-totally recyclable (Siracusa et al. Citation2008). These packaging materials have caused many ecological and environmental problems, often contaminated by foodstuffs and biological substances, increasing waste disposal in nature (Avérous and Pollet Citation2012; Robertson Citation2004).
Biodegradable (hybrid) polymers are one alternative solution to substitute non-degradable wastes and limit their detrimental impact on the environment. Biodegradable hybrid polymers are a combination of bio-based polymer matrices and fillers used as reinforcing agents in a polymer matrix to enhance the packaging properties. Then, combinations lead to desirable properties that allow the product to compete with the existing petroleum-based polymers. Hybrid leads to new material that can exhibit new properties that cannot be found in individual components and the mixture of two materials as a composite. The materials of the polymeric matrices and the fillers for the hybrid polymer films are classified into natural and synthetic. The natural materials of biopolymer typically come from agricultural wastes and living organisms, while the synthetic materials biopolymer is from nonrenewable sources and materials produced from the fermentation process using bacterial to produce aliphatic polyesters (Marrazzo, Di Maio, and Iannace Citation2007; Shariatinia and Fasihozaman-Langroodi Citation2019). Many reports are available on the combination of natural and synthetic polymers. The research focuses on the preparation method to modify the packaging film based on polysaccharide, protein, PLA, PVA, PCL, and PHB, which provide good compatibility with other polymers or fillers (Calva-Estrada, Jiménez-Fernández, and Lugo-Cervantes Citation2019; Cazón et al. Citation2017; C. H. Lee et al. Citation2020). The filler also improved the films physicochemical, mechanical, and thermal depending on factors such as an equilibrium between the degree of cross-linking of the polymer matrices and the addition of additive (Nandhavathy et al. Citation2017; Rogovina Citation2016). Combining bio-based polymers with other polymers also offers great potential for packaging applications.
Many reviews on biofilm materials have tried to address the addition of different types of biopolymers and additives. However, adding a combination of polymer and filler into hybrid packaging films still needs to be reviewed. This review provides a systematic discussion on recent developments of biodegradable hybrid polymer materials for packaging. The type of polymeric matrices, fillers, plasticizer and characteristics of component in hybrid films are detailed. Lastly, perspectives on the future development and direction for biodegradable hybrid polymers film for packaging are also included.
Biopolymeric matrices
The biodegradable polymer is derived from renewable organic substances and compounds to make bio-based packaging that is biodegradable at the end of its life cycle. Based on specific criteria, a biodegradable polymer can be classified into numerous categories based on the presence of its elements. However, the most used criteria to classify biodegradable are the source of raw materials and the synthesized process (Yuvaraj et al. Citation2021). Biopolymers are classified into two important groups, namely biologically derived or natural biopolymers and synthetics biopolymers. Natural biopolymers come from agricultural wastes and living organisms. On the other hand, synthetic biopolymers are mostly produced from nonrenewable sources like petroleum, natural gas, and polymers obtained by microbial production (Vroman and Tighzert Citation2009). As illustrated in , the natural biopolymers mainly include polysaccharide and protein-based, while the synthetic biopolymers mainly include polyvinyl alcohol (PVA), polylactic acid (PLA), polyhydroxyalkanoates (PHA), and polycaprolactone (PCL). All biopolymer matrices are summarized in and discussed in detail in the following sections.
Table 1. Summary of natural and synthetic polymeric matrices of selected materials.
Natural biopolymers
Polysaccharides
A polysaccharide is one of the types of carbohydrates that can take different forms with varying numbers of carbon atoms. They have been used as polymer-based to form film for food packaging products. The applications of polysaccharide-based film in the packaging industry have offered the possibility to develop a new packaging material (Cazón et al. Citation2017). Several polysaccharide substances have been considered as packaging matrices. They include starch, cellulose, chitosan, and various other substances. It has been reported in many studies that several types of polysaccharide-based such as starch, cellulose, chitosan, and pectin have excellent film-forming ability (Choo et al. Citation2016; Edhirej et al. Citation2017; Espitia et al. Citation2014; Mose and Moffat Maranga Citation2011; Xu et al. Citation2016; Zafar et al. Citation2016).
There are a number of polysaccharide-based and low-cost biopolymer materials available on the market, including starch. There are a wide variety of plants that produce starch, including wheat, corn, beans, and potatoes. It consists of linear chain amylose and branched amylopectin (Pawar and Purwar Citation2013). In its native form, starch is hardly usable because of its brittleness and poor mechanical properties, which lead to poor film-forming capacity. These weaknesses are overcome through plasticization, blending with other polymers, and the addition of fillers (Bonilla et al. Citation2013). Cellulose is one of the most abundant organic molecules and has been widely studied and used as one of the biodegradable materials because of its properties such as renewability, low cost, non-toxicity, biocompatibility, and physical-chemical stability (S. Wang, Lu, and Zhang Citation2016). Chitosan is another abundant natural polysaccharide that has been explored as polymer matrices in packaging material. It is obtained by the alkaline N-deacetylation of chitin and is mainly extracted from the waste fishery industry (Haghighi et al. Citation2020). Chitosan is insoluble in water and most organic solvents and can be combined with other synthetic polymers to improve the thermal properties of the resulting composite film. However, chitosan films are highly permeable to water vapor, which limits their use as food packaging material (Aider Citation2010; Cazón et al. Citation2017).
Protein-based
Protein-based biopolymer films recently have received attention and are increasingly being utilized in food packaging applications because of their consumer demand to get a natural preservatives in food packaging (Calva-Estrada, Jiménez-Fernández, and Lugo-Cervantes Citation2019). Many studies on protein-based biopolymers in food packaging focus on animal and vegetable proteins because of their relative abundance, renewability, excellent film formation ability, biodegradability, and high nutritive value (Calva-Estrada, Jiménez-Fernández, and Lugo-Cervantes Citation2019; Wakai and Almenar Citation2015). Protein-based films are mostly made from collagen, gelatin, soy protein, whey protein, and zein (Kumar, Kaur, and Bhatia Citation2017). Applications of this material are diverse from emulsifiers to biodegradable composite films, driven by the requirement to change synthetic material with natural and biodegradable material. Collagen and gelatin-based films have shown excellent barriers against oxygen and aroma compounds at low relative humidity with good mechanical properties (Garavand et al. Citation2017; Liu et al. Citation2017; Nuanmano, Prodpran, and Benjakul Citation2015). On the other hand, whey protein and zein are a byproduct in soybean, cheese, and corn starch industries that form a good film-forming capacity with an excellent barrier against oxygen at low relative humidity (Ciannamea, Stefani, and Ruseckaite Citation2016; Hadidi et al. Citation2022; Kashiri et al. Citation2016; Pellicer et al. Citation2017).
Properties of polysaccharide-based and protein-based film
The properties of polysaccharide-based and protein-based materials are one major literature study in considerable research to give insight into improving the characteristic of hybrid packaging film. The physical and mechanical properties of these materials are summarized in . Biodegradable films are based on polysaccharides and proteins, such as starch, chitosan, cellulose, pectin, and whey protein. When starch with high amylose was used for starch-based films, the obtained film gave higher tensile strength and a lower percentage of elongation than films obtained from starch with low amylose. Both types of starch also showed a decrease in the tensile strength and an increase in the elongation percentage when glycerol as a plasticizer was added into films with a concentration above 15%. The addition of a plasticizer reduces the intra-molecular attraction forces between the starch molecules and plasticizer, resulting in greater flexibility for films (Muscat et al. Citation2012). The plasticizer is the most effective in reducing the rigid structure and brittleness in biodegradable films and commonly decreases the tensile strength and increases the elongation of the film.
Table 2. Physical and mechanical properties of the selected natural and synthetic biopolymer (polysaccharide, protein, PLA, PVA, PHA, and PCL-based film).
Another study on starch-based films shows that adding plasticizers affects the mechanical properties of starch-based films. shows that the tensile strength decreased while the elongation percentage increased with increasing plasticizer in all starch-based films (Sessini et al. Citation2016). The mechanical properties of films only with starch polymer matrix demonstrated higher tensile strength than films with plasticizer addition because of their influence in the botanical origin of starch, precisely the proportion of amylose and amylopectin (Hulleman, Janssen, and Feil Citation1998).
Figure 2. Mechanical properties (A) tensile strength and (B) elongation at break of a starch-based film with different glycerol, catechin and starch nanocrystal concentrations (Sessini et al. Citation2016).
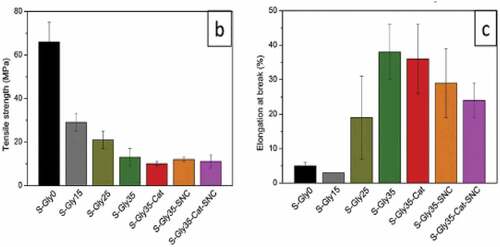
For chitosan-based films with the addition of protein from quinoa seed give a lower tensile strength and elongation than the neat chitosan films. These indicate that adding another biopolymer, such as protein, decreased the mechanical properties of chitosan film. The presence of protein in films also increased the extensibility up to four times compared to films made with only chitosan-based (Abugoch et al. Citation2011). In another study, the chitosan-based films also had the same result: a higher tensile strength value compared to film with the addition of additives (Shen and Pascal Kamdem Citation2015).
In cellulose-based films, the effect of adding fillers on the physical and mechanical properties of cellulose film has been increased. The incorporation of fillers into polymer matrix formulation resulted in a significant increase in tensile strength and elongation. In films of cellulose acetate containing cellulose nanowhisker fillers, the film’s tensile strength prepared using 4.5 wt % of fillers solution increased by 9% and the elongation percentage by 44% (Yang et al. Citation2013). shows that the increase in filler concentrations also increases the tensile strength and elongation.
Figure 3. The mechanical properties of the cellulose-based film with different cellulose nanowhisker filler content (Yang et al. Citation2013).
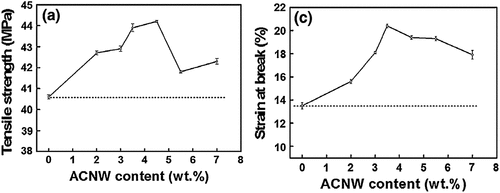
In pectin-based films, the mechanical properties analysis showed that low-methyl pectin content led to stronger and stiffer films than high-methyl pectin because of the higher occurrence of a polar group in low-methyl pectin and possibly leading to higher content of hydrogen bonds and more compact pectin network (Lorevice et al. Citation2016). This study also used chitosan nanoparticles as reinforcement to improve the tensile strength and elongation of both types of pectin. The addition of chitosan nanoparticles enhances more than 50% of the mechanical properties for high-methyl pectin and low-methyl pectin (Lorevice et al. Citation2016).
For protein-based films, incorporating cellulose nanofibers as fillers with different concentrations increased the tensile strength but decreased the elongation. Results show that the highest tensile strength value was observed in the composition of whey protein isolate and 7.5% cellulose nanofibers (15.85 MPa), which increased by 54.8% compared to pure whey protein isolate-based films without fillers (Alizadeh-Sani, Khezerlou, and Ehsani Citation2018). On the other hand, elongation decreased because the biopolymer such as a protein with rigid fillers causes a higher hardness and brittleness effect on films than pure protein films. However, the rigidness and hardness in the incorporation of filler can be improved by adding a plasticizer. The smaller the plasticizer’s molecular weight, the more effective for film, and plasticizers with low polarity are less effective due to their low competition with hydrogen bonding sites (Wihodo and Moraru Citation2013).
Synthetic biopolymers
Biopolymer produces by chemical fusion from biomass monomer
Polylactic acid (PLA)
Polylactic Acid (PLA) is a synthetic thermoplastic biopolymer derived from the fermentation of agricultural products such as corn, wheat, sugarcane, and tapioca which make it renewable and compostable. PLA has been explored intensely in biofilm studies because of its remarkable properties like biodegradability, compatibility, and easier processability compared with other synthetic biopolymers (Kamal and Khoshkava Citation2015). However, PLA as a packaging material poses major weaknesses, including low thermal and mechanical properties as well as high water vapor and gas permeabilities. The combination of biopolymers and fillers with PLA matrices is known as one of the most efficient and cost-effective strategies to enhance the resulting composite properties (Mahmoodi, Ghodrati, and Khorasani Citation2019; Monika et al. Citation2018; Nagarajan, Mohanty, and Misra Citation2016).
Polyvinyl alcohol (PVA)
Polyvinyl alcohol (PVA) is one of the synthetic biopolymers easily obtained from renewable bio-based monomers or mixed sources of biomaterial and petroleum (Aslam, Ali Kalyar, and Ali Raza Citation2018; Ciannamea, Stefani, and Ruseckaite Citation2016; Jun Feng Citation2017). PVA also possesses good biocompatible, biodegradable, nontoxic, odorless, water-soluble, and has a higher crystalline biopolymer (Srivastava et al. Citation2019). It has interesting mechanical properties and excellent film-forming ability because of the abundance of hydroxyl groups and intermolecular hydrogen bonding (Choo et al. Citation2016). PVA has been attracted great attention as a potential packaging material. However, PVA-based film has low resistance to water and humid environments because of its hydrophilic nature that leads to swelling, poor oxygen barrier, and mechanical properties (C. H. Lee et al. Citation2020). To overcome those drawbacks, it can be blending with other biopolymers and reinforcement.
Biopolymer produces by microbial production
Polyhydroxyalkanoate (PHA)
Polyhydroxy Alkanoate (PHA) is a biobased polymer and a family of polyesters of several R-hydroxy alkanoic acids. It can be processed thermally and synthesized by several microorganisms in the presence of excess carbon and when essential nutrients like oxygen, nitrogen, or phosphorus are limited (Anjum et al. Citation2016; Cinelli et al. Citation2019). PHA is biodegradable, compatible, and can be obtained from renewable resources. These polymers have similar thermoplastic properties, good mechanical properties, and possess excellent biodegradability in various applications with melting points ranging from 40 to 180°C (Yalcin et al. Citation2006). Despite their good properties and excellent biodegradability, PHA film has some drawbacks due to its high crystallinity, leading to brittle and rigid film, low toughness, and poor resistance to high temperatures. The properties of PHA also depend on the monomer composition and microbial fermentation technique (Modi, Koelling, and Vodovotz Citation2011; Reichert et al. Citation2020).
Polycaprolactone (PCL)
Polycaprolactone (PCL) is an aliphatic polyester and biodegradable polymer produced by chemical synthesis from crude oil via the ring-opening polymerization of caprolactone (Sharmin et al. Citation2012). This biopolymer, with a low melting (approximately 60°C) and glass transition (around −60°C) temperature, offers an ideal biodegradable matrix for natural antimicrobial agents as it can be processed at low temperature and have the potential for use in commercial applications. PCL is widely used in food packaging because of its degradability, biocompatibility, and superior rheology properties. However, there is some drawback to this biopolymer which has lower modulus and rigidity that limits their applications (Khalid et al. Citation2018).
Properties of PLA, PVA, PHA, and PCL based film
The PLA, PVA, PHA, and PCL-based film materials are shown in their mechanical properties and summarized in . The PLA-based film incorporating cellulose nanocrystals gives a higher tensile strength than the pure PLA film. The highest tensile strength value of 294 ± 7.2 MPa was obtained using PLA-based film incorporating cellulose nanocrystal 0.1% (Z. Wang et al. Citation2019). However, the elongation of the film decreased with increasing the concentration of cellulose nanocrystal. This reduction can be attributed to the mobility of the polymer matrix caused by the increased stiffness in the PLA films. Another study of PLA-based film with cellulose microfibers also has the same result and gives a higher tensile value than film without filler (Mármol, Gauss, and Fangueiro Citation2020). In PVA and whey protein isolate film, an increase of nanosilica filler also slightly increases the elongation. shows the difference in tensile strength and elongation of PVA and whey protein-based film with and without fillers. The tensile strength value of 10.2 MPa was obtained using nanosilica 4% (Lara et al. Citation2021). This increase can occur because of the mobility restriction that provided a more rigid film.
Figure 4. Mechanical properties of a PVA/WPI-based film with different nanosilica (NS) concentrations (Lara et al. Citation2021).
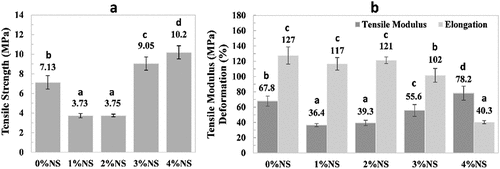
In PHA-based film, the mechanical properties showed the improvement of tensile strength and elongation value with the addition of cellulose microfibers filler. Results show that the addition of cellulose microfiber gives higher tensile strength and elongation value with 23.5 MPa and 0.93%, respectively (Mármol, Gauss, and Fangueiro Citation2020). The improvement in this study showed affinity between cellulose microfiber and the polymer matrix of PHA without the addition of a coupling agent to improve the reinforcing effect of the fibers in PHA-based film. For PCL-based film, incorporating starch and pomegranate rind as fillers with different concentrations increased the tensile strength but decreased the elongation. Results show that the highest tensile strength value was observed in addition to 25% starch and pomegranate rind 20% (8.41 MPa) (Khalid et al. Citation2018). On the other hand, elongation percentage decreased in addition to the filler by 20.14%. In another study, PCL-based film with chitosan added higher mechanical properties than PCL film with starch with 18.8 MPa and 195.5% for tensile strength and elongation, respectively (Zeng et al. Citation2020).
Fillers
Filler or reinforcement is added to the polymer matrix to improve the barrier, physical, and mechanical properties while also filling voids in the polymer matrix with a relatively inexpensive molecule. Various materials can be added to achieve these criteria, including natural and synthetic polymers. The addition of filler into hybrid material also offers numerous environmental advantages for the packaging industry, such as lower density, lower cost, reduced pollutant emission, and enhanced mechanical strength of hybrid films (Faruk et al. Citation2012).
Natural fillers
Natural-based fillers are very popular because of their renewability and the volatility of other petroleum-based fillers. Natural fillers from natural fiber have been extensively used to fabricate hybrid and composite films. Their advantages, such as low cost, low density, non-abrasive to processing equipment, low production energy, and their renewable and degradable features are some of the important properties of natural filler resources, which make them more suitable fibers to use as a filler in hybrid polymer film (Saba, Md Tahir, and Jawaid Citation2014). Many reports are available on using lignocellulose as reinforcement for polymer matrix. Lignocellulose fibers are mainly composed of cellulose, hemicellulose, lignin, and other extractives in smaller amounts (Pandey et al. Citation2012; Prado and Spinacé Citation2019). The origin and type of material greatly influence the composition of natural filler resources. Therefore, detailed information about the building block of lignocellulose is very important to explore its potential as reinforcement for hybrid polymer in packaging applications. The chemical composition of some natural filler resources is listed in .
Table 3. Chemical compositions of selected natural materials (Pandey et al. Citation2012; Prado and Spinacé Citation2019; Wang et al. Citation2019).
Natural-based filler is also susceptible to degradation, which is affected by the compositions (Gurunathan, Mohanty, and Nayak Citation2015). A component-like hemicellulose is mainly responsible for biological and thermal degradation and hygroscopic property. In contrast, lignin is responsible for UV degradation and is a thermally very stable component (Mochane et al. Citation2019). The physical and mechanical properties of selected natural-based filler resources are presented in . The high tensile strength of flax as one of the natural resources for filler compared to other listed fibers can be attributed to flax’s unidirectional cellulose microfibrils and tubular structure (Mochane et al. Citation2019; Sanjay et al. Citation2018).
Table 4. Physical and mechanical properties of selected natural (Gurunathan, Mohanty, and Nayak Citation2015).
Synthetic fillers
Some synthetic fillers have been introduced because of their unique value and functional properties. Inorganic fiber, such as glass and carbon fibers, are the most used filler in the hybrid composite film (Mochane et al. Citation2019). Most of these materials have been experienced their success in different industrial sectors such as large-scale production, construction, and many others (Haldorai, Jin Shim, and Taek Lim Citation2012). Synthetic fillers possess high mechanical properties, good stability, and have a long-lasting life span. These properties advance the synthetic fillers over the natural fillers, in which the latter suffer from inconsistency because of the variation in growth conditions as well as their environmental conditions (Gangil et al. Citation2020). In a previous study, adding Nano clay filler achieved a higher impact and tensile strength, whereas glass fiber has optimum flexural strength value (Mutalikdesai et al. Citation2018). By lowering the reinforcing addition, this filler lowers the cost without sacrificing the characteristics of the composite. Particularly these fillers improved the cost of carbon, kevlar, and glass fiber composites. The cost to performance ratio is an important consideration for the production of these fillers in order to come up with a low-cost manufacturing process. The game-changing properties there are their high tensile strength (1.9 to 3.5 GPa for glass fibers) and tensile modulus (between 50 and 90 GPa) that overshadow other disadvantages, resulting in the successful applications in industrial scale (Salman Citation2019).
Plasticizers
Plasticizer additive is used to strengthen the flexibility, elasticity, and toughness of polymer films and at the same time also decrease hardness and stiffness (Malathi, Santhosh, and Udaykumar Citation2014). The plasticizer can be used in polymers that are brittle and fragile at room temperature and have a lower glass transition temperature, and can be used to produce film or plastic for packaging. Currently, many plasticizer products have been applied in polymers as packaging. Plasticizers used in the film-forming solution are summarized in .
Table 5. Plasticizer used in biodegradable film-forming solutions (Malathi, Santhosh, and Udaykumar Citation2014).
Plasticizers generally have an average molecular weight between 300 and 600 kDa, a high boiling point, and linear or cyclic carbon chains (14–40 carbons) (Vieira et al. Citation2011). The small molecular size of plasticizers allows occupying of intermolecular spaces between polymer matrix chains and decreases secondary forces among them. As a result, there is an increase in free volume and molecular mobility. The polymer–plasticizer interactions are dominant at low plasticizer concentrations, while at high plasticizer concentrations, plasticizer-plasticizer interaction can become more significant. This also explains the observation of non-plasticization, wherein very low concentrations of plasticizer can increase the rigidity of the polymer (Höfer and Ecosiris Citation2012). Different type of elasticity and flexibility of biodegradable polymers mostly depends on the chemical structure, molecular weight, chemical composition, and functional group of the plasticizer (Hourston Citation2010; Rungsinee and Krochta Citation2005). The variety of plasticizers also affects the flexibility of the final product materials (Cao, Yang, and Fu Citation2009).
Formulation of a natural biopolymer-based film can alter some properties like microstructure, water vapor, and gas permeability. The starch film with two different plasticizers (sorbitol and glycerol) was tested in different concentrations (1–8 g/L) (García, Martino, and Zaritzky Citation2000). Results show that the addition of plasticizer improved starch-based film performance by increasing barrier properties to water vapor and maintaining the selective gaseous permeability. In other studies, adding a blend plasticizer (Sorbitol/glycerol) also improves protein-based films’ flexibility and barrier properties (Jafarzadeh et al. Citation2018).
Properties hybrid polymer film
Physicochemical properties
Biodegradability, gas barrier, and moisture barrier are essential physicochemical properties of hybrid polymer films. The biodegradability of hybrid film is used to determine its lifespan. Environmental conditions such as temperature, moisture, pH, and nutrient availability that the materials are exposed to in the presence of microorganisms affect biodegradation (Obasi et al. Citation2013). The film should have a particular lifespan that allows for ample time for use while also allowing for rapid degradation when disposed of. shows the standard methods for determining the biodegradability of packaging film.
Table 6. Standard methods to measure biodegradation of packaging film (Obasi et al. Citation2013).
Biodegradability consists of two phases. The first phase is characterized by the defragmentation of film material initiated by the presence of moisture, heat, and enzymes excreted by a microorganism like bacteria, fungi, or algae (Naveena and Sharma Citation2020). The second phase is biodegradation, initiated by naturally occurring enzyme and acids, which transforms long into short compounds (Naveena and Sharma Citation2020; Zhai et al. Citation2004). Subsequently, the molecules are reduced to a smaller size and absorbed/fixated through the cell walls of the microorganisms, where they are then metabolized for energy. The metabolisms eventually produce carbon dioxide or methane depending on the pathways (Prathipa, Sivakumar, and Shanmugasundaram Citation2018).
Different standard methods or principles for evaluating biodegradation for packaging film are available. To determine the biodegradation of hybrid polymer films there are mainly three methods, which include laboratory test, simulation test, and field test, as illustrated in . The laboratory test is the most reproducible biodegradation test, where specific media are used, such as synthetic media, and inoculated with one of the mixed microbial populations from wastewater or individual microbial strains, which may have been specially chosen for particular polymers (R. Müller Citation2002).
Figure 5. Illustration of the biodegradation test (Müller Citation2002).
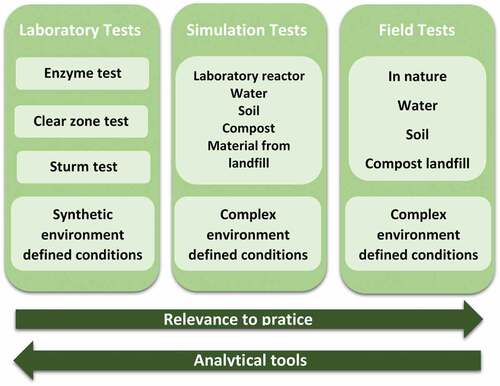
The method for field test situations is by burying film or plastic materials in soil and placing them in an open landscape or performing a full-scale composting process with films that can represent the ideal practical with environmental conditions. This test also has several disadvantages like environmental conditions such as temperature, humidity, and pH content that cannot be controlled when the test occurs (R. Ciencia and Andes Citation2018; Müller Citation2002). This type of test also limits the analytical opportunities to monitor the degradation process.
As alternatives to this type of test, different simulations have been used to measure the biodegradation of films. The degradation test might take place in the soil, compost, or seawater placed in a controlled reactor in a laboratory (R. Müller Citation2002). Despite this, the environment is still very close to the field test situation. The parameters such as temperature, pH content, and humidity can be controlled and adjusted when the test occurs. Occasionally, to reduce the time taken to process the tests, nutrients are added to the reactor to increase the microbial activity and stimulate the degradation process (Naveena and Sharma Citation2020).
Gas and moisture barriers are also important physicochemical properties of the hybrid polymer film. To withstand shelf life and maintain the quality of food during storage, specific gas pressure conditions are required for the food. The gas mixture consists of oxygen, carbon dioxide, and nitrogen, or a combination of these three gases in most packaging applications. To achieve the gas pressure condition and certain gas compositions, the material in the film needs certain gas barrier properties. These film properties are closely related to the permeation capacity of the material to exchange low molecular weight substances through film. The use of multilayers could give better barrier properties for packaging materials (Cazón et al. Citation2017).
Moisture barrier properties of the film refer to the ability of film to resist the entry of undesired vapor, such as vapor by permeability, diffusivity, solubility across the barrier, and the affinity of the packaging film materials toward water (Cazón et al. Citation2017). The term permeability describes the overall mass transport of the gas or liquid across the film, whereas the term of diffusivity describes the movement of the molecules inside the bulk of polymer (Siracusa Citation2012). There are studies about the hydrophobic type of bio-based materials that reduce natural polymers water vapor permeation. These properties depend upon the crystallinity and chain conformation of material resources in the film. Generally, hybrid films from natural biopolymers have a higher value of gas and moisture barrier than synthetic materials. Because of the higher value for barrier properties, many studies have been done to decrease the value by adding fillers and layers to natural biopolymer-based films. The barrier properties of the selected hybrid film are shown in .
Table 7. Barrier Properties of selected hybrid film.
Biopolymer films based on cellulose materials are very efficient in preserving oxygen and aroma compounds. Among the available cellulose derivatives, methylcellulose is one of the most studied in materials biopolymer films. Studies about the effect of methylcellulose content with the addition of starch on the barrier properties resulted in significant variation in the water vapor permeability from 0.65 × 10−11 to 25.9 × 10−11 g/m. s. Pa for concentrations ranging from 45% to 30% (Arvanitoyannis and Biliaderis Citation1999). These values are explained by a hydrophilic characteristic of the film resulting from the hydroxyl groups in the polymer chain of methylcellulose and starch. When a combination of methylcellulose and starch was used as a polymer matrix and fillers, the water vapor permeability increased significantly as the polymer concentrations decreased (Arvanitoyannis and Biliaderis Citation1999).
In starch-based films, the addition of chitosan decreased the water vapor permeability value from 12.1 × 10−11 to 2.8 × 10−11 g/m. s. Pa (Vásconez et al. Citation2009). This decreasing trend can be attributed to the higher hydrophobicity when compared to starch. Additionally, hydrogen bond interaction between chitosan and starch reduces the availability of the hydrophilic groups and decreases the interaction between materials and water molecules, affecting the value of barrier properties.
Recently, the addition of nanofiller for improving the barrier properties of films has been the main focus in several studies. The materials that are commonly used for nanoparticle materials in biodegradable hybrid films are chitosan, cellulose, and starch. Chitosan nanoparticle materials have been widely used as a filler to improve barrier properties and thermo-stability (Antoniou et al. Citation2015).
The studies of chitosan nanoparticles and bulk chitosan with tara gum films showed that the chitosan nanoparticle affected the water vapor permeability values. The permeability decreased from 9.91 × 10−11 to 1.28 g/m. s. Pa, when 10% of chitosan nanoparticle was incorporated (Antoniou et al. Citation2015). The presence of chitosan nanoparticles in tara-gum films could increase the tortuosity of the two biopolymers, leading to a slower diffusion process and lower permeability (Akter et al. Citation2014).
Cellulose and derivative nanoparticles were also studied in this topic. In methylcellulose films, the addition of nanocellulose resulted in the value of water vapor permeability decreasing sharply as the concentration of nanocellulose increased. Thus, a 26% reduction of water vapor permeability value in films was obtained at 1% nanocellulose addition (Khan et al. Citation2010). The effect of nanocellulose content on the water vapor permeability is shown in .
Figure 6. Effect of different nanocellulose concentrations on the water vapor permeability of methylcellulose-based films (Khan et al. Citation2010).
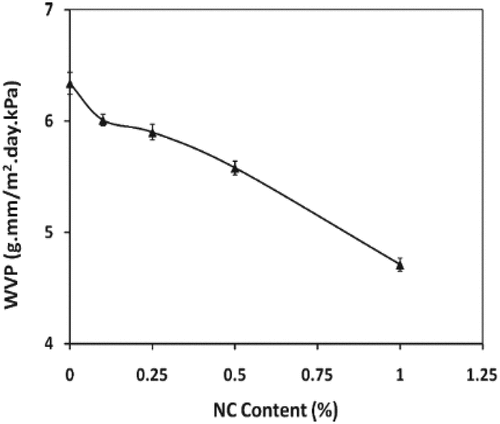
Other materials for enhancing barrier properties are clay nanoparticles and silver nanoparticles. In starch-based films, it was observed that the clay nanoparticles addition caused a significant decrease in the water vapor permeability of 8.33 × 10−11 g/m. s. Pa (Müller, Borges Laurindo, and Yamashita Citation2011). In chitosan/starch-based films, the addition of silver nanoparticles increased the water vapor permeability value (Yoksan and Chirachanchai Citation2010). The growth in this permeability might be a result of the obstruction of intermolecular hydrogen bond formation between chitosan and starch molecules, causing the incompatibility of the film polymer matrix and adsorption of water vapor at the hydrophilic section of chitosan and starch molecules (Yoksan and Chirachanchai Citation2010). In another study with cellulose-based films, a decrease in the water vapor permeability value of the cellulose-based film was observed. The addition of silver nanoparticles with smaller sizes give varied result in different particle sizes from cellulose-based films containing from 41 nm to 10 nm (De Moura, Mattoso, and Zucolotto Citation2012).
Mechanical properties
The mechanical properties of hybrid polymer film are the most crucial in packaging applications. They include tensile strength (TS), elongation (E), and Young modulus (YM). They depend on the hybrid film blend and the nature of every component in film. Mechanical properties are very important in packaging hybrid film products. They are considered because the material can withstand external stress while maintaining the film’s consistency. shows the mechanical property values of some selected hybrid films. In whey protein-based films, the reinforcement of cellulose nanofibers and TiO2 nanoparticles offers good mechanical properties. The results show that the addition of 7.5% cellulose nanofibers and 1.5% TiO2 nanoparticle into whey protein-based films reached a higher value in tensile strength (17.03 MPa) and reduction in elongation (59.04%) (Alizadeh-Sani, Khezerlou, and Ehsani Citation2018). The improved tensile strength of hybrid films can be ascribed by the suitable compatibility between two biopolymers and nanoparticles through a unique interaction (El-Wakil et al. Citation2015). In another study, whey protein-based films were also blended with synthetic biopolymer such as polyvinyl alcohol. The addition of synthetic biopolymer increased elongation and decreased the tensile strength and Young modulus of the whey protein films (Lara et al. Citation2019). Despite the lower mechanical properties of these blend films, the result can be considered close to the low-density polyethylene (LDPE) films, which are materials with large applications in the food packaging sector (Doak and James Citation1986).
Table 8. Mechanical properties of selected hybrid film.
In , mechanical properties show that whey protein films behaved as a fragile materials, and polyvinyl alcohol gives an elastic structure in protein-based films. The addition of polyvinyl alcohol caused an increase in elongation for all ratios of whey protein and polyvinyl alcohol blends, but on the other hand, the tensile strength and Young modulus decreased by increasing the loading of polyvinyl alcohol (Lara et al. Citation2019). This reduction in tensile value strength and Young modulus was caused by the chain characteristic in polyvinyl alcohol that provided high film flexibility. It was shown that the whey protein and polyvinyl alcohol films with a ratio of 70/30 resulted in a lower value of tensile strength and higher value in elongation than the blend film of whey protein and polyvinyl alcohol with the ratio of 90/10 (Lara et al. Citation2019).
Figure 7. Value of Tensile strength (a), Young modulus (b), and Elongation (c) of hybrid films with different ratios of whey protein and polyvinyl alcohol (Lara et al. Citation2019).
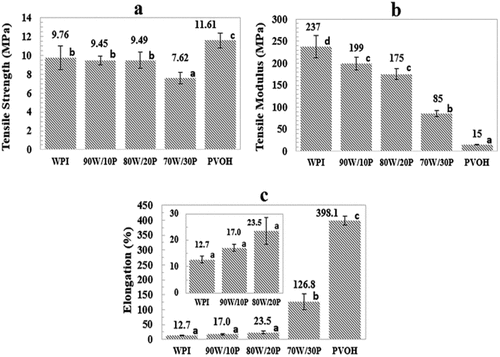
Apart from increasing the flexibility in films, polyvinyl alcohol is also used to combine a polymeric matrix with chitosan and cellulose nanocrystal as a filler. It showed that the tensile properties of polyvinyl alcohol and chitosan films are affected by their blending and the incorporation of different concentrations of nanocrystals cellulose (El Miri et al. Citation2015). After adding fillers into the polyvinyl alcohol and chitosan blend films, an increase in tensile strength and Young modulus was visible. This could be present in the form of more hydrogen bonds interaction that occurred between the fillers and polymer matrix blend. When 5% nanocrystal cellulose was added in blend films, the tensile strength and Young modulus increased by 77% and 105%, respectively (El Miri et al. Citation2015). On the other hand, the elongation decreased with a higher concentration of nanocrystalline cellulose. The same result also appears in the starch-based film, in which the addition of nanofillers such as nano-clay and nanocrystalline cellulose increased the tensile strength and Young modulus but decreased the elongation (Chung et al. Citation2010; Müller, Borges Laurindo, and Yamashita Citation2011; Slavutsky and Bertuzzi Citation2014). In chitosan films, the use of polyvinyl alcohol and polylactic acid with a 1:1 ratio and ZnO nanoparticles as fillers improved the mechanical properties of the resulting hybrid films. Results of all samples in the study showed that the addition of fillers with 6% imposed the highest tensile strength of 11.54 MPa, which increased from 2.92 MPa without the addition of fillers (Shariatinia and Fasihozaman-Langroodi Citation2019). The ZnO nanoparticle also reduced the elongation of films from 50.56% to 25.56%, which can be attributed to the origin characteristic of these materials with low elasticity.
Thermal properties
Excellent thermal properties ensure the protection of the product against thermal damage during a period of storage in the application. Thermal properties are also the most critical function for the hybrid biodegradable film in which they determine the suitability of biofilm for a certain application. Various techniques are applied in the processing of bio-film. They include plasticization, reinforcement of filler, blending with other polymer matrices, and converting biofilm into the thermoplastic phase to improve the hybrid films thermal properties (Prathipa, Sivakumar, and Shanmugasundaram Citation2018). shows a general thermogravimetric analysis (TGA) graph for the decomposition process of biodegradable polymers and fillers as material components. In thermogravimetric curve for hybrid biodegradable film shows a process of thermal degradability in the sample. The model of the thermogravimetric curve in the sample is determined by various kinetic parameters of the pyrolysis process, such as reaction order, frequency factor, and activation energy. The values in these parameters depend upon conditions, weight, shape, flow rate, heating rate, and the treatment used before evaluating the data from the sample film (Azwa et al. Citation2013). Theoretically, when a reaction in the process develops in a differential thermal analysis (DTA), the change in thermal properties of the sample film is indicated by deflection or a peak in the curve. If the reaction rate in the process varies with different temperatures, the position of the peak will also vary from the heating rate if different experiment conditions are stable. This difference in peak temperature could determine the activation energy for the reaction of different reaction orders in the process (Di Franco et al. Citation2004; Lee and Wang Citation2006; Suardana, Ku, and Kyoo Lim Citation2011; S. H.). Shortly, thermogravimetric (TG) and derivative thermogravimetric (DTG) curves are mostly used to determine the weight loss in materials and to determine the decomposition of material at a certain temperature for development in the study of thermal in materials hybrid.
Figure 8. The general thermogravimetric decomposition process of biodegradable polymers and fillers from natural resources (Azwa et al. Citation2013; Di Franco et al. Citation2004; Lee and Wang Citation2006; Suardana, Ku, and Kyoo Lim Citation2011).
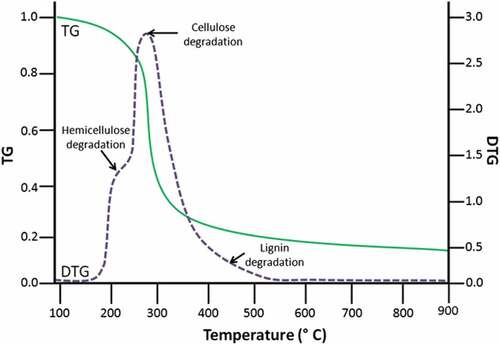
Concluding remarks and perspectives
Green materials are an alternative packaging for the future food industry. Many materials from natural and synthetic biopolymers can be a good prospect for changing the properties of packaging. Hybrid packaging with more than two sources of materials that combine and be degradable packaging is a challenging material for the future and hopes to be sustainable for many applications, including as a replacement for plastic. Materials made from bioresources, such as reinforcing matrix and filler, will greatly impact the environment. Where currently, various countries are competing to reduce petroleum-based plastics. Of course, these bioresources can reduce environmental hazards and pollution, so this plastic hybrid is an alternative to that problem. With superior properties such as good mechanical, thermal, and environmental, hybrids film should be looked at as a source of future packaging. In addition, the method of making hybrids films can also be done in a big way and is an advantage for the industry to be able to produce on a large scale, and this also supports the world economy as well as solving environmental problems.
Highlights
This paper reviews recent developments in biodegradable film-based packaging.
Biodegradable film-based packaging is seen as viable alternative to replace the ones from petroleum derivatives.
The weak mechanical properties of bioresource-based film can be enhanced by forming composite.
Biomass-based material can be used as a matrix and a filler in hybrid polymer-based packaging.
Hybrid material enhanced physicochemical, mechanical, and thermal properties of the resulting films.
Disclosure statement
No potential conflict of interest was reported by the author(s).
Additional information
Funding
References
- Abugoch, L. E., C. Tapia, M. C. Villamán, M. Yazdani-Pedram, and M. Díaz-Dosque. 2011. Characterization of quinoa protein-chitosan blend edible films. Food Hydrocolloids 25 (5):879–22. Elsevier Ltd. doi:10.1016/j.foodhyd.2010.08.008.
- Aider, M. 2010. Chitosan application for active bio-based films production and potential in the food industry: review. LWT - Food Science and Technology 43 (6):837–42. Elsevier Ltd. doi:10.1016/j.lwt.2010.01.021.
- Akter, N., R. A. Khan, M. O. Tuhin, M. Emdadu Haque, M. Nurnabi, F. Parvin, and R. Islam. 2014. Thermomechanical, barrier, and morphological properties of chitosan-reinforced starch-based biodegradable composite films. Journal of Thermoplastic Composite Materials 27 (7):933–48. doi:10.1177/0892705712461512.
- Alizadeh-Sani, M., A. Khezerlou, and A. Ehsani. 2018. Fabrication and Characterization of the bionanocomposite film based on whey protein biopolymer loaded with TiO2 Nanoparticles, Cellulose Nanofibers and Rosemary Essential Oil. Industrial Crops and Products 124:300–15. doi:10.1016/j.indcrop.2018.08.001.
- Anjum, A., M. Zuber, K. Mahmood Zia, A. Noreen, M. Naveed Anjum, and S. Tabasum. 2016. Microbial production of polyhydroxyalkanoates (phas) and its copolymers: a review of recent advancements. International Journal of Biological Macromolecules 89: 161–74. Elsevier B.V. doi:10.1016/j.ijbiomac.2016.04.069.
- Antoniou, J., F. Liu, H. Majeed, and F. Zhong. 2015. Characterization of tara gum edible films incorporated with bulk chitosan and chitosan nanoparticles: A comparative study. Food Hydrocolloids 44:309–19. doi:10.1016/j.foodhyd.2014.09.023.
- Arvanitoyannis, I., and C. G. Biliaderis. 1998. Physical properties of polyol-plasticized edible films made from sodium caseinate and soluble starch blends. Food Chemistry 62 (3):333–42. doi:10.1016/S0308-8146(97)00230-6.
- Arvanitoyannis, I., and C. G. Biliaderis. 1999. Physical properties of polyol-plasticized edible blends made of methyl cellulose and soluble starch. Carbohydrate Polymers 38 (1):47–58. doi:10.1016/S0144-8617(98)00087-3.
- Aslam, M., M. Ali Kalyar, and Z. Ali Raza. 2018. Polyvinyl Alcohol: A Review of Research Status and Use of Polyvinyl Alcohol Based Nanocomposites. Polymer Engineering and Science 58 (12):2119–32. doi:10.1002/pen.24855.
- Avérous, L., and E. Pollet. 2012. Environmental silicate nano-biocomposites. Green Energy and Technology 50. doi:10.1007/978-1-4471-4108-2.
- Azwa, Z. N., B. F. Yousif, A. C. Manalo, and W. Karunasena. 2013. A review on the degradability of polymeric composites based on natural fibres. Materials & Design 47:424–42. doi:10.1016/j.matdes.2012.11.025.
- Bonilla, J., L. Atarés, M. Vargas, and A. Chiralt. 2013. Properties of wheat starch film-forming dispersions and films as affected by chitosan addition. Journal of Food Engineering 114 (3):303–12. Elsevier Ltd. doi:10.1016/j.jfoodeng.2012.08.005.
- Brinchi, L., F. Cotana, E. Fortunati, and J. Kenny. 2013. Production of nanocrystalline cellulose from lignocellulosic biomass: Technology and applications. Carbohydrate Polymers 94 (1):154–69. doi:10.1016/j.carbpol.2013.01.033.
- Calva-Estrada, S. J., M. Jiménez-Fernández, and E. Lugo-Cervantes. 2019. Protein-based films: advances in the development of biomaterials applicable to food packaging. Food Engineering Reviews 11 (2):78–92. Food Engineering Reviews. doi:10.1007/s12393-019-09189-w.
- Cao, N., X. Yang, and Y. Fu. 2009. Effects of various plasticizers on mechanical and water vapor barrier properties of gelatin films. Food Hydrocolloids 23 (3):729–35. Elsevier Ltd. doi:10.1016/j.foodhyd.2008.07.017.
- Cazón, P., G. Velazquez, J. A. Ramírez, and M. Vázquez. 2017. Polysaccharide-based films and coatings for food packaging: Areview. Food Hydrocolloids 68:136–48. doi:10.1016/j.foodhyd.2016.09.009.
- Choo, K., Y. Chee Ching, C. Hock Chuah, S. Julai, and N. Shang Liou. 2016. Preparation and characterization of polyvinyl alcohol-chitosan composite films reinforced with cellulose nanofiber. Materials 9 (8):1–16. doi:10.3390/ma9080644.
- Chung, Y. L., S. Ansari, L. Estevez, S. Hayrapetyan, E. P. Giannelis, and H. Mei Lai. 2010. Preparation and properties of biodegradable starch-clay nanocomposites. Carbohydrate Polymers 79 (2):391–96. Elsevier Ltd. doi:10.1016/j.carbpol.2009.08.021.
- Ciannamea, E. M., P. M. Stefani, and R. A. Ruseckaite. 2016. Properties and antioxidant activity of soy protein concentrate films incorporated with red grape extract processed by casting and compression molding. LWT - Food Science and Technology 74: 353–62. Elsevier Ltd. doi:10.1016/j.lwt.2016.07.073.
- Ciencia, R., and L. Andes. 2018. An Overview of Starch-Based Biopolymers and Their Biodegradability Una Revisión Sobre Biopolímeros Con Base En Almidón y Su Biodegradabilidad. Ciencia e Ingeniería 39 (3):245–58.
- Cinelli, P., M. Seggiani, N. Mallegni, V. Gigante, and A. Lazzeri. 2019. Processability and degradability of pha-based composites in terrestrial environments. International Journal of Molecular Sciences 20 (2). doi: 10.3390/ijms20020284.
- De Moura, M. R., L. H. C. Mattoso, and V. Zucolotto. 2012. Development of cellulose-based bactericidal nanocomposites containing silver nanoparticles and their use as active food packaging. Journal of Food Engineering 109 (3):520–24. doi:10.1016/j.jfoodeng.2011.10.030.
- Di Franco, C. R., V. P. Cyras, J. P. Busalmen, R. A. Ruseckaite, and A. Vázquez. 2004. Degradation of Polycaprolactone/Starch Blends and composites with sisal fibre. Polymer Degradation and Stability 86 (1):95–103. doi:10.1016/j.polymdegradstab.2004.02.009.
- Doak, K. W., and D. E. James. 1986. Ethylene Polymers. In Encyclopedia of Polymer Science and Engineering, Vol. 6, 383–490. New york: John-Wiley & Sons.
- Edhirej, A., S. M. Sapuan, M. Jawaid, and N. Ismarrubie Zahari. 2017. Cassava/Sugar palm fiber reinforced cassava starch hybrid composites: physical, thermal and structural properties. International Journal of Biological Macromolecules 101: 75–83. Elsevier B.V. doi:10.1016/j.ijbiomac.2017.03.045.
- El Miri, N., K. Abdelouahdi, M. Zahouily, A. Fihri, A. Barakat, A. Solhy, and M. El Achaby. 2015. Bio‐nanocomposite films based on cellulose nanocrystals filled polyvinyl alcohol/chitosan polymer blend. Journal of Applied Polymer Science 132 (22):132 (22. doi:10.1002/app.42004.
- El-Wakil, N. A., E. A. Hassan, R. E. Abou-Zeid, and A. Dufresne. 2015. Development of wheat gluten/nanocellulose/titanium dioxide nanocomposites for active food packaging. Carbohydrate polymers 124: 337–46. Elsevier Ltd. doi:10.1016/j.carbpol.2015.01.076.
- Espitia, P. J. P., W. X. Du, R. de Jesús Avena-Bustillos, N. de Fátima Ferreira Soares, and T. H. McHugh. 2014. Edible films from pectin: Physical-mechanical and antimicrobial properties - a review. Food Hydrocolloids 35: 287–96. Elsevier Ltd. doi:10.1016/j.foodhyd.2013.06.005.
- Faruk, O., A. K. Bledzki, H. Peter Fink, and M. Sain. 2012. Biocomposites reinforced with natural fibers: 2000-2010. Progress in Polymer Science 37 (11):1552–96. Elsevier Ltd. doi:10.1016/j.progpolymsci.2012.04.003.
- Gangil, B., L. Ranakoti, S. Verma, T. Singh, and S. Kumar. 2020. Natural and synthetic fibers for hybrid composites. Hybrid Fiber Composites 1–15. doi:10.1002/9783527824571.ch1.
- Garavand, F., M. Rouhi, S. Hadi Razavi, I. Cacciotti, and R. Mohammadi. 2017. Improving the integrity of natural biopolymer films used in food packaging by crosslinking approach: A review. International Journal of Biological Macromolecules 104:687–707. doi:10.1016/j.ijbiomac.2017.06.093.
- García, M. A., M. N. Martino, and N. E. Zaritzky. 2000. Lipid addition to improve barrier properties of edible starch-based films and coatings. Journal of Food Science 65 (6):941–44. doi:10.1111/j.1365-2621.2000.tb09397.x.
- Gurunathan, T., S. Mohanty, and S. K. Nayak. 2015. A review of the recent developments in biocomposites based on natural fibres and their application perspectives. Composites Part A, Applied Science and Manufacturing 77:1–25. Elsevier Ltd. doi:10.1016/j.compositesa.2015.06.007.
- Hadidi, M., S. Jafarzadeh, M. Forough, F. Garavand, S. Alizadeh, A. Salehabadi, A. Mousavi Khaneghah, and S. Mahdi Jafari. 2022, September. Plant protein-based food packaging films; Recent advances in fabrication, characterization, and applications. Trends in Food Science & Technology 120:154–73. ( 2021 Elsevier Ltd). doi: 10.1016/j.tifs.2022.01.013.
- Haghighi, H., F. Licciardello, P. Fava, H. Wilhelm Siesler, and A. Pulvirenti. 2020, March. Recent advances on chitosan-based films for sustainable food packaging applications. Food Packaging and Shelf Life 26:100551. ( Elsevier). doi: 10.1016/j.fpsl.2020.100551.
- Haldorai, Y., J. Jin Shim, and K. Taek Lim. 2012. Synthesis of polymer-inorganic filler nanocomposites in supercritical CO 2. The Journal of Supercritical Fluids 71: 45–63. Elsevier B.V. doi:10.1016/j.supflu.2012.07.007.
- Höfer, R., and E. Ecosiris. 2012. Processing and performance additives for plastics. Polymer Science:A Comprehensive Reference 10: Elsevier B.V. doi:10.1016/B978-0-444-53349-4.00272-7.
- Hourston, D. J. 2010. Degradation of plastics and polymers. Shreir’s Corrosion 2:2369–86. doi:10.1016/B978-044452787-5.00116-5.
- Hulleman, S. H. D., F. H. P. Janssen, and H. Feil. 1998. The role of water during plasticization of native starches. Polymer 39 (10):2043–48. doi:10.1016/S0032-3861(97)00301-7.
- Jafarzadeh, S., A. Karim Alias, F. Ariffin, and S. Mahmud. 2018. Physico-mechanical and microstructural properties of semolina flour films as influenced by different sorbitol/glycerol concentrations. International Journal of Food Properties 21 (1):983–95. Taylor & Francis. doi:10.1080/10942912.2018.1474056.
- Jun Feng, S. 2017. Biodegradable soy protein isolate/poly(vinyl alcohol) packaging films. Handbook of Composites from Renewable Materials 1–8. doi:10.1002/9781119441632.ch103.
- Kamal, M. R., and V. Khoshkava. 2015. Effect of Cellulose Nanocrystals (CNC) on rheological and mechanical properties and crystallization behavior of PLA/CNC nanocomposites. Carbohydrate Polymers 123: 105–14. Elsevier Ltd. doi:10.1016/j.carbpol.2015.01.012.
- Kashiri, M., J. P. Cerisuelo, I. Domínguez, G. López-Carballo, P. Hernández-Muñoz, and R. Gavara. 2016. Novel antimicrobial zein film for controlled release of Lauroyl Arginate (LAE). Food Hydrocolloids 61: 547–54. Elsevier Ltd. doi:10.1016/j.foodhyd.2016.06.012.
- Khalid, S., L. Yu, M. Feng, L. Meng, Y. Bai, A. Ali, H. Liu, and L. Chen. 2018, August. Development and characterization of biodegradable antimicrobial packaging fi lms based on polycaprolactone, starch and pomegranate rind hybrids. Food Packaging and Shelf Life 18:71–79. ( Elsevier). doi:10.1016/j.fpsl.2018.08.008.
- Khan, R. A., S. Salmieri, D. Dussault, J. Uribe-Calderon, M. R. Kamal, A. Safrany, and M. Lacroix. 2010. Production and properties of nanocellulose-reinforced methylcellulose-based biodegradable films. Journal of Agricultural and Food Chemistry 58 (13):7878–85. doi:10.1021/jf1006853.
- Kumar, N., P. Kaur, and S. Bhatia. 2017. Advances in bio-nanocomposite materials for food packaging: A review. Nutrition and Food Science 47 (4):591–606. doi:10.1108/NFS-11-2016-0176.
- Lara, B. R. B., A. C. M. A. Araújo, M. Vilela Dias, M. Guimarães, T. Amorim Santos, L. Fonseca Ferreira, and S. Vilela Borges. 2019, June. Morphological, mechanical and physical properties of new whey protein isolate/polyvinyl alcohol blends for food flexible packaging. Food Packaging and Shelf Life 19:16–23. ( 2018 Elsevier). doi: 10.1016/j.fpsl.2018.11.010.
- Lara, B. R. B., P. S. de Andrade, M. Guimarães Junior, M. Vilela Dias, and L. Ayra Pereira Alcântara. 2021. Novel whey protein isolate/polyvinyl biocomposite for packaging: Improvement of mechanical and water barrier properties by incorporation of nano-silica. Journal of Polymers and the Environment 29 (8):2397–408. Springer US. doi:10.1007/s10924-020-02033-x.
- Lee, C. H., S. M. Sapuan, R. A. Ilyas, S. H. Lee, and A. Khalina. 2020. Development and processing of pla, pha, and other biopolymers. In Advanced Processing, Properties, and Applications of Starch and Other Bio-Based Polymers, Elsevier Inc. doi:10.1016/b978-0-12-819661-8.00005-6.
- Lee, S. H., and S. Wang. 2006. Biodegradable polymers/bamboo fiber biocomposite with bio-based coupling agent. Composites Part A, Applied Science and Manufacturing 37 (1):80–91. doi:10.1016/j.compositesa.2005.04.015.
- Liu, F., B. Sen Chiou, R. J. Avena-Bustillos, Y. Zhang, Y. Li, T. H. McHugh, and F. Zhong. 2017. Study of combined effects of glycerol and transglutaminase on properties of gelatin films. Food Hydrocolloids 65:1–9. Elsevier Ltd. doi:10.1016/j.foodhyd.2016.10.004.
- Lorevice, M. V., C. Gomide Otoni, M. R. de Mourra, and L. Henrique Capparelli Mattoso. 2016. Chitosan nanoparticles on the improvement of thermal, barrier, and mechanical properties of high- and low-methyl pectin films. Food Hydrocolloids 52: 732–40. Elsevier Ltd. doi:10.1016/j.foodhyd.2015.08.003.
- Mahmoodi, A., S. Ghodrati, and M. Khorasani. 2019. High-strength, low-permeable, and light-protective nanocomposite films based on a hybrid nanopigment and biodegradable PLA for food packaging applications. ACS Omega 4 (12):14947–54. doi:10.1021/acsomega.9b01731.
- Malathi, A. N., K. S. Santhosh, and N. Udaykumar. 2014. Recent Trends of Biodegradable Polymer. Current Trends in Technology and Sciences 3 (1):1–8.
- Mármol, G., C. Gauss, and R. Fangueiro. 2020. Potential of cellulose microfibers for PHA and PLA biopolymers reinforcement. Molecules 25:20. doi:10.3390/molecules25204653.
- Marrazzo, C., E. Di Maio, and S. Iannace. 2007. Foaming of synthetic and natural biodegradable polymers. Journal of Cellular Plastics 43 (2):123–33. doi:10.1177/0021955X06073214.
- Mochane, M. J., T. C. Mokhena, T. H. Mokhothu, A. Mtibe, E. R. Sadiku, S. S. Ray, I. D. Ibrahim, and O. O. Daramola. 2019. Recent progress on natural fiber hybrid composites for advanced applications: A review. express polymer letters 13 (2):159–98. doi:10.3144/expresspolymlett.2019.15.
- Modi, S., K. Koelling, and Y. Vodovotz. 2011. Assessment of PHB with varying hydroxyvalerate content for potential packaging applications. European Polymer Journal 47 (2):179–86. Elsevier Ltd. doi:10.1016/j.eurpolymj.2010.11.010.
- Monika, P. A. K., S. M. Bhasney, P. Bhagabati, and V. Katiyar. 2018. Effect of dicumyl peroxide on a poly(Lactic Acid) (PLA)/Poly(Butylene Succinate) (PBS)/Functionalized chitosan-based nanobiocomposite for packaging: A reactive extrusion study. ACS Omega 3 (10):13298–312. doi:10.1021/acsomega.8b00907.
- Mose, B. R., and S. Moffat Maranga. 2011. A review on starch based nanocomposites for bioplastic materials. Formerly Part of Journal of Materials Science and Engineering 1:239–45.
- Müller, R. 2002. Biodegradability of polymers: Regulations and methods for testing. Biopolymers Online 365–74. doi:10.1002/3527600035.bpola012.
- Müller, C. M. O., J. Borges Laurindo, and F. Yamashita. 2011. Effect of nanoclay incorporation method on mechanical and water vapor barrier properties of starch-based films. Industrial Crops and Products 33 (3):605–10. doi:10.1016/j.indcrop.2010.12.021.
- Muscat, D., B. Adhikari, R. Adhikari, and D. S. Chaudhary. 2012. Comparative study of film forming behaviour of low and high amylose starches using glycerol and xylitol as plasticizers. Journal of Food Engineering 109 (2):189–201. Elsevier Ltd. doi:10.1016/j.jfoodeng.2011.10.019.
- Mutalikdesai, S., A. Hadapad, S. Patole, and G. Hatti. 2018. Fabrication and Mechanical Characterization of Glass fibre reinforced Epoxy Hybrid Composites using Fly ash/Nano clay/Zinc oxide as filler. IOP Conference Series: Materials Science and Engineering 376:012061. doi:10.1088/1757-899X/376/1/012061.
- Nagarajan, V., A. K. Mohanty, and M. Misra. 2016. Perspective on Polylactic Acid (PLA) Based sustainable materials for durable applications: focus on toughness and heat resistance. ACS Sustainable Chemistry & Engineering 4 (6):2899–916. doi:10.1021/acssuschemeng.6b00321.
- Nandhavathy, G., S. Periyar Selvam, M. Mahesh Kumar, and E. Rotimi Sadiku. 2017. Optimization of pomegranate peel fibers reinforced with polyvinyl alcohol biocomposite film using response surface methodology. Rasayan Journal of Chemistry 10 (2):542–48. doi:10.7324/RJC.2017.1021724.
- Naveena, B., and A. Sharma. 2020. Review on properties of bio plastics for packaging applications and its advantages. International Journal of Current Microbiology and Applied Sciences 9 (5):1428–32. doi:10.20546/ijcmas.2020.905.163.
- Nuanmano, S., T. Prodpran, and S. Benjakul. 2015. Potential use of gelatin hydrolysate as plasticizer in fish myofibrillar protein film. Food Hydrocolloids 47:61–68. Elsevier Ltd. doi:10.1016/j.foodhyd.2015.01.005.
- Obasi, H. C., F. N. Onuoha, I. O. Eze, and S. C. Nwanonenyi. 2013, July. Effect of soil burial on properties of polypropylene (pp)/plasticized potato starch (pps) blends. The International Journal of Engineering and Science 2013:1813–2319. ( 2013). doi:10.1155/2013/326538.
- Pandey, J. K., H. Takagi, A. Norio Nakagaito, D. Ram Saini, and S. Hoon Ahn. 2012. An overview on the cellulose based conducting composites. Composites Part B: Engineering 43 (7):2822–26. Elsevier Ltd. doi:10.1016/j.compositesb.2012.04.045.
- Pawar, P. A., and A. H. Purwar. 2013. Biodegradable polymers in food packaging. American Journal of Engineering Research (05):151–64.
- Pellicer, E., D. Nikolic, J. Sort, M. Dolors Baró, F. Zivic, N. Grujovic, R. Grujic, and S. Pelemis. 2017. Advances in applications of industrial biomaterials. Advances in Applications of Industrial Biomaterials 1–214. doi:10.1007/978-3-319-62767-0.
- Prado, K. S., and M. A. S. Spinacé. 2019. Isolation and characterization of cellulose nanocrystals from pineapple crown waste and their potential uses. International Journal of Biological Macromolecules 122: 410–16. Elsevier B.V. doi:10.1016/j.ijbiomac.2018.10.187.
- Prathipa, R., C. Sivakumar, and B. Shanmugasundaram. 2018. Biodegradable polymers for sustainable packaging applications. International Journal of Mechanical Engineering and Technology 9 (6):293–303.
- Psomiadou, E., I. Arvanitoyannis, and N. Yamamoto. 1996. Edible films made from natural resources; microcrystalline cellulose (MCC), methylcellulose (MC) and corn starch and polyols—part 2. Carbohydrate Polymers 31 (4):193–204. doi:10.1016/S0144-8617(96)00077-X.
- Reichert, C. L., E. Bugnicourt, M. Beatrice Coltelli, P. Cinelli, A. Lazzeri, I. Canesi, F. Braca, B. M. Martínez, R. Alonso, L. Agostinis, et al. 2020. Bio-based packaging: materials, modifications, industrial applications and sustainability. Polymers. 12(7):1558. doi:10.3390/polym12071558.
- Robertson, G. L. 2004. Book Review: Food Packaging Technology. Packaging Technology and Science: An International Journal. 17(6):333–335. doi:10.1002/pts.655.
- Rogovina, S. Z. 2016. Biodegradable polymer composites based on synthetic and natural polymers of various classes. Polymer Science - Series C 58 (1):62–73. doi:10.1134/S1811238216010100.
- Rungsinee, S., and J. M. Krochta. 2005. Plasticizers in edible films and coatings. Innovations in Food Packaging 403–33. doi:10.1016/B978-012311632-1/50055-3.
- Saba, N., P. Md Tahir, and M. Jawaid. 2014. A review on potentiality of nano filler/natural fiber filled polymer hybrid composites. Polymers 6 (8):2247–73. doi:10.3390/polym6082247.
- Salman, S. D. 2019. Partial replacement of synthetic fibres by natural fibres in hybrid composites and its effect on monotonic properties. Journal of Industrial Textiles 51:258–76. doi:10.1177/1528083719878843.
- Sanjay, M. R., P. Madhu, M. Jawaid, P. Senthamaraikannan, S. Senthil, and S. Pradeep. 2018. Characterization and properties of natural fiber polymer composites: A comprehensive review. Journal of Cleaner Production 172: Elsevier B.V. doi:10.1016/j.jclepro.2017.10.101.
- Sessini, V., M. P. Arrieta, J. Maria Kenny, and L. Peponi. 2016. Processing of edible films based on nanoreinforced gelatinized starch. Polymer Degradation and Stability 132:157–68. doi:10.1016/j.polymdegradstab.2016.02.026.
- Shariatinia, Z., and K. Fasihozaman-Langroodi. 2019. Biodegradable polymer nanobiocomposite packaging materials. Trends in Beverage Packaging Elsevier Inc. doi:10.1016/b978-0-12-816683-3.00008-6.
- Sharmin, N., R. A. Khan, S. Salmieri, D. Dussault, and M. Lacroix. 2012. “Fabrication and characterization of biodegradable composite films made of using poly (caprolactone) reinforced with chitosan,” 698–705. doi:10.1007/s10924-012-0431-8.
- Shen, Z., and D. Pascal Kamdem. 2015. Development and characterization of biodegradable chitosan films containing two essential oils. International Journal of Biological Macromolecules 74: 289–96. Elsevier B.V. doi:10.1016/j.ijbiomac.2014.11.046.
- Siracusa, V. 2012. Food packaging permeability behaviour: A report. International Journal of Polymer Science 2012:1–11. 2012. doi:10.1155/2012/302029.
- Siracusa, V., P. Rocculi, S. Romani, and M. Dalla Rosa. 2008. Biodegradable polymers for food packaging: A review. Trends in Food Science & Technology 19 (12):634–43. Elsevier Ltd. doi:10.1016/j.tifs.2008.07.003.
- Slavutsky, A. M., and M. A. Bertuzzi. 2014. Water barrier properties of starch films reinforced with cellulose nanocrystals obtained from sugarcane bagasse. Carbohydrate Polymers 110: 53–61. Elsevier Ltd. doi:10.1016/j.carbpol.2014.03.049.
- Souza, A., R. Benze, E. Ferrão, C. Ditchfield, A. Coelho, and C. Tadini2012. Cassava starch biodegradable films: Influence of glycerol and clay nanoparticles content on tensile and barrier properties and glass transition temperature. LWT - Food Science and Technology 46 (1):110–17. Elsevier Ltd. doi:10.1016/j.lwt.2011.10.018.
- Srivastava, K. R., M. Kumar Singh, P. Kumar Mishra, and P. Srivastava. 2019. Pretreatment of banana pseudostem fibre for green composite packaging film preparation with polyvinyl alcohol. Journal of Polymer Research 26 (4):4. doi:10.1007/s10965-019-1751-3.
- Suardana, N. P. G., M. S. Ku, and J. Kyoo Lim. 2011. Effects of diammonium phosphate on the flammability and mechanical properties of bio-composites. Materials & Design 32 (4):1990–99. Elsevier Ltd. doi:10.1016/j.matdes.2010.11.069.
- Vásconez, M. B., S. K. Flores, C. A. Campos, J. Alvarado, and L. N. Gerschenson. 2009. Antimicrobial activity and physical properties of chitosan-tapioca starch based edible films and coatings. Food Research International 42 (7):762–69. Elsevier Ltd. doi:10.1016/j.foodres.2009.02.026.
- Vieira, M. G. A., M. Altenhofen Da Silva, L. Oliveira Dos Santos, and M. Masumi Beppu. 2011. Natural-based plasticizers and biopolymer films: A review. European Polymer Journal 47 (3):254–63. Elsevier Ltd. doi:10.1016/j.eurpolymj.2010.12.011.
- Vroman, I., and L. Tighzert. 2009. Biodegradable Polymers. Materials 2 (2):307–44. doi:10.3390/ma2020307.
- Wakai, M., and E. Almenar. 2015. Effect of the presence of montmorillonite on the solubility of whey protein isolate films in food model systems with different compositions and PH. Food Hydrocolloids 43:612–21. Elsevier Ltd. doi:10.1016/j.foodhyd.2014.07.022.
- Wang, S., A. Lu, and L. Zhang. 2016. Recent advances in regenerated cellulose materials. Progress in Polymer Science 53:169–206. Elsevier Ltd. doi:10.1016/j.progpolymsci.2015.07.003.
- Wang, Z., Z. Yao, J. Zhou, M. He, Q. Jiang, A. Li, S. Li, M. Liu, S. Luo, and D. Zhang. 2019. Improvement of polylactic acid film properties through the addition of cellulose nanocrystals isolated from waste cotton cloth. International Journal of Biological Macromolecules 129:878–86. Elsevier B.V. doi:10.1016/j.ijbiomac.2019.02.021.
- Wihodo, M., and C. I. Moraru. 2013. Physical and chemical methods used to enhance the structure and mechanical properties of protein films: Areview. Journal of Food Engineering 114 (3):292–302. doi:10.1016/j.jfoodeng.2012.08.021.
- Xu, Q., C. Chen, K. Rosswurm, T. Yao, and S. Janaswamy. 2016. A facile route to prepare cellulose-based films. Carbohydrate Polymers 149:274–81. Elsevier Ltd. doi:10.1016/j.carbpol.2016.04.114.
- Yalcin, B., M. Cakmak, A. Hakan Arkin, B. Hazer, and B. Erman. 2006. Control of optical anisotropy at large deformations in PMMA/Chlorinated-PHB (PHB-Cl) blends: mechano-optical behavior. Polymer 47 (24):8183–93. doi:10.1016/j.polymer.2006.09.051.
- Yang, Z. Y., W. Jun Wang, Z. Qiang Shao, H. Dong Zhu, Y. -H. Li, and F. Jun Wang. 2013. The transparency and mechanical properties of cellulose acetate nanocomposites using cellulose nanowhiskers as fillers. Cellulose 20 (1):159–68. doi:10.1007/s10570-012-9796-z.
- Yoksan, R., and S. Chirachanchai. 2010. Silver nanoparticle-loaded chitosan-starch based films: fabrication and evaluation of tensile, barrier and antimicrobial properties. Materials Science and Engineering: C 30 (6):891–97. Elsevier B.V. doi:10.1016/j.msec.2010.04.004.
- Yuvaraj, D., J. Iyyappan, R. Gnanasekaran, G. Ishwarya, R. P. Harshini, V. Dhithya, M. Chandran, V. Kanishka, and K. Gomathi. 2021, September. Heliyon advances in bio food packaging – an overview. Heliyon 7 (9):e07998. Elsevier Ltd. doi: 10.1016/j.heliyon.2021.e07998.
- Zafar, R., K. Mahmood Zia, S. Tabasum, F. Jabeen, A. Noreen, and M. Zuber. 2016. Polysaccharide based bionanocomposites, properties and applications: A review. International Journal of Biological Macromolecules 92: 1012–24. Elsevier B.V. doi:10.1016/j.ijbiomac.2016.07.102.
- Zeng, A., Y. Wang, D. Li, J. Guo, and Q. Chen. 2020. Preparation and Antibacterial Properties of Polycaprolactone/Quaternized Chitosan Blends. Chinese Journal of Chemical Engineering 32:462–71. doi:10.1016/j.cjche.2020.10.001.
- Zhai, M., L. Zhao, F. Yoshii, and T. Kume. 2004. Study on antibacterial starch/chitosan blend film formed under the action of irradiation. Carbohydrate Polymers 57 (1):83–88. doi:10.1016/j.carbpol.2004.04.003.