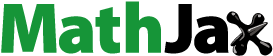
ABSTRACT
Crotalaria juncea bast fibers a novel cellulose rich material is valorized by producing cellulose nanocrystals (CNCs) which gained much attention due to its unique properties. CNCs obtained during this study consisted of two steps: pretreatment of C. juncea fibers to obtain chemically purified cellulose followed by sulfuric acid hydrolysis. Efficacy of two different pretreatment methods chlor-alkali method (pre-treatment-I) and ultra sound assisted chlorine free alkaline peroxide (pre-treatment-II) methods was examined for CNC preparation. Pre-treatment-I was found to be more effective yielding higher crystallinity and higher surface sulfate ester groups containing CNCs compared to CNCs obtained using pre-treatment-II. Moreover the cellulose structure was altered with more pure cellulose-I structure obtained from pre-treatment-I. The process conditions of pre-treatment – I was optimized for CNC preparation. The acid concentration of 80%(w/v) was found to be optimized to produce CNCs with~43% yield, 80.9% crystallinity index having a rod-like structure (Length −120 ± 26 nm and diameter − 25 ± 5.5 nm). The surface charge density of the optimized CNC was found to be 0.34 meqv/g and a zeta potential −27.7 mV was recorded emphasizing stable dispersion.
摘要
芥菜蔓藤韧皮纤维是一种新型的富含纤维素的材料,通过制备纤维素纳米晶(CNC)而得到重视,因为其独特的财产. 在这项研究中获得的CNCs包括两个步骤: 对酒渣菜纤维进行预处理以获得化学纯化的纤维素,然后进行硫酸水解. 研究了两种不同的预处理方法——氯碱法(预处理I)和超声波辅助无氯碱性过氧化物(预处理II)的CNC制备效果. 发现与使用预处理II获得的CNCs相比,预处理I更有效,产生更高的结晶度和更高的含CNCs的表面硫酸盐基团. 此外,用从预处理I获得的更纯的纤维素-I结构改变了纤维素结构. 预处理–I的工艺条件针对CNC制备进行了优化. 发现80%(w/v)的酸浓度被优化以生产具有约43%产率、80.9%结晶度指数的棒状结构(长度-120 ± 26 nm,直径-25 ± 5.5 nm)的CNCs. 发现优化的CNC的表面电荷密度为0.34meqv/g,记录到的zeta电位为-27.7 mV,强调了稳定的分散.
Introduction
In recent years nanocellulose has gained much attention due to ever increasing environmental regulations and shift from petroleum-based products toward green environment-friendly materials (Dhali et al. Citation2021). Valorization of lignocellulosic biomass waste has been center of research for past decade as an alternative source of energy, but preparation of high-valued products such as nanocellulose from waste lignocellulosic biomass could open new avenues of sustainable circular economy by waste reutilization and minimization (Hafemann et al. Citation2019; S. Yu et al. Citation2021; Dhali et al. Citation2021).
Lignocellulosic biomass mainly consists of lignin, cellulose and hemicellulose. Due to recalcitrant nature of lignin, pretreatment is often employed toward lignocellulosic biomass for facilitating lignin removal and easy accessibility of cellulose (Baksi et al. Citation2019). Nanocellulose is categorized mainly in three subcategories depending on the sources and extraction methods, such as i) cellulose nanocrystals (CNCs), ii) cellulose nanofibers (CNFs), and iii) bacterial nanocellulose (BNC) Hafemann et al. (Citation2019); Sudeshna, Hemraz, and Boluk (Citation2020); Jozala et al. (Citation2016).
Cellulose nanocrystals (CNC) are typical rod-shaped particles with 6–10 nm in width and 80–200 nm in length, obtained commonly by acid hydrolysis of cellulose (Sudeshna, Hemraz, and Boluk Citation2020). Cellulose nanofibers (CNFs) on the other hand are fibril like structures having width of 5-30 nm and length in several micrometer, commonly prepared by mechanical disintegration (J. Song et al. Citation2018) and or TEMPO mediated oxidation (Saito et al. Citation2007). Bacterial nanocellullose (BNC) is produced by the bacterium Gluconacetobacter xylinus under static or stirred culture media consisting of three main steps of (i) polymerization of glucose residues in β-1–4 glucan, (ii) extracellular secretion of linear chains, and (iii) organization and crystallization of glucan chains (Jozala et al. Citation2016).
In recent years, cellulose nanocrystals (CNC) captured attention of scientific community as well as industries due to its potential applications in various fields such as coatings (He et al. Citation2021; Mekonnen, Haile, and Ly Citation2021), personal care (Mendoza et al. Citation2021; Zhang et al. Citation2019), pharmaceutical formulation (Sunasee, Hemraz, and Ckless Citation2016), food (Huang et al. Citation2020) and household products, oil fields (Sudeshna, Hemraz, and Boluk Citation2020), building material additive (Reza, Boluk, and Bindiganavile Citation2019), drug delivery (Long et al. Citation2021; Min et al. Citation2020), composite materials (Chen et al. Citation2020) etc. Along with several interesting properties such as relatively low density, nontoxic character, uniform size distribution, high aspect ratio, high surface area, thermal properties and high modulus of elasticity, the commercialization prospect of CNC inspires researchers to discover new fields of applications (Klemm et al. Citation2011). A recent market research forecasted nanocellulose market value to reach $ 2.712 billion by 2025 with annual growth rate of 18.8% (S. Yu et al. Citation2021).
Crystallinity and physicochemical properties of CNCs are highly dependent on source material and extraction methods. A substantial research has been dedicated toward optimization of process variables for extraction of CNCs from various sources e.g. woody plant materials such as soft wood, hardwood (Beck-Candanedo, Roman, and Gray Citation2005); cotton materials such as cotton (Pandi, Sonawane, and Anand Kishore Citation2021), cotton linters (Montanari et al. Citation2005), waste cotton (Thambiraj and Shankaran Citation2017); non woody plant materials for instance corn husk, corn cob, rice straw, wheat straw, sugarcane bagasse, cassava bagasse, coconut husk fibers, pineapple leaf fibers, sisal, ramie, carded and pristine hemp fibers (Alves et al. Citation2013; Johar, Ahmad, and Dufresne Citation2012; Saha and Ghosh Citation2019; Sain and Panthapulakkal Citation2006; Smyth et al. Citation2017). Although, sulfuric acid is the most extensively used acid, hydrochloric acid (Yu et al. Citation2014), phosphoric acid (Espinosa et al. Citation2013) and hydrobromic acid (Hasan et al. Citation2011) were also explored for acid hydrolysis. Recently, advanced extraction methods employing TEMPO-mediated oxidation (Zhong-Yan, Guo-Lin Tong, and Zhou Citation2011), hydrolysis using deep eutectic solvent (Ling et al. Citation2019), ionic liquid extraction (Zakaria et al. Citation2011), microwave assisted hydrothermal treatment (De Melo, Clark, and Matharu Citation2017) have also been studied.
In the present work Crotalaria juncea, nonedible, cellulose rich, highly crystalline lignocellulose is valorized for the fabrication of nanocrystalline cellulose which according to author’s knowledge has not reported earlier. Crotalaria juncea commonly used as a bast fiber and green manure is fast growing, tropical cover crop (Parenti et al. Citation2021; Sengupta and Debnath Citation2018). Due to high amount of fiber and nitrogen content with negligible ash, C. juncea fiber is being explored toward production of transportation fuels such as bioethanol (Baksi et al. Citation2019), biogas (Sinbuathong and Sillapacharoenkul Citation2020). Sunn hemp seeds have been explored to extract oil (Dutta, Sarkar, and Mukherjee Citation2017) and transformed to produce biodiesel (Sadhukhan and Sarkar Citation2016) in recent years.
In the present study C. juncea fiber, a novel source, was valorized for the first time for fabrication of CNCs. Efficacy of two different pretreatment methods, chlor-alkali (pre-treatment-I) and ultrasound assisted chlorine free alkaline peroxide methods (pre-treatment-II) on C. juncea bast fibers, difficult to fragment due to high tensile strength, were valorized for efficient production of chemically purified cellulose. Furthermore, acid hydrolysis conditions for chlor-alkali pretreated samples were optimized for fabrication of CNCs. The CNCs obtained by various hydrolysis conditions were characterized for their physico-chemical structure using DLS-Zeta, FT-IR, XRD, SEM, TEM, TGA and also the surface charge was determined using conductometric titrations.
Materials and methods
Materials
Crotalaria juncea of K12 variety was collected from ICAR-CRIJAF, Pratapgarh, UP, India, washed, dried and size reduced to 40 mesh size screen before pretreatment using Willey mill. The ground fiber was dried in hot air oven for 6 h at 70°C for removal of remaining moisture. Other chemical reagents such as sodium chlorite, acetic acid, sodium sulfite, sodium hydroxide, acetone, dimethylsulfoxide and sulfuric acid were procured from Merck India.
Preparation of CNC
Preparation of cellulose nanocrystals (CNCs) from lignocellulosic biomass mainly consists of two steps: a) Pre-treatment and b) Hydrolysis.
Pre-treatment-I
Pre-treatment-I consisted of four steps as elaborated by Mandal and Chakrabarty (Citation2011). In a typical experiment, 1 g of the as prepared fiber was treated with 50 ml of 0.7% (w/v) sodium chlorite solution at its boiling temperature for 5 h at pH4, adjusted by 5% acetic acid and maintained with buffer solution of pH4, residue obtained was washed with distilled water and oven-dried at 40°C for overnight (PM-1).
PM-1 was then boiled with 250 ml of 5% (w/v) sodium sulfite solution for 5 h. Then the residue was washed with adequate distilled water for complete removal of lignin and partial removal of hemicellulose followed by drying (PM-2).
PM-2 was further treated with 250 ml of 17.5% (w/v) NaOH solution for 5 h at the boiling condition to remove hemicelluloses. The insoluble residue (cellulose) was collected by filtration and washed thoroughly until neutralization and air-dried (PM-3). PM-3 was further treated with 50 ml dimethyl sulfoxide (DMSO) at 80°C in an oil bath for 3 hours to increase the porosity into the cellulose rich substrate. The product thus obtained was then filtered, washed with distilled water and air-dried (PM-4). The schematic of pre-treatment-I is presented in .
Pre-treatment-II
An alternate method was devised by us (Saha and Ghosh Citation2019) to pre-treat CJ to obtain CNC as represented in . In a typical experiment, 5 g of the milled C. juncea fiber was dispersed in 300 ml of distilled water using ultra-sonication (35 KHz Bio base Sonicator bath) at 50°C for about 30 min. The aqueous suspension was then filtered and residue was left for drying at hot air oven at 100°C for about 3 hours and then left under vacuum overnight. The dry residue was mixed with 200 ml 5 wt% NaOH. To the suspension 11 wt% H2O2 was added drop-wise for about 5 minutes under continuous sonication. The experiment was carried out for 2 hours at 50°C. Then the residue was washed with distilled water and dried under hot air oven at 50°C for 6 hours followed by overnight vacuum drying (PM-5).
Acid-Hydrolysis
In the second step pre-treated dried residue (PM-4) was subjected to acid hydrolysis by heating with varying concentrations of sulfuric acid (fiber to liquor ratio of 1:20) at 50◦C under strong agitation. The hydrolysis was quenched by adding 5-fold excess water (100 ml) to the reaction mixture. The acid hydrolysis conditions of PM-4 were optimized by varying the acid concentration from 60% to 95% using 5 h till 80% and 1 h and 45 mins for 90% and 95% (w/v) respectively. The process conditions for different hydrolysis concentrations are summarized in .
Table 1. Reaction conditions for acid hydrolysis.
The optimized sulfuric acid concentration of 80% (w/v) was employed to compare the efficacy of different pretreatment conditions. Consequently, both the pre-treated dried residues (PM-4 and PM-5) were subjected to acid hydrolysis by heating with 80% (w/v) sulfuric acid (fiber to liquor ratio of 1:20) for 1 h at 50◦C under strong agitation yielding CNC-I and CNC-II.
The reaction mixture was cooled to room temperature and centrifuged for 10 min at 10,000 rpm. Supernatant was removed and the sediment was redispersed into distilled water and centrifuged for 3 to 4 times until it became turbid. To maintain exact ph 7 the turbid mixture was washed by distilled water using dialysis membrane. Then it was freeze dried (Labogene Coolsafe −110°C) to obtain powdered CNCs for further characterizations.
Yield determination
Yield of different pre-treated materials and CNCs after acid hydrolysis was determined gravimetrically based on chemically purified cellulose (PM-4) and raw material.
Structural and chemical characterizations
The structural variations of raw material, pre-treated materials and CNC were observed by FTIR spectroscopy using a JASCO FT/IR-4700 spectrophotometer. The FTIR spectrum of the samples was noted in the transmittance mode in the range of 4000–450 cm−1.
X-ray diffraction data were collected using a Rigaku Miniflex X-ray diffractometer equipped with Cu Kα radiation at 30kV and 15 mA to investigate the XRD spectra of the cellulosic sample. Scattered radiation was detected in the range 2θ = 5–50°, at a speed of 3°/min. Crystallinity Index of all the samples was calculated using EquationEquation 1(1)
(1) according to Segal’s method (Segal et al. Citation1959)
Scanning electron microscopy (SEM) photographs of raw material, pretreated material and CNC particles were captured using SEM JEOL JSM–6360 using a gold coating. A drop of dilute suspension of CNC was placed on a copper grid followed by drying it under table lamp followed by staining for 3 min with Ruthenium vapor. Transmission electron micrographs (TEM) photographs were taken using a TECNAIT12 FEI (Germany) transmission electron microscope with a voltage of 80 kV.
Particle Size was measured after equilibriating CNC suspension (0.1 wt. %) at room temperature for 1 hour, in a temperature regulated cell at 25°C, DLS/Zeta measurements were conducted by Malvern Zetasizer Nano-ZS instrument working at 173° scattering angle. Effective hydrodynamic diameters and size distributions were obtained using DLS.
Conductometric titration was used to quantify the sulfate half ester content CNC through the determination of surface charge density following the procedures of (Beck, Méthot, and Bouchard Citation2015) with some modification. A 150 mg of CNC sample was suspended into 50 ml of 0.001 M NaCl solution and stirred for 10 min and the resulting suspension was then titrated with 0.01 M NaOH solution. The sulfation value was then calculated using EquationEquation 2(2)
(2) (Feng, Esker, and Roman Citation2010).
where μ=surface charge density (meqv/gm),
CNaOH= Concentration of NaOH used for titration, VNaOH=Volume of NaOH required for Titration, Ccnc=Concentration of CNC suspension, αcnc= amount of CNC suspension for titration.
Thermal stability of CNC was checked using Pyris Diamond TG/DTA, Perkin-Elmer, Singapore. Approximately 3 mg of each sample was heated from 30°C to 750°C at a heating rate of 15°C/min in a platinum crucible with alpha alumina powder as reference under N2 flow of 150 ml/min.
Result and discussions
C. juncea is a cellulose rich energy crop containing only 7.04% lignin, 3.06% hemicellulose and rest 89.9% cellulose (Baksi et al. Citation2019) abundantly available in subtropical countries.
Optimization of acid hydrolysis conditions for pre-treatment-I
Yield of pre-treated materials and CNCs
Sodium sulfite employed in pre-treatment-I solubilized lignin-chlorine complex obtained during digestion with sodium chlorite. To certain extent hemicellulose was also removed through solubilization with sodium sulfite. Further treatment with NaOH, intermolecular ester bonds between lignin and hemicellulose were saponified facilitating removal of lignin and dissolution of hemicellulose. DMSO treatment helped to swell the cellulose enabling easy transport of hydrolyst (sulfuric acid) into the fibers in the subsequent acid hydrolysis step. Treatment of the chemically purified cellulose (CPC) substrate with sulfuric acid leads to esterification of hydroxyl groups while removal of the amorphous part takes place keeping the crystalline part intact. Grafting of negatively charged sulfate groups during acid hydrolysis leads to formation of stable dispersion in water due to electrostatic repulsion of electrical double layer. However, upon freeze drying, the crystalline cellulose became rod-like and aggregated to some extent due to the formation of hydrogen bonds resulting high surface energy of the CNC (Mandal and Chakrabarty Citation2011).
The yield of various pre-treated materials during pre-treatment-I is presented in . The major changes in yield results were observed for RM to PM-1 and PM-2 to PM-3. This was expected as most of the lignin was removed during pre-treatment of RM with sodium chlorite solution in the first step while hemicelluloses were removed during treatment of PM-2 with NaOH. The weight loss was lower in case of PM-1 to PM-2 as remaining lignin and partial depolymerization of hemicellulose occurred during this step while the lowest weight loss of PM-3 to PM-4 attributed toward incorporation of porosity to the cellulose structure.
Table 2. Yield of pre-treated materials (a) and CNCs from C. juncea (b).
Yields of CNCs after acid hydrolysis with various sulfuric acid concentrations from chemically pure cellulose (PM-4) and raw material are tabulated and presented in . With increase in acid concentrations, CNC yield increased (81% from PM-4 and 50.2 ± 0.18% from RM) till 70% (w/v) sulfuric acid concentrations while a decrease in yield was observed with further increase in acid concentrations. The initial increase in yield was due to efficient hydrolysis of chemically purified cellulose with increase in acid concentrations. The decrease in yield thereafter was probably due to the combined effect of lower reaction time and dissolution of more amorphous regions along with degradation of some crystalline cellulose structure at higher acid concentrations (Hafemann et al. Citation2019; Kusmono, Waziz Wildan, and Noer Ilman Citation2020). High CNC yield from C. juncea (~50% from raw material and 81% from purified cellulose) was obtained in the present study compared to 50% from purified corncob (Alves et al. Citation2013), 15.61% from Zea mays (Smyth et al. Citation2017), 55% from treated pineapple leaves (Marcos et al. Citation2013), 30% cassava bagasse (Pasquini et al. Citation2010), 46.4% from waste cotton (Wang et al. Citation2017) etc.
FT-IR analysis
Changes in the chemical structure of C. juncea during the course of pre-treatment-I and acid hydrolysis with varying sulfuric acid concentrations are depicted in respectively. Since major constituent of C. juncea is cellulose, the raw material exhibited almost all the characteristic groups of cellulose and thus very minute changes were observed during the course of pre-treatment. Broad peak around 3400 cm−1 assigned to – OH symmetric stretching, characteristic peaks of cellulose was present in all the spectra. A peak shift was observed from 2865 cm−1 for raw C. juncea attributed to – CH symmetrical stretching vibrations of polysaccharides to all the pre-treated materials and CNCs to 2966 cm−1 attributed to asymmetric – CH stretching of polysaccharides. The peak at 1720 cm−1 in the FTIR spectrum of ground C. juncea attributed to the C=O stretching vibration for the acetyl and uronic ester linkages in lignin, hemicellulose, pectin shifted to 1764 cm−1 after pre-treatment with sodium chlorite (PM-1) due to formation of lignin chlorine complex and disappeared in the subsequent steps of pre-treatment indicating removal of lignin (Saha and Ghosh Citation2019). The spectral bands at 1514 cm−1 depict the aromatic ring present in lignin with C=C symmetrical stretching vibrations disappeared completely after first step of pre-treatment indicated efficient lignin removal in the very first step of pre-treatment-I. In addition, peak around 1660 cm−1 signifying O-H stretching of the absorbed water to cellulose become prominent with the course of pre-treatment indicated increase in cellulose content with the advancement of pre-treatment. The peak at 1242 cm−1 present in the spectra of C. juncea ascribed to C-O stretching vibrations in aryl group of lignin tends to disappear after pre-treatment. While the bands at 1178 cm−1 and 1073 cm−1 were mainly due to asymmetric stretching vibrations of C-O-C bridge and also skeletal vibrations involving C-O stretching respectively assigned to polysaccharide structure became strong and prominent during the progression of pre-treatment. The band at 906 cm−1 ascribed to characteristic peak of glycosidic bond symmetric ring of polysaccharides became prominent with advancement of pre-treatment signifies increase in cellulose content and decrease in lignin (Hafemann et al. Citation2019). Peak around 670 cm−1 attributed to C-OH out of plane bending of cellulose became strong and prominent after pre-treatment.
Figure 2. FTIR spectra of raw (a) C. juncea (PM) and pre-treated materials (PM-1 – PM-4), (b) different CNCs isolated with varying acid concentrations, (C) variation of TCI and LOI of RM, different pre-treated materials and CNCs with varying acid concentrations.
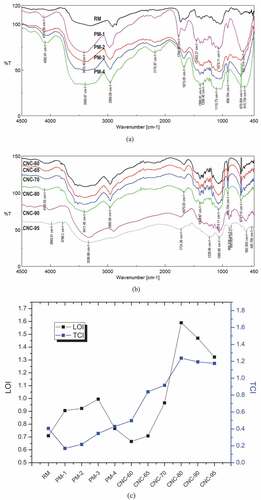
There was no significant change in FTIR spectra observed between PM-4 and CNCs demonstrating main cellulose structure to be unaltered during acid hydrolysis as reported elsewhere (Shaheen and Emam Citation2017). Increase in acid concentrations did not show any significant alterations of cellulose backbone structure while exhibiting the characteristic peaks of cellulose (1370 cm−1, 1335 cm−1, 1162 cm−1, 1070 cm−1, 906 cm−1, 677 cm−1). Nevertheless, with increase in acid concentrations the peak intensities at 906 cm−1 and 677 cm−1 increased till 80% w/v concentration. Minute changes in FTIR spectra were observed for CNC-90 and CNC-95 as peak shift from 906 cm−1 to 885 cm−1 occurred along with the appearance of a new satellite peak around 850 cm−1. Also cellulose characteristic peak at 677 cm−1 got significantly reduced for CNC-90 and CNC-95 demonstrating initiation of cellulose degradation and or formation of cellulose-II structure.
The lateral order index (LOI) (1430 cm−1/906 cm−1) and total crystallinity index (TCI) (1390 cm−1/2960 cm−1) were calculated according to Xu and Wang (Feng and Wang Citation2015) and were presented in . The total crystallinity index decreased significantly from RM to PM-1 while increased thereafter with the progression of pre-treatment and increase in acid concentrations during hydrolysis till 80% w/v exhibiting strong correlation with cellulose rich structure. Decrease in the same index with further increase in acid concentrations could be attributed to degradation of crystalline cellulose structure. On the contrary no strong correlation could be found for lateral order index with progression of pre-treatment or acid concentrations during hydrolysis. There was an initial increase in LOI from RM to PM-3 while a decrease in the same was observed for PM-4 and CNC-60. A further increase in the same index was observed with increase in acid concentrations till 80% (w/v) and decrease in the same with further increase in acid concentrations. Since 1430 cm−1 attributes contributions from all the constituents, an initial increase could probably due to abundance of hemicellulose and cellulose structure due to removal of lignin. LOI also showed similar trends as TCI with the increase in acid concentrations, initial increase till 80% (w/v) and decrease thereafter strengthening the hypothesis of degradation of crystalline structure of cellulose at higher acid concentration.
XRD analysis
Adjacent cellulose molecules are linked together by the interaction of hydrogen bonds and van der Waals forces ensuing crystalline structure of cellulose (Gabriel et al. Citation2021). shows the XRD patterns of all the pre-treated materials and CNCs obtained using various acid concentrations, all of which demonstrated peaks corresponding to crystalline cellulose structure. PM-1 and PM-2 exhibited cellulose-I structure with characteristic peaks around 2θ = 22.5, 14.8, 16.05, 35.5 corresponding to (2 0 0), (−1 1 0), (1 1 0) and (4 0 0) lattice planes respectively (Orrabalis et al. Citation2019; Yu et al., Citation2014). A change was observed from cellulose-I structure to cellulose-II for PM-2 to PM-3, PM-4 could be attributed to alkaline treatment of PM-2 by directly interacting with cellulose. PM-3, PM-4 exhibited three main characteristic peaks of cellulose-II structure at around 2θ = 12.01, 19.85 and 21.85 (Gabriel et al. Citation2021; Yu et al. Citation2014). Although there was a structural change in cellulose, the crystallinity index remained almost constant during the advancement of pre-treatment as depicted in . CNC-60, CNC-65, and CNC-70 also demonstrated similar cellulose-II structure as PM-3 and PM-4 but there was an increase in intensity after acid hydrolysis owing to dissolution of amorphous regions of cellulose which was further supported by the increase in crystallinity after acid hydrolysis as illustrated in . While increasing the acid concentrations from 60% to 70% (w/v) although no structural changes took place, intensities of all the peaks became diminished. This can directly be correlated to lower crystallite size with increase in acid concentrations while no significant change in crystallinity index was observed (). Further increase in acid concentrations not only altered the cellulose-II to cellulose-I structure but the peaks become narrower and intense (Yu et al., Citation2014) while the crystallinity index remained similar for CNC-80. Small decrease in crystallinity index was observed for CNC-90 while significant decrease in the same was observed for further increase in acid concentrations (CNC-95) confirming degradation in crystalline structure of cellulose. High crystallinity index for various acid concentrations (~81%) obtained during present study was higher or comparable with reported values for CNCs from different sources (Pandi, Sonawane, and Anand Kishore Citation2021; Pasquini et al. Citation2010; Zhong-Yan et al., Szyma et al. Citation2019; Alves et al. Citation2013; Wang et al. Citation2017).
Morphological analysis
The morphology of the raw material, pre-treated materials (PM-3 and PM-4) and CNCs (CNC-60 and CNC-80) were recorded using SEM images whereas single cellulose nanocrystal rod like morphology was observed by TEM analysis. The RM showed smooth cylindrical structure as presented in while disintegrated fibrillar cellulosic structure was observed for PM-3 (). The diameter of the original plant fiber was larger compared to the diameter of pre-treated materials. Moreover, they appear as a composite form of several microfibrils . The fiber surface of the raw material shown in the images found to be smooth due to the presence of waxes and oil. At first sodium chlorite was used for removal of lignin through depolymerization. On subsequent alkali treatments removes hemicellulose from the rest of fiber and make the cellulose water soluble. These processes destroy the composite form of microfibrils and result in micrograph in whereas the diameter of the fibrils was also reduced to a great extent, as the consequence of removal of non-cellulosic constituents from the fiber (Cherian et al. Citation2010). PM-4 showed fibrous structure with higher porosity induced by DMSO as illustrated in . CNC-60 exhibited disintegrated cylindrical structure () while rod shaped structure was evident for CNC-80 (). Although the EDS spectra of CNC-60 did not show any sulfate group due to low degree of sulfation, CNC-80 exhibited sulfate group of approximately 0.32 which was a close approximation of the calculated degree of sulfation (0.34) for CNC-80 as discussed in next section.
Figure 4. SEM (a) untreated crotalaria juncea (RM), (b) alkali treated crotalaria juncea (PM-3), SEM-EDS micrograms and spectra of (c) PM-4, (d) CNC-60 and (e) CNC-80; (f) TEM images of cellulose nanocrystals prepared under different hydrolysis conditions: 60% acid concentration; 80% acid concentration.
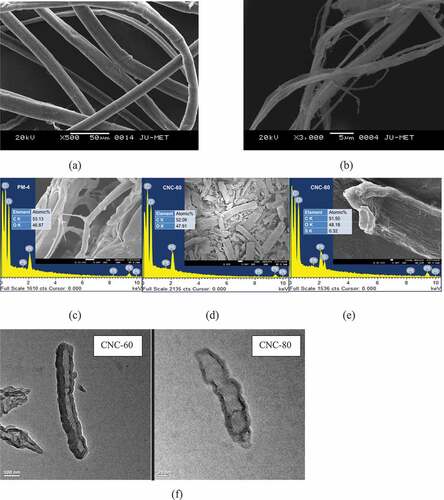
Single crystal TEM micrographs of CNC-60 and CNC-80 are compared in . It is evident from the figure that the diameter and length of CNCs decrease with increasing acid concentrations. The length and diameter of CNC-60 were 500 ± 34 nm and 80 ± 6 nm respectively while length and diameter of CNC-80 reduced to 120 ± 26 nm and 25 ± 5.5 nm respectively. From this figure it can also be concluded that due to presence of surface half ester groups, individual particles repel each other and with highly dilute dispersion it is possible to obtain single crystal micrograph.
Degree of sulfation
represents changes in degree of sulfation with the variation in sulfuric acid concentrations. With increase in sulfuric acid concentration there was an increase in degree of sulfation from 0.04 ± 0.0032 meqv/g for CNC-60 to 0.43 ± 0.0083 meqv/g for CNC-90 while a decrease to 0.31 ± 0.0035 meqv/g was observed for CNC-95. This was due to the fact that increase in acid concentration increased available half-sulfate ester group to react to cellulose thus increasing the degree of sulfation. Decrease in the same could be attributed to the fact that some crystalline structure degraded at this very high sulfuric acid concentration resulting desulfation and drastic decrease in crystallinity of CNC.
Diffractive Light Scattering (DLS) and zeta potential
DLS experiment was carried out to obtain a rough estimate of hydrodynamic diameter of the cellulose nano materials, widely accepted technique for size determination.
The particle size analysis results depicted in illustrated initial decrease in hydrodynamic diameter with increase in acid concentrations till 80% (w/v) while an increase with further increase in acid concentrations could be attributed to incomplete reactions and degradation of cellulose nanocrystals. Initial decrease in diameter was due to dissolution of higher amount of amorphous regions leading to smaller sizes of cellulose nanocrystals.
The zeta potentials, the most important parameter for determination of the stability of CNC in aqueous media, of a series of samples prepared under various hydrolysis conditions (sulfuric acid percentage) were measured and presented in . CNC-60, CNC-65, CNC-70 exhibited almost similar around −24 mV zeta potential although a decrease in trend was observed with increase in acid concentrations. The sample prepared using 80% sulfuric acid showed lower negative value (−27.7 mV) and this was found to decrease further with increase in percentage of sulfuric acid. This was mainly due to the presence of a larger amount of negatively charged sulfate groups on the surface of the CNCs leading to repulsive forces and thus producing stable dispersions. The colloidal system becomes unstable between Zeta Potential values of+20 mV to −20 mV. It can be concluded from the above results that the CNCs fabricated by varying acid concentrations during this study produced stable dispersions in water owing to their small size and high half sulfate surface ester groups.
Thermogravimetric (TGA) analysis
TGA/DTG curves of Crotalaria juncea (RM), pure cellulose (PM-4) and the acid hydrolyzed nanocelluloses (CNC-80 and CNC-90) are shown in . A single degradation peak around 380°C was observed for both RM and PM-4. High thermal stability of RM and PM-4 can be attributed to very high cellulose content (90%) of C. juncea fibers (Baksi et al. Citation2019) having highly crystalline structure (Hafemann et al. Citation2019). PM-4, more thermally stable compared to RM (degradation peak shifted from 380°C to 390°C), was due to removal lignin and hemicelluloses which has low decomposition temperature during alkaline pre-treatment of C. juncea. Owing to amorphous nature, hemicellulose containing acetyl group and lignin having complex aromatic ring structure are less thermally stable compared to cellulose (Kusmono, Waziz Wildan, and Noer Ilman Citation2020; K. Song et al. Citation2019). The initial weight losses started at ∼33°C for both untreated Crotalaria juncea (RM) and PM-4 while CNCs showed higher initial weight loss temperature (∼35°C). High solvation capacity with water molecule was responsible for higher weight loss temperature of CNCs (35°C). Water was evaporated near about 110°C for all samples. Higher weight loss around 100°C for CNCs compared to RM and PM-4 was attributed to moisture absorption by isolated CNCs. The highest weight loss for CNC-80 for this region attributed to higher moisture absorption (Gabriel et al. Citation2021; Kusmono, Waziz Wildan, and Noer Ilman Citation2020; K. Song et al. Citation2019; Hafemann et al. Citation2019) and less dehydration at lower acid concentration during hydrolysis. The degradation of raw Crotalaria juncea started at 310°C and the rate of degradation continued up to 400°C whereas PM-4 degradation began at 300°C and the rate of degradation was maximum at 370°C. The degradation of CNC-90 and CNC-80 took place around 260°C and 310°C leading to lower thermal stability because of their nano-sizes, greater number of free ends in the chain of CNCs, and presence of highly sulfated amorphous regions. In general, thermal degradation of pure cellulose involves some major steps including dehydration, depolymerization and decomposition of glycosyl followed by formation of residue. A second peak of weight loss around 600°C observed for CNC-90, was due to the formation of lower molecular weight gaseous products from charred residues (K. Song et al. Citation2019). Presence of sulfate groups lower the activation energy, resulting lower thermal stability of CNCs (Hafemann et al. Citation2019). Higher sulfate content in CNC-90 was responsible for lower thermal stability. In addition, formation of cellulose-II structure might also lowered the thermal stability of CNC-90 in comparison with CNC-80 as cellulose-II has lower degradation temperature than cellulose-I (Xing et al. Citation2018). This could also be the reason for higher weight loss for CNC-90 compared with that of CNC-80.
Comparison of pre-treatment-I and pre-treatment-II on preparation of CNCs
In this section CNCs obtained by acid hydrolysis using different pre-treatment methods have been compared to comprehend the efficacy of two different pre-treatment methods on the formation and properties of CNCs. Since previous results of pre-treatment-I revealed 80% (w/v) sulfuric acid concentration to be the optimum for preparation of CNC (CNC-I), this acid concentration was further employed for pre-treatment-II (CNC-II) for comparison purposes.
FTIR analysis of the prepared CNCs (CNC-I and CNC-II) revealed crystalline chemical structure of cellulose associated with these samples (). The peak at 3411 cm−1 signifies the presence of – OH group, as the peak is bulgy. The most prominent band in alcohols is due to the O-H bond, and it appeared as a strong, broad band covering the range of about 3000 – 3700 cm−1 for both CNC-I and CNC-II. A carboxylic acid functional group combines the features of alcohols and ketones because it has both the O-H bond and the C=O bond. Therefore, carboxylic acids showed a very strong and broad band covering a wide range between 2800 and 3500 cm−1 for the O-H stretch. At the same time they also show the stake-shaped band in the middle of the spectrum around 1710 cm−1 corresponding to the C=O stretch which was absent for both CNC-I and CNC-II (Mandal and Chakrabarty Citation2011). But a peak around 1760 cm−1 was evident for CNC-II which can be ascribed to presence of carbonyl groups generated due to oxidation during pre-treatment-II with high amount of hydrogen peroxide, a strong oxidizing agent. While the bands at 1178 cm−1 and 1073 cm−1 were mainly due to anti-symmetric stretching vibrations of C-O-C bridge and also skeletal vibrations involving C-O stretching which contributes to the cellulose backbone were observed for both CNC-I and CNC-II. The band at 906 cm−1, the characteristic peak of glyosidic bonds present in the cellulose was evident in both CNC-I and CNC-II. But this characteristic peak was sharper in CNC-I compared to that of CNC-II confirming higher amount of ordered cellulose structure. Another cellulose characteristic peak around 677 cm−1 showed differences in shape for CNC-I and CNC-II was probably due to formation of cellulose-II structure for CNC-II as observed during XRD characterization.
Figure 8. (A) FTIR spectra and (b) XRD patterns of CNC-I and CNC-II isolated using different pre-treatment methods.
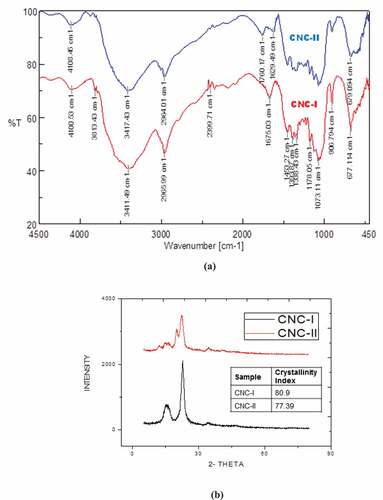
XRD characterizations were performed to analyze the crystallinity of CNC extracted from Crotalaria juncea using conventional pre-treatment method (CNC-I) as well as that of CNC obtained after pre-treatment using sonication method (CNC-II). Structural differences were observed between CNC-I and CNC-II structure as evident from XRD data (). Cellulose-I structure was conformed for CNC-I while CNC-II exhibited presence of cellulose-II structure confirming the fact that not only acid concentrations during hydrolysis reaction but pre-treatment method also play an important role in formation of different cellulose structure. The acid hydrolysis treatment of CNC is expected to better dissolve amorphous zones under the specified conditions used in this study. This process shows hydronium ions can penetrate into amorphous regions of cellulose, promoting the hydrolytic cleavage of glycosidic bonds and the release of individual crystallites. The crystallinity index of CNC-I (80.9), higher than that of CNC-II (77.39) was due to transformation of cellulose-I to cellulose-II structure and also due to sharper diffraction peak at 2θ = 22.5°. These results are in accordance with FTIR findings.
CNC obtained by H2SO4 hydrolysis often possesses a negatively charged surface, which help uniform dispersion in water due to electrostatic repulsion. The calculated value of degree of sulfation for CNC- I was found to be 0.34 meqv/g, which confirmed higher degree of sulfation compared to CNC-II (0.067 meqv/g). This was probably due to the difference in pre-treatment which directly affected the formation and structural differences in naocrystalline cellulose structure.
The physico-chemical properties of CNCs obtained in this study could effectively be used as a reinforcing agent for cement paste for building materials, nanocomposites, coating additives, hydrogel for controlled drug release, etc., as similar properties of CNCs obtained from various source materials are reported elsewhere (Molnes et al. Citation2018; Szyma Citation2019; Mendoza et al. Citation2021; Mekonnen, Haile, and Ly Citation2021; Sengupta and Debnath Citation2018; Zhang et al. Citation2019; Li et al. Citation2013; Yin et al. Citation2016) as depicted in .
Table 3. Application of CNCs derived from various sources.
Conclusions
C. juncea proved to be an excellent source for crystalline nanocellulose (CNC) preparation with yield as high as~43% from raw material having crystallinity index of~80.9. 80% H2SO4 concentration proved to be the optimized acid concentration for this present study as highest yield of CNCs (~43%) with highest crystallinity index (~80.9) was observed for CNC-80. The FTIR results also revealed similar trend and highest LOI and TCI was observed for CNC-80 confirming higher crystallinity. Although highest degree of sulfation was observed for CNC-90, it was less thermally stable compared to CNC-80 as demonstrated by TGA analysis. The DLS-Zeta results confirmed lowest hydrodynamic diameter for CNC-80 having a zeta potential value of −27.7 mV confirming formation of stable dispersion in water. Conventional and ultrasound assisted pre-treatment was further compared for 80% acid hydrolysis condition and conventional pre-treatment proved to be more effective compared to that of ultrasound assisted pre-treatment. CNC-I (produced by conventional pre-treatment) exhibited higher degree of sulfation and higher crystallinity compared to CNC-II (produced by ultrasound assisted pre-treatment). In the present study transformation of cellulose-I to cellulose-II structure was observed for conventional pre-treatment to ultrasound assisted pre-treatment.
Highlights
C. juncea is successfully valorized to produce crystalline nanocellulose (CNC) with crystallinity index of~80.9.
80%(w/v) H2SO4 concentration proved to be the optimized acid concentration for CNC production(CNC-80).
Highest degree of sulfation was observed for CNC-90 but was less thermally stable compared to CNC-80.
The DLS-Zeta results confirmed lowest hydrodynamic diameter for CNC-80 having a zeta potential value of −27.7Wang, ZhanhongmV confirming formation of stable dispersion in water.
Transformation of cellulose-I to cellulose-II structure was observed for conventional pre-treatment to ultrasound assisted pre-treatment
Supplemental Material
Download Zip (204 KB)Disclosure statement
No potential conflict of interest was reported by the authors.
Supplemental data
Supplemental data for this article can be accessed online at https://doi.org/10.1080/15440478.2023.2181275
Additional information
Funding
References
- Alves, H., W. Pires, F. Neto, N. Oliveira, and D. Pasquini. 2013. Extraction and characterization of cellulose nanocrystals from corncob for application as reinforcing agent in nanocomposites. Industrial Crops & Products 44:427–20. Elsevier B.V. doi:10.1016/j.indcrop.2012.10.014.
- Baksi, S., S. Saha, C. Birgen, U. Sarkar, H. A. Preisig, S. Markussen, B. Wittgens, and A. Wentzel. 2019. Valorization of lignocellulosic waste (crotalaria juncea) using alkaline peroxide pretreatment under different process conditions: an optimization study on separation of lignin, cellulose, and hemicellulose. Journal of Natural Fibers 16 (5):662–76. Taylor and Francis Inc. doi:10.1080/15440478.2018.1431998.
- Beck-Candanedo, S., M. Roman, and D. G. Gray. 2005. Effect of reaction conditions on the properties and behavior of wood cellulose nanocrystal suspensions. Biomacromolecules 6 (2):1048–54. doi:10.1021/bm049300p.
- Beck, S., M. Méthot, and J. Bouchard. 2015. General procedure for determining cellulose nanocrystal sulfate half-ester content by conductometric titration. Cellulose 22:101–16. doi:10.1007/s10570-014-0513-y.
- Chen, Y., J. Zhu, H. -Y. Yu, and Y. Li. 2020. Fabricating robust soft-hard network of self-healable polyvinyl alcohol composite films with functionalized cellulose nanocrystals. Composites Science and Technology 194 (March):108165. Elsevier Ltd. doi:10.1016/j.compscitech.2020.108165.
- Cherian, B. M., A. L. Leão, S. F. I. de Souza, S. Thomas, L. A. Pothan, and M. Kottaisamy. 2010. Isolation of nanocellulose from pineapple leaf fibres by steam explosion. Carbohydrate Polymers 81 (3):720–25. Elsevier. doi:10.1016/J.CARBPOL.2010.03.046.
- De Melo, E. M., J. H. Clark, and A. S. Matharu. 2017. The Hy-MASS concept: hydrothermal microwave assisted selective scissoring of cellulose for: in situ production of (meso)porous nanocellulose fibrils and crystals. Green Chemistry 19 (14):3408–17. Royal Society of Chemistry. doi:10.1039/c7gc01378g.
- Dhali, K., M. Ghasemlou, F. Daver, P. Cass, and B. Adhikari. 2021. Science of the total environment a review of nanocellulose as a new material towards environmental sustainability. The Science of the Total Environment 775:145871. Elsevier B.V. doi:10.1016/j.scitotenv.2021.145871.
- Dutta, R., U. Sarkar, and A. Mukherjee. 2017. Study of transient behaviour of modified soxhlet apparatus for extraction of a bio-fuel oil from crotalaria juncea seed. International Journal of Green Energy 14 (8):675–86. Taylor & Francis. doi:10.1080/15435075.2017.1318283.
- Espinosa, S., T. Kuhnt, E. J. Foster, and C. Weder. 2013. Isolation of Thermally Stable Cellulose Nanocrystals by Phosphoric Acid Hydrolysis. Biomacromolecules 14 (4):1223–30. doi:10.1021/bm400219u.
- Feng, J., A. R. Esker, and M. Roman. 2010. Acid-catalyzed and solvolytic desulfation of H2SO 4-Hydrolyzed cellulose nanocrystals. Langmuir 26 (23):17919–25. doi:10.1021/la1028405.
- Feng, X., and D. Wang. 2015. Chapter 2 - analysis of lignocellulosic biomass using infrared methodology. In Pretreatment of Biomass, ed. A. Pandey, S. Negi, P. Binod, and C. Larroche, 7–25. Amsterdam: Elsevier. doi:10.1016/B978-0-12-800080-9.00002-5.
- Gabriel, T., A. Belete, G. Hause, R. H. H. Neubert, and T. Gebre-Mariam. 2021. Isolation and characterization of cellulose nanocrystals from different lignocellulosic residues: A comparative study. Journal of Polymers and the Environment 29 (9):2964–77. Springer US. doi:10.1007/s10924-021-02089-3.
- Hafemann, E., R. Battisti, C. Marangoni, and R. A. F. Machado. 2019. Valorization of royal palm tree agroindustrial waste by isolating cellulose nanocrystals. Carbohydrate Polymers 218 (May):188–98. Elsevier. doi:10.1016/j.carbpol.2019.04.086.
- Hasan, S., I. Filpponen, S. P. Clarke, and D. S. D. F. Brougham Argyropoulos. 2011. Production of cellulose nanocrystals using hydrobromic acid and click reactions on their surface. Journal of Materials Science 46 (22):7344–55. doi:10.1007/s10853-011-5696-0.
- He, Y., H. Li, X. Fei, and L. Peng. 2021. Carboxymethyl cellulose/cellulose nanocrystals immobilized silver nanoparticles as an effective coating to improve barrier and antibacterial properties of paper for food packaging applications. Carbohydrate Polymers 252 (August 2020):117156. Elsevier Ltd. doi:10.1016/j.carbpol.2020.117156.
- Huang, S., X. Liu, C. Chang, and Y. Wang. 2020. Recent developments and prospective food-related applications of cellulose nanocrystals: A review. Cellulose 27 (6):2991–3011. Springer Netherlands. doi:10.1007/s10570-020-02984-3.
- Johar, N., I. Ahmad, and A. Dufresne. 2012. Extraction, preparation and characterization of cellulose fibres and nanocrystals from rice husk. Industrial Crops & Products 37 (1):93–99. Elsevier B.V. doi:10.1016/j.indcrop.2011.12.016.
- Jozala, A. F., L. Celia De Lencastre-Novaes, A. Moreni Lopes, V. De Carvalho Santos-Ebinuma, P. Gava Mazzola, and A. Pessoa-Jr. 2016. Bacterial nanocellulose production and application: A 10-year overview. Applied Microbiology and Biotechnology 100 (5):2063–72. doi:10.1007/s00253-015-7243-4.
- Klemm, D., D. Klemm, F. Kramer, S. Moritz, T. Lindström, M. Ankerfors, D. Gray, and A. Dorris. 2011. Nanocelluloses: A new family of nature-based materials angewandte. Angewandte Chemie International Edition 50 (24):5438–66. doi:10.1002/anie.201001273.
- Kusmono, R. F. L., M. Waziz Wildan, and M. Noer Ilman. 2020. Preparation and characterization of cellulose nanocrystal extracted from ramie fibers by sulfuric acid hydrolysis. Heliyon 6 (11):e05486. Elsevier Ltd. doi:10.1016/j.heliyon.2020.e05486.
- Li, F., P. Biagioni, M. Bollani, A. Maccagnan, and L. Piergiovanni. 2013. Multi-functional coating of cellulose nanocrystals for flexible packaging applications. Cellulose 20 (5):2491–504. doi:10.1007/s10570-013-0015-3.
- Ling, Z., J. Vincent Edwards, Z. Guo, N. T. Prevost, S. Nam, Q. Wu, A. D. French, and F. Xu. 2019. Structural variations of cotton cellulose nanocrystals from deep eutectic solvent treatment: micro and nano scale. Cellulose 26 (2):861–76. Springer Netherlands. doi:10.1007/s10570-018-2092-9.
- Long, W., H. Ouyang, C. Zhou, W. Wan, S. Yu, K. Qian, M. Liu, X. Zhang, Y. Feng, and Y. Wei. 2021. Simultaneous surface functionalization and drug loading: a novel method for fabrication of cellulose nanocrystals-based ph responsive drug delivery system. International Journal of Biological Macromolecules 182 (June):2066–75. Elsevier B.V. doi:10.1016/j.ijbiomac.2021.05.193.
- Mandal, A., and D. Chakrabarty. 2011. Isolation of nanocellulose from waste Sugarcane Bagasse (SCB) and its characterization. Carbohydrate Polymers 86 (3):1291–99. Elsevier. doi:10.1016/J.CARBPOL.2011.06.030.
- Marcos, R., W. Pires, F. Neto, H. Alves, D. Ferreira, N. Oliveira, and D. Pasquini. 2013. Cellulose nanocrystals from pineapple leaf, a new approach for the reuse of this agro-waste. Industrial Crops & Products 50:707–14. Elsevier B.V. doi:10.1016/j.indcrop.2013.08.049.
- Mekonnen, T. H., T. Haile, and M. Ly. 2021. Applied surface science hydrophobic functionalization of cellulose nanocrystals for enhanced corrosion resistance of polyurethane nanocomposite coatings. Applied Surface Science 540 (1):148299. Elsevier B.V. doi:10.1016/j.apsusc.2020.148299.
- Mendoza, D. J., M. Maliha, V. S. Raghuwanshi, C. Browne, L. M. M. Mouterde, G. P. Simon, F. Allais, and G. Garnier. 2021. Diethyl sinapate-grafted cellulose nanocrystals as nature-inspired UV fi lters in cosmetic formulations. Materials Today Bio 12 (August):100126. Elsevier Ltd. doi:10.1016/j.mtbio.2021.100126.
- Min, Y., Y. Suk, T. Kim, K. Yang, K. Nam, D. Choe, and Y. Hoon. 2020. Cationic cellulose nanocrystals complexed with polymeric SiRNA for efficient anticancer drug delivery. Carbohydrate Polymers 247 (June):116684. Elsevier. doi:10.1016/j.carbpol.2020.116684.
- Molnes, S. N., A. Mamonov, K. G. Paso, S. Strand, and K. Syverud. 2018. Investigation of a New Application for Cellulose Nanocrystals: A Study of the Enhanced Oil Recovery Potential by Use of a Green Additive. Cellulose 25 (4):2289–301. Springer Netherlands. doi:10.1007/s10570-018-1715-5.
- Montanari, S., M. Roumani, L. Heux, and M. R. Vignon. 2005. Topochemistry of Carboxylated Cellulose Nanocrystals resulting fromTEMPO-mediated oxidation. Macromolecules 38 (5):1665–71. doi:10.1021/ma048396c.
- Orrabalis, C., D. Rodríguez, L. G. Pampillo, C. Londoño-Calderón, M. Trinidad, and R. Martínez-García. 2019. Characterization of nanocellulose obtained from cereus forbesii (a South American Cactus). Materials Research 22 (6):1–10. doi:10.1590/1980-5373-MR-2019-0243.
- Pandi, N., S. H. Sonawane, and K. Anand Kishore. 2021. Synthesis of Cellulose Nanocrystals (CNCs) from cotton using ultrasound- assisted acid hydrolysis. Ultrasonics - Sonochemistry 70 (May 2020):105353. Elsevier. doi:10.1016/j.ultsonch.2020.105353.
- Parenti, A., G. Cappelli, W. Zegada-Lizarazu, C. Martín Sastre, M. Christou, A. Monti, and F. Ginaldi. 2021. SunnGro: A new crop model for the simulation of sunn hemp (Crotalaria Juncea L.) grown under alternative management practices. Biomass & bioenergy 146:105975. doi:10.1016/j.biombioe.2021.105975.
- Pasquini, D., E. De Morais, A. Aprígio, M. Naceur, and A. Dufresne. 2010. Extraction of cellulose whiskers from cassava bagasse and their applications as reinforcing agent in natural rubber. Industrial Crops & Products 32 (3):486–90. Elsevier B.V. doi:10.1016/j.indcrop.2010.06.022.
- Reza, M., Y. Boluk, and V. Bindiganavile. 2019. The effect of Cellulose Nanocrystal (CNC) particles on the porosity and strength development in oil well cement paste. Construction and Building Materials 205:456–62. Elsevier Ltd. doi:10.1016/j.conbuildmat.2019.01.073.
- Sadhukhan, S., and U. Sarkar. 2016. Production of biodiesel from Crotalaria Juncea (Sunn-Hemp) oil using catalytic trans-esterification: process optimisation using a factorial and box – behnken design. Waste and Biomass Valorization 7 (2):343–55. Springer Netherlands. doi:10.1007/s12649-015-9454-4.
- Saha, S., and R. Ghosh. 2019. Cellulose nanocrystals from lignocellulosic agro-waste: A comparative study on conventional and ultrasonic assisted preparation methods. Materials Today: Proceedings 11 (January):628–36. Elsevier. doi:10.1016/J.MATPR.2019.03.020.
- Sain, M., and S. Panthapulakkal. 2006. Bioprocess preparation of wheat straw fibers and their characterization. Industrial Crops and Products 23 (1):1–8. doi:10.1016/j.indcrop.2005.01.006.
- Saito, T., S. Kimura, Y. Nishiyama, and A. Isogai. 2007. Cellulose nanofibers prepared by tempo-mediated oxidation of native cellulose. Biomacromolecules 8:2485–91. doi:10.1021/bm0703970.
- Segal, L., J. J. Creely, A. E. M. Jr, and C. M. Conrad. 1959. An empirical method for estimating the degree of crystallinity of native cellulose using the X-ray diffractometer. Textile Research Journal 29 (10):786–94. doi:10.1177/004051755902901003.
- Sengupta, S., and S. Debnath. 2018. Industrial crops & products development of Sunnhemp (Crotalaria Juncea) fi bre based unconventional fabric. Industrial Crops & Products 116 (October 2017):109–15. Elsevier. doi:10.1016/j.indcrop.2018.02.059.
- Shaheen, T. I., and H. E. Emam. 2017. Sono-chemical synthesis of cellulose nanocrystals from wood sawdust using acid hydrolysis Cellulose Nanocrystal (CNC) is a unique material obtained from naturally occurring. International Journal of Biological Macromolecules 107:1599–606. doi:10.1016/j.ijbiomac.2017.10.028.
- Sinbuathong, N., and B. Sillapacharoenkul. 2020. Enhancement of biogas production from sunnhemp using alkaline pretreatment. International Journal of Hydrogen Energy 46 (6):4870–78. Elsevier Ltd. doi:10.1016/j.ijhydene.2020.04.058.
- Smyth, M., A. García, E. J. F. Chris Rader, and J. Bras. 2017. Extraction and process analysis of high aspect ratio cellulose nanocrystals from corn (Zea Mays) agricultural residue. Industrial Crops & Products 108 (May):257–66. Elsevier. doi:10.1016/j.indcrop.2017.06.006.
- Song, J., C. Chen, Z. Yang, Y. Kuang, T. Li, Y. Li, and H. Huang. 2018. Highly compressible, anisotropic aerogel with aligned cellulose nano fi bers. ACS Nano 12 (1):140–47. doi:10.1021/acsnano.7b04246.
- Song, K., X. Zhu, W. Zhu, and X. Li. 2019. Preparation and characterization of cellulose nanocrystal extracted from calotropis procera biomass. Bioresources and Bioprocessing 6 (1):Springer Singapore. 10.1186/s40643-019-0279-z
- Sudeshna, S., U. D. Hemraz, and Y. Boluk. 2020. The effects of high pressure and high temperature in semidilute aqueous cellulose nanocrystal suspensions. Biomacromolecules 21 (2):1031–35. doi:10.1021/acs.biomac.9b01130.
- Sunasee, R., U. D. Hemraz, and K. Ckless. 2016. Cellulose nanocrystals: A versatile nanoplatform for emerging biomedical applications. Expert Opinion on Drug Delivery 13 (9):1243–56. Taylor & Francis. doi:10.1080/17425247.2016.1182491.
- Szyma, M., M. Grzegorczyk-Frańczak, M. Szymańska-Chargot, and G. Łagód. 2019. Effect of eco-friendly cellulose nanocrystals on physical properties of cement mortars. Polymers 11 (12):11. doi:10.3390/polym11122088.
- Thambiraj, S., and D. R. Shankaran. 2017. Preparation and physicochemical characterization of cellulose nanocrystals from industrial waste cotton. Applied Surface Science 412:405–16. doi:10.1016/j.apsusc.2017.03.272.
- Wang, Z., Z. Yao, J. Zhou, and Y. Zhang. 2017. Reuse of waste cotton cloth for the extraction of cellulose. Carbohydrate Polymers 157:945–52. Elsevier Ltd. doi:10.1016/j.carbpol.2016.10.044.
- Xing, L., G. Jin, W. Zhang, T. Dengyun, and H. Chuanshuang. 2018. Cellulose I and II nanocrystals produced by sulfuric acid hydrolysis of tetra pak cellulose I. Carbohydrate Polymers 192 (February):184–92. Elsevier. doi:10.1016/j.carbpol.2018.03.042.
- Yin, S., I. Ahmad, M. Cairul, and I. Mohd. 2016. Cellulose nanocrystals extracted from rice husks as a reinforcing material in gelatin hydrogels for use in controlled drug delivery systems Gelatin/CNC hydrogel gelatin hydrogel. Industrial Crops & Products 93:227–34. Elsevier B.V. doi:10.1016/j.indcrop.2015.11.082.
- Yu, S., J. Sun, Y. Shi, Q. Wang, J. Wu, and J. Liu. 2021. Environmental science and ecotechnology nanocellulose from various biomass wastes: Its preparation and potential usages towards the high value-added products. Environmental Science and Ecotechnology 5:100077. Elsevier Ltd. doi:10.1016/j.ese.2020.100077.
- Yu, H., C. Yan, X. Lei, Z. Qin, and J. Yao. 2014. Novel approach to extract thermally stable cellulose nanospheres with high yield. Materials Letters 131:12–15. Elsevier. doi:10.1016/j.matlet.2014.05.159.
- Zakaria, M., N. Muhammad, A. Sarwono, M. V. K. Mohamad Azmi Bustam, and S. Rafiq. 2011. Preparation of cellulose nanocrystals using an ionic liquid. Journal of Polymers and the Environment 19 (3):726–31. doi:10.1007/s10924-011-0323-3.
- Zhang, Z., B. Zhang, N. Grishkewich, R. Berry, and K. C. Tam. 2019. Cinnamate-functionalized cellulose nanocrystals as UV-shielding nanofillers in sunscreen and transparent polymer films. Advanced Sustainable Systems 3 (4):1800156. doi:10.1002/adsu.201800156.
- Zhong-Yan, Q., Y. C. F. C. Guo-Lin Tong, and J.C. Zhou. 2011. Preparation of ultrasonic-assisted high carboxylate content cellulose nanocrystals by tempo oxidation. BioResources 6 (2):1136–46.