Abstract
A series of nonionic fluorin surfactants containing poly(ethylene glycol) (PEG) and their acrylates were synthesized using PEGs of different molecular weight (Mw 600, 1000, 1500, 2000, 4600 g/mol), TDI, acryloyl chloride, and pentadecafluorooctanoic chloride as the main starting materials. Their chemical structures were characterized by means of FTIR and 1H NMR. The surface tension (γ) of the fluorine surfactants were evaluated by drop weight method. The γ value was found to increase with the length of PEG chains. The acrylates were adopted as functionalizing monomers and grafted onto linear low-density polyethylene (LLDPE) through a melt reactive extrusion procedure. The graft degrees of LLDPE were determined by FTIR. Five graft LLDPE samples with grafting degrees of 0.79% (A-I), 0.72% (A-II), 0.68% (A-III), 0.63% (A-IV), and 0.57% (A-V) were prepared. Their surface properties were characterized by measuring contact angles with water and by X-ray Photoelectron Spectroscopy (XPS). Thermal properties of graft LLDPE samples were studied using differential scanning calorimetry. Crystallization rates of graft LLDPEs were faster than that of plain LLDPE at a given crystallization temperature because graft chains could act as nucleating agents. The isothermal crystallization behavior of grafted LLDPE was in accordance with the Avrami model only in the first stage of the process, and deviated from the model by increasing the crystallization time.
Introduction
Polyethylenes (PEs) are a class of important thermoplastics, which have been widely applied owing to their excellent mechanical properties and easy processability.[Citation1–7] The surface properties of PE-based materials, such as adhesion, wettability, biocompatibility, friction behavior, and permeation to gases and vapors are largely dependent on the surface chemical composition as well as the surface structure, which could exert a profound impact on a variety of applications possible for these materials. It is therefore of primary importance to modify the surface properties of the existing PE grades via physical and chemical approaches. During the past decades, it has been reported that a variety of techniques such as the surface treatment by means of plasma, flame, chemical reactions, coating deposition, surface migration of low molecular additives from bulk.[Citation8–17] The wide-spreading applicability of the PE-based materials motivates the efforts to improve their surface properties via chemical or physical approaches.
Perfluorinated surfactants show outstanding properties such as low surface tension, chemical inertness, thermal stability, peculiar friction properties, lipophobicity, and hydrophobicity.[Citation18] Nonetheless, perfluorinated compounds are inherently incompatible with other polymers due to their high internal cohesive energies, resulting from the high electronegativity of fluorine atoms, short C–F bond, and high bond energy. The copolymerization of fluorinated and hydrogenated compounds has been demonstrated to be an efficient approach to introduce fluorine atoms into polymers. For instance, excellent surface hydrophobicity was obtained for PE using fluorinated compounds as co-monomers of ethylene even at a concentration as low as 0.5 wt.%. Dynamic contact angle measurements with water showed that the resultant polymers exhibit advancing contact angles of about 120°.[Citation19] It has been proposed that the improvement of surface hydrophobicity is due to the surface enrichment in perfluoropolyether chains, which are very flexible, highly apolar, contemporary hydro- and oleophobic, and without any crystallization tendency.[Citation20] Alternatively, the fluorinated segments can be incorporated into existing polymers via reactive processing.
In this work, we reported the modification of a linear low-density polyethylene (LLDPE) with fluorinated compounds via reactive extrusion. Toward this end, a series of new semi-fluorinated acrylic monomers (see Figure ), bearing poly(ethylene glycol) (PEG) sequences of various length were firstly synthesized and characterized. Thereafter, these fluorine-containing monomers were grafted onto LLDPE chains via reactive extrusion by means of a pilot-scale twin-screw extruder. It is expected that the fluorinated acrylic monomers grafted onto LLDPE are long enough to exert an effective antifog action in marked contrast to traditional PE-based materials obtained via physical blending with low molecular weight fluorine compounds.
Experimental
Materials
Toluene 2,4-diisocyanate (TDI), chloroform, poly(ethylene glycol) (PEG) grades (Mw = 600, 1000, 1500, 2000, 4600 g/mol), magnesium sulfate, pentadecafluorooctanoic chloride, n-heptane, acryloyl chloride were purchased from Aldrich Co., USA. Triethylamine (TEA) was purchased from Fluka. Linear low density polyethylene (LLDPE) (LLDPE-7042), with a quoted melting flow rate of 2.0 g/10 min, was kindly provided by Daqing Petrochemical Co., China. Before use, PEGs were dried via the azeotropic distillation with anhydrous toluene to remove the moisture.
Synthesis of monomers
Typically, PEG (Mw = 600) (0.11 mol) was dropped into a mixture of 0.05 mol TDI and 60 mL chloroform under nitrogen atmosphere at room temperature; the reaction was carried out by stirring for 1 h and then further chloroform (150 mL) was added. The resulting mixture was washed with 30 mL water thrice. All the organic phase were combined and remove the solvent. Then the product was washed with 30 mL water and 60 mL normal hexane thrice and dried with anhydrous MgSO4. After distilling off normal hexane, the intermediate product I(600) was obtained with the yield of 73%. The abovementioned reaction was traced by infrared spectroscopy and the degree of purity of the product was detected by GPC (or HPLC). FTIR I(600) (ν, cm−1): 3473 (OH), 3297 (NH2), 1725 (C=O), 1599, 1550, 1459 (Ph-H), 1599 (C=C), 1455 (CH2), 1103 (C–O). 1H NMR I(600) (δ, ppm): 10.85 (NH), 6.74–7.80 (Ph-H), 4.29–4.33 (O=C–OCH2–), 3.59–3.67 (OCH2CH2O), 2.20 (OH), 1.99 (CH3-Ph).
Pentadecafluorooctanoic chloride (0.081 mol) was slowly added into a mixture of 0.081 mol intermediate product I(600) and 30 mL CHCl3. After 1 h, acryloyl chloride (0.081 mol) was added into the same reaction vessel and the mixture was kept at 50 °C for 2 h. The mixture was then extracted by mixed solvent (CHCl3:H2O = 3:1) thrice. The organic extracts were combined, dried with MgSO4, and filtrated. After distilling off chloroform, product III(600) bearing the reactive acrylic double bond was obtained. The reaction proceeding was followed by FTIR.
All the reactive acrylic monomers III were prepared by the same method as the product III(600).
Preparation of grafting copolymers
The grafting reaction onto LLDPE was carried out in a homemade co-rotating twin-screw extruder. The diameter of the screws was 30 mm and the ratio of length to diameter (L/D) was 40. More specifically, L/D was 24 for the reactive zone and 16 for the melting zone. The maximum screw torque was 2 × 147 N•M. LLDPE pre-irradiated by 60Co and each prepared monomer III were premixed and added into the extruder through the feeder. The processing temperature in this test was set at about 170 °C, and the recorded fluctuation of temperature was within ± 2 °C. The grafted LLDPE samples were pelletized after extrusion.
Approximately 4 g of each grafted LLDPE (LLDPE-g-III) sample was dissolved into 120 mL of boiling xylene. The thus-formed solution was then filtered and poured into 500 mL of acetone under stirring. The precipitate was filtered, washed with acetone, and dried in a vacuum oven at 60 °C for one week.
Fourier transform infrared spectroscopy (FTIR)
A BIO-RAD FTS-135 IR spectrometer was used for the FTIR measurements. The resolution was 4 cm−1 and the number of scans was 16. FTIR spectroscopy was used to demonstrate the formation of the intermediate products I-III and the occurrence of the grafting reaction as well as to determine the grafting degrees of LLDPE. To this purpose, the LLDPE-g-III samples were compression-molded at 170 °C into thin films.
Nuclear magnetic resonance spectroscopy (1H NMR)
The 1H NMR measurements were carried out on a Bruker AV 400 MHz NMR spectrometer at room temperature. The samples were dissolved in deuterobenzene and tetramethylsilane (TMS) was used as the internal reference.
Measurements of surface tension and contact angles
The surface tension of the LLDPE-g-III copolymers was measured by drop weight method at 20 °C. Water contact angles were determined on compression-molded film specimens obtained from purified copolymers. By means of a microscrew-driven syringe, 5-10 μL of distilled water was added onto the film surface. The used apparatus was a JY-82 model made by Chengde Test Machine Co. Ltd, China.
X-ray photoelectron spectroscopy analysis (XPS)
The chemical composition of film surfaces was analyzed and the oxygen content on the surface of grafted LLDPE films was determined by XPS, using a VG ESCALAB MKII instrument with Mg Kα X-ray source (1253.6 eV).
Determination of thermal properties of grafted LLDPE (DSC)
The thermal properties of the graft LLDPE copolymers were investigated by differential scanning calorimetry using a Perkin-Elmer DSC-7 instrument. The samples (8–10 mg) were sealed in aluminum crucibles. They were first heated from room temperature up to 150 °C, kept at this temperature for 2 min to erase any previous thermal history, then cooled down to ambient temperature, and reheated up to 150 °C. Temperature scan rates in all cases were 10 °C/min.
Results and discussion
Synthesis of polymerizable fluorine surfactants
In Figure , the FTIR spectra of I(600) sample, recorded at different reaction times, are shown. The stretching vibration of –NCO groups of TDI was detected at ca. 2266 cm−1. The evolution of the PEG addition can be traced by following the change of the –NCO band in intensity as a function of time. It was seen that, with the occurrence of the reaction, the abovementioned band practically disappeared while the features of the stretching vibration band of the pendant hydroxyl groups (−OH) in the range 3530–3250 cm−1 changed and contemporary a new band appeared at 1729 cm−1, which is assignable to the stretching vibration of the carbonyl double bond in the carbamate structure (–NH–COO–) of urethane being formed.
The intermediate products I containing PEG, chains of different molecular weight such as I(1000), I(1500), I(2000), and I(4600) were prepared by the same method to I(600). Obviously, their infrared spectra were similar because of their homologous chemical structures. But the reaction rate became slow with the increase of the molecular weight of PEG chains involved in the reaction.
The intermediate product II were obtained through the reactions between products I and pentadecafluorooctanoic chloride. The reaction extent was estimated according to the disappearance of the peak at 924 cm−1 due to the C–Cl band of pentadecafluorooctanoic chloride and the formation of a new carbonyl peak at 1802 cm−1.
After purifying the intermediate II, the fluorine surfactants containing a reactive α-double bond were synthesized by reacting acryloyl chloride and the intermediate II. The reaction course was monitored recording to disappearance of the peak of C–Cl band (971 cm−1) (Figure should become Figure ). The purity of the products was detected by GPC(THF).
Surface tension of the fluorine surfactants
Shown in Figure is the plot of surface tension as a function of the PEG length of the fluorine surfactants III. It is shown that the effectiveness of the nonionic surfactant decreased with increasing the amount of ethylene oxide units in PEG for PEG nonionic surfactants containing the same lipophilic group. In other words, the effectiveness of the nonionic surfactant decreased obviously with an increase of the chain length of PEG.
Grafting reaction of fluorine surfactants onto LLDPE
Hydroperoxide and diperoxide groups appeared on the molecular chains of LLDPE after it was pre-irradiated by γ-rays in the presence of oxygen. The peroxidation mechanism was summarized in another paper.[Citation21] The formation of LLDPE graft copolymers has been confirmed by FTIR. Absorption peaks at 1740 and 2020 cm−1 were characteristic of C=O ester bond in monomers and –CH2– in LLDPE backbone, respectively. FTIR spectra of a series of LLDPE mixtures with different amount of grafted monomer were carried out and the plot of grafted monomer content in the mixture vs. the ratio of A1740 to A2020 was employed as the calibration curve (not shown). Ratios of A1740 to A2020 in the spectra of purified graft products were used to estimate grafting degrees of the resultant graft copolymers, which was 0.79, 0.72, 0.68, 0.63, and 0.57%, respectively.
Thermal, polarity, and rheological properties of grafted LLDPE
The crystallization behavior of polymers under isothermal conditions can be analyzed by means of Avrami equation. By plotting log [−ln(1 − Xt) against log t, it is possible to determine the value of the Avrami exponent (n) from the slope of the curve. As an example, the Avrami plots of the graft copolymer LLDPE-g-III (1500) obtained at different temperatures are shown in Figure . A similar trend was found for the other graft copolymers, obtained using PEGs with different length. It is evident that the plots are in accordance with the Avrami model only in the first stage of the crystallization process and deviate from the model at longer times; The Avrami exponents are summarized in Table and values of n were in the range from 2.4 to 3.8, this suggests that the crystallization (nucleating and growing) for all the above mentioned materials should occur in the three dimensions. Values of n for the graft copolymers are higher than those of neat LLDPE, this seems to indicate that the effect of grafted branch chains on nucleation and growth of functionalized LLDPE crystals increases with increasing the length of PEG sequences in the grafted chains.
Table 1. Isothermal crystallization temperature Tc, melting temperature Tm, Avrami exponent n, kinetic constant K and time for crystallization to the half of the total crystallinity t1/2 of LLDPE and grafted LLDPE.
As shown in Figure , values of crystallization half-time (t1/2) for the graft LLDPE samples were lower than that of the plain LLDPE determined at the same crystallization temperatures. It means that the crystallization rates of LLDPE-g-III copolymers were higher than that of plain LLDPE; moreover, they increased with the length of the grafted PEG chains. This behavior could be explained taking into account that the grafted chains containing PEG sequences play the role of nucleating agents, thus accelerating the crystallization process. This conclusion was also confirmed by results obtained in non-isothermal crystallization tests. As shown in Figure , DSC cooling curves of grafted LLDPE samples exhibit a crystallization exotherm whose peak is located at higher temperature with respect to the plain LLDPE and the higher is the length of PEG sequences, the more the crystallization peak is shifted towards higher temperature. The graft chains consisting of PEG and pentadecafluorooctanoic group were not compatible with LLDPE. Higher crystallization rates of the grafted LLDPE came from the poor compatibility of the grafting chains which acted as nucleating agents (Table ).
Figure 7. Half-time, t1/2, for crystallization of neat and graft LLDPE as a function of crystallization temperature, Tc.
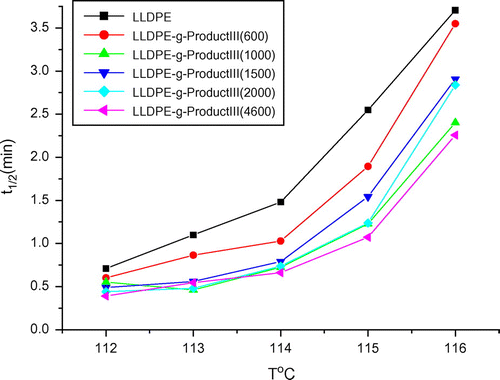
Shown in Figure are the XPS results of the LLDPE-g-III copolymers containing PEG chains with different molecular weights. The oxygen content varied with the length of PEG. In particular, the oxygen content increased with an increase of the PEG chain length when the PEG molecular weight was below 1500. However, the oxygen content decreased with an increase of the PEG chain length when the PEG molecular weight was above 1500. This finding could be due to the difficulty for PEG chains to stretch on the material surface when, because of high molecular weight, PEG is crystalline. The pentadecafluorooctanoyl group could not act as a compatilizer because it is at the same time hydrophobic and lipophobic. Thus, the poor compatibility of the graft chains with LLDPE and the crystallization behavior of long PEG chains is both not advantageous to migration of the grafted macro-monomers to the surface.
Shown in Figure are the water contact angle values measured on the surface of compression-molded films of the graft LLDPE copolymers. As compared with pure LLDPE, decreases in the advancing and receding angles for graft copolymers were observed. As for the graft copolymers containing different length chains, the contact angle of the LLDPE-g-III(1500) sample is the lowest and that of LLDPE-g-III(600) copolymer is the highest. This trend is in line with the results already observed for the XPS measurements.
Conclusions
A series of fluorine surfactants and their acrylates was successfully obtained from PEG and pentadecafluorooctanoic chloride as starting materials. The activity of the prepared fluorine surfactants containing hydrophilic groups and perfluorinated moieties, which are either hydrophobic or lipophobic, increased when increasing the length of PEG chains. A series of graft copolymers of LLDPE was obtained by a melt reactive extrusion procedure. The crystallization rates of graft copolymers were higher with respect to the plain LLDPE samples. Also, the crystallization rates of graft copolymers increased with the length of PEG sequences. The grafted chains played the role of nucleating agents that could accelerate the crystallization process. The wettability of the copolymers increased although the graft chains contained perfluorinated groups, but it reduced when the molecular weight of PEG was more than 1500 g/mol. The results of XPS analysis was in accordance with the contact angle measurements.
Funding
We acknowledge the financial support of National Natural Science Foundation of China [grant number 50873084]; the Shandong Natural Science Foundation of China [grant number ZR2010BM029].
References
- Yamashita S, Kodama K, Ikeda Y, Kohjiya S. Chemical modification of Butyl Rubber. I. Synthesis and properties of poly (ethylene oxide) -crafted Butyl Rubber. J. Polym. Sci. Polym. Chem. 1993;31:2437–2444.10.1002/pola.1993.080311003
- Berlinnova IV, Amzil A, Panayotov IM. Synthesis and some properties of graft copolymers with uniform polyoxyethylene side chains. J M S Pure Appl. Chem. 1992;A29:975–986.
- Xie HQ, Liu Y. Synthesis, characterization, and propertiesof amphiphilic poly(ethyl acrylate) with uniform polyoxyethylene grafts. J. Appl. Polym. Sci. 2001;80:903–912.10.1002/(ISSN)1097-4628
- Bergbreiter DE. Polyethylene surface chemistry. Prog. Polym. Sci. 1994;19:529–560.10.1016/0079-6700(94)90004-3
- Ohmichi T, Tamaki H, Kawasaki H, Tatsuta S. Phyicochemical aspects of polymer surfaces. In: Mittal KL, editor. Plenum Press: New York; 1983. p. 793.
- Bergbreiter DE, Srinivas B. Surface selectivity in blending polyethylene-poly(ethy1ene glycol) block cooligomers into high-density polyethylene. Macromolecules. 1992;25:636–643.10.1021/ma00028a024
- Bergbreiter DE, Chen Z, Hu HP. Entrapment of functionalized ethylene oligomers in polyethylene. Macromolecules. 1984;17:2111–2116.10.1021/ma00140a041
- Nava-Ortiz CAB, Burillo G, Bucio E, Alvarez-Lorenzo C. Modification of polyethylene films by radiation grafting of glycidyl methacrylate and immobilization of b-cyclodextrin. Radiat. Phys. Chem. 2009;78:19–24.10.1016/j.radphyschem.2008.07.005
- Akovali Güneri. Plasma surface modification of polyethylene with organosilicon and organotin monomers. Eur. Polym. J. 1996;32:375–383. http://www.sciencedirect.com/science/article/pii/0014305795000690
- Richey T, Iwata H, Oowaki H, Uchida E, Matsuda S, Ikada Y. Surface modification of polyethylene balloon catheters for local drug delivery. Biomaterials. 2000;21:1057–1065.10.1016/S0142-9612(99)00281-1
- Zhao G, Chen Y, Wang X. Surface modification of polyethylenefilm by acrylamide graft and alcoholysis for improvement of antithrombogenicity. Appl. Surf. Sci. 2007;253:4709–4714.10.1016/j.apsusc.2006.10.036
- Bongiovanni R, Di Gianni A, Priola A, Pollicino A. Surface modification of polyethylene for improving the adhesion of a highly fluorinated UV-cured coating. Eur. Polym. J. 2007;43:3787–3794.10.1016/j.eurpolymj.2007.06.037
- Zhao J, Geskens G. Surface treatment of polymers VI. Thermal and radiochemical grafting of acrylamide on polyethylene and polystyrene. Eur. Polym. J. 1999;35:2115–2123.10.1016/S0014-3057(99)00026-9
- Rajput AB, Rahaman SJ, Sarkhel G, Ghosh NN. Preparation and characterization of flexible polybenzoxazine -LLDPE composites. Des. Monomers and Polym. 2013;16:177–184.
- Fresnais J, Chapel JP, Benyahia L, Poncin-Epaillard F. Plasma-treated superhydrophobic polyethylene surfaces: fabrication, wetting and dewetting properties. J. Adhesion Sci. Tech. 2009;23:447–467.
- Li WF, Yao ZH, Yao RX, Liu SM. Polyethylene grafted polyether pentaerythritol mono-maleate to improve wettability of liquid on polyethylene films polym-plast. Polym-Plast. Tech. Eng. 2013;52:603–606.
- Li WF, Yao ZH, Jiang GW, Zheng XQ, Li LX, Yin JH. Preparation, characterization, and properties of pre-irradiated linear low density polyethylene grafted itaconic anhydride by reactive extrusion. J. Macromol. Sci. Part B. 2010;49:75–85.
- Bongiovanni R, Malucelli G, Lombardi V, Priola A, Siracusa V, Tonelli C, Di Meo A. Surface properties of methacrylic copolymers containing a perfluoropolyether structure. Polymer. 2001;42:2299–2305.10.1016/S0032-3861(00)00557-7
- Bongiovanni R, Malucelli G, Pollicino A, Tonelli C, Simeone G, Priola A. Perfluoropolyether structures as surface modifying agents of UV-curable system. Macromol Chem. Phys. 1998;199:1099–1105.10.1002/(ISSN)1521-3935
- Priola A, Bongiovanni R, Malucelli G, Pollicino A, Tonelli C, Simeone G. UV-curable systems containing perfluoropolyether structures: synthesis and characterisation. Macromol. Chem. Phys. 1997;198:1893–1907. http://onlinelibrary.wiley.com/doi/10.1002/macp.1997.021980618/abstract.
- Xin Z, Ding Y, Yin J, Ke Z, Xu X, Gao Y, Costa G. Preparation and physical properties of novel nonionic surfacants and their grafting copolymers with LLDPE. J. Polym. Sci. 2005;43:314–322.10.1002/(ISSN)1099-0488