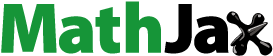
ABSTRACT
Natural fibers are an attractive solution in the composite material industry, for achieving the biodegradability and sustainability that synthetic fibers do not offer. In this study, the effect of the alkali treatment (AT) on the physical properties, chemical composition, morphology, thermal behavior, and tensile strength of fibers extracted from Agave angustifolia Haw leaves was studied. Fibers were treated with 5% NaOH solution (v/v) for 10, 30, and 60 min. Tensile tests of single treated fibers (TF) were carried out at three-gauge lengths. The percentages of lignin and hemicellulose showed a decrease with AT which, in turn, induced a modification of morphological and crystalline structures. Thermal analysis revealed that, due to the presence of hemicellulose constituents, the untreated fibers (UF) had lower thermal stability than TF. Tensile tests revealed that the strength and strain decreased with the increase in the diameter and the test gauge length of the agave fibers.
摘要
天然纤维在复合材料工业中是一种很有吸引力的解决方案,可以实现合成纤维所不能提供的生物降解性和可持续性. 本研究研究了碱处理(AT)对狭叶龙舌兰叶纤维的物理性质、化学成分、形态、热行为和拉伸强度的影响. 用5%NaOH溶液(v/v)处理纤维10、30和60分钟. 单处理纤维(TF)的拉伸试验在三个标距长度下进行. 木质素和半纤维素的百分比随着AT的降低而降低,这反过来又导致了形态和晶体结构的改变. 热分析表明,由于存在半纤维素成分,未处理纤维(UF)的热稳定性低于TF. 拉伸试验表明,随着龙舌兰纤维直径和测试标距长度的增加,强度和应变降低.
Introduction
Recently, the demand for renewable materials like natural fibers as alternative reinforcement in polymer matrix composites has increased extensively (Madhu et al. Citation2020; Panaitescu et al. Citation2019). The main advantages of the use of natural fibers in the development of composite materials include: passive safety, the fact that cellulose fibers offer a relatively high Young’s modulus and high strength, low density, and minimum abrasion of the processing equipment, minimum health risks during handling, biodegradability, their low cost as a raw material, a good surface finish of molded parts and their potential as a reusable material (Panaitescu et al. Citation2019). On the other hand, the main disadvantages are their low temperature processing due to the possibility of fiber degradation, a tendency to form bundles, and, mainly, their hydrophilic nature that can lead to problems of adhesion with the chosen polymer matrix. However, Madhu et al. (Citation2020) and Parre et al. (Citation2020) mentioned that there are different treatments to modify natural fibers and AT is widely used to clean and modify the natural fiber surface when it is necessary to enhance the interface bonding between the fiber and the polymeric matrix (Elkhaoulani et al. Citation2013).
A.angustifolia Haw is a native plant from Oaxaca, Mexico, used as raw material to elaborate on a distilled alcoholic beverage named “mezcal,” 2,500 agave plants/ha were cultivated in the last decade and 3,400 ha have been harvested annually (Cortés-Martínez and García-Méndez Citation2017; García-Méndez, Cortés-Martínez, and Almendárez-Camarillo Citation2020). In this context, García-Méndez, Cortés-Martínez, and Almendárez-Camarillo (Citation2020) report that A. angustifolia Haw fibers mechanically extracted from the leaves are thermally stable, their tensile strength is acceptable, the strain at failure decreases with the increase of the gauge length but the opposite situation was observed with the Young’s modulus. It is well known that chemical treatments of agave fibers improves their thermal and mechanical properties, with benefits on the stiffness, strength, and dynamic moduli of the composites reinforced with them because it relates to the increased interfacial bond strength and adhesion between the matrix and the fibers (Rasana et al. Citation2019). Hence, the aim of this study was to investigate the effect of AT on physical, thermal, and mechanical properties of A. angustifolia Haw fibers. Also, morphology and the chemical composition of UF and TF were evaluated.
Materials and methods
Extraction and chemical treatments of A. angustifolia haw fibers
5 kilograms of fiber was obtained from agave leaves by the mechanical process (García-Méndez, Cortés-Martínez, and Almendárez-Camarillo Citation2020). Subsequently, the fibers were washed with water and dried at 25–30°C for 4 h. 200 grams of randomly selected fibers was separated, of which 100 g was AT. Following the methodology of Ben Sghaier et al. (Citation2012), the dried fibers were separated into three groups and treated with a 5% NaOH (v/v) solution for different treatment times (TT) 10, 30, and 60 min at 30°C. Then, they were washed with tap water, rinsed with distilled water, and placed in an oven to dry at 100°C for 1 h.
Diameter and cross-section area
The cross-sectional area of TF and UF was calculated based on the measurement of the apparent mean diameter as suggested by literature (Bezazi et al. Citation2014). In order to determine the apparent diameter, the fibers were placed under the lens of 40× or 100× of the digital microscope to obtain images of their longitudinal section. After that, measurements in 10 positions through the gauge length of the fibers were made. Measurements were made in millimeters using a digital microscope (model BW1008, Micro-measure® brand), which produced the histogram corresponding to the distribution of the diameter. Subsequently, the cross-sectional area was calculated with the formula for the area of a circle and the average value was used to calculate the stress in N/m2.
Mechanical properties
The preparation of the fiber specimens was performed according to ASTM C1557. The TF and UF were cut at 10, 15, and 20 mm in fiber length (FL) and were mounted and glued on a piece of hard cardboard with a central window. Then, the cardboard was gripped by the universal testing machine Instron model 4442, with a 100 N load cell. For each interval in the statistical distribution of the diameter of the A. angustifolia Haw fibers, a total of 10 fibers were randomly selected and individually subjected to a tensile test at a constant deformation velocity of 0.2 mm·min−1. Tukey’s test was used to compare the minimal differences between the mean values of the mechanical properties using the statistical software MINITAB 17.
Analysis of fiber morphology by SEM
In order to study the surface texture of the agave fibers and to evaluate changes in the surface provoked by the chemical treatments, UF and TF were analyzed by scanning electron microscopy (SEM) using the microscope Superprobe JEOL® JXA 820. All samples were gold-coated with approx. 20 nm, with a Denton Vacuum Model Desk V used to avoid electrostatic charge and to improve image resolution. The SEM was operated using an acceleration voltage of 25kV and a 30 mm working distance.
Chemical characterization
The moisture content, cellulose content, lignin, and ashes of the UF and TF were determined using their corresponding standard test methods ASTM E871–82, ASTM D 1106–96, TAPPI TUM 250, and TAPPI 211 om-12, respectively. The hemicellulose content was calculated as a direct function of the difference between the cellulose-lignin and the total content.
Spectroscopy characterization
The chemical structure was determined by Fourier transformed infrared (FTIR) spectra using a Bruker Tensor 27 spectrophotometer. The samples of UF and TF were analyzed through the KBr technique, having been previously dried and ground to powder and pressed (10 g of sample to 100 mg of KBr) into a disk shape for measurements. The sample collection was obtained using 32 scans in the range of 4000–400 cm−1 with a resolution of 1 cm−1.
X-Ray diffraction test
X-ray measurements were carried out using a Siemens® D5000 diffractometer with a Ni-Filtered CuKα radiation generator (wavelength of 1.5406 Å). Patterns were recorded from 5° to 40° (in 2θ) with 5 s standing per step.
Thermal analysis
Thermal decomposition of UF and TF was evaluated by thermogravimetric analysis (TGA) using a Shimadzu SDT machine, model Q600, in N2 atmosphere at heating rate of 10 ºC min−1, from 70 to 500 ºC. The fiber samples were analyzed using a calorimeter (MTDSC TA Instrument, model Q2000) at a temperature range of 30–400°C, heating speed of 10°C·min−1 and into a nitrogen atmosphere with a pressure of 104 Pa. This technique was used to determine the transition phases of the fiber components.
Results and discussion
Diameter and cross-section area
The histogram in shows the frequency distribution of the mean diameter of the UF and TF for 10, 30, and 60 min of AT. In all cases, seven groups with a range of diameter intervals were obtained. The range was 0.102–0.394 mm for UF, with an average value of 0.2041 ± 0.07088 mm. However, the fiber diameter decreased as the time of AT increased: for TF10, 0.1855 ± 0.07105 mm; for TF30, 0.1627 ± 0.05904 mm; and for TF60, 0.1623 ± 0.04837 mm. This tendency of reducing the diameter by time of AT, is similar to that reported for sisal fibers (Belaadi et al. Citation2014) and for jute (da Costa, Loiola, and Monteiro Citation2010).
Figure 1. Diameter distribution of fibers obtained from leaves of A. angustifolia Haw. UF: untreated fibers; TF: treated fibers during 10, 30 and 60 min.
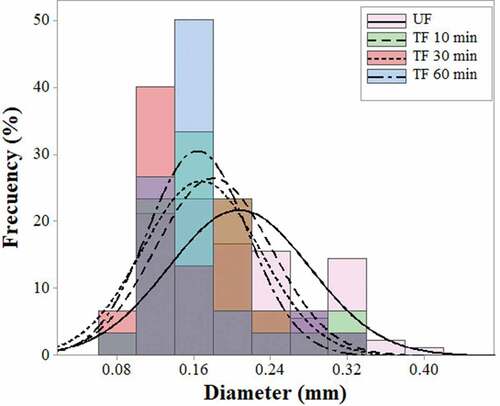
It is well known that chemical treatment removes impurities from the surface of the fiber, thus decreasing its diameter and modifying its topography (Belaadi et al. Citation2014). (a) shows that the cross-sectional area of A. angustifolia Haw fiber has a ribbon and bean shape (García-Méndez, Cortés-Martínez, and Almendárez-Camarillo Citation2020; Sfiligoj et al. Citation2013). The cross-sectional area is similar to that of sisal fibers (Belaadi et al. Citation2014), blue bagasse (Kestur et al. Citation2013), Agave Americana leaf fibers (Hulle, Kadole, and Katkar Citation2015) and is different from that of A. Sisalana fibers that exhibit a typical “horseshoe” transversal section as reported by Zuccarello (Citation2019).
Figure 2. Scanning electron micrograph view at 500× magnification of transversal section of a) untreated A. angustifolia Haw fiber, b) treated A. angustifolia Haw fiber.
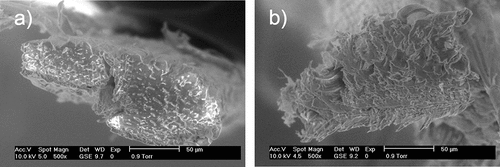
shows a split of fiber bundles into smaller fibrils of TF, whereas UF does not show any fibrils and contains more surface impurities (wax, lignin, and hemicellulose), that usually contribute to the mechanical strength of the composite structure (Parre et al. Citation2020). After AT with 5%NaOH, these components were removed partially and the fiber shows a visible separation of the fibrils (). The aim of this treatment was to increase the surface area and decrease the hydrophilic groups. This hydrophilic nature of the fiber can lead to incompatibility and poor wettability in a hydrophobic polymer matrix, and result in weak bonding in the fiber/matrix interface of the composite.
Mechanical properties
According to the P-value test, the chemical treatment time (TT) does not affect the strain (p > .05), but does influence the strength and Young’s modulus (p < .05). However, the FL influences all three of the mechanical properties that were evaluated (p < .05).
In general, shows that the tensile strength and Young’s modulus of the raw fiber increased with increasing TT, but the opposite tendency occurs with the strain (this decreased by increasing the TT). Increasing the TT allows greater removal of the impurities that are found on the fiber surface, highlighting the defects and discontinuities that generate poor interfacial bonding that had provoked the fiber to fail earlier.
Figure 3. Tensile mechanical properties of individual fibers from leaves of A. angustifolia Haw subject to surface treatment with a solution of NaOH (5% v/v) during 10, 30 and 60 min in three-gauge lengths. a) tensile strength, b) strain (%) and c) Young’s modulus.
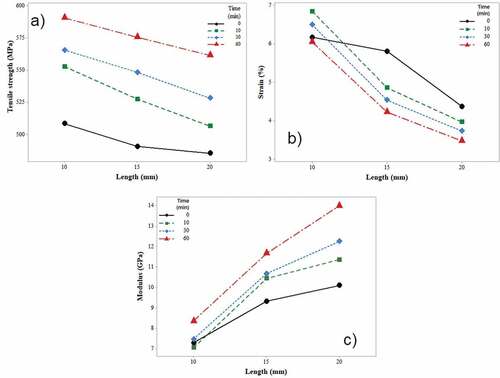
shows the mechanical properties of different natural fibers as a function of fiber length. In first place, it can be established that the tensile strength and modulus of elasticity of the UF and TF reported in this work are superior to the fibers of sisal, bamboo, palm leaft, jute, agave americana, tequila bagasse, and mezcal. These data indicate that the fiber strength is sensitive to the gauge length, which means a decrease in fracture strength with increasing gauge length was observed (Kestur et al. Citation2013). This is related to the likelihood of finding more flaws in longer fiber, where the strength characteristic of natural fibers decreases as the gauge length increases. The variability in Young’s modulus is probably related to the variability in microstructure of the fiber and possible damage during the extraction process, as previously reported by (Alves Fidelis et al. Citation2013), since the Young’s modulus is actually not dependent from gage length. These results are generally attributed to the methods used for the characterization of single fiber tensile tests and the computation of its mechanical properties, the fiber morphology, its structure, and composition, as well as the degree of maturity of the plant source (Bezazi et al. Citation2014).
Table 1. Mechanical properties of A. angustifolia Haw fibers and other natural fibers in function of FL.
According to this information, it was established that the strength and strain of the agave fiber in relation to the FL were determined by constitution of its microfibers and the number of imperfections along the fiber, observing a decrement of these properties if FL increased.
presents the tensile strength of the A. angustifolia Haw fibers related to the diameter intervals. As shown in the graphs, when diameter increases, the resistance decreases. This decreasing response was also reported for sisal (Belaadi et al. Citation2014), Agave americana L. natural fibers (Bezazi et al. Citation2014) and banana (Alwani et al. Citation2015).
Figure 4. Variation of the mean tensile strength in relation to the mean diameter of untreated fiber (UF) and treated fiber (TF) for 10, 30 and 60 min.
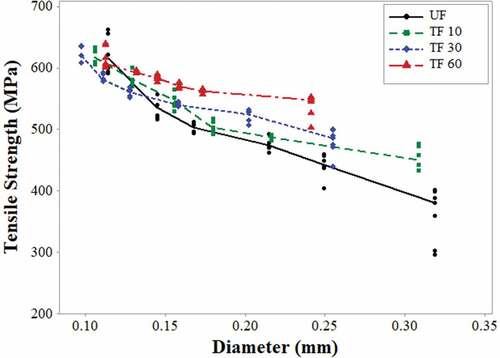
It can be seen that there is an inverse relationship between tensile strength (TS) and diameter (D). The equations 1, 2, 3, and 4 correlate these two variables for each graph, as well as obtain their respective determination coefficient statistics. This interpretation seems to be more consistent and can be demonstrated by the regression hyperbolic equation obtained (Ali Citation2012):
Similar behavior was reported for sisal fiber (Ali Citation2012; Bezazi et al. Citation2014) and jute (da Costa, Loiola, and Monteiro Citation2010), where, similar to the increase of length, an increase in the diameter of the fiber tends to increase the number of defects that causes the failure of the samples in an earlier stage of the tensile test.
SEM Analysis
The surface of UF as shown in looks irregular, presenting globular protrusions, covered with impurities, such as hemicelluloses, lignin, pectin, and waxy substances (Rosli, Ahmad, and Abdullah Citation2013) with variable roughness, because of this, it would be expected that this rough and uneven fiber surface can favor good adhesion to the polymeric matrix by providing fiber-resin mechanical interlocking (Alwani et al. Citation2015).
shows that the TF began to look smoother than the raw one as the cementing materials (such as lignin and hemicellulose) were dissolved from the fiber surface (Bezazi et al. Citation2014). Hemicellulose is hydrolyzed and becomes water-soluble upon application of the AT (Parre et al. Citation2020), and this is confirmed by the study of the chemical composition in and FTIR analysis. This phenomenon helps defibrillation and the opening of the fiber bundles, with the diameter of the fibrils being reduced to a great extent.
Table 2. Chemical composition of A. angustifolia Haw fibers and other natural fibers.
Chemical properties of agave fibers
summarizes the chemical composition of A. angustifolia fiber and compares it with other types of agave fibers. First, it is observed that UF has the highest percentage of hemicellulose and lignin and the lowest percentage of cellulose. Then, when the fiber is subjected to a chemical treatment with NaOH, the percentage of the hemicellulose and lignin decreases while the percentage of cellulose increases. The removal of lignin is much more important for TF; when the fibers are subjected to AT, the hemicellulose is partially hydrolyzed and the lignin is depolymerized, giving rise to sugars and phenolic compounds that are soluble in water (Ben Sghaier et al. Citation2012). Secondly, the percentage of ash, moisture, lignin, cellulose, and hemicellulose, compared with other natural fibers shows that ash content value (1.76%) is higher with respect to that reported by Hidalgo-Reyes et al. (Citation2015) and lower than that previously reported by (Kestur et al. Citation2013). This difference can be attributed to the variability of mineral components in fibrous vegetables, which differs among the different species, and is influenced by the soil characteristics in which the plant was cultivated, climatic conditions where the species has developed, among other factors. The moisture content obtained (7.08%), with a high content of hydroxyl groups which gives it its hygroscopic properties, is similar to what was previously reported by Hidalgo-Reyes et al. (Citation2015), but is lower than that reported by Hulle, Kadole, and Katkar (Citation2015).
The chart above shows that cellulose (61.8%) is the most abundant element in the A. angustifolia Haw fibers. Cellulose determined the mechanical properties of the agave fibers and their hydrophilic nature (Elkhaoulani et al. Citation2013), generating poor links between the natural fiber and the hydrophobic polymeric matrix when they are used to elaborate composites. The lignin content obtained from the fiber was 11.24%, which is a value similar to that reported for A. sisalana (Senthilkumar et al. Citation2018), higher than that of t A. americana fiber (Hulle, Kadole, and Katkar Citation2015), but lower than for the fibers A. tequilana bagasse (Kestur et al. Citation2013), or A. angustifolia bagasse (Hidalgo-Reyes et al. Citation2015).
In summary, the main components of agave fibers are the cellulose and lignin. Both macromolecules are polar because they have a high content of hydroxyl groups (Djafari Petroudy Citation2017); therefore, it is expected that there will be a proper interaction with polyurethanes mainly through hydrogen bonding.
Fourier transform infrared analysis
shows the FTIR spectra of UF and TF. The peak at around 3300 cm−1 suggests a stretching of O – H and a band~2950 cm−1 a stretching of C – H (Satyanarayana, Guimarães, and Wypych Citation2007). The two peaks at 1733 cm−1 and 1238 cm−1 disappeared after the mercerization. The first peak (1730 cm−1) is associated to C=O unconjugated stretching of a carboxylic acid or ester of the hemicellulose. The second peak (1230 cm−1) is assigned to the C – O stretching vibration of acyl group present in the lignin. Lignin is an amorphous substance that is partly aromatic in nature and provides the structural rigidity and stiffness and is responsible for holding the fibers together (Kim and Netravali Citation2010). Similar results are also observed in the literature due to AT (Elkhaoulani et al. Citation2013).
Figure 6. FTIR of untreated fibers (UF) and treated fibers (TF) extracted from leaves of A. angustifolia Haw.
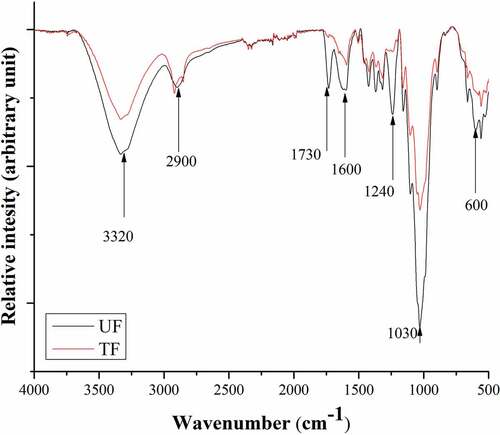
Usually, the chemical treatments reduce the hydrogen bonds from the cellulose hydroxyl group along with the elimination of the carboxyl group in fibers and this is noticeable around the peak 1025 cm−1, correlated with C-OH stretching of lignin (Madhu et al. Citation2020). The C-O-C symmetric glycosidic stretch at 1108 cm−1 arises from the cellulose, hemicellulose, and lignin components (Elkhaoulani et al. Citation2013). The peak observed at 898 cm−1 is attributed to the presence of β-glucoside linkage between the glucose units in cellulose. In summary, the treatment with NaOH removed most of the lignin and hemicellulose components. Furthermore, the treatment changed the hydrophilic nature of the fiber to a hydrophobic nature (Parre et al. Citation2020).
X-Ray diffraction (XRD) test
shows the X-ray diffraction pattern of UF and TF. The peaks are nearly located at 2θ = 14.66, 16.32, 20.99, and 32.87. For natural cellulose, a typical X-ray diffraction diagram is observed with three equatorial diffraction peaks at angles of about 14°, 16° and the strongest diffraction peak at 22° (Sfiligoj et al. Citation2013). Due to the content of amorphous hemicellulose and lignin in agave fiber, an overlapping of the two peaks at angles of 14.66° and 16.32° on the diffraction pattern is observed, corresponding to the (101) and (101*) crystallographic planes, respectively (Ben Sghaier et al. Citation2012). Those which are reported for cellulose presented a decrement once the modification was performed after the NaOH treatment. A similar observation has been reported as an effect of the cellulose modification (Tronc et al. Citation2007) and can be explained when considering that the formation of ester groups opens hydrogen bonds, turning crystalline cellulose into amorphous.
The major crystalline peak on each pattern occurs at around 2θ = 21°, which represents the cellulose crystallographic plane (002). The X-ray diffractogram shows that the intensity of the crystallographic plane (002) was significantly increased and the crystallinity index increased due to AT of the agave fibers. This relationship suggests a better packing and stress relaxation of cellulose chains as a result of the removal of pectin and other amorphous constituents from the fiber, as Kozłowski (Citation2012) explain. It is thought that the increase in crystallinity obtained by AT is the main contributing factor for the increase in fiber strength.
Thermogravimetric analysis
shows the TGA/DTG curves of the untreated fibers () and treated fibers () of the fibers as a function of the temperature. The UF and TF samples showed a weight loss between 70°C and 120°C of 4–5%. Loss that has been attributed typically, to moisture evaporation (Madhu et al. Citation2020). shows a peak in the interval between 235°C and 336°C (see zone 2) with a mass loss of 30%. This transition has been attributed to the degradation of hemicellulose (Panaitescu et al. Citation2019), a crystalline polysaccharide that exhibits higher thermal stability than amorphous hemicelluloses, exhibiting maximum thermal degradation. On the other hand, this peak is not present in the TF sample. This result confirms the effect of the chemical treatment, which removed the hemicellulose. The main change was observed between 336°C and 419°C for UF and 220–404°C for TF, with maximum peaks at 374°C and 346°C, respectively. In this region, the degradation of the cellulose of the fibers has been reported previously. In our case, a mass loss of 38% for the UF and 46% for TF, were observed. Finally, a change occurs between 400°C and 600°C with a maximum of 540°C in both cases, which can be related to the degradation of lignin (Satyanarayana, Guimarães, and Wypych Citation2007) and ash by the degradation of more complex polymers and inorganic salts (Hidalgo-Reyes et al. Citation2015). This transition was observed with a mass loss of 9% for UF and 10% for TF.
Differential scanning calorimetry (DSC)
shows the thermal response of the UF and TF as a function of the temperature. Both fibers exhibited one broad exothermic peak between 80°C and 90°C, which corresponds to fiber dehydration and may be associated with losses at the interstitial spaces within the fibers (Belaadi et al. Citation2014). The region between 110°C and 200°C shows no exothermic or endothermic changes, which reflects that the fibers were thermally stable.
Figure 9. DSC analysis of treated fibers (TF) and untreated fibers (UF) extracted from leaves of A. angustifolia Haw.
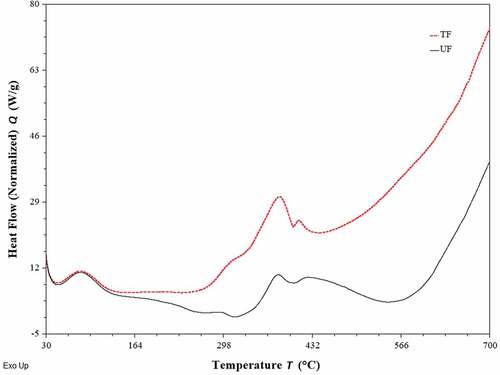
The second exothermic peak at 350–400 ºC for UF and TF is due to the degradation of lignin, hemicellulose, and α-cellulose, its predominant constituent. This peak is attributed to dehydration and depolymerization of cellulose, which leads to the formation of flammable volatile products (Martin et al. Citation2010). As a result, the thermal stability of the TF was increased compared to the UF. The small peak at 410–430°C may be attributed to the oxidative degradation of the charred residue (Belaadi et al. Citation2014). These DSC thermogram observations were similar to those reported by other researchers (Belaadi et al. Citation2014; Madhu et al. Citation2020). It was noted that the chemical treatment could increase the thermal stability of fiber materials.
Conclusions
The AT improves the physical, thermal, and mechanical properties of the fibers mechanically extracted from leaves of A. angustifolia Haw. The diameter of TF for 60 min was diminished from 0.207 ± 0.073 to 0.164 ± 0.052 mm. Cellulose is the major constituent of UF and TF, with 62% and 72%, respectively, while hemicellulose and lignin were removed from TF.
The highest values of tensile strength and Young’s modulus were registered in TF for 60-min subject at 10 mm gauge length. Moreover, the tensile strength of TF showed an inverse correlation with the fiber diameter and may be explained because the cross-section area at different ranges has the lowest standard deviation. The fiber is thermally stable, probably due to its crystallinity and lignin content and because the chemical treatment improves their thermal behavior. In future studies, the A. angustifolia Haw fibers should be evaluated as reinforcement material in eco-friendly composite materials. Cortés-Martínez and García-MéndezCarlos
Highlights
The following highlights are reported in the manuscript:
The percentages of lignin and hemicellulose showed a decrease with alkaline treatments which, in turn, induced a modification of both morphological and crystalline structures
The tensile strength decreased with the increase of diameter and gauge length of agave fibers
The variability in Young’s modulus is probably related to the variability in microstructure of the fiber and possible damage during the extraction process, since the Young’s modulus not dependent from gage length.
Thermal analysis revealed that, due to the presence of hemicellulose constituents, the untreated fibers had lower thermal stability than treated agave fiber.
An inverse relationship between tensile strength and the diameter, a hyperbolic equation could adjust this inverse correlation.
Acknowledgements
The authors would like to extend their sincere appreciation to biochemistry laboratory at Tecnológico Nacional de México campus Oaxaca
Disclosure statement
The authors have no financial interest and gain no benefit from the direct applications of the research described in this manuscript.
Additional information
Funding
References
- Ali, M. 2012. Natural Fibres as Construction Materials. Journal of Civil Engineering and Construction Technology 3 (3):80–14. doi:10.5897/JCECT11.100.
- Alves Fidelis, M. E., T. Vitorino Castro Pereira, O. Da Fonseca Martins Gomes, F. De Andrade Silva, and R. Dias Toledo Filho. 2013. “The effect of fiber morphology on the tensile strength of natural fibers.” Journal of Materials Research and Technology 2 (2): 149–57. 10.1016/j.jmrt.2013.02.003.
- Alwani, M., H. P. S. A. K. Siti, O. Md Nazrul Islam, A. Z. Sulaiman, and R. Dungani. 2015. Microstructural study, tensile properties, and scanning electron microscopy fractography failure analysis of various agricultural residue fibers. Journal of Natural Fibers 12 (2):154–68. doi:10.1080/15440478.2014.905216.
- Belaadi, A., A. Bezazi, M. Bourchak, F. Scarpa, and C. Zhu. 2014. Thermochemical and Statistical Mechanical Properties of Natural Sisal Fibres. Composites Part B: Engineering 67:481–89. doi:10.1016/j.compositesb.2014.07.029.
- Bezazi, A., A. Belaadi, M. Bourchak, F. Scarpa, and K. Boba. 2014. Novel extraction techniques, chemical and mechanical characterisation of agave americana l. natural fibres. Composites Part B: Engineering 66:194–203. doi:10.1016/j.compositesb.2014.05.014.
- Bourahli, M., H. El, and H. Osmani. 2013. Chemical and mechanical properties of diss (ampelodesmos mauritanicus) fibers. Journal of Natural Fibers 10 (3):219–32. doi:10.1080/15440478.2012.761115.
- Cortés-Martínez, C. I., and R. F. García-Méndez. 2017. Morphology of the bagasse fibers obtained from the elaboration process of mezcal and effects on their tensile properties. Journal of Natural Fibers142:250–61.10.1080/15440478.2016.1193089
- Costa, L. L. D., R. L. Loiola, and S. N. Monteiro. 2010. Diameter dependence of tensile strength by weibull analysis: Part II jute fiber. Revista Materia 15 (2):97–102. doi:10.1590/S1517-70762010000200004.
- d’Almeida, J. R. M., R. C. M. P. Aquino, and S. N. Monteiro. 2006. Tensile mechanical properties, morphological aspects and chemical characterization of piassava (attalea funifera) fibers. Composites Part A, Applied Science and Manufacturing 37 (9):1473–79. doi:10.1016/j.compositesa.2005.03.035.
- Djafari Petroudy, S. R. 2017. Physical and mechanical properties of natural fibers. In Advanced high strength natural fibre composites in construction, 59–83. Elsevier Inc. doi:10.1016/B978-0-08-100411-1.00003-0.
- Elkhaoulani, A., F. Z. Arrakhiz, K. Benmoussa, R. Bouhfid, and A. Qaiss. 2013. Mechanical and thermal properties of polymer composite based on natural fibers: moroccan hemp fibers/polypropylene. Materials & Design 49:203–08. doi:10.1016/j.matdes.2013.01.063.
- García-Méndez, R. F., C. I. Cortés-Martínez, and A. Almendárez-Camarillo. 2020. Thermochemical and tensile mechanical properties of fibers mechanically extracted from leaves of agave angustifolia haw. Journal of Natural Fibers 00 (00):1–15. doi:10.1080/15440478.2020.1840480.
- Guo, M., T. H. Zhang, B. W. Chen, and L. Cheng. 2014. Tensile strength analysis of palm leaf sheath fiber with weibull distribution. Composites Part A, Applied Science and Manufacturing 62:45–51. doi:10.1016/j.compositesa.2014.03.018.
- Hidalgo-Reyes, M., M. Caballero-Caballero, L. Héctor Hernández-Gómez, and G. Urriolagoitia-Calderón. 2015. Chemical and morphological characterization of agave angustifolia bagasse fibers. Botanical Sciences 93 (4):807–17. doi:10.17129/botsci.250.
- Hulle, A., P. Kadole, and P. Katkar. 2015. Agave Americana leaf fibers. In Fibers. MDPI Multidisciplinary Digital Publishing Institute. doi:10.3390/fib3010064.
- Kestur, G., T. Satyanarayana, H. S. Flores-Sahagun, L. Pereira Dos Santos, J. Dos Santos, I. Mazzaro, and A. Mikowski. 2013. characterization of blue agave bagasse fibers of Mexico. Composites Part A, Applied Science and Manufacturing 45:153–61. doi:10.1016/j.compositesa.2012.09.001.
- Kim, J. T., and A. N. Netravali. 2010. mercerization of sisal fibers: effect of tension on mechanical properties of sisal fiber and fiber-reinforced composites. Composites Part A, Applied Science and Manufacturing 41 (9):1245–52. doi:10.1016/j.compositesa.2010.05.007.
- Kozłowski, R. M. 2012. Handbook of natural fibers volume 2: processing and applications. ed., R. M. Kozłowski. Oxford Cambridge Philadelphia New Delhi: Woodhead Publishing.
- Madhu, P., M. R. Sanjay, M. Jawaid, S. Siengchin, A. Khan, and C. Iulian Pruncu. 2020. A new study on effect of various chemical treatments on agave americana fiber for composite reinforcement: Physico-chemical, thermal, mechanical and morphological properties. Polymer Testing 85 (May):106437. doi:10.1016/j.polymertesting.2020.106437.
- Martin, A. R., M. Alice Martins, O. R. R. F. Da Silva, and L. H. C. Mattoso. 2010. Studies on the thermal properties of sisal fiber and its constituents. Thermochimica Acta 506 (1–2):14–19. doi:10.1016/j.tca.2010.04.008.
- Panaitescu, D. M., Z. Vuluga, C. Gabriela Sanporean, C. Andi Nicolae, A. Raluca Gabor, and R. Trusca. 2019. High flow polypropylene/sebs composites reinforced with differently treated hemp fibers for injection molded parts. Composites Part B: Engineering 174 (October):107062. doi:10.1016/j.compositesb.2019.107062.
- Parre, A., B. Karthikeyan, A. Balaji, and R. Udhayasankar. 2020. “Investigation of chemical, thermal and morphological properties of untreated and naoh treated banana fiber.” In Materials Today: Proceedings, 22:347–52. Elsevier Ltd. 10.1016/j.matpr.2019.06.655.
- Peponi, L., J. Biagiotti, L. Torre, J. M. Kenny, and I. Mondragon. 2008. Statistical Analysis of the Mechanical Properties of Natural Fibers and Their Composite Materials. I. Natural Fibers. Polymers and Polymer Composites 29 (3):313–20. doi:10.1002/pc.
- Rasana, N., K. Jayanarayanan, B. D. S. Deeraj, and K. Joseph. 2019. The thermal degradation and dynamic mechanical properties modeling of MWCNT/glass fiber multiscale filler reinforced polypropylene composites. Composites Science and Technology 169 (January):249–59. doi:10.1016/j.compscitech.2018.11.027.
- Rosli, N. A., I. Ahmad, and I. Abdullah. 2013. Isolation and Characterization of Cellulose Nanocrystals from Agave Angustifolia Fibre. BioResources 8 (2):1893–908. doi:10.15376/biores.8.2.1893-1908.
- Satyanarayana, K. G., J. L. Guimarães, and F. Wypych. 2007. Studies on Lignocellulosic Fibers of Brazil. Part I: Source, Production, Morphology, Properties and Applications. Composites Part A, Applied Science and Manufacturing 38 (7):1694–709. doi:10.1016/j.compositesa.2007.02.006.
- Senthilkumar, K., N. Saba, N. Rajini, M. Chandrasekar, M. Jawaid, S. Siengchin, and O. Y. Alotman. 2018. Mechanical properties evaluation of sisal fibre reinforced polymer composites: a review. In Construction and building materials. Elsevier Ltd. doi:10.1016/j.conbuildmat.2018.04.143.
- Sfiligoj, M., S. Hribernik, K. Stana, and T. Kreze. 2013. Plant Fibres for Textile and Technical Applications. Advances in Agrophysical Research 369–97. doi:10.5772/52372.
- Sghaier, A. E. O. B., Y. Chaabouni, S. Msahli, and F. Sakli. 2012. Morphological and crystalline characterization of NaOH and NaOCl treated agave Americana L. fiber. Industrial Crops and Products 36 (1):257–66. doi:10.1016/j.indcrop.2011.09.012.
- Silva, F. D. A., N. Chawla, and D. T. F. Rd. 2008. Tensile behavior of high performance natural (sisal) fibers. Composites Science and Technology 68 (15–16):3438–43. doi:10.1016/j.compscitech.2008.10.001.
- Sreenivasan, V. S., S. Somasundaram, D. Ravindran, V. Manikandan, and R. Narayanasamy. 2011. Microstructural, physico-chemical and mechanical characterisation of sansevieria cylindrica fibres - an exploratory investigation. Materials & design 32 (1):453–61. doi:10.1016/j.matdes.2010.06.004.
- Tripathy, S. S., L. Di Landro, D. Fontanelli, A. Marchetti, and G. Levita. 2000. Mechanical properties of jute fibers and interface strength with an epoxy resin. Journal of Applied Polymer Science 75 (13):1585–96. doi:10.1002/(SICI)1097-4628(20000328)75:13<1585:AID-APP4>3.0.CO;2-Q.
- Tronc, E., C. A. Hernández-Escobar, R. Ibarra-Gómez, A. Estrada-Monje, J. Navarrete-Bolaños, and E. A. Zaragoza-Contreras. 2007. Blue agave fiber esterification for the reinforcement of thermoplastic composites. Carbohydrate Polymers 67 (2):245–55. doi:10.1016/j.carbpol.2006.05.027.
- Wang, F., and J. Shao. 2014. Modified weibull distribution for analyzing the tensile strength of bamboo fibers. Polymers 6 (12):3005–18. doi:10.3390/polym6123005.
- Zuccarello, B. 2019. Static and dynamic mechanical properties of eco-friendly polymer composites. Sustainable Polymer Composites and Nanocomposites. doi:10.1007/978-3-030-05399-4_9.