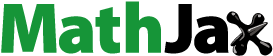
ABSTRACT
The acrylic acid treated rattan fiber reinforced epoxy (RF/Epoxy) composite has been fabricated by taking various weight percentages (5, 10, 15, 20, and 25 wt%) of fibers using hand layup followed by compression molding technique. The optimum fiber loading has been determined by regression analysis and it is found that 18 wt% of rattan fiber gives maximum tensile strength. The interaction of rattan fiber with epoxy matrix has been studied by Fourier transform infrared spectroscopy and X-ray diffraction. Scanning electron microscope (SEM) has been used to study the morphology of chemically modified rattan fiber and RF/Epoxy composite. The mechanical, thermal, and dynamic mechanical thermal properties of 18 wt% RF/Epoxy composite have been studied as per ASTM standards. From the results, it is observed that RF/Epoxy composite gives best properties at optimum (18 wt%) fiber loading. The maximum tensile strength and flexural strength of the composite are found to be 47.5 and 121 MPa, respectively, which is better in comparison to other natural fiber composites used for manufacturing different automobile body parts. Hence, it can be concluded that 18 wt% RF/Epoxy composite can be considered as a potential candidate for automotive body parts.
摘要
丙烯酸处理的藤纤维增强环氧树脂(RF/环氧树脂)复合材料是通过采用手工叠层和压缩模塑技术,以不同重量百分比(5、10、15、20、25重量%)的纤维制备的. 通过回归分析确定了最佳纤维负荷,发现18 wt%的藤纤维具有最大的拉伸强度. 用FTIR和XRD研究了藤纤维与环氧树脂基体的相互作用. 利用扫描电子显微镜(SEM)研究了化学改性藤纤维和RF/环氧树脂复合材料的形态. 根据 ASTM 标准研究了18 wt%RF/环氧树脂复合材料的机械、热和动态机械热性能. 从结果中观察到,RF/环氧树脂复合材料在最佳(18 wt%)纤维负载下具有最佳性能. 发现复合材料的最大拉伸强度和弯曲强度分别为47.5MPa和121MPa,这与用于制造不同汽车车身部件的其他天然纤维复合材料相比更好. 因此,可以得出结论,18 wt%的 RF/环氧树脂复合材料可以被视为汽车车身部件的潜在候选材料.
Introduction
Polymer-based composites are playing a vital role in important applications for the last few decades. These materials are emerging rapidly as the prospective substitute to the metal or ceramic based materials in a number of applications including automotive, aerospace, nautical, sporting goods, and electrical and electronic industries. Among various composite materials, recently natural fiber reinforced polymer composites are attracting research communities because of certain advantages such as low cost, low density, easy availability, low energy content, recyclability, and above all eco-friendly (Al-Oqla et al. Citation2016). Besides that recently natural fibers combined with biodegradable polymers have been used to develop bio-composites (Greco et al. Citation2013; Scaffaro et al. Citation2021) and characterized by complete degradation in soil or in composting processes in order to protect environment. In spite of certain limitations, the renewed interest in the use of natural fibers has resulted in a large number of modifications to compete with synthetic fibers for the development of automotive component products. From the study, it has been found that the use of natural fiber composite in automotive applications has increased many fold during the beginning 21st century as they show better crash behavior (Bledzki and Gassan Citation1999; Bledzki, Speber, and Frank Citation2002; Ceccarini and Angelini Citation2010; Mueller Citation2004; Timmins et al. Citation2011).
Among various natural fibers studied so far, rattan belongs to the subfamily of “Calamoideae” and is widely used in making chairs, clothing, medicines, handicraft, and arts and also its fruit is edible. From the studies (Rachchh, Ujeniya, and Misra Citation2014), it has been found that rattan fiber is emerging as cost effective and apparently ecologically superior substitutes to glass fibers in composites. Sahoo et al. (Citation2019) have shown that acrylic acid treated rattan fiber could be a potential candidate for composites because of its excellent mechanical and thermal properties. Further, in subsequent research, Sahoo et al. (Citation2021, Citation2021) have developed composites using short rattan fibers in different thermoplastic polymers, such as polyethylene terephthalate and polyvinyl alcohol and have studied their mechanical and thermal properties. Firdaus and Dachyar (Citation2018) have fabricated silane treated rattan fiber reinforced epoxy laminated composites and investigated their mechanical properties in terms of flexural, tensile strength, and thermal properties.
The utilization of lightweight, low cost natural fibers offers the potential to replace a large segment of the glass and mineral fibers in various automotive interior and exterior parts. Most of the automotive manufacturing companies have already experienced an increase in natural-fiber usage. Mercedes-Benz has used jute fiber reinforced epoxy composite in the door panels in its E-class vehicles back in 1996 (Suddell et al. Citation2005). Audi has used polyurethane reinforced with a mixed flax/sisal material (Mohanty et al. Citation2005) in the door trim panels of A2 midrange car. Further, Ford has used wheat straw as reinforcement for storage bin and inner lid in its 2010 Flex crossover vehicle, while BMW has used natural fiber mats and a unique thermosetting acrylic copolymer for the lower door panel (Stewart Citation2010) in its 7 Series sedan. As far as automotive application of rattan fiber based composite is concerned, Osoka, Onukwuli, and Kamalu (Citation2018) have found that out of some selected natural fiber in epoxy resin, rattan palm-epoxy composite has highest impact strength and can be used as substitute for low carbon steel for making auto body parts. Irawan and Sukania (Citation2018) in another study have found that the flexural strength of laminated composite made of woven rattan fiber in epoxy resin is comparable with the composite made from plastic material which can be used as automobile spoiler products. However, the study of composites made of short randomly oriented rattan fiber, reinforced in epoxy resin is scanty in literature. The aim of the present research is to develop short randomly oriented rattan fiber epoxy composite (RF/Epoxy composite) and to investigate its mechanical, thermal, and rheological properties which can be considered as a potential candidate for making automotive body parts.
Materials and methods
Materials
Epoxy resin (LY556) and hardener (HY951) have been purchased from CF COMPOSITES, New Delhi, India. The density of epoxy resin and hardener are 1.15 and 1 g/cm3, respectively (obtained from manufacturer’s test report). The chemicals such as sodium hydroxide, benzene, acrylic acid, etc., have been purchased from Sreemaa Chemicals Ltd. Kolkata, India. The stems of rattan have been collected from local agricultural resources (Sambalpur Region, Odisha, India).
Extraction of fibers
The stems of rattan have been allowed to soak in water for about 30 days to extract the fiber by retting process. The extracted fibers have been washed several times for the complete removal of debris and then dried at room temperature for 24 h to evacuate the dampness totally. These fibers are termed as untreated fibers.
Chemical treatments of rattan fibers
Sodium hydroxide treatment
The untreated fibers have been treated with 5% NaOH solution. After this the fibers have been rinsed in distilled water and then dried at a temperature of 80°C to remove moisture. This treatment has been conducted to activate the hydroxyl groups of the cellulose and lignin in the fiber. Surface modification of natural fibers with aqueous sodium hydroxide solution promotes the ionization of the hydroxyl group to alkoxide as per the following reaction (Agrawal et al. Citation2000):
Acrylic acid treatment
The alkaline pre-treated fibers have been first soaked in a solution of water and benzene (45:5 cm3) at a temperature of 85°C for 15 min. After that, the fibers have been treated with 0.3 M acrylic acid and rinsed first with an alkaline solution of NaOH and NaCl for 15 min and then with distilled water for 1 h. The resulting fibers have been oven dried at 70°C for 24 h. Acrylic acid (CH2=CHCOOH) is used to enhance the interfacial bonding between the fiber and matrix. CH2=CHCOOH reacts with the cellulosic hydroxyl groups of the fiber and provides more access of reactive cellulose macro-radicals to the polymerization medium. The carboxylic acids from coupling agents form the ester linkages with the cellulose hydroxyl groups. It reduces hydrophilic hydroxyl groups from the fiber structure and improves moisture resistance properties. The mechanism of reaction of acrylic acid with rattan fiber is presented in EquationEquation 2(2)
(2) (Sreekala, Kumaran, and Thomas Citation2002):
Fabrication of composites
The mold plate used for preparing short rattan fiber reinforced epoxy (RF/Epoxy) composite have been made from rectangular mild steel mold having dimension of 150 × 150 × 3 mm3 as shown in . The mold has been cleaned, dried, and sprayed with silicon (as releasing agent) before applying the uncured epoxy resin mixture. The untreated and acrylic acid treated rattan fibers have been cut into an approximate size of 2–3 mm. The homogenous mixture has been prepared by mixing epoxy resin and hardener in the ratio of 10:1 by mechanical stirrer. Then, the resin mixture have been thoroughly mixed with rattan fiber in different weight percentages (5, 10, 15, 20, and 25 wt%) to fabricate composite specimens by hand layup followed by compression molding technique in a compression molding machine having model HYPR−30T (Soumya Technocrats, GIDC, Gujarat, India) with capacity of 30 ton. The whole mixture has been poured into the mold and kept on compression molding machine after closing the mold plate. After that uniform pressure of 3.92 MPa has been applied over the mold plates (purpose of this is to maintain uniform thickness and to avoid void formation during curing) for 24 h at room temperature. After curing, molds have been opened to remove the RF/Epoxy composite specimens ().
Characterization
The Fourier transform infrared spectroscopy (FTIR) spectra of RF/Epoxy composite has been conducted in the range of 400–4000 cm−1 using Nicolet 6700 Thermo Scientific Spectrophotometer. The samples have been taken in powder form and prepared into pellets by using KBr. The X-ray diffraction (XRD) analysis has been carried out with a Mini Flex diffractomer (Rigaku, Tokyo, Japan) in order to investigate the crystallinity of RF/Epoxy composite. The XRD patterns have been obtained under CuKα (λ = 1.54) radiation at 40 kV and 150 mA in reflection mode, with 0.05° step and 1 s of counting time.
The tensile tests have been performed using servo-hydraulic static testing machine (INSTRON 3382) with a load cell of 5 kN. The tensile test specimens of 165 mm in length and 3.2 mm thickness have been prepared as per ASTM D 638 specification. Five samples have been tested at each fiber loading, e.g., 0, 5, 10, 15, and 25 wt% at a cross head speed of 2 mm/min, out of which average readings have been taken at each fiber loading. The displacement has been measured with a 50 mm extensometer. All the tests have been carried out at room temperature (23 ± 2°C) with a controlled humidity of 54 ± 5%. The flexural tests have been performed on the same machine (INSTRON 3382) using three-point bending method. The flexural specimens having dimensions 127 × 12.7 × 3 mm3 have been prepared according to ASTM D790-99 standard and the tests have been conducted at different fiber loadins similar to tensile tests at a cross head speed of 1 mm/min. The impact test has been carried out on Izod impact tester (Tinius Olsen IT 504, USA) according to ASTM D256 standard at a hammer velocity of 3.46 m/s and hammer weight of 0.905 kg. Similar to tensile and flexural tests, five specimens have been tested at each fiber loading and the average reading has been recorded. The micro-hardness of RF/Epoxy composite having specimen size of 50 × 50 cm2 has been obtained using Vickers’ hardness tester as per ASTM E 384 standard at a load of 80 g and dwell time of 10 s. The reading has been taken in three different locations with an error bar. For each composition, five samples have been tested and average values have been recorded.
The dynamic mechanical thermal analysis (DMTA) have been carried out on DMA Q 800 TA instrument as per ASTM D 5026 standard in shear mode, using the specimen with dimension of 32 × 13 × 3 mm3. The test parameters are: frequency = 1 Hz; temperature range = 33–180°C; heating rate = 2 K/min and maximum shear strain = 0.2%. Thermo gravimetric analysis (TGA) has been performed using Perkin Elmer/STA 8000 instrument with a heating rate of 10°C/min. The surface morphology of fiber and RF/Epoxy composite have been studied by using SEM Quanta FEG 650 instrument at 10 kV.
Result and discussion
Optimum weight percentage of RF/Epoxy composite
The measured tensile strength data of synthesized RF/Epoxy composite have been plotted against different weight percentage (0, 5, 10, 15, and 25 wt%) of acrylic acid treated rattan fibers in . It is observed that the tensile strength first increases with fiber loading and reaching a maximum value then it decreases. The weight percentage of rattan fiber at optimum strength has been obtained by regression analysis.
As depicted from , the data fit well by second degree polynomial with regression coefficient (R2-value) of 0.9688 which gives the optimum strength (i.e., 45.5 MPa) at 18 wt% of fiber loading. This weight percentage of rattan fiber has been considered as the optimum fiber percentage for the development of RF/Epoxy composite for subsequent studies.
Properties of RF/Epoxy composite
Various mechanical properties such as tensile strength, Young’s modulus, flexural strength, impact strength, and hardness of neat epoxy and acrylic acid treated RF/Epoxy composites at different fiber loadings (5, 10, 15, 18, 20, and 25 wt%) have been measured and presented in .
Table 1. Mechanical properties of RF/Epoxy composite at different fiber loadings.
In addition to that the data for untreated RF/Epoxy composite (control sample) at optimum fiber loading (18 wt%) have been given for comparison. The measured properties have also been presented in in the form of bar chart.
Figure 3. Bar chart of RF/Epoxy composite at different fiber loadings: (a) tensile strength, (b) flexural strength, (c) impact strength, (d) hardness.
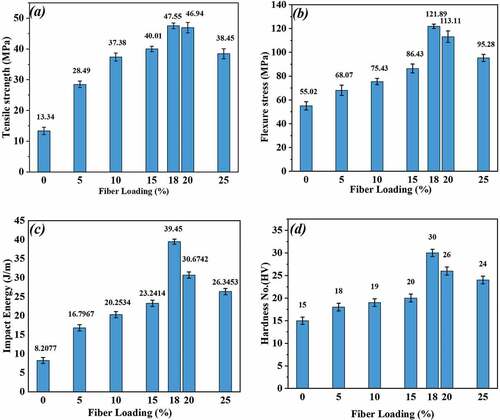
Following the common law of short fiber reinforced polymer composites, it is evident from the results that the properties peaks occur at optimum (i.e. 18 wt%) fiber content. After that all the properties show a decreasing trend. The maximum values of tensile strength, flexural strength, impact strength, and hardness of acrylic acid treated RF/Epoxy composite at optimum fiber loading are 47.5 MPa, 121.89 MPa, 39.45 J/m, and 30 HV, respectively. When compared to untreated RF/Epoxy composite at optimum fiber loading, these values increase to 21.17%, 32.74%, 40.14%, and 20%, respectively. Similarly, the Young’s modulus and flexural modulus increase by 41.44% and 14.66%, respectively. The reason for maximum values of mechanical properties at optimum fiber loading may be due to the fact that at this stage the fibers have reasonable amounts which act as stress transferring medium and also have proper interfacial adhesion between the fiber and matrix. On the other hand, the reason for decreasing trend in the mechanical properties after optimum fiber loading may be due to insufficient matrix coverage which causes voids to appear thereby leading to poor interfacial adhesion. Further, at higher fiber content, the fibers act as flaws and crazing occurs thus causing stress concentration areas which are responsible for decreasing in mechanical properties.
As far as application of natural fiber polymer composite is concerned over the last couple of decades, its use is continuously increasing in door panels, package trays, hat racks, instruments panels, internal engine covers, sun visors, boot liners, oil/air filters, spoilers, seat backs, and exterior under floor paneling. Most of the international automotive manufactures use natural fiber polymer composite materials and their use is expected to increase in this area (Faruk et al. Citation2014). Irawan and Sukania (Citation2018) have found that the flexural strength of woven rattan fiber laminated with epoxy resin is 45.37 MPa in comparison to the flexural strength of commercially available plastic material which is 55.72 MPa. Holbery and Houston (Citation2006) have compared the properties of glass fiber and flax fiber reinforced unsaturated polyester composites used for automobiles from the collected literature data. In that study, it has been observed that the flexural strength and flexural modulus of flax fiber reinforced unsaturated polyester composite are 70 MPa and 6.0 GPa, respectively. However, in the present research, it is found that the flexural strength and flexural modulus of 18 wt% RF/Epoxy composite are 121.89 MPa and 7.82 GPa, respectively, which are much better than the above values. Further, from the collected literature data by Graupner, Herrmann, and Mussig (Citation2009), it has been found that the tensile strength of flax/hemp fiber reinforced epoxy composite used for interior parts of automobile is in the range of 40–60 MPa. In the present case, the tensile strength of 18 wt% RF/Epoxy composite is 47.5 MPa which is comparable. Hence, considering the tensile and flexural strengths, the RF/Epoxy composite can be a potential candidate for use in interior automotive products.
Dynamic mechanical thermal analysis (DMTA)
The mechanical behavior of RF/Epoxy composite has been studied using dynamic mechanical thermal analysis (DMTA) to investigate the properties of stiffness and damping. The effect of frequency on the DMTA of RF/Epoxy composite and neat epoxy resin over a temperature range of 20–180°C and at a heating rate of 10°C/min has been shown in .
Figure 4. DMTA of neat epoxy and 18wt% RF/Epoxy composite at different fiber loadings: (a) storage modulus, (b) loss modulus, (c) tan δ.
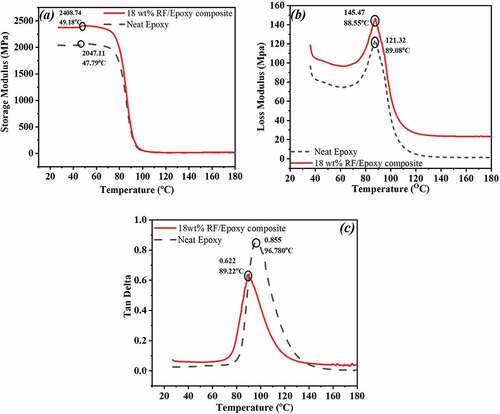
From , it can be observed that the storage modulus (G’) value of 18 wt% RF/Epoxy composite is found to be 2408.74 MPa at 49.18°C, whereas for neat epoxy it is 2047.11 MPa at 47.79°C. A prominent increase in storage modulus (15.01%) of the composite in comparison to neat epoxy may be due to an increase in inter molecular hydrogen bonding resulting from hydroxyl groups which leads to closed packing of the cellulose chain in the RF/Epoxy composite.
The variation of loss modulus (G”) with temperature for neat epoxy and RF/Epoxy composite is shown in . From the figure, it is found that the loss modulus value of composite has dominated the value of neat epoxy throughout the temperature range (20–180°C). The reason is due to the stiffness of fibers which is greater than the neat epoxy matrix. The maximum value of loss modulus of composite is 145.47 MPa at 88.55°C, whereas for neat epoxy it is 121.32 MPa at 89.08°C. In addition, it is also found that the loss modulus increases and then declines after reaching a maximum value which may be due to the addition of fiber.
The glass transition temperature (Tg) has been determined from the peak position of damping parameter (tan δ), due to the transformation of rigid to elastic state of the material. The variation of tan δ with temperature for epoxy matrix and RF/Epoxy composite at the frequency of 1 Hz is shown in . The tan δ value of neat epoxy (0.855 at 96.78°C) is higher than that of RF/Epoxy composite (0.622 at 89.22°C). The incorporation of treated rattan fiber reduces the damping property of the composite when compared to neat epoxy, due to the restricted movement of polymeric molecules which has raised the storage modulus value and reduced the viscoelastic lag between stress and strain (Ray et al. Citation2002). As a result, the amount of matrix (volume) is inadequate to dissipate the vibrational energy properly and hence tan δ decreases. The lower value of tan δ indicates that the RF/Epoxy composite has good load bearing capacity, high interfacial adhesion and improved stress transfer (Shanmugam and Thiruchitrambalam Citation2013).
FTIR spectroscopy
represents the FTIR results of neat epoxy and 18 wt% acrylic acid treated RF/Epoxy composite. Various transmission bands can be observed in the FTIR spectra. The peak observed at 3386 cm−1 is connected with the characteristic of O–H stretching vibration and hydrogen bond of the hydroxyl groups (Manimaran et al. Citation2018) of neat epoxy. The O–H band for the RF/Epoxy composite has become more pronounced and broader and has been shifted slightly to 3326 cm−1. This is probably due to the “free” hydroxyl groups that are now engaged in hydrogen bonding (Wong, Shanks, and Hodzic Citation2004). The peak at 2921 cm−1 is in connection with C–H stretching vibration of CH and CH2 in cellulose and hemicellulose (Indran and Raj Citation2015). The wave number around 1634 cm−1 belongs to the carbonyl groups (C=O) of lignin and hemicellulose (Belouadah, Ati, and Rokbi Citation2015). The peak at 1503 cm−1 indicates C=C stretching of aromatic lignin which has been shifted to 1514 cm−1 in RF/Epoxy composite. Vibration peak of 1234 cm−1 belongs to C–O stretching vibration of the acetyl groups in lignin (Dalmis et al. Citation2020). The peak at 1157 cm−1 is ascribed to C–O–C groups of cellulose and hemicellulose. The wavenumber at 1030 cm−1 manifests the existence of C–O groups of cellulose (Manimaran et al. Citation2018).
X-ray diffraction
From the XRD study (), the crystallinity peak of virgin epoxy at 2θ value of 18.5° is obtained almost in the same place as that of RF/Epoxy composite which represents the cellulose crystallographic planes. However, the curve of RF/epoxy composite is bulged slightly toward right with higher intensity as compared to epoxy resin. From the XRD plot, it is evident that the addition of rattan fiber in the epoxy matrix does not result any significant changes to its crystallinity. Thus the analysis provides the information that there is no transformation to the trans-crystalline phase in the system, indicating that there is a few or no change to the fundamental 3-dimensional cured epoxy network crystal structure, induced due to the incorporated rattan fiber.
Thermo gravimetric analysis (TGA)
The TGA curves of neat epoxy and RF/Epoxy composite are shown in . From the figure, it is observed that the initial small weight loss occurs at around 100°C for both neat epoxy and RF/Epoxy composite indicating the removal of moisture and other volatile products present in the samples. The thermal decomposition of the composites started at comparatively higher temperatures than that of the pure epoxy matrix. The decomposition of pure epoxy has started at a temperature of 225°C and maximum rate of weight loss occurred at 344°C. In case of RF/Epoxy composite the onset temperature of degradation occurs at around 237°C and maximum rate of weight loss occurs at 356°C and a certain quantity of charred residue of carbonaceous products has been left. This indicates that the incorporation of rattan fibers into epoxy polymer enhanced the thermal stability of the composites, which might be due to an increase in strength and stiffness of the fibers. Further, it can be noted that the onset temperature of degradation and the temperature of maximum rate of weight loss for the composite have been increased with rattan fiber loading in the composite, which indicates that the strong interfacial bonding between rattan fiber and epoxy matrix enhanced the thermal stability of the composite. In composite material, the percent residue at 600°C is found to be higher than that obtained for pure epoxy matrix. This also ensures a higher thermal stability in the composite system.
Scanning electron microscope (SEM)
shows the SEM image of both acrylic acid treated rattan fiber and RF/Epoxy composite. From the figure, it is observed that the SEM of chemically treated fiber are found to be distinct and debundled () whereas, the SEM image of RF/Epoxy composite () shows a uniform distribution of fiber with epoxy resin matrix.
However, epoxy resin might be locally agglomerated in the composite surface due to black patch in the SEM image. Surface morphology of RF/Epoxy composite can be explained by the dispersion of chemically treated rattan fiber within epoxy resin matrix. Further, SEM micrograph indicates sufficient interfacial adhesion between the matrix and fiber. It has observed that rattan fibers are not pulled out from the matrix and the surface of the rattan fibers are covered by polymers.
Conclusion
In the present work, short randomly oriented natural fiber reinforced polymer composite has been fabricated by reinforcing acrylic acid treated rattan fiber in epoxy resin using hand layup followed by compression molding technique. The fabricated samples have been characterized and the results of various properties are reported. From the results it is observed that 18 wt% of fiber loading gives the best mechanical properties from regression analysis. After chemical treatment of rattan fiber, it is found that the cellulose content increases, while hemicelluloses, lignin and other materials content decrease as confirmed by FTIR spectra. The SEM image of the composite shows better fiber – matrix interaction and absence of voids. The DMTA result suggests that the composite is extremely good in terms of dynamic mechanical properties. The thermo gravimetric analysis reveals that the composite has higher thermal stability with less char yield. As far as application of rattan fiber reinforced epoxy composite is concerned, the mechanical properties such as tensile strength, flexural strength, and flexural modulus at 18 wt% fiber loading is better in comparison to other existing natural fiber thermosetting composites used for automobile body parts. Hence, it can be considered that the developed RF/Epoxy composite can be a potential candidate for automobile industries.
Highlights
Short randomly oriented rattan fiber reinforced epoxy (RF/Epoxy) composites at different weight percentages (5, 10, 15, 25 wt%) have been fabricated by hand layup followed by compression molding technique.
By regression analysis, 18 wt% of fiber gives optimum mechanical properties with 121 MPa flexural strength and 47.5 MPa tensile strength which is better in comparison to other natural fiber composites used in automobile body parts.
As far as dynamical mechanical properties and thermal properties are concerned, RF/Epoxy composite at 18 wt% of fiber loading gives better result in comparison to other fiber loadings.
The structural and morphological properties of 18 wt% RF/Epoxy composite have been analyzed by XRD, FTIR and SEM.
Supplemental Material
Download Zip (10.6 KB)Disclosure statement
No potential conflict of interest was reported by the authors.
Supplemental data
Supplemental data for this article can be accessed online at https://doi.org/10.1080/15440478.2022.2163024.
References
- Agrawal, R., N. S. Saxena, K. B. Sharma, S. Thomas, and M. S. Sreekala. 2000. Activation energy and crystallization kinetics of untreated and treated oil palm fiber reinforced phenol formaldehyde composites. Materials Science and Engineering: A 277:77–13. doi:10.1016/S0921-5093(99)00556-0.
- Al-Oqla, F. M., S. M. Sapuan, M. R. Ishak, and A. A. Nuraini. 2016. A decision-making model for selecting the most appropriate natural fiber–polypropylene-based composites for automotive applications. Journal of Composite Materials 509 (4):543–56. doi:10.1177/0021998315577233.
- Belouadah, Z., A. Ati, and M. Rokbi. 2015. Characterization of new natural cellulosic fiber from Lygeum spartum L. Carbohydrate Polymers 134:429–37. doi:10.1016/j.carbpol.2015.08.024.
- Bledzki, A. K., and J. Gassan. 1999. Composites reinforced with cellulose based fibres. Progress in Polymer Science 24 (2):221–74. doi:10.1016/S0079-6700(98)00018-5.
- Bledzki, A. K., V. E. Speber, and O. Frank. 2002. Natural and wood fiber reinforcement in polymers. Rapra Review Report 13(8):1–144.
- Ceccarini, L., and L. G. Angelini. 2010. Spartiumjunceum L. A new crop for natural fiber for automotive industry. A paper presented to the Department of Agronomy, University of Pisa, Italy.
- Dalmis, R., G. B. Kilic, Y. Seki, S. Koktas, and O. Y. Keskin. 2020. Characterization of a novel natural cellulosic fiber extracted from the stem of Chrysanthemum morifolium. Cellulose 27 (15):8621–34. doi:10.1007/s10570-020-03385-2.
- Faruk, O., A. K. Bledzki, H. P. Fink, and M. Sain. 2014. Progress report on natural fiber reinforced composites. Macromolecular Materials and Engineering 299 (1):9–26. doi:10.1002/mame.201300008.
- Firdaus, F. E., and M. Dachyar. 2018. Fiber surface modification; Characterization of rattan fiber reinforced composite. International Journal of Engineering & Technology 7 (3):113–16. doi:10.14419/ijet.v7i3.7.16250.
- Graupner, N., A. S. Herrmann, and J. Mussig. 2009. Natural and man-made cellulose fibre-reinforced poly (lactic acid) (PLA) composites: An overview about mechanical characteristics and application areas. Composite: Part A 40:810–21. doi:10.1016/j.compositesa.2009.04.003.
- Greco, A., R. Gennaro, A. Timo, F. Bonfantini, and A. Maffezzoli. 2013. A comparative study between bio-composites obtained with opuntia ficus indica cladodes and flax fibers. Journal of Polymers and the Environment 21:910–16. doi:10.1007/s10924-013-0595-x.
- Holbery, J., and D. Houston. 2006. Natural-fiber-reinforced polymer composites in automotive applications. The Journal of the Minerals, Metals & Materials Society (TMS) 58:80–86. doi:10.1007/s11837-006-0234-2.
- Indran, S., and R. E. Raj. 2015. Characterization of new natural cellulosic fiber from Cissus quadrangularis stem. Carbohydrate Polymers 117:392–99. doi:10.1016/j.carbpol.2014.09.072.
- Irawan, A. P., and I. W. Sukania. 2018. Flexural strength of car spoiler materials made from rattan fiber composites. IOP Conference Series: Materials Science and Engineering 420 (1):012015. doi:10.1088/1757-899X/420/1/012015.
- Manimaran, P., P. Senthamaraikannan, M. R. Sanjay, M. K. Marichelvam, and M. Jawaid. 2018. Study on characterization of Furcraea foetida new natural fiber as composite reinforcement for lightweight applications. Carbohydrate Polymers 181:650–58. doi:10.1016/j.carbpol.2017.11.099.
- Mohanty, A. K., M. Misra, T. L. Drzal, S. E. Selke, B. R. Harte, and G. Hinrichsen. 2005. Natural fibers, biopolymers, and biocomposites: An introduction. In Natural fibers, biopolymers, and biocom posites, ed. A. Mohanty, M. Misra, and T. Drzal, 1–36. Boca Raton: Crc Press-Taylor & Francis Group.
- Mueller, D. H. 2004. Improving the impact strength of natural fiber reinforced composites by specifically designed material and process parameters. International Nonwovens Journal 4:1558925004os. doi:10.1177/1558925004os-1300405.
- Osoka, E., O. D. Onukwuli, and C. Kamalu. 2018. Mechanical properties of selected natural fiber reinforced composites for automobile application. American Journal of Engineering Research 7:384–88.
- Rachchh, N. V., P. S. Ujeniya, and R. K. Misra. 2014. Mechanical characterisation of rattan fibre polyester composite. Procedia Materials Science 6:1396–404. doi:10.1016/j.mspro.2014.07.119.
- Ray, D., B. K. Sarkar, S. Das, and A. K. Rana. 2002. Dynamic mechanical and thermal analysis of vinylester-resin-matrix composites reinforced with untreated and alkali-treated jute fibres. Composites Science and Technology 62:911–17. doi:10.1016/S0266-3538(02)00005-2.
- Sahoo, S. K., J. R. Mohanty, B. K. Nanda, S. Nayak, S. K. Khuntia, K. R. Panda, P. K. Jena, and R. Sahu. 2021. Fabrication and characterization of acrylic acid treated rattan fiber reinforced polyethylene terephthalate composites for packaging industries. Journal of Natural Fibers 19:1–14. doi:10.1081/15440478.2021.1889439.
- Sahoo, S. K., J. R. Mohanty, S. Nayak, and B. Behera. 2019. Chemical treatment on rattan fibers: Durability, mechanical, thermal, and morphological properties. Journal of Natural Fibers 18 (11):1762–71. doi:10.1080/15440478.2019.1697995.
- Sahoo, S. K., J. R. Mohanty, S. Nayak, S. K. Khuntia, P. K. Jena, K. R. Panda, and R. Sahu. 2021. Effectiveness of rattan fiber as a reinforcing material in polymer matrix composites: an experimental study. Journal of Natural Fibers 19:1–10. doi:10.1080/15440478.2021.1929650.
- Scaffaro, R., A. Maio, E. F. Gulino, G. Alaimo, and M. Morreale. 2021. Green composites based on PLA and agricultural or marine waste prepared by FDM. Polymers 13 (9):1361–78. doi:10.3390/polym13091361.
- Shanmugam, D., and M. Thiruchitrambalam. 2013. Static and dynamic mechanical properties of alkali treated unidirectional continuous palmyra palm leaf stalk fiber/jute fiber reinforced hybrid polyester composites. Materials & Design 50:533–42. doi:10.1016/j.matdes.2013.03.048.
- Sreekala, M. S., M. G. Kumaran, and S. Thomas. 2002. Water sorption in oil palm fiber reinforced phenol formaldehyde composites. Composites: Part A, Applied Science and Manufacturing 33:763–77. doi:10.1016/S1359-835X(02)00032-5.
- Stewart, R. 2010. Automotive composites offer lighter solutions. Reinforced Plastics 54:22–30. doi:10.1016/S0034-3617(10)70061-8.
- Suddell, B., and W. Evans. 2005. Natural fiber composites in automotive applications. In Natural fibers, biopolymers, and biocomposites, ed. A. Mohanty, M. Misra, and T. Drzal, 30. CRC Press.
- Timmins, N., R. Almaguer, A. Clark, and N. Odea. 2011. Opportunities in natural fiber composites, creating the equation for growth. Lucintel Texas USA. www.Lucintel.com/LucintelBrief/PotentialofNaturlafibercomposites.
- Wong, S., R. Shanks, and A. Hodzic. 2004. Interfacial improvements in poly (3-hydroxybutyrate)-flax fibre composites with hydrogen bonding additives. Composites Science and Technology 64:1321–30. doi:10.1016/j.compscitech.2003.10.012.