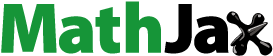
ABSTRACT
Synthetic fibers are restricted from being used as reinforcements due to increasing awareness of environmental issues and strict laws from government agencies. In recognition of this, the engineering and scientific communities switched their attention to using natural fibers as reinforcement in polymers to make sustainable composites. The fiber was extracted through the water retting process, and characterized from the stem of the Tithonia diversifolia (TD) plant. Physical, chemical, and mechanical properties were investigated and it was found that this fiber has high cellulose content of 65.33 wt.%, and less wax content of 0.67%. X-ray diffraction (XRD) confirmed the crystallinity index as 45%. Surface morphology was carried out through Scanning Electron Microscope (SEM) analysis. Fourier Transform Infrared Spectroscopy (FTIR) results confirmed the chemical functional groups. Thermogravimetric Analysis (TGA), TG and DTG curves were used to evaluate the fiber thermal stability. This result confirms that TD fiber can be used as potential fiber reinforcement in biocomposites.
摘要
由于人们对环境问题的认识日益提高,政府机构颁布了严格的法律,合成纤维被限制用作增强材料. 认识到这一点,工程界和科学界将注意力转向使用天然纤维作为聚合物的增强材料,以制造可持续的复合材料. 该纤维是通过水沤制过程提取的,并从天香(Tithonia diversifolia,TD)植物的茎中进行了表征. 对物理、化学和机械性能进行了研究,发现这种纤维的纤维素含量高达65.33 wt%,蜡含量低达0.67%. X射线衍射(XRD)证实结晶度指数为45%. 通过扫描电子显微镜(SEM)分析进行表面形貌. 傅里叶变换红外光谱(FTIR)结果证实了化学官能团. 热重分析(TGA)、TG和DTG曲线用于评估纤维的热稳定性. 这一结果证实了TD纤维可以用作生物复合材料中的潜在纤维增强材料.
Introduction
In almost every field of manufacture, there is a need for synthetic materials, and the demand is increasing as a result. Synthetic materials have become an inevitable part of our modern society. As of now, some materials have been banned by environmental protection agencies for their hazardous effect on the environment. Although man-made fibers such as polyester, nylon, and aramid have been used for many years, they have various drawbacks (Balu et al. Citation2020; Senthamaraikannan et al. Citation2018; Mohanty, Misra, and Drzal Citation2002). In response to the demands from government environmental protection agencies, researchers all are exploring natural-based materials that are capable of meeting the same criteria as those found in synthetic materials (Bhuvaneshwaran et al. Citation2019; Mylsamy et al. Citation2019; Nickel and Riedel Citation2003) Such as acceptable specific strength, low cost, low density, better thermal and acoustic insulating properties compared to conventional reinforcement material (Nagappan et al. Citation2021; Vijay et al. Citation2020; Mylsamy et al. Citation2020). The attention of researchers turns toward natural fiber with an exhibit of potential properties of reinforcement materials either with thermoset or thermoplastic matrix. Several lightweight materials are made from natural fibers. They may be extracted from a variety of plant organs, including the bark, stem, root, and leaf (Mylsamy et al. Citation2020; Balu et al. Citation2020; Manimaran et al. Citation2018). Urtica dioica natural fiber was chosen for this study, and it was discovered that this fiber can be made to fabricate environmentally acceptable natural fiber reinforced composites (Bodros and Baley Citation2008). Natural banana fiber reinforced with epoxy resin was found to be eco-friendly and is utilized for manufacturing household appliances with minimum cost (Sapuan and Maleque Citation2005). Tithonia Diversifolia Fiber (TDF) has yet to be used as reinforcement in the polymer matrix, so the basic characteristics of TDF should be investigated for their application suitability. TDF were subjected to chemical analysis, XRD, FTIR, scanning electron microscope, and Thermogravimetric. The suitability of TDF as reinforcement in polymer composite materials was investigated in this study.
Materials and methods
Fiber extraction
The matured TD stem was collected from Thailavaram region, which is in Chengalpattu district, Tamil Nadu, India. shows the TD stem fiber extraction process, where TD stem was immersed in water for 3 weeks to allow microbial degradation (Bhuvaneshwaran, Sampath, and Sagadevan Citation2019). This is the simplest way for producing high-quality fiber from the plant’s stem. The outer layers are removed manually followed by the removal of the inner fibrous layers from TD stem. The fibers are then washed and sundried for 1 week, the fibers were extracted through a combing process with the help of a metal teeth brush (Saravanakumar et al. Citation2013).
Determination of chemical composition of TD stem fiber
To determine the percentages of cellulose, hemicelluloses, moisture and lignin contents of TDSF were found out by applying the common analysis methods (Doree Citation1950; Pearl Citation1967). The density of TDSF was determined using the balancing method (Indran, Raj, and Sreenivasan Citation2014). The content of wax was evaluated as per the common protocol (Conrad Citation1944). ASTM standard E1755–01 was used to analyze the ash content (Reddy and Yang Citation2008).
X-ray diffraction spectroscopy (XRD)
Using a diffractometer (Model: D8 Advance Davinci, make: Bruker USA) and CuKα radiation as a radiation source, 30 mA current, and 40 kV voltage were maintained for this experiment. The pulverized TDF sample was scanned at a rate of 5° per minute over a 2θ range between 10° and 80°. Segal empirical method was employed to measure crystallinity index (CI) and crystallite size (CS) (O’Connor, DuPre, and Mitcham Citation1958; Segal et al. Citation1959).
Fourier transform infrared analysis (FTIR)
An FTIR spectrometer was used to determine the functional groups present in TDSFs between 400 and 4000 cm−1 (Model: FTIR-8400S Spectrum, Make: SHIMADZU). The pelletized fiber samples were placed in the sample holder of the spectrometer, and a vacuum was applied to eliminate moisture. The sample was then exposed to infrared radiation at a rate of 32 scans per minute with a resolution of 2 cm−1 to get spectral outputs.
Physical and single fiber tensile strength
For a randomly selected sample of TDSFs (n = 30), a tensile test was conducted using a universal testing machine equipped with a load cell of 5 kN and a cross head speed of 0.1 mm/min. The test was conducted according to ASTM 3822 M14. Gauge length was 50 mm used.
Morphological analysis
A SEM was used to examine the surface of the TDSF images obtained by a Schottky Emitter Field emission scanning electron microscope (Model: Thermo Scientific Apreo). The test was conducted at a voltage of 30kV and a vacuum quantity of 1.5 × 10−3 Pa. All specimens were sprayed with a fine layer of gold to avoid electrical charges during analyses. An optical microscope was used to determine the fiber diameter (Olympus B×51).
Thermogravimetric analysis (TGA)
A simultaneous thermal analyzer (Netzsch STA, model 449F3) was used to determine the thermal stability of TDF using thermogravimetry (TG), derivative thermogravimetry (DTG), and differential scanning calorimetry (DSC). As a precaution to avoid the effects of oxidation on charging, the experiment was carried out in a nitrogen atmosphere with a flow rate of 20 mL/min. The temperature was steadily increased at a rate of 10°C/min from room temperature to 600°C.
Results and discussion
Physico-chemical and mechanical properties
Compared to other cellulosic natural fibers, TDSF exhibits a different chemical composition and physical properties. TD stem fiber has a high cellulose content, which determines its stiffness and strength. The strength and stability of plant fibers mainly depends on the cellulose content of the fibers (Baley Citation2002; Gopinath, Billigraham, and Sathishkumar Citation2021). TDSF contains 65.33% of cellulose, which is comparable to Coccinia indica (64.56%), Acacia concinna (59.43%), Banana inflorescence bracts (56.48%), and Catharanthus roseus (47.3%). TDSF contains lignin (15.06%), which is higher than Coccinia indica (12.55%), Acacia concinna (14.64%), and Chloris barbata (9.32%). 0.67% wax amount of wax was discovered in the TDSF, which is lesser compared with that of other natural fibers, such as Banana inflorescence bracts (1.05%), Albizia saman (1.5%), Catharanthus roseus (2.3%), and Eleusine indica grass (2.9%). When compared to low-lignin content fiber, the higher lignin content has made fiber stiffer (Amutha, Sudha, and Saravanan Citation2022). shows the chemical composition of TD fiber and compared to other natural fibers. Composite materials with low wax content of natural fibers have enhanced properties while fibers with high content of wax are characterized by a lack of interfacial interaction between the fiber and the polymer matrix (Amutha and Senthilkumar Citation2021).
Table 1. Chemical composition of raw TD fiber and compared to other natural fibers.
TDF has a high ash content of 6.78%, which decreases the fire resistance of the material and results in the loss of amorphous elements. The low density of TDF is which makes it attractive for making lightweight materials. It is nearly half the density of sisal, red coconut fruit bunches, banana ribbons, and banana fibers. displays the density and tensile strength of TD fiber and compared with other natural fibers. High tensile strength and Young’s modulus are exhibited from natural fibers are based on cellulose content and rigidity is based on lignin content (Manivel et al. Citation2021).
Table 2. Crystalline, mechanical, and thermal properties of raw TD fiber are compared with various natural fibers.
X-ray diffraction analysis
Analyses of X-ray diffraction (XRD) determined the compositions of TDF as amorphous and crystalline. depicts the X-ray diffraction of TDF and observed crystallographic planes are (200) and (110), corresponding to two well-defined crystalline peaks at 15.97 and 22.35, respectively. The crystallite Index (CI) of TDF is found by using the following Segal EquationEquation (1)(1)
(1) , the value of CI for TDFs was calculated to be 45%. thus this fiber is higher than other fiber such as Acacia Concinna (Amutha and Senthilkumar Citation2021).
The crystalline content of cellulose in stem fibers is the primary factor affecting the stiffness and strength of fibers. Scherrer’s formula (EquationEquation 2(2)
(2) ) was used to determine the crystal size of TDFs, and the size was 3.00 nm. depicts the crystalline properties of TD fiber and compares it to various natural fibers.
FTIR analysis
depicts the optical spectrum of TDF showing the chemical groups of components such as cellulose, hemicellulose, and lignin. On the cellulose arrangement of the TDF, a first peak appears on frequencies 3367 cm−1 related to OH stretching vibration of cellulose. It shows that wax is present in the less ordered alkyl chain band and that the peak at 2917 cm−1 denotes the stretching vibration between CH in cellulose (Silverio et al. Citation2013). The CH symmetry, which caused the bending of the band, is found at approximately 1413 cm−1 (Vijay et al. Citation2020). This is due to O-H vibrations in the hemicellulose region, which are absorbed in the carbonyl region. As the aromatic ring lignin bends, the vibration is stretched at 1048 cm−1 (Yan, Chouw, and Jayaraman Citation2014).
Thermogravimetric analysis
Thermogravimetric analysis was used to calculate the TG and DTG curves of the TD fiber as shown in . TD fiber degraded at different stages as shown in the figure. At 76.6°C, an overall mass change of 9.1% was found to be predicted, which shows the loss of moisture (Bhuvaneshwaran et al. Citation2021). Lower temperature thermal peak noted for cell debris and evaporation of water molecules that are associated with cellulosic fiber (Amutha, Sudha, and Saravanan Citation2022). The next peak, which measured from 69.16°C to 204.16°C, showed a mass change of 11.71%, which is consistent with lignin pyrolysis (French Citation2014). With a mass change of 24.17%, at 204.16°C to 376.3°C, cellulose and part of lignin are degraded in the third stage. A similar peak was observed for hemp, kenaf, and bamboo fibers at 308°C, 309.2°C, and 321°C respectively (Yao et al. Citation2008). This phenomenon is due to cellulose degradation, which is greater in the TD fiber, causing a significant mass change in the third stage. In the final stage, a portion of the cellulose and lignin degrade at a temperature exceeding 376.3°C in the final stage, and a mass change of 18.91% was recorded. shows the thermal properties of TD fiber and compared with other natural fibers.
Surface morphological analysis
shows the surface morphology of TDF, which shows the impurities, micro-cracks, and micro holes respectively along with the longitudinal direction of the fiber. These holes and cracks in the polymer matrix may lead to high contact area in fiber. SEM image was present with colored microparticles, and it may be seen due to the occurrence of amorphous constituents in fiber namely cellulose, lignin, and hemicellulose (Gopi Krishna, Kailasanathan, and Nagaraja Ganesh Citation2020). The existence of impurities is indicated by white layers on the surface of the fiber.
shows the optical microscope images. The diameter of the fibers were measured with an aid of an optical microscope, and it shows a range of 56.09 to 76.02 µm.
Conclusion
This study indicates the main need of natural stem fiber for the preparation of polymer composite, and it can be used as reinforcement material and it also adds merit to an understanding of natural stem fibers. While comparing existing natural fibers, high cellulose content (65.33%) of TD fiber with lower density and higher rigidity, which may enable for making rope and carpet weaving. The controlled and large-scale cultivation of the plant is encouraged to meet the demand of the light weight polymer composites and pulp and paper production industries. TD is the best alternative material for conventional fibers such as glass and carbon on polymer matrices since it contains desirable tensile properties. Relatively lower elongation and higher strength, conferred to TDSF by the good value of Crl (45%) and magnitude of crystallite size. TDSF thermal stability up to 237°C was discovered through thermogravimetric analysis. Future studies will include a comprehensive investigation of TDF reinforcement material for manufacturing biocomposite laminates and it is important to evaluate the thermal and mechanical properties.
Declaration of conflicting interests
The author(s) declared no potential conflicts of interest with respect to the research, authorship, and/or publication of this article.
Highlights
Extraction of new natural cellulose fiber from the Stem of Tithonia Diversifolia (TD) Plant.
TD Fibers were rich in cellulose content found by chemical composition testing methods.
TD Fibers were characterized by means of XRD, FTIR, TGA, and SEM performed.
includes chemical compositions of raw Tithonia diversifolia Stem Fiber and different natural fibers.
includes mechanical, crystalline, and thermal properties of raw Tithonia diversifolia stem fiber and various natural fibers.
Acknowledgments
The author would like to thank SRM Institute of Science and Technology, Kattankulathur, Chennai, India for providing their facilities to prepare samples. In addition, we would like to acknowledge South India Textile Research Association, Coimbatore, Tamil Nadu, India and PSG COE INDUTECH, Coimbatore, Tamil Nadu, India for providing their lab facilities.
Disclosure statement
No potential conflict of interest was reported by the author(s).
Additional information
Funding
References
- Amutha, V., and B. Senthilkumar. 2021. Physical, chemical, thermal, and surface morphological properties of the bark fiber extracted from acacia concinna plant. Journal of Natural Fibers 18 (11):1661–11. doi:10.1080/15440478.2019.1697986.
- Amutha, K., A. Sudha, and D. Saravanan. 2022. Characterization of natural fibers extracted from banana inflorescence bracts. Journal of Natural Fibers 19 (3):872–81. doi:10.1080/15440478.2020.1764437.
- Balasundar, P., P. Narayanasamy, P. Senthamaraikannan, S. Senthil, R. Prithivirajan, and T. Ramkumar. 2018. Extraction and characterization of new natural cellulosic chloris barbata fiber. Journal of Natural Fibers 15 (3):436–44. doi:10.1080/15440478.2017.1349015.
- Baley, C. 2002. Analysis of the flax fibres tensile behaviour and analysis of the tensile stiffness increase. Composites Part A, Applied Science and Manufacturing 33 (7):939–48. doi:10.1016/S1359-835X(02)00040-4.
- Balu, S., P. S. Sampath, M. Bhuvaneshwaran, G. Chandrasekar, A. Karthik, and S. Sagadevan. 2020. Dynamic mechanical analysis and thermal analysis of untreated Coccinia indica fiber composites. Polimery 65 (5):357–62. doi:10.14314/polimery.2020.5.3.
- Baskaran, P. G., M. Kathiresan, P. Senthamaraikannan, and S. S. Saravanakumar. 2018. Characterization of new natural cellulosic fiber from the bark of dichrostachys cinerea. Journal of Natural Fibers 15 (1):62–68. doi:10.1080/15440478.2017.1304314.
- Bhuvaneshwaran, M., P. S. Sampath, S. Balu, and S. Sagadevan. 2019. Physicochemical and mechanical properties of natural cellulosic fiber from Coccinia Indica and its epoxy composites. Polimery 64 (10):656–64. doi:10.14314/polimery.2019.10.2.
- Bhuvaneshwaran, M., P. S. Sampath, and S. Sagadevan. 2019. Influence of fiber length, fiber content and alkali treatment on mechanical properties of natural fiber-reinforced epoxy composites. Polimery 64 (2):93–99. doi:10.14314/polimery.2019.2.2.
- Bhuvaneshwaran, M., S. P. Subramani, S. K. Palaniappan, S. K. Pal, and S. Balu. 2021. Natural cellulosic fiber from Coccinia Indica stem for polymer composites: Extraction and characterization. Journal of Natural Fibers 18 (5):644–52. doi:10.1080/15440478.2019.1642826.
- Bodros, E., and C. Baley. 2008. Study of the tensile properties of stinging nettle fibres (Urtica dioica). Materials letters 62 (14):2143–45. doi:10.1016/j.matlet.2007.11.034.
- Conrad, C. M. 1944. Determination of wax in cotton fiber, a new alcohol extraction method. Industrial Engineering Chemistry, Analytical Edition 16 (12):745–48. doi:10.1021/i560136a007.
- Doree, C. 1950. The methods of cellulose chemistry. 2nd ed. New York: Springer US.
- French, A. D. 2014. Idealized powder diffraction patterns for cellulose polymorphs. Cellulose 21 (2):885–96. doi:10.1007/s10570-013-0030-4.
- Gopi Krishna, M., C. Kailasanathan, and B. Nagaraja Ganesh. 2020. Physico-chemical and Morphological Characterization of Cellulose Fibers Extracted from Sansevieria roxburghiana Schult & Schult F Leaves. Journal of Natural Fibers 19 (9):3300–16. doi:10.1080/15440478.2020.1843102.
- Gopinath, R., P. Billigraham, and T. P. Sathishkumar. 2021. Physicochemical and thermal properties of cellulosic fiber extracted from the bark of Albizia saman. Journal of Natural Fibers 19 (13):6659–75. doi:10.1080/15440478.2021.1929654.
- Indran, S., R. E. Raj, and V. S. Sreenivasan. 2014. Characterization of new natural cellulosic fiber from Cissus quadrangularis root. Carbohydrate Polymers 110:423–29. doi:10.1016/j.carbpol.2014.04.051.
- Kale, R. D., T. G. Alemayehu, and V. G. Gorade. 2018. Extraction and characterization of lignocellulosic fibers from girardinia bullosa (Steudel) wedd. (Ethiopian Kusha Plant). Journal of Natural Fibers 17 (6):906–20. doi:10.1080/15440478.2018.1539940.
- Khan, A., R. Vijay, D. L. Singaravelu, M. R. Sanjay, S. Siengchin, F. Verpoort, K. A. Alamry, and A. M. Asiri. 2021. Extraction and characterization of natural fiber from Eleusine indica grass as reinforcement of sustainable fiber reinforced polymer composites. Journal of Natural Fibers 18 (11):1742–50. doi:10.1080/15440478.2019.1697993.
- Khuntia, T., and S. Biswas. 2020. Characterization of a Novel Natural Filler from Sirisha Bark. Journal of Natural Fibers 19 (8):3083–92. doi:10.1080/15440478.2020.1838997.
- Kulandaivel, N., R. Muralikannan, and S. KalyanaSundaram. 2018. Extraction and characterization of novel natural cellulosic fibers from pigeon pea plant. Journal of Natural Fibers 17 (5):769–79. doi:10.1080/15440478.2018.1534184.
- Kumar, R., N. R. J. Hynes, P. Senthamaraikannan, S. Saravanakumar, and M. R. Sanjay. 2018. Physicochemical and thermal properties of ceiba pentandra bark fiber. Journal of Natural Fibers 15 (6):822–29. doi:10.1080/15440478.2017.1369208.
- Maheshwaran, M. V., N. R. J. Hyness, P. Senthamaraikannan, S. S. Saravanakumar, and M. R. Sanjay. 2018. Characterization of natural cellulosic fiber from Epipremnum aureum stem. Journal of Natural Fibers 15 (6):789–98. doi:10.1080/15440478.2017.1364205.
- Manimaran, P., M. Prithiviraj, S. S. Saravanakumar, V. P. Arthanarieswaran, and P. Senthamaraikannan. 2018. Physicochemical, tensile, and thermal characterization of new natural cellulosic fibers from the stems of Sida cordifolia. Journal of Natural Fibers 15 (6):860–69. doi:10.1080/15440478.2017.1376301.
- Manivel, S., N. Pannirselvam, R. Gopinath, and T. P. Sathishkumar. 2021. Physico-mechanical, chemical composition and thermal properties of cellulose fiber from hibiscus vitifolius plant stalk for polymer composites. Journal of Natural Fibers 19 (13):6961–76. doi:10.1080/15440478.2021.1941484.
- Mohanty, A., M. Misra, and L. Drzal. 2002. Sustainable bio-composites from renewable resources: Opportunities and challenges in the green materials world. Journal of Polymers and the Environment 10 (1):19–26. doi:10.1023/A:1021013921916.
- Mylsamy, B., V. Chinnasamy, S. K. Palaniappan, S. P. Subramani, and C. Gopalsamy. 2020. Effect of surface treatment on the tribological properties of Coccinia Indica cellulosic fiber reinforced polymer composites. Journal of Materials Research and Technology 9 (6):16423–34. doi:10.1016/j.jmrt.2020.11.100.
- Mylsamy, B., S. K. Palaniappan, P. S. Sampath, S. K. Pal, and A. Karthik. 2019. Impact of nanoclay on mechanical and structural properties of treated Coccinia indica fibre reinforced epoxy composites. Journal of Materials Research and Technology 8 (6):6021–28. doi:10.1016/j.jmrt.2019.09.076.
- Mylsamy, B., S. K. Palaniappan, S. P. Subramani, S. K. Pal, and B. Sethuraman. 2020. Innovative characterization and mechanical properties of natural cellulosic Coccinia Indica fiber and its composites. Materials Testing 62 (1):61–67. doi:10.3139/120.111451.
- Nagappan, S., S. P. Subramani, S. K. Palaniappan, and B. Mylsamy. 2021. Impact of alkali treatment and fiber length on mechanical properties of new agro waste Lagenaria Siceraria fiber reinforced epoxy composites. Journal of Natural Fibers 19 (13):6853–64. doi:10.1080/15440478.2021.1932681.
- Nickel, J., and U. Riedel. 2003. Activities in biocomposites. Materials Today 6 (4):44–48. doi:10.1016/S1369-7021(03)00430-9.
- O’Connor, R. T., E. F. DuPre, and D. Mitcham. 1958. Applications of infrared absorption spectroscopy to investigations of cotton and modified cottons: Part I: Physical and crystalline modifications and oxidation. Textile Research Journal 28 (5):382–92. doi:10.1177/004051755802800503.
- Palai, B. K., S. K. Sarangi, and S. S. Mohapatra. 2021. Investigation of physiochemical and thermal properties of Eichhornia Crassipes fibers. Journal of Natural Fibers 18 (9):1320–31. doi:10.1080/15440478.2019.1691110.
- Pearl, I. A. 1967. The chemistry of lignin, Chapter 4. New York: Marcel Dekker.
- Prithivirajan, R., P. Balasundar, R. Shyamkumar, N. S. Al-Harbi, S. Kadaikunnan, T. Ramkumar, and P. Narayanasamy. 2019. Characterization of cellulosic fibers from Morus alba L. stem. Journal of Natural Fibers 16 (4):503–11. doi:10.1080/15440478.2018.1426079.
- Raja, K., B. Prabu, P. Ganeshan, V. S. Chandra Sekar, and B. Nagaraja Ganesh. 2021. Characterization studies of natural cellulosic fibers extracted from shwetark stem. Journal of Natural Fibers 18 (11):1934–45. doi:10.1080/15440478.2019.1710650.
- Ramasamy, R., K. Obi Reddy, and A. Varada Rajulu. 2018. Extraction and characterization of calotropis gigantea bast fibers as novel reinforcement for composites materials. Journal of Natural Fibers 15 (4):527–38. doi:10.1080/15440478.2017.1349019.
- Reddy, N., and Y. Yang. 2008. Characterizing natural cellulose fibers from velvet leaf (Abutilon theophrasti) stems. Bioresource Technology 99 (7):2449–54. doi:10.1016/j.biortech.2007.04.065.
- Sapuan, S. M., and M. A. Maleque. 2005. Design and fabrication of natural woven fabric reinforced epoxy composite for household telephone stand. Materials & design 26 (1):65–71. doi:10.1016/j.matdes.2004.03.015.
- Saravanakumaar, A., A. Senthilkumar, S. S. Saravanakumar, M. R. Sanjay, and A. Khan. 2018. Impact of alkali treatment on physico-chemical, thermal, structural and tensile properties of Carica papaya bark fibers. International Journal of Polymer Analysis and Characterization 23 (6):529–36. doi:10.1080/1023666X.2018.1501931.
- Saravanakumar, S. S., A. Kumaravel, T. Nagarajan, P. Sudhakar, and R. Baskaran. 2013. Characterization of a novel natural cellulosic fiber from Prosopis juliflora bark. Carbohydrate Polymers 92 (2):1928–33. doi:10.1016/j.carbpol.2012.11.064.
- Segal, L., J. J. Creely, A. E. Martin, and C. M. Conrad. 1959. An empirical method for estimating the degree of crystallinity of native cellulose using the X-ray diffractometer. Textile Research Journal 29 (10):786–94. doi:10.1177/004051755902901003.
- Senthamaraikannan, P., M. R. Sanjay, K. S. Bhat, N. H. Padmaraj, and M. Jawaid. 2018. Characterization of natural cellulosic fiber from bark of Albizia amara. Journal of Natural Fibers 16 (8):1124–31. doi:10.1080/15440478.2018.1453432.
- Shariff, M. D., S. Madhu, and K. Palani. 2021. Suitability evaluation of mercerized Albizia julibrissin fiber as a potential reinforcement for bio-composites. Journal of Natural Fibers 19 (14):8383–98. doi:10.1080/15440478.2021.1964130.
- Silverio, H. A., W. P. F. Neto, N. O. Dantas, and D. Pasquini. 2013. Extraction and characterization of cellulose nanocrystals from corncob for application as reinforcing agent in nanocomposites. Industrial Crops and Products 44:427–36. doi:10.1016/j.indcrop.2012.10.014.
- Umashankaran, M., and S. Gopalakrishnan. 2021. Effect of sodium hydroxide treatment on physico-chemical, thermal, tensile and surface morphological properties of pongamia Pinnata L. bark fiber. Journal of Natural Fibers 18 (12):2063–76. doi:10.1080/15440478.2019.1711287.
- Vijay, R., J. D. James Dhilip, S. Gowtham, S. Harikrishnan, B. Chandru, M. Amarnath, and A. Khan. 2020. Characterization of natural cellulose fiber from the barks of vachellia farnesiana. Journal of Natural Fibers 19 (4):1343–52. doi:10.1080/15440478.2020.1764457.
- Vijay, R., D. L. Singaravelu, A. Vinod, M. R. Sanjay, and S. Siengchin. 2019. Characterization of alkali-treated and untreated natural fibers from the stem of parthenium hysterophorus. Journal of Natural Fibers 18 (1):80–90. doi:10.1080/15440478.2019.1612308.
- Vinod, A., R. Vijay, D. L. Singaravelu, M. R. Sanjay, S. Siengchin, and M. M. Moure. 2019. Characterization of untreated and alkali treated natural fibers extracted from the stem of Catharanthus roseus. Materials Research Express 6 (8):085406. doi:10.1088/2053-1591/ab22d9.
- Yan, L., N. Chouw, and K. Jayaraman. 2014. Flax fibre and its composites–a review. Composite Part B: Engineering 56:296–317. doi:10.1016/j.compositesb.2013.08.014.
- Yao, F., Q. Wu, Y. Lei, W. Guo, and Y. Xu. 2008. Thermal decomposition kinetics of natural fibers: Activation energy with dynamic thermogravimetric analysis. Polymer Degradation and Stability 93 (1):90–98. doi:10.1016/j.polymdegradstab.2007.10.012.