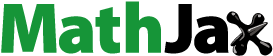
ABSTRACT
Bio-composites were prepared by incorporating broom grass, fishtail palm, sansevieria fibers as reinforcement in unsaturated polyester resin using hand lay-up method. The thermo physical and fire properties of bio-composites has been examined by varying the fiber content (0 to 39 wt. %) and temperature (30–120°C). The thermal insulation and heat storage capability of samples was assessed using guarded heat flow meter and differential scanning calorimeter. The experimental results reveal that, as the weight fraction of fiber increased, the insulation capability of composites increased, whereas it decreased with the temperature. The response of specific heat and thermal diffusivity of composites with temperature was analyzed. Temperature distribution and heat transfer through the composite materials was computed using ANSYS fluent solver. The rate of heat transfer through the fishtail palm fiber composite is 14.02% lesser than glass fiber composite. Cone calorimeter was used to measure fire behavior of the samples and the results reveal that the broom grass fiber composite material possesses better fire resistance characteristics against fire hazard. Morphological study of composites was performed with the help of Scanning Electron Microscopy (SEM) for the visualization of homogeneity of surfaces. Developed bio-composites are the potential materials to replace petrochemical-based products.
摘要
采用手工铺层法,将扫帚草、鱼尾棕、三叶草纤维作为不饱和聚酯树脂的增强材料,制备了生物复合材料. 通过改变纤维含量(0至39重量%)和温度(30至120°C),研究了生物复合材料的热物理性能和燃烧性能. 使用防护热流计和差示扫描量热计评估了样品的隔热和储热能力. 实验结果表明,随着纤维重量分数的增加,复合材料的绝缘性能提高,但随温度的升高而降低. 分析了复合材料的比热和热扩散率随温度的变化. 使用ANSYS fluent求解器计算了复合材料的温度分布和传热. 通过鱼尾棕榈纤维复合材料的传热速率比玻璃纤维复合材料低14.02%. 用锥形量热计测量了样品的火灾行为,结果表明扫帚草纤维复合材料具有更好的防火性能. 借助扫描电子显微镜(SEM)对复合材料进行了形态学研究,以显示表面的均匀性. 开发的生物复合材料是替代石化产品的潜在材料.
Introduction
Natural fiber composites are the promising materials to replace petroleum-based materials in electrical and electronic, automotive, aeronautical, building, and construction industries. These materials are cheap, eco-friendly, biodegradable, light weight, and versatile. Because of the advantages of natural fiber composites, the stringent rules imposed by several governments across the globe, the demand for green composite materials attracts the focus of the researchers to develop new materials. The straw and reed hybrid composite and sea grass fiber-based composites are the new eco-friendly materials for thermal insulation applications (Aliaksandr, Florindo, and Boltrushevich Citation2022; Mayer et al. Citation2022). Rajesh, Ratna Prasad, and Gupta (Citation2018) studied structural behavior of elephant grass, sisal, and jute fiber-based materials and summarized that the elephant grass composite exhibited better mechanical properties than other two materials. Flexural and impact strength of alkali-treated short jute fiber-reinforced composite was greater than the untreated composites (Rajesh, Ratna Prasad, and Gupta Citation2016). Sabarinathan et al. (Citation2020) studied the structural behavior of fishtail palm fiber and summarized that this material is the promising material for structural applications. The mechanical properties of flax, date palm, and kenaf fibers were investigated and reported that specific strength of natural fibers was higher than glass fiber (Al-Sulaiman Citation2002; Malik, Ahmad, and Gunister Citation2021; van den Oever, Bos, and van Kemenade Citation2000).
Ramlee et al. (Citation2019) and Ramlee, Naveen, and Jawaid (Citation2021) studied the thermal insulation capacity of oil palm empty fruit bunch and sugarcane bagasse fibers and concluded that safe, renewable, economic, and sustainable energy saving materials are the alternatives to wood. Abu-Jdayil et al. (Citation2019) have noticed that the conductivity varied with temperature (0 to 60℃) from 0.166 to 0.17 W/m/K for date pit-polyester composite and 0.366 to 0.456 W/m/K for banana-epoxy composite. Takagi et al. (Citation2007) adopted the hot wire method to measure thermal conductivity of bamboo-Poly lactic acid (PLA) composite and concluded that thermal conductivity of bamboo-PLA composite is smaller than glass/carbon fiber-reinforced composites. Kim et al. (Citation2006) measured the thermal conductivity of hemp, kenaf, flax, and sisal fiber/polypropylene composites. The experimental data indicate that the thermal conductivity of composites is in the range of 0.05–0.07 W/m/K at 48.5% fiber content. Kim, Dutta, and Bhattacharyya (Citation2018) reported that the flammability and thermal decomposition of the composites is a prerequisite to choose suitable composites. High flammability of bio-fiber composites is the main disadvantage for various applications. Lee, Salit, and Hassan (Citation2014) studied the fire behavior of kenaf/PLA material and concluded that the heat release rates considerably decreased with kenaf fiber content and emphasized that fire properties are significant factors for the composites in terms of safety. Earlier researchers Ducoulombier and Lafhaj (Citation2017) and Lamrani et al. (Citation2017) studied the fire behavior and smoke generation of bio-composites by varying the fiber content. The bonding between hydrophobic biopolymers and hydrophilic bio-fibers and low fire retardant are the drawbacks of green composites (Akampumuza et al. Citation2017). Vahedi et al. (Citation2022) are analyzed the thermo physical properties and char formation characteristics of sandwich bridge decks at 850℃. Thermo physical properties depend on the combustion, direction of heat flow and density and concluded that the charring rate in the direction of reinforcement is 1.5 times higher than transverse direction. Flammability is one of the significant fire properties of material and that often limit the application of the composites (Kozłowski and Władyka-Przybylak Citation2008). The HRR decreased with the addition of kenaf and wool with polypropylene (Bhattacharyya et al. Citation2015). Natural fibers mainly consist of cellulose, lignin, and other substances. Cellulose is the main component of fiber and it offers good strength, stiffness, and structural stability (Fiore, Scalici, and Valenza Citation2014). The properties of natural fibers are summarized in the . It was noticed that the cellulose content of fibers considered in this study is in the range of 70 to 80% higher than the other natural fibers (Pratim Das and Chaudhary (Citation2021). The natural fibers with high lignin content exhibit good fire-resistance properties (Fatima and Mohanty Citation2011). Thermal conductivity of natural fiber-reinforced composites depends on the pore structure, density, humidity, and temperature (Koru, Buyukkaya, and Kan Citation2022). Muthu Kumar et al. (Citation2021) developed the needle punched nonwoven fabrics from textile waste for thermal insulation applications and noticed that thermal insulation of composite was increased with the porosity of nonwovens. The thermal conductivity of fibers aligned in longitudinal and transverse direction was investigated and reported that the fibers placed in transverse direction exhibited better insulation behavior (Ioannou, Hodzic, and Gitman Citation2017).
Table 1. Properties of natural fibers.
Several investigators studied the structural behavior of the natural fiber-reinforced composites. Nevertheless, the limited literature is available on thermophysical and fire behavior of bio-fiber composites. A comprehensive study on thermophysical and fire properties of bio-fiber composites does not exist in the literature to select suitable bio-composite material for different applications. Therefore, in this research work, comprehensive study on thermophysical and fire behavior of broom grass, fishtail palm, sansevieria fiber-reinforced composites was carried out and verified the potential use for thermal insulation applications.
Materials and methods
Preparation of composites
Broom grass, fishtail palm, and sansevieria fibers were extracted using water retting method (Mohan Rao and Mohana Rao Citation2017). Extracted fibers were dried under sun light for a period of two days for the removal of moisture content. The preparation of the composites and tests carried out in this study is shown in . Cobalt (1.5%) and Methyl Ethyl Ketone Peroxide (1.5%) are added to resin as accelerator and catalyst in the preparation of the matrix. Composite samples are prepared using Hand lay-up method. Resin is used as matrix and fibers are used as reinforcement in the preparation of composites. Releasing agent is applied on the surface of the mold to avoid sticking of samples to the mold. The mold is filled with the alternate layer of matrix and fibers. Pressure is applied on the filled mold using the rollers for the removal of entrapped air and is allowed to cure for a period of 24 h under the compressive load of 50 kN. The composite is taken out from the mold and cut it into the test samples as per ASTM standard size of 100 mm × 100 mm × 10 mm for testing the fire properties and a circular disc of 50 mm diameter with 10 mm thickness for the measurement of thermal conductivity. The prepared fibers and samples are shown in .
Measurement of thermophysical properties
Thermal conductivity (W/m/K) of the samples was measured according to the procedure adopted in ASTM E1530-99 standards. Thermal conductivity meter (DTC 300 model: TA instruments) shown in is used for the measurement of thermal conductivity of composite samples under steady-state condition. The pressure applied on the specimen is 0.7 bar to maintain the contact between the sample and the guard surface. The thermal conductivity was measured in the temperature range of 30 to 120℃. EquationEquations (1)(1)
(1) –(Equation3
(3)
(3) ) are used for the calculation of thermal conductivity. In these equations, q is the heat flux (W/m2), L is the thickness of the sample (m), and R is the resistance of sample (m2 K/W).
A differential scanning calorimeter (DSC) is used to test the specific heat of the composites. The density of the samples was measured using picnometer. The diffusivity of the composites was calculated using EquationEquation (4)(4)
(4) .
Measurement of fire properties
A Cone calorimeter is used for the measurement of fire properties of the composites per ASTM E 1354 standards. The significantly measured fire properties in this research work are the Time to ignition, Time to flame out, Heat release rate, Peak heat release rate, Time to Peak heat release, Total heat release, Mass loss rate, Effective heat of combustion, Average Carbon monoxide yield (kg/kg), Average Carbon dioxide yield (kg/kg), Total smoke release, and Maximum average heat rate emission.
Results and discussion
Thermal characterization of composites
The conductivity of three materials at different weight fraction fiber is shown in . It was noticed that, as the fiber content increases, the insulation capability of composite increased. This increase is due to the porosity of fiber. The thermal conductivity of air (0.026 W/m/K) is lower than the natural fibers. The presence of air in the pores of fiber increases with the content of fiber, therefore conductivity of the composites is decreased (Liu et al. Citation2012; Mia et al. Citation2017).
The experimental values of thermal conductivity of fishtail palm, sansevieria, and broom grass fiber composites are 0.163 W/m/K, 0.183 W/m/K, and 0.196 W/m/K, respectively, at weight fraction of fiber 0.39. The insulation capability of fishtail palm fiber composite is 16.8% higher than broom grass fiber composite. Fishtail palm composite could be considered as energy saving material in automotive and building industries. At weight fraction of fiber 0.39, the response of conductivity against temperature is depicted in . The response of fishtail palm fiber composite is very less against temperature (300C to 1200C) and more for broom grass-based material. The conductivity of fishtail palm (0.176 W/m/K) is lowest and broom grass (0.198 W/m/K) is highest at 1200C. Thermal conductivity of sansevieria fiber composite is less sensitive to temperature compared to the other composites. The thermal response of three materials is depicted in .
Material stores large amount of heat at higher value of Cp. The heat absorbed by the materials increased against temperature due to the molecules vibration. The intensity of vibrations was increased against temperature (Qiu et al. Citation2019, Citation2020, Citation2021). Among the three materials tested, Cp of broom grass material is maximum at room temperature and high temperature. Hence, it is recommended for heat storage applications. Specific heat of broom grass composite is 40.65%, 18.5% greater than sansevieria and fishtail palm fiber-based materials. The specific heat of broom fiber composite at 300C, 600C, 900C, and 1200C are 1493, 1521, 1586, and 1639 J/kgK, respectively, and it is increased with the temperature. Broom grass composite is better material compared to other two composites for energy storage applications due to its higher specific heat capacity. Thermal diffusivity is a measure of the rate of heat penetration into the material with respect to change in temperature and it is a significant parameter. The effect of temperature on thermal diffusivity is shown in . Thermal diffusivity of fishtail palm fiber composite is lowest (0.86 × 10−7m2/s) compared to other composites. Hence, it is recommended to select the fishtail palm composite material for heating, ventilation, and air-conditioning applications. Thermal properties of three materials are given in . The density of the materials considered in this study is in the range of 1095 to 1312 kg/m3. Hence, these materials are suitable, where high specific strength is important. The comparative study reveals that the fishtail palm fiber material is the promising material to replace synthetic-based materials for thermal insulation applications.
Table 2. Thermo-physical properties of composites at 0.39 volume fraction.
Computational analysis on composites
A rectangular plate of size 1.82 × 0.91 × 0.02 m was created in ANSYS workbench and hexahedral mesh generated in plate with 56,645 elements. The plate dimensions and mesh generated is shown in .
ANSYS Fluent solver was used for computational analysis. The measured density, k, and Cp of the composites were used as an input data in computational analysis. Glass and banana fiber-reinforced composite material properties have been taken from open literature and wood material properties were taken from the fluent data base. Energy equation was enabled in solver. Convective boundary condition was defined for inner surface of the plate exposed to conditioned air at 25℃. Natural convective heat transfer coefficient considered is 6 W/m2K for analysis. Wall boundary condition was defined for outer surface of the plate and assumed that this wall is at a temperature of 45℃. The remaining surfaces of the plate are considered as adiabatic wall for simulation. The contours of temperature on plate are shown in and the computed temperature at the inner surface of the plate is of 37℃. Total surface heat flux through the plate was computed from the software for each material for the defined boundary conditions and the data are given in .
Table 3. Heat transfer through the composites.
Among all the composites, the total surface heat flux is relatively lowest for fishtail palm composite. This analogy emphasizes that fishtail palm composite thermal insulation was good and the experimental data are conveying the same. Temperature distribution along the plate thickness for different fiber-reinforced composites and wood is plotted in .
The wall temperature on conditioned air side is lowest for fishtail palm fiber composite and lower temperature was observed across the thickness of plate compared with other composites. The temperature distribution of the composites studied is very close to the wood. Therefore, these materials can be used in place of wood for energy-saving applications. The surface heat flux of glass material and fishtail composite is 78.85 W/m2 and 69.1 W/m2, respectively. Therefore, insulation capability of the tested composites is better than the glass fiber composite and the synthetic composites can be replaced by the eco-friendly developed composites in this study. The developed fibers are inexpensive and light weight. The density of the composites is in the range of 1095 to 1312 kg/m3 whereas the density of glass fiber composite is 1760 kg/m3. The cost of the glass fiber is 1–2 $/kg but the fibers used for the development of composites are extracted from waste plants and the preparation cost for the fibers is in the range of 0.13 to 0.2 $.
Fire properties of composites
Fire behavior of bio composites was presented in . TTI is an important fire property because it defines how quickly combustion of composite will occur when exposed to a heat source. As per TTI results, the broom grass and fishtail palm fiber composites begin to catch fire slower than sansevieria. The pHRR of the broom grass, fishtail palm, and sansevieria fiber-reinforced composites was reduced by 36.4%, 35.6%, and 25.7% than pure resin. FIGRA is the ratio of pHRR to time to reach pHRR. Higher magnitude of FIGRA of material indicates that it easily catches the fire. FPI is the ratio of TTI to pHRR. Higher values of FPI indicate that the fire risk of composites is less. Broom grass composite performance is 37.8% higher than sansevieria composite. The broom fiber material MAHRE magnitude is less. EHC is less for broom fiber material (19.92 MJ/kg). SEA reflects the quantity production of smoke during the combustion process. The reduction of SEA of sansevieria fiber composite is 7.8% less than the matrix, and it produces less quantity of smoke. The comparative study reveals that fishtail-based material is appropriate fire retarding material. More amount of smoke generated during the process of combustion lead to create breathing issues to the human beings. TSR is lowest (12964 m2/m2) for broom grass fiber composite. Broom grass fiber composite emits minimum CO (0.0328 kg/kg). The broom grass-based material is the better material for fire safety.
Table 4. Comparison of fire properties of different natural fiber composites.
Morphology study
The structure of the samples is examined using a VEGA3-TESCAN SEM with 15 kV of accelerating voltage. A layer of gold coating was applied on a specimen in vacuum chamber to increase image resolution and to avoid an electrostatic charge. The measured range of diameter and length of the fibers are given in . The structures of the fishtail palm, sansevieria, and broom grass composites are illustrated in . It was observed that the fibers are properly distributed and homogenized in the matrix. More pores are observed in fishtail palm compared with other two composites. The presence of these pores enhances the thermal insulation of the composite materials.
Conclusions
Energy saving, biodegradable, eco-friendly, cheap, lightweight, sustainable broom grass, fishtail palm, and sansevieria fiber-reinforced composites were developed. The effect of fiber content and temperature on thermo physical properties of the composites was studied and fire characteristics of the composites were elucidated. This systematic study reveals that the thermal insulation of broom grass, fishtail palm, and sansevieria fiber-based materials is improved with the weight percentage of fiber. At maximum volume fraction, thermal conductivity of fishtail composite is lowest (0.0163 W/m/K). All three developed composites possess good thermal insulation characteristics and are suitable for energy-saving applications. The broom fiber-based composite is the best fire retardant material compared to other two materials. The composites studied in this research are suitable for industrial applications to save energy loss. The heat transfer through the composite plate made up of fishtail palm, broom grass, and sansevieria fiber reinforced composites is lower than glass fiber composite and close to the wood. This quantitative assessment builds up confidence to use these composites in place of wood and glass fiber composite.
Highlights
Computational analysis of composites
Development of eco-friendly sustainable energy saving natural fiber composites
Fishtail palm, broom grass, and sansevieria fibers are used as reinforcement
Investigation of thermo physical properties of natural fiber composites
Supplemental Material
Download Zip (70.7 KB)Acknowledgement
The authors are thankful to the management of V R Siddhartha Engineering College for providing the test facilities of the centre of excellence in composites.
Supplementary material
Supplemental data for this article can be accessed online at https://doi.org/10.1080/15440478.2022.2162653
Disclosure statement
No potential conflict of interest was reported by the authors.
References
- Abu-Jdayil, B., A. Mourad, W. Hittini, M. Hassan, and S. Hameed. 2019. Traditional, state-of-the-art and renewable thermal building insulation materials: An overview. Construction and Building Materials 214:709–14. doi:10.1016/j.conbuildmat.2019.04.102.
- Akampumuza, O., P. M. Wambua, A. Ahmed, and X. H. Qin. 2017. Review of the applications of biocomposites in the automotive industry. Polymer Composites 38 (11):2553–69. doi:10.1002/pc.23847.
- Al-Sulaiman, F. A. 2002. Mechanical properties of date palm fiber reinforced composites. Applied Composite Materials 9 (6):369–77. doi:10.1023/A:1020216906846.
- Aliaksandr, B., G. Florindo, and N. Boltrushevich. 2022. Thermal insulation material based on reed and straw fibres bonded with sodium silicate and rosin. Construction and Building Materials 352:129055. doi:10.1016/j.conbuildmat.2022.129055.
- Bhattacharyya, D., A. Subasinghe, and N. K. Kim. 2015. Chapter 4 natural fibers: Their composites and flammability characterizations. In Multifunctionality of polymer composites: Challenges and new solutions, ed. U. Breuer. Amsterdam: Elsevier. doi:10.1016/B978-0-323-26434-1.00004-0.
- Ducoulombier, L., and Z. Lafhaj. 2017. Comparative study of hygrothermal properties of five thermal insulation materials. Case Studies in Thermal Engineering 10:628–40. doi:10.1016/j.csite.2017.11.005.
- Fatima, S., and A. R. Mohanty. 2011. Acoustical and fire-retardant properties of jute composite materials. Applied Acoustics 72 (2–3):108–14. doi:10.1016/j.apacoust.2010.10.005.
- Fiore, V., T. Scalici, and A. Valenza. 2014. Characterization of a new natural fiber from Arundo donax L. as potential reinforcement of polymer composites. Carbohydrate Polymers 106:77–83. doi:10.1016/j.carbpol.2014.02.016.
- Ioannou, I., A. Hodzic, and I. M. Gitman. 2017. Numerical investigation of thermal and thermo-mechanical effective properties for short fibre reinforced composite. Applied Composite Materials 24 (5):999–1009. doi:10.1007/s10443-016-9569-1.
- Kim, N. K., S. Dutta, and D. Bhattacharyya. 2018. A review of flammability of natural fibre reinforced polymeric composites. Composites Science and Technology 162 (7):64–78. doi:10.1016/j.compscitech.2018.04.016.
- Kim, S. W., S. H. Lee, J. S. Kang, and K. H. Kang. 2006. Thermal conductivity of thermoplastics reinforced with natural fibers. International Journal of Thermophysics 27 (6):1873–81. doi:10.1007/s10765-006-0128-0.
- Koru, M., K. Buyukkaya, and M. Kan. 2022. The effect of orientation, and temperature on thermal conductivity in nettle fiber/polyester composites. International Journal of Thermophysics 43 (10):155. doi:10.1007/s10765-022-03079-w.
- Kozłowski, R., and M. Władyka-Przybylak. 2008. Flammability and fire resistance of composites reinforced by natural fibers. Polymers for Advanced Technologies 19 (6):446–53. doi:10.1002/pat.1135.
- Lamrani, M., N. Laaroussi, A. Khabbazi, M. Khalfaoui, M. Garoum, and A. Feiz. 2017. Experimental study of thermal properties of a new ecological building material based on peanut shells and plaster. Case Studies in Construction Materials 7:294–304. doi:10.1016/j.cscm.2017.09.006.
- Lee, C. H., M. S. Salit, and M. R. Hassan. 2014. A review of the flammability factors of kenaf and allied fibre reinforced polymer composites. Advances in Materials Science and Engineering 2014:1–8. doi:10.1155/2014/514036.
- Liu, K., H. Takagi, R. Osugi, and Z. Yang. 2012. Effect of lumen size on the effective transverse thermal conductivity of unidirectional natural fiber composites. Composites Science and Technology 72 (5):633–39. doi:10.1016/j.compscitech.2012.01.009.
- Malik, K., F. Ahmad, and E. Gunister. 2021. A review on the kenaf fiber reinforced thermoset composites. Applied Composite Materials 28 (2):491–528. doi:10.1007/s10443-021-09871-5.
- Mayer, A. K., A. Kuqo, T. Koddenberg, and C. Mai. 2022. Seagrass- and Wood-Based Cement Boards: A Comparative Study in Terms of Physico-Mechanical and Structural Properties. Composites Part A Applied Science and Manufacturing 156:106864. doi:10.1016/j.compositesa.2022.106864.
- Mia, R., M. A. Islam, B. Ahmed, and J. I. A. Mojumdar. 2017. Woolenization of jute fibre. European Scientific Journal 13 (30):314–26. doi:10.19044/esj.2017.v13n30p314.
- Mohan Rao, K. M., and K. Mohana Rao. 2017. Extraction and tensile properties of natural fibers: Vakka, date and bamboo. Composite Structures 77 (3):288–95. doi:10.1016/j.compstruct.2005.07.023.
- Muthu Kumar, N., G. Thilagavathi, S. Periasamy, and V. Vinoth. 2021. Development of needle punched Nonwovens from natural fiber waste for thermal insulation application. Journal of Natural Fibers. Advance online publication. doi: 10.1080/15440478.2021.1990175
- Vahedi, N., T. Carlos, P. Anastasios Vassilopoulos, J. R. Correia, and K. Thomas. 2022. Thermophysical properties of balsa wood used as core of sandwich composite bridge decks exposed to external fire. Construction and Building Materials 329:127164. doi:10.1016/j.conbuildmat.2022.127164.
- Pratim Das, P., and V. Chaudhary. 2021. Moving towards the era of bio fibre based polymer composites. Cleaner Engineering and Technology 4:100182. doi:10.1016/j.clet.2021.100182.
- Qiu, L., P. Guo, X. Yang, Y. Ouyang, Y. Feng, X. Zhang, J. Zhao, X. Zhang, and Q. Li. 2019. Coating-boosted interfacial thermal transport for carbon nanotube array nano-thermal interface materials. Journal carbon 145:725–33. doi:10.1016/j.carbon.2019.01.085.
- Qiu, L., X. Zhang, Z. Guo, and Q. Li. 2021. Interfacial heat transport in nano-carbon assemblies. Journal carbon 178:391–412. doi:10.1016/j.carbon.2021.02.105.
- Qiu, L., N. Zhu, Y. Feng, E. E. Michaelides, G. Żyła, D. Ing, X. Zhang, P. M. Norris, C. N. Markides, and O. Mahian. 2020. A review of recent advances in thermophysical properties at the nanoscale: From solid state to colloids. Physics Reports 843:1–80. doi:10.1016/j.physrep.2019.12.001.
- Rajesh, G., A. V. Ratna Prasad, and A. V. S. S. K. S. Gupta. 2016. Preparation and properties of successive alkali treated completely biodegradable short jute fiber reinforced PLA composites. Polymer Composites 37 (7):2160–70. doi:10.1002/pc.23395.
- Rajesh, G., A. V. Ratna Prasad, and A. V. S. S. K. S. Gupta. 2018. Mechanical and degradation properties of natural fiber reinforced PLA composites jute, sisal, and elephant grass. Polymer Composites 37 (7):1125–36. doi:10.1002/pc.24041.
- Ramlee, N. A., M. Jawaid, E. S. Zainudin, and S. A. Karim Yamani. 2019. Modification of oil palm empty fruit bunch and sugarcane bagasse biomass as potential reinforcement for composites panel and thermal insulation materials. International Journal of Biological Macromolecules 16 (1):175–88. doi:10.1007/s42235-019-0016-5.
- Ramlee, N. A., J. Naveen, and M. Jawaid. 2021. Potential of oil palm empty fruit bunch (OPEFB) and sugarcane bagasse fibers for thermal insulation application - a review. Construction and Building Materials 271:121519. doi:10.1016/j.conbuildmat.2020.121519.
- Sabarinathan, P., K. Rajkumar, V. E. Annamalai, and K. Vishal. 2020. Characterization on chemical and mechanical properties of silane treated fish tail palm fibres. International Journal of Biological Macromolecules 163:2457–64. doi:10.1016/j.ijbiomac.2020.09.159.
- Takagi, H., S. Kako, K. Kusano, and A. Ousaka. 2007. Thermal conductivity of PLA-bamboo fiber composites. Advanced Composite Materials 16 (4):377–84. doi:10.1163/156855107782325186.
- van den Oever, M. J. A., H. L. Bos, and M. J. J. M. van Kemenade. 2000. Influence of the physical structure of flax fibres on the mechanical properties of flax fibre reinforced polypropylene composites. Applied Composite Materials 7 (5/6):387–402. doi:10.1023/A:1026594324947.