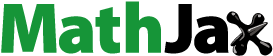
ABSTRACT
Natural fibers are gaining importance due to environmental concerns and sustainability issues. However, their mechanical performance is not up to the mark. To overcome this problem, natural fiber-based 3D woven structures are used in structural applications. The mechanical performance of 3D woven structures can be further enhanced by adding auxetic mechanisms to the structures. Auxetic structures have exceptional mechanical properties due to a negative Poisson’s ratio. In the present study, 3D woven orthogonal warp, weft, and bidirectional interlock structures were developed with jute yarn, and the effect of interlocking pattern on the auxeticity and different mechanical properties (tensile, stiffness, tear) of the structures was investigated. The results revealed that the 3D warp interlock structure showed the highest auxeticity, while the bidirectional interlock depicted the least auxeticity. Due to higher auxeticity, the thickness of the warp interlock structure was increased after applying force to it. The change in the thickness of the woven structure also increases its energy dissipation capability. Furthermore, structures having higher auxeticity also manifest higher tensile, stiffness, and tear properties as compared to other structures. The results are also statistically analyzed using one-way ANOVA (Tukey).
摘要
由于环境问题和可持续性问题,天然纤维越来越重要. 然而,它们的机械性能达不到标准. 为了克服这个问题,在结构应用中使用基于天然纤维的3D编织结构. 3D编织结构的机械性能可以通过向结构添加增强机制来进一步增强. 由于负泊松比,辅助结构具有特殊的机械性能. 在当前的研究中,用黄麻纱线开发了三维机织正交经、纬和双向互锁结构,并研究了互锁图案对结构的强度和不同力学性能(拉伸、刚度、撕裂)的影响. 结果表明,三维翘曲互锁结构显示出最高的凹凸度,而双向互锁显示出最小的凹凸度. 由于较高的弹性,在施加力后,经纱互锁结构的厚度增加. 编织结构厚度的变化也增加了其能量耗散能力. 此外,与其他结构相比,具有更高强度的结构还表现出更高的拉伸、刚度和撕裂性能. 结果也通过单向方差分析(Tukey)进行统计分析.
Introduction
Woven structures are classified into two types, i.e., two-dimensional (2D) woven structures and three-dimensional (3D) multilayer interlock woven structures (Mengru et al. Citation2022; Umair et al. Citation2022; Zhang et al. Citation2020). Two-dimensional woven structures have significant length and width but a low thickness, whereas three-dimensional woven structures have significant length, width, and considerable value of thickness too (Mawkhlieng, Majumdar, and Laha Citation2020; Wambua and Anandjiwala Citation2011). The problem with 2D woven structures is that they have poor out-of-plane mechanical performance (Bahei-El-Din and Zikry Citation2003). This problem is resolved by multilayer interlock structures. The presence of yarns in the Z-axis improves the out-of-plane mechanical performance of 3D woven structures (Ansar, Xinwei, and Chouwei Citation2011; Chiu and Cheng Citation2003). Multilayered woven structures are divided into two types based on the interlocking pattern of yarns, i.e., (i) orthogonal interlock multilayered structures and (ii) angle interlock multilayered structures. These are further divided into layer-to-layer (LL) interlock and through-thickness (TT) interlock structures (Chen, Waterton Taylor, and Tsai Citation2011; Nawab, Legrand, and Koncar Citation2012).
Examples of 3D structures are spacer fabrics, shell fabrics, terry structures, and multilayer structures (Chen, Taylor, and Tsai Citation2015). 3D woven structures improve mechanical performance and create a balance between in-plane and out-of-plane mechanical properties of the structure as compared to 2D woven structures (Gnaba et al. Citation2019; Kashif et al. Citation2019).
Nawab et al. (Citation2018) studied the effect of interlocking patterns on the mechanical performance of 3D woven structures. The results concluded that a layer-to-layer hybrid structure showed higher tensile strength, elongation, and thickness as compared to a through-thickness hybrid structure. Similarly, Umair et al. (Citation2018) developed warp, weft, and bidirectional interlock structures and compared their mechanical properties. The results revealed that warp and weft interlock structure-based composites showed higher tensile strength, while bidirectional interlock structure-based composites showed higher flexural and impact strength. Dynamic mechanical analysis results showed that the maximum capacity of energy dissipation was shown in bidirectional interlock samples, while the loss of moduli and maximum storage was shown in warp interlock samples. The mechanical performance of 3D woven structures can be further enhanced by adding auxetic mechanisms to the structures. Auxetic structures behave opposite to normal structures or materials. Commonly, when tensile force is applied to non-auxetic materials, they shrink or contract in a direction perpendicular to the applied force. On the other hand, auxetic materials expand in a perpendicular direction or increase their thickness under tensile force (Attard et al. Citation2020; Farrugia, Gatt, and Grima Citation2020). This is due to their internal structure and inherent properties of the material. Due to this unique behavior, auxetic materials have a negative Poisson’s ratio (K. Alderson et al. Citation2012; Liu et al. Citation2010).
(Steffens, Rana, and Fangueiro Citation2016) stated that due to the exceptional impact performance of auxetic structures, it can be used in protective helmets, cut-resistance fabric, and in bulletproof vests. Auxetic structures can also be used in medical applications in the form of controlled drug delivery and smart bandages that contain healing agents. These bandages open the pores according to the size of the swollen part. As the swollen part reduces, the pores become narrower, and the release of a drug or healing agent is controlled. Auxetic structures also improve the thermophysiological comfort of fabric by varying the air permeability and moisture management capability under different tension according to the requirement, during exercise athlete stretches their body, as a result, tensile force is applied to the garment, if the garment is made from auxetic fabric then it expands in a lateral direction and increases the pore size in the garment, therefore air permeability and moisture management of the garment is increases (Wang and Hong Citation2014b).
The auxetic structure can be developed through different methods, such as by using inherently auxetic fibers (Alderson et al. Citation2002; Ravirala et al. Citation2005) or from the buckling networks of randomly distributed nanofibers to develop random auxetic structures (Domaschke et al. Citation2019). Auxetic structures can also be developed by using helical auxetic yarn in the structure as warp and weft (J. Chen et al. Citation2021; Razbin et al. Citation2022; Ullah, Ahmad, and Nawab Citation2020), or by using the auxetic weave structures, such as reentrant, rotating units, and chiral (Zulifqar, Hua, and Hong Citation2018). Due to low cost, continuous manufacturing, and no limitation of materials, develop the interest of researchers to introduce the auxeticity at the structural level. Non-woven and knitted-based auxetic structures can be widely used as scaffolds in medical applications (Deshpande et al. Citation2020; Sharma, Kushawah, and Rawal Citation2019). (Rawal et al. Citation2020) developed nonwoven-based auxetic structures, which can be used as scaffolds in biomedical applications. Auxetic-based nonwoven structures showed higher porosity and mechanical strength than conventional nonwoven-based structures. A similar type of work was done by Paxton et al. (Citation2020) to develop a scaffold from tubular auxetic structures via the melt electro-writing technique. Jin et al. (Citation2021) used the same melt electro-writing technique to develop nanofiber-based tunable auxetic scaffolds.
Braided-based auxetic structures can be used as filters due to the variable opening of the braided structure in response to tensile load. This concept was used by Shen and Adanur (Citation2019) to develop an auxetic braided structure from helical auxetic yarn, which reduces its opening in response to tensile load. Researchers have done a lot of work on the development of knitted auxetic structures (Hong, Wang, and Liu Citation2011; Luan et al. Citation2020; Ugbolue et al. Citation2010; Wang and Hong Citation2014a; Zhao et al. Citation2020). Kevlar-based, rhombus-shaped grid reentrant weft knitted auxetic structures were developed, and their stab resistance performance was studied. The results showed that due to its auxetic behavior the reentrant weft knitted auxetic structure showed higher stab resistance than a non-auxetic plain knitted structure with the same raw materials and stitch length (Sun et al. Citation2021). However, due to poor structural stability, it cannot be preferred to be used in impact applications. Weaving technology is currently used to develop more stable auxetic structures for high-end applications. Zulifqar, Hua, and Hong (Citation2020) developed single- and double-layered auxetic woven structures from foldable geometry using non- auxetic yarn. Initially, 2D auxetic structures were developed and used as reinforcement in composites, but due to poor TT properties and delamination problem, researchers shifted from 2D auxetic structures to 3D auxetic structures (Moshtaghian et al. Citation2022).
Liaqat et al. (Citation2016) compared the mechanical performance of 3D woven auxetic and non-auxetic structure-based composites. The results concluded that the auxetic structure-based composite showed 8% higher energy dissipation capability than the non-auxetic structure-based composite. Khan et al. (Citation2019) developed different 3D woven structures and studied the effects of auxeticity on mechanical performance. The results concluded that a higher auxetic structure has improved the 184.7% impact strength as compared to the lower auxetic structure. Khan et al. (Citation2019) studied the effect of Poisson’s ratio or structure auxeticity on the mechanical properties of developed structures.
As per available literature, maximum work was found on the development of 2D woven auxetic structures, and very few studies were found on 3D woven auxetic structures. However, up to the best of our knowledge, no published data is available on the comparison of auxetic and mechanical properties (tear strength, tensile strength, and stiffness) of warp, weft, and bidirectional interlock structures. The objective of this study was to develop 3D woven warp, weft, and bidirectional interlock structures and evaluate their auxetic behavior and also to correlate the effect of auxeticity on the mechanical properties (tear strength, tensile strength, and stiffness) of developed structures. Results are also statistically analyzed through the one-way ANOVA (Tukey) technique. This study suggests the most suitable structure for protective textile applications.
Materials and method
Singeing of jute yarn
Jute yarn was purchased from Sargodha Jute Mill Ltd., Faisalabad, Pakistan; untreated jute yarn has a rough surface, and it has a high number of protruding fibers on the surface, which create clinging during the weaving process, and as a result yarn can easily break during the fabric manufacturing process. To avoid the yarn breakage problem, either sizing or signing can be done. Sizing creates a separate layer on yarn, so complete removal of size material from yarn is difficult, therefore in this study, the singing process was used as an alternative for the sizing process.
Linear density, breaking force, and tenacity of jute yarn before singeing are 6.5 (NEC), 744.7 (cN), and 8.19 (cN/tex), respectively. After singeing the properties become 6.8 (NEC), 730 (cN), and 8.45 (cN/tex). After the singeing process, the linear density of yarn becomes higher due to the burning of protruding fibers, while the tenacity of singed jute yarn is slightly increased as compared to unsinged yarn. This may be due to the leftover lignin in the structure after the singeing process (Asghar et al. Citation2021).
Development of 3D woven structures
LL interlock structures showed better mechanical properties than TT interlock structures (Umair et al. Citation2018). Therefore, in the present study three types of 3D woven orthogonal LL interlock structures such as warp, weft interlock, and bidirectional interlock (warp and weft combined) were developed. The warp and weft density for all three structures remain the same, i.e., 36/inch. With the help of Texgen software cross-sectional view of warp interlock, weft interlock, and warp-wise cross-section of bidirectional interlock, weft-wise cross-section of bidirectional interlock structures are shown in (a, b,c1,c2), respectively. All samples were developed on the terry loom.
Figure 1. Cross-sectional views of the orthogonal layer-to-layer (a) warp interlock, (b) weft interlock, (c1) warp wise cross-section of bidirectional interlock, and (c2) weft wise cross-section of bidirectional interlock.
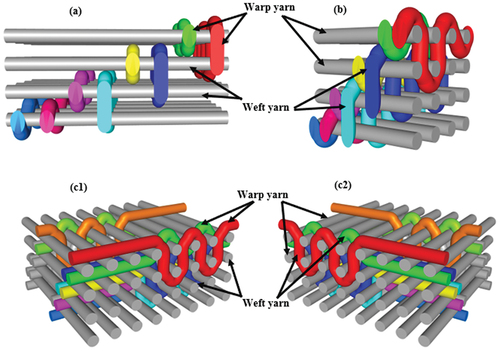
shows the structure construction, warp, and weft-wise crimp %, and areal density for each structure.
Table 1. Construction parameters of woven structures.
Testing
Different tests were performed to evaluate the mechanical performance and auxeticity of the developed samples. The auxeticity of 3D woven reinforcement was measured on a fabric tensile strength tester (1992 model) with the attachment of a digital thickness meter. The sample size for the auxeticity test was 152.4 mm × 101.6 mm (Length × Width). The initial thickness of reinforcement was measured at zero force, and then the reinforcement was stretched to 10 mm, and again the final thickness was measuredusing the digital thickness meter. Record the values and put them into Poisson’s ratio formula to calculate the reinforcement’s auxeticity in both warp and weft directions.
Equation 1 shows the mathematical equation for Poisson’s ratio.
where is the Poisson’s ratio,
represents a change in thickness, and Ɛx represents the axial strain. Put the values of axial strain and change in thickness in the equation to calculate the out-of-plane Poisson’s ratio of the samples. The tensile strength test was performed according to the standard test procedure ASTM D 5034 on Universal Testing machine UTM (Allroundline Z100, Zwick/Roell, Germany) has been shown in , the sample size for tensile testing was (length × width) 152.4 × 101.6 mm. A stiffness test was performed on a fabric stiffness tester (King precision measurement, Greensboro, NC) according to the standard procedure ASTM D4032. The sample size for the stiffness test was 102 × 102 mm. The tear strength test was performed on a pneumatic tear strength tester (Gatelab Elmendorf tear strength tester) according to the standard test procedure ASTM D1424, and the sample size for the tear test was (length × width) 100 × 63.5 mm.
shows the coding of samples, which was used for the notation in characterization instead of the complete sample name, as each test was performed in the warp and weft direction of the structure therefore coding was done in the same way. Wp is used for warp interlock and (P) is used for warp-wise direction; similarly, Wt is used for weft interlock and (T) is used to represent weft-wise direction. B represents the bidirectional interlocking, and the same notation is used for warp and weft-wise direction as in above samples.
Table 2. Sample coding for characterization.
Results and discussions
Auxeticity
The initial length of all samples was 152.4 mm, and the final length of all samples was 162.4 mm. The Poisson’s ratio was calculated from the ratio of the change in thickness to the axial strain. The results of Poisson’s ratio are shown in . The Poisson‘s ratio was calculated on a tensile strength tester with an attachment of a thickness meter as shown in .
Figure 2. (a) Poisson’s ratio of 3D woven samples and (b) modified tensile strength tester for auxeticity test.
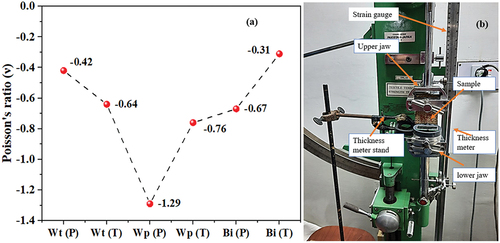
Maximum auxetic behavior was shown for the warp interlock structure in the warp direction, and the Poisson’s ratio of the respective sample was −1.29. This is due to less number of intersections in the warp interlock structure, therefore it shows maximum auxetic behavior (Khan et al. Citation2019; Umair et al. Citation2018). When a force is applied on the warp interlock structure, then due to the less number of intersections, interlocking yarn can easily push the layers in opposite directions to increase the resultant thickness. While the minimum auxetic behavior was shown by a bidirectional interlock structure in the weft direction, the value of Poisson’s ratio was −0.31. The bidirectional interlock has a high number of intersection points, which restricts the movement of yarns; therefore, layers cannot easily move in the opposite direction to increase the resultant thickness.
Tensile test
Tensile strength test results are divided into two parts, the warp-wise and weft-wise tensile strength of all samples. shows the tensile strength versus elongation (%) curves of the warp interlock, weft interlock, and bidirectional interlock structure in the warp direction. The warp interlock structure showed the highest tensile strength of 2172 Pa and a minimum elongation of 5.2%. It is due to the higher auxetic behavior of the warp interlock structure. When force is applied to the sample, the sample increases its thickness and dissipates more force within the sample; therefore, its tensile strength is maximum, and elongation is minimum as compared to other samples in the warp direction. The weft interlock structure showed the least tensile strength 1662 Pa and a higher elongation of 12.5%. Elongation is higher due to the easy movement of warp yarn in the weft interlock structure because the weft yarn is responsible for interlocking in the weft interlock structure. Bidirectional samples showed better tensile strength than the weft interlock and higher elongation than the warp interlock. Better tensile strength is due to the section of warp interlock in the structure, while the elongation in the sample is due to the part of the weft interlock in the structure. shows the universal testing machine, which was used for the tensile testing of fabric.
Figure 3. (a) Tensile strength and elongation results of weft, warp, and bidirectional interlocks (Warp direction), and (b) universal testing machine.
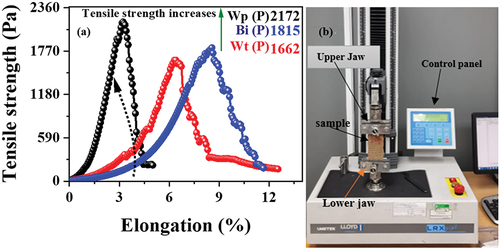
shows the tensile strength versus elongation (%) curves of warp interlock, weft interlock, and bidirectional samples in the weft direction. The maximum tensile strength is shown by the warp interlock structure. While elongation is maximum in a bidirectional interlock sample. Bidirectional samples have higher tensile strength than weft interlock samples due to both interlocking patterns in the structure; therefore, they have the collective properties of both warp and weft interlock samples. While the warp interlock structure showed the highest tensile strength and minimum elongation, due to its higher auxetic nature, the applied force is initially consumed in the structure modification then after increasing the thickness, the force dissipation ability of the sample is increased; therefore, it has higher tensile strength and lower elongation than weft and bidirectional interlock sample. Elongation in the structure significantly depends on the crimp % and mobility of the yarn in the structure, elongation % has a direct relation with crimp %. The bidirectional interlock sample has a maximum elongation % due to having a higher number of crimps as compared to the weft and warp interlock sample.
Figure 4. Tensile strength and elongation results of weft, warp interlock, and bidirectional interlocks (Weft direction).
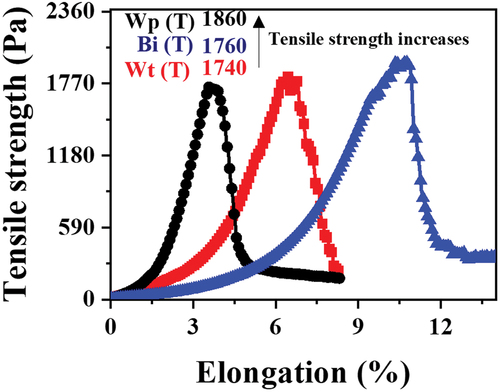
Statistical analysis of tensile test
Tukey comparison tool of one-way ANOVA was used to study the effect of auxeticity on the tensile strength of the structure. P value and R square during one-way ANOVA are 0.000 and 96.92%, respectively. The p-value indicates that the effect of Poisson’s ratio on tensile strength is significant because it is less than 0.05. It means that by changing the Poisson’s ratio of 3D woven structure, their tensile strength in warp and weft directions also changed. Moreover, the coefficient of determination R-square (R-sq) is the percentage that indicates how much the model can explain the variation in the response. The higher the R-square value, the higher the accuracy of the model, as it will more accurately explain the variation in the response. In the case of tensile strength results warp-wise and weft-wise, the R-sq value was 96.92%. Tukey comparison and interval plots for tensile strength are shown in , respectively. Interval plots explain the range of tensile strength results, while the Tukey comparison is used to evaluate whether the difference between the pair of groups is statistically significant or non-significant. According to Tukey’s comparison if the difference between the means of the two confidence intervals is not equal to zero is considered significant.
Figure 5. Tensile strength: (a) tukey simultaneous plot and (b) interval plot of warp interlock, weft interlock, and bidirectional interlock structure.
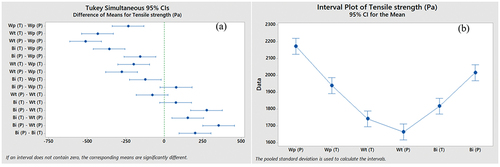
shows the Tukey simultaneous plot for tensile strength in warp and weft directions; only three pairs of means, namely, Bi (p)-Wp (T), Wt (P)-Wt (T), and Bi (T)-Wt (T) have zero in their range, which showed their differences were non-significant. While the rest of the combination of pairs have non-zero values in their range therefore their differences were considered practically significant. shows the interval plots of tensile strength in warp and weft directions. Wp (T) overlaps with Bi (P), and Wt (T) overlaps with Wt (P) and Bi (T), so therefore the difference in means of these intervals was considered non-significant. Only Wp (P) interval does not overlap with any other intervals; therefore, the difference in means of this interval is significantly different.
Stiffness test
To evaluate the rigidity of the fabric, a stiffness test was performed on the fabric stiffness tester. indicates that the warp interlock structure shows the highest stiffness at 34.32 N (3500) gf. This is due to the auxetic behavior of the warp interlock structure. When force is applied to the fabric, the thickness of the auxetic structure is increased in response to the applied force, so more force is required to pass through the hole of the stiffness meter to measure the stiffness of the structure. The bidirectional sample has a stiffness value of 15.88 N (1620 gf), its stiffness value is slightly higher than the weft interlock due to the presence of a warp interlock section, and the weft interlock sample has a stiffness value of 15.00 N (1530gf). The fabric stiffness tester is shown in .
Statistical analysis of stiffness test
One-way ANOVA (Tukey comparison) was used to study whether the effect of Poisson’s ratio on fabric stiffness of 3D woven structure is significant or non-significant. P value and R square during One-way ANOVA are 0.000 and 99.98%, respectively. P values indicate that the effect of Poisson’s ratio on stiffness is significant. The R square value indicates that the model accurately explains the variation in response. Tukey comparison and interval plots for the structural stiffness are shown in respectively.
Figure 7. Fabric stiffness: (a) Tukey simultaneous plot and (b) interval plot of warp, weft, and bidirectional interlocks.
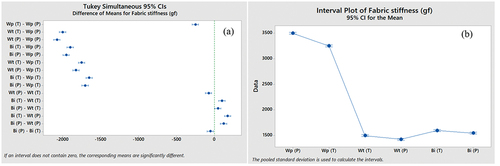
Tukey simultaneous plot of structural stiffness for warp interlock, weft interlock, and bidirectional interlock is shown in ; it indicates that only two pairs of intervals, namely, Bi (P)-Bi (T), and Bi (P)-Wt (T) have 0 in their range, so practically, these pairs were considered non-significant. The rest of the pairs have a non-zero mean value in their range, so all others are considered practically significant.
Interval plots of structural stiffness for warp, weft, and bidirectional interlock structures are shown in . Wp (P) and Wp (T) do not overlap with any other intervals; therefore, the differences in means of Wp (P) and Wp (T) intervals are significantly different. While Wt (T) overlaps with Wt (P) and Bi (T) overlaps with Bi (P), so, therefore, the difference in means of these intervals is non-significant.
Tear test
Tear strength is used to evaluate the ability of structural resistance to tear along a breach or damaged position in the process of use. depicts the tear strength of warp, weft, and bidirectional interlock structures. According to the results, a structure with a lower Poisson’s ratio has a higher tear strength. It is shown that the auxeticity has an inverse relation with the tear strength of the structure. At higher auxeticity, the structure increases its thickness in response to an external force, so a higher force is required to tear it. Therefore, by increasing the auxeticity of the structure, the tear strength of the structure also increases. The warp interlock structure shows the highest tear strength value of 294 N in the warp direction, whereas the bidirectional interlock structure shows the least tear strength value of 250 N. shows a pneumatic pendulum tear strength tester.
Statistical analysis of tear test
Tukey comparison tool of one-way ANOVA was used to study the effect of auxeticity on the tear strength of 3D woven structure is significant or non-significant. P value and R square value during one-way ANOVA are 0.000 and 93.09%, respectively. Tukey comparison and interval plots for tear strength are shown in , respectively.
Figure 9. Tear strength: (a) Tukey simultaneous plot and (b) interval plot of warp, weft, and bidirectional interlocks.
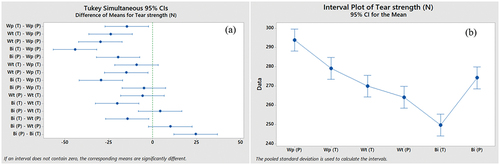
The Tukey simultaneous plot of tear strength for warp, weft, and bidirectional interlock structures is shown in ; the confidence interval of the Tukey plot indicates that five pairs of intervals, namely, Bi (P)-Wt (P), Bi (P)- Wt (T), Bi (P)-Wp (T), Wt (T)-Wp (T), and Wt (T)-Wt (P) have 0 in their range; so practically, these pairs were considered non-significant. The rest of the pairs have a non-zero mean value in their range, so all others are considered practically significant.
Interval plots of tear strength for warp, weft, and bidirectional interlock structure are shown in . Wp (P) and Bi (T) did not overlap with any other intervals; therefore, the differences in means of Wp (P) and Bi (T) intervals are significantly different. Wp (T), Wt(T), Wt(P), and Bi(P) overlap with each other; therefore, the differences in means of these intervals are non-significant.
depicts the relation of Poisson’s ratio with tensile strength, tear strength, and structure stiffness. It was concluded that Poisson’s ratio has an inverse relation with tensile strength, tear strength, and structural stiffness. The warp interlock structure has the lowest negative Poisson’s ratio; therefore, it has the highest tensile strength, tear strength, and fabric stiffness. Due to the higher auxeticity, the applied force is initially used to change the structural dimensions by increasing the thickness. With increasing structure thickness, the energy absorption capacity of the structure increases, so the structure that has higher auxetic behavior has higher mechanical properties. The least mechanical properties were shown by the bidirectional interlock structure in the weft direction, due to lower auxetic behavior.
Conclusions
In this study, three types of auxetic 3D woven structures (warp interlock, weft interlock, and bidirectional interlock structures) were developed. The characterization techniques including the auxeticity test, tensile strength, stiffness test, and tear strength test were performed to evaluate the auxetic and mechanical performance of developed samples. Auxetic results depict that warp interlock structures showed the highest auxeticity, while bidirectional structures showed the least auxeticity. The auxeticity of the structure strongly influences the mechanical performance of these structures. The warp interlock structure showed the highest tensile strength in the warp and weft direction, due to the higher auxeticity of the warp interlock structure. The thickness of the warp interlock structure increases with increasing the applied force; therefore, its energy-absorbing capability also increases. Due to the high energy absorption capability, the tensile strength of the warp interlock structure also increases. The stiffness test results concluded that more force is required to bend the auxetic structure due to increases in thickness and indentation property of the auxetic fabric. Therefore, the warp interlock structure showed higher stiffness as compared to the rest of the samples. A similar trend was observed in tear strength results. The higher the auxeticity of the structure, the higher will be the tear strength of the structure. Overall, the warp interlock structure showed the highest tear strength, while the bidirectional structure showed the least tear strength. The results were also analyzed statistically with one-way ANOVA (Tukey comparison). The auxetic structure of fabric significantly affects the mechanical performance of 3D woven structures with different interlocking patterns such as warp, weft, and bidirectional interlock 3D woven structures. Conclusively, the warp interlock structure has excellent mechanical properties, making it ideal for applications such as ballistics and protective textiles.
Highlights
Warp, weft, and bidirectional interlock 3D woven structures were developed from singed jute yarn, and their auxeticity, tensile strength, stiffness, and tear strength were tested.
Warp interlock showed the highest auxeticity, and bidirectional interlock showed the minimum auxeticity. Under tensile load, the structure with higher auxeticity increases its thickness due to the negative Poisson’s ratio.
Warp interlock has higher tensile strength, followed by bidirectional and weft interlocks due to their higher auxetic behavior.
Warp interlock has higher stiffness value; due to higher auxeticity, the structure requires more force to bend; therefore it has higher stiffness value as compared to other structures.
The shear strength of warp interlock is higher as compared to other samples, due to increase in thickness after applying force on it.
The results are statistically analyzed with the help of one-way ANOVA (Tukey), which showed that auxeticity has a significant effect on the tensile strength, fabric stiffness, and tear strength results.
Ethical approval
This material is the authors’ own original work, which has not been previously published elsewhere.
Acknowledgments
During the sampling, we appreciate the assistance provided by the Director of Advanced Textile Research and Innovation Center at National Textile University. A special thanks goes to the Director of NCCM National Textile University for his assistance during samples testing.
Disclosure statement
No potential conflict of interest was reported by the authors.
Additional information
Funding
References
- Alderson, K., A. Alderson, S. Anand, V. Simkins, S. Nazare, and N. Ravirala. 2012. Auxetic warp knit textile structures. Physica Status Solidi (B) 249 (7):1322–14. doi:10.1002/pssb.201084216.
- Alderson, K. L., A. Alderson, G. Smart, V. R. Simkins, and P. J. Davies. 2002. Auxetic polypropylene fibres:Part 1 - manufacture and characterisation. Plastics, Rubber and Composites 31 (8):344–49. doi:10.1179/146580102225006495.
- Ansar, M., W. Xinwei, and Z. Chouwei. 2011. Modeling strategies of 3D woven composites: A review. Composite Structures 93 (8):1947–63. doi:10.1016/j.compstruct.2011.03.010.
- Asghar, M. A., A. Imad, Y. Nawab, M. Hussain, and A. Saouab. 2021. Effect of yarn singeing and commingling on the mechanical properties of jute/polypropylene composites. Polymer Composites 42 (2):828–41. doi:10.1002/pc.25868.
- Attard, D., P. S. Farrugia, R. Gatt, and J. N. Grima. 2020. Starchirals – A novel class of auxetic hierarchal structures. International Journal of Mechanical Sciences 179 (August):105631. doi:10.1016/j.ijmecsci.2020.105631.
- Bahei-El-Din, Y. A., and M. A. Zikry. 2003. Impact-induced deformation fields in 2D and 3D woven composites. Composites Science and Technology 63 (7):923–42. doi:10.1016/S0266-3538(03)00021-6.
- Chen, J., L. Yonggui, T. Yan, X. Liu, J. Cao, and D. Zhaoqun. 2021. Influence of re-entrant hexagonal structure and helical auxetic yarn on the tensile and auxetic behavior of parametric fabrics. Textile Research Journal 92 (February):004051752199349. doi: 10.1177/0040517521993490.
- Chen, X., L. W. Taylor, and L. J. Tsai. 2015. Three-dimensionaL fabric structures. Part 1 - An overview on fabrication of three-dimensional woven textile preforms for composites. Handbook of Technical Textiles: Second Edition 1 (2):285–304. doi:10.1016/B978-1-78242-458-1.00013-3.
- Chen, X., L. Waterton Taylor, and L.J. Tsai. 2011. An overview on fabrication of three-dimensional woven textile preforms for composites. Textile Research Journal 81 (9):932–44. doi:10.1177/0040517510392471.
- Chiu, C.H., and C.C. Cheng. 2003. Weaving method of 3D woven preforms for advanced composite materials. Textile Research Journal 73 (1):37–41. doi:10.1177/004051750307300107.
- Deshpande, M. V., A. J. West, S. H. Bernacki, K. Luan, and M. W. King. 2020. Poly(ε-caprolactone) resorbable auxetic designed knitted scaffolds for craniofacial skeletal muscle regeneration. Bioengineering 7 (4):134. doi:10.3390/bioengineering7040134.
- Domaschke, S., A. Morel, G. Fortunato, and A. E. Ehret. 2019. Random auxetics from buckling fibre networks. Nature Communications 10 (1):1–8. Springer US. doi:10.1038/s41467-019-12757-7.
- Farrugia, P.S., R. Gatt, and J. N. Grima. 2020. The push drill mechanism as a novel method to create 3d mechanical metamaterial structures. Physica Status Solidi (RRL) – Rapid Research Letters 14 (7):2000125. doi:10.1002/pssr.202000125.
- Gnaba, I., X. Legrand, P. Wang, and D. Soulat. 2019. Through-the-thickness reinforcement for composite structures: A review. Journal of Industrial Textiles 49 (1):71–96. doi:10.1177/1528083718772299.
- Hong, H., Z. Wang, and S. Liu. 2011. Development of auxetic fabrics using flat knitting technology. Textile Research Journal 81 (14):1493–502. doi:10.1177/0040517511404594.
- Jin, Y., C. Xie, Q. Gao, X. Zhou, L. Guangyong, D. Jianke, and H. Yong. 2021. Fabrication of multi-scale and tunable auxetic scaffolds for tissue engineering. Materials & Design 197 (January):109277. The Author(s). Published by Elsevier Ltd. doi:10.1016/j.matdes.2020.109277.
- Kashif, M., S. Talha Ali Hamdani, Y. Nawab, M. Ayub Asghar, M. Umair, and K. Shaker. 2019. Optimization of 3D woven preform for improved mechanical performance. Journal of Industrial Textiles 48 (7):1206–27. doi:10.1177/1528083718760802.
- Khan, M. I., J. Akram, M. Umair, S. T. A. Hamdani, K. Shaker, Y. Nawab, and M. Zeeshan. 2019. Development of composites, reinforced by novel 3D woven orthogonal fabrics with enhanced auxeticity. Journal of Industrial Textiles 49 (5):676–90. doi:10.1177/1528083718795912.
- Liaqat, M., H. Abdul Samad, S. Talha Ali Hamdani, and Y. Nawab. 2016. The development of novel auxetic woven structure for impact applications. The Journal of the Textile Institute (September):1–7. doi:10.1080/00405000.2016.1239330.
- Liu, Y., H. Hong, J. K. C. Lam, and S. Liu. 2010. Negative Poisson’s Ratio weft-knitted fabrics. Textile Research Journal 80 (9):856–63. doi:10.1177/0040517509349788.
- Luan, K., A. West, E. DenHartog, and M. McCord. 2020. Auxetic deformation of the weft-knitted miura-ori fold. Textile Research Journal 90 (5–6):617–30. doi:10.1177/0040517519877468.
- Mawkhlieng, U., A. Majumdar, and A. Laha. 2020. A review of fibrous materials for soft body armour applications. RSC advances 10 (2):1066–86. doi:10.1039/C9RA06447H.
- Mengru, L., P. Wang, F. Boussu, and D. Soulat. 2022. A review on the mechanical performance of three-dimensional warp interlock woven fabrics as reinforcement in composites. Journal of Industrial Textiles 51 (7):1009–58. doi:10.1177/1528083719894389.
- Moshtaghian, Z., H. Hasani, M. Zarrebini, and M. Pourheidar Shirazi. 2022. Development and auxetic characterization of 3D composites produced with newly-designed multi-cell flat-knitted spacer fabrics. Journal of Industrial Textiles 51 (2_suppl):2010S–25S. doi:10.1177/1528083720971696.
- Nawab, Y., X. Legrand, and V. Koncar. 2012. Study of changes in 3D-woven multilayer interlock fabric preforms while forming. The Journal of the Textile Institute 103 (12):1273–79. doi:10.1080/00405000.2012.676267.
- Nawab, Y., M. Kashif, M. Ayub Asghar, A. Asghar, M. Umair, K. Shaker, and M. Zeeshan. 2018. Development & characterization of green composites using novel 3D woven preforms. Applied Composite Materials 25 (4):747–59. doi:10.1007/s10443-018-9720-2.
- Paxton, N. C., R. Daley, D. P. Forrestal, M. C. Allenby, and M. A. Woodruff. 2020. Auxetic tubular scaffolds via melt electrowriting. Materials & Design 193 (August):108787. The Authors. doi:10.1016/j.matdes.2020.108787.
- Ravirala, N., A. Alderson, K. L. Alderson, and P. J. Davies. 2005. Expanding the range of auxetic polymeric products using a novel melt-spinning route. Physica Status Solidi (B) 242 (3):653–64. doi:10.1002/pssb.200460384.
- Rawal, A., S. Sharma, D. Singh, N. Kumar Jangir, H. Saraswat, D. Sebők, A. Kukovecz, D. Hietel, M. Dauner, and L. Onal. 2020. Out-of-plane auxetic nonwoven as a designer meta-biomaterial. Journal of the Mechanical Behavior of Biomedical Materials 112 (April):104069. doi:10.1016/j.jmbbm.2020.104069.
- Razbin, M., M. Jamshidi Avanaki, A. Asghar Asghariyan Jeddi, and H. Dabiryan. 2022. Double-core helical auxetic yarn: A novel structure, geometrical modeling and experimental verification. The Journal of the Textile Institute 113 (7):1256–69. Taylor & Francis. doi:10.1080/00405000.2021.1923928.
- Sharma, S., D. Kushawah, and A. Rawal. 2019. Designing nonwoven auxetic metamaterials with spatially textured functionalities. Materials letters 241:214–18. Elsevier B.V. doi:10.1016/j.matlet.2019.01.038.
- Shen, Y., and S. Adanur. 2019. Mechanical analysis of the auxetic behavior of novel braided tubular structures by the finite element method. Textile Research Journal 89 (23–24):5187–97. doi:10.1177/0040517519851840.
- Steffens, F., S. Rana, and R. Fangueiro. 2016. Development of novel auxetic textile structures using high performance fibres. Materials & Design 106 (1):81–89. doi:10.1016/j.matdes.2016.05.063.
- Sun, Y., X. Wanli, W. Wei, M. Pibo, and F. Xia. 2021. Stab-resistance of auxetic weft-knitted fabric with kevlar fibers at quasi-static loading. Journal of Industrial Textiles 50 (9):1384–96. doi:10.1177/1528083719865044.
- Ugbolue, S. C., Y. K. Kim, S. B. Warner, Q. Fan, C.L. Yang, O. Kyzymchuk, and Y. Feng. 2010. The formation and performance of auxetic textiles. Part I: Theoretical and technical considerations. The Journal of the Textile Institute 101 (7):660–67. doi:10.1080/00405000902733790.
- Ullah, T., S. Ahmad, and Y. Nawab. 2020. Development of helical auxetic yarn with negative poisson’s ratio by combinations of different materials and wrapping angle. Journal of Industrial Textiles 51 (July):152808372094111. doi: 10.1177/1528083720941116.
- Umair, M., K. Shaker, M. Usman Javaid, M. Hussain, M. Kashif, and Y. Nawab. 2022. Effect of weaving patterns on damage resistance of 3D woven jointless T and H shaped reinforcements. Mechanics of Advanced Materials and Structures 29 (1):104–17. doi:10.1080/15376494.2020.1751356.
- Umair, M., S. Talha Ali Hamdani, M. Ayub Asghar, T. Hussain, M. Karahan, Y. Nawab, and M. Ali. 2018. Study of influence of interlocking patterns on the mechanical performance of 3D multilayer woven composites. Journal of Reinforced Plastics and Composites 37 (7):429–40. doi:10.1177/0731684417751059.
- Wambua, P. M., and R. Anandjiwala. 2011. A review of preforms for the composites industry. Journal of Industrial Textiles 40 (4):310–33. doi:10.1177/1528083709092014.
- Wang, Z., and H. Hong. 2014a. 3D auxetic warp-knitted spacer fabrics. Physica Status Solidi (B) 251 (2):281–88. doi:10.1002/pssb.201384239.
- Wang, Z., and H. Hong. 2014b. Auxetic materials and their potential applications in textiles. Textile Research Journal 84 (15):1600–11. doi:10.1177/0040517512449051.
- Zhang, D., G. Yuanhui, Z. Zhang, M. Jia, S. Yue, and L. Gan. 2020. Effect of off-axis angle on low-velocity impact and compression after impact damage mechanisms of 3D woven composites. Materials & Design 192 (1):108672. doi:10.1016/j.matdes.2020.108672.
- Zhao, S., H. Hong, H. Kamrul, Y. Chang, and M. Zhang. 2020. Development of auxetic warp knitted fabrics based on reentrant geometry. Textile Research Journal 90 (3–4):344–56. doi:10.1177/0040517519866931.
- Zulifqar, A., T. Hua, and H. Hong. 2018. Development of uni-stretch woven fabrics with zero and negative poisson’s ratio. Textile Research Journal 88 (18):2076–92. doi:10.1177/0040517517715095.
- Zulifqar, A., T. Hua, and H. Hong. 2020. Single‐ and double‐layered bistretch auxetic woven fabrics made of nonauxetic yarns based on foldable geometries. Physica Status Solidi (B) 257 (10):1900156. doi:10.1002/pssb.201900156.