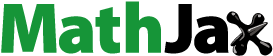
ABSTRACT
The present work deals with the valorization of agro-industrial by-products to realize bonded abrasives. Four by-products were studied because of their wide availability and mechanical properties: palm nuts shells (Elaeis guineensis), Coco Nucifera shells, fruit kernels of Canarium schweinfurthii and fruit kernels of Raffia Vinifera. The Oliver and Pharr hardness and Young’s modulus of the raffia cores are obtained by instrumented macro indentation, giving the values 101 MPa and 1.82 GPa, respectively. The development of the abrasive wheels was based on the experimental method of full factorial design at 2 levels. Porosity, hardness, resilience, material removal rate and wear were determined. Leeb 280 HL hardness shoe sole material was used for tribological testing. The optimal formulations have 20% binder content and 1 mm grain size of the four agro-industrial by-products used with a higher material removal rate and a longer life than commercial grinding wheels. These results presage their use in the shoe industry and abrasive disc huskers.
摘要
目前的工作涉及农用工业副产品的价格化,以实现粘结磨料. 由于其广泛的可用性和机械财产,我们对四种副产品进行了研究:棕榈果壳(Elaeis guineensis)、椰子壳、橄榄果仁和拉菲亚葡萄果仁. 通过仪器化宏观压痕获得了拉菲亚岩心的奥利弗硬度和法尔硬度以及杨氏模量,分别给出了101MPa和1.82GPa的值. 砂轮的开发基于两个层次的全因子设计实验方法. 测定了孔隙率、硬度、弹性、材料去除率和磨损. Leeb 280HL硬度鞋底材料用于摩擦学测试. 最佳配方的粘合剂含量为20%,使用的四种农用工业副产品的粒度为1mm,与商用砂轮相比,材料去除率更高,使用寿命更长. 这些结果预示着它们在制鞋行业和研磨盘脱壳机中的应用.
Introduction
Bonded abrasives play a significant role in the industry (Goossens, Cherif, and Cahuc Citation2013). Used for polishing, grinding, sharpening, cutting or reshaping operations, they consist of grains agglomerated in a vitrified or organic binder (Jamrozik, Strzemiecka, and Voelkel Citation2018). Among the organic binders, epoxy resin can be used because, it is compatible with plant products (Jiang et al. Citation2015; Nagatani et al. Citation2019; Sabaa and Fahad Citation2018). Epoxy resin has a density of 1.24 g/cm3 to 1.30 g/cm3, a viscosity of up to 3300 MN/m2, a coefficient of thermal expansion of 55 × 106/0C and a curing shrinkage of 1% to 2% (Suresha et al. Citation2006). One of the characteristics of abrasives is their hardness; it plays a significant role in the grinding process (Nadolny, Sutowski, and Herman Citation2015). The topography of grinding wheels facilitates the analysis and characterization of grinding processes, given the orientation of abrasive grains in the wheels (Arunachalam and Ramamoorthy Citation2007; Chakrabarti and Paul Citation2008). Abrasive grains can be of natural origin such as corundum, garnet (Calligaro et al. Citation2006; Jani et al. Citation2016), emery (Syreyshchikova and Yu Pimenov Citation2017), flint (Nadolny, Sutowski, and Herman Citation2015; Sestier Citation2010) or synthetic origin such as aluminum oxide (Herman and Markul Citation2004); (Jamrozik et al. Citation2020; a; Jamrozik et al. Citation2020 b), silicon carbide (Odior and Oyawale Citation2010; Odior1 and Oyawale Citation2013), cubic boron nitride (Huang et al. Citation2021; Toenshoff, Grabner, and Zinngrebe Citation2007) or diamond for specific applications due to its high hardness although its production cost is higher (Watanabe et al. Citation2010). To date, the raw material allowing to obtain abrasives faces a certain number of limits which are mainly translated by progressive exhaustion of the deposits of alluvial quarries in the course of exploitation and especially with constraints related to environmental protection tend to limit certain exploitations. Therefore, artificial abrasives remain an effective solution although their implementation requires enormous technical means (Jamrozik, Strzemiecka, and Voelkel Citation2018), which are difficult to produce locally. It becomes necessary to find alternative materials to conventional abrasives. Plant products like of hard cores or shells can be an interesting alternative in a context where the valorization of waste or by-products from agriculture remains a major research challenge (Prevot Citation2010).
The availability of these by-products can be assessed from the cultivation of their plants. Oil production from palm nuts (Elaeis guineensis) is estimated at 230,000 tons annually in Cameroon (Iyabano Citation2014). According to the Food and Agriculture Organization, Cocos nucifera nuts reached 62 million tons in 2013, with a cultivable area of close to 12 million hectares (Kodjo et al. Citation2015). The fruit production of Canarium schweinfurthii (Engl) is estimated at 1000 tons per harvest season in West Cameroon (Njoukam and Peltier Citation2002).
Previous studies evaluated the physical and mechanical characteristics of these plant by-products (Kodjo et al. Citation2015; Koungang et al. Citation2020; Morino et al. Citation2020; Ndapeu et al. Citation2013; Njeugna et al. Citation2016; Sikame Tagne et al. Citation2014; Stanislas et al. Citation2020), while some others used it at reinforcement charge composite materials (Dieunedort et al. Citation2020, Citation2020; Lagel et al. Citation2015; Oliveira Filho et al. Citation2020; Pathmanaban, Musharath Aalam, and Sr Citation2019). While many studies have focused on the stem and fibers of raffia vinifera (Mbou et al. Citation2017; Sikame Tagne et al. Citation2014, Citation2020), very few, if any, studies have focused on the fruit and specifically on its pit. Moreover, work on bonded abrasives based on hard shells and cores has not been the subject of in-depth studies to date. This work aims to elaborate and characterize agglomerated abrasives based on palm nut shells, coconut shells, Canarium schweinfurthii cores and Raffia cores, in order to study the influence of the parameters related to the nature and the number of constituents on the abrasive properties. The mechanical properties of raffia fruit cores were determined to complete the information on the characterization of the by-products used. Then this study was followed by the development of abrasive materials on the factorial design model, and finally, tests were conducted to evaluate the influence of parameters on the abrasive properties.
Materials and methods
Mechanical characterization of raffia fruit cores
Data on the hardness and Young’s modulus of palm nut shells, coconut shells and canarium cores (Lucas et al. Citation2009; Morino et al. Citation2020) can be found in the literature. However, raffia fruit kernels have not yet been subjected to the same tests. Thus, the raffia fruit cores were harvested in the western region of Cameroon and subjected to physical, thermal and mechanical characterization. The mechanical characterization of the raffia fruit allowed the determination of the hardness and Young’s modulus according to the Oliver and Pharr method based on the contact equations. This method has the advantage of characterizing the surface materials and the mechanical properties of the material interfaces without destroying the bodies (Kermouche, Saint-Etienne, and Bergheau Citation2014). The experimental macro indentation bench was developed at the laboratory and made it possible to carry out similar work on shells (Morino et al. Citation2020). The cut specimens () are parallelepipedic in shape with dimensions of 15 mm x 10 mm x 10 mm.
Two measurement points were selected on each of the faces of 11 specimens at room temperature. The indentation curve (load/unload) was obtained by increasing the 5 kg masses 10 times with a dwell time of 15 s, until a total load of 500 N was obtained thus complying with ISO 14,577 (Kaupp and Reza Naimi-Jamal Citation2011). The hardness and modulus of elasticity of the indented raffia cores are based on the contact equations of Hertz and the method of Oliver and Pharr (Oliver and Pharr Citation1992). The fit of the discharge curve is obtained by EquationEquation 1(1)
(1) .
where P is the instantaneous load, h is the displacement of the indenter (indentation depth), hf is the residual indentation depth, Pm and hm are, respectively, the maximum load and displacement, m is a constant that can be adjusted according to experimental data, being m = 1 for a spherical indenter (Oliver and Pharr Citation1992).
The initial slope of the discharge curve, S, known as contact stiffness, is calculated at the point of maximum applied load using EquationEquation 2(2)
(2) .
The reduced modulus of elasticity ER of the material is determined from the stiffness S calculated at the maximum depth on the discharge curve and the contact area Ac (Kossman, Chicot, and Iost Citation2017). For spherical indenters, the relationship that links ER to AC (Fischer-Cripps Citation2000) is obtained from EquationEquation 3(3)
(3) .
ER is also related by Young’s modulus and Poisson’s ratio of the indenter (Ei, νi) and the material (E, ν) by the relation (4).
The Young’s modulus E presented in Equationequation (5)(5)
(5) is obtained from EquationEquation 4
(4)
(4)
Oliver and Pharr introduce the contact depth hc over which the indenter is in contact with the material surface as shown in EquationEquation 6(6)
(6) .
ε is a recommended value that depends on the geometry of the indenter, which takes the value of 0.75 for a sphere (Pharr and Oliver Citation2004). Knowing this geometry, the contact surface area Ac can be estimated by EquationEquation 7(7)
(7) .
where R is the radius of the spherical indenter and a is the radius of the projected contact. The hardness (H) is determined by the relationship (8) from the maximum applied load (Pm) and the contact area (Ac).
Production of abrasive wheels
Experimental design model
Four plant by-products were used in the formulation of the abrasive wheels: palm nut shells, coconut shells, canarium schweinfurthii fruit kernels and raffia fruit kernels. They were cleaned in a distilled water bath. Drying was carried out in a Memmert UF110 oven at a temperature of 105°C for 24 hours (Enih et al. Citation2017). They were then introduced into a grinder for transformation into fragments. Particles with a particle size between 1 mm and 0.8 mm for large sizes (P20) and between 0.2 mm and 0.160 mm (P80) were obtained by sieving according to the FEPA standard (Elaissi et al. Citation2020). The binder used is an epoxy resin available in the local market. Our scientific approach is based on two level full factorial experimental designs. The geometry of the abrasive grains is more or less spherical after grinding and sieving. The determining factors are the percentage of resin and the size of the abrasive grains. The mathematical model presented in EquationEquation 12(12)
(12) is a first-degree model developed by (Goupy Citation1990).
is the response variable;
is the level assigned to the percentage of resin
is the level assigned to the grain size
is the value of the response at the center of the study domain;
is the effect of the resin percentage factor;
is the effect of the grain size factor;
is the interaction between the percentage of resin and the grain size.
is the gap.
Responses Y are classified based on relation to each experimental trial ().
Table 1. Design of experiments.
The different combinations are formulated from epoxy resin percentages set at 20% and 40% representing, respectively, the low and high levels of factor 1 and the particle size of the different plant by-products ranging from 0.2 mm to 1 mm, representing factor 2. provides information on the different formulations of the by-product-based abrasives obtained through the experiment.
Table 2. Formulations of epoxy-based abrasives and by-products.
Shaping of abrasives
The abrasives are shaped by the cold compression molding process. The first step consists in mixing the grains, and the resin previously weighed thanks to a mini mixer of 1000 W power for 2 minutes, thus making the constituents more homogeneous. Then, the mixture is filled into a hardened steel mold of internal dimensions 125 × 15×20 machined for the molding operation. The second step consists in compacting the mixture under a pressure of 17 MPa, for 30 minutes (polymerization time) using a hydraulic press with a cylinder of type E. RASSANT. The last step also called the curing phase, allows the abrasive wheels obtained to be maintained at 40°C for 2 hours in a Memmert UF110 type universal oven.
Characterization of bonded abrasives
Physicochemical and thermal characterization
Porosity
The porosity (P) of the grinding wheels was performed using EquationEquation 12(12)
(12) from ISO 5017 (Pinot Citation2015). Ten specimens in cubic shapes were used.
: bulk density determined by the gravimetric method based on Archimedes’ principle according to ASTM-D3800-99 (Sikame Tagne et al. Citation2020).
: real density of the abrasive obtained through the geometric method of the NF P 94,410–2 standard (Mansouri et al. Citation2007).
Thermogravimetric analysis (TGA) of processed abrasives
The test was carried out using a thermo balance STQ PT-1000 according to ISO 11,358:1997. The test allows the evaluation of the thermal stability of the abrasives. The 3 to 5 mg grinding wheel powders are introduced into a platinum crucible and heated in the furnace at a constant heating rate of 10°C/min over a temperature range of 30°C to 600°C (Shukla, Kumar, and Srivastava Citation2006) under a nitrogen flow at a rate of 50 ml/min.
Differential Scanning Calorimetry (DSC) of manufactured abrasives
Differential scanning calorimetry was used to determine the maximum curing temperature of the processed abrasives. The measurements were carried out using the STQPT-1000 thermo balance. 5 mg of powder to be analyzed was taken from the abrasives of different by-products with 40% binder content and 1 mm grain size in the temperature range of 60 to 200°C with a heating/cooling rate of 10°C/min under nitrogen atmosphere (Achchaq et al. Citation2009).
Mechanical and tribological characterization
Leeb Hardness
The hardness of the samples was evaluated using a TH110 g drinking water hardness tester following the ASTM E140 standard. The principle is based on the dynamic rebound method (Asiri, Corkum, and El Naggar Citation2016). The samples used for the measurement are cubic with a 20 mm edge. Ten samples of each formulation are prepared and six measurements are performed on each of the six faces to obtain the average Leeb hardness values.
Resilience testing
Testing was performed on each abrasive formulation to determine impact fracture toughness using fracture energy. The device used is a Charpy pendulum hammer conforming to the ASTM D256 standard (William et al. Citation2022). The specimens are sized 4 × 3 × 27 mm3 by the DIN 50,119 standard (Guillou, Guttmann, and Dumoulin Citation1981). The value of resilience is obtained by EquationEquation 12(12)
(12) .
where l, g, m, α, β, and S are the length of the pendulum (310 mm), the intensity of gravity, the mass of the pendulum, the angle of rising after breakage, the angle of the free rise of the pendulum, and the cross-sectional area of the test piece, respectively.
Efficiency and wheel wear
The efficiency of the grinding wheels was determined by evaluating the material removal rate (MRR) of a predefined material. The choice of the material depends on the field of application of the developed grinding wheel. The material chosen was a polymer for shoe soles with a hardness of Leeb 280 HL. The test device is a disc tribometer (Dieunedort et al. Citation2020, where the different grinding wheels are mounted on the motor plate (7), and the polymer material is mounted on the jaw holder (6), as shown in .
Measurements of the mass loss of the grinding wheel and the polymer are carried out using a precision balance (10−3 g). Each test lasts 10 seconds and is repeated three times in order to obtain the average material removal rates (MRR) given by equation (12) and the average wheel wear rates (WR). The contact pressure between the grinding wheel and the polymer of 400 mm2 section is 0.125 MPa. The grinding wheels are driven at a speed of 1380 rpm.
mi is the initial mass before the test and mf is the final mass after the test expressed in grams. The coefficient of friction (µ) between the manufactured wheels and the selected test material can be determined during the wear test. It was obtained by the relation (13)
is the friction force obtained by the calibration relationship () of the device. The calibration of the tribometer consists in establishing the correlation between the horizontal displacement of the pin plate (4) measured with a comparator and the imposed load determined with a precision digital dynamometer (10−3 Kg). FN represents the normal load applied during the test.
Results and discussion
Characterization of Raphia fruit cores
Physical and mechanical characterization
The values of hardness and Young’s modulus of Raphia fruit kernel obtained from Equationequations (5)(5)
(5) and EquationEquation 8
(8)
(8) are slightly lower than those of other by-products. The values are 100.67 MPa and 1.82 GPa respectively. shows the variation of hardness H and Young’s Modulus E as a function of contact depth.
An increasing evolution of hardness and Young’s modulus with contact depth is observed. This behavior, although it is a plant product, is similar to the variation of hardness as a function of contact depth for titanium (TiW) and aluminum (Al) tungsten thin films deposited on a silicon (Si) substrate (Randall Citation2004). compares the hardness and Young’s modulus values of the raffia core with other plant by-products.
Table 3. Comparison of physical and mechanical characteristics of by-products.
The hardness, Young’s modulus and density of raffia fruit kernel are closer to the values of palm nut shells than cocos nut shells and fruit kernel of canarium schweinfurthii. Although the hardnesses of the by-products remain low compared to the hardnesses of some synthetic aluminum oxide abrasive grains that can reach a Knoop hardness of 20.3 GPa (Nadolny, Sutowski, and Herman Citation2015) they can be used in the realization of plant by-product abrasives (Njeugna et al. Citation2016) to abrade less hard materials. The production of abrasives, despite all the technological improvements, can be a severe source of pollution, requiring technical solutions to minimize environmental impacts (Mihăiescu et al. Citation2011), and bonded abrasives based on plant by-products are a particular solution to this concern.
Thermogravimetric analysis
shows the thermal stability of the raffia fruit kernel. The results reveal that the initial weight loss, attributed to moisture content, is equal to 9.22%. The first phase of degradation is linked to the thermal depolymerization of the hemicellulose and the cleavage of the glycosidic bonds of the cellulose, with a loss of mass ranging from 9.22% to 28.34%.
The TG and DTG curves show at the last phase of degradation related to the slow decomposition of lignin a higher mass loss of 47.56% between 352°C and 472°C. Owing to the complex structure of lignin (aromatic compound rings with various branches), its degradation occurs slowly within the whole temperature (Liu et al. Citation2004). These mass loss variations are close to plant-based fibrous materials reported by (Achchaq et al. Citation2009; Neto et al. Citation2015). It is also seen from the DSC curve that the Raphia fruit kernel has a significant heat release from 307°C onwards, accompanied by an exothermic peak at about 484°C, corresponding to thermal degradation.
Characterization of the abrasives produced
Physical and thermal characterizations
Sixteen formulations of the abrasive wheels were made from the four mentioned by-products. shows some of the wheels developed from the experimental approach.
Figure 5. Bonded abrasives made with different by-products: (a) Coconut grinding wheel EN 40–1; (b) Canarium core grinding wheel EC 20–1; (c) Palm nut grinding wheel EP 20–1; (d) Raffia core grinding wheel ER 20–1.
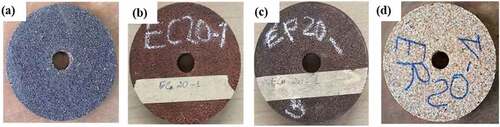
Thermogravimetric analysis of grinding wheels
The thermogravimetric analysis shows, the behavior of Coco EN 40–1, Palm EP 40–1, Canarium EC 40–1 and Raphia ER 40–1 abrasives. The general behavior is similar, with two significant degradation phases and a loss of moisture at the beginning of the test. shows the summary data of the thermal behavior of the abrasives produced. This table, shows that the abrasives produced can easily withstand temperature gradients of the order of 200°C while retaining most of their properties. Although these results are globally appreciable, the raffia core abrasives show better thermal stability than the others with exothermic peaks up to 502°C. This high thermal stability is attributed to the presence of 40% resin content in the abrasive (Nagatani et al. Citation2019) but especially to the good thermal stability of the raffia core (Iwar et al. Citation2021).
Table 4. Summary of the thermal behavior of bonded abrasives.
The TG analysis of cresol-based benzoxazine abrasive binders shows a loss of half their mass between 240°C and 380°C (Jamrozik et al. Citation2020). These data from the literature are also close to the TG results of EN 40–1, EP 40–1 and ER 40–1 abrasives. Heat resistance is a key parameter for abrasive materials, because friction stress can induce significant heating of the surfaces.
Porosity of the abrasives made
Citation2019) show that a high-porosity wheel has lower grinding temperatures and a higher material removal rate. It can be seen from that the abrasives of different combination by-products 20–1 have high porosities. This situation is due to the small quantity of resin of 20% and especially the abrasive grains of considerable size (1 mm). The porosity values are between 11.03 and 23.09% for all the wheels produced. These values are close to the porosities of grinding wheels based on abrasive grains made of aluminum oxide and vitrified binder (Mansouri et al. Citation2007). The technique used in processing modern abrasives to increase the porosity especially, of vitrified bonded abrasives is the use of pore inducers (Davis Citation2005).
It can be seen from that the porosity decreases as the binder increases. This is linked to the capacity of the binder to fill the voids by encrusting the grain particle. In addition, the larger abrasive grain size (1 mm) increases the porosity of the material due to the large number of voids created during molding.
Mechanical characteristics
Leeb hardness (HL) of grinding wheels
The Leeb hardness was carried out on all formulations. It can be seen that the hardness values increase with the binder content and the size of the particles. The HL hardness values are between 220 HL and 342 HL.
The analysis of the results shows that the abrasives of different by-products produced have a high hardness when the binder content is 40% and with a particle size of 1 mm. This may be because when the abrasive grain sizes are close to their natural dimensions, they offer the best mechanical properties and also the mechanical properties of the resin, whose Young’s modulus at room temperature can reach 3.74 GPa (Passilly et al. Citation2017). This behavior, on the one hand, is similar to abrasives based on periwinkle shells and polyester binder, indicating that increasing the concentration of polyester from 4 to 12% increases the hardness (Obot, Yawas, and Aku Citation2017). compares the hardness of bonded abrasives made from 40–1 formulations with selected abrasives.
Table 5. Comparative values of material hardnesses.
The studies on the hardness of the by-products are in line with the results of the bonded abrasives produced. With regard to , coconut-based abrasives have hardnesses comparable to abrasives of natural origin and certain friction materials.
Resilience of grinding wheels
Impact tests were carried out on all formulations. provides information on the impact resistance values of manufactured bonded abrasives. The impact values of coconut-based abrasives range from 2.52 to 2.65 J/cm2, canarium core-based abrasives from 2.2 to 2.36 J/cm2, palm nut-based abrasives from 2.56 to 2.97 J/cm2 and raffia core-based abrasives from 2.2 to 2.48 J/cm2. Regardless of the formulation, these values remain high compared to the breaking energy of epoxy resin measuring 100 to 300 j/m2 (Barrère and Dal Maso Citation1997). Those based on palm nuts show high impact resistance. It was found that the impact strength was lower for grinding wheels of identical formulations, when the hardness was increased.
Table 6. Impact strength of some composite materials.
From , we note that the abrasive grains of vegetable origin significantly increase the impact resistance of grinding wheels. The results show that the smaller base wheels are more resistant to impact. Some authors have concluded that a decrease in the resilience of abrasives can allow greater force to be applied and more material to be removed (Syreyshchikova and Yu Pimenov Citation2017).
Tribological characterization and effectiveness of abrasives
Abrasive efficiency
The efficiency of the grinding wheel is characterized by its material removal rate (MRR). A commercial grinding wheel marked COM was subjected to the same test and under the same conditions in order to compare the different results. shows the material removal rate behavior and its evolution as a function of time.
Figure 7. Material removal rate behavior: (a) Removal rate of processed grinding wheels; (b) Evolution of material removal as a function of time.
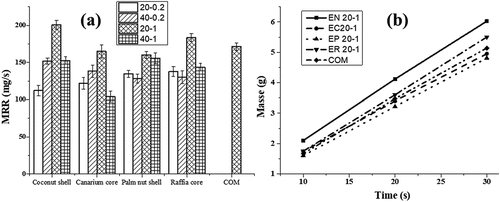
Looking at , it can be seen that the material removal is higher by the 20–1 wheels for all types of abrasive grains. The MRR of the commercial wheel (COM) is 171.3 mg/s and is close to the values of the 20–1 wheels. The EN 20–1 coconut wheel has the highest efficiency, with a removal rate of 200.8 mg/s.
From the full 2-level factorial design, the influence of resin percentage and particle size on the efficiency of the developed grinding wheels was analyzed. The trend of the effect of the factors is general for the by-product-based grinding wheels, as shown in .
Table 7. Influence of factors on material removal rate of abrasives.
shows the influence of shaping factors on coconut-based grinding wheels. The average MRR on coconut-based grinding wheels is 154.33 mg/s. The effect of factor 1 is −2.18 mg/s for a 10% variation in binder percentage, and grain size is 22.27 mg/s for a 0.4 mm variation in abrasive grains.
Figure 8. Interaction of factors on material removal: (a) Rate resin percentage (factor 1); (b) Size of abrasive grains (factor 2).
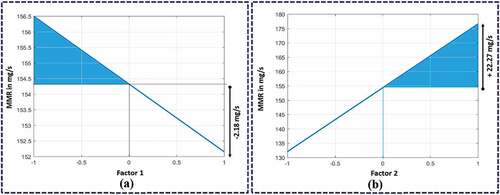
It can be seen that the increase of 10% of the binder negatively influences the efficiency of the grinding wheels based on agro-industrial by-products. It would therefore be advisable to stabilize the binder content at the limit of less than 20%. However, the data in show that it is possible to reduce it further to 10% for canarium core and raffia wheels as the effect of factor 1 are −11.15 and −11.90 respectively. On the other hand, increasing the abrasive grain size has a favorable influence on material removal. It seems evident that the optimal formulation of these grinding wheels is the 20–1 composition with 20% binder and 1 mm abrasive grain size. These compositions are strongly related to wheels with the highest porosity. The porosity of the bonded abrasives is, therefore, a parameter of the efficiency of the wheels (Davis Citation2005; Mansouri et al. Citation2007; Zhao et al. Citation2019).
Wheel wear and service life
In this study, the most effective agglomerated grinding wheel formulations are those with a 20% binder percentage and a particle size of 1 mm. Wheels can also be characterized by the wear rate WR, as shown in . The wear was determined during the material removal tests by measuring the mass variation at each test phase. shows the evolution of the friction coefficient obtained from the grinding wheels as a function of time.
Table 8. Wear values and service life of 20–1 wheels.
The WR of the COM wheel is higher and is around 2.8 mg/s. This wheel also has the highest µ values of up to 0.51. The EN 20–1 and EP 20–1 wheels have almost a WR of around 0.7 mg/s, which is very low compared to benzoxazine and cresol-based abrasive materials (Jamrozik et al. Citation2020). The ER 20–1 wheel has a small WR of 0.1 mg/s and the lowest µ value, a with an average value of 0.24. The EC 20–1 grinding wheel has the largest WR of the developed materials with a value of 0.8 mg/s and an average friction coefficient of 0.35. In general, the friction increases during the first four seconds of the test. The wear values of the grinding wheels differ according to the type of grain of the by-products. This can be attributed to the porosity, friction temperature and intrinsic properties of the constituents.
The life of grinding wheels is often estimated from their wear (Mansouri et al. Citation2007). In context of this study, the grinding wheel ceases to be functional from the loss of half of its geometric configuration or dimension from the periphery to the center. In other words, once half of the initial mass is lost, it becomes difficult for the grinding wheel operator to shape the object. The life of the grinding wheels can be expressed in a number of phases corresponding to the duration of the wear test. shows the values of the wear rates and the phases of operation of the wheels for the 20–1 combinations.
The wear of processed wheels is low when the average friction coefficient is reduced. Baky and Kamel (Citation2019) observed this same abrasive wear phenomenon on jute-glass-carbon reinforced composites. Raffia-based wheels have the longest life and operating phases amounting to 124,723, corresponding to 346 hours, and a very low WR of 0.1 mg/s. This longer life can be attributed to the cohesion of the abrasive grains with the resin, its low wear rate and the good thermal stability of the raffia core grains. The COM wheel has the lowest number of operating phases with a high RW of 2.8 mg/s. The wheels developed 20–1 and thus have good abrasive properties.
Conclusion
This work has identified four by-products that are sufficiently available locally, namely palm nut shells, Canarium fruit kernels, Coconut shells and Raphia Vinifera fruit kernels. On the other hand, there is no information in the literature on the mechanical characteristics of the raffia fruit kernel. This study contributed to determining raffia fruit kernel, hardness and Young’s modulus by instrumented macro indentation method, which are 101 MPa and 1.82 GPa, respectively. These four by-products were processed into fine P80 and coarse P20 abrasive grains according to FEPA standard. The 2-level full factorial design method was adopted to analyze the influence of epoxy binder content and grit size on abrasive properties. Densities are lighter compared to the mineralbased grinding wheels. Increasing the abrasive grain size of the by-products and the binder content has a beneficial influence on the Leeb hardness, whose values range from 220 HL to 342 HL. Porosity is an attractive property as it is related to the efficiency of the grinding wheels. The efficiency of the wheels was evaluated by determining the material removal rate of a polymer material (Leeb hardness 280 HL) used to manufacture shoe soles. The EN 20–1, EC 20–1, EP 20–1, and ER 20–1 wheels have material removal rates of 200.8 mg/s, 165 mg/s, 160.3 mg/s and 183.4 mg/s, respectively, which are close to commercial wheels at 171.3 mg/s. These wheels are the ones with the best formulations in the experimental approach. Their wear rates are very low compared to commercial wheels, and their material working life is much higher. In sum, bonded abrasives made with 20–1 formulations can be used effectively in industrial applications for shaping shoe soles, rubber silent blocks, stripping operations, paint removal, and even in abrasive disc hullers. The microscopic and topographic analyses are necessary to further understand the behavior of grains of vegetable origin in the material removal phase.
Highlights
Determination of the hardness and Young’s modulus of raffia vinifera core;
Elaboration of abrasives based on 4 plant by-products;
Physico-chemical, thermal, tribological and mechanical characterization of abrasives;
Formulation 20-1 has the best tribological performance;
Areas of application (shoemaking industry, abrasive disc strippers, pickling).
Ethical approval
I confirm that all the research meets ethical guidelines and adheres to the legal requirements of the study country
Authors Contribution
July 10th, 2022 To Editor-in-Chief journal of natural fibers, Dear Mr. Ryszard M. Kozłowski, I declare that all authors had a significant involvement in the development of this work and indicated as follows: Narcisse Defo: Conception, investigation, experimentation and writing; Rodrigue Nicodème Tagne Sikame: Conception, supervision, review and editing; William Paul Mejouyo Huisken: Investigation, experimentation and editing; Dieunedort Ndapeu: Review and editing; Stanislas Tiwa Tido: Investigation, writing, review and editing; Sophie Bistac-Brogly: Supervision, review and editing; Ebenezer Njeugna: Conception, supervision, review and editing; Thank you for your consideration of this manuscript. Sincerely,
Acknowledgements
The authors would like to thank the Douala-Bassa Technical High School in Cameroon for the use of the hydraulic press during the molding of the abrasive wheels.
Disclosure statement
The authors declare that they have no known competing financial interests or personal relationships that could have appeared to influence the work reported in this paper
References
- Aalil, I., K. Beck, X. Brunetaud, K. Cherkaoui, A. Chaaba, and M. Al-Mukhtar. 2015. Estimation de La Porosité et de l ’ Absorption d ’ Eau Des Pierres à l. Aide Des Essais Non Destructifs : Cas de La Calcarenite de Volubilis .” 35 (1):125–18.
- Achchaq, F., K. Djellab, L. Marmoret, and H. Beji. 2009. Analyse Thermogravimétrique Appliquée Aux Matériaux Isolants Fibreux. Laboratoire Des Technologies Innovantes, Amiens 2014 (May):1–6.
- Arunachalam, N., and B. Ramamoorthy. 2007. Texture analysis for grinding wheel wear assessment using machine vision. Proceedings of the Institution of Mechanical Engineers, Part B: Journal of Engineering Manufacture 221 (3):419–30. doi:10.1243/09544054JEM577.
- Asiri, Y., A. Corkum, and H. El Naggar. 2016. Leeb hardness test for UCS estimation of sandstone (modified copy) leeb hardness test for ucs estimation of sandstone. October.
- Baky, M. A. A. E., and M. Kamel. 2019. Abrasive wear performance of jute – glass – carbon- reinforced composites: Effect of stacking sequence and fibers relative amounts abrasive wear performance of jute – glass – carbon-reinforced composites: Effect of stacking sequence and fibers relative. Journal of Natural Fibers 1–16. doi:10.1080/15440478.2019.1616347.
- Barrère, C., and F. Dal Maso. 1997. Résines Époxy Réticulées Par Des Polyamines : Structure et Propriétés. Revue de l’Institute Francais Du Petrole 52 (3):317–35. doi:10.2516/ogst:1997043.
- Benbrinis, I., and B. Redjel. 2017. Nature & Technology Caractérisation Expérimentale Physico Mécanique et Étude Tribologique Des Sabots de Frein En Matériau Composite C / C à Matrice Organique Des Wagons SNTF. 1–9.
- Calligaro, T., P. Perin, F. Vallet, and J. P. Poirot. 2006. Contribution à l’étude Des Grenats Mérovingiens (Basilique de Saint-Denis et Autres Collections Du Musée d’Archéologie Nationale, Diverses Collections Publiques et Objets de Fouilles Récentes) : Nouvelles Analyses Gemmologiques et Géochimiques Effectuées. Antiquités Nationales (Saint-Germain-En-Laye) (38):111–44.
- Chakrabarti, S., and S. Paul. 2008. Numerical modelling of surface topography in superabrasive grinding. International Journal of Advanced Manufacturing Technology 39 (1–2):29–38. doi:10.1007/s00170-007-1201-y.
- Davis, T. D. 2005. Butyl carbamate from green grinding wheels with supercritical CO 2. 1733:2–6. doi:10.1111/j.1551-2916.2005.00276.x.
- Dieunedort, N., D. Nitidem Augustine, S. Tagne Nicodème R, G. Koungang Morino Bernard, D. Narcisse, and N. Ebénezer. 2020. Characterization of a brake lining composite based on aiele fruit cores (Canarium Schweinfurthii) and palm kernel fibers (Elaeis Guineensis) with a urea-formaldehyde matrix. International Journal of Scientific & Engineering Research (5) May.
- Dieunedort, N., F. Tamwo, M. Bernard Nganou Koungang, G. Tchuen, N. R. Sikame Tagne, S. Bistac, and E. Njeugna. 2020. Elaboration and characterization of a composite material based on Canarium Schweinfurthii engl cores with a polyester matrix. Materials Sciences and Applications 11 (03):204–15. doi:10.4236/msa.2020.113014.
- Elaissi, A., H. Alibi, M. Jabli, and A. Ghith. 2020. Development of abrasives from non-woven based on used textiles. Journal of Natural Fibers 00 (00):1–15. doi:10.1080/15440478.2020.1807439.
- Enih, R., H. P. S. A. K. Md Sohrab Hossain, W. O. Wan Nadirah, A. S. N. A. Rudi Dungani, N. L. M. Suraya, H. M. Fizree, A. K. Mohd Omar, H. M. Fizree, and A. K. Mohd Omar. 2017. Properties enhancement using oil palm shell nanoparticles of fibers reinforced polyester hybrid composites. Advanced Composite Materials 26 (3):259–72. doi:10.1080/09243046.2016.1145875.
- Fischer-Cripps, A. C. 2000. A review of analysis methods for sub-micron indentation testing ଝ. Materials Science Aspects of PVD Hard Coatings 58:569–85. doi:10.1016/S0042-207X(00)00377-8.
- Flores-Johnson, E. A., J. G. Carrillo, C. Zhai, R. A. Gamboa, Y. Gan, and L. Shen. 2018. Microstructure and Mechanical Properties of Hard Acrocomia Mexicana Fruit Shell. Scientific Reports (December 2017):1–12. doi:10.1038/s41598-018-27282-8.
- Goossens, F., M. Cherif, and O. Cahuc. 2013. Analyse Expérimentale et Modélisation Du Procédé de Polissage Abrasif de l ’ INOX 316L Abstract. (August):1–6.
- Goupy, J. L. 1990. Etude Comparative de Divers Plans d’expérience. Revue Des Statistiques Appliquées 4:5–44.
- Guillou, R., M. Guttmann, and P. Dumoulin. 1981. Role of Molybdenum in Phosphorus-. Induced Temper Embrittlement of 12 % Cr Martensitic Stainless Steel. February 15:63–72. doi:10.1179/030634581790426552.
- Herman, D., and J. Markul. 2004. Influence of microstructures of binder and abrasive grain on selected operational properties of ceramic grinding wheels made of alumina. International Journal of Machine Tools & Manufacture 44 (5):511–22. doi:10.1016/j.ijmachtools.2003.10.026.
- Huang, Z., W. Zhao, W. Zhao, C. Xiaojing, and L. Wentao. 2021. Tribological and anti-corrosion performance of epoxy resin composite coatings reinforced with differently sized Cubic Boron Nitride (CBN) particles. Friction 9 (1):104–18. doi:10.1007/s40544-019-0329-8.
- Iwar, R. T., K. Ogedengbe, K. Kayode Katibi, and L. Esekwe Oshido. 2021. Meso-microporous activated carbon derived from raffia palm shells: Optimization of synthesis conditions using response surface methodology. Heliyon 7 (6):e07301. doi:10.1016/j.heliyon.2021.e07301.
- Iyabano, A. H. 2014. Plantations Villageoises de Palmier à Huile et Huile de Palme Artisanale Au Cameroun Aboubakar Hayatou Iyabano. June. doi:10.13140/RG.2.1.2793.8648.
- Jamrozik, A., M. Barczewski, G. Framski, D. Baranowski, P. Jakubowska, Ł. Klapiszewski, T. Jesionowski, A. Voelkel, and B. Strzemiecka. 2020. Synthesis and characterization of low-cost cresol-based benzoxazine resins as potential binders in abrasive composites. Materials 13 (13):1–16. doi:10.3390/ma13132995.
- Jamrozik, A., B. Strzemiecka, and A. Voelkel. 2018. Additives for abrasive materials. doi:10.5772/intechopen.74822.
- Jani, S. P., A. Senthil Kumar, M. Adam Khan, and M. Uthaya Kumar. 2016. Machinablity of hybrid natural fiber composite with and without filler as reinforcement. Materials and Manufacturing Processes 31 (10):1393–99. doi:10.1080/10426914.2015.1117633.
- Jennings, J. S., and N. H. Macmillan. 1986. A Tough Nut to Crack. Journal of Materials Science 21 (5):1517–24. doi:10.1007/BF01114704.
- Jiang, C., H. Hui, X. Yao, Y. Peng, L. Zhou, and D. Jia. 2015. In situ dispersion and compatibilization of lignin/epoxidized natural rubber composites: Reactivity, morphology and property. Journal of Applied Polymer Science 132 (23):1–10. doi:10.1002/app.42044.
- Kaupp, G., and M. Reza Naimi-Jamal. 2011. Nutshells’ mechanical response: From nanoindentation and structure to bionics models. Journal of Materials Chemistry 21 (23):8389–90. doi:10.1039/c0jm03713c.
- Kermouche, G., M. Saint-Etienne, and J. M. Bergheau. 2014. Simulation Numérique de l’essai de Rayure. (May) 2009.
- Kodjo, N. F., K. Jean-Louis Konan, G. Gladys Doue, S. Didier, M. Yao, K. Allou, and S. Niamke. 2015. Caractérisation Physico-Chimique Des Composantes de Noix Immature et Mature de l ’ Hybride de Cocotier (Cocos Nucifera L .) Nain Jaune Malaisie x Grand Vanuatu Cultivé En Côte d. Ivoire 27 (1):4193–206.
- Kossman, S., D. Chicot, and A. Iost. 2017. Indentation instrumentée multi-échelles appliquée à l’étude des matériaux massifs métalliques. Matériaux & Techniques 105:104. doi:10.1051/mattech/2017007.
- Koungang, B. M. G., D. Ndapeu, G. Tchemou, P. William Huisken Mejouyo, B. Wenga Ntcheping, J. Tendo Foba, L. Courard, and E. Njeugna. 2020. Physical, water diffusion and micro-structural analysis of ‘canarium schweinfurthii engl’. Materials Sciences and Applications 11 (09):626–43. doi:10.4236/msa.2020.119042.
- Lagel, M. C., A. Pizzi, M. C. Basso, and S. Abdalla. 2015. Development and characterization of abrasive grinding wheels with a tannin-furanic resins matrix. Industrial Crops and Products 65:343–48. doi:10.1016/j.indcrop.2014.11.020.
- Liu, W., A. K. Mohanty, L. T. Drzal, P. Askel, and M. Misra. 2004. Effects of alkali treatment on the structure, morphology and thermal properties of native grass fibers as reinforcements for polymer matrix composites. Journal of Materials Science 39 (3):1051–54. doi:10.1023/B:JMSC.0000012942.83614.75.
- Lucas, P. W., P. J. Constantino, J. Chalk, C. Ziscovici, B. W. Wright, D. M. Fragaszy, D. A. Hill, J.J. -W. Lee, H. Chai, B. W. Darvell, et al. 2009. Indentation as a technique to assess the mechanical properties of fallback foods. American Journal of Physical Anthropology. 140(4):643–52. doi:10.1002/ajpa.21026.
- Mansouri, S., R. Benbouta, K. Loucif, and M. Benyahia. 2007. Densification et Caractérisation d’un Outil Abrasif En Corindon Aggloméré et Détermination de Sa Durée de Vie. Matériaux & Techniques 95 (3):179–83. doi:10.1051/mattech:2008002.
- Mbou, E., E. N. Tiaya, A. Kemajou, N. R. T. Sikame, and D. Ndapeu. 2017. Modelling of the water absorption kinetics and determination of the water diffusion coefficient in the pith of Raffia Vinifera of Bandjoun, Cameroon. Advances in Materials Science and Engineering 2017:1–12. doi:10.1155/2017/1953087.
- Mihăiescu, R., T. Mihăiescu, N. Ajtai, Z. Török, and A. Alexandru Ozunu. 2011. Air Quality Modelling as a Tool Used in Selecting Technological Alternatives for Developing a New Abrasive Facility. Advances in Environmental Sciences - International Journal of the Bioflux Society 5 (1):23–29.
- Morino, B., G. Koungang, D. Ndapeu, J. Tchoufang Tchuindjang, B. Wenga Ntcheping, G. Tchemou, S. Bistac, E. Njeugna, and L. Courard. 2020. In Fl uence of temperature on the creep behaviour by macroindentation of cocos nucifera shells and Canarium Schweinfurthii cores (bio-shellnut wastes in Cameroon). Materials Research Express 7 (10):105306. doi:10.1088/2053-1591/abbebb.
- Nadolny, K., P. Sutowski, and D. Herman. 2015. Analysis of aluminum oxynitride AlON (Abral®) abrasive grains during the brittle fracture process using stress-wave emission techniques. International Journal of Advanced Manufacturing Technology 81 (9–12):1961–76. doi:10.1007/s00170-015-7338-1.
- Nagatani, M., A. Tsurumaki, K. Takamatsu, H. Saito, N. Nakamura, and H. Ohno. 2019. Preparation of epoxy resins derived from lignin solubilized in tetrabutylphosphonium hydroxide aqueous solutions. International Journal of Biological Macromolecules 132:585–91. doi:10.1016/j.ijbiomac.2019.03.152.
- Ndapeu, D., E. Njeugna, S. B. Brogly Bistac, J. Y. Yves Drean, M. Fogue, and J. N. Ngenefeme Foba. 2013. Experimental study of the drying kinetics of the coconut shells (Nucifera) of Cameroon. Materials Sciences and Applications 04 (12):822–30. doi:https://doi.org/10.4236/msa.2013.412105.
- Neto, S., R. Alfredo, M. A. M. Araujo, R. M. P. Barboza, A. S. Fonseca, G. H. D. Tonoli, F. V. D. Souza, L. H. C. Mattoso, and J. M. Marconcini. 2015. Comparative study of 12 pineapple leaf fiber varieties for use as mechanical reinforcement in polymer composites. Industrial Crops and Products 64:68–78. doi:10.1016/j.indcrop.2014.10.042.
- Njeugna, E., M. B. K. Ganou, D. Ndapeu, J. N. T. Foba, N. R. T. Sikame, and P. W. M. Huisken. 2016 July. An instrumented macro-indentation method for determining the mechanical properties of coconut shell (Coco Nucifera of Cameroon). Mechanics, Materials Science & Engineering doi:10.13140/RG.2.1.1447.3846.
- Njoukam, R., and R. Peltier. 2002. L’aiélé (Canarium Schweinfurthii Engl.) : Premier Essai de Plantation Dans l’ouest Du Cameroun. Fruits 57 (4):239–48. doi:10.1051/fruits:2002021.
- Obot, M. U., D. S. Yawas, and S. Y. Aku. 2017. Development of an abrasive material using periwinkle shells. Journal of King Saud University - Engineering Sciences 29 (3):284–88. doi:10.1016/j.jksues.2015.10.008.
- Odior1, A. O., and F. A. Oyawale. 2013. Performance evaluation of abrasive grinding. Nigerian Journal of Technology (NIJOTECH) 32 (2):318–24.
- Odior, A. O., and F. A. Oyawale. 2010. Manufacture of abrasive grains from locally sourced raw materials in Nigeria. Journal of Emerging Trends in Engineering and Applied Sciences (JETEAS) 1 (1):40–47.
- Oliveira Filho, E. G., F. S. Luz, R. T. Fujiyama, A. C. Silva, V. S. Candido, and S. Neves Monteiro. 2020. Effect of chemical treatment and length of Raffia fiber (Raphia Vinifera) On mechanical stiffening of polyester composites. Polymers 12 (12):1–17. doi:10.3390/polym12122899.
- Oliver, W. C., and G. M. Pharr. 1992. An improved technique for determining hardness and elastic modulus using load and displacement sensing indentation experiments. Materials Research Society 7 (6):1564–83. doi:10.1557/JMR.1992.1564.
- Passilly, B., O. Smerdova, P. Zannese, M. Pecora, J. M. Roche, and M. Gigliotti. 2017. Comportement de La Resine Époxy En Nanoindentation à Haute Température Mechanical Behavior of Époxy Resin under High Temperature Nanoindentation Test. Comptes Rendus Des JNC 20 – Ecole Des Ponts ParisTech 1–10.
- Pathmanaban, P., A. Musharath Aalam, and S. Sr. 2019. Testing of coconut shell reinforced brake PADS abstract. International Journal of Scientific Research and Engineering Development 2 (5):853–59.
- Pharr, G. M., and W. C. Oliver. 2004. Measurement of hardness and elastic modulus by instrumented indentation: Advances in understanding and refinements to methodology. Journal of Materials Research 19 (01):3–20. doi:10.1557/jmr.2004.19.1.3.
- Pinot, P. 2015. Détermination de La Porosité de Roches Calcaires : Méthode et Incertitude de Mesure. Revue Française de Métrologie 37:37–53. doi:10.1051/rfm/2015004.
- Prevot, G. 2010. Valorisation Énergétique Des Déchets de Biomasse d ’ Origine Végétale. Etude RECORD 08(123) .
- Randall, N. X. 2004. “Direct measurement of residual contact area and volume during the nanoindentation of coated materials as an alternative method of calculating hardness.” IMEKO TC5 Conference on Hardness Measurements Theory and Application in Laboratories and Industries, HARDMEKO 2004d July 2002): 98–103. 10.1080/01418610210133504.
- Sabaa, Z. M., and B. M. Fahad. 2018. Glass and porcelain waste as abrasives investigated at different conditions. IOP Conference Series: Materials Science and Engineering 454:1. doi:10.1088/1757-899X/454/1/012117.
- Sestier, C. 2010. Méthode d’étude de La Retouche Des Outils Sur Lames de Silex Pressigniennes: Critères Techno-Fonctionnels Quantitatifs et Qualitatifs. ArchéoSciences 34 (1):9–24. doi:10.4000/archeosciences.2576.
- Shukla, S. K., P. Kumar, and D. Srivastava. 2006. Study of degradation kinetics of blends of epoxy and resole: A statistical approach. Materials and Manufacturing Processes (October):37–41. doi:10.1081/AMP-100104306. 2014.
- Sikame Tagne, N. R., T. E. Mbou, O. Harzallah, D. Ndapeu, W. Huisken, D. Nkemaja, E. Njeugna, M. Fogue, and J. Y. Drean. 2020. Physicochemical and mechanical characterization of Raffia Vinifera Pith. Advances in Materials Science and Engineering 2020:1–10. doi:10.1155/2020/8895913.
- Sikame Tagne, N. R., E. Njeugna, M. Fogue, J. Y. Drean, A. Nzeukou, and D. Fokwa. 2014. Study of water absorption in Raffia Vinifera fibres from Bandjoun, Cameroon. Scientific World Journal 2014:1–11. January. doi: 10.1155/2014/912380.
- Stanislas, T. T., J. Foba Tendo, E. Beckley Ojo, O. Fayen Ngasoh, P. Azikiwe Onwualu, E. Njeugna, and H. Savastano Junior. 2020. Production and characterization of pulp and nanofibrillated cellulose from selected tropical plants. Journal of Natural Fibers 00 (00):1–17. doi:10.1080/15440478.2020.1787915.
- Suresha, B., G. Chandramohan, P. Samapthkumaran, S. Seetharamu, and S. Vynatheya. 2006. Friction and wear characteristics of carbon-epoxy and glass-epoxy woven roving fiber composites. Journal of Reinforced Plastics and Composites 25 (7):771–82. doi:10.1177/0731684406063540.
- Syreyshchikova, N. V., and D. Yu Pimenov. 2017, March. Quality assessment of emery cloth-based abrasive tool using elasticity technological parameter. ( 2018) Procedia Engineering 206:1155–60. doi:10.1016/j.proeng.2017.10.610.
- Toenshoff, H. K., T. Grabner, and M. Zinngrebe. 2007. A breakthrough in production grinding with bn wheels -a result of systematic scientific work. Advanced Manufacturing Processes (December):37–41. 2014. doi:10.1080/10426918608953156.
- Watanabe, N., Y. Kondo, D. Ide, T. Matsuki, H. Takato, and I. Sakata. 2010. Characterization of polycrystalline silicon wafers for solar cells sliced with novel fixed-abrasive wire. Progress in Photovoltaics: Research and Applications 18 (7):485–90. doi:10.1002/pip.923.
- William, P., M. Huisken, G. Tchemou, N. Rodrigue, S. Tagne, D. Ndapeu, and E. Njeugna. 2022. Effect of the addition of oil palm mesocarp fibers on the physical and mechanical properties of a polyester matrix composite. 2022. 10.1155/2022/3399986
- Yahaya, R., S. M. Sapuan, M. Jawaid, Z. Leman, and E. S. Zainudin. 2016. Water Absorption Behaviour and Impact Strength of Kenaf-Kevlar Reinforced Epoxy Hybrid Composites. Advanced Composites Letters 25 (4):98–102. doi:10.1177/096369351602500403.
- Zhao, B., W. Ding, Z. Chen, and C. Yang. 2019. Pore structure design and grinding performance of porous metal-bonded CBN abrasive wheels fabricated by vacuum sintering. Journal of Manufacturing Processes 44 (May):125–32. doi:10.1016/j.jmapro.2019.06.001.