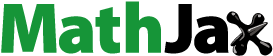
Abstract
A new model for entropy generation number in hexagonal microchannel is developed going from the equation proposed by Bejan. The effect of Cu, CuO, Al2O3 and TiO2 mixed with pure water inside the microchannel is evaluated via entropy generation analysis. To show the contribution of entropy heat-transfer generation, Bejan number is also investigated. The effects of heat flux in the range of [2000–12000] W/m2, and volume fraction and nanoparticles size, respectively, on entropy generation numbers and Bejan number are all evaluated. The results demonstrate that increasing heat flux increases both thermal entropy generation and Bejan number but decreases the frictional entropy production. The results also show that thermal and friction entropy generation numbers exhibit an inverse variation trend when varying volume percentage and nanoparticle diameter.
1. Introduction
The global expansion of energy necessitates the improvement of heat transmission and the decrease of energy losses. Optimizing the design of new energetic gadgets and developing sophisticated technological systems may effectively increase energy contribution to create rising demand. The necessity of understanding the comportment of flow in microsystems is an important step for technological application [Citation1]. Furthermore, recent advancements have shown that microfluidic devices have a variety of advantageous features [Citation2,Citation3]. The concept of microchannel and nanosize equipment has attracted the attention of many researchers because of its ability to advance the heat transfer in industrial systems and remove the generation of high heat flux within electronic components [Citation4]. Therefore, scientists [Citation5–9] studied different shapes of microchannels in order to predict the best configuration to improve heat transfer and fluid flow in small equipment.
In addition to heat-exchanger geometrical design, the utilization of nanofluids becomes an interesting way of heat transfer enhancement [Citation10]. Nanofluids are suspensions of solid particles of nanometric size in a base fluid. The suspension of small solid particles in energy transmission fluids can enhance their thermal conductivity and supplies an efficient and innovative way to improve their heat transfer characteristics significantly. Abollahi et al. [Citation11] evaluated the effects of using different nanofluids on heat transfer and performance of microchannel heat sink. They found that Al2O3, SiO2, CuO and ZnO in water had better heat transfer enhancement in comparison with pure water, and that SiO2 nanofluid with nanoparticle concentration of 2% and size of 30 nm had the greatest performance compared to other nanofluids. Alkasmoul et al. [Citation12] studied the performance of this discovered fluid, and proved that nanofluids are beneficial. They reported experimentally a comprehensive evaluation of heat transfer for Al2O3, TiO2 and CuO–water nanofluids for cooling configuration. Vasefi et al. [Citation13] studied the turbulent forced convection of CuO–water nanofluid through a horizontal channel. They investigated the effect of adding CuO nanoparticles to the base fluid on the dimensioness mean and fluctuations of velocity and temperature profiles. Jung and Park [Citation14] analysed the heat transfer of Al2O3–water nanofluid in microchannel heat sink. They evaluated flow behaviours and compared the flow velocity, circulation and Reynold’s shear stress. They found, as a result, that those properties exposed higher values for Al2O3 nanofluid rather than water.
Increasing the number of fins particles or shrinking the size of the system is the best approach to increase heat transmission in thermal systems [Citation15].
In reality, increasing entropy or decreasing thermal efficiency always has an impact on energy devices. As a result, it is critical to reduce entropy creation, which explains why systems’ capacity to generate work is decreasing. As a result, assessing entropy creation or exergy destruction due to heat or friction entropy is critical for optimization. As a result, entropy generation minimization is used as a design criterion for optimal thermal systems [Citation16]. According to the thermodynamics second law, Bahiraei et al. [Citation17] investigated the impact of water–Al2O3 nanofluid with different nanoparticles’ shapes in microchannel, on thermal, friction, total entropy generation and Bejan number at various Reynold’s numbers. Torabi et al. [Citation18] looked into the processes that control the rate of entropy generation in micro-energy systems. They conducted an extensive literature review on the analysis of the second law in microthermal and thermochemical systems. They covered essential entropy generation equations, the entropy production idea in single-phase and multiphase flow, and research on the rate of entropy development within microchannels and nanofluid flows. Manay et al. [Citation19] conducted experiments to determine the effect of nanofluid and microchannel heat sink height on entropy production. They also tested the influence of TiO2 nanoparticles volume fraction. Bazdidi-Tehrani et al. [Citation20] studied the turbulent mixed convection of CuO–water nanofluid in a vertical square duct. They explored influence of nanoparticles on thermal and fractional entropy generation. They found that increasing the nanoparticle volume fraction decreases the ratio of thermal entropy generation and the frictional entropy generation. Hosseini et al. [Citation21] analytically studied the nanofluid entropy production in a porous horizontal microchannel under MHD field. In another analytical investigation, Sheikhzadeh et al. [Citation22] studied parameters that influence entropy generation such as volume fraction, Reynold’s number and diameter of the microchannel. Based on the second law of thermodynamics, Khlifi et al. [Citation23] theoretically examined the creation of entropy in two various microchannels. They developed mathematical models to predict entropy generation in rectangular and elliptical microchannel and used different type of nanofluids. Shah et al. [Citation24] also used a theoretical method and analysed mathematically entropy generation of nanofluid flow.
Different research on entropy production and exergy analysis in nanofluid within microchannels have also been conducted [Citation25–27]. As far as is known, the entropy generation in hexagonal microchannel has not been studied much. The purpose of this research is to develop a new model for estimating entropy production rate in regular hexagon microchannel and to investigate entropy generation using nanofluids. Four nanofluids are used and compared with pure water. The heat flux effects imposed on the microchannel surface, as well as on the volume fraction and size of nanoparticles, are investigated in terms of entropy generation numbers and Bejan number.
2. Methodology
2.1. Problem of the issue
The issues addressed in this study include an examination of entropy generation using nanofluid flow in hexagonal microchannel cross sections. The considered configuration is displayed in Figure which describes a fully developed steady-state microchannel laminar flow in arbitrary regular hexagonal cross section with hydraulic diameter equal to 278 µm, with a perimeter P, a cross-sectional area A and length of 0.01 m.
A uniform wall heat flux in the range 2000–12000 W/m2 heats the hexagonal channel, where
is the aspect ratio of the regular hexagonal:
This work proposes a development of a model for entropy generation number in arbitrary hexagonal microchannel in the first section. The mathematical formulation is described in the second section. Important results as well as comparative study, influence of working fluids, nanoparticles volume fraction and size are analysed in the third section.
2.2. Entropy generation formulation
Based on the analytical formula derived by Bejan [Citation28], the development of the present model started.
(1)
(1) In Equation (1), the entropy generation is composed of two contributions, entropy generation resultant of heat transfer and friction losses, which is formulated by Bejan as [Citation23]:
(2)
(2) After integrating (Equation (2)), the expression obtained is independent of the form of cross section of the channel [Citation29]:
(3)
(3) In order to get a dimensionless formula of entropy generation rate, the following expression presents the entropy generation number Ns
(4)
(4) Consequently, thermal and frictional entropy generation numbers are
(4a)
(4a)
(4b)
(4b) where Tave, Nu and f are, respectively, the fluid temperature, the Nusselt number and the friction factor that are estimated as follows:
The average temperature is given by
(5)
(5) Using the energy balance of the outlet and inlet section of the channel, Tout can be estimated as
(6)
(6) Substituting (Equation (6)) into (Equation (5)), to get the expression of Tave, the following equation can be used:
(7)
(7) To estimate Nusselt number and Poiseuille number, two compact models were proposed, respectively, by [Citation30], and [Citation31], which investigates
and
of a laminar flow in microchannel of regular polygonal cross section as
(8)
(8)
(9)
(9) Equations (8) and (9) are the functions of the perimeter P, the area A of the regular polygonal cross-section and the dimensionless inertia polar moment from the cross-section centre
.
Besides, the length characteristic of Nusselt number and Poiseuille number is the square root of cross-sectional area. In the present work, Nu and fRe are related to the hydraulic diameter of the cross section.
So, they are converted as follows:
(10)
(10)
(11)
(11) As a result, Nu and Re in Equation (4a) and Equation (4b) are used with the following expressions:
(12)
(12)
(13)
(13) The parameters A, P and
are illustrated, respectively, as follows. A, P and
are expressed as functions of the side number (n) in regular polygons.
For regular hexagon, n is 6.
(14)
(14)
(15)
(15)
(16)
(16)
After having replaced the previous formulas in Equations (12) and (13), the Nusselt and Poiseuille numbers obtained are
(17)
(17)
(18)
(18) Afterwards, by using the following formulas of hydraulic diameter, Reynold’s number and the mass flow rate, a theoretical development is done for Equation (4) as follows:
(19)
(19)
(20)
(20)
(21)
(21) As a result, a dimensionless expression of the total entropy generation number inside hexagonal microchannel of laminar fluid flow is obtained as
(22)
(22) where
(22a)
(22a)
(22b)
(22b) In order to estimate the contribution of the heat transfer component’s entropy creation, the Bejan number [Citation32] is determined as follows:
(23)
(23)
2.3. Thermophysical properties
The identification of thermophysical properties is essential for understanding the nanofluid behaviour. For that, various formulas have been used to evaluate nanofluid properties, namely, specific heat, density, dynamic viscosity and thermal conductivity.
The correlations used to evaluate the density and specific heat are given in, respectively, (Equation (24)) and (Equation (25)) as [Citation33]
(24)
(24)
(25)
(25) The thermal conductivity of nanofluids is calculated using the Hamilton–Crosser [Citation34] model depending on volume fraction and the Corione [Citation35] depending on diameter nanoparticle.
(26)
(26)
(27)
(27) where
. The dynamic viscosity is evaluated using Corcione [Citation35] model depending on nanoparticles volume fraction and size.
(28)
(28) where
The nanoparticle properties and base fluid are indicated in Table .
Table 1. Nanoparticle and base fluid properties.
3. Results and discussion
3.1. Comparative research
To validate the present model of entropy generation number (i.e. Equation (22)), developed for a regular hexagon microchannel, and to show its accuracy, the general model derived by Ratts and Raut [Citation36] have been used. Figures indicate, respectively, frictional, thermal and total entropy generation numbers when varying the imposed heat flux.
So far, only pure water is considered. Clearly, the current model gives results similar to the past results published from the reference model. Furthermore, the results show that increasing the heat flux led to thermal entropy generation number increase, owing to the considerable influence on fluid temperature. Figure shows a decreasing frictional entropy generation number, because of the existence of a heat flow term in the denominator of Equation 22b. Simultaneously, an increase in heat flux resulted in a decrease in total entropy generation number, indicating that in this case, entropy generation due to friction losses is the dominant part of the total number, as presented in Figure .
3.2. Effect of different nanofluids
This section demonstrates how heat flow influences the thermal, frictional and total entropy generation numbers of various nanofluids consisting of Cu, CuO, Al2O3 and TiO2 nanoparticles mixed with pure water. The volume concentration of nanoparticles is 4% in all cases, and the nanoparticle size is 25 nm.
Figure depicts the relationship between the thermal entropy generation number and the heat flow for various nanofluids. It is evident that all forms of nanofluids have lower thermal entropy generation numbers than pure water, because of the nanofluids’ higher thermal conductivity, where the Hamilton crosser model was used to compute thermal conductivity in this section. It is also worth noting that Cu has the lowest thermal entropy generation number.
While this is true, the nanofluids viscosity is larger than that of pure water, resulting in a drop in frictional entropy production number three times more than that one of pure water, as seen in Figure . This figure indicates that all considered nanofluids have the same amount of frictional entropy production number. This behaviour is the resultant of the fact that Equation (22b) highly depends on the dynamic viscosity, and that the Corcione model calculates the viscosity by considering the base fluid properties and nanoparticles concentration.
Furthermore, as illustrated in Figures and , the frictional entropy generation number is bigger than that of the thermal entropy generation. Consequently, the total entropy generation number is determined by friction irreversibility, as shown in Figure . Total entropy generation follows the same variation pattern as frictional entropy in all nanofluids, up to the heat flux interval between 4000 and 8000 W/m2, where the Cu–water nanofluid has the lowest total entropy values.
Figure presents the change of the Bejan number function of heat flux. To track the variation of the Bejan number, copper oxide was combined with water at 4% volume and measured at 25 nm.
A Bejan number close to zero indicates that the fluid viscous contribution to entropy generation is greater, whereas a Bejan number close to 1 indicates that the fluid friction contribution is minimal. The Bejan number rises with increasing heat flux and is lower in CuO–water nanofluid than in pure water. This phenomenon is derived from the data obtained for the thermal entropy generation number, which demonstrates that this number increases with heat flux augmentation and exhibits the least amount of irreversibility in the case of nanofluids.
3.3. Effect of volume fraction
The CuO–water nanofluid is the working fluid in order to investigate the influence of nanoparticle concentration on entropy generation numbers. In this paragraph, CuO volume fraction is varied between 2%, 4% and 6%, and the nanoparticle diameter is fixed at 25 nm.
The results show that the thermal and frictional entropy production numbers always vary with heat flux in the same way.
Figures and illustrate that the heat flux increase leads to rising the thermal entropy generation number and fulling the frictional entropy generation number simultaneously. Furthermore, Figure indicates that increasing the particle fraction results in decreasing the thermal entropy generation number. This is related to the addition of nanoparticles to the base fluid, from 2% to 6%, increased thermal conductivity and consequently ameliorate the heat exchange and decrease the temperature difference. In addition, in Figure , the frictional entropy generation number is the consequence of increasing the volume fraction. This is because raising the volume percentage of nanoparticles induced an increase in dynamic viscosity.
Figure 9. Variation of thermal entropy generation number vs. heat flux for different volume fraction of CuO–water.
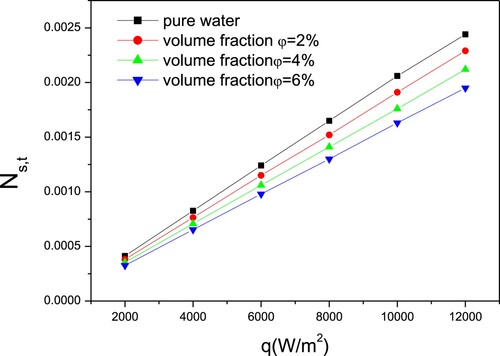
Figure 10. Variation of frictional entropy generation number vs. heat flux for different volume fraction of CuO–water.
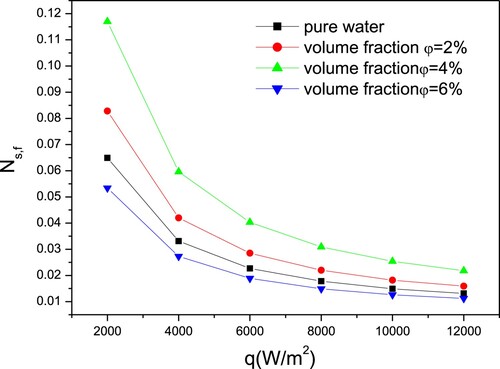
Figure presents the overall entropy generation number variation vs. heat flow for various volume fraction. It has the same tendency as the frictional entropy generation number, which continues to be the most important contribution. As a result, increasing the volume percentage of nanoparticles preceded with an increase in the overall entropy generation number.
Figure indicates that the volume fraction grows jointly with the Bejan number. This is coming as a result that introducing tiny particles into the base fluid resulted in thermal entropy generation number decrease.
3.4. Nanoparticle diameter effect
Rarely is the influence of the diameter of nanoparticle on entropy generation studied. This paragraph introduces the effect of heat flux and nanoparticle size on entropy generation numbers and Bejan number.
Figure shows the thermal entropy generation number vs. heat flux for CuO–water nanofluid as its diameter varies. The volume fraction of CuO–water is 4% and the diameter varied from 25 to 200 nm. Consequently, the variation vs. heat flux is the same. The number of thermal entropy production increases as the nanoparticles’ diameter increases, which is explained by the statement that increasing the nanoparticles size decreases the thermal conductivity of nanoparticles of nanofluids, which is estimated in this instance using the Corcione model.
Figure 13. Variation of thermal entropy generation number vs. heat flux for various nanoparticles diameter of CuO–water.
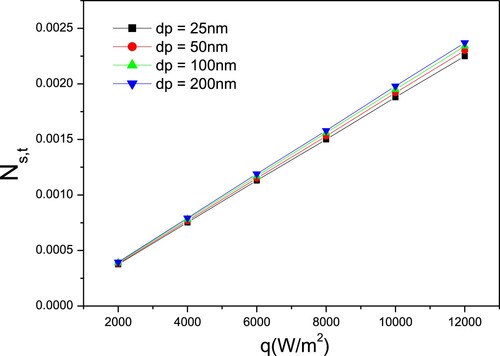
Furthermore, Figure revealed that the number of frictional entropy production decreases as nanoparticle diameter increases, since increasing the size of nanoparticles decreases the dynamic viscosity of nanofluids.
Figure 14. Variation of frictional entropy generation number vs. heat flux for various nanoparticles diameter of CuO–water.
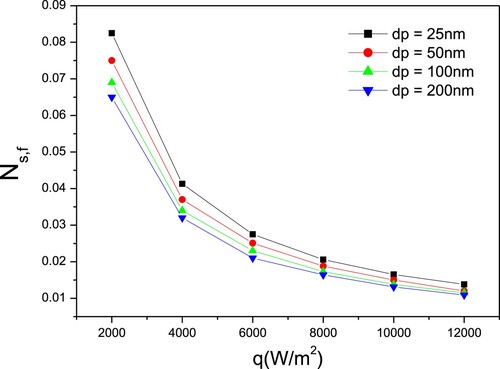
Figure exhibits similar results to the frictional entropy production number, indicating that when the size of CuO nanoparticles increases, the overall entropy generation number decreases. Figure depicts the change of the Bejan number vs. heat flux for various nanoparticle sizes. It has been discovered that as the diameter of nanoparticles decreases, so does the Bejan number.
4. Conclusion
An analytical analysis was provided in this work in order to decrease irreversibility and achieve thermodynamic optimization. A theoretical model for calculating the entropy generation number in hexagonal microchannels has been created.
Various working fluids are utilized to demonstrate their impact on the entropy generation number. The effects of heat flow, volume fraction and nanoparticle size on thermal, frictional and total entropy production numbers and the Bejan number were studied. The following are the crucial points:
Increasing the heat flux imposed on the channel results in increasing the thermal entropy generation number and reducing the entropy caused by the viscous dissipation.
Since the thermal entropy generation number is small by reference to the frictional entropy generation number, it has less influence on the total entropy generation number.
The nanoparticles addition in the base fluid results in increasing the thermal conductivity and decreasing the thermal entropy generation number. Therefore, the increase in volume fraction is effective in improving heat transfer and minimizing thermal irreversibility.
Smaller nanoparticles led to minimizing the frictional entropy generation number.
Rising the heat flux, the nanoparticles size and the volume fraction results in decreasing the Bejan number.
Acknowledgements
This Project was funded by the Deanship of Scientific Research (DSR) at King Abdulaziz University, Jeddah, under grant no. (G: 21-305-1442). The authors, therefore, acknowledge with thanks DSR for technical and financial support.
Disclosure statement
No potential conflict of interest was reported by the author(s).
References
- Aissa A, Slimani M, Mebarek-Oudina F, et al. Pressure-driven gas flows in micro channels with a slip boundary: a numerical investigation. Fluid Dynam Mater Process. 2020;16:147–159.
- Hajji H, Kolsi L, Hassen W, et al. Finite element simulation of antigen-antibody transport and adsorption in a microfluidic chip. Physica E. 2018;104:177.
- Hajji H, Kolsi L, Askri F, et al. Heat transfer and flow structure through a backward and forward-facing step micro-channels equipped with obstacles. Therm Sci. 2021;25:2483–2492.
- Japara W, Che Sidika N, Matb S. A comprehensive study on heat transfer enhancement in microchannel heat sink with secondary channel. Int Commun Heat Mass Transfer. 2018;99:62–81.
- Li F, Zhu W, Hea H. Field synergy analysis on flow and heat transfer characteristics of nanofluid in microchannel with non-uniform cavities configuration. Int J Heat Mass Tran. 2019;144:118617.
- Vasilev M, Abiev R, Kumar R. Effect of microchannel heat sink configuration on the thermal performance and pumping power. Int J Heat Mass Tran. 2019;141:845–854.
- Rajiv, Kumar H, Singh Sokhal G. Effect of geometries and nanofluids on heat transfer and pressure drop in microchannels: a review. Mater Today: Proc. 2020;28:1841.
- Zhu Q, Chang K, Chen J, et al. Characteristics of heat transfer and fluid flow in microchannel heat sinks with rectangular grooves and different shaped ribs. Alexandria Eng J. 2020;59:4593–4609.
- Monavari A, Jamaatia J, Bahiraei M. Thermohydraulic performance of a nanofluid in a microchannel heat sink: Use of different microchannels for change in process intensity. J Taiwan Inst Chem E. 2021;125:1–14.
- Ghachem K, Aich W, Kolsi L. Computational analysis of hybrid nanofluid enhanced heat transfer in cross flow micro heat exchanger with rectangular wavy channels. Case Stud Therm Eng. 2021;24:100822.
- Abdollahi A, Mohammed H, Mokhtarpour S, et al. Fluid flow and heat transfer of nanofluids in microchannel heat sink with V-type inlet/outlet arrangement. Alexandria Eng J. 2017;56:161–170.
- Alkasmoul FS, Al-Asadi MT, Myers TG, et al. A practical evaluation of the performance of Al2O3-water, TiO2-water and CuO-water nanofluids for convective cooling. Int J Heat Mass Transf. 2018;126:639–651.
- Vasefi S, Bazdidi-Tehrani F, Reyhani L. Assessment of mean and fluctuating velocity and temperature of CuO/water nanofluid in a horizontal channel: large eddy simulation. Numer Heat Transf. 2018;74:1520–1538.
- Jung SY, Park H. Experimental investigation of heat transfer of Al2O3 nanofluid in a microchannel heat sink. Int J Heat Mass Tran. 2021;179:121729.
- Ali AM, Angelino M, Rona A. Numerical analysis on the thermal performance of microchannel heat sinks with Al2O3 nanofluid and various fins. Appl Therm Eng. 2021;198:117458.
- Chauhan P, Kumar R, Bharja R (s.d.). Optimization of the circular microchannel heat sink under viscous heating effect using entropy generation minimization method. Therm Sci Eng Prog. 2451–9049.
- Bahiraei M, Monavari A, Naseri M, et al. Irreversibility characteristics of a modified microchannel heat sink operated with nanofluid considering different shapes of nanoparticles. Int J Heat Mass Tranf. 2020;151:119359.
- Torabi M, Karimi N, Torabi M, et al. Generation of entropy in micro thermofluidic and thermochemical energy systems-A critical review. Int J Heat Mass Transf. 2020;163:120471.
- Manay E, Akyürek E, Sahin B. Entropy generation of nanofluid flow in a microchannel heat sink. Results Phys. 2018;9:615–624.
- Bazdidi-Tehrani F, Vasefi S, Anvari A. Analysis of particle dispersion and entropy generation in turbulent mixed convection of CuO-Water nanofluid. Heat Transf Eng. 2017;40(1-2):1–14.
- Hosseini S, Ghasemian M, Sheikholeslami M, et al. Entropy analysis of nanofluid convection in a heated porous microchannel under MHD field considering solid heat generation. Powder Technol. 2019;344:914–925.
- Sheikhzadeh G, Aghaei A, Ehteram H, et al. Analytical study of parameters affecting entropy generation of nanofluid turbulent flow in channel and micro-channel. Therm Sci. 2016;20:2037–2050.
- Khlifi B, Kalech B, Bouterra M, et al. Thermodynamic optimisation of rectangular and elliptical microchannels with nanofluids. Int J Exergy. 2018;25:252.
- Shah F, Khan MI, Hayat T, et al. Theoretical and mathematical analysis of entropy generation in fluid flow subject to aluminum and ethylene glycol nanoparticles. Comput Methods Programs Biomed. 2019;182:105057–105057.
- Mohammadi I, Ajam H. A theoretical study of entropy generation of the combustion phenomenon in the porous medium burner. Energy. 2019;188:116004.
- Bahiraei M, Jamshidmofid M, Amani M, et al. Investigating exergy destruction and entropy generation for flow of a new nanofluid containing graphene–silver nanocomposite in a micro heat exchanger considering viscous dissipation. Powder Technol. 2018;336:298–310.
- Sundar L, Mesfin S, Raman E, et al. Experimental investigation of thermo-physical properties, heat transfer, pumping power, entropy generation, and exergy efficiency of nanodiamond+Fe3O4/60:40% water-ethylene glycol hybrid nanofluid flow in a tube. Therm Sci Eng. 2021;21:100799.
- Bejan A. Entropy generation through heat and fluid flow. New York: Wiley; 1982.
- Bejan A. Entropy generation minimization. Boca Raton: CRC Press; 1996.
- Sadeghi E, Bahrami M, Djilali N. Estimation of Nusselt number in microchannels of arbitrary cross section with constant axial heat flux. Heat Transf Eng. 2011;31(8).
- Bahrami M, Yovanovich MM, Culham J. Pressure drop of fully-developed, laminar flow in microchannels of arbitrary cross-section. J Fluids Eng. 2006;128(5):1036–1044.
- Al-Rashed A, Ranjbarzadeh R, Aghakhani S, et al. Entropy generation of boehmite alumina nanofluid flow through a minichannel heat exchanger considering nanoparticle shape effect. Physica A. 2019;521:724–736.
- Khanafer K, Vafai K. A critical synthesis of thermophysical characteristics of nanofluids. Int J Heat Mass Transf. 2011;54:4410–4428.
- Hamilton R, Crosser O. Thermal conductivity of heterogeneous two component systems. Ind Eng Chem Fund. 1962;1:187–191.
- Corcione M. Empirical correlating equations for predicting the effective thermal conductivity and dynamic viscosity of nanofluids. Energy Convers Manage. 2011;52:789–793.
- Ratts EB, Raut AG. Entropy generation minimization of fully developed internal flow With Constant heat flux. J Heat Transfer. 2004;126:656.