ABSTRACT
The work carried out under the XMat research programme (Materials Systems for Extreme Environments, EPSRC Programme Grant number EP/K008749/1-2) in the field of ultra-high temperature ceramic matrix composites has been focused on the design, development and manufacture of complex shapes and large panels for use under extreme conditions. The composites are made from 2.5D woven carbon fibre preforms impregnated with HfB2 powders and with a pyrolytic carbon, PyC, matrix created using chemical vapour infiltration, CVI. More recently, the knowledge acquired during the development of these Cf-HfB2-C composites has been focused on shortening the densification time by moving from conventional CVI to Radio Frequency-heated CVI; the work has also switched to Cf-ZrB2-C composites. In addition, the use of 3D carbon fibre preforms has begun to be explored to improve the mechanical properties and also the replacement of PyC matrix with ZrB2 to reducing the oxidation of the composites at ultra-high temperature.
Introduction
Interest in advanced materials with a temperature capability over 2500°C for a range of aerospace applications involving launch and/or re-entry into Earth’s atmosphere has increased over the last few decades [Citation1–4]. The most promising lightweight materials are carbon/carbon (C/C) composites; however, there is a critical need to improve their oxidation [Citation5–7] and ablation [Citation8–10] resistance. Carbon fibre-based composites have received much attention due to their excellent high-temperature strength in reducing or neutral atmospheres, high thermal conductivity, low coefficient of thermal expansion and excellent thermal shock resistance [Citation11–13]; however, they suffer badly from oxidation, in air, even at temperatures below 1000oC [Citation14,Citation15]. The addition of SiC, as a powder or a dense matrix, can provide protection up to 1300–1400°C or, for short periods, at temperatures up to 1600°C via the formation of a SiO2 film. However, at higher temperatures the silica begins to soften dramatically and in a low-oxygen atmosphere it develops a substantial vapour pressure [Citation16]. The addition of SiC, therefore, is not suitable for applications at temperatures above 1600°C. Addition of UHTCs, which inherently have a higher thermal conductivity and form in situ oxidation scales, have been reported to improve the oxidation and ablation resistance of C/C, C/SiC and SiC/SiC composites [Citation17,Citation18]. UHTCs such as HfB2 and ZrB2 have melting points in excess of 3000°C and their oxides melt at >2500°C, they can be used to protect the Cf preforms from oxidation [Citation17]. The mechanism by which they do this is still the subject of investigation. Achieving the optimal amount of UHTC in the carbon fibre preforms is a challenging and enduring topic; too little and the preform is not sufficiently protected, too much and the component’s mass is unnecessarily high. Different methods are being investigated to prepare C/C-UHTC composites, including slurry infiltration [Citation17], precursor infiltration and pyrolysis (PIP) [Citation19], reactive melt infiltration (RMI) [Citation20], chemical vapour decomposition (CVD), chemical vapour infiltration (CVI) [Citation21], and, in the future, combinations of them.
The ceramic matrix used in the design of the composite is going to depend on the working temperature, exposure time and mechanical stresses that the material needs to bear for the application. This paper begins by describing the investigation carried out on Cf-UHTCMCs at the University of Birmingham, UK, during the XMAT research programme funded by EPSRC, which included additional DSTL and MBDA hyper-velocity systems programmes. The MBDA programme focused on the design of complex-shaped prototypes made from a Cf-UHTCMC, while the parallel, DSTL-funded programme concentrated on the creation of large panels for thermal protection system (TPS). The development of Cf-UHTCMC has since continued with the C3HARME project, funded by the EU-H2020 research and innovation programme under Grant Agreement no. 685594, and lead by ISTEC, Italy. includes a listing of the participants, projects, materials and techniques applied in the different programs.
Table 1. Listing of the participants, projects, materials and techniques of the different programs.
XMat – materials systems for extreme environments
The overall objective of this programme was to establish the UK’s capability to discover and understand new materials that can operate under increasingly extreme conditions, thus enabling a wide range of new technologies. The vision was to develop the required understanding of how the processing, microstructures and properties of materials systems operating in extreme environments interact to the point where materials with the required performance could be designed and then manufactured.
Immediately before this project, DSTL funded research (at Loughborough University in the UK where the team was based at the time) where carbon fibre reinforced UHTC materials were developed and tested at temperatures exceeding 2500°C and HfB2 particulate filled Cf/C composites were deemed to have the best oxidation resistance [Citation17], . The erosion rate after 60 s for the samples shown in was 4 mm for the CC composite (though the extent of the erosion area was very large), 4.8 and 5.3 mm for Cf-ZrB2 and Cf-ZS20, respectively (composition abbreviations are defined in the figure caption). The highest erosion rate corresponded to Cf-ZS20-1La, indicating that the addition of SiC and LaB6 had a negative impact on the oxidation resistance of UHTC composites at 2500°C. In this work, C-HfB2 showed an erosion rate of <2 mm after 60 s [Citation17] but this result was improved in subsequent work when the processing conditions were optimised. Zero ablation could be achieved in this system after 60 s of oxyacetylene torch (OAT) testing at ∼2700oC [Citation22] and these samples are also able to survive much longer times, at least 300 s even at temperatures up to 2950oC [Citation23]. Very uniform Cf-HfB2 powder composites were developed using 2.5D carbon fibre preforms (Surface Transforms, UK) impregnated with a HfB2 powder/phenolic resin/acetone slurry and densified using carbon deposited via conventional C-CVI; details of the process have been provided elsewhere [Citation23,Citation24]. These new materials were shown to be capable of withstanding temperatures up to 3000°C, heat fluxes up to 17 MWm−2 and gas velocities up to Mach 0.6. Subsequently, their 4-point flexural strength was measured at room temperature and 1400°C; the results obtained were comparable to those of current generation TPS materials. In addition, the samples retained their shape and the surface erosion was minimal, even after arc-jet testing at 2700oC [Citation25].
Figure 1. Micro-CT images of C–C and Cf–UHTC composites after 60 s oxyacetylene torch test [Citation17]. C-C carbon-carbon benchmark; Cf-ZrB2 carbon fibre – ZrB2; Cf-ZS20 carbon fibre-ZrB2-20 vol.-% SiC; Cf-ZS20-1La carbon fibre-ZrB2-20 vol.-%SiC-10 vol.-% LaB6; Cf-HfB2 carbon fibre-HfB2; Cf-HfC carbon fibre-HfC.
![Figure 1. Micro-CT images of C–C and Cf–UHTC composites after 60 s oxyacetylene torch test [Citation17]. C-C carbon-carbon benchmark; Cf-ZrB2 carbon fibre – ZrB2; Cf-ZS20 carbon fibre-ZrB2-20 vol.-% SiC; Cf-ZS20-1La carbon fibre-ZrB2-20 vol.-%SiC-10 vol.-% LaB6; Cf-HfB2 carbon fibre-HfB2; Cf-HfC carbon fibre-HfC.](/cms/asset/7a60c2e2-e1c5-4b93-928c-7f647901e655/yaac_a_1475140_f0001_ob.jpg)
The aim of the MBDA-funded programme was to investigate the same UHTCMC technology for its industrial potential. A key output of this study was the design and production of a demonstrator with a complex shape, (a), and other samples were produced with a range of shape and dimensions to allow the determination of the mechanical and thermal properties of the composite. After mechanical testing, the strongest and weakest samples were analysed post-mortem to determine their failure mode. In general, the composites suffered a degree of delamination during testing and this suggested that the creation of 3D preform-based structures would enhance the mechanical properties of the composite by avoiding the delamination issues.
The tensile strength was measured at both room temperature and 1000°C. The values were around 80 MPa at both temperatures, however the behaviour of the material tested at 1000°C exhibited greater fibre pull-out, probably as a result of the partial oxidation of the carbon fibres and carbon matrix. As a result, the replacement of the carbon matrix by UHTC matrices, also deposited by CVI, was proposed as a new step to improve the composites.
The thermal ablation behaviour of the Cf-HfB2 composite was also characterised using two different torches. The samples tested by OAT, showed erosion on the surface of ∼1 and ∼2 mm at 60 and 300 s, respectively, at 10 mm distance from the nozzle tip, while the erosion was negligible for samples tested by the oxypropane torch (OPT), at the same distance. The characteristics of the torches can be found in . The reduced damage area and higher heat fluxes applied by OAT indicate a more severe test than with the OPT facility.
Table 2. Characteristics of OAT and OPT.
The work funded by DSTL focused on the design and optimisation of a manufacturing route to produce large plates of Cf-HfB2 composite measuring 300 × 300 × 18 mm and 150 × 250 × 18 mm for TPS applications; these were satisfactorily achieved, (b).
At the end of the three research programmes, it could be concluded that the Cf reinforced UHTC composite material demonstrated excellent thermal resistance, thermal insulation and good structural properties and could be made as both large panels and complex-shaped components. Through the design, manufacture and testing, a TRL of 3 to 4 was achieved for the Cf-UHTC composite technology.
C3HARME – next generation ceramic composites for combustion harsh environments and space
The European Union-funded C3HARME project has focused on extending the capabilities of the composite further, particularly in terms of manufacturing efficiency, reliability, cost-effectiveness and scalability.
The project is based on the design and development of materials for applications as low-erosion nozzle inserts and thermal protection tiles for rocket launch and re-entry operations with the goal of achieving TRL 5. The routes investigated to obtain the next generation of UHTCMCs include Spark Plasma Sintering (SPS) carried out by ISTEC and Tecnalia, Reactive Metal Infiltration (RMI) by DLR, German Aerospace Centre, Polymer Impregnation and Pyrolysis (PIP) by Airbus Central Research and Technology (formerly Airbus Group Innovation) as well as Radio Frequency (RF)-CVI by the University of Birmingham, UoB.
The work developed at UoB is now focused on further developing the same 2.5D Cf preforms as the base reinforcement material, while also exploring the potential offered by 3D Cf Noobed preforms (Fureho AB, Boras, Sweden) to improve the mechanical properties of the composite by reducing the delamination issues. Since the conditions required by C3HARME’s intended applications are less demanding than those for XMat’s applications, the HfB2 powder has been substituted with ZrB2 powder. Although this means that the composites are limited to about 2500°C, it also means that they are likely to be up to 10 times cheaper.
The ZrB2 powder is introduced into the preform by a vacuum impregnation-based process, which reduces the initial porosity of the preforms from 77 vol.-% and 60 vol.-% for the 2.5D and 3D Cf preforms, respectively, to ∼45 vol.-% in both cases. The final densification of the samples is achieved using RF-CVI. During the XMat and related research programmes, conventionally heated CVI was used (at Surface Transforms, UK), this took 3–4 months to decrease the final porosity to 10–11 vol.-%. In this process, the impregnated preforms were heated as slowly as possible to the CVI temperature; nevertheless, the outside surface temperature of each sample was the hottest location, leading to surface deposition and the porosity becoming blocked. Then the process needed to be stopped and the sample skinned; this was required approximately every three weeks. At least four runs were therefore needed to reach the final density indicated above. The RF heating approach being investigated during the C3HARME programme uses an RF coil operating at 200 kHz and with up to 2500 W of power, (a). The latter yields an inverse heating profile, from inside out, initiating the deposition at the centre of the sample, (b). The uninfiltrated Cf – ZrB2 composite reached 1000°C, the working temperature for PyC deposition, in just a few seconds and then developed a uniform temperature distribution in both cylindrical and rectangular samples, (c). The preliminary results obtained to date show a promising reduction in time required; just 16 vol.-% porosity remained after just 14 h infiltration. Work is continuing to reduce the porosity to the minimal level possible, but it is clear that Rf-CVI is a much more faster densification technique than conventional CVI; the latter took three months to deposit sufficient matrix to reduce the porosity to 11 vol.-%.
Figure 3. (a) RF-CVI facility, (b) the C deposition distribution on a cylindrical plain 2.5D Cf preform after 2 h infiltration and (c) rectangular Cf preform heated uniformly by RF during CVI densification process.
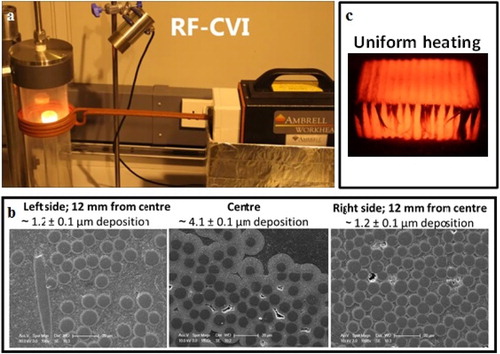
Finally, the replacement of C by ZrB2 deposition is also being addressed in the C3HARME project. The RF-CVI of ZrB2, from BCl3 (g) and ZrCl4 (g) precursors, is in the early stage of development. The current focus is on achieving pure ZrB2 and increasing the deposition rate.
Conclusions
The impregnation of 2.5D woven carbon fibre preform with UHTC powder before infiltration with carbon has allowed the temperature capabilities of the carbon–carbon composites to be extended beyond 2500°C. Using ZrB2 powder, the composites are capable of withstanding ∼2500°C, while with HfB2 powder this is extended up to ∼3000°C. Several research programmes funded by EPSRC, DSTL, MBDA and the European Commission have made possible the development of these materials, initially at Loughborough University and then, in much more detail, at the University of Birmingham, both in the UK. The ceramic powder that showed the highest temperature capability, HfB2, was chosen to achieve the goals of the next programmes, sponsored by DSTL and MBDA within the EPSRC-funded XMat programme. In both cases, the potential applications required greater than 2500°C temperature resistance for short durations. The densification of the materials produced during these programmes was carried out using the deposition of pyrolytic carbon via conventional CVI. The composites produced had strengths that were approximately the same as for the current generation of TPS materials at both room temperature and this was retained up to at least 1400°C. The improvement in these UHTCMC’s for the next programme, C3HARME, was focused on the mechanical properties, exploring the potential offered by 3D carbon fibre preform architecture, and shorter densification times via investigating the use of RF CVI. In addition, work is underway on investigating whether the substitution of the PyC matrix by a ZrB2 matrix deposited by RF CVI will lead to enhanced oxidation resistance.
Acknowledgement
This paper was originally presented at the Ultra-High Temperature Ceramics: Materials for Extreme Environments Applications IV Conference (Windsor, UK) and has subsequently been revised and extended before consideration by Advances in Applied Ceramics.
Disclosure statement
No potential conflict of interest was reported by the authors.
ORCID
P. Ramanujam http://orcid.org/0000-0001-7396-7405
J. Binner http://orcid.org/0000-0003-1496-6837
Additional information
Funding
References
- Savino R. Aerothermodynamic study of UHTC-based thermal protection systems. Aerosp Sci Technol. 2005;9(2):151–160. doi: 10.1016/j.ast.2004.12.003
- Chamberlain AL, Fahrenholtz WG, Hilmas GE, et al. Characterization of zirconium diboride for thermal protection systems. Key Eng Mat. 2004; Euro Ceramics VIII, 264–268:493–496. doi: 10.4028/www.scientific.net/KEM.264-268.493
- Yang Y, Yang J, Fang D. Research progress on thermal protection materials and structures of hypersonic vehicles. Appl Math Mech. 2008;29(1):51–60. doi: 10.1007/s10483-008-0107-1
- Wuchina E, Opila E, Opeka M, et al. UHTCs: ultra-high temperature ceramic materials for extreme environment applications. Electrochem Soc Interface. 2007;16(Winter):30–36.
- Chu YH, Li HJ, Fu QG, et al. Oxidation protection of C/C composites with a multilayer coating of SiC and Si+SiC+SiC nanowires. Carbon N Y. 2012;50:1280–1288. doi: 10.1016/j.carbon.2011.10.048
- Ren XR, Li HJ, Fu QG, et al. Li, TaB2-SiC-Si multiphase oxidation protective coating for SiC-coated carbon/carbon composites. J Eur Ceram Soc. 2013;33:2953–2959. doi: 10.1016/j.jeurceramsoc.2013.06.028
- Lu XK, Xiao P. Short time oxidation behavior and residual mechanical properties of C/C composites modified by in situ grown carbon nanofibers. Ceram Int. 2014;40:10705–10709. doi: 10.1016/j.ceramint.2014.03.057
- Jayaseelan DD, Sa RG, Brown P, et al. Reactive infiltration processing (RIP) of ultra high temperature ceramics (UHTC) into porous C/C composites tubes. J Eur Ceram Soc. 2011;31:361–368. doi: 10.1016/j.jeurceramsoc.2010.10.013
- Zeng Y, Xiong X, Li GD, et al. Microstructure and ablation behavior of carbon/carbon composites infiltrated with Zr–Ti. Carbon N Y. 2013;54:300–309. doi: 10.1016/j.carbon.2012.11.042
- Cui YY, Li AJ, Li B, et al. Microstructure and ablation mechanism of C/C-SiC composites. J Eur Ceram Soc. 2014;34:171–177. doi: 10.1016/j.jeurceramsoc.2013.08.026
- Blanco C, Casal E, Granda M, et al. Influence of fibre-matrix interface on the fracture behaviour of carbon-carbon composites. J Eur Ceram Soc. 2003;23:2857–2866. doi: 10.1016/S0955-2219(03)00298-X
- Luo RY, Liu T, Li JS, et al. Thermophysical properties of carbon/carbon composites and physical mechanism of thermal expansion and thermal conductivity. Carbon N Y. 2004;42:2887–2895. doi: 10.1016/j.carbon.2004.06.024
- Han JC, He XD, Du SY. Oxidation and ablation of 3D carbon-carbon composite at up to 3000 °C. Carbon N Y. 1995;33:473–478. doi: 10.1016/0008-6223(94)00172-V
- Lamouroux F, Bertrand S, Pailler R, et al. Oxidation-resistant carbon-fiber-reinforced ceramic-matrix composites. Compos Sci Technol. 1999;59:1073–1085. doi: 10.1016/S0266-3538(98)00146-8
- Westwood ME, Webster JD, Day RJ, et al. Oxidation protection for carbon fibre composites. J Mat Sci. 1996;31:1389–1397. doi: 10.1007/BF00357844
- Sciti D, Zoli L, Silvestroni L, et al. Design, fabrication and high velocity oxy-fuel torch tests of a Cf-ZrB2-fiber nozzle to evaluate its potential in rocket motors. Mater Des. 2016;109:709–717. doi: 10.1016/j.matdes.2016.07.090
- Paul A, Venugopal S, Binner JGP, et al. UHTC–carbon fibre composites: preparation, oxyacetylene torch testing and characterisation. J Eur Ceram Soc. 2013;33:423–432. doi: 10.1016/j.jeurceramsoc.2012.08.018
- Carney C. Ultra high temperature ceramic-base composites. Comprehensive Composite Materials II. 2017;5:281–292.
- Corral EL, Walker LS. Improved ablation resistance of C-C composites using zirconium diboride and boron carbide. J Eur Ceram Soc. 2010;30:2357–2364. doi: 10.1016/j.jeurceramsoc.2010.02.025
- Zhu YL, Wang S, Li W, et al. Preparation of carbon fiber-reinforced zirconium carbide matrix composites by reactive melt infiltration at relative low temperature. Scripta Mater. 2012;67:822–825. doi: 10.1016/j.scriptamat.2012.07.044
- Sun W, Xiong X, Huang BY, et al. Zrc ablation protective coating for carbon/carbon composites. Carbon N Y. 2009;47:3365–3380. doi: 10.1016/j.carbon.2009.07.047
- Paul A, Jayaseelan DD, Venugopal S, et al. UHTC composites for hypersonic applications. Am Ceram Soc Bull. 2012;91(1):22–29.
- Rubio V, Ramanujam P, Ramachandran DK, et al. Thermal ablation performance of Cf-HfB2 composites with and without a C matrix deposited by CVI. HTCMC-9 &GFMAT 2016. In: Advances in high temperature ceramic matrix composites and materials for sustainable development. Vol. CCLXIII. Toronto: Ceramic Transactions; 2017. p. 211–222.
- Paul A, Binner JGP, Vaidhyanathan B, et al. Heat flux mapping of oxyacetylene flames and their use to characterise Cf-HfB2 composites. Adv Appl Ceram. 2016;115(3):158–165. doi: 10.1080/17436753.2015.1104050
- Paul A, Rubio V, Binner J, et al. Evaluation of the high temperature performance of HfB2 UHTC particulate filled Cf/C composites. Int J Appl Ceram Technol. 2017: 1–10. DOI:10.1111/ijac.12659