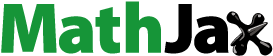
ABSTRACT
Natural fibers obtained from the agricultural wastes are a promising source within the field of acoustic and have already shown favorable results for mitigating the noise pollution. Supported by the experimental data and via an eco-friendly approach, the current study evaluates the impact of fiber size on the sound absorption values of the samples fabricated from sugarcane bagasse (SCB) waste fibers. The samples were formed based on the fiber size and constant bulk densities and thicknesses. The empirical models such as Delany-Bazley (D-B model) along with Best-fit-Nelder-Mead method were also employed to predict the acoustic absorption coefficients of the samples. Therefore, the least-square fit procedure was taken to evaluate the results which is compatible with both the impedance test tube and prediction models. Hence, according to the analyses, the lowest fiber size measured the highest absorption performance (α≃0.63) and airflow resistivity (σ = 6750), indicating that the performance of the fibers reached peaks at lower frequency and slightly decreased at mid and high frequency ranges while the fiber size 0.29–0.37 mm saw a slight rise again. Also, airflow resistivity and sound absorption performance of the SCB fibers decreased with increased fiber sizes.
摘要
从农业废弃物中获得的天然纤维是声学领域中一个很有前途的来源,并且已经显示出减轻噪声污染的有利结果. 在实验数据的支持下,通过一种环保方法,本研究评估了纤维尺寸对甘蔗渣(SCB)废纤维制备的样品的吸声值的影响. 基于纤维尺寸和恒定的体积密度和厚度形成样品. 经验模型如Delany Bazley(D-B模型)和最佳拟合Nelder-Mead方法也被用于预测样品的吸声系数. 因此,采用最小二乘拟5408程序来8BC4估与阻抗测试管和9884测模型都兼容的结果. 因此,根据分6790,最低的纤维5C3A;寸测量到最高的吸收性能(α≈0.63)和气流电阻率(σ = 6750),表明纤维的性能在较低频率达到峰值,在中高频范围略有下降,而纤维尺寸0.29-0.37 mm再次略有上升. 此外,SCB纤维的气流阻力和吸声性能随着纤维尺寸的增加而降低.
Introduction
Extensive urbanization and industrialization have contributed to the pervasive disturbances such as overwhelming noise pollution all around the world. Chronic and excessive exposure to higher levels of noise in cites and occupational settings is the principal cause of numerous adverse health effects such as hearing loss, stress-related disorders, hypertension, heart and internal organ failures, annoyance and even elevated rates of accidents (Tang, Liu, and Yan Citation2022; Yang et al. Citation2016, Citation2018; Zeydabadi et al. Citation2019). As a result, various methods have been developed with the aim of keeping noise exposure below the recommended limits, one of which is the utilization of typical synthetic sound absorbers like glass fibers, mineral wool, polyurethane open-cell foams, etc. However, from the environmental and public health perspective, such absorbers have never been free from problematic issues such as producing a significant amount of carbon footprints during manufacturing and recycling processes as well as their harmful effects on human health (Alves et al. Citation2010; Fouladi et al. Citation2012; Khair et al. Citation2014; Yang et al. Citation2020, Citation2020b). Therefore, the need for sustainable and environmentally friendly alternatives has been emphatically highlighted within the literature. Over the recent decade, the use of acoustic sound absorbers fabricated from natural fibers has received considerable scholarly attention mainly because of the fact that these fibers are relatively inexpensive, readily available, easily recyclable, simply biodegradable and have acceptable sound-absorbing properties (Berardi and Iannace Citation2015b; Buratti et al. Citation2018; Samaei et al. Citation2021; Yang et al. Citation2020a, Citation2022).
In many countries, agricultural solid wastes or crop residues are considered as an environmental challenge owing to the staggering quantity and space they occupy (Othmani et al. Citation2017). In order to dispose of such nuisance, farmers or those in charge of waste management systems usually have no options but burning such wastes in-situ, which in turn contributes to severe environmental pollution. These wastes, however, could be considered as a potential sustainable source for extracting natural fibers. It is assumed that by introducing these fibers into the field of acoustics, it is anticipated that both environmental concerns and noise pollution would be mitigated to a considerable extent (Abdi et al. Citation2021; Tang, Liu, and Yan Citation2022).
Accordingly, the relationships as an agricultural waste and a by-product from sugar industry, bagasse is one of the main solid heterogeneous fibrous residues remaining after the extraction of the sugar-bearing juice from sugarcane. It is estimated that bagasse constitutes over 30% of the sugarcane agricultural product by weight worldwide (Michel et al. Citation2013; Selman-Housein et al. Citation2000).
A hectare of sugarcane plantation roughly generates about 10 tons of sugarcane waste; and each year (Institute, Appropriate Rural Technology Citation2012) and 54 million tons of bagasse are roughly produced all over the world (Hemmasi et al. Citation2011). Only in Iran and particularly in Khuzestan, a province in the southwest of the country, this reaches up to 4.3 million tons annually (Agricultural ministry of Iran). Although a considerable amount of the bagasse all over the world and in Iran is used for conventional purposes such as producing alcohol, pulp, paper board, and even cattle feeding, still tons of wastes materials are accumulated from such processes and disposed inattentively (Mahmud and Anannya Citation2021; Mohammadi et al. Citation2020).
Applying the sugarcane waste fibers or bagasse as an alternative sound absorbing material has therefore been at the center of attention scholarly. Putra et al. conducted a study on the acoustic absorption properties of the samples fabricated from sugarcane waste fibers in 2013. According to the results from this study which had considered the effect of binder composition and fiber density on sound absorption coefficient values of the samples, the sound absorbing properties of the samples with the thickness of 0.5 inch were almost identical to that of commercial acoustic absorbers with average absorption coefficient of 0.65 at frequency 1.2–4.5 kHz.
In the study by Othmani et al. (Othmani et al. Citation2016) the effect of several physical properties such as thickness, fiber size (coarse, medium and fine) and resin content were both experimentally and theoretically investigated on the acoustic absorption performance of the samples fabricated from sugarcane waste materials. The authors employed an impedance tube system as well as three empirical models, Delany-Bazley, Miki and Kumatsu in order to measure and predict the acoustic absorption coefficients of the samples based on their measured air flow resistivity values. The results from this study revealed that the flow resistance and acoustic absorption coefficient both increase as the fiber size was reduced. The experimental data and the theoretical predictions were also found to be in reasonable accord.
In their second study in 2017, Othmani et al. (Othmani et al. Citation2017) conducted yet another study on the samples made from recycled sugarcane wastes. They considered several physical parameters of the waste materials such as flow resistivity, porosity, tortuosity, and viscous and thermal characteristic lengths as well as employing the direct and inverse methods in order to predict the values of sound absorption coefficients by Johnson – Champoux–Allard (JCA) model. According to the results from this study, the experimentally obtained values of the acoustic absorption coefficients agreed well with those predicted by the Johnson-Allard model, indicating that the studied material has a considerable capability for the sound absorption.
Malawade and Jadhav carried out a study to predict the acoustic absorption coefficients of samples of bagasse fibrous material by utilizing an empirical model based on airflow resistivity. The study findings indicated that the thickness of bagasse material has a positive correlation with both the acoustic absorption coefficient and the air flow resistivity of the samples. Moreover, the results highlighted the fact that in the low frequency region, the theoretical and experimental findings are in good agreement and the inclusion of an air gap behind the samples increased the sound absorption capabilities as well (Malawade and Jadhav Citation2020).
In another study, Rozli and Azmir (Rozli and Azmir Citation2020) measured the sound absorption coefficients as well as the transmission loss values of the sample composites fabricated from raw sugarcane bagasse and polyvinyl acetate as the binder. The results from the experimental measurements showed that increasing the thickness of the samples as well as the addition of an air gap behind them would relatively enhance their acoustical performance in middle range frequency. Optimal density also contributed to greater sound absorption performance; in a way that at a frequency of 0.98 kHz, the sample with the optimal density, exhibited the best sound absorption value. The results also showed that the sound absorption performance of the sugarcane bagasse samples at certain thickness is higher than that of the synthetic foam composite absorber and its sound transmission loss is comparable with the synthetic one.
Isa et al. (Isa and Wahid Citation2021) investigated the sound absorption properties as well as thermal conductivity and water absorption of an acoustic panel fabricated from sugarcane bagasse and wood dust. They concluded that the acoustic panel fabricated from the green composite of sugarcane bagasse and wood dust can effectively absorb the high-frequency sound.
In the study by Doost-hoseini et al. (Doost-Hoseini, Reza Taghiyari, and Elyasi Citation2014) the physical, mechanical, and sound absorption properties of the insulation boards made from sugar cane bagasse were studied and the results indicated that sound absorption coefficients of such boards are significantly influenced by the type of the board and the resin used in this study.
As cited in some of the above mentioned studies, the scientific techniques such as empirical and phenomenological models have facilitated estimating the acoustic performance of the samples made from natural fibers (Bansod and Mohanty Citation2016; Iannace, Ciaburro, and Trematerra Citation2020; Samaei et al. Citation2021). These mathematical models have been employed in many applications in this field as well. The phenomenological models are mostly accepted in large group of previous studies since they mainly focused on the multi-parametric study methodology (Taban et al. Citation2021). In that regard, the models such as Johnson – Champoux–Allard (JCA) have been frequently used in case of natural fiber material modeling along with a microscopic approach. These models provide an option for simulating the materials under investigation; particularly based on the non-acoustic parameters such as characteristics of impedance and propagation of the sound via samples under study. They usually take into account the values of airflow resistivity, tortuosity, porosity, viscosity, and thermal characteristic length of the sample and have been specified for the evaluation of acoustic characteristics of the materials (Taban et al. Citation2019).
The single-parametric models such as Delany-Bazley (Delany and Bazley Citation1970), Miki (Miki Citation1990), Garai-Pompoli (Garai and Pompoli Citation2005) and Komatsu (Komatsu Citation2008), on the other hand, predict the acoustic absorption characteristic of the materials through empirical relations with the help of regression models. These models particularly rely on the test parameters such as the resistivity of the sound absorbers against the airflow.
With regard to the previous literature, the present study aimed to investigate the impact of fiber size on the sound absorption behavior of sugarcane bagasse waste fibers via the assessment of sound absorption characteristics of such fibers using Delany and Bazley (D-B) model and experimental analysis based on the impedance tube system at a specific frequency range.
Material and methods
Sample preparation
The crushed sugarcane bagasse (SCB) waste fibers were selected as the test material in this study. The waste materials were obtained from a sugarcane industry located in Khuzestan province southwest of Iran prior to be treated, washed, crushed, and sieved to the required fiber size as follows:
The test materials were initially crushed and then mixed in a mixer until a mass of lumpy fibers was formed. The mass was then grinded in a rotary machine to obtain fine and coarse fibers.
Selected sieves were later used to establish the following classification of mesh sizes:
The fine fiber size: from 0.29 mm to 0.37 mm (),
The semi-fine fiber size: from 0.79 mm to 1.3 mm (),
The semi-coarse fiber size: from 2.32 mm to 3.34 mm (),
The coarse fiber size: from 5.31 mm to 7.20 mm ().
Having specified for size, the total mass of the fibers required for fabricating each sample (i.e. prepared from the mixture of fibers and binder), was calculated based on the preferred sample bulk density and thickness.
In this study, polyvinyl alcohol (PVA, Sigma-Aldrich Co. LLC, UK) was used as the binder to hold the SCB waste fibers together and form the samples. 5 g of PVA was dissolved in 100 ml of water and stirred for 3 h at 80°C with a rotation of 500 rpm until a homogenous solution of 5% PVA was achieved. Accordingly, the volume of binder required to create each sample was determined by trial and error and the quantity of the binder was estimated to be 10% of the total mass of the fibers.
According to , the mixture of fiber and binder was formed using a set of pistons and cylindrical molds. The mixture was first inserted into the mold and a manual press machine exerted the force on the mold for 30 min to shape the sample. The samples formed through this process () were then left to be dried in an oven for six hours.
The resulting samples were then left to cool down before being evaluated in terms of their acoustic absorption coefficients.
By modifying the values of the fiber size during fabrication process, four types of samples were obtained from the SCB waste materials. shows the major characteristics of these samples.
Table 1. The main characteristics of the fabricated samples.
All fabricated samples had a constant thickness of 30 mm, bulk density of 200 kg/m3 and a binder ratio of 10% (). The fiber sizes, however, ranged between 0.29 mm and 7.20 mm; which allowed for evaluation of the effect of fiber size on sound absorption coefficients of the samples.
Experimental procedures
Porosity: Porosity (φ) of the materials can be characterized based on their physical properties that impact the performance of sound absorption. Accordingly, porosity is defined as the ratio of the pore volume observed by a single fiber to the total volume of the pore in fabricated samples (Allard, Depollier, and Guignouard Citation1989; Yang et al. Citation2022). In this study, the porosity of the samples was calculated based on the fibers’ density (ρ fiber) and bulk density (ρ bulk):
, depicts the physical representation of the Field Emission Scanning Electron Microscopic (FESEM) of the sugarcane fibers. Using the image processing technique, the diameter of the SCB fibers was measured as 320 ± 80 μm.
Figure 4. FESEM image of the test samples for fiber size. (a) sample #1, (b) sample #2, (c) sample #3, (d) sample #4.
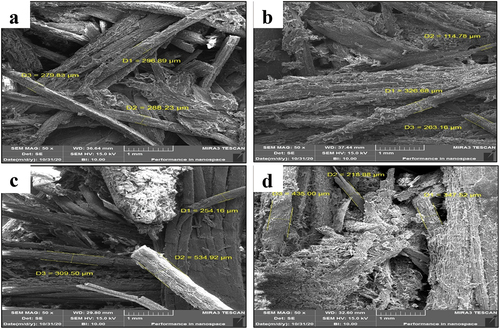
Measurement of the airflow resistivity: In the field of acoustics, airflow resistivity of the materials is a key determinant parameter for estimating the acoustic absorption performance (Dunne, Desai, and Sadiku Citation2017). In this case, the airflow resistivity of the samples was determined by considering a given volumetric flow rate and calculating the differential pressure while the air stream was passing through the sample. According to the mathematical relationships, the airflow resistivity of the samples is calculated by the following equation:
Measurement of the acoustic absorption coefficient: The measurement of sound absorption coefficient values of the samples was conducted by means of an impedance tube method according to ISO 10,534–2. Accordingly, a two-microphone impedance system was used to record the acoustic signals generated by the system loudspeaker prior to conducting the analysis and specifying the sound absorption coefficient values of the samples. The data obtained from the data acquisition component of the system were then processed with the aid of the software developed by BSWA VA-Lab4 (produced by BSWATechnology Co. Ltd., Beijing, China). Before using the software, the calibration was performed at 1 kHz and 114 dB sound pressure level.
Both smaller and larger tubes of the impedance tube system with different tube diameters (30 cm and 100 mm) and microphone spacing were applied to calculate the acoustic absorption coefficients of the samples. The assessment was conducted by referring to the frequency range of 0.2 to 6.3 kHz. Each test was repeated at least three times for all samples in order to minimize the possible errors as well as enhancing the reliability and repeatability of impedance tube measurements. All environmental conditions such as background noise levels, ambient temperature, etc. remained constant during the measurements.
Modeling of the acoustic absorption coefficients
Modeling and prediction of sound absorption coefficient values were carried out using the model presented by Delany and Bazley. Similar to the other empirical models of this kind, D-B model does not necessarily take into account the propagation of sound waves in the pores of the porous media (Delany and Bazley Citation1970). The model, however, considers the power-law relations and non-acoustic parameters based on the following equations:
Finally, the sound absorption coefficient is calculated by:
In order to address the limitations of the selected empirical models, this work implemented the best-fit Nelder-Mead Simplex (NMS) algorithm approach proposed by Berardi and colleagues (Berardi and Iannace Citation2017) to generate the appropriate ci (with i = 1 … 8) coefficients. In addition, the results were compared with the data obtained from the experiments. MATLAB software was utilized to define the codes and optimize the NMS method. The generated ci coefficients are presented in . Accordingly, the mathematical Equationequations 9(9)
(9) to Equation11
(11)
(11) were assigned to estimate the squared difference between the measured and predicted values.
Table 2. D-B model’s coefficients obtained via best fitting and power-law functions approaches.
Results and discussion
Impact of Fiber size on sound absorption performance
With various fiber sizes applied, the sound absorption performance of the samples made from SCB waste fibers also changed. The mathematical modeling (D-B model) along with the best-fit method were applied to predict the acoustic performance of the samples as well. Moreover, the results from the experimental findings were compared with the predicted data to obtain a better understanding of the sound absorption properties of different samples.
According to , with the increase in the level of fiber size, the average sound absorption performance decreases at all frequency ranges. The first peak in the acoustic absorption is the result of a quarter wavelength resonance; i.e. is at the frequency such that the wavelength of sound within the material corresponds to four times the thickness. This depends on the speed of the sound wave in the material, which in turn depends on the air permeability and tortuosity, as well as thickness. In addition, the peak value of the sound absorption was obtained at frequency of 1000 Hz which indicates that the sugarcane waste fibers are sufficiently efficient for noise control at lower frequency range with slight decrease from mid and higher frequency intervals ().
According to , sample # 1 with constant thickness and density of 200 kg/m3 came up with superior absorption coefficient value of 0.92 at 1000 Hz. Sample # 2 showed a peak at frequency range from 2.5 kHz (0.99).
Table 3. Acoustic absorption coefficient value and its difference between experimental and empirical model results.
The effect of airflow resistivity on sound absorption performance
The exertion of the resistance by samples against the airflow is called airflow resistivity. It is a crucial physical characteristic of the fibrous materials for nondestructive measurement of sound absorption performance as well as determining the absorption coefficients obtained from sample data (Dunne, Desai, and Sadiku Citation2017). In other words, the acoustic absorption capability of the samples can be evaluated based on these values of resistivity. Pelegrinis et al. (Horoshenkov, Groby, and Dazel Citation2016; Hurrell, Horoshenkov, and Pelegrinis Citation2018; Pelegrinis, Horoshenkov, and Burnett Citation2016) made use of Kozeny – Carman model to predict the flow resistivity of polyester fiber samples with different bulk material densities and fiber diameters from their acoustic absorption coefficient values. Experimental as well as theoretical findings of this study demonstrated that the flow resistivity of polyester fiber samples increases proportionately with the square of the bulk material density and reduces proportionally with the square of the fiber diameter.
As the fiber size values vary, the resistivity against the airflow and therefore the sound absorption coefficients of the samples vary as well. According to , there is a direct relationship between the values of the airflow resistivity and acoustic performance of the samples. In other words, the elevated levels of resistivity contribute to improved acoustic absorption of the samples. Notwithstanding this, an inverse relationship was found between the fiber size values and both the airflow resistivity and the sound absorption coefficient. The absorption coefficient was found to be rather significant for mid-range frequencies. As a result, a greater level of surface friction brings about an increase in the quantity of energy loss, which in turn leads to an improvement in the level of acoustic performance (Koizumi, Tsujiuchi, and Adachi Citation2002; Samaei et al. Citation2021).
Hence, reduction of the fiber size improves the acoustic absorption of the samples. According to , when the fiber size increases, airflow resistivity and, thus, sound absorption coefficient decreases.
Our results also indicated that the increase in the fiber size led to a decrease in airflow resistivity and significantly affected the absorption capability of the samples.
Comparison with mathematical models
The use of models for predicting the acoustic absorption capabilities of natural fibers has been widely reported by many researchers in the field of acoustics (Lim et al. Citation2018; Taban et al. Citation2021). These models are mainly divided either as empirical or phenomenological. In that regard, in this paper, the D-B empirical model along with the best fit-NMS method was applied to obtain the sound absorption coefficients in addition to the experimental analysis of the samples. The results obtained from both methods were compared with each other and showed that there is an agreement between the model’s prediction and experimental analysis of sound absorption coefficients and the ones obtained from D-B model.
The comparison of the results from applying the D-B model, best-fit method and experimental technique in and , suggest that the resulting coefficients are sufficiently consistent for estimating the acoustic absorption performance of the samples.
shows the values of sound absorption average (SAA) estimated by experiments, D-B model and best-fit approach. As seen in this table, the values of SAA significantly decreased as the fiber size increased. Its values were slightly increased from 200–2500 Hz in one-third octave band frequency. Furthermore, reveals that the best-fit model predicted values at mid-frequency ranges efficiently.
Conclusion
Fibers obtained from sugarcane waste bagasse were considered as potential sustainable and efficient sound absorbers. Although the synthetic sound absorbers have been widely used in the field of acoustics, their environmental and health impacts are considered as a prohibitive factor. This paper has identified the sugarcane waste fibers as a reliable sound absorber by comparing the empirical approach (D-B model) and best-fitted inverse laws on the one hand, and experimental results obtained through the use of impedance tube on the other hand. The results from the best-fit method exhibited a better outcome when compared with data obtained from the impedance tube. When correction has been made to avoid errors from specimen’s placement, there were promising results among the measured and predicted data particularly for finer fiber.
The average absorption coefficient for samples # 1–4 was, 0.63, 0.60, 0.57, and 0.51, respectively. Similarly, the results obtained from the D-B and fitted models also revealed that the values of the sound absorption coefficient were gradually decreased from the finest to coarse fibers. For the same fiber size, the values can approach 0.99 at 1 kHz. However, as the fiber size increased, the values of sound absorption coefficient of each sample proportionately declined as well. SCB is a suitable material for applications including buildings, automobiles, and airplanes owing to its advantageous characteristics. In a majority of these applications, the thermal resistance characteristics of the sound absorber are of the utmost significance. In addition to the sound absorption properties, the sound transmission loss of the materials is also significant for building applications. The authors are actively doing research these properties.
Highlights
The impact of fiber size on the sound absorption performance of sugarcane bagasse (SCB) fibers was studied.
The surface morphology of the SCB fibers was investigated.
The empirical model for prediction of sound absorption coefficient was proposed.
Best-fit-Nelder-Mead method have a good agreement with the experimental data.
Acknowledgements
We are thankful to Mashhad University of Medical Science for providing the necessary laboratory facilities for this work.
Disclosure statement
No potential conflict of interest was reported by the authors.
Additional information
Funding
References
- Abdi, D. D., M. Monazzam, E. Taban, A. Putra, F. Golbabaei, and M. Khadem. 2021. Sound absorption performance of natural fiber composite from chrome shave and coffee silver skin. Applied Acoustics 182:108264. doi:10.1016/j.apacoust.2021.108264.
- Allard, J. F., C. Depollier, and P. Guignouard. 1989. Free field surface impedance measurements of sound-absorbing materials with surface coatings. Applied Acoustics 26 (3):199–15. doi:https://doi.org/10.1016/0003-682X(89)90053-4.
- Alves, C., P. M. C. Ferrão, A. J. Silva, L. G. Reis, M. Freitas, L. B. Rodrigues, and D. E. Alves. 2010. Ecodesign of automotive components making use of natural jute fiber composites. Journal of Cleaner Production 18 (4):313–27. doi:10.1016/j.jclepro.2009.10.022.
- Bansod, P. V., and A. R. Mohanty. 2016. Inverse acoustical characterization of natural jute sound absorbing material by the particle swarm optimization method. Applied Acoustics 112:41–52. doi:https://doi.org/10.1016/j.apacoust.2016.05.011.
- Berardi, U., and G. Iannace. 2015a. Acoustic characterization of natural fibers for sound absorption applications. Building and Environment 94:840–52. doi:https://doi.org/10.1016/j.buildenv.2015.05.029.
- Berardi, U., and G. Iannace. 2015b. Acoustic characterization of natural fibers for sound absorption applications. Building and Environment 94:840–52. doi:10.1016/j.buildenv.2015.05.029.
- Berardi, U., and G. Iannace. 2017. Predicting the sound absorption of natural materials: Best-fit inverse laws for the acoustic impedance and the propagation constant. Applied Acoustics 115:131–38. doi:https://doi.org/10.1016/j.apacoust.2016.08.012.
- Buratti, C., E. Belloni, E. Lascaro, F. Merli, and P. Ricciardi. 2018. Rice husk panels for building applications: Thermal, acoustic and environmental characterization and comparison with other innovative recycled waste materials. Construction and Building Materials 171:338–49. doi:10.1016/j.conbuildmat.2018.03.089.
- Delany, M. E., and E. N. Bazley. 1970. Acoustical properties of fibrous absorbent materials. Applied Acoustics 3 (2):105–16. doi:https://doi.org/10.1016/0003-682X(70)90031-9.
- Doost-Hoseini, K., H. Reza Taghiyari, and A. Elyasi. 2014. Correlation between sound absorption coefficients with physical and mechanical properties of insulation boards made from sugar cane bagasse. Composites Part B: Engineering 58:10–15. doi:10.1016/j.compositesb.2013.10.011.
- Dunne, R., D. Desai, and R. Sadiku. 2017. A review of the factors that influence sound absorption and the available empirical models for fibrous materials. Acoustics Australia 45 (2):453–69. doi:https://doi.org/10.1007/s40857-017-0097-4.
- Fouladi, H., S. Y. P. Mohammad, S. Yi Wen, P. Zong Xin, M. Jailani Mohd nor, M. Afiq Mohd Saleh, and T. Chan Seng. 2012. Replacement of synthetic acoustic absorbers with natural fibers. ASME International Mechanical Engineering Congress and Exposition 83–87.
- Garai, M., and F. Pompoli. 2005. A simple empirical model of polyester fibre materials for acoustical applications. Applied Acoustics 66 (12):1383–98. doi:https://doi.org/10.1016/j.apacoust.2005.04.008.
- Hemmasi, A. H., A. Samariha, A. Tabei, M. Nemati, and A. Khakifirooz. 2011. Study of morphological and chemical composition of fibers from Iranian sugarcane bagasse. American-Eurasian Journal of Agricultural & Environmental Sciences 11 (4):478–81.
- Horoshenkov, K. V., J.P. Groby, and O. Dazel. 2016. Asymptotic limits of some models for sound propagation in porous media and the assignment of the pore characteristic lengths. The Journal of the Acoustical Society of America 139 (5):2463–74. doi:10.1121/1.4947540.
- Hurrell, A. I., K. V. Horoshenkov, and M. T. Pelegrinis. 2018. The accuracy of some models for the airflow resistivity of nonwoven materials. Applied Acoustics 130:230–37. doi:10.1016/j.apacoust.2017.09.024.
- Iannace, G., G. Ciaburro, and A. Trematerra. 2020. Modelling sound absorption properties of broom fibers using artificial neural networks. Applied Acoustics 163:107239. doi:10.1016/j.apacoust.2020.107239.
- Institute, Appropriate Rural Technology. 2012. Briquetted charcoal from sugarcane trash, www.arti-india.org.
- Isa, N. M., and A. Z. A. Wahid. 2021. A study of sugarcane bagasse and wood dust as acoustic panel in building. Progress in Engineering Application and Technology 2 (1):319–27.
- Khair, F. A., A. Putra, M. Jailani Mohd nor, N. Atiqah, and M. Zulkefli Selamat. 2014. Preliminary study on bamboo as sound absorber. Applied Mechanics and Materials 554:76–80. doi:10.4028/AMM.554.76.https://www.scientific.net/
- Koizumi, T., N. Tsujiuchi, and A. Adachi. 2002. The development of sound absorbing materials using natural bamboo fibers. WIT Transactions on the Built Environment 59. doi:10.2495/HPS020161.
- Komatsu, T. 2008. Improvement of the Delany-Bazley and Miki models for fibrous sound-absorbing materials. Acoustical Science and Technology / Edited by the Acoustical Society of Japan 29 (2):121–29. doi:10.1250/ast.29.121.
- Lim, Z. Y., A. Putra, M. J. M. Nor, and M. Y. Yaakob. 2018. Sound absorption performance of natural kenaf fibres. Applied Acoustics 130:107–14. doi:10.1016/j.apacoust.2017.09.012.
- Mahmud, M. A., and F. R. Anannya. 2021. Sugarcane bagasse - a source of cellulosic fiber for diverse applications. Heliyon 7 (8):e07771. doi:10.1016/j.heliyon.2021.e07771.
- Malawade, U. A., and M. G. Jadhav. 2020. Investigation of the acoustic performance of bagasse. Journal of Materials Research and Technology 9 (1):882–89. doi:10.1016/j.jmrt.2019.11.028.
- Michel, D., B. Bachelier, J.Y. Drean, and O. Harzallah. 2013. Preparation of cellulosic fibers from sugarcane for textile use. Hindawi Publishing Corporation 2013 (651787):6. doi:10.1155/2013/651787.
- Miki, Y. 1990. Acoustical properties of porous materials. Modifications of Delany-Bazley models. Journal of the Acoustical Society of Japan (E) 11 (1):19–24. doi:10.1250/ast.11.19.
- Mohammadi, F., A. Roedl, M. Ali Abdoli, M. Amidpour, and H. Vahidi. 2020. Life cycle assessment (LCA) of the energetic use of bagasse in Iranian sugar industry. Renewable Energy 145:1870–82. doi:10.1016/j.renene.2019.06.023.
- Othmani, C., M. Taktak, A. Zain, T. Hantati, N. Dauchez, T. Elnady, T. Fakhfakh, and M. Haddar. 2017. Acoustic characterization of a porous absorber based on recycled sugarcane wastes. Applied Acoustics 120:90–97. doi:10.1016/j.apacoust.2017.01.010.
- Othmani, C., M. Taktak, A. Zein, T. Hentati, T. Elnady, T. Fakhfakh, and M. Haddar. 2016. Experimental and theoretical investigation of the acoustic performance of sugarcane wastes based material. Applied Acoustics 109:90–96. doi:https://doi.org/10.1016/j.apacoust.2016.02.005.
- Pelegrinis, M. T., K. V. Horoshenkov, and A. Burnett. 2016. An application of Kozeny–Carman flow resistivity model to predict the acoustical properties of polyester fibre. Applied Acoustics 101:1–4. doi:10.1016/j.apacoust.2015.07.019.
- Rozli, S. R. B., and N. A. Azmir. 2020. The study on acoustic properties of sugarcane bagasse as sound absorber. Advanced Research in Natural Fibers 2 (1):5–9.
- Samaei, E., U. B. Seyed, E. Taban, P. Soltani, and S. Mohammad Mousavi. 2021. Natural fibro-granular composite as a novel sustainable sound-absorbing material. Applied Acoustics 181:108157. doi:10.1016/j.apacoust.2021.108157.
- Selman-Housein, G., M. A. Lopez, O. Ramos, E. R. Carmona, A. D. Arencibia, E. Menéndez, and F. Miranda. 2000. “Towards the improvement of sugarcane bagasse as raw material for the production of paper pulp and animal feed.” Plant genetic engineering: towards the third millennium: Proceedings of the International Symposium on Plant Genetic Engineering, Havana, Cuba, 6-10 December, 1999.
- Taban, E., S. Amininasab, P. Soltani, U. Berardi, D. Dugasa Abdi, and S. Ehsan Samaei. 2021. Use of date palm waste fibers as sound absorption material. Journal of Building Engineering 41:102752. doi:10.1016/j.jobe.2021.102752.
- Taban, E., A. Khavanin, A. Ohadi, A. Putra, A. Jonidi Jafari, M. Faridan, and A. Soleimanian. 2019. Study on the acoustic characteristics of natural date palm fibres: Experimental and theoretical approaches. Building and Environment 161:106274. doi:10.1016/j.buildenv.2019.106274.
- Taban, E., F. Valipour, D. D. Abdi, and S. Amininasab. 2021. Mathematical and experimental investigation of sound absorption behavior of sustainable kenaf fiber at low frequency. International Journal of Environmental Science and Technology 18 (9):2765–80. doi:10.1007/s13762-020-03024-0.
- Tang, X., X. Liu, and X. Yan. 2022. Investigation on the sound absorption properties of waste green tea residues covered by woven fabric. Journal of Natural Fibers 19 (4):1323–32. doi:10.1080/15440478.2020.1764455.
- Yang, T., H. Lizhu, M. Petrů, X. Wang, X. Xiong, Y. Deyou, R. Mishra, and J. Militký. 2021. Determination of the permeability coefficient and airflow resistivity of nonwoven materials. Textile Research Journal 92 (1–2):126–42. doi:10.1177/00405175211029212.
- Yang, T., L. Lizhu, X. Xiong, M. Petrů, M. T. Noman, R. Mishra, and J. Militký. 2020a. Sound absorption properties of natural fibers: A review. Sustainability 12 (20):8477. doi:10.3390/su12208477.
- Yang, T., L. Lizhu, X. Xiong, M. Petrů, M. T. Noman, R. Mishra, and J. Militký. 2020b. Sound absorption properties of natural fibers: A review. Sustainability 12 (20):20. doi:10.3390/su12208477.
- Yang, T., L. Lizhu, X. Xiong, M. Petrů, M. T. Tayyab Noman, R. Mishra, and J. Militký. 2020. Sound absorption properties of natural fibers: A review. Sustainability 12 (20):8477. doi:10.3390/su12208477.
- Yang, T., H. Lizhu, X. Xiong, M. Venkataraman, M. Petrů, J. Novák, and J. Militký. 2022. Acoustical evaluation and comparative study of maple leaves and coir and polyester fibers. Journal of Natural Fibers 19 (15):10813–18. doi:10.1080/15440478.2021.2002770.
- Yang, T., L. Lizhu, D. Yu, X. Xiong, J. Chvojka, M. Venkataraman, M. Petrů, B. Tomková, H. Morikawa, and J. Militký. 2022. Simple determination of key structural parameters for fibrous materials enabled by Ergun-Type and Kozeny-type equations. Polymer Testing 108:107514. doi:10.1016/j.polymertesting.2022.107514.
- Yang, T., X. Xiong, R. Mishra, J. Novák, J. Chaloupek, F. Sanetrnik, and J. Militký. 2016. Investigation on acoustic behavior and air permeability of struto nonwovens. Fibers and Polymers 17 (12):2078–84. doi:10.1007/s12221-016-6967-9.
- Yang, Y., E. Zhang, J. Zhang, S. Chen, Y. Gongchang, X. Liu, C. Peng, M. F. Lavin, Z. Du, and H. Shao. 2018. “Relationship between occupational noise exposure and the risk factors of cardiovascular disease in China: A meta-analysis.” Medicine 97 (30):e11720–e11720. doi: 10.1097/MD.0000000000011720.
- Zeydabadi, A., J. Askari, M. Vakili, S. J. Mirmohammadi, M. A. Ghovveh, and A. H. Mehrparvar. 2019. The effect of industrial noise exposure on attention, reaction time, and memory. International Archives of Occupational and Environmental Health 92 (1):111–16. doi:10.1007/s00420-018-1361-0.