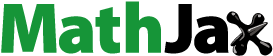
ABSTRACT
Banana fiber (BF) is a renewable resource which can be a good reinforcer to polylactic acid, enhancing the polymers stiffness and accelerating biodegradability rates. However, due to the difference in nature between banana fibers (hydrophilic) and polylactic acid (hydrophobic), a good adhesion between the fiber and the matrix cannot be achieved. To tackle the problem, the fibers were chemically treated using sodium hydroxide under three factors (temperature, concentration, and treatment time). The factors interactions were given by response surface methodology and the statistical interactions were observed by ANOVA. Alkaline effect on fiber’s morphology, composition, mechanical, and morphological properties of composites produced were observed. Young’s modulus values have increased substantially compared to untreated fiber’s composites, with a slight increase in the tensile strength values. However, the elongation at break values have slightly dropped with the fiber’s alkaline treatment. Scanning electron microscope observations had shown a successful removal of impurities (e.g. hemicellulose, wax) and between the fiber’s strands, and an improvement of surface structure. Fourier-transform infrared spectroscopy analysis showed the successful removal of impurities, and interaction between PLA and banana fibers.
摘要
香蕉纤维(BF)是一种可再生资源,可以很好地增强聚乳酸; 提高聚合物硬度并加速生物降解速率. 然而,由于香蕉纤维(亲水性)和聚乳酸(疏水性)之间的性质差异,纤维和基质之间无法实现良好的粘合. 为了解决这个问题,使用氢氧化钠在三个因素(温度、浓度和处理时间)下对纤维进行化学处理. 通过响应面方法给出因子间的相互作用,通过方差分析观察统计相互作用. 观察了碱对所制复合材料的纤维形态、组成、力学和形态财产的影响. 与未经处理的纤维复合材料相比,杨氏模量值显著增加,拉伸强度值略有增加. 然而,随着纤维的碱处理,断裂伸长率值略有下降. 扫描电子显微镜观察表明,成功地去除了纤维束之间的杂质(如半纤维素、蜡等),并改善了表面结构. 傅里叶变换红外光谱分析表明,PLA和香蕉纤维之间的相互作用成功地去除了杂质.
Introduction
The increase of demand on packaging materials has led scientists to find an alternative to petroleum-based plastic, owing to the issues related to the massive production of plastic on human’s health, and environmental health; since these products are non-biodegradable, the disposing techniques lead to global warming by the massive emission of CO2, and high levels of toxicity. Biodegradable polymers and natural fibers make up a durable biodegradable composite.
Bio-based polymer composite demand is rising in different fields to achieve more environmentally friendly products. Among the commonly used polymers is poly-lactic acid (PLA). Polymer-fiber composites have been excessively studied in the past few years. Dong et al. (Citation2014) reported that reinforcing PLA with coir fibers improved the mechanical and biodegradability properties while reducing the cost of the composite. Pine fiber is also reported to improve the mechanical and biodegradable properties of PLA (Zhao et al. Citation2020). In addition, previous studies have reported the improvements in the mechanical and biodegradability properties of PLA-banana fiber composites (Komal, Lila, and Singh Citation2020).
Although PLA and fibers make a great composite, the adhesion between fibers and PLA is weak due to the existence of hemicellulose (hydrophilic) and other impurities on the interfacial area of the fibers resulting a weak composite. The interfacial adhesion between both materials plays a crucial role in the composite mechanical strength (Shesan et al. Citation2019). Thus, surface modification is recommended to remove impurities (e.g. hemicellulose, lignin, wax), roughen the surface of fibers and improve the structure of cellulose, hence improving and increasing the interfacial area between fiber strands and PLA (Patel and Parsania Citation2017).
Chemical treatment is one of the widely used methods in natural fibers’ modification. Different methods and chemicals are used in the removal of surface impurities (e.g. hemicellulose, lignin, wax), improving the interfacial properties, and creating new bonds between the polymer and fiber. Among the methods are alkaline treatment, saline treatment, acetylation of the fiber, and benzoylation treatment (Kabir et al. Citation2012).
Alkaline treatment conditions have an impact on the fiber’s physical characteristics, since different type of fiber’s have different properties (Hashim et al. Citation2017); different treatment conditions should be optimized, to obtain maximum enhancement.
Short fiber composites are found to improve the stiffness and strength of polymers, offering a better dimensional stability and creep resistance, easiness in shaping complex and smaller models (Santulli et al. Citation2017). Thus, in the applications of packaging and furniture, short fibers are preferred in the preparation of composites. While the common method used is injection molding. Unlike synthetic fibers, natural fibers are thermally unstable, higher thermal exposure can highly affect the physical properties of lignocellulose, and shorter fiber size are more prone to getting burn in the process (Santulli et al. Citation2017). Hence, solution casting method is used to prevent the physical degradation of the fibers, and to improve the dispersion of the fiber in the polymer.
This paper focuses on optimizing the chemical treatment of pseudo banana stem fiber, under different time intervals, alkaline concentration, and temperature to ensure maximum removal of impurities while maintaining the physical properties of the fibers. Solution casting method is used to prevent fiber’s thermal degradation and to test the feasibility of using this method in preparing PLA-fiber composite over. Up to our knowledge, this work is first to test and optimize the alkaline treatment process on pseudo banana stem fiber with PLA, using solution casting method.
Materials and method
Materials
PLA (IngeoTM biopolymer 3251D) was purchased from Nature Works LLC, Minnetonka, MN, USA Banana pseudo-stem was obtained from Kelantan farms, Malaysia. Analytical grade of chloroform and sodium hydroxide (NaOH) were purchase from HmbG and Sigma-Aldrich.
Banana fiber preparation
The first sheaths of the pseudo-stem were cut using a knife, and peeled off until no rotten sheaths were left. The inner ones were separated, cut into long pieces, cleaned with ethanol and water to remove any dirt, soil and impurities, dried at 60°C in an oven for 24 h. Then, dried fibers were grinded into the approximate size of (0.2 × 2 mm). Fibers were treated using NaOH with different parameters based on design of experimented tabulated in . Following the treatment process, fibers were washed thoroughly and dried until weight was constant.
Table 1. Optimization by DOE by FCCCD under RSM.
Design of experiment
The optimum parameters for surface modification were determined by face-centered central composite design (FCCCD) of Response Surface Methodology (RSM) using Stat-Ease Design-Expert v13. The runs are shown in . The three tested factors were temperature, NaOH concentration, and pretreatment time. The samples code was designed as follows: Te25C3T1, refers to 25°C of temperature, 3% of NaOH concentration, and 1 hour of pretreatment time.
Blend preparation
Composite was prepared using solution casting method using chloroform as solvent. PLA was dried for 24 h prior to mixing in a vacuum oven at 40°C. PLA was dissolved in chloroform and mixed for 4 h. Fibers were wet with chloroform prior to mixing with PLA to enhance the dispersion of the fibers in the PLA. The mixture was left to mix for 12 h, then poured into petri dish, and left to dry in the fume-hood for 24 h. The PLA/BF was fixed at 80:20.
Material characterization
Mechanical testing was performed to determine Young’s modulus, tensile strength, and elongation at break values of the composites. Samples size were as follows: width of 1 cm, length of 4 cm, and thickness of 1 mm.
Samples were prepared according to ASTM D-882 type-V, with crosshead speed of 5 mm/min (Heena et al. Citation2019). Five specimens for each composite were prepared and tested. Untreated and treated fibers, composite fracture surface was coated with palladium prior to SEM analysis. To observe the functional groups and type of interaction between polymer and fibers, neat PLA, untreated and treated fibers, and composite were characterized using FTIR.
Results and discussion
Mechanical test and optimization using response surface methodology
Alkaline treatment of fiber has substantially affected their structure. Hence, major variations are observed in the mechanical properties’ values, namely Young’s modulus, tensile strength, and elongation at break of the composites prepared using the treated fibers. In general, a substantial increase in Young’s modulus is observed with the addition of treated fibers (as shown in ). In addition, there is a slight increase in tensile strength with composites prepared with treated fibers over untreated fiber composites as shown in . However, a drop in the elongation at break values has been observed in the treated fiber composites, over untreated fiber composite (). These mechanical properties were analyzed using ANOVA. All models are significant (p < .05) and the lack of fits are not significant (p > .05) (). The “Pred R-Squared” are all in reasonable agreement with the “Adj - R Squared.” All models are also indicating an adequate signal (ratio greater than 4). All models can be used to navigate the design space. Hence, final equations in terms of coded factors for Young’s modulus, tensile strength, and elongation at break are given in EquationEquations (1(1)
(1) ) to (Equation3
(3)
(3) ), respectively. The model graphs for Young’s modulus, tensile strength, and elongation at break are given in , respectively. Some of the interaction model graphs are not available due to model reduction to achieve above-mentioned characteristic of significant model.
Figure 2. 3D plot of Young’s modulus showing the interaction between (a) NaOH concentration and temperature and(b) NaOH concentration and time.
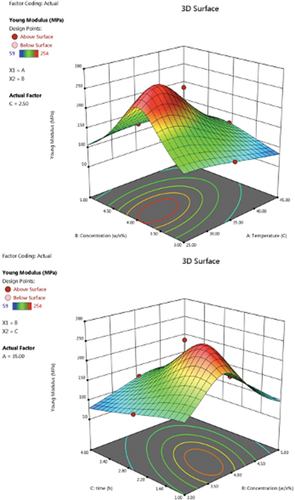
Figure 4. 3D plot of tensile strength showing the interaction between (a) NaOH concentration and temperature, and(b) NaOH concentration and time.
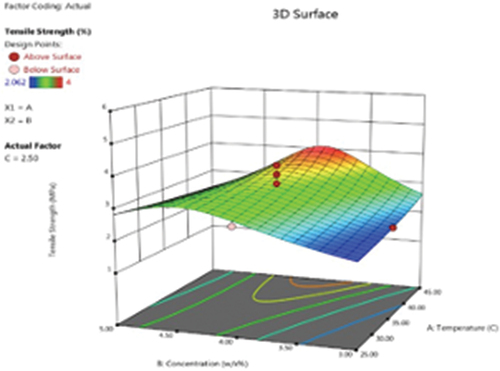
Table 2. ANOVA for quadratic model for Young’s modulus.
Table 3. ANOVA for reduced quadratic model (tensile strength).
Young’s modulus
shows the Young’s modulus of untreated fiber (UN) and PLA/BF composites prepared at 80:20 using BF pretreated at condition as described in . High Young’s modulus values were observed in the samples Te25C4T2.5, Te25C5T4, Te35C4T1, and Te35C4T2.5 replicates average (a, b, c) in comparison with untreated fiber composite by 77%, 50%, 53%, and 73% respectively. The Young’s modulus was analyzed using analysis of variance (ANOVA) as shown in .
The adequacy of the model was examined using ANOVA which was tested using Fisher’s statistical analysis and the results are shown in . The Young’s modulus model is significant (p < .05) with F value of 378.16. All the terms in the models, especially the
two-factor terms, are significant except for one-factor term B (NaOH concentration). EquationEquation (1)(1)
(1) shows the Young’s modulus equation in terms of coded factors. The 3D model of Young’s modulus is the graphical representation of EquationEquation (1)
(1)
(1) to investigate interaction between NaOH concentration and temperature; and between NaOH concentration and soaking time as shown in , respectively. The figure shows that increasing the temperature and soaking duration of the BF in NaOH solution substantially decreases the stiffness of the composite. The global optimum is obtained when NaOH is around 4%(w/v) at temperature and soaking time of 27.5°C and 1.6 h, respectively. The alkaline process removes hydrogen bonding in the network structure of cellulose. The penetration sodium hydroxide to the crystalline region in cellulose-I forms alkali cellulose, then Na+ ions removal by water leads to the conversion of alkali cellulose into cellulose-II, unlike cellulose-I which exists in parallel strands without inter-sheet hydrogen bonding, cellulose-II presents in antiparallel strains with inter-sheet hydrogen bonding (Shankaran Citation2018), which gives it a more thermodynamically stable structure (Shah, Srinivasulu, and Shit Citation2013). This improved the surface roughness, thus better interfacial bonding between PLA and cellulose in comparison with untreated fibers.
Tensile strength
There was a slight increase in the tensile strength of composites prepared with treated fibers over the untreated fiber composites as shown in .However, the values were slightly lower than values reported in previous literature, in which the common method used is injection molding. This drop might have occurred due to the impurities still existing on the fibers surface, similarly reported by Patel and Parsania (Citation2017). In addition, void (i.e. pores) within the composites structure plays a crucial role in decreasing materials withstanding stress; pores affect the stress distribution in the matrix of the composite. Along the stretching direction, the larger stress appears on both sides of the pore, which is the source of potential cracks, resulting in a sharp decrease in the mechanical properties of the composite (Li et al. Citation2020). For pore elimination, instead of letting chloroform evaporate under ambient temperature, it was suggested by Pandele et al. (Citation2020) to place the samples in the oven for chloroform to evaporate at 40°C for 72 h. In addition, fiber’s orientation plays a crucial role in the tensile strength of the composite,;since the method used in this research was melt-blending, it is nearly impossible to control the fiber’s orientation. Thus, different fiber orientations were present in the composite. Ariawan, Surojo, and Triyono (Citation2018) reported that orientation over 30° of fibers in matrix noticeably decreases composites’ tensile strength. This is because fibers are stronger in the longitudinal direction (0°) (Almeida et al. Citation2015).
The tensile strength model is significant (p < .05) with insignificant of lack of fit as shown in . Some of the model terms are removed to increase the precision of prediction. The reduced model for tensile strength is shown in EquationEquation (2)(2)
(2) and represented by the 3D model as in . Like Young’s modulus, the NaOH concentration in pre-treatment influences the tensile strength of the composite and peak around 4% w/v in 1 h soaking time (). Unlike Young’s modulus, tensile strength is maximized at the highest mixing temperature (). This increase could be owed to the improvement of adhesion between the fiber and polymer following the impurities removal by alkaline treatment.
Elongation at break
The elongation at break percentage has decreased in composites prepared with treated fibers by more than 9% compared with composites prepared with untreated fibers. Alkaline treatment removes a certain amount of lignin, wax, and oils covering the external surface of the fiber cell wall, depolymerizes cellulose, changes the fine structure of native cellulose-I to cellulose-III and exposes the short length crystallites (Wei and Liu Citation2015). These modifications lead to changes in the very basic properties, like fiber’s elongation value. Moreover, the removal of hemicellulose, lignin, and waxes increases the percentage of cellulose in the fibers, hence increasing their stiffness, which explains the drop of elongation at break of the composites. Like tensile strength, the elasticity of the composite decreases with fiber orientation over 30° degrees as reported by Ariawan, Surojo, and Triyono (Citation2018) ().
The elongation at break model is significant (p < .05) as shown in . The reduced model for elongation at break is shown in EquationEquation (3)(3)
(3) and represented by the 3D model as in . The 3D graph shows no substantial effect of different treatment conditions on the elongation at break value. However, moderate alkaline concentration and longer soaking time affect the performance of composite reinforced with fibers at the interaction factor.
Table 4. ANOVA for reduced quadratic model (elongation at break).
Fourier transform infrared spectroscopy (FTIR)
To study the functional groups in untreated and treated fibers in , and to observe the type of interfacial interaction in the neat PLA, Te35C4T2.5 (center point) composites were observed as shown in . The main constituents of fibers are cellulose, hemicellulose, and lignin as shown by both untreated (UN-BF) and treated banana fiber (T-BF), the typical vibration band of the component. The spectrum shows the absence of peak 1250 cm−1 after the alkaline treatment; this is an indication on the successful removal of hemicellulose, as the band indicates this constituents, similarly as reported by Parre et al. (Citation2020). The spectra show the presence of large OH stretching vibration between 3000 and 3500 cm−1 indicating the presence of hydroxyl group in the fiber. The absorption of this peak has dropped in the treated fibers, showing a disturbance in the interaction linking between cellulose and impurities, which was similarly reported by Zhou, Fan, and Chen (Citation2016). Peaks in the range between 2887 and 2894 cm−1 indicate C-H stretching from the CH2. The bands between 1400 and 1700 cm−1 indicates the functional groups of hemicellulose and lignin; there was a decrease of the transmittance around these peaks in treated fibers, indicating the removal of impurities surrounding cellulose (hemicellulose, lignin) (Zhou, Fan, and Chen Citation2016) In the neat PLA sample, the peak at 1720–1740 indicates the stretching of carbonyl group. The same peak, with slightly reduced stretching, is indicated in the (Te35C4T2,5) composite, indicating the interaction between PLA and treated banana fibers (Lee, Khalina, and Lee Citation2021).The major peaks of treated BF were not seen in the composite; this might be due to the coverage of other strong peaks of PLA, since the mass of fibers used was 4 times lesser than the amount of PLA.
Figure 7. (a) Fourier transform infrared spectroscopy (FTIR) spectrum of (a)t-BF, and UN-BF (b) Fourier transform infrared spectroscopy (FTIR) spectrum of Te35C4T2.5 composite, neat PLA.
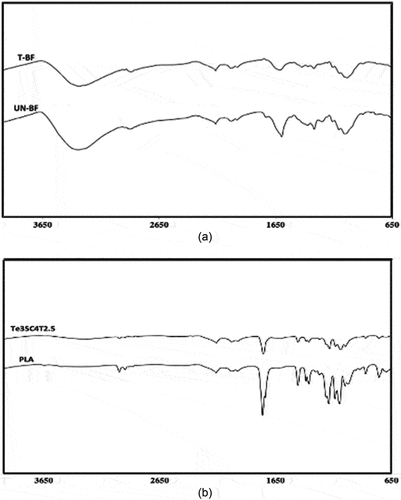
However, the presence of the peaks between 1200 and 1300 cm−1 indicates that the fibers were introduced into the polymer matrix (Ali et al. Citation2015).
SEM observation
Surface morphology of untreated BF, treated BF, and Te35C4T2.5 composite were analyzed by scanning electron microscope (SEM), and the results presented in . shows the morphological structure of untreated BF. As can be observed, the surface of fibers is excessively coated with impurities (i.e. wax, hemicellulose, lignin). While shows the morphological structure of treated BF at 35°C, 4% of NaOH concentration and 2.5 h of treatment duration. The figure shows that hemicellulose was removed along with partial removal of lignin which presents between the fiber single strands. It also can be observed in of treated fibers that the fiber strands are more visible compared to of untreated fibers. The surface looks more visible, clean, and tough in comparison with the untreated fibers and a slight separation between fibers can be seen. Within the composite, there are two types of interactions; one is the cohesion among the fiber’s which are connected through the presence of lignin, second is the adhesion between PLA and banana fiber, with the chemical treatment, lignin on the surface of the fiber, and in between the strands is partially removed, the fiber’s cohesion is reduced, and more surface area for PLA and fiber interaction. To elaborate, show the surface of tensile failed composite. Fiber cut instead of pulling out in is evidence of strong adhesion between PLA and fibers over the fibers cohesion as explained previously. In addition, shows a slight fiber pull out in the center, proving a stronger adhesion between fibers and PLA in comparison with the fibers’ cohesion; pull outs have occurred due to the slight removal of lignin during the treatment process.
Conclusion
The effect of alkaline treatment (i.e. NaOH concentration, temperature and treatment time) on the banana pseudo-stem fiber was investigated using RSM based on the response toward the mechanical properties of the composite. Although the elongation at break values have slightly dropped, the stiffness of the composite somehow increased as shown by the Young’s modulus values, and slight increase in the tensile strength values was observed. Different interactions of treating parameters have different effects on mechanical strength values as represented by 3D plot of interaction. The FTIR proved that there was an interaction between PLA and treated banana fibers, while SEM images shown the successful removal of impurities from fiber’s surface. Fiber cut shows evidence of strong adhesion between PLA and fibers. A new approach in the preparation of composites with shorter fiber size was introduced to maintain the physical properties of the fibers, and to avoid the effect of high temperature was tested. Although the mechanical values were lower than the values reported previously, it is believed that certain enhancements to the methodology and fiber’s size could potentially result in better outcomes comparable to the results reported previously. Certain improvements like reduction of amount of organic solvent used, studying different fiber sizes, and oven-drying the samples. Moreover, we would highly suggest performing alkaline treatment multiple times under lower alkaline concentration and shorter immersion time respectively; this is believed to gradually remove the lignin presenting between the fibers, allowing for more interactional area between the PLA and the fiber, while maintaining the main properties of the fiber (i.e. maintaining elasticity).
Highlights of the work
Banana fiber (BF) was chemically treated using sodium hydroxide with variation of three factors (temperature, concentration, and treatment time) prior to preparation of PLA/BF composite using solution casting method.
The interactions of the three factors were analyzed by response surface methodology and the statistical interactions were observed by ANOVA.
The mechanical strength of the composite was improved after the alkaline treatment of the fiber. Young’s modulus values showed the best improvement, followed by tensile strength, and lastly elongation at break values.
Alkaline treatment has improved the interaction between the fiber’s and polymer in the composite, which is shown in the FTIR results and SEM images.
Disclosure statement
No potential conflict of interest was reported by the authors.
References
- Ali, M. E., C. K. Yong, Y. C. Ching, C. H. Chuah, and N. S. Liou. 2015. Com effect of single and double stage chemically treated kenaf fibers on mechanical properties of polyvinyl alcohol film. BioResources 10 (1):822–13.
- Almeida, J. H. S., C. C. Angrizani, E. C. Botelho, and S. C. Amico. 2015. Effect of fiber orientation on the shear behavior of glass fiber/epoxy composites. Materials & Design 65 (January):789–95. doi:10.1016/J.MATDES.2014.10.003.
- Ariawan, D., E. Surojo, and J. Triyono. 2018. Effect of fiber orientation on tensile and impact properties of zalacca midrib fiber-HDPE composites by compression molding articles you may be interested in. doi:10.1063/1.5024119.
- Dong, Y., A. Ghataura, H. Takagi, H. J. Haroosh, A. N. Nakagaito, and K. Tak Lau. 2014. Polylactic acid (PLA) biocomposites reinforced with coir fibres: Evaluation of mechanical performance and multifunctional properties. Composites Part A, Applied Science and Manufacturing 63 (August):76–84. doi:10.1016/J.COMPOSITESA.2014.04.003.
- Hashim, M. Y., A. Mohd Amin, O. Mohd, F. Marwah, H. Othman, M. Radzi, M. Yunus, and N. Chuan Huat. 2017. The effect of alkali treatment under various conditions on physical properties of kenaf fiber. IOP Publishing IOP Conference of Series: Journal of Physics: Conference of Series 914:12030. doi:10.1088/1742-6596/914/1/012030.
- Heena, A., S. A. Nur, M. Soleiman Barre, F. B. Ali, and H. Anuar. 2019. Degradation properties of biodegradable polymers. Journal of Wastes and Biomass Management 1 (2):05–08. doi:10.26480/jwbm.02.2019.05.08.
- Kabir, M. M., H. Wang, K. T. Lau, and F. Cardona. 2012. Chemical treatments on plant-based natural fibre reinforced polymer composites: An overview. Composites Part B: Engineering 43 (7):2883–92. doi:10.1016/J.COMPOSITESB.2012.04.053.
- Komal, U. K., M. K. Lila, and I. Singh. 2020. PLA/banana fiber based sustainable biocomposites: A manufacturing perspective. Composites Part B: Engineering 180 (January):107535. doi:10.1016/J.COMPOSITESB.2019.107535.
- Lee, C. H., A. Khalina, and S. H. Lee. 2021. Importance of interfacial adhesion condition on characterization of plant-fiber-reinforced polymer composites: A review. Polymers 13 (3):1–22. doi:10.3390/polym13030438.
- Li, D., S. Song, D. Zuo, and W. Wu. 2020. Effect of pore defects on mechanical properties of graphene reinforced aluminum nanocomposites. Metals 10 (4):1–9. doi:10.3390/met10040468.
- Pandele, A. M., A. Constantinescu, I. C. Radu, F. Miculescu, S. Ioan Voicu, and L. T. Ciocan. 2020. Synthesis and characterization of PLA-micro-structured hydroxyapatite composite films. Materials 13 (2):1–13. doi:10.3390/ma13020274.
- Parre, A., B. Karthikeyan, A. Balaji, and R. Udhayasankar. 2020. Investigation of chemical, thermal and morphological properties of untreated and NaOH treated banana fiber. Materials Today: Proceedings 22:347–52. doi:10.1016/J.MATPR.2019.06.655.
- Patel, J. P., and P. H. Parsania. 2017. Characterization, testing, and reinforcing materials of biodegradable composites. In Biodegradable and biocompatible polymer composites: Processing, properties and applications. Elsevier Ltd. doi:10.1016/B978-0-08-100970-3.00003-1.
- Santulli, C., F. Sarasini, D. Puglia, and J. M. Kenny. 2017. 8 injection moulding of plant fibre composites. Advanced Composite Materials: Properties and Applications August:420–39. doi:10.1515/9783110574432-008.
- Shah, H., B. Srinivasulu, and S. C. Shit. 2013. Influence of Banana Fibre Chemical Modification on the Mechanical and Morphological Properties of Woven Banana Fabric/Unsaturated Polyester Resin Composites. Polymers from Renewable Resources 4 (2):61–84. doi:10.1177/204124791300400202.
- Shankaran, D. R. 2018. Cellulose nanocrystals for health care applications. Applications of Nanomaterials 415–59. doi:10.1016/B978-0-08-101971-9.00015-6.
- Shesan, J., A. C. Owonubi, A. G. Chioma, R. Neerish, and S. E. Rotimi. 2019. Fiber-matrix relationship for composites preparation. In Renewable and sustainable composites. IntechOpen. doi:10.5772/intechopen.84753.
- Wei, Y., and Z. Liu. 2015. Recent progress in mesostructured materials. Recent Progress in Mesostructured Materials 165.
- Zhao, X., K. Li, Y. Wang, H. Tekinalp, G. Larsen, D. Rasmussen, R. S. Ginder, L. Wang, D. J. Gardner, M. Tajvidi, et al. 2020. High-strength polylactic acid (PLA) biocomposites reinforced by epoxy-modified pine fibers. ACS Sustainable Chemistry & Engineering 8 (35):13236–47. doi:10.1021/ACSSUSCHEMENG.0C03463.
- Zhou, Y., M. Fan, and L. Chen. 2016. Interface and bonding mechanisms of plant fibre composites: An overview. Composites Part B: Engineering 101 (September):31–45. doi:10.1016/J.COMPOSITESB.2016.06.055.