ABSTRACT
The present research deals with various design factors materials)Polyethylene, Polypropylene and Lorg Wood(, hole type, holes’ spacing and box edge thickness) in regard to stresses exerted onto the pear packaging boxes. At first, Solid Works 2018 Software was employed to design 81 boxes and the material factors (polyethylene, polypropylene and Lorg wood), box edge thickness (0.35, 0.5 and 0.65 cm), holes’ type (circular, square and rectangular) and holes’ spacing (2.1, 2.4 and 2.7 cm) were taken into account. The entire boxes were analyzed using Ansys 2018 and the maximum stress rates were calculated. Then, the obtained stress rates were subjected to statistical analysis through taking advantage of SAS 9.2 software. The study results indicated that equivalent stress, total deformation, equivalent elastic strain, shear elastic strain, normal stress and shear stress correspondingly are equal to 638.8pa (rectangular hole type and 0.5 cm edge thickness), 1.91 × 10−11 m (circular hole type and 0.5 cm edge thickness), 3.7 × 10−9 m/m (2.7 cm hole spacing and circular hole type), 4.43 × 10−9 m/m (0.50 cm box edge thickness and circular hole type), 305.66pa (2.7 cm hole spacing and circular hole type) and 225pa (rectangular hole type and 0.5 cm box edge thickness); the highest amounts were 5914.7pa (square hole type and 0.65 cm edge thickness), 1.11 × 10−9 m (square hole type and 0.5 cm box edge thickness), 3.21 × 10−8 m/m (0.65 cm box edge thickness and square hole type), 4.17 × 10−8 m/m (0.65 cm box edge thickness and square hole type), 2880.6pa (0.65 cm box edge thickness and square hole type), 2304.8pa square hole type and 0.65 cm box edge thickness, respectively.
Introduction
Programmable designs, interfirm competitions, quality enhancement and influence of the customer perception have caused the creation of various and unique designs in packing. It is said that the packaging design plays the most important role provoking the purchase or not to purchase because packaging can transfer a sense of satisfaction to the consumers (Djatna and Kurniati, Citation2015). There is a need for an attractive and unique packaging to be designed in order to enable the decision to purchase in the consumer. Designing should be touched by the consumers’ feelings and the emotional experiences have to be created in packaging through looking at or touching the container (Jiao et al., Citation2006). The importance and the role of packaging have undergone changes during these years. The packaging, besides serving the protection and preservation of the products in regard of the external effects, has to be easily and readily transportable and have a favorable look (Stanujkic et al., Citation2015). In fact, the use of agricultural product packaging aims at protecting them against damage and providing for ease of transportation and integrated storage of the agricultural products (Caleb et al., Citation2013; Barkai-Golan, Citation2001). Because the wooden or cardboard crates are used only once after which they are either totally destroyed or sent to be recycled, the use of plastic boxes has drawn a great deal of attention due to their being recyclable. Also, these plastic boxes can be washed and reused several times. Of course, the important point in making use of wooden and cardboard boxes is in that they are constructed based on renewable raw materials while the plastic boxes are made of petroleum products (Albrecht et al., Citation2013). On the other hand, the use of an appropriate packaging in regard of the intended product’s sanitation is highly considered and the material type of interest has to be investigated in terms of microbe attraction and contamination (Kregiel et al., Citation2014). Inappropriate processing and packaging (and/or insufficient and inadequate packaging) can be accompanied by product weight reduction between 25% and 50%. Such wastages are more frequent in developing countries and some 10% of the fruits and vegetables are rendered disagreeable and spoiled during transportation for unacceptable quality. This high level of post-harvest wastage is suggestive of the idea that the production of foodstuff is only half the way to the world population’s nourishment (Opara and Mditshwa, Citation2013). Also, considering the fact that the fruits and vegetables are to be still considered as living creatures undergoing metabolic processes incessantly, they have to have an appearance devoid of scratch and bruise during storage and transportation. The lack of a proper packaging method during transportation and storage causes reduction of moisture, bruise, bad flavor and so forth of the products (Han et al., Citation2017; Jianglian, Citation2013). In regard of the idea that packaging is remarkably important in preserving the quality and healthiness of the products and facilitation of the foodstuff transportation in the course of production to consumption chain and considering the fact that the wastages of products in packaging and the bioenvironmental effects thereof is the topic constantly spoken of in packaging discussions pertinent to food and agricultural materials industry, the current research paper aims at highlighting the role of packaging in food industry according to the effect of packaging on the amount of stress imposed on the packaging boxes when loading and/or storing in line with the preservation of the product quality and safety and reduction of the foodstuff wastage and spoiling of agricultural products after their reaching of a nutritional value.
Materials and Methods
Box Design
Solid Works 2018 Software was utilized to design 81 boxes with 0.35, 0.5 and 0.65 cm in thickness ()) and 2.1, 2.4 and 2.7 cm spacing of the holes in the floor and body of the boxes ( canda) and three hole types, namely circular, square and rectangular () and three material types, i.e. polyethylene, polypropylene and wood, ().
Table 1. Specifications of each invoice.
Figure 1. The size of the intended spaces; a) holes’ spacing on floor; b) body thickness of the box; c) holes’ spacing on the box body; d) box width; f) box height.
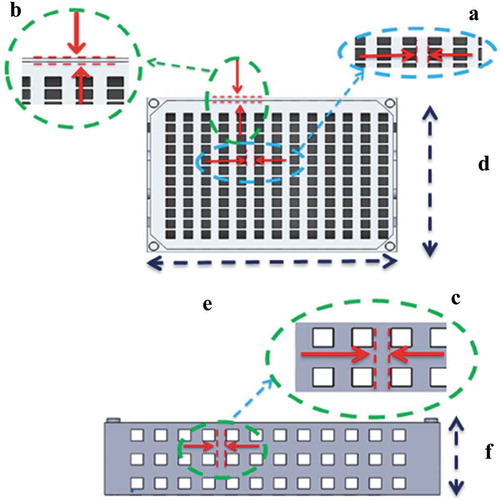
Also, the boxes were designed considering the specifications are given in (Ebrahimi, Citation1997; Lokensgard, Citation2016). The characteristics of the design parameters are shown in briefly
Table 2. Structural specifications of the designed boxes’ material.
The dimensional parameters taken into consideration in the design of the boxes were identical and the entire designed boxes had lengths, widths, and heights equal to 38, 26 and 9 cm, respectively.
Box Analysis
The entire boxes were analyzed using Ansys 18 software. The refinement type mesh featuring 96321 nodes and 47254 elements were utilized. The amount of the compressive load exerted onto the boxes was equivalent to the weight of a pear box, 200N. The entire boxes were subject to plate compression the type of loading for all boxes was as a page ().
The supporting body of the boxes subject to the compressive load was their floor part. The equivalent stress, equivalent elastic strain, total deformation, shear elastic strain, normal stress and shear stress were computed for the designed boxes. The maximum values obtained were ordered using Ansys software in Excel Spreadsheet.
Statistical Analysis
The values of the equivalent stress, equivalent elastic strain, total deformation, shear elastic strain, normal stress and shear stress of the designed boxes were sorted out in Excel. The results were analyzed by taking advantage of factorial experiments within the format of completely randomized blocks using SAS software.
Results and Discussion
The following summarizes the variance analysis of the maximum values of the equivalent stress, equivalent elastic strain, total deformation, shear elastic strain, normal stress and shear stress for box material, box thickness, holes’ type, and holes’ spacing; in addition the mutual effect rates of these factors have also been listed.
Table 3. Variance analysis of maximum equivalent stress, equivalent elastic strain, shear elastic strain, normal stress and shear stress exerted on the boxes and total deformation.
Equivalent (Von-Mises) Stress
The Interaction of Holes’ Spacing on the Types of the Box Holes
According to , the mutual effects of the holes’ spacing and the holes’ type were found statistically significant in a 1% significance level. Based on , the highest and the lowest equivalent stress values respectively were 5027Pa (for a 2.7 cm inter-hole spacing and square type of hole) and 658.67Pa (for a 2.7 cm inter-hole spacing and rectangular type of hole).
The Interaction of Holes’ Spacing on Box Edge Thickness
According to , the mutual effects of the holes’ spacing and the box edge thickness were found statistically significant in a 1% significance level. Based on , the highest and the lowest equivalent stress values respectively were 4010.4Pa (for a 2.7 cm inter-hole spacing – box edge thickness: 0.65 cm) and 658.67Pa (for a 2.4 cm inter-hole spacing – box edge thickness: 0.65 cm).
The Interaction of Types of the Box Holes on Box Edge Thickness
According to , the mutual effects of the mutual and the box edge thickness were found statistically significant in a 5% significance level. Based on , the highest and the lowest equivalent stress values respectively were 5914.7.4Pa (for a box edge thickness: 0.65 and square type of hole) and 638.8Pa (for a box edge thickness: 0.50 and rectangular type of hole).
The Effect of Box Material on Equivalent Stress
According to , the Box material was not effective on Equivalent Stress. The highest Equivalent Stress was found in the polyethylene and the lowest in the wood. However, according to the results, there is no significant difference between the three genuses for Equivalent Stress ().
Total Deformation
The Interaction of Holes’ Spacing on the Types of the Box Holes
According to , the mutual effects of the holes’ spacing and the holes’ type were found statistically significant in a 1% significance level. Based on , the highest and the lowest Total Deformation values respectively were 10.7 × 10−10 m (for a 2.1 cm inter-hole spacing and square type of hole) and 1.80 × 10−10 m (for a 2.7 cm inter-hole spacing and rectangular circle of the hole).
The Interaction of Holes’ Spacing on Box Edge Thickness
According to , the mutual effects of the holes’ spacing and the box edge thickness were found statistically significant in a 1% significance level. Based on , the highest and the lowest Total Deformation values respectively were 7.39 × 10−10 m(for a 2.7 cm inter-hole spacing – box edge thickness: 0.65 cm) and 2.4 × 10−10 m (for a 2.7-cm inter-hole spacing – box edge thickness: 0.35 cm).
The Interaction of Types of the Box Holes on Box Edge Thickness
According to , the mutual effects of the mutual and the box edge thickness were found statistically significant in a 1% significance level. Based on , the highest and the lowest Total Deformation values respectively were 1.11 × 10−9 m(for a box edge thickness: 0.65 and square type of hole) and 191 × 10−10 m(for a box edge thickness: 0.50 and circle type of hole).
The Effect of Box Material on Total Deformation
According to , the Box material was not effective on Total Deformation. The highest Total Deformation was found in the polyethylene and the lowest in the wood. However, according to the results, there is no significant difference between the three genuses for Total Deformation ().
Equivalent Elastic Strain
The Interaction of Holes’ Spacing on the Types of the Box Holes
According to , the mutual effects of the holes’ spacing and the holes’ type were found statistically significant in a 1% significance level. Based on , the highest and the lowest Equivalent Elastic Strain values respectively were 2.74 × 10−8 m/m (for a 2.7 cm inter-hole spacing and square type of hole) and3.7 × 10−9 m/m(for a 2.7 cm inter-hole spacing and circle type of hole).
The Interaction of Holes’ Spacing on Box Edge Thickness
According to , the mutual effects of the holes’ spacing and the box edge thickness were found statistically significant in a 1% significance level. Based on , the highest and the lowest Equivalent Elastic Strain values respectively were 2.24 × 10−8 m/m(for a 2.7 cm inter-hole spacing – box edge thickness: 0.65 cm) and 6.26 × 10−9 m/m(for a 2.7 cm inter-hole spacing – box edge thickness: 0.65 cm).
The Interaction of Types of the Box Holes on Box Edge Thickness
According to , the mutual effects of the mutual and the box edge thickness were found statistically significant in a 1% significance level. Based on , the highest and the lowest Equivalent Elastic Strain values respectively were 3.21 × 10−8 m/m(for a box edge thickness: 0.65 and square type of hole) and 3.49 × 10−8 m/m(for a box edge thickness: 0.65 and rectangular type of hole).
The Effect of Box Material on Equivalent Elastic Strain
According to , the Box material was not effective on Equivalent Elastic Strain. The highest Equivalent Elastic Strain was found in the polyethylene and the lowest in the lorg wood. However, according to the results, there is no significant difference between the three genuses for Equivalent Elastic Strain ().
Normal Stress
The Interaction of Holes’ Spacing on the Types of the Box Holes
According to , the mutual effects of the holes’ spacing and the holes’ type were found statistically significant in a 1% significance level. Based on , the highest and the lowest Normal Stress values respectively were 2626 Pa (for a 2.7 cm inter-hole spacing and square type of hole) and 3056.6 Pa (for a 2.7 cm inter-hole spacing and circle type of hole).
The Interaction of Holes’ Spacing on Box Edge Thickness
According to , the mutual effects of the holes’ spacing and the box edge thickness were found statistically significant in a 5% significance level. Based on , the highest and the lowest Normal Stress values respectively were 2079.3Pa (for a 2.7 cm inter-hole spacing – box edge thickness: 0.65 cm) and 565Pa (for a 2.7 cm inter-hole spacing – box edge thickness: 0.35 cm).
The Interaction of Types of the Box Holes on Box Edge Thickness
According to , the mutual effects of types of the box holes on box edge thickness were found statistically significant in a 1% significance level. Based on , the highest and the lowest Normal Stress values respectively were 2880.6Pa (for a box edge thickness: 0.65 and square type of hole) and 310.7Pa (for a box edge thickness: 0.35 and rectangular type of hole).
The Effect of Box Material on Normal Stress
According to , the Box material was not effective on Normal Stress. The highest Normal Stress was found in the polyethylene and the lowest in the wood. However, according to the results, there is no significant difference between the three genuses for Normal Stress ().
Shear Stress
The Interaction of Holes’ Spacing on the Types of the Box Holes
According to , the mutual effects of the holes’ spacing and the holes’ type were found statistically significant in a 1% significance level. Based on , the highest and the lowest Shear Stress values respectively were 2070.2Pa (for a 2.7 cm inter-hole spacing and square type of hole) and 260.58a (for a 2.7 cm inter-hole spacing and circle type of hole).
The Interaction of Holes’ Spacing on Box Edge Thickness
According to , the mutual effects of the holes’ spacing and the box edge thickness were found statistically significant in a 1% significance level. Based on , the highest and the lowest Shear Stress values respectively were 1687 Pa (for a 2.7 cm inter-hole spacing – box edge thickness: 0.65 cm) and 454.4Pa (for a 2.7 cm inter-hole spacing – box edge thickness: 0.35 cm).
The Interaction of Types of the Box Holes on Box Edge Thickness
According to , the mutual effects types of the box holes on of box edge thickness were found statistically significant in a 5% significance level. Based on , the highest and the lowest Shear Stress values respectively were 2304.8Pa (for a box edge thickness: 0.65 and square type of hole) and 225Pa (for a box edge thickness: 0.50 and rectangular type of hole).
Effect of Box Material on Shear Stress
According to , the Box material was not effective on Shear Stress. The highest Shear Stress was found in the polyethylene and the lowest in the wood. However, according to the results, there is no significant difference between the three genuses for Shear Stress ().
Shear Elastic Strain
The Interaction of Holes’ Spacing on the Types of the Box Holes
According to , the mutual effects of the holes’ spacing and the holes’ type were found statistically significant in a 1% significance level. Based on , the highest and the lowest Shear Elastic Strain values respectively were 3.6 × 10−8 m/m (for a 2.7 cm inter-hole spacing and square type of hole) and 4.63 × 10−9 m/m (for a 2.7 cm inter-hole spacing and rectangular type of hole).
The Interaction of Holes’ Spacing on Box Edge Thickness
According to the , the mutual effects of the holes’ spacing and the box edge thickness were found statistically significant in a 1% significance level. Based on , the highest and the lowest Shear Elastic Strain values respectively were 2.93 × 10−8 m/m(for a 2.7 cm inter-hole spacing – box edge thickness: 0.65 cm) and 8 × 10−8 (for a 2.7 cm inter-hole spacing – box edge thickness: 0.35 cm).
The Interaction of Types of the Box Holes on Box Edge Thickness
According to the , the mutual effects of types of the box holes on box edge thickness were found statistically significant in a 1% significance level. Based on , the highest and the lowest Shear Elastic Strain values respectively 4.17 × 10−8 m/m (for a box edge thickness: 0.65 and square type of hole) and 4.43 × 10−9 m/m(for a box edge thickness: 0.50 and rectangular type of hole).
Effect of Box Material on Shear Elastic Strain
According to , the Box material was not effective on Shear Elastic Strain. The highest Shear Elastic Strain was found in the polyethylene and the lowest in the wood. However, according to the results, there is no significant difference between the three genuses for Shear Elastic Strain ().
Conclusion
According to the obtained results:
Considering the holes’ spacing and holes’ type, the best box design was found featuring the square shape of holes and a 2.7 cm inter-hole spacing. That was because the highest equivalent stress, equivalent elastic strain, total deformation, shear elastic strain, normal stress and shear stress were obtained in this state.
Considering the holes’ spacing and box edge thickness, the best box design was found featuring a 0.65 cm edge thickness and a 2.7 cm inter-hole spacing because the highest equivalent stress, equivalent elastic strain, total deformation, shear elastic strain, normal stress and shear stress were obtained in this state.
Considering the box edge thickness and holes’ type, the best box design was found featuring square holes and a 0.65 cm edge thickness because the highest equivalent stress, equivalent elastic strain, total deformation, shear elastic strain, normal stress and shear stress were obtained in this state.
No significant difference was evidenced between the box materials but the highest values were calculated for polyethylene boxes and the lowest values were obtained for wooden boxes in terms of equivalent stress, equivalent elastic strain, total deformation, shear elastic strain, normal stress and shear stress.
Literature cited
- Albrecht, S., P. Brandstetter, T. Beck, P. Fullana-I-Palmer, K. Grönman, M. Baitz, and M. Fischer. 2013. An extended life cycle analysis of packaging systems for fruit and vegetable transport in Europe. Int. J. Life Cycle Assess. 18(8):1549–1567. doi: 10.1007/s11367-013-0590-4.
- Barkai-Golan, R. 2001. Postharvest diseases of fruits and vegetables: Development and control. Amsterdam, The Netherlands: Sara Burgerhartstraat.
- Caleb, O.J., U.L. Opara, P.V. Mahajan, M. Manley, L. Mokwena, and A.G.J. Tredoux. 2013. Effect of modified atmosphere packaging and storage temperature on volatile composition and postharvest life of minimally-processed pomegranate arils (cvs. “Acco” and “Herskawitz”). Postharvest Biol. Technol. 79:54–61. doi: 10.1016/j.postharvbio.2013.01.006.
- Djatna, T., and W.D. Kurniati. 2015. A system analysis and design for packaging design of powder shaped fresheners based on Kansei Engineering. Procedia Manuf. 4(Iess):115–123. doi: 10.1016/j.promfg.2015.11.021.
- Ebrahimi, C. 1997. Mechanical strengths wood and them Element. Tehran University.
- Han, J.W., J.P. Qian, C.J. Zhao, X.T. Yang, and B.L. Fan. 2017. Mathematical modelling of cooling efficiency of ventilated packaging: Integral performance evaluation. Int. J. Heat Mass Transf. 111:386–397. doi: 10.1016/j.ijheatmasstransfer.2017.04.015.
- Jianglian, D. 2013. Application of chitosan based coating in fruit and vegetable preservation: A review. J. Food Process. Technol. 4(5):5–8. doi: 10.4172/2157-7110.1000227.
- Jiao, J., Y. Zhang, and M. Helander. 2006. A Kansei mining system for affective design. Expert Syst. Appl. 30(4):658–673. doi: 10.1016/j.eswa.2005.07.020.
- Kregiel, D., A. Otlewska, and H. Antolak. 2014. Attachment of Asaia bogorensis originating in fruit-flavored water to packaging materials. Biomed Res. Int. 2014:514190. doi: 10.1155/2014/514190.
- Lokensgard, E. 2016. Industrial plastics: Theory and applications. Cengage Learning.
- Opara, U.L., and A. Mditshwa. 2013. African journal of agricultural research a review on the role of packaging in securing food system: Adding value to food products and reducing losses and waste. Afr. J. Agric. Res. 8(22):2621–2630. doi: 10.5897/AJAR2013.6931.
- Stanujkic, D., D. Karabasevic, and E.K. Zavadskas. 2015. A framework for the selection of a packaging design based on the SWARA method. Eng. Econ. 26(2):181–187. doi: 10.5755/j01.ee.26.2.8820.