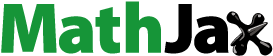
ABSTRACT
Concrete has experienced significant improvements in recent decades, resulting in lower Portland cement consumption as well as a lower carbon footprint through CO2 injection while keeping comparable fresh, mechanical, and durability performance. The use of CO2 injection in concrete (CarbonCure) in the United States and Canada has enabled advances such as green concrete under normal and severe conditions. While incorporating novel developments, this study focuses on CarbonCure concrete modification in the extreme weather of the Arabian Gulf region. This is a relatively new option that has entered the field in the Middle East. The materials, process, and fresh and hardened properties of the CarbonCure concrete made and field cured in the Arabian Gulf region will be considered here and evaluated in detail. Along with adding CO2 to the mix, the cementitious material was lowered without impacting the quality or performance of the structural concrete. The developed green mix included up to 0.2% CO2 by mass of cementitious material. Because of the benefit of early carbonation, which strengthened the concrete product even with less cementitious material, this green concrete mix retained a 28% increase in slump compared to the standard concrete mix without CO2, a 28-day compressive strength of 48 MPa, low water absorption of 1.3%, and resistance to aggressive chemicals, all within the limits defined by the standard codes. Due to these benefits, and because this green concrete was tested against the severe coastal climate, it would be ideal for maritime applications.
Introduction
Cement is the second most widely used material after water with annual global cement production exceeding 4 billion metric tons in each of the last ten years. Cementitious composites are common in construction because of their availability, durability, and ease of molding [Citation1–3]. CO2 emissions resulting from the decomposition of carbonates in the production of cement clinker were about 1.6 billion metric tons in 2022. Besides, the CO2 emissions resulting from the combustion of fuels to produce the heat required were an additional one billion metric tons in 2022 [Citation3]. Thus, a significant amount of CO2 has been released into the atmosphere, implying that this gas is the principal cause of global warming. Nowadays, CO2 emissions arising from a wide range of human activities can be captured, stored, and then introduced to the concrete mix during batching [Citation4–7].
Lately, ready-mix concrete industries in the United States, Canada, and Saudi Arabia utilized CO2 in the production of concrete where the CarbonCure technology has been applied [Citation7]. They incorporated the carbon dioxide into concrete during mixing. The desired carbon dioxide quantity was discharged from a pressurized CO2 container into the batch after the dry ingredients of concrete were first mixed with water. The resulting chemical reaction between the carbon dioxide and the dissolved cement phases including the tricalcium and dicalcium silicates formed nano carbonates (), which is well known as the early carbonation of concrete. These produced nano carbonates are expected to act as nucleation sites in the pore solution for earlier precipitation of the calcium silicate hydrates resulting from the cement hydration reaction as well as filling the pores in the mature concrete [Citation7–9]. However, it is worth mentioning that CarbonCure Technologies released that the tallest high-rise ever built that incorporated CarbonCure-ready mixed concrete was the 300 NMA Tower at 300 North Michigan Avenue in Chicago, IL, with 47 floors. It was completed in 2022. The goal behind this CarbonCure technology is to achieve neutral carbon and achieve a balance between releasing carbon dioxide into the atmosphere and permanently preserving carbon dioxide in concrete.
Figure 1. SEM image shows the formation of nano carbonates (CaCO3) as a result of the addition of CO2 to the concrete material (photo by CarbonCure technologies).
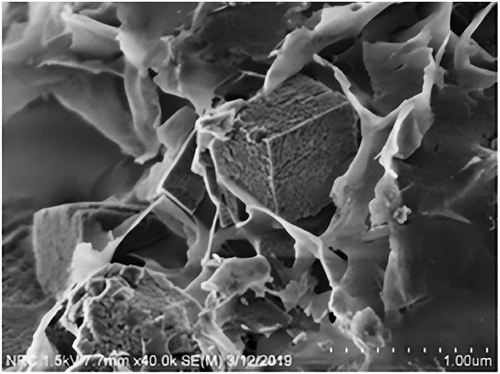
In this paper, CarbonCure concretes were made and field-cured in the Arabian Gulf environment, which is known for its elevated ambient temperature, increased humidity, and increased salinity levels with high concentrations of aggressive ions [Citation10]. This application is assessed and discussed with emphasis on the potential of reducing the total volume of greenhouse gases as well as reducing cement requirements. The manufactured CarbonCure concrete had comparable fresh and hardened properties to conventional concrete even though it was cured in the extreme weather conditions of the Arabian Gulf climate, which would be suitable for the marine industry and its associated services.
Literature review
The validation of the CarbonCure concrete was assessed and discussed in the literature [Citation6], where the amount of carbon dioxide that was injected into the concrete was estimated and compared to the amount of carbon dioxide that was permanently mineralized. In their study, a Carbon/Sulfur Analyzer CS-800 was used to measure the amount of carbon and sulfur contents in a reference and CO2-injected freshly produced masonry concrete samples. When each cast sample was dried via a hot plate and sieved through an 80 µm sieve, the carbon and sulfur contents were measured via the ELTRA CS-800. The measured quantities from the analysis were taken as an objective measure of the injection quantity of carbon dioxide. The results of the ELTRA CS-800 tests revealed on average that about 93% of the total injected carbon dioxide quantity was converted to carbonates. The lowest conversion rate was 76% which indicated that almost three-quarters of the total injected carbon dioxide quantity was mineralized and permanently stored in mature concrete.
The development of this methodology (CarbonCure) with an average conversion rate of about 93% of the total carbon dioxide being injected into concrete [Citation6], is becoming increasingly exciting to turn the waste CO2 into a useful mineral in concrete. This detailed technical measurement of a 93% average conversion rate is considered valuable to remove any conservative scientific uncertainties about the efficiency of CO2 mineralization in concrete.
The early carbonation reaction between the injected CO2 and dissolved silica ions from cement phases i.e. C3S and C2S during the first early age of hydration is represented in Equationequations 1(1)
(1) and Equation2
(2)
(2) [Citation7]. It is worth noting here that the early carbonation reaction during mixing time is different from the atmospheric (weather) carbonation reaction in the hydrated concrete [Citation7]. The atmospheric carbonation reaction is considered (if it happened) a severe durability problem for mature concrete while the early carbonation is expected to strengthen the concrete due to the formation of nano calcites during cement hydration (). These nano calcites act as nucleation sites (seeds) for the precipitation of calcium silicates produced during cement hydration. Also, these nano calcites act as fillers of nano and micropores in concrete leading to a dense concrete matrix with less porosity.
The recent literature further explored the efficiency of CO2 mineralization in concrete not only in the gaseous form of CO2 but also the liquid, and solid ones [Citation11–14]. The liquid form of CO2 is known as carbonic acid [Citation11]. Carbonic acid is a solution of saturated CO2. When manufactured in the laboratory, the carbonated water should be allowed to equilibrate in the presence of extra CaCO3 for at least three days. The mixing water may be carbonated at the laboratory using a soda maker. The supplied CO2 from the soda maker should be > 99% pure. The injection (dissolution) of CO2 into the mixing water would turn it into an acidic solution. After equilibration, it is anticipated that the pH of the produced carbonated water is around 4.2. The produced carbonated water should be preserved in a pressure-sealed container and allowed to equilibrate before its utilization.
The solid form of carbon dioxide (CO2) is known as dry ice [Citation12]. It is created by a process known as deposition, in which CO2 transitions from a gas to a solid phase (dry ice). The deposition, sometimes called sublimation, happens at -78.5 °C (-109.3 °F) at atmospheric pressure. Thermal insulation is required for its handling and storage where the temperature is preserved. The holding period of conventional vacuum flasks varies depending on size and construction and can range from a few hours to a few weeks. Dry ice may now be kept and transported for extended periods without losing its properties because of the recent availability of pressurized super-insulated vacuum containers. However, there has been minimal research on how dry ice, an alternate type of CO2, influences the Portland cement hydration process [Citation13,Citation14]. When dry ice dissolves in the mixing water, it forms carbonic acid which increases the acidity of the medium and reduces its pH. The carbonic acid, precisely the bicarbonate radical (), then reacts with the dissolved silicon ions in the pore solution to precipitate as CaCO3 in the nanoscale [Citation13].
Overall, the main advantage of this CarbonCure (early carbonation or mineralization) technology is that it can permanently store carbon dioxide in concrete structures even if those concrete structures are later demolished when approaching the end of their expected service life. Thus, the CarbonCure technology not only benefits the environment by reducing greenhouse gases but also allows the production of CarbonCure concrete made from reduced binder content having comparable quality to that of conventional concrete [Citation7]. This technology safely allows ready-mixed concrete industries to reduce the binder (cement or cementitious) content and incorporate carbon dioxide into the concrete mixes without affecting the quality or performance of the produced concretes which simultaneously lowers the carbon footprint in the atmosphere [Citation7].
Experimental program
Materials
Binders
Type I ordinary Portland cement (OPC) meeting the ASTM C 150 [Citation15] specifications was employed in this investigation as the main cementitious material. It had a specific gravity of 3.15. However, type F fly ash was used as a partial replacement of cement to about 30%.
CO2
The present ready-mixed CarbonCure concrete technology injects CO2 gas into the concrete batch via a discharge tube connected to a container containing pressurized liquid CO2. Once the CO2 pure gas is introduced to the batch, it reacts with the dissolved calcium ions of the cement phases to instantly produce CaCO3 during the first few minutes of mixing. A pressurized CO2 gas in a storage tank is shown in .
Aggregates
The coarse aggregate used in this project was crushed limestone with a nominal maximum size of ¾ inch. Its measured water absorption capacity was 2 to 2.3%. The limestone rocks are naturally available in the eastern region of Saudi Arabia. Thus, the crushed limestone aggregates were more economical to use in our project. It was acquired from Riyadh Road in Saudi Arabia. The fine aggregate was dune sand. Its water absorption capacity was 0.7%. It was acquired from Al Nairyah in the eastern province of Saudi Arabia.
Superplasticizers
A high-efficiency superplasticizer, named Fluidum PC 314, was used in this study. It was made based on modified synthetic carboxylate polymers. Its properties were as follows: viscous liquid, brownish in color, and its specific gravity was 1.1 at 20 ºC. Its recommended addition rates were 0.3 to 2.5% by weight of cement. Also, a water reducer with a set retardation effect, named Arcrete D 10, was used in this study. It was especially made for use in hot weather climates. Its properties were as follows: liquid, dark brown in color, and its specific gravity was 1.12 at 20 ºC. Its recommended addition rates were 0.1 to 0.8% by weight of cement.
Mix proportions, mixing, and sample preparation
There were many trials conducted at the Qanbar Ready Mix Concrete in the eastern region of Saudi Arabia, however, the presented CarbonCure mixes in this manuscript were approved to be disclosed to the academia. The considered three mix designs: i) a reference concrete mixture using 70% Type I Portland cement and 30% Type F fly ash designed to have a 28-day compressive strength of 40 MPa, ii) a concrete mixture incorporating CO2 addition as an admixture (denoted here as the CarbonCure I mix) using 70% Type I Portland cement and 30% Type F fly ash designed to have a 28-day compressive strength of 40 MPa, and iii) a concrete mixture incorporating CO2 addition as an admixture (denoted here as the CarbonCure II mix) using 100% Type I Portland cement designed to have a 28-day compressive strength of 40 MPa. The proportions for the three mix variations are presented in . The data set considered a reduced Type I Portland cement content for the CarbonCure I mix compared to the reference mix.
Table 1. Mix design proportions for the reference and CarbonCure mixes (kg/m3.).
The CO2 content, which was 0.135 and 0.2% by weight of binder in the CarbonCure I and II, respectively, was discharged from a storage tank holding pressurized liquid CO2. The required amount of CO2 was released into the mix via a control chamber.
Hot weather concreting and maritime curing
Following the completion of the field casting (), the molds containing the cast specimens were held at room temperature for 24 hours. Then, the cast specimens were de-molded and kept in an open site located one kilometer away from the shore of the Arabian Gulf in the eastern region of Saudi Arabia. This field-cured concrete was exposed to the severe marine environment, which is known for its elevated salinity with increased chlorides, and sulfates as shown in [Citation10], in the hot region of the Middle East for a period of 3, 7, and 28 days at an average ambient temperature of 30 ºC in the month of November. shows the ambient and concrete temperature measurements in the afternoon of the day of casting for a discharge of about 90 minutes (from 2:30 pm to 4:39 pm). The ambient temperature (black line) decreased as the day progressed into nighttime. The ice flakes were added to the mixes during the mixing stage as part of the designed mixing water up to 50 to 75%.
Figure 3. The CO2-concrete product is being cast in 6 x 12-inch cylinders at qanbar ready mix concrete, Saudi Arabia (photo by gulf construction).
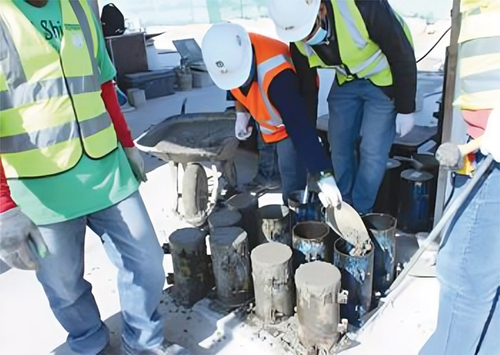
Table 2. The chemical analysis of water in the Arabian gulf compared to drinkable water.
The workability (slump) of concrete was tested for each mix at three time intervals: i) immediately after concrete mixing, ii) 30 minutes later, and iii) 60 minutes later. After the concrete was cured for 3, 7, and 28 days, its hardened properties were determined including its uniaxial compressive strength, density, water absorption, chloride permeability, soluble chlorides, and sulfate contents. The average of three replicas was taken as a representative value for each conducted experiment.
Results and discussion
CO2 effect on slump
The average slump results are shown in for the reference and CarbonCure mixes, which were conducted per ASTM C 143 [Citation16] specifications. The average slump for the reference mix decreased from 220 to 190, and then to 160 mm after 30 and 60 minutes, respectively. Also, the average slump for the CarbonCure I mix decreased from 210 to 197.5, and then to 185 mm after 30 and 60 minutes, respectively. And the average slump for the CarbonCure II mix decreased from 220 to 212.5, and then to 203.3 mm after 30 and 60 minutes, respectively. This shows that there is no significant loss of the initial workability in the freshly made CarbonCure mixes compared to the reference mix. The slump of the series mixes after a time interval of 30 and 60 minutes from mixing was better in the CarbonCure mixes than that of the standard mix. This fact is explained by the increased availability of water molecules in the pore fluid in the case of the CarbonCure mixes as a result of increasing the incorporated admixtures dosages, It is also worth noting that the CarbonCure mixes contained reduced binder contents.
CO2 effect on compressive strength
shows the compressive strengths of the reference and CarbonCure mixes after 3, 7, and 28 days, which were conducted per ASTM C 39 [Citation17] and ASTM C 109 [Citation18] specifications. It clearly illustrates a good growth of strength throughout time intervals of 3, 7, and 28 days for the CarbonCure concretes similar to the behavior of normal reference concrete. The average compressive strength at 28 days was 52.6 MPa for the reference mix. However, the average compressive strength at 28 days was 42.2 and 47.73 MPa for the CarbonCure mixes I and II, respectively. The CarbonCure I mix had a 19.77% lower average compressive strength than the reference mix. And, the CarbonCure II mix had a 9.26% lower average compressive strength than the reference mix. This observed decrease in the compressive strengths of the CarbonCure mixes compared to the standard mix could be justified by the reduction of the binder content by 10 and 15 kg/m3 for the CarbonCure I and CarbonCure II mixes, respectively.
CO2 effect on density
presents the concrete densities for the reference and CarbonCure mixes after 3, 7, and 28 days. All CarbonCure concrete specimens investigated in this study maintained respective density values similar to that of conventional concrete. The reference mix maintained a 28-day density of 2567 kg/m3. The CarbonCure I and II mixes maintained a 28-day density of 2373 and 2411 kg/m3, respectively. This demonstrates that there is no indication of a negative physical and durability effect associated with the CO2 injection of the CarbonCure concretes in comparison to the reference mix.
CO2 effect on water absorption
The effect of CO2 injection on the water absorption of concrete was examined and the average results for the reference and CarbonCure mixes after 28 days of field curing are shown in . According to these results, the addition of CO2 to the CarbonCure mixes reduces water absorption by around one-third compared to the reference mix. This proves that the CO2 injection of the CarbonCure concrete has no detrimental but advantageous physical and durability impact when compared to the reference mix.
CO2 effect on chloride permeability
The total charge passed in the investigated mixes, after 28 days of field curing, is presented in . No change in the total charge passed in the CarbonCure I concrete mix, relative to the reference mix, was observed. The CarbonCure II mix exhibited about a 23.25% increase in the total charge passed relative to the control mix. However, according to ASTM C 1202 [Citation19] specifications, all concrete mixes, including reference and CarbonCure concretes, have low chloride ion permeability, offering a low risk of concrete deterioration.
CO2 effect on soluble chloride and sulfate ions
The total soluble chloride and sulfate concentrations were tested after 28 days of field curing, and the results are presented in . A significant change in the total chloride concentration in the CarbonCure concrete mixes, relative to the reference mix, was observed (). The CarbonCure I mix was more than three times the total chloride concentration in the reference mix. The CarbonCure II mix was about two times the total chloride concentration in the reference mix. However, according to ACI PRC-222 [Citation20], all concrete mixes, including reference and CarbonCure concretes, have less soluble chlorides compared to the maximum limit specified for reinforced concrete in wet conditions i.e. a maximum of 0.08% by mass of cementitious material. Also, according to ACI 318 [Citation21], all concrete mixes, including reference and CarbonCure concretes, are with soluble chlorides that are far less than the maximum limit specified for reinforced concrete exposed to moisture and chlorides in the service of concrete, i.e. a maximum of 0.15% by mass of cementitious material. Thus, concretes that were made offered a low risk of concrete deterioration when exposed to chlorides.
Further, it can be observed from that there is a slight reduction in the sulfate ion concentrations in the blended CarbonCure concrete mixes relative to the reference mix. This indicates that there is a comparable and finely improved resistance to sulfate diffusion in the developed CarbonCure mixes with CO2 compared to the reference mix. The acid-soluble sulfate ion contents for reference, CarbonCure I, and CarbonCure II concrete tested after 28 days of field curing were 0.51, 0.49, and 0.44% by mass of cementitious material, respectively. However, according to BS 5328 [Citation22], all concrete mixes, including reference and CarbonCure concretes, have acid-soluble sulfate ions that are far less than the specified maximum limit of 4 to 5% by mass of cementitious material, offering a low risk of concrete deterioration exposed to sulfates.
It is worth mentioning that acid extraction is frequently used when the most severe sulfate conditions of the material are the center of attention. BS 1377 [Citation23] noted that all naturally occurring sulfates, with few exceptions, are acid-soluble. Calcium sulfate, the most common sulfate salt, has poor water solubility.
CO2 effect on mix performance
summarizes the results of the three mix designs, including reference and CarbonCure concretes, in terms of cement efficiency. EquationEquation 3(3)
(3) was used to calculate cement efficiency.
Table 3. Efficiency of cement and cementitious materials in reference and CarbonCure mixes (MPa∙kg−1∙m3).
The reference mix design demonstrates a 28-day cement efficiency of 0.2 MPa∙kg−1∙m3, while the CarbonCure mixes demonstrate a lower cement efficiency of 0.17 and 0.13 MPa∙kg−1∙m3 for CarbonCure I, and CarbonCure II, respectively. A similar calculation of cementitious efficiency, utilizing cementitious mass instead of cement mass, shows 0.14 MPa∙kg−1∙m3 cementitious efficiency for the reference mix and 0.11, and 0.13 MPa∙kg−1∙m3 cementitious efficiency for CarbonCure I, and CarbonCure II, respectively. The reduction in the cement efficiency of the CarbonCure mixes compared to the reference mix could be justified by the reduced binder content in the developed CarbonCure mixes. However, the results indicate that the reference and CarbonCure II mix designs offer almost the same cementitious efficiency for the developed concretes even though the binder content of the CarbonCure II mix was reduced by 15 kg/m3 compared to the standard mix.
Calcination reaction
Following the reaction between the injected CO2 and the dissolved calcium ions in the concrete mix, which occurs during the mixing process, insoluble calcium carbonates (CaCO3) are produced [Citation7–9]. These are stable in the hardened concrete, as shown by Equationequations 1(1)
(1) and Equation2
(2)
(2) unless the concrete is exposed to fire [Citation24], in which case CO2 could be released again into the atmosphere (Equationequation 4
(4)
(4) ). In the temperature range of 600 to 800 ºC, the CaCO3 calcination reaction – which was conducted experimentally using a thermo-gravimetric analyzer (TGA) – converts into lime (CaO) and CO2 ().
Conclusions
This study demonstrated the possibility of using CarbonCure technology in readily available commercial concrete. The use of CO2 as an additive into freshly produced concrete with a reduced binder content maintained a 28-day compressive strength of 48 MPa while delivering a comparable slump to the reference concrete. The addition of CO2 to concrete reduced water absorption owing to the early carbonation reaction which led to the formation of calcite and provided nucleation sites for the cement hydration products. This study also validated the great chemical resistance of the developed CarbonCure mixes to chlorides and sulfates according to the standard codes. Comparable mix performance was observed between the CarbonCure II concrete created in this investigation and the traditional reference concrete mix. When this study was compared to the available literature, it was discovered that there is still a mixed literature on the performance of CO2 in concrete material, which warns against the use of CO2 addition to concrete and postpones prospective commercial uses [Citation7,Citation11–14]. While some studies indicated an improvement in overall strength, others reported a decrease [Citation11], depending on the cement type and CO2 incorporation technique.
Research limitations and future recommendations
Despite the experimental work discussed in this article, CO2-injected concrete is still in the early stages of discovery, providing the foundation for real-world industrial applications. Therefore, the development of standards and confirmations for the effective utilization of CO2 in cement-based materials would be encouraging and useful for further exploration, both at the laboratory scale and in applications on the factory floor.
Currently, CO2 gas injection is mostly regulated by the ready-mix concrete industry. However, for future laboratory testing, a feasible option for the approach described in this investigation is diluted CO2, also known as carbonic acid, which is available in liquid form and can be added as part of the mixing water for cement. Carbonic acid is more practical and easier to use in laboratories and in-site mixing compared to gas injection.
Author statement
Abbas Albu Shaqraa: Conceptualization, Methodology, Investigation, Software, Validation, Formal analysis, Writing – original draft, Writing – review & editing.
Acknowledgments
The author feels privileged to acknowledge King Fahd University of Petroleum and Minerals (KFUPM), Dhahran, Saudi Arabia. The author is also thankful to Qanbar Ready Mix Concrete, Saudi Arabia for providing the experimental data.
Disclosure statement
The author declares that he has no known competing financial interests or personal relationships that could have appeared to influence the work reported in this paper.
Data availability statement
Data will be made available upon request.
Additional information
Funding
References
- Kosmatka S, Wilson M. Design and control of concrete mixtures. 15th ed. Skokie, IL: Portland Cement Association; 2011.
- Aïtcin P-C, Flatt RJ. Science and technology of concrete admixtures. Cambridge: Elsevier/Woodhead Publishing; 2016.
- Andrew RM. Global CO2 emissions from cement production, 1928–2018. Earth Syst Sci Data. 2019;11:1675–1710. doi: 10.5194/essd-11-1675-2019
- Monkman S, Kenward PA, Dipple G, et al. Activation of cement hydration with carbon dioxide. J Sustainable Cement-Based Mater. 2018;7(3):160–181. doi: 10.1080/21650373.2018.1443854
- Monkman S, MacDonald M, Hooton RD, et al. Properties and durability of concrete produced using CO2 as an accelerating admixture. Cem Concr Compos. 2016;74:218–224. doi: 10.1016/j.cemconcomp.2016.10.007
- Monkman S. Sustainable ready mixed concrete production using waste CO2: a case study. SP-330 Proceedings Fourteenth International Conference: Recent Advances in Concrete Technology and Sustainability Issues; Beijing, China, American Concrete Institute; 2018. p. 163–174.
- Shaqraa A. Evaluation of concrete injected with CO2 and exposed to coastal environment. Proceed Int Struct Engg Construct Conf: Innovative Theory Pract Struct Engg Construct, Chicago, United States, ISEC Press. 2023;10(1):SUS–22. doi: 10.14455/ISEC.2023.10(1).SUS-22
- Goodbrake CJ, Young JF, Berger RL. Reaction of beta-dicalcium silicate and tricalcium silicate with carbon dioxide and water vapor. J Amer Ceramic Soc, Wiley. 1979;62(3–4):168–171. doi: 10.1111/j.1151-2916.1979.tb19046.x
- Berger RL, Young JF, Leung K. Acceleration of hydration of calcium silicates by carbon dioxide treatment. Nat Phys Sci. 1972;240(97):16–18. doi: 10.1038/physci240016a0
- Bader M. Evaluation of concrete exposed to underground coastal environment in Eastern Province of Saudi Arabia. 6th International Conference on the Deterioration and Repair of Reinforced Concrete in Arabian Gulf, Bahrain; 2000. p. 829–842.
- Lippiatt N, Ling TC. Rapid hydration mechanism of carbonic acid and cement. J Buil Eng. 2020;31:101357. doi: 10.1016/j.jobe.2020.101357
- Musharafafnan S, Shelke NL, Deosarkar M. Influence of dry ice on performance of fresh concrete. Int J Innov Res Technol Sci Eng Technol. 2020;9(7):6439–6446.
- Wang Y, He F, Yang L. Influence of dry ice on the performance of Portland cement and its mechanism. Constr Build Mater. 2018;188:898–904. doi: 10.1016/j.conbuildmat.2018.08.109
- Xuan MY, Lee S, Hu H, et al. Adding dry ice into ultra-high-performance concrete to enhance engineering performance and lower CO2 emissions. Constr Build Mater. 2023;392:131858. doi: 10.1016/j.conbuildmat.2023.131858
- ASTM C 150. Standard specification for Portland cement. West Conshohocken, PA: ASTM International; 2020.
- ASTM C 143. Standard test method for slump of hydraulic-cement concrete. West Conshohocken, PA: ASTM International; 2015.
- ASTM C 39. Standard test method for compressive strength of cylindrical concrete specimens. West Conshohocken, PA: ASTM International; 2021.
- ASTM C 109. Standard test method for compressive strength of hydraulic cement mortars. West Conshohocken, PA: ASTM International; 2002.
- ASTM C 1202. Standard test method for electrical indication of concrete’s ability to resist chloride ion penetration. West Conshohocken, PA: ASTM International; 2019.
- ACI PRC-222. Guide to protection of metals in concrete against corrosion. Farmington Hills, Michigan: American Concrete Institute; 2019.
- ACI 318. Building code requirements for structural concrete and commentary. Farmington Hills, Michigan: American Concrete Institute; 2019.
- BS 5328-1. Concrete part 1: guide to specifying concrete, British standard. 1997.
- BS 1377-3. Methods of test for soils for civil engineering purposes part 3: chemical and electro-chemical tests. British Standard; 1990.
- Zhang H, Ma S, Wu Y. Building materials in civil engineering. Oxford: Woodhead Pub; 2011.