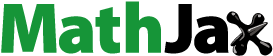
ABSTRACT
Zirconium carbide and oxycarbide bulks were produced via Reactive Spark Plasma Sintering (RSPS) using zirconia and carbon powders. The effects of dwell temperature, uniaxial pressure and heating rate on final chemical composition/stoichiometry were investigated. Heating rates (20–200°C min–1) had no significant effect on RSPS. The carbothermal reduction was hindered by increasing the sintering pressure. This was because of gases entrapped within the closed porosity. Under pressure-less conditions, the reaction onset started at ∼1300°C and the reduction was completed within 10 min resulting in an oxygen content as low as 1.47 at.-%. Under 16 MPa applied pressure, the reaction onset was shifted to 1830°C. Sub-micrometric zirconia powder (<0.1 µm) impacted negatively on the carbothermal reaction because of enhanced ZrO2 sintering preceding the carbothermic reaction. The RSPS reaction mechanism began with zirconia particle densifications between 900 and 1400°C followed by nucleation and growth of an intermediate O-rich ZrOC phase, between 1800 and 2100°C almost all zirconia was consumed. The ZrOC phase then reacted out its oxygen while simultaneously sintering. The results suggest that an optimised RSPS involve a two-step process employing a pressure-less SPS synthesis followed by a pressure-assisted sintering.
Introduction
Zirconium carbide (ZrC) is one of the transition metal carbide refractory ceramics considered as a candidate material for high-temperature nuclear fuel applications such as coated fuel [Citation1–3]. Its properties of most interest are its high melting point >3000 K [Citation4], refractoriness [Citation5,Citation6] and its fission product retention capabilities [Citation7–10] within tri-structural isotropic (TRISO) fuel particles. The use of ZrC over SiC in very high-temperature reactor (VHTR) as pressure vessel layer has shown promising results in retaining isotopes of Ag [Citation11], Cs [Citation8,Citation9,Citation12] and Ba [Citation11,Citation13].
Several processing routes are available for producing ZrC: self-propagating synthesis (SHS) [Citation14–17], mechanochemical synthesis [Citation18–20], solution-based fabrication [Citation21–24], and vapour routes such as chemical vapour deposition [Citation25–27] and physical vapour deposition (PVD) [Citation28–30]. For bulk production, the carbothermic reduction of zirconia is commonly used due to its low cost and reproducibility, similar to the Acheson [Citation31] process for fabricating silicon carbide (SiC). To produce stoichiometric ZrC via the carbothermic reaction enough carbon must be provided to both remove oxygen and form a bond with Zr:(1)
(1) According to the phase diagram, zirconium carbide can accommodate a range of ZrCx stoichiometries ranging from ZrC0.56 to ZrC0.98 at 1850°C [Citation32,Citation33]. When creating sub-stoichiometric compositions from the carbothermic reduction of the metal oxide, following Equation. (1), it has been shown that oxygen is retained effectively forming an oxycarbide [Citation34,Citation35]; this is intrinsic to the reaction as the intermediate step involves formation of an oxygen-rich oxycarbide [Citation36,Citation37].
The carbothermic reduction is a lengthy process requiring several hours for completion at temperatures above 1657°C [Citation38]. Sun et al. [Citation39] proposed a reactive Reactive Spark Plasma Sintering (RSPS) route involving both carbothermic reduction and subsequent sintering. At 1750°C, the reaction was completed within 5 min. Further heating to 1900°C (60 MPa a 10 min dwelling time) resulted in a relative density of 92.3% was achieved.
This paper aims to provide a deeper understating of SPS synthesis/sintering mechanisms of zirconium carbide and oxycarbide bulks. The focus was on the relationship between processing parameters (powder mixture preparation, particle size, heating rate, pressure) and final chemistry/stoichiometry, density and morphology of the produced pellets.
Experimental
Material processing
Acetylene carbon black was used (ABCR product number (P/N): AB119801) together with two undoped ZrO2 (Sigma Aldrich) powders: coarse (P/N: 230693) and fine (P/N: 544760), powder properties are listed in . Powder particle size distributions were obtained by light diffraction analysis (LDA) (Malvern Mastersizer 2000) and powder morphology was observed by both scanning electron microscopy (SEM) (LEO Gemini 1525 FEG-SEM, LEO Electron Microscopy Inc, 1 Zeiss Dr) and transmission electron microscopy (TEM) (JEOL JEM-2100). Quantitative chemical analysis (QCA) (Horiba EMGA 830 (O/N/H) and EMIA 920 V2 (C/S) analysers) was also performed on the ZrO2 powders to check their purity.
Table 1. Properties of as-received powders. Data as provided by the manufacturer.
Dry milling was ineffective for producing a homogeneous mixture with coarse ZrO2. The reacted powder was not homogenous. shows defects and inhomogeneities where carbon and zirconia rich regions, carbon voids, highly densified ZrO2 rich regions, and isolated O-rich oxycarbide regions (lower BSE contrast) are visible. Wet milling reduced greatly or eliminated these defects in the final pellets [Citation40] highlighting the importance of a homogenous powder mixture.
Figure 1. SEM micrographs showing defects due to poor precursors produced from dry milling, (a) axial cross-section showing densified ZrO2 and carbon particles, (b) carbon-rich elongated void, (c) carbon-rich poorly sintered region, (d) highly densified regions with lower porosity fraction than the surrounding bulk, (e and f) lower contrast O-rich phase.
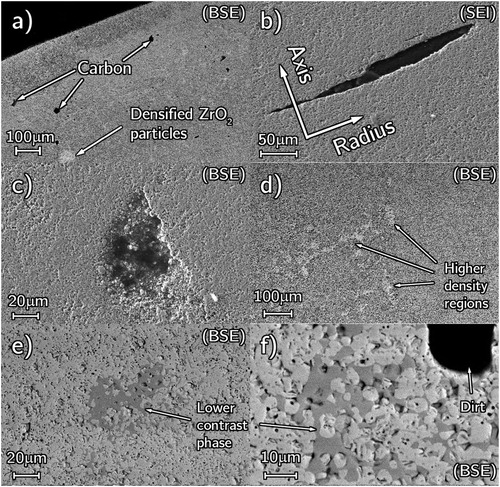
Powder mixtures were all prepared in ethanol. Different target final stoichiometries were attempted following Equation (1). Coarse ZrO2 and acetylene carbon black were prepared in a 500 mL zirconia lined jar using a 1:5 weight ratio (w.r.) of powder to TZP milling media (1:1 w.r. of 5 and 10 mm Ø). Fine ZrO2 and acetylene carbon black were prepared in a 250 mL nylon using a 1:10 weight ratio of powder to TZP milling media (1:1 w.r. of 2.5 and 5 mm Ø).
For both coarse and fine ZrO2, milling was performed in a planetary ball mill (Retsch PM 100) for 4 h at 400 rpm in alternating directions. Drying of powders was done in an oven at 130°C for at least 12 h.
Three sets of experiments () were undertaken to study the RSPS fabrication process of ZrC:
RSPS fabrication (set samples T, Pressure 16 MPa, Temperature 1700–2100°C): to investigate the most suitable heat treatment required to achieve a complete carbothermic reduction.
Effects heating rates and pressures (set of samples RP, heating rate 20–200°C min–1 and pressures from 16 to 38 MPa): to investigate whether heating rate/applied pressure schedule would influence the carbothermic reaction and its final chemistry.
Pressure-less RSPS: applied pressure expected to hinder gas evolution within the reacting powders.
Table 2. Summary of conditions under which pellets were fabricated via RSPS.
All RSPS procedures were carried out within the SPS (FCT Systeme GmbH type HP D 25) using a 20 mm Ø graphite die and punches (unless otherwise stated). A graphite felt was used to minimise radiative heat loss during heat treatment. The inside of the die and punches were lined with graphite paper 0.3 mm thick. The minimum contact force the SPS system would apply to the powders was 5 kN (≈16 MPa). Each sample was made using 8 g of powder (unless otherwise stated).
All reactive-sintering conditions are summarised in .
RSPS fabrication
From a single powder batch, using coarse ZrO2 with ZrC0.9 target composition, three pellets were produced at different dwell temperatures of 1700, 1800 and 1900°C. Each sample was heated at a rate of 50°C min–1 and held for a 1 h dwell time. A further sample (T04) was produced following a full reactive-sintering cycle (see schematic in ) using heating rate of 100°C min–1 and dwell of 2100°C for 22 min, allowing a 10 min period for the reaction, a 2 min application time for raising the sintering pressure of 38 MPa, and 10 min sintering time.
Pressure and heating rate effects
A total of 10 pellets were produced using four different heating rates of 20, 50, 100 and 200°C min–1 up to a 2100°C dwell temperature after which either a minimum (16 MPa) or high sintering pressure was applied (38 MPa). The temperature dwells were held for 22 min allowing for a 10 min reaction, 2 min pressure application and 10 min sinter.
Powder mixtures of fine ZrO2 and carbon were used to make eight pellets with a target composition of ZrC0.9. To observe the effect of powder composition on the end product 2 pellets of target compositions ZrC0.5 and ZrC0.7 were produced using a 100°C min–1 heating rate and high sintering pressure.
For SEM analysis, samples were fractured along the centreline and lightly ground to observe the centre microstructure. Unreacted powders were analysed by QCA together with their resulting products post reaction.
Pressure-less
A single sample was produced using a pressure-less SPS configuration which employs a hollow die having 30 mm outer Ø, 10 mm inner Ø, and 50 mm height. The pressure was applied on the die.
Coarse ZrO2 was mixed to a target composition of ZrC0.7 and reacted using a heating rate of 100°C min–1 to 2000°C and held for a 45 min dwell.
For this reaction, the temperature was measured directly from the die surface rather than from the inside punch as done for all the other samples.
Sample characterisation
The as-received powders were lightly ground by hand, dispersed in water, and deposited on a Cu grid by evaporation for viewing by TEM. High-resolution observation was made in bright field imaging mode. Selected area diffraction patterns (SADP) were obtained using an intermediate aperture and indexed with Powder Diffraction File (PDF) patterns.
All produced samples were analysed by X-Ray Diffraction (XRD) and SEM. XRD was performed in the Bragg–Brentano geometry using a PANalytical XPert Pro diffractometer; lattice parameters were extracted from the diffraction patterns using a Nelson–Riley function (NRF) extrapolation, phases were matched using PDF patterns. Spectra for Rietveld refinement were acquired with a Soller slit angle of 0.02 rad and at 0.017 2θ intervals; standard-less Quantitative Phase Analysis was performed in TOPAS-Academic (Ver. 4.1). Sample topography was viewed using secondary electron imaging (SEI) in the SEM whereas backscatter electron (BSE) imaging was used to view compositional contrast; energy dispersive X-ray spectroscopy (EDS) maps were obtained over 10 min for known present elements. Bulk densities and open porosity were obtained using an Archimedes density kit (Sartorius YDK01LP) with a water infiltration process in accordance with Ref. [Citation41].
Chemical quantification of carbon and oxygen was done by combustion and inert gas fusion (IGF) analyses respectively. Combustion analysis was performed in flowing oxygen forming CO/CO2 gas that yields carbon content. IGF was performed in flowing helium with added free carbon that bonds with released oxygen to form CO/CO2 gas.
Results and discussion
Starting powders
QCA of the ZrO2 powders gave an oxygen content of 66.3 at.-% with N and C contamination below 0.05 at.-% meaning they were pure. SADP for both coarse and fine ZrO2 were identified as monoclinic P21/c1 (PDF 01-087-0047) (). The turbostratic layers within the acetylene carbon black () was matched with the graphite Rm (PDF 01-075-2078) phase.
Figure 3. TEM of as-received ZrO2 powder (a) bright field image of area selected for diffraction, and (b) SADP.
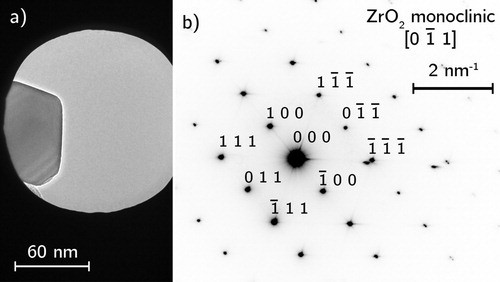
Figure 4. TEM analysis of as-received acetylene carbon black (a) selected area for diffraction, (b) indexed annular SADP, (c) high-resolution image of turbostratic graphitic layers.
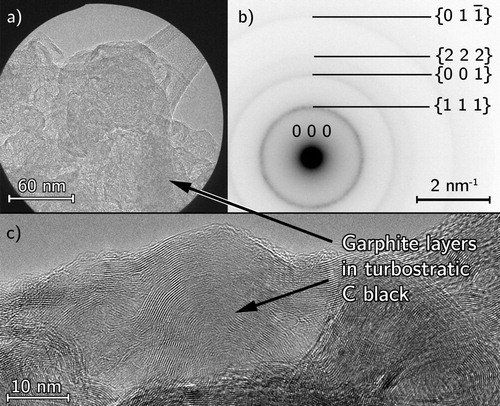
The coarse ZrO2 powder was found to have a mean particle size of 2 µm with some 10 µm hard agglomerates as seen by LDA and SEM in . The wet milling process significantly broke down these agglomerates to mitigate the defect formation in the final samples. Fine ZrO2 was attempted to ensure a powder mixture free from such agglomerates ().
RSPS fabrication
During RSPS pellet fabrication, the carbothermic reaction can be detected as a loss of vacuum pressure in the SPS chamber due to the release of CO gas [Citation42]. As the reaction reached completion gas release stopped allowing vacuum pressure to be regained. By looking at , it is clear that any temperature below 1900°C did not achieve a favourable reaction rate. At 1900°C, the temperature was high enough to promote rapid reactions, this temperature was higher than 1750°C reported by Sun et al. [Citation39]. In their work, a front pyrometer rather than a top one was used as a reference temperature, this could explain temperature difference.
Figure 7. Gas release during RSPS for sample T03, the gas release curve has been smoothed for ease of visualisation.
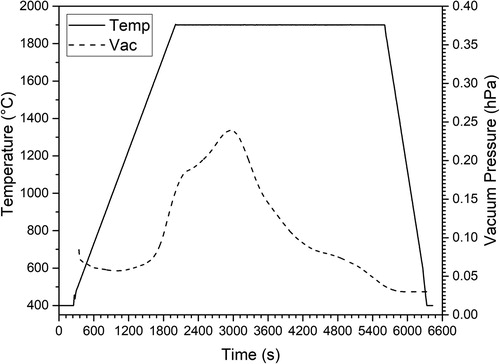
Gas release is a good indicator for the completion of the carbothermic reduction. suggests that sample T03 reacted at 1900°C releasing gas in a broad peak throughout most of its dwell time, meaning the reaction was incomplete. The principal phases detected by XRD () for samples T01, T02 and T03 were monoclinic ZrO2 (m-ZrO2) and ZrC as well as some tetragonal ZrO2 (t-ZrO2) and unreacted C. Through Rietveld refinement approximate phase weight fractions are given in . QCA analysis of the final samples () showed that T03 had a significantly lower C/Zr ratio than T01 and T02. The reaction was still far from being complete with an O/Zr ratio exceeding 0.52.
Figure 8. XRD for samples T01–T04 (a–d) and PDF reference patterns for (e) ZrC, (f) monoclinic ZrO2 and (g) tetragonal ZrO2.
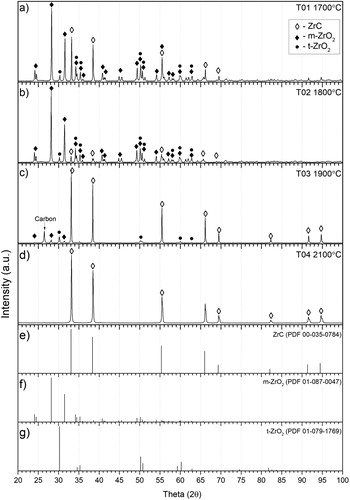
Table 3. Phase lattice parameters and wt-% obtained by Rietveld analysis for T01–T03.
Table 4. QCA for various samples reacted at increasing temperatures as well as P01 reacted without applied pressure.
These findings suggest that a further raising of the temperature would increase reaction yield. Another pellet was produced (T04) using a higher dwell temperature of 2100°C (100°C min–1 heating rate) for 22 min with a sintering pressure of 38 MPa applied during the final 10 min. Under these conditions, the carbothermic reaction took 6 min with an onset temperature of 1690°C as shown by the vacuum pressure curve in . According to their XRD results, a complete reaction was achieved by Sun et al. [Citation39] within 10 min at a dwell of 1750°C (50°C min–1 heating rate), the reaction onset was at 1500°C. The SPS unit used by Sun et al. [Citation39] was capable of applying a minimum pressure of only 5 MPa compared to the 16 MPa used in this study. The higher pressure applied in this study inhibited the gases released within the sintering compacts pushing up the reaction temperatures.
Figure 9. RSPS reaction for T04 showing piston travel, vacuum pressure and applied power. The Roman numerals denote the various reaction segments given in .
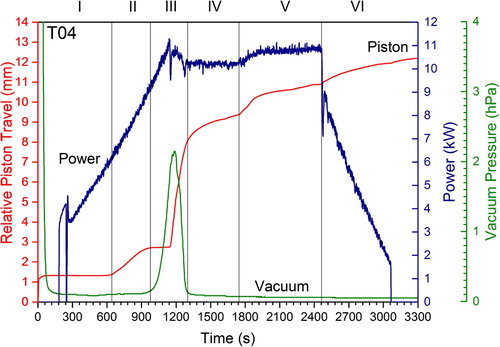
The final product T04 (2100°C) had a 98% TD (), a low O content of 2.70 at.-% (), and an average grain size of 6.1 µm () marking a near complete reaction-sinter cycle. From the various segments of the RSPS process can be identified (denoted by Roman numerals): in segment-I (S-I) thermal ramping commences, in S-II an axial compression (later discussed) is observed, powder reaction occurs in S-III followed by slow sintering in S-IV and pressure-assisted sintering in S-V.
Figure 10. Compositional SEM of T04 (top left) and with overlaid EDS elemental map showing the Zr, C and O distribution thus. Phases are identified in the top-left micrograph as ZrC (bulk), O-rich ZrOC (dark grains), closed submicron pores (dark spots).
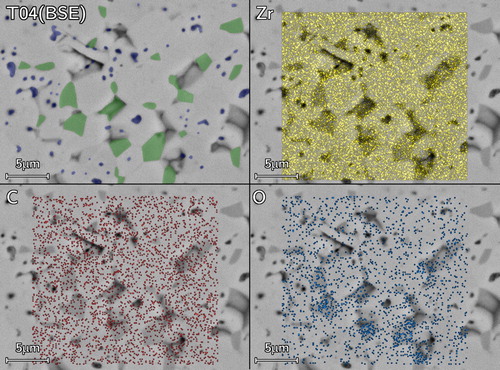
Table 5. Lattice parameters, densities and free carbon contents for all samples, ZrC theoretical density (TD) is taken as 6.59 g cm–3 [Citation18].
Grains with a darker phase contrast were observed in backscatter SEM micrographs of sample T04 (). Qualitative elemental distribution from energy dispersive spectroscopy (EDS) mapping suggested the darker grains had a higher O content. The O-rich grains (identified as dark grains ) were homogeneously dispersed throughout the sample suggesting that these intermediate ZrOC grains did not consume all the oxygen before closed porosity appeared.
Effects of pressure and heating rate
The effect of heating rate and/or sintering pressure on the reaction and final product was investigated using a fine zirconia powder to ensure a homogeneous powder mixtures.
shows the piston travel and vacuum pressure (gas release) for all samples with target composition ZrC0.9 with 100°C min–1 heating (for lower heating rates time was normalised by speeding up time). The onset of the carbothermic reduction (in S-III) occurred around 1830°C ((a)). Vacuum pressure peaks suggest that the reaction terminated sooner for 20 and 50°C min–1 heating rates compared to 100 and 200°C min–1.
Figure 11. (a) Piston travel and (b) gas release during RSPS of RP samples plotted as function of time.
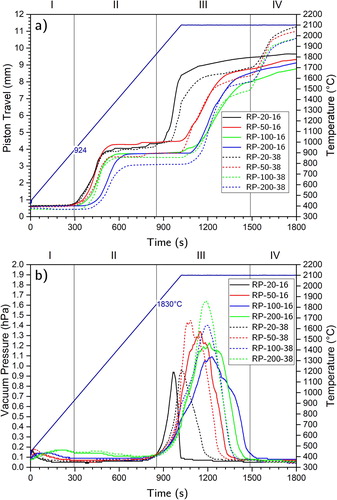
The onset of the first axial compression (in S-II) occurred at 924°C ((a)) with maximum piston speed at ∼1200°C and plateauing at ∼1400°C. Undoped monoclinic ZrO2 undergoes a temperature-induced martensitic transformation from monoclinic to tetragonal polymorphs (m–t) between 930 and 1220°C with an associated 3% volume contraction [Citation43–45], this was not detectable in the shrinkage curves [Citation46].
The chemical compositions of the starting powders, as well as the final pellets, are listed in . Oxygen content of 4.8 at.-% with the average (O + C)/Zr ratio being 1.06 was achieved for samples RP-20-16. The approximated final compositions of powders and pellets were similar suggesting no significant carbon uptake from the die/punches and graphite paper occurred.
Table 6. Experimental QCA and calculated elemental ratios for all samples produced by reactive SPS at 2100°C from the heat rate and pressure set. In addition, initial compositions of the precursor powders are shown.
An average TD of 55% (, RP-50-16) was achieved when applying minimum pressure while 78% TD (, RP-50-35). The extra pressure aided the sintering process, however, comparing with (T04) 98% TD produced under comparable conditions (2100°C dwell, 38 MPa sinter) but with coarse powders. It is concluded that fine ZrO2 particle had a negative impact on the carbothermic reaction advancement due to its enhanced sintering in S-II. RP samples with target composition ZrC0.5 and ZrC0.7 achieved the highest TD while possessing the highest oxygen content of the set. Plotting bulk density against O content for this sample set () shows a trend suggesting O content aids sintering. It was shown by Gendre et al. [Citation35] that O-rich ZrOC samples began shrinkage and achieved maximum densification rates at lower temperatures samples with low O content.
Figure 12. Correlation between oxygen content and bulk density for the set of heating rate and pressure samples produced by RSPS at 2100°C (Minimum Pressure = 16 MPa, Sintering Pressure = 38 MPa.)
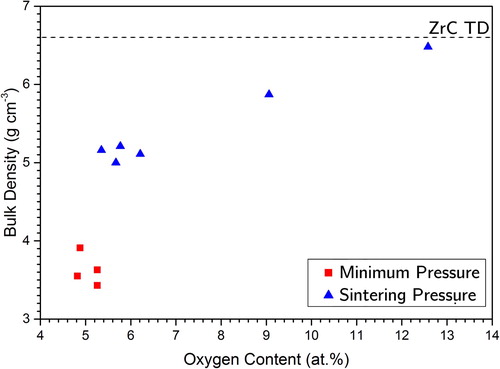
XRD analysis () revealed only ZrC peaks for all pressure and heating rates (their calculated lattice parameters reported in ). Clearly, XRD results are insensitive to the C/O ratio suggesting the need for other techniques. According to David et al. [Citation36], the carbothermic reaction would have been in the maturation phase and composed of a predominantly C-rich ZrOC phase with some remaining free carbon.
Free carbon was observed from the SEM fracture surface micrographs (). The fracture surface revealed fine ZrOC grains (>5 µm) with visible necking (). The samples were then lightly ground to reveal the carbon which smeared across the surface appearing black ((a,b)) meaning it was located between the ZrOC grains. The carbon was generally observed in the centre region of the pellets suggesting the enhanced ZrO2 sintering would have decreased CO release.
Figure 14. SEM micrographs of RP-100-38 showing free carbon between interconnected ZrOC grains (a) boundary between ground surface (appearing black from smeared carbon) and a fractured surface of primarily light contrast ZrOC grains and high magnification images of (b) smeared carbon and (c) ZrOC grains illustrating necking.
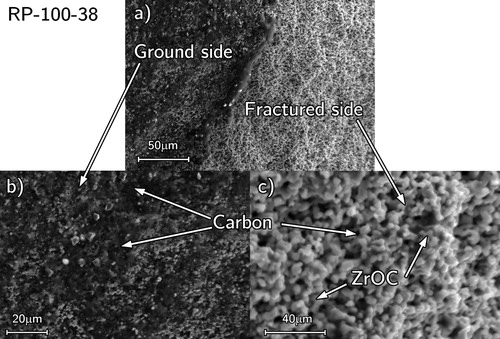
These results suggest the carbothermic reduction during RSPS fabrication follows the same mechanism as described by David et al. [Citation36]; a two-stage process with firstly condensation and nucleation of an oxygen-rich ZrOC crystalline phase with an amorphous shell from the gases, and secondly maturation of the ZrOC particles into ZrC by progressive carburisation once the ZrO2 is consumed. However, during the RSPS process sintering of both the initial zirconia particles and of the newly formed ZrOC (as observed in Figures and ) also occurs during the two stages. These can play a role in retarding the progression of each phase by gradually reducing the ability to remove CO gas from the sample. As observed in these experiments, the size of the zirconia grains also plays an important role in reaction advancement with finer grains rapidly sintering before the carbothermic onset.
The RSPS mechanism is summarised in . Zirconia particles are surrounded by free carbon (a). Between 930 and 1400°C necking and shrinkage of the zirconia particles that make contact occurs (b). Depending on the applied axial pressure the carbothermic reaction begins between 1300 and 1830°C by nucleating an oxygen-rich ZrOC phase in the carbon (c) which continues growing (d) until the zirconia is consumed (e). The ZrOC phase reacts out its remaining oxygen (f) by converting CO into CO2 gas while simultaneously densifying until all O is reacted out or the all pore channels have been closed inhibiting CO gas extraction (g). Further densification occurs with added axial pressure (h).
Figure 16. Mechanism of the RSPS process, (a) starting ZrO2 + C powders, (b) onset of sintering of the ZrO2 forming necks at contact points, (c) nucleation of the O-rich ZrOC phase, (d) simultaneous growth of the ZrOC and consumption of the ZrO2 phases, (e) neck formation at contact points between the ZrOC particles, (f) upon consumption of all ZrO2 the oxygen is reacted out of the ZrOC phase producing ZrC, (g) once all C is consumed ZrC is the only phase remaining and (h) is its sintering in the final phase of the RSPS.
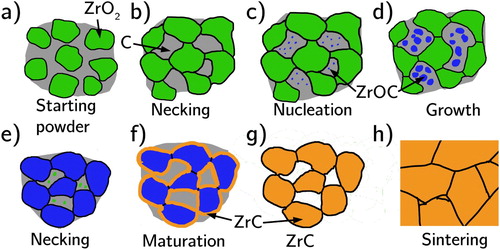
Pressureless sintering
With applied pressure during the RSPS reaction phase having an adverse impact on both gas release and reaction onset, a pressureless reaction was attempted. Using a 45 min dwell at 2000°C (100°C min–1), the reaction took just under 10 min with the reaction onset temperature ∼1300°C; however, minor gas release continued for an additional 20 min at >0.2 hPa. A sample was produced having 37% of TD with the majority of the open porosity located at its centre ((a)). It was composed of interconnected moderately sintered clusters ((a)–(c)) with the densest regions being around the outer rim thus suggesting the reaction started from the outer rim and proceeded inwards leaving the central open porosity ((d)). This minor core ((b)) rim (b) differences were attributed to the contact with graphite tooling which enhanced reactivity and grain growth. This figure also reveals no free carbon in the pellet.
Figure 17. SEM micrographs of pressureless reacted P01 taken from mid pellet height (a) low magnification of pellet centre (b) to rim (c). A higher magnification (d) backscatter image in the rim region.
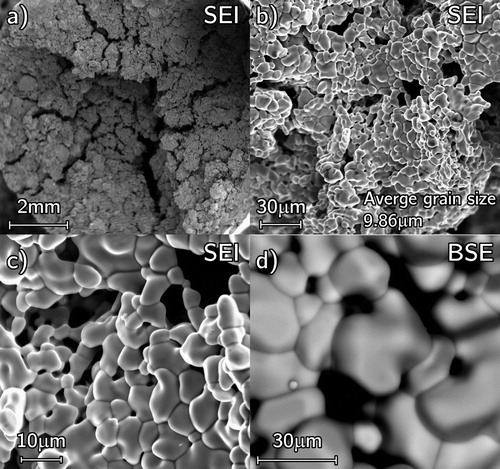
The abundant open porosity suggests that gases from all regions of the pellet had many potential escape pathways during the carbothermic reduction resulting in a highly reacted ZrC product with less than 2 at.-% O content () and a final composition of ZrC0.95. .
Conclusions
The Zr/C stoichiometry, unreacted C/O and final density of pellets produced via RSPS was dependent on two concurrent and competing mechanisms: carbothermic reduction and densification.
When performing the RSPS with a heating cycle up to 2100°C, the minimum applied axial pressure of 16 MPa promoted zirconia sintering (at 930 and 1400°C) between particles in contact. With 16 MPa of applied pressure the reaction onset temperature was at ∼1800°C; when performing RSPS under pressureless conditions the onset temperature occurred much sooner at ∼1300°C. Applied axial pressure hindered gas evolution from the die consequently retarding carbothermic reaction.
The use of low pressure (or pressureless conditions) RSPS was highly favourable to complete the carbothermic reaction. Under such conditions, the reaction was able to occur in significantly shorter periods of time, about 10 min, when compared to traditional carbothermic reductions in furnaces requiring several hours.
Zirconia particle size (0.1 and 5 µm) and mixing method were proved to be an important factor in achieving a chemically and compositionally homogeneous final pellet. Dry mixing resulted in poor mixing and segregation of the zirconia and carbon in the final materials. Surprisingly, a fine zirconia powder (<0.1 µm) was detrimental for the reaction completion because of its enhanced sinterability resulting suppressing carbothermic reduction. Best results were achieved for wet mixing of coarse (5 µm) powders were pellets with a 98% TD a low oxygen content (2.70 at.-%) were obtained in a single SPS cycle. For comparison, commercial ZrC powders have typically an O content between 1 and 2% atomic.
The final pellet chemistry was controlled by varying the zirconia to carbon ratio in the initial powder mixture. The carbothermic reduction of zirconia passes through an intermediate oxycarbide phase phases allowing ZrOC with variable stoichiometries.
To produce near stoichiometric ZrC or ZrOC samples with controlled composition, the zirconia phase and powder mixing must be carefully controlled and a heating regime that minimises zirconia sintering should be selected. It is anticipated that a two-step process employing a pressureless reaction step followed by a pressure-assisted sintering step might allow the fabrication of dense and homogenous ZrCx with controllable stoichiometry.
Acknowledgements
The authors acknowledge Prof Mike Reece, Nanoforce Technology Ltd., Queen Mary, University of London, UK for providing access to the Spark Plasma Sintering facility. EG acknowledges the support of the Centre for Nuclear Engineering (CNE) for his doctoral research at Imperial College London through funding from the Engineering and Physical Sciences Research Council (EPSRC) grant number EP/I003320/1. EG also acknowledges support from Horiba Jobin Yvon SAS, Longjumeau, France for assisting with quantitative chemical analyses of the samples. This paper was originally presented at the Ultra-High Temperature Ceramics: Materials for Extreme Environments Applications IV Conference (Windsor, UK) and has subsequently been revised and extended before consideration by Advances in Applied Ceramics.
Disclosure statement
No potential conflict of interest was reported by the authors.
Additional information
Funding
References
- Verfondern K, Nabielek H, Kendall JM. Coated particle fuel for high-temperature Gas-cooled reactors. Nucl Eng Technol. 2007;39(5):603. doi: 10.5516/NET.2007.39.5.603
- Ueta S, Aihara J, Sawa K, et al. Development of high temperature gas-cooled reactor (HTGR) fuel in Japan. Prog Nucl Energy. 2011;53(7):788–793. doi: 10.1016/j.pnucene.2011.05.005
- Zhou XW, Tang CH. Current status and future development of coated fuel particles for high temperature gas-cooled reactors. Prog Nucl Energy. 2011;53(2):182–188. doi: 10.1016/j.pnucene.2010.10.003
- Jackson HF, Jayaseelan DD, Manara D, et al. Laser melting of zirconium carbide: determination of phase transitions in refractory ceramic systems. J Am Ceram Soc. 2011;94(10):3561–3569. doi: 10.1111/j.1551-2916.2011.04560.x
- Harrison RW, Lee WE. Processing and properties of ZrC, ZrN and ZrCN ceramics: a review. Adv Appl Ceram. 2016;115(5):294–307. doi: 10.1179/1743676115Y.0000000061
- Ogawa T, Ikawa K. High-temperature heating experiments on unirradiated ZrC-coated fuel particles. J Nucl Mater. 1981;99(1):85–93. doi: 10.1016/0022-3115(81)90141-0
- Minato K, Ogawa T, Koya T, et al. Retention of fission product caesium in ZrC-coated fuel particles for high-temperature gas-cooled reactors. J Nucl Mater. 2000;279(2–3):181–188. doi: 10.1016/S0022-3115(00)00015-5
- Minato K, Ogawa T, Fukuda K, et al. Fission product release from ZrC-coated fuel particles during postirradiation heating at 1600°C. J Nucl Mater. 1995;224(1):85–92. doi: 10.1016/0022-3115(95)00032-1
- Minato K, Ogawa T, Fukuda K, et al. Fission product release from ZrC-coated fuel particles during post-irradiation heating at 1800 and 2000°C. J Nucl Mater. 1997;249(2–3):142–149. doi: 10.1016/S0022-3115(97)00223-7
- Bullock RE. Fission-product release during postirradiation annealing of several types of coated fuel particles. J Nucl Mater. 1984;125(3):304–319. doi: 10.1016/0022-3115(84)90558-0
- Chernikov AS, Khromov YF, Lyutikov RA, et al. Fission product diffusion in fuel element materials for HTGR. Spec. meeting on fission product release and transport in Gas-cooled reactors. Berkeley: International Atomic Energy Agency (IAEA); 1985. p. 170–181.
- Reynolds GH, Janvier JC, Kaae JL, et al. Irradiation behavior of experimental fuel particles containing chemically vapor deposited zirconium carbide coatings. J Nucl Mater. 1976;62(1):9–16. doi: 10.1016/0022-3115(76)90279-8
- Ogawa T, Ikawa K. Diffusion of metal fission products in ZrC1.0. J Nucl Mater. 1982;105(2–3):331–334. doi: 10.1016/0022-3115(82)90391-9
- Shabalin I, Luchka M, Shabalin L. Vacuum SHS in systems with group IV transition metals for production of ceramic compositions. Phys Chem Solid State. 2007;8(1):159–175.
- Song MS, Ran MW, Kong YY. In situ fabrication of ZrC powder obtained by self-propagating high-temperature synthesis from Al–Zr–C elemental powders. Int J Refract Met Hard Mater. 2011;29(3):392–396. doi: 10.1016/j.ijrmhm.2011.01.013
- Vasudevamurthy G, Knight TW, Roberts E, et al. Laboratory production of zirconium carbide compacts for use in inert matrix fuels. J Nucl Mater. 2008;374(1–2):241–247. doi: 10.1016/j.jnucmat.2007.08.016
- Li J, Fu ZY, Wang WM, et al. Preparation of ZrC by self-propagating high-temperature synthesis. Ceram Int. 2010;36(5):1681–1686. doi: 10.1016/j.ceramint.2010.03.013
- Mahday AA, El-Eskandarany MS, Ahmed HA, et al. Mechanically induced solid state carburization for fabrication of nanocrystalline ZrC refractory material powders. J Alloys Compd. 2000;299(1–2):244–253. doi: 10.1016/S0925-8388(99)00679-9
- Tsuchida T, Kawaguchi M, Kodaira K. Synthesis of ZrC and ZrN in air from mechanically activated Zr-C powder mixtures. Solid State Ionics. 1997;101–103(Part 1):149–154.
- Yen BK. X-ray diffraction study of mechanochemical synthesis and formation mechanisms of zirconium carbide and zirconium silicides. J Alloys Compd. 1998;268(1–2):266–269. doi: 10.1016/S0925-8388(97)00581-1
- Sacks M, Wang C-A, Yang Z, et al. Carbothermal reduction synthesis of nanocrystalline zirconium carbide and hafnium carbide powders using solution-derived precursors. J Mater Sci. 2004;39(19):6057–6066. doi: 10.1023/B:JMSC.0000041702.76858.a7
- Sham EL, Farfán-Torres EM, Bruque-Gámez S, et al. Synthesis of ZrC/ZrO2 by pyrolysis of modified zirconium alkoxide precursors. Solid State Ionics. 1993;63–65:45–51. doi: 10.1016/0167-2738(93)90084-G
- Dollé M, Gosset D, Bogicevic C, et al. Synthesis of nanosized zirconium carbide by a sol–gel route. J Eur Ceram Soc. 2007;27(4):2061–2067. doi: 10.1016/j.jeurceramsoc.2006.06.005
- Yan Y, Huang Z, Liu X, et al. Carbothermal synthesis of ultra-fine zirconium carbide powders using inorganic precursors via sol–gel method. J Solgel Sci Technol. 2007;44(1):81–85. doi: 10.1007/s10971-007-1595-x
- Wang Y, Liu Q, Liu J, et al. Deposition mechanism for chemical vapor deposition of zirconium carbide coatings. J Am Ceram Soc. 2008;91(4):1249–1252. doi: 10.1111/j.1551-2916.2007.02253.x
- Liu B, Liu C, Shao Y, et al. Deposition of ZrC-coated particle for HTR with ZrCl4 powder. Nucl Eng Des. 2012;251:349–353. doi: 10.1016/j.nucengdes.2011.10.012
- Ueta S, Aihara J, Yasuda A, et al. Fabrication of uniform ZrC coating layer for the coated fuel particle of the very high temperature reactor. J Nucl Mater. 2008;376(2):146–151. doi: 10.1016/j.jnucmat.2008.02.068
- Craciun D, Socol G, Lambers E, et al. Optical and mechanical properties of nanocrystalline ZrC thin films grown by pulsed laser deposition. Appl Surf Sci. 2015;352:28–32. doi: 10.1016/j.apsusc.2015.01.076
- Krebs H-U, Weisheit M, Faupel J, et al. Pulsed laser deposition (PLD) – a versatile thin film technique. In: Kramer B, editor. Advances in solid state physics. Vol. 43. Berlin: Springer; 2003. p. 505–518.
- Woo A, Bourne G, Craciun V, et al. Mechanical properties of ZrC thin films grown by pulsed laser deposition. J Optoelectron Adv Mater. 2006;8(1):20–23.
- Acheson EG. Carborundum: its history, manufacture and uses. J Franklin Inst. 1893;136(3):194–203. doi: 10.1016/0016-0032(93)90311-H
- Guillermet AF. Analysis of thermochemical properties and phase stability in the zirconium-carbon system. J Alloys Compd. 1995;217(1):69–89. doi: 10.1016/0925-8388(94)01310-E
- Storms E, Griffin J. Vaporization behavior of the defect carbides. IV. The zirconium-carbon system. High Temp. Sci. 1973;5(4):291–310.
- Henney J, Jones J. Ternary phases in the zirconium-carbon-oxygen system. Berkshire: Harwell; 1964.
- Gendre M, Maître A, Trolliard G. Synthesis of zirconium oxycarbide (ZrCxOy) powders: influence of stoichiometry on densification kinetics during spark plasma sintering and on mechanical properties. J Eur Ceram Soc. 2011;31(13):2377–2385. doi: 10.1016/j.jeurceramsoc.2011.05.037
- David J, Trolliard G, Gendre M, et al. TEM study of the reaction mechanisms involved in the carbothermal reduction of zirconia. J Eur Ceram Soc. 2013;33(1):165–179. doi: 10.1016/j.jeurceramsoc.2012.07.024
- Maître A, Lefort P. Solid state reaction of zirconia with carbon. Solid State Ionics. 1997;104(1–2):109–122. doi: 10.1016/S0167-2738(97)00398-6
- Prescott CH. The equilibrium between zirconium oxide and carbon and their reaction products at incandescent temperatures. J Am Chem Soc. 1926;48(10):2534–2550. doi: 10.1021/ja01421a008
- Sun S-K, Zhang G-J, Wu W-W, et al. Reactive spark plasma sintering of ZrC and HfC ceramics with fine microstructures. Scr Mater. 2013;69(2):139–142. doi: 10.1016/j.scriptamat.2013.02.017
- Giorgi E. Processing and modelling of Non-stoichiometric zirconium carbide for advanced nuclear fuel applications. Dept Materials, Imperial College. 2016.
- “Part 2: Determination of density and porosity,” in Advanced technical ceramics. Monolithic ceramics. Gerneral and textural properties, no. BS EN 623–2, BSI, 1993.
- Berger L-M, Langholf E, Jaenicke-Rößler K, et al. Mass spectrometric investigations on the carbothermal reduction of titanium dioxide. J Mater Sci Lett. 1999;18(17):1409–1412. doi: 10.1023/A:1006619306945
- Leger JM, Tomaszewski PE, Atouf A, et al. Pressure-induced structural phase transitions in zirconia under high pressure. Phys Rev B. 1993;47(21):14075–14083. doi: 10.1103/PhysRevB.47.14075
- Patil RN, Subbarao EC. Monoclinic-tetragonal phase transition in zirconia: mechanism, pretransformation and coexistence. Acta Crystallographica Section A. 1970;26(5):535–542. doi: 10.1107/S0567739470001389
- Lynch CT, Vahldiek FW, Robinson LB. Monoclinic-tetragonal transition of zirconia. J Am Ceram Soc. 1961;44(3):147–148. doi: 10.1111/j.1151-2916.1961.tb13732.x
- Cutler RA, Reynolds JR, Jones A. Sintering and characterization of polycrystalline monoclinic, tetragonal, and cubic zirconia. J Am Ceram Soc. 1992;75(8):2173–2183. doi: 10.1111/j.1151-2916.1992.tb04480.x