Abstract
Nanofiltration (NF) is a membrane-based separation process having significant potential for the treatment of industrial effluents to enable water reuse. It has the ability to remove low molecular weight trace contaminants from water, which cannot be separated by conventional treatment methods. In the present investigation, a thin film composite polyamide membrane was synthesized by interfacial polymerization technique and evaluated for the treatment of biscuit industrial effluent. The synthesized membrane was characterized using Fourier transform infrared spectroscopy, X-ray diffraction, thermogravimetric analysis, and scanning electron microscopy to elucidate structure and intermolecular interactions, crystallinity, thermal stability and cross-sectional morphology, respectively. The influence of operating parameters such as feed pressure 0–21 kg/cm2 and total dissolved solids (TDS) of 3160 ppm on water flux and impurity rejection was determined. An average flux of 11.63 L/m2 h was obtained at a constant pressure of 21 kg/cm2. The TDS, chemical oxygen demand (COD), and biochemical oxygen demand (BOD) rejections were found to be 53.62, 80, and 74%, respectively, at a water recovery of 65%. A statistical mechanical model was used to validate the experimental data. Based on this study, a detailed economic estimation for processing biscuit effluent of 1 m3/h feed capacity using commercial NF system is presented. The study revealed that the synthesized NF membrane could be an effective alternative for the treatment of various industrial effluents as well as to reduce the load on reverse osmosis process for desalination of seawater and effluent treatment through high degree of COD and BOD separation.
1. Introduction
Nanofiltration (NF) is a pressure-driven membrane process which basically separates molecules large enough to avoid reverse osmosis (RO), but easily pass through ultrafiltration membranes.[Citation1,2] In addition, NF membranes provide high rejection of organic molecules or multivalent ions having molecular weights ranging from 150 to 1000 with a relatively high water flux, but lower operating pressure compared to RO.[Citation3,4] These characteristics led to a growing list of applications for NF at industrial sectors especially in water softening,[Citation5,6] purification of drinking water,[Citation7,8] wastewater treatment and reclamation, [Citation9,10] solvent recovery, [Citation11,12] etc.
Thin film composite (TFC) polyamide membranes are currently the main class of NF membranes available in the market. They are deposited on top of an ultraporous support as a thin layer by interfacial polymerization [Citation13,14] which is based on a polycondensation reaction between two monomers, a polyfunctional amine such as piperazine (PIP) or m-phenylenediamine and a polyfunctional acid chloride such as trimesoyl chloride (TMC).[Citation15] The monomers are dissolved in mutually immiscible solvents such as water and hexane. The aqueous amine solution initially impregnates the ultraporous support from which excess water is drained off before immersion in hexane medium containing the acid chloride monomer thus enabling the formation of a polyamide TFC layer at the hexane–water interface, which is subsequently cross-linked by heating.[Citation16] Practically, the polymerization reaction stops when the interfacial polyamide film prevents any further diffusion of amine molecules into the organic phase.[Citation17,18]
In the synthesis of NF membrane, several factors such as nature and concentration of monomer,[Citation19,20] solvent type,[Citation21,22] cross-linking agent, [Citation23] and phase-transfer catalyst [Citation24] can influence the structure and property of the polyamide layer. For instance, a highly hydrophilic NF membrane for desalination and water treatment was developed by Ahmad et al., [Citation25] through interfacial polymerization using TMC, PIP, and 3,5-diaminobenzoic acid. Authors noticed that pure water permeability could be improved by as much as 20% through addition of 3,5-diaminobenzoic acid into the PIP aqueous phase. The membrane thus obtained was negatively charged and exhibited excellent rejection property with respect to divalent ions. Chiang et al., [Citation26] prepared novel NF membranes through interfacial polymerization of hyperbranched polyethyleneimine (PEI) with TMC or terephthaloyl chloride on a polyacrylonitrile ultraporous substrate. They found that charged NF membranes with enhanced permselectivity for desalination could be obtained by employing this water soluble grade of hyper branched PEI. Abu Seman et al., [Citation27,28] focused their attention on developing TFC polyester NF membranes with improved antifouling properties using bisphenol and TMC as aqueous and organic phase monomers, respectively.
In response to the challenge of developing new membrane materials, TFC polyamide NF membrane was synthesized in this study for the removal of inorganic and organic pollutants from biscuit industrial effluent. The indigenous membrane was characterized by Fourier transform infrared spectroscopy (FTIR), X-ray diffraction (XRD), thermogravimetric analysis (TGA), and scanning electron microscopy (SEM) to study the structure, crystallinity, thermal stability, surface, and cross-sectional morphologies, respectively. The effect of various operating parameters such as feed pressure and total dissolved solids (TDS) concentration on water flux and % impurity rejection was evaluated. The influence of TDS, conductivity, turbidity, chemical oxygen demand (COD), and biochemical oxygen demand (BOD) on membrane performance was determined. The obtained experimental results were validated using statistical mechanical model through computer programs written in MATLAB 7.0 software. A detailed economic estimation of a commercial NF system for processing 1 m3/h of biscuit industrial effluent is also presented.
2. Experimental
2.1. Materials and methods
Polyethersulfone (PES) of average molecular weight 20,800, PIP, and TMC was purchased from Sigma-Aldrich, Mumbai, India. The biscuit industrial effluent was obtained from Delta Foods Pvt. Ltd, IDA, Jeedimetla, Hyderabad, India, and its detailed characteristics are depicted in Table . N,N-dimethylformamide (DMF), hexane, propionic acid, chemicals required for estimating COD and BOD values of the samples [Citation29] besides cleaning/storage of the membranes were procured from SD Fine Chemicals, Mumbai, India. Instruments such as a BOD incubator (RCI-S.NO-313, India), COD analyzer (DRB 200 COD Reactor, Germany), Colorimeter (Hach-DR-890, Bangalore, India), Conductivity (DCM-900), and pH meters (DPH-504) were purchased from Global Electronics, Hyderabad, India, for detailed analysis of feed, permeate, and reject samples.
Table 1. Characteristics of feed permeate and reject streams of biscuit industrial effluent treated by NF.
2.1.1. Synthesis of TFC polyamide membrane
PES solution was prepared by dissolving 15 g of polymer in 85 mL of DMF solvent containing 3% propionic acid as pore former. The bubble-free solution was then cast to the desired thickness on a nonwoven polyester fabric support affixed onto a clean glass plate using doctor’s blade followed by immersion in ice-cold water bath to obtain ultraporous PES substrate. The substrate was then soaked in 0.5% PIP aqueous solution for 1 min and then dip coated in hexane bath containing 0.1% TMC for 30 s. The membrane was then thermal cross-linked at 110 °C for 10 min to obtain TFC polyamide membrane as shown in Figure .[Citation29] The schematic representation of TFC polyamide membrane with a total thickness of 137 μm is shown in Figure .
2.2. Membrane characterization
The synthesized membrane was characterized for the presence of various functional groups and intermolecular interactions by scanning in the IR spectrum range of 400–4000 cm−1 wavenumber using Nicolet-740, Perkin-Elmer-283B FTIR spectrophotometer (Boston, MA, USA) by KBr pellet method. A Siemens D 5000 powder X-ray diffractometer (NZ, USA) fitted with a CuK-alpha source to generate X-rays of 1.54 Å wavelengths (λ) was used to assess the solid-state morphology of the membrane. The angle of diffraction (2θ) was varied from 2° to 60° to determine the d-spacing (d) that represents the extent of inter-segmental spacing between atomic layers of the polymeric membrane.[Citation30] The variable d values can be calculated using the following relationship proposed by Braggs:(1)
Crystalline nature can be established by the presence of sharp peaks associated with lower d-spacing that allows selective permeation through the membrane thereby improving the selectivity while amorphous nature is associated with broad peaks and large inter-segmental spacing that makes the membrane more open, resulting in high flux.
Thermal stability of the membrane was examined using a Seiko 220TG/DTA analyzer, Japan, in the temperature range of 25–800 °C at a heating rate of 10 °C/min with continuous flushing of pure N2 gas flowing at 200 mL/min, to determine thermal stability and decomposition characteristics. The surface and cross-sectional morphology of the membrane was studied by SEM instrument (Model JEOL JSM-6380, LA, USA). In preparing the specimens, the fracture surface and cross section of the active polyamide membrane layer, ultraporous PES substrate, and nonwoven polyester fabric support were obtained by cutting the membrane in liquid nitrogen to ensure smooth morphology.
2.3. Description of NF system
Figure is a schematic representation of the NF pilot plant used in the studies. A feed tank of 30 L capacity made of stainless steel 3l6 was provided for storage and supply of industrial effluent to the membrane system. A polypropylene (PP) prefilter cartridge of 5 μm pore size was installed upstream of the flat sheet membrane module to prevent the entry of suspended solid particles. A high-pressure pump (Hironisha, Japan) capable of maintaining a pressure up to 25 kg/cm2 was installed for transporting the feed liquid throughout the system. The pump was run by a 2 HP single phase motor (Crompton, India). The feed tank had a provision for recycling of the concentrate after it passed through a heat exchanger that was installed for maintaining a constant feed temperature (27 ± 1 °C). The heat exchanger consisted of a lengthy glass shell, which was circulated with ice-cooled water while the effluent flowed in the tube side of concentric glass coils placed inside the shell, which provided a large heat transfer area. The reject coming out of the heat exchanger was then recycled to the feed tank as concentrate. A restricting needle valve was provided in the concentrate outlet line at an appropriate position after the membrane module to pressurize the feed to a desired value as indicated by a pressure gauge installed upstream of the needle valve in the reject line. Permeate and concentrate flow rates were measured using calibrated rotameters.
2.4. Experimental procedure
NF membrane of effective area 0.015 m2 was fixed in the indigenously fabricated flat sheet test cell unit. Initially, the experiments were carried out using deionized water to study the effect of feed pressure on pure water flux. Deionized water was allowed to pass through the membrane module using the high-pressure pump. In order to maintain constant feed concentration, the concentrate line was allowed to flow into the drain instead of recycling it to the feed tank. The system was pressurized by throttling the needle valve installed in the concentrate line. The flow rates of permeate and concentrate were recorded at regular intervals of time at each pressure using rotameters.
Biscuit effluent of 30 L capacity was introduced into the feed tank and the pump was run to displace the distilled water accumulated in the system as dead volume. Initial feed sample was collected for analysis. Experiments were carried out to study the effect of feed concentration on flux and % rejection by varying the pressure from 3 to 21 kg/cm2. This time the concentrate or reject was recycled until 65% water recovery was achieved. Permeate flow rate was measured at predetermined time intervals to observe any decline in flux. After attaining the stipulated water recovery, the samples of initial feed, final concentrate, and average permeate were analyzed to determine TDS, COD, conductivity, BOD, and turbidity values. Finally, the system was washed using cleaning chemicals such as citric acid, NaOH, EDTA chelating reagent, and sodium lauryl sulfate to remove metal precipitates, mineral, and organic scales and to polish the membrane surface as per the cleaning protocols desired in the authors’ earlier publication.[Citation29]
3. Results and discussion
3.1. Membrane characterization
3.1.1. Fourier transform infrared spectroscopy
Figure represents the FTIR spectra of NF composite membrane prepared by interfacial polymerization on a PES substrate. The peak observed at 1781.45 cm−1 represents the carbonyl group (–C=O), whereas the bands at 1661 (amide I) and 1577.73 cm−1 (amide-II) are attributed to bending and stretching vibrations of –NH amide group, respectively.[Citation31,32] The peak at 2588.90 cm−1 represents –CH2 stretching vibration, whereas the small peaks at 3486.12 cm−1 correspond to stretching –NH vibrations of primary and secondary amines associated with terminal amine groups. The absorption bands at 2263.13 and 2219.05 cm−1 are a consequence of vibrations of nitrile group of amide. The characteristic peaks over the wave number range of 1507.73–1408.28, 1295.36, 1241.68, and 1162.74–1010.92 cm−1 are assigned to C–C aromatic, O=S=O (symmetric), C–O–C and O=S=O (asymmetric) stretching vibrations of PES part of the composite, respectively.[Citation33] The peaks observed at 3622.07 and 3549.11 cm−1 are formed due to stretching vibration of –OH group.
3.1.2. XRD analysis
XRD studies not only indicate the nature of the polymer but can also help to identify the inter-segmental spacing between the molecular chains. It is a well-known fact that the d-spacing gives an indication of the existence of empty space or free volume in the polymer matrix. The X-ray diffractogram of synthesized NF membrane revealed semi-crystalline nature (Figure ). This is based on the observation of sharp peaks at 38° and 45° of 2θ scale which corresponded to d-spacing values of 2.34 and 2.02 Å. The presence of broad peaks at around 9° to 28° of 2θ scale implies amorphous nature of the polymer.
3.1.3. TGA studies
The TGA curve of NF membrane is shown in Figure . The thermal stability and degradation behavior of the sample was evaluated under an inert N2 atmosphere. TGA curve of the membrane showed a gradual weight reduction up to 250 °C owing to loss of water molecules bound to the matrix besides volatile organic compounds. Later the membrane exhibited a rapid weight loss from 420 to 480 °C, which may be attributed to the decomposition of amide bonds and disintegration of the polymer chains.
3.1.4. SEM analysis
Figure reveals the surface and cross-sectional images of NF membrane. The surface image revealed morphology in nanoporous range with the pores being distributed unevenly (Figure (a)). The cross-sectional view of the membrane shows the formation of three different layers, in which the top layer represents nanoporous polyamide layer, middle layer corresponds to ultraporous PES layer, whereas the lower layer represents the nonwoven polyester fabric support with adequate penetration of the intermediate PES layer (Figure (b)). Neither any agglomerations nor cluster formations were observed in the multilayered polymer materials.
3.2. Effect of pressure on flux and % rejection
The effect of pressure on flux and % rejection of NF membrane for pure water and biscuit industrial effluent is shown in Figure . As expected, a rise in pressure caused an enhancement in both flux and % rejection. When the driving force of the process increases, it results in enhancement of flux due to increased affinity between H2O molecules and –CONH moiety of polyamide layer from hydrogen bonding and dipole–dipole interactions. On the other hand, the flux of solute molecules remains more or less the same owing to the absence of any interaction with the membrane. Hence, increasing water concentration in permeate would consequently enhance % rejection. The flux was low (~2.56 L/m2 h) at applied pressure less than 3 kg/cm2, due to high osmotic pressure arising from substantial concentration of dissolved solids in the effluent feed. An increase in the flux value from 5.63 to 11.76 L/m2 h was observed in pressure was raised from 5 to 7 kg/cm2. At higher pressures, a gradual enhancement in flux was noticed which may be attributed to solution–diffusion mechanism. A maximum flux with 53% rejection of solids and 65% water recover was achieved at an operating pressure of 21 kg/cm2. Rejection of COD was as high as 80% and BOD nearly 74%. It can be concluded that the membrane exhibited improved performance at higher pressures.
3.3. Effect of operating time on flux and % rejection
Effect of time on flux and % rejection at a constant pressure of 21 kg/cm2 is graphically illustrated in Figure . Flux and rejection gradually declined to values of 3.76 L/m2 h and 4.84%, respectively, over a period of 85 min, which could be restored by following membrane cleaning procedures.[Citation29] The reduction in flux and rejection of impurities is attributed to increasing concentration polarization near the membrane surface arising from continuous retention of inorganic and organic solutes, which also enhances osmotic pressure which opposes the driving force of externally applied feed pressure.
3.4. Separation of TDS, conductivity, turbidity, COD, and BOD
Table depicts the TDS, conductivity, turbidity, COD, and BOD values of feed, average permeate, and final reject in NF process. A water recovery of 65% was obtained at a reasonable average flux of 20.15 L/m2 h. From the observations, it can be concluded that the membrane significantly reduced TDS, conductivity, turbidity, COD, and BOD rejections of 80 and 74%, respectively, present in the effluent. Analysis of permeate as per APHA standard methods [Citation34] indicated that permeate could be recycled for utilization in agricultural activities or industrial cooling towers if not safely disposed as per Pollution Control Board strictures. NF could also serve as a pretreatment to RO to achieve permeate water of high quality and reduce TDS/COD load on RO process to ensure maximum membrane life.
3.5. Model validation for NF
As described elsewhere,[Citation29] a statistical mechanical model for NF system was validated using experimental data generated from laboratory. In this process, the experiments were carried out by recycling the entire reject stream back to the feed tank. During the time of operation, the concentration of dissolved solids in the feed tank was continuously enhanced due to their rejection by the NF membrane. Figure exhibits a comparison of theoretically predicted results with experimental values with respect to parameters such as reject stream composition, % solute rejection, and water flux. It can be seen that experimental and simulated results were in good agreement with a small deviation of <5%. The obtained regression coefficients were found to be C1 = 6.83E-08, C2 = 0.56, D1 = −1.714E-18, and D2 = 9.27E-18.
Figure 10. Effect of feed concentration on flux and % rejection of composite NF membrane at 21 kg/cm2.
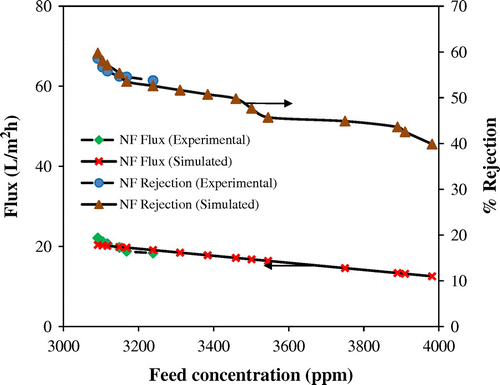
The developed model could also be useful in designing pilot or commercial plants for processing various industrial effluents by NF technique.
3.6. Scale-up and economic estimation
3.6.1. Capital investment and list of equipment for NF process
List of equipment and capital costs are provided in Table , in which the unit price for the high-pressure centrifugal pump (Grundfos, Denmark), TFC polyamide NF membrane modules with pressure vessels, and skid costs are included. The total capital investment for processing 1 m3/h of biscuit effluent is approximately 4387 USD (INR 2.80 Lacs).
Table 2. Capital investment for commercial NF system capable of processing 1 m3/h of biscuit industrial effluent.
3.6.2. Operation and maintenance cost
Operation and maintenance costs of the NF system are provided in Table , which includes membrane and prefilter cartridge replacement costs, electric power consumption besides chemicals for cleaning and storage of the membranes. Feed capacity and recovery were assumed to be 1 m3/h and 65%, respectively. The operating duration was assumed to be 18 h per day and duration of membrane module replacement as 3 years. Depreciation and interest on capital were taken as 10% each of total capital investment. The cost per liter of permeate produced was found to be Rs. 0.0942 (1.42 × 10−3 USD) with a payback period of 0.66 years.
Table 3. Operation and maintenance cost of NF system for processing 1 m3/h biscuit industrial effluent.
4. Conclusions
The study revealed that indigenously synthesized TFC polyamide NF membrane can be effectively used for the treatment of biscuit industrial effluent. The cross-sectional morphology of the membrane showed the presence of active polyamide layer with thickness of <2 μm. Moreover, the composite membrane exhibited significant thermal stability. The flux and % rejection with respect to the effluent was evaluated under various operating conditions. Moderate flux of 22.1 L/m2 h was obtained with a salt rejection of 53.6% at a constant pressure of 21 kg/cm2. The membrane effectively reduced TDS, turbidity, COD, and BOD from the effluent to a considerable extent. COD and BOD rejection were considerably high in the range 73–80%. Further, the simulation results and experimental values were in good agreement with each other which establishes the accuracy of the statistical mechanical model. This study indicated that purification of biscuit industrial effluent by NF process is more economical, energy efficient, and eco-friendly and could be effectively combined with RO to extend membrane life and achieve high purity water in permeate by considerably reducing COD and BOD load. The NF membrane exhibited considerably high water permeability and substantial anti-fouling ability which clearly offers enormous scope for the treatment of effluents coming from dairy, biochemical, food, and bulk drug industries. The highlight of this study is the capability of the NF membrane to efficiently reject larger organic molecules in the form of COD and BOD to facilitate economical treatment of industrial effluents at lower pressures.
Funding
This work was supported by the Council of Scientific and Industrial Research (CSIR) through MATES XII Five Year Plan project in supporting our research activities.
Acknowledgement
The first author thanks BVRIT, Narsapur, Medak for giving him opportunity to carry out his PhD research.
Disclosure statement
No potential conflict of interest was reported by the authors.
References
- Zacharof MP, Lovitt RW. The filtration characteristics of anaerobic digester effluents employing cross flow ceramic membrane microfiltration for nutrient recovery. Desalination. 2014;341:27–37.10.1016/j.desal.2014.02.034
- Mulder M. Basic principles of membrane technology. 2nd ed. Dordrecht: Kluwer Academic Publishers; 1998.
- Baker RW. Membrane technology and applications. 2nd ed. Chichester: Wiley; 2004.10.1002/0470020393
- Nguyen M, Reynolds N, Vigneswaran S. By-product recovery from cottage cheese production by nanofiltration. J. Clean. Prod. 2003;11:803–807.10.1016/S0959-6526(02)00130-0
- Hilal N, Busca G, Hankins N, et al. The use of ultrafiltration and nanofiltration membranes in the treatment of metal-working fluids. Desalination. 2004;167:227–238.10.1016/j.desal.2004.06.132
- Petrinic I, Bajraktari N, Helix-Nielsen C. Membrane technologies for water treatment and reuse in the textile industry. In: Basile A, Cassano A, Rastogi NK, editors. Advances in membrane technologies for water treatment: materials, processes and applications. 1st ed. Cambridge: Elsevier; 2015. Chapter 17; p. 537–550, ISBN: 978-1-78242-121-4.
- Gobi K, Vadivelu VM. By-products of palm oil mill effluent treatment plant – a step towards sustainability. Renewable Sustainable Energy Rev. 2013;28:788–803.10.1016/j.rser.2013.08.049
- Harisha RS, Hosamani KM, Keri RS, et al. Arsenic removal from drinking water using thin film composite nanofiltration membrane. Desalination. 2010;252:75–80.10.1016/j.desal.2009.10.022
- Lau WJ, Ismail AF. Polymeric nanofiltration membranes for textile dye wastewater treatment: preparation, performance evaluation, transport modelling, and fouling control – a review. Desalination. 2009;245:321–348.10.1016/j.desal.2007.12.058
- Braeken L, Van der Bruggen B. Feasibility of nanofiltration for the removal of endocrine disrupting compounds. Desalination. 2009;240:127–131.10.1016/j.desal.2007.11.069
- Galanakis CM. Recovery of high added-value components from food wastes: conventional, emerging technologies and commercialized applications. Trends Food Sci. Technol. 2012;26:68–87.10.1016/j.tifs.2012.03.003
- Tarleton ES, Robinson JP, Low JS. Nanofiltration: a technology for selective solute removal from fuels and solvents. Chem. Eng. Res. Des. 2009;87:271–279.10.1016/j.cherd.2008.09.006
- Salehi F. Current and future applications for nanofiltration technology in the food processing. Food Bioprod. Process. 2014;92:161–177.10.1016/j.fbp.2013.09.005
- Jianquan Luo JM, Wan Y. Desalination of effluents with highly concentrated salt by nanofiltration: from laboratory to pilot-plant. Desalination. 2013;315:91–99.
- Freger V. Nanoscale heterogeneity of polyamide membranes formed by interfacial polymerization. Langmuir. 2003;19:4791–4797.10.1021/la020920q
- Nadler R, Srebnik S. Molecular simulation of polyamide synthesis by interfacial polymerization. J. Membr. Sci. 2008;315:100–105.10.1016/j.memsci.2008.02.023
- Kim CK, Kim JH, Roh IJ, et al. The changes of membrane performance with polyamide molecular structure in the reverse osmosis process. J. Membr. Sci. 2000;165:189–199.10.1016/S0376-7388(99)00232-X
- Zhou Y, Yu S, Liu M, et al. Polyamide thin film composite membrane prepared from m-phenylenediamine and m-phenylenediamine-5-sulfonic acid. J. Membr. Sci. 2006;270:165–168.
- Saha NK, Joshi SV. Performance evaluation of thin film composite polyamide nanofiltration membrane with variation in monomer type. J. Membr. Sci. 2009;342:60–69.10.1016/j.memsci.2009.06.025
- Veríssimo S, Peinemann KV, Bordado J. Influence of the diamine structure on the nanofiltration performance, surface morphology and surface charge of the composite polyamide membranes. J. Membr. Sci. 2006;279:266–275.10.1016/j.memsci.2005.12.014
- Jegal J, Min SG, Lee KH. Factors affecting the interfacial polymerization of polyamide active layers for the formation of polyamide composite membranes. J. Appl. Polym. Sci. 2002;86:2781–2787.10.1002/(ISSN)1097-4628
- Kim SH, Kwak SY, Suzuki T. Positron annihilation spectroscopic evidence to demonstrate the flux-enhancement mechanism in morphology-controlled thin-film-composite (TFC) membrane. Environ. Sci. Technol. 2005;39:1764–1770.10.1021/es049453k
- Zhou Y, Yu S, Liu M, et al. Effect of mixed crosslinking agents on performance of thin-film-composite membranes. Desalination. 2006;192:182–189.10.1016/j.desal.2005.05.029
- Duan M, Wang Z, Xu J, et al. Influence of hexamethyl phosphoramide on polyamide composite reverse osmosis membrane performance. Sep. Purif. Technol. 2010;75:145–155.10.1016/j.seppur.2010.08.004
- Ahmad AL, Ooi BS, Mohammad AW, et al. Development of a highly hydrophilic nanofiltration membrane for desalination and water treatment. Desalination. 2004;168:215–221.10.1016/j.desal.2004.07.001
- Chiang YC, Hsub YZ, Ruaan RC, et al. Nanofiltration membranes synthesized from hyperbranched polyethyleneimine. J. Membr. Sci. 2009;326:19–26.10.1016/j.memsci.2008.09.021
- Abu Seman MN, Khayet M, Hilal N. Nanofiltration thin-film composite polyester polyethersulfone – based membranes prepared by interfacial polymerization. J. Membr. Sci. 2010;348:109–116.
- Abu Seman MN, Khayet M, Hilal N. Development of antifouling properties and performance of nanofiltration membranes modified by interfacial polymerisation. Desalination. 2011;273:36–47.10.1016/j.desal.2010.09.038
- Venkata Swamy B, Madhumala M, Prakasham RS, et al. Nanofiltration of bulk drug industrial effluent using indigenously developed functionalized polyamide membrane. Chem. Eng. J. 2013;233:193–200.10.1016/j.cej.2013.08.045
- Kalyani S, Smitha B, Sridhar S, et al. Blend membranes of sodium alginate and hydroxyethylcellulose for pervaporation-based enrichment of t-butyl alcohol. Carbohydr. Polym. 2006;64:425–432.10.1016/j.carbpol.2005.12.012
- Mária P, Ondrej S, Alena K, et al. FTIR spectroscopy study of polyamide-6 irradiated by electron and proton beams. Polym. Degrad. Stab. 2012;97:523–531.
- El-Aassar A-hMA. Polyamide thin film composite membranes using interfacial polymerization: synthesis, characterization and reverse rsmosis performance for water desalination. Aust. J. Basic Appl. Sci. 2012;6:382–391.
- Tin PS, Chung TS, Liu Y, et al. Effects of cross-linking modification on gas separation performance of Matrimid membranes. J. Membr. Sci. 2003;225:77–90.10.1016/j.memsci.2003.08.005
- Standard methods for examination of water and wastewater. 20th ed. Washington, DC: APHA-AWWA-WPCF; 1998.